Технология сварки высоколегированных сталей: Сварка высоколегированных сталей – технология и режимы
alexxlab | 20.04.2023 | 0 | Разное
Сварка высоколегированных сталей – технология и режимы
1 / 1
Виды сталей с количеством легирующих элементов от 10 до 55% называются высоколегированными. Кроме того, существуют высоколегированные сплавы на железоникелевой и никелевой основах. Состав этих материалов описан ГОСТом 5632 – 72. Всего описано 94 марки стали и 22 марки сплавов. Существуют различные системы их классификации. Наибольшее распространение получила классификация по типу легирующих добавок. По этому принципу различают следующие виды высоколегированных сталей:
Не лишним будет упомянуть самые распространенные высоколегированные сплавы: никелевые, никелехромистые, никелехромовольфрамовые и никелехромокобальтовые. Эти материалы обладают уникальными полезными свойствами, широко применяются в изготовлении ответственных изделий и требуют особых методов сварки.
Режим сварки высоколегированных сталей
Различные требования предъявляются к сварным швам таких сталей в зависимости от того, в каком качестве их используют: хладостойких, жаропрочных или коррозиестойких.
Присущий в этих сталях низкий коэффициент теплопроводности способствует перегреву, как в самом шве, так и в околошовной зоне. Это увеличивает глубину проплавления и способствует короблению металла. Другой особенностью высоколегированных сталей является высокое сопротивление прохождению электрического тока, результатом чего может стать перегрев сварочной проволоки или электрода. Для нивелирования этих особенностей применяют режимы со следующими характеристиками:
-
максимальная концентрация тепловой энергии;
-
уменьшенная длина электрода или сварочной проволоки;
-
увеличенная скорость подачи электрода;
-
уменьшенная плотность сварочного тока.
Например, при толщине свариваемого материала равной 2 мм. выбирают электрод диаметром 2 мм., длиной 150 – 200 мм. Сваривание проводят током 30 – 50 ампер.
Выбор электродов
Электроды с основным покрытием не используются для сварки аустенитных сталей, так как они провоцируют науглероживание шва, результатом которого будет пониженная стойкость к межкристаллической коррозии. Это явление провоцируется разложением мрамора, который присутствует в этом покрытии в большом количестве. Электроды с рутило-основными и рутило-флюоритноосновными покрытиями – группа, предназначенная для сваривания высоколегированных сталей.
Аустенитная сталь является разновидностью нержавеющих сталей, которые делятся на четыре типа:
-
аустенитная;
-
ферритная;
-
мартенситная;
-
дуплексная.
Главная особенность аустенитной группы состоит в способности не увеличивать твердость при тепловых воздействиях. В эту группу входит сплав 20, который работает в горячей серной кислоте. Серия 300 (из этой группы) используется для изготовления посуды. Стали 309 и 310 используются для работы при температурах 800 С0.
ГОСТ 2246 – 70 содержит 41 марку сварочной проволоки, которая предназначена для сваривания высоколегированных сталей. В качестве примера можно привести следующие марки: Св-04Х19Н9, Св-05Х19Н9Ф3С2, Св-06Х19Н9Т, Св-07Х19Н10Б, Св-08Х20Н9С2БТЮ, Св-10Х16Н25М6А.
ГОСТ 10052 – 75 содержит 49 типов электродов. Вот наиболее популярные: Э-02Х19Н9Б, Э-04Х20Н9, Э-07Х20Н9, Э-06Х22Н9, Э-06Х13Н, Э-08Х20Н9Г2Б, Э-08Х14Н65М15В4Г2, Э-10Х20Н70Г2М2В.
Может возникнуть естественный вопрос о том, для чего такое количество типов сварочной проволоки и электродов. Многообразие типов проволоки и электродов вытекает из разнообразия требований к сварным швам. Как мы уже упоминали ранее: от швов требуют различных качеств в зависимости от того, в каких условиях будет работать то или иное сварное изделие. В зависимости от назначения сварного изделия, по микроструктуре и марке свариваемой детали подбирается марка электрода или сварочной проволоки, вид покрытия (обмазка) и режим сварки.
Как вы могли уже заметить, сварка высоколегированных сталей не является простым процессом. Для ведения работ необходимо обладать достаточными знаниями и немалым опытом. Нужно иметь справочную литературу и уметь ею пользоваться. Это необходимые условия для получения качественного результата сваркия таких материалов.
В домашних условиях, где требования к надежности и долговечности соединения не столь критичны, можно практиковать сварку таких материалов, если знать их марку и иметь таблицу для подбора электродов. К тому же необходимо уметь читать обозначения на электродах. Условные обозначения оговариваются в ГОСТе 9466 – 75. Вторая строка обозначения содержит группу индексов, по которым можно определить характеристики металла шва и наплавленного металла. Аустенитно-ферритная группа имеет четыре цифровых индекса, остальные три. Цифрами закодировано:
-
первый индекс – стойкость против межкристаллической коррозии;
-
второй индекс – максимальная температура, при которой рекомендовано применение изделия;
-
третий индекс – допустимая рабочая температура для изделий, сваренных этими электродами;
-
четвертый индекс – содержание ферритной фазы (необходимо для обеспечения аустенитно-ферритной структуры наплавленного металла).
Все эти сведения можно найти и в паспортах на конкретные электроды.
Выбор флюсов
Соединение высоколегированных сталей можно проводить под слоем флюса, что способствует получению сварочных соединений высокого качества и надежности. Однако особенности технологии позволяют применять такой вид сварки только к швам в нижнем положении.
-
мрамор 28%;
-
фарфор 30%;
-
ферромарганец 10%;
-
ферросилиция 6%;
-
ферротитана 6%;
-
двуокиси титана 20%
Это состав флюса марки НЖ-8.
Выбор защитного газа
Сам процесс сварки был уже неоднократно описан нами, остается только заметить, что и в случае сварки высоколегированных сталей используются те же защитные газы: аргон, гелий, смеси на основа аргона. Отмечается улучшение комфортности при ведении работ в связи со значительным повышением стабильности дуги.
Технология сварки высоколегированных аустенитных сталей и сплавов
Высоколегированные аустенитные стали и сплавы обладают комплексом положительных свойств. Поэтому одну и ту же марку стали иногда можно использовать для изготовления изделий различного назначения, например коррозионно-стойких, хладостойких, жаропрочных и т.д. В связи с этим и требования к свойствам сварных соединений будут различными. Это определит и различную технологию сварки (сварочные материалы, режимы сварки, необходимость последующей термообработки и т.д.), направленную на получение сварного соединениях необходимыми свойствами, определяемыми составом металла шва и его структурой.
Характерные для высоколегированных сталей теплофизические свойства определяют некоторые особенности их сварки. Пониженный коэффициент теплопроводности при равных остальных условиях значительно изменяет распределение температур в шве и околошовной зоне (рис.
Поэтому для уменьшения коробления изделий из высоколегированных сталей следует применять способы и режимы сварки, характеризующиеся максимальной концентрацией тепловой энергии. Примерно в 5 раз более высокое, чем у углеродистых сталей, удельное электросопротивление обусловливает больший разогрев сварочной проволоки в вылете электрода или металлического стержня электрода для ручной дуговой сварки. При автоматической и полуавтоматической дуговой сварке следует уменьшать вылет электрода и повышать скорость его подачи. При ручной дуговой сварке уменьшают длину электродов и допустимую плотность сварочного тока.
Одна из основных трудностей при сварке рассматриваемых сталей и сплавов – предупреждение образования в швах и околошовной зоне горячих трещин. Предупреждение образования этих дефектов достигается:
1) Ограничением (особенно при сварке аустенитных сталей) в основ ном и наплавленном металлах содержания вредных (серы, фосфора) и ликвирующих (свинца, олова, висмута) примесей, а также газов – кислорода и водорода. Для этого следует применять режимы, уменьшающие долю основного металла в шве, и использовать стали и сварочные материалы с минимальным содержанием названных примесей. Техника сварки должна обеспечивать минимальное насыщение металла шва газами. Этому способствует применение для сварки постоянного тока обратной полярности. При ручной сварке покрытыми электродами следует поддерживать короткую дугу и сварку вести без поперечных колебаний. При сварке в защитных газах, предупреждая подсос воздуха, следует поддерживать коротким вылет электрода и выбирать оптимальными скорость сварки и расход защитных газов. Необходимо также принимать меры к удалению влаги из флюса и покрытия электродов, обеспечивая их необходимую прокалку.
