Станок копировальный самодельный: Как сделать токарный станок по дереву с копиром своими руками: чертежи
alexxlab | 29.05.2023 | 0 | Разное
Три идеи копировально-фрезерных станочка
Содержание
Как сделать копировально-фрезерный станок
Используя данный станочек, можно с помощью ручного фрезера вырезать из фанеры или дерева заготовки самой различной формы.
Для изготовления самодельного копировально-фрезерного станка потребуются такие материалы:
- фанера;
- профильная труба (квадратная) из алюминия;
- оргстекло.
Своим личным опытом изготовления станка-кондуктора для ручного фрезера поделился с нами автор YouTube канала YASUHIRO TV. Рекомендуем взять на заметку!
Основные этапы работВ первую очередь необходимо будет изготовить стойку. Вырезаем две заготовки из фанеры толщиной 20 мм и склеиваем их вместе.
Крепим стойку к основанию и по бокам дополнительно усиливаем ее с помощью косынок, вырезанных из фанеры.
После этого необходимо будет изготовить держатель для профильной трубы. Высверливаем в нем отверстия, вставляем резьбовую гайку и вкручиваем барашковый болт (для фиксации профтрубы в посадочном месте).
В торце профтрубы вклеиваем деревянную заглушку. Высверливаем в ней отверстия. Потом крепим квадратную заготовку из плексигласа, к которой будут прикручиваться копировальные шаблоны для ручного фрезера.
На следующем этапе прикручиваем держатель-хомут вместе с профильной трубой к верхней части стойки — как показано на фото ниже.
Далее необходимо будет изготовить копировальные шаблоны. Узор или рисунок может быть любой. Автор сделал шаблоны для вырезания соединительных элементов.
Крепим копировальный шаблон к основанию пластины из оргстекла. Дополнительно изготавливаем корпус для фрезера. Устанавливаем корпус с фрезером и можно приступать к вырезанию заготовки. В данном случае мы вырезаем посадочное место для соединительного элемента.
Чтобы вырезать сам соединительный элемент, нам потребуется другой копировальный шаблон. Автор изготовил его из эпоксидной смолы.
Подробно о том, как сделать копировально-фрезерный станок, можно посмотреть ниже — в авторском видеоролике. Спасибо за внимание.
Template Routing Small Parts | Woodworking IdeasКопировальный гравировальный станок на основе дремеля
Дремель (так же, как и болгарка или дрель) является довольно универсальным инструментом для домашней мастерской.
На его основе можно сделать много разных полезных приспособлений, в том числе и копировальный гравировальный станок.
Большая часть конструкции изготовлена из фанеры. Однако немного металла также потребуется.
Первым делом потребуется подготовить основание для станка. Для этого можно использовать кусок фанеры, ДСП или МДФ с размерами 80х80 см.
К основанию крепятся металлические опоры для вала. Затем в них вставляется сам вал с линейными подшипниками.
Основные этапы работ
На следующем этапе из кусков фанеры автор изготавливает две стойки. Крепим их к линейным подшипникам. Между этими стойками устанавливается еще один вал с подшипниками.
Далее склеиваем два куска фанеры толщиной 18 мм. крепим к ней небольшой вертикальный упор. В итоге у нас получилась площадка, на одном конце которой будет крепиться дремель, а на другом — стилус.
При помощи простых соединительных элементов, изготовленных из фанеры, крепим площадку к линейным подшипникам. Устанавливаем дремель и стилус, и можно приступать к работе.
Подробно о том, как сделать копировальный гравировальный станок на основе дремеля, можно посмотреть на видео ниже. Идея принадлежит автору YouTube канала Hobi Market.
Amazing Woodworking Tool // Router Copy Carver — DuplicatorКак сделать фрезерный станок из дремеля своими руками
Заводские фрезерные станки стоят дорого, и не каждому по карману. Но для домашней мастерской, если вы занимаетесь деревообработкой, можно своими руками сделать простейший аналог на базе обычного дремеля. Основные элементы станка изготавливаются из дерева.
При помощи самодельного фрезерного станка из дремеля можно фрезеровать различные заготовки из дерева или фанеры. Сложные узоры, конечно, сделать не получится. Но для простых орнаментов такой станочек вполне сгодится.
Первым делом нужно напилить заготовки требуемых размеров, из которых потом будет собираться поворотная площадка с креплением для дремеля.
