Свариваемость стали 20: технологические нюансы выполнения швов в зависимости от вида выполнения работ
alexxlab | 30.01.1970 | 0 | Разное
Страница не найдена – ccm-msk.com
Сварщикам
Содержание1 Сколько зарабатывает сварщик1.1 От чего зависит оклад1.2 Сколько зарабатывает сварщик в России1.3 Сколько
Информация
Содержание1 Сварочный аппарат1.
Вопросы
Содержание1 Пайка нержавейки оловом1.1 Преимущества процесса спаивания нержавеющей стали при помощи олова1.2 Недостатки спаивания
Сталь
Содержание1 Сталь марки Р18: характеристики и применение1. 1 Химический состав и основные эксплуатационные свойства1.2 ГОСТ1.3
Пайка
Содержание1 Паяльники: как выбрать — лучшие паяльники, мощность и виды1.1 Виды паяльников1.2 Электрические паяльники1.3
Вопросы
Содержание1 Как выбрать недорогой сварочный инвертор для дома и дачи1. 1 Особенности подключения инверторного аппарата1.2
Страница не найдена – ccm-msk.com
Нержавейка
Содержание1 Технология сварки нержавейки полуавтоматом: особенности металла1.1 Специфика нержавеющей стали1.2 Низкая теплопроводность1.3 Небольшая температура
Информация
Содержание1 5 лучших сварочных инверторов1. 1 Aurora1.2 Blueweld1.3 Daewoo1.4 Elitech2.5 FUBAG1.6 Patriot1.7 Интерскол1.8 Ресанта1.9 лучших
Информация
Содержание1 Температура пайки полипропиленовых труб: таблица значений + инструктаж по самостоятельной сварке1.1 Пайка как
Вопросы
Содержание1 Аргонодуговая сварка неплавящимся электродом1.
Информация
Содержание1 Как своими руками сварить алюминий полуавтоматом1.1 Основные нюансы и сложности1.2 Выбор полуавтомата для
Информация
Содержание1 Нахлест арматуры при вязке: таблицы размеров стыковки всех диаметров по СНиП, правила соединения
Страница не найдена – ccm-msk.
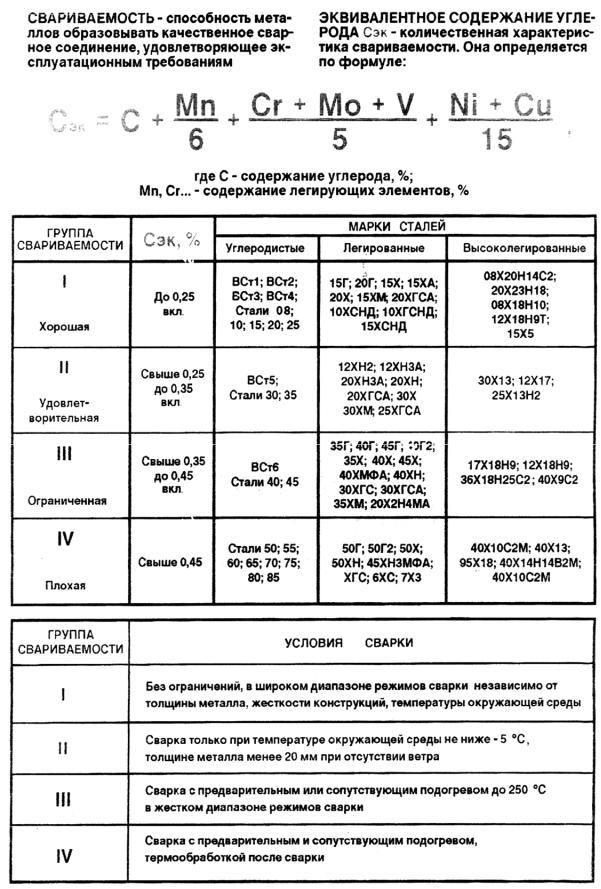
Информация
Содержание1 Технология сварки труб1.1 Виды трубопроводов и сварка1.2 Сварка труб электросваркой плавящимся и неплавящимся
Пайка
Содержание1 Ремонт наушников голыми руками, без паяльника! | Гик1. 1 Первым делом бесцеремонно перерезаем AUX-кабель:1.2
Информация
Содержание1 История развития сварки1.1 Историческая неточность1.2 Открытие Бенардоса1.3 Работы Славянова1.4 Многообразие видов сварки1.5 Применение
Информация
Содержание1 Журнал сварочных работ Образец и бланк 2019 года1. 1 Как заполняются графы1.2 Выполнение работы1.3
Содержание1 Как выбрать шлифовальную машинку: какая для чего нужна?1.1 Профинструмент1.2 Бытовые устройства1.3 Угловые1.4 Прямые1.5
Как правильно
Содержание1 Как паять медные трубы: разбираемся в технологиях1.
Страница не найдена – ccm-msk.com
Вопросы
Содержание1 Как заточить сверло по металлу своими руками: рекомендации1.1 Когда стоит точить сверло1.2 Геометрия
Вопросы
Содержание1 Как выбрать пилки для электрического лобзика1. 1 Расшифровка маркировки1.2 Виды пилок для лобзика1.3 Полотна
Металл
Содержание1 Как заточить сверло по металлу и какие углы заточки бывают?1.1 Как правильно заточить
Информация
Содержание1 Сварка в защитных газах1. 1 Преимущества и недостатки способа1.2 Подготовка кромок и их сборка
Информация
Содержание1 Выбор оптимального варианта сварочного аппарата для дома1.1 Подготовка к покупке1.2 Основные типы техники1.3
Пайка
Содержание1 Пайка латунью: как и чем правильно паять латунь1. 1 Условия и область применения пайки1.2
Марка стали | Заменитель | Свариваемость |
---|---|---|
ГОСТ 380-94 — Сталь углеродистая обыкновенного качества. | ||
Ст 0 | нет | Сваривается без ограничений. |
Ст2пс Ст2кп Ст2сп | Ст2сп Ст2пс | Сваривается без ограничений. Для толщины более 36 мм. рекомендуется подогрев и последующая термообработка. |
Ст3кп | Ст3пс | Сваривается без ограничений.![]() |
Ст3пс Ст3сп | Ст3сп Ст3пс | Сваривается без ограничений. Для толщины более 36 мм. рекомендуется подогрев и последующая термообработка. |
Ст3Гпс | Ст3пс Ст18Гпс | Сваривается без ограничений. Для толщины более 36 мм. рекомендуется подогрев и последующая термообработка. |
Ст4пс | Ст4сп | Сваривается ограниченно. |
Ст5пс Ст5сп | Ст6сп | Сваривается ограниченно. Рекомендуется подогрев и последующая термообработка. |
Ст6пс | Ст5сп | Сваривается ограниченно. Рекомендуется подогрев и последующая термообработка. |
Марка стали | Заменитель | Свариваемость |
ГОСТ 5058-65 — Сталь низколегированная конструкционная.![]() | ||
09Г2С | 09Г2, 09Г2ДТ, 09Г2Т, 10Г2С | Свариваемость стали хорошая без ограничений. |
Марка стали | Заменитель | Свариваемость |
ГОСТ 1050-2013 — Сталь углеродистая качественная конструкционная. | ||
08 | 10 | Сваривается без ограничений, кроме деталей после химико-термической обработки. |
08кп | 08 | Сваривается без ограничений, кроме деталей после химико-термической обработки. |
10 | 08; 15; 08кп | Сваривается без ограничений, кроме деталей после химико-термической обработки. |
10кп 10пс | 08кп; 15кп; 10 | Сваривается без ограничений, кроме деталей после химико-термической обработки. |
15 | 10 20 | Сваривается без ограничений, кроме деталей после химико-термической обработки.![]() |
15кп 15пс | 10кп 15кп. | Сваривается без ограничений. |
18кп | Сваривается без ограничений. | |
20 | 15 | Сваривается без ограничений, кроме деталей после химико-термической обработки. |
20кп 20пс | 15кп | Сваривается без ограничений, кроме деталей после химико-термической обработки. |
25 | 20, 30 | Сваривается без ограничений, кроме деталей после химико-термической обработки. |
30 | 25, 35 | Сваривается ограниченно. Рекомендуется подогрев и последующая термообработка. |
35 | 30, 40 35Г | Сваривается ограниченно. Способы сварки: РДС, АДС (под флюсом и газовой защитой), ЭШС. Рекомендуется подогрев и последующая термообработка. КТС без ограничений. |
40 | 35, 45 40Г | Сваривается ограниченно. Рекомендуется подогрев и последующая термообработка.![]() |
45 | 40Х, 50 50Г | Трудно свариваемая. Способы сварки: РДС и КТС. Необходим подогрев и последующая термообработка. |
50 | 45 50Г 50Г2 55 | Трудно свариваемая. Необходим подогрев и последующая термообработка. |
55 | 50, 60 50Г | Не применяется для сварных конструкций |
60 | 55 65Г | Не применяется для сварных конструкций |
Марка стали | Заменитель | Свариваемость |
ГОСТ 1414-75 — Сталь конструкционная, повышенной обрабатываемости резанием. “автоматка” | ||
А20 | А12 | Не применяется для сварных конструкций |
А30, А40Г | А40Г | Не применяется для сварных конструкций |
Марка стали | Заменитель | Свариваемость |
ГОСТ 1435-90 — Сталь инструментальная нелегированная.![]() | ||
У7, У7А | У8 | Не применяется для сварных конструкций |
У8, У8А | У7, У7А, У10, У10А | Не применяется для сварных конструкций |
У9, У9А | У7, У7А, У8, У8А | Не применяется для сварных конструкций |
У10, У10А | У12, У12А | Не применяется для сварных конструкций |
У12, У12А | У10, У10А | Не применяется для сварных конструкций |
Марка стали | Заменитель | Свариваемость |
ГОСТ 4543-71— Сталь конструкционная легированная хромистая. | ||
15Х | 20Х | Сваривается без ограничений, кроме деталей после химико-термической обработки. |
20Х | 15Х 20ХН, 18ХГТ | Сваривается без ограничений, кроме деталей после химико-термической обработки. |
30Х | 35Х | Ограниченно свариваемая.![]() |
35Х | 40Х | Ограниченно свариваемая. |
38ХА | 40Х | Трудно свариваемая. |
40Х | 45Х 38ХА 40ХС | Трудно свариваемая. Способы сварки: РДС, ЭШС. Необходимы подогрев и последующая т.о. КТС – необходима последующая т.о. |
45Х | 40Х, 50Х | Трудно свариваемая. Необходим подогрев и последующая термообработка. |
50Х | 40Х,45Х 50ХН | Трудно свариваемая. Необходим подогрев и последующая термообработка. |
30ХГСА | 40ХФА, 35ХМ, 40ХН, 25ХГСА, 35ХГСА | Трудно свариваемая. Необходим подогрев и последующая термообработка. |
Марка стали | Заменитель | Свариваемость |
ГОСТ 5632-72 — Сталь высоколегированная, и сплавы коррозийностойкие жаростойкие и жаропрочные. | ||
40Х9С2 | Не применяется для сварных конструкций | |
40X1 ОС2М | Трудносвариваемая | |
08X13 12X13 20X13 25X1 ЗН2 | Стали: 12X13 12Х18Н9Т Сталь: 20X13 Стали: 12X13 14X1 7Н2 | Ограниченно свариваемая |
30X13 40X13 | Сталь: 40X13 Сталь: 30X13 | Не применяется для сварных конструкций |
10Х14АП6 | Стали: 12Х18Н9, 08X1 8Н10, 12Х18Н9Т, 12Н18Н10Т | Сваривается без ограничений |
12X17 | Сталь: 12Х18Н9Т | Трудносвариваемая |
08X1 7Т 08X1 8Т1 | Стали: 12X17, 08X1 8Т1 Стали: 12X17, 08X1 7Т | Ограниченно свариваемая |
95X18 | Не применяется для сварных конструкций | |
15Х25Т | Сталь: 12Х18Н10Т | Трудносвариваемая |
15X28 | Стали: 15Х25Т, 20Х23Н18 | Трудносвариваемая |
20Х23Н13 | Трудносвариваемая | |
20Н23Н18 | Стали: 10Х25Т 20Х23Н13 | Ограниченно свариваемая |
10Х23Н18 | Ограниченно свариваемая | |
20Х25Н20С2 | Ограниченно свариваемая | |
15Х12ВНМФ | Трудносвариваемая | |
20Х12ВНМФ | Стали: 15Х12ВНМФ, 18Х11МНФБ | Трудносвариваемая |
08Х17Н13М21 | Сталь: 10Х17Н13М21 | Трудносвариваемая |
10Х17НЗМ2Т | Трудносвариваемая | |
31Х19Н9МВБТ | Трудносвариваемая | |
10Х14Г14Н4Т | Стали: 20Х13Н4Г9, 12Х18Н9Т, 12Х18Н10Т, 08Х18Н10Т | Сталь удовлетворительно свариваемая всеми видами сварки.![]() |
14Х17Н2 | Сталь: 20X1 7Н2 | Трудносвариваемая. Способ сварки РДС, АрДС. После сварки необходим отпуск при 680-700С в течении 30-60 мин. |
12Х18Н9 17Х18Н9 | Стали: 20Х13Н4Г9, 10Х14Г14Н4Т Сталь: 20Х13Н4Г9 | Сваривается без ограничений |
08X1 8Н10 08Х18Н10Т 12Х18Н9Т | Сталь: 12Х18Н10Т Стали: 15Х25Т, 08Х18Г8Н2Т, 10Х14Г14Н4Т | Сваривается без ограничений |
Марка стали | Заменитель | Свариваемость |
ГОСТ 20072-74 — Сталь теплоустойчивая. | ||
12Х1МФ | Ограниченно свариваемая. Необходим подогрев и последующая термообработка. | |
Основными характеристиками свариваемости сталей является их склонность к образованию трещин и механические свойства сварного шва. По свариваемости стали подразделяют на четыре группы: | ||
К группе 1 относят стали, сварка которых может быть выполнена без подогрева до сварки и в процессе сварки и без последующей термообработки. Но применение термообработки, не исключается для снятия внутренних напряжений. Хорошей свариваемостью обладают стали Ст1 – Ст4 по ГОСТ 380-94; стали 08; 10: 15; 20; 25 по ГОСТ 1050-2013; стали 15Л; 20Л по ГОСТ 977-88, стали 15Г; 20Г; 15Х; 20Х; 20ХГСА; 12ХН2 по ГОСТ 4543-71. Стали 12Х18Н9Т; 08Х18Н10; 20Х23Н18 по ГОСТ 5632-72 К группе 2 относят преимущественно стали, при сварке которых в нормальных производственных условиях трещины не образуются, а также стали, которые для предотвращения трещин нуждаются в предварительном нагреве, стали, которые необходимо подвергать предварительной и последующей термообработке. К группе 3 относят стали, склонные к образованию трещин в обычных условиях сварки. Их предварительно подвергают термообработке и подогревают. Большинство сталей этой группы термически обрабатывают и после сварки. Ограниченной свариваемостью обладают стали Ст6пс. Ст6сп по ГОСТ 380-94; стали 40; 45; 50 по ГОСТ 1050-2013; стали 30ХМ; 30ХГС; ЗЗХС; 20Х2Н4А по ГОСТ 4543-71; стали 17Х18Н9; 12Х18Н9 по ГОСТ 5632-72. К группе 4 относят стали, наиболее трудно сваривающиеся и склонные к образованию трещин. Сваривают обязательно с предварительной термообработкой, подогревом в процессе сварки и последующей термообработкой. Плохой свариваемостью обладают стали 40Г; 45Г; 50Г; 50Х по ГОСТ 4543-71. сталь 55Л по ГОСТ 977-88; стали У7; У8; У8А; У8Г; У9; У10; У11; У12 по ГОСТ 1435-90; стали 65; 75; 85; 60Г; 65Г; 70Г; 50ХГ; 50ХГА; 55С2; 55С2А; 60С2; 60С2А по ГОСТ 14959-79; стали Х12; XI2M; 7X3; 8X3. | ||
Технология сварки углеродистых и низколегированных сталей
Температура плавления углеродистой стали составляет 1535°С. Наиболее часто аргонодуговой сваркой неплавящимся электродом сваривают стали, используемые в теплоэнергетике
Углеродистые и низколегированные стали
Марка стали | Свариваемость | Технологические особенности сварки | |
Сталь 10, Сталь 20, 15ГС | Хорошая | Присадок Св-08Г2С, Св-08ГС | Зачистка кромок до металлического блеска |
12МХ, 15ХМ | Присадок Св-08НХ, Св-08ХМ | ||
15Г2С | Удовлетворительная | Присадок Св-08Г2С, Св-08ГС | |
12X1МФ, 15Х1М1Ф, 12Х2М1, 12Х2МФСР, 12Х2МФБ | Присадок Св-08ХМФА, Св-08ХГСМФА |
ТРУДНОСТИ ПPИ СВАРКИ. Основная – трудно избежать образования пор из-за недостаточного раскисления основного металла. Средством борьбы с порообразованием служит снижение доли основного металла в наплавленном металле шва
Подготовка к сварке. Для разделки сталей, а также подготовки кромок используют газовую, плазменную или воздушно-дуговую резку. После нее участки нагрева металла зачищают резцовым или абразивным инструментом до удаления следов термообработки. Непосредственно перед сборкой стыка кромки зачищают на ширину 20 мм до металлического блеска и обезжиривают.
