Свариваемость 30хгса: Сталь 30ХГСА – расшифровка и характеристики
alexxlab | 23.02.1987 | 0 | Разное
Марка стали 30ХГСА расшифровка, характеристики, применение, аналоги и заменители
Содержание
- 1 Аналоги, Заменители
- 2 Расшифровка стали 30ХГСА
- 3 Применение 30ХГСА
- 4 Свариваемость
- 5 Характеристики
- 5.1 Плотность ρ кг/см3 при температуре испытаний, °С
- 5.2 Коэффициент теплопроводности λ Вт/(м*К) при температуре испытаний, °С
- 5.3 Удельная теплоемкость c, Дж/(кг*К), при температуре испытаний, °С
- 5.4 Коэффициент теплопроводности λ, Вт/(м*К), при температуре испытаний, °С
- 5.5 Коэффициент линейного расширения α*106, К-1, при температуре испытаний, °С
- 5.6 Модуль нормальной упругости Е, ГПа, при температуре испытаний, °С
- 5.7 Модуль упругости при сдвиге на кручением G, ГПа, при температуре испытаний °С
- 6 Температура критических точек
- 7 Химический состав, % (ГОСТ 4345-2016)
- 8 Механические свойства
- 9 Механические свойства в зависимости от сечения
- 10 Механические свойства в зависимости от температуры отпуска
- 11 Механические свойства при повышенных температурах
- 12 Предел выносливости
- 13 Ударная вязкость КСМ
- 14 Технологические свойства
- 15 Критический диаметр d после закалки в различных средах
- 16 Узнать еще
Аналоги, Заменители
Стали заменители 40ХФА, 35ХМ, 40ХН, 25ХГСА, 35ХГСА.
Расшифровка стали 30ХГСА
Цифра 30 указывает среднее содержание углерода в сотых долях %, т.е. содержание углерода в стали около 0,3%.
Буква Х — указывает на присутствие в стали хрома, отсутствие после буквы цифры означает, что содержание хрома не превышает 1,5%.
Буква Г — указывает на присутствие в стали марганца, отсутствие после буквы цифры означает, что содержание марганца не превышает 1,5%.
Буква С — указывает на присутствие в стали кремния, отсутствие после буквы цифры означает, что содержание кремния не превышает 1,5%.
Буква А в конце маркировки стали означает, что сталь является высококачественной.
Применение 30ХГСА
Сталь 30ХГСА применяется для изготовления валов, осей, зубчатых колес, фланцев, корпусов обшивки, лопаток компрессорных машин, работающих при температуре до 200 °С, рычагов, толкателей, ответственных сварных конструкций, детали работающие при знакопеременных нагрузках, крепежные детали, детали работающие при низких температурах.
Свариваемость
Сталь 30ХГСА является ограничено свариваемой. Способы сварки: РДС, АДС под флюсом и газовой защитой, АрДС, ЭШС. Рекомендуется подогрев и последующая термообработка. КТС (Контактно Точечная Сварка) без ограничений
Характеристики
Удельное электросопротивление ρ, при при 20 °С — 210 нОм*м
Плотность ρ кг/см
3 при температуре испытаний, °ССталь | 20 | 100 | 200 | 300 | 400 | 500 | 600 | 700 | 800 | 900 |
30ХГСА | 7850 | 7830 | 7800 | 7760 | 7730 | 7700 | 7670 | — | — | — |
Коэффициент теплопроводности λ Вт/(м*К) при температуре испытаний, °С
Сталь | 20 | 100 | 200 | 300 | 400 | 500 | 600 | 700 | 800 | 900 |
30ХГСА | 38 | 38 | 37 | 37 | 36 | 34 | 33 | 31 | 30 | — |
Удельная теплоемкость
c, Дж/(кг*К), при температуре испытаний, °С20-100 | 20-200 | 20-300 | 20-400 | 20-500 | 20-600 | 20-700 | 20-800 | 20-900 | 20-1000 |
496 | 504 | 512 | 533 | 554 | 584 | 622 | 693 | — | — |
Коэффициент теплопроводности λ, Вт/(м*К), при температуре испытаний, °С
20 | 100 | 200 | 300 | 400 | 500 | 600 | 700 | 800 | 900 |
46 | 46 | — | 41 | — | — | 33 | — | — | 29 |
Коэффициент линейного расширения
α*106, К-1, при температуре испытаний, °С20-100 | 20-200 | 20-300 | 20-400 | 20-500 | 20-600 | 20-700 | 20-800 | 20-900 | 20-1000 |
11,7 | 12,3 | 12,9 | 13,4 | 13,7 | 14,0 | 14,3 | 12,9 | — | — |
Модуль нормальной упругости Е, ГПа, при температуре испытаний, °С
Сталь | 20 | 100 | 200 | 300 | 400 | 500 | 600 | 700 | 800 | 900 |
30ХГСА | 215 | 211 | 203 | 196 | 184 | 173 | 164 | 143 | 125 | — |
Модуль упругости при сдвиге на кручением G, ГПа, при температуре испытаний °С
Сталь | 20 | 100 | 200 | 300 | 400 | 500 | 600 | 700 | 800 | 900 |
30ХГСА | 84 | 82 | 79 | 75 | 71 | 66 | 62 | 54 | 47 | — |
Температура критических точек
Ас1 | Ас3 | Ar3 | Ar1 | Mн |
760 | 830 | 705 | 670 | 352 |
Химический состав, % (ГОСТ 4345-2016)
Сталь | C | Si | Mn | Cr | Ni | Mo | Al | Ti | V | B |
30ХГСА | 0,28-0,34 | 0,90-1,20 | 0,80-1,10 | 0,80-1,10 | — | — | — | — | — | — |
По ГОСТ 4345-2016 массовая доля азота (N) не должна превышать:
в кислородно-конвертерной стали:
— без внепечной обработки:
0,006 % — для тонколистовой металлопродукции и ленты;
0,008 % — для остальных видов металлопродукции;
— с внепечной обработкой:
0,010 % — для тонколистовой металлопродукции и ленты;
0,012 % — для остальных видов металлопродукции;
в стали, выплавленной в электропечах, — 0,012 %.

Массовая доля азота в стали не нормируется и не контролируется в случаях:
— если в стали массовая доля общего алюминия составляет не менее 0,020 % или кислоторастворимого алюминия — не менее 0,015 %, или
-вводятся, по отдельности или в любом сочетании, азотосвязывающие элементы (титан — не более 0,040 %, ванадий — не более 0,05 %, ниобий — не более 0,05 %), при этом суммарная массовая доля алюминия, титана, ванадия и ниобия должна быть от 0,02 % до 0,15 %. Массовая доля перечисленных элементов должна быть указана в документе о качестве.
Допускается массовая доля остаточных элементов, не более: вольфрама — 0,20 %, молибдена — 0,11 %, ванадия — 0,05 % и остаточного или преднамеренно введенного титана (за исключением стали марок, перечисленных в примечании 1 настоящей таблицы) — не более 0,03 %.
По ГОСТ 4345-2016 массовая доля фосфора, серы и остаточных элементов (меди, никеля и хрома) по анализу ковшовой пробы и в готовой металлопродукции должна соответствовать требованиям таблицы 2.
Механические свойства
Источник | Состояние поставки | Сечение, мм | КП | σ0,2 МПа | σв МПа | δ5, % | ψ, % | KCU, Дж/см2 | Твердость HB, не более |
не менее | |||||||||
ГОСТ 4543-71 | Пруток. Закалка с 880 °С в масле; отпуск при 540 °С, охл. в воде или масле | 25 | — | 830 | 1080 | 10 | 45 | 49 | — |
ГОСТ 8479-70 | Поковка. Закалка + отпуск | До 100 | 490 | 490 | 655 | 16 | 45 | 59 | 212-248 |
100-300 | 490 | 490 | 655 | 13 | 40 | 54 | 212-248 | ||
До 100 | 540 | 540 | 685 | 15 | 45 | 59 | 223-262 | ||
До 100 | 590 | 590 | 735 | 14 | 45 | 59 | 235-277 | ||
100-300 | 590 | 590 | 735 | 13 | 40 | 49 | 235-277 | ||
До 100 | 640 | 640 | 785 | 13 | 42 | 59 | 248-293 | ||
До 100 | 675 | 675 | 835 | 13 | 42 | 59 | 262-311 | ||
Пруток.![]() 860-880 °С в масле; отпуск при 200-250 °С, охл. на воздухе | 30 | — | 1270 | 1470 | 7 | 40 | — | HRCэ 43-51 | |
Пруток. Закалка с 860-880 °С в масле; отпуск при 540-560 °С, охл. в воде или масле | 60 | — | 690 | 880 | 9 | 45 | 59 | 225 |
Механические свойства в зависимости от сечения
Сечение, мм | σ0,2 МПа | σв МПа | δ5, % | ψ% | KCU, Дж/см2 |
30 | 880 | 1000 | 12 | 50 | 69 |
60 | 760 | 880 | 12 | 50 | 69 |
80 | 740 | 860 | 14 | 50 | 78 |
120 | 670 | 820 | 14 | 50 | 78 |
160 | 590 | 740 | 14 | 60 | 78 |
200 | 530 | 720 | 14 | 45 | 59 |
240 | 490 | 710 | 14 | 46 | 59 |
Примечание. Закалка с 880 °С в масле; отпуск при 600 °С, охл. в воде.
Механические свойства в зависимости от температуры отпуска
tотп., °С | σ0,2 МПа | σв МПа | δ5, % | ψ% | KCU, Дж/см2 | Твердость HB, не более |
200 | 1570 | 1700 | 11 | 44 | 88 | 487 |
300 | 1520 | 1630 | 11 | 54 | 69 | 470 |
400 | 1320 | 1420 | 12 | 56 | 49 | 412 |
500 | 1140 | 1220 | 15 | 56 | 78 | 362 |
600 | 940 | 1040 | 19 | 62 | 137 | 300 |
Механические свойства при повышенных температурах
tисп., °С | σ0,2 МПа | σв МПа | δ5, % | ψ% | KCU, Дж/см2 |
Пруток.![]() | |||||
300 | 820 | 980 | 11 | 50 | 127 |
780 | 900 | 16 | 69 | 98 | |
500 | 640 | 690 | 21 | 84 | 78 |
550 | 490 | 540 | 27 | 84 | 64 |
Образец диаметром 5 мм, длиной 25 мм, прокатанный. Скорость деформирования 2 мм/мин; скорость деформации 0,0013 1/с | |||||
700 | — | 175 | 59 | 51 | — |
800 | — | 85 | 62 | 75 | — |
900 | — | 53 | 84 | 90 | — |
1000 | — | 37 | 71 | 90 | — |
1100 | — | 21 | 59 | 90 | — |
1200 | — | 10 | 85 | 90 | — |
Предел выносливости
Прочностные характеристики | σ-1, МПа | τ -1, МПа | n |
σв = 1670 МПа | 490 | 1666 | 107 |
σв = 880 МПа | 372 | 882 | 107 |
σв = 1080 МПа | 470 | — | 106 |
Закалка с 870 °С; отпуск при 200 °С | 696 | — | — |
Закалка с 870 °С; отпуск при 400 °С | 637 | — | — |
Ударная вязкость КСМ
Термообработка | KCU, Дж/см2, при температуре, °С | ||||
+20 | -20 | -40 | -60 | -80 | |
Закалка с 880 °С в масле; отпуск при 580-600 °С, σв = 1000 МПа | 69 | 55 | 41 | 35 | 23 |
Технологические свойства
Температура ковки, °С: начала 1240, конца 800. Сечения до 50 мм охлаждаются на воздухе, сечения 51—100 мм — в ящиках.
Обрабатываемость резанием — Kv тв.спл = 0,75 и Kv б.ст = 0,85 в горячекатаном состоянии при НВ 207-217 иов =710 МПа.
Флокеночувствительность — чувствительна.
Склонность к отпускной хрупкости — склонна.
Критический диаметр d после закалки в различных средах
Количество мартенсита, % | Критическая твердость HRC3 | d, мм, после закалки | |
в воде | в масле | ||
50 | 38-43 | 60-91 | 34-60 |
90 | 43-48 | 40-68 | 18-40 |
Министерство образования и науки РФ Федеральное Государственное Бюджетное Образовательное Учреждение высшего Образования «МОСКОВСКИЙ ПОЛИТИХНИЧЕСКИЙ УНИВЕРСИТЕТ» Факультет «МАШИНОСТРОЕНИЕ» Кафедра «Оборудование и технологии сварочного производства» КУРСОВАЯ РАБОТА по дисциплине: «Свариваемость металлов» на тему: «Расчет свариваемости стали 30ХГС» Группа 142232 Студент ________ Корючев Н. Руководитель работы, ________ Л.П. Андреева должность, звание ДОПУСКАЕТСЯ К ЗАЩИТЕ Руководитель работы, ________ Л.П. Андреева должность, звание оценка работы ________ дата _________ МОСКВА 2017 Содержание 1. Свариваемость стали……………………………………………………………………………… 2. Способы расчета свариваемости…………………………………………………………….. 2.1. Основной способ оценки теоретической свариваемости сталей…………… 2.2. Свариваемость металлов. Метод проб………………………………………………….. 3. Косвенный метод расчета свариваемости………………………………………………. 3.1. Расчет свариваемости стали для РДС………………………………………………….. 3.2. Расчет свариваемости для сварки под флюсом………………………………… 3.3. Расчет свариваемости для сварки в среде защитных газов…………………… 4. Вывод……………………………………………………………………………………………………. 5. Список используемой литературы………………………………………………………….. 1. Свариваемость стали 30ХГС Сталь 30ХГС является конструкционной легированной(хромансиль) Она нашла своё применение в машиностроительном производстве, а именно используется для изготовления различных улучшаемых деталей: валов, осей, зубчатых колес, тормозных лент моторов, фланцев, корпусов обшивки, лопаток компрессорных машин, рычагов, толкателей, крепежных деталей, а так же ответственных сварных конструкций, работающих при знакопеременных нагрузках. Легированные конструкционные стали изготавливают в соответствии с ГОСТ 2590-98 и маркируют в соответствии с ГОСТ 4543-71. Как пример возьмём сталь 30ХГС (Содержание углерода в стали 0,20% С). Свариваемость стали: Сталь 30ХГС является ограниченно свариваемой. Её можно сваривать следующими видами сварки: РДС, АДС под флюсом, ЭШС. Рекомендуется использовать предварительный подогрев и последующую термообработку. Для того чтобы получить качественное сварное соединение необходимо произвести дополнительные операции, а именно –предварительный подогрев стали до 200-300 ºС до сварки и термическую обработку после сварки – отжиг На величину временных напряжений существенно влияет скорость охлаждения. Самыми опасными и распространёнными дефектами в ЗТВ являются холодные трещины ( холодные трещины- локальное межкристаллическое разрушение металла сварных соединений, возникающие под действием собственных сварочных напряжений), которые возникают в закалённой структуре металла под влиянием водорода и сварочных напряжений. Технологические особенности: во избежание появления холодных трещин при сварке легированных конструкционных сталей необходимо использовать предварительных подогрев, так же возможно варьирование режимов сварки корневых и последующих швов для создания градиента жёсткости. Тепловые режимы сварки: максимальные скорости охлаждения выбираются с учетом предотвращения образования холодных трещин в ОШЗ. Минимальные скорости охлаждения влияют на ударную вязкость в зоне перегрева. Для того чтобы предотвратить неблагоприятные изменения структуры необходимо снизить погонную энергию и время пребывания отдельных зон при температурах, превышающих температуру отпуска стали. В зависимости от толщины пластины скорости охлаждения регулируются погонной энергией. Рис.1 Диаграмма Шеффлера Согласно расчету сталь относится к ферритно-мартенситному классу [Cr] = 2,53 [Ni]=10,07 2. Способы расчета свариваемости Формулы углеродного эквивалента сталей и других параметрических выражений для оценки свариваемости Для оценки свариваемости сталей применяют такую величину, как углеродный эквивалент сталей (Сэкв). При определении углеродного эквивалента учитывается химический состав сталей, т.к. влияние легирующих элементов на свариваемость стали очень большое. Для определения склонности металла к образованию холодных трещин при сварке, применяют следующие формулы расчёта углеродного эквивалента: СЭКВ = C + Mn/6+(Cr+Mo+V)/5+(Ni+Cu)/ 15, % – данная формула принята для расчёта в Европейском стандарте СЭКВ=С+Мn/6+Sі/24+Nі/40+Сг/5+Мо/4, % – эта формула для определения углеродного эквивалента стали в стандартах Японии СЭКВ=С+Мn/20+Nі/15+(Сг+Мо+V)/ 10, % – такая формула углеродного эквивалента предлагается Британским институтом сварки Однако, как оказалось на практике, для микролегированных сталей с пониженным содержанием углерода эти уравнения не могут охарактеризовать снижение прочности из-за роста зёрен. Немцем Дюреном была выведена формула углеродного эквивалента микролегированных сталей, которая достаточно точно характеризует их склонность к образованию холодных трещин: СЭКВ =C+Si/25+(Mn+Cu)/16+Cr/20+Ni/20+Mo/40+V/15, % Значение углеродного эквивалента позволяет определить, к какой группе свариваемости сталей относится та, или иная марка, кроме того, то значение понадобится, чтобы определить температуру предварительного подогрева при сварке металлов. Т = 350 – , °С где С – общий эквивалент углерода, который можно вычислить следующим образом: С=СЭКВ+СS, СЭКВ – химический эквивалент углерода, вычисляется по формулам, приведённым выше; CS – эквивалент углерода, в зависимости от толщины листа, в мм. Вычисляется по формуле: СS=0,005* S * СЭКВ. В итоге, получаем: С=Сэкв*(1+0,005*S) Кроме углеродного эквивалента для определения и оценки свариваемости сталей существуют несколько параметрических формул, из которых наибольшую популярность получила формула Ито-Бессио: PCM=C+Si/3O+Mn/20+Cu/20+Ni/60+Cr/20+Mo/15+V/15+5B, % РW=Рсм+Н/60+К/(40* 104),% Где К – коэффициент интенсивности жёсткости, который Ито и Бессио применяли при расчётах на основании данных, которые они получили при оценке свариваемости сталей с У-образной разделкой кромок. К=Ко*S, где Ко – константа, равная 69; S – толщина листа, мм. Рсм – коэффициент, характеризующий снижение прочности вследствие структурного преобразования сплава; Н – количество растворённого водорода в металле, образующего сварной шов, измеряется в мл/100г. В Японских стандартах величина Н=0,64, в Европейских Н=0,93. Многочисленные измерения показали, что при Рw>0,286, то возникает риск возникновения холодных трещин в сварном соединении. Если речь идёт об опасности образования горячих трещин в металле сварного шва, то оценить свариваемость стали по этому критерию можно при помощи показателя HCS, вычисляемого по формуле: HCS=(C*[S+P+Si/25+Ni/100]*1000)/(3Mn+Cr+Mo+V) Если получившаяся величина HCS>4, то возникает риск образования горячих трещин. Однако, если выполняется сварка высокопрочных сталей большой толщины, то риск возникновения данного дефекта сварного шва возникает уже при показателе HCS>1,6…2. На практике одним из основных и, зачастую, трудноопределимым дефектом сварного шва являются холодные трещины. Поэтому, наиболее популярной оценкой свариваемости стали, является определение углеродного эквивалента Сэкв по вышеуказанным формулам. Исходя из получившейся величины, можно условно разделить стали на 4 группы свариваемости: СЭКВ не более 0,2 – свариваемость стали хорошая; СЭКВ свыше 0,2 и не более 0,35 – свариваемость стали удовлетворитель- ная; A СЭКВ свыше 0,35 и не более 0,45 – сталь ограниченно свариваемая; СЭКВ свыше 0,45 – свариваемость стали плохая (трудносвариваемая). 