Сварка меди контактная – Контактная сварка меди
alexxlab | 21.05.2020 | 0 | Разное
Контактная сварка меди
Для меди и ее сплавов контактная сварка затруднена вследствие их высокой электрической проводимости и теплопроводности, а также узкого диапазона температур, в котором металл может свариваться давлением. Свариваемость медных сплавов лучше, чем технической меди, так как они обладают пониженной электрической проводимостью и теплопроводностью. Однако не все сплавы свариваются одинаково хорошо. Чаще контактная сварка применяется для латуней и кремнистых бронз. Среди них хорошо свариваются α-латуни (например, марки Л68), электрическая проводимость , которых не более 28% электрической проводимости меди. Повышение содержания цинка в латуни приводит к ухудшению ее свариваемости вследствие уменьшения пластичности сплава. Уменьшение концентрации цинка неблагоприятно влияет на свариваемость, поскольку понижается электросопротивление сплава. Хорошо свариваются кремнистая бронза (до 4% Si, электрическая проводимость равна примерно 10% электрической проводимости меди) и медно-никелевые сплавы, например мельхиор (80% Сu, 20% Ni, электрическая проводимость . равна 8% электрической проводимости меди).
Для получения чистой контактной поверхности заготовок рекомендуется их очистка механическим способом, а также травлением в тетрахлорметане или растворе каустической соды с последующей тщательной промывкой в проточной воде. Для растворения пленки оксидов применяют травление в следующих смесях: 10% -ный раствор серной кислоты, бихромат натрия; серная кислота, фтористый алюминий и 6dхромат натрия.
Точечная и роликовая сварка меди.
Точечная и роликовая сварка меди возможна только с применением электродов из тугоплавких металлов, обладающих теплопроводностью и электрической проводимостью, более низкими, чем основной металл, для уменьшения отвода теплоты во время сварки (например, из вольфрама или молибдена). При использовании таких электродов поверхность деталей сильно нагревается, а местами расплавляется, портится внешний вид изделия и быстро изнашиваются электроды. В связи с этим точечная и роликовая сварка технической меди ограниченно пригодна для промышленного применения.
Качество сварных точечных швов можно повысить, используя теплоизолирующие прокладки (например, из нержавеющей стали), размещаемые между электродами и поверхностями свариваемых деталей, а также покрывая соприкасающиеся поверхности деталей, например, серебром.
Для медных сплавов применение мягких режимов нецелесообразно. Обычно длительность нагрева медных сплавов при точечной сварке ограничивается 0,2-0,4с. Точечная сварка латуни производится короткими импульсами при больших значениях сварочного тока. В связи с высокой электрической проводимостью латуни толщина свариваемых листов на одной и той же машине принимается примерно в 2 раза меньше, чем толщина листов из стали. Шовная сварка латуни требует относительно большого удельного давления электродов, чем точечная. При сварке латуни марки Л62 υ
Таблица 1. Ориентировочные режимы точечной сварки латуни Л62
b, мм | Радиус поверхности электрода, мм | р, кПа | Р, кН | Iсв, кА | t, с | Потребляемая мощность, кВА |
0,5+0,5 | 50 | 67 | 1,3 | 1,6 | 0,1 | 68 |
1,0+1,0 | 50 | 98 | 1,8 | 18,3 | 0,2 | 95 |
1,5+1,5 | 70 | 78 | 2,6 | 26,8 | 0,2 | 167 |
3,0+3,0 | 150 | 117 | 3,9 | 38,6 | 0,35 | 290 |
При точечной сварке медных сплавов с высоким электросопротивлением (кремнистая бронза, мельхиор) по сравнению со сваркой малоуглеродистой стали ток увеличивают примерно на 25%, мощность на 50%, давление на электроды принимают близким давлению при сварке стали.
Стыковая сварка оплавлением.
Стыковая сварка оплавлением требует особой техники из-за трудности поддержания на торцах свариваемых деталей слоя жидкого металла, а также при прогреве их на значительную глубину для последующей осадки. Лучшие результаты получаются при осадке стыка под током. Установочную длину вылета медных деталей определяют по формуле:
где d – диаметр свариваемых стержней, мм. Скорость оплавления ориентировочно равна 10 мм/с. Цикл сварки не должен превышать 1-2 с. Прочность стыка прутков из меди марки Ml в среднем составляет 206-215,8 МПа, угол загиба 180°.
Таблица 2. Ориентировочные режимы шовной сварки латуни Л62
b, мм | Ширина роликов, мм | Р, кН | IСВ, кА | Потребляемая мощность, кВА |
0,5+0,5 | 3 | 2,45 | 22,3 | 110 |
0,5+0,5 | 3-4 | 2,45 | 25,5 | 140 |
1,0 + 1,0 | 4-5 | 3,7 | 27,0 | 160 |
Таблица 3. Ориентировочные режимы стыковой сварки оплавлением заготовок из меди
Параметр | Размер заготовки, мм | ||
Пруток, d=10 | Труба, 9,5×1,5 | Полоса, 44,5×10 | |
Установочная длина, мм | 20 | 20 | 20 |
Давление осадки, МПа | 372 | 284,5 | 216 |
Сварочный ток, к А | 33 | 20 | 60 |
Вторичное напряжение, В | 6 | 5 | 10 |
Удельная мощность, кВА/мм2 | 2,6 | 2,7 | 1,4 |
Медь соединяют стыковой сваркой сопротивлением. Провод и прутки из чистой меди диаметром 7-16 мм сваривают при i=380 А/мм2 и средней температуре нагрева 0,7-0,75Тпл. Начальное давление составляет 0,98-2,9 МПа, а конечное 343,4-392,4 МПа. Концентрированный нагрев контактной зоны и большие скорости осадки (150-250 мм/с) исключают разупрочнение металла и обеспечивают высокие пластические и электрические свойства соединений. Для соединения медных проволок успешно применяется стыковая конденсаторная сварка. Латунь и бронза соединяются стыковой сваркой легче, чем медь. Для их сварки требуются большие конечные скорости оплавления и осадки. Хорошо соединяются стыковой сваркой заготовки из деформируемых бронз марок Бр.Х0,5; Бр.ОФ6,5-0,15; Бр.АМц9-2. Поскольку скорость охлаждения бронзы значительно больше, чем стали, и бронза в интервале температур 750-770° С имеет достаточно высокую прочность, при ее сварке давление должно быть выше, чем при сварке стали. В ряде случаев для повышения пластичности сварных соединений рекомендуется их последующая термическая обработка: для соединений из бронзы типа Бр.Х0,5 – закалка в воде от 950-980°С, из бронзы Бр.ОФ6,5-0,15 отжиг при 500-550 °С (его можно дать после сварки на машине).