Стыки собирают в сборочных кондукторах либо с помощью прихваток, которые выполняют с полным проваром и их переплавкой при наложении основного шва. Прихватки с недопустимыми дефектами следует удалять механическим способом. На потолочные участки шва прихватки накладывать не рекомендуется, поскольку там они труднее поддаются переплавке при выполнении основного шва. На сталях 10 и 20 прихватки выполняют только с помощью присадочной проволоки. Ее поверхность должна быть чистой, без окалины, ржавчины и грязи. Очищать проволоку можно как механическим способом, гак и химическим травлением в 5%-ном растворе соляной кислоты.
Высота прихваток, мм | 2-3 | 3-4 |
Толщина кромок свариваемых изделий, мм | до 10 | св. 10 |
1-5 – очередность установки прихваток А, Б – выводные планки для начала и окончания сварки
Выбор параметров режима. Сварку ведут на постоянном токе прямой полярности. Сварочный ток назначают: при однопроходной сварке – в зависимости от толщины конструкции, а при многопроходной – исходя из высоты шва. Высота шва (валика) при ручной аргонодуговой сварке должна составлять 2-2,5 мм. Ориентировочно сварочный ток выбирают из расчета 30-35 А на 1 мм диаметра вольфрамового электрода.
Напряжение на дуге должно быть минимально возможным, что соответствует сварке короткой дугой.
Скорость сварки выбирают с учетом гарантированного проплавления кромок и формирования требуемой выпуклости сварного шва.
Техника сварки. При выполнении первого (корневого) шва возможна сварка без присадочной проволоки, но при этом все прихватки должны быть проплавлены. Нельзя сваривать без присадочной проволоки конструкционные углеродистые стали марок 10 и 20, так как в металле шва могут появиться поры. Сварку ведут углом вперед. Присадочную проволоку подают навстречу движению горелки, причем угол между ними должен составлять 90°. Следует избегать резких движений проволокой – они приведут к разбрызгиванию присадочного металла или окислению конца проволоки.
Присадок должен всегда находиться в зоне защиты аргоном.
Корневой шов сваривают без поперечных колебаний. При наложении последующих слоев горелкой совершают колебательные движения, амплитуда которых зависит от формы разделки кромок.
Кратер шва при отсутствии системы плавного снижения сварочного тока заваривают путем введения в кратер капли присадочного металла, одновременно плавно увеличивая дугу до ее естественного обрыва. Газовую защиту убирают, отводя горелку через 10-15 с после обрыва дуги.
РЕЖИМЫ СВАРКИ НИЗКОУГЛЕРОДИСТЫХ И НИЗКОЛЕГИРОВАННЫХ СТАЛЕЙ
Подготовка кромок и вид сварного соединения (1-6 – очередность проходов) | Размер, мм | Сварочный ток, А | Диаметр электрода, мм | Диаметр присадки, мм | Расход аргона, л/мин | Число проходов | ||
s | b | с | ||||||
0,8 | 0,2 | – | 70 | 2 | 1,6 | 8-10 | 1 | |
2 | 0,5 | – | 110 | 3 | 1,6 | 8-10 | 1 | |
4 6 | 1 1,5 | – – | 120 140 | 3,5 4 | 2 2 | 10-12 10-12 | 2 2 | |
4 | 2 | 1 | 120 | 3,5 | 2 | 10-12 | 2 | |
6 | 2 | 1 | 140 | 4 | 2 | 10-12 | 4 | |
8 10 | 2 2 | 1 1 | 140 140 | 4 4 | 2 2 | 10-12 10-12 | 6 6 |
Свариваемость конструкционных сталей
Конструкционная сталь представляет собой сталь применяемую для изготовления разнообразных конструкций, деталей, которые применяются в строительстве и машиностроении.
Для сварочных работ с конструкционной сталью крайне необходимо знать свойства данной стали,её свариваемость.
Давайте рассмотрим таблицы свариваемости марок конструкционных сталей.
| Заменитель | Свариваемость |
Ст 0 | – | Сваривается без каких либо ограничений |
Ст2пс | Ст2сп | Ограничений в сварке нет. При работах с продуктами толще 36 миллиметров, необходим подогрев и термообработка. |
Ст2кп | Ст2пс | |
Ст2сп |
| |
Ст3кп | СТ3пс | |
Ст3пс | Ст3сп | |
Ст3сп | Ст3пс | |
Ст3Гпс | Ст3пс | |
Ст18Гпс | ||
Ст4кп | нет |
|
Ст4пс | Ст4сп | Сваривается ограниченно. |
Ст5пс | Ст6сп | Сваривается ограниченно. Рекомендовано произведение подогрева и термообработки. |
Ст5сп | Ст4сп | |
Ст6пс |
| |
Ст6сп | Ст5сп |
Сталь углеродистая качественная конструкционная ГОСТ 1050-88
Марка стали | Заменитель | Свариваемость |
08 | Ст10 | Сваривается без ограничений, кроме изделий после химической и термической обработки. |
08кп | Ст08 | |
08пс | ||
Ст10 | Ст08 | |
15, 08кп | ||
Ст10кп | Ст08кп, 15кп, 10 | |
Ст10пс | ||
Ст15 | Ст10 | |
Ст20 | ||
Ст15кп | Ст10кп | Сваривается без ограничений. |
Ст15пс | Ст15кп. | |
Ст18кп |
| |
Ст20 | Ст15 | Сваривается без ограничений, кроме деталей после химико-термической обработки. |
Ст20 | ||
Ст20кп | Ст15кп | |
Ст20пс | ||
Ст25 | Ст20, 30 | |
Ст30 | Ст25, 35 | |
Ст 35 | Ст30, 40 | |
Ст35Г | ||
Ст40 | Ст35, 45 | |
Ст40Г | ||
Ст45 | Ст40Х, 50 | |
Ст50Г | ||
Ст50 | Ст45 | Трудно свариваемая. |
Ст50Г | ||
50Г2 | ||
Ст55 | ||
Ст55 | Ст50, 60 | Не применяется для сварных конструкций |
Ст50Г | ||
Ст60 | СТ55 | |
Ст65Г | ||
*ГОСТ 1055-88 содержит и другие марки стали |
Сталь конструкционная ГОСТ 1414-75, а так же сталь инструментальная нелегированная ГОСТ 1435-90 не используется для сварных конструкций.
Сталь конструкционная легированная хромистая ГОСТ 4543-71
Марка стали | Заменитель | Свариваемость |
Ст15Х | Ст20Х | Сваривается без ограничений, кроме деталей после химико-термической обработки. |
Ст20Х | Ст15Х | |
20ХН, | ||
18ХГТ | ||
Ст30Х | Ст35Х | Ограниченно свариваемая. |
Ст35Х | Ст40Х | |
Ст38ХА | Ст40Х | Трудно свариваемая. |
Ст40Х | Ст45Х | Трудно свариваемая. Необходим подогрев и последующая термообработка. |
Ст38ХА | ||
Ст40ХС | ||
Ст45Х | Ст40Х, 50Х | |
Ст50Х | Ст40Х,45Х | |
Ст50ХН |
Читайте так же:
Резка листового металла
Швеллер перфорированный оцинкованный
Свариваемость материалов – нержавеющая сталь
Нержавеющие стали выбираются из-за их повышенной коррозионной стойкости, стойкости к высокотемпературному окислению или их прочности. Выявлены различные типы нержавеющей стали и даны инструкции по сварочным процессам и технологиям, которые можно использовать при изготовлении компонентов из нержавеющей стали без ухудшения коррозионных, окислительных и механических свойств материала или появления дефектов в сварном шве.
Типы материалов
Уникальные свойства нержавеющих сталей обусловлены добавлением в сталь легирующих элементов, в основном хрома и никеля. Обычно для производства нержавеющего чугуна требуется более 10% хрома. Четыре марки нержавеющей стали классифицированы в зависимости от свойств материала и требований к сварке:
- аустенитный
- Ферритный
- Мартенситный
- Ферритно-аустенитный (дуплекс)
Группы сплавов обозначаются в основном в соответствии с их микроструктурой.Первые три состоят из одной фазы, но четвертая группа содержит в микроструктуре как феррит, так и аустенит.
Поскольку никель (плюс углерод, марганец и азот) способствует развитию аустенита, а хром (плюс кремний, молибден и ниобий) способствует образованию феррита, структуру сварных швов коммерчески доступных нержавеющих сталей можно в значительной степени предсказать на основе их химического состава. Прогнозируемая структура металла сварного шва показана на диаграмме Шеффлера, на которой аустенитные и ферритные промотирующие элементы показаны в единицах эквивалентов никеля и хрома.
Из-за разной микроструктуры группы сплавов имеют разные сварочные характеристики и подверженность дефектам.
Аустенитная нержавеющая сталь
Аустенитные нержавеющие стали обычно имеют состав в диапазоне от 16 до 26% хрома (Cr) и от 8 до 22% никеля (Ni). Обычно для сварных конструкций используется сплав типа 304, который содержит примерно 18% Cr и 10% Ni. Эти сплавы можно легко сваривать, используя любой из процессов дуговой сварки (TIG, MIG, MMA и SA).Поскольку они не затвердевают при охлаждении, они обладают хорошей ударной вязкостью, и нет необходимости в термообработке до или после сварки.
Как избежать дефектов сварного шва
Хотя аустенитная нержавеющая сталь легко сваривается, металл шва и растрескивание в зоне термического влияния могут образоваться. Растрескивание металла шва при затвердевании более вероятно в полностью аустенитных структурах, которые более чувствительны к трещинам, чем структуры, содержащие небольшое количество феррита. Благоприятный эффект феррита в основном объясняется его способностью растворять вредные примеси, которые в противном случае образовали бы сегрегации с низкой температурой плавления и междендритные трещины.
Поскольку присутствие 5-10% феррита в микроструктуре чрезвычайно полезно, выбор состава присадочного материала имеет решающее значение для снижения риска растрескивания. Индикация баланса феррит-аустенит для различных составов обеспечивается диаграммой Шеффлера. Например, при сварке нержавеющей стали типа 304 используется присадочный материал типа 308, который имеет немного другое содержание сплава.
Ферритная нержавеющая сталь
Ферритные нержавеющие стали обычно имеют содержание Cr в пределах 11–28%.Обычно используемые сплавы включают марку 430, содержащую 16-18% Cr, и марку 407, содержащую 10-12% Cr. Поскольку эти сплавы можно рассматривать как преимущественно однофазные и не закаливаемые, их можно легко сваривать плавлением. Однако крупнозернистая ЗТВ будет иметь низкую ударную вязкость.
Как избежать дефектов сварного шва
Основная проблема при сварке этого типа нержавеющей стали – низкая ударная вязкость в зоне термического влияния. Чрезмерное укрупнение зерна может привести к растрескиванию сильно затянутых соединений и материала толстого сечения.При сварке материала с тонким сечением (менее 6 мм) никаких специальных мер предосторожности не требуется.
В более толстом материале необходимо использовать низкое тепловложение, чтобы минимизировать ширину зоны укрупнения зерна, и аустенитный наполнитель для получения более жесткого металла сварного шва. Хотя предварительный нагрев не приведет к уменьшению размера зерна, он снизит скорость охлаждения ЗТВ, сохранит температуру металла шва выше температуры вязко-хрупкого перехода и может снизить остаточные напряжения. Температура подогрева должна быть в пределах 50-250 град.C в зависимости от состава материала.
