Структура стали – Структура сталей :: Книги по металлургии
alexxlab | 03.03.2020 | 0 | Разное
закаленная, углеродистая, эвтектоидная, легированная, влияние на свойства
Сталь – это многокомпонентный сплав, который состоит из железа и углерода. Под разным давлением и температурой свойства и тип кристаллической ячейки этих двух компонентов может меняться. Структура сталей – это характеристики ее свойств. Под структурой подразумеваются: строение, форма и характер расположение фаз, которые образуют зерна. Для того чтобы просмотреть эти зерна, необходимо изучить излом.
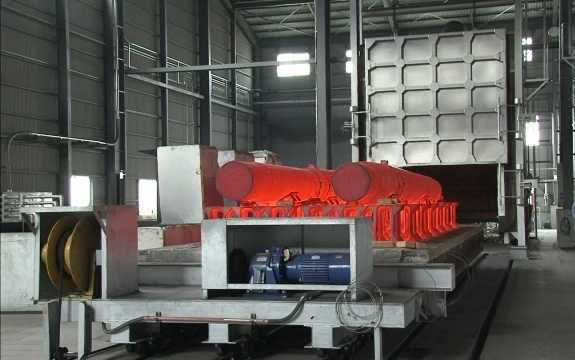
Сплавы из стали подлежат обязательной термической обработке, во время которой значительно повышаются показатели прочности.
Исследование фаз проводится под микроскопом. Все зерна могут иметь разную форму и размер. Это все зависит от метода получения металла и от механической обработки. К примеру, в кованом металле зерна имеют небольшой размер, в свою очередь литой металл характеризуется большими размерами зерна.
Структуру сталей очень важно изучать, поскольку это дает возможность улучшить свойства материала, тем самым сделать готовые изделия максимально надежными и повысить их эксплуатационные свойства.
В большей степени структура сталей зависит от того, какие химические реакции происходят между ее компонентами. Различаю такие фазы, как:
- жидкий раствор;
- твердый раствор;
- химическое соединение.
Читайте также:
Какие бывают дефекты сварных швов.
В чем особенности газовой сварки.
Как варить полуавтоматом читайте здесь.
Классификация структуры стали
Схема классификации сталей по химическому составу.
Основные марки сталей:
- Техническое железо применяется при создании сердечников трансформаторов. Такой сплав содержит от 0,006 до 0,02 % углерода.
- Доэвтектоидная сталь содержит от 0,02 до 0,8 % углерода. Из такого материала изготавливают различные детали машин и других конструкций.
- 0,8% углерода в составе характеризует эвтектоидную сталь, которая сегодня используется для изготовления мерительных и режущих инструментов.
- Заэвтектоидная содержит в своем составе углерод в пределах от 0,8 до 2,14 %. Этот материал также используется для производства режущих и измерительных инструментов.
- Доэвтектический белый чугун характеризуется достаточно большим процентом углерода от 2,14 до 4,3. С такого материала изготавливаются детали с высокой износоустойчивостью.
Самое большое содержание углерода от 4,3 до 6,67 % находится в заэвтектическом белом чугуне.
Влияние углерода на свойства и структуру стали
Таблица содержания углерода в различных марках стали.
Железо в чистом виде – это очень пластичный и непрочный материал, который не используется для изготовления технических конструкций и деталей. Для этой цели самым подходящим вариантом является сталь. Ее основные свойства будут зависеть от того, какое количество углерода входит в ее состав. Стоит понимать, что углерод – это не металл, в природе его можно встретить в трех видах:
- каменный уголь;
- графит;
- алмаз.
В стали углерод вноситься в связанном состоянии в виде цементита. Чем больше цементита входит в состав стали, тем она становиться прочнее и тверже, при этом пластичность материала снижается. Механические свойства также будут обусловлены формой и размером структурных частиц. Чем меньше размеры и тоньше пластины феррита и цементита, тем более высокими будут прочность и твердость стали.
Чем больше в составе содержится углерода, тем хуже становится пластичность и способность к деформации, особенно в холодном состоянии.
Основным достоинством высокоуглеродистых сталей является их износостойкость и твердость, именно поэтому они относятся к группе инструментальных.
Термическая обработка: особенности
Для того чтобы изменить прочность и твердость стали, необходимо провести термообработку.
Таблица деформации стали до, во время и после термической обработки.
Такая обработка заключается в поочередной смене разных температур – нагревании и охлаждении. В зависимости от того, какая температура используется для нагрева и как быстро охлаждается сталь, различают несколько видов термообработки.
Отжиг – термическая обработка, во время которой материал нагревается до температуры, которая превышает фазовые изменения. После такого нагрева следует постепенное охлаждение, чаще всего вместе с печью. Благодаря такой обработке можно изменить неправильные структуры стали, улучшить механические показатели после таких процессов, как сварка, ковка, литье.
