Сварные швы гост обозначение на чертеже: ГОСТ 2.312-72* «ЕСКД. Условные изображения и обозначения швов сварных соединений»
alexxlab | 04.01.2023 | 0 | Разное
виды швов и соединений
В процессе выполнения сварочных работ получают различные соединения. Сварочные швы способны соединять не только металлы, но и другие разнородные материалы. Стыковочные элементы в цельном узле представляют собой соединение, которое можно разграничить на несколько участков.
Зоны сварного соединения
Соединение, полученное в процессе сварки, делится на следующие зоны:
- Место сплавления – граница между основным металлом и металлом полученного шва. В этой зоне находятся зерна, отличающиеся по своей структуре от состояния основного металла. Это связано с частичным расплавлением в процессе сварки.
- Зона термического влияния – зона основного металла, не подвергшегося оплавлению, хотя при нагреве металла его структура изменилась.
- Сварочный шов – участок, образовавшийся при кристаллизации при остывании металла.
Виды сварных соединений
В зависимости от расположения соединяемых изделий по отношению друг к другу соединения подразделяются на следующие виды:
- Встык.
Склеивание элементов конструкции осуществляется в одной плоскости торцами, обращенными друг к другу. В зависимости от толщины соединяемых деталей торцы могут быть смещены по вертикали друг относительно друга.
- Косынка. В этом случае концы выравниваются под углом. Процесс сварки осуществляется на смежных кромках деталей.
- Перекрытие. Сварочные детали располагаются параллельно с частичным перекрытием.
- Концевое соединение. Свариваемые элементы выравниваются параллельно друг другу и состыковываются по концам.
- Тройник. При этом конец одного куска примыкает к боковой части другого под углом.
Сварные соединения также характеризуют виды сварочных швов, которые можно классифицировать по некоторым признакам.
Индексы сварки
Существует несколько параметров, по которым можно охарактеризовать все полученные сварочные швы:
- Ширина – размер между границами шва, по которым проведены видимые линии сплавления;
- Корень шва – обратная его сторона, расположенная на максимальном расстоянии от лицевой;
- Выпуклость – определяется в наиболее выпуклой части шва и обозначается расстоянием от плоскости основного металла до границы наибольшего выступа;
- Вогнутость – данный показатель актуален, если она имеет место в сварном шве, т.
к., по сути, является дефектом; Этот параметр определяют в том месте, где шов имеет наибольший прогиб – от него до плоскости основного металла измеряют величину вогнутости;
- Шов – выполняется только в угловом и Т-образном стыке; Это измеряется наименьшим расстоянием от боковой поверхности одной свариваемой детали до граничной линии шва на поверхности второй.
Виды швов по способу выполнения
- Швы односторонние сварные. Их выполняют с полным проваром металла по всей длине.
- Двустороннее исполнение. По технологии после выполнения односторонней сварки корень шва удаляют, и только потом производят сварку с другой стороны.
- Однослойные швы. Выполнена однопроходная сварка одним плавящимся валиком.
- Многослойные швы. Их применение целесообразно при большой толщине металла, то есть когда сварка за один проход невозможна по технологии. Шовный слой будет состоять из нескольких валиков (проходов). Это позволит ограничить распространение зоны термического воздействия и получить прочный и качественный сварной шов.
Виды сварных швов по их пространственному положению и протяженности
Различают такие положения сварки:
- Снизу, когда сварной шов находится в нижней горизонтальной плоскости, т.е. под углом 0° по отношению к земле;
- Горизонтальный, направление сварки горизонтальное, а деталь может находиться под углом от 0º до 60º;
- Вертикальное, в этом положении свариваемая поверхность находится в плоскости от 60º до 120º, а сварка ведется в вертикальном направлении;
- Потолочный, когда работы ведутся под углом 120-180º, то есть сварочные швы располагаются над мастером;
- «В лодке» это касается только угловых или тавровых соединений, деталь устанавливается под углом, а сварка производится «в угол».
Разбивка по длине:
- Непрерывные, поэтому почти все швы выполняются, но есть исключения;
- Прерывистые швы, встречаются только в угловых соединениях; Двусторонние швы этого типа могут выполняться как в шахматном, так и в цепочном порядке.