Таблица 4. Ориентировочные режимы стыковой конденсаторной сварки медной проволоки
dпр, мм | СК, мкФ | U, кВ | Усилие осадки, кН |
1,6 | 256 | 0,9 | 1,4 |
2,0 | 380 | 1,0 | 1,4 |
2,8 | 380 | 1,4 | 1,5 |
3,0 | 540 | 1,5 | 1,6 |
3,2 | 550 | 1,8 |
Таблица 5. Ориентировочные режимы стыковой сварки латуни и бронзы
Параметр | Сплав | ||
Л 62 | Бр.ОФ6,5-0,15 | ||
Толщина металла, мм | 3-5 | 2-5 | 5-8 |
Установочная длина (суммарная), мм | 30 | 30 | 45 |
Припуск на оплавление, мм | 15 | 15 | 22 |
Длительность оплавления, с | 3 | 3 | 9 |
Скорость оплавления перед осадкой мм/с | 11 | 11 | 6 |
Средняя скорость оплавления, мм/с | 5 | 5 | 2,5 |
Длительность осадки под током, с | 0,3 | 0,3 | 0,5 |
Давление осадки, МПа | 157 | 177 | 137-157 |
Удельная мощность при оплавлении, кВА/мм2 | 0,05 | 0,07 | 0,03-0,035 |
Удельная мощность при осадке, кВА/мм2 | 0,4 | 0,4 | 0,2 |
oitsp.ru
Сварка меди в домашних условиях, как варить медь инвертором?
Сваривание металлических деталей – это технологическая процедура, позволяющая получать неразъемные соединения посредством формирования связи между межмолекулярными и межатомными частицами материала при значительном нагреве до расплавления, пластической деформации. Точечная сварка меди в домашних условиях используется, как правило, для соединения многих металлов, их сплавов во всех производственных сферах, даже медицине.
Для осуществления сварочных работ могут использоваться разные источники энергии: трение, ультразвук, электрическая дуга, электрический ток. Современные технологии настолько совершенны, что работы, связанные со сварочным соединением металлических конструкций можно выполнять не только на промышленных предприятиях, но и в полевых условиях, на водоемах, под водой, даже в космосе.
Но, как и в любом виде деятельности существуют свои нюансы, преимущества и недостатки, требования к безопасности проведения работ и прочее. Так, при организации сварочных работ в домашних условиях с заготовками из меди, алюминия, латуни, нержавеющей стали необходимо соблюдать установленные меры предосторожности. Данный тип деятельности относится к особо опасным для здоровья человека: существует опасность поражения ультрафиолетовыми излучениями органов зрения, попадания расплавленного металла на кожу, поражения электрическим током и пр.
Технология газовой сварки меди
Газовая сварка меди в домашних условиях является самой распространенной технологией, применяемой в бытовых условиях. Получаемый сварочный шов по данной методике отличается высокой прочностью. Именно благодаря этому параметру газовая сварка пользуется большим спросом у домашних мастеров. Для выполнения соединения медных изделий на дому необходимо иметь под рукой:
- Сварочный аппарат
- Газовые горелки
- Баллоны с газом (ацетилен)
- Проволока из меди
- асбест
Некоторые советы опытных сварщиков
- Если толщина изделия из меди не больше 1 см, соединение можно производить одной горелкой.
- При толщине медного образца более 1 см уже нужно использовать сразу две горелки, вторая будет служить для подогрева.
- Чтобы снизить в данном случае отток тепловой энергии, дополнительно понадобятся асбестовые листы.
- Рекомендуется при сваривании медных изделий использовать электротехническую проволоку из меди, предварительно очищенную лакокрасочных изоляционных покрытий.
- Зачистка обязательно проводится и свариваемых краев изделий. Этим условием не стоит пренебрегать, так как от него зависит возможность образования закиси меди.
Все необходимые условия предварительной подготовки к сварочным работам выполнены. Значит можно приступать непосредственно к соединению подготовленных медных изделий.
Рекомендации
- Нагретые участки соединения, которые расположены вблизи друг к другу, нужно стараться не перегревать.
- Пламя концентрированное необходимо направлять перпендикулярно шву непосредственно на край проволоки.
- Проволока должна расплавляться раньше краев изделия. Процесс варения продолжается до тех пор, пока не сформируется весь шов до конца.
- Необходимо помнить, что приостановка незаконченного соединения способна привести к перегреванию некоторых участков изделия, соответственно закиси меди, формированию трещин.
- Законченный сварной шов обязательно проковывается.
- Для небольшой толщины изделий проволоку нужно вести холодной.
- Если толщина изделия составляет больше 0,5 см, тогда проволока должна быть разогрета до температуры 200 градусов. Допускается и большая температура, но не более 500 градусов, так как будет образовываться зернистость металла, который впоследствии станет довольно хрупким.
- Сварной, прокованный шов необходимо довести до температуры 500 градусов и мгновенно охладить.
На этом можно считать соединение медных деталей завершенным.
Аргонно-дуговая сварка медных образцов
Аргонно-дуговая сварка в домашних условиях выполняется при помощи сварочного оборудования с использованием постоянного тока, неплавящимися вольфрамовыми электродами. Процедура напоминает паяние изделий: электрод нагревается до высокой температуры. В результате медь начинает плавиться.
При такой методике сваривания важно мгновенно охлаждать соединяемые участки. Аргонно-дуговая сварка предусматривает использование аргона, медной присадочной проволоки, которая предварительно очищается от лакокрасочного изоляционного покрытия.
При значительной толщине медных заготовок сваривание производится с их предварительным нагреванием. Данная процедура обеспечит наиболее глубокое проникновение, усилит прочность соединения.
Сварка меди: область применение технологии
Аргоновая сварка применяется для проведения ремонта конструкций, изготовленных из меди. Она достаточно эффективно себя показала при выполнении сварочных работ на труднодоступных участках.
Аргонно-дуговая сварка достаточно востребована на производственных предприятиях, а при наличии соответствующего оборудования также успешно может применяться в бытовых условиях. Если в наличии есть инверторное оборудование для сварки, специальные плавкие электроды, процедуру соединения медных образцов можно осуществлять по технологии сваривания стальных изделий. Принципиальных отличий в данном случае практически нет. Но, при такой методике соединения намного сложнее сделать вертикальный шов, нежели горизонтальный.