2.2. Свариваемость металлов. Метод проб Проба на свариваемость производится для определения способности металлов прочно свариваться. Для этого два отрезка трубы сваривают и из сварного соединения вырезают образцы для испытания на растяжение, загиб и ударную вязкость. В сертификате указывают марку стали, номер партии и плавки и химический состав по данным завода-изготовителя металла результаты контрольного химического анализа металла, произведенного на заводе-изготовителе труб, результаты механических испытаний (на растяжение, ударную вязкость и твердость), металлографических исследований (на макроструктуру и микроструктуру), технологических проб (на сплющивание и бортование или на раздачу) и гидравлического испытания труб пробным давлением. Кроме указанных исследований и испытаний, трубы могут быть подвергнуты другим видам контроля (рентгенографическим исследованиям, испытаниям на свариваемость и др.), результаты которых также вносятся в сертификат. К материалам, подвергаемым контролю в сварочном производстве, относятся свариваемый металл, электроды, различные присадочные материалы, флюсы и защитные газы. Контроль материалов сводится к проверке их соответствия требованиям ГОСТов и ТУ. Особо важное значение имеет контроль при изготовлении ответственных конструкций. Металл в этом случае должен подвергаться специальному лабораторному химическому и металлографическому анализу, механическим испытаниям и пробам на свариваемость. Наряду с этим должны систематически проводиться испытания технологических свойств электродов согласно ГОСТу и выбраковка электродов с такими дефектами, как козырьки, неравномерное, потрескавшееся или влажное покрытие и т.п. Микроструктура околошовной зоны показывает аустенит с некоторым количеством включений карбидов и рост зерна в зоне перегрева. Образцы из торцовой пробы на свариваемость, исследованные на межкристаллитную коррозию в стандартной среде показали стойкость околошовной зоны, равную стойкости основного металла. Ремонтопригодность сварных конструкций определяется свариваемостью металла, характеризующей его реакцию на физико-химическое воздействие процесса сварки и включающей пригодность металла к сварке, надежность И экономическую целесообразность сварки. Свариваемость оценивают с помощью ряда качественных и количественных показателей, отражающих как возможность получения сварных соединений с определенными свойствами, так и уровень этих свойств, выраженных в абсолютных или относительных величинах по сравнению с нормативными значениями или по сравнению с основным металлом. Холодные трещины обусловлены диффузионной способностью водорода, который накапливается преимущественно в местах высокой концентрации напряжений, понижая запас пластичности металла и способствуя возникновению очагов разрушения. Методы количественной оценки сопротивляемости сталей образованию холодных трещин основаны на том, что условия образования холодных трещин при сварке позволяют рассматривать их как один из случаев замедленного разрушения стали под действием остаточных напряжений. Применяемые при оценке склонности сталей к образованию холодных трещин технологические пробы (ТКС, Лихайская, МВТУ, Теккен, ЛПТ-2 И т.д.), имитирующие сварные соединения с жестким закреплением свариваемых элементов, как известно, имеют существенный недостаток – отсутствует количественная оценка критерия, и они не характеризуют технологический запас прочности, B связи с этим они пригодны лишь для сравнительной оценки материалов. Свариваемость стабилизированных хромоникелевых сталей аустенитного класса при реакции на термический цикл характеризуется отсутствием структурных составляющих, понижающих коррозионную стойкость. По кривой распределения твердости в зоне термического влияния, полученной при исследовании стали 20Х2Н4А торцовой пробой на свариваемость, определена твердость, практически равная твердости основного металла. Проба на сплющивание труб применяется для определения способности металла к деформациям при сплющивании до определенного размера. Отрезок трубы, равный ее наружному диаметру, сплющивают ударами молотка, кувалды или под прессом до пределов, заданных величиной. При сплющивании вплотную в = 0) допускается петля диаметром до 0,25. В сварных трубах шов должен быть расположен по диаметральной плоскости, перпендикулярной к линии действия сил. 3. Косвенный метод расчета свариваемости Инженерный программный комплекс “Свариваемость легированных сталей” предназначен для оперативного анализа технологических вариантов сварки типовых стыковых соединений жесткозакрепленных элементов из легированных сталей, а также для подбора значений конструктивно-технологических параметров, обеспечивающих стойкость сварного соединения против образования ХОЛОДНЫХ трещин. Комплекс реализован на основе алгоритма и является плодом многолетней работы коллектива лаборатории «Свариваемость материалов» МГТУ им. Н.Э. Баумана. В программном комплексе реализовано имитационное моделирование физических процессов, протекающих в металле при сварке, на базе фундаментальных законов термодинамики, металлофизики, механики с использованием статических моделей и концептуальной модели образования холодных трещин, предложенной профессором Э. Структурного – соотношение структурных составляющих, содержание в них углерода, размер аустенитного зерна; Водородного – концентрации диффузионно-подвижного водорода; Силового – уровня сварочных напряжений 1-го рода. Инженерный программный комплекс ”Свариваемость легированных сталей” позволяет определить:
3.1. Расчет свариваемости стали для РДС Параметры режима сварки:
Предварительный подогрев 200°С Послесварочный подогрев 200°С, 4ч Рис.2 Геометрия разделки кромок шва под РДС Сварочные материалы: сварочные электроды НИАТ-3М предназначены для сварки особо ответственных конструкций из легированных сталей повышенной и высокой прочности с временным сопротивлением до 1130 МПа во всех пространственных положения шва постоянным током обратной полярности. Покрытие электродов- основное. Диаметр электрода равен 4мм. Результаты расчёта на свариваемость приведены на рисунках 3-8. Рис.3 Трещиностойкость Рис.4 Соотношение структурных составляющих. Рис.5 Форма проплавления Рис.6 Критическое и сварочное напряжение Рис.7 Максимальная температура нагрева Рис.8 Твёрдость(HV), ОШЗ 3.2. Расчет свариваемости для сварки под флюсом Параметры режима сварки:
Предварительный подогрев 200°С Послесварочный подогрев 200°С, 4ч Рис.9 Геометрия разделки кромок шва под автоматическую сварку под флюсом Сварочные материалы: Сварочная проволока Св-18ХГС принадлежит к классу нержавеющих сварочных проволок, имеет в своем составе марганец, хром и кремний и широко используется для сварки и наплавки металла. Результаты расчета на свариваемость приведены на рисунках 10-14. Рис.10 Трещиностойкость Рис.11 Соотношение структурных составляющих Рис.11 Форма проплавления Рис.12 Критическое и сварочное напряжение Рис.13 Максимальная температура нагрева Рис.14 Твёрдость(HV), ОШЗ 3.3. Расчет свариваемости для сварки в среде защитных газов (СО2) Параметры режима сварки:
Предварительный подогрев 200°С Послесварочный подогрев 200°С, 3ч Рис. Сварочные материалы: Сварочная проволока Св-18ХГС принадлежит к классу нержавеющих сварочных проволок, имеет в своем составе марганец, хром и кремний и широко используется для сварки и наплавки металла. Применяется для сварки элементов металлоконструкций, выполненных из легированных и конструкционных сталей. Рекомендуют сварочную проволоку данной марки для сварки под флюсом и в среде защитных газов и отмечают высокие показатели прочности получаемого сварного шва, а также его стойкость к коррозии. Кроме того, проволоку Св-18ХГС можно применять для сварки под воздействием высокого давления. Диаметр проволоки равен 2мм. Результаты расчета на свариваемость приведены на рисунках 16-20. Рис.16. Максимальная температура нагрева Рис.17 Соотношение структурных составляющих Рис.18 Критическое и сварочное напряжение Рис.19 Трещиностойкость Рис.20 Форма проплавления 4. В данной курсовой работе мы рассмотрели сталь 30ХГС. Была дана оценка свариваемости металла на холодные и горячие трещины, так же было определено, что данная сталь относится к ферритно–мартенситному классу.В свою очередь сталь 30ХГС является ограниченно свариваемой. Способы сварки применимые к ней это: РДС, АДС под флюсом и газовой защитой, АрДС, ЭШС . Проведен косвенный метод оценки свариваемости металла через программу «Свариваемость 2.1» для 3 способов сварки – РДС, сварка в СО2 и автоматической сварки под флюсом. Подобраны и обоснованы сварочные материалы. Рассмотрев три косвенных метода расчёта на свариваемость стали 30ХГС, работающей в одинаковых условиях после сварки, сделаем вывод, что наилучшим способом является сварка в защитной среде CO2, так как в результате проведённой сварочной операции мы получаем наименьшую вероятность образования холодных трещин, меньшую зону термического влияния и меньшая температура нагрева околошовной зоны. Список литературы, использованной при выполнении курсового проекта 1. «Оборудование и технология сварочного производства» / В.Н. Волченко, В.М. Ямпольский‚ В.А. Винокуров и др.; Под редакцией B.B. Фролова. М.: Высшая школа, 1988. 5590. 2. Сварка B машиностроении: Справочник. В 4-х томах. / Редкол.: Г.А. Николаев (пред.) И др. М: Машиностроение, 1978-79. 3. Марочник сталей и сплавов / /В.Г. Сорокин, А.В. Волосникова‚ С.А. Вяткин и др.; Под общей редакцией Б.Г. Сорокина. М.: Машиностроение, 1989. 640 с. 4. Сварка и свариваемые материалы: Справочник. В 3-х томах. /Ред. проф. докт. техн. наук В. Н. Волченко, Э. Л. Макаров и др. М: “Металлургия” Том 1. 1991. 528 с. 5. Сварка и свариваемые материалы: Справочник. В 3-х томах. /Ред. проф. докт. техн. наук В. Н. Волченко, Э. Л. Макаров и др. М: “Металлургия” Том 2. 1991. 528 с. 6. Сварочные материалы для дуговой сварки: Справочное пособие. В 2-х томах. / Под ред. Н. Н. Потапова. М: “Машиностроение” 1989. 544C. 7. ГОСТ 29273-92 Свариваемость. Определение. Комитет стандартизации и метрологии СССР. Государственный стандарт союза СССР. Москва. 1992г. 8. ГОСТ 2590-88 Прокат стальной горячекатаный круглый. Издательство стандартов. Москва. 1988г. 9. ГОСТ 4543-71 Прокат из легированной конструкционной стали. Технические условия. Издательство стандартов. Москва. 1973г. Каталог: files -> portfolio жүктеу/скачать 160. Достарыңызбен бөлісу: |
Сталь 30ХГСА | ТД СпецСплав
ГОСТ 5950-2000; 4543-71. Круги, поковки, полоса 5ХНМ, Х12МФ, 38ХН3МФА
Марка | 30ХГСА |
Заменитель: | 40ХФА, 35ХМ, 40ХН, 25ХГСА, 35ХГСА |
Классификация | Сталь конструкционная легированная |
Применение | различные улучшаемые детали: валы, оси, зубчатые колеса, фланцы, корпуса обшивки, лопатки компрессорных машин, работающие при температуре до 200°С, рычаги, толкатели, ответственные сварные конструкции, работающие при знакопеременных нагрузках, крепежные детали, работающие при низких температурах. |
ГОСТ | ГОСТ 4543-71 |
Химический состав в % материала 30ХГСА
C | Si | Mn | Ni | S | P | Cr | Cu |
0.![]() | 0.9 — 1.2 | 0.8 — 1.1 | до 0.3 | до 0.025 | до 0.025 | 0.8 — 1.1 | до 0.3 |
Температура критических точек материала 30ХГСА
Ac1 = 760 , Ac3(Acm) = 830 , Ar3(Arcm) = 705 , Ar1 = 670 , Mn = 352 |
Механические свойства при Т=20
oС материала 30ХГСАСортамент | Размер | Напр. | sв | sT | d5 | y | KCU | Термообр.![]() |
— | мм | — | МПа | МПа | % | % | кДж / м2 | — |
Пруток | Ж 25 | 1080 | 830 | 10 | 45 | 490 | Закалка 880oC, масло, Отпуск 540oC, вода, | |
Лист отожжен. | 500-750 | 14 |
Твердость
Твердость материала 30ХГСА после отжига , | HB 10 -1 = 229 МПа |
Физические свойства материала 30ХГСА
T | E 10— 5 | a 10 6 | l | r | C | R 10 9 |
Град | МПа | 1/Град | Вт/(м·град) | кг/м3 | Дж/(кг·град) | Ом·м |
20 | 2.![]() | 38 | 7850 | 210 | ||
100 | 2.11 | 11.7 | 38 | 7830 | 496 | |
200 | 2.03 | 12.3 | 37 | 7800 | 504 | |
300 | 1.96 | 12.9 | 37 | 7760 | 512 | |
400 | 1.84 | 13.4 | 36 | 7730 | 533 | |
500 | 1.73 | 13.7 | 34 | 7700 | 554 | |
600 | 1.![]() | 14 | 33 | 7670 | 584 | |
700 | 1.43 | 14.3 | 31 | 622 | ||
800 | 1.25 | 12.9 | 30 | 693 | ||
T | E 10— 5 | a 10 6 | l | r | C | R 10 9 |
Технологические свойства материала 30ХГСА
Свариваемость: | ограниченно свариваемая. |
Флокеночувствительность: | чувствительна. |
Склонность к отпускной хрупкости: | склонна.![]() |
Обозначения:
Механические свойства : | |
sв | — Предел кратковременной прочности , [МПа] |
sT | — Предел пропорциональности (предел текучести для остаточной деформации), [МПа] |
d5 | — Относительное удлинение при разрыве , [ % ] |
y | — Относительное сужение , [ % ] |
KCU | — Ударная вязкость , [ кДж / м2] |
HB | — Твердость по Бринеллю , [МПа] |
Физические свойства : | |
T | — Температура, при которой получены данные свойства , [Град] |
E | — Модуль упругости первого рода , [МПа] |
a | — Коэффициент температурного (линейного) расширения (диапазон 20o — T ) , [1/Град] |
l | — Коэффициент теплопроводности (теплоемкость материала) , [Вт/(м·град)] |
r | — Плотность материала , [кг/м3] |
C | — Удельная теплоемкость материала (диапазон 20o — T ), [Дж/(кг·град)] |
R | — Удельное электросопротивление, [Ом·м] |
Свариваемость : | |
без ограничений | — сварка производится без подогрева и без последующей термообработки |
ограниченно свариваемая | — сварка возможна при подогреве до 100-120 град.![]() |
трудносвариваемая | — для получения качественных сварных соединений требуются дополнительные операции: подогрев до 200-300 град. при сварке, термообработка после сварки — отжиг |
30ХГСА – Промышленная Компания Митра
Марка : | 30ХГСА |
Заменитель: | 40ХФА, 35ХМ, 40ХН, 25ХГСА, 35ХГСА |
Классификация : | Сталь конструкционная легированная |
Дополнение: | Сталь хромокремнемарганцовая. |
Применение: |
Различные улучшаемые детали: валы, оси, зубчатые колеса, фланцы, корпуса обшивки, лопатки компрессорных машин, работающие при температуре до 200°С, рычаги, толкатели, ответственные сварные конструкции, работающие при знакопеременных нагрузках, крепежные детали, работающие при низких температурах.![]() |
C | Si | Mn | Ni | S | P | Cr | Cu |
0.28 – 0.34 | 0.9 – 1.2 | 0.8 – 1.1 | до 0.3 | до 0.025 | до 0.025 | 0.8 – 1.1 |
до 0.![]() |
Примечание: Также хим. состав указан в ГОСТ 10543-98 |
Температура критических точек материала 30ХГСА.
