Технология вулканизации резины к металлу: Основные способы крепления резины к металлу — Резинщик.ру
alexxlab | 05.02.2023 | 0 | Разное
Навигация: Главная Случайная страница Обратная связь ТОП Интересно знать Избранные Топ: Организация стока поверхностных вод: Наибольшее количество влаги на земном шаре испаряется с поверхности морей и океанов… Основы обеспечения единства измерений: Обеспечение единства измерений – деятельность метрологических служб, направленная на достижение… Характеристика АТП и сварочно-жестяницкого участка: Транспорт в настоящее время является одной из важнейших отраслей народного… Интересное: Уполаживание и террасирование склонов: Если глубина оврага более 5 м необходимо устройство берм. Варианты использования оврагов для градостроительных целей… Распространение рака на другие отдаленные от желудка органы: Характерных симптомов рака желудка не существует. Подходы к решению темы фильма: Существует три основных типа исторического фильма, имеющих между собой много общего… Дисциплины: Автоматизация Антропология Археология Архитектура Аудит Биология Бухгалтерия Военная наука Генетика География Геология Демография Журналистика Зоология Иностранные языки Информатика Искусство История Кинематография Компьютеризация Кораблестроение Кулинария Культура Лексикология Лингвистика Литература Логика Маркетинг Математика Машиностроение Медицина Менеджмент Металлургия Метрология Механика Музыкология Науковедение Образование Охрана Труда Педагогика Политология Правоотношение Предпринимательство Приборостроение Программирование Производство Промышленность Психология Радиосвязь Религия Риторика Социология Спорт Стандартизация Статистика Строительство Теология Технологии Торговля Транспорт Фармакология Физика Физиология Философия Финансы Химия Хозяйство Черчение Экология Экономика Электроника Энергетика Юриспруденция |
⇐ ПредыдущаяСтр 14 из 15Следующая ⇒ горячее крепление – невулканизованную (сырую) резиновую смесь соединяют с другими материалами в процессе вулканизации, – холодное крепление – вулканизованную резину крепят адгезивами (т.
В промышленности РТИ применяются несколько видов горячего крепления: а) эбонитом в качестве промежуточного слоя; б) термопреновым клеем; в) нанесением тонкого слоя латуни на поверхность металла; г) специальными клеями (из производных каучука, изоцианатными и др.).
Горячее крепление Для изготовления деталей применяется сырая резина, приобретающая необходимые свойства в процессе вулканизации В процессе горячего крепления резина присоединяется к металлу либо непосредственно, либо через промежуточный слой. Непосредственно прикрепляются к металлам эбонит или резина, в состав которых введены соединения меди, железа или некоторых других металлов. Объясняется это тем, что основным звеном, связывающим каучук с металлом, является сера, наличие которой в резиновой смеси является обязательным. В качестве промежуточных слоев при креплении резины к металлам используются эбонит, латунь и различные клеи, обладающие способностью хорошо прилипать как к металлам, так и к резине в процессе ее вулканизации.
1) Крепление с применением латунирования – крепление через промежуточный слой латуни – является наиболее современным, известным методом, С помощью этого метода крепят резину к стали, алюминию, бронзе и др. Сущность способа заключается в предварительном электролитическом осаждении тонкого (0,00125—0,0015 мм) слоя латуни (например, из цианистых электролитов) на поверхность металлических деталей, подлежащих обрезиниванию, и непосредственном креплении резины к латунированной поверхности металла. После промывки и сушки латунированная арматура поставляется на вулканизацию. Резиновая смесь должна быть свежекаландрованной или свежеэкструдированной. Формы с латунированными деталями иногда заполняют резиновой смесью методом литья под давлением. Латунирование состоит из трех основных операций: обезжиривания, травления и электроотложения, сопровождаемых промывками водой. Для удаления углерода, остающегося на поверхности металла после травления, применяется механическая обработка стальными щетками (так называемое крацевание). Для удаления пленки окислов применяется химическая обработка (так называемое декапирование). Основные операции проводятся в электролитических ваннах при определенных режимах. Промывка производится в горячей (40—80 °С) и холодной проточной воде, а сушка — в термостате при 80—100 °С с продувкой воздуха Достоинства метода: высокая прочность, наибольшая температуростойкость, масло- и бензостойкость, хорошее сопротивление ударам и вибрациям. Недостатки: метод пригоден в основном для крепления резины к небольшим деталям, т.к. на поверхность больших деталей сложной конфигурации трудно равномерно и прочно осадить латунь. Также метод требует сложных подготовительных операций, требующих специального оборудования. Применяется для производства латунированного металлокорда, используемого для изготовления автопокрышек и безбандажных массивных шин.
2) Крепление через слой эбонита – наиболее простой и достаточно надежный способ крепления резины к металлам Этим способом крепят резину к стали, дюралюминию, латуни, бронзе и другим сплавам. Способ заключается в подготовке поверхности металла (очистке, обезжиривании), нанесении эбонитового клея и слоя эбонитовой смеси, наложении резиновой смеси, формовании и вулканизации под давлением. Прочность соединения эбонитов с металлами достигает 15—20 МПа. Наличие молекулярного контакта между резиной и слоем эбонитовой смеси к началу вулканизации не является обязательным, так как связи между ними возникают значительно позже, когда эбонитовая смесь и резина находятся в стадии размягчения и опрессование полностью заканчивается. К преимуществам крепления через эбонитовую прослойку относятся простота и надежность метода. Однако имеются и существенные недостатки, обусловленные специфическими свойствами самого эбонита. Недостатки метода: вулканизация эбонита – процесс длительный, что снижает производительность оборудования и плохо отражается на свойствах резины. Применяется в производстве массивных шин применяется довольно часто.
3) Специальные клеи. Первыми клеями для холодного крепления были клеи на основе бутумов и нефтяных пеков, иногда в смеси с каучуком или гуттаперчей. Широкое применение находят клеи на основе хлоропренового каучука. Значительная прочность крепления клеями из хлоркаучука объясняется тем, что высокое содержание хлора создает сильную поляризацию каучуковых молекул, образующих прослойку между металлом и резиной. Для крепления резины из бутадиен-нитрильного каучука рекомендован клей из хлоркаучука с содержанием хлора 65—68%, дающий прочность крепления 300—400 Н/см2 при температуре до 100 °С; с дальнейшим повышением температуры прочность такого клея сильно падает. Для крепления резин на натуральном каучуке применяют клей Q; для резин нефтестойких — клей S; имеются и другие виды этого клея, в том числе и для крепления без вулканизации. Базой этих клеев является гидрохлорид каучука. Ряд клеев рекомендован Научно-исследовательским институтом резиновой промышленности, в том числе клей 88Н для крепления резины к металлу без нагрева и лейконат для крепления в процессе вулканизации. Лейконат представляет собой раствор триизоцианаттрифенилметана в дихлорэтане. Раствор этого же изоцианата в метиленхлориде известен под названием десмодура R.