Что необходимо знать об электродах, используемых для сваривания медных деталей
Чтобы сварочный шов получился высокого качества, рекомендуется применять электроды, покрытые специальным составом. Подобное покрытие необходимо для продуцирования шлака, образующегося с окислами металла. Оно не будет давать воздуху соприкасаться со сварным швом. Обмазка заполняет пустоты, формирующиеся в момент сваривания деталей за счет выгорания компонентов и впоследствии вводит новые компоненты в шов. Такая обмазка способствует лучшей устойчивости электрической дуги. Шлаковый слой, продуцируемый данным покрытием, будет замедлять охлаждение расплавленной меди, при этом из шва будет выходить больше газов.
Электроды, применяемые в процессе сваривания, подразделяются на два типа:
- плавящиеся – для их производства используется проволока из меди, стали, алюминия, чугуна;
- неплавящиеся – для их производства используется синтетический графит, электротехнический уголь.
При выборе электродов необходимо смотреть на их цвет:
- желтые электроды предназначены для образцов, выполненных из жаропрочных, коррозийно-стойких сталей;
- красные – используются для электродуговой сварки медных изделий;
- серые – для заготовок из цветных металлов;
- синие – предназначены для соединения теплоустойчивых компонентов.
Сваривание латунных конструкций
Сварка латуни в домашних условиях – это довольно сложная процедура, так как в состав латуни входит цинк, который при нагревании испаряется, в результате чего изделие теряет первоначальную прочность.
При осуществлении сварочных работ с латунными образцами выделяются вредные для человеческого здоровья вещества. С применением аргона процедура соединения латуни выполняется достаточно быстро – это большой технологический прорыв в сфере обработки металлов.
Сама латунь представляет собой сплав с цинком. Технология соединения деталей, изготовленных из латуни, считается сложной из-за испарения цинка при высоких температурах, данный химический элемент мгновенно окисляется, в результате чего формируется ядовитая тугоплавкая окись. Поэтому сварка латунных образцов должна производиться в специально оборудованных местах, оснащенных вытяжкой, сварщики должны работать в респираторах.
Основные требования, предъявляемые при сварке латуни
- Чистота процесса при использовании аргонно-дуговой сварки. Перед началом работ изделия тщательно зачищаются до характерного металлического блеска поверхности.
- На поверхности свариваемых деталей не должно быть окислов, при наличии которых их обязательно нужно убрать. Для этого используется азотная кислота. После выполнения такой очистки изделие промывается в горячей воде, затем сушится.
При необходимости соединения латунных изделий толщиной более 0,5 см – аргонодуговая сварка идеальный вариант. Электрод передвигается в проводящую зону горелки, кромки соединяемого металлического образца плавятся под влиянием электрической дуги.
При выполнении сваривания деталей аргоном ощущается характерный непрерывный треск, а сварочная дуга имеет удивительный цвет. Это все из-за наличия в сплаве цинка. Латунь в процессе соединения не прогорает, не отлетает отдельными кусками, так как она плавится. Опытные сварщики советуют варить латунь отдельными участками, не расплавлять ее сплошным слоем. При сплошном расплавлении материала существует вероятность прожигания металла.
Если необходимо заварить кратер, тогда рекомендуется постепенно уменьшать напряжение сварки, повышать длину дуги с отведением впоследствии ее в сторону от обрабатываемого изделия. В процессе такого соединения шов заполняется в полном объеме, поджаривание цинка приводит к его испарению, в результате чего в металле образуются дефекты. Чтобы уменьшить испарение данного химического элемента, необходимо увеличить в пламени наличие кислорода, использовать присадочные материалы, легированные бором, алюминием, кремнием.
Совет! При выполнении соединения деталей из латуни осуществляйте сварочные работы на улице, не пренебрегайте требований безопасности!
electrod.biz
Контактная сварка меди
Медь является уникальным по своим физико-химическим свойствам материалом. Она имеет достаточно высокую коррозийностойкость в различных средах и агрессивных воздействиях на металл. Эти технологические качества обуславливают весьма широкое использование меди в легкой и тяжелой промышленности.
К выполнению сварки меди контактным способом выдвигаются достаточно строгие требования. При чем от чистоты наплавляемого металла зависят требования, выдвигающиеся к проведению сварочных работ по данному металлу.
По своим физическим и химическим свойствам медь, в обычных температурах является инертным металлом, но при воздействие процесса нагрева ее поверхности она имеет свойство вступать во взаимодействие с кислородом, галогенам, серой и фосфором. Все эти факторы значительно затрудняют выполнение контактной сваркой меди и ее сплавов.
При выполнении сварки давлением необходимо принимать во внимание весьма маленький температурный диапазон позволяющий выполнять сварные работы давлением. В своем большинстве контактную сварку применяют для сваривания не только меди, но и соединений меди с бронзой и латунью. Для получения чистой контактной поверхности заготовок, необходимо проводить некоторые механические действия по ее очистки.
Также необходимо применять химическое травление и последующее тщательное смывание всех используемых кислот и щелочек для травления в проточной воде. Применение электродов зависит от выбранного способа выполнения сварных работ.
Так для роликовой и точечной контактной сварке широко используются электроды, изготовленные из тугоплавким металлов состоящие из вольфрама и молибдена. Рекомендуется использовать медь без примесей для обеспечения повышенного качества сварного шва. Из-за плохих литейных свойств меди очень большую роль при выполнении контактной сварки играет присадочный материал.
В качестве присадочного материала широко используется сплавы меди с достаточно большим содержанием раскислителей, которые в свою очередь обеспечивают получение в процессе выполнения работ качественного и плотного и прочного литого соединения.
Техническая медь, используемая, в качестве присадочного материала при сварке делится на пять марок, которые отличаются друг от друга количеством примесей содержащихся в металле. Такие примеси как бериллий повышают теплопроводность металла, а алюминиевые примеси повышают устойчивость к коррозии. Есть и такие примеси, которые способны ухудшать свойства. К этим элементам относятся водород, мышьяк и свинец. При сварке меди необходимо принимать во внимания все перечисленные выше показатели.