Процесс изготовления самодельного фрезерного станка
Из напиленных деревянных заготовок собирается рамка квадратной формы, по краям которой автор при помощи перового сверла сверлит отверстия под болты. Потом на болты накручиваются гайки, и затягиваются ключом.
Далее в получившейся конструкции необходимо сделать посадочное место под дремель, и закрепить инструмент с помощью самодельных деревянных хомутов.
На последнем этапе работ необходимо изготовить основание с поворотным элементом, и соединить его с деревянной площадкой с дремелем при помощи мебельной петли. После этого можно испытать приспособление в работе.
Подробно о том, как сделать фрезерный станок из дремеля своими руками, смотрите в видеоролике на нашем сайте.
How to Make a Pantograph Router/ Power Carving Tool at Home |DIY|
Андрей Васильев
Задать вопрос
Вертикальный фрезерно-копировальный станок G 90 Griggio (Италия)
Фрезерно-копировальные станки широко используются в столярном и мебельном производстве для работы с концевым инструментом небольшого диаметра. Станок предназначен для фрезерования прямолинейных и криволинейных контуров, пазов и гнезд, а также сверления и зенкования отверстий в мебельных и столярных заготовках. Характерный пример обрабатываемых деталей дверные полотна и мебельные фасады.
Возможно выполнение 2-х видов работ:
– прямолинейное фрезерование рельефа на боковых гранях пласти;
– фрезерование рисунка на плоскости (например ложной филенки) по копиру.
Благодаря применению копировального приспособления становится возможным производство серийных изделий. Эти станки можно применять для фрезерования сложных контуров, таких как арочные окна и двери, рамки для зеркал, мебельные фасады и другие декоративные элементы мебели. Конструктивно станок состоит из несущей рамы, рабочего стола, фрезерной головки.
Рабочий стол регулируется по высоте, фрезерная головка оснащена электродвигателем привода и двухступенчатым передаточным механизмом, обеспечивающим две рабочие скорости фрезерного вала. На рабочем столе имеется отверстие, в котором закрепляется копировальный палец. Он подбирается в соответствии с режущим диаметром фрезы. К нижней части заготовки крепится предварительно изготовленный шаблон. Подавая шаблон по копировальному пальцу, обводим деталь и получаем нужный профиль по заданному контуру. Меняя шаблоны и инструмент, можно получить различные изделия.
Станки имеют прочную конструкцию. Управление станка расположено на фрезерной головке и легко доступно.
В комплект поставки входят:
– Ременная передача
– Шпиндель МК2 с двумя цангами (10 и 12) – цанги можно заказывать другого диаметра.
– Пневматическое управление от педали
– Правое вращение шпинделя.
Порядок работы на станке с шаблоном:
1. В шаблоне из листового материала вырезается паз необходимого профиля.
2. Шаблон устанавливается на стол. При этом обкатной палец стола входит в паз.
3. Сверху на шаблоне крепится заготовка. При ручной подаче палец снизу обкатывает профильный паз шаблона, а сверху на заготовке фрезеруется заданный рисунок.
Обработка ведется вертикальным высокоскоростным шпинделем верхнего расположения. Шпиндельный узел имеет вертикальное перемещение от пнемопривода.
Опции
- Направляющая на столе
- Механический прижим (см. фото в галерее)
- Дополнительный зажим МК2
- Дополнительная цанга
- Передние и боковые удлинители стола – общий размер стола 1200х1000 мм
- Монофазный мотор
- Усиленный мотор 3 /4 ЛС (G 60)
Механичес.![]() |
Аспирацион. колпак | Вакуумный прижим |
Авт. подача | Направляющая на столе |
Производитель: Griggio
Родина бренда: Италия
Размер рабочего стола | 750 x 600 мм |
Вертикальный ход стола | 150 мм |
Вертикальный ход шпинделя | 80 мм |
Частота вращения шпинделя, об/мин | 9000 и 18000 |
Макс. расстояние от стола до головки (без патрона) | 195 мм |
Мотор | 3 кВт |
Диам. аспирационного патрубка | 80 мм |
Расстояние между шпинделем и колонной | 900 мм |
Вес нетто | 400 кг |
Габаритный размер | 1400х800х1900 мм |
Размер в упаковке | 1410х900х2000 мм |
Пока нет отзывов на данный товар.
Оставить свой отзыв
Ваш отзыв поможет другим людям сделать выбор. Спасибо, что делитесь опытом!
