Термическая обработка жаропрочных сталей: Термическая обработка аустенитных жаропрочных сталей и сплавов
alexxlab | 10.10.1984 | 0 | Разное
Термическая обработка жаропрочных сталей и сплавов :: Книги по металлургии
- КЛАССИФИКАЦИЯ ЖАРОПРОЧНЫХ СПЛАВОВ ПО ИХ ТЕРМИЧЕСКОЙ ОБРАБОТКЕ
Понятие «жаропрочные сплавы» объединяет большую группу металлических материалов, применяемых для изготовления деталей машин и конструкций, работающих под нагрузкой при повышенных температурах. Интервал таких рабочих температур очень широк (100—1000° С и более). Этим обусловливается большое разнообразие сплавов, используемых в качестве жаропрочных.
При сравнительно невысоких температурах (100—400° С) в качестве жаропрочных могут применяться обычные конструкционные стали (углеродистые и малолегированные), а также сплавы на основе меди, алюминия и титана. При более высоких температурах (500—700° С) применяются легированные стали перлитного, ферритного, (феррито-мартенситного) и аустенитного классов. Для работы при еще более высоких температурах (700— 1000° С) детали изготовляют из высоколегированных сплавов, содержащих железа меньше 50%, а также безжелезных сплавов на основе никеля, кобальта, хрома, молибдена и других металлов.
Для весьма высоких температур (выше 1000—1200° С) используются металлокерамические сплавы.
Разнообразие жаропрочных металлических сплавов, резко отличающихся между собой по химическому составу, способу производства, структуре и свойствам, естественно затрудняет их классифицирование. Наиболее рациональной на наш взгляд является классификация, предложенная П. Б. Михайловым-Михеевым . Она охватывает почти все металлические сплавы (кроме сплавов на основе меди, алюминия и некоторых других) и более полно по сравнению с ранее предложенными классификациями [2]—[5] учитывает признаки, по которым можно сплавы делить на группы.
По способности подвергаться термической обработке жаропрочные сплавы (как и все металлические сплавы вообще) можно разделить на три группы: сплавы, не имеющие вовсе фазовых превращений в твердом состоянии; сплавы, у которых фазовые превращения связаны с перестройкой кристаллической решетки (полиморфные превращения) и сплавы, у которых фазовые превращения обусловлены только изменением предельной растворимости избыточных компонентов при нагревании и охлаждении.
К первой группе относятся главным образом однофазные жаропрочные сплавы-твердые растворы, такие, например, как чисто ферритные и аустенитные стали, а также нихромы (не содержащие избыточных компонентов, образующих фазы выделения), молибдено-вольфрамовые и другие сплавы. Эти сплавы можно подвергать только такой термической обработке, при которой нагрев производится до температур, находящихся ниже линии солидуса.
Вторую группу составляют сплавы, претерпевающие полиморфные превращения. К ним относятся углеродистые стали и жаропрочные чугуны, мало- и среднелегированные стали перлитного и феррито-мартенситного классов, а также титановые, кобальтовые и другие сплавы.
К сплавам третьей группы относятся дисперсионно-твердеющие аустенитные стали, алюминиевые, никелехромовые и другие сплавы.
Сплавы второй и третьей групп можно подвергать всем видам термической обработки.
На фиг. 1 схематически представлена предлагаемая классификация жаропрочных сплавов по способности подвергаться термической обработке. Все сплавы делятся на три группы: сплавы на железной основе, на нежелезной основе и металлокерамические сплавы.
Первые две группы имеют по три подгруппы, в которых сплавы объединены по способности воспринимать термическую обработку. Металлокерамические сплавы в данной книге не рассматриваются.
К сплавам на железной основе отнесены углеродистые и легированные стали и жаропрочные чугуны. Согласно ГОСТ 5632-61 на коррозионностойкие, жаростойкие и жаропрочные стали и сплавы к легированным жаропрочным сталям условно отнесены сплавы, в которых содержание железа больше 50%. К железохромоникелевым сплавам условно отнесены сплавы, основной структурой которых является твердый раствор хрома и других элементов в железе. При этом суммарное содержание никеля и железа в них должно быть больше 65%. К жаропрочным никелевым сплавам по этому же ГОСТу условно отнесены сплавы, основной структурой которых является твердый раствор хрома (и других легирующих элементов) в никеле, если содержание Ni в сплаве превышает 55%.
Такой же принцип, несмотря на его условность, видимо, следует распространить и на другие сплавы на нежелезной основе — называть кобальтовыми, хромовыми и т. д. при содержании в них соответствующих элементов более 50—55%.
2. ВИДЫ ТЕРМИЧЕСКОЙ ОБРАБОТКИ, ПРИМЕНЯЕМОЙ ДЛЯ ЖАРОПРОЧНЫХ СПЛАВОВ И ЕЕ ТЕРМИНОЛОГИЯ
Многочисленные разновидности термической обработки, которой подвергаются черные и цветные металлы и сплавы, А. А. Бочвар разделил на пять видов [6]. В основу классификации положены изменения, происходящие в металлах (сплавах) при термической обработке — изменения фазового состава, структуры и свойств. Эта классификация получила широкое признание [7], [8] и др.
Рассмотрим виды термической обработки, применяемые для изделий из жаропрочных сплавов.
Отжиг 1-го рода. Заключается в нагреве до температуры, лежащей ниже линий диаграммы состояния, выдержки при этих температурах и охлаждения с определенной скоростью. Отжигу 1-го рода подвергаются главным образом однофазные жаропрочные сплавы-твердые растворы (нихромы, молибденовольфрамовые сплавы и др. ). Для этих сплавов такой отжиг является единственно возможным видом термической обработки, не считая химико-термическую. Отжиг преследует разные цели. Его применяют для снятия внутренних напряжений и восстановления структуры и свойств (прочности, пластичности, электропроводности и др.)» изменившихся в результате предшествовавшей обработки. Такой отжиг называется рекристаллизационным или возвратом. При этом нагрев производят до сравнительно невысоких температур. Отжигу 1-го рода также подвергают однофазные жаропрочные сплавы для устранения дендритной ликвации. В этом случае сплав нагревают до высоких температур, лежащих вблизи линии солидуса, выдерживают при этих температурах длительное время (десятки часов) для более полного и легкого происхождения процесса диффузии. Эта разновидность отжига 1-го рода является гомогенизацией или диффузионным отжигом.
Отжиг 1-го рода применим также и для термообработки жаропрочных сплавов, имеющих фазовые превращения. Для его осуществления сплавы нагревают до температур, находящихся ниже линии фазовых превращений.
Все процессы, происходящие при отжиге 1-го рода, являются необратимыми.
Отжиг 2-го рода. Отжигу 2-го рода подвергают только такие жаропрочные сплавы, которые имеют фазовые превращения в твердом состоянии. Если фазовые превращения обусловлены лишь изменением предельной растворимости, то происходит перекристаллизация только избыточных фаз — при нагреве выше линии предельной растворимости они полностью исчезают, растворяясь в основной фазе, а при охлаждении выделяются из твердого раствора, т. е. происходит их новая кристаллизация. Если же в сплаве возможны полиморфные превращения, то фазовые изменения при нагревании и охлаждении протекают во всем объеме — происходит перекристаллизация всех фазовых составляющих. Примером служит образование аустенита при переходе через верхнюю критическую точку при нагревании и образование смеси феррит + цементит при охлаждении у перлитных жаропрочных сталей.
Жаропрочные сплавы с фазовыми превращениями можно подвергать высокотемпературному диффузионному отжигу (гомогенизации) для устранения или уменьшения дендритной ликвации. По существу гомогенизация для таких сплавов является также разновидностью отжига 2-го рода, так как при этом происходит фазовая перекристаллизация.
Обычно диффузионный отжиг применяется для отливок сложной формы из высоколегированных многокомпонентных сплавов.
Закалка. Закалке могут подвергаться жаропрочные сплавы, не имеющие полиморфных превращений, и те, которые имеют их. В первом случае в результате закалки при комнатной температуре может быть зафиксировано состояние, свойственное высоким температурам, лежащим выше линии фазового превращения. Такую закалку А. А. Бочвар назвал «истинной закалкой». Структура сплава после закалки представляет собой пересыщенный твердый раствор. Характерным примером «истинной закалки» является закалка жаропрочыых дисперсионно-твердеющих аустенитных сталей и никелехромовых сплавов. В обоих случаях охлаждение от температур, лежащих в однофазной области с достаточно большой скоростью (превышающей критическую скорость закалки), фиксирует при комнатной температуре однофазное состояние, устойчивое только при высоких температурах (см. фиг. 2). При комнатной температуре это состояние сплава неустойчиво. Операция, в результате которой появилось такое состояние структуры, является типичной закалкой и нет никакой нужды давать ей другое название, как это делается, например, в технической литературе США, где она называется: «Solid Solution treatment» (обработка на твердый раствор).
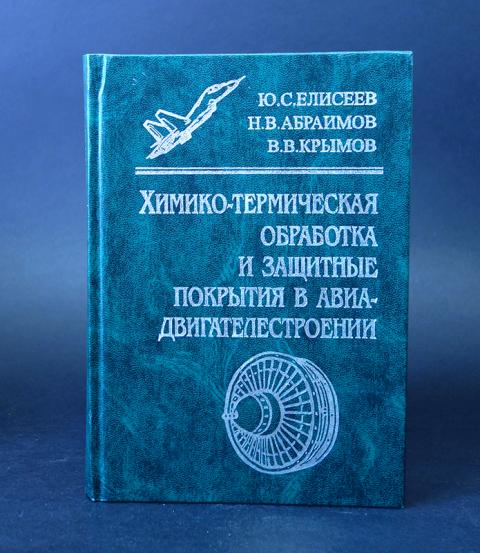
При закалке жаропрочных сплавов, имеющих полиморфные превращения, обычно образуется промежуточное состояние.
Однако и в сплавах, не имеющих полиморфных превращений, наблюдаются случаи, когда охлаждение, даже с весьма большой скоростью, не в состоянии полностью сохранить при комнатной температуре структуру, характерную для высокой температуры.
В этих случаях образуется неустойчивая структура из продуктов распада твердого раствора высокой степени дисперсности. Это сопровождается повышением твердости, прочности, а иногда и хрупкости. В частности, это наблюдается в некоторых высоколегированных никелехромовых сплавах.
Отпуск. Отпуск является всегда операцией вторичной, следующей после закалки, поэтому для упорядочения терминологии нецелесообразно операцию отжига 1-го рода (низкого отжига), которая по режиму похожа на отпуск (температура нагрева лежит ниже критических точек), называть высоким отпуском.