Мартенситная нержавеющая сталь
Наиболее распространенные мартенситные сплавы, например тип 410, имеют умеренное содержание хрома, 12-18% Cr, с низким содержанием Ni, но, что более важно, имеют относительно высокое содержание углерода. Принципиальным отличием от сварки аустенитных и ферритных марок нержавеющей стали является потенциально твердая мартенситная структура ЗТВ и соответствующий состав металла шва. Этот материал можно успешно сваривать при условии соблюдения мер предосторожности во избежание растрескивания в ЗТВ, особенно в компонентах с толстым сечением и сильно зажатых соединениях.
Как избежать дефектов сварного шва
Высокая твердость в ЗТВ делает этот тип нержавеющей стали очень склонным к водородному растрескиванию. Риск растрескивания обычно увеличивается с увеличением содержания углерода. Меры предосторожности, которые необходимо предпринять для минимизации риска, включают:
- с использованием процесса с низким содержанием водорода (TIG или MIG) и обеспечения сушки флюса или расходных материалов с покрытием из флюса (MMA и SAW) в соответствии с инструкциями производителя;
- с предварительным нагревом от 200 до 300 градусов.C. Фактическая температура будет зависеть от процедуры сварки, химического состава (особенно содержания Cr и C), толщины сечения и количества водорода, попадающего в металл шва;
- поддерживает рекомендованную минимальную температуру промежуточного прохода.
- для проведения термообработки после сварки, например при 650-750 град. C. Время и температура будут определяться химическим составом.
Тонкий профиль из низкоуглеродистого материала, обычно менее 3 мм, часто можно сваривать без предварительного нагрева, при условии, что используется процесс с низким содержанием водорода, соединения имеют низкую фиксацию и внимание уделяется очистке области соединения. Для материала с более толстым сечением и большим содержанием углерода (> 0,1%), вероятно, потребуется предварительный нагрев и термообработка после сварки. Термическую обработку после сварки следует проводить сразу после сварки, чтобы не только закалить (упрочнить) структуру, но и дать водороду возможность диффундировать от металла шва и ЗТВ.
Дуплексные нержавеющие стали
Дуплексные нержавеющие стали имеют двухфазную структуру с почти равными пропорциями аустенита и феррита. Состав наиболее распространенных дуплексных сталей находится в диапазоне 22-26% Cr, 4-7% Ni и 0-3% Mo, обычно с небольшим количеством азота (0.1-0,3%) для стабилизации аустенита. Современные дуплексные стали легко поддаются сварке, но для получения правильной структуры металла сварного шва необходимо строго соблюдать процедуру, особенно поддержание диапазона погонной энергии.
Как избежать дефектов сварного шва
Хотя можно использовать большинство сварочных процессов, обычно избегают сварочных процедур с низким тепловложением. Предварительный нагрев обычно не требуется, и необходимо контролировать максимальную температуру между проходами. Выбор присадочного материала важен, поскольку он предназначен для создания структуры металла сварного шва с балансом феррит-аустенит, соответствующим основному металлу.Чтобы компенсировать потерю азота, наполнитель может быть чрезмерно легирован азотом, или сам защитный газ может содержать небольшое количество азота.
Эта статья Job Knowledge была первоначально опубликована в Connect, сентябрь 1996 г. Она была обновлена, поэтому веб-страница больше не отражает в точности печатную версию.
Обрабатываемость, свариваемость и способность стали
Сталь определяется в первую очередь их химическим составом, а именно тем, что они представляют собой сплавы, состоящие из железа и других легирующих элементов [1].Есть много классов стали, таких как легированная сталь, углеродистая сталь и нержавеющая сталь. Свойства стали указывают на то, насколько легко с ней можно обращаться на практике. Это отличается от стали, но определяется ее свойствами, которые включают механические свойства, такие как предел прочности и твердость, термические свойства, такие как коэффициент теплового расширения, и другие.
Здесь вы узнаете о:
- Обрабатываемость стали
- Литейность стали
- Формуемость стали
- Прокаливаемость стали и методы ее измерения
- Свариваемость различных марок стали
Рисунок 1. Трубы стальные разных форм
Обрабатываемость стали
Обрабатываемость определяется как легкость, с которой металл может быть обработан. Проще говоря, это легкость, с которой стальная стружка может быть удалена при различных операциях обработки, сохраняя при этом удовлетворительную отделку. Как правило, обрабатываемость стали снижается с увеличением механических характеристик.
Факторами, влияющими на обрабатываемость стали, являются ее физические свойства, такие как модуль упругости, теплопроводность и твердость. Состояние стали также влияет на ее обрабатываемость. Микроструктура, размер зерна, термическая обработка, изготовление, химический состав, предел текучести и предел прочности определяют состояние стали.
Количественная оценка обрабатываемости затруднена, так как на нее влияет множество факторов. Тем не менее, некоторые критерии, которые следует учитывать при оценке обрабатываемости стали, представлены в таблице ниже.
Таблица 1. Критерии оценки обрабатываемости стали
Критерии оценки обрабатываемости стали | Описание |
Стойкость инструмента | Стойкость инструмента описывает, как долго служит инструмент, и является полезным параметром для оценки обрабатываемости стали.Однако это также зависит от других факторов, таких как скорость резания, материал режущего инструмента, геометрия режущего инструмента, геометрия реза и состояние станка. |
Сила резания | Стали, требующие более высоких усилий резания для обработки в определенных условиях, менее поддаются обработке. |
Обработка поверхности | Качество обрезанной кромки также можно использовать для определения обрабатываемости металла.Стали с высокой способностью к деформационному упрочнению имеют тенденцию к образованию наростов на кромках во время резки, что приводит к плохой чистоте поверхности. Холоднодеформированные стали не имеют склонности к образованию наростов на кромках, поэтому их лучше обрабатывать. |
Обрабатываемость различных типов стали можно сравнить со стандартной сталью, используя индекс обрабатываемости . Он определяется как , отношение скорости резания исследуемой стали за 20 минут к скорости резания стандартной стали за 20 минут .Углеродистая сталь SAE 1212 используется в качестве стандарта для расчета индекса обрабатываемости.
Таблица 2: Индекс обрабатываемости для различных марок стали [2].
Литейность стали
Под литейными качествами стали понимается легкость формования квалифицированных заготовок путем литья. На него влияют свойства текучести , усадки и сегрегации .
- Текучесть стали определяется как способность расплавленной стали заполнять полости формы.
- Усадка означает степень уменьшения объема при затвердевании расплавленной стали. Низкая усадка способствует разливке стали.
- Сегрегация относится к неоднородному распределению химического состава стального объекта. Это происходит из-за того, как сталь охлаждается во время литья: в первую очередь охлаждают те области, которые контактируют со стенками кристаллизатора. Считается, что сталь с хорошей литейной способностью имеет низкую или незначительную сегрегацию.Ее можно преодолеть медленным охлаждением или последующей термообработкой.
Рис. 2. Процесс литья, когда расплавленный металл выливают в форму.
Формуемость стали
Формуемость стали – это способность стальной заготовки претерпевать пластическую деформацию без повреждений. Проще говоря, это способность металла принимать желаемую форму без образования шейки или трещин.
Формуемость стали во многом зависит от ее пластичности, и поэтому ее можно оценить путем измерения деформации разрушения во время испытания на прочность на разрыв.Марки стали, которые демонстрируют большое удлинение во время этого испытания, обладают хорошей формуемостью. Например, сталь A537 CL1 имеет удлинение 22% при 20 ⁰C. Применяется при строительстве котлов и сосудов под давлением.
Рисунок 3. Листы стали прокатываются благодаря своей формуемости.
Прокаливаемость
Способность стали образовывать мартенсит при закалке называется способностью к закалке. Не следует путать с твердостью стали.Твердость стали – это ее способность противостоять постоянной деформации, а закаливаемость стали – это ее способность закаливаться на определенную глубину при определенных условиях.
Испытание на закалку Джомини часто проводят для определения прокаливаемости стали [3]. Здесь стальной пруток обрабатывается до определенного размера, прежде чем он нагревается до температуры аустенизации. После этого на торцевую поверхность стержня распыляется объем воды, который, в свою очередь, охлаждает образец с этого конца.
Скорость охлаждения варьируется между обоими концами стального стержня. Это быстро на закаленном конце и медленнее на противоположном конце. После закалки образца параллельные плоскости, расположенные на 180 друг от друга, шлифуют на глубину 0,015 дюйма (0,38 мм) по всей длине цилиндрического стержня. Затем на стальном образце наносят маркировку с интервалами 1/16 и . Каждые 1/16 дюйма проводят испытание на твердость C по Роквеллу, и строят кривую. Типичный график этих значений твердости и их положения на стальном стержне показан на Рисунке 4 [3].Это дает четкое представление о глубине затвердевания. Кроме того, по рисунку можно определить приблизительную скорость охлаждения в обозначенных местах.
Рис. 4. График твердости и скорость охлаждения как функция расстояния от закаленного конца [3].
Свариваемость стали
Свариваемость стали трудно определить, но часто под понимается способность стали свариваться с использованием обычных процессов без возникновения холодных трещин. Свариваемость стали обратно пропорциональна ее прокаливаемости. Поскольку содержание углерода играет важную роль в закаливаемости стали, оно также влияет на ее свариваемость. Следовательно, с увеличением содержания углерода свариваемость снижается. Другие легирующие элементы, такие как марганец, никель и кремний, также влияют на свариваемость стали. Однако их влияние не так существенно, как наличие содержания углерода.
Рисунок 5. Сварка двух стальных труб.
Другими факторами, влияющими на свариваемость стали, являются теплопроводность, температура плавления, удельное электрическое сопротивление и коэффициент теплового расширения.
- Теплопроводность : Типы стали с низкой теплопроводностью обычно очень легко свариваются.
- Точка плавления: Чем ниже точка плавления определенного типа стали, тем легче сваривать.
- Удельное электрическое сопротивление : Поскольку тепловая энергия важна для процесса сварки, типы стали с высоким электрическим сопротивлением обычно труднее сваривать электрическими средствами.
- Коэффициент теплового расширения : При сварке двух металлов очень важно учитывать их коэффициенты теплового расширения. Если разница между двумя коэффициентами значительна, деформация растяжения и сжатия при охлаждении может вызвать растрескивание.
Сталь бывает четырех групп по химическому составу: углеродистая сталь, легированная сталь, нержавеющая сталь и инструментальная сталь. Эти классы стали представлены в таблице ниже.
Таблица 3. Свариваемость и применение сталей разных классов.
Тип | Свариваемость | Заявка |
Низкоуглеродистая сталь | Содержит менее 0,3 мас.% Углерода и 0,4 мас.% Марганца. Также демонстрирует хорошую свариваемость при низком уровне примесей. Для низкоуглеродистой стали подходит любой процесс сварки. | Подходит для декоративных изделий, например, фонарных столбов. Примером может служить нормализованная сталь марки 07М20 БС 970-1. Он имеет предел прочности на разрыв 430 МПа и предел текучести 215 МПа при 20 ⁰C. |
Среднеуглеродистая сталь | Содержит 0,3 – 0,6 мас.% Углерода и 0,6 – 1,6 мас.% Марганца. Более высокое содержание углерода делает его склонным к растрескиванию. Следовательно, их труднее сваривать. Процесс сварки с низким содержанием водорода подходит для среднеуглеродистой стали. | Подходит для автомобильных компонентов. Примером может служить холоднокатаная сталь AISI 1541. |
Высокоуглеродистая сталь | Содержит 0,6–1,0 мас.% Углерода и 0,30–0,90 мас.% Марганца. Он также имеет плохую свариваемость и легко трескается. При сварке этих сталей необходимо использовать присадки с низким содержанием водорода. | Используется для изготовления ножей, осей и пробойников. Примером может служить горячекатаный прокат AISI 1080. |
Легированная сталь | Легированные стали часто имеют более высокую твердость по сравнению со сталями других категорий. Следовательно, они также обладают плохой свариваемостью и склонны к растрескиванию. Для легированных сталей необходимо использовать процесс сварки с низким содержанием водорода. В процессе сварки необходимо уделять внимание предварительному нагреву, скорости охлаждения и термообработке после сварки, поскольку легированные стали также склонны к растрескиванию. | Легированные стали имеют разные механические свойства в зависимости от химического состава.Их используют при производстве трубопроводов, электродвигателей и генераторов энергии. Примером может служить нормализованная сталь AISI 8620. Он имеет предел текучести 360 МПа и предел прочности на разрыв 640 МПа при 20 ⁰C. |
Нержавеющая сталь | Нержавеющие стали – это группа легированных сталей. Они содержат не менее 10,5 мас.% Хрома и других элементов, улучшающих их термостойкость и улучшающих механические свойства [4]. Аустенитная нержавеющая сталь обладает хорошей свариваемостью и не требует термической обработки до или после сварки.Зерно ферритного типа быстро растет при высокой температуре, что делает их хрупкими. Следовательно, у них плохая свариваемость. | Аустенитная сталь используется в производстве труб, кухонной утвари и прочего пищевого оборудования. Ферритная сталь также используется в автомобильной промышленности и промышленном оборудовании. Нержавеющая сталь SUS 321, поставляемая TJC Iron & Steel Co., Ltd, подходит для сосудов под давлением. |
Инструментальная сталь | Инструментальная сталь содержит до 2 шт.5 мас.% Углерода. Имеет плохую свариваемость. | Применяется для режущего и сверлильного оборудования. Мягкая отожженная сталь марки C105W1 по DIN 17350 подходит для изготовления метчиков, штампов, оправок и молотков. |
Будущее обработки стали
Открытие новых способов работы со сталью – это огромная область исследований в области материаловедения и инженерии. Например, в последнее время наблюдается бум интереса к аддитивному производству стальных компонентов [5].Этот процесс можно использовать для эффективного производства стальных компонентов сложной геометрии с меньшими затратами.
Рисунок 6. Аддитивное производство стальных деталей. (TRUMPF)
[1] Г. Краусс, Стали . Парк материалов, Огайо: ASM International, 2010, стр. 2.