3g-svarka.ru
Контактная сварка меди
Для меди и ее сплавов контактная сварка затруднена вследствие их высокой электрической проводимости и теплопроводности, а также узкого диапазона температур, в котором металл может свариваться давлением. Свариваемость медных сплавов лучше, чем технической меди, так как они обладают пониженной электрической проводимостью и теплопроводностью. Однако не все сплавы свариваются одинаково хорошо. Чаще контактная сварка применяется для латуней и кремнистых бронз. Среди них хорошо свариваются α-латуни (например, марки Л68), электрическая проводимость , которых не более 28% электрической проводимости меди. Повышение содержания цинка в латуни приводит к ухудшению ее свариваемости вследствие уменьшения пластичности сплава. Уменьшение концентрации цинка неблагоприятно влияет на свариваемость, поскольку понижается электросопротивление сплава. Хорошо свариваются кремнистая бронза (до 4% Si, электрическая проводимость равна примерно 10% электрической проводимости меди) и медно-никелевые сплавы, например мельхиор (80% Сu, 20% Ni, электрическая проводимость . равна 8% электрической проводимости меди).
Для получения чистой контактной поверхности заготовок рекомендуется их очистка механическим способом, а также травлением в тетрахлорметане или растворе каустической соды с последующей тщательной промывкой в проточной воде. Для растворения пленки оксидов применяют травление в следующих смесях: 10% -ный раствор серной кислоты, бихромат натрия; серная кислота, фтористый алюминий и 6dхромат натрия.
Точечная и роликовая сварка меди.
Точечная и роликовая сварка меди возможна только с применением электродов из тугоплавких металлов, обладающих теплопроводностью и электрической проводимостью, более низкими, чем основной металл, для уменьшения отвода теплоты во время сварки (например, из вольфрама или молибдена). При использовании таких электродов поверхность деталей сильно нагревается, а местами расплавляется, портится внешний вид изделия и быстро изнашиваются электроды. В связи с этим точечная и роликовая сварка технической меди ограниченно пригодна для промышленного применения.
Качество сварных точечных швов можно повысить, используя теплоизолирующие прокладки (например, из нержавеющей стали), размещаемые между электродами и поверхностями свариваемых деталей, а также покрывая соприкасающиеся поверхности деталей, например, серебром.
Для медных сплавов применение мягких режимов нецелесообразно. Обычно длительность нагрева медных сплавов при точечной сварке ограничивается 0,2-0,4с. Точечная сварка латуни производится короткими импульсами при больших значениях сварочного тока. В связи с высокой электрической проводимостью латуни толщина свариваемых листов на одной и той же машине принимается примерно в 2 раза меньше, чем толщина листов из стали. Шовная сварка латуни требует относительно большого удельного давления электродов, чем точечная. При сварке латуни марки Л62 υCB= 1 м/мин обеспечивает прочный плотный шов. При ширине роликов, равной 3-5 мм, сварочный ток для латуни приблизительно определяется из уравнения
Таблица 1. Ориентировочные режимы точечной сварки латуни Л62
b, мм | Радиус поверхности электрода, мм | р, кПа | Р, кН | Iсв, кА | t, с | Потребляемая мощность, кВА |
0,5+0,5 | 50 | 67 | 1,3 | 1,6 | 0,1 | 68 |
1,0+1,0 | 50 | 98 | 1,8 | 18,3 | 0,2 | 95 |
1,5+1,5 | 70 | 78 | 2,6 | 26,8 | 0,2 | 167 |
3,0+3,0 | 150 | 117 | 3,9 | 38,6 | 0,35 | 290 |
Латунь малых толщин (0,05-0,5 мм) можно соединять конденсаторной сваркой.
При точечной сварке медных сплавов с высоким электросопротивлением (кремнистая бронза, мельхиор) по сравнению со сваркой малоуглеродистой стали ток увеличивают примерно на 25%, мощность на 50%, давление на электроды принимают близким давлению при сварке стали.
Стыковая сварка оплавлением.
Стыковая сварка оплавлением требует особой техники из-за трудности поддержания на торцах свариваемых деталей слоя жидкого металла, а также при прогреве их на значительную глубину для последующей осадки. Лучшие результаты получаются при осадке стыка под током. Установочную длину вылета медных деталей определяют по формуле:
где d – диаметр свариваемых стержней, мм. Скорость оплавления ориентировочно равна 10 мм/с. Цикл сварки не должен превышать 1-2 с. Прочность стыка прутков из меди марки Ml в среднем составляет 206-215,8 МПа, угол загиба 180°.
Таблица 2. Ориентировочные режимы шовной сварки латуни Л62
b, мм | Ширина роликов, мм | Р, кН | IСВ, кА | Потребляемая мощность, кВА |
0,5+0,5 | 3 | 2,45 | 22,3 | 110 |
0,5+0,5 | 3-4 | 2,45 | 25,5 | 140 |
1,0 + 1,0 | 4-5 | 3,7 | 27,0 | 160 |
Таблица 3. Ориентировочные режимы стыковой сварки оплавлением заготовок из меди
Параметр | Размер заготовки, мм | ||
Пруток, d=10 | Труба, 9,5×1,5 | Полоса, 44,5×10 | |
Установочная длина, мм | 20 | 20 | 20 |
Давление осадки, МПа | 372 | 284,5 | 216 |
Сварочный ток, к А | 33 | 20 | 60 |
Вторичное напряжение, В | 6 | 5 | 10 |
Удельная мощность, кВА/мм2 | 2,6 | 2,7 | 1,4 |
Медь соединяют стыковой сваркой сопротивлением. Провод и прутки из чистой меди диаметром 7-16 мм сваривают при i=380 А/мм2 и средней температуре нагрева 0,7-0,75Тпл. Начальное давление составляет 0,98-2,9 МПа, а конечное 343,4-392,4 МПа. Концентрированный нагрев контактной зоны и большие скорости осадки (150-250 мм/с) исключают разупрочнение металла и обеспечивают высокие пластические и электрические свойства соединений. Для соединения медных проволок успешно применяется стыковая конденсаторная сварка. Латунь и бронза соединяются стыковой сваркой легче, чем медь. Для их сварки требуются большие конечные скорости оплавления и осадки. Хорошо соединяются стыковой сваркой заготовки из деформируемых бронз марок Бр.Х0,5; Бр.ОФ6,5-0,15; Бр.АМц9-2. Поскольку скорость охлаждения бронзы значительно больше, чем стали, и бронза в интервале температур 750-770° С имеет достаточно высокую прочность, при ее сварке давление должно быть выше, чем при сварке стали. В ряде случаев для повышения пластичности сварных соединений рекомендуется их последующая термическая обработка: для соединений из бронзы типа Бр.Х0,5 – закалка в воде от 950-980°С, из бронзы Бр.ОФ6,5-0,15 отжиг при 500-550 °С (его можно дать после сварки на машине).