Закалка – процесс, при котором температура нагревания достигает аутентичного состояния, но в отличие от предыдущего процесса остывание происходит быстро. За счет этого сталь приобретает максимальные показатели прочности.
Отпуск – это термическая обработка, при которой сталь нагревается не доходя до аустенитного состояния и очень медленно охлаждается.
Старение – процесс распада твердых растворов, которых в составе стали большое количество.
Для того чтобы получить качественный результат, стоит правильно подобрать температуру нагрева, необходимое время выдержки, скорость охлаждения.
Схемы микроструктур углеродистой стали в зависимости от содержания углерода.
Температура закалки может быть двух видов: полная закалка и неполная. Полная закалка – это температура, при которой достигается аустенитное состояние, неполная – температура подымается до достижения аустеннито-цементитного состояния.
Выдерживать изделия в печи крайне необходимо. Именно на этом этапе происходит прогревание всего изделия по всему объему. Это способствует завершению фазовых превращений, выравниванию температуры и растворению карбидов. Время для выдержки зависит от размера изделия, температуры нагрева и химического состава.
Скорость охлаждения будет зависеть от марки стали и среды охлаждения. Самый быстрый способ остудить изделие – окунуть его в воду, менее быстрый – использовать вместо воды масла; и самый медленный метод – охладить изделия и оставить на открытом воздухе.
Увеличение износостойкости промышленных деталей
Машинные детали должны обладать высокими показателями износостойкости, поскольку детали длительное время трутся друг о друга. Для того чтобы повысить износостойкость таких поверхностей, используют химико-термическую обработку – поверхностное легирование. Вследствие такого процесса меняется микроструктура от поверхности к сердцевине.
Во время этого процесса поверхность насыщается такими материалами, как углерод, азот, бром, кремень, алюминий или хром. После такой обработки поверхность будет отличаться от состава всего изделия.
moyasvarka.ru
Структурные составляющие в сталях
Феррит – мягкая, малопрочная, пластичная
структурная составляющая стали. Твердость
НВ = 700÷800
МПа, предел прочности
Цементит (карбид железа)– химическое соединение, отвечающее формуле Fe3С, содержит углерода 6,67%. Цементит обладает высокой твердостью НВ=8000 МПа, он хрупкий, имеет пластичность, практически равную нулю.Увеличение количества цементита в сталях приводит к повышению твердости и снижению пластичности.Во всех сталях присутствует цементит, входящий в состав перлита. Структурно свободный цементит (вторичный) содержится в заэвтектоидных сталях. Избыточный вторичный цементит не только повышает твердость сталей, но и охрупчивает их (см. рис. 2.1).
Перлит– эвтектоидная фазовая смесь феррита и цементита с концентрацией углерода 0,8%. Свое название он получил по перламутровому оттенку шлифа после травления. В зависимости от формы цементита перлит бывает зернистым и пластинчатым. Пластинчатый перлит образуется при медленном охлаждении аустенита, зернистый получают отжигом. Их свойства различаются. Пластинчатый перлитимеет предел прочности при растяжении около 800 МПа, твердость НВ = 2000 МПа, относительное удлинение 15%. Чем выше скорость охлаждения, тем мельче пластиночки перлита, тем выше твердость и прочность, ниже пластичность.Зернистый перлитменее прочен и тверд, чем пластинчатый, но более пластичен и вязок (НВ = 1870 МПа). Пластинчатый перлит затрудняет обрабатываемость резанием. Поэтому металлургические заводы, согласно ГОСТу, обязаны выпускать инструментальные стали со структурой зернистого перлита.
Влияние углерода на свойства стали
Р
12
ешающая роль в составе стали отводится углероду. Углерод повышает прочность сталей, но снижает их пластичность и вязкость, повышает порог хладноломкости (t50), увеличивая чувствительность к хрупкому разрушению (рис. 2.1).Изменение механических свойств объясняется наличием различных структурных составляющих.
В соответствии с диаграммой состояния
«Fе–Fe
доэвтектоидные(с содержанием углерода менее 0,8%),
эвтектоидные(0,8% С),
заэвтектоидные(более 0,8% С).
Структура доэвтектоидных сталейсостоит из феррита и перлита. Чем больше содержание углерода, тем меньше феррита и больше перлита, следовательно, выше твердость и прочность, ниже пластичность и вязкость.
Структура
эвтектоидной сталисостоит только
из перлита. Эта сталь имеет высокую
твердость и износостойкость, поэтому
применяется в качестве инструментальной.
Высокую твердость сталь приобретает
при закалке с низким отпуском.