[2] Таблица индексов обрабатываемости для стали, алюминия, магния, чугуна, углеродистой стали, легированной стали и нержавеющей стали – Engineers Edge », Engineersedge.com , 2020. [Онлайн]. Доступно: https://www.engineersedge.com/materials/machinability-steel-aluminium.htm.
[3] Дж. Доссет, Основы и процессы термической обработки стали . Парк материалов, Огайо: ASM International, 2014, стр. 29.
[4] Дж. Липпольд, Д. Котецки, Металлургия сварки и свариваемость нержавеющих сталей . Норвуд Массачусетс: Books24x7.com, 2005, стр. 5.
[5] А. Зади-Маад, Р. Рохиб и А. Ираван, «Аддитивное производство сталей: обзор», IOP Conf.Серия: Материаловедение и инженерия , 2017. Доступно: 10.1088 / 1757-899X / 285/1/012028.
Сталь 20: характеристики, свойства, аналоги
Сталь20 – высококачественная нелегированная сталь, применяемая в металлических конструкциях и элементах, работающих при температурах от -40 ° С до + 450 ° С. Прокат горячекатаный и кованый из стали марки 20 соответствует стандартам ДСТУ 7809 и ГОСТ 1050.
Классификация: Сталь конструкционная высокосортная углеродистая.
Продукция: Лист стальной, сортовой.
Химический состав стали 20 по ДСТУ 7809%
Si | млн | п. | S | Кр | Cu | Ni | |
0.17-0,37 | 0,35–0,65 | ≤0,035 | ≤0,040 | ≤0,25 | ≤0,30 | ≤0,30 |
Механические свойства стали 20 после нормализации
Минимальный предел текучести, Н / мм2, не менее | Предел прочности при растяжении, Н / мм2, не менее | Минимальный коэффициент удлинения,%, не менее | Степень усадки,%, не менее |
245 | 410 | 25 | 55 |
Аналоги стали 20
США | 1020, 1023, 1024, G10200, G10230, h20200, M1020, M1023 |
Япония | S20C, S20CK, S22C, STB410, STKM12A, STKM12A-S, STKM13B, STKM13B-W |
ЕС | 1.1151, 2C22, C20E2C, C22, C22E |
Китай | 20, 20G, 20R, 20Z |
Швеция | 1450 |
Австралия | 1020, M1020 |
Швейцария | Ck22 |
Южная Корея | SM20C, SM20CK, SM22C |
Приложение
В строительстве применяется сталь20; машиностроение; котельно-емкостное производство; и нагревательные элементы различной спецификации.Высококачественная нелегированная конструкционная сталь 20 в виде плоского и проката используется при изготовлении деталей сварных конструкций, трубопроводов, аккумуляторов, вкладышей подшипников, стропов и других изделий. Термохимическая обработка (цементация, азотирование, нитроцементация и т. Д.) Придает осям, шестерням, червячным винтам, фрикционным дискам, валам, шпинделям, болтам, зубьям, штифтам и другим стальным компонентам высокую твердость поверхности и долговечность, несмотря на низкую прочность сердечника. .
Сварка
Допускается любой вид сварки, кроме компонентов, прошедших термохимическую обработку.Стандартные методы сварки – это ручная дуговая сварка, автоматическая дуговая сварка, автоматическая дуговая сварка под флюсом в газовой защите и контактная стыковая сварка.
Свариваемость стали | Металлический пресс от onlinemetals.com
Виды стали
По данным Американского института железа и стали (AISI), сталь подразделяется на четыре основные группы в зависимости от химического состава. Каждая группа различается по содержанию углерода и, следовательно, обладает различной свариваемостью. К четырем группам относятся углеродистая сталь, легированная сталь, нержавеющая сталь и инструментальная сталь.
Углеродистая сталь
Легкость сварки углеродистой стали во многом зависит от количества присутствующего углерода. По мере увеличения содержания углерода свариваемость имеет тенденцию к снижению. Это связано с тем, что увеличение твердости делает сталь более склонной к растрескиванию. Однако большинство углеродистых сталей по-прежнему поддаются сварке.
Низкоуглеродистая сталь (низкоуглеродистая сталь)
Эти стали обычно содержат менее 0,3% углерода и до 0,4% марганца. Низкоуглеродистые стали с 0.15-0,3% углерода и до 0,9% марганца обладают хорошей свариваемостью. Идеально подходят те, у которых менее 0,2% углерода.
До тех пор, пока содержание примесей остается низким, эти металлы редко вызывают проблемы во время процесса сварки. Стали с содержанием углерода более 0,25% склонны к растрескиванию в определенных областях применения. И наоборот, стали с содержанием углерода менее 0,12% могут иметь пористость. Любую низкоуглеродистую сталь можно сваривать, используя любой из обычных способов сварки. Но стали с большим содержанием углерода лучше всего сваривать с низким содержанием водорода или с наполнителями с низким содержанием водорода.
Сталь среднеуглеродистая
Среднеуглеродистые стали содержат 0,30–0,60% углерода и 0,60–1,65% марганца. Они прочнее, чем низкоуглеродистая сталь, но их труднее сваривать. Это потому, что они более склонны к растрескиванию. Среднеуглеродистые стали всегда следует сваривать с использованием процесса сварки с низким содержанием водорода или контролируемых водородных наполнителей.
Высокоуглеродистая сталь (инструментальная углеродистая сталь)
Высокоуглеродистая сталь содержит 0,60–1,0% углерода и 0,30–0,90% марганца. Они очень твердые и прочные, но также плохо свариваются, и их трудно сваривать без образования трещин.
После термообработки они становятся чрезвычайно твердыми и хрупкими. При сварке высокоуглеродистые стали требуют предварительного нагрева, тщательного контроля температуры между проходами и снятия напряжений после сварки. При сварке этих сталей необходимы процессы с низким содержанием водорода и присадки с низким содержанием водорода.
Углеродисто-марганцевые стали Углеродисто-марганцевые сталисодержат 0,15-0,5% углерода и 1,0-1,7% марганца. Обычно эти стали поддаются сварке, хотя для некоторых сталей требуется контроль предварительного нагрева и подводимой теплоты.При сварке углеродисто-марганцевых сталей с повышенным содержанием углерода рекомендуется использовать процессы сварки с низким содержанием водорода или контролируемые водородные наполнители.
Как и другие углеродистые стали, многие низколегированные стали пригодны для сварки. Но их свариваемость снова зависит от содержания углерода. В частности, свариваемость легированных сталей зависит от углеродного эквивалента его легирующих добавок: марганца, хрома, молибдена, ванадия и никеля.
ОБЩЕЕ ОПИСАНИЕ И СВАРОЧНОСТЬ ЧЕРНЫХ МЕТАЛЛОВ 7-10.СТАЛЬ С НИЗКИМ УГЛЕРОМа. Общие . К низкоуглеродистым (мягким) сталям относятся стали с содержанием углерода до 0,30% (рис. 7-7). В большинстве низкоуглеродистых сталей содержание углерода составляет от 0,10 до 0,25 процента, марганца – от 0,25 до 0,50 процента, фосфора – не более 0,40 процента, а серы – не более 0,50 процента. Стали этого диапазона наиболее широко используются в промышленном производстве и строительстве. Эти низкоуглеродистые стали не сильно затвердевают при сварке, и поэтому не требуют предварительного или последующего нагрева, за исключением особых случаев, например, когда необходимо сваривать тяжелые секции.В целом при сварке низкоуглеродистых сталей трудностей не возникает. Правильно выполненные сварные швы из низкоуглеродистой стали будут равны прочности основного металла или превосходить его. Низкоуглеродистые стали мягкие, пластичные, их можно прокатывать, штамповать, резать и обрабатывать как в горячем, так и в холодном состоянии. Они поддаются механической обработке и легко свариваются. Литая сталь имеет шероховатую темно-серую поверхность, за исключением случаев механической обработки. Прокат имеет мелкие линии на поверхности, идущие в одном направлении. Кованую сталь обычно можно узнать по форме, следам от молотков или ребрам.Цвет излома – ярко-серый, кристаллический, и искровой тест дает искры с длинными желто-оранжевыми полосами, которые имеют тенденцию превращаться в белые раздвоенные бенгальские огни. При плавлении сталь выделяет искры и почти мгновенно затвердевает. Низкоуглеродистые стали можно легко сваривать с помощью любых процессов дуговой, газовой и контактной сварки. г. Для сварки низкоуглеродистой стали следует использовать прутки с медным покрытием. Размеры стержней для листов различной толщины следующие:
ПРИМЕЧАНИЕ Стержни от 5/16 до 3/8 дюйма(От 7,9 до 9,5 мм) доступны для тяжелой сварки. Тем не менее, тяжелые сварные швы можно выполнить с помощью стержней 3/16 или 1/4 дюйма (4,8 или 6,4 мм), правильно контролируя лужу и скорость плавления стержня. г. Соединения могут быть подготовлены газовой резкой или механической обработкой. Тип подготовки (рис. 7-8) определяется толщиной листа и положением сварки. г. Пламя должно быть нейтральным. В зависимости от толщины свариваемых пластин можно использовать метод сварки спереди или сзади. e. Расплавленный металл не следует перегревать, так как это вызовет кипение металла и чрезмерное искрение. В результате зернистая структура металла сварного шва будет большой, прочность будет снижена, а сварной шов будет иметь сильные рубцы. ф. Низкоуглеродистые стали не затвердевают в зоне плавления в результате сварки. г. Дуговая сварка металла . (1) При дуговой сварке низкоуглеродистой стали можно использовать электроды с экранированной дугой без покрытия, с тонким или толстым покрытием.Эти электроды относятся к низкоуглеродистому типу (от 0,10 до 0,14 процента). (2) Листы или листовые материалы с низким содержанием углерода, подвергшиеся воздействию низких температур, перед сваркой следует слегка нагреть до комнатной температуры. (3) При сварке листового металла толщиной до 3,2 мм (1/8 дюйма) можно использовать подготовку кромок для стыкового стыка с гладким квадратным стыком. Когда в этих материалах должны свариваться длинные швы, края должны быть расположены на расстоянии друг от друга, чтобы учесть усадку, потому что наплавленный металл имеет тенденцию стягивать пластины вместе.Эта усадка менее значительна при дуговой сварке, чем при газовой сварке, и достаточно будет расстояния примерно 1/8 дюйма (3,2 мм). (4) Для коротких швов, фиксируемых на месте, следует использовать технику сварки обратным шагом или пропуском. Это предотвратит коробление или деформацию и сведет к минимуму остаточные напряжения. (5) Тяжелые пластины должны иметь фаску, чтобы обеспечить угол наклона до 60 градусов, в зависимости от толщины. Детали следует прихватывать с короткими интервалами вдоль шва.Первый или корневой валик должен быть выполнен с помощью электрода достаточно малого диаметра, чтобы обеспечить хорошее проникновение и сплавление в основании соединения. Для этой цели подходит электрод 1/8 или 5/32 дюйма (3,2 или 4,0 мм). Перед нанесением дополнительных слоев наплавленного металла первый валик следует тщательно очистить путем скалывания и чистки проволочной щеткой. Дополнительные проходы присадочного металла следует выполнять с помощью электрода 5/32 или 3/16 дюйма (4,0 или 4,8 мм). Проходы должны выполняться плетением для плоского, горизонтального или вертикального положения.При сварке над головой наилучшие результаты достигаются при использовании валиков по всей длине сварного шва. (6) При сварке тяжелых профилей со скошенными кромками с обеих сторон валики плетения следует укладывать попеременно с одной стороны, а затем с другой. Это уменьшит деформацию сварной конструкции. Перед нанесением дополнительного металла каждый валик следует тщательно очистить, чтобы удалить всю окалину, оксиды и шлак. Движение электрода следует контролировать так, чтобы валик был однородным по толщине и не допускал подрезов и перекрытий на краях сварного шва.Все шлаки и оксиды должны быть удалены с поверхности готового сварного шва, чтобы предотвратить ржавление. ч. Углеродно-дуговая сварка . Листы с низким содержанием углерода и лист толщиной до 3/4 дюйма (19,0 мм) можно сваривать с использованием процесса дуговой сварки углеродом. Дуга зажигается по краям пластины, которые подготавливаются аналогично тому, как это требуется для дуговой сварки металла. На соединение следует нанести флюс и добавить присадочный металл, как при кислородно-ацетиленовой сварке. Вокруг расплавленного основания должен быть предусмотрен газовый экран.Также следует использовать присадочный металл с помощью сварочного прутка с флюсовым покрытием. Сварку нужно производить без перегрева расплавленного металла. Несоблюдение этих мер предосторожности может привести к тому, что металл сварного шва поглотит чрезмерное количество углерода из электрода, кислорода и азота из воздуха и вызовет хрупкость сварного соединения. 7-11. СРЕДНИЙ УГЛЕРОДАа. Общие . Среднеуглеродистые стали – это нелегированные стали, содержащие от 0 до 0.От 30 до 0,55 процентов углерода. Эти стали могут подвергаться термообработке после изготовления и использоваться для общей механической обработки и ковки деталей, требующих твердости и прочности поверхности. Выпускаются в прутковой форме в холоднокатаном или нормализованном и отожженном состоянии. При сварке термообработанных сталей их следует предварительно нагреть от 300 до 500 ° F (от 149 до 260 ° C) в зависимости от содержания углерода (от 0,25 до 0,45 процента) и толщины стали. Температуру предварительного нагрева можно проверить, приложив полоску припоя 50-50 (точка плавления 450 ° F (232 ° C)) к пластине в месте соединения и отметив, когда припой начинает плавиться.Во время сварки зона сварного шва затвердеет при быстром охлаждении, и после сварки необходимо снять напряжение. Среднеуглеродистые стали можно сваривать любым способом: дуговой, газовой или контактной сваркой. г. При более высоком содержании углерода и марганца следует использовать электроды с низким содержанием водорода, особенно в более толстых секциях. Электроды с низким содержанием углерода, с толстым покрытием, прямой или обратной полярности, аналогичные тем, которые используются для дуговой сварки низкоуглеродистых сталей, подходят для сварки среднеуглеродистых сталей. г. Перед сваркой мелкие детали следует отжечь для придания им мягкости. Детали следует предварительно нагреть в месте стыка и сварить присадочной пруткой, обеспечивающей термообработанные сварные швы. После сварки вся деталь должна быть подвергнута термообработке для восстановления первоначальных свойств. г. Для сварки среднеуглеродистых сталей можно использовать низкоуглеродистый или высокопрочный пруток. Сварочное пламя должно быть настроено на легкое науглероживание, а лужа металла должна быть как можно меньше, чтобы соединение было надежным.Сварка науглероживающим пламенем приводит к быстрому нагреву металла, поскольку тепло выделяется, когда сталь поглощает углерод. Это позволяет выполнять сварку на более высоких скоростях. e. Следует позаботиться о медленном охлаждении деталей после сварки, чтобы предотвратить растрескивание сварного шва. Для снятия напряжений со всей свариваемой детали необходимо нагреть ее до температуры от 1100 до 1250 ° F (от 593 до 677 ° C) в течение одного часа на дюйм (25,4 мм) толщины, а затем медленно охладить. Охлаждение можно осуществить, покрыв детали огнестойким материалом или песком. ф. Среднеуглеродистые стали можно паять с помощью предварительного нагрева от 200 до 400 ° F (от 93 до 204 ° C), хорошего бронзового стержня и припоя. Однако эти стали лучше сваривать дуговой сваркой с использованием электродов, экранированных из низкоуглеродистой стали. г. При сварке низкоуглеродистой стали помните о следующих общих технологиях: (1) Пластины должны быть подготовлены к сварке аналогично тому, как это используется для сварки низкоуглеродистых сталей.