Обрезка кромок
Эта конструктивная особенность используется, когда толщина металла, используемого для сварки, превышает 7 мм. Обрезка кромок – это снятие металла с кромок в определенной форме. Этот процесс выполняется при сварке однопроходных стыковых швов. Это необходимо для того, чтобы получить правильный сварной шов. Что касается толстого материала, то резка необходима для того, чтобы расплавить первоначальный корневой проход и затем наварить следующие валки, равномерно заполняя полость, чтобы сварить металл по всей толщине.
Обрезку кромок можно выполнять при толщине металла не менее 3 мм. Потому что его более низкое значение приведет к ожогам. Резка характеризуется такими конструктивными параметрами: зазор – R; Угол режущих кромок – α; Притупление – с. Расположение этих параметров показывает чертеж сварочного шва.
Режущие кромки увеличивает количество расходных материалов. Поэтому эту сумму стараются всячески минимизировать. Делится на несколько типов конструктивного исполнения:
- V-образный;
- Х-образный;
- Y-образный;
- U-образный;
- Щель.
Особенности разделки кромок
При малых толщинах свариваемого материала от 3 до 25 мм обычно применяют одностороннюю V-образную резку. Скос может быть выполнен на обоих концах или на одном из них. Металл толщиной 12-60 мм целесообразно сваривать двусторонней Х-образной разделкой. Угол α для резки в форме X, V равен 60°, если скос выполнять только на одной кромке, то значение α будет равно 50°. Для толщины 20-60 мм наиболее экономичен расход металла шва при П-образной разделке. Скос также может быть выполнен по одному или с обоих концов. Притупление составит 1-2 мм, а величина зазора 2 мм. При большой толщине металла (свыше 60 мм) наиболее эффективным способом является продольная кромочная резка. Для сварного соединения эта процедура очень важна, она влияет на несколько факторов шва:
- Исправность соединения;
- Прочность и качество сварного шва;
- Эконом.
Стандарты и ГОСТы
- Ручная дуговая сварка. Сварные швы и стыки по ГОСТ 5264-80 включают виды, расчетные размеры для сварки, покрываемые электродами во всех пространственных положениях.
Сюда не входят только стальные трубопроводы.
- Сварка стальных трубопроводов. ГОСТ 16037-80 – определяет основные виды, разделку кромок, конструктивные размеры при механизированном способе сварки.
- Сварка трубопроводов из меди и медно-никелевых сплавов. ГОСТ 16038-80.
- Дуговая сварка алюминия. Сварные швы. ГОСТ 14806-80 – Форма, размеры, подготовка кромок под ручную и механизированную сварку алюминия и его сплавов, процесс проводят в защитной среде.
- Под флюсом. ГОСТ 8713-79 – сварку швов и стыков выполняют автоматической или механизированной сваркой на весу, на флюсовой подушке. Он распространяется на металл толщиной от 1,5 до 160 мм.
- Сварка алюминия в инертных газах. ГОСТ 27580-88 – стандарт на ручную, полуавтоматическую и автоматическую сварку. Выполняется неплавящимся электродом в инертных газах с присадочным материалом и распространяется на алюминий толщиной от 0,8 до 60 мм.
Обозначение сварного шва
Согласно нормативным документам наличие сварных швов показывают на сборочных чертежах или в общем виде. Сварные швы показаны сплошными линиями, если они видны. А если наоборот – то пунктиром. От этих линий назначаются выноски с односторонними стрелками. Обозначение сварочных швов выполняется на полке от выноски. Надпись делается над полочкой, если шов с лицевой стороны. В обратном варианте обозначение будет под полкой. Сюда включается информация о шве в следующей последовательности:
- Вспомогательные знаки. На пересечении выноски с полкой может быть значок:
○ – закрытый шов;
┐ – сварка шва производится при монтаже.
- Обозначение сварных швов, их конструктивных элементов и соединений ГОСТ.
- Наименование шва по стандарту.
- Метод сварки в соответствии с нормативными стандартами.
- Указан катет, этот пункт относится только к угловым соединениям.
- Прерывистость шва, если таковой имеется. Здесь вы указываете шаг и расположение сегментов сварки.
- Дополнительные значки дополнительных значений. Считайте их отдельным пунктом.
