Теплопроводность чугуна и алюминия – Чугунные или алюминиевые батареи? | Строительный блог
alexxlab | 03.04.2020 | 1 | Разное
Чугунные или алюминиевые батареи? | Строительный блог
Наверное, все при ремонте сталкивались с такой проблемой, оставить чугунные батареи или поставить, модные сейчас алюминиевые батареи. Вопрос не легкий, до сих пор идут споры. Кто-то защищает чугунные батареи, мол — «проверены годами», кто-то однозначно стоит за алюминиевые батареи, называя их эстетичными и высокопроизводительными. У каждого, правда своя. Но все, же чугунные или алюминиевые батареи? Давайте подумаем……..
Отопительный период в условиях России тянется от двух до восьми месяцев в году, и чем севернее находится местность, тем отопительный сезон длится дольше. Также с каждым годом растут цены на энергоносители, газ, электричество. И вопрос экономии становится на первое место. Соответственно мы задаемся вопросом, как экономично нагреть пространство, какие трубы применить для отопления, из какого материала? Чугун или алюминий? Если вспомнить школьный курс физики, то становится понятно, что нагрев помещения зависит от такой величины как теплопроводность материала. Теплопроводность материала – это передача тепла от нагретых источников к холодным, посредством движения молекул и атомов. Так какой же металл стоит на первом месте по теплопроводности (я не беру драгоценные и дорогие металлы). На первом месте стоит медь, затем идет алюминий, а уже потом идут чугун и сталь. Причем теплопроводность алюминия, хуже, чем у меди в 4 раза, а теплопроводность чугуна хуже, теплопроводности меди в 8 – 10 раз. Так что самый лучший материал это медь. Однако медь достаточно дорогой и хрупкий материал. Радиатор из меди стоял бы в 3 – 4 раза дороже, чем из алюминия и в 10 раз дороже, чем чугунный. Теперь предлагаю поговорить о самих батареях.
Чугунная батарея
Как мы узнали, чугун имеет самую низкую теплопроводность. А при наличии своего локального отопления, от котла, вы будете тратить больше энергоносителей (газ, электричество) для отопления площади. Соответственно такая система будет работать неэффективно. Секция из чугуна весом в 8 килограмм, вмещает в себя 4,5 — 6 литров воды. Для того чтобы вам протопить комнату в 13 квадратных метров, вам нужно установить, чугунную батарею из 10 секций (примерно 1 секция протопит — 1,2 – 1,3 метра квадратных). Теперь представьте сколько нужно воды или незамерзающей жидкости, для того чтобы протопить полностью квартиру или дом. Это десятки, если не сотни литров. Большой объем воды требует большой теплоотдачи от котла, то есть котел должен работать практически на максимуме, разогревать жидкость до 70 – 80 градусов, чтобы в батарею она попала температурой 60 – 70 градусов. С эстетической части вопроса, чугун также проигрывает. Батареи из чугуна, сделаны грубо, и часто не вписываются в интерьер. На них конечно можно купить защитные белые щиты (или креативно украсить, под старину), но это дополнительные расходы. Единственный плюс чугунных батарей, это их прочность, по сравнению с оппонентом. Чугун очень прочный материал, и сломать такую батарею не просто, даже если вы что-то уроните или чем-то заденете ее. Конечно, подвержен ржавчине или гниению, однако этот процесс не такой быстрый как у стали. Наверное, все помнят чугунные батареи в доме у родителей, которые уже прослужили не один десяток лет. Если подвести итог, чугунная батарея это устаревший отопительный элемент. Теперь предлагаю поговорить об алюминиевой батарее.
Алюминиевая батарея
Давайте рассмотрим следующие типы батарей, на этот раз разговор пойдет об алюминии. Скажу сразу алюминиевая батарея намного эффективнее. Как мы уже разобрались выше, алюминий имеет большую теплопроводность, чем у чугуна. Одна секция алюминиевого радиатора, потребляет всего от 0,7 до 1,0 литра воды, то есть в 4 раза меньше, а тепло такая секция выделяет больше. В среднем 1 секция алюминиевого радиатора способна отопить 1,8 – 2,0 квадратных метра площади, что почти в два раза больше чем у чугуна. Вес одной секции алюминиевого радиатора около 2 килограмм. Так как алюминиевая батарея требует меньше жидкости, то и в системе отопления, такой жидкости будет намного меньше. Что позволит работать котлу (в частном доме), в щадящем режиме. Если у вас частный дом, то с алюминиевыми радиаторами, принято ставить газовый котел, который имеет двигатели. Эти двигатели толкают воду (жидкость) по системе отопления, а соответственно система быстрее нагревается и быстрее отдает тепло (алюминиевые батареи). Таким образом, экономии газа можно достичь до нескольких раз. На алюминиевые радиаторы можно поставить клапаны регулировки, это такие ручки которые позволяют регулировать температуру батареи, если в комнате слишком жарко, на чугун такие клапаны не устанавливаются. Опять же эстетически алюминиевая батарея намного выигрывает у чугунной, алюминий не гниет, а значит, такую батарею не нужно будет красить каждый год или два. Алюминий можно закрепить даже на стене из ГВЛ, потому как сама батарея очень легкая, а вот чугунную батарею закрепить на стене из ГВЛ не удастся, потому как она нереально тяжелая. Единственный минус таких батарей, это их хрупкость. Производители чтобы добиться максимальной теплоотдачи, делают стенки батарей очень тонкими, и поэтому, при установки нужно с ними обращаться очень аккуратно. Одно не правильное действие, и вам нужно будет покупать новую секцию. Также не стоит ничего ронять на алюминиевые батареи, по причине их хрупкости. Бывали случаи, когда край стола, резко придвинутого к батареи пробивал ее. Так что будьте аккуратны. Но есть и более прочные варианты батарей, так называемые БИМЕТАЛЛИЧЕСКИЕ.
Итог. Таким образом, алюминиевая батарея намного эффективнее, эстетичнее и, если так можно выразиться, экономичнее в эксплуатации. Чугун доживает свой век, к сожалению, чугунные батареи, как мне кажется, скоро сойдут на нет. На этом все.
remo-blog.ru
Что ставить: чугунные или алюминиевые батареи?
Насущный вопрос в наших краях. Осень и зима длятся добрых полгода, жилые помещения отапливаются еще дольше. Все это время в доме трудятся малозаметные глазу отопительные радиаторы, или батареи в просторечии. Все мы привыкли к старым унылым чугунным радиаторам. Но когда заходит дело о капитальном ремонте или даже строительстве нового жилья, поднимается вопрос о выборе новых радиаторов. Так что же ставить: чугунные или алюминиевые радиаторы?
Давайте для начала определимся с классификацией. В заголовок вынесен вопрос далекого от наших проблем человека. Он привык, что обычно стоит чугун, а в новое жилье обязательно покупаем алюминий. Но на самом деле все сложнее.