Ac1 = 760 , Ac3(Acm) = 830 , Ar3(Arcm) = 705 , Ar1 = 670 , Mn = 352 |
Технологические свойства материала 30ХГСА .
Свариваемость: | ограниченно свариваемая. |
Флокеночувствительность: |
чувствительна.![]() |
Склонность к отпускной хрупкости: | склонна. |
Механические свойства при Т=20oС материала 30ХГСА .
Сортамент | Размер | Напр. | sв | sT | d5 | y | KCU | Термообр. |
– | мм | – | МПа | МПа | % | % | кДж / м2 | – |
Трубы, ГОСТ 8731-87 | 686 | 11 | ||||||
Трубы холоднодеформир.![]() |
491 | 18 | ||||||
Пруток, ГОСТ 4543-71 | Ø 25 | 1080 | 830 | 10 | 45 | 490 | Закалка 880oC, масло, Отпуск 540oC, вода, | |
Лист толстый, ГОСТ 11269-76 | 490-740 | 20 | Нормализация | |||||
Лист толстый, ГОСТ 11269-76 | 1080 | 9 | 490 | Закалка и отпуск | ||||
Лист тонкий, ГОСТ 11268-76 | 490-740 | 20 | Нормализация | |||||
Лист тонкий, ГОСТ 11268-76 | 1080 | 10 | Закалка и отпуск |
Твердость 30ХГСА после отжига , ГОСТ 4543-71 | HB 10 -1 = 229 МПа |
Твердость 30ХГСА , Трубы холоднодеформир.![]() |
HB 10 -1 = 229 МПа |
Твердость 30ХГСА , Пруток горячекатан. ГОСТ 10702-78 | HB 10 -1 = 217 МПа |
Твердость 30ХГСА нормализованного , Лист толстый ГОСТ 11269-76 | HB 10 -1 = 156 – 217 МПа |
Физические свойства материала 30ХГСА .
T | E 10– 5 | a 10 6 | l | r | C | R 10 9 |
Град | МПа | 1/Град | Вт/(м·град) | кг/м3 | Дж/(кг·град) | Ом·м |
20 |
2.![]() |
38 | 7850 | 210 | ||
100 | 2.11 | 11.7 | 38 | 7830 | 496 | |
200 | 2.03 | 12.3 | 37 | 7800 | 504 | |
300 |
1.![]() |
12.9 | 37 | 7760 | 512 | |
400 | 1.84 | 13.4 | 36 | 7730 | 533 | |
500 | 1.73 | 13.7 | 34 | 7700 | 554 | |
600 |
1.![]() |
14 | 33 | 7670 | 584 | |
700 | 1.43 | 14.3 | 31 | 622 | ||
800 | 1.25 | 12.9 | 30 | 693 | ||
T | E 10– 5 | a 10 6 | l | r | C | R 10 9 |
Зарубежные аналоги материала 30ХГСА
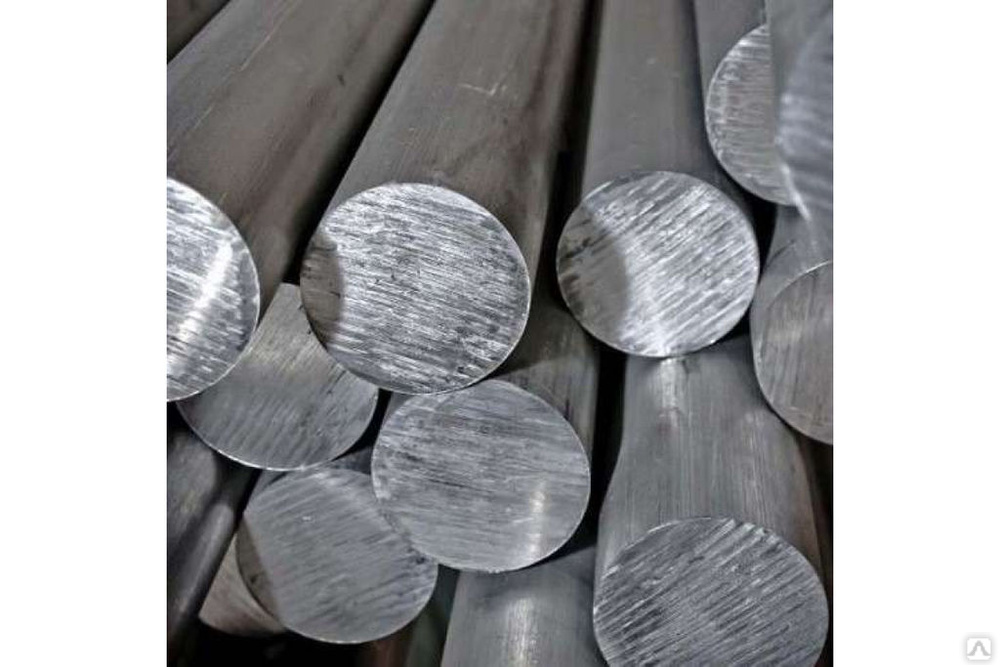
Болгария | Польша | Чехия | |||
BDS | PN | CSN | |||
|
|
Обозначения:
Механические свойства : | |
sв | – Предел кратковременной прочности , [МПа] |
sT | – Предел пропорциональности (предел текучести для остаточной деформации), [МПа] |
d5 | – Относительное удлинение при разрыве , [ % ] |
y | – Относительное сужение , [ % ] |
KCU | – Ударная вязкость , [ кДж / м2] |
HB | – Твердость по Бринеллю , [МПа] |
Физические свойства : |
|
T | – Температура, при которой получены данные свойства , [Град] |
E | – Модуль упругости первого рода , [МПа] |
a | – Коэффициент температурного (линейного) расширения (диапазон 20o – T ) , [1/Град] |
l | – Коэффициент теплопроводности (теплоемкость материала) , [Вт/(м·град)] |
r | – Плотность материала , [кг/м3] |
C | – Удельная теплоемкость материала (диапазон 20o – T ), [Дж/(кг·град)] |
R | – Удельное электросопротивление, [Ом·м] |
Свариваемость : |
|
без ограничений | – сварка производится без подогрева и без последующей термообработки |
ограниченно свариваемая |
– сварка возможна при подогреве до 100-120 град.![]() |
трудносвариваемая |
– для получения качественных сварных соединений требуются дополнительные операции: подогрев до 200-300 град. при сварке, термообработка после сварки – отжиг |
1. Общая характеристика стали 30ХГСА
1. Общая характеристика материала: сталь 30ХГСА.
Конструкционная
легированная сталь 30ХГСА является одним
из многочисленных достижений отечественной
науки. Она была разработана во время
Великой Отечественной войны советскими
учеными Всероссийского Института
Авиационных Материалов специально для
нужд авиации. Рождение этой марки было
прорывом в области создания металлов.
Ведь теперь СССР обогнали США на несколько
лет, кроме того, советская авиация
получила преимущество при войне с
Германией и способствовала победе, ведь
технические характеристики 30ХГСА
намного превзошли хромомолибденовую
сталь, которую применяли в то время.
Второе название стали 30ХГСА – «хромансиль». Это сокращение от названий входящих в ее состав легирующих элементов. Хром – повышает стойкость к коррозии и твердость. Марганец дает устойчивость к ударным нагрузкам и износостойкость. Ну а кремний повышает ударную вязкость и температурный запас вязкости. В настоящее время, под хромансилем подразумевают несколько марок, но изначально под ним подразумевалась именно 30ХГСА.
Приятной особенностью этой высококачественной стали является то, что стоимость ее сравнительно недорогая, так как она не содержит дефицитных легирующих элементов. Также 30ХГСА обладает хорошей свариваемостью.
1. 1.
Химический состав
Fe | C | Si | Mn | Ni | S | P | Cr | Cu |
~96 | 0,28 –0,34 | 0,90 –1,20 | 0,80 –1,10 | до 0,30 | до 0,025 | до 0,025 | 0,80 –1,10 | до 0,30 |
1. 2.
Механические свойства
Сталь 30ХГСА по сравнению со сталью 25ХГСА имеет больше углерода, поэтому она обладает повышенными механическими свойствами, имеет удовлетворительную пластичность в оттаженном состоянии.
σ0,2, МПа | σu, МПа | δ % | ψ, % | Твердость HB, не более |
690 | 880 | 9 | 45 | 225 |
1. 3.
Термическая обработка
1.4. Технологические свойства
Свариваемость – ограниченно свариваемая.
Способы сварки: РДС, АДС под флюсом и газовой защитой, АрДС, ЭШС. Рекомендуется подогрев и последующая термообработка. КТС без ограничений.
Флокеночувствительность – чувствительна.
Склонность к отпускной хрупкости – склонна.
1.5. Применение
Применяется для изготовления сварных штампованных, клепанных и механически обрабатываемых деталей, различные улучшаемые детали: валы, оси, зубчатые колеса, фланцы, корпуса обшивки, лопатки компрессорных машин, работающие при температуре 200 С0, рычаги, толкатели, ответственные сварные конструкции, работающие при знакопеременных нагрузках, крепежные детали, работающие при низких температурах.
Д. | Лист | |||||
Изм. | Лист | № докум. | Подп. | Дата |
Марка 30ХГСА. Сталь конструкционная легированная 30ХГСА | Ленстальинвест
12Г2 для холодной штамповки, в том числе для вытяжки
12Х2НВФА для изготовления тонколистового проката, применяемого в термически обработанном состоянии
10Г2 Крепежные и другие детали, работающие при температуре от —70 °С под давлением.
12Х2Н4А Зубчатые колеса, валы, ролики, поршневые пальцы и другие крупные особо ответственные цементуемые детали, к которым предъявляются требования высокой прочности, пластичности и вязкости сердцевины и поверхностной твердости, работающие под действием ударных нагрузок или при отрицательных температурах до -120 °С.
10Х2М для изготовления неответственных деталей, изготавливаемых методом холодной штамповки и высадки- заготовок деталей для АЭС
12Х2НВФМА для изготовления тонколистового проката, применяемого в термически обработанном состоянии
12ХН2 Шестерни, валы, червяки, кулачковые муфты, поршневые пальцы и другие цементуемые детали, к которым предъявляются требования высокой прочности, пластичности и вязкости сердцевины и высокой поверхностной твердости, работающие под действием ударных нагрузок и при отрицательных температурах.
12Х2НМФА для изготовления тонколистового проката, применяемого в термически обработанном состоянии
12ХН Для изготовления зубчатых венцов, зубчатых колес, пальцев и других ответственных деталей, работающих в условиях ударных и знакопеременных нагрузок
12ХН2А шестерни, валы, червяки, кулачковые муфты, поршневые пальцы и другие цементуемые детали, к которым предъявляются требования высокой прочности, пластичности и вязкости сердцевины и высокой поверхностной твердости, работающие под действием ударных нагрузок и при отрицательных температурах.
14Х2ГМР тяжелонагруженные сварные детали и узлы.
14Х2Н3МА в цементованном и улучшенном состоянии применяется для ответственных деталей, к которым предъявляются требования высокой прочности, вязкости и износостойкости, а также для деталей, подвергающихся высоким вибрационным и динамическим нагрузкам. Сталь может применяться при температуре от —70 до +450 °С.
12ХН3А Шестерни, валы, червяки, кулачковые муфты, поршневые пальцы и другие цементуемые детали, к которым предъявляются требования высокой прочности, пластичности и вязкости сердцевины и высокой поверхностной твердости, работающие под действием ударных нагрузок или при отрицательных температурах до -100 °С.
14ХГН Для изготовления крестовин кардана автомобилей
15Г После улучшения — заклепки ответственного назначения- после цементации или цианирования — поршневые пальцы, фрикционные диски, пальцы рессор, кулачковые валики, болты, гайки, винты, шестерни, червяки и другие детали с высокой твердостью и износостойкостью поверхности- без термообработки — сварные подмоторные рамы, башмаки, косынки, штуцера, втулки.
15Н2М (15НМ) Зубчатые венцы, зубчатые колеса, пальцы и другие ответственные детали, работающие в условиях ударных и знакопеременных нагрузок
15ХА Втулки, пальцы, шестерни, валики, толкатели и другие цементуемые детали, к которым предъявляется требование высокой поверхностной твердости при невысокой прочности сердцевины, детали, работающие в условиях износа при трении.
15Х втулки, пальцы, шестерни, валики, толкатели и другие цементуемые детали, к которым предъявляется требование высокой поверхностной твердости при невысокой прочности сердцевины, детали, работающие в условиях износа при трении.
15ХГН2ТА (15ХГНТА) Зубчатые венцы, шатуны, зубчатые колеса и т.д.
15ХГНМ для изготовления изделий методом холодного выдавливания и высадки и горячекатаного проката (подката, катанки) для изготовления калиброванного и со специальной отделкой поверхности проката и проволоки
15ХФ Для некрупных деталей, подвергаемых цементации и закалке с низким отпуском (зубчатые колеса, поршневые пальцы, распределительные валики, плунжеры, копиры)
16ХСН для изготовления деталей методом холодной высадки
18Х2Н4ВА в цементованном и улучшенном состоянии применяется для ответственных деталей, к которым предъявляются требования высокой прочности, вязкости и износостойкости, а также для деталей, подвергающихся высоким вибрационным и динамическим нагрузкам. Сталь может применяться при температуре от —70 до +450 °С.
18Х2Н4МА В цементованном и улучшенном состоянии применяется для ответственных деталей, к которым предъявляются требования высокой прочности, вязкости и износостойкости, а также для деталей, подвергающихся высоким вибрационным и динамическим нагрузкам. Сталь может применяться при температуре от —70 до +450 °С.
16Г2 для холодной штамповки, в том числе для вытяжки
18ХГТ Улучшаемые или цементуемые детали ответственного назначения, от которых требуется повышенная прочность и вязкость сердцевины, а также высокая поверхностная твердость, работающие под действием ударных нагрузок.
18ХГ Для цементуемых деталей небольших сечений, работающих на трение
19Х2НВФА для изготовления тонколистового проката, применяемого в термически обработанном состоянии
19ХГН Для производства крестовин карданных валов автомобилей
20Г2 для производства инструментальной оснастки повышенной износостойкости, работающей при умеренных и значительных давлениях без разогрева режущей кромки
19Х2НМФА для изготовления тонколистового проката, применяемого в термически обработанном состоянии
20Г После улучшения — заклепки ответственного назначения- после цементации или цианирования — поршневые пальцы, фрикционные диски, пальцы рессор, кулачковые валики, болты, гайки, шестерни, червяки и другие детали с высокой твердостью и износостойкостью поверхности. Без термообработки — сварные подмоторные рамы, башмаки, косынки.
12Х2НМ1ФА для изготовления тонколистового проката, применяемого в термически обработанном состоянии
20Н2М (20НМ) Зубчатые венцы, зубчатые колеса, пальцы и другие ответственные детали, работающие в условиях ударных и знакопеременных нагрузок
20Х12Н12Г6 Для производства катанки и луженой проволоки, предназначенных для изготовления бандажей роторов электрических машин.
20Х Втулки, шестерни, обоймы, гильзы, диски, плунжеры, рычаги и другие цементуемые детали, к которым предъявляются требования высокой поверхностной твердости при невысокой прочности сердцевины, детали, работающие в условиях износа при трении.
20Х14 Для изготовления горячекатаной и холоднотянутой проволоки, предназначенной для механизированной электродуговой наплавки.
20Х17Н3М Для изготовления горячекатаной и холоднотянутой проволоки, предназначенной для механизированной электродуговой наплавки.
20Х2Н4А Шестерни, вал-шестерни, пальцы и другие цементуемые особо ответственные высоконагруженные детали, к которым предъявляются требования высокой прочности, пластичности и вязкости сердцевины и высокой поверхностной твердости, работающие под действием ударных нагрузок или при отрицательных температурах.
20ХГНМ Для изготовления деталей, подвергающихся высоким вибрационным и динамическим нагрузкам.