Крепление с помощью термопреновых клеев.
При действии на натуральный каучук серной кислоты и сульфокислот образуются термопрены. В зависимости от условий получения и количества серной кислоты можно получить термрпрены разной твердости. Термопрены термопластичны, способны размягчаться при нагревании. Получение термопренов. Сульфокислоты (нелетучи и равномерно распределяются в каучуке) 6-7% смешивают с натуральным каучуком на вальцах, полученную резиновцю смесь при 140°С нагревают в течении 3-5 ч. После термообработки промывают смесь для удаления кислот и сушат . Состав термопрена близок к (С5Н8)х. Получают термопреновый клей, растворяя термопрен в бензине в обогреваемой клеемешалке при 50 °С. Соотношения термопрена и бензина в термопреновом клее 1 :8 и 1:12. Подготовленный к обкладке металл промазывают 2—3 раза термопреновым клеем, сначала жидким, а затем более густым, с тщательным просушиванием каждого слоя промазки. Далее следуют накладка и прикатка обкладочных смесей. Вулканизация. Обкладку на термопреновой прослойке целесообразно вулканизовать в котле при давлении пара 2,5—3-105 Па, затем следует охлаждение в котле под давлением, достигаемое подачей в котел сжатого воздуха и вбрызгиванием холодной воды. Давление воздуха доводится до 6-105 Па и поддерживается, пока температура не понизится до 60—70 °С, т. Применение термопренового клея позволяет прикрепить предварительно вулканизованную пластину мягкой резины к металлу или дереву. Чтобы обеспечить лучшее сцепление вулканизованной резиновой обкладки с термопреновым слоем, поверхность пластины делают шероховатой, закатывая пластину перед вулканизацией на барабан с прослойкой грубой ткани. На швы обкладки накладывают ленточки из сырой, быстро вулканизующейся смеси. Разогрев термопренового слоя и вулканизацию швов производят при 100 °С. Удовлетворительная прочность крепления при использовании термопреновых клеев достигается только при охлаждении под давлением детали после вулканизации. Недостатки: понижение прочности крепления с повышением температуры, т.
Крепление с помощью латексно-альбуминных и термопреновых клеев.
Плёнка альбумина ( Альбумин – это серосодержащий водорастворимый белок, который коагулирует (слипается) при нагревании) обладает хорошей адгезией к металлу, но она не эластична. Поэтому к ней добавляют латекс, получая эластичную плёнку с хорошей адгезией. На очищенную поверхность металла наносят 1-2, а иногда и большее число слоёв клея. Достоинства метода: нетоксичность латексно – альбуминных клеев. Недостатки: необходимость тепловой обработки клеевых плёнок, нестабильность самого клея, необходимость применения натурального латекса.
Методы горячего крепления резины к металлу посредством латексно-альбуминных и термопреновых клеев в промышленности на данный момент практически не используются.
Крепление посредством клеёв на основе хлорированного и гидрохлорированного каучуков В 50-х годах прошлого века были разработаны клеи на основе хлорированного (ХК) и гидрохлорированного (ГХК) каучуков, которые обеспечивали такую же прочность крепления резины к металлу, как латунь, а также такую же масло- и теплостойкость. С 1946 года метод крепления резины к металлу посредством ХК и ГХК стал конкурировать с методом крепления посредством латунирования. Для приготовления клеев следует брать ХК с содержанием хлора около 60%. Такой ХК во время вулканизации резинометаллической детали в течение 20-60 минут при 140-150°С сохраняет достаточную устойчивость. Он не горюч, стоек к действию холодной и горячей воды, кислот (серной, соляной, азотной), к действию щелочей и окислителей. Раствор ХК (клей) применяют для крепления резины к чугуну, стали, алюминию и его сплавам, магнию, цинку и другим материалам. Прибавление серы к клеям из ХК способствует повышению адгезии при креплении. С их помощью крепят резины из неопрена к латуни. При креплении резин из натуральных каучуков и бутадиен-стирольных каучуков между клеем и резиной вводиться промежуточный слой клея из хлоропренового каучука или прослойка резины из него. Резины из бутил-каучука крепятся плохо. Достигаемая прочность крепления резины к металлу при испытания на отрыв: 40-60 кг/см2. С повышением температуры прочность падает до 20-30% начальной. Достоинства метода: хорошая сопротивляемость старению, стойкость к действию кислот, щелочей и морской воды (в этом способ крепления резины к металлу посредством ХК превосходит даже крепление латунированием). Недостатки: крепление неустойчиво к воздействию ароматических углеводородов, животных и растительных масел, эфиров и кетонов. Гидрохлорированные каучуки впервые были получены при пропускании влажного HCl через хлороформенный раствор каучука. По окончании реакции происходит резкое падение вязкости раствора.
⇐ Предыдущая6789101112131415Следующая ⇒ Организация стока поверхностных вод: Наибольшее количество влаги на земном шаре испаряется с поверхности морей и океанов (88‰)… Общие условия выбора системы дренажа: Система дренажа выбирается в зависимости от характера защищаемого… Поперечные профили набережных и береговой полосы: На городских территориях берегоукрепление проектируют с учетом технических и экономических требований, но особое значение придают эстетическим… Индивидуальные и групповые автопоилки: для животных. Схемы и конструкции… |
Способы крепления резины к металлам
Способы крепления резины к металлам
Способы крепления резины к металлам можно разделить на две основные группы: «горячее крепление» резины к металлу в процессе формования и вулканизации и «холодное крепление» уже вулканизованной резины к металлу с помощью клеев холодного отверждения.
При горячем креплении резина прикрепляется к металлу непосредственно либо через промежуточный слой материала, имеющего хорошую адгезию как к резине, так и к металлу.
Непосредственно к металлу прикрепляются эбонит или резина, имеющие в своем составе соединения меди, железа, кобальта или некоторых других металлов. Это объясняется тем, что согласно современным представлениям каучук связан с металлом через серу, которая обязательно присутствует в резиновой смеси как вулканизующий агент. Сера, вступая в реакцию с металлами, образует сульфидные соединения, обеспечивающие крепление резины к поверхности металла.
Рекламные предложения на основе ваших интересов:
Дополнительные материалы по теме:
Наиболее активно сера вступает в реакцию с медью. На этом основан способ крепления резины через промежуточный слой латуни к таким металлам как сталь, алюминий, бронза и др. Сущность способа заключается в предварительном электролитическом осаждении тонкого (0,00125—0,0015 мм) слоя латуни (например, из цианистых электролитов) на поверхность металлических деталей, подлежащих обрезиниванию, и непосредственном креплении резины к латунированной поверхности металла. Соединение имеет высокую прочность, температуро-масло- и бензостойкость, хорошее сопротивление ударам и вибрациям. При этом резина хорошо крепится только к латуни, свободной от оксидов или каких-либо поверхностных загрязнений.