Существуют такие типы отопительных радиаторов: чугунные, алюминиевые, стальные панельные и биметаллические.
Чугунные радиаторы.
С чугунными радиаторами знакомы все, описывать их смысла нет.
Преимущества чугунных батарей:
1. Высокая устойчивость к коррозии. Во время эксплуатации внутри радиатора образуется сухая ржавчина, которая уберегает батарею от воздействия агрессивной среды. Чугун не боится агрессивных кислот, абразивного износа из-за песка и мусора, попадающего в отопительный контур.
2. Невысокая стоимость.
3. Большая тепловая инертность. После выключения подачи горячей воды батареи еще долго держат и отдают в помещение тепло.
4. Долговечность. Производители гарантируют чугунному радиатору службу не менее 30 лет. Известны массовые примеры, когда чугунные радиаторы никогда не менялись в хрущевках, простоявших 40 лет.
Недостатки батарей из чугуна:
1. Низкая теплопроводность металла и малая поверхность теплоотдачи.
2. Большая тепловая инертность иногда является недостатком, так как чугунные радиаторы совершенно не подходят для регулируемых автоматических систем водяного отопления.
4. Спорный дизайн, вписать который в современные модные интерьеры порой бывает проблематично.
Стальные радиаторы панельного типа
Стальные панельные радиаторы представляют собой два листа стали толщиной около 1,5 мм, которые стыкуются между собой либо горизонтальными коллекторами, соединенными вертикальными колонками, либо горизонтальными каналами, которые параллельно и последовательно приварены к одной панели.
Преимущества стальных радиаторов:
1. Большое количество типоразмеров.
2. Хорошая теплоотдача. Хорошо регулируются радиаторными термостатами, обладают малой тепловой инерцией. Хорошо приспособлены для регулируемых автоматических систем водяного отопления.
3. Малое водосодержание.
Недостатки стальных батарей отопления:
1. Слабая устойчивость к корозии. Это самый большой и главный недостаток. Не выносят слива теплоносителя, не любят открытых систем отопления и систем, в которых используются трубы, неустойчивые к диффузии кислорода воздуха (например, некоторые виды полипропиленовых труб). При самых благоприятных условиях скорость коррозии стали в год составляет 0,1 мм. Считайте сами: лет пять-шесть и металл на участках сварки пластин может быть уничтожен.
2. Низкое рабочее давление.
3. Малая площадь нагревательной поверхности.
Алюминиевые радиаторы.
Алюминиевые секционные радиаторы, изготовленные из алюминиевого сплава с добавлением кремния, стали очень популярными, так как они первыми попали на наш строительный рынок как альтернатива чугуну, к тому же они имеют привлекательные размеры и массу.
Алюминиевые радиаторы выпускаются в двух вариантах: литой и экструзионный. В первом случае каждую секцию радиатора отливают как цельную деталь, во втором — секция состоит из нескольких частей. Занимают как бы промежуточное положение между стальными и чугунными радиаторами и объединяют в себе практически все их преимущества и недостатки.
Преимущества алюминиевых радиаторов:
1. Высокий уровень теплоотдачи и скорость нагрева помещения. Хорошо приспособлены для регулируемых автоматических систем водяного отопления. Теоретики не стесняются говорить о 30-процентной экономии энергии при отоплении.
2. Высокое рабочее давление, причем от параметров рабочего давления зависит стоимость радиатора: чем оно выше, тем радиатор дороже.
3. Малая масса, элегантный дизайн. Возможность выбора оборудования с необходимым количеством секций и терморегуляция.
Недостатки алюминиевых батарей:
1. Подвержены электрохимической коррозии: при неправильном монтаже алюминий вступает в химическую реакцию со стальными и медными трубами отопительного контура. На срок службы влияет и химический состав теплоносителя, оптимальный уровень ph которого должен равняться 7-8.
Биметаллические радиаторы.
Это радиаторы со стальным сердечником и алюминиевой рубашкой, разработаны для использования при высоких давлениях теплоносителя. Отсюда следует не только название, но и отсутствие недостатков, свойственных стальным и алюминиевым радиаторам.
Преимущества биметаллических радиаторов:
1. Высокая степень теплоотдачи, которую обеспечивает алюминий. Это главное преимущество биметаллических радиаторов.
2. Устойчивы к коррозии. За счет того, что трубы биметаллического радиатора сделаны из стали, теплоноситель с алюминием не соприкасается, что позволяет избежать негативных химических реакций.
3. Выдерживают высокое рабочее давление. Разработаны для многоэтажного строительства.
Недостатки биметаллических батарей:
1. Обладают недостаточной площадью поверхности теплообмена, а, значит, и невысокой полезной мощностью.
2. Высокая цена. Применение в малоэтажном строительстве экономически нецелесообразно.
Таким образом, мы можем сделать некоторые выводы и дать определенные рекомендации.
Если вы живете в старом доме с центральным отоплением, смысла менять чугунные батареи на что-то другое нет. Биметаллические дороги и будут окислятся от воды неизвестного происхождения. Алюминий и сталь — то же самое. Замена батарей отопления из чугуна на алюминиевые или любые другие имеет смысл особенно тогда, когда вы решили изменить интерьер вашей квартиры, и чугунные радиаторы ну никак не вписываются в обстановку, жена расстроена и начинаются скандалы. Будьте готовы к авариям через несколько лет.
Сложно придумать причину, по которой можно рекомендовать установку стальных радиаторов. Бюджетный вариант. При выборе стальных батарей ориентируйтесь больше на дизайн и типоразмеры: технология производства стальных радиаторов везде одинакова. Поэтому изделия, чешского завода Kоrado сравнимы по качеству с немецким Kеrmi.
Алюминиевые радиаторы имеет смысл ставить в тех случаях, когда чугунные или стальные по каким-либо причинам не отвечают поставленным требованиям. Необходимо обращать внимание на производителя: качество радиатора во многом зависит от фирмы-изготовителя и качества исходного сырья. Отличный выбор для автономных систем отопления, когда владелец сам контролирует качество теплоносящей жидкости.
Биметаллические батареи стоит покупать для установки в новостройках с автономной домовой котельной.
housedb.ru
Шаг пятый. Медь vs алюминий
Шаг пятый.Предыдущие шажки можно увидеть здесь.
Достался мне тут недавно бракованный кулер Titan D5TB/Cu35. Все было нормально, но основание не отшлифовано совсем, медный пятак имел частые борозды видимо от отрезного станка глубиной примерно 0,5 мм.
Решено было – отполировать и поставить.
Эффект превзошел все ожидания. Температура, под нагрузкой, упала до 47 градусов.
Как это возможно? Алюминий эффективней меди?