При сварке электродами из низкоуглеродистой стали необходимо тщательно контролировать температуру сварки, чтобы избежать перегрева металла шва и чрезмерного проникновения в боковые стенки соединения. Этот контроль достигается путем направления электрода больше к ранее нанесенному присадочному металлу, прилегающему к боковым стенкам, чем непосредственно к боковым стенкам. При использовании этой процедуры металл шва вымывается на сторону стыка и плавится с ним без глубокого или чрезмерного проникновения. (2) Высокая температура сварки приведет к тому, что большие участки основного металла в зоне плавления, прилегающей к сварным швам, станут твердыми и хрупкими. Площадь этих твердых зон в основном металле можно свести к минимуму, выполнив сварку серией небольших нитей или валиков, которые ограничат подвод тепла. Каждый валик или слой наплавленного металла будет измельчать зерно в сварном шве непосредственно под ним, отжигать и уменьшать твердость, полученную в основном металле предыдущим валиком. (3) По возможности, готовое соединение после сварки следует подвергнуть термообработке. Снятие напряжений обычно используется при соединении низкоуглеродистой стали, а высокоуглеродистые сплавы следует отжигать. (4) При сварке среднеуглеродистых сталей электродами из нержавеющей стали металл следует наносить в виде валиков, чтобы предотвратить растрескивание металла шва в зоне плавления. При наплавке металла шва в верхние слои швов, выполненных на тяжелых участках, плетение электрода не должно превышать трех диаметров электрода. (5) Каждый последующий валик сварного шва должен быть снят, зачищен щеткой и очищен перед укладкой следующего валика. 7-12. ВЫСОКОУГЛЕРОДИСТЫЕ СТАЛИа. Общие . К высокоуглеродистым сталям относятся стали с содержанием углерода более 0,55%. Необработанная поверхность высокоуглеродистой стали темно-серого цвета и похожа на поверхность других сталей. Высокоуглеродистые стали обычно дают очень мелкозернистый излом, более белый, чем низкоуглеродистые стали.Инструментальная сталь тверже и хрупче, чем листовая сталь или другой низкоуглеродистый материал. Высокоуглеродистую сталь можно закалить путем нагревания до хорошего красного цвета и закалки в воде. Низкоуглеродистая сталь, кованое железо и стальные отливки не подлежат закалке. Расплавленная высокоуглеродистая сталь ярче, чем низкоуглеродистая сталь, а поверхность плавления имеет ячеистый вид. У нее более легкая искра, чем у низкоуглеродистой (мягкой) стали, и искры более белые. Эти стали используются для производства инструментов, которые после изготовления подвергаются термообработке для создания твердой структуры, необходимой для выдерживания высокого напряжения сдвига и износа.Они производятся в виде стержней, листов и проволоки, а также в отожженном или нормализованном и отожженном состоянии, чтобы быть пригодными для механической обработки перед термообработкой. Высокоуглеродистые стали трудно сваривать из-за закаливающего воздействия тепла на сварное соединение. Из-за высокого содержания углерода и термической обработки, обычно применяемой для этих сталей, их основные свойства ухудшаются при дуговой сварке. г. Тепло сварки изменяет свойства высокоуглеродистой стали в непосредственной близости от сварного шва.Для восстановления первоначальных свойств необходима термическая обработка. г. Перед сваркой высокоуглеродистые стали следует предварительно нагреть от 500 до 800 ° F (от 260 до 427 ° C). Температуру предварительного нагрева можно проверить с помощью сосновой палки, которая при этих температурах обугливается. г. Поскольку высокоуглеродистые стали плавятся при более низких температурах, чем низко- и среднеуглеродистые стали, следует соблюдать осторожность, чтобы не перегреть сварной шов или основной металл. О перегреве свидетельствует чрезмерное искрение расплавленного металла.Сварка должна быть завершена как можно скорее, а количество искры должно использоваться для проверки сварочного тепла. Пламя должно быть настроено на науглероживание. Этот тип пламени способствует образованию прочных сварных швов. e. Для сварки следует использовать сварочный пруток со средним или высоким содержанием углерода. После сварки необходимо снять напряжение со всей детали путем нагрева до температуры от 1200 до 1450 ° F (от 649 до 788 ° C) в течение одного часа на дюйм (25,4 мм) толщины, а затем медленного охлаждения.Если детали можно легко размягчить перед сваркой, для соединения следует использовать сварочный стержень с высоким содержанием углерода. Затем всю деталь следует подвергнуть термообработке для восстановления исходных свойств основного металла. ф. В некоторых случаях мелкий ремонт этих сталей можно произвести пайкой. Для этого процесса не требуются такие высокие температуры, как при сварке, поэтому на свойства основного металла это серьезно не влияет. Пайку следует использовать только в особых случаях, потому что прочность соединения не такая высокая, как у исходного основного металла. г. Электроды из мягкой или нержавеющей стали могут использоваться с высокоуглеродистой сталью. ч. Дуговая сварка высокоуглеродистой стали требует критического контроля температуры сварного шва. Следует помнить о следующих методах: (1) Теплота сварки должна быть отрегулирована, чтобы обеспечить хорошее плавление боковых стенок и основания стыка без чрезмерного провара. Контроль нагрева сварочного шва может быть осуществлен путем наплавки металла шва небольшими валиками.Следует избегать чрезмерного образования луж на металле, поскольку это может привести к отрыву углерода от основного металла, что, в свою очередь, сделает металл сварного шва твердым и хрупким. Сплав присадочного металла и боковых стенок должен быть ограничен узкой зоной. Используйте процедуру поверхностной сварки, предписанную для среднеуглеродистых сталей (пункты 7-11). (2) Та же процедура подготовки кромок, очистки сварных швов и последовательности сварки валиков, которая предписана для низко- и среднеуглеродистых сталей, также применяется к высокоуглеродистым сталям. (3) Небольшие детали из высокоуглеродистой стали иногда ремонтируют путем наращивания изношенных поверхностей. Когда это будет сделано, изделие следует отжечь или размягчить, нагревая до красного огня и медленно охлаждая. Затем деталь следует сварить или укрепить электродами из среднеуглеродистой или высокопрочной стали и после сварки подвергнуть термообработке для восстановления ее первоначальных свойств. 7-13. ИНСТРУМЕНТАЛЬНАЯ СТАЛЬа. Общие . Стали, используемые для изготовления инструментов, пуансонов и штампов, являются, пожалуй, самыми твердыми, прочными и прочными сталями, используемыми в промышленности.Как правило, инструментальные стали – это стали от среднего до высокоуглеродистого, с определенными элементами, включенными в различных количествах для обеспечения особых характеристик. Искровой тест показывает умеренно большой объем белых искр с множеством мелких повторяющихся вспышек. г. Углерод входит в состав инструментальной стали, чтобы помочь упрочнить сталь для обеспечения устойчивости к резанию и износу. Другие элементы добавляются для обеспечения большей прочности или прочности. В некоторых случаях добавляются элементы, чтобы сохранить размер и форму инструмента во время операции закалки при термообработке или сделать операцию закалки более безопасной и обеспечить красную твердость, чтобы инструмент сохранял свою твердость и прочность, когда он становится очень горячим.Железо является преобладающим элементом в составе инструментальных сталей. Другие добавленные элементы включают хром, кобальт, марганец, молибден, никель, вольфрам и ванадий. Инструментальная или штамповая сталь предназначена для специальных целей в зависимости от ее состава. Некоторые инструментальные стали производятся для изготовления штампов; одни предназначены для изготовления форм, другие – для горячей обработки, а третьи – для высокоскоростной резки. г. Другой способ классификации инструментальных сталей – по типу закалки, необходимой для упрочнения стали.Самая тяжелая закалка после нагрева – закалка в воде (водоотверждаемые стали). Менее жесткой закалкой является закалка в масле, получаемая при охлаждении инструментальной стали в масляных ваннах (закаленные в масле стали). Наименее резкая закалка – охлаждение на воздухе (закаленные на воздухе стали). г. Инструментальные стали и штампы также можно классифицировать в соответствии с работой, которую должен выполнять инструмент. Это основано на количестве классов. (1) Стали класса I используются для изготовления инструментов, которые работают с режущими или режущими действиями, таких как отрезные штампы, режущие штампы, вырубные штампы и обрезные штампы. (2) Стали класса II используются для изготовления инструментов, которые создают желаемую форму детали, заставляя обрабатываемый материал, горячий или холодный, течь под действием напряжения. Сюда входят штампы для волочения, формовочные штампы, переходные штампы, штамповочные штампы, пластиковые формы и штампы для литья под давлением. (3) Стали класса III используются для изготовления инструментов, которые воздействуют на обрабатываемый материал, частично или полностью реформируя его без изменения фактических размеров.Сюда входят гибочные штампы, гибочные штампы и штампы для скручивания. (4) Стали класса IV используются для изготовления штампов, которые работают под высоким давлением и создают поток металла или другого материала, придающий им желаемую форму. Сюда входят штампы для обжима, штампы для тиснения, штампы для товарных позиций, штампы для экструзии и штампы для кольцевания. e. Стали в группе инструментальных сталей имеют содержание углерода от 0,83 до 1,55 процента. Их редко сваривают дуговой сваркой из-за чрезмерной твердости в зоне плавления основного металла.Если необходимо выполнить дуговую сварку, можно использовать электроды из низкоуглеродистой или нержавеющей стали. ф. При сварке инструментальных сталей необходимо использовать равномерно высокие температуры предварительного нагрева (до 1000 ° F (583 ° C)). г. Как правило, следует соблюдать те же меры предосторожности, что и при сварке высокоуглеродистых сталей. Сварочный раструб следует отрегулировать на науглероживание, чтобы предотвратить выгорание углерода в металле шва. Сварку нужно производить как можно быстрее, стараясь не перегреть расплавленный металл.После сварки сталь следует подвергнуть термообработке для восстановления первоначальных свойств. ч. Буровые штанги можно использовать в качестве присадочных стержней, поскольку их высокое содержание углерода близко к содержанию инструментальных сталей. и. Флюс, подходящий для сварки чугуна, следует использовать в небольших количествах, чтобы защитить лужу высокоуглеродистой стали и удалить оксиды в металле шва. Дж. Сварочная техника . При сварке инструментальных сталей следует учитывать следующие методы: (1) Если свариваемые детали небольшие, их следует отжечь или размягчить перед сваркой.Затем края следует предварительно нагреть до 1000 ° F (538 ° C), в зависимости от содержания углерода и толщины листа. Сварку следует выполнять либо низкоуглеродистым, либо высокопрочным электродом. (2) Высокоуглеродистые электроды нельзя использовать для сварки инструментальных сталей. Углерод, захваченный присадочным металлом из основного металла, приведет к тому, что сварной шов станет твердым как стекло, тогда как металл сварного шва из мягкой стали может поглощать дополнительный углерод, не становясь чрезмерно твердым. Затем сварную деталь следует подвергнуть термообработке для восстановления ее первоначальных свойств. (3) При сварке электродами из нержавеющей стали край пластины следует предварительно нагреть, чтобы предотвратить образование твердых зон в основном металле. Наплавленный металл следует наносить небольшими валиками, чтобы свести к минимуму тепловложение. В целом, процедура нанесения такая же, как и для средне- и высокоуглеродистых сталей. к. Существует четыре типа штамповых сталей, которые подлежат ремонту с помощью сварки. Это штампы для закалки в воде, штампы для закалки в масле, штампы для закалки на воздухе и инструменты для горячей обработки.Также можно отремонтировать быстроходные инструменты. 7-14. ВЫСОКОПРОЧНЫЕ СПЛАВНЫЕ СТАЛИа. Общие . Было разработано большое количество и разнообразие высокопрочных, высокотвердых, коррозионно-стойких сталей, обладающих стойкостью и другими особыми свойствами. Для большинства этих сталей требуется специальный процесс термообработки для достижения желаемых характеристик в готовом состоянии. Легированные стали обладают большей прочностью и долговечностью, чем другие углеродистые стали, а заданная прочность обеспечивается меньшим весом материала. г. К легированным сталям высокой твердости относятся: (1) Стали, легированные хромом . Хром используется в качестве легирующего элемента в углеродистых сталях для повышения прокаливаемости, коррозионной стойкости и ударопрочности, а также обеспечивает высокую прочность с небольшой потерей пластичности. Хром в больших количествах укорачивает искровую струю вдвое по сравнению с той же сталью без хрома, но не влияет на яркость струи. (2) Никелевые легированные стали .Никель увеличивает ударную вязкость, прочность и пластичность сталей и снижает температуру закалки, поэтому для закалки используется закалка в масле, а не в воде. Никелевая искра имеет короткую резко очерченную полосу яркого света прямо перед вилкой. (3) Стали с высоким содержанием хромоникелевых сплавов (нержавеющие) . Эти высоколегированные стали имеют широкий диапазон составов. Их нержавеющие, коррозионные и жаропрочные свойства меняются в зависимости от содержания сплава и обусловлены образованием очень тонкой оксидной пленки, которая образуется на поверхности металла.Искры соломенного цвета возле точильного круга и белые ближе к концу полосы. Имеется средний объем полос с умеренным количеством разветвленных пакетов. (4) Марганцевые легированные стали . Марганец используется в стали для повышения прочности, износостойкости, облегчения горячей прокатки и ковки. Увеличение содержания марганца снижает свариваемость стали. Стали, содержащие марганец, создают искру, похожую на искру углерода. Умеренное увеличение содержания марганца увеличивает объем искровой струи и интенсивность вспышек.