Для этого способа, однако, необходимы сложные дорогостоящие установки, а равномерное и прочное осаждение латуни на большие поверхности бандажей и ободов-ступиц массивных шин многих типоразмеров сопряжено со значительными техническими трудностями. Поэтому способ латунирования металлов, из которых изготовляют бандажи и обода-ступицы, не находит большого распространения и применяется для производства латунированного металлокорда, используемого для изготовления автопокрышек и безбандажных массивных шин.
Эбонитовое крепление. Одним из самых старых (известен с 1853 г.), наиболее простым и достаточно надежным способом крепления резины к металлам является способ крепления через эбонитовую прослойку. Способ заключается в подготовке поверхности металла (очистке, обезжиривании), нанесении эбонитового клея и слоя эбонитовой смеси, наложении резиновой смеси, формовании и вулканизации под давлением. Прочность соединения эбонитов с металлами достигает 15—20 МПа.
Высокая прочность крепления резины с металлом через эбонитовую прослойку обусловливается межмолекулярным взаимодействием полярных серосодержащих групп эбонита с металлом, малой деформируемостью эбонита и высокой прочностью связи между эбонитом и резиной в результате совместной вулканизации.
Наличие молекулярного контакта между резиной и слоем эбонитовой смеси к началу вулканизации не является обязательным, так как связи между ними возникают значительно позже, когда эбонитовая смесь и резина находятся в стадии размягчения и опрессование полностью заканчивается.
К преимуществам крепления через эбонитовую прослойку относятся простота и надежность метода. Однако имеются и существенные недостатки, обусловленные специфическими свойствами самого эбонита.
Рис. 1. Зависимость прочности связи резины с металлом от температуры при креплении различными способами:
1 — клеем лейконат; 2 — через эбонитовую прослойку.
При температуре выше 60 °C эбонит размягчается, что снижает прочность крепления в несколько раз. Термический коэффициент линейного расширения у эбонита в 3—5 раз больше, чем у металла, поэтому при резких изменениях температуры эбонит нередко отслаивается от металла, а при низких температурах — растрескивается. При больших давлениях во время вулканизации эбонитовая смесь, сильно размягчаясь, легко смещается по поверхности металла и при отсутствии на бандажах закраин выдавливается на торцы. При небольшой толщине резинового массива эбонит вследствие своей хрупкости легко разрушается при эксплуатации шин в условиях динамических нагрузок большой частоты. Для «удержания» эбонитовой прослойки и для увеличения площади сцепления эбонита с металлом на поверхности бандажей и ободов-ступиц, подлежащей обрезиниванию, необходимо делать рифления в форме «ласточкина хвоста». К недостаткам способа следует отнести также трудоемкость наложения эбонитовой прослойки на рифленую поверхность бандажей и ободов-ступиц.
Тем не менее этот способ крепления резины к металлу в производстве массивных шин применяется довольно часто.
Клеевое крепление. Наиболее широкое распространение в промышленности получило крепление резины к металлу различными клеями горячего отверждения. Клеи представляют собой растворы органических высокомолекулярных веществ в органических растворителях. Они обладают хорошей адгезией как к металлу, так и к резине, и способны удерживать их после затвердевания пленки клея.
К клеям, применяемым для крепления резины к металлам, предъявляют следующие требования:
— высокая прочность крепления после склеивания;
— универсальность, т. е. возможность склеивания разных резин с различными металлами;
— высокая клеящая способность и хорошая схватываемость;
— малая токсичность и огневзрывоопасность;
— продолжительная сохранность при перевозках и хранении;
— способность клеевого соединения не вызывать коррозии на поверхности металлов как в процессе обрезинивания, так и при эксплуатации;
— стойкость клеевого соединения к старению любого вида;
— сохранение эластичности клеевого соединения после крепления резины к металлу;
— способность клеевого соединения воспринимать ударную нагрузку без разрушения;
— низкая стоимость клея, малый расход на изготовление одного изделия.
Современная промышленность располагает клеями, которые способны удовлетворить большинству приведенных выше требований.
Клеи на основе изоцианатов. Наибольшее распространение в резиновой и шинной отраслях промышленности получили клеи на основе изоцианатов [24]. В производстве массивных шин применяется в основном клей «лейконат».
Способ крепления резины к металлу при помощи клеев по сравнению с креплением через латунную или эбонитовую прослойки проще, дешевле, позволяет механизировать производство. Массивные шины с клеевым креплением резины к бандажам или ободам-ступицам более выносливы в тяжелых динамических и температурных условиях, хорошо переносят ударные нагрузки и вибрации.
Прочность крепления на границе клей—металл обусловливается химическим взаимодействием изоцианатных групп с оксидными и гидроксидными группами на поверхности металла и прочностью образующихся связей. Прочность крепления с резиной определяется взаимодействием изоцианатных групп с молекулами каучука, а также диффузией изоцианата в слой каучука с дальнейшей полимеризацией в нем.
Хорошая адгезия достигается при тщательной очистке поверхности металла.
Исследованиями установлены некоторые особенности применения лейконата для крепления резины к металлам. На прочность крепления оказывают влияние такие факторы, как толщина клеевой пленки, температура и продолжительность сушки, влажность воздуха, давление при формовании и вулканизации. Разбавление клея дихлорэтаном в отношении 1 : 1 или 1 : 3 не снижает прочности крепления, но дает возможность получить более равномерную и тонкую пленку.
(более 65%) возможно увлажнение поверхности бандажей (ободов-ступиц).
Затвердевшая после испарения растворителя пленка лейконата вновь размягчается при нагревании и легко смещается. При длительном воздействии высокой температуры пленка клея становится менее подвижной и отверждается. Смещение пленки клея в начальный период ее размягчения не влияет на прочность крепления. Однако, если в это время происходит интенсивное течение резиновой смеси, то оно может вызвать дефекты крепления. Степень снижения адгезионных свойств клеевой пленки практически одинакова как в случае смещения пленки после нагревания, так и в случае одного только нагревания без смещения, и связана со структурными изменениями самого изоцианата под действием высокой температуры.
Поэтому хранение металлических бандажей и ободов-ступиц после нанесения лейконата до наложения резиновой смеси и вулканизации не должно превышать 8 ч.
На прочность крепления резины к металлу влияют также условия вулканизации. Связь между резиновым слоем и клеевой пленкой образуется уже в первые минуты формования и вулканизации. При испытании образцов, вулканизовавшихся всего 5 мин, не наблюдается оголения пленки клея, тонкий слой резины удерживается на металле. Для получения достаточной прочности крепления еще до начала вуканизации должен быть обеспечен контакт резиновой смеси со всей поверхностью металла, на которую нанесен клей. Значительное течение резиновой смеси в пресс-форме при вулканизации допустимо только в начальный период размягчения клеевой пленки, так как нагревание в течение 5—7 мин уже приводит к структурированию пленки и понижению адгезионных свойств клея. После того, как резиновая масса опрессована и по всей поверхности прижата к металлу, сама вулканизация может производиться при давлении, достаточном лишь для того, чтобы удержать пресс-форму закрытой.