Термическая обработка Категория: Жаропрочное стальное литье Термическая обработка Литые хромоникелевые стали аустенитных марок характеризуются преимущественно крупнокристаллическим строением и большой степенью неоднородности химического состава в микрообъемах. В процессе длительной эксплуатации литых изделий, при высокой температуре, происходит выпадение карбидов из твердого раствора в виде мелкодисперсной фазы, которая затем коагулирует. Выделение карбидов хрома по границам зерен, вызываемое распадом твердого раствора, является главной причиной нестабильности стали и вызывает понижение пластичности, а также повышение склонности стали к межкристаллитной коррозии. Поэтому необходима стабилизация структуры литой стали аустенитных марок небольшими карбидообразующими добавками титана или ниобия. Эти элементы резко уменьшают количество карбидов хрома, выделяемых по границам зерен, и, следовательно, препятствуют обеднению основного твердого раствора хромом. Кроме карбидов хрома, в литой хромоникелевой стали аустенитных марок иногда обнаруживается в незначительных количествах хрупкая составляющая —сигма-фаза, которая, так же как и карбиды хрома, повышает склонность сплава к разупрочнению и межкристаллитной коррозии. Для уменьшения склонности к межкристаллитной коррозии аустенитных сталей рекомендуется понижение содержания углерода и, как уже ранее отмечалось, введение в сталь сильных карбидо-образующих элементов титана и ниобия в количествах, необходимых для полного связывания имеющегося в стали углерода в стойкие карбиды (TiC, NbC) или карбонитриды. В сталях, содержащих титан, принято иметь приблизительно пятикратное отношение титана к углероду, а в сталях, содержащих ниобий, восьми — десятикратное отношение ниобия к углероду. Сталь такого состава практически не склонна к межкристаллитной коррозии в электролите. Механические и жаропрочные свойства ее при комнатной и повышенных температурах значительно превышают свойства стали с обычным содержанием углерода и меньшим содержанием титана. Уменьшение содержания углерода до 0,06% в стали с ниобием приводит к появлению сигма-фазы. В отдельных случаях, а также при более высоких содержаниях углерода, кроме карбидов хрома, в литой хромоникелевой стали аустенитных марок иногда по границам зерен можно наблюдать образование сигма-фазы, что связано с наличием в стали ферритообразующих элементов в избыточном количестве. Ввиду того, что наличие сигма-фазы в стали крайне нежелательно, такие элементы следует добавлять точно в заданных количествах. Все эти процессы происходят в металле очень медленно, но так как срок службы деталей исчисляется несколькими десятками тысяч часов, то за это время в структуре металла, а следовательно, и в свойствах его происходят большие изменения. Перечисленные явления обнаруживаются испытаниями на ползучесть, длительную прочность, релаксацию, старение, усталость при высоких температурах. Для повышения механических свойств металла нужно, чтобы легирующие элементы, в особенности карбидообразующие, переводились в твердый раствор. Для более полного растворения углерода в аусте-ните и уменьшения выделенияшвторичных фаз отливки из стали таких марок следует подвергать закалке с последующеи стаоилизацией. Необходимо также учитывать, что теплопроводность стали аустенитных марок приблизительно в 3 раза меньше теплопроводности углеродистой стали, что дополнительно способствует локализации тепла в отдельных «термических» узлах отливки. Коэффициент же расширения стали таких марок больше углеродистых на 50%, поэтому надо иметь в виду более высокие остаточные напряжения и повышенное коробление отливок. Термическая обработка особенно важна для аустенитных отливок сложной конфигурации, у которых имеются особенно большие внутренние напряжения, резко понижающие эксплуатационные свойства деталей турбин. Крайне незначительное повышение механических свойств при комнатной температуре, наблюдаемое в стали аустенитных марок, после применения соответствующего режима термической обработки не является постоянным, так как происходящие при эксплуатации или при искусственном старении процессы постепенно приводят сталь в более равновесное для данных температурных, условий состояние. В структуре литых деталей турбин из аустенитной стали по границам зерен довольно часто встречаются микро- и макротрещины. Большинство исследователей склонны возникновение этих трещин отнести за счет термических напряжений. В отдельных литературных источниках наличие внутрикристаллических трещин объясняется воздействием коррозионной среды и тепловых ударов в процессе термической обработки. Появление горячих трещин может быть объяснено также низкой температурой плавления эвтектики, в состав которой входит карбид ниобия, обладающий меньшей пластичностью в толстостенных отливках. Исследования структуры опытных и промышленных отливок из стали аустенитных марок ЛА1, ЛАЗ, ЛА4, 1Х20Н12Т-Л и др. показывают, что в тонких сечениях (40—80 мм) наблюдается преимущественно крупное столбчатое строение с направлением кристаллов от поверхности к центру, а в более толстостенных отливках (80— 180 мм) наряду со столбчатым строением в центре наблюдаются зоны более мелких дезориентированных кристаллов. Освещаемые на страницах отечественной и зарубежной литературы взгляды по вопросам, связанным с определением оптимального размера зерна литого изделия из стали аустенитного класса, весьма разноречивы. Например, некоторые советские исследователи утверждают, что в условиях высоких температур крупнозернистое строение существенно влияет на жаропрочные свойства аустенитной стали в сторону понижения этих свойств. В работах отдельных зарубежных исследователей отмечается существенное влияние различных режимов термической обработки на величину зерна кованой стали. Например, длительная прочность сплава 18-8 почти совершенно не зависит от величины зерна, тогда как уменьшение величины зерна с № 2—5 до № 8 способствует существенному повышению удлинения при длительном разрыве. Свойства сплавов 25-20 и 25-12 также существенно меняются с изменением величины зерна. С уменьшением величины зерна предел длительной прочности указанных сплавов снижается. Отмечается, что роль величины зерна тем меньше, чем выше температура испытания, например, при температуре 870° величина зерна не оказывает практически никакого влияния. Наибольшее падение предела длительной прочности при уменьшении величины зерна с № 2/4 до № 8 наблюдаете для сплава 25-20 при температуре 538°. Соответственно понижается удлинение при испытании на длительный разрыв. Особенно заметно влияет величина зерна сплава 25-20 на предел ползучести. Уменьшение величины зерна с № 2/4 до № 8 при температуре 538° способствует понижению предела ползучести с 11 до 3,5 кг/мм2, т. е. приблизительно в 3 раза. С повышением температуры испытания сплава 25-20 влияние величины зерна на предел ползучести постепенно прекращается. Отдельными работами подтверждается, что на процессы ползучести влияют не только свойства собственно кристаллов, но и свойства вещества межкристаллитных прослоек. Отношение объема, занимаемого межкристаллитной прослойкой, к объему собственно кристаллов зависит от размера кристаллов. Это отношение в случае мелкозернистых сплавов больше, чем при крупнозернистых, так как объем межкристаллитного вещества при мелкозернистом строении наибольший. Термическая обработка отливок из стали Режим термической обработки для отливок из аустенитной стали ЛА1 разработан работниками ЦНИИТМАШа под руководством чл.-корр. АН СССР И. А. Одинга. Сталь ЛА1 обладает четко выраженной дендритной кристаллизацией, слабо поддающейся воздействию термической обработки. Вследствие отсутствия фазовых превращений в аустенитных сталях можно только незначительно повлиять на устранение транскристаллизации и дендритного строения отливки. Поэтому термической обработкой преследуются весьма ограниченные цели — гомогенизация твердого раствора с частичным растворением карбидов сложного состава (WC, Сг23С6, МоС, TiC, NbC). На основании многочисленных литературных данных для стали ЛА1 рекомендуется термическая обработка, состоящая из аусте-низации (закалки) и последующей стабилизации (высокого отпуска). С целью более полного перевода в твердый раствор карбидов хрома температура закалки повышается до 1175—1180°. Указанный режим термической обработки находит ширкое применение при производстве отливок из стали аустенитных марок типа ЛА1 для паровых и газовых турбин высоких параметров. Двойной режим термической обработки состоит из двух стадий: аустенизации, применяемой после отрезки литников и прибылей отливок, и последующей стабилизации, производимой после выборки литейных пороков, обдирки и заварки выбранных участков. АУСТЕНИЗАЦИЯ 1) Посадка в печь при температуре не выше 200°. Дальнейшее охлаждение на спокойном воздухе. СТАБИЛИЗАЦИЯ 1) Посадка в печь при температуре не выше 200°. Особый интерес представляет исследование влияния различных режимов термической обработки на качество отливок. Для изучения влияния сварочных напряжений в указанной отливке была произведена специальная выборка глубиной до 60 мм* которая затем была заварена, зачищена и протравлена. Подготовленная таким образом отливка была разрезана на части, подвергнута термической обработке по трем различным режимам термической обработки А, Б и” В. РЕЖИМ А — СТАБИЛИЗАЦИЯ ПОСЛЕ ЗАВАРКИ 1) Посадка в печь при температуре не выше 200°. РЕЖИМ В — СТАБИЛИЗАЦИЯ ПОСЛЕ АУСТЕНИЗАЦИИ ПО РЕЖИМУ Б 1) Посадка в печь при температуре не выше 200° С. После термической обработки по всем приведенным выше режимам каких-либо новых пороков на поверхности отливки не было, обнаружено. Проведенное исследование не позволило установить причины появления интеркристаллитных трещин в процессе заварки и последующей стабилизации, так как разрезка исследуемых частей отливки на мелкие темплеты, по-видимому, сняла имеющиеся напряжения. Заварка же и термическая обработка мелких частей отливки вряд ли могла повлиять на возникновение напряжений, способных вызвать, трещины и надрывы. Обширное исследование режимов термической обработки и влияние их на свойства металла было произведено ЦНИИТМАШем и НЗ им. Ленина на опытно-промышленной отливке из аустенитной стали ЛА4 (модификация стали ЛА1 с несколько повышенным содержанием титана). В качестве объекта для исследования служила отливка сопловой коробки паровой турбины СВК-150. Макроструктура металла этой отливки характеризуется темплетом, представленным на рис. Микроструктура стали в различных участках отливки несколько различна. Однако в большинстве участков она. в основном, состоит из крупнозернистой основы с небольшим количеством выделений состоящих главным образом из карбидов и карбонитридов титана которые достаточно равномерно располагаются в виде включений как внутри аустенитных зерен, так и в виде цепочек по их границам (рис. 2). Рис. 1. Макроструктура отливки сопловой коробки паровой турбины CBK-I50 из стали ЛA4. Рис. 2. Микроструктура металла отливки сопловой коробки паровой турбины СВК-150 из стали ЛА4. Для изучения влияния температуры нагрева при закалке на структуру стали ЛA4 литые заготовки незначительных размеров в лабораторных условиях подвергались нагреву в соляной ванне в течение около 20 мин. Структура и технологические свойства стали ЛА4 проверялись на более крупных промышленных отливках после приведенных ниже режимов термической обработки: Первые три режима термической обработки различаются только температурой максимального нагрева отливок. Все остальные условия термической обработки (скорости нагрева и охлаждения, длительность выдержек) одинаковые. Результаты механических испытаний образцов после различных режимов термической обработки не показывают преимущества того или иного режима термической обработки. Прочностные и пластические свойства стали ЛА4 при 650° в результате старения в течение 2300 и 3000 час. практически не меняются, что свидетельствует о малой чувствительности ее к изменениям режимов термической обработки. При исследовании структуры стали в зависимости от термической обработки для устранения влияния фактора массы образцы отбирали из одинаковых смежных участков отливки. При рассмотрении структуры отливок установить какую-либо зависимость ее от термической обработки не представилось возможным. Заметного роста зерен У стали ЛА4 не наблюдалось даже при очень высоких температурах (1250 и 1300° при кратковременных нагревах). При этих нагревах, по-видимому, возможны только незначительные изменения в структуре отдельных зерен, так как методом оптической металлографии (исключая электронную микроскопию) они не выявляются. Рис. 3. График режима термической обработки (первый вариант). Рис. 4. График режима термической обработки (второй вариант). Рис. 5. График режима термической обработки (третий вариант). При термической обработке с различными нагревами до температур 950, 1050 и 1150° количество выделенных вторичных фаз и характер их распределения во всех случаях остаются примерно одинаковыми. Более заметное изменение структуры стали ЛА4 наблюдается после длительного старения при 700°. При сопоставлении исходной и конечной структуры стали после длительной выдержки при 700° замечается увеличение количества мелких выделений вторичных фаз, концентрирующихся главным образом около границ аустенитных зерен. Выделение субмикроскопических вторичных фаз подтверждается повышением травимости микрошлифов при длительном старении. Рис. 6. График режима термической обработки (четвертый вариант): а — аустенизация; б — стабилизация. Дилатометрические испытания с повышением температуры термической обработки дают сближение кривых нагрева и охлаждения, а также размеров образцов до и после термической обработки. Проведенные исследования показывают, что более высокая температура (1150°) термической обработки стали JIA4 увеличивает стабильность ее при последующих нагревах. В зависимости от применяемого режима термической обработки показатели длительной прочности изменяются следующим образом. Образцы, вырезанные из отливки после термической обработки по режиму: посадка в печь при температуре 20—250°, нагрев до 500° со скоростью 30—50° в час, выдержка при 500° 3 часа, нагрев до 950° со скоростью 90—120° в час, нагрев до 1070° со скоростью 50° в час, выдержка 3—4 часа, охлаждение с печью до 850°, охлаждение до 250° со скоростью 25—30° в час, дальнейшее охлаждение на воздухе, имели при 650° предел длительной прочности, равный 8,5 кг/мм2. Металл этой же отливки после закалки со стабилизацией по режиму: закалка с 1150° после двухчасовой выдержки и последующая стабилизация при 800° в течение 10 час. —имеет предел длительной прочности (ст-105) при 650° — 10 кг!мм2 вместо 8,5 кг!мм2. Приведенные выше эксперименты и ряд других работ по исследованию режимов термической обработки свидетельствуют о том, что для аустенитной стали ЛА4 и ей подобных совмещенный режим термической обработки с максимальной температурой нагрева 1050° в отношении длительной прочности оказался менее рациональным, чем двойной режим термической обработки, состоящей из закалки при 1150° и последующей стабилизации при 800°. Подвергавшаяся исследованию литая сталь марки ЛА4 была выплавлена на свежих шихтовых материалах. В связи с необходимостью применения в качестве шихтовых материалов —50% отходов производства в виде прибылей, литников и продувки жидкой ванны кислородом возникает необходимость дополнительной проверки режима термической обработки для отливок из такой стали. Рис. 7. Дилатометрические кривые нагрева и охлаждения стали ЛA4: 1 — обработанной при 950”; 2 — обработанной при 1050°; 3 — обработанной при 1150° С. Результаты исследований стали ЛA4, выплавленной с применением 50% отходов в шихте, подтвердили целесообразность применения следующего режима термической обработки. Рис. 8. Макроструктура отливки обоймы уплотнения газовой турбины ГТ-12-3 из стали ЛA4. При 1050 —1080° —2 часа, нагрев до 1160°— 3 часа, выдержка при 1160 —1180°—4 часа и охлаждение на воздухе. Указанный выше режим термической обработки был проверен на отливке обоймы уплотнения газовой турбины (плавка № 24214) и Дал положительные результаты. Макроструктура темплетов, вырезанных из разных частей отливки обоймы, характеризуется плотным строением и крупными столбчатыми кристаллами. — При изготовлении сварных узлов авиационных конструкций важное место занимает термическая обработка. Обычно термической обработке подвергаются детали и узлы из сталей, черных сплавов, титановых сплавов и некоторых других материалов. Узлы из легких сплавов, как правило, свариваются из предварительно закаленных и состаренных элементов и последующей термической обработке не подвергаются. При изготовлении сварных узлов из сталей и черных сплавов могут быть два варианта исходного состояния деталей перед сваркой. В первом случае детали термически обрабатываются только до сварки. По второму варианту узлы изготовляются из отожженных или нормализованных элементов с термической обработкой всей конструкции после сварки. Заготовки и узлы в соответствии с технологическим процессом их изготовления могут неоднократно подвергаться различным операциям термической обработки. Подготовительная термическая обработка имеет целью обычно подготовить материал, поступающий с металлургических заводов, к механической обработке, обработке давлением и сварке. В качестве операций подготовительной обработки для сталей, в частности, можно назвать: Промежуточная термическая обработка чаще применяется для узлов и конструкций, подвергающихся после сварки значительной правке или механической обработке. В качестве промежуточной термической обработки часто используются: 3. Закалка для аустенитных сталей и сплавов с целью снятия напряжений, выравнивания структуры и повышения пластичности. К промежуточной термической обработке можно отнести и предварительный подогрев деталей перед сваркой и сопутствующий нагрев сварных соединений при сварке, снимающий внутренние напряжения для предотвращения трещин. Окончательная термическая обработка ставит своей целью придание сварному узлу механических свойств, обусловленных техническими условиями и чертежом, а также снятие внутренних напряжений в изделии, появившихся в результате предыдущих операций. К операциям окончательной термической обработки относятся: Термообработку узлов после сварки стремятся проводить при минимальных припусках на последующую механическую обработку, а часто и при окончательных размерах. Но для крупных узлов со сложной конфигурацией обычные методы термической обработки часто сопровождаются возникновением больших короблений. Особенно это характерно для операции закалки. Правка же закаленных на высокую прочность узлов не всегда желательна ввиду возможности образования трещин. К тому же изотермическая обработка, снижая деформации, способствует тем самым уменьшению припусков на механическую доработку. Выдержка при охлаждении производится в селитровых ваннах при температуре 260 — 270 °С. Большое внимание необходимо также уделять правильному конструированию приспособлений для поддержания изделий при нагреве в закалочной печи, а также быстроте и удобству захвата узлов при выгрузке их из печи и переносе в селитровую ванну или закалочную ванну. Большое значение имеет также выбор правильного расположения изделия в печи в зависимости от его конфигурации. При этом основным требованием является устранение возможности деформации узла за счет провисания его под собственной тяжестью. Охлажденные на воздухе после обработки в селитровой ванне узлы должны быть немедленно и тщательно промыты в горячей воде во избежание разъедания металла, особенно на поверхностях с окончательными размерами. Обычно детали после заготовительно-штамповочных работ, связанных с нагартовкой материала, подвергаются отжигу для снятия имеющихся напряжений с последующим травлением для снятия поверхностных окислов. Детали из титановых сплавов, подвергаемые сварке плавлением, и сварочную проволоку желательно отжигать в вакууме с целью снижения содержания водорода и, как следствие, повышения их пластичности. Отжиг производится при температуре 700 — 800° С и вакууме 10~3 — 10~4 мм рт. .