Структура заэвтектоидной стали состоит из перлита и вторичного цементита. Максимальное содержание углерода в углеродистых инструментальных сталях 1,3%. При медленном охлаждении из однофазного аустенитного состояния перлит получается пластинчатым, а вторичный цементит выделяется в виде сетки по границам зерен перлита. Цементитная сетка не допускается ГОСТом, она резко снижает ударную вязкость, упругость и прочность сталей. Цементитная сетка дробится при обработке давлением и при нормализации. Форма включений вторичного цементита в инструментальных сталях – сферическая.
studfiles.net
Структуры сталей при различных температурах
Стали, как указывалось выше, являются сплавами железа с углеродом.
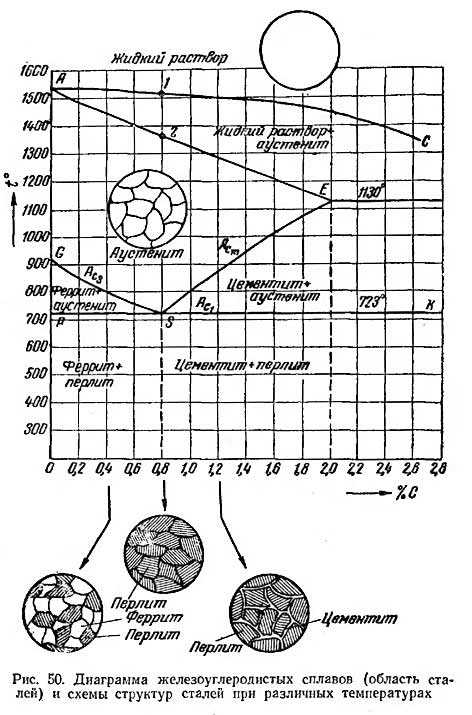
Структуры углеродистых сталей в зависимости от содержания в них углерода, а также структурные превращения, которые происходят в этих сталях при нагреве и медленном охлаждении, изучаются по диаграмме Fe—С.
На рисунке приведена часть диаграммы Fe—С, характеризующая структуры сталей
Прежде чем рассматривать структурные превращения в сталях, выясним, какие структуры в них встречаются при комнатных температурах и при нагреве.
Линии диаграммы определяют температуры, при которых в сталях происходят какие-либо структурные, превращения.
Феррит
Феррит — твердый раствор углерода в железе а. При комнатной температуре в феррите может растворяться не более чем 0,006% углерода.
Если содержание углерода встали больше чем 0,006%, то, кроме феррита, в структуре стали имеются другие структурные составляющие.
Феррит обладает небольшой прочностью и твердостью, но высокой пластичностью. Он имеет хорошие магнитные свойства.
Цементит
Цементит — химическое соединение железа с углеродом, отвечающее формуле Fe3C. Содержание углерода в цементите составляет 6,67% и не изменяется во всем интервале температур, вплоть до температуры плавления.
Цементит является самой твердой структурной составляющей стали. Он имеет высокую прочность, но чрезвычайно хрупок.
Перлит
Перлит — механическая смесь феррита и цементита (после травления эта структура имеет перламутровый отлив).
Перлит бывает пластинчатым (цементит в виде пластинок) и зернистым (цементит в виде зернышек). Твердость перлита выше, чем у феррита, но меньше, чем у цементита.
Аустенит
Аустенит (название дано в честь английского металловеда Аустена) — твердый раствор углерода в железе γ (модификация железа с гранецентрированной кристаллической решеткой). Максимальная растворимость углерода в железе γ составляет 2% при температуре 1130°.
Аустенит имеет невысокую твердость, обладает достаточно высокой прочностью наряду с хорошей пластичностью, большой стойкостью против коррозии, высоким электросопротивлением. Он немагнитен.
Диаграмма железоуглеродистых сплавов
Вернемся к вышеприведенной диаграмме, так линия АС показывает, при каких температурах при охлаждении начнется процесс кристаллизации в стали. Линия АЕ показывает, при каких температурах кристаллизация закончится, т.е. сплав затвердеет.
Из диаграммы видно, что чистое железо кристаллизуется при постоянной температуре (1539°).
Сталь с содержанием С=0,8% кристаллизуется не при постоянной температуре, а в некотором интервале температур. Точка 1 определяет температуру начала кристаллизации, точка2 — температуру конца кристаллизации стали с содержанием С = 0,8%.
Таким образом, при температурах ниже линии АЕ сталь будет находиться в твердом состоянии и структура стали будет аустенит. При этом весь углерод, который в стали имеется, будет растворен в аустените.
Структура аустенита сохранится в стали и при последующем охлаждении до температур, определяемых линиямиGS иSE.