Клеи на основе хлорированных каучуков. В последние годы широкое распространение получили клеевые композиции на основе поли-2,3-дихлорбутадиена: «хемлок», «тай-плай», «хемосил» и др. Они обладают ценным комплексом технологических и эксплуатационных свойств. Эти клеи считаются лучшими средствами горячего крепления резин к металлам, обладают хорошей адгезией к резинам практически на основе всех каучуков как общего, так и специального назначения. Клеевое соединение отличается высокой прочностью, стойкостью к тепловому старению, а также действию влаги, растворителей и масел. Гибкость клеевой пленки обеспечивает прочность соединения при воздействии динамических нагрузок. Основным достоинством этих клеев является то, что их применение не требует такого строгого соблюдения условий технологического процесса как в случае применения изоцианатных клеев. Наибольшее распространение получили клеи хемосил-211 и хемосил-220 (221) ф. «Henkel» (ФРГ).
Для обеспечения надежности клеевого соединения в тяжелых условиях эксплуатации, в которых обычно работают массивные шины, необходимо применять двухслойную систему клеев: первый слой — хемосил-211, второй слой — хемосил-220 (221), который наносят после просушки в течение 25—40 мин первого слоя. Это в определенной степени усложняет технологию подготовки металлической арматуры перед наложением резины, а наличие плотного быстрообразующегося осадка в этих клеях требует их периодического тщательного перемешивания.
Помещения, где производится нанесение клеев хемосил на металлическую арматуру (бандажи, обода-ступицы) и сушка, должны быть оборудованы принудительной вентиляцией для удаления паров растворителей ввиду их высокой токсичности.
Отечественная промышленность клеи типа «хемосил» пока не выпускает.
Способы нанесения клеев. Клеи наносят пульверизацией (распылением), кистями или щетками, маканием.
Пульверизация из краскораспылителя позволяет наносить слой клея любой толщины и удобна в тех случаях, когда подготовке под крепление подлежит одна сторона плоской арматуры. Известно, что пленка лейконата должна быть равномерной, без подтеков и чем пленка тоньше, тем прочнее будет крепление. Оказалось, что это требование при нанесении лейконата на бандажи (обода-ступицы) пульверизацией выполнить не удается. Кроме того, пульверизация требует применения воздуха, очищенного и осушенного на специальных установках.
Маканием (погружением) наносят клей на детали небольших размеров, у которых обрезиниванию подлежит вся поверхность. Совершенно очевидно, что этот способ в применении к массивным шинам не обеспечивает нанесения тонкого равномерного слоя клея и приводит к значительному перерасходу клея.
Поэтому в производстве массивных шин клеи наносят путем легкого прижатия к обрезиниваемой поверхности вращающегося бандажа или обода-ступицы мягкой волосяной кисти или щетки, смоченной клеем.
Клеи для холодного крепления резины к металлу. Клеи холодного отверждения дают возможность производить крепление вулканизованной резины к металлам при обычной температуре (15—30 °C). Известны клеи для холодного крепления резины к различным материалам, которые кроме эластомера содержат в своем составе компоненты, способствующие его структурированию при температуре 18—23 °C и вводимые в клей перед его употреблением. К ним относятся клеи типа 88 и 88Н на основе хлоропренового каучука, а также ряд других.
На шинных заводах для производства массивных шин клеи холодного отверждения не применяют.
Сборки резины с металлом: рекомендации по проектированию и изготовлению
Сборки резина-металл состоят из эластомера, который формуется и химически связывается с чистой металлической поверхностью с помощью специального клея. В процессе литья под давлением, переноса или компрессионного формования вулканизация резины и отверждение клея происходят одновременно. Области применения включают небольшие виброопоры и массивные компоненты подвески вагонов весом более 200 фунтов.
Химические соединения могут быть прочными, но соединения резины с металлом должны по возможности включать механический фиксирующий механизм. Этот металлический замок может быть инкапсулирован, например, с прорезиненными головками болтов. Чтобы покрыть металл резиной, в подложке должно быть сквозное отверстие или другая деталь, такая как ручка или шейка, вокруг которой можно формовать резину.
Инженерам есть о чем подумать, когда речь идет о соединениях резины с металлом. Если клей выйдет из строя или резина не будет работать должным образом, деталь может выйти из строя преждевременно и потребовать замены, что может вывести актив из строя. Вот обзор пяти аспектов проектирования и производства. Для получения дополнительной информации или обсуждения вашего конкретного применения склеивания свяжитесь с нами.
№ 1 Конструкция детали и условия применения Геометрия детали может создавать проблемы для сборок с соединением резина-металл. Поскольку каучук, заполняющий форму, имеет низкую вязкость, существует риск того, что сложные детали могут быть покрыты неадекватно или неравномерно. Отвержденный клей также может подвергнуться воздействию, если поверхность раздела резина-металл подвергнется воздействию замкнутой жидкости, такой как горячая смесь гликоля и воды. Также важно выбрать эластомер, обеспечивающий необходимую устойчивость к окружающей среде.
Некоторые эластомеры легче склеивать из-за их более высокой полярности, более высокого уровня ненасыщенности, а также типа и количества наполнителей. Соединения с глиной и диоксидом кремния, как правило, легче связывать, в то время как соединения, которые содержат мало или совсем не содержат серы или содержат менее 40 частей на сотню сажи, обычно труднее склеивать. Этот ресурс от Parker LORD содержит дополнительную информацию.
#3 Подготовка металла и поверхности Для соединений резина-металл могут использоваться различные типы стали, латуни и алюминия. Поскольку свинец химически противодействует связыванию резины, металлы с самым низким содержанием свинца легче склеиваются. Подготовка поверхности металла также важна. Ржавчина, технологическое масло и смазочные материалы мешают склеиванию. Чтобы выдерживать суровые условия, металлическая подложка может потребовать химической обработки.
Выбор правильной системы покрытия имеет решающее значение. В большинстве случаев используется двухслойная система с грунтовкой и финишным покрытием; однако некоторые однокомпонентные продукты также доступны. Системы покрытий также различаются по химическому составу и включают категории, включающие водные, гибридные и основанные на растворителе. Подготовка грунтовки и клея является ключевым моментом, но также важно наносить их таким образом, чтобы оптимизировать толщину сухой пленки клея.
#5 Процесс формования Независимо от того, какой процесс формования резины используется, формовщики должны оптимизировать давление в пресс-форме, вязкость эластомера и температурную однородность для прочности сцепления. Предварительный обжиг, нагрев деталей с покрытием при их загрузке в полости пресс-формы, оптимизирует условия отверждения и помогает предотвратить эрозию клея. Слишком высокая температура может привести к преждевременному отверждению клея и плохому соединению.
Для получения дополнительной информации о соединениях резины с металлом обращайтесь в The Rubber Group.
«Вулканизированное резино-металлическое соединение. Оптимизация параметров адгезии и когезии» — Vernay — Flow Control Solutions
(Примечание: «Оптимизация параметров адгезии и сцепления в вулканизированном резинометаллическом соединении», опубликованная в журнале Rubber World, выпуск за август 2014 г., была представлена «12-я -я -я Международная конференция по науке и технологии адгезии и адгезивов», Йорк, Великобритания, сентябрь 2013 г.)
«Вулканизированное резинометаллическое соединение, Оптимизация параметров адгезии и когезии»
Автор: Махмуд Кардан*, Стив Глэнси, Роберт Фергюсон; и Rebecca Seitz
Vernay, Yellow Springs, Ohio, USA
* Автор, ответственный за корреспонденцию: Mahmoud Kardan, Ph. D.
РЕФЕРАТ
Изучение сцепления резины с металлом в процессе формования является предметом постоянного обзора из-за его широкого разнообразия применений в медицине, потребительских товарах, полиграфии, автомобильной и аэрокосмической промышленности. Процесс, при котором резина вулканизируется и приклеивается непосредственно к металлической вставке, требует сложной технологии и понимания кинетики процесса вулканизации.
Процесс вулканизации представляет собой термически индуцированную стадию сшивки, которая придает сырой резине прочность, сопротивление течению и эластичность. Хотя вулканизация серой была обнаружена первой, ее применение было ограничено из-за некоторых экологических проблем. Кроме того, отверждение серой требует углерод-углеродной ненасыщенности каучука. С другой стороны, отверждение пероксидом позволяет вулканизировать как ненасыщенные, так и насыщенные каучуки, что приводит к образованию сетки со стабильной ковалентной углерод-углеродной связью с превосходной термостойкостью и стойкостью к растворителям, а также с хорошими показателями остаточной деформации при сжатии по сравнению с каучуками, отвержденными серой. Однако эти превосходные силы сцепления могут возникать за счет сил сцепления между резиновой смесью и металлическими подложками.
Это исследование касается изучения сил когезии и адгезии при соединении резины с металлом, отвержденной перекисью. Измеренные сдвиги внахлест между отвержденной резиной и металлической подложкой коррелируют со структурными изменениями, связанными с процессом отверждения резины, обнаруженными с помощью спектроскопии и термического анализа. Эти результаты могут оказать существенное влияние на механизм развития силы адгезионных сил соединения резины с металлом для получения однородного высококачественного продукта, не подверженного разрушению.
ВВЕДЕНИЕ:
Химические изменения полимеров позволяют создавать многочисленные новые классы высокомолекулярных соединений и изменять свойства и области применения синтетических полимеров в широком диапазоне. Примером такого химического превращения полимеров является вулканизация каучука для производства полезных резиновых изделий. Этот сложный химический и физико-химический процесс резко изменяет физико-механические свойства каучука. Эти изменения связаны, прежде всего, с химическими реакциями сшивки между полимерными молекулами.
Процесс вулканизации представляет собой термически индуцированную стадию сшивки, которая придает сырой резине прочность, сопротивление течению и эластичность. Начиная с первого эксперимента Гудьира по вулканизации при нагревании натурального каучука с небольшим количеством серы (1839 г.), этот процесс был наиболее практичным методом придания радикальных изменений свойств не только натуральному каучуку, но и диеновым синтетическим эластомерам, таким как бутадиен-стирольный каучук. , бутиловый и нитрильный каучуки. Однако с первых лет открытия вулканизации было обнаружено, что ни тепло, ни сера не являются существенными для процесса вулканизации. Отверждение серой требует углерод-углеродной ненасыщенности каучука. С другой стороны, отверждение пероксидом позволяет вулканизировать как ненасыщенные, так и насыщенные каучуки, что приводит к образованию сетки со стабильной ковалентной углерод-углеродной связью с превосходной термостойкостью и стойкостью к растворителям, а также с хорошей остаточной деформацией при сжатии по сравнению с каучуками, отвержденными серой. Тем не менее, использование соагентов в каучуках, отвержденных пероксидом, может привести к значительно более высокой плотности поперечных связей и лучшим механическим свойствам, таким как предел прочности при растяжении, модуль и твердость. Увеличение плотности поперечных связей, увеличение межмолекулярных сил в полимере изменит его конформацию, а также его ориентацию на металлической подложке.
Исследования Кардана и его сотрудников 1-6 показали, что когда полимер наносится на подложку, каждая структурная единица полимера имеет определенную ориентацию на внешней поверхности. Ориентация полимера на поверхности и его адгезия к подложке зависят от его конформационных изменений, на которые большое влияние оказывает взаимодействие полимера со средой 7-11 . Однако при пероксидной вулканизации, когда среднее число поперечных связей увеличивается, материал становится более жестким и хрупким и теряет свою гибкость для конформационных изменений, чтобы принять определенную ориентацию на поверхности подложки. Таким образом, превосходные силы сцепления эластомеров с пероксидным отверждением могут быть достигнуты за счет сил сцепления между резиновой смесью и металлическими подложками из-за жесткости макромолекулы и потери ее конформации в высокосшитом полимере. В этом исследовании ATR FT-IR используется в качестве основного метода для анализа микроструктурных изменений полимера в композитах, отвержденных пероксидом FKM. Корреляция результатов инфракрасного излучения с измеренным сдвигом внахлест для композитов, когда плотность поперечных связей увеличивается, может быть полезной для выяснения механизма отверждения перекисью и его связи с силами сцепления-когезии в эластомерах. Изучение адгезии вулканизированной резины к металлу в процессе литья представляет большой интерес, поскольку ее применение во многих областях, таких как медицина, товары народного потребления, полиграфия, автомобилестроение и аэрокосмическая промышленность, имеет важное значение для связывания с металлической поверхностью.
ЭКСПЕРИМЕНТАЛЬНАЯ ИНФОРМАЦИЯ
Смеси двух эластомеров FKM, имеющих одинаковую химическую структуру с различной вязкостью по Муни, были приготовлены для получения пригодной для переработки резиновой смеси. Затем из этой смеси были изготовлены композиты путем смешивания наполнителей, пероксида и вспомогательных агентов с резиновой смесью с использованием технологических добавок (запатентованных Vernay) в точно таких же условиях. Химическая структура пероксида, используемого в этом исследовании, представляет собой 2,5-диметил-2,5-ди-(трет-бутилпрокси)гексан. Для всех приготовленных композитов уровень смеси каучуков и всех ингредиентов, кроме пероксида, поддерживался постоянным. Уровень пероксида варьировали от 0,5 до 3,5 частей на сто частей каучука.
Для измерения физических свойств образцы каждого компаундированного композита формовали в виде пластин 6x6x 0,075 дюйма при 200°C в течение 2 минут и подвергали пост-отверждению в печи при 230°C в течение 4 часов. Эти формы затем разрезаются на различные формы, необходимые для проверки твердости, прочности на растяжение, модуля, удлинения и остаточной деформации при сжатии.