ст. в течение 1 — 2 час. В качестве окончательной термической обработки также обычно используется отжиг. Отжиг титановых сплавов, как правило, не воздействует на механические свойства сварных соединений (для сплавов типа ВТ-1, ВТ-4, 0Т4 и др.), но снижает внутренние напряжения, возникающие в изделии при сварке. Целесообразно отжиг производить в приспособлениях, не допускающих короблений узлов. В некоторых случаях допускается производить местный отжиг сварных соединений с помощью газовой горелки. Операции термической обработки используются также для целого ряда других материалов и сплавов. В зависимости от типа материала и поставленных целей назначаются и соответствующие виды и режимы обработки. Эти вопросы излагаются в специальной литературе. Реклама:Читать далее:Термическая обработка отливок арматуры из стали 1Х20Н12Т-Л, 1Х18Н9Т-Л и других
Статьи по теме:
Главная → Справочник → Статьи → Блог → Форум |
Обратная связь ПОЗНАВАТЕЛЬНОЕ Сила воли ведет к действию, а позитивные действия формируют позитивное отношение Как определить диапазон голоса – ваш вокал Как цель узнает о ваших желаниях прежде, чем вы начнете действовать. Как компании прогнозируют привычки и манипулируют ими Целительная привычка Как самому избавиться от обидчивости Противоречивые взгляды на качества, присущие мужчинам Тренинг уверенности в себе Вкуснейший “Салат из свеклы с чесноком” Натюрморт и его изобразительные возможности Применение, как принимать мумие? Мумие для волос, лица, при переломах, при кровотечении и т.д. Как научиться брать на себя ответственность Зачем нужны границы в отношениях с детьми? Световозвращающие элементы на детской одежде Как победить свой возраст? Восемь уникальных способов, которые помогут достичь долголетия Как слышать голос Бога Классификация ожирения по ИМТ (ВОЗ) Глава 3. Оси и плоскости тела человека – Тело человека состоит из определенных топографических частей и участков, в которых расположены органы, мышцы, сосуды, нервы и т.д. Отёска стен и прирубка косяков – Когда на доме не достаёт окон и дверей, красивое высокое крыльцо ещё только в воображении, приходится подниматься с улицы в дом по трапу. Дифференциальные уравнения второго порядка (модель рынка с прогнозируемыми ценами) – В простых моделях рынка спрос и предложение обычно полагают зависящими только от текущей цены на товар. |
1. 2. Назовите способы упрочнения аустенитных сталей. 3. Основной вид термической обработки для гомогенных аустенитных сталей. 4. Назовите области использования аустенитных сталей. 5. Основные назначение легирования стали никелем. 6. Влияние хрома на свойства аустенитной жаропрочной стали. 7. Области применения никелевых сплавов в качестве жаропрочных. 8. Легирование никелевых жаропрочных сплавов. 9. Основные принципы легирования жаропрочных сплавов. 10. Основные свойства никелевых жаропрочных сплавов 11. Какие фазы снижают жаростойкость, жаропрочность и стабильность сплавов на никелевой основе? 12. Влияние внешних факторов на жаропрочность. 13. Жаропрочные А стали. Термообработка аустенитных сталей. 14. Зачем углеродистые стали легируют? Какой термической обработке подвергают легированные стали? 15. 16. Виды хрупкости хромистых и хромоникелевых сталей. 17. Где можно применять мартенситные и мартенситно-ферритные стали? 18. Какие недостатки присущи этим сталям? 19. Способы упрочнения М сталей. 20. Объясните влияние δ-феррита на уровень прочностных свойств. 21. Какой термической обработке подвергают высоколегированные стали для получения заданного уровня свойств? 22. Какие фазы упрочняют сплавы на никелевой основе? 23. Какова роль карбидной фазы в формировании структуры и свойств сплавов на никелевой основе? 24. Классификация никелевых жаропрочных сплавов. 25. Термическая обработка сплавов на никелевой основе, ее цель. 26. Упрочняющая обработка сплавов типа ХН77ТЮР, нимоников. 27. 28. Преимущества жаропрочных сплавов на основе кобальта. 29. Применение сплавов на основе кобальта. 30. Основные легирующие элементы сплавов на основе кобальта. Раздел 6 Стали и сплавы с особыми физическими свойствами. 1. Магнитотвердые сплавы. Требования. Термическая обработка. 2. Сплавы с низким коэффициентом линейного расширения. 3. Термопарные сплавы. Их термическая обработка. 4. Магнитотвердые сплавы и материалы. Их структура. Требования к ним. 5. Термообработка магнитомягких сталей. 6. Назначение пермаллоев и перминдюров. Что это за материалы? 7. Способы упрочнения сплавов типа элинвары. 8. Чем характерны термопарные сплавы? 9. Назначение термопарных сплавов. Температурный интервал их использования. 10. 11. Легирование сплавов с постоянным модулем упругости. 12. Инвар. Свойства, назначение. 13. Сплавы с низким коэффициентом линейного расширения. 14. Основные свойства, позволяющие применять платинит для пайки со стеклом. 15. Отличительные особенности инвара, суперинвара, платинита. 16. Назовите сплавы, имеющие высокий коэффициент удельного электросопротивления. 17. Назначение сплавов с высокий коэффициентом удельного электросопротивления.
КОНТРОЛЬНЫЕ ЗАДАНИЯ
1. Найти марку стали для изготовления роликов толкателей, имеющую твердость после обработки более 64 НRС. Определите режим ее термической обработки и объясните структурные изменения, происходящие в стали при термообработке. 2. Определите марку стали для изготовления крупных подшипников с диаметром шарика > 60 мм. 3. Опишите износостойкую сталь для работы при температуре до 500°С в агрессивной среде, для изготовления подшипников и втулок. Определите оптимальный режим термообработки. Объясните структурные превращения. Твердость должна быть не менее 57 НRС. 4. Найдите сталь для изготовления крупных подшипников прокатных станов, испытывающих в процессе работы сильные динамические нагрузки. Определите режим термической обработки с объяснением температурноскоростного режима. 5. Выберите сталь для изготовления подшипников на железнодорожный транспорт. Определите ее структуру, термообработки и дайте описание основных свойств. 6. Найти сталь для изготовления втулок, осей, стержней, работающих при Т < 500°С, подвергающихся действию агрессивных сред (морской воды, щелочных растворов), к которым предъявляют требования повышенной износостойкости и прочности. 7. Подобрать материал для изготовления подшипников ответственного назначения, работающих при повышенных ударных нагрузках. Твердость сердцевины 40-45 НRС. Определите режим термической обработки и структуру. 8. Определите марку стали и ее термическую обработку для изготовления роликовых подшипников при условии, что твердость более 58 НRС. Сталь должна быть износостойкой с достаточной контактной прочностью, прокаливаемость – сквозная. Размеры роликов – диаметр 20 мм, толщина стенки 20 мм. 9. Дайте характеристику рессорной стали для независимой подвески в автотракторостроении, если известно, что она должна обладать σв = 1175 МПа, σт = 1270 МПа, δ = 6 %, = 25 %, НВ > 241. Укажите марку стали, ее структуру после термообработки и вид термообработки объясните. 10. Найти сталь для изготовления хирургического инструмента, обладающего после термической обработки коррозионной стойкостью в среде органических соединений, твердостью более 58-60 НRС. 11. Для изготовления фасонных резцов, сверл применяют инструментальные стали с твердостью 63-66 НRС. Найти сталь, выбрать режим ее термической обработки, если прочностные свойства, требуемые для эксплуатации должны соответствовать σв =2300-2500 МПа, σт = 1800-2000 МПа, красностойкость 630°. При обработке стали с твердостью более 280-300 НВ резцы из быстрорежущей стали не имеют достаточной стойкости. Найти состав сплава, обладающего более высокими режущими свойствами. Опишите состав этого сплава, возможность его упрочнения. Покажите, какой металл можно использовать для державки резца, как изготовить такой резец. На предприятии имеются в наличие стали Р6М5 и Р9М4К8. Объясните различия в основных свойствах этих сталей и рекомендуйте оптимальное назначение каждой из них. Выбрать марку стали для резания с высокой скоростью. Укажите состав, структуру, вид и режим термической обработки стали, основные свойства стали и сравните их с аналогичными свойствами быстрорежущих сталей. Объясните, почему для обработки сталей применяют другие стали, чем для обработки чугунов. Для изготовления фрез, для обработки деталей из труднообрабатываемых жаропрочных сплавов и сталей с высокой твердостью необходимо выбрать сталь, описать режим ее термической обработки. Указать структуру стали в состоянии поставки, в состоянии эксплуатации, основные требования к таким материалам. Выбрать сталь для изготовления режущего инструмента, работающего в пищевой промышленности в слабоагрессивной среде. Описать оптимальный режим термообработки, свойства стали, если твердость должна быть не менее 50 НRС. 17. Выбрать материал для изготовления сверл диаметром 7 мм длиной 70 мм, работающих со скоростью резания 20 м/мин. Требуется, чтобы теплостойкость сохранялась до 500°С. Твердость сверла 62-66 НRС. Описать режим термообработки с обоснованием температуры, среды, времени выдержки. 18. Для изготовления плоскогубцев, имеющих высокую износостойкость и достаточную коррозионную стойкость в атмосферных условиях необходимо выбрать сталь, обосновать режим ее термической обработки. НRC 59-61, КCV 35-40 Дж/см . Описать структуру до и после термической обработки. 19. Для штампов (вытяжных матриц), работающих при нагреве до 400°С с высокой скоростью вытяжки, имеющих высокую твердость 58-62 НRС, необходимо выбрать материал, обосновать режим его обработки и структуру. 20. Найти сталь для изготовления хирургического инструмента, если сталь имеет НRС > 57, устойчива против коррозии, σв=1150 МПа, σт=90 МПа, δ = 12%, ψ = 30%. 21. Выбрать сталь для изготовления клапанов гидравлических прессов, подвергающихся ударным нагрузкам, работающих в агрессивных средах. Сталь должна иметь σв > 850 МПа, σт > 650 МПа, δ = 15%, ψ = 50%. Назначить режим термической обработки и объяснить ее назначение, а также исходную и конечную структуру стали, выбранной Вами. 22. Найти сталь для коррозионностойких пружин, работающих при температурах до 600°С, если сталь должна иметь σв = 1100 МПа, σт = 850 МПа, δ = 12%, ψ= 35% и высокий предел упругости. Описать легирующие элементы, введенные в сталь для повышения предела упругости и указать необходимый режим термической обработки. 23. Определить марку стали для изготовления кухонной посуды. Объяснить возможность ее легирования, режим термической обработки. Назвать необходимые требования к сталям для изготовления посуды. 24. Выбрать сталь для изготовления коррозионностойких уплотнительных втулок, работающих в малоагрессивных средах. Сталь должна иметь: σв = 850 МПа, σт > 650 МПа, δ = 10%, КСV = 60 Дж/см . Определить марку стали, режим ее термической обработки и структуру стали в состоянии эксплуатации. 25. Для изготовления лопаток паровых турбин применяют хромистые стали типа 40Х13 и 30Х13, но они быстро выходят из строя. Объясните причины этого и найдите материал для замены хромистых сталей для увеличения срока службы лопаток. 26. Определите марку стали, режим ее термической обработки для изготовления карбюраторных игл, если известно, что сталь должна иметь твердость НRС > 60, σв = 1150 МПа, σт = 950 МПа, δ = 12%. 27. Для изготовления поршневых колец необходимо применять стали, обладающие высокой твердостью, коррозионной стойкостью и сохраняющая эти свойства до сравнительно высоких температур. Найдите возможные марки стали, определите режим их термообработки для получения необходимых свойств. 28. Найти сталь для изготовления клапанов автомобильных моторов, если известно, что рабочие температуры могут достигать 800°С. Определить режим термообработки и структуру стали до и после термообработки. 29. Найти сталь для изготовления руля и судовых валов, если известно, что σв = 850 МПа, σт = 750 МПа, δ = 12%, ψ = 40% (условия работы: возможно действие морской воды). Дать характеристику структуры стали, режим термической обработки для получения свойств. 30. Найти сталь для изготовления лопаток паровых турбин, работающих при температурах до 500-550 °С. Определите химический состав стали, влияние элементов на механические и технологические свойства стали. Дайте основные характеристики свойств при комнатной температуре и при температурах выше 500 °С. Обоснуйте режим термообработки. 31. Определите марку стали для изготовления медицинских инструментов с твердостью 55 НRС, дайте обоснование режима и вида термической обработки, структуры стали и условий эксплуатации. 32. Дайте примерную марку стали для изготовления крыльевых устройств самолетов с прочностными характеристиками: σв = 1200 МПа, σт = 850 МПа, δ = 12%, ψ = 50%, КСV = 60 Дж/см . Описать структуру и режим термообработки для получения этих свойств. 33. Выбрать сталь для изготовления дисков турбин, работающих при температурах 670-700 °С. Выбрать и обосновать режим термической обработки стали. Технические требования: σв = 790 МПа, σт = 390 МПа, δ = 37%, ψ = 47%. 34. Подобрать материал для изготовления емкостей для хранения компонентов ракетного топлива (сжиженный гелий, водород). Технические требования: σв = 270 МПа, σт = 510 МПа, ψ = 45%. Подобрать режим термической обработки. Описать структуру стали до и после термообработки. 35. Подобрать материал для изготовления валов морских судов, если необходимо, чтобы они обладали σв = 1200 МПа, σт = 900 МПа, δ = 10 %, ψ = 45%. 36. Найти сталь для изготовления мембран, работающих в атмосферных условиях, уксуснокислых и других солевых средах при температурах до 700-850 °С. Необходимые свойства: σв = 1200 МПа, σт = 900 МПа, δ = 20%, ψ = 45%. Выбрать и обосновать структурный класс стали, режим термообработки. 37. Найти сталь для изготовления деталей выхлопных систем, работающих при 600-650°С в среде газов длительное время. Определите структуру, режим термообработки. Укажите основные особенности и недостатки стали. 38. Многие детали паровых турбин(диски, лопатки) работают при температурах 600-650°С в условиях воздействия пара и влаги. Сталь должна обладать устойчивостью против коррозии и ползучести в данном интервале температур. Выбрать марку стали и режим термообработки. Описать структуру готового изделия. 39. Выбрать сталь, хорошо сваривающую, работающую в разбавленных кислотах и солях под давлением при температурах -196 до 650°С для изготовления трубопровода в химической промышленности. 40. Выбрать сталь для изготовления клапанов паровых турбин, длительное время работающих при температурах 600-500 °С, обладающих жаропрочностью до 750 °С, если необходимые требования к клапанам: σв = 850 МПа, σт = 650 МПа, δ = 10%, КСV = 60 Дж/см . Выбрать и обосновать режим термообработки, описать структуру стали. 41. Выбрать сталь для изготовления крыльевых устройств самолетов с прочностными характеристиками σв = 1200 МПа, σт = 850 МПа, δ = 12%, ψ = 50%, КСV = 60 Дж/см . Найти и обосновать режим термообработки и структурный класс стали. 42. Найти сталь для изготовления клапанов гидравлических прессов, подвергающихся ударным нагрузкам и работающим в агрессивных средах, если сталь должна удовлетворять следующим требованиям: σв = 850 МПа, σт = 650 МПа, δ = 15%, ψ = 60%. Обосновать режим термообработки и описать структуру стали. 43. 44. Сравните стали 30Х13 и 40Х13 после термообработки (Закалка + Н.О. 200-300 °С). Их минимальную твердость НRС 50 и 52, соответственно. Объясните почему. 45. Выбрать сталь для изготовления скальпелей, если известно, что σв = 160 МПа, σт = 130 МПа, НRС > 45-50, δ = 10%, НВ 350-340. Обосновать вид и режим термообработки для получения необходимых свойств. Описать влияние легирующих элементов на свойства стали. 46. Найти сталь, обладающую стойкостью против действия ряда химических сред (органических кислот) и стойкой против межкристаллитной коррозии после сварки. Дать режим термообработки с обоснованием температурно-скоростного параметра. Объясните причины возникновения МКК.