Оценка товара:
Достоинства:
Недостатки:
Комментарий:
Имя:
E-mail: не публикуется
В отзывах запрещено:
Использовать нецензурные выражения, оскорбления и угрозы;
Публиковать адреса, телефоны и ссылки содержащие прямую рекламу;
Писать отвлеченные от темы и бессмысленные комментарии.
Джуниор проектирует и собирает самодельный 3D-принтер — The Dispatch компьютерная лаборатория в спальне когда он добавляет последние штрихи к своему последнему инженерному проекту.
Во-первых, начало сложного проекта по созданию самодельного полностью функционирующего 3D-принтера в октябре 2021 года. Кнопфле потребовалось девять напряженных месяцев, чтобы заставить принтер работать. Хотя теперь он работает, Knoepfle полон решимости собрать более совершенный принтер.
«Я очень близок к завершению. Он функционален, но есть вещи, которые нужно немного доработать», — сказал Кнопфле. «Это как торт, но без декоративной глазури».
Используя этот настрой, Knoepfle прошлым летом доработал последние несколько деталей. Начинающий инженер-электрик, Кнопфле зачислен на инженерный курс здесь, в Боуи, под названием «Инженерное проектирование и решение проблем», который преподает преподаватель CTE Кристофер Редмонд.
«Лукас уже пришел на урок с большим объемом информации, — сказал Редмонд. «Он много знал, когда шел в класс. Я помог ему как бы усовершенствовать его знания и немного сфокусировать их, выясняя, как проектировать детали для клиентов».
Прежде чем присоединиться к инженерному сообществу здесь, в кампусе, Кнопфле провел годы, переваривая столько материалов по электрике и математике, к которым у него был доступ.
«Почти все, что я узнал, было получено благодаря чтению книг и статей, просмотру видео, посещению онлайн-форумов, и многое из этого я просто пытался понять, что часто означает поиск всего, что мне нужно знать», — Кнопфле. сказал. «Некоторые примеры ресурсов, из которых я учился: форум блога EEV и канал YouTube, книги по электротехнике для колледжей, спецификации, веб-сайты, предлагающие информацию о технологиях Keysight, электронные сабреддиты и каналы YouTube Great Scott и Marco Reps».
Используя свои базовые знания и экспериментируя методом проб и ошибок, Кнопфле смог починить собственную электронику, такую как случайно сломанный MacBook, радио или газонокосилку. Недавно он начал создавать свои собственные предметы с нуля. Его свободное время часто уходит на поиск и устранение неисправностей старых радиоприемников и пополнение растущего ассортимента незавершенного оборудования.
«Я начал заниматься более крупными проектами только в последние два или три года, — сказал Кнопфле. «Но, помимо принтера, моими наиболее заметными проектами были: радиоуправляемая машина, которую я построил почти полностью с нуля для соревнований во время COVID, работающий самоуправляемый автомобиль, напечатанный на 3D-принтере, простой двоичный калькулятор, я изготовил небольшую панель управления питанием. , и я построил антенную башню, которая могла вращаться на нашем заднем дворе».
Всегда ища более сложные проекты для своей коллекции, он хотел получить более сложное задание. Купив собственный 3D-принтер в декабре 2020 года, он смог наблюдать, как он работает, и был уверен, что сможет воссоздать свой собственный.
«Я видел, насколько хороши принтеры, созданные другими людьми, и мне нужен принтер получше, чтобы я мог участвовать в соревновании 3DBenchy SpeedBoatRace, — сказал Кнопфле. лодку как можно быстрее, соблюдая определенные правила».
Как только принтер заработал, он смог начать печатать товары для других людей. Боуи-младший Джоаб Астран встретил Нопфле на уроке «Введение в инженерию и дизайн» и обнаружил, что Кнопфле изготовил свой собственный 3D-принтер. Оттуда и начался полиграфический бизнес Кнопфле. Астран — лишь один из немногих студентов, которые обратились к Лукасу с просьбой распечатать предметы в 3D.
«Я купил шлем для одного персонажа из сериала, — сказал Астран. «Это того стоило. Товар высокого качества, выглядит прочным и имеет очень мелкие детали».