Кривые отверждения или реограммы для каждого композита были получены путем построения графика зависимости значений крутящего момента (силы) от времени в течение 6 минут при 180°С с использованием Monsanto Rheometer MDR (Moving Die Rheometer), модель 2000. В этом методе образец помещали между двумя умирает. Нижняя матрица колеблется, а верхняя матрица соединена с датчиком крутящего момента для измерения реакции резины на крутящий момент при деформации.
Для измерения остаточной деформации при сжатии для каждого композита были изготовлены цилиндры диаметром 1 дюйм ( ASTM Button) толщиной 0,5 дюйма, подготовленные путем формования при 200°C в течение 30 минут и последующего отверждения при 230°C в печи в течение 4 часов.
Для получения информации об ориентации молекул и конформационных изменениях полимера были получены спектры (область 400-4000 см -1 ) всех образцов соединений до и после отверждения пероксидом с использованием Varian 610 ATR FT-IR. Микроскоп спектрометр. Данные были сохранены в компьютере для дальнейшего анализа.
ДСК (дифференциальный сканирующий калориметр) использовали для изучения экзотермической реакции пероксида в каждом композите. Образцы каждого соединения (10-20 мг) подвергали одиночному циклу нагревания от 23°С до 250°С со скоростью 10°С в минуту с использованием модели TA Instruments DSC Q20-1558.
Стальные подложки шириной 2,54 см (один дюйм) промывали в толуоле, автоклавировали и сушили в печи. Для измерения силы сцепления со стальной подложкой образцы каждого композита были отформованы до 6,45 см 2 (один квадратный дюйм) подложки в течение 4 минут при 180°C. В этом процессе формования часть подложки оставалась несвязанной в виде хвоста подложки, а часть формованной резины (шириной один дюйм) оставалась несвязанной в виде резинового хвоста. . Все образцы подвергались постотверждению в течение 30 минут в печах при 230°С. Используя прибор для испытаний на растяжение Instron 5565, измеряли сдвиг внахлестку для каждого образца подготовленной резины, формованной на стальной подложке, путем объединения резины с подложки до отделения. .
РЕЗУЛЬТАТЫ И ОБСУЖДЕНИЕ
Замена водорода фтором в органических полимерах привела к получению материалов с замечательными характеристиками, называемых фторэластомерами (FKM). Одной из основных целей нашего анализа является характеристика структурных аспектов FKM в композитах при отверждении с различным количеством пероксида и того, как эти структурные единицы способствуют связыванию металлов. Коммерчески доступные FKM, используемые в этом исследовании, включают сополимеры винилиденфторида (VDF), гексафторпропилена (HFP), терполимеры тетрафторэтилена (TFE), а также перфторметилвиниловый эфир (PMVE) с содержанием фтора примерно от 66 до 70%. Характеристики FKM, особенно нерастворимость, могут быть улучшены путем вулканизации пероксидом. Отверждение FKM перекисью приводит к превосходной стойкости к пару, кислоте, агрессивным моторным маслам и химическим веществам.
В дополнение к отверждению перекисью эффективность FKM в агрессивных химикатах зависит от природы ингредиентов, используемых для формования конечных продуктов. Эти характеристики могут значительно различаться при изменении ингредиентов в рецептуре. В этом исследовании, сохраняя неизменными все ингредиенты, технологические добавки и сам процесс, поскольку они являются собственностью Vernay, мы концентрируемся на изменении содержания пероксида в процессе и изучаем его влияние на силы сцепления и адгезии FKM при формовании.
Одной из целей данного исследования является показать, что уровень содержания пероксида является критическим фактором в достижении степени модификации каучука для желаемого конечного применения, включая адгезию к подложке. В этом исследовании уровень содержания пероксида варьировался, исследовать силы сцепления в резине в зависимости от степени вулканизации.
Общепринято, что образование свободных радикалов в пероксиде является первой стадией вулканизации пероксида в качестве стадии инициации, за которой следует распространение и прекращение. На этапе распространения свободный радикал, образованный перекисью, отрывает атом водорода от полимерной цепи и создает другой свободный радикал на самом полимере, что вызывает образование поперечных связей, однако неясно, как возникает структурный беспорядок, когда перекись смешивается с полимером. резина. Также неясно, какие структурные различия существуют между каучуками, вулканизированными разным количеством пероксидов. Эти структурные изменения связаны с концентрацией пероксида и его взаимодействием со средой.
Из-за слабой связи между атомами кислорода перекись нестабильна и легко расщепляется на реакционноспособные свободные радикалы посредством гемолитического расщепления, то есть два электрона, которые участвуют в связи, распределяются один за другим между двумя частицами.
Эти свободные радикалы очень реактивны по отношению к другим веществам или даже к самим себе. В нашем случае первичный распад пероксида 2,5-диметил-2,5-ди(трет-бутилперокси)гексана приводит к образованию трет-бутоксирадикала, который может отрывать атом водорода с образованием трет- бутанол или разлагаются на метильный радикал ( 120 С) и ацетон. Этот метильный радикал может либо отрывать атом брома от полимера, либо присоединяться к соагенту с образованием более стабильного радикала. Этот стабильный радикал, в свою очередь, может отделять бром от полимера и генерировать полимерный свободный радикал для инициирования сшивки с использованием соагента в качестве сшивающего агента.
Теоретически следует ожидать одну поперечную связь на каждую молекулу пероксида, но на практике она ниже из-за побочных реакций, которые потребляют свободные радикалы. Например, при высоких температурах кислород может соединяться с радикалом в основной цепи полимера и образовывать гидроперекисный радикал, что вместо образования поперечных связей приводит к деградации полимера.
График измеренного сдвига в зависимости от удлинения для различных частей каучука в композите, приходящегося на затрудненную часть (pph) каучука, показан на Рис. поверхность уменьшается. Частично это может быть связано с конформационными изменениями полимера, как мы обсудим позже в этой статье. Стадия инициирования вулканизации пероксида (разложение пероксида) следует кинетике реакции первого порядка, т. Е. Расщепление молекулы пероксида пропорционально только концентрации пероксида в любой момент времени. Доминирующей чертой на рисунке 1 является резкое изменение графика, когда уровень пероксида превышает примерно 2 части на миллион. Кроме того, было интересно отметить, что по мере увеличения pph пероксида до определенного предела композит становится физически хрупким и вызывает нарушение когезии в системе. Это наблюдение предполагает, что когда уровень пероксида превышает определенный предел в каучуке, это может вызвать разрушение и нарушение когезии. Эти результаты показывают, что важно рассчитать или экспериментально получить оптимальную концентрацию пероксида при температуре отверждения полимерной смеси в данном композите, чтобы свести к минимуму остаточный пероксид, поскольку остаточный пероксид может привести к окислению и обрыву цепи или образованию дополнительные поперечные связи в зависимости от температуры во время процесса.