Доверь свою работу ✍️ кандидату наук! Имя Поможем с курсовой, контрольной, дипломной, рефератом, отчетом по практике, научно-исследовательской и любой другой работой Выберите тип работыЧасть дипломаДипломная работаКурсовая работаКонтрольная работаРешение задачРефератНаучно – исследовательская работаОтчет по практикеОтветы на билетыТест/экзамен onlineМонографияЭссеДокладКомпьютерный набор текстаКомпьютерный чертежРецензияПереводРепетиторБизнес-планКонспектыПроверка качестваЭкзамен на сайтеАспирантский рефератМагистерская работаНаучная статьяНаучный трудТехническая редакция текстаЧертеж от рукиДиаграммы, таблицыПрезентация к защитеТезисный планРечь к дипломуДоработка заказа клиентаОтзыв на дипломПубликация статьи в ВАКПубликация статьи в ScopusДипломная работа MBAПовышение оригинальностиКопирайтингДругое Нажимая кнопку “Продолжить”, я принимаю политику конфиденциальности |
Жаропрочные стали и сплавы – Металловедение легированных сталей и сплавов и их эксплуатационные свойства
5.7 Жаропрочные стали и сплавы
Жаропрочностью называется способность сталей и сплавов сопротивляться деформированию и разрушению при повышенных температурах в течении определенного времени . При температуре до 600С обычно применяют термин теплоустойчивость. Стали и сплавы, предназначены для работы при повышенных и высоких температурах должны обладать не только жаропрочностью, но и жаростойкостью.
Стали и сплавы, предназначены для работы при повышенных и высоких температурах, подразделяют на группы:
1) теплоустойчивые стали , работающие в нагруженном состоянии при температурах до 600С в течении длительного времени;
2) жаропрочные стали и сплавы, работающие в нагруженном состоянии при высоких температурах в течении определенного времени и обладающие при этом достаточной жаростойкостью.
В группу теплоустойчивых сталей входят углеродистые, низко- легированные и хромистые стали. Структура их зависит от степени легирования и режима термической обработки стали. После нормализации в структуре стали образуется феррит или ферритокарбидная смесь разной дисперсности( перлит, трости, бейнит).
К жаропрочным относятся стали аустенитного класса на хромо-никелевой и хромоникельмарганцевой основах с различным дополнительным легированием. Условно эти стали подразделяют на три подгруппы :
– гомогенные (однофазные) аустенитные стали, жаропрочность которых обеспечивается в основном легированностью твердого раствора;
– стали с карбидным упрочнением;
– стали с интерметаллидным упрочнением. Такое разделение сделано по преимущественному типу упрочнения.
Жаропрочные сплавы разделены по металлу основы: сплавы на основе никеля и кобальта. Эти сплавы чаще всего подразделяют и по способу производства: на деформируемые и литые.
Основные характеристики, определяющие служебные свойства теплоустойчивых и жаропрочных материалов: предел ползучести и предел длитель ной прочности.
Ползучесть – непрерывная деформация металлов под действием постоянно приложенных напряжений.
Сопротивление ползучести характеризуется пределом ползучести – напряжением, которое вызывает данную скорость ползучести или заданную суммарную деформацию ползучести за определённое время при заданной температуре. Например, = 150 МПа – означает напряжение, вызывающее в металле скорость ползучести 1× 10-3 %/ч при 700 °С; = 150 МПа – означает суммарную деформацию ползучести 1 % за 1000 часов при 700 °С.
Пределом длительной прочности называют напряжение, которое приводит к разрушению образца при заданной температуре за определённое время, соответствующее условиям эксплуатации изделия. Предел длительной прочности обозначается как напряжение , где индексы t и τ обозначают температуру в градусах Цельсия (°С) и время испытания в часах до разрушения. Например, = 250°С.
Легирование жаропрочных сталей и сплавов
Состав жаропрочных сталей и сплавов должен обеспечить высокое сопротивление ползучести и газовой коррозии в течение заданного срока службы. При выборе основы для создания жаропрочных сплавов в первую очередь учитывают величину сил межатомной связи. Чем больше силы межатомной связи у металла, тем большей жаропрочностью должны обладать сплавы на его основе. В качестве основы служат Fe, Ni, Co, имеющие высокие температуры плавления и другие характеристики сил межатомной связи.
Существующие жаропрочные стали и сплавы представляют собой многокомпонентные твёрдые растворы на основе Fe, Ni, или Co, которые упрочняются дисперсными выделениями избыточных фаз – карбидов, карбонитридов, боридов, интерметаллидов.
Рассмотрим принципы легирования жаропрочных сталей и сплавов. При ползучести деформация осуществляется как сдвиговым путём, т. е. перемещением дислокаций, так и диффузионным путём в основном, перемещением вакансий. Чем выше рабочая температура. тем сильнее проявляется второй механизм, контролируемый диффузией вакансий к границам зёрен и образованием и ростом пор на границах. При рабочей температуре выше 600 °С этот механизм играет основную роль. Поэтому, чтобы повысить характеристики жаропрочности, нужно уменьшить концентрацию и подвижность вакансий. Диффузионная подвижность вакансий определяется энергией межатомного взаимодействия: чем она выше, тем в меньшей степени идут диффузионные процессы. Легирующие элементы, упрочняющие твёрдый раствор, повышающие силы связи в решётке, затрудняют диффузионные перемещения, уменьшают концентрацию и подвижность вакансий и тем самым повышают жаропрочность. Таким образом, надо ориентироваться на металлы и твёрдые растворы этих металлов, обладающих высокой энергией межатомного взаимодействия. Такие металлы, как Cr, Mo, W, Nb, Ta наиболее сильно упрочняют твёрдый раствор, поэтому жаропрочные материалы легируют этими элементами.
Аустенитные стали с ГЦК решёткой имеют значительно большую жаропрочность, чем стали с ОЦК решёткой. Это связано с тем, что ГЦК решётка более плотно упакована, поэтому коэффициент самодиффузии в γ-Fe на два порядка меньше, чем в α-Fe.
Проведенные испытания показали, что сопротивление ползучести при 850 °С аустенитных сплавов значительно выше, чем ферритных, причём аустенитные сплавы даже при 850 °С более жаропрочны, чем ферритные при 650 °С. Максимальной жаропрочностью должны обладать γ – твёрдые растворы, имеющие предельную легированность. Переход к двухфазным α + γ – структурам приводи к резкому снижению жаропрочности.
Чем выше температура рекристаллизации, тем выше жаропрочность, а температура рекристаллизации зависит от температуры плавления, поэтому нужно легировать элементами с высокой температурой плавления (Mo, W, Nb, Ta).
Одним из главнейших факторов жаропрочности сталей и сплавов является образование упрочняющих фаз. Для повышения жаропрочности нужно легировать элементами, которые создают очень устойчивые к коагуляции и растворению упрочняющие фазы. Чем выше устойчивость этих фаз, тем до более высокой температуры сохраняется их упрочняющее действие. При температуре 600-700 °С такими фазами являются карбиды сильных карбидообразующих элементов (V, Nb, Ti). При более высоких рабочих температурах это интерметаллиды и прежде всего геометрически плотноупакованные γ‘ – фазы типа Ni3Al, Ni3(Al,Ti,Nb), а также фазы Лавеса Fe2Mo, Fe2W, Co2Ti,; h – фазы типа Ni3Al, m – фазы типа Fe7(Mo,W)6. Введение в сталь сильных карбидообразующих элементов (V, Nb, Ti) связывает практически весь углерод и азот в дисперсные, устойчивые к коагуляции карбиды, которые упрочняют твёрдый раствор, и вместе с тем это позволяет молибдену и вольфраму оставаться в твёрдом растворе, значительно упрочняя его и повышая температуру рекристаллизации.
При температуре более 600 °С деформация при ползучести происходит путём межзёренного скольжения, при этом зерна перемещаются друг относительно друга вдоль общих границ в узкой приграничной области. Для повышения жаропрочности требуется упрочнение границ.
Легкоплавкие примеси (Pb, Cd, Bi, Si и др.), обладающие очень малой растворимостью в жаропрочных сплавах, оказывают резко отрицательное влияние на их жаропрочность, даже при небольшом содержании этих элементов. Эти примеси концентрируются по границам зерен, образуют легкоплавкие соединения или эвтектики и способствуют межзёренному разрушению при ползучести. Введение в сплавы малых количеств щелочноземельных (Mg, Ca, Ba) и редкоземельных элементов (La, Ce), а также циркония и бора оказывает положительное влияние на их жаропрочность по следующим основным причинам: эти элементы очень незначительно растворяются в сплавах (поэтому их вводят в очень малых количествах – тысячные и сотые доли атомных процентов) и концентрируются в приграничных объёмах, замедляя приграничную диффузию; они имеют большое химическое сродство к кислороду, сере, азоту, водороду и образуют тугоплавкие оксиды и сульфиды. Эти элементы способны образовывать тугоплавкие химические соединения с примесями легкоплавких цветных металлов и частично нейтрализовать их отрицательное влияние.
В порядке уменьшения эффективности влияния на жаропрочность никелевых сплавов эти добавки можно расположить следующим образом: D, La, Ce, Ba. Содержание добавки свыше оптимального уменьшает не только жаропрочность, но и технологическую пластичность сплавов.
Чем крупнее зерна, тем меньше протяженность межзёренных границ и слабее межзеренное скольжение и диффузионный перенос вакансий вдоль границ. Поэтому при рабочих температурах выше 600 С требуется создание в материалах крупнозернистой структуры.
Таким образом, состав и обработка жаропрочных сплавов должны обеспечить высокий уровень сил межатомной связи; тонкую субмикроскопическую неоднородность строения сплавов; условия для выделения оптимального количества упрочняющих фаз в наиболее эффективных для упрочнения форме и состоянии; препятствия для развития межзеренной деформации и диффузии, особенно при высокотемпературной ползучести; стабильность структуры сплавов в течение заданного срока эксплуатации; нейтрализацию вредных примесей и посредством создания тугоплавких соединений и рафинирования сплавов.
Теплостойкие стали
К теплостойким (теплоустойчивым) сталям относятся стали. используемые в энергетическом машиностроении для изготовления котлов, паронагревателей, паропроводов, лопаток турбин, роторов, дисков, крепёжных деталей и др. Эти же стали применяют в химическом и нефтяном машиностроении для работы при повышенных температурах. Рабочие температуры теплостойких сталей достигают 600-650 °С, а давление газовых или жидких сред 20¸30 Мпа. Так, рабочие температуры в паросиловых установках составляют 585 °С при давлении 25,5 Мпа, а в наиболее мощных установках достигают 650 °С при 31,5 Мпа. Детали таких установок должны работать длительное время без замены (100000 ¸ 200000 ч), поэтому заданное значение длительной прочности и сопротивление ползучести за весь ресурс эксплуатации.
Теплостойкие стали разделяют на низколегированные и среднелегированные перлитного и мартенситного класса, на которые распространяется ГОСТ 20072 – 74, и высоколегированные хромистые стали, состав которых регламентируется ГОСТ 5632 – 72.
Перлитные стали предназначены для длительной эксплуатации при температурах до 600 °С и применяются, в основном, в котлостроении.
Необходимая теплостойкость перлитных сталей достигается комплексным легированием карбидообразующими элементами (Cr, Mo, V, Nb). Содержание каждого из этих элементов не превышает 1 %, за исключением хрома, содержание которого для повышения жаропрочности доводят до 2,5¸3,0 %. Это низкоуглеродистые стали с содержанием углерода 0,08¸0,2 % (иногда до 0,25¸0,3 %). Низкое содержание углерода обеспечивает хорошую свариваемость, и образование карбидов типа МеС, а не Ме23С6 и Ме2С, выделение которых обеднило бы твёрдый раствор хромом и молибденом.
К сталям перлитного класса относятся 12ХМ, 12Х1МФ, 25Х2МФ, 12Х2МФСР и др.
Наиболее широкое применение при температурах 550-600 °С нашла сталь 12Х1МФ, которая применяется на всех мощных электростанциях для изготовления пароперегревателей, коллекторов, паропроводов и т. п. Наиболее часто для этих сталей окончательной термической обработкой является нормализация и последующий высокий отпуск. Так, для стали 12ХМ – нормализация (910-930 °С) и высокий отпуск (670-690 °С) с охлаждением на воздухе; для стали 12Х1МФ – нормализация (960-980 °С) и высокий отпуск (700-750 °С) с охлаждением на воздухе; для стали 25Х2МФ – нормализация (1030-1050 °С) и высокий отпуск (650 -720 °С).
Хромистые стали мартенситного и мартенситно-ферритного класса применяются для различных деталей энергетического машиностроения, работающих при температурах 450-600 °С и отличающихся от перлитных сталей повышенной жаростойкостью в атмосфере пара или топочных газов. Хром, который повышает жаропрочность и жаростойкость, присутствует во всех сталях в количестве 5¸13 %.
Различают две группы мартенситных сталей: с содержанием 10¸12 %Cr, добавками Mo, V, W, Nb и низким, в пределах 0,10¸015 %, содержанием углерода и сильхромы с содержанием 5¸10 %Cr, добавками кремния в количестве до 2,0¸3,0 % и повышенным содержанием углерода, до 0,4 %.