Для печати объектов Лукас использует бесплатное приложение для моделирования под названием Fusion 360 для проектирования объектов перед печатью. Такие приложения, как Fusion 360, имеют решающее значение для работы процесса печати, поскольку дизайн, созданный в Fusion 360 (или аналогичном приложении), — это то, чему будет следовать механика принтера в течение фактического периода времени печати.
«На разработку некоторых деталей у меня уйдет четыре часа, а на печать — час, — говорит Кнопфле, — тогда как на разработку некоторых деталей уходит час, а на печать — пять часов».
После того, как объект был спроектирован в Fusion 360, принтер использует эту предварительно разработанную модель для создания множества слоев расплавленного пластика, уложенных друг на друга, пока не будут созданы требования, которые программирует Knoepfle. Редмонд особенно впечатлен Knoepfle.
«Лукас вышел за рамки простого создания 3D-принтера, пытаясь раздвинуть границы того, на что способны эти принтеры, используя экспериментальную и не полностью уточненную геометрию», — сказал Редмонд. «Так что это впечатляет, потому что это 3D-принтер, и они действительно крутые. Но определенно впечатляет то, что этот тип принтера еще не полностью принят сообществом».
Редмонд призывает своих учеников искать инженерные возможности помимо 90-минутного урока. Хотя он не хотел бы, чтобы его ученики создавали какой-то конкретный предмет, он надеется, что каждый из его учеников найдет применение своим инженерным знаниям за пределами классной комнаты.
«В самих заданиях много открытых вариантов, — сказал Редмонд. «Таким образом, они могли бы сделать все возможное и создать новые аспекты каждого проекта, которые будут более впечатляющими. Если я прошу какое-то творение базового уровня, они могут сделать его настолько сложным или всеобъемлющим, насколько захотят».
Надеясь получить специальность в области электротехники или астрофизики, многие коллеги Кнопфле задаются вопросом, чего Кнопфле достигнет в ближайшие годы. Редмонд особенно возлагает большие надежды на своего звездного ученика.
«Я думаю, что следующим шагом для Лукаса будет университетская программа, — говорит Редмонд. «Я ожидаю, что в будущем из этого юного ума выйдут действительно крутые вещи, независимо от того, какую школу он посещает».
195 долларов
500 долларов
Вклад
Наша цель
Ваше пожертвование пойдет на поддержку студентов-журналистов средней школы имени Джеймса Боуи. Ваш вклад поможет покрыть наши ежегодные расходы на хостинг веб-сайта. Любые взносы, сделанные через эту услугу, НЕ облагаются налогом. Если вы хотите сделать пожертвование, не облагаемое налогом, ИЛИ подписаться на наше печатное издание, свяжитесь с нами по адресу [email protected]
Как печатать на бумаге Deckle Edge ручной работы — Indian Cotton Paper Co.
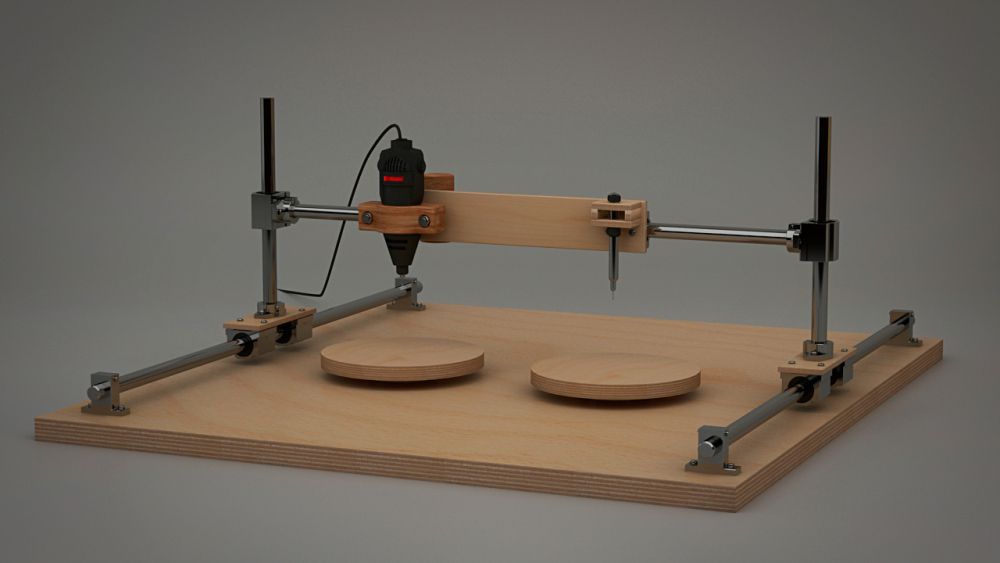
|
Войти / Создать учетную запись
Руководства по вопросам и ответам художников
Печать на бумаге с кромкой ручной работы может быть сложной для новичков в этом носителе — от навигации по настройкам принтера до предотвращения чернильных следов на перистых краях. Мы собрали важные советы, чтобы помочь, охватывая оборудование и методы от некоторых из наших любимых дизайнеров канцелярских товаров, в том числе, когда лучше всего выбрать профессиональный дизайн и услуги печати.