Экзотермические графики ДСК для композитов, использованных в этом исследовании, отвержденных различным количеством пероксидов, показаны на рис. 2. Один экзотермический пик для низких уровней пероксида обусловлен расщеплением пероксида на реактивные свободные радикалы и удалением водорода из полимера с образованием другого свободный радикал, который инициирует вулканизацию. Очевидно, что при превышении концентрации пероксида определенного уровня начинает формироваться вторая экзотермическая пачка, которая увеличивается по мере увеличения уровня пероксида. Механизм образования второго пика при микроструктурном анализе мы обсудим далее в этой статье. Этот пик указывает на образование побочных продуктов, обсуждавшихся выше, и не в пользу сил когезии или адгезионных связей между каучуком и металлической подложкой.
Таблица I суммирует результаты механических свойств, измеренных для композитов из смеси фторэластомеров, отвержденных с различными концентрациями (pph) пероксида. Прочность на растяжение при разрыве (напряжение при растяжении в момент разрыва испытуемого образца) достигает максимума при содержании пероксида около 1,5-2,0 частей на миллион. В этот момент композит становится жестким. Хотя при более высоких концентрациях перекиси она возрастает до еще более высоких значений, но композит становится более хрупким и теряет целостность.
Наша интерпретация результатов ДСК (рис. 2) и предела прочности при разрыве, показанных в таблице 1, согласуется с результатами сдвига, представленными на рис. 1. На рис. 1 резкое изменение графика при уровне пероксида 3,5 pph не связано с нарушение адгезии к подложке, но это произошло из-за нарушения когезии, которое вызывает разрыв композита задолго до нарушения адгезии.
Измеренное значение крутящего момента на кривых отверждения MDR для каждого композита, представленного на рис. 3, которое является прямым показателем модуля сдвига образца (сопротивление сдвиговой деформации), может не показывать таких резких изменений, когда концентрация пероксида превышает 2 pph, возможно , в связи с тем, что модуль сдвига не чувствителен к конформации полимера и его ориентации на поверхности подложки. Однако на рисунке 3 два важных параметра ts 1 и ts 2 , время, необходимое для увеличения на 1 единицу и 2 единицы от минимального крутящего момента, соответственно, такое же, как концентрация пероксида превышает 2 pph. Эти два параметра, ts 1 и ts 2 , известны как время подвулканизации и указывают время начала процесса сшивки. После достижения максимального крутящего момента небольшое изменение графика для избыточного количества пероксида (3,5 частей на миллион) может свидетельствовать о некоторой деградации при более высоких температурах. Это также согласуется с измерениями адгезионного сдвига и микроструктурными изменениями, которые описаны в следующем разделе.
При анализе микроструктурных изменений с помощью ATR FT-IR микроскопии наши обсуждения сначала будут сосредоточены на структуре смеси фторэластомеров, используемой в этом исследовании, а затем будут обсуждаться структурные изменения, поскольку будут обсуждаться различные количества пероксида, измельченного в каучуковом композите. Задача упрощается за счет анализа правильно распределенных инфракрасных колебаний, которые локализованы в природе с четко определенными переходными моментами.
На рис. 4 показано сравнение спектров НПВО для смеси фторэластомеров, использованной в этом исследовании, по сравнению с той же смесью, смешанной в мельнице в присутствии пероксида. Преобладающая полоса на рис. 3 около 1100 см -1 , который отнесен к C-F и C-F2 валентным колебаниям 12, 13 и, по-видимому, не показывает каких-либо значительных изменений интенсивности в зависимости от структуры упаковки полимера. Электроотрицательность атома фтора во фторэластомерах подразумевает сильные и очень короткие связи C-F, более высокую прочность связей C-C, а также очень сильные силы Ван-дер-Ваальса между атомами водорода и фтора 12, 13 в этих соединениях. Это приведет к недостатку подвижности атомов водорода в этих эластомерах и, следовательно, к отсутствию колебаний С-Н, активных в инфракрасном диапазоне. Из рисунка 4 совершенно очевидно, что для области растяжения СН в области 2800-3000 существуют существенные различия в интенсивности между полимером и полимером, смешанным в мельнице, в присутствии пероксида из-за разрыва некоторых водородных связей в полимере.
Хотя они не так хорошо изучены, инфракрасные активные полосы в высокочастотной области растяжения CH в диапазоне 2800-3000 могут содержать чрезвычайно богатую структурную информацию. Относительная интенсивность валентных колебаний метила и метилена дает ценную информацию об ориентации последовательностей С-С 1,4,5,6 на металлической поверхности, что влияет на адгезию полимера к подложке. Две полосы вблизи области 2923 см -1 и 2852 см -1 могут быть отнесены к асимметричному и симметричному валентным колебаниям Ch3 соответственно, а полоса вблизи 2954 см -1 можно отнести к асимметричным колебаниям Ч4. Две полосы вблизи 1428 см -1 (изгиб Ch3) и 1396 см -1 (колебание Ch3) также чувствительны к структуре полимерной упаковки и структурно-конформационным изменениям полимера в композите. Далее в этом разделе мы определяем и интерпретируем некоторые другие чувствительные полосы колебаний для растяжения СС, изгиба CF2 и скручивания Ch3.
Изменения интенсивности для области растяжения полимера C-H при отверждении с различными уровнями пероксида показаны на рисунке 5. Очевидно, что общие колебания метилена и метила C-H замедляются и имеют ограниченные движения по мере увеличения плотности поперечных связей в результате вулканизации с перекиси и поэтому их общая интенсивность снижается. Из рис. 5 видно, что суммарная интенсивность растяжения С-Н достигает своего минимального значения при уровне пероксида 1,5-2,0 pph для исследуемого композита. Поэтому мы интерпретируем этот уровень как максимальный и конструктивный уровень сшивки соединения. Интересно отметить, что по мере того, как пероксид превышает этот уровень, общая интенсивность C-H снова увеличивается. Это, скорее всего, связано с образованием побочных продуктов и некоторым разложением полимера, когда пероксид превышает этот уровень, как мы обсуждали ранее в этой статье. Дополнительным свидетельством максимальной поперечной связи при уровне пероксида около 2,0 частей на миллион является сдвиг волнового числа (энергии) для асимметричного колебания Ch3 от около 2923 почти до 2926 при максимальном сшивании и обратно до 2924 по мере того, как пероксид превышает оптимальный уровень.
Хотя общая вибрация растяжения C-H уменьшается по мере увеличения плотности поперечных связей, но асимметричных вибраций будет относительно больше по сравнению с симметричными вибрациями, если таковые имеются. Следовательно, мы далее интерпретируем увеличение асимметричных/симметричных колебаний Ch3 в инфракрасном диапазоне как увеличение плотности поперечных связей в соединении. Как видно на Рисунке 6, соотношение асимметричный/симметричный Ch3 резко возрастает для компаундов, отвержденных в печи, при 230°C, когда уровень пероксида увеличивается примерно до 1,5-2,0 частей на миллион, а затем выравнивается, что еще раз указывает на то, что избыточный уровень пероксида не способствует прочному и максимальному сшиванию и может повредить резину. Эти изменения менее выражены для компаундов, отвержденных в форме при 180°С. Не исключено, что эти различия являются результатом дальнейшего разложения полимера при 230°С из-за избыточного количества пероксида и в присутствии кислорода. Было интересно отметить, что соотношение выравнивается для тех же образцов после отверждения, которые выдерживались в течение 30 дней при комнатной температуре, что указывает на то, что разорванные связи снова сшиваются по мере старения отвержденного состава.