Сталь, содержащая более чем нормальное количество марганца, будет давать искру, аналогичную высокоуглеродистой стали с более низким содержанием марганца. (5) Молибденовые легированные стали . Молибден увеличивает прокаливаемость, то есть глубину затвердевания, возможную при термообработке. Ударно-усталостные свойства стали улучшены за счет содержания молибдена до 0,60%. При содержании молибдена более 0,60% ухудшается собственно ударная усталость. Износостойкость улучшается при содержании молибдена выше примерно 0.75 процентов. Иногда молибден объединяют с хромом, вольфрамом или ванадием для получения желаемых свойств. Стали, содержащие этот элемент, дают характерную искру с отделенным наконечником стрелы, похожую на искру из кованого железа, которую можно увидеть даже при довольно сильных выбросах углерода. Стали, легированные молибденом, содержат никель и / или хром. (6) Стали, легированные титаном и колумбием (ниобием) . Эти элементы используются в качестве дополнительных легирующих добавок в коррозионно-стойких сталях с низким содержанием углерода.Они поддерживают стойкость к межкристаллитной коррозии после того, как металл подвергается воздействию высоких температур в течение длительного периода времени. (7) Стали легированные вольфрамом . Вольфрам, как легирующий элемент в инструментальной стали, имеет тенденцию давать мелкое плотное зерно при использовании в относительно небольших количествах. При использовании в больших количествах, от 17 до 20 процентов, и в сочетании с другими сплавами, вольфрам дает сталь, сохраняющую твердость при высоких температурах.Этот элемент обычно используется в сочетании с хромом или другими легирующими добавками. В искровом испытании вольфрам будет иметь тускло-красный цвет в искровом потоке возле колеса. Это также укорачивает искровой поток и уменьшает размер или полностью исключает выброс углерода. Вольфрамовая сталь, содержащая около 10 процентов вольфрама, вызывает короткие изогнутые оранжевые острия на концах несущих линий. Еще более низкое содержание вольфрама приводит к появлению небольших белых всплесков на конце пети копья.Несущие линии могут быть от тускло-красного до оранжевого, в зависимости от других присутствующих элементов, при условии, что содержание вольфрама не слишком велико. (8) Ванадиевые легированные стали . Ванадий используется для контроля размера зерна. Он имеет тенденцию к повышению закаливаемости и вызывает заметную вторичную твердость, но устойчив к отпуску. Его добавляют в сталь во время производства для удаления кислорода. Легированные стали, содержащие ванадий, создают искры с отделенными наконечниками стрелок на конце несущей линии, аналогичные искрам, возникающим в молибденовых сталях. (9) Кремнистые легированные стали . Кремний добавляется в сталь для повышения прокаливаемости и коррозионной стойкости. Его часто используют с марганцем для получения прочной и вязкой стали. (10) Быстрорежущие инструментальные стали . Эти стали обычно представляют собой специальные сплавы, предназначенные для режущих инструментов. Содержание углерода колеблется от 0,70 до 0,80 процента. Их трудно сваривать, кроме как индукционным методом.Искровой тест покажет несколько длинных раздвоенных лопаток, которые имеют красный цвет около колеса и соломенный цвет около конца искрового потока. г. Многие из этих сталей можно сваривать электродом с толстым покрытием типа экранированной дуги, состав которого аналогичен составу основного металла. Электроды с низким содержанием углерода также могут использоваться с некоторыми сталями. Электроды из нержавеющей стали эффективны там, где предварительный нагрев невозможен или нежелателен. По возможности термообработанные стали следует предварительно нагревать, чтобы свести к минимуму образование твердых зон или слоев в основном металле, прилегающем к сварному шву.Расплавленный металл не должен перегреваться, а температуру сварки следует контролировать, наплавляя металл узкими валиками. Во многих случаях процедуры сварки среднеуглеродистых сталей (параграфы 7-11) и высокоуглеродистых сталей (параграфы 7-12) могут использоваться при сварке легированных сталей. 7-15. КОНСТРУКЦИОННАЯ СТАЛЬ С ВЫСОКОЙ ПРОЧНОСТЬЮ, С НИЗКИМ ЛЕГКИМ ЛЕГКИМа. Общие . Низколегированные конструкционные стали с высоким пределом текучести (конструкционные легированные стали) – это специальные стали, прошедшие отпуск для получения исключительной прочности и долговечности.Специальные сплавы и общий состав этих сталей требуют специальной обработки для получения удовлетворительных сварных швов. Эти стали представляют собой специальные низкоуглеродистые стали, содержащие определенные небольшие количества легирующих элементов. Их закаливают и отпускают для получения предела текучести от 90 000 до 100 000 фунтов на квадратный дюйм (от 620 550 до 689 500 кПа) и прочности на разрыв от 100 000 до 140 000 фунтов на квадратный дюйм (от 689 500 до 965 300 кПа), в зависимости от размера и формы. Конструкционные элементы, изготовленные из этих высокопрочных сталей, могут иметь меньшие площади поперечного сечения, чем обычные конструкционные стали, и при этом иметь равную прочность.Эти стали также более устойчивы к коррозии и истиранию, чем другие стали. При испытании на искру эти сплавы создают искру, очень похожую на искру с низким содержанием углерода. г. Сварочная техника . Надежная сварка низколегированных конструкционных сталей с высоким пределом текучести может выполняться при соблюдении следующих правил: ВНИМАНИЕ Для предотвращения растрескивания под валиком при сварке низколегированных конструкционных сталей с высоким пределом текучести следует использовать только электроды с низким содержанием водорода. (1) Правильные электроды. Водород – враг номер один для прочных сварных швов легированных сталей; поэтому используйте только электроды с низким содержанием водорода (MIL-E-18038 или MIL-E-22200/1), чтобы предотвратить растрескивание под валиком. Растрескивание под валиком возникает из-за того, что водород захватывается покрытием электрода, выделяется в дугу и поглощается расплавленным металлом. (2) Контроль влажности электродов. Если электроды находятся в герметичном контейнере, поместите их сразу после открытия контейнера в вентилируемую печь для выдержки, установленную на 250–300 ° F (121–149 ° C).Если электроды не находятся в герметичном контейнере, поместите их в вентилируемую печь для выпечки и запекайте в течение 1-1 / 4 часа при 800 ° F (427 ° C). Запеченные электроды, пока они еще теплые, должны быть помещены в печь для выдержки до использования. Электроды должны быть сухими, чтобы исключить поглощение водорода. Тестирование на влажность должно проводиться в соответствии со стандартом MIL-E-22200. ПРИМЕЧАНИЕ Стабилизатор влажности NSN 3439-00-400-0090 – идеальная печь для выдержки в полевых условиях (MIL-M-45558). г. Выбор электрода с низким содержанием водорода. Электроды идентифицируются по классификационным номерам, которые всегда указаны на контейнерах с электродами. Для покрытий с низким содержанием водорода два последних числа в классификации должны быть 15, 16 или 18. Чаще всего используются электроды диаметром 5/32 и 1/8 дюйма (4,0 и 3,2 мм), поскольку они больше адаптирован ко всем видам сварки этой стали. В таблице 7-14 перечислены электроды, используемые для сварки низколегированных конструкционных сталей с высоким пределом текучести.Таблица 7-15 представляет собой список электродов, используемых в настоящее время в системе снабжения армии. г. Выбор комбинаций проволока-флюс и проволока-газ . Проволочные электроды для дуговой сварки под флюсом и в среде защитного газа не классифицируются по прочности. Сварочная проволока и комбинации проволока-флюс, используемые для снятия напряжений в сталях, должны содержать не более 0,05 недавнего ванадия. Сваривать металл более 0.05% ванадия может стать хрупким при снятии напряжения. При использовании процессов дуговой сварки под флюсом или газовой дуговой сварки для сварки конструкционных сталей с высоким пределом текучести, низколегированных конструкционных сталей с низкопрочными сталями комбинация проволока-флюс и проволока-газ должна быть такой же, как и для низкопрочных сталей. e. Предварительный нагрев . Для сварочных пластин толщиной менее 1,0 дюйма (25,4 мм) температура выше 50 ° F (10 ° C) не требуется, за исключением удаления поверхностной влаги с металла. Таблица 7-16 содержит рекомендуемые температуры предварительного нагрева. ф. Тепловая сварка . (1) Общие . Важно избегать чрезмерной концентрации тепла, чтобы область сварного шва быстро остыла. Для определения тепловложения в сварной шов можно использовать номограмму тепловложения или калькулятор тепловложения. (2) Номограмма тепловой мощности . Чтобы использовать номограмму тепловой мощности (рис. 7-9), найдите значение вольта в столбце 1 и проведите линию к значению в амперах в столбце 3.От точки, где эта линия пересекает столбец 2, проведите еще одну линию до значения дюйм / мин в столбце 5. Считайте единицы тепла в точке, где эта вторая линия пересекает столбец 4. Тепловые единицы представляют собой тысячи джоулей на дюйм. Например, при 20 вольт и 300 ампер линия пересекает столбец 2 при значении 6. При 12 дюймах / мин подвод тепла определяется как 30 тепловых единиц или 30 000 джоулей / дюйм. (3) Вычислитель тепловой энергии .Калькулятор тепловложения можно сделать, скопировав рисунок, напечатанный на внутренней стороне задней обложки данного руководства, на пластик, светлый картон или другой подходящий материал и вырезав кусочки. Если подходящего материала нет, калькулятор можно собрать, вырезав выкройку из задней обложки. После того, как две части будут вырезаны, в центре каждой проделывается отверстие. Затем они собираются с помощью бумажной застежки или другого подобного устройства, которое позволяет деталям вращаться.Чтобы определить погонную энергию при сварке с помощью калькулятора, поворачивайте до тех пор, пока значение на шкале вольт не совпадет со значением на шкале скорости (дюймы / мин). Значение на шкале ампер будет выровнено прямо напротив расчетного значения для тепловых единиц. Как и в случае с номограммой, тепловые единицы представляют собой тысячи джоулей на дюйм. (4) Максимальное тепловложение . Сравните значение погонной энергии, полученное с помощью номограммы или калькулятора, с максимальными значениями, указанными в таблицах 7-17 и 7-18.Если расчетное значение слишком велико, отрегулируйте ток, скорость движения или температуру предварительного нагрева до тех пор, пока расчетное тепловложение не будет в надлежащем диапазоне. (Таблицы применимы только к процессам с одинарной дугой, дугой в экранированной среде, дугой под флюсом, дугой вольфрамовым электродом, порошковой проволокой и металлической дугой в газовой среде. Они не применимы к многодуговой сварке, электрошлаковой сварке или другим процессы вертикальной сварки с высоким тепловложением, так как сварные швы, выполненные ими в сталях марки «Т-1», необходимо подвергать термообработке закалкой и отпуском.) Для условий сварки, выходящих за пределы диапазона номограммы или калькулятора, тепловложение можно рассчитать по следующей формуле: г. Сварочный процесс . Надежная сварка низколегированной конструкционной стали с высоким пределом текучести может быть выполнена формально, если выбрать электрод с низким содержанием водорода или выбрать правильную комбинацию проволока-флюс или проволока-газ при использовании дуговой сварки под флюсом или процессов металлической дуги в газе.По возможности используйте прямой стрингер. Избегайте использования рисунка плетения; однако, если необходимо, его следует ограничить узором частичного плетения. Наилучшие результаты достигаются при небольшом круговом движении электрода с площадью переплетения, не превышающей двух диаметров электрода. Никогда не используйте полный узор переплетения. Рисунок частичного переплетения не должен превышать двойного диаметра электрода. Пропустите сварку, насколько это целесообразно. Иногда рекомендуется упрочнение сварного шва для снятия напряжений при охлаждении более крупных деталей.Угловые швы должны быть гладкими и иметь правильный контур. Избегайте трещин на пальцах и подрезов. Электроды, используемые для угловых швов, должны иметь меньшую прочность, чем электроды, используемые для стыковой сварки. Упрочнение угловых швов с помощью пневмоударника может помочь предотвратить образование трещин, особенно если в сварных швах необходимо снять напряжение. Пьедестал из мягкой стальной проволоки может помочь поглотить усилия усадки. Масляная сварка в области носка перед фактической угловой сваркой укрепляет зону, где может начаться трещина на носке. В области носка накладывается валик, который затем шлифуется перед самой угловой сваркой.Этот валик масляного сварного шва должен быть расположен так, чтобы кончик углового шва проходил прямо над ним во время фактической угловой сварки. Из-за того, что при угловой сварке используется дополнительный материал, скорость охлаждения увеличивается, а тепловложение может быть увеличено примерно на 25 процентов. 7-16. ЧУГУНа. Общие . Чугун – это сплав железа, углерода и кремния, в котором количество углерода обычно составляет более 1,7% и менее 4.5 процентов. (1) Серый чугун – наиболее широко используемый тип чугуна. Серый чугун имеет множество составов, но обычно это перлит с множеством рассредоточенных чешуек графита. (2) Есть также чугуны из сплавов, которые содержат небольшое количество хрома, никеля, молибдена, меди или других элементов, добавленных для придания определенных свойств. (3) Другой легированный чугун – это аустенитный чугун, модифицированный добавками никеля и других элементов для снижения температуры превращения, так что структура становится аустенитной при комнатной или нормальной температуре.Аустенитные чугуны обладают высокой степенью коррозионной стойкости. (4) В белом чугуне почти весь углерод находится в комбинированной форме. Это обеспечивает более высокую твердость чугуна, что используется для обеспечения устойчивости к истиранию. (5) Ковкий чугун получают путем специальной термообработки белого чугуна с отжигом для изменения структуры углерода в чугуне. Структура меняется на перлитную или ферритную, что увеличивает ее пластичность. (6) Чугун с шаровидным графитом и высокопрочный чугун изготавливаются путем добавления магния или алюминия, которые либо связывают углерод в комбинированном состоянии, либо придают свободному углероду сферическую или узловую форму, а не обычную чешуйчатую форму серого цвета. чугун. Эта структура обеспечивает большую пластичность или пластичность отливки. (7) Чугуны широко используются в сельхозтехнике; на станках в качестве оснований, кронштейнов и крышек; для трубопроводной арматуры и чугунных труб; и для автомобильных блоков двигателя, головок, коллекторов и водоподготовки.