Познакомьтесь с художниками
Каждый из наших дизайнеров канцелярских товаров занимается собственным бизнесом, создавая уникальные наборы со своей собственной эстетикой для свадеб и особых случаев. Они дают свои идеи для начинающих, рисуя с их собственной точки зрения и опыта работы с хлопковой бумагой ручной работы с краем декеля.
Виктория Перес
Креативный директор и дизайнер бутика канцтоваров
Пенсильвания, США
слон лимбо
Виктория — мексиканский дизайнер изобразительного искусства и издательского дела. В 2017 году она начала управлять прекрасной студией свадебных канцтоваров в пригороде Филадельфии. Она черпает вдохновение в разнообразной архитектурной, природной и визуальной культуре Мексики. Обладая более чем 10-летним опытом работы в редакционном дизайне, она любит привносить свой художественный опыт в современные свадьбы. Подсознательно она приняла мексиканско-французский стиль из-за иберийско-европейского влияния в ее жизни.
Таанея и Адитья
Бутик дизайнеров канцелярских товаров
Бангалор, Индия
инвайт_муч
Таанея и Адитья руководят Invite Much — бутик-студией дизайна, расположенной в Бангалоре, Индия. Как дизайнеры они стремятся объединить современный дизайн, традиции, продуманную эстетику и неожиданные макеты, чтобы переосмыслить любовь и праздник. Таанея и Адитья любят экспериментировать с различными материалами, бумагой и методами печати, чтобы создавать действительно уникальные наборы для своих клиентов.
Мартина Лайонс
Дизайнер канцелярских товаров и каллиграф
Жирона, Испания
Мартина Лайонс
Родом из Словакии, Мартина работает в своей мастерской в средневековом городе Жирона в прекрасном регионе Каталонии. Работа Мартины включает в себя ее навыки каллиграфа, художника и иллюстратора. Природа — самый большой источник вдохновения для Мартины, независимо от времени года.
Хайди Филпот
Дизайнер бутика канцтоваров
Вагга Вагга, Австралия
quilldesignau
Хайди управляет Quill — студией канцелярских принадлежностей на заказ, расположенной в Австралии. Будучи художницей в душе, ее дизайн включает в себя роскошные элементы ручной работы из нарисованных цветов, ручных надписей и ее уникальный стиль иллюстраций. Бумага была большой частью ее творческой жизни, когда она была маленьким ребенком, который любил искусство квиллинга. Создание свадебных канцелярских принадлежностей позволяет ей исследовать и развивать свою страсть ко всему бумаге.
Вопросы и Ответы
Дизайн из бумаги ручной работы
- Почему вы используете бумагу ручной работы?
Печать дома
- Есть ли у вас какие-либо советы по печати дома?
- Что посоветуете по выравниванию листов?
- Каким принтером вы пользуетесь?
- Какую толщину вы рекомендуете для печати дома?
Профессиональная печать
- Вы когда-нибудь пользовались услугами профессиональной цифровой печати?
Печать иллюстраций
- Каков ваш рабочий процесс с иллюстрациями и рукописными элементами в печатном дизайне?
Печать светлых тонов
- У вас есть опыт печати светлых тонов на темной бумаге?
Сделай сам или профессиональная печать
- Есть ли у вас какие-либо советы для невест, которые думают о том, чтобы воспользоваться услугами дизайнера, а не печатать приглашения самостоятельно?
Дизайн из бумаги ручной работы
Почему вы используете бумагу ручной работы?
«Мне это просто нравится.
Я чувствую, что это связывает вас с другим видом искусства и повышает ценность финальной части. Это идеальное сочетание осознания того, что кто-то потратил время на создание каждой части, сочетая естественную текстуру и вневременность. .”
«Мы используем бумагу ручной работы из-за того, что она придает нашей работе тактильность и выразительность. Это похоже на любовное письмо от нашего клиента к его гостям. Нас также привлекает то, что бумага ручной работы, возвышенная и персонализированная. отличный выбор для нашего бренда, потому что он соответствует нашей философии воспевания несовершенства и подлинности. Мы рекомендуем бумагу ручной работы клиентам, у которых есть на это бюджет. Это определенно делает нашу работу намного более особенной и придает ей определенное ощущение уникальности. И нашим клиентам это нравится!»
«Как заядлый любитель бумаги, бумага ручной работы предлагает уникальное качество, с которым другие просто не могут сравниться.
В несовершенствах есть грубость и красота».
«Бумага ручной работы — прекрасный материал, который придает свадебным канцелярским принадлежностям особый и неповторимый вид. Я люблю сочетать бумажные приглашения ручной работы с классическим конвертом. Контраст становится еще лучше, когда бумага ручной работы имеет неровные края, а поверхность конверта имеет красивую гладкую и гладкую поверхность. Это идеальное сочетание современного и классического внешнего вида. Я тоже люблю бумажные конверты ручной работы! Каждая из них настолько уникальна, что с их неровными краями кажется, что они полны истории. Они просто идеальны с восковыми печатями и шелковыми лентами».
Печать дома
Есть ли у вас какие-либо советы по печати дома?
«Когда вы печатаете в цифровом виде на бумаге ручной работы, вы должны быть осторожны, так как принтер может иногда оставлять чернила на краях. Маленький трюк — попробуйте перед печатью прогладить края, чтобы они были ровными».
«Я настоятельно рекомендую подумать о большем количестве экземпляров, чем необходимо, особенно если вы впервые печатаете дома!»
«Прежде всего, наберитесь терпения, потому что это более медленный процесс, чем печать на объекте. Закажите дополнительную бумагу, чтобы сделать несколько тестовых отпечатков и иметь их на случай, если печать будет смещена. поглощает много чернил, что приводит к более темному отпечатку.В большинстве домашних принтеров вы можете получить замятие бумаги, даже если замятия нет.Это проявляется, потому что ваши бумажные ролики собирают волокна с бумаги ручной работы и не могут наматывать новую бумага внутри. Совет: используйте ватный тампон, смоченный дистиллированной водой, чтобы очистить ролики. На YouTube есть множество видеороликов о том, как это сделать».
«Убедитесь, что у вас есть дополнительная бумага для пробной печати. Подать бумагу может быть сложно, и я обычно обнаруживаю, что если она не будет подаваться, мне нужно приклеить мельчайший кусочек двустороннего скотча сзади и приклеить его.
на стандартный лист бумаги. Кроме того, всегда проверяйте, что головки принтера очищены перед печатью. К сожалению, вы мало что можете сделать, чтобы чернила не попали на края, для достижения наилучших результатов полезно использовать настройку печати на конверте. всегда имейте под рукой нож или скальпель, чтобы «оттянуть» края, на которых есть чернила, чтобы сохранить неровный край».
Что посоветуете по выравниванию листов?
«Поскольку каждая часть может иметь неправильную форму, чтобы информация была максимально сосредоточена и чтобы не тратить бумагу, мы фактически сортируем их и печатаем наборами по 5 штук. Таким образом, мы можем выровнять каждый набор по углу лотка принтера и гарантировать, что (почти) все листы будут готовы к использованию!»
«В зависимости от того, как ваш принтер подает бумагу, я обычно стараюсь установить нестандартный размер бумаги в настройках печати, чтобы обеспечить правильную печать.
В противном случае я наклею небольшой кусочек двустороннего скотча на обратную сторону и приклею его к верхнему углу. страницы формата A4, убедившись, что вы выбрали правильное положение в диалоговом окне печати».
«Печатайте небольшими партиями по 10–15 штук и старайтесь использовать листы из одной партии. Партии легко отличить, так как они очень похожи. В некоторых случаях аккуратное отрывание тонких краев бумаги помогает получить лучший результат, так как принтеру легче обрабатывать».
«Я всегда помещаю квадратный угол в верхний левый угол и всегда делаю пробный отпечаток на листе обычной бумаги того же размера, чтобы увидеть, как он будет выглядеть. печать, чтобы увидеть, как чернила прикрепляются к бумаге, например, заполняют ли они крошечные дефекты на поверхности бумаги.Я настраиваю печать на максимальном разрешении.Я должен сказать, что я не печатаю канцтовары дома для своих клиентов, так как я у меня нет профессиональной печатной машины, для этого я обращаюсь к своему типографу в городе, поэтому печатаю дома только для стилизованных фотосессий и собственных проб, чтобы убедиться, что все настроено правильно — дизайн по центру, размеры элементов, макет правильный, прежде чем идти в профессиональную типографию».
Какой принтер вы используете?
«Мы используем принтер HP smart tank 790 среднего уровня. Этот принтер достаточно хорошо оптимизирует распределение цветов и является экономичным. Он может печатать более 6000 цветных отпечатков с одной заправкой. Это был наш первый выбор при покупке студийного принтера. и мы очень довольны!”
«Epson Expression XP-960. Это отличный принтер среднего класса с потрясающим качеством печати. Если позволяет бюджет, Canon Pixma 100 — очень популярный выбор среди канцелярских работников».
Какую толщину вы рекомендуете для печати дома?
«Я предпочитаю использовать 300 г/кв.
«Все, что меньше 250 г/м², пройдет через большинство домашних принтеров».
«Бумага средней плотности 200 г/м идеально подходит для каллиграфии, цифровой или плоской печати. Более толстая бумага плотностью 210 г/м² может использоваться для мелкой высокой печати, а плотная бумага (250-300 г/м²) идеально подходит для высокой печати, поскольку она оставляет красивый глубокий оттиск.
Я использую, а также предлагаю в своем портфолио дизайн с цифровой печатью на бумаге ручной работы. толщиной 210 гр. Многие каллиграфы и канцелярские работники не предлагают этот вариант, но я думаю, что он выглядит красиво, а также отлично подходит для повседневных предметов, таких как номера столов, планы столов и меню — это означает, что вы можете сочетать их со своими свадебными приглашениями».
«Мы рекомендуем 200–300 г/м². Все, что выше, может привести к застреванию бумаги и смещению рисунков на ваших листах».
Профессиональная печать
Вы когда-нибудь пользовались услугами профессиональной цифровой печати?
«Обычно мы печатаем все сами! Однако белые чернила на темной бумаге мы обычно отдаем на аутсорсинг, в основном потому, что я всегда предпочитаю, чтобы над нашими работами работал кто-то с большим опытом в этой области. Обычно для полей требуется 30% дополнительных листов. ошибки».
«Да, всегда! На самом деле, если вы печатаете большие заказы, ничто не сравнится с качеством профессиональной типографии. Плюс дополнительное преимущество в виде экономии времени».
«Да, и мне очень нравится результат профессиональной цифровой печати на бумаге ручной работы! Линии очень тонкие, четкие, а черный отпечаток суперчерный — просто элегантный и красивый! В моей местной типографии используется Xerox Color C60/C70. машина Размер вашей бумаги, которую я использовал для своих дизайнов приглашений, обычно A6, поэтому мой городской принтер просто устанавливает печать на размер карты A6, который можно выбрать в настройках. Они также выбрали «масштабировать бумагу по размеру» (каждая печатная машина имеет одинаковое или похожее название для этой опции). Сначала мы попробовали распечатать несколько приглашений, чтобы проверить, возьмет ли машина бумагу, и проблем не было, на самом деле все прошло довольно легко, и мы были очень довольны результатом! Цифровая печать — отличный вариант для клиентов с небольшим бюджетом, но все же желающих использовать бумагу ручной работы.
Это действительно выглядит великолепно, эти тонкие линии действительно меня заводят! Я обычно печатаю на листах белого цвета и цвета слоновой кости, и оба выглядят потрясающе, особенно мне нравится комбинация на белой бумаге, она великолепна! Я понимаю непревзойденную красоту высокой печати и золотой/металлической горячей фольги, но цифровая печать, безусловно, тоже обладает магией».
Печать иллюстраций
Каков ваш рабочий процесс с иллюстрациями и рукописными элементами в печатном дизайне?
«Я всегда сначала делаю наброски своих иллюстраций, а затем использую лист прозрачной бумаги, чтобы сесть поверх наброска и сделать более подробную версию с помощью ручки. Затем я сканирую набросок, переношу его в Illustrator и векторизирую. любой дизайн в любом размере!”
«Я люблю рисовать, иллюстрировать и рисовать. Если я делаю иллюстрацию, я сначала рисую иллюстрацию на белой бумаге, сканирую ее, а затем очищаю в Photoshop.
Затем я редактирую ее в Illustrator, меняя иллюстрацию. из пикселей в вектор, проследив его, а также сделав его прозрачным, чтобы я мог использовать его для целей печати.С помощью этого процесса я могу настроить его без потери качества – я могу сделать его больше, меньше, напечатать на небелой поверхности, установить это под текстом, над текстом, поверх него и т. д.»
«Вся наша работа создается и разрабатывается на дому. В большинстве случаев мы начинаем с простого эскиза на бумаге, а затем работаем над его оцифровкой в Adobe Illustrator и Photoshop. Когда мы работаем с коллажем и изображениями, мы идем прямо в Photoshop, чтобы вырезать, утонченность и рисование на элементах, которые мы используем в нашей работе».
Печать светлых тонов
У вас есть опыт печати светлых тонов на темной бумаге?
«Да, мне это очень нравится! Пока ваш дизайн работает в одном цвете, он будет работать и при печати специальными чернилами, такими как белые чернила».
«Да, однако мы предпочитаем аутсорсинг для такого рода работ профессионалу, который на этом специализируется».
«Я пытался напечатать дизайн дома более светлыми чернилами на темной/черной бумаге ручной работы, но это не сработало. Необходимо купить тонер с белыми чернилами, это специальный тонер для печати белым цветом на более темной бумаге».
Сделай сам против профессиональной печати
Есть ли у вас какие-либо советы для невест, которые думают о том, чтобы воспользоваться услугами дизайнера, а не печатать приглашения самостоятельно?
«Я бы посоветовал вам поговорить со своим продавцом канцтоваров о том видении, которое у вас есть, и о бюджете, с которым вы хотели бы работать. У вас может быть много вариантов, о которых вы не знаете! Мой совет — доверяйте своему продавцы».
«В общем, если вам нравится стиль и вкус дизайнера, полностью доверьте ему все, что он сделает за вас.
Свадебное или любое другое канцелярское дело – очень сложная работа! Лично я предпочитаю делать все с нуля, теперь я предлагаю только индивидуальный дизайн, поэтому, когда мои клиенты получают в руки окончательные канцелярские товары, готовые и красивые, они готовы отправить их своим гостям. Моим клиентам не нужно беспокоиться о вариантах бумаги, вариантах печати, дизайне, выборе цвета, материалах и т. д., они доверяют мне заботиться обо всем за них. Как дизайнер, я имею большой опыт работы с инструментами, методами, рабочим процессом и знаю сквозной процесс для получения наилучшего возможного результата. Я очень благодарна своим клиентам и их доверию, потому что не просто общаться виртуально и не видеть дизайны лично, но они всегда очень довольны конечным результатом. Я бы никогда не стал создавать то, что мне самому не нравится, я любитель деталей!»
«Свадебные канцтовары — это эстетика и вкус. Это истинное отражение вашей истории любви и праздник вашей любви, поэтому полезно сотрудничать с профессиональной дизайнерской студией, такой как мы, чтобы помочь воплотить это видение в жизнь.
Мы действительно сосредоточены на мельчайшие детали. Каждый шрифт тщательно подобран, а цветовая палитра создана продуманной и изысканной. Мы любим использовать элементы дизайна неожиданным образом, отдавая дань культуре и традициям. Мы ставим высокую планку и стремимся создать нечто вневременное для наших клиентов, уделяя особое внимание мельчайшим деталям, которые требуют внимательного взгляда с многолетней практикой».
«В конце концов, все зависит от стиля вашей свадьбы, времени и бюджета. и т. д. Если вы ищете что-то, что вы будете ценить и хранить как память о вашем большом дне, я настоятельно рекомендую нанять дизайнера, который поможет вам. Дизайнеры занимаются этой профессией не просто так — они хорошо обучены и имеют большой опыт в том, что делают, поэтому вы можете быть уверены в потрясающем готовом продукте».
Магазин
- Бумага с краем декеля
- Конверты Deckle Edge
Отзывы
- От каллиграфов
- От DIY-невест
- Из принтеров
Галерея
- Просмотр наборов приглашений
- Обзор цифровой печати
- Посмотреть каллиграфию
Руководства для начинающих
- Совет каллиграфам.
- Совет каллиграфам.