20ХГНТР крестовины кардана автомобилей
20ХГР Зубчатые колеса, вал-шестерни, червяки, кулачковые муфты, валики, пальцы, втулки и другие улучшаемые или цементуемые детали, работающие в условиях ударных нагрузок.
20ХГНР Зубчатые колеса, вал-шестерни, червяки, кулачковые муфты, валики, втулки и другие ответственные детали, работающие в условиях ударных нагрузок.
20ХГСА Ходовые винты, оси, валы, червяки и другие детали, работающие в условиях износа и при знакопеременных нагрузках при температурах до 200 °С.
20ХМ Для изготовления зубчатых колес коробок передач
20ХН шестерни, втулки, пальцы, детали крепежа и другие детали, от которых требуется повышенная вязкость и умеренная прокаливаемость.
20ХН2М (20ХНМ) Шестерни, полуоси, сателлиты, кулачки, шарниры и другие детали.
20ХН3А Шестерни, валы, втулки, силовые шпильки, болты, муфты, червяки и другие цементуемые детали, к которым предъявляются требования высокой прочности, пластичности и вязкости сердцевины и высокой поверхностной твердости, работающие под действием ударных нагрузок и при отрицательных температурах.
20ХНР зубчатые колеса, валы-шестерни, червяки, кулачковые муфты, валики, пальцы, втулки и другие нагруженные крупные детали, работающие в условиях ударных нагрузок.
20ХФ для некрупных деталей, подвергаемых цементации и закалке с низким отпуском (зубчатые колеса, поршневые пальцы, распределительные валики, плунжеры, копиры)
21Х2НВФА для изготовления тонколистового проката, применяемого в термически обработанном состоянии
20ХН4ФА Клапаны впуска, болты, шпильки и другие ответственные детали, работающие в коррозионной среде при повышенных температурах (300— 400 °С).
21Х2НМФА для изготовления тонколистового проката, применяемого в термически обработанном состоянии
23Х2НМФА для изготовления тонколистового проката, применяемого в термически обработанном состоянии
23Х2НВФА для изготовления тонколистового проката, применяемого в термически обработанном состоянии
25Г После улучшения — заклепки ответственного назначения- после цементации или цианирования — поршневые пальцы, фрикционные диски, пальцы рессор, кулачковые валики, болты, гайки, винты, шестерни, червяки и другие детали с высокой твердостью и износостойкостью поверхности- без термообработки — сварные подмоторные рамы, башмаки, косынки, штуцера, втулки.
25Х2ГНТА балки, болты, оси, нагруженные внутренним давлением сосуды
25Х2Н4ВА Крупногабаритные шатуны, муфты и другие детали большой вязкости и прокаливаемости
25Х2Н4МА Крупногабаритные шатуны, муфты и другие детали большой вязкости и прокаливаемости
25ХГМ зубчатые колеса коробки передач
25ХГНМТ Для изготовления деталей приборов работающих на трение- деталей вспомогательных узлов машин и приспособлений.
25ХГСА Ответственные сварные и штампованные детали, применяемые в улучшенном состоянии: ходовые винты, оси, валы, червяки, шатуны, коленчатые валы, штоки и другие детали.
27ХГР Детали ответственного назначения: кулачки шарнира переднего ведущего моста, зубчатые колеса и др.
25ХГТ Нагруженные зубчатые колеса и другие детали, твердость которых более НRСэ 59.
30Г Улучшаемые детали, к которым предъявляются требования невысокой прочности: тяги, оси, цилиндры, диски, болты, гайки, винты и другие.
30Г2 Коленчатые валы, полуоси, цапфы, рычаги сцепления, вилки переключения передач, фланцы
30Х10Г10Т Для изготовления горячекатаной и холоднотянутой проволоки, предназначенной для механизированной электродуговой наплавки.
30Х Крепежные детали для работы при температурах не выше 400 град.
30Х3МФ Детали судовых дизелей и др. детали, которые должны обладать износостойкостью при высоких давлениях-сталь подвергается азотированию, теплоустойчива до 450 град. С
30Х5 Для изготовления горячекатаной и холоднотянутой проволоки, предназначенной для механизированной электродуговой наплавки.
30ХГСН2А (30ХГСНА) Шестерни, фланцы, кулачки, пальцы, валики, оси, шпильки и другие ответственные тяжелонагруженные детали.
30ХГСНМА Для изготовления труб
30ХГТ Улучшаемые и цементуемые детали, от которых требуется высокая прочность, вязкая сердцевина и высокая поверхностная твердость, работающие при больших скоростях и повышенных удельных давлениях под действием ударных нагрузок.
30ХН2ВА Для изготовления коленчатых валов, шатунов, ответственных болтов, шпилек, специального крепежа, дисков, звездочек и других ответственных деталей, работающих в сложных условиях нагружения при нормальных, пониженных и повышенных температурах.
30ХН2ВФА Валы, цельнокованые роторы, диски, детали редукторов, болты, шпильки и другие ответственные детали турбин и компрессорных машин, работающие при повышенных температурах.
30ХГС Различные улучшаемые детали: валы, оси, зубчатые колеса, тормозные ленты моторов, фланцы, корпуса обшивки, лопатки компрессорных машин, рычаги, толкатели, ответственные сварные конструкции, работающие при знакопеременных нагрузках, крепежные детали.
30ХН2МА (30ХНМА) Коленчатые валы, шатуны, ответственные болты, шпильки, диски, звездочки и другие ответственные детали, работающие в сложных условиях нагружения при нормальных, пониженных и повышенных температурах
30ХН2МФА Валы, цельнокованые роторы, диски, детали редукторов, болты, шпильки и другие ответственные детали турбин и компрессорных машин, работающие при повышенных температурах.
30ХН3М2ФА диски паровых турбин.
30ХРА Оси, валики, рычаги, болты, гайки и другие некрупные детали, а также зубчатые колеса, валы и нагруженные шпильки
30ХН3А Венцы ведомых колес тяговых зубчатых передач электропоездов, шестерни и другие улучшаемые детали. Может применяться при температуре —80 °С (толщина стенки не более 100 мм).
33ХС Улучшаемые детали пружинного типа сравнительно небольших сечений, от которых требуется высокая прочность, износостойкость и упругость.
34ХН1М диски, вали, роторы турбин и компрессорных машин, вала экскаваторов, оси, муфты, шестерни, полумуфты, вал-шестерни, болты, сило-вые шпильки и другие особо ответственные высоконагруженные детали, к которым предьявляются высокие требования по механическим свойствам и работающие при температуре до 500 °С
34ХН1МА валы, роторы, диски парових турбин, валы-шестерни, муфты, зубчатые колеса и другие особо ответственные тяжелонагруженные детали, работающие при температуре до 500 град.С
34ХН3МА валы, роторы, диски парових турбин, валы-шестерни, муфты, зубчатые колеса и другие особо ответственные тяжелонагруженные детали, работающие при температуре до 500 град.С
35Г Тяги, оси, серьги, траверсы, рычаги, муфты, валы, звездочки, цилиндры, диски, шпиндели, соединительные муфты паровых турбин, болты, гайки, винты и другие детали, к которым предъявляются требования невысокой прочности.
34ХН3М крупные особо ответственные детали с высокими требованиями к механическим свойствам.
35Г2 Валы, полуоси, цапфы, рычаги сцепления, вилки, фланцы, коленчатые валы, шатуны, болты, кольца, кожухи, шестерни и другие детали, применяемые в различных отраслях машиностроения, к которым предъявляются требования повышенной износостойкости.
35ХГ2 для цементуемых деталей небольших сечений, работающих на трение
35Х Оси, валы, шестерни, кольцевые рельсы и другие улучшаемые детали.
35ХГН2
35ХГСА Фланцы, кулачки, пальцы, валики, рычаги, оси, детали сварных конструкций и другие улучшаемые детали сложной конфигурации, работающие в условиях знакопеременных нагрузок.
35ХГФ Валы, кулаки, звездочки, оси, рычаги, работающие в условиях трения и повышенных нагрузок в автотракторном и с/х машиностроении
36Г2С для изготовления бесшовных бурильных труб и муфт к ним, применяемых при геологоразведочном колонковом бурении.
36Х2Н2МФА (36ХН1МФА) Для крупных ответственных деталей-дисков, крепежных болтов и т. д.
38Х2Н2ВА Валы, шатуны, болты, шпильки и другие крупные особо ответственные тяжелонагруженные детали сложной конфигурации, применяемые в улучшенном состоянии
35ХН1М2ФА оси, диски, валы и другие особо ответственные крупные детали с высокими требованиями к механическим свойствам.
38Х2Н2МА (38ХНМА) Валы, шатуны, болты, шпильки и другие крупные особо ответственные тяжелонагруженные детали сложной конфигурации, применяемые в улучшенном состоянии.
38Х2Н3М ответственные детали контейнеров с высокими требованиями по механическим свойствам при повышенных температурах.
38Х2НМФ ответственные детали тяжелого и транспортного машиностроения типа осей, валов и другие высоконагруженные детали, а также детали, используемые в условиях низких температур
38Х2НМ ответственные детали тяжелого и транспортного машиностроения типа осей, валов и другие высоконагруженные детали, а также детали, используемые в условиях низких температур.
38Х2Ю (38ХЮ) трущиеся детали приборов, детали вспомогательных узлов машин и приспособлений
38ХВ Ответственные детали турбин и компрессоров
38ХГМ Для изготовления зубчатых колес коробок передач
38ХГН Детали экскаваторов, крепеж, валы, оси, зубчатые колеса, серьги и другие ответственные детали, к которым предъявляются требования повышенной прочности.
38ХМ Ответственные детали турбин и компрессоров, работающие при температуре до 400 град.С
38ХМА ответственные детали общего назначения в машиностроении.
38ХГНМ для изготовления специального крепежа, валов, осей и других ответственных деталей горно-металлургического и нефтедобывающего оборудования, к которым предъявляются требования повышенной прочности.
38ХН3МА Валы, оси, шестерни и другие крупные особо ответственные детали.
38ХН3МФА Наиболее ответственные тяжелонагруженные детали, работающие при температурах до 400 °С.
38ХА Червяки, зубчатые колеса, шестерни, валы, оси, ответственные болты и другие улучшаемые детали.
38ХС Валы, шестерни, муфты, пальцы и другие улучшаемые летали небольших размеров, к которым предъявляются требования высокой прочности, упругости и износостойкости.
40Г Оси, коленчатые валы, шестерни, штоки, бандажи, детали арматуры, шатуны, звездочки, распределительные валики, головки плунжеров и другие детали, к которым предъявляются требования повышенной прочности.
40ГР Для изготовления после улучшения — заклепок ответственного назначения- после цементации или цианирования — поршневых пальцев, фрикционных дисков, пальцев рессор, кулачковых валиков, болтов, гаек, винтов, шестерней, червяков и других деталей с высокой твердостью и износостойкостью поверхности- без термообработки — сварных подмоторных рам, башмаков, косынок, штуцеров, втулок- звеньев гусениц тракторов.
40Х Оси, валы, вал-шестерни, плунжеры, штоки, коленчатые и кулачковые валы, кольца, шпиндели, оправки, рейки, губчатые венцы, болты, полуоси, втулки и другие улучшаемые детали повышенной прочности.
40Х2Г2М Для изготовления горячекатаной и холоднотянутой проволоки, предназначенной для механизированной электродуговой наплавки.
40Г2 Оси, коленчатые валы, поршневые штоки, рычаги, распреде лительные валики, карданные валы, полуоси и другие детали.
40Х2Н2ВА Крупные изделия: валы, диски, редукторные шестерни, а также крепежные детали
40Х3Г2МФ Для изготовления горячекатаной и холоднотянутой проволоки, предназначенной для механизированной электродуговой наплавки.
40ХГНМ деталей вспомогательных узлов машин и приспособлений- деталей шасси автомобилей
40Х2Н2МА (40Х1НВА) Крупные изделия: валы, диски, редукторные шестерни, а также крепежные детали.
40ХГТР Валы, кулаки, звездочки, оси, рычаги, работающие в условиях трения и повышенных нагрузок в автотракторном и с/х машиностроении
38ХН3ВА Валы, оси, шестерни и другие крупные особо ответственные детали.
40ХМФА Шлицевые валы, щтоки, шатуны, крепежные детали трубопроводов, работающие при температуре до 400 град. С
40ХН Оси, валы, шатуны, зубчатые колеса, валы экскаваторов, муфты, валы-шестерни, шпиндели, болты, рычаги, штоки, цилиндры и другие ответственные нагруженные детали, подвергающиеся вибрационным и динами ческим нагрузкам, к которым предъявляются требования повышенной прочности и вязкости. Валки рельсобалочных и крупносортных станов для горячей прокатки металла.
40ХСН2МА для высоконагруженных деталей, не имеющих значительных концентраторов напряжения и работающих при температуре от -70 до 250°C
40ХН2МА (40ХНМА) Коленчатые валы, клапаны, шатуны, крышки шатунов, ответственные болты, шестерни, кулачковые муфты, диски и другие тяжелонагруженные детали. Валки для холодной прокатки металлов.
40ХС Валы, шестерни, муфты, пальцы и другие улучшаемые детали небольших размеров, к которым предъявляются требования высокой прочности, упругости, износостойкости.
40ХФА В улучшенном состоянии—шлицевые валы, штоки, установочные винты, траверсы, валы экскаваторов и другие детали, работающие при температуре до 400 °С- после закалки и низкого отпуска — червячные валы и другие детали повышенной износостойкости.
45Г Коленчатые валы, шатуны, оси, карданные валы, тормозные рычаги, диски трения, зубчатые колеса, шлицевые и шестеренные валы, анкерные болты.
45Г2 Валы-шестерни, коленчатые и карданные валы, полуоси, червяки, крышки шатунов, шатуны, звенья конвейерных цепей и другие крупногабаритные средненагруженные детали.
45Х Валы, шестерни, оси, болты, шатуны и другие детали, к которым предъявляются требования повышенной твердости, износостойкости, прочности и работающие при незначительных ударных нагрузках.
45Х4В3ГФ Для изготовления горячекатаной и холоднотянутой проволоки, предназначенной для механизированной электродуговой наплавки.
45ХН2МФА (45ХНМФА) Торсионные валы, коробки передач и другие нагруженные детали, работающие при скручивающих повторно-переменных нагрузках и испытывающие динамические нагрузки.
47ГТ Полуоси автомобилей.
50Г Диски трения, валы, шестерни, шлицевые валы, шатуны, распределительные валики, втулки подшипников, кривошипы, шпиндели, ободы маховиков, коленвалы дизелей и газовых двигателей и другие детали, к которым предъявляются требования повышенной прочности и износостойкости.
45ХН Коленчатые валы, шатуны, шестерни, шпиндели, муфты, болты и другие ответственные детали.
50Г2 Шестерни, диски трения, шестеренные валы и другие детали, работающие на истирание.
50Х3В10Ф Для изготовления горячекатаной и холоднотянутой проволоки, предназначенной для механизированной электродуговой наплавки.
50Х Валы, шпиндели, установочные винты, крупные зубчатые колеса, редукторные валы, упорные кольца, валки горячей прокатки и другие улучшаемые детали, к которым предъявляются требования повышенной твердости, износостойкости, прочности и работающие при незначительных ударных нагрузках.
50ХН Валки для горячей прокатки, валы-шестерни, зубчатые колеса, бандажи, коленчатые валы, шатуны, болты, выпускные клапаны и другие крупные ответственные детали.
Г13А Для изготовления горячекатаной и холоднотянутой проволоки, предназначенной для механизированной электродуговой наплавки.
50Х6ФМС Для изготовления горячекатаной и холоднотянутой проволоки, предназначенной для механизированной электродуговой наплавки.
Х6Ф1 Для изготовления лемехов плугов
50ХНМ Для изготовления горячекатаной и холоднотянутой проволоки, предназначенной для механизированной электродуговой наплавки.
Сталь 30 кггса / EVEK
Сталь 06х1
Сталь 06х1F
Сталь 06хGR
Сталь 06хF
Сталь 07х3GNMюA
Сталь 08G8 08.08.1108.108.108.118.1108.118.1108.118.1108.1108.
. 08хMчA (08хMч)
Сталь 09GSFA (09GSF)
Сталь 09N2MFABA (09N2MERA-A)
сталь 09SFA (09SF)
сталь 09 ° С.
9000 9000 9000.9.9.3.3md2md2md2md2md2md2md2.3.0003Сталь 09хN4MD (AB4)
Сталь 10G2 (10G2A)
Сталь 10GN (10GNA)
Сталь 10х1S2M
Сталь 10х2GNM (10х2GNMA)
Сталь 10KH3M11HEM13.3000.301HNMA13.3.0003.101HNMA13.301HNMA
.101HNMA 2 9000.3000.101HNMA 2.19.301HNMA) 9000 3. Ø2)Сталь 12G1R
Сталь 12KH3N4A (эI83)
Сталь 12KH3NVFA (эI712)
Сталь 12KH3NVFMA (эP506; эI712M)
9000. 19.13.13.13.13.13.19.13.m.19.0003
Сталь 12хGNM
Сталь 12хGNMP
Сталь 12KHN
Сталь 12KHN2
Сталь 12хN2A
Сталь 12хN2MD (AB1)
сталь 12KHN3A
. 138-2
Сталь 13N2хA
Сталь 13N5A
Сталь 13х3NVM2P0002 Steel 13HFA (13ХФ)
Steel 14Н2МФД (14Н2МФДА)
Steel 14Х2ГМР
Steel 14Х2Н3МА
Steel 14Х3ГМЮ
Steel 14ХГ2САФД
Steel 14KHGN
Steel 14ХГН2МДАФБ (14ХГНМДАФБ)
Steel 14ХГНМДАФБРТ (14ХГНМД)
Steel 14 ° С.С.С. (эP176; DI3A)
Сталь 14хN3MA
Сталь 15G (15G1)
Сталь 15GюT
Сталь 15N2M (15NM)
Steel 15N3MA
Steel 15KH
Steel 15.11SMMMMA
сталь 15KH 9000 3
Steel 15.11SMMA
.0003
Steel 15Х2ГН2ТА
Steel 15Х2ГН2ТРА
Steel 15KHA
Steel 15ХГН2МАФАч
Steel 15KHGN2TA (15ХГНТА)
Steel 15KHGNM (15ХГНМА)
Steel 15ХМФА (15ХМФ)
Steel 15ХН3
Steel 15ХР
Steel 15ХСМФБ ( ЭP79)
Сталь 15хPA (15 к / чф)
Сталь 16G2
Сталь 16х2N3MFAю (16х2N3MPAR; VKS7)
16х3NVPHEB (VKS-5; DI39)
Стальная сталь 16-1666 (а. 16).0003
Steel 16ХН3МА
Steel 16KHSN
Steel 17Н3МА
Steel 17ХГ
Steel 18Г2ХФЮД
Steel 18Kh3N4VA
Steel 18Kh3N4MA
Steel 18KHG
Steel 18ХГН2МФБ
Steel 18HGT
Steel 18ХН2Т
Steel 18ХН3МА
Сталь 18ХНВА
Сталь 18ХНМФД (18ХНМФДА)
Сталь 19Х3НВФА (ЭИ763)
Сталь 19Х3НМФА
Сталь 19ХГН
Сталь 19ХГНМАХGNM)
Сталь 19хGS
Сталь 20G (20G1)
Сталь 20G2
Сталь 20 Г2аф (20G2APS)
Сталь 20G2R
Сталь 20GHOT
Стальная сталь 20N2M (20NM)
. 20KHСталь 20х2MA
Сталь 20х2MFA
Сталь 20KH3N4A
Сталь 20х2N4MP (20х2N4MFA)
Сталь 20х3NME (20х3NMFA)
Steel 20000
9000 9000 2 9000 2 9000 2 9000 2 9000 2 9000 2 9000 2 9000 2 9000 2 9000 2 9000 2 9000 2 9000 2 9000 2 9000 2 9000 2Steel 20KHGNTR
Steel 20KHGR
Steel 20KHGSA
Steel 20ХГСР
Steel 20KHM
Steel 20KHN
Steel 20KHN2M (20ХНМ)
Steel 20KHN3A
Steel 20ХН3МФА (20ХН3МФ)
Steel 20KHN4FA
Steel 20KHNR
Сталь 20ХФА (20ХФ)
Сталь 21Н5А (ЭИ56)
Сталь 21Х3НВФА
Сталь 21Х3НМФА
Сталь 22ХНМА (220ХГН 9М
)30002 Steel 23Г2Д
Steel 23Kh3NVFA (ЭИ659)
Steel 23Kh3NMFA
Steel 23ХН2М
Steel 24Г2
Steel 24Х3МФ (24Х3МФА)
Steel 24ХНМ
Steel 25G (25Г2)
Steel 50G
Steel 50Г2
Сталь 50S
Сталь 50 кн
Сталь 5хNM2
Сталь 85GPE
Сталь Ак32
Сталь Ак33
Сталь Ак34
Сталь Ак35
Стальная0003
Steel АК48
Steel АК49
Steel АК50
Steel 25N
Steel 25Н3А
Steel 25Kh3N4VA
Steel 25Kh3N4MA
Steel 25ХГ2СФР
Steel 25KHGM
Steel 25ХГНМА (25ХГНМ)
Steel 25KHGNMT (25ХГНМТА)
Сталь 25 кггса
Сталь 25 кггт
Сталь 25хM
Сталь 25хN3
Сталь 25хNTц
Сталь 26G1
Сталь 26х1MA (26х1M)
Сталь 26х2NVMBRR (KVK-26)
Сталь 26х2NVMBRR (KVK-26)
Стальная0003
Steel 26ХГМ
Steel 26ХГМФ (26ХГМФА)
Steel 26ХМА (26ХМ; 25ХМ)
Steel 27KHGR
Steel 30G (30Г1)
Steel 30Г1Р
Steel 30G2
Steel 30T
Steel 30KH
Steel 30х2N2yfa
Сталь 30х2N2 мг. 0003
Steel 30Х3НВА
Steel 30KHGS
Steel 30KHGSA
Steel 30KHGT
Steel 30KHM
Steel 30KHMA
Steel 30KHN2VA
Steel 30KHN2VFA
Steel 30KHN2MA (30ХНМА)
Steel 30KHN2MFA
Steel 30KHN3A
Steel 30ХН3М
Сталь 30ХНМФА (30ХНВФА)
Сталь 30ХРА
Сталь 30ХСНВФА (ВП30)
Сталь 32Г2
Сталь 32Г2С 30ХНВФА
3202С
0003Steel 33Х3СНМВФА (СП33; ЭП613)
Steel 33ХН3МА
Steel 33KHS
Steel 34ХН1ВА (0ХН1В)
Steel 34ХН3М
Steel 35G
Steel 35Г1Р
Steel 35G2
Steel 35KH
Steel 35Х2ГЮФ
Стальная 35GN2
Стальная 35HGSA
35 км стали
сталь 35хN2P0003
Steel 37Г2С
Steel 37Х2НВМБР (ERC-37)
Steel 37ХН3А
Steel 38h3MYUA (38ХМЮА)
Steel 38Kh3N2VA
Steel 38Kh3N2MA (38ХНМА)
Steel 38Х2Н3М
Steel 38Х2НМ
Steel 38Х2НМФ
Steel 38х2ю (38х2юa)
Стальная 38 кха
сталь 38 кгм
Сталь 38 кхгггггггггггну
Сталь 38 кгггг
сталь 38хGA (38хGS)
Steel 38KHM (42хMM)
сталь
сталь 38 км (42х мг. 0003
Steel 38KHN3VA
Steel 38KHN3MA
Steel 38KHS
Steel 38ХФР (40ХФР)
Steel 40G
Steel 40G2
Steel 40GR (40Г1Р)
Steel 40X (40ХА)
Steel 40Kh3N2VA
Steel 40Х2Н2МА
сплав 40х3M2PA (USP-40)
Сталь 40 кгггггг
сталь 40 ° СМА
Сталь 40 кггт
Сталь 40KHMFA (40хME)
сталь 40 кн
Сталь 40хN2A (40хNA)
.0002 Сталь 40 КН2МА (40HNMA)
Сталь 40хR
Сталь 40HS
Сталь 40хSN2MA
Сталь 40 КХФА (40хF)
Сталь 42х2NVMBR (KVK-42)
Сталь 42NMBRREBR (KVK-42)
. Сталь 44х2NMBR (ABO70В)
Сталь 45G
Сталь 45G2
Сталь 45 кх
сталь 45KHN
Сталь 45KHN2MFA (45GHNMFA)
сталь 47G3953333333333333333333333333333333333333333333333333333333333333333333333333333333333333 3333333333333333333333333333333333333333333333333333333333333333333333333333333.0554 Имя Значение
Описание
Сталь 30ХГСА применяется: для производства горячекатаного толстого листа и прессованных профилей экстрацель; различные модернизируемые детали (валы, оси, шестерни, фланцы, обшивки корпусов, лопатки компрессоров), работающие при температуре до +200 °С; рычаги, толкатели, ответственные сварные конструкции, работающие при знакопеременных нагрузках; монтаж деталей, работающих при низких температурах, бесшовных труб для изготовления деталей и конструкций в мотовелотехнике; проволока, предназначенная для изготовления заклепок и болтов методом холодной осадки; сварочная проволока; трубы, используемые в авиационной технике.
Примечание
Сталь конструкционная высококачественная хромонемат.
Стандарты
Наименование | Код | Стандарты |
---|---|---|
Прутки и профили | В32 | ГОСТ 1051-73, ГОСТ 4543-71, ГОСТ 7417-75, ГОСТ 8559-75, ГОСТ 8560-78, ГОСТ 10702-78, ГОСТ 14955-77, ОСТ 1-76, ТУ 14-1-5414-2001 , ТУ 14-1-1885-85, ТУ 14-1-2118-77, ТУ 14-1-2765-79, ТУ 14-1-658-73, ТУ 14-1-950-74, ТУ 1-9-30-82, ТУ 14-1-3238-81, ТУ 14-11-245-88, ТУ 14-1-3238-2006, ТУ 14-1-1271-75, ТУ 14-1-5228-93, ТУ 14-136-367-2008 |
Листы и полосы | В33 | ГОСТ 11268-76, ГОСТ 11269-76, ТУ 14-105-490-86, ТУ 14-1-1409-75, ТУ 14-1-1699-76, ТУ 14-1-1904-76, ТУ 14- 1-1994-76, ТУ 14-1-2360-78, ТУ 14-1-4013-85, ТУ 14-1-4118-86, ТУ 14-229-276-88, ТУ 14-1-4118-2004 |
Прутки и профили | В22 | ГОСТ 1133-71, ГОСТ 8319.0-75, ГОСТ 2590-2006, ГОСТ 2591-2006, ГОСТ 2879-2006 |
Листы и полосы | В23 | ГОСТ 82-70, ГОСТ 103-2006 |
Обработка металлов давлением.![]() | В03 | ГОСТ 8479-70, ОСТ 5Р.9125-84, СТ ЦКБА 010-2004 |
Трубы стальные и фитинги к ним | В62 | ГОСТ 8732-78, ГОСТ 8734-75, ГОСТ 9567-75, ГОСТ 12132-66, ГОСТ 19277-73, ГОСТ 21729-76, ГОСТ 23270-89, ГОСТ 24950-81, ГОСТ 8733-87, ГОСТ 8731-87, ГОСТ Р 53383-2009, ТУ 14-3-1140-82, ТУ 14-3-271-74, ТУ 14-3-674-78, ТУ 14- 3-675-78, ТУ 14-3-531-76, ТУ 14-3-473-76, ТУ 14-159-241-93, ТУ 14-3-957-80, ТУ 14-3-1654-89 |
Классификация, номенклатура и общие правила | В20 | ОСТ 1-91 |
Заготовки. Из заготовки. Плиты | В21 | ОСТ 14-13-75 |
Заготовки. Из заготовки. Плиты | В31 | ОСТ 3-1686-90, ТУ 14-1-1563-75, ТУ 14-1-1672-76, ТУ 14-1-1687-76, ТУ 14-1-3716-84, ТУ 14-1-4944 -90, ТУ 14-1-4992-91, ТУ 14-1-4797-90, ТУ 1-92-156-90 |
Сварка и резка металлов. Пайка, клепка | В05 | ТУ 14-1-4816-90 |
Лента | В34 | ТУ 14-4-1152-81 |
Стальная проволока со средним и высоким содержанием углерода | В72 | ТУ 14-4-385-73 |
Химический состав
Стандарт | С | С | Р | Мн | Кр | Си | Ni | Фе | Медь | В | Ти | Пн | Вт |
---|---|---|---|---|---|---|---|---|---|---|---|---|---|
ТУ 14-1-1885-85 | 0,28-0,34 | ≤0,015 | ≤0,025 | 0,8-1,1 | 0,8-1,1 | 0,9-1,2 | ≤0,3 | Остальное | ≤0,25 | – | – | – | – |
ТУ 14-1-2765-79 | 0,28-0,34 | ≤0,015 | ≤0,025 | 0,8-1,1 | 0,8-1,1 | 0,9-1,2 | ≤0,3 | Остальное | ≤0,25 | ≤0,05 | ≤0,03 | ≤0,15 | ≤0,2 |
ТУ 14-4-385-73 | 0,28-0,34 | ≤0,025 | ≤0,025 | 0,8-1,1 | 0,8-1,1 | 0,9-1,2 | ≤0,3 | Остальное | ≤0,25 | ≤0,05 | ≤0,03 | ≤0,15 | ≤0,2 |
ТУ 14-1-4118-2004 | 0,28-0,34 | ≤0,025 | ≤0,025 | 0,8-1,1 | 0,8-1,1 | 0,9-1,2 | ≤0,3 | Остальное | ≤0,3 | ≤0,05 | ≤0,03 | ≤0,15 | ≤0,2 |
ТУ 14-3-674-78 | 0,28-0,34 | ≤0,005 | ≤0,025 | 0,8-1,1 | 0,8-1,1 | 0,9-1,2 | ≤0,3 | Остальное | – | – | – | – | – |
Fe является основой.
ГОСТ 4543-71 регламентирует содержание сортовой стали: Р≤0,025%; S≤0,015%; Сu≤0,25%.
По ТУ 14-1-2765-79 химический состав приведен для стали 30ХГСА-Ш.
По ТУ 14-1-3238-81 для стали марки 30ХГСА-СШ содержание S≤0,015%. Для стали марки 30ХГСА (выбрать) содержание углерода установлено на уровне С = 0,27-0,32 %.
По ТУ 14-3-674-78 химический состав приведен для стали 30ХГСА-ВД.
По ГОСТ 19277-73 химический состав приведен для стали 30ХГСА-ВД; Сталь марки 30ХГСА должна иметь химический состав по ГОСТ 4543. При выплавке стали скаппроцессом массовая доля меди должна быть ≤ 0,25 % в сталях марок 30ХГСА и 30ХГСА-ВД. Предельное отклонение по химическому составу – по ГОСТ 4543. Для стали марки 30ХГСА-ВД суммарная массовая доля серы и фосфора не должна превышать 0,25 %, допускается отклонение по марганцу плюс 0,1 и минус 0,2 %.
По ГОСТ 21729-76 химический состав приведен для стали 30ХГСА-ВД; Сталь марки 30ХГСА должна иметь химический состав по ГОСТ 4543. При выплавке стали скаппроцессом массовая доля меди должна быть ≤ 0,25 % в сталях марок 30ХГСА и 30ХГСА-ВД. Предельное отклонение по химическому составу – по ГОСТ 4543. Для стали марки 30ХГСА-ВД суммарная массовая доля серы и фосфора не должна превышать 0,22%.
По ТУ 14-1-1885-85 химический состав приведен для стали марки 30ХГСА-ВД. Для обеспечения требуемой крупности ванадий допускается вводить в выплавку стали из расчета содержания его в стали не более 0,10 %, содержание которого в стали не определяют. Наличие вольфрама до 0,20 %, молибдена до 0,15 %, титана до 0,030 % не является дефектом. Допустимый разброс содержания марганца в стали +0,010/-0,020%.
Механические свойства
Сечение, мм | t отпускания, °С | с Т |с 0,2 , МПа | σ U , МПа | д 5 , % | д 4 | д 10 | г, % | KCU, кДж/м 2 | НВ, МПа | HRc |
---|---|---|---|---|---|---|---|---|---|---|
Сталь калиброванная и калиброванная со специальной обработкой поверхности | ||||||||||
– | – | – | 490-740 | – | – | – | – | – | – | – |
– | – | – | ≤690 | – | – | – | ≥57 | – | ≤229 | – |
Трубы бесшовные холодно- и горячедеформированные в состоянии поставки термообработанные (НВ – стенка >10 мм) | ||||||||||
– | – | ≥686 | ≥11 | – | – | – | – | – | – | |
– | – | ≥491 | ≥18 | – | – | – | – | ≤229 | – | |
Поковки.![]() | ||||||||||
≤100 | – | ≥490 | ≥655 | ≥16 | – | – | ≥45 | ≥590 | 212-248 | – |
100-300 | – | ≥490 | ≥655 | ≥13 | – | – | ≥40 | ≥540 | 212-248 | – |
≤100 | – | ≥540 | ≥685 | ≥15 | – | – | ≥45 | ≥590 | 223-262 | – |
≤100 | – | ≥590 | ≥735 | ≥14 | – | – | ≥45 | ≥590 | 235-277 | – |
100-300 | – | ≥590 | ≥735 | ≥13 | – | – | ≥40 | ≥490 | 235-277 | – |
≤100 | – | ≥640 | ≥785 | ≥13 | – | – | ≥42 | ≥590 | 248-293 | – |
≤100 | – | ≥675 | ≥835 | ≥13 | – | – | ≥42 | ≥590 | 262-311 | – |
Стальной прокат.![]() | ||||||||||
120-160 | – | ≥590 | ≥740 | ≥14 | – | – | ≥50 | ≥780 | – | – |
Диаметр прутка 20-70 мм. Закалка в масло при 880 °С + Отпуск, охлаждение в воду | ||||||||||
– | 200 | ≥1570 | ≥1700 | ≥11 | – | – | ≥44 | – | ≥487 | – |
Градация эксплуатационных свойств готовых термообработанных деталей по ОСТ 1-91 | ||||||||||
– | – | – | 690-880 | – | – | – | – | – | 212-262 | 19-27 |
Образец диаметром 5 мм, длиной 25 мм, ламинированный. Скорость деформации 2 мм/мин Скорость деформации 0,0013 1/ | ||||||||||
– | – | – | ≥175 | ≥59 | – | – | ≥51 | – | – | – |
Сталь горячекатаная и горячекатаная со специальной отделкой поверхности.![]() | ||||||||||
– | – | – | – | – | – | – | – | – | ≤217 | – |
Стальной прокат. Закалка в масло при 880 °С + Ст при 600 °С, охлаждение в воде | ||||||||||
15-30 | – | ≥880 | ≥1000 | ≥12 | – | – | ≥50 | ≥690 | – | – |
Диаметр прутка 20-70 мм. Закалка в масло при 880 °С + Отпуск, охлаждение в воду | ||||||||||
– | 300 | ≥1520 | ≥1630 | ≥11 | – | – | ≥54 | – | ≥470 | – |
Градация эксплуатационных свойств готовых термообработанных деталей по ОСТ 1-91 | ||||||||||
– | – | – | 880-1080 | – | – | – | – | – | 262-311 | 27-34 |
Образец диаметром 5 мм, длиной 25 мм, ламинированный.![]() | ||||||||||
– | – | – | ≥85 | ≥62 | – | – | ≥75 | – | – | – |
Стальной прокат. Закалка в масло при 880 °С + Ст при 600 °С, охлаждение в воду | ||||||||||
160-200 | – | ≥530 | ≥720 | ≥14 | – | – | ≥45 | ≥590 | – | – |
Диаметр прутка 20-70 мм. Закалка в масло при 880 °С + Отпуск, охлаждение в воду | ||||||||||
– | 400 | ≥1320 | ≥1420 | ≥12 | – | – | ≥56 | – | ≥412 | – |
Градация эксплуатационных свойств готовых термообработанных деталей по ОСТ 1-91 | ||||||||||
– | – | – | 1080-1270 | – | – | – | – | – | 311-363 | 34-39 |
Образец диаметром 5 мм, длиной 25 мм, ламинированный.![]() | ||||||||||
– | – | – | ≥53 | ≥84 | – | – | ≥90 | – | – | – |
Стальной прокат. Закалка в масло при 880 °С + Ст при 600 °С, охлаждение в воде | ||||||||||
200-240 | – | ≥490 | ≥710 | ≥14 | – | – | ≥45 | ≥590 | – | – |
Диаметр прутка 20-70 мм. Закалка в масло при 880 °С + Отпуск, охлаждение в воду | ||||||||||
– | 500 | ≥1140 | ≥1220 | ≥15 | – | – | ≥56 | – | ≥362 | – |
Градация эксплуатационных свойств готовых термообработанных деталей по ОСТ 1-91 | ||||||||||
– | – | – | 1080-1420 | – | – | – | – | – | 311-401 | 34-43 |
Образец диаметром 5 мм, длиной 25 мм, ламинированный.![]() | ||||||||||
– | – | – | ≥37 | ≥71 | – | – | ≥90 | – | – | – |
Кольцо цилинкерное по ОСТ 1-76. Закалка в масло с 865-895 °С + Отпуск при 490-590 °С, охлаждение в масло или воду | ||||||||||
– | ≥833 | ≥1020 | ≥9 | – | – | ≥40 | ≥392 | – | – | |
Стальной прокат. Закалка в масло при 880 °С + Ст при 600 °С, охлаждение в воду | ||||||||||
30-50 | – | ≥760 | ≥880 | ≥12 | – | – | ≥50 | ≥690 | – | – |
Диаметр прутка 20-70 мм. Закалка в масло при 880 °С + Отпуск, охлаждение в воду | ||||||||||
– | 600 | ≥940 | ≥1040 | ≥19 | – | – | ≥62 | – | ≥300 | – |
Образец диаметром 5 мм, длиной 25 мм, ламинированный.![]() | ||||||||||
– | – | – | ≥21 | ≥59 | – | – | ≥90 | – | – | – |
Лист стальной горячекатаный (4-60 мм) 4-й и 5-й категорий. Закалка в масло при 880±15°С + Отпуск при 480-570°С, охлаждение в масло | ||||||||||
– | – | ≥1080 | ≥9 | – | – | – | ≥490 | – | – | |
Стальной прокат. Закалка в масло при 880 °С + Ст при 600 °С, охлаждение в воду | ||||||||||
50-80 | – | ≥740 | ≥860 | ≥14 | – | – | ≥50 | ≥780 | – | – |
Образец диаметром 5 мм, длиной 25 мм, ламинированный. Скорость деформации 2 мм/мин Скорость деформации 0,0013 1/ | ||||||||||
– | – | – | ≥10 | ≥85 | – | – | ≥90 | – | – | – |
Лист тонкой (≤3,9мм) горяче- и холоднокатаный.![]() | ||||||||||
– | – | ≥1080 | ≥10 | – | – | – | – | – | – | |
Стальной прокат. Закалка в масло при 880 °С + Ст при 600 °С, охлаждение в воду | ||||||||||
80-120 | – | ≥670 | ≥820 | ≥14 | – | – | ≥50 | ≥780 | – | – |
Стержень. Закалка в масло при 880 °С + Отпуск при 560 °С, охлаждение на воздухе | ||||||||||
– | – | ≥820 | ≥980 | ≥11 | – | – | ≥50 | – | – | – |
Плоские с другой 14-1-4118-2004 | ||||||||||
– | – | 490-736 | – | ≥20 | ≥16 | – | – | – | – | |
Стержень.![]() | ||||||||||
– | – | ≥780 | ≥900 | ≥16 | – | – | ≥69 | – | – | – |
Провод на другой 14-4-385-73 в состоянии поставки. Субангина с предварительным отжигом до зернистого перлита | ||||||||||
– | – | 490-687 | ≥8 | – | – | – | – | – | – | |
Стержень. Закалка в масло при 880 °С + Отпуск при 560 °С, охлаждение на воздухе | ||||||||||
– | – | ≥640 | ≥690 | ≥21 | – | – | ≥84 | – | – | – |
Прутки горячекатаные, кованые и калиброванные. Закалка в масло 865-895°С + Выдержка 510-570°С, охлаждение в масле | ||||||||||
– | ≥830 | ≥1080 | ≥10 | – | – | ≥45 | ≥490 | 311-375 | – | |
Стержень.![]() | ||||||||||
– | – | ≥490 | ≥540 | ≥27 | – | – | ≥84 | – | – | – |
Прутки и полосы горячекатаные и кованые. Закалка в масло с 865-895 °С + Отпуск при 510-570 °С, охлаждение в масло | ||||||||||
– | ≥835 | ≥1080 | ≥10 | – | – | ≥45 | ≥490 | 311-363 | – | |
Стержни из стали 30ХГСА по пр. 14-1-1885-85. Закалка в масло с 870-890°С + Отпуск при 510-570°С, охлаждение в масле. На графике KCU значения KCU показаны вдоль волокна/KCU поперек волокна | ||||||||||
Образец 25х25 | – | ≥885 | ≥1080 | ≥10 | – | – | ≥45 | ≥490/294 | 310-363 | – |
Прутки и прутки стальные, обработанные в ковше синтетическим шлаком в состоянии поставки по др.![]() | ||||||||||
– | – | – | ≥6 | – | – | ≥28 | ≥294 | – | – | |
Стальной прокат. Закалка в масло с 860-880 °С + Отпуск при 200-250 °С с воздушным охлаждением | ||||||||||
15-30 | – | ≥1270 | ≥1470 | ≥7 | – | – | ≥40 | – | – | 43-51 |
Стальной прокат. Закалка в масло с 860-880 °С + Отпуск при 540-560 °С, охлаждение в воду или масло | ||||||||||
30-60 | – | ≥690 | ≥880 | ≥9 | – | – | ≥45 | ≥590 | 225 | – |
Трубы бесшовные: для масло- и топливопроводов по ГОСТ 19277-73, холодные, холодные и топлокатные по ГОСТ 21729-76 термически обработанные в состоянии поставки | ||||||||||
– | – | ≥490 | ≥18 | – | – | – | – | – | – |
Описание механических меток
Наименование | Описание |
---|---|
с Т | с 0,2 | Предел текучести или предел пропорциональности с допуском на остаточную деформацию 0,2% |
σ U | Предел кратковременной прочности |
д 5 | Удлинение после разрыва |
г 4 | Удлинение после разрыва |
д 10 | Удлинение после разрыва |
у | Относительное сужение |
ККУ | Прочность |
НВ | Число твердости по Бринеллю |
Твердая сталь | Твердость по Роквеллу (индентор алмазный сфероконический) |
Физические характеристики
Температура | Å, гПа | Г, ГПа | р, кг/м 3 | л, Вт/(м·°С) | Р, г·м | а, 10 -6 1/°С | С, Дж/(кг·°С) |
---|---|---|---|---|---|---|---|
0 | 215 | 84 | 7850 | 38 | 210 | – | – |
20 | 215 | 83 | 7850 | 38 | 210 | – | – |
100 | 211 | 82 | 7830 | 38 | – | 117 | 496 |
200 | 203 | 80 | 7800 | 37 | – | 123 | 504 |
300 | 196 | 75 | 7760 | 37 | – | 129 | 512 |
400 | 184 | 71 | 7730 | 36 | – | 134 | 533 |
500 | 173 | 66 | 7700 | 34 | – | 137 | 554 |
600 | 164 | 61 | 7670 | 33 | – | 14 | 584 |
700 | 143 | 55 | – | 31 | – | 143 | 622 |
800 | 125 | 48 | – | 30 | – | 143 | 622 |
1000 | – | – | – | – | – | 129 | 693 |
Описание физических символов
Имя | Описание |
---|---|
Е | Нормальный модуль упругости |
Г | Модуль упругости при сдвиге и кручении |
р | Плотность |
л | Коэффициент теплопроводности |
Р | УД.![]() |
и | Коэффициент линейного расширения |
Технологические свойства
Наименование | Значение |
---|---|
Свариваемость | Ограниченная свариваемость. Методы сварки: РДС, АДС под флюсом и газовой защитой, АРДС, ЭШС. Рекомендуется нагрев и последующая термообработка ССС без ограничений. |
Склонность к отпускной хрупкости | Наклонный. |
Температура ковки | Начало – 1240°С, конец – 800°С. Сечения до 50 мм охлаждают в штабелях на воздухе, 51-100 мм – в ящиках. |
Чувствительность к флоку | Чувствительный. |
Обрабатываемость | В горячекатаном состоянии на воздуходувке НВ 207-217 SB=710 МПа Kn тв.узд.=0,85 Kn b.ст.=0,75. |
Макроструктура и загрязнение | Макроструктура стали при испытаниях на разрыв в продольном направлении и поперечном направлении, отобранная из проката, не должна иметь усадки, пористости, пузырей, трещин, расслоений, включений и дефектов разрушения, перечисленных в приложении 3 ГОСТ 10243.![]() |
Закаленные и упрочняемые металлы, пригодные для изготовления доспехов
Закаленные и упрочняемые металлы, пригодные для изготовления доспехов [Вернуться к Главная страница брони]Закаленные и упрочняемые металлы, пригодные для изготовления доспехов
Последнее изменение: 22 октября 2020 г.
Общие примечания
Примечания относительно пластичности, необходимой для брони
Одно из эмпирических правил, которое я разработал, касается того, насколько пластичной должна быть сталь, используемая для спортивной брони полного контакта. По моему мнению, абсолютный минимум измеренного в лаборатории удлинения на разрыв для материала при термообработке, которую вы используете, должен составлять 10%. Основываясь на результатах, полученных с 4130 и нержавеющей сталью 17-7ph, я бы рекомендовал 11,5% для тела и 13% для шлемов.
Краткий справочник по пределу текучести и пластичности:
Мягкая сталь 29ksi /39% EBB
304 Нестандартная сталь 42Ksi /55% EBB
1050 Carbon Steel / C50 / ST50 AT RC39 ~ 150Ksi / rebb
4130/13729 ~ 150Ksi / rebb
4130 /1301301301301301301301303 4130313031303132. 208Ksi / 11,5% EBB
65G / GOST 65 (Россия / Украина) ~ 155KSI /? / 12% EBB
17-7ph Нержавеющая сталь (США) 150ksi / ??% EBB
Full Hard 301 Нержавеющая сталь 140ksi / 9% минимум EBB
17-4ph Нерж. / 14% EBB (227ksi с поправкой на плотность)
Титан – класс 2 / “Чистый титан” (США) 49ksi / 28% EBB (85ksi с поправкой на плотность)
Титан – OT-4 (Россия/Украина) 99ksi / 18% EBB (171ksi с поправкой на плотность)
EBB = Удлинение перед разрывом
~ = Я предполагаю предел текучести на основе наиболее похожего материала, для которого я могу найти паспорт материала.
Типы броневого металла, широко доступные в США
Мягкая сталь
304 Нержавеющая сталь
1050 Углеродистая сталь (закаливаемая)
4130 (Легированная / закаливаемая)
410ph Нержавеющая сталь (0903) 9 Закаливаемый)
Полностью твердый Нержавеющая сталь 301 (предварительно закаленный)
Нержавеющая сталь 17-4ph (закаливаемый)
Титан – Сорт 5 / 6Ал-4В
Титан – Сорт 2 / «Чистый титан»
Типы броневого металла, распространенные в Украине/России
Мягкая сталь
420 Нержавеющая сталь (закаливаемая)
ST50 (0,50% Нержавеющая сталь / закаливаемая)
65G (0,65% углеродистой стали / закаливаемая)
30HGSA (легированная сталь / закаливаемая)
Типы броневого металла, обычно доступные в Индии
Мягкая сталь
)
Предварительно закаленная нержавеющая сталь 202
EN9 (0,50% углеродистой стали / закаливаемая)
Основные металлы
Мягкая сталь / 1008
устойчивостью и очень низким пределом текучести. Предел текучести 2% составляет 29 тысяч фунтов на квадратный дюйм с относительным удлинением до разрыва 39%.
Нержавеющая сталь 304 / (EN) X2CrNiN18-7
Обладает высокой степенью коррозионной стойкости и пределом текучести примерно на 1/3 выше, чем у низкоуглеродистой стали. Сопротивление вмятинам обычно считается сопротивлением мягкой стали, в 1,33 раза превышающей ее толщину, или примерно двумя калибрами листового металла.
Предел текучести 2 % составляет 42 тысяч фунтов на квадратный дюйм с относительным удлинением до разрыва.
55%.
Закаливаемые стали
1050 Углеродистая сталь / C50 / ST50
В отожженном состоянии ей можно придать форму, аналогичную мягкой стали. Он подвергается термообработке путем нагревания до 1652F / 900C и закалки в воде или масле с последующим отпуском в течение 1 часа. При закалке в воде и отпуске до 752F / 400C твердость составляет Rc37. Его устойчивость к вмятинам примерно в 2,5 раза больше, чем у нержавеющей стали 304.
EN9 / 1055 Углеродистая сталь
EN9 – это обычная углеродистая сталь, обычно доступная в Индии. В отожженном состоянии он может иметь форму, очень похожую на мягкую сталь. Он подвергается термообработке путем нагревания до 1652F / 900C и закалки в воде или масле с последующим отпуском в течение 1 часа. При закалке в воде и отпуске до 842F / 450C твердость составляет Rc38. Его устойчивость к вмятинам примерно в 2,5 раза больше, чем у нержавеющей стали 304.
Я НЕ рекомендую закалку 10XX выше Rc40.
4130 / (EN) 25CrMo4
На мой взгляд, 4130 является лучшим материалом для брони SCA, BotN и ACL во всех областях, кроме устойчивости к ржавчине. Процесс термообработки с углеродистой сталью 4130 гораздо более щадящий, чем с углеродистой сталью 1050. Предел текучести и пластичность лучше при более высокой твердости, чем у стали 1050.
В настоящее время в США легче купить в небольших количествах сталь 4130, чем сталь 1050. Присадочная проволока доступна для стали марки 4130, но не для марки 1050. 4130 это Rc52, для 1050 это Rc62. Результатом этого является то, что случайное падение или удар по незакаленной пластине 4130 с гораздо меньшей вероятностью приведет к ее растрескиванию. Температуры отпуска, подходящие для брони, намного ниже, чем для углеродистой стали 1050. В результате для закалки 4130 пластин можно использовать кухонную печь с хорошим регулятором температуры.
Чтобы закалить 4130, нагрейте его до 1650–1700F в зависимости от того, сколько времени вам потребуется, чтобы поместить его в закалочную ванну после того, как вы откроете дверцу печи и закалите его в воде. При закалке при 400F в течение 30 минут кажется, что он устойчив к вмятинам так же, как нержавеющая сталь 304, толщина которой в 2,8–3 раза больше. В технических характеристиках нержавеющей стали 4130 указан предел текучести 2% при этом отпуске как 220ksi с относительным удлинением до разрыва 10%. При отпуске до 500°F в течение 30 минут предел текучести 2% при этом отпуске составляет 208ksi с удлинением до разрыва 11,5%. При отпуске до 600F в течение 30 минут предел текучести 2% при этом отпуске равен 19.5ksi с удлинением до разрыва 13%.
Для ACL-брони, кроме шлемов, я рекомендую закалку 500F / Rc48. Для шлемов я рекомендую закалку 600F/RC45. Если вы используете печь для закалки, которая нагревается только до 550F, это должно быть хорошо.
65Г / ГОСТ 65 (Россия/Украина)
Я получил достаточное количество незакаленной российской стали 65Г (1065) толщиной 0,8 мм. Глядя на то, что 0,65% углерода содержат масло, а не воду, вероятно, будет лучшим выбором для закалочной среды, но не для других сталей, с которыми я обычно работаю, для закалки в масле. Я предпочитаю использовать водяную закалку, потому что она у меня была под рукой. Критическая температура закалки для этого вида прямой углеродистой стали должна быть около 800°С. Чтобы быть уверенным, что тонкие детали достигли полной твердости, я установил печь на 900C для учета охлаждения деталей между моментом открытия дверцы печи и погружением деталей в закалочную воду.
После закалки деталей в воде твердость измерена в диапазоне Rc57-58. Отпуск в течение 30 минут при 350°С дал твердость Rc49, при 400°С – твердость Rc43, а при 450°С – твердость Rc37. При фиксации основы в большом количестве бригантиновых пластин я заметил, что 65G при твердости Rc43 гораздо более хрупкий, чем 1050 при той же твердости. Если закаленные пластины требуют значительного изменения формы, то растрескивание вокруг слабых мест представляет собой серьезную проблему. Даже при твердости Rc37 65G был намного более хрупким, чем 1050 при твердости Rc43, и намного более хрупким, чем 4130 при твердости Rc48.
Я рекомендую использовать 1-часовой отпуск при 450°C для получения твердости Rc37 для стали 65G. Я бы не рекомендовал закалку 65G проходить твердость Rc37.
30ХГСА / 30ХГСА (Россия/Украина)
Этот сплав аналогичен сплаву 4130, за исключением того, что он не содержит молибдена. Большая часть изложенной ниже информации основана на переводе научно-исследовательской работы по этой легированной стали «Влияние отпуска на фактурную вязкость стали 30ХГСА» Т. М. Головинская и Н.И. Черняк опубликовано в Киеве, Украина, в “Пробелмы Прочности” 16, 19 сентября.74.
Рекомендуемая термическая обработка заключается в нагревании стали до 880°C и закалке в масле. Лично я обнаружил, что в зависимости от того, насколько тонка сталь или как быстро она закаливается после открытия печи, может потребоваться нагреть ее до 900°C или даже 920°C для достижения полной твердости. Часовой отпуск при температуре 340°C должен привести к пределу текучести 192ksi / 1324MPa. Я обнаружил, что сталь, подвергнутая термообработке этим процессом, имеет твердость Rc43.
При сравнении 30ХГСА с титаном ОТ-4, обычно используемым в бронетехнике в России и Украине, 30ХГСА равен 9На 4% прочнее по объему и на 12% прочнее по весу. Обратите внимание, что под прочным я подразумеваю предел текучести, который является хорошей мерой того, насколько хорошо металл будет сопротивляться вмятинам. При этом не учитывается, насколько металл изгибается при ударе оружием. Выбирая толщину легированной стали для использования в доспехах, вы должны иметь в виду, что даже если броня не повреждена, если владелец ранен, она все равно выйдет из строя.
Я рекомендую использовать 1-часовой отпуск при 340°C для получения твердости Rc43 для легированной стали 30HGSA.
Закаливаемые нержавеющие стали
Нержавеющая сталь 410
Коррозионная стойкость намного ниже, чем у нержавеющей стали 304, но намного лучше, чем у мягкой стали или пружинной стали 1050. В отожженном состоянии предел текучести такой же, как у нержавеющей стали 304, но пластичность составляет примерно половину от пластичности нержавеющей стали 304.
При нагреве до 1850°F и закалке на воздухе, а затем отпуске до 400°F в течение 2 часов кажется, что он устойчив к вмятинам так же, как нержавеющая сталь 304, толщина которой в 2,3 раза больше. В листах данных для нержавеющей стали 410 указан предел текучести 2% при этом отпуске как 156 тысяч фунтов на квадратный дюйм с удлинением до разрыва 12%.
Я рассматриваю этот материал как компромисс между пружинной сталью 1050 и нержавеющей сталью 304. Вы получаете некоторую коррозионную стойкость нержавеющей стали 304 и некоторую устойчивость к вмятинам пружинной стали 1050.
ЭТО ОЧЕНЬ ВАЖНО: если вы не отпустили нержавеющую сталь 410 достаточно долго после закалки в воде, она может стать очень хрупкой, но при этом иметь нормальную твердость, я НЕ рекомендую закалку в воде, это только увеличивает напряжение, которое вы Потребуется облегчение на этапе закалки. Воздушная закалка безопаснее и проще. Я не уверен, есть ли смысл закаливать пластины в масле, поскольку закалка на воздухе работает очень хорошо и обеспечивает полную твердость пластин.
Нержавеющая сталь 420A
Это более углеродистая версия нержавеющей стали 410 с содержанием углерода 0,15–0,25 %. Этот материал, кажется, легко доступен в Украине и России, но в США он доступен только в том случае, если вы покупаете грузовик за один раз.
Исходя из спецификаций для этого материала, кажется, что предел текучести составляет 190-195 тысяч фунтов на квадратный дюйм при относительном удлинении до разрыва не менее 12%. На бумаге это МОЖЕТ быть хорошим выбором для брони. Некоторые из проблем заключаются в том, что она по-прежнему будет иметь плохую стойкость к ржавчине для чего-то, что классифицируется как нержавеющая сталь, как в случае с нержавеющей сталью 410, это сталь с «воздушной закалкой», поэтому горячая обработка или сварка проблематичны. Еще одна большая проблема в США заключается в том, что большая часть листового металла, продаваемого как нержавеющая сталь 420, на самом деле представляет собой 420B, 420C или 420HC, каждая из которых содержит слишком много углерода для использования в производстве брони.
Нержавеющая сталь 17-7ph (США)
Коррозионная стойкость на уровне нержавеющей стали 301 и близка к нержавеющей стали 304. В отожженном состоянии / состоянии А предел текучести несколько ниже, чем у нержавеющей стали 304, а пластичность несколько ниже, чем у нержавеющей стали 304. По сравнению с отожженной нержавеющей сталью 410 нержавеющая сталь 17-7ph легче поддается холодной штамповке. Благодаря термообработке Th2100 он устойчив к вмятинам так же, как и нержавеющая сталь 304, в 2,2 раза толще.
Согласно паспорту материала, предел текучести нержавеющей стали 17-7ph в состоянии термообработки RH950 на 18% выше, чем в состоянии Th2050. Однако процесс термообработки для состояния RH950 является гораздо более техническим, трудоемким и дорогостоящим. На примере партии испытательных пластин из нержавеющей стали 17-7ph, подвергнутых термообработке до состояния RH950, я заметил заметное увеличение хрупкости, но не заметил большой разницы в стойкости к вмятинам. Обратите внимание, что я измерил твердость тестовых пластин, чтобы убедиться, что процесс термообработки был выполнен правильно. Для брони я теперь рекомендую термообработку Th2100. Я видел достаточно отказов брони из нержавеющей стали 17-7ph, термообработанной до Th2050, чтобы оправдать это изменение.
Обратите внимание, что для термообработки нержавеющей стали 17-7ph необходима электрическая печь с автоматическим регулятором температуры. Кроме того, из-за длительности процесса термообработки нержавеющая сталь 17-7ph намного дороже подвергать промышленной термообработке, чем нержавеющую сталь 1050, 4130 или 410. Стоимость листового металла из нержавеющей стали 17-7ph также намного выше, чем из нержавеющей стали 1050, 4130 или 410.
Высокопрочные или предварительно закаленные металлы
Полностью твердая нержавеющая сталь 301
Коррозионная стойкость близка к коррозионной стойкости нержавеющей стали 304. Этот материал трудно поддается формованию, поэтому он подходит только для деталей, которые имеют только простую кривую или умеренную сложную кривую. Сопротивление вмятинам похоже на сопротивление нержавеющей стали 304 в 1,8-2 раза больше ее толщины.
Нержавеющая сталь 202, закаленная до HRC40
Нержавеющая сталь 201/202 — более дешевый вариант нержавеющей стали 301/302. Закаленная сталь 202 обычно доступна в Индии, где закаленная нержавеющая сталь 301/302 обычно недоступна. Коррозионная стойкость близка к нержавеющей стали 304. Этот материал трудно поддается формованию, поэтому он подходит только для деталей, которые имеют только простую кривую или умеренную сложную кривую. Сопротивление вмятинам похоже на сопротивление нержавеющей стали 304 в 1,8-2 раза больше ее толщины.
Этот материал закаляют на сталелитейном заводе, пропуская его через холодный прокатный стан, пока он не затвердеет до Rc40. Я не рекомендую использовать нержавеющую сталь 202, которая была закалена выше, чем HRC42. Если этот материал подвергается горячей обработке, он возвращается в свое отожженное состояние и не может быть повторно закален.
Нержавеющая сталь 17-4ph
Коррозионная стойкость близка к коррозионной стойкости нержавеющей стали 304. Этот материал очень трудно поддается формованию, поэтому он подходит только для деталей, которые имеют только простую кривую или небольшую сложную кривую. Этот материал должен быть подвергнут термообработке перед формованием. Термическая обработка до h2150 лишь незначительно повышает предел текучести, но увеличивает пластичность с 5% до разрыва до 11%.
301 из полностью твердой нержавеющей стали примерно вдвое дешевле, когда я проверял. Предел текучести нержавеющей стали 17-4ph при достаточно пластичной термообработке для брони очень близок к пределу текучести полностью твердой нержавеющей стали 301. Нержавеющая сталь 17-4ph требует термообработки, а полностью твердая нержавеющая сталь 301 – нет. Я не вижу веских причин выбирать нержавеющую сталь 17-4ph вместо полностью твердой нержавеющей стали 301.
Титан – класс 5/6Al-4V (США)
Этот материал не ржавеет. Предел текучести на единицу объема составляет 128 тыс. фунтов на кв. дюйм / 880 МПа, а плотность — 4,43 г/куб. см / 0,160 фунта/дюйм³. Плотность легированной стали 4130 составляет 7,85 г/куб.см / 0,284 фунта/дюйм³, поэтому она в 1,775 раза тяжелее по объему. Если вы умножите 1,775 на предел текучести 128 тысяч фунтов на квадратный дюйм, чтобы получить представление о соотношении прочности к весу по сравнению с легированной сталью 4130, получится 227 тысяч фунтов на квадратный дюйм / 1565 МПа, что равно 9.% больше, чем 208ksi / 1434MPa. Удлинение перед разрывом составляет 14%.
Титан – класс 2 / «Чистый титан» (США)
Материал не ржавеет. Предел текучести на единицу объема составляет 49 тыс. фунтов на кв. дюйм / 340 МПа, а плотность — 4,51 г/куб. см / 0,163 фунта/дюйм³. Плотность легированной стали 4130 составляет 7,85 г/куб. см / 0,284 фунта/дюйм³, поэтому она в 1,742 раза тяжелее по объему. Если вы умножите 1,742 на предел текучести 49 тысяч фунтов на квадратный дюйм, чтобы получить представление о прочности по отношению к весу по сравнению с легированной сталью 4130, получится 85 тысяч фунтов на квадратный дюйм / 586 МПа, что на 41% меньше, чем 208 тысяч фунтов на квадратный дюйм / 1434 МПа. Удлинение до разрыва составляет 28%.
Титан – ОТ-4 (Россия/Украина)
Материал не ржавеет. Предел текучести на единицу объема составляет 99 тыс. фунтов на кв. дюйм / 685 МПа, а плотность — 4,51 г/куб. см / 0,164 фунта/дюйм³. Плотность легированной стали 4130 составляет 7,85 г/куб. см / 0,284 фунта/дюйм³, поэтому она в 1,732 раза тяжелее по объему. Если вы умножите 1,732 на предел текучести 99 тысяч фунтов на квадратный дюйм, чтобы получить представление о прочности по отношению к весу по сравнению с легированной сталью 4130, получится 171 тысяч фунтов на квадратный дюйм / 1179 МПа, что на 18% меньше, чем 208 тысяч фунтов на квадратный дюйм / 1434 МПа.
[Вернуться на главную страницу брони]
Copyright 2014 Крейг В. Надлер Все права защищены
Влияние способа газовой защиты при сварке плавящимся электродом на теплораспределение в свариваемом изделии
[1]
В. В. Фролов, Теория сварочных процессов, Высшая школа, Москва, (1988).
[2] К.В. Багрянский, З.А. Добротина, К.К. Хренов, Теория сварочных процессов, Вища школа, Киев, (1976).
[3] Н.Н. Рыкалин, Расчеты тепловых процессов при сварке, Машгиз, Москва, (1951).
[4]
Б.М. Березовский, Математические модели дуговой сварки, Основы тепловых процессов в сварных узлах, Южно-Уральский государственный университет, Челябинск, (2006).
[5] М.Х. Шоршоров, Металлургия сварки сталей и титановых сплавов, Наука, Москва, (1965).
[6] Л.С. Лившиц, А.Н. Хакимов, Металлургия сварки и термическая обработка сварных соединений, Машиностроение, Москва (1989).
[7] Ю.М. Лахтин, Металлургия и термическая обработка металлов, Металлургия, Москва, (1983).
[8]
Сварка и свариваемые материалы, Сварочные характеристики материалов, Металлургия, Москва, (1991).
[9] Потапьевский А.Г. Сварка плавящимся электродом в газовой среде. М.: Машиностроение, 1974.
[10] В.А. Ленивкин, Н.Г. Дюргеров, Х.Н. Сагиров, Технологические свойства сварочной дуги в условиях газовой защиты, Машиностроение, Москва, (1989).
[11] В.П. Столбов, Сварочная ванна., Тольяттинский ТГУ, (2007).
[12]
Д. А. Чинахов, Газодинамический контроль свойств сварных соединений из высокопрочных легированных сталей, China Welding, 23(3) (2014) 27-31.
[13] Ю.М. Лахтин, В.П. Леонтьева, Материаловедение: Учебник для втузов, Машиностроение, Москва (1990).
[14] Д.А. Чинахов, А.В. Зуев, А.Г. Филимоненко, Газодинамическое воздействие струи защитного газа на перенос капли при сварке плавящимся электродом, Перспективные исследования материалов, 1040 (2014) 850-853.
DOI: 10.4028/www. scientific.net/amr.1040.850
[15] Д.А. Чинахов, Э.Д. Чинахова, Ю.М. Готовщик, С.В. Гричин, Влияние сварки с двухструйной газовой защитой на формирование сварного соединения, Конф. Серия: Материаловедение и инженерия, 125 (2016) 012013.
DOI: 10.1088/1757-899x/125/1/012013
[16] Д.А. Чинахов, Исследование термического цикла и скорости охлаждения однопроходных сварных соединений стали 30ХГСА, Прикладная механика и материалы, 52-54 (2011) 442-447.
DOI: 10.4028/www.scientific.net/amm.52-54.442
[17]
М. Х. Шоршоров, В.В. Белов, Фазовые превращения и изменение свойств стали при сварке, Атлас, Наука, (1977).
|
Особенности ремонтной сварки элементов силового гидроцилиндра
- УЖМЭМС
- Все тома и выпуски
- Том 6, номер 2, 2020 г.
- Особенности ремонтной сварки элементов силового гидроцилиндра
УЖМЭМС.
Том 6, номер 2
: 43-52
https://doi.org/10.23939/ujmems2020.02.043
Получено: 18 марта 2020 г.
Пересмотрено: 22 апреля 2020 г.
Принято: 30 сентября 2020 г.
Авторы:
- Андрей Дзюбик
- Игорь Назар
- Дзюбик Людмила
1
Национальный университет «Львовская политехника»
2
Национальный университет «Львовская политехника»
3
Национальный университет «Львовская политехника»
В настоящее время использование силовых гидроцилиндров является неотъемлемой частью большинства промышленного оборудования. Они обеспечивают поступательные и горизонтальные перемещения, замену товаров, фиксацию и т. д. Эти устройства являются необходимыми элементами оборудования, где применяется приложение соответствующего уровня усилия. Часто гидроцилиндры создаются специализированными для выполнения определенных видов работ. Следует отметить, что часть элементов силового цилиндра при изготовлении совмещается со сваркой. Такие цельные соединения обеспечивают жесткость монтажа, герметичность конструкции, усталостную прочность при многоцикловых нагрузках.
Сложные условия эксплуатации, значительные нагрузки, наличие различных внешних факторов часто приводят к разрушению отдельных элементов цилиндра. При этом стоимость ремонта оборудования, предполагающего замену на новые силовые приборы, достаточно высока. Это обуславливает выполнение ремонтно-восстановительных работ, проводимых на специализированных предприятиях. Однако в случае ремонта часто возникает ряд проблем, требующих оперативного решения в производственных условиях. К ним следует отнести обеспечение основных материалов с близкими физико-химическими свойствами, установление режимов сварки, подбор необходимых сварочных материалов, применение соответствующих приемов ведения дугового процесса и т. д. Поэтому ремонтируемая сварная конструкция корпуса силового гидроцилиндра нуждается в дополнительной проработке на предмет свариваемости отдельных элементов между собой, образования зоны термодеформационного воздействия. В целом отремонтированный гидроцилиндр должен соответствовать требованиям эксплуатации установки в зависимости от назначения.
Конструкция рассматриваемого гидроцилиндра прессовой установки является достаточно технологичной с точки зрения обеспечения автоматизации сварочного процесса. Он содержит длинные сварные швы простой кольцевой конфигурации. В то же время значительные линейные размеры и наличие цилиндрической поверхности обусловливают некоторую сложность реализации процессов. Материалом конструкции силового гидроцилиндра являются малоуглеродистые низколегированные стали. Анализ технологической свариваемости свидетельствует о склонности к образованию трещин вследствие термического цикла сварки.
В работе выполнено моделирование сварных швов силового гидроцилиндра. Количество роликов учитывалось при получении стыковых швов. Проведен сравнительный анализ различных электродных материалов с различными системами легирования. Определены наиболее применимые сварочные материалы по химическому составу и свойствам металла шва.
По литературным данным и результатам сравнительного анализа установлен оптимальный диапазон скорости охлаждения основного материала гидроцилиндра. Исследованы свойства и структура зоны термического влияния стыковых швов силового гидроцилиндра.
Исследована величина деформаций и напряжений, вызванных термическим циклом сварки оболочечной конструкции гильзы гидроцилиндра. Определены допустимые параметры зоны пластических деформаций при стыковой сварке.
силовой гидроцилиндр
режимы сварки
деформации гильзы гидроцилиндра
сварочные электродные проволоки
ремонт гидроцилиндра
[1] Федорец В. О. и др., Гидроприводы та гидропневмоавтоматика . Киев, Украина: Выща школа, 1995. [на украинском языке].
[2] Назар И.Б., Дзюбик А.Р., Войтович А.А. Дрогобыч, Украина: Посвит, 2020. [на украинском языке].
[3] Палаш В.М., Дзюбык А.Р., Хомыч И.Б. Федык В., “Особенности сварности стали 30ХГСА”, Научный вестник УНФУ , том 27, вып. 9, с. 68–72, 2017. [на украинском языке]. https://doi.org/10.15421/40270915
[4] Дзюбик А. и др., «Комплексный подход к подготовке специалистов в области инженерного образования», Украинский журнал машиностроения и материаловедения , vol. . 6, нет. 2020. Т. 1. С. 39–46. https://doi.org/10.23939/ujmems2020.01.039
. в гражданском строительстве] . Дрогобыч, Украина: Посвит, 2018. [на укр. языке].
[6] В. М. Палаш, Металлознавчи аспекты сварности зализовухлецевых сплавов . – Львов, Украина: Издательство KINPATRI LTD, 2003. [на укр. языке].
[7] М.Х. Шоршоров, В. В. Белов, Фазовые преобразования и изменения свойств стали при сварке . Атлас [Фазовые превращения и изменение свойств стали при сварке. Атлас] . Москва, Россия: Наука, 1972.
[8] В. Н. Волченко и др., Теория сварочных процессов [Теория сварочных процессов] . Москва, Россия: Высшая школа, 1988.
[9] А. Р. Дзюбик, В. М. Палаш, В. И. Панкив, “Повышение эффективности сваривания стыков труб”, Научный Вестник Львовского политехнического национального университета , нет. 702, стр. 88–9.1, 2011. [на украинском языке].
[10] Дзюбик А., Палаш В., Хомыч И., Гринус С. Оптимизация режимов сварки высокопрочной низколегированной стали Domex 700 // Украинский журнал машиностроения и материаловедения. 3, нет. 2017. Т. 2. С. 47–54. », Материаловедение , вып. 56, стр. 203–209., 2020. https://doi.org/10.1007/s11003-020-00416-y
[12] Технология электрической сварки плавлением , Б.Е. Патон, Эд. Москва, Россия: Машиностроение, 1977.
[13] Дзюбик А.Р., Назар И.Б., Палаш Р.В., Повышение эффективности сварки магистральных трубопроводов при их эксплуатации и ремонте . Львов, Украина: Сполом, 2013. [на украинском языке].
[14] Б. С. Касаткин, В. М. Прохоренко, Ю. М. Чертов, Напряжения и деформации при сварке [Сварочные напряжения и деформации] . – Киев, Украина: Выща школа, 1987.
[15] Р. М. Кушнир, М. М. Николишин, В. А. Осадчук, Пружный та пружинно-пластический гарантийный стан оболонок с дефектами. Львов, Украина: Сполом, 2003. [на украинском языке].
[16] Дзюбик А. и др. «Обеспечение технологической прочности сварных стыков обсадных труб», Автоматизация производных процессов у машин2. 50. С. 94–102, 2016. [на украинском языке].
[17] Справочник сварщика , В. В. Степанов, Под ред. Москва, Россия: Машиностроение, 1982.
[18] ЭСАБ «Сварочные материалы». Проволока для сварки MIG/MAG. [Онлайн]. Режим доступа: https://www. esab.ru/ru/ru/products/filler-metals/mig-mag-wires-gmaw/inde…. Дата обращения: 30 сентября 2020 г.
А. Дзюбик, И. Назар, Л. Дзюбик, “Особенности ремонтной сварки элементов силовых гидроцилиндров”, Украинский журнал машиностроения и материаловедения, вып. 6, нет. 2, стр. 43-52, 2020.
СТРОИТЕЛЬСТВО И ОБЩАЯ ПРОМЫШЛЕННОСТЬ… ГОСТ 4543 30ХГСА 8-200 1,500-3,200 6,000-12,200 Толстый прокат конструкционный легированный специального назначения ГОСТ 11269 30ХГСА 6-40 Низколегированный
СТРОИТЕЛЬСТВО И ПРОМЫШЛЕННОСТЬ
1 Тарелки
СТРОИТЕЛЬСТВО И ОБЩАЯ ПРОМЫШЛЕННОСТЬ СТРОИТЕЛЬСТВО И ОБЩАЯ ПРОМЫШЛЕННОСТЬ
Тарелки2 3Плиты
СОДЕРЖАНИЕ
СТРОИТЕЛЬСТВО И ОБЩАЯ ПРОМЫШЛЕННОСТЬ Производство Метинвеста в Европе
Европейские стандарты
американские стандарты
Производство Метинвеста в Украине
Европейские стандарты
американские стандарты
Стандарты Украины и СНГ
Прочие стандарты
СОСУДА ПОД ДАВЛЕНИЕМ Производство Метинвеста в Европе
Европейские стандарты
американские стандарты
Производство Метинвеста в Украине
Европейские стандарты
американские стандарты
Стандарты Украины и СНГ
МАШИНОСТРОЕНИЕ Производство Метинвеста в Европе
Европейские стандарты
Производство Метинвеста в Украине
Европейские стандарты
американские стандарты
Стандарты Украины и СНГ
5
5
6
7
8
9
10
11
12
13
13
14
15
15
15
16
16
17
17
18
19
19
20
20
21
23
ТРУБОПРОВОДЫ, ОФФШОРНЫЕ И ЭНЕРГЕТИЧЕСКИЕ Производство Метинвеста в Европе
Европейские стандарты
американские стандарты
Производство Метинвеста в Украине
Европейские стандарты
американские стандарты
Стандарты Украины и СНГ
СУДОСТРОЕНИЕ Производство Метинвеста в Европе
американские стандарты
Судовые регистры
Производство Метинвеста в Украине
американские стандарты
Стандарты Украины и СНГ
Судовые регистры
КОНТАКТЫ
FERRIERA VALSIDER Spartan UK АЗОВСТАЛЬ
ТРАМЕТАЛ ИЛЬИЧ СТАЛЬ
400 000 220 000 2 100 000
600 000 2 400 000
Производство плит Годовая мощность, т
СТРОИТЕЛЬСТВО И ОБЩАЯ ПРОМЫШЛЕННОСТЬ СТРОИТЕЛЬСТВО И ОБЩАЯ ПРОМЫШЛЕННОСТЬ
Тарелки4 5Плиты
Товар Стандарт Марка стали Толщина, мм Ширина, мм Длина, мм Вес, т
Углерод конструкционные стали
АСТМ А36/ А36М А36/ А36М
4-150
1 500–3 150 4 000–25 000
30 макс.
Пластины из углеродистой стали для общего применения
АСТМ А283/ А283М С, Д
Высокопрочный низколегированная конструкционная стали
АСТМ А572/А572М
50 4-100 20 макс.
55 5-50
14 макс. 60 8-32
Конструкционный углерод стальные пластины из улучшенная прочность
АСТМ А573/ А573М 58, 65, 70 4-40
Высокопрочный низколегированная конструкционная стали
АСТМ А588/ А588М А, В 4-80 16 макс.
Нормализованный высокий- прочность низколегированная пластины из конструкционной стали
АСТМ А633/ А633М
А, В, Д 4-100
20 максЕ 8-100
Углерод и высокопрочный низколегированная конструкционная стали для мостов
АСТМ А709/ А709М
50 тип 1, тип 2 4-100
50 Вт тип A, тип B 5-80 16 макс.
Производство Метинвеста в Европе
Европейские стандарты
Товар Стандарт Марка стали Толщина, мм Ширина, мм Длина, мм Вес, т
Нелегированные конструкционные стали EN 10025-2
С185
4-180
1 500–3 150 4 000–25 000
35 макс.
С235ДЖР, S235J0, S235J2
С275ДЖР, С275ДЖ0, С275ДЖ2
С355ДЖР, С355ДЖ0, С355ДЖ2, С355К2
Е295
Нормализованный катаный мелкозернистый конструкционные стали
ЕН 10025-3
С275Н
4-150 30 макс. S275NL
С355Н
С355НЛ
С420Н, С420НЛ 8-100
20 макс. С460Н, С460НЛ
Стали конструкционные с улучшенный атмосферный устойчивость к коррозии
EN 10025-5 S355J0W, S355J2W, S355K2W 5-100
Размеры, технические требования и вес плоского проката согласовываются при заключении договоров.
HUDSON YARDS – САРАЙ Нью-Йорк, США
Культурный центр в Hudson Yards, крупнейшая частная недвижимость развития в США. Его восьмиуровневое базовое здание имеет несколько архитектурных особенностей, в том числе театр на 500 мест. и знаковая подвижная часть. Используемая сталь Метинвеста: толстолистовой горячекатаный прокат.
американские стандарты
Размеры, технические требования и вес плоского проката согласовываются при заключении договоров.
СТРОИТЕЛЬСТВО И ОБЩАЯ ПРОМЫШЛЕННОСТЬ СТРОИТЕЛЬСТВО И ОБЩАЯ ПРОМЫШЛЕННОСТЬ
Тарелки6 7 Тарелки
Производство Метинвеста в Украине
Европейские стандарты
Товар Стандарт Марка стали Толщина, мм Ширина, мм Длина, мм Вес, т
Нелегированные конструкционные стали EN 10025-2
С235ДЖР, S235J0, S235J2
6-200
1 500–3 200 6 000–12 500 12,3 макс.
С275ДЖР, С275ДЖ0, С275ДЖ2
С355ДЖР, С355ДЖ0, С355ДЖ2, С355К2
Нормализованный катаный мелкозернистый конструкционные стали
ЕН 10025-3
С275Н, С275НЛ 6-200
С355Н, С355НЛ
С420Н, С420НЛ 6-100
С460Н, С460НЛ
Термомеханически катаный мелкозернистый конструкционные стали
ЕН 10025-4
С275М, С275МЛ
6-50 С355М, С355МЛ
С420М, С420МЛ
С460М, С460МЛ
Стали конструкционные с улучшенный атмосферный устойчивость к коррозии
ЕН 10025-5
С235ДЖ0В, S235J2W
6-130S355J0W, S355J2W, S355K2W
Мелкозернистая структурная стали, закаленные и закаленный
ЕН 10025-6
С690К, S690QL, S690QL1
8-100
С890К 8-25
Нелегированные конструкционные стали
ЕН 10025 + А1:1993
С235ДЖР, S235JRG1, S235JRG2, S235J0, С235ДЖ2Г3,
С235ДЖ2Г4
6-200
С275ДЖР, S275JRG1, S275JRG2, S275J0, С275ДЖ2Г3, S275J2G4
С355ДЖР, S355JRG2, S355J0, С355ДЖ2Г3, С355ДЖ2Г4, С355К2Г3, С355К2Г4
Стали конструкционные для общее применение DIN 17100
ул 33, Ст 37-2, Ст 37-3, РСт 37-2, УСт 37-2, Ст 44-2, Ст 44-3, Ст 52-3
6-200
Размеры, технические требования и вес плоского проката согласовываются при заключении договоров.
Для плит толщиной 135-200 мм механические свойства согласовываются при заключении договора.
Производство Метинвеста в Украине
американские стандарты
Товар Стандарт Марка стали Толщина, мм Ширина, мм Длина, мм Вес, т
Углерод конструкционные стали
АСТМ А36/А36М А36/А36М 6-200
1 500–3 200 6 000–12 500 12,3 макс.
АСМЭ СА36/ СА36М СА36
Пластины из углеродистой стали для общего применения
ASTM A283/ A283M A, B, C, D 6-200
АСМЭ СА283/ 283М Д
Закаленный и закаленный пластины из легированной стали
АСТМ А514/А514М
Б 8-31.8
Ф 8-65
Н 8-50,8
Вопрос 8-152.4
Высокопрочный низколегированный конструкционные стали
АСТМ А572/А572М
42 6-150
50 6-100
55 6-50
60 6-32
65 6-32
Структурные пластины из углеродистой стали повышенной прочности
ASTM A573/ A573M 58, 65, 70 6-40
Высокопрочный низколегированный конструкционная сталь
АСТМ А588/А588М А, Б 6-200
К 6–50 1 500–2 700 6 000–12 500 9,4 макс.
Нормированный высоко- прочность низколегированная пластины из конструкционной стали
АСТМ А633/ А633М А 8-50
1 500-3 200
6000-12200
12,3 макс.
Углерод и высокопрочный низколегированная конструкционная сталь для мостов
ASTM A709/ A709M 36, 50, 50 Вт 6–100 6 000–12 500
Лист из углеродистой стали, предоставлено химическому сочинение требования
ASTM A830/ A830M 1045 8–200 6 000–12 200
Размеры, технические требования и вес плоского проката согласовываются при заключении договоров. Для плит толщиной 135-200 мм механические свойства согласовываются при заключении договора.
СТРОИТЕЛЬСТВО И ОБЩАЯ ПРОМЫШЛЕННОСТЬ СТРОИТЕЛЬСТВО И ОБЩАЯ ПРОМЫШЛЕННОСТЬ
Тарелки8 9Тарелки
Производство Метинвеста в Украине
Стандарты Украины и СНГ
Товар Стандарт Марка стали Толщина, мм Ширина, мм Длина, мм Вес, т
Углеродистая сталь прокатные плиты
ДСТУ 8803/ ГОСТ 14637
Ст2пс, Ст2сп, Ст3пс, Ст3сп, Ст3Гпс, Ст3Гсп, Ст4пс, Ст4сп, Ст5пс, Ст5сп, Ст5Гпс
6-200 1500-3200 6000-12500
12,3 макс.
Конструкционная сталь толстолистовой прокат ГОСТ 1577
08, 10, 15, 20, 25, 30, 35, 40, 45, 50, 65Г, 20ч, 40ч
Стальной прокат с повышенная прочность
ДСТУ 8541/ ГОСТ 19281
09Г2С, 09Г2СД, 09Г2Д, 10Г2С, 14Г2, 15ГФ, 16ГС, 17ГС, 17Г1С, 17Г1С-У, 16Г2АФ и другие
Сталь конструкционная прокатная тарелки
ДСТУ 8539/ ГОСТ 27772
С235, С245, С255, С275, С345, С345К, С355, С390, С390К, С440
Стали конструкционные легированные ДСТУ 7806/ ГОСТ 4543 30ХГСА 8-200
1 500–3 200 6 000–12 200
Сплав конструкционный высокопрочный сортовой прокат плиты для спец. цели
ГОСТ 11269 30ХГСА 6-40
Низколегированные конструкционные стальной прокат для мостов
ДСТУ 8817/ ГОСТ 6713
16Д 8-60
15ХСНД 8-50
10ХСНД 8-40
Прокат конструкционный из сплава сталь мостовая ГОСТ Р 55374
10ХСНД, 15ХСНД 8-50
Высокая прочность пластины из низколегированной стали
ТУ 5.