Чугун редко используется в конструкционных работах, за исключением элементов сжатия. Он широко используется в строительной технике для противовесов и в других областях, где требуется вес. г. Серый чугун имеет низкую пластичность и поэтому не будет расширяться или растягиваться в значительной степени перед разрушением или растрескиванием. Из-за этой характеристики при сварке чугуна методом кислородно-ацетиленовой сварки необходим предварительный нагрев. Однако его можно сваривать дуговым методом без предварительного нагрева, если тепло сварки тщательно контролируется.Это может быть достигнуто путем сварки только коротких участков стыка за один раз и охлаждения этих участков. Благодаря этой процедуре тепло сварки ограничивается небольшой площадью и исключается опасность растрескивания отливки. Крупные отливки со сложным сечением, такие как моторные блоки, можно сваривать без демонтажа и предварительного нагрева. Обычно желательны специальные электроды, предназначенные для этой цели. Ковкий чугун, такой как ковкий чугун, высокопрочный чугун и чугун с шаровидным графитом, можно успешно сваривать.Для достижения наилучших результатов эти типы чугунов следует сваривать в отожженном состоянии. г. Сварка используется для восстановления новых чугунных отливок, ремонта отливок, вышедших из строя, а также для соединения отливок друг с другом или со стальными деталями в производственных процессах. В Таблице 7-19 показаны сварочные процессы, которые можно использовать для сварки чугуна с шаровидным графитом, ковкого чугуна и чугуна с шаровидным графитом. Выбор процесса сварки и присадочных металлов зависит от типа желаемых свойств сварного шва и ожидаемого срока службы.Например, при использовании процесса дуговой сварки экранированным металлом можно использовать различные типы присадочного металла. Присадочный металл будет влиять на соответствие цвета сварного шва по сравнению с основным материалом. Соответствие цвета может быть определяющим фактором, особенно при утилизации или ремонте отливок, когда разница в цвете недопустима. г. Независимо от того, какой из сварочных процессов выбран, необходимо произвести определенные подготовительные действия.Важно определить точный тип свариваемого чугуна, будь то чугун серый, ковкий или пластичный. Если точная информация неизвестна, лучше всего предположить, что это серый чугун с низкой пластичностью или без нее. Как правило, не рекомендуется сваривать ремонтные отливки из серого чугуна, которые при нормальной эксплуатации подвергаются нагреву и охлаждению, особенно когда нагрев и охлаждение изменяются в диапазоне температур, превышающих 400 ° F (204 ° C). Если в качестве присадочного материала не используется чугун, металл сварного шва и основной металл могут иметь разные коэффициенты расширения и сжатия.Это будет способствовать возникновению внутренних напряжений, которые не может выдержать серый чугун. Ремонт этих типов отливок может быть произведен, но надежность и срок службы такого ремонта невозможно спрогнозировать с точностью. e. Подготовка к сварке . (1) При подготовке отливки к сварке необходимо удалить все поверхностные материалы, чтобы полностью очистить отливку в области сварного шва. Это означает удаление краски, смазки, масла и других посторонних материалов из зоны сварки.Желательно нагреть зону сварного шва на короткое время, чтобы удалить захваченный газ из зоны сварного шва основного металла. Кожа или поверхность с высоким содержанием кремния также должны быть удалены рядом с областью сварного шва как на лицевой, так и на корневой стороне. Края стыка должны быть вырезаны или отшлифованы, чтобы получился угол 60 ° или фаска. Там, где есть канавки, следует использовать V-образную канавку под углом 60-90 °. V должен выступать примерно на 3,2 мм (1/8 дюйма) от дна трещины. На каждом конце трещины следует просверлить небольшое отверстие, чтобы она не расширилась.Всегда следует использовать сварные швы с полным проплавлением, поскольку не полностью устраненные трещины или дефекты могут быстро появиться снова в условиях эксплуатации. (2) Предварительный нагрев желателен для сварки чугунов любым сварочным процессом. Его можно уменьшить при использовании очень пластичного присадочного металла. Предварительный нагрев уменьшит температурный градиент между сварным швом и остальной частью чугуна. Температуры предварительного нагрева должны зависеть от процесса сварки, типа присадочного металла, массы и сложности отливки.Предварительный нагрев можно произвести любым из обычных методов. Нагрев горелки обычно используется для относительно небольших отливок весом 30,0 фунтов (13,6 кг) или меньше. Более крупные детали могут быть предварительно нагреты в печи, и в некоторых случаях временные печи строятся вокруг детали, а не в печи. Таким образом, детали могут поддерживаться при высокой температуре промежуточного прохода во временной печи во время сварки. Предварительный нагрев должен быть общим, так как он помогает улучшить пластичность материала и распределяет усадочные напряжения по большой площади, чтобы избежать критических напряжений в какой-либо одной точке.Предварительный нагрев помогает смягчить область, прилегающую к сварному шву; способствует дегазации отливки, что, в свою очередь, снижает возможность образования пористости наплавленного металла шва; и это увеличивает скорость сварки. (3) Медленное охлаждение или последующий нагрев улучшает обрабатываемость зоны термического влияния в чугуне, прилегающей к сварному шву. Последующее охлаждение должно быть как можно медленнее. Это можно сделать, накрыв отливку изоляционным материалом, чтобы не допустить проникновения воздуха или ветров. ф. Сварочная техника . (1) Электроды . (a) Чугун можно сваривать стальным электродом с покрытием, но этот метод следует использовать только в крайних случаях. При использовании стального электрода необходимо учитывать усадку металла сварного шва, углерод, улавливаемый из чугуна металлом сварного шва, и твердость металла сварного шва, вызванную быстрым охлаждением. При переходе из расплавленного в твердое состояние сталь дает усадку больше, чем чугун.При использовании стального электрода эта неравномерная усадка вызывает деформации стыка после сварки. Когда на стык наносится большое количество присадочного металла, чугун может треснуть сразу за линией плавления, если не будут приняты профилактические меры. Чтобы преодолеть эти трудности, подготовленное соединение следует сварить, наплавив металл шва в виде коротких валиков длиной от 0,75 до 1,0 дюйма (от 19,0 до 25,4 мм). Они выполняются периодически, а в некоторых случаях – с помощью процедуры обратного шага и пропуска.Во избежание образования твердых участков дугу следует зажигать в V, а не по поверхности основного металла. Каждый короткий отрезок металла сварного шва, нанесенный на соединение, следует слегка обработать в горячем состоянии небольшим ударным молотком и дать ему остыть перед нанесением дополнительного металла сварного шва. Упрочнение приводит к ковке металла и уменьшению деформации при охлаждении. (b) Используемые электроды должны иметь диаметр 1/8 дюйма (3,2 мм) для предотвращения чрезмерного нагрева при сварке. Сварку следует производить с обратной полярностью.Плетение электрода должно быть сведено к минимуму. Перед добавлением дополнительного металла каждый наплавленный металл следует тщательно очистить. (c) Чугунные электроды должны использоваться там, где требуется последующая обработка сварного соединения. Электроды из нержавеющей стали используются, когда обработка сварного шва не требуется. Процедура выполнения сварных швов этими электродами такая же, как и для сварки электродами из низкоуглеродистой стали. Электроды из нержавеющей стали обеспечивают отличное сплавление присадочного металла и основного металла.Следует проявлять особую осторожность, чтобы избежать растрескивания сварного шва, которое сжимается примерно на 50 процентов больше, чем из-за того, что нержавеющая сталь расширяется, а низкоуглеродистая сталь расширяется при одинаковых изменениях температуры. (2) Дуговая сварка . (a) Процесс дуговой сварки в защитном металлическом корпусе может использоваться для сварки чугуна. Можно использовать четыре типа присадочных металлов: электроды с чугунным покрытием; покрытые электроды из сплава на основе меди; покрытые электроды из сплава на основе никеля; и электроды, покрытые мягкой сталью.Существуют причины для использования каждого из различных конкретных типов электродов, которые включают обрабатываемость наплавки, соответствие цвета наплавке, прочность наплавки и пластичность окончательного сварного шва. (b) При дуговой сварке чугунными электродами (ECI) предварительно нагрейте до 250–800 ° F (от 121 до 425 ° C), в зависимости от размера и сложности отливки, а также от необходимости обработки наплавки и прилегающих к ней поверхностей. области. Чем выше степень нагрева, тем легче будет обработать наплавленный металл.В общем, лучше всего использовать электроды небольшого размера и относительно низкую настройку тока. Следует использовать дугу средней длины, и, если это возможно, сварку следует выполнять в горизонтальном положении. Следует использовать блуждающую или пропущенную процедуру сварки, а упрочнение поможет снизить напряжения и свести к минимуму деформацию. Рекомендуется медленное охлаждение после сварки. Эти электроды обеспечивают отличное цветовое соответствие серого чугуна. Прочность сварного шва будет равна прочности основного металла. Существует два типа электродов на основе меди: сплав медно-оловянный и медно-алюминиевый.Медно-цинковые сплавы нельзя использовать для электродов для дуговой сварки из-за низкой температуры кипения цинка. Цинк улетучивается в дуге и вызывает пористость металла сварного шва. (c) При использовании электродов с медной основой рекомендуется предварительный нагрев от 250 до 400 ° F (от 121 до 204 ° C). Следует использовать электроды малого диаметра и слабый ток. Дуга должна быть направлена против наплавленного металла или лужи, чтобы избежать проникновения и смешивания основного металла с металлом сварного шва.После сварки рекомендуется медленное охлаждение. Электроды на медной основе не обеспечивают хорошего соответствия цвета. (d) Существует три типа никелевых электродов, используемых для сварки чугуна. Эти электроды можно использовать без предварительного нагрева; однако рекомендуется нагревание до 100 ° F (38 ° C). Эти электроды можно использовать во всех положениях; однако рекомендуется горизонтальное положение. Сварочный шлак следует удалять между проходами. Отложения никеля и никелевого железа чрезвычайно пластичны и не станут хрупкими из-за улавливания углерода.Твердость зоны термического влияния можно минимизировать за счет уменьшения проникновения в основной металл чугуна. Упомянутый выше прием, заключающийся в воспроизведении дуги на лужице, а не на основном металле, поможет свести к минимуму разбавление. Медленное охлаждение и, при необходимости, последующий нагрев улучшают обрабатываемость зоны термического влияния. Электроды на никелевой основе не обеспечивают близкого соответствия цвета. (e) Электроды медно-никелевого типа двух марок. Любой из этих электродов можно использовать так же, как никелевый или железоникелевый электрод, с примерно той же технологией и результатами.Отложения этих электродов не обеспечивают совпадение цвета. (f) Электроды из мягкой стали не рекомендуются для сварки чугуна, если требуется механическая обработка наплавки. Отложения из мягкой стали собирают достаточно углерода для образования высокоуглеродистых отложений, которые невозможно обработать механической обработкой. Кроме того, наплавка из мягкой стали будет иметь пониженный уровень пластичности в результате повышенного содержания углерода. Этот тип электрода следует использовать только для небольшого ремонта и не должен использоваться, когда требуется механическая обработка.Для небольших ремонтных работ возможен минимальный предварительный нагрев. Для минимизации разбавления и во избежание концентрации усадочных напряжений рекомендуется использовать небольшие электроды при слабом токе. Следует использовать короткие сварные швы в произвольной последовательности, а сварной шов следует как можно быстрее после сварки. Наплавленный электрод из низкоуглеродистой стали обеспечивает хорошее соответствие цвета. (3) Углеродно-дуговая сварка чугуна . Отливки из чугуна можно сваривать с помощью угольной дуги, чугунного прутка и сварочного флюса для чугуна.Шов следует предварительно нагреть, перемещая угольные электроды по поверхности. Это предотвращает слишком быстрое охлаждение после сварки. Расплавленную лужу металла можно обрабатывать углеродным электродом так, чтобы перемещать любой образующийся шлак или оксиды на поверхность. Сварные швы, выполненные с помощью угольной дуги, охлаждаются медленнее и не так тверды, как сварные швы с использованием металлической дуги и чугунного электрода. Сварные швы поддаются механической обработке. (4) Газовая сварка на кислородном топливе . Процесс кислородно-топливного газа часто используется для сварки чугуна.Можно использовать большую часть топливных газов. Пламя должно быть нейтральным или слегка уменьшающимся. Следует использовать флюс. Доступны два типа присадочных металлов: чугунные стержни и медно-цинковые стержни. Сварные швы, выполненные подходящим чугунным электродом, будут такими же прочными, как и основной металл. Все эти сварочные покрытия обеспечивают хорошее соответствие цветов. Следует использовать оптимальную процедуру сварки в отношении подготовки стыка, предварительного нагрева и последующего нагрева. Медно-цинковые стержни позволяют производить пайку. Существует две классификации: марганцевая бронза и бронза с низким содержанием дымовых газов.Осажденная бронза имеет относительно высокую пластичность, но не обеспечивает совпадения цветов. (5) Пайка и сварка припоем . (a) Пайка используется для соединения чугуна с чугуном и сталью. В этих случаях конструкция соединения должна выбираться для пайки так, чтобы капиллярное притяжение заставляло присадочный металл течь между близко прилегающими деталями. Обычно используется факельный метод. Кроме того, в качестве источников тепла можно использовать угольную дугу, двойную угольную дугу, газо-вольфрамовую дугу и плазменную дугу.Обычно используются два металлических сплава припоя; оба являются сплавами меди и цинка. Для соединения чугуна также можно использовать пайку. При сварке пайкой присадочный металл не втягивается в соединение за счет капиллярного притяжения. Иногда это называют сваркой бронзы. Следует использовать наполнитель с жидкостью выше 850 ° F (454 ° C). Сварка пайкой не обеспечивает совпадения цвета. (b) Сварка пайкой может также выполняться с помощью дуговой сварки в защитном металлическом корпусе или с помощью дуговой сварки металлическим газом.