К первой группе относятся стали типа 45Х11МФБ, 18Х11МФБ, 13Х11Н2В2МФ, 13Х14Н3В2ФР и др. Оптимальный режим термической обработки сталей этой группы заключается в закалке или нормализации от 980-1100 °С (для растворения карбидов) с дальнейшим высоким отпуском при 600-740 °С. Структура термически обработанных сталей – смесь легированного феррита и мелких карбидов обеспечивает необходимую жаропрочность и сопротивление коррозии. Благодаря высокому содержанию легирующих элементов, стали глубоко прокаливаются даже при нормализации (до 120¸200 мм). При длительной работе они надёжно работают до 600 °С. Из них изготавливают диски, лопатки, бандажи, роторы паровых турбин, а также трубы пароперегревателей и детали крепления.
При высоком содержании хрома (10¸12 %) и других ферритообразующих элементов и низком содержании углерода стали становятся феррито-мартенситными (15Х12ВНМФ, 18Х12ВМБФР и др.). Количество феррита в этих сталях невелико (не более 10¸15 % d – феррита), поэтому по характеристикам жаропрочности они близки к мартенситным. Упрочнение этих сталей обеспечивается созданием мартенсито-ферритной основы и выделением различных карбидов (типа Ме23С6 и МеС) и фаз Лавеса Fe2(W,Mo). Используется в термически упрочненном состоянии после закалки (нормализации) и старения (высокого отпуска).
Сильхромы (40Х9СА, 40Х10С2М и др.) повышенной жаростойкостью в среде горячих выхлопных газов и используются для изготовления клапанов двигателей внутреннего сгорания. Оптимальные свойства сильхромы имеют после закалки с 1030-1050 °С и дальнейшего отпуска при 720-780 °С на структуру сорбит. В сталях без молибдена охлаждение после отпуска быстрое во избежание отпускной хрупкости. Чем больше содержание хрома и кремния, тем выше рабочая температура. При длительной эксплуатации сильхромы могут применяться до 600-650 °С.
Жаропрочные стали аустенитного класса
Эти стали по жаропрочности превосходят перлитные и мартенситные стали и используются при температурах выше 600С. В интервале температур от 600 до 750С используют аустенитные стали трех групп:
1) гомогенные стали;
2) стали с карбидным или карбонитридным упрочнением;
3) стали с интерметаллидным упрочнением.
Гомогенные стали
К этой группе относятся главным образом низкоуглеродистые хромоникелевые стали, дополнительно легированные элементами, упрочняющими γ – твердый раствор (10Х18Н12Т, 08Х15Н24В4ТР, 10Х14Н16МВБ, 10Х14Н18В2БРЧ). Их жаропрочность обеспечивается в основном растворенными в твердом растворе легирующими элементами. Термин « гомогенные стали » следует понимать условно, так как в структуре этих сталей обычно присутствует количество карбидов и карбонитридов титана или ниобия. Гомогенные аустенитные стали используются преимущественно в энергомашиностроении для изготовления труб паронагревателей и паропроводов, арматуры установок сверхвысоких параметров и рассчитаны на длительную службу при 650-700С. При легировании этих сталей стремятся получить максимально стабильную аустенитную структуру, избежать или замедлить выделение вторых фаз( карбиды, карбонитриды, фаз Лавеса), что позволяет иметь необходимый уровень длительной прочности и пластичности в течение всего ресурса эксплуатации. Важно для этих сталей обеспечить также высокое технологические свойства, такие как способность к горячей пластической деформации, прошиваемость при изготовлении цельнотянутых труб, свариваемость и др. Эти цели достигаются легированием стали содержат 13-15 %Cr , обеспечивающего жаропрочность и жаростойкость . Чтобы получить стабильную аустенитную структуру добавляют аустенито-образующие элементы Ni, Mn , иногда N.
В основе сталей лежат композиции Cr-Ni, Cr-Mn, Cr-Ni-Mn. В Cr-Ni композициях для получения стабильной аустенитной структуры отношение Ni/Cr должно быть больше 1. Углерода мало (0,06¸0,12 %). чтобы не образовывались карбидные фазы типа Ме23С6, которые выводят Cr из твёрдого раствора, что снижает жаропрочность и жаростойкость, а также, чтобы обеспечить хорошую свариваемость и пластичность. в состав сталей вводят сильные карбидообразующие элементы Ti, Nb, V, образующие карбиды МеС и карбонитриды Me(C,N), которые препятствуют образованию карбидных фаз типа Ме23С6 и обеднению хромом твёрдого раствора. Это обеспечивается соотношением Ti, Nb/С > 10. Повышенная жаропрочность таких сталей объясняется высокой легированностью твёрдого раствора такими элементами, как W (2¸5 %) и Мо (до 2,5 %). Наличие стабильных карбонитридных фаз и высоколегированного аустенита обуславливает высокие температуры рекристаллизации сталей этого типа.
Многими исследователями также отмечается положительное влияние бора и редкоземельных металлов на жаропрочность сталей этого типа. Бор, церий и другие редкоземельные элементы являются сильными раскислителями, поэтому в их присутствии уменьшается содержание газов и неметаллических включений в сталях, что повышает их качество. Влияние малых добавок РЗМ и бора на сопротивление ползучести также связывают с их горофильностью, т.е. способностью адсорбироваться по границам зерен, что затрудняет зернограничную диффузию и упрочняет границы. Кроме того, бор образует в сталях сложные бориды типа Ме23В2 и Ме2В, которые обладают высокими температурами плавления. Зависимость длительной прочности от содержания бора имеет экстремальный характер. Это связано с тем, что при высоком содержании бора ( > 0,3 %) в большом количестве образуются крупные бориды, которые обедняют твердый раствор ниобием, вольфрамом, хромом и другими элементами. Кроме того, бор обладает увеличенной склонностью к ликвации и образованию строчечной структуры, а что отрицательно сказывается на их пластических и жаропрочных свойствах.
Таким образом, микролегирование аустенитных сталей бором и РЗМ оказывает положительное влияние на жаропрочность и пластичность как вследствие рафинирующего действия при выплавке, так и упрочнения границ зерен благодаря их горофильности.
Термическая обработка аустенитных гомогенных сталей состоит из закалки (аустенизации) от высоких температур (1050¸1200 °С) или аустенизации и стабилизирующего отпуска (700¸750 °С) и преследует цель получить более однородный γ – твёрдый раствор, заданную величину зерна (балл 3¸6) и стабильную структуру, а также напряжения, которые могут возникнут в процессе изготовления деталей. Следует отметить, что улучшение служебных характеристик и удешевление сталей этого типа обычно связывают со следующими направлениями исследований: оптимизация состава сталей, в частности, частичная замена никеля марганцем и азотом, использование сталей в наклёпанном состоянии (холодная деформация или термомеханическая обработка),особенно при рабочих температурах более низких, чем температура рекристаллизации; более широкое использование легирования сталей бором, р.з.м.; усовершенствование технологии выплавки, обработки давлением и режима термической обработки.
Применяются аустенитные гомогенные стали в энергомашиностроении дл изготовления труб паронагревателей и паропроводов, длительное время работающих при 600¸700 °С, а также крепёжных деталей.
Стали с карбидным и карбонитридным упрочнением
Стали с карбидным упрочнением предназначены для работы при температурах 650¸750 °С и, довольно, высоких уровнях напряжений (37Х12Н8Г8, 37Х12Н8Г8МФБ). Их используют для изготовления деталей энергомашиностроения (диски и лопатки турбин, крепёжные детали и др. ).
Основу сталей с карбидным упрочнением составляют Cr-Ni, Cr-Ni-Mn – аустенит, содержащий 0,25¸0,5 % углерода.
Никель частично может быть заменен менее дефицитным марганцем.
Карбидообразующие элементы Nb, V, W, Мо связывают часть углерода в специальные карбиды, а также упрочняют матрицу.
Упрочняющими карбидными фазами в аустенитных сталях в основном являются карбиды ванадия и ниобия (VC, NbC), а также карбиды хрома. Последние обычно растворяют в себе другие элементы, поэтому состав этих карбидов изменяется в зависимости от легирования стали и режима термической обработки.
Карбиды ванадия выделяются при старении в высокодисперсном состоянии и обеспечивают значительную долю упрочнения этих сталей.
Специальные карбиды типа МеС в процессах старения практически не участвуют, так как имеют высокие температуры растворения при аустенитизации, карбиды и карбонитриды ниобия начинают растворяться только после нагрева выше 1250 °С, а в основном присутствуют в сталях в виде первичных выделений. Положительная роль этих фаз заключается в том, что они препятствуют росту аустенитного зерна при нагреве, и, в частности, образованию разнозернистости.
Термическая обработка включает закалку с температур 1150¸1200 °С и старение при температурах 780¸1200 °С.
Стали с интерметаллидным упрочнением
Жаропрочные хромоникелевые стали с интерметаллидным упрочнением, а также сплавы на хромоникелевой основе с высоким содержанием никеля (до 38 %) нашли применение при изготовлении компрессоров. турбин , дисков, сварных изделий, шпилек, болтов и других деталей, работающих при температурах до 750¸850 °С. Легирование сталей этого типа преследует цель создания высоколегированного железоникелевого аустенита, обладающего склонностью к распаду при старении, и образования фаз-упрочнителей – интерметаллидных фаз типа γ‘ (Fe,Ni)3(Al,Ti,Nb) и фаз Лавеса Fe2Mo, Fe2W, Fe2(Mo,W)/
Стали с интерметаллидным упрочнением содержат 12¸15 %Cr, менее 0,1 %С, до 3,5 % Мо и W, повышенное количество Al, Ti, Nb для образования интерметаллидных фаз. Примерами таких сталей могут быть Х14Н35ВТЮ, 08Х14Н35ВТЮРЧ и др.
Эти стали подвергают закалке с высоких температур (1100¸1180 °С) и старению при 750¸800 °С в течение 15¸25 ч с охлаждением на воздухе.
Жаропрочные сплавы на основе никеля , кобальта,
тугоплавких металлов
Сплавы на никелевой основе применяют в качестве жаропрочных материалов, предназначенных для работы при температурах от 700 до 1100 °С. Их используют в газовых турбинах двигателей самолетов, кораблей, энергетических установок, при изготовлении деталей ракетно-космической техники, в нефтехимическом оборудовании. Так,, в авиационном газотурбинном двигателе более 70 % массы составляют жаропрочные сплавы на никелевой и железоникелевой основах – это диски, сопловые и рабочие лопатки турбин, камеры сгорания и т.п. Резко возросло применение этих сплавов и при изготовлении стационарных газовых турбин, так как повышение рабочих температур позволяет значительно улучшить их технико-экономические показатели.
Несмотря на сложность составов, можно сформулировать следующие основные принципы жаропрочных никелевых сплавов:
1. Жаропрочные сплавы представляют собой γ – твёрдый раствор на хромо-никелевой основе, легированный кобальтом и тугоплавкими элементами-упрочнителями (Nb, W, Мо ).
2. В сплавах обязательно присутствуют титан, ниобий и алюминий (суммарно до 8¸10 %), которые в основном обеспечивают образование главной упрочняющей фазы этих сплавов γ’ – фазы.
3. Присутствующие в сплавах хром и алюминий обеспечивают сопротивление окислению и газовой коррозии вследствие образования защитных пленок, богатых оксидами Сr2О3 и А12Оз.
4. Углерод содержится в сплавах в небольших количествах (обычно 0,08¸0,12 %), образуя карбиды и карбонитриды.. Существенное влияние оказывает также бор, который вводится в сплавы в количествах 0,005¸0,015 % и образует бориды типа МеВ2. Кинетика выделения и морфология карбидных и боридных фаз при кристаллизации, термообработке и в процессе эксплуатации также в значительной степени определяет жаропрочность сплавов на никелевой основе.
5. Важное значение имеют в никелевых сплавах легкоплавкие примеси (Pb, Cd, Ag, Sb, S), содержание которых следует ограничивать, так как они снижают их жаропрочные и технологические свойства. Уменьшение количества примесей возможно благодаря применению чистых шихтовых материалов, введению р.з.м. и обработке расплавов специальными шлаками, применением различных методов специальной металлургии (ЭШП, ЭЛЛ, ВДУ и др.).
Таким образом, жаропрочность, жаростойкость и другие характеристики сплавов на никелевой основе связаны с оптимизацией их состава по соотношению легирующих элементов, входящих в матричный γ – твердый раствор и упрочняющие интерметаллидные, карбидные и боридные фазы, а также с уровнем содержания вредных легкоплавких примесей.
Выбор состава сплава следует проводить с учетом его рабочей температуры, напряжений, агрессивности среды, ресурса и режима работы.
В сплавы, предназначенные для работы при сравнительно невысоких температурах (750¸850 °С) длительное время, вводят повышенное количество хрома (до 16¸18 %), молибдена и вольфрама (до 10¸12 % суммарно), титана, ниобия и алюминия (8¸10 % суммарно). Это дает возможность получить большое количество упрочняющей γ’- фазы, высокую легированность и жаропрочность матрицы.
Для высокотемпературной (975¸1050 °С) работы важно положение температуры солидуса сплава. Поэтому в сплавах ограничивают содержание хрома (6¸10 %), молибдена (3¸4 %) и титана. Введение дополнительно кобальта и вольфрама несколько повышает температуру солидуса, что полезно.
Применяемые никелевые сплавы подразделяют на деформируемые и литейные.
Термическая обработка Сплавов на никелевой основе заключается в закалке (иногда двойной закалке от разных температур) и старении, которые проводят в одну или две стадии: низко- и высокотемпературные.
Цель такой сложной термической обработки – обеспечить наиболее оптимальное сочетание количества и морфологии упрочняющих фаз в сплавах и, следовательно, благоприятное сочетание характеристик жаропрочности и пластичности.
Для деформируемых сплавов первую закалку проводят с целью гомогенизации структуры, растворения γ ‘- фазы и карбидных фаз. Чем легированнее сплав, чем больше в сплаве упрочняющей γ ‘-фазы, тем выше температура закалки. Так, сплавы ХН77ТЮР (ЭИ437Б), нимоник 80 (в которых содержится около 10 % γ ‘ – фазы) закаливают от 1080 °С, а сплавы ХН55ВМТКЮ (ЭИ929), нимоник 110, 115 (35¸45 % γ ‘ – фазы) – от 1200 °С. После такой обработки сплав состоит в основном из γ – матрицы, первичных карбидов МеС и в сложнолегированных сплавах небольшого количества γ ‘ – фазы, которая образуется в процессе охлаждения на воздухе.
В лекции “8 Обязательное право” также много полезной информации.