Однако природа этих воссоединенных соединений может отличаться от первоначальных отвержденных соединений.
Разложение полимера при 230°С в виде перекиси превышает оптимальный уровень, что может быть связано с предрасположенностью части этого эластомерного сополимера к гидролизу некоторых двойных связей и образованию карбонильной группы. Появление полосы около 1743 см-1 на фиг.4 указывает на образование этой группы в очень небольшом количестве, даже когда фторэластомеры компаундируют в присутствии пероксида без нагревания. Здесь мы утверждаем, основываясь на данных инфракрасного излучения, что, скорее всего, только часть ПВДФ фторэластомеров подвергается дегидрофторированию, когда уровень пероксида превышает определенный уровень и создает двойную связь. В свою очередь, эта двойная связь подвергается гидролизу с образованием карбонильной полосы.
Из-за сильных связей между углеродом и фтором, как упоминалось ранее, во фторэластомерах атомы углерода, с которыми связан фтор, колеблются со значительно меньшей амплитудой, чем атомы углерода, связанные с атомом водорода. Недельная полоса при 854 см -1 , появляющаяся при высоких уровнях пероксида в соединении на рис. 7, соответствует симметричному валентному колебанию С-С связи ПВДФ, рассчитанному анализом нормальных координат 12, 13 с небольшим вкладом растяжения. связи C-F (16%) и деформации угла H-C-H (12%). Делаем вывод, что дегидрофторирование из-за избыточного количества пероксида происходит на ПВДФ и, скорее всего, на другие сополимеры в ФКМ эти явления не повлияют. Группа, появляющаяся на высоте 765 см -1 , рассчитано на 761 см. -1 отнесено к CF 2, , который, очевидно, не чувствителен к дегидрофторированию. Кроме того, полоса 892, назначенная качательной вибрации Ch3, или полоса 942, рассчитанная на 938 и назначенная крутящейся вибрации Ch3, остаются постоянными во время этих изменений.
ВЫВОДЫ
Свойства, связанные с прочностью, такие как силы когезии и адгезии в отвержденных пероксидом композитах из фторэластомеров, чувствительны к уровню пероксида в композите. Наши результаты показывают, что существует оптимальный уровень пероксида, который следует использовать для балансировки сил когезии и адгезии для получения благоприятных связей во фторэластомерных системах, связанных с металлом. Эти оптимальные концентрации необходимо рассчитать или получить экспериментально для каждого композита на основе количества полимеров, их структуры и количества других ингредиентов, используемых в композите. Конформация полимера, уровень пероксида и степень, в которой сополимер может подвергаться дегидрофторированию, поскольку пероксид превышает оптимальный уровень, играют важную роль в когезионных силах каучука, т. резинометаллические адгезионные соединения.
Мы предоставили некоторые доказательства того, что часть ПВДФ сополимеров фторэластомеров претерпевает изменения, когда концентрация пероксида превышает оптимальный уровень в композите, и, скорее всего, остальные структуры сополимера остаются неизменными. Мы также продемонстрировали, что когда концентрация пероксида находится ниже оптимальных значений, плотность сшивки не оптимизируется, и целостность полимера не достигает максимального значения. .
РЕКОМЕНДАЦИИ
- Кардан, М., Химия и технология каучука , 74 , 614 (2001).
- Kardan, M., GAK Gummi Fasern Kunststoffe , Немецкое издание для полимерной промышленности 7, 435 (2002).
- Kardan, M., GAK Gummi Fasern Kunststoffe , Немецкое издание для полимерной промышленности 8, 520 (2003).
- Кардан, М. Кайто, А., Хсу, С.Л., Тхакур, Р., Лилия, К.П., J.Phys.Chem , 19, 1809 (1987).
- Кардан, М., Рейнхольд, Б.Б., Хсу, С.Л., Такур, Р., Лилия, С.П., Макромолекулы , 19, 616 (1986).
- Kaito, A. Kardan, M, Hsu, S.L., Thakur, R., Lillya, C.P., Polymer Preprints , 28, 11 (1987).
- Кардан, М., Новости резины и пластика , 6 августа 2001 г.
- Kardan, M, Производство клеев и герметиков , октябрь/ноябрь 2001 г.
- Kardan, M, Adhesive Ages , сентябрь 2000 г.
- Кардан, М., Лакокрасочная промышленность , май 2000 г.
- Кардан, М., Coating World , сентябрь 1999 г.
- Boerio F.J., Koeing, J.L., JPolymer Sci , A-2, 9 (1971) 1517).
Boerio F.J., Koenig, J.L., J.Polymer Sci , A2, 7(1969) 1489
, 2,0, 2,5 и 3,5 частей на миллион снизу вверх соответственно. вверху соответственно. Рисунок 3. Профиль MDR (6 минут при 180°C) композитов FKM с содержанием пероксида от 0,5 до 3,5 частей на миллион (снизу вверх) в композите. Таблица 1. Физические свойства композитов FKM, отвержденных с различными концентрациями пероксида. Рисунок 4. Спектры FT-IR с НПВО смеси компаундированного FKM, использованной в этом исследовании (нижние спектры), по сравнению с той же смесью, смешанной в измельченном виде в присутствии пероксида (спектры вверху).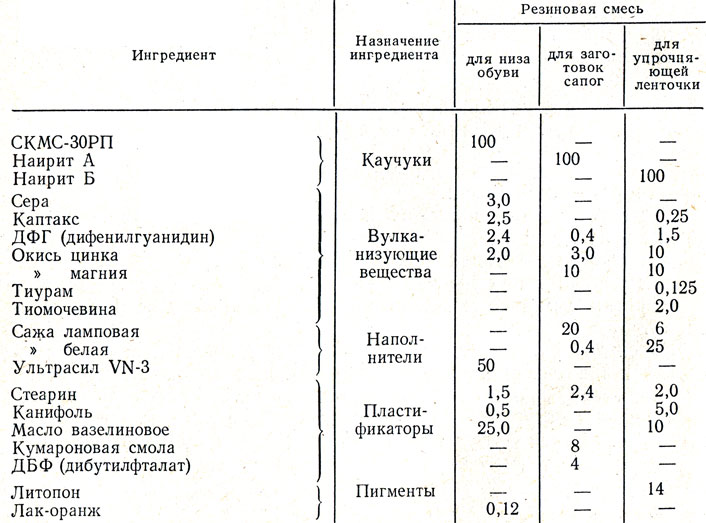