В теории:
Теплопроводность:
Алюминий 180-200 Вт/м*К
Медь обычная 300-320 Вт/м*К
Плотность:
Рал=2700 кг/м3
Рмед=8940 кг/м3, где Р-плотность
Удельная теплоёмкость:
Алюминий – 880 Дж / кг*К
Медь – 385 Дж / кг*К
видим, что:
· плотность меди выше, чем у алюминия примерно в 3,31 раза
· теплопроводность меди выше, чем у алюминия примерно в 1,66-1,75 раза
· теплоёмкость медного радиатора меньше, чем у алюминиевого примерно в 2,28 раза, при равной массе.
Таким образом, если радиаторы одинаковые по размерам и форме, то выполненный из меди будет в 3,31 раза тяжелее, его теплоемкость будет примерно в 1.44 раз больше чем у алюминиевого. Следовательно, при одинаковой нагрузке медный радиатор нагреется в 1.44 раза меньше. При большей разнице температур между процессорным ядром и радиатором теплообмен проходит эффективнее, следовательно, медный радиатор лучше.
Но на практике, я заменил медный радиатор на алюминиевый и выиграл. Почему?
В данном случае я заменил небольшой, но тяжелый радиатор от Thermaltake Volcano 10, с частыми тонкими ребрами, на вдвое больший радиатор от Titan D5TB/Cu35 с достаточно редкими и толстыми ребрами. Масса радиаторов примерно равна, поэтому теплоемкость алюминиевого радиатора будет больше. Следовательно, нагреваться он будет дольше. Кроме того, сопротивление воздушному потоку меньше из-за большей ширины каналов. Следовательно, через алюминиевый радиатор проходит большее количество воздуха, и он (воздух) забирает больше тепла. Тепловой баланс устанавливается на низшей отметке температуры, так как, во-первых, за единицу времени больше тепла отдается в атмосферу вследствие большего количества проходящего воздуха, а площадь теплообмена у обоих радиаторов примерно равна. А во-вторых, сам радиатор нагревается медленнее вследствие большей теплоемкости, поэтому для достижения равной с медным радиатором температуры алюминиевому требуется больше времени, что усугубляет первое положение. Кроме того, возможно в радиаторе от Thermaltake Volcano 10 образовывались не продуваемые зоны, в которых застаивался теплый воздух.
Основное преимущество меди, большая теплопроводность, в данном случае существенного влияния не оказывает, ввиду слабого воздушного потока вследствие чего и алюминиевый и медный радиаторы успевают равномерно распределить тепло по поверхности своих ребер и, следовательно, единица площади ребер обоих радиаторов отдает воздуху примерно равное количество тепла.
Все, что здесь написано, отражает мою личную точку зрения и не более. Я не старался придерживаться классической терминологии и возможно применил неверные определения, за что прошу строго меня не судить.
Конструктивная критика принимается здесь.
overclockers.ru
ЧУГУН Теплопроводность – Энциклопедия по машиностроению XXL
Форма графита, его выделение и распределение также влияют ка теплопроводность. Например, высокопрочный чугун имеет более низкую теплопроводность, чем серый чугун. Теплопроводность чугуна с вермикулярным графитом (ЧВГ) выше, чем у ЧШГ, и близка к X серого чугуна с пластинчатым графитом [9]. [c.60]Поршни из алюминиевых сплавов обладают меньшей прочностью и износостойкостью, но значительно легче чугунных и применяются в двигателях с высокой частотой вращения. Поршень, изготовленный из алюминиевого сплава, несмотря на большую (для обеспечения необходимой прочности) толщину стенок, на 25—30 % легче чугунного. Теплопроводность алюминиевых сплавов в 3—4 раза выше, чем у чугуна, поэтому температу- [c.85]
Теплопроводность — это способность металла проводить тепло. Наиболее теплопроводными являются алюминий, медь и сплавы цветных металлов, менее теплопроводными — стали и чугуны. Теплопроводность имеет важное значение при нагреве металла. Чем меньше теплопроводность, тем больше опасность появления трещин при нагреве. [c.23]
Чистые металлы всегда обладают большей теплопроводностью, чем соответствующие сплавы. Малоуглеродистые стали обладают более высокой теплопроводностью, чем углеродистые стали и чугуны. Низкой теплопроводностью обладают высоколегированные кислотоупорные стали и чугуны. Теплопроводность материалов следует учитывать при изготовлении сварной аппаратуры, так как это определяет технологические режимы сварки и последующей термообработки. Обычно малая теплопроводность характеризует плохую свариваемость металлов и их склонность к образованию трещин при термической обработке. [c.79]
Для технических серых чугунов теплопроводность колеблется в пределах 0,110—0,137 кал/(см -с град) и уменьшается с повышением температуры. Однако склонность к росту, как уже указывалось, зависит еще от окисляемости чугуна, его газонасыщенности (особенно водородом), что в формуле (46) не учтено. Поэтому имеются расхождения в оценке склонности чугуна к росту по данным расчета и эксперимента. [c.148]
Таким образом, форма графита оказывает существенное влияние на уровень теплопроводности чугуна. Теплопроводность ЧВГ выше теплопроводности ЧШГ и близка к теплопроводности ЧПГ. Такая закономерность сохраняется и в интервале температур 100-500 °С, хотя теплопроводность всех чугунов с увеличением температуры снижается (табл. 3.4.16). [c.593]
Чугунные поршни отличаются малым коэффициентом линейного расширения, высокой прочностью и износостойкостью, но имеют большую массу по сравнению с алюминиевыми. Поршни из алюминиевых сплавов обладают меньшей прочностью и износостойкостью, но значительно легче чугунных. Теплопроводность алюминиевых сплавов в 3…4 раза выше, чем у чугуна, поэтому температура днища поршней из алюминиевых сплавов ниже, чем у чугунных поршней. В этой связи в двигателях с поршнями из алюминиевых сплавов улучшается наполнение цилиндра свежим зарядом и уменьшаются затраты энергии на трение поршня о цилиндр вследствие меньшего коэффициента трения алюминиевых сплавов. [c.167]
Для изготовления поршней двигателей обычно применяют алюминиевые сплавы, преимуществом которых являются малый удельный вес и высокая теплопроводность. Чугун более прочен и износоустойчив, но из-за большого удельного веса его применяют обычно для поршней относительно тихоходных двигателей. [c.439]
Коэффициент теплоотдачи от газов к ребристой поверхности а = 46,5 Вт/(м -°С) коэффициент теплопроводности чугуна Х = = 52,4 Вт/(м-°С). [c.23]
Под воздействием лазерного излучения за короткий промежуток времени (10″ —10″ с) поверхность детали из стали или чугуна нагревается до очень высоких температур Распространение теплоты в глубь металла осуществляется путем теплопроводности. После прекращения действия лазерного излучения происходит закалка нагретых участков, благодаря интенсивному отводу тепла в глубь металла (самозакалка). [c.225]
Теплоемкость серого чугуна также зависит от вышеперечисленных факторов и в интервале температур 0…700 °С равна 16 кал/(г С). Теплопроводность равна 0,16 кал/(см-с С). Средний коэффициент линейного термического расширения в интервале температур 0…100 С можно принять (10…11)1 О см/(см- С), а в интервале температур 100…700 С он равен НТО см/(см- С) [c.57]