Таблица 4. Ориентировочные режимы стыковой конденсаторной сварки медной проволоки
dпр, мм | СК, мкФ | U, кВ | Усилие осадки, кН |
1,6 | 256 | 0,9 | 1,4 |
2,0 | 380 | 1,0 | 1,4 |
2,8 | 380 | 1,4 | 1,5 |
3,0 | 540 | 1,5 | 1,6 |
3,2 | 550 | 1,5 | 1,8 |
Таблица 5. Ориентировочные режимы стыковой сварки латуни и бронзы
Параметр | Сплав | ||
Л 62 | Бр.ОФ6,5-0,15 | ||
Толщина металла, мм | 3-5 | 2-5 | 5-8 |
Установочная длина (суммарная), мм | 30 | 30 | 45 |
Припуск на оплавление, мм | 15 | 15 | 22 |
Длительность оплавления, с | 3 | 3 | 9 |
Скорость оплавления перед осадкой мм/с | 11 | 11 | 6 |
Средняя скорость оплавления, мм/с | 5 | 5 | 2,5 |
Длительность осадки под током, с | 0,3 | 0,3 | 0,5 |
Давление осадки, МПа | 157 | 177 | 137-157 |
Удельная мощность при оплавлении, кВА/мм2 | 0,05 | 0,07 | 0,03-0,035 |
Удельная мощность при осадке, кВА/мм2 | 0,4 | 0,4 | 0,2 |
oitsp.ru
Электроды для контактной сварки. Виды и рекомендуемый материал
Точечная сварка, благодаря появлению компактных ручных аппаратов типа BlueWeldPlus, становится популярной не только при промышленных масштабах применения, но и в быту. Слабым местом такой технологии являются электроды для контактной сварки: их низкая стойкость во многих случаях отпугивает потребителя.
Причины недолговечности электродов контактной электросварки
Процесс контактной сварки состоит из следующих стадий:
- Предварительной подготовки поверхности соединяемых деталей – она должна быть непросто очищена от загрязнений и окислов, но и очень ровной, чтобы исключить неравномерность возникающего напряжения электрического поля.
- Ручного или механического прижима свариваемых изделий – с увеличением усилия прижима растут интенсивность диффузии и механическая прочность сварного шва.
- Локального расплавления металлов в зоне прижима теплом электрического тока, в результате чего формируется сварочное соединение. Прижим электродов на этой стадии препятствует образованию сварочных брызг.
- Отключения тока и постепенного остывания сварного шва.
Таким образом, материал электродов для контактной сварки претерпевает не только значительные термические напряжения, но и механические нагрузки. Поэтому к нему предъявляется ряд требований – высокая электропроводность, высокая термическая стойкость (в том числе – и от постоянных колебаний температуры), повышенные значения предела прочности на сжатие, малый коэффициент теплоёмкости. Таким комплексом свойств обладает ограниченное число металлов. В первую очередь – это медь, и сплавы на её основе, однако и они не всегда удовлетворяют производственным требованиям.
В связи с постоянным повышением энергетических характеристик производимых сварочными клещями для точечной сварки многие торговые марки ориентируют потребителя на применение только «своих», фирменных электродов, что не всегда соблюдается. В результате снижается качество сварных швов, получаемых по такой технологии, подрывается доверие к самому процессу контактной электросварки.
Преодоление указанных проблем производится двумя путями: совершенствованием видов и конструкций сварочных электродов для точечной сварки, и разработкой новых материалов, используемых для изготовления таких электродов. Для частных пользователей имеет значение также и цена вопроса.
Материалы электродов
Согласно ГОСТ 2601, критерием качества готового шва является его прочность на разрыв или сдвиг. Она зависит от интенсивности тепловой мощности в зоне электрического разряда, а потому связывается в первую очередь с теплофизическими характеристиками материала электродов.
Использование медных электродов малоэффективно по двум причинам. Во-первых, медь, являясь высокопластичным металлом, не обладает достаточной упругостью, чтобы в период между рабочими циклами полностью восстановить геометрическую форму электродов. Во-вторых, медь весьма дефицитна, а частая замена электродов обуславливает и высокие финансовые затраты.
Попытки использовать более твёрдую, упрочнённую медь успеха не имеют: для нагартованного материала параллельно с повышением твёрдости снижается температура рекристаллизации, поэтому с каждым рабочим циклом износ рабочего торца электрода для контактной сварки будет возрастать. Поэтому практическое применение получили медные сплавы с добавлением ряда других металлов. В частности, введение в медный сплав кадмия, бериллия, магния, цинка и алюминия мало изменяет показатель теплопроводности, зато улучшает твёрдость при нагреве. Стойкость электрода от динамических тепловых нагрузок увеличивают железо, никель, хром и кремний.
При подборе оптимального материала сварочных электродов для контактной сварки ориентируются на показатель удельной электропроводности сплава. Чем меньше он будет отличаться (в меньшую сторону) от электропроводности чистой меди – 0,0172 Ом·мм2/м, тем лучше.
Наиболее эффективную стойкость против износа и деформации показывают сплавы, в состав которых входят кадмий (0,9…1,2%), магний (0,1…0,9%) и бор (0,02…0,03%).
Выбор материала для электродов точечной сварки зависит также и от конкретных задач процесса. Можно выделить три группы:
- Электроды, предназначенные для проведения контактной сварки в жёстких условиях (непрерывное чередование циклов, поверхностные температуры до 450…500ºС). Их изготавливают из бронз, содержащих хром и цирконий (Бр.Х, Бр.ХЦр 0,6-0,05. В эту же группу включают никель- кремнистые бронзы (Бр.КН1-4), а также бронзы, дополнительно легированные титаном и бериллием (Бр.НТБ), используемые для точечной сварки нержавеющих и жаропрочных сталей и сплавов.
- Электроды, применяемые при контактных температурах на поверхности до 250…300ºС (сварка обычных углеродистых и низколегированных сталей, медных и алюминиевых изделий). Их производят из медных сплавов марок МС и МК.
- Электроды для относительно лёгких режимов эксплуатации (поверхностные температуры до 120…200ºС). В качестве материалов применяется кадмиевая бронза Бр.Кд1, хромистая бронза Бр.Х08, кремненикелевая бронза Бр.НК и др. Такие электроды могут использоваться также и для роликовой контактной электросварки.
Следует отметить, что по убыванию удельной электропроводности (по отношению к чистой меди) эти материалы располагаются в следующей последовательности: Бр.ХЦр 0,6-0,05→МС→МК→Бр.Х→Бр.Х08→Бр.НТБ→Бр.НК →Бр.Кд1→Бр.КН1-4. В частности, разогрев до требуемой температуры электрода, изготовленного из бронзы Бр.ХЦр 0,6-0,05 произойдёт примерно вдвое быстрее, чем полученного из бронзы Бр.КН1-4.