Предварительный нагрев при высокой температуре обычно не требуется для сварки пайкой, если только деталь не является очень тяжелой или сложной по геометрии. Наплавленный бронзовый металл шва имеет чрезвычайно высокую пластичность, которая компенсирует недостаточную пластичность чугуна. Тепла дуги достаточно, чтобы довести поверхность чугуна до температуры, при которой сплав присадочного металла на основе меди будет сцепляться с чугуном. Поскольку перемешивание материалов незначительное или отсутствует, зона, прилегающая к сварному шву в основном металле, не затвердевает в значительной степени.После завершения сварки сварной шов и прилегающий участок можно обработать. Как правило, для большинства применений достаточно предварительного нагрева до 200 ° F (93 ° C). Скорость охлаждения не очень важна, и термообработка для снятия напряжения обычно не требуется. Этот тип сварки обычно используется для ремонтной сварки автомобильных деталей, деталей сельскохозяйственных орудий и даже блоков и головок автомобильных двигателей. Его можно использовать только в том случае, если отсутствие соответствия цветов не вызывает возражений. (6) Дуговая сварка металлическим газом .Процесс газовой дуговой сварки может использоваться для сварки ковкого чугуна и углеродистой стали. Можно использовать несколько типов электродной проволоки, в том числе: (a) Мягкая сталь с использованием 75% аргона + 25% CO 2 для защиты. (b) Никель-медь с использованием 100% аргона для защиты. (c) Кремниевая бронза с использованием 50% аргона + 50% гелия для защиты. Во всех случаях следует использовать электродную проволоку малого диаметра при слабом токе.При использовании электродной проволоки из мягкой стали выделяется смесь защитного газа аргон-CO 2 для минимизации проникновения. В случае присадочного металла на основе никеля и присадочного металла на основе меди наплавленный присадочный металл является чрезвычайно пластичным. Низкоуглеродистая сталь обеспечивает хорошее соответствие цвета. Обычно требуется более высокий предварительный нагрев, чтобы снизить остаточные напряжения и склонность к растрескиванию. (7) Порошковая сварка . Этот процесс недавно стал применяться для сварки чугунов.Более успешным применением была порошковая проволока на никелевой основе. Эта электродная проволока обычно работает с защитным газом CO 2 , но когда более низкие механические свойства не являются нежелательными, она может работать без внешнего защитного газа. Можно использовать минимальные температуры предварительного нагрева. Этот метод должен минимизировать проникновение в основной металл чугуна. Последующий нагрев обычно не требуется. Подбор цвета не получается. (8) Шпилька .Трещины в крупных отливках иногда заделывают шпильками (рис. 7-10). В этом процессе трещина удаляется шлифовкой V-образной канавки. Отверстия просверливаются и нарезаются под углом с каждой стороны канавки, и в эти отверстия ввинчиваются шпильки на расстояние, равное диаметру шпилек, при этом верхние концы выступают примерно на 1/4 дюйма (6,4 мм) над канавкой. чугунная поверхность. Шпильки следует герметично приварить на месте с помощью одного или двух валиков вокруг каждой шпильки, а затем связать вместе металлическими швами.Сварные швы следует выполнять короткими отрезками, и каждый отрезок подвергается закалке в горячем состоянии, чтобы предотвратить высокие напряжения или растрескивание при охлаждении. Перед нанесением дополнительного металла каждому бусинке необходимо дать остыть и тщательно очистить. Если метод шипов не может быть применен, края стыка следует вырезать или обработать инструментом с круглым концом, чтобы образовалась U-образная канавка, в которую должен быть наплавлен металл сварного шва. (9) Для чугуна можно использовать другие способы сварки.Термитная сварка использовалась для ремонта определенных типов деталей станков из чугуна. Пайка может использоваться для соединения чугуна и иногда используется для ремонта небольших дефектов в небольших отливках. Сварку оплавлением можно также использовать для сварки чугуна. Доверенность |
Горячекатаный прокат C1018 / 20 | Металлические супермаркеты
Описание сорта : Низкоуглеродистая сталь с более высоким содержанием марганца, чем низкоуглеродистая сталь и различные другие низкоуглеродистые стали.Более высокое содержание марганца делает эту сталь лучшей для науглероживания деталей, поскольку она обеспечивает более твердый и однородный корпус. Он также имеет более высокие механические свойства, включая твердость по Бринеллю, и лучшие характеристики обработки. Благодаря специальному производственному контролю получается качественный продукт, подходящий для таких областей применения, как ковка, термообработка, холодное волочение, механическая обработка и т. Д.
Типичные области применения: Шестерни, шестерни, червяки, шкворни, штифты цепи, трещотки, собачки, клинья и вкладыши масляного инструмента, шпильки, анкерные штифты, специальные болты, стяжные шпильки.Любые науглероженные детали, требующие твердой поверхности и мягкого сердечника.
Анализ: C – .15 / .20 Mn – .60 / .90 P – .04 Макс. S – 0,05 Макс.
Механические свойства: (следующие значения являются средними и репрезентативными)
в прокатном состоянии | нормализованное | Отожженный | |
Предел прочности (фунт / кв. Дюйм) | 67 000 | 66 000 | 60 000 |
Предел текучести (фунт / кв. Дюйм) | 45 000 | 43 000 | 40 000 |
Относительное удлинение (% на 2 дюйма) | 36 | 37 | 38 |
Уменьшение площади (%) | 58 | 60 | 62 |
Твердость по Бринеллю | 137 | 137 | 121 |
Обрабатываемость: 78% от B1112. Свариваемость : Легко сваривается всеми сварочными процессами, а полученные сварные швы и соединения имеют чрезвычайно высокое качество. Марка используемого сварочного прутка зависит от условий сварки, таких как толщина сечения, конструкция, требования к обслуживанию и т. Д. Ковка : Нагрев до 2150–2250º F. Нормализация : Нагрев до 1650–1750º F. Отжиг : Нагрев до 1550º – 1650º F. Охладите в печи. Закалка : Этот сорт подходит для любых стандартных методов науглероживания и последующей термообработки.Для твердого корпуса и прочного сердечника науглерожите при 1650–1700 º F в течение примерно 8 часов, охладите в коробке, повторно нагрейте до 1400–1450 º F, закалите в воде и вытяните при 300–350 º F.
Завод Инжиниринг | Сварка низкоуглеродистой стали: найдите подходящий присадочный материал
Низкоуглеродистые сталиобладают многочисленными преимуществами – от легкой свариваемости до способности сгибать и формовать материал – что делает их хорошо подходящими для широкого спектра сварочных работ. При наличии множества доступных вариантов низкоуглеродистой стали, как в ходе операции определить, какой присадочный металл является правильным выбором для конкретного применения?
Что такое низкоуглеродистая сталь?
Базовые материалы, которые считаются низкоуглеродистой сталью, обычно не содержат легирующих элементов.Низкоуглеродистые стали имеют предел содержания углерода 0,25% и также называются низкоуглеродистыми сталями. Две распространенные мягкие стали, используемые во многих сферах производства и производства, – это ASTM A36 и AISI 1018.
Характеристики мягкой стали различаются в зависимости от типа материала, но, как правило, мягкая сталь имеет более низкий предел прочности и предел текучести, чем низколегированные стали. Предел прочности на разрыв обычно составляет 70 кг на квадратный дюйм (тыс. Фунтов на квадратный дюйм) или ниже, а предел текучести может составлять всего 30 фунтов на квадратный дюйм.
Более низкие пределы прочности и текучести означают, что материал не такой твердый, поэтому его можно сгибать или раскатывать в разные формы.В тех случаях, когда требуются более высокие показатели текучести и прочности на разрыв, материал может быть разделен на более толстые и тяжелые секции, чтобы компенсировать более низкие значения прочности.
В целом, мягкие стали обладают очень хорошей свариваемостью, и отсутствие дополнительных легирующих элементов в мягких сталях также делает их экономически выгодным вариантом для многих сварочных работ.
Варианты присадочного металла
Присадочные металлы из низкоуглеродистой стали обычно имеют более высокие характеристики, чем базовые материалы, с более высоким пределом прочности и пределом текучести.
Известно, что стандартные присадочные металлы из низкоуглеродистой стали обладают хорошей свариваемостью. Присадочные металлы из низкоуглеродистой стали для сварки проволокой доступны в вариантах сплошной, порошковой и порошковой проволоки для производства и изготовления.
Жесткие провода
Жесткие провода универсальны для многих применений, поскольку их можно использовать при очень низких или очень высоких токах. При сварке более толстых материалов сплошной проволокой рекомендуется использовать процесс переноса распылением; для более тонких материалов лучше всего подходит процесс передачи короткого замыкания.Сплошная проволока обеспечивает хорошую скорость перемещения и внешний вид валика, а также возможность глубокого проплавления при сварке более плотных стыков или углов из-за более узкого профиля проплавления. Обычные присадочные металлы для сплошной проволоки из мягкой стали включают такие классификации Американского сварочного общества (AWS), как ER70S-3 и ER70S-6.
Сплошная проволока обычно используется в автомобильной и роботизированной сварке. Поскольку сплошные проволоки имеют высокую прочность колонны и часто имеют медное покрытие, они немного жестче, чем другие проволоки, и обеспечивают хорошую подачу.Однако имейте в виду, что сплошная проволока может иметь более высокие тепловыделения, чем проволока с металлическим сердечником, поэтому глубокая ведущая дуга сплошной проволоки может иногда приводить к чрезмерному проникновению или прожогу.
Также имейте в виду, что сплошная проволока не смачивает поверхности с прокатной окалиной. Поскольку в сплошную проволоку добавлено меньше раскислителей, она не справляется с поверхностными загрязнениями так же, как другие присадочные металлы, поэтому сварщики должны использовать более низкие скорости перемещения для материалов с прокатной окалиной или ржавчиной.
Металлопорошковая проволока
Порошковая проволока может использоваться практически в любом сварочном аппарате для низкоуглеродистой стали, в котором используется сплошная проволока.Если сплошная проволока имеет более узкий, пальцевидный профиль проникновения, то проволока с металлическим сердечником имеет более широкий и более широкий профиль проникновения, который не такой глубокий. В результате проволока с металлическим сердечником лучше смачивается и крепится к боковым стенкам, и, как правило, может использоваться при меньших тепловыделениях при сохранении того же внешнего вида валика. Более широкий профиль проникновения и дополнительное смачивание также могут сделать размещение проволоки более щадящим.
Поскольку проволока с металлическим сердечником имеет порошковую сердцевину, в ее состав может входить больше раскислителей, чем в проволоке сплошного сечения.Благодаря этому они могут лучше справляться с прокатной окалиной и грязными основными материалами и с более высокими скоростями движения. Их более высокая производительность наплавки приводит к более высокой производительности. Хотя порошковая проволока обычно бывает дороже, чем сплошная проволока, повышение производительности может обеспечить быструю окупаемость инвестиций. Из-за этих факторов порошковую проволоку часто рекомендуют при выполнении сварных швов от 6 дюймов и более, а также для операций, направленных на увеличение скорости движения. Один из наиболее распространенных вариантов с металлическим сердечником для низкоуглеродистой стали – E70C-6M.
Порошковая проволока в газовой среде
При сварке низкоуглеродистой стали используются два распространенных варианта порошковой проволоки в среде защитных газов: E70T-1 для плоских и горизонтальных швов и E71T-1 для сварки во всех положениях.
Предлагая аналогичные или более высокие скорости наплавки, чем у металлической порошковой проволоки, присадочные металлы E70T-1 хорошо подходят для толстых и тяжелых сварных соединений, требующих большого количества сварочного металла. Эта проволока также является хорошим вариантом для материалов с тяжелой прокатной окалиной или ржавчиной и может обеспечить хороший внешний вид валика и более высокую скорость движения даже на этих материалах.
Поскольку при использовании проволоки с металлическим сердечником и сплошной проволокой может быть труднее выполнить большие сварные швы, которые не провисают, плоская и горизонтальная порошковая проволока подходят для этих целей, поскольку шлак помогает удерживать сварной шов на месте при его охлаждении. Однако шлак требует больше времени на очистку после сварки.
Если приложение не позволяет выполнять сварку в плоском или горизонтальном положении, порошковая проволока E71T-1 предлагает вариант во всех положениях. Эта проволока хорошо подходит для сварки вертикально вверх или над головой, обеспечивает более высокую скорость перемещения и более плоский профиль валика.Как и присадочные материалы E70T-1, проволока для установки во всех положениях действительно образует шлак, который необходимо удалить после сварки. Рекомендуется использовать технику перетаскивания для проволоки, образующей шлак, и технику проталкивания для проволоки, которая не образует шлак.
Советы по выбору присадочных материалов для низкоуглеродистой стали
При выборе подходящего присадочного металла для сварки низкоуглеродистой стали необходимо учитывать некоторые дополнительные факторы.
Состояние основного материала является важным фактором при выборе присадочного металла.Некоторые мягкие стали A36 и 1018 бывают горячекатаные или холоднокатаные. Горячекатаная низкоуглеродистая сталь может привести к образованию прокатной окалины на поверхности материала, которую труднее правильно сварить. Низкоуглеродистые стали, подвергнутые холодной прокатке, имеют чистую отделку, но иногда на поверхности есть легкое масло.
Если на основном материале есть легкая прокатная окалина или ржавчина, рекомендуется ее удалить. Если это невозможно, выберите металлическую или порошковую проволоку, которая, как правило, дает лучшие результаты в таких ситуациях.Для деталей, подвергнутых холодной прокатке или имеющих легкое масло на поверхности, допустимы наплавочные металлы из твердой проволоки, такие как ER70S-6.
Конструкция свариваемого соединения также имеет значение. Сварное соединение с узкой V-образной канавкой может потребовать более глубокого проникновения в более узкое место и лучше всего подходит для сплошной проволоки. Порошковая проволока, устанавливаемая во всех положениях, не обеспечивает такого глубокого проникновения, как у сплошных проволок, и лучше подходит для сварки неглубоких соединений.
Материалы из низкоуглеродистой стали обеспечивают легкую свариваемость и гибкость во многих сварочных операциях.Понимание характеристик типа основного материала из низкоуглеродистой стали, целей применения сварки и конструкции сварного шва, а также его согласование с подходящим присадочным металлом из низкоуглеродистой стали помогает повысить производительность, производительность и качество сварки.