Жидкотекучесть — способность жидкого металла полностью заполнять полости литейной формы и четко воспроизводить очертания отливки. Жидкотекучесть зависит от химического состава, температуры заливаемого в форму сплава и теплопроводности материала формы. Фосфор, кремний и углерод улучшают ее, а сера ухудшает. Серый чугун содержит углерода и кремния больше, чем сталь, и поэтому обладает лучшей жидкотекучестью. Повышение температуры жидкого металла улучшает жидкотекучесть, и чем выше его перегрев, тем более тонкостенную отливку можно получить. Увеличение теплопроводности материала формы снижает жидкотекучесть. Так, песчаная форма отводит теплоту медленнее и расплавленный металл заполняет ее лучше, чем металлическую форму, которая интенсивно охлаждает расплав. Минимально воз- [c.51]
Пример 10-5. Рассчитать теплоотдачу круглого чугунного ребра постоянной толщины S = 3,6 мм внутренний радиус ребра г- = 60 мм и наружный Га = 120 мм, коэффициент теплоотдачи а = 30 Вт/(м -°С), коэффициент теплопроводности чугуна X, = 30 Вг/(м °С), = 80°С. [c.313]
Основной задачей в области создания высокоэффективных типов фрикционных материалов остается создание материала со стабильным коэффициентом трения и высокой износоустойчивостью при работе в широких диапазонах температур. По-видимому, такими материалами все же будут металлокерамические накладки, не имеющие в своем составе органических веществ и, следовательно, мало изменяющие значение коэффициента трения при нагреве, а также обладающие относительно высокой износоустойчивостью. Наиболее вероятным путем создания фрикционных материалов для особо напряженных условий работы явится сочетание металлического жаростойкого компонента (например, нихрома или нержавеющей стали) и тугоплавких карбидов, но надо иметь в виду, что в этом случае применение чугунного контртела будет нецелесообразным из-за его недостаточной износоустойчивости. Высокая теплопроводность таких материалов позволит существенно уменьшить тепловой удар, возникающий на поверхности трения при интенсивной работе. Удовлетворительное решение проблемы создания надежной фрикционной пары современных высоконагруженных тормозов возможно только в случаях применения более теплостойких материалов, при одновременной разработке конструкций тормозов, обеспечивающих образование более низких температур нагрева поверхности трения. [c.588]
В замкнутом тормозе часть поверхности трения тормозного шкива соприкасается с фрикционной накладкой. В этом случае тепловой поток разделяется на две части, одна из которых расходуется на нагрев шкива, а другая — на нагрев накладки. Соотношение частей общего теплового потока определяется физическими свойствами трущихся тел. Совершенно очевидно, что если теплопроводность фрикционного материала будет высокой, то тепловой поток, проходящий через него, будет также велик, и нагрев тормозного шкива уменьшится. Анализ распределения теплового потока между двумя трущимися телами показывает, что при работе с фрикционным материалом на асбестовой основе (вальцованная лента, асбестовая тканая лента) только незначительная часть (3—4%) теплового потока расходуется на нагрев тормозной накладки, основная же часть его (96—97%) проходит через металлический тормозной шкив. При использовании фрикционных материалов металлокерамического типа (на медной или железной основе) через тормозную накладку проходит значительно большая часть теплового потока, а часть его, проходящая через тормозной шкив, снижается соответственно до 62% (при стальном шкиве) и до 79% (при чугунном шкиве). Таким образом, характер распространения тепла в фрикционной накладке определяет собой условие на границе исследуемого тела (шкива). Это условие также выражается уравнением Фурье [c.605]
Фиг. 360. Зависимость установившейся температуры от давления для колодочного тормоза ТК-300 с чугунным ждалось некоторым повышением температуры (фиг. 360). В первом случае это объясняется увеличением работы трения, приходящейся на каждый квадратный сантиметр поверхности трения накладки, во втором — возрастанием интенсивности торможения. Многочисленными опытами было доказано, что генерирование тепла зависит от скорости торможения чем быстрее тормозится машина, тем выше поднимается температура поверхности трения. При уменьшении времени торможения образование тепла происходит в более короткое время, и хотя теплопроводность шкива велика, она все же является конечной величиной, и для распределения тепла по массе шкива требуется некоторое время. Кроме того, наиболее интенсивное охлаждение происходит во время торможения, а так как уменьшается время торможения, то уменьшается и время наиболее интенсивного охлаждения. Надо отметить также, что при уменьшении времени торможения несколько увеличивается работа торможения, так как соответственно уменьшается тормозящее действие внутренних сил сопротивления механизма. Это обстоятельство также способствует увеличению температуры поверхности трения. | ![]() |
Теплопроводность. Теплопроводность сплавов и смесей, в отличие от теплоёмкости, не может быть определена по правилу смешения. Влияние отдельных элементов на теплопроводность чугуна [11] можно установить лишь приблизительно. Формулы для определения теплопроводности стали по её химическому составу не пригодны для чугуна, так как они не учитывают изменения структуры и, в частности, количества выделяющегося графита [36, 37]. [c.7]
Теплопроводность главнейших структурных составляющих чугуна выражается следующими данными [c.7]
Влияние фосфора приведено в табл. 10 [39], составленной для чугунов с приблизительно одинаковой структурой, за исключением увеличивающегося содержания фосфидной эвтектики. Расхождение значений теплопроводности с данными других исследователей [41,44] может быть объяснено тем, что фосфор [c.8]
Влияние фосфора на теплопроводность чугуна [c.8]
Влияние серы на теплопроводность не изучалось, но можно полагать [И], что этот элемент снижает теплопроводность чугунов. [c.8]
В противоположность рбычному чугуну теплопроводность у ЖЧС5Ш и ЖЧС5 мало различается и при этом возрастает с повышением температуры (рис. 1.67). У ферросилида она еще меньше и составляет около 0,025 кал/(см-с-°С). Плотность кремнистого чугуна снижается с повышением содержания 81 и колеблется в пределах 6,7—7,0 г/см . [c.116]
На структуру п Boii TBa серого чугуна существенное влияние оказывают его химический состав и скорость охлаждения отливок в форме. Углерод, кремний и марганец улучшают механические и литейные свойства чугуна. Сера вызывает отбел в тонких частях отливок и снижает жидкотекучесть. Фосфор придает чугуну хрупкость. Поэтому содержание серы и фосфора в сером чугуне должно быть минимальным. Увеличение скорости охлаждения достигается путем уменьшения толщины отливки и увеличения теплопроводности литейной формы. В тонких частях отливки у ее поверхности скорость кристаллизации будет выше, чем в более массивных частях и в сердцевине. Поэтому в тонких частях отливки образуется более мелкая структура с повышенным содержанием перлита и мелкими включениями графита, что обеспечивает высокие механические свойства этих зон. Там, где чугун затвердевает медленнее, образуется крупио- [c.158]