Вспомогательные обозначения
Эти знаки также наносят сверху полки, если на чертеже виден сварочный шов, и под ним, когда невидим:
- Снятие арматуры;
- Обработка поверхности, обеспечивающая плавный переход к основному металлу, устранение задиров и неровностей;
- Шов выполняется по открытой линии; Этот знак относится только к видимым на чертеже сварным швам;
- Чистота обработки поверхности сварного соединения.
Для простоты, если все швы конструкции выполнены по одному ГОСТу, имеют одинаковые кромки и размеры, обозначение и норма сварки указываются в технических требованиях. В дизайне может быть не все, а большое количество одинаковых швов. Затем их делят на группы и присваивают им порядковые номера в каждой группе отдельно. На одном шве указывают полное обозначение. На остальных ставятся только порядковые номера. Количество групп и количество швов в каждой из них должны быть указаны в нормативной документации.
Стандартные ручные стеллажи для поддонов | Полезная информация
Сегодня практически в каждой стране существуют свои стандарты работы ассоциации производителей паллетного стеллажного и стеллажного оборудования (например, в Великобритании это SEMA). Более 10 лет назад Федерация европейских производителей (отдел стеллажного оборудования) рекомендовала использовать стандарты проектирования и эксплуатации стеллажей. Паллетные стеллажи ФЭМ 10.2.02. – Стандартный дизайн и МКЭ 10.3.01 – компоненты допуска.
В России производство и эксплуатацию паллетных стеллажей регламентируют следующие стандарты:
– ГОСТ 14757_81 Cтеллажи сборно-разборные. Типы, основные параметры и размеры (с изменением N 1, 2) – Постановление Госстандарта СССР от 10.07.1981 N 3323
– Стандарт от 10.07.1981 N 14757-81;
– ГОСТ 16140_77 Полки разборные. Технические условия Постановления Госстандарта СССР от 28.10.1977 N 2528 ГОСТ от 28.10.1977 N 16140-77;
– ГОСТ 28766_90 Стеллажи.
Однако перечисленные стандарты не распространяются на стеллажи специального назначения. Это означает, что производство и поставка паллетных стеллажей может осуществляться на основании собственных технических условий, без соблюдения требований вышеуказанных нормативных документов.
ГОСТ 16140-77 на изготовление и эксплуатацию полок разборных.
СОДЕРЖАНИЕ
Типы, основные параметры и размеры
ТЕХНИЧЕСКИЕ ТРЕБОВАНИЯ
Требования к безопасности
Пакет
Принятие терминов
Методы испытаний
Маркировка, упаковка, транспортировка и хранение
Типы, основные параметры и размеры стеллажей – по ГОСТ 14757-81.
2. ТЕХНИЧЕСКИЕ ТРЕБОВАНИЯ
2.1. Полки должны быть сооружены в соответствии с требованиями типовых рабочих чертежей, утвержденных в установленном порядке.
2.2. Конструкция стеллажей должна быть рассчитана на использование на механизированных складах.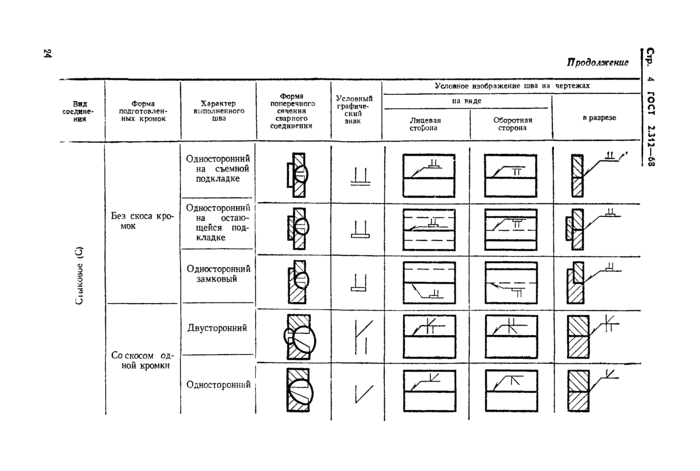
2.3. Механические свойства материалов деталей и сборочных единиц полок должны обеспечивать восприятие нагрузок, предусмотренных ГОСТ 14757-81, с учетом условий эксплуатации стеллажей.
2.4. Кривизна стоек и полок в сборе с балками должна быть не более 3 мм при длине 1000 мм и 0,1 % от общей длины (см. рис. 1).
2.5. Скручивание стоек и балок относительно их продольной оси не должно быть больше 0,5 мм на длину 1000 мм и 0,05 % от общей дин (см. рис. 2).