Конструкции электродов
Наименее стойким местом электрода является его сферическая рабочая часть. Электрод бракуется, если увеличение размеров торца превышает 20% от первичных размеров. Конструкция электродов определяется конфигурацией свариваемой поверхности. Различают следующие исполнения инструмента
- С цилиндрической рабочей частью и конической посадочной частью.
- С коническими посадочной и рабочей частью, и переходным цилиндрическим участком.
- Со сферическим рабочим торцом.
- Со скошенным рабочим торцом.
Кроме того, электроды могут быть сплошными и составными.
При самостоятельном изготовлении (либо перезаточке) рекомендуется выдерживать следующие соотношения размеров, при которых инструмент будет обладать максимальной стойкостью:
- Для расчёта диаметра электрода d пользуются зависимостью Р = (3…4)d2, где Р – фактически необходимое сжатие электродов при проведении процесса контактной электросварки. В свою очередь, рекомендуемые значения давления осадки, при котором получаются наиболее качественные соединения, составляет 2,5…4,0 кг/мм2 площади получаемого сварного шва;
- Для электродов с конической рабочей частью оптимальный угол конусности варьируется от 1:10 (для инструмента с диаметром рабочей части до 30…32 мм) до 1:5 – в противоположном случае;
- Выбор угла конуса определяется также и наибольшим усилием сжатия: при максимальных усилиях рекомендуется принимать конусность 1:10, как обеспечивающую повышенную продольную стойкость электрода.
Основные формы электродов для контактной сварки устанавливает ГОСТ 14111, поэтому, применяя те или иные соотношения размеров, следует учитывать размеры посадочного пространства под инструмент для конкретной модели машины контактной сварки.
Значительную экономию материала даёт применение составных конструкций. При этом для изготовления корпуса применяют материалы с высокими значениями электропроводности, а съёмную рабочую часть изготавливают из сплавов с высокой твёрдостью и износостойкостью (в том числе и термической). В частности, подобным сочетанием свойств обладают металлокерамические сплавы от швейцарской фирмы АМРСО марок A1W или A1WC, содержащие 56% вольфрама и 44% меди. Их электропроводность достигает 60% от электропроводности чистой меди, что определяет малые потери на нагрев при выполнении сварки. Рекомендуемым материалом могут быть и бронзовые сплавы с добавками хрома и циркония, а также вольфрам.
Электроды для контактной сварки лёгких сплавов, где не требуется значительного усилия прижима, выполняют со сферической рабочей частью, а для контактных губок аппаратов точечной электросварки целесообразно применять кремнистые бронзы.
Механические характеристики электродов должны находиться в следующих пределах:
- Твёрдость по Бринеллю, НВ – 1400…2600;
- Модуль Юнга, ГПа – 80…140;
- Предельный изгибающий момент, кгсм – не ниже 750…800.
Конструкции электродов всегда должны быть полыми, для обеспечения эффективного охлаждения.
proinstrumentinfo.ru
Контактная сварка меди
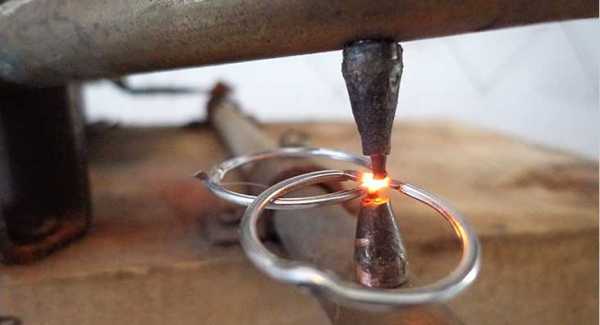
Этот способ насчитывает несколько разновидностей. Они имеют свои технологические особенности и применяются в тех или иных случаях. Однако два способа, а именно шовная и точечная сварка медных элементов, практически не используется. Обработка стыков с помощью оплавления происходит с затруднениями, так как связана с некоторыми сложностями. Для такого способа на торцах изделия в местах сварочных работ требуется постоянно поддерживать слой расплавленного металла.
Также неудобство вызывает необходимость поддержания определенной температуры на торцах обрабатываемого изделия. Прогревать металл требуется довольно глубоко, иначе последующая его осадка будет затруднена. Чаще всего для осуществления такой осадки нужно воздействовать на медь с помощью довольно большого давления, примерно до 400 МПа.
Особенности стыковой контактной сварки
Этот вид обработки особо распространен при соединении медных трубопроводов, ленты или проволоки. Чаще всего медь выступает не в чистом виде, а в виде её различных сплавов.
При проведении стыковой контактной сварки образовывается намного меньше искр, чем при аналогичной обработке черных металлов. При обработке медных изделий искры похожи на крупные капли расплавленного металла, а не на искрящийся сноп огней. Для получения высококачественного шва нужно произвести осадку стыков под воздействием тока. В случае применения такой тактики вы получите довольно прочный шов. Он не будет уступать в прочностных характеристиках самой меди, поэтому детали с таким соединением будут выдерживать значительные нагрузки.
Широкое практическое применение имеет способ соединения проволоки методом разряда конденсатора с высоким вольтажом.
Примерные режимы стыковой контактной сварки
Параметры режима сварки | Пруток, диаметром 10мм | Труба 9,5х1,5мм | Лента 44,5х10мм |
Установочная длина, мм | 20 | 20 | – |
Припуск на оплавление, мм | 12 | – | – |
Припуск на осадку, мм | 8 | – | – |
Скорость оплавления, мм/сек | 8 | – | – |
Скорость осадки, мм/сек | 200 | – | – |
Удельное давление осадки, МПа | 372,2 | 284,4 | 215,7 |
Удельная мощность, кВт/мм2 | 2,6 | 2,66 | 1,35 |
Сила сварочного тока, кА | 33 | 20 | 60 |
Вторичное напряжение, В | 6 | 5 | 10 |
Ориентировочные режимы сварочных работ с помощью разряда конденсатора
Диаметр проволоки, мм | Ёмкость конденсатора, мкФ | Напряжение заряда, В | Начальное расстояние в стыке, мм | Усилие осадки, Н |
1,6 | 256 | 900 | 14 | 1373 |
2,0 | 380 | 1000 | 15 | 1373 |
2,8 | 380 | 1400 | 16 | 1471 |
3,0 | 440 | 1500 | 16 | 1569 |
3,0 | 1200 | 1000 | 9 | 1177 |
3,0 | 1200 | 800 | 5 | 1177 |
3,0 | 550 | 1400 | 5 | 1471 |
3,0 | 540 | 1300 | 8 | 1569 |
3,0 | 540 | 1500 | 12 | 1569 |
3,2 | 550 | 1500 | 14 | 1765 |
Относительная длина вылета элементов определяется по формуле L=(2,0…2,5)d.
Где L – длина вылета, а d – диаметр изделия. Считается в миллиметрах.
Оплавление происходит со скоростью около 10 миллиметров в секунду. Весь цикл сварочных работ в основном занимает 1-2 секунды. При сваривании медных прутков марки M1 прочность шва будет составлять от 206 до 216 МПа. Угол загиба составляет 180 градусов. Твердость сварного шва немного выше, чем твердость основного материала.
atl-met.ru
способы (аргоном, дуговая, газовая, контактная, точечная), электроды (угольные, графитные), технология, припой, аппарат, трудности
В домашних условиях часто возникает необходимость сварки меди в процессе установки водопроводов и систем отопления. В большинстве случаев водопроводные трубы изготавливаются из меди. Материал имеет гладкое основание, не поддается коррозии, способен обеспечить хороший ток воды и не имеет каких-либо вредных веществ.
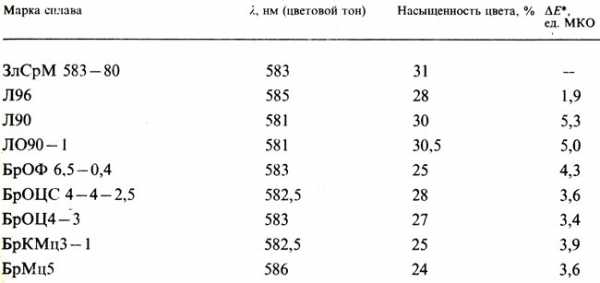
Цветовые характеристики сплавов меди.
Сварка – это процесс образования неразъемных соединений между разными элементами. Этого можно достичь путем нагрева свариваемых металлов или их деформирования. Для сварки используются различные источники энергии:
- пламя от газа;
- электрическая дуга;
- ультразвук;
- лазерное излучение и др.
Процесс сварки меди значительно отличается от сварки сталей, так как цветные металлы имеют высокий уровень теплопроводности, а в расплавленном состоянии они будут реагировать с газами. Чтобы избежать возникновения негативных последствий, понадобится правильно выбрать материалы для сварки, произвести подготовку соединяемых элементов и соблюдать инструкцию по сварке.
Читайте также:
Как производится сварка чугуна.
Какова технология выполнения сварного шва.
На сегодняшний день сделать сварку можно не только на предприятиях, но и в домашних условиях. Следует знать, что процесс сварки меди имеет большое количество нюансов. Во многом сварка будет зависеть от физико-химических свойств материала.
Трудности сварки меди связаны со склонностью материала к окислению в расплавленном состоянии, высоким уровнем теплопроводности, высоким уровнем линейного расширения металла в процессе нагревания и высокой текучестью.
Свариваемость металла может ухудшиться при наличии в нем серы, свинца и других элементов. Свинец придаст подобному металлу хрупкости.
Контактная сварка своими руками.
В процессе сварки меди кислород будет поглощаться из атмосферы, потому следует это учитывать.
На сегодняшний день существует несколько различных способов сварки данного цветного металла.
Элементы, которые будут необходимы для того, чтобы самостоятельно произвести качественную сварку меди:
- Баллоны с ацетиленом.
- Горелки.
- Асбестовые листы.
- Проволока.
- Вода.
- Профилированная проставка.
- Припои.
- Флюсы.
Что нужно знать об электродах для сварки меди?
Конструкция трансформаторов для точечной сварки.
Чтобы получить качественный и ровный сварочный шов, следует использовать электрод, который покрыт особым составом. Покрытие используется для продуцирования шлака, который появляется с окислами металла. Состав будет препятствовать соприкосновению шва сварки с воздухом. Обмазка заполнит убыль, которая образуется в процессе сварки за счет выгорания элементов и вводит в шов новые элементы. Благодаря обмазке будет увеличена устойчивость электрической дуги. Шлаковый покров, который продуцируется подобным покрытием, будет замедлять остывание расплавленной меди, в результате чего из шва выделится большее количество газов.
Электроды, которые используются в процессе соединения металлов, можно разделить на 2 вида:
- Плавящиеся, которые изготавливаются из медных, алюминиевых, стальных или чугунных проволок.
- Неплавящиеся, которые изготавливаются из электротехнического угля, синтетического графита и других элементов.
Чтобы подобрать подходящие электроды, понадобится обратить внимание на их цвет:
- Электроды красного цвета используются для электродуговой сварки меди.
- Синие электроды применяются для обработки теплоустойчивых элементов.
- Электроды желтого цвета применяются для заготовок из коррозийностойких и жаропрочных сталей.
- Электроды серого цвета можно использовать для обработки цветных металлов.
Газовый метод сварки меди
Технология газовой сварки.
Если соблюдать технологию, то медь можно с легкостью сварить баллонами с ацетиленом. Сварное соединение отличного качества есть возможность получить путем проковки шва.
Медь имеет высокий уровень теплопроводности, потому для ее сварки понадобится пламя высокой мощности, 150 л/час, если есть материал толщиной менее 10 мм, и 200 л/час, если есть материал толщиной более 10 мм. Если производится сварка меди большой толщины, то понадобится использовать две горелки. Одна из них – для подогрева, а другая – для сварки деталей.
Чтобы уменьшить отвод теплоты, с нижней и верхней частей элемента понадобится уложить асбестовые листы. В данном случае рекомендуется использовать восстановительное пламя, ядро которого ориентируется к кромкам меди практически под прямым углом. Для уменьшения формирования закиси металла и предотвращения появления трещин высокой температуры понадобится производить соединение металлов с максимальной скоростью, без перерывов. В процессе нужно строго следить за сбережением восстановительного пламени.
Перед соединением элементов прихватки применять не нужно. Сварка меди производится в специальной сборочно-сварочной конструкции. В качестве присадки можно использовать проволоку из прочного металла или материала с раскислителями. Диаметр используемой проволоки должен быть не более 8 мм.
Расчет расхода защитного газа при сварке.