Вторую закалку проводят от 1040¸1100 °С. В результате происходит повторное растворение γ ‘ – фазы и ее выделение при охлаждении в более дисперсном виде, но главная цель этой обработки – образование выделений карбидных фаз благоприятных типов и морфологии, в частности стремление избежать образования сплошной пленки карбидов типа Ме23С6 по границам зерен и добиться образования зернистых карбидов типа МеС и Ме7Сз.
Старение при повышенных температурах (обычно выше рабочих температур) проводят для выделения γ ‘ – фазы и стабилизации структуры сплава, а окончательное низкотемпературное старение для дополнительного выделения γ ‘ – фазы в мелкодисперсном виде.
Литейные сплавы также можно подвергать высокотемпературной закалке, которая гомогенизирует их структуру и способствует более равномерному выделению упрочняющих фаз. Старение этих сплавов чаще проводят в одну высокотемпературную стадию, так как литейные сплавы обычно работают при более высоких температурах. Иногда эти сплавы используют непосредственно в литом состоянии, причем старение происходит в процессе эксплуатации.
Жаропрочные сплавы на основе кобальта имеют более низкие характеристики жаропрочности по сравнению со сплавами на основе никеля, но имеют более высокую жаростойкость – сопротивление газовой коррозии , особенно в продуктах сгорания топлива, содержащего серу. Поэтому из них изготовляют сопловые и рабочие лопатки мощных газовых турбин.
Структура сплавов: аустенитная γ ‘ – матрица с г.ц.к. структурой, упрочняющие фазы – карбиды, карбонитриды, бориды., фазы Лавеса. Содержание никеля в кобальтовых сплавах 10¸30 %. Он стабилизирует аустенитную структуру. Хром обеспечивает высокую жаропрочность и жаростойкость; его содержание, обычно, 18¸20 %. Кроме того. в сплавы вводят до 10 % W или Мо и W (суммарно), а также Nb, Ti, V. Молибден и вольфрам являются одновременно упрочнителями твёрдого раствора и частично входят в карбидные фазы, а Nb, Ti, V, в основном, присутствуют в карбидах. В кобальтовых сплавах, обычно, образуются карбиды МеС, Ме6С, Ме7С3, Ме23С6, Для образования карбидов в этих сплавах содержание углерода повышено и составляет 0,25¸1,0 %.
Сплавы на основе тугоплавких металлов (Ni, Mo, Cr, Ta, W, Re) применяются при рабочих температурах до 2200 °С. Так, сплавы на основе молибдена работоспособны до 1300¸1400 °С; на основе тантала – до 2000 °С, а на основе вольфрама – до 2000¸2200 °С.
Презентация на тему: ЖАРОПРОЧНЫЕ СТАЛИ И СПЛАВЫ
Жаропрочность – способность сталей и сплавов выдерживать механические нагрузки при высоких температурах в течение определенного времени.
Жаростойкость – сопротивление металлов и сплавов газовой коррозии при высоких температурах.
Стали и сплавы, предназначенные для работы при
повышенных и высоких температурах, подразделяют на группы: Теплоустойчивые стали, работающие в нагруженном
состоянии при температурах до 6000С в течение длительного
времени;
Жаропрочные стали и сплавы, работающие в нагруженном состоянии при высоких температурах в течение определенного
времени и обладающие остаточной теплостойкостью;
Жаростойкие (окалиностойкие) стали и сплавы, работающие в ненагруженном или слабонагруженном состоянии при температурах выше 5500С и обладающие стойкостью против химического разрушения поверхности в газовых средах.
2
Теплоустойчивые стали.
Применяются в энергетическом, химическом, нефтяном машиностроении.
Основное требование: заданное значение длительной прочности и сопротивление ползучести за весь ресурс эксплуатации (100000… 200000 ч).
Используют углеродистые, низколегированные и хромистые стали. Структура зависит от степени легирования и режима термической обработки. После нормализации образуется феррит или феррито-
карбидная смесь разной дисперсности (перлит, троостит, бейнит).
Углеродистые и низколегированные стали. Ст2, Ст3, 12К, 16К, 12Х1МФ.
Применяют для работы при температурах до 1200С.
ЛЭ: Cr, W, Mo, V, Nb. Содержание этих элементов не превышает 1%, кроме Cr. Содержание углерода 0,08…0,2%, т.к. при более высоком его содержании ускоряется коагуляция карбидных фаз и перераспределение легирующих элементов между твердым раствором и карбидами.
С повышением температуры эксплуатации состав сталей
усложняется. | 3 |
Термическая обработка проводится с целью получения стабильной структуры, которая не менялась бы в процессе эксплуатации.
Углеродистые стали подвергают нормализации. Низколегированные стали подвергают улучшению (закалка+
высокий отпуск). При этом температура отпуска должна быть выше эксплуатационной температуры на 100…1200С (рисунок слева).
Структура после термообработки представляет собой феррит+карбиды цементитного типа и МеС.
880…9000С |
640…6600С |
4 |
Хромистые стали мартенситного и мартенсито-ферритного классов.
15Х5, 15Х5МФ, 12Х8ВМ1БФР.
Применяют в основном в энергетическом машиностроении для деталей, работающих длительное время при температурах 600… 6500С.
Содержат от 5 до 13% Cr и дополнительно легированы Mo, W, Nb, V. Содержание углерода в них 0,08…0,22%.
В их структуре в зависимости от состава и термообработки могут быть следующие составляющие:
мартенсит, -феррит, карбиды (Ме23С6, Ме7С6, МеС) и интерметаллиды.
5
Термическая обработка этих сталей включает нормализацию при температурах 850…10500С (чем более легирована сталь, тем выше температура) и высокий отпуск.
Прочность и теплоустойчивость этих сталей обеспечивает упрочнением вследствие фазового наклепа при мартенситном превращении и последующем дисперсионном твердении при отпуске.
850… |
10500С |
700…8000С |
6
Жаропрочные стали.
К жаропрочным относят стали аустенитного класса на хромоникелевой и хромоникельмарганцевой основах. Подразделяют на гомогенные (однофазные) аустенитные стали, стали с карбидным упрочнением и
стали с интерметаллидным упрочнением.
Гомогенные стали.
10Х18Н12Т, 08Х15Н24В4ТР. Низкоуглеродистые хромоникелевые стали.
Рассчитаны на длительную (до 100000 ч) эксплуатацию при 650-7000С
Жаропрочность обеспечивается легированностью твердого раствора. Основная цель легирования – получение максимально стабильной аустенитной структуры, исключение или замедление выделения вторых фаз – карбидов, карбонитридов, интерметаллидов. Термическая обработка аустенитных гомогенных сталей проводится для получения более однородного твердого раствора, заданной величины зерна и стабильной структуры. Термообработка состоит из закалки (аустенизации) от высоких температур 1050…12000С или аустенизации и стабилизирующего отпуска (700…7500С).
7
Стали с карбидным упрочнением.
37Х12Н8Г8МФБ (ЭИ481), 40Х15Н7ГФ2МС (ЭП388). Предназначены для работы при температурах 650…7500С и используются для ответственных деталей энергомашиностроение (диски и лопатки турбин, крепежные детали).
Основу этих сталей составляет Cr-Ni или Cr-Ni-Mn аустенит, содержащий 0,25…0,5% С.
Карбидообразующие элементы V, Nb, W, Mo связывают часть углерода в специальные карбиды и упрочняют матрицу. Упрочняющими карбидными фазами являются VC и NbC, а также карбиды хрома типа Ме23С6 и Ме7С3.
Карбиды ванадия выделяются при старении.
Другие карбиды МеС в процессах старения не участвуют, т.к. температура их растворения выше 12500С, а присутствуют в сталях в виде первичных. Они препятствуют росту аустенитного зерна при нагреве.
8
1 – 37Х12Н8Г8,
2 – 37Х12Н8Г8МФБ
Уровень жаропрочности зависит от температуры старения. При низких температурах (500…6000С)
выделение карбидных фаз протекает медленно, образуются высокодисперсные частицы, прочностные свойства при выдержке возрастают. С повышением температуры старения скорость процессов выделения и коагуляции возрастает, достигается максимум упрочнения, положение которого зависит от состава стали. Чем сложнее карбидные фазы, чем легированнее аустенит, тем больше эффект упрочнения при старении.
9
1140… |
12200С |
660… |
8000С |
1180… | 8000С |
12200С | |
| 6600С |
Обычная термообработка состоит из закалки с температур аустенизации 1140…12200С и длительного (16 ч) старения при 660…8000С
После низкотемпературного старения сталь 40Х15Н7ГФ2МС приобретает высокую твердость, высокую чувствительность к надрезу и нестабильность жаропрочных свойств. Поэтому для этой стали применяется двойное старение: 6600С – 16 ч и 8000С – 16 ч. Старение при повышенной температуре способствует снятию напряжений, возникающих при низкотемпературном старении.
10
Жаропрочные стали и сплавы
Практикум
- формат pdf
- размер 818,85 КБ
- добавлен 28 октября 2015 г.
Метод. указания / Д.А. Барчуков, А.В. Беляков. Тверь: ТвГТУ, 2015. 24 с. Предназначены для выполнения лабораторных работ по курсу «Материаловедение» для студентов, обучающихся по направлениям «Теплоэнергетика и теплотехника» и «Электроэнергетика и электротехника». Даны определения жаростойких и жаропрочных сталей и сплавов.Приведена классификация жаростойких и жаропрочных сталей и сплавов с указанием примеров маркировки указанных материалов. Пред…
- формат pdf
- размер 54,38 МБ
- добавлен 20 июля 2012 г.
Пер. с англ. — М.: Металлургиздат, 1961. — 381 с. В книге подробно описаны свойства жаропрочных никелехромовых сплавов типа нимоник при нормальной и повышенных температурах, методы горячей и холодной обработки давлением и термической обработки этих сплавов, а также их сварки, пайки, литья и механической обработки. Кроме того, рассмотрены методы анализа и контроля сплавов нимоник, а также возможности их применения. Книга предназначена для инженеро…
- формат djvu
- размер 22.53 МБ
- добавлен 30 ноября 2008 г.
Издатель: Москва, Машиностроение, 1998. В книге представлены результаты исследований, выполненные авторами с сотрудниками за последние 15 лет в Государственном научном центре “Всероссийский институт авиационных материалов”. Рассмотрены экспериментальные данные по жаропрочности деформируемых и литейных никелевых сплавов. Показана статистическая природа характеристик жаропрочности и изучены закономерности их изменения с температурой и временем. И…
Статья
- формат pdf
- размер 1.45 МБ
- добавлен 08 августа 2011 г.
Статья. Опубликована в “Вестник Московского университета”. – Серия 2. Химия. – 2005. – Т. 46. – № 3. – С. 155-167. Проведен анализ работ по созданию современных жаропрочных никелевых сплавов (ЖНС) для литья монокристаллических лопаток газовых турбин. Рассмотрены особенности легирования, фазовый состав и физико-химические факторы жаропрочности ЖНС, содержащих рений; принципы сбалансированного легирования и методы компьютерного конструирования моно. ..
- формат pdf
- размер 7.38 МБ
- добавлен 23 августа 2011 г.
М. Машиностроение, 1987. —116 с. В книге дан обзор свойств и фазового состава современных отечественных и зарубежных литейных жаропрочных никелевых сплавов. Книга предназначена для научных работников, а также специалистов КБ и заводов, занимающихся разработкой и применением жаропрочных сплавов. Табл. 24. ил. 15, список лит. 164 наз.
Статья
- формат djvu
- размер 237.08 КБ
- добавлен 08 августа 2011 г.
Статья. Опубликована в “Металловедение и термическая обработка металлов”. – № 1. – 1999. – С. 29. В настоящей работе исследовали влияние модифицирования гафнием жаропрочных сплавов на их структуру и свойства. Рассмотрено влияние модифицирования гафнием на размеры и количество хрупкой составляющей в изломе, расстояние между осями дендритов второго порядка, а также морфологию карбидов.
- формат djvu
- размер 1.94 МБ
- добавлен 15 апреля 2009 г.
М.: Металлургия, 1983. – 192 с. Приведены свойства жаропрочных и окалиностойкнх сталей и сплавов, отвечающих общесоюзным стандартам и техническим условиям. Обобщены сведения об указанных материалах, опубликованные в отечественной и зарубежной литературе. Рассмотрены стали всех классов и сплавы на основе железа и никеля. Для инженерно-технических и научных работников, конструкторов металлургической, машиностроительной, судостроительной, авиацио…
Реферат
- формат doc
- размер 15.
35 КБ
- добавлен 25 декабря 2008 г.
Введение, Сплавы обладают высокими механическими свойствами, Направленная кристаллизация сообщает сплавам повышение предела выносливости, длительной прочности и пластичности, Химический состав сплавов, Для получения оптимальной структуры и необходимых свойств диски подвергаются закалке и старению, Заключение.
- формат pdf
- размер 11,49 МБ
- добавлен 28 мая 2015 г.
Пер. с англ. — М.: Металлургия, 1976. — 568 с.: ил. Рассмотрены свойства жаропрочных сплавов на основе никеля, железа, кобальта и хрома. Подробно проанализированы фазовый состав и условия образования вредных сигма, мю и Лавес – фаз, вызывающих снижение механических свойств. Показаны важная роль карбидов, их влияние на долговечность, пластичность и прочность жаропрочных сплавов. Установлена зависимость свойств сплавов от их химического и фазового…
- формат djvu
- размер 18.81 МБ
- добавлен 16 декабря 2011 г.
М.: “Металлургия”, 1976. – 568 с. Рассмотрены свойства жаропрочных сплавов на основе никеля, железа, кобальта и хрома. Подробно проанализированы фазовый состав и условия образования вредных сигма, мю и Лавес – фаз, вызывающих снижение механических свойств. Показаны важная роль карбидов, их влияние на долговечность, пластичность и прочность жаропрочных сплавов. Установлена зависимость свойств сплавов от их химического и фазового составов, микростр…
- формат pdf
- размер 75.9 МБ
- добавлен 11 апреля 2011 г.
Издательство: Металлургия. г. Москва-1969г. Страниц: 752 В книге подробно рассмотрены механические свойства жаропрочных сталей и сплавов при комнатной и высокой температурах, влияние легирующих элементов на структуру и фазовый состав, методы термической, горячей обработки давлением и способы производства сплавов. Рассмотрены жаропрочные сплавы на железной, никелевой и кобальтовой основах, а также ряд тугоплавких металлов (W, Mo, Nb, Та, Re, Сr) и…
- формат pdf
- размер 10,97 МБ
- добавлен 01 марта 2012 г.
М.: Машиностроение, 1997. – 336 с. Рассмотрены физические основы металловедения никелевых жаропрочных сплавов и методы их компьютерного проектирования, теоретические аспекты процесса направленной кристаллизации, конструкции установок, а также способы получения монокристальных лопаток и определения их ориентации. Обобщены результаты исследований структурного совершенства дендритных монокристаллов различных ориентаций. Большое внимание уделено во…
- формат pdf
- размер 6.82 МБ
- добавлен 17 декабря 2011 г.
Published in North America by CRC Press LLC, 6000 Broken Sound Parkway, NW, Suite 300, Boca Raton, FL 33487, USA First published 2008, Woodhead Publishing Limited and CRC Press LLC 678 pages Woodhead Publishing ISBN 978-1-84569-178-3 (book) Woodhead Publishing ISBN 978-1-84569-401-2 (e-book) CRC Press ISBN 978-1-4200-7088-0 CRC Press order number: WP7088 General Introduction The development of creep-resistant steels Specifications for creep-res…
- формат pdf
- размер 131.16 МБ
- добавлен 15 января 2012 г.
ASM International, 1997, ISBN: 0871705966, Pages: 591 ASM Speciality Handbook This latest handbook brings together in one volume a comprehensive reference source of information on engineering metallic and nonmetallic heat-resistant materials from carbon and alloy steels to refractory metals, and ceramics to carbon-carbon composites. The volume covers the complete spectrum of technology dealing with heat-resistant materials including high-tempe…
- формат pdf
- размер 7.81 МБ
- добавлен 20 января 2012 г.
Cambridge University Press, 2006, ISBN: 0521859042, 372 pages Superalloys are unique high-temperature materials used in gas turbine engines, which display excellent resistance to mechanical and chemical degradation. This book presents the underlying metallurgical principles which have guided their development and practical aspects of component design and fabrication from an engineering standpoint. The topics of alloy design, process development…
термостойкие стали-Ispatguru
Теплостойкие стали
- Satyendra
- 25 октября 2013
- 2 Комментарии
- Austenite, Bainite, BCC, Carbides, Carbo-Nitride, Creave, Fartite, Fccc, Fccc, Fccc, Fccc, Fcccc, BCC, Carbides, Carbo-Nitrides, Creave, Farititict, Fcc, Fccccc, BCC, Carbides, Carbo-Nitride, Creave, Fartititict, FCC, FCC, FCC, FCC, FCC, FCC, FCCC, FCC, FCC, FCCC, BC жаропрочная сталь, мартенсит, нитриды, перлит,
Жаропрочные стали
Жаропрочные стали широко используются для изготовления высокотемпературных компонентов и охватывают широкий спектр областей применения. Свойства стали и ее предел текучести значительно ухудшаются, так как сталь поглощает тепло при воздействии высоких температур. Жаростойкость означает, что сталь устойчива к образованию окалины при температурах выше 500 градусов С. Жаропрочные стали предназначены для использования при температурах выше 500 градусов С, поскольку они обладают хорошей прочностью при этой температуре и особенно устойчивы к кратковременным и длительным воздействиям. воздействие горячих газов и продуктов сгорания при температуре выше 500°С. Эти стали являются легированными сталями, упрочненными твердым раствором.
Уровень жаропрочности жаропрочных сталей зависит от условий окружающей среды, в которых они работают, и не может быть охарактеризован единым методом испытаний. Максимальные рабочие температуры, которые могут быть увеличены до 1000°C в зависимости от содержания сплава, могут быть значительно снижены из-за присутствия некоторых соединений, таких как сернистые соединения, водяной пар или зола. Стойкость к жидкому металлу и шлаку у этих сталей также ограничена.
Поскольку жаропрочные стали используются в определенном широком диапазоне температур, эти стали обычно упрочняют с помощью жесткого механизма термической обработки, твердого раствора и осаждения. Все жаропрочные стали состоят из нескольких легирующих элементов с целью достижения желаемых свойств и используются в приложениях, где критически важна устойчивость к повышенным температурам.
Высокотемпературная коррозия является основным фактором, влияющим на срок службы оборудования, используемого для работы в горячем режиме, и скорость коррозии увеличивается с повышением температуры. В общем, увеличение содержания хрома (Cr) делает материалы более устойчивыми к коррозии, а коррозионная стойкость резко возрастает, когда содержание Cr превышает 20 %.
Жаропрочные стали обычно подразделяются на ферритные/мартенситные стали и аустенитные стали. Ферритно-мартенситные стали имеют ту же объемно-центрированную кубическую (ОЦК) кристаллическую структуру, что и железо (Fe). Они содержат просто железо с относительно небольшим добавлением легирующих элементов, таких как основной элемент Cr, добавленный от 2 % до примерно 13 %. Эти ферритные/мартенситные марки также содержат небольшой процент марганца (Mn), молибдена (Mo), кремния (Si), углерода (C) и азота (N2), в основном включенных из-за их преимуществ в дисперсионном упрочнении и стимулировании поведения при высоких температурах. . Обычно используются ферритные марки, поскольку они экономичны из-за низкого содержания легирующих элементов. Они также обладают некоторой устойчивостью к окислению при красном калении, которая прямо пропорциональна содержанию Cr.
Жаропрочные стали широко используются для изготовления высокотемпературных компонентов и охватывают широкий спектр областей применения. Отдельно используются различные виды жаропрочных сталей в зависимости от их конкретного назначения. Жаропрочными сталями обычно являются ферритные стали и аустенитные стали. Ферритные стали включают углеродистые стали, низколегированные стали (0,5 % Mo, 2,25 % Cr-1 % Mo), среднелегированные стали (от 5 % до 10 % Cr) и высоколегированные стали (мартенситные стали с 12 % Cr и 12–18 % Cr). ферритные стали серии AISI 400). Аустенитные стали включают стали с содержанием 18 % Cr–8 % Ni (никеля) и стали с содержанием 25 % Cr–20 % Ni серии AISI 300, стали с содержанием 21 % Cr–32 % Ni, такие как Alloy 800H, и хромомарганцевые стали AISI200. серии. Ферритные стали обычно не содержат Ni, и, поскольку в составе 2 % Cr, 9% и 12 % отличаются особой прочностью, широко используются.
Ферритные/мартенситные стали, используемые для работы при высоких температурах, можно разделить на два типа в зависимости от их микроструктуры и состава. Первый тип – это низколегированные стали, которые содержат от 1 % Cr до 3 % Cr и имеют общее содержание легирующих элементов менее 5 %. Второй тип называется мартенситной сталью 9-12Cr и обычно содержит легирующие элементы в диапазоне от 10 % до 20 %. По мере ужесточения требований к работе при высоких температурах перлитные стали заменяются мартенситными.
В последние годы растет спрос на стали, способные выдерживать более высокое давление и более высокие рабочие температуры. Ведутся разработки новых марок, являющихся модификацией существующей марки 9-12Cr с добавками ванадия (V), ниобия (Nb) и N2. Самые передовые мартенситные стали сегодня могут подвергаться воздействию температур ниже 650°C.
Когда к сталям Fe-Cr добавляется достаточное количество Ni, легированная сталь становится аустенитной, имеющей гранецентрированную кубическую (ГЦК) кристаллическую структуру. . Аустенитные стали обладают высокой прочностью и пластичностью, а также обладают более высоким пределом прочности при ползучести, чем ферритные/мартенситные стали. При комнатной температуре аустенитные стали более пластичны и обычно легче изготавливаются. Аустенитные стали более дороги из-за высокого содержания в них легирующих элементов и обычно используются при температуре выше 650°С. На рис. 1 показаны ОЦК и ГЦК типы кристаллических структур.
Рис. 1 Тип кристаллической структуры
Жаропрочные стали представляют собой легированные стали, упрочненные твердым раствором, для использования при температурах выше 500°C и до 750°C. Поскольку эти стали используются в определенном широком диапазоне температур, они обычно упрочняются механизмом упрочнения термической обработкой, твердым раствором и осаждением. Для достижения желаемых свойств все жаропрочные стали наряду с основными элементами имеют несколько легирующих элементов. Их сложные композиции обеспечивают выдающиеся высокотемпературные свойства.
В жаропрочных сталях наиболее важными легирующими элементами являются Cr для стойкости к окислению и Ni для прочности и пластичности. Другие элементы добавляются для улучшения высокотемпературных свойств. Влияние различных легирующих элементов описано ниже.
Хром – Хром – единственный элемент, присутствующий во всех жаропрочных сталях. Помимо придания стойкости к окислению, хром повышает прочность при высоких температурах и устойчивость к науглероживанию. Cr является элементом, который делает микроструктуру ферритной. И Cr, и Fe имеют тенденцию образовывать феррит, чему противодействует Ni. Высокий уровень Cr также способствует образованию сигма-фазы.
Никель – Ni при добавлении в жаропрочные стали повышает их пластичность, жаропрочность и стойкость как к науглероживанию, так и к азотированию. Ni стремится сделать атомную структуру аустенитной. Это снижает растворимость как C (углерода), так и N2 в аустените. Сплавы на основе железа становятся аустенитными при добавлении определенного количества никеля, и, следовательно, он является важным элементом в аустенитной стали. Аустенитные жаропрочные стали содержат не менее 8 % Ni.
Углерод – С является самым важным упрочняющим неметаллическим элементом. C в жаропрочных сталях регулируется в определенных пределах. При повышении уровня С сталь становится прочнее, но теряет пластичность. Большинство кованых жаропрочных сталей содержат от 0,05 % до 0,1 % С. Литые жаростойкие стали обычно содержат от 0,35 % до 0,75 % С. С растворяется в легированной стали и вызывает прочность раствора. Он также присутствует в виде небольших твердых частиц, называемых карбидами, которые представляют собой химические соединения углерода с металлическими элементами, такими как Cr, Mo, Nb и Ti (титан) и т. д.
Азот – N2 присутствует в жаропрочных сталях в небольших количествах и служит для упрочнения как мартенситных, так и аустенитных сталей.
Кремний – Si снижает растворимость углерода в стали. Металлургически это увеличивает химическую «активность» C в сталях, и, следовательно, это важная переменная в процессе производства стали. Это упрочняющий элемент, содержание которого обычно превышает 0,04 %. Si улучшает стойкость к окислению и науглероживанию, а также стойкость к поглощению N2 в жаропрочных сталях при высоких температурах. Слой оксида кремния (SiO2), образующийся непосредственно под окалиной оксида хрома (Cr2O3) на сталях, помогает стали противостоять науглероживанию и поглощению N2.
Сера – S обычно рассматривается как примесь и обычно указывается 0,01 % в качестве верхнего предела для жаропрочных сталей. S ухудшает свариваемость, но улучшает обрабатываемость. Но преимущество заключается в улучшении обрабатываемости, поэтому для сталей марок 304 и 316 поддерживается на уровне около 0,02 %.
Фосфор s – Фосфор (P) обычно является нежелательным элементом в жаропрочных сталях, так как он оказывает разрушающее действие при сегрегации на границе зерен. Это также вредно для свариваемости легированной никелем стали. Обычно он указывается как верхний предел для большинства жаропрочных сталей. Даже присадки для сварки Ni должны содержать не более 0,015 % P.
Другие легирующие элементы – Другими легирующими элементами, используемыми в жаропрочных сталях, являются Mn, Mo, V, Ti, Nb, W (вольфрам), Al (алюминий), Co (кобальт), Zr (цирконий), Cu ( медь) и редкоземельные элементы, такие как B (бор), Ce (церий), La (лантан) и Y (иттрий). Эти элементы улучшают интеграционные свойства сталей при высоких температурах. В то время как некоторые из этих элементов используются для прочности, другие используются в основном для устойчивости к окислению, технологичности и стабильности микроструктуры.
С 1960 г. был проведен ряд исследований влияния легирующих элементов на сопротивление ползучести сталей 9-12Cr. Легирующие элементы для сталей 9-12Cr легко понять, если сгруппировать их по своим свойствам и влиянию на (i) Cr, (ii) Mo, W и Re, (iii) V, Nb, Ti и Ta. (тантал), (iv) C и N2, (v) B, (vi) Si и Mn и (vii) Ni, Cu и Co.
Cr является основным легирующим элементом для жаропрочных сталей, а Содержание повышает устойчивость к окислению и коррозии. Хотя Cr «сам по себе» не оказывает заметного влияния на сопротивление ползучести, более вероятно, что высокая прочность будет достигнута при процентном содержании Cr 2 % и 9 %.% до 12% в ферритных сталях, а прочность снижается в композициях между двумя покрытиями. Причина этого остается неизвестной.
Mo, W и Re (рений) являются элементами, полезными для упрочнения раствора. W и Mo уже давно используются для жаропрочных сталей. Эти элементы также дополнительно улучшают сопротивление ползучести жаропрочных сталей при добавлении в больших количествах. Однако если их добавки превышают определенный предел, то выделяется дельта-феррит и снижается прочность, а выделение фазы Лавеса снижает ударную вязкость. Кроме того, влияние W на сопротивление ползучести примерно вдвое меньше, чем у Мо. Совместное добавление W и Мо может быть эффективным для повышения прочности. Сообщается, что Re повышает предел ползучести при добавлении в количестве около 0,5 %, и этот эффект аналогичен действию W и Mo9.0021
V, Nb, Ti и Ta объединяются с C и/или N2 с образованием карбидов, нитридов или карбонитридов, которые тонко и когерентно осаждаются на ферритной матрице, демонстрируя заметный эффект дисперсионного упрочнения. Среди них V и Nb показывают особенно оптимальное содержание, около 0,2 % и 0,05 % соответственно. Эффект их совместного добавления может быть высоким, что свидетельствует о том, что образования выделений, состоящих из V и Nb, связаны друг с другом.
Так как C и N2 являются аустенитообразователями, они полезны для ингибирования дельта-феррита. Также их содержание связано с выделением и укрупнением карбидов и нитридов Cr. В частности, для С, если добавка превышает 0,1%, сопротивление ползучести часто снижается, и считается, что должно быть оптимальное добавление в зависимости от типа и содержания и т. д. карбидообразующих элементов. N2 считается элементом, необходимым для повышения сопротивления ползучести в 9% хромистых сталей. Добавление N2 часто составляет около 0,05 %, и считается, что его содержание должно быть оптимальным по сравнению с другими нитридобразующими элементами, такими как B.
B улучшает прокаливаемость и увеличивает прочность границ зерен, а также может значительно улучшить сопротивление ползучести. Кроме того, исследования показывают, что он проявляет эффект стабилизации карбидов за счет проникновения в M23C6.
Что касается Si и Mn, Si является ферритообразующим, тогда как Mn является аустенитообразующим. Их действия рассматриваются как противоречащие друг другу, и уменьшение содержания обоих этих элементов может улучшить сопротивление ползучести. Кроме того, Si способствует снижению ударной вязкости, способствуя образованию фазы Лавеса, в то время как Mn, хотя и полезен для повышения ударной вязкости, может ухудшить высокотемпературную стабильность ферритовой структуры, снижая температуру превращения A1 таким же образом, как и Ni.
Ni, Cu и Co являются аустенитообразователями, и при добавлении в качестве легирующих элементов они препятствуют образованию дельта-феррита за счет снижения эквивалента Cr, но одновременно снижают температуру превращения A1. Однако уровень этого снижения варьируется среди этих элементов, и снижение, наблюдаемое при добавлении Cu и Co, не больше, чем при добавлении Ni. Следовательно, если добавляют Cu и/или Co, можно ожидать эффекта ингибирования образования дельта-феррита, что делает возможным высокотемпературный отпуск.
Допустимое напряжение является хорошим показателем высокотемпературных прочностных характеристик жаропрочных сталей и часто определяется пределом прочности при ползучести в реальных условиях эксплуатации. Следовательно, чтобы повысить надежность высокотемпературных компонентов, необходимо установить предел прочности при ползучести до 100 000 часов (основа для определения допустимого напряжения) или сделать точную оценку этого и полностью оценить взаимосвязь между изменениями. в прочности на разрыв при ползучести и конструкции в течение длительных периодов времени. При выборе материалов необходимо учитывать как жаропрочность, так и экономичность. Как правило, более дорогие материалы обладают большей жаропрочностью.
На рис. 2 показаны химические составы типичных жаропрочных сталей, используемых под нагрузкой на тройной фазовой диаграмме Fe-Cr-Ni. Ферритные/мартенситные стали обычно не содержат никеля, и, поскольку составы Cr 2 %, 9 % и 12 % обладают особенно высокой прочностью, они широко используются. Среди аустенитных сталей коммерческие материалы располагаются вдоль границы между полной гамма-фазой и гамма-фазой, содержащей альфа-фазу и/или сигма-фазу. Стали с полной гамма-фазой содержат относительно высокое содержание никеля, и их высокая стоимость обычно компенсируется высоким сопротивлением ползучести. Напротив, стали гамма-фазы с альфа- и/или сигма-фазой, хотя и менее дорогие, нуждаются в некотором улучшении для повышения сопротивления ползучести.
Рис. 2 Составы жаропрочных сталей, используемых в тройной фазовой диаграмме Fe-Cr-Ni
Осадки и явление выделения
Жаропрочные стали упрочняются за счет явления выделения. В этом отношении сложнолегированные стали более выгодны, чем просто легированные, поскольку они имеют преобладающую характеристику реакции выделения. Однако чем сложнее сталь, тем сложнее протекают реакции осаждения.
Большинство осадков представляют собой нитрокарбиды, и лишь немногие из них представляют собой интерметаллические соединения. Выделения являются продуктами межзерновых и граничных выделений, а также различных карбидных реакций. Морфология, размер и распределение этих осаждающихся частиц модифицируются легирующими элементами, которые улучшают свойства из-за тех карбидных реакций, которые сопровождаются микроструктурными и микрохимическими изменениями. Типы выделений, присутствующих в конкретной жаропрочной стали, зависят от ее состава и термической обработки. Типы выделений, которые обычно образуются в ферритных жаропрочных сталях, представляют собой M23C6, M3C, M2C, M6C, MX (M означает атом растворенного вещества), фаза Лавеса и Z-фаза.
Существует простая взаимосвязь между карбидной структурой и металлическими элементами. В условиях эксплуатации наиболее распространенными вторичными фазами в жаропрочных сталях являются карбиды М23Х6, карбонитриды МХ, фаза Лавеса и фаза Z. Следовательно, большое внимание было уделено этим осадкам из-за их заметного влияния на характеристики ползучести.
М23С6 является основным компонентом большинства жаропрочных сталей. Считается, что количество М23С6, его размер и распределение сильно влияют на сопротивление ползучести жаропрочных сталей. Обычно этот карбид богат хромом, а Fe, Ni, Mn и Mo частично заменяют Cr. Доля этих замещающих атомов может составлять до 40 %. Кристаллическая структура M23C6 представляет собой сложную гранецентрированную кубическую (ГЦК) структуру, которая слегка меняется в зависимости от металлических элементов. Являясь основными карбидами в жаропрочных сталях, M23C6 выделяется в основном по границам зерен во время отпуска, и некоторые частицы могут образовываться на стадии процесса. Несмотря на то, что выделения M23C6 представляют собой очень устойчивые выделения по структуре, они укрупняются при воздействии ползучести при высокой температуре. Их средний размер увеличивается, а плотность уменьшается с увеличением времени экспозиции. Крупные частицы растут за счет растворения мелких частиц, но объемная доля остается постоянной.
MX — еще один типичный вид осадка нитрида углерода с кубической структурой типа NaCl. При отпуске и выдержке при высокой температуре при добавлении в легированные стали прочных формообразующих элементов V, Ti, Nb и W выделяется большое количество мелкодисперсных и дисперсных межкристаллитных частиц MX. Карбонитриды MX обычно образуются на дислокациях в матрице, поэтому они увеличивают сопротивление ползучести за счет закрепления дислокаций. Несмотря на то, что выделения MX стабильны и не сильно укрупняются при ползучести, обнаружено, что они могут растворяться и образовывать сложную нитридную Z-фазу при длительном воздействии ползучести.
Z-фаза, Cr(V,Nb)N, представляет собой еще один нитридный осадок с такими же элементами, как MX. Его кристаллическая структура тетрагональна. В высокохромистых ферритных сталях после длительной ползучести обнаруживается Z-фаза. Кроме того, было замечено, что Z-фаза выделяется после ползучести как в металле сварного шва, так и в зоне термического влияния. Обнаружение выделения Z-фазы в сталях 9-12Cr поставило серьезные вопросы о долгосрочной стабильности. Очень мало известно о поведении Z-фазы в 9-12Cr, так как наблюдалось его осаждение только после длительного воздействия или после длительного испытания на ползучесть. Недавно было установлено, что образование Z-фазы снижает долгосрочный предел ползучести, поскольку на образование Z-фазы расходуются мелкие частицы углеродного нитрида MX, которые являются основными упрочняющими частицами в ферритных сталях 9-12Cr. Z-фаза выделяется в виде крупных частиц, которые не способствуют дисперсионному упрочнению, и, таким образом, сопротивление ползучести стали значительно снижается.
Добавки W и Mo в легированные стали улучшают их характеристики ползучести. Однако эти элементы склонны к образованию интерметаллической фазы Лавеса (Fe,Cr)2(Mo,W). Частицы фазы Лавеса обычно выделяются на границах зерен вблизи карбидов М23С6 равноосной формы при ползучести. Кристаллическая структура фазы Лавеса гексагональная с диапазоном составов.
Установлено, что размер частиц фазы Лавеса быстро увеличивается при более высокой температуре воздействия. Выделение фазы Лавеса приводит к обеднению двух элементов Mo и W в матрице и к уменьшению эффекта упрочнения твердого раствора в легированных сталях. С другой стороны, выделение фазы Лавеса может увеличить сопротивление ползучести за счет дисперсионного твердения до того, как оно огрубеет. Считается, что фаза Лавеса оказывает негативное влияние, когда ее размер становится одним из самых крупных выделений в легированных сталях.
Тип осадков, присутствующих в указанной стали, зависит от ее химического состава и термической обработки. На самом деле жаропрочные стали показали очень сложные металлургические характеристики. Например, одна и та же сталь при разной плавке или одна и та же сталь, подвергнутая воздействию разных условий, может содержать разные карбиды с разным осаждением, морфологией или распределением.
Виды и применение жаропрочных сталей
Жаропрочные стали обладают химической стойкостью, достаточной прочностью, газовой коррозионной стойкостью. Эти стали можно разделить на низколегированные, мартенситные и аустенитные в зависимости от их химического состава и микроструктуры.
Низколегированные стали – Благодаря хорошим механическим свойствам при высоких температурах и достаточной коррозионной стойкости низколегированные стали широко используются в деталях, работающих под давлением в котлах. Самым последним достижением в области низколегированных сталей является разработка сталей 3Cr-3W(Mo)V, которые имеют более высокий предел ползучести, чем сталь 2,25Cr-1Mo и сталь 2,25Cr-1,6W-VNb.
В целом низколегированные хромомолибденовые ферритные стали прочны и пластичны при более низких рабочих температурах и сохраняют хорошую прочность при более высоких температурах. К сожалению, при длительном воздействии промежуточных рабочих температур эти стали могут стать охрупчивающимися с сопутствующим снижением вязкости разрушения и сдвигом температуры вязко-хрупкого перехода (DBTT) в сторону более высоких температур. Охрупчивание в основном вызвано изменениями в микрохимии границ зерен, что называется охрупчиванием при отпуске. Отпускное охрупчивание является неупрочняющим охрупчиванием и вызывается сегрегацией по границам зерен примесных элементов, таких как P, Sn (олово) и Sb (сурьма), в результате длительного воздействия в диапазоне температур от 350°С до 600°С. Р считается основным охрупчивающим примесным элементом в стали.
Другим типом низколегированных сталей, широко используемых для различных компонентов машиностроения, являются стали Cr1Mo, такие как 12Cr1MoV, 14CrMo4-5 (ISO 9328-2, 1991), 13CrMo4-5 (EN 10028-2, 1992) или 12C1. 1. (ASTM A182-96) и др. Эти стали являются жаропрочными сталями с низкими добавками легирующих элементов в химическом составе. Эти марки обычно используются для трубопроводов, предназначенных для транспортировки перегретого пара в диапазоне температур от 500°С до 560°С и под давлением от 10 МПа до 15 МПа.
Исходная микроструктура низколегированных сталей феррито-бейнитная или феррито-перлитная. Обычно жаропрочные стали Cr-Mo и Cr-W используются в нормализованном и отпущенном состоянии. Нормализация заключается в нагреве выше равновесной температуры А1, при котором феррит превращается в аустенит, и последующем охлаждении на воздухе.
В низколегированных сталях с содержанием Cr менее 5 % образуется бейнит (феррит, содержащий высокую плотность дислокаций и карбиды), полигональный феррит или комбинация этих двух составляющих в зависимости от размера сечения. Их сопротивление ползучести повышается за счет образования выделений, представляющих собой стабильные сплавы карбидов и интерметаллидов, полученных после нормализующей термической обработки, а затем подвергнутых очень жесткому отпуску (около 700 град в течение нескольких часов).
Низколегированные стали могут содержать любые выделения карбидов или карбонитридов, такие как M3C, M(C, N), M2(C, N), M7C3, M23C6, M6C, фазы Лавеса и интерметаллические выделения. Последовательности осаждения при высокой температуре для некоторых низколегированных сталей: (i) марка стали 2,25Cr1Mo – от M3C до M3C + M2C до M3C + M2C + M7C3 до M3C + M2C + M7C3+ M23C6, (ii) марка стали 3Cr1,5Mo – от M3C до M3C + M7C3 до M3C + M7C3 + M2C + M23C6 до M7C3 + M2C + M23C6, и (iii) марка стали Cr1MoV – M3C + MC до M3C + MC + M23C6 до M3C + MC + M23C6 + M7C3 до MC + M23C6 + М7С3.
Последовательность выделения карбидов в различных низколегированных сталях заметно различается, хотя термодинамические движущие силы, по-видимому, схожи. Считается, что различие в последовательности выделения связано с изменяющейся движущей силой для различных выделений в разных сталях.
При длительной эксплуатации в режиме ползучести в таких условиях изменяется микроструктура стали, происходит разложение бейнита/перлита и выделение карбидов по границам зерен, идут процессы укрупнения карбидов. Изменения структуры вызывают образование полостей и развитие внутренних повреждений. Это связано с тем, что существует тесная связь между изменениями микроструктуры и ухудшением механических свойств. В связи с этим необходимо уделить внимание изучению кинетики выделения карбидов из жаропрочных сталей при старении или длительной эксплуатации при высоких температурах. Цель состоит в том, чтобы попытаться определить любые микроструктурные параметры, которые могут быть использованы для оценки истории службы и могут быть применимы для оценки остаточного срока службы оборудования.
Мартенситные стали – Мартенситные жаропрочные стали включают среднехромистую сталь, содержащую от 5 % до 9 % Cr, и высокохромистую сталь, содержащую 12 % Cr. Мартенситная сталь 9-12Cr используется в нескольких областях, таких как компоненты котлов и паровых турбин. В котлах эти стали используются для труб в пароперегревателях и подогревателях, работающих при температуре металла до 620°С. Было признано, что стали 9-12 Cr являются ключевыми материалами для повышения теплового КПД паросилы. растения. За последние три десятилетия появился ряд новых 9Стали -12%Cr с улучшенным сопротивлением ползучести были разработаны для длительной эксплуатации при температурах, близких к 650°С, в высокотемпературных компонентах ультрасверхкритических электростанций.
Стабильно улучшенная прочность на разрыв при ползучести новых мартенситных сталей с содержанием 9-12% Cr была использована для создания новых усовершенствованных паровых электростанций, работающих на ископаемом топливе, с более высоким КПД. Применение этих новых легированных сталей обеспечивает не только высокую эффективность, но и снижение выбросов CO2 и других вредных для окружающей среды газов не менее чем на 20 %.
Для длительного применения новых сталей необходимо оценить микроструктурные изменения, которые могут произойти во время эксплуатации, и оценить влияние таких изменений на характеристики ползучести при высоких температурах. Эта информация может помочь в определении проектных значений для компонентов, изготовленных из сталей.
В целом мартенситные легированные стали имеют более низкий коэффициент теплового расширения и более высокую теплопроводность, чем аустенитные стали, и, следовательно, ожидается, что они будут более устойчивыми к термоциклированию.
Разработка сталей 9-12Cr, имевшая место около века назад, с использованием стали с содержанием 12 % Cr и от 2 % до 5 % Mo для лопаток паровых турбин. Мартенситные стали с высоким содержанием Cr и высоким содержанием C были твердыми и впоследствии были коммерчески разработаны для таких применений, как ножи для столовых приборов, бритвенные лезвия, лезвия скальпелей, а также жаропрочные инструменты и подшипники, конкурирующие с аустенитными нержавеющими сталями.
Начиная со стали 12CrMoV, внедренной на электростанциях в середине 19В 60-х годах разработка жаропрочных сталей за последние десятилетия привела к появлению новых сталей для паровых труб, таких как модифицированