Станок в работе – Работа на ЧПУ станке: обязанности, требования, обучение
alexxlab | 24.03.2020 | 0 | Разное
Бытовой станок. Виды и работа. Применение и выбрать. Особенности
Существует множество разновидностей станков для обработки древесины, каждый из которых предназначен для выполнения определенных функций. Такое оборудование стоит недешево, и занимает пространство в мастерской. В связи с этим, позволить себе купить все разновидности станков трудно не только в финансовом плане, но и сложно реализуемо с практической точки зрения, поскольку чтобы разместить полный набор оборудования нужно много места. При ограниченном бюджете и пространстве большинство мастеров и любителей используют бытовой станок универсального типа.
Что может деревообрабатывающий бытовой станок
Универсальные станки бытового типа представляют собой многофункциональное оборудование, которое может выполнять широкий набор функций. Такая установка имеет один двигатель, который передает вращение на вал. При этом сам вал может оснащаться различными деревообрабатывающими насадками. Станина для закрепления деталей имеет ряд регулировок, а также набор съемных деталей, которые расширяют возможности станка, и позволяют проводить точную регулировку параметров обработки.
Многофункциональный бытовой станок предлагают зарубежные и отечественные производители, поэтому на рынке представлен ассортимент различного ценового сегмента. Его мощность, диапазон настройки, а также набор функций отличается, но практически любое оборудование универсального типа может выполнять:
- Распиловку.
- Фугование.
- Рейсмусование.
- Фрезерование.
- Сверление.
Распиловка
Что касается функции распиловки, то ее может проводить даже самое дешевое оборудование из низкого ценового сегмента. Любой бытовой станок внешне напоминает стандартный циркулярный стол, за исключением того, что имеет навесное оборудование для расширения функций. В него можно устанавливать обычный пильный диск и проводить распиловку древесины на заготовки. Зачастую более дорогие модели бытового оборудования оснащаются линейками, а также регулируемыми опорами, которые позволяют настраивать обрезку под требуемым углом. Это позволяет срезать заготовку под 45 или 90 градусов, что является необходимым при точной сборке ящиков, полок, мебели, беседок, пчелиных ульев и прочих изделий. Даже если модель станка не имеет в комплектации таких упоров, сделать их своими руками не составит особого труда, поэтому даже самое дешевое оборудование можно модернизировать.
Еще одной возможностью данного оборудования является установка точильного диска. Вполне возможно установить точильный камень для проведения заточки ножей и прочего инструмента. Конечно, работать на обычном наждачном станке гораздо удобней, но при его отсутствии можно обойтись и универсальным оборудованием.
Фугование
Немного в стороне на валу, к которому зажимается пильный диск, закреплены ножи для фугования. Благодаря вырезу на столешнице они открыты, что позволяет проводить обработку заготовок. В зависимости от мощности станка глубина регулировки фугования может отличаться. Для оборудования оснащенного двигателем на 1,5-2,2 кВт этот показатель обычно составляет от 0 до 4 мм.
Стоит отметить, что фуговальные ножи выступают из столешницы даже при работе пильного диска, поэтому с таким станком нужно быть предельно внимательным. В некоторых станках предусмотрен специальный щит, который позволяет прикрыть фуговальную часть, чтобы обезопасить оператора. Также данная часть столешницы имеет возможность установки бокового упора, чтобы проводить фугование под углом. Данная функция является необходимой при создании пустотелых колонн.
Рейсмусование
Отдельные модели многофункциональных бытовых станков позволяют проводить перенастройку фуговального станка под рейсмус. Для этого на столешницу устанавливается верхний упор, который позволяет прижать заготовку к станине. Стоит отметить, что удобства регулировки такого навесного оборудования существенно уступают настоящим рейсмусам. Хотя при работе с таким условным рейсмусом и придется повозиться, но можно получить вполне качественную заготовку для склейки мебельного щита. Глубина строгания полностью соответствует тем показателям, на которые способен станок при использовании в качестве фуганка.
Более дорогие модели станков имеют продуманную систему настройки рейсмусовых насадок, поэтому изменение высоты среза можно проводить практически на ходу, без потери времени.
Насадка рейсмуса выполнена в виде рамки для прижима, вверху которой имеются ролики для прокатывания заготовки. Они не подключены к приводу, поэтому затягивание детали для строгания осуществляется только фуганком. В большинстве случаев станки не протягивают заготовку сами, поэтому ее нужно толкать. Такое неудобство не позволяет обрабатывать большое количество древесины, но для бытовых целей этого вполне достаточно.
Фрезерование
Вместо пильного диска возможно установить поперечную фрезу, которая на него похожа, но является более широкой. С ее помощью можно обрабатывать торцы заготовок для создания пазов, применяемых в ящичном соединении. Также дисковая фреза при продольном распиле позволяет создать паз для установки шипа.
Конструкция некоторых станков позволяет устанавливать на вал фрезерную головку с ножами. При этом они выходят через вырез в столешнице, предназначенный для пильного диска. На головку можно устанавливать ножи различной формы, что позволяет за один проход строгать ровные заготовки, превращая их в фигурную поверхность. Благодаря этому бытовой станок можно применять для создания наличников, багетов и плинтусов.
Сверление
На конце вала станка, на котором проводится крепление пильного диска, а также ножей фуганка, имеется зажимной патрон. В него можно устанавливать сверло, и проводить сверление отверстий в древесине или прочих материалах. По функциональности данное расширение станка уступает ручной дрели, но также имеет свои преимущества. Возможно провести точное позиционирование точек сверления, что особенно важно при производстве корпусной мебели. Фактически, можно провести тот самый объем работ, что и на присадочном станке. Конечно, за один раз проводится сверление только одного отверстия, но при точной разметке можно добиться вполне качественного результата.
Если вместо сверла установить фрезу, которая применяется в ручных фрезерах, то можно создавать выборку древесины. Таким образом, чтобы получить четверть или паз можно не использовать более дорогие дисковые фрезы или пильный диск.
Одна из малоизвестных функций, которыми обладает бытовой станок, является возможность подсоединения гибкого вала к зажимному патрону. Он не идет в комплектации с оборудованием, но встречается в продаже в любом магазине инструментов и электрооборудования.
Установка гибкого вала позволяет превратить станок в гравер. Нужно отметить, что такое расширение не совсем удобно. Дело в том, что установленный в станке двигатель чрезмерно мощный, поэтому потребляет довольно много энергии. При этом использование многофункционального станка в таком качестве дает такой же результат, как и гравер на 100-200 Вт. При этом наблюдается довольно высокий уровень шума, что не совсем удобно. Несмотря на это, для выполнения кратковременных несложных задач и применяется бытовой станок. К преимуществам его использования можно отнести то, что мощный двигатель не останавливается при нагрузке, что является распространенной проблемой в слабых граверах.
Можно ли сравнивать профессиональное оборудование и бытовые станки
Бытовые станки отличаются от профессионального оборудования тем, что имеют компактные габариты и могут выполнять не одну задачу, а имеют целый набор функций. С практической точки зрения использование бытового оборудования не настолько удобно как профессионального. Такие станки имеют меньшую производительность, они не предназначены для обработки крупногабаритных заготовок, а кроме этого их конструкция разборная. Фактически, выполнив один вид работ, оборудование нужно перенастроить, сняв одни детали и установив другие. Естественно на это нужно время. В конечном счете получается, что на профессиональном оборудовании один объем работы можно сделать в несколько раз быстрее, чем применяя бытовой станок.
Для профессионального занятия деревообработкой бытовые станки не лучшее решение, если необходимо работать быстро и много. Если же оборудование задействуется нечасто, или выполняет небольшие объемы, что характерно для любителей деревообработки или частных мастеров делающих мебель из массива на заказ, то универсальные установки идеальное решение. Фактически в мастерской находится только один компактный станок, при этом все остальное пространство можно занять заготовками и ручным инструментом.
На что обратить внимание при покупке
Покупая бытовой станок для обработки древесины, следует обратить внимание в первую очередь на мощность двигателя. Оборудование со слабым мотором до 2 кВт не сможет работать с твердой древесиной, такой как бук или дуб. Пильный диск может останавливаться, а глубина строгания будет слишком низкой. Мощный двигатель залог удобной работы.
Также стоит обратить внимание на наличие подставки. Многофункциональные станки выпускаются в настольном варианте, а также напольном с ножками. В случае отсутствия в мастерской стола для установки следует брать модель с подставкой.
Что касается набора функции, то в различных модификациях станков их количество может отличаться. В этом плане нужно ориентироваться только отталкиваясь от тех действий, которые будут выполняться на данном оборудовании. Немаловажным аргументом в пользу определенной модели станка является наличие дополнительного навесного оборудования для расширения функций, а также простота регулировки. В одних моделях настройка проводится по удобной шкале специальными ручками, которые можно крутить вручную, в то время как с другими нужно вращать гаечный ключ и все перепроверять, прикладывая линейку.
Похожие темы:
tehpribory.ru
Основные направления развития металлообработки в России и Европе
В середине XVIII столетия человеческая цивилизация вплотную приблизилась к одному из наиболее значимых этапов своего развития – периоду, который историки впоследствии назовут промышленной революцией, или Великим индустриальным переворотом. К этому времени в наиболее развитых странах мира, список которых тогда возглавляла подпитываемая многочисленными колониями Англия, начался активный процесс перехода от преимущественно аграрного устройства экономики к индустриальному. Зарождающийся промышленный капитализм обусловил потребность в повышении производительности труда, а также улучшении качества и снижении себестоимости продуктов производства.
Данным преобразованиям способствовало множество факторов: развитие торговли и формирование рынка наемного труда, становление банков и системы кредитования, эволюция права и расцвет точных наук, рост количества изобретений и технических новаций. Примитивный ручной труд и деревянные орудия труда уже не могли обеспечить потребности общества. Фабрики и мануфактуры остро нуждались в механизмах и машинах, изготовленных из металла. Именно быстро прогрессирующая
Металлообработка, как основа фабричного производства машин и механизмов
До начала индустриального переворота технологии обработки металлов путем резания, сверления и шлифовки совершенствовались крайне медленно, и эта работа носила разрозненный характер. В мануфактурный период потребность в новых инструментах подвигла владельцев фабрик к созданию вспомогательных мастерских, оборудованных элементарными сверлильными, точильными и шлифовальными станками. Часть из них приводилась в действие мускульной силой, другие – энергией воды. Но общим для всех этих приспособлений была минимальная степень механизации процесса обработки, что обуславливало низкое качество изделий.
В начале XVIII века изготовление деталей на станке выполнялось рабочим, который был вынужден удерживать обрабатывающий инструмент в руке. К сожалению, мировая техническая общественность тогда не узнала об изобретении талантливого русского механика А.К.Нартова – суппорте резцедержателе, которым он еще в 1717 году оснастил построенный им же токарный копировальный станок. В России тех лет данная разработка, как и многие другие изобретения этого талантливого «начальника» придворной токарни и воспитанника царя реформатора Петра I, была не востребована, и на время забыта.
Только ближе к концу столетия конструкция Нартова была изучена и стала отправной точкой для создания управляемого механического суппорта английским механиком и изобретателем Генри Модсли. После этого события устройство почти всех основных видов станков, применявшихся в мануфактурах и на фабриках, подверглось основательной модернизации. До этого токарные работы выполнялись при помощи примитивных держателей резца, что не позволяло обеспечить необходимую точность обработки. С появлением управляемого суппорта данная проблема была окончательно устранена.
«Социальный» заказ и потребность фабрик в новых, воплощенных в металле средствах производства, всячески стимулировали развитие способов металлообработки. Эта востребованность стала реальным катализатором процессов индустриализации, и привела к созданию новой отрасли промышленного производства – машиностроения. Однако, для того чтобы в полной мере удовлетворить технические запросы быстро развивавшегося общества, машиностроению предстояло совершить качественный технологический прорыв.
Важнейшие разработки и изобретения эры индустриального переворота
1.Токарный станок 
В Англии революционные преобразования экономики начались с бурного прогресса в текстильной промышленности. Обеспечить эту отрасль новыми, более производительными машинами удалось благодаря не менее быстро развивавшимся технологиям и совершенствованию методов металлообработки. Спрос обеспечил быструю эволюцию средств производства, и, в первую очередь, одного из основных на то время технических средств обработки металлов резанием – токарного станка. На протяжении XVIII – XIX столетий конструкция токарного станка претерпела множественные усовершенствования, среди которых следует особо отметить следующие:
● 1712 г. Изобретение российским механиком Андреем Константиновичем Нартовым самоходного суппорта, обеспечившего возможность фиксированного крепления резца и его точного линейного перемещения вдоль обрабатываемой детали.
●1718 – 1729 г.г. Совершенствование А.К.Нартовым устройства токарного станка – копира, в котором траектория хода привода суппорта и передвижение копировального пальца управлялись различными участками ходового винта с отличающимися параметрами нарезки.
● 1751 г. Первый в мире полностью металлический токарный станок универсального типа от француза Жака де Вокансона. Его отличала тяжелая станина, мощные, изготовленные из металла центры, и V-образные направляющие.
● 1778 г. Новые типы винторезных станков авторства английского механика Д. Рамедона. Для изготовления резьбы с тем или иным шагом, в одном из них применялись сменные шестерни, в другом за движение резца отвечала специальная струна, которая наматывалась на вал определенного диаметра.
● 1795 г. Усовершенствованный французским механиком Сено функционал винторезного станка. Помимо уже применявшихся в станках Рамедона сменных шестерен и большого ходового винта, очевидным отличием данной разработки стал оригинальный конструктив механизированного суппорта.
● 1798 – 1800 г.г. Совершенная модель универсального токарного станка, построенная английским инженером Генри Модсли и его учениками. Данная конструкция стала прообразом токарно-винторезных станков будущего, и во многом определила направление развития данного вида металлообрабатывающего оборудования на сто, и более лет вперед. Кроме того, Г. Модсли первым начал процесс стандартизации резьбовых соединений.
● 1815 – 1826 г.г. Работы учеников и последователей Генри Модсли – Р.Робертса и Д.Клемента. Первому из них удалось улучшить станки за счет оптимального расположения ходового винта, создать элементарный вариатор в виде зубчатого перебора и сделать более удобным управление, вынеся все переключающие органы ближе к рабочему месту токаря. Д.Робертсу историки станкостроения приписывают создание лоботокарного станка, позволившего обрабатывать детали крупных диаметров.
● 1835 г. Важнейшая доработка механизма подачи токарных станков британским инженером-механиком и изобретателем Джозефом Витуортом – еще одним учеником Г.Модсли. Он разработал механизм поперечной передачи и связал его с продольным приводным механизмом.
● 1845 г. Автоматизированный револьверный станок американского инженера С.Фитча, предложившего прототип револьверной головки с восемью закрепленными в ней сменными резцами. Быстрая смена режущих инструментов снизила до минимума потери времени на их переустановку, и резко повысила производительность труда при обработке серийных изделий.
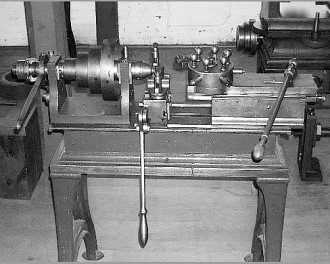
● 1873 г. Создание прообраза металлорежущего токарного станка автомата американским инженером и предпринимателем Х.Спенсером, который усовершенствовал конструкцию разработанных его предшественниками револьверных станков. Важной новацией авторства Х.Спенсера стала модернизированная система управления с использованием кулачкового механизма и распределительного вала.
● 1880 – 1895 г.г. Начало мелкосерийного выпуска токарных систем фирмы «Кливленд» и металлорежущего оборудования других производителей, построенного по принципу многошпиндельного станка автомата. Достигнутое таким образом расширение функциональных возможностей позволило реализовать давнишнюю мечту разработчиков промышленного металлорежущего оборудования – за счет совмещения различных операций многократно повысить производительность и экономическую эффективность работы станочного парка.
2.Фрезерный станок
Обтачивая вращающуюся деталь, невозможно выполнить обработку продольных и наклонных плоских поверхностей, а также устройство всевозможных пазов, канавок, подсечек, сплошных «карманов» и окон. Закрепив неподвижно деталь, и сделав подвижным вращающийся режущий инструмент, человечество открыло для себя фрезерные работы еще в XVII веке, когда китайские мастера изготовили достаточно примитивный станок, тем не менее, позволивший обработать крупную плоскую деталь для астрономического прибора.
Однако обеспечить точную работу механизма подачи вращающейся фрезы, достаточную для выполнения мелких работ по металлу, оказалось значительно сложнее, чем управлять суппортом с неподвижно закрепленным резцом в токарном станке. Разнообразные конструкции для фрезерования плоских поверхностей, разработанные в XVII веке, годились только для обработки изделий из дерева или кости. Многочисленные попытки создать станок для фрезерования металлических деталей успехом в то время не увенчались.
В полной мере решить эту задачу смог американский промышленник и инженер Илай Уитни, который в 1818 году построил полноценный фрезерный станок с механизированным суппортом, длительное время применявшийся на принадлежавшем ему оружейном заводе. Несмотря на наличие деревянной станины, деревянного двухступенчатого шкива и кустарный внешний вид, фрезерный станок конструкции Илая Уитни успешно справился со всеми возложенными на него функциями, и работал практически без поломок.
Заслуживают нашего внимания конструкции специализированных фрезерных станков, разработанных российскими механиками для оружейного завода в Туле. Уже к 1826 году там были сданы в эксплуатацию два станка для подрезки казенных концов ружейных стволов. Закрепленный в специальном подвижном приспособлении, ствол подавался в рабочую зону торцовой фрезы, Конструктивно и по внешнему виду изготовленные тульскими мастерами станки были совершеннее изделий Илая Уитни, и обеспечивали более высокое качество обработки поверхности деталей.
В первой половине XVIII века технический прогресс в области совершенствования конструкций и функциональных возможностей фрезерных станков был связан с потребностями оружейников. Очередной и более совершенный, чем разработки предшественников, прототип фрезерного станка в 1835 году был изготовлен механиками американской оружейной компании «Гай, Сильвестр и Ко». Отличительной особенностью данной конструкции стала уникальная система перемещения фрезы в вертикальной плоскости, которая впоследствии была преобразована в более надежный механизм подъема стола.
В середине XVIIIвека возможности фрезерных станков наконец-то были востребованы «мирными» предприятиями, которые уже вовсю работали на нужды индустриальной революции, и вынуждены были обрабатывать плоские поверхности шлифованием. Первой разработкой гражданского назначения стал станок английской компании «Нэсмит и Гейскелл», который выполнял фрезерование плоских граней гаек. Несмотря на узкую специализацию, это устройство, по сути, являлось универсальным горизонтально-фрезерным станком, и вполне могло применяться на множестве других операций.
Еще более совершенную конструкцию фрезерного станка в 1855 году разработала и воплотила в металле американская компания «Линкольн» (Phoenix Iron Works Джорджа Линкольна). Рабочий стол этого изделия, как и у предшественников, приводился в движение ременной передачей и червячным механизмом, но для продольного перемещения стола здесь был применен ходовой винт с маховиком. Установка фрезы в вертикальной плоскости выполнялась в данной конструкции перемещение подшипников оправки, что также стало определенной технической новацией, обеспечившей удобство и повысившей точность работы. Схема станка стала классической и была заимствована многими производителями фрезерного оборудования.
История создания этого популярного станка и его широкого распространения тесно связана с именами людей, которые впоследствии основали всемирно известную и в наши дни компанию. Фрэнсис Пратт, создатель «Линкольна», работал начальником производства в Phoenix Iron Works вместе с Эмосом Уитни (родственником родоначальника фрезерного оборудования Илая Уитни). Оба были талантливыми механиками и изобретателями и в 1860 году основали Pratt & Whitney Company, специализирующуюся на выпуске металлообрабатывающего оборудования. В годы Гражданской войны в США компания существенно разрослась и станки под этой маркой стали продаваться по всему миру. В настоящее время Pratt & Whitney– крупнейший поставщик газотурбинных двигателей и генераторных установок.
3.Паровой двигатель Уатта – востребованный привод станочного оборудования
Приводимые в действие силой ветра или падающей воды токарные, сверлильные и фрезерные станки не могли в полной мере обеспечить необходимые параметры вращения заготовок или инструментов, что существенно сказывалось на качестве обработки металлов. Чтобы организовать фабричный выпуск новых машин и других средств производства, требовался мощный движитель, который смог бы с необходимой скоростью и силой приводить в действие механизмы станочного оборудования. Таким двигателем стала созданная шотландским инженером, механиком и изобретателем Джеймсом Уаттом универсальная паровая машина.
Оригинальную конструкцию «парового насоса» в 1698 году разработал и изготовил Томас Сэвери, который в том же году запатентовал свое изобретение и применил его для откачивания шахтных вод. По причине низкой производительности и большого расхода топлива использовать этот двигатель в качестве привода агрегатов станочного оборудования было невозможно. Данную конструкцию, начиная с 1705 года, пытался улучшить другой англичанин – Томас Ньюкомен. Он довел построенный на ее основе водоподъемный насос до мелкосерийного производства, однако из-за недостаточной мощности для применения в промышленности этот двигатель также не подходил.
Свой вариант парового двигателя научный консультант университета в Глазго Джеймс Уатт разработал в 1764 году. Но только спустя 12 лет, когда его партнером стал состоятельный промышленник Мэтью Болтон, изобретателю удалось организовать производство и коммерческую продажу изготовленных паровых машин. Именно Уатт сумел преобразовать поступательное движение поршней своих машин во вращение нагрузочного выходного вала. Начальная конструкция потом многократно дорабатывалась и становилась все более мощной и экономичной. Но главное было сделано – в конце XVIII века металлорежущие станки получили такой необходимый, и не зависящий от природных явлений, автономный привод.
Дальнейшее развитие металлообрабатывающих станков
Индустриальная революция обусловила необходимость в разработке и выпуске машин практически для всех отраслей промышленного производства. От уровня развития средств металлообработки зависело состояние экономики, поэтому техническая база станкостроения непрерывно совершенствовалась. Конструкция механического суппорта, первично разработанная для крепления и управляемого перемещения резцов токарного станка, была с успехом применена в других видах станочного оборудования.
Для создания новых металлообрабатывающих устройств применялся не только механический суппорт, но и другие конструктивные узлы токарного станка – система зубчатой передачи, механизм подачи, зажимные устройства и элементы кинематики. Многочисленные американские машиностроительные заводы, которые к середине XIX века в техническом развитии обогнали родоначальников станкостроения – англичан, массово выпускали шлифовальные, расточные, токарно-револьверные, универсально-фрезерные и карусельные станки, ставшие со временем основой промышленного расцвета и мощи США.
В 60-е годы XIX века машиностроение начало стремительно развиваться в Германии и России. В нашей стране одним из пионеров станкостроения стал Тульский оружейный завод, который для собственных нужд начал выпуск токарных, фрезерных, сверлильных, резьбонарезных, шлифовальных, протяжных и шлифовальных станков. Успешно начали работу машиностроительные предприятия, построенные в Москве, Ижевске, Сестрорецке, Воронеже и Санкт-Петербурге. Первым специализированным предприятием станкостроения стал московский завод братьев Бромлей, позднее переименованный в «Красный Пролетарий».
Российские заводы быстро освоили производство всего необходимого ассортимента станочного оборудования, включая оригинальные собственные разработки продольно-строгальных и колесотокарных станков. Несмотря на эти очевидные успехи, общий уровень российского станкостроения тех лет существенно отставал от количественных и качественных показателей машиностроительных отраслей Англии, США и Германии, поэтому основная масса станочного оборудования для заводов и фабрик России приобреталась их владельцами за рубежом. Типовым оснащением металлообрабатывающих предприятий того времени были станки шести видов:
● Токарные, на которых обтачивали наружные и внутренние поверхности тел вращения, выполнялась обработка гладких и ступенчатых валов, изделий в форме шара или конуса, растачивались цилиндрические детали и нарезалась резьба.
● Фрезерные станки, позволявшие обрабатывать внешние и внутренние поверхности заготовок деталей сложной формы, к которым предъявлялись повышенные требования по точности и качеству.
● Строгальные станки горизонтального и вертикального типа, предназначенные для обработки заготовок и изделий с плоскими поверхностями.
● Сверлильные станки, при помощи которых высверливались, растачивались и обрабатывались отверстия, а также могли нарезаться резьбы.
● Шлифовальные машины, на которых производилась чистовая обработка изделий специальным абразивным инструментом и материалами.
● Станки специального назначения, разработанные и изготовленные для выполнения ограниченного количества или одной конкретной операции технологического процесса.
В конце XIX века металлообрабатывающее оборудование всех основных групп дифференцировалось, и выпускалось в виде универсальных станков, либо машин специального назначения. Действительно, зачем тратиться на сложный и дорогой станок, если он будет использоваться для выполнения всего нескольких однотипных операций. К примеру, так появилось специальное расточное оборудование, применявшееся для изготовления стволов орудий и обработки любых других изделий цилиндрической формы и большой длины.
При попытке приспособить токарный станок к работе с заготовками малой длины и значительных диаметров была разработана конструкция лоботокарного станка. Подобным образом, под конкретную задачу, появились токарно-карусельные станки для обработки заготовок большого веса и размера, с которыми не могло работать оборудование стандартного исполнения. Для обработки крупногабаритных изделий были разработаны конструкции радиально-сверлильных и продольно-строгальных станков с длинными подвижными столами.
Наивысшим достижением станкостроительной отрасли конца XIX века стали станки токарно-револьверного типа, оборудованные головками для одномоментной установки до 16 инструментов, а также карусельно-фрезерное оборудование, позволявшее вести обработку сразу нескольких изделий крупного веса и размеров. Не менее востребованными стали все специализированные машины, предназначенные для нарезки зубьев и обработки зубчатых колес – станки зубофрезерного, зубодолбежного и зубострогального типа.
На рубеже XX века конструкторы и инженеры механики считали, что дальнейшее развитие станочного оборудования для металлообработки должно быть связано с автоматизацией, дальнейшим повышением точности и скорости выполнения операций. Огромное значение для будущего отрасли имело изобретение американскими инженерами Уайтом и Тэйлором высоколегированной «быстрорежущей» стали для изготовления резцов и других металлорежущих инструментов. Однако открывшимися в связи с этим изобретением возможностями обработки металлов на повышенных скоростях станкостроители смогли в полной мере воспользоваться уже в XX веке.
Избранные персоны промышленной революции
Основой любых прогрессивных изменений в жизни общества, будь то социальные, экономические или технологические преобразования, являются конкретные личности. Кроме потребностей общества в совершенствовании технического базиса производства, необходимым условием индустриальной революции стала созидательная деятельность множества талантливых людей – станочников, механиков, изобретателей и инженеров конструкторов.
Именно они, дополняя и совершенствуя разработки друг друга, создали в итоге станочный парк, который позволил наладить производство необходимого количества новых и более совершенных средств производства. Для примера перечислим хотя бы нескольких «действующих лиц» индустриальной революции, не забыв и о наших великих соотечественниках, также внесших свой весомый вклад в практику и теорию металлообработки:
● А.К.Нартов – выходец из народа, начавший карьеру токарем дворцовой мастерской Петра I, и закончивший свой земной путь в генеральском чине статского советника. После обучения за границей, молодой заведующий придворной «токарней» Андрей Нартов еще в 1717 году предложил конструкцию механизированного суппорта токарного станка. Впоследствии А.К.Нартов детально разработал механизмы еще 34 станков, но после его смерти рукописи попали в придворную библиотеку, и были найдены потомками только через 200 лет.
● Генри Модсли – английский механик, который увековечил свое имя созданием в 1794 году совершенной конструкции крестового механического самоходного суппорта. Он же в 1798 году при разработке токарно-винторезного станка применил сменный ходовой винт, и впервые предложил стандартизовать все резьбовые детали и соединения. Кроме того, Генри Модсли известен тем, что обучил и воспитал на собственном заводе целую плеяду учеников, каждый из которых продолжил дело учителя и внес собственный вклад в дальнейшее развитие средств металлообработки.
● Джозеф Витуорт. Этот британский инженер и предприниматель вошел в историю не только усовершенствованием конструкции поперечной передачи токарного станка. Впоследствии Д,Витуорт стал промышленником, построил собственный механический завод, а главное – еще в 1841 году предложил принципы унификации деталей машин и стандарты винтовой резьбы, которые носят его имя и применяются поныне. Он же является автором системы калибров, которую разработал и вместе с особо точными измерительными приборами ввел в практику работы своего завода, показав тем самым пример станочникам всего мира.
● И.А.Тиме – российский ученый и инженер механик, впервые изучивший и осветивший в своих трудах процессы, которые происходят при механической обработке металла. Изучая параметры образования стружки при различных скоростях подачи и резания, он смог установить важные закономерности, позволившие ему в 1870 году опубликовать рекомендации по настройке оптимальных режимов работы металлорежущих станков.
● К.А.Зворыкин – выпускник Санкт-Петербургского механического технологического института, впоследствии профессор. Константин Алексеевич Зворыкин продолжил изыскания И.А.Тиме и опубликовал труды, посвященные проблемам оптимального резания металлов, в которых привел уточненную схему усилий, воздействующих на резец. В 1883 году К.А.Зворыкин создал прибор, позволявший определить силу резания, и вывел формулу, по которой можно было рассчитать наиболее эффективные режимы работы станка.
● Фредерик Тэйлор – американский инженер, в течение 26 лет изучавший процессы резания металлов резцами различной формы, под различными углами и на всех возможных скоростных режимах. Он выявил закономерности, влияющие на качество обработки, затраты времени, толщину стружки, параметры охлаждения и стойкости резцов. В результате он практическим путем установил самые выгодные режимы металлообработки, и в 1884 году создал на основе своих исследований специальную счетную линейку рабочего – станочника, по которой можно было определить оптимальный режим резания. Работы Ф.Тейлора имели неоценимое значение для совершенствования способов металлообработки, и с благодарностью были приняты профильными специалистами всего мира.
Российское станкостроение на пороге XX века
Индустриальная революция в России, с ее преимущественно аграрным укладом экономики, запоздала почти на столетие. Однако, начавшись в середине XIX столетия, за достаточно короткий по историческим меркам период в 50 лет промышленная революция подвергла всю производственную и социально-экономическую сферу российского государства необратимой реформации. После отмены крепостного права в стране окончательно утвердился капитализм и присущие ему рыночные отношения, быстро шли процессы накопления капитала и создания промышленных предприятий. Как сто лет назад в Англии, внедрение высокопроизводительных машин началось на фабриках хлопчатобумажной промышленности.
По данным статистики, к началу 1900 года в России начитывалось 1805 предприятий машиностроения и металлообработки, оснащенных 2966 механическими двигателями. Общее количество и видовое разнообразие металлорежущих станков история, к сожалению, не сохранила. В то же время на 185 ткацких фабриках применялось более 150 тысяч механических ткацких станков, многие из которых были изготовлены на отечественных машиностроительных предприятиях. Российское станкостроение, хотя значительно отставало от уровня ведущих стран мира, развивалось поистине семимильными шагами. К концу XIX века по уровню оснащенности промышленных предприятий металлообрабатывающими станками Россия вышла на среднемировые показатели.
kospas.ru
Небольшой станок ЧПУ для DIY в работе
В предыдущей статье я написал о покупке и сборке небольшого станка с ЧПУ
Напомню, что покупал я этот станок в магазине GEARBEST по цене чуть менее $200 с доставкой
Пора проверить этот станок в действии
Подключив Ардуино к компьютера, на USB/COM порту на скорости 115200, я увидел приглашение:
В Ардуино работает последняя версия программы GRBL, позволяющая управлять принтером/гравером/фрезерным станком через G-коды.
Посылка $$ показывает текущие настройки контроллера
$$ $0=10 (step pulse, usec) $1=25 (step idle delay, msec) $2=0 (step port invert mask:00000000) $3=6 (dir port invert mask:00000110) $4=0 (step enable invert, bool) $5=0 (limit pins invert, bool) $6=0 (probe pin invert, bool) $10=3 (status report mask:00000011) $11=0.020 (junction deviation, mm) $12=0.002 (arc tolerance, mm) $13=0 (report inches, bool) $14=1 (auto start, bool) $20=0 (soft limits, bool) $21=0 (hard limits, bool) $22=0 (homing cycle, bool) $23=0 (homing dir invert mask:00000000) $24=25.000 (homing feed, mm/min) $25=500.000 (homing seek, mm/min) $26=250 (homing debounce, msec) $27=1.000 (homing pull-off, mm) $100=800.000 (x, step/mm) $101=800.000 (y, step/mm) $102=800.000 (z, step/mm) $110=800.000 (x max rate, mm/min) $111=800.000 (y max rate, mm/min) $112=800.000 (z max rate, mm/min) $120=50.000 (x accel, mm/sec^2) $121=50.000 (y accel, mm/sec^2) $122=50.000 (z accel, mm/sec^2) $130=200.000 (x max travel, mm) $131=200.000 (y max travel, mm) $132=200.000 (z max travel, mm) ok
1 2 3 4 5 6 7 8 9 10 11 12 13 14 15 16 17 18 19 20 21 22 23 24 25 26 27 28 29 30 31 32 33 34 |
$$ $0=10 (step pulse, usec) $1=25 (step idle delay, msec) $2=0 (step port invert mask:00000000) $3=6 (dir port invert mask:00000110) $4=0 (step enable invert, bool) $5=0 (limit pins invert, bool) $6=0 (probe pin invert, bool) $10=3 (status report mask:00000011) $11=0.020 (junction deviation, mm) $12=0.002 (arc tolerance, mm) $13=0 (report inches, bool) $14=1 (auto start, bool) $20=0 (soft limits, bool) $21=0 (hard limits, bool) $22=0 (homing cycle, bool) $23=0 (homing dir invert mask:00000000) $24=25.000 (homing feed, mm/min) $25=500.000 (homing seek, mm/min) $26=250 (homing debounce, msec) $27=1.000 (homing pull-off, mm) $100=800.000 (x, step/mm) $101=800.000 (y, step/mm) $102=800.000 (z, step/mm) $110=800.000 (x max rate, mm/min) $111=800.000 (y max rate, mm/min) $112=800.000 (z max rate, mm/min) $120=50.000 (x accel, mm/sec^2) $121=50.000 (y accel, mm/sec^2) $122=50.000 (z accel, mm/sec^2) $130=200.000 (x max travel, mm) $131=200.000 (y max travel, mm) $132=200.000 (z max travel, mm) ok |
К использованию мощных управляющих программ типа MATh4 я пока не готов, ставлю простейшую программку GRBL CONTROLLER
В окошке управления осями получаю работу шаговых двигателей. Правда на команду 10мм получаю реальный сдвиг на 20мм. Видимо данные настройки рассчитаны на другую шпильку
Устанавливаю шаг моторов:
$100=1600 $101=1600 $102=1600
$100=1600 $101=1600 $102=1600 |
Заодно устанавливаю ограничения перемещения по осям
$130=130 $131=110 $132=45
Вот в общем то и все. Галочка «Spindle On» приводит к срабатыванию реле и включению мотора шпинделя.
Загружаю из китайского архива первый пример и… ломаю кончик первой фрезу (((. Перемещение по оси Z с максимальной скоростью ниже уровня стола. Значит пора разбираться G-кодом и его получением. Добавляю в станок четыре аппаратные кнопки, который помогают быстро остановить/продолжить работу программы.
Программное обеспечение
3D гравировку и изучение программы ARTCAM я отложил в светлое будущее. Основное назначение данного станочка для меня — гравировка и сверловка печатных плат, нарезание отверстий в корпусах приборов и гравировка различных надписей и рисунков. Начну с того, чем я умею пользоваться — CorelDraw и SprintLayout6.
CorelDraw
Рисуем изображение в кривых и размещаем его в центре документа, а затем сохраняем его в формате файла плоттера HGLT и расширением .plt,
Для генерации G-кода нашел простейший конвертер StepCam понимающий форматы CorelDraw, SprintLayout, Autocad и даже BMP
Программа позволяет установить скорость перемещения при резке, глубину реза и некоторые другие параметры и формирует готовый G-код
После чего загружаем сгенеренный файл в GRBL CONTOLLER
Устанавливаем вручную точку начала координат по трем осям и нажимаем кнопку «ZeroPosition», а после этого — «Begin»
Если поставить перемещение по оси Z на толщину материала — получаем обрезку по контуру
А вот овал получился слегка рубленным. Забыл перевести в кривые в Corel
Возомнив себя ЧПУшником 80-го уровня решил вырезать детальку из 3мм акрила и сломал вторую фрезу — «рыбий хвост» купленный отдельно на АЛИ.
Фреза быстро перегрелась, акрил начал плавится и застывать причудливым и очень твердым комом
Интернет мне рассказал, что резка акрила производится с принудительным охлаждением фрезы, либо на очень маленькой скорости и за несколько проходов. И еще нужно учиться, учиться и еще раз учиться, осваивать и подбирать параметры процесса для каждого материала.
Впрочем 1мм пластик от коробочки CD «дался» без проблем
Изготовление печатных плат
С печатными платами оказалось все неплохо — процесс, обычная гравировка, текстолит — материал комфортный для резки
Для начала еще раз выставляю горизонталь всего чего можно
Сперва уровнем
А затем резкой тонкой бумажки на рабочем столе.
Подготовка платы — процесс не сложный. В SprintLayout делаю «Экспорт->данные фрезер HPGL .plt». Выбираю фрезеровку нужного слоя, устанавливаю требуемый отступ фрезы от дорожки
Получаю G-код все той де StepCam и получаю емкостной сенсор для системы мониторинга влажности почвы
Управляющая плата с готового проекта под ЛУТ
Проблемы
1. Станок очень капризен к USB-проводу. Короткие шнурки из комплекта мне показались неудобными, а вот из полутора метровых более менее заработал только один. При этом, если шпиндель подключен к реле, то очень часто возникает сбой программы. Может там общий минус нужно сделать или кондеров нга мотор шпинделя понавесить?
2. Заметил что при длительной работе микросхемы драйверов шаговых двигателей сильно греются. Увидел, что в интернете такие платки продаются с радиатором. Попытался вырезать радиатор из 2мм алюминия фрезой «рыбий хвост» 2мм. Не вышло. На скорости 40мм/мин китайская фреза приказала долго жить
Выпилил кусочки алюминия, наклеил на микросхемки, но, видимо, что-то закоротил. В результате теперь у меня нет одного драйвера шагового двигателя (((
Выводы
Отличный стартовый набор для вхождения в мир ЧПУ.
Для коммерции слишком медленный, маленький и маломощный.
Вполне подходит для домашнего использования: изготовления печатных плат (фрезеровка, сверловка, обрезка по контуру), фрезеровке отверстий в DIY корпусах, изготовление некрупных деталей из пластика, текстолита, фанеры, гравировка на разных материалах. Наверное, не сложная 3D гравировка
Что понравилось
- Все детали металлические.
- Все собирается «из коробки» и работает.
- Есть перспективы к некоторой модернизации
Что не понравилось
- Сэкономлено на многих деталях, радиаторах драйвера, патроне шпинделя
- Размеры маловаты. Хотелось бы иметь что-то хотя бы 200х150 на Х и Y
- Мотор шпинделя слабоват для серьезных материалов
- Тормозной контроллер
Что планирую сделать:
- Увеличить габариты по оси Х до 300мм. Для этого заказал профиль 2020, шпильку привода и направляющие с держателями на 400мм. Из того что освободится увеличить высоту для изготовления отверстий в корпусах.
- Сделать большой рабочий стол из дерева или толстого текстолита. На нем большинство заготовок отлично фиксируется при помощи двухстороннего скотча
- Заменить патрон шпинделя на нормальный ER11 с разными цангами
- Поставить ШИМ регулятор на мотор шпинделя
- Попробовать приспособить в качестве шпинделя гравер
- Купить разного инструмента
Читайте об этом в следующих обзорах
Тимофей активно помогает.
со своего сайта.
samopal.pro
Мир самоделок – Работа на токарном станке по дереву
Если вы никогда не работали на токарном станке, то попросите кого-либо из взрослых, практически знакомых с токарным делом, показать вам как стоять за станком, как держать резец и обрабатывать болванку.
Кроме того, твердо усвойте несколько простых, но очень важных правил:
1. Всегда будьте осторожны при работе.
2. Во время работы на станке не носите свободную одежду, то есть такую, которую может захватить шпиндель или болванка. Рукава (если они без манжет с пуговицами) завяжите у кистей рук. Девочки должны убирать волосы под косынку.
3. Не прикасайтесь руками к вращающимся маховику, шкиву, шпинделю и обрабатываемому предмету, а также к движущемуся приводному ремню.
Не пытайтесь затормозить руками вращающуюся деталь. Прекратите движение педали и подождите пока станок остановится сам.
4. Следите за чистотой и порядком на рабочем месте. Не кладите инструменты и другие предметы на салазки, подручник и бабки.
5. Не наклоняйтесь низко к станку, иначе можно засорить глаза.
6. Не пускайте станок в код, если возле вас самого товарищи, а тем более — маленькие дети. Попросите их отойти и не мешать работе; это нужно и для их безопасности.
Теперь мы расскажем о выборе и подготовке материалов для токарных работ.
Лучший материал для точения — древесина однородного строения, совершенно сухая, не суковатая и не слоистая. Начинающим следует брать древесину мягких пород — липу или осину Сосна и ель хотя и не очень тверды, но из-за своей слоистости менее пригодны для токарных работ. Обычно они используются для простых изделий, не требующих чистой отделки. Очень хорошо точится ольха, но шлифуется она плохо. Когда вь научитесь точить, то сможете пользоваться березой, кленом, грушей, буком; это, пожалуй самые подходящие материалы для точения.
Во многих случаях вам придется подготавливать древесину (то есть сушить ее), подобрав поленья дро соответствующих древесных пород. Для того, чтобы дерево не трескалось, разделите полено на отдельные отрезки, а торцы заклейте бумагой или закрасьте. Круглое дерево сушите, не снимая коры.
Первые ваши работы на станке — учебные. Сперва научитесь точить цилиндры.
Выберите подходящий кусок дерева и обработайте («оболваньте») его топором в виде цилиндра или шестигранной призмы. На торцах наметьте центры и по этим отметкам установите болванку так, чтобы один ее центр приходился на средний зуб вилки шпинделя, а другой — на центр задней бабки. Закрепите бабку клином и зажмите болванку центром прижимного винта (рис. 1). Снимите болванку со станка, просверлите в ее центрах отверстия глубиной 6—8 мм, смажьте центр задней бабки маслом и снова поставьте болванку на станок. Зажмите ее центром прижимного винта и закрепите этот винт стопором. Помните что крепление болванки должно быть прочным, чтобы она не могла сдвинуться с места или выскочить. Следите за правильностью установки болванки: центр вилки шпинделя, ось болванки и центр задней бабки должны составлять одну прямую линию.
Рис.1
Установите подручник так, чтобы резец во время работы плотно прижимался к нему и как можно ближе к обтачиваемой болванке, чтобы точка опоры резца лежала далее его центра.
Резец держите двумя руками. Правая рука обхватывает ручку резца, а левая — самый инструмент- Опираясь на подручник, эта рука дает резцу твердую точку опоры. Правая рука управляет инструментом, как этого требуют обточка вещи
Сначала лезвие резца должно как бы скользить по обрабатываемой поверхности; оно направляется под некоторым углом к болванке. Затем осторожно приподнимайте ручку до тех пор пока лезвие не начнет снимать стружку достаточной, но не очень большой толщины. Не стремитесь снимать слишком толстую стружку: резец будет дергаться, а болванка может выскочить, что очень опасно.
Снимайте стружку от середины к концам болванки, ставя рейер немного на правое ребро — при движении вправо и на левое — при движении влево. В ту же сторону отворачивайте ручку резца.
Когда болванка будет обточена почти до нужного размера, отложите рейер и переходите на обработку поверхности мазелем.
Обычно мазель держат на подручнике так же, как и рейер. Но при мелких работах удобнее обхватить клинок мазеля пальцами левой руки, а указательным пальцем захватить подручник и плотно прижимать инструмент к его ребру.
Рис.2
Мазель держите несколько наклонно (рис. 2) так, чтобы направление лезвия составляло угол около 45 с направлением обтачиваемого цилиндра. Тупой угол мазеля обращается в сторону движения. Держите мазель твердо и следите, чтобы он не скользил по обтачиваемой поверхности и не отталкивался от подручника.
Мы рассказали о точении цилиндров. Перейдем к более сложным операциям.
Рис.3
Если торец цилиндра нужно закруглить, делайте это мазелем, как показано на рисунке 3, ведите работу медленно и осторожно, постепенно срезая и закругляя угол.
Если же торец должен быть плоским, то срезайте его мазелем, поставленным на ребро тупым углом кверху. Резец немного углубите в дерево, потом перенесите вправо и сделайте косой подрез, направленный к первому прямому надрезу (рис. 4).
Рис.4
Чередуйте эти приемы, пока не останется цилиндрик диаметром 10—12 мм. Глужбе резать нельзя, иначе цилиндрик может сломаться и изделие соскочит с центров. Окончательно выровняйте торец, сняв последнюю, тонкую стружку. Остановите станок и приложите к плоскости торца ребро угольника. Если торец обточен ровно, то просвета не должно быть. Снимите изделие со станка и срежьте оставшийся цилиндрик острой стамеской.
Займитесь теперь тренировочными работами.
Подберите нетолстую заготовку длиной около 250 мм, поставьте на станок и обточите до диаметра 50—60 мм. Торцевать не нужно.
Не снимая цилиндр со станка, разметьте его циркулем на несколько равных частей (рис. 5а) и сделайте мазелем надрезы по размеченным линиям, придав им форму желобков (рис. 5б). Тем же инструментом сделайте выемки так, чтобы изделие приобрело форму, показанную на рисунке 5в. Отметьте карандашом середину каждой части и точите тупым углом лезвия мазеля книзу так, чтобы получился профиль, изображенный на рисунке 5г. Затем, попеременно пользуясь мазелем в высоких местах и рейером в углублениях, придайте изделию волнообразную форму (рис. 5д), На другом таком же цилиндре проделайте ряд новых работ. Также разделите его на равные части, н» сделайте прямые выточки (рис. 5е), торцуя их стороны и выбирая середину узким мазелем или грабштихелем. Теперь попробуйте закруглить выступающие части (рис. 5ж).
На последующих рисунках (5з—5н) изображены образцы различных точеных фигур для тренировочных работ.
Внутреннее точение изделий значительно сложнее. В этом случае вилку шпинделя надо снять, а вместо нее поставить патрон или планшайбу в зависимости от величины изделия и характера его обработки.
Рис.6
В патроне заготовку зажимают (рис. 6), а к планшайбе привинчивают шурупами (рис. 7). Нередко делают иначе: привинчивают к планшайбе деревянный диск, а уже к нему прикрепляют (привинчивают или приклеивают) обрабатываемый предмет. При этом нужно следить, чтобы шурупы не попали под резец.
Заготовку, закрепленную в патроне, при наружном точении прижимают центром задней бабки. Затем бабку отодвигают в сторону, чтобы она не мешала, и выбирают нужное углубление рейером. Подача инструмента должна быть очень небольшом. Забирайте стружку концом лезвия, направляя его от края торца к центру. Для этого ручку инструмента постепенно приподнимайте кверху и так же постепенно отзодите вправо. При этом смотрите, чтобы железка рейера не терлась о края выемки.
Рис.7
Примерно так же точат внутреннюю часть изделия, закрепленного на планшайбе.
При внутреннем точении подручник ставьте косо к оси центров станка или даже перпендикулярно: так легче работать.
Внутреннюю поверхность, вчерне обработанную рейером, сгладьте грабштихелем с закругленным концом (если выемка овальная или круглая) или прямым (если стенки выемки прямые).
Готовое изделие, зажатое в патрон, торцуют, но со стороны передней бабки. Следовательно, заготовка должна иметь некоторый запас по длине, достаточный для того, чтобы можно было свободно делать косые подрезы.
mir-samodelok.ru
|
|
funer.ru