2) Получением такого химического состава металла шва, который обеспечил бы в нем двухфазную структуру. Для жаропрочных и жаростойких сталей с малым запасом аустенитности и содержанием никеля до 15 % это достигается получением аустенитно-ферритной структуры с 3 … 5 % феррита. Большее количество феррита может привести к значительному высокотемпературному охрупчиванию швов ввиду их сигматизации. Стремление получить аустенитно-ферритную структуру швов на глубокоаустенитных сталях, содержащих более 15 % Ni, потребует повышенного их легирования ферритообразующими элементами, что приведет к снижению пластических свойств шва и охрупчиванию ввиду появления хрупких эвтектик, а иногда и ?-фазы.
Поэтому в швах стремятся получить аустенитную структуру с мелкодисперсными карбидами и интерметаллидами. Благоприятно и легирование швов повышенным количеством молибдена, марганца и вольфрама, подавляющих процесс образования горячих трещин. Количество феррита в структуре швов на коррозионно-стойких сталях может быть повышено до 15 … 25 %. Высоколегированные стали содержат в качестве легирующих присадок алюминий, кремний, титан, ниобий, хром и другие элементы, обладающие большим сродством к кислороду, чем железо. Поэтому при наличии в зоне сварки окислительной атмосферы возможен их значительный угар, что может привести к уменьшению содержания или к полному исчезновению в структуре шва ферритной и карбидной фаз, особенно в металле с небольшим избытком ферритизаторов.
Для сварки рекомендуется использовать неокислительные низкокремнистые, высокоосновные флюсы (фторидные) и покрытия электродов (фтористокальциевые). Сварка короткой дугой и предупреждение подсоса воздуха служит этой же цели. Азот – сильный аустенитизатор, способствует измельчению структуры за счет увеличения центров кристаллизации в виде тугоплавких нитридов. Поэтому азотизация металла шва способствует повышению их стойкости против горячих трещин.
Высокоосновные флюсы и шлаки, рафинируя металл шва и иногда модифицируя его структуру, повышают стойкость против горячих трещин. Механизированные способы сварки, обеспечивая равномерное проплавление основного металла по длине шва и постоянство термического цикла сварки, позволяют получить и более стабильные структуры на всей длине сварного соединения;
3) Применением технологических приемов, направленных на изменение формы сварочной ванны и направления роста кристаллов аустенита. Действие растягивающих сил, перпендикулярное направлению роста столбчатых кристаллов, увеличивает вероятность образования горячих трещин (рис. 2). При механизированных способах сварки тонкими электродными проволоками поперечные колебания электрода, изменяя схему кристаллизации металла шва, позволяют уменьшить его склонность к горячим трещинам;
4) Уменьшением силового фактора, возникающего в результате термического цикла сварки, усадочных деформаций и жесткости закрепления свариваемых кромок. Снижение его действия достигается ограничением силы сварочного тока, заполнением разделки швами небольшого сечения и применением соответствующих конструкций разделок. Этому же способствует хорошая заделка кратера при обрыве дуги. Кроме перечисленных общих особенностей сварки высоколегированных сталей и сплавов, есть специфические особенности, определяемые их служебным назначением. При сварке жаропрочных и жаростойких сталей обеспечение требуемых свойств во многих случаях достигается термообработкой (аустенизацией) при температуре 1050 … 1110 °С, снимающей остаточные сварочные напряжения, с последующим стабилизирующим отпуском при температуре 750 … 800 °С. При невозможности термообработки сварку иногда выполняют с предварительным или сопутствующим подогревом до температуры 350 … 400 °С. Чрезмерное охрупчивание швов за счет образования карбидов предупреждается снижением содержания в шве углерода. Обеспечение необходимой окалиностойкости достигается получением металла шва, по составу идентичного основному металлу.
Это же требуется и для получения швов стойких к общей жидкостной коррозии.
При сварке коррозионно-стойких сталей различными способами для предупреждения МКК не следует допускать повышения в металле шва содержания углерода за счет загрязнения им сварочных материалов (графитовой смазки проволоки и т.д.), длительного и многократного пребывания металла сварного соединения в интервале критических температур.