§
www.conatem.ru
6.5 Формирование структуры сталей
Кристаллизация сталей (сплавы 2 – 6) может проходить в один (сплавы 5, 6), два (сплав 3) либо три (сплавы 2, 4) этапа. Кристаллизация сплавов 2 – 4 начинается с образования кристаллов -феррита. Состав этих кристаллов во время охлаждения изменяется в соответствии с наклоном линии АН, а состав жидкости – в соответствии с наклоном линии АВ. При температуре линии НJB во всех случаях жидкость принимает концентрацию точки В, а кристаллы – точки Н.
В условиях небольшого переохлаждения относительно линии НJB начинается перитектическая кристаллизация, в результате которой за счет взаимодействия кристаллов -феррита и жидкости образовываются кристаллы аустенита. Перитектическая кристаллизация протекает при постоянной температуре. В зависимости от состава стали перитектическая кристаллизация может завершиться полным исчезновением фаз, которые существовали раньше (сплав 3), либо сохраняется избыток -феррита (сплав 2 ) или жидкости (сплав 4). В последнем случая имеет место третий этап кристаллизации, во время которого в температурном интервале между линиями НJB и JE кристаллизуется аустенит.
В сплавах 5, 6 кристаллизация происходит в температурном интервале между линиями ВC и JE. Образовываются кристаллы аустенита. Во время кристаллизации химический состав кристаллов и жидкости изменяется в соответствии с наклоном линий JE и ВC. Кристаллы аустенита растут в форме дендритов. В связи с повышенной подвижностью атомов углерода, дендритная ликвация почти не выражена.
Дальнейшее формирование структуры зависит от состава стали. В эвтектоидной стали (сплав 5) аустенит остается стабильным при охлаждении до точки S. При некотором переохлаждении относительно этой точки при постоянной температуре происходит эвтектоидное превращение, в результате которого формируется структура эвтектоида, состоящего обычно, из чередующихся пластин феррита и цементита. Такой эвтектоид называется перлитом. Таким образом, после полного охлаждения структура эвтектоидной стали представляет собой перлит.
Во время охлаждения доэвтектоидной стали аустенит теряет свою стабильность ниже линии GS. Начинается полиморфное превращение аустенита в феррит, которое имеет место в температурном интервале между точками 16 и 17 (сплав 3). Кристаллы феррита образовываются преимущественно на границах зерен аустенита и растут обычно в форме равноосных зерен. В некоторых случаях возможно образование ферритной сетки на границах аустенитных зерен. Превращение сопровождается изменением химического состава аустенита в соответствии с линией GS. Важно подчеркнуть, что при эвтектоидной температуре аустенит всегда имеет эвтектоидное содержание углерода. При некотором переохлаждении будет иметь место эвтектоидное превращение. В результате описанных процессов структура доэвтектоидной стали будет состоять из феррита и перлита.
Путем рассуждений можно определить количественное соотношение между ферритом и перлитом в структуре доэвтектоидной стали. Для этого cледует иметь в виду, что перлит образуется из аустенита, который сохраняется до эвтектоидной температуры. Относительное количество аустенита и феррита при эвтектоидной температуре легко определить по правилу отрезков. С помощью аналогичных рассуждений можно решить обратную задачу – определить ориентировочно содержание углерода в стали в зависимости от соотношения в структуре феррита и перлита. Надо, однако, иметь в виду, что такой метод годен только тогда, когда наверняка известно, что охлаждение стали было медленным.
В заэвтектоидной стали (сплав 6) ниже линии ЕS аустенит становится перенасыщенным углеродом. Избыточный углерод выделяется из аустенита в виде вторичного цементита, который располагается на границах аустенитных зерен. Во время охлаждения в интервале температур между точками 22, 23 аустенит обедняется углеродом в соответствии с линией ЕS. Как и в предыдущем случае, при эвтектоидной температуре аустенит имеет эвтектоидную концентрацию и при дальнейшем охлаждении при постоянной температуре превратится в перлит. Таким образом, структура заэвтектоидной стали будет состоять из перлита и вторичного цементита.
Превращения при нагреве cталей происходят в обратном порядке. Полагаем, что студент схематично может произвести такой анализ самостоятельно. Более детальный обзор этих вопросов будет представлен в курсе ” Термическая обработка “.
studfiles.net
Структура углеродистых сталей
Сталями называется сплавы железа с углеродом, содержащие от 0,02 % до 2,14 % углерода. При содержании углерода до 0,006 % сплавы однофазные и имеют структуру феррита, например, электролитическое железо.
Сплавы, содержащие от 0,006 % до 0,02 % углерода называются техническим железом (рисунок 4.7).
Увеличение содержания углерода вследствие его незначительной растворимости в феррите вызывает появление второй фазы – цементита третичного. При содержании углерода до 0,025 % структурно свободный цементит выделяется, главным образом, по границам зерен феррита. Это существенно понижает пластичность и вязкость стали, особенно, если цементит распола-
гается цепочками или образует сетку вокруг зерен феррита.
При увеличении содержания углерода выше 0,025 % в структуре стали образуется перлит; одновременно еще до 0,10 – 0,15 % С в стали появляются включения структурно свободного (третичного) цементита. С дальнейшим повышением содержания углерода третичный цементит входит в состав перлита.
За превращениями, протекающими в сталях в процессе их нагрева и охлаждения, можно проследить, пользуясь левой частью диаграммы состояния (рисунок 4.6).
По микроструктуре стали делятся на доэвтектоидные, эвтектоидные и заэвтектоидные (рисунки 4.8, 4.9, 4.10). Стали с содержанием углерода от 0,02 до 0,8 % называют доэвтектоидными; с содержанием 0,8 % углерода – эвтектоидными; с содержанием от 0,8 % до 2,14 % – заэвтектоидными.
Как следует из диаграммы Fe-Fe3C, при комнатной температуре в равновесном состоянии микроструктура доэвтектоидной стали состоит из феррита и перлита (рисунок 4.8). Количественное соотношение между структурными составляющими (Ф и П) в доэвтектоидных сталях определяется содержанием углерода. Чем ближе содержание углерода к эвтектоидной концентрации, тем больше в структуре перлита.
Микроструктура эвтектоидной стали (0,8 % С) состоит только из перлита (рисунок 4.9). Образуется из аустенита при охлаждении стали У8 (линия PSK). Строение перлита вследствие его значительной дисперсности (мелкозернистости) может быть детально различимо только при сравнительно больших увеличениях (×600).
Микроструктура заэвтектоидной стали (рисунок 4.10) состоит из перлита и вторичного цементита. Образуется у стали У9-У13 из аустенита при охлаждении. Сетка цементита начинает образовываться на линии ES, перлит – на линии PSK. Максимальное количество структурно свободного цементита (~ 20 %) будет в сплаве с содержанием углерода 2,14 %.
также светлую окраску, необходимо шлиф, протравленный 4 %-ным раство-
ром азотной кислоты, заново перешлифовать, переполировать и заново про-
травить раствором пикрата натрия, который окрашивает цементит в темный
цвет.
По микроструктуре доэвтектоидной стали можно приблизительно определить содержание в ней углерода, для чего нужно ориентировочно определить площадь (в процентах), занимаемую перлитом, в связи с тем, что в феррите растворено очень небольшое количество углерода, практически можно считать, что в доэвтектоидной стали весь углерод находится в перлите.
С =100⋅ 0,8 П S ,
где С – концентрация углерода в сплаве, в процентах;
П S – видимая часть площади микроструктуры, занимаемая перлитом
в процентах.
По количественному соотношению перлита и феррита, согласно ГОСТ 8233-56 Сталь. Эталоны микроструктуры, ферритно-перлитные структуры классифицируются по десятибальной шкале (таблица 4.1). Оценка производится визуально при 100-кратном увеличении по средней площади, занимаемой перлитом на микрошлифе.
Зависимость механических свойств углеродистых сталей от
Содержания углерода
Изменение содержания углерода вызывает изменения в структуре стали, что, в свою очередь, оказывает определяющее влияние на свойства стали.
В соответствии с диаграммой состояния структура стали в равновесном состоянии представляет собой смесь феррита и цементита, причем количество цементита увеличивается пропорционально содержанию углерода. Феррит малопрочен и пластичен, цементит твёрд и хрупок. Поэтому увеличение цементита приводит к повышению твердости, прочности и снижению пластичности.
оказывает вторичный цементит, образующий хрупкий каркас вокруг зерен
перлита. Под нагрузкой этот каркас преждевременно разрушается, вызывая
снижение прочности, пластичности. Из-за этого заэвтектоидные стали при-
меняют после специального отжига со структурой зернистого перлита, отли-
чающегося от пластинчатого перлита меньшей твердостью и большей пла-
стичностью.
Углерод изменяет технологические свойства стали: обрабатываемость резанием, давлением, свариваемость. Увеличение содержания углерода ведет к снижению обрабатываемости резанием. Лучшей обрабатываемостью резанием обладают стали с содержанием 0,3 – 0,4 % С.
С увеличением содержания углерода снижается технологическая пластичность – способность деформироваться в горячем и, особенно, в холодном состоянии. Для сложной холодной штамповки содержание углерода ограничивается 0,1 %.
Углерод затрудняет свариваемость сталей. Хорошей свариваемостью обладают низкоуглеродистые стали. Для иллюстрации на рисунке 4.11 приведен график зависимости механических свойств стали от содержания углерода.
Классификация и маркировка углеродистых сталей
Углеродистые стали подразделяют на низкоуглеродистые до 0,25 % C, среднеуглеродистые (0,3 – 0,6 % C), высокоуглеродистые (более 0,6 % С). По применению углеродистые стали подразделяются на конструкционные и инструментальные. Конструкционные стали классифицируют на стали обык-
новенного качества и качественные.
Конструкционная углеродистая сталь обыкновенного качества обозначается буквами Ст, после которых стоит цифра от 0 до 6, обозначающая но-
мер марки стали (с увеличением номера возрастает содержание углерода),
например: Ст1, Ст2, …, Ст6. Чем больше номер, тем выше прочность и твер-
дость, но ниже пластичность (таблица 4.2). Наиболее пластичные и наименее
твердые – Ст0, Ст1, Ст2 – идут на изготовление кровельных листов, крепеж-
ных изделий; наиболее твердая и прочная сталь этой группы – Ст6 применя-
ется, например, в производстве рельсов, рессор. Стали обыкновенного каче-
ства выпускают в виде проката (прутки, балки, листы, уголки, швеллеры и
т.п.).
Углеродистые качественные стали характеризуются более низким, чем у сталей обыкновенного качества содержанием вредных примесей и неме-
таллических включений.
Качественную сталь маркируют двузначным числом, обозначающим среднее содержание углерода в сотых долях процента. Низкоуглеродистую сталь марок 08, 10, 15, 20, 25 применяют для изготовления метизов и деталей, от которых не требуется высокой прочности. Среднеуглеродистые стали 30, 35, …, 55 отличаются большей прочностью, меньшей пластичностью, чем низкоуглеродистые. Высокоуглеродистые стали марок 60, 65, …, 85 имеют большую твердость и прочность и применяются для изготовления ответст-
венных деталей машин.
Качественные инструментальные стали маркируют буквой У и цифрой, указывающей на содержание углерода в десятых долях процента: У7, У8 и т.д. Высококачественные инструментальные стали маркируют так же, как и
качественные, но в конце марки ставят букву А: У7А, У8А – У12А.
Порядок выполнения работы
4.8.1 Изучите по диаграмме состояния Fe – Fe3C превращения, проис-
ходящие в железоуглеродистых сплавах при охлаждении.
4.8.2 Ознакомьтесь со структурными составляющими железоуглероди-
стых сплавов. Найдите на диаграмме состояния области существования этих
структур.
4.8.3 Получите у лаборанта микрошлифы образцов различных сталей. С помощью металлографического микроскопа изучите структурные
составляющие железоуглеродистых сплавов. Определите вид сплава: сталь
(доэвтектоидная, эвтектоидная, заэвтектоидная).
4.8.4 Зарисуйте все просмотренные структуры с указанием фазовых и
структурных составляющих. Микроструктуры зарисовать в квадратах разме-
ром 50 × 50 мм. Основное при зарисовке микроструктуры – уловить харак-
терные особенности микроструктуры и передать их на рисунке. Нет надобно-
сти передавать на рисунке фотографически точное изображение. Фазы и
структурные составляющие указывать стрелками, на полях писать их наиме-
нование.
Содержание отчета
4.9.1 Цель работы.
4.9.2 Краткое описание структурных составляющих железоуглероди-
стых сплавов.
4.9.3 Рисунок диаграммы состояния Fe – Fe3C.
4.9.4 Схемы и описание микроструктуры сталей и чугунов.
4.9.5 Выводы по работе. В выводах указывается влияние содержания
углерода на структуру и механические свойства; влияние формы графитовых
включений и структуры металлической основы на свойства чугунов.
4.10 Контрольные вопросы
4.10.1 Какие железоуглеродистые сплавы относятся к техническому
железу, сталям и чугунам?
4.10.2 Каковы фазовые и структурные составляющие системы Fe-C?
Характеристика структурных составляющих.
4.10.3 Какая из структур железоуглеродистых сплавов является меха-
нической смесью феррита и цементита?
4.10.4 Что такое ледебурит?
4.10.5 Как классифицируют по структуре стали и чугуны?
Приложение А
(справочное)
Приобретение навыков работы с диаграммой состояния железо-углерод
Исходные данные:
Сплав содержит 0,7 % углерода. Заданная температура 600 °С.
Номера темпе- ратурных интервалов | Температурные границы интер- валов, °С | Концентрация углерода в фазовых состояниях, % | Струк- тур- ный состав | Вариантность системы | |||
верхние границы | нижние границы | наименование фазы | на верх- ней гра- нице тем- пера- турного интервала | на ниж- ней гра- нице тем- пера- турного интервала | |||
Ж А | 0,7 0,2 | 2,25 0,7 | Ж+А | ||||
А | 0,7 | 0,7 | А | ||||
А Ф | 0,7 0,016 | 0,8 0,02 | А+Ф | ||||
Ф А Fe3С | 0,8 0,02 6,67 | 0,8 0,02 6,67 | А+Ф+ П | ||||
Ф Fe3С | 0,02 6,67 | 0,01 6,67 | Ф+П | ||||
Ж – жидкость, А – аустенит, Ф – феррит, П – перлит, Fe3С – цементит |
Лабораторная работа № 5
Упражнения по диаграмме железо-углерод *)
Цель работы
Приобретение навыков работы с диаграммами состояния на примере
диаграммы железо-углерод.
Общие сведения
Диаграммы состояния представляют собой графическое изображение состояния сплавов. Свойства сплавов определяются, прежде всего, составом фаз и их количественным соотношением. Сведения о составе и соотношении фазовых составляющих можно получить, анализируя диаграмму состояния. Зная диаграмму состояния, можно представить полную картину кри-
сталлизации любого сплава, формирования его структуры. Диаграмма со-
стояния позволяет оценить свойства сплавов, найти оптимальные параметры
таких технологических процессов как литье, термическая и химико-
термическая обработка, сделать заключение о возможности обработки давле-
нием и т.д.
Порядок выполнения работы
5.3.1 Получите у преподавателя задание на выполнение работы (на пер-
вом этапе – концентрацию углерода в сплаве, на втором – температуру спла-
ва).
5.3.2 Опишите процесс кристаллизации сплава заданного состава (этап
первый). В процессе работы заполните таблицу 5.1.
Таблица 5.1 – Фазовый и структурный состав сплава в температурных
интервалах
Номера темпе- ратурных интервалов | Температурные границы интер- валов, °С | Концентрация углерода в фазовых состояниях, % | Струк- тур- ный состав | Вариантность системы | |||
верхние границы | нижние границы | наименование фазы | на верх- ней гра- нице тем- пера- турного интервала | на ниж- ней гра- нице тем- пера- турного интервала | |||
Не нашли то, что искали? Воспользуйтесь поиском гугл на сайте:
zdamsam.ru
Структура – сталь – Большая Энциклопедия Нефти и Газа, статья, страница 1
Структура – сталь
Cтраница 1
Структура сталей У7, У8, У9А в закаленном состоянии состоит из одного мартенсита. [2]
Структура стали с 0 7 % С показана на фиг. Здесь феррит, хотя и располагается белой сеткой ( как избыточный цементит), но сетка эта более широкая и неравномерная, по характеру отличающаяся от цементитной. [3]
Структура стали после коррозионно-усталостных испытаний более дефектонасышена. [4]
Структура стали зависит от содержания в ней углерода. В состав структуры стали входят феррит, цементит, перлит. [6]
Структура сталей, подвергавшихся диффузионному хромированию при указанных условиях, показана на фиг. [7]
Структура стали с содержанием 0 83 % С состоит из одних только зерен перлита. Эту сталь называют эвтектоидной. [8]
Структура сталей с содержанием больше 0 83 % С состоит из зерен перлита и цементита. [9]
Структура стали после неполной закалки состоит из феррита и мартенсита. Твердость стали при этом по сравнению с нормально закаленной сталью пониженная, так как феррит – мягкая структурная составляющая. [10]
Структура стали при зтом состоит из аустенита и феррита. При дальнейшем повышении температуры феррит также превращается в аустенит. Чем больше в стали углерода, тем быстрее ( при более низких температурах) она принимает структуру аустенита. [12]
Структура стали и чугуна изменяется в зависимости от скорости охлаждения. [14]
Структура стали после закалки – мартенсит и остаточный аусте-нит, а структура сталей с 0 6 % С содержит еще и избыточные карбиды. Стали, содержащие вольфрам и кремний, чувствительны к обезуглероживанию, что требует защиты при нагреве под закалку. Как указывалось, для этих сталей целесообразно проводить изотермическую закалку с выдержкой выше температуры М для получения основной бейнитной структуры. Изотермическую закалку проводят для улучшения вязкости, пластичности и уменьшения деформации. После отпуска, который чаще всего выполняют на твердость HRC 50 – 52, получается трооститная структура. [15]
Страницы: 1 2 3 4 5
www.ngpedia.ru
2.2 Структура отожженной стали.
Из диаграммы состояния видно, что техническое железо может быть однофазным (Ф) или двухфазным (Ф+Ц3). Округлые зерна феррита при протравлении шлифа 4-6- процентным раствором азотной кислоты в спирте имеют цвет светлой солому. Светло-голубой Ц3 располагается в виде тонких включений по границам зерен феррита. Феррит мягок и пластичен (). Цементит тверд (800 HB) и хрупок, разрушение при растяжении происходит практически без удлинения образца.
В структуре сталей по мере увеличения содержание углерода возрастает массовая доля цементита и соответственно уменьшается доля феррита. Это приводит к повышению твердости прочности стали, к снижению е пластичности, изменению физических и технологических свойств. Таким образом, структура сталей зависит от содержания углерода.
Доэвтектоидные стали содержат С<0.8% и состоит из феррита (светлые зерна) и перлита (темные зерна). Пропорционально увеличению в них содержания углерода растет доля перлита (см. рис.).
Общее количество углерода в стали равно: C = Cферрита + Cперлита = Cперлита
В последнем, находится практически весь углерод стали, т.к. в феррите при комнатной температуре углерода крайне мало (10-7%). Если допустить, что значения плотности феррита и цементита соизмеримы, то по структуре стали, находящейся в равновесном состоянии, можно определить содержание в ней углерода. Для этого при любом рекомендуемое увеличение микроскопа определяется площадь поверхности шлифа стали, занятой перлитом.
Рис.4. Структура доэвтектоидных сталей с различным содержанием углерода (Са<Сб<Св).
Например, если в стали содержится 50% перлита, то количество углерода в ней:
С = 0,40%,
Где 0,8 – процентное содержание углерода в перлите.
По ГОСТ 1050-88 сталь, содержащая 0,40% С, является качественной конструкционной марки 40.
Эвтектоидной называется сталь, содержащая 0,8 % С, структура которой состоит только из перлита. Перлит (перламутр) является двухфазной структурной составляющей, представляющей собой смесь феррита и цементита пластинчатого (см. рис.) или зернистого (см. рис.) строения. Пластинчатый перлит состоит из чередующихся пластинок феррита и цементита. Они образуются при температуре 727 0С, (точка S см. рис.) на границах зерен исходной высокотемпературной фазы (аустенита) и растут одновременно по направлению от границ к центру аустенитного зерна. В результате аустенитное зерно разделяется на несколько частей с определенной, но различной относительно друг друга, ориентировкой взаимно параллельных пластинок феррита и цементита. Каждая такая часть представляет собой перлитное зерно. Следовательно, в одном аустенитном зерне при эвтектоидном превращении формируются несколько зерен перлита. Перлит состоит из двух фаз феррита и цементита, обладающих различной твердостью, полируемостью и травимостью в реактивах. При полировке и травлении шлифа на его поверхности создается рельефность. Твердые малотравящиеся пластины цементита выступают над ферритными и остаются светлыми и блестящими. Утопающий между ними мягкий феррит оказывается затененным и кроме того из-за повышенной травимости, тусклым и темным. Поскольку в перлите содержится сравнительно мало (около 9%) цементита, перлит в сталях (и в белых чугунах) при микроскопическом исследовании выглядит темным, но не черным, как различного рода пустоты.
Перлит зернистый всегда светлый, цементит в нем имеет округлую форму. Зернышки (сфероиды) цементита расположены в ферритной матрице. Структура перлита зернистого после специальной термической обработки могут иметь не только эвтектоидная, но и до- и заэвтектоидные стали. Поэтому определять содержание углерода в стали по структуре зернистого перлита не рекомендуется. Зернистый перлит имеет меньшую твердость (160-220 НВ), чем пластинчатый (200-250 НВ), лучше обрабатывается резанием.
Заэвтектоидные стали содержат от 0,8 до 2,14% С и имеют структуру П+Ц2. Темные перлитные участки окружены более или менее сплошной светлой сеткой цементита вторичного (см. рис.), толщина которой увеличивается с повышением содержания углерода в стали. Отличительными особенностями сетки цементита вторичного от сетки феррита избыточного в доэвтектоидных сталях с повышенным содержанием углерода являются разобщенность зерен феррита и их стремление к округлению.
а) б)
Рис.5. Структура заэвтектоидной стали:
а) травление 4% раствором HNO3; б) травление пикратом натрия.
Таким образом, феррит и цементит встали при обычном травлении (4% раствором HNO3 в спирте) видны в виде светлых составляющих. Для установления фазового состава светлой сетки вокруг перлитных участков шлиф переполировывают и травят раствором пикрата натрия, который окрашивает цементит в черный цвет и не действует на феррит.
При определении содержания углерода в заэвтектоидной стали по ее структуре следует с помощью микроскопа установить площадь поверхностей шлифа, занятых перлитом и цементитом вторичным. Затем из соответствующих пропорций определить содержание углерода, находящегося в перлите и цементите вторичном. Сумма полученных результатов представляет собой содержание углерода в заэвтектоидной стали.
studfiles.net