2.6. На поверхностях деталей стеллажей не допускаются трещины, задиры, расслоения, закаты и заусенцы.
2.7. параметры шероховатости по ГОСТ 2789-73 обрабатываемых металлических поверхностей должны быть Ra? 50 микрон.
(Измененное издание, Изменение. Номер 1).
2.8. Типы элементов конструкций и сварных швов – по ГОСТ 8713-79, ГОСТ 5264-80, ГОСТ 11533-75, ГОСТ 11534-75, ГОСТ 14771-76.
Места сварки должны быть очищены от грязи, масла, окалины и коррозии.
2.9. В швах сварных соединений не допускаются:
непровары;
Местные узелки;
шлаковые включения и поры диаметром более 1 мм;
подрезы основного металла более 0,5 мм;
перелом всех видов.
2.10. Размеры деталей и сборочных единиц стоек следует выполнять с недопустимыми отклонениями грубее 14 класса качества по ГОСТ 25347-82.
2.11. Каркас стеллажа допускается изготавливать из двух и более разъемных частей по высоте.
2.12. Поверхность стоек необходимо загрунтовать и покрасить в серый или серебристый цвет.
Краски и покрытия должны соответствовать внешнему виду класс V ГОСТ 9.032-74, условия эксплуатации – группа У2 ГОСТ 9.104-79.
Допускается по согласованию с заказчиком изготавливать стеллажи только грунтованные.
Крепеж должен иметь защитное покрытие по ГОСТ 9.306-85.
(Измененное издание, Изменение. Номер 1).
2.13. Перпендикулярность стоек стеллажей в сборе должна быть не более 1 мм без нагрузки к горизонтальным полкам длиной 1000 мм, а под действием горизонтальной нагрузки не более 4 мм при длине 1000 мм и длине 6 мм.
Перпендикулярность опорной поверхности ячейки к стойкам стеллажа без нагрузки должна быть не более 5 мм на длину 1000 мм. 2.14. Полки должны быть испытаны на прочность и устойчивость к действию вертикальных и горизонтальных нагрузок.
3. ТРЕБОВАНИЯ БЕЗОПАСНОСТИ
3.1. Конструкция стоек и деталей их крепления должна обеспечивать жесткость, прочность, устойчивость, безопасность и простоту монтажа и обслуживания. Элементы стеллажей не должны иметь острых углов, ребер и поверхностей с неровностями.
3.2. Полки должны иметь защитное заземление по ГОСТ 12.2.007.0-75.
4. УПАКОВКА
4.1. В комплект должны входить элементы стеллажа и сборочные единицы, количество которых указывается на чертежах конструкции.
4.2. Каждая стойка должна сопровождаться инструкцией по установке и эксплуатации, а также паспортом по ГОСТ 2.601-68.
5. ПРИНЯТИЕ УСЛОВИЙ
5.1. Для проверки соответствия стеллажей требованиям настоящего стандарта изготовитель должен проводить приемочные испытания и периодические испытания.
5.2. При приемочных испытаниях на соответствие требованиям пп. 2.1-2.14 Должны быть проверены сборочные единицы в деталях каждого вида стеллажей, взятых наугад в количестве, необходимом для сборки трехсекционного стеллажа.
5.3. Периодические испытания на соответствие требованиям пп. 2.1-2.14 следует проводить один раз в год. Периодическим испытаниям подвергаются сборочные единицы и детали каждого вида стеллажей, отобранные произвольно в количестве, необходимом для сборки трехсекционного стеллажа и прошедшие приемочные испытания.
5.4. Результаты приемочных испытаний отражают в паспорте на стеллаж.
Результаты периодических испытанийрегистрируются в протоколах в соответствии с ГОСТ 15.001-88.
6. МЕТОДЫ ИСПЫТАНИЙ
6.1. Качество материалов защитного покрытия и поверхностей стеллажей деталей (№ 2.6 и 2.12) проверяют осмотром.
6.2. Качество сварных соединений (№ 2.8 и 2.9) проверяют по ГОСТ 3242-79.
6.3. При испытании на прочность и устойчивость к вертикальным и горизонтальным нагрузкам (п. 2. 14) стойка, имеющая все элементы, предусмотренные рабочими чертежами, собирается из трех секций и подвергается действию статических нагрузок. стеллажная опора должна иметь жесткое соединение с основанием, закрепленным на полу.
6.4. При испытании на вертикальную нагрузку (см. рис. 3, 4) к каждой ячейке укладывают через жесткие балки длину приложенной нагрузки
2qB = 1,25Q,
, где q – интенсивность распределения нагрузки;
Q – датчик допустимых нагрузок по ГОСТ 14757-81.
Нагрузка на стеллаж – 1,25 Qn, где n – количество ячеек в стеллаже.
Продолжительность загрузки – 10 мин.
После снятия вертикальной нагрузки произведено испытание горизонтальной статической нагрузкой (см. рис. 5, 6). В точке B/H 2 на высоте одной полки торцевые секции через брус фиксированной длины V прикладывают в течение 10 минут при горизонтальной нагрузке P=Q/2
Затем измеряют перпендикулярность полки стойки к горизонтальной плоскости и снимают нагрузку Р. После этого через жесткую балку длиной L в течение 10 мин прикладывают нагрузку Р в точке L/2 того же сечения, измеряют перпендикулярность стоек секций стойки к горизонтальной плоскости Р и нагрузку снимают.
Стеллаж с настилом
Стеллаж консольный
6.5. После испытаний влияние вертикальной и горизонтальной стеллажной нагрузки должно соответствовать требованиям п. 2.13. Швы сварных соединений – требования п. 2.9.. Детали стойки не должны иметь повреждений и остаточной деформации.
Стеллаж с настилом
Стеллаж консольный
7. МАРКИРОВКА, УПАКОВКА, ТРАНСПОРТИРОВКА И ХРАНЕНИЕ
7.1. На видном месте первой рамы плиты стоек должны быть установлены по ГОСТ 12970-67 и ГОСТ 12971-67, в составе:
товарный знак изготовителя;
стойка типа;
размер стеллажа ячейки в плане;
грузоподъемность, ячейка и сечение;
дата выдачи.
7.2. Каркасы стеллажей должны быть надежно уложены в пачке, крепежные элементы – дощатыми в ящиках по ГОСТ 16536-84 и ГОСТ 15623-84.
7.3. Полная масса упаковки – не более 5 м.
7.4. Связки должны быть надежно перевязаны в поперечном направлении проволокой или лентой не менее чем в двух местах, обеспечивающих сохранность пачек просыпи и сохранность деталей и сборочных единиц от деформации в области перевязки. Монтажные пакеты должны гарантировать надежную транспортировку и хранение.
К каждой пачке и коробке прикрепляется этикетка с указанием товарного знака изготовителя, условного обозначения, количества деталей и сборочных единиц стеллажа, массы брутто.
7.5. В упаковку деталей, отправляемых одному заказчику, вкладывается одна коробка документации в соответствии с требованиями п.п. 4.2.
7.6. Маркировка упаковок – по ГОСТ 14192-77.
7.7. Транспортирование, хранение деталей и сборочных единиц стеллажей – на групповых условиях хранения Ж1 ГОСТ 15150-69.
При хранении и транспортировании деталей и сборочных единиц стеллажи не должны испытывать ударных нагрузок, приводящих к остаточной деформации.
8. ИНСТРУКЦИЯ ПО ЭКСПЛУАТАЦИИ
8.1. Полки на объекте должны быть установлены в соответствии с инструкцией по установке и инструкцией по эксплуатации.
8.2. Стеллажи следует устанавливать на ровных площадках с твердым покрытием, уклоном с учетом ровности 0,002.
8.3. С целью проверки технического состояния и соответствия требованиям настоящего стандарта стеллажи на объекте должны быть осмотрены и испытаны статической нагрузкой в соответствии с требованиями эксплуатационной документации.
9. ГАРАНТИЯ
9.1. Изготовитель должен обеспечить соответствие стеллажей требованиям настоящего стандарта при эксплуатации, транспортировании и хранении.
9.2. Гарантийный срок – 24 месяца. с момента ввода в эксплуатацию стека. (Измененная редакция, Изменение. Номер 1).
10. ИНФОРМАЦИОННЫЕ ДАННЫЕ
1. РАЗРАБОТАН И ВНЕСЕН Министерством автомобильной промышленности СССР
РАЗРАБОТЧИКИ
Антонов Р.Д., Серов Р.Д., Новиков С.