В связи с этим сварку необходимо выполнять при наименьшей погонной энергии, используя механизированные способы сварки, обеспечивающие непрерывность получения шва. Повторные возбуждения дуги при ручной сварке, вызывая нежелательное тепловое действие на металл, могут вызвать появление склонности его к коррозии. Шов, обращенный к агрессивной среде, по возможности следует сваривать в последнюю очередь, чтобы предупредить его повторный нагрев, последующие швы в многослойных швах – после полного охлаждения предыдущих. Следует принимать меры к ускоренному охлаждению швов. Брызги, попадающие на поверхность основного металла, могут быть впоследствии очагами коррозии. Следует тщательно удалять с поверхности швов остатки шлака и флюса, так как взаимодействие их в процессе эксплуатации с металлом может повести к коррозии или снижению местной жаростойкости.
Для повышения стойкости швов к межкристаллитной коррозии и создания в их металле аустенитно-ферритной структуры при сварке их обычно легируют титаном или ниобием. Однако титан обладает высоким сродством к кислороду и поэтому при способах сварки, создающих в зоне сварки окислительную атмосферу (ручная дуговая сварка, сварка под окислительными флюсами), выгорает в количестве 70 … 90 %. Легирование швов титаном возможно при сварке в инертных защитных газах, при дуговой и электрошлаковой сварке с использованием фторидных флюсов. В металле швов содержание титана должно соответствовать соотношению Ti/C > 5. Ниобий при сварке окисляется значительно меньше и его чаще используют для легирования шва при ручной дуговой сварке. Его содержание в металле шва должно соответствовать Nb/C > 10. Однако он может вызвать появление в швах горячих трещин.
Газовая сварка обеспечивает большую зону разогрева, значительный перегрев расплавленного металла и замедленное охлаждение. При этом происходит значительный угар легирующих элементов. Она наименее благоприятна для сварки этих особенно кислотостойких сталей, в которых может развиваться значительная межкристаллитная коррозия. Газовая сварка может использоваться для сварки жаропрочных и жаростойких сталей толщиной 1 … 2 мм. Сварка ведется нормальным пламенем с мощностью пламени 70 … 75 л/ч на 1 мм толщины. Процесс следует вести с возможно большей скоростью левым способом, мундштук держать под углом 45° к поверхности. В сварных соединениях образуются большие коробления.
Ручная дуговая сварка это высокоманевренный способ. При сварке высоколегированных сталей сварочные проволоки одной по ГОСТу марки имеют достаточно широкий допуск по химическому составу. Различие типов сварных соединений, пространственного положения сварки и т.п. способствует изменению глубины проплавления основного металла, а также изменению химического состава металла шва. Все это заставляет корректировать состав покрытия с целью обеспечения необходимого содержания в шве феррита и предупреждения, таким образом, образования в шве горячих трещин. Этим же достигаются и необходимая жаропрочность и коррозионная стойкость швов.
Применением электродов с фтористокальциевым покрытием, уменьшающим угар легирующих элементов, достигается получение металла шва с необходимым химическим составом и структурами. Уменьшению угара легирующих элементов способствует и поддержание короткой дуги без поперечных колебаний электрода. Это снижает вероятность появления дефектов на поверхности основного металла в результате попадания на него брызг.
Тип покрытия электрода диктует необходимость применения постоянного тока обратной полярности (при переменном или постоянном токе прямой полярности дуга неустойчива). Тщательная прокалка электродов, режим которой определяется их маркой, способствует уменьшению вероятности образования в швах пор и вызываемых водородом трещин. Некоторые данные о режимах и выборе электродов для ручной дуговой сварки приведены в табл. 1 и 2, а о свойствах сварных соединений – в табл. 3 и на рис. 3.
Табл. 1 Ориентировочные режимы ручной дуговой сварки аустенитных сталей
Табл. 2 Некоторые марки электродов для сварки высоколегированных сталей и сплавов
Табл. 3 Типичные механические свойства металла шва при комнатной температуре
Сварка под флюсом. Этот один из основных способов сварки высоколегированных сталей толщиной 3 … 50 мм имеет большое преимущество перед ручной дуговой сваркой покрытыми электродами ввиду стабильности состава и свойств металла по всей длине шва при сварке с разделкой и без разделки кромок. Это достигается отсутствием частых кратеров, образующихся при смене электродов, равномерностью плавления электродной проволоки и основного металла по длине шва (при ручной сварке меньшая скорость плавления электрода вначале его использования и большая в конце изменяет долю основного металла в шве, а значит, и его состав), более надежной защитой зоны сварки от окисления легирующих компонентов кислородом воздуха и др.
Хорошее формирование поверхности швов с мелкой чешуйчатостью и плавным переходом к основному металлу, отсутствие брызг на поверхности изделия заметно повышают коррозионную стойкость сварных соединений. При этом способе уменьшается трудоемкость подготовительных работ, так как разделку кромок выполняют на металле толщиной свыше 12 мм (при ручной сварке свыше 3 … 5 мм). Возможна сварка с повышенным зазором и без разделки кромок стали толщиной до 30 … 40 мм. Уменьшение потерь на угар, разбрызгивание и огарки электродов на 10 … 20 % снижает расход дорогостоящей сварочной проволоки.
Однако при сварке под флюсом некоторых марок жаропрочных сталей требование обеспечения в металле шва регламентированного количества ферритной фазы не всегда может быть достигнуто. Это объясняется трудностью получения необходимого состава металла шва за счет выбора только сварочных флюсов и проволок (последние имеют значительные колебания химического состава в пределах стали одной марки) при сварке металла различной толщины (различная форма разделки и, значит, доля участия основного металла в формировании шва).
Отличие техники сварки высоколегированных сталей и сплавов от техники сварки обычных низколегированных сталей заключается в уменьшении вылета электрода в 1,5 … 2 раза ввиду повышенного электросопротивления сварочных проволок. Для предупреждения перегрева металла и связанного с этим огрубления структуры, возможности появления трещин и снижения эксплуатационных свойств сварного соединения многослойные швы повышенного сечения рекомендуется сваривать швами небольшого сечения. Это предопределяет использование сварочных проволок диаметром 2 … 3 мм. Аустенитные сварочные проволоки в процессе изготовления сильно наклёпываются и имеют высокую жесткость, что затрудняет работу правильных, подающих и токоподводящих узлов сварочных установок, снижая срок их службы. Легировать шов можно через флюс (табл. 4) или проволоку (табл. 5).
Легирование через проволоку более предпочтительно, так как обеспечивает повышенную стабильность состава металла шва. При сварке используют безокислительные низкокремнистые фторидные и высокоосновные флюсы, создающие в зоне сварки безокислительные или малоокислительные среды, способствующие минимальному угару легирующих элементов. Остатки шлака и флюса на поверхности швов, которые могут служить очагами коррозии сварных соединений на коррозионно- и жаростойких сталях, необходимо тщательно удалять. Тип флюсов предопределяет преимущественное использование для сварки постоянного тока обратной полярности. При этом достигается и повышенная глубина проплавления. Некоторые данные о механических свойствах металла сварных швов и соединений приведены в табл. 6 и 7
Табл. 4 Флюсы для электродуговой и электрошлаковой сварки высоколегированных сталей
Табл. 5 Некоторые марки сварочных проволок для электродуговой сварки под флюсом и электрошлаковой сварки высоколегированных сталей
Табл. 6 Кратковременные механические свойства при температуре 20 °С металла шва и сварного соединения высоколегированных сталей и сплавов
Электрошлаковая сварка. Важнейшая особенность способа – пониженная чувствительность к образованию горячих трещин, что позволяет получать чисто аустенитные швы без трещин. Это объясняется специфическими особенностями электрошлаковой сварки: малой скоростью перемещения источника нагрева и характером кристаллизации металла сварочной ванны, отсутствием в стыковых соединениях угловых деформаций. Однако малая концентрация нагрева и скорость сварки, повышая длительность пребывания металла шва и околошовной зоны при повышенных температурах, увеличивают его перегрев и ширину околошовной зоны.
Табл. 7 Длительная прочность сварных соединений высоколегированных сталей и сплавов
Длительное пребывание металла при температурах 1200 … 1250 °С, приводя к необратимым изменениям в его структуре, снижает прочностные и пластические свойства. Это повышает склонность сварных соединений теплоустойчивых сталей к локальным (околошовным) разрушениям в процессе термообработки или эксплуатации при повышенных температурах. При сварке коррозионно-стойких сталей перегрев стали в околошовной зоне может привести к образованию в ней ножевой коррозии. Для предупреждения этих дефектов необходима термообработка сварных изделий (закалка или стабилизирующий отжиг). Применение неокислительных флюсов, особенно при сварке жаропрочных сталей и сплавов, не исключает угара легкоокисляющихся легирующих элементов (титана, марганца и др.) за счет проникновения кислорода воздуха через поверхность шлаковой ванны. Это вызывает необходимость в ряде случаев защищать поверхность шлаковой ванны путем обдува ее аргоном.
Электрошлаковую сварку можно выполнять проволочным или пластинчатыми электродами (табл. 8). Изделия большой толщины со швами небольшой протяженности целесообразнее сваривать пластинчатым электродом. Изготовление пластинчатого электрода более простое. Но сварка проволокой позволяет в более широких пределах, варьируя режим, изменять форму металлической ванны и характер кристаллизации металла шва, а это один из действенных факторов, обеспечивающих получение швов, свободных от горячих трещин. Однако жесткость сварочной проволоки затрудняет длительную и надежную работу токоподводящих и подающих узлов сварочной аппаратуры.
Табл. 8 Типовой режим электрошлаковой сварки высоколегированных сталей и сплавов
Сварка в защитных газах. В качестве защитных используют инертные (аргон, гелий) и активные (углекислый) газы, а также различные смеси инертных или активных газов и инертных с активными. Этот способ сварки по сравнению с рассмотренными выше имеет ряд существенных преимуществ. Его можно использовать для соединения металлов широкого диапазона толщин – от десятых долей до десятков миллиметров. При сварке толстых металлов в некоторых случаях этот способ сварки может конкурировать с электрошлаковой сваркой.
Применение инертных газов существенно повышает стабильность дуги. Значительное различие теплофизических свойств защитных газов и применение их смесей, изменяя тепловую эффективность дуги и условия ввода теплоты в свариваемые кромки, значительно расширяют технологические возможности дуги. При сварке в инертных газах наблюдается минимальный угар легирующих элементов, что важно при сварке высоколегированных сталей. При сварке в защитных газах возможности изменения химического состава металла шва более ограничены по сравнению с другими способами сварки и возможны за счет изменения состава сварочной (присадочной) проволоки или изменения доли участия основного металла в образовании металла шва (режим сварки), когда составы основного и электродного металлов значительно различаются.
При сварке плавящимся электродом появляется возможность изменения характера металлургических взаимодействий за счет значительного изменения состава защитной атмосферы, например, создания окислительных условий в дуге, путем применения смеси газов, содержащих кислород, углекислый газ и др. Этим способом можно выполнять сварку в различных пространственных положениях, что делает ее целесообразной в монтажных условиях по сравнению с ручной дуговой сваркой покрытыми электродами. Сварку в защитных газах можно выполнять неплавящимся вольфрамовым или плавящимся электродом.
Вольфрамовым электродом сваривают в инертных газах или их смесях. Для сварки высоколегированных сталей используют аргон высшего или 1-го сортов по ГОСТ 10157-79. Обычно сварку вольфрамовым электродом технически и экономически целесообразно использовать при сварке металлов толщиной до 7 мм (при толщине до 1,5 мм применение других способов дуговой сварки практически невозможно из-за образования прожогов). Однако в некоторых случаях, например при сварке неповоротных стыков труб, сварку вольфрамовым электродом применяют на сталях и больших толщин.
Высокое качество формирования обратного валика вызывает необходимость применения этого способа и при сварке корневых швов в разделках при изготовлении ответственных толстостенных изделий. В зависимости от толщины стали и конструкции сварного соединения сварку выполняют с присадочным материалом или без него вручную с использованием специальных горелок или автоматически. Сварку ведут на постоянном токе прямой полярности. Исключение составляют стали и сплавы с повышенным содержанием алюминия, когда для разрушения поверхностной пленки окислов, богатой алюминием, следует применять переменный ток.
Что такое высоколегированные стали при сварке?
Welding Tech
Высоколегированные стали – это те, которые содержат более 10% легирующих элементов. Нержавеющая сталь — это один из видов высоколегированной стали, содержащий более 10 % хрома. Из-за высокого содержания легирующих элементов эти стали часто плохо поддаются сварке. Однако при правильном процессе и технике сварки можно успешно сваривать высоколегированные стали.
Что следует учитывать при сварке высоколегированных сталей?
При сварке высоколегированных сталей необходимо учитывать несколько моментов:
- Во-первых, важно использовать правильный процесс сварки.
- Во-вторых, сварщик должен иметь соответствующую подготовку и опыт.
- В-третьих, необходимо использовать правильное сварочное оборудование.
- Наконец, необходимо правильно соблюдать процедуру сварки.
При сварке высоколегированных сталей важно использовать правильный процесс сварки. Наиболее распространенными процессами сварки высоколегированных сталей являются дуговая сварка металлическим электродом в среде защитного газа (GMAW) и дуговая сварка с флюсовой проволокой (FCAW). GMAW является наиболее популярным процессом сварки высоколегированных сталей, поскольку он с меньшей вероятностью вызывает дефекты сварки. FCAW можно использовать для высоколегированных сталей, но это с большей вероятностью приведет к дефектам сварки.
Сварщик должен иметь соответствующую подготовку и опыт сварки высоколегированных сталей. Сварщик должен быть сертифицирован Американским обществом сварщиков (AWS). Сварщик также должен иметь опыт сварки подобных материалов.
В чем разница между высоколегированной и низколегированной сталью?
Основное различие между высоколегированными и низколегированными сталями заключается в количестве хрома. Высоколегированные стали содержат больше хрома, чем низколегированные стали. Дополнительный хром придает стали коррозионную стойкость и ударную вязкость. Низколегированные стали слабее и менее устойчивы к коррозии, чем высоколегированные стали.
Является ли высоколегированная сталь такой же, как нержавеющая сталь?
Нет, высоколегированная сталь — это не то же самое, что нержавеющая сталь. Нержавеющая сталь — это разновидность высоколегированной стали, которая содержит хром. Есть много других типов высоколегированных сталей, не содержащих хрома.
Ссылки по теме
Легированная сталь
Высоколегированная сталь – обзор | ScienceDirect Topics
Разница между низколегированной и высоколегированной сталью; Разница между низколегированной сталью и высоколегированной сталью
Типы и применение легированной стали
Разница между низколегированной и высоколегированной сталью
Влияние легирующих элементов на свойства стали.
Подробнее
Высоколегированная сталь Katana – CASIberia.
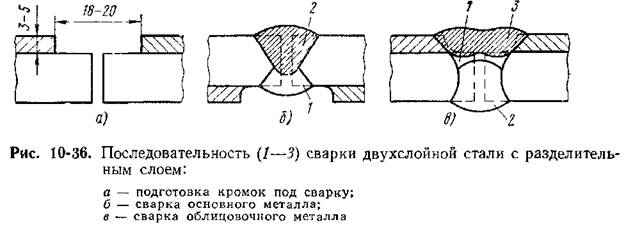
Подробнее
Тест высокоуглеродистой стали и мягкой стали
Подробнее
Сварка ВИГ низколегированной высокопрочной стали
7 Сталь 0 AlloyПодробнее
Подробнее in Технологические трубопроводы Низколегированные и высоколегированные стали – Учебное видео по трубопроводам-4
Посмотреть ещё
Глоссарий категорийСварка высоколегированных материалов
Сварка высоколегированных материалов – Неоникель
polski (польский)Nederlands (голландский)Italiano (итальянский)Français (французский)Español (испанский)EnglishDeutsch (немецкий)Čeština (чешский)
Контакт
Большинство сплавов, поставляемых NeoNickel, представляют собой материалы с высокими эксплуатационными характеристиками и при сварке предназначены для использования в сложных условиях. Как таковые, они требуют тщательной и контролируемой сварки, чтобы гарантировать, что свойства каждого из них сохраняются для конкретного использования.
Характеристики сварки сплавов, как правило, удовлетворительные, если для каждой марки используются правильные методы, обеспечивающие достижение как металлургических, так и структурных свойств. Каждая группа сплавов будет иметь немного отличающиеся требования и характеристики.
Необходимо обращаться к соответствующим инструкциям по технике безопасности производителя для каждого сплава, чтобы обеспечить безопасную сварку сплавов.
Однако большинство инструкций по технике безопасности для металлов аналогичны и требуют осторожности, но не ограничиваются:
- использование электрооборудования
- хорошая вентиляция и вытяжка при сварке
- и что рекомендуется постоянно носить СИЗ
Протокол квалификации процедуры сварки (WPQR)
Подробную информацию можно получить из различных источников, а также от производителей. Часто стандартной практикой является заполнение протокола аттестации процедуры сварки (WPQR), чтобы показать, что существует приемлемая процедура для производства качественных сварных швов. Это требуется либо конечным потребителем, либо применимыми законодательными или промышленными нормами. Существует ряд сертификационных органов, которые могут использоваться для утверждения процедуры сварки, если это необходимо, и эти руководящие принципы помогут в написании процедуры и ее квалификации для удовлетворения этим требованиям. Поскольку эти сплавы могут быть довольно сложными с металлургической точки зрения, рекомендуется использовать опытного изготовителя для каждого типа сплава, поскольку производители несут ответственность за эффективное применение рекомендаций.
NeoNickel может помочь и предложить несколько опытных производителей – свяжитесь с нами сегодня.
Общие правила
- Изготовители также должны иметь чистую зону, отдельную от любых изделий из углеродистой стали, и чтобы инструменты не смешивались.
- Очень важно, чтобы основные материалы были чистыми, не содержали оксидов и предпочтительно сваривались в состоянии отжига на твердый раствор, поскольку чрезмерная холодная обработка, превышающая 7–10%, может привести к растрескиванию сварного шва или ЗТВ в некоторых сплавах.
- Рекомендуется исключить любые щели для коррозионно-стойких применений, поэтому стыковые сварные швы должны быть с полным проплавлением для сохранения прочности и предотвращения образования щелей для достижения оптимальных коррозионных характеристик. Угловые сварные швы не обязательно должны быть с полным проплавлением, если достигнута требуемая толщина шва и отсутствуют любые щели или они загерметизированы.
- Рекомендуется получить хорошую посадку с минимальным смещением, а обработанная обработка и сильная прихватка могут облегчить это.
- Тонкие материалы, т. е. <3 мм, можно использовать с закрытой квадратной стыковой препаровкой, более толстые материалы в диапазоне от 3 до 20 мм требуют V-образной препаровки (одно- или двусторонней), а более толстые материалы выиграют от U-образной препаровки.
- Подготовка может производиться с использованием холодных процессов, таких как резка, распиловка, механическая обработка, шлифовка или резка водой, с соблюдением мер по предотвращению загрязнения и удалению остатков смазочно-охлаждающей жидкости.
- Следует проявлять осторожность в отношении загрязнений, которые могут быть вызваны, помимо прочего, смазочно-охлаждающими жидкостями, смазками, маслами, воском, мелками для разметки, краской или грунтовкой, клейкой лентой или рабочими инструментами.
- Если имеются какие-либо разрывы или повреждения поверхности сварного шва, их следует соответствующим образом зачистить до чистого металла.
- Если используется горячая обработка, такая как лазерная плазменная дуга, угольная дуга, необходимо отшлифовать до чистого металла.
- Любая смазка или другие загрязнения должны быть удалены с поверхности перед сваркой. Можно использовать любой подходящий метод очистки, но рекомендуется использовать чистящие составы, не содержащие хлоридов, особенно для нержавеющей стали.
- Подходящий присадочный металл следует выбирать для марки сплава, используемого процесса и для обеспечения требуемых свойств в зоне сварки для предполагаемого использования. Как правило, для высоколегированных материалов можно использовать любой процесс сварки, кроме кислородно-ацетиленовой сварки.
Процесс сварки должен быть выбран таким образом, чтобы обеспечить наилучшую скорость наплавки, при которой также будут достигнуты требуемые свойства. Следует учитывать металлургические или структурные свойства и пределы деформации.
- Как правило, предварительный нагрев не требуется, только для обеспечения отсутствия влаги в холодных условиях.
- Межпроходные температуры, как правило, рекомендуются с особыми рекомендациями для каждого сплава и должны соблюдаться.
- Межпроходная температура должна быть максимальной температурой в зоне сварки.
- Следует соблюдать осторожность при использовании маркерных мелков, чтобы не допустить их загрязнения.
- Как правило, используются диапазоны тепловложения от низкого до среднего, и опять же, более конкретные инструкции можно найти в инструкциях к сплаву.
- Завершенная зона сварки должна быть осмотрена в соответствии с требованиями заказчика или нормами, и для большинства сплавов можно использовать обычные методы неразрушающего контроля, такие как визуальный, размерный, поверхностный проникающий анализ, ультразвуковое исследование, радиографию.