В процессе сварки тепло нужно распределять так, чтобы проволока расплавилась раньше кромок свариваемого металла. Присадочный материал должен наплавиться на кромки. Скос кромок на листах толщиной больше 3 мм производится под углом 45°. Перед соединением кромки надо будет зачистить до блеска нового металла. Можно также протравить кромки при помощи смеси азотной кислоты, после чего промыть водой.
Для измельчения зерен наплавленной меди и повышения плотности сварных швов после соединения материал толщиной до 5 мм нужно проковывать при низкой температуре. Если используется медь толщиной более 5 мм, то проковывать нужно при температуре 200-300°С.
Шов подвергается отжигу после проковки швов при температуре 530-550°С, после этого быстро охлаждается водой. Для предотвращения появления трещин не нужно вести проковку при температуре более 500°С, так как в таком случае металл станет хрупким.
Соединение металла аргонодуговым методом
Аргонная сварка своими руками.
Дуговая сварка плавлением часто используется для получения сварных конструкций из меди. Для того чтобы получить шов сварки высокого качества, понадобится применять защитные газы, в качестве которых выступает аргон. Дуговая сварка меди чаще всего производится вольфрамовым электродом.
В качестве присадки понадобится использовать профилированную проставку небольшой ширины или проволоку, которую нужно будет заложить встык. Подобный метод сварки меди отличается хорошей устойчивостью дуги. Механическая дуговая сварка используется в процессе соединения деталей маленькой толщины и в местах, доступ в которые затруднен.
Сварка меди вольфрамовым электродом производится при постоянном токе. Электрод должен находиться строго в плоскости стыка. Если сваривается медь толщиной более 5 мм, то ее понадобится предварительно прогреть до температуры 300-400°С. Кромки соединяемого металла и проволоку электрода рекомендуется первым делом зачистить до состояния нового металла.
Материал толщиной до 5 мм может свариваться без зачистки кромок.
Если производится соединение деталей толщиной 2-3 мм, то прогрев свариваемого металла выполнять не нужно. Технология сварки подобного металла толщиной более 4 мм подразумевает прогрев металла до 300-400°С. В данном случае можно использовать и плавящиеся электроды.
Как правильно самостоятельно паять медь?
Схема капиллярной пайки.
Следует знать, что цветные металлы гораздо легче паять, чем сваривать. Особенно это касается медных труб с тонкими стенками, которые применяются для систем отопления, водопровода, газопровода и т.д.
Произвести пайку металла может даже человек без соответствующего опыта работы, но сваривать металл самому не получится. Структуру меди пайка изменять не будет. В данном случае не понадобится использовать какое-либо дорогостоящее оборудование.
Соединения пайки в случае соблюдения технологии и применения материалов хорошего качества получатся прочными, они смогут выдерживать нагрузки.
В процессе пайки подобного материала понадобится использовать нахлесточные способы соединений, которые дают возможность получить высокую прочность заготовок, даже если использовались мягкие припои, имеющие сравнительно малую прочность. Чтобы обеспечить приемлемый уровень прочности шва пайки, понадобится делать нахлест не менее 5 мм. Чаще всего применяются более высокие показатели для обеспечения большого запаса прочности.
Существующие виды припоев
Сплавы меди есть возможность соединять пайкой высокой и низкой температуры. На сегодняшний день можно найти достаточно большое количество оборудования для сварки подобного металла и его пайки, а также различные твердые и мягкие припои, которые способны обеспечить отличное качество пайки элементов. Для пайки при низкой и высокой температурах предпочтительнее всего использовать припой и флюс одинакового изготовителя.
Низкотемпературные припои
Сварка меди в среде инертных газов.
Использование низкотемпературных припоев дает возможность производить соединение элементов при температуре, которая мало влияет на прочность металла, но предоставляет швы с не лучшими механическими характеристиками. Припой для пайки при высокой температуре способен обеспечить хорошую прочность швов и позволяет эксплуатировать систему при высокой температуре. Однако в данном случае может произойти отжиг металла, в связи с чем работу может произвести лишь квалифицированный специалист.
Пайка при низкой температуре чаще всего используется при монтаже системы отопления. Следует знать, что низкотемпературные припои смогут обеспечить отличную прочность соединений, если учитывать большую площадь контакта трубопроводных элементов.
На сегодняшний день существуют такие низкотемпературные припои, которые гарантируют отличное качество пайки меди: сплавы олова с медью, сурьмой, серебром и другими элементами. Для пайки при низкой температуре можно использовать и припои из свинца и олова, однако если понадобится соединить трубопровод для питьевой воды, то их использовать не допускается в связи с вредными свойствами свинца.
Высокотемпературные припои
Сварка неплавящимся электродом.
Припои такого типа допускается применять в случае, когда надо будет паять трубопровод при высокой температуре.
Если понадобится спаять трубопровод из металлических труб, следует использовать лишь пайку при высокой температуре, так как в таком случае можно будет получить соединение отличной прочности. Следует знать, что пайка при низкой температуре в газоснабжении не используется.
Припои из меди и фосфора не требуют обязательного использования флюсов в процессе пайки. Характеристики расширения подобного металла и припоя практически одинаковы, что является дополнительным преимуществом. Твердые припои производятся в форме прута.
Данное соединение является хрупким, потому подобные припои ни в коем случае нельзя использовать для пайки материалов с содержанием никеля более 10%. Применять такие припои не допускается и для соединения алюминиевой бронзы.
Флюсы для соединения медных заготовок
Флюс для аргонодуговой сварки изделий из медных сплавов.
В процессе соединения подобных элементов лучше всего использовать специальные устройства для сварки металлических элементов и флюсы, которые способны защитить расплавленную медь от окисления, растворить и превратить появившиеся окислы в шлаки. Их понадобится вносить в ванну сварки. Флюсами можно покрыть концы кромки соединяемых деталей и прутьев, а также заднюю часть свариваемой заготовки.
На сегодняшний день для соединения металлов при низкой температуре в качестве флюсов чаще всего используются составы, в которых содержится хлорид цинка. В процессе приобретения флюса важно уделить внимание его составу. Флюсы могут состоять из прокаленной буры и других элементов.
На сегодняшний день можно найти большое количество флюсов для пайки подобного металла. Понадобится лишь выбрать любой состав, который подходит для работы данного вида.
Сварка меди в домашних условиях значительно отличается от процесса сварки остальных металлов, так как медь имеет некоторые особенности. Целесообразнее производить пайку подобного металла. Материал раскисляется, а окислы удаляются в шлак, потому обязательно понадобится использовать подходящие припои и флюсы.
moyasvarka.ru