Определить количество теплоты, отдаваемой с поверхности ребра трубы длиной L—25QQ мм. Высота ребра h=30 мм, толщина ребра у поверхности трубы 6i=3 мм, толщина конца ребра бз=1 мм. Коэффициент теплопроводности чугуна Я,=52,3 Вт/(м.°С). [c.25]
Сочетание высокой прочности, вязкости, твердости, термо- и химо-стойкости, малой плотности, а также пшрокие возможности формоизменения и применения производительных методов формообразования — все это делает ситаллы перспективным конструкционным материалом. По механическим свойствам ситаллы близки к чугунам и могут во многих случаях заменить последние, выгодно отличаясь от них малой плотностью, гораздо более высокой твердостью и теплостойкостью. Однако следует учитывать их низкую теплопроводность. [c.192]
Пластмассовые колеса должны работать в паре со стальными или чугунными колесами достаточной твердости в связи с низкой теплопроводностью пластмасс и опасностью заеданий. Стальные колеса целесообразно закаливать до 45 HR , и шлифовать или перед закалкой шевинго-вать. Пластмассовые колеса делают уже, чем сопряженные, во избежание повышенного износа кромками сопряженных колес. [c.163]
Седла клапанов. Седла клапанов двигателей внутреннего сгорания работают в особо тяжелых ударно-переменных нагрузках и высоких температурных (700 – 1000°С) режимах. Поэтому к жаропрочному материалу для седел клапанов предъявляют особые требования необходимы высокая жаростойкость и сопротивление к газовой эрозии, коррозия и ползучести, высокие механические свойства, хорошая теплопроводность и небольшой коэ(1зфициент линейного расширения. В составе чугуна, кроме основных элементов (С, Si, Мп, S, Р), содержатся карбидообразующие элементы 2,75 – 3,25% Сг 4 – 5% Мо и до 0,3% Ni. [c.66]
По данным многочисленных исследований, степень эвтектично-сти чугуна для изложниц рекомендуется принимать близкой к единице (0,97 – 1,05). Для этого увеличивают содержание углерода, не повышая концентрацию кремния более 2%, так как кремний, растворяясь в феррите, снижает теплопроводность чугуна и повышает его хрупкость. Концентрацию углерода и кремния в чугуне рекомендуется поддерживать соответственно в пределах 3,4 – 4,2 и 1,4 – 2,2%. В чугунах для изложниц массой более 3 т содержание углерода целесообразно поддерживать на верхнем, а кремния – на нижнем пределах. [c.340]
Выбирая состав и структуру чугуна, не следует забывать, что необходимо стремиться к оптимальному сочетанию теплопроводности, пластических и прочностных свойств сплава. Изложницы из высокопрочного чугуна с шаровидным графитом характеризуются более высокой по сравнению с серым чугуном (в 1,5-2 раза) стойкостью при производстве мелких и средних слитков. Однако стойкость изложниц из чугуна с пластинчатым графитом для крупных слитков (массой более 50 т) мало отличается от стойк(Зсти таких же изложниц из чугуна с шаровидным графитом. [c.341]
Более перспективным материалом для изложниц, очеви.цно, является чугун с вермикулярным графитом. Особенностью этого материала является его более высокая (в 1,5 раза) теплопроводность по сравнению с чугуном, имеющим шаровидный графит. В то же время модуль упругости его значительно ниже. [c.341]
Хи.мически стойкие композиции для ремонта стеклоэмалевых покрытий Композиции для ремонта стеклоэмалевых покрытий должны обладать, помимо химической стойкости в рабочих средах, хорошей адгезией к металлу и стеклоэмали, теплопроводностью, достаточно высокой прочностью и низким коэффициентом термического расширения (КТР), близким к аналогичному показателю сталей и чугунов. Ряд композиций, удовлетворяющих в определенной мере сочетанию таких свойств, рекомендован к применению стандартом /93/ и приводится в табл. 13. [c.127]
Материалы фрикционных катков должны иметь высокий коэффициент трения /, что уменьшает требуемую силу прижатия F/, высокий модуль упругости Е, что уменьшает потери на трение высокую износостойкость контактную прочность и теплопроводность. Наиболее распространенное сочетание материалов катков закаленная сталь по закаленной стали чугун по чугуну текстолит, фибра или гетинакс по стали (в малонагруженных передачах). Иногда для повышения коэффициента трения один из катков облицовывают прессованным асбестом, прорезиненной тканью и т. п. Как правило, рекомендуется ведомый каток делать из более твердого материала, чтобы избежать образования на нем лысок, появляющихся при буксовании передачи. Буксование наступает при перегрузках, когда не соблюдается условие (7,1), При буксовании ведомый каток останавливается, а ведущий скользиг но нему, вызывая местный износ (лыски). Передачи с неметаллическими рабочими поверхностями могут работать только [c.112]
В табл. 11-1 приведены некоторые данные о значениях коэффициента теплопроводности для разных веществ. Из нее видно, что наихудшими проводникам тепла являются газы, для которых Я = 0,006 -f– 0,6 вт1 м-град). Некоторые чистые металлы, наоборот, отличаются высокими значениями X и для них величина его колеблется от 12 до 420 втЦм -град). Примеси к металлам вызывают значительное уменьшение коэффициента теплопроводности. Так, у чугуна X тем меньше, чем больше содержится в чугуне углерода. Для строительных материалов Я = 0,164-1,4 вт/ (м-град). Пористые материалы, плохо проводящие тепло, называют теплоизоляционными и для, них значения X находятся в пределах от 0,02 до 0,23 вт1 м-град). К этим материалам относят шлаковату, минеральную шерсть, диатомит, ньювель, совелит, асбест и др. Чем более порист материал, т. е- чем больше содержится в нем пузырьков малотеплопроводного воздуха, чем меньше его плотность, тем менее он теплопроводен. Очень широкое применение получил теплоизоляционный материал диатомит в 1 см которого содержится до 2-10 скорлупок, заполненных внутри воздухом. [c.139]
Материалы фрикционных катков должны обладать высоким коэффициентом трения, что уменьшает требуемую силу прижатия высоким модулем упругости, что уменьшает потери на трение, связанные с размерами площадки контакта контактной выносливостью износостойкостью и хорошей теплопроводностью. Последние два свойства особенно важны для передач, работающих всухую. Обычно один из катков изготовляют из качественной закаленной стали (например, ШХ15), а другой – из стали, серого чугуна. [c.296]
Изготовляются ребристые поверхности по-разному. В одних случаях они являются сплошной отливкой из чугуна, в других ребра изготовляются отдельно и затем прикрепляются к соответствующей поверхности. В последнем случае имеется то преимущество, что ребра можно изготовлять из другого, более теплопроводного материала, чем сама стенка, и вся конструкция может быть выполнена более легкой. Плотный контакт между стенкой и ребрами осуществляется путем насадки ребер в горячем состоянии и последующей пропайки мест соединения. Как правило, плоскость ребра должна быть направлена по движению рабочей жидкости, а при свободном движении — вертикально. Однако иногда с целью искусственной турбулизации потока жидкости и разрушения вязкого подслоя низкие и широко расставленные ребра устанавливаются и поперек потока. [c.193]
При трении фрикционного материала по металлам с различными значениями коэффициента теплопроводности Я в той паре, в которой металл обладает большим коэффициентом теплопроводности, поверхностная температура будет меньше, а температурный градиент во фрикционном материале — больше. Для этой пары значения коэффициента трения и износостойкость будут соответственно выше. На фиг. 327 показано изменение износостойкости вальцованной ленты 6КВ-10 при трении в одинаковых условиях по металлическим элементам, имеющим различную теплопроводность. Так, точка А получена при трении по стали 55ЛП, точка Б — по чугуну СЧ 15-32, а точка В — по биметаллическому шкиву, имеющему металлизированный слой, состоящий из 50% стали 10 и 50% Си. [c.551]
Металлическими элементами трущейся пары, сочетающими хорошие фрикционные свойства с высокой теплопроводностью и достаточной механической прочностью, являются хромистые бронзы типа Бр.Х0,8. В отношении износоустойчивости эта бронза в паре с материалом Ретинакс несколько уступает паре Ретинакс — ЧНМХ [190]. Однако вследствие более высокой теплопроводности бронзы (превышающей теплопроводность чугуна в 5 раз) температуры на поверхности трения оказываются более низкими и кривая и.зменения тормозного момента в процессе торможения не имеет характерного пикового возрастания к концу торможения, как это наблюдается при трении пара Ретинакс —ЧНМХ, что способствует увеличению плавности торможения. Максимальное значение коэффициента трения материала Ретинкс ФК-16Л по этой бронзе при температуре около 400° С было равно 0,45, а минимальное значение — 0,2. Для металлокерамики ФМК-8 соответственные значения коэффициента трения были 0,6 и 0,25. Поверхность трения бронзы после многократных торможений в паре с материалом Ретинакс покрывается /580 [c.580]
Углеродистые материалы используют также вместо шамотных огнеупоров. На всех современных доменных печах лещадь и горн сооружают из углеродистых блоков. Большая теплопроводность таких блоков улучшает теплопередачу от кладки к охлаждающим устройствам. Благодаря химической инертности к железу, шлаку и щелочам, лучшей сопротивляемости истиранию, чем шамотный кирпич, иесмачивае-мости чугуном, а также большой механической прочности при резких изменениях температуры угольные блоки с успехом применяют для футеровки спускных желобов доменных печей и вагранок. Тигли, лодочки, изложницы и формы различных конфигурации из углеграфита или особо чистых графитовых материалов используют в производстве твердых сплавов, для плавки высокотемпературных сплавов и получения сверхчистых металлов. [c.385]
В зависимости от используемых наполнителей пластмассы подразделяют на композитные и слоистые. Некоторые пластмассы представляют собой чистые смолы и применяются без наполнителей. Композиции из смолы и наполнителей обычно прочнее чистой смолы. Наполнитель влияет на водостойкость, химическую стойкость и диэлектрические свойства, на теплостойкость и твердость пластмассы. Наполнители существенно снижают стоимость пластмасс. Положительные свойства пластмасс малая плотность, удовлетворительная механическая прочность, не уступающая в ряде случаев цветным металлам и сплавам и серому чугуну химическая стойкость, водо-масло- и бензостойкость высокие электроизоляционные свойства фрикционные и антифрикционные шумо- и вибропоглощающие свойства возможность окрашивания в любой цвет малая трудоемкость переработки пластмасс в детали машин. Отдельные виды пластмасс обладают прозрачностью, превышающей прозрачность стекла. Вместе с тем, применение пластмасс ограничивается их отрицательными свойствами. Недостаточная теплостойкость некоторых разновидностей пластмасс вызывает их обугливание и разложение при температуре свыше 300° С. Эксплуатационная температура для изделий из пластмасс обычно не превышает 60° С и реже 120° С. Только пластмассы отдельных видов допускают эксплуатационную температуру 150—260 С и выше. Низкие теплопроводность и твердость, а также ползучесть пластмасс в ряде случаев нежелательны. Свойства и методы испытания пластмасс приведены ниже. [c.151]
Магний — пластичный металл блестящего серебристо-белого цвета. Плотность литого магния 1,737 г/см и уплотненного 1,739 г/см . Температура плавления 65ГС, кипения — 1107° С. Скрытая теплота плавления 70 кал/г. Теплопроводность 0,376 кал/(см-с-°С). Удельная теплоемкость, кал/(г-°С 0,241 — при 0° С 0,248 — при 20° С 0,254 — при 100 С и 0,312 — при 650° С. Коэффициент линейного расширения 25 10 +0,0188 г° (в пределах О—550° С). Удельное электрическое сопротивление при 18° С 0,047 Ом/(мм /м). Стандартный электродный потенциал 2,34 В. Электрохимический эквивалент 0,454 г/(А-ч). Магний неустойчив против коррозии, образующаяся поверхностная окисная пленка не защищает массу металла. Магний горюч, порошок или тонкая лента из него сгорают в воздухе с ярким ослепительным пламенем. Используется в магние-термии, в качестве твердого топлива — в реактивной технике. При повышения температуры возможно самовоспламененпе магниевого порошка или стружки. Магний устойчив против щелочей, фтористых солей, плавиковой кислоты и т. д. Чистый магний в качестве конструкционного материала почти не ис-по.льзуется, но является основой эффективных магниевых сплавов. Применяется в производстве стали, высокопрочного (магниевого) чугуна, для катодной защиты стали. [c.145]
mash-xxl.info
Чугун vs Алюминий. Во сколько раз чугун тяжелее алюминия?
Прицепился я к новым алюминиевым моторам. На тему, что алюминиевые блоки долго не «ходят» и т.д.
Не заглядывая в интернет, скажите, во сколько раз чугун тяжелее алюминия? В 10 раз? В 5 раз? Грубо говоря, если чугунный блок в нормальном моторе может выходить 500.000-1.000.000, а алюминиевый 150.000-200.000, то я был бы готов пожертвовать надежностью за разницу в весе в раз 5. Т.е. если чугунный блок весит 100 кг, а алюминиевый 20 кг, то это хорошо, я согласен, разница в 80 кг — это много.
А что на самом деле имеем? Т.к. алюминий менее прочный, то блок приходится делать чуть толще/больше. Движущиеся детали все равно делают из стали, п.э. в чугунных и алюминиевых моторах «патраха», допустим, будут одинаковыми.
А теперь, барабанная дробь, 1 кубометр алюминия весит 2.7 тонны, а чугуна 7.0 тонны.
Т.е. блок алюминиевый весит, в идеале, в два раза легче чугунного. А это значит, что в идеале, при весе чугунного блока 100 кг (это большой блок, а ля М30В35), алюминиевый будет весить 50 кг. При средней массе современного автомобиля 1500 кг. это 3% его массы))) Это мешок картошки в багажнике)))
Еще раз))) Мы пожертвовали надежностью двигателей за 3% массы автомобиля))) И при этом приобрели гемороя с надежность, хрупкостью, повышенным износом цилиндров, хитрыми покрытиями стенок цилиндров и т.д.
50 кг — это пара мощным аккумуляторов, которых даже не хватит для гибридного авто)))
Я бы понял, если алюминиевые блоки применяли только на спорт карах, там важен каждый грамм. Но на гражданском авто…. Только подумайте, на сколько производство чугуна дешевле, чем алюминия. На сколько капиталка чугунного блока проще и дешевле алюминиевого.
Если тебя уж очень приперло и хочешь уменьшить вес авто на 3%, то выкинь запаску (оставь докатку) и лишнее барахло в багажнике. Да современные кресла с электроприводами весят под 40-50 кг)))
А теперь еще возьмем малолитражный 4-х цилиндровый мотор, там экономия будет от силы 20 кг.))
Автопром+маркетинг=дорога в Ад ))
www.classicbmw.ru
Теплопроводность сплавов алюминия – технические характеристики.
Теплопроводность алюминия — это технический параметр, характеризующий свойства металла и сплавы на его основе. Значение этого показателя учитывается при формировании составов для изготовления литейных, деформируемых изделий, промышленного производства деталей и установок.
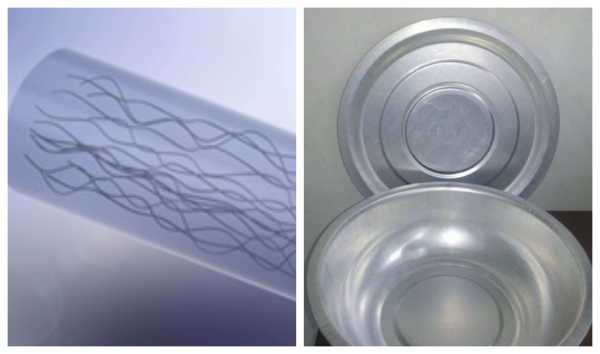
Характеристики теплопроводности учитываются при использовании его в производстве.
Характеристика теплопроводности материалов
Понятие теплопроводности материалов характеризуется способностью переносить тепловую энергию в пределах определенного объекта от нагретых частей к холодным. Процесс осуществляется атомами, молекулами, электронами и происходит в любых телах с неравномерным распределением температуры.
С позиций кинетической физики этот процесс происходит в результате взаимодействия частиц молекул более нагретых участков в пределах образца с другими элементами, отличающимися низшей температурой. Механизм и скорость переноса теплоты зависит от агрегатного состояния вещества.
Категория теплопроводности предусматривает определение скорости нагревания образца материала и перемещение температурной волны в определенном направлении. Показатель зависит от физических параметров:
- плотности;
- температуры фазового перехода в жидкое состояние
- скорости распространения звука (для диэлектриков).
Коэффициент теплопроводности равен количеству теплоты, которая проходит через единицу площади однородного материала за единицу времени при разнице температуры.
Физические свойства алюминия
Химический элемент алюминий имеет кубическую кристаллическую структуру. Его удельный вес при 20 °C составляет 2,7 г/см³, температура плавления — +657…+660,2 °C, скрытая теплота плавления — 94,6 °C.
Алюминий высокой чистоты кипит при +1800…+2060 °C. При нагревании увеличивается показатель удельной теплоемкости металла, проводимость тепла и коэффициент линейного расширения.
Электропроводность алюминия возрастает с понижением температуры: при 189 °C составляет 156 ед., а при 400 °C — 12,5.
Среди химических элементов алюминий отличается высокой активностью. Он легко реагирует с кислородом, образуя плотную окисную пленку, предохраняющую металл от дальнейшего влияния среды.
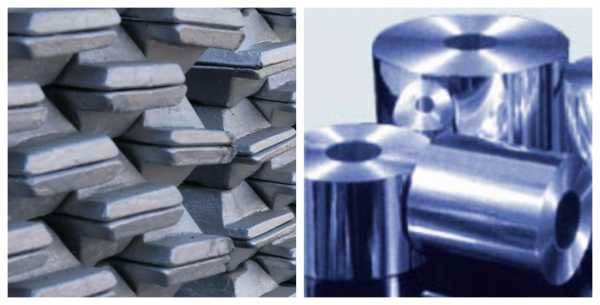
Свойства сплавов определяются входящими в его состав элементами.
По мере повышения температуры в металле растворяется водород, повышающий пористость материала. Примеси щелочных химических элементов (калия, натрия, кальция), кремния, магния способствуют резкому увеличению пористости алюминия.
Добавки меди, ниобия, никеля, марганца, железа, хрома, ванадия, циркония создают однородную структуру при остывании расплавленного материала. Влияние лигатурных добавок других компонентов на физические свойства металла и его сплавы учитывается в технологии литья изделий.
Наличие дополнительных материалов изменяет показатель проводимости тепла состава и температуру плавления. Например, при обычных условиях формирования алюминиевых сплавов сера и ее соединения уходят в шлак, не оказывая вредного влияния на свойства состава.
Такое же воздействие имеют фосфор, углерод, азот. Они не изменяют механические свойства сплава. Для производства литейных изделий из-за пониженной прочности чистый алюминий применяется редко.
Коррозионная стойкость металла тем выше, чем ниже в нем содержание примесей железа и кремния. Но их наличие несколько повышает прочность материала, снижая при этом пластичность и электропроводность.
Технические характеристики некоторых сплавов на основе алюминия
По технологическим особенностям сплавы подразделяются на основные группы:
- литейные — обладают повышенными литейными технологическими свойствами;
- деформируемые — легко поддаются обработке под давлением.
Например, создание алюминиевой конструкции, используемой в строительстве, требует особого вида сплава с повышенной прочностью, выдерживающего давление и нагрузку.
В зависимости от назначения составов на основе алюминия при их формировании руководствуются нормами и правилами, учитывающими:
- проводимость тепла материалом;
- точку перехода из расплава в твердое состояние;
- наличие лигатурных компонентов, влияющих на технические параметры состава и повышающих прочность.
Соотношение основного компонента к добавкам влияет на показатель проводимости тепла сплава, учитывающегося при изготовлении радиаторов и других видов изделий, предназначенных для монтажа тепловых коммуникаций.
Сводные данные о проводимости тепла алюминиевых сплавов собраны в специальных справочниках. В них приводятся значения распространенных сплавов металла с кремнием, магнием, медью, цинком, дюралюминия. Имеются характеристики литейных сплавов при различных температурах с указанием теплофизических свойств состава. Основными считаются показатели:
- плотности;
- коэффициента теплопроводности;
- коэффициента линейного теплового расширения;
- температуры изменения прочности;
- коррозионной устойчивости на воздухе;
- удельного электрического сопротивления.
Анализ данных свидетельствует о зависимости коэффициента теплопроводности от роста температуры и состава материала. Низкая теплопроводность свойственна в основном литейным составам на основе алюминия с маркировками АК4, АЛ1, АЛ8.
Наиболее высокой плотностью обладают составы основного компонента с кремнием, цинком. Из легких материалов наиболее плотным является состав, содержащий магний. Содержание меди в материале повышает его прочность и устойчивость к коррозии.
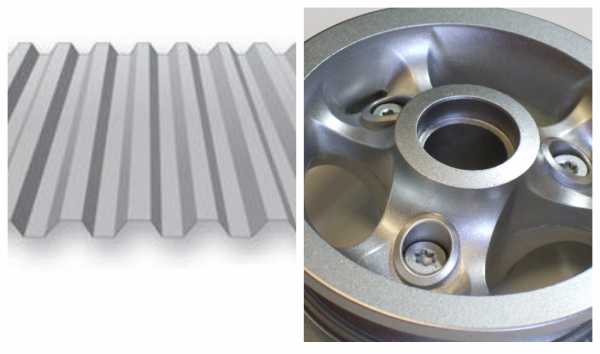
Самые плотные сплавы с цинком и магнием
Чем выше содержание в составе на основе алюминия, тем больше его теплопроводность, которая увеличивается при нагревании материала. Наличие лития в составе сплава приводит к уменьшению значения коэффициента теплопроводности.
Удельная теплоемкость сплава с содержанием магния и кремния увеличивается при нагревании. Среди алюминиевых сплавов системы Al-Cu-Mn наиболее теплопроводным является деформируемый состав Д20.
Он содержит в незначительных количествах (0,05–7%) примеси железа, кремния, марганца, титана, циркония, магния, цинка и 91–93,5% алюминия и предназначен для изготовления сварных изделий, работающих при комнатных или кратковременно повышенных температурах.
Похожие статьи
ometallah.com
Материал | Коэффициент теплопроводности, Вт/м*К |
Алебастровые плиты | 0,47 |
Алюминий | 230 |
Асбест (шифер) | 0,35 |
Асбест волокнистый | 0,15 |
Асбестоцемент | 1.76 |
Асбоцементные плиты | 0,35 |
Асфальт | 0,72 |
Асфальт в полах | 0,8 |
Бакелит | 0,23 |
Бетон на каменном щебне | 1,3 |
Бетон на песке | 0,7 |
Бетон пористый | 1,4 |
Бетон сплошной | 1,75 |
Бетон термоизоляционный | 0,18 |
Битум | 0,47 |
Бумага | 0,14 |
Вата минеральная легкая | 0,045 |
Вата минеральная тяжелая | 0,055 |
Вата хлопковая | 0,055 |
Вермикулитовые листы | 0,1 |
Войлок шерстяной | 0,045 |
Гипс строительный | 0,35 |
Глинозем | 2,33 |
Гравий (наполнитель) | 0,93 |
Гранит, базальт | 3,5 |
Грунт 10% воды | 1,75 |
Грунт 20% воды | 2,1 |
Грунт песчаный | 1,16 |
Грунт сухой | 0,4 |
Грунт утрамбованный | 1,05 |
Гудрон | 0,3 |
Древесина – доски | 0,15 |
Древесина – фанера | 0,15 |
Древесина твердых пород | 0,2 |
Древесно-стружечная плита ДСП | 0,2 |
Дюралюминий | 160 |
Железобетон | 1,7 |
Зола древесная | 0,15 |
Известняк | 1,7 |
Известь-песок раствор | 0,87 |
Иней | 0,47 |
Ипорка (вспененная смола) | 0,038 |
Камень | 1,4 |
Картон строительный многослойный | 0,13 |
Картон теплоизолированный БТК-1 | 0,04 |
Каучук вспененный | 0,03 |
Каучук натуральный | 0,042 |
Каучук фторированный | 0,055 |
Керамзитобетон | 0,2 |
Кирпич кремнеземный | 0,15 |
Кирпич пустотелый | 0,44 |
Кирпич силикатный | 0,81 |
Кирпич сплошной | 0,67 |
Кирпич шлаковый | 0,58 |
Кремнезистые плиты | 0,07 |
Латунь | 110 |
Лед 0°С -20°С -60°С | 2.21 2.44 2.91 |
Липа, береза, клен, дуб (15% влажности) | 0,15 |
Медь | 380 |
Мипора | 0,085 |
Опилки – засыпка | 0,095 |
Опилки древесные сухие | 0,065 |
ПВХ | 0,19 |
Пенобетон | 0,3 |
Пенопласт ПС-1 | 0,037 |
Пенопласт ПС-4 | 0,04 |
Пенопласт ПХВ-1 | 0,05 |
Пенопласт резопен ФРП | 0,045 |
Пенополистирол ПС-Б | 0,04 |
Пенополистирол ПС-БС | 0,04 |
Пенополиуретановые листы | 0,035 |
Пенополиуретановые панели | 0,025 |
Пеностекло легкое | 0,06 |
Пеностекло тяжелое | 0,08 |
Пергамин | 0,17 |
Перлит | 0,05 |
Перлито-цементные плиты | 0,08 |
Песок 0% влажности 10% влажности 20% влажности | 0.33 0.97 1.33 |
Песчаник обожженный | 1,5 |
Плитка облицовочная | 105 |
Плитка термоизоляционная ПМТБ-2 | 0,036 |
Полистирол | 0,082 |
Поролон | 0,04 |
Портландцемент раствор | 0,47 |
Пробковая плита | 0,043 |
Пробковые листы легкие | 0,035 |
Пробковые листы тяжелые | 0,05 |
Резина | 0,15 |
Рубероид | 0,17 |
Сланец | 2,1 |
Снег | 1,5 |
Сосна обыкновенная, ель, пихта (450…550 кг/куб.м, 15% влажности) | 0,15 |
Сосна смолистая (600…750 кг/куб.м, 15% влажности) | 0,23 |
Сталь | 52 |
Стекло | 1,15 |
Стекловата | 0,05 |
Стекловолокно | 0,036 |
Стеклотекстолит | 0,3 |
Стружки – набивка | 0,12 |
Тефлон | 0,25 |
Толь бумажный | 0,23 |
Цементные плиты | 1,92 |
Цемент-песок раствор | 1,2 |
Чугун | 56 |
Шлак гранулированный | 0,15 |
Шлак котельный | 0,29 |
Шлакобетон | 0,6 |
Штукатурка сухая | 0,21 |
Штукатурка цементная | 0,9 |
Эбонит | 0,16 |
Эбонит вспученный | 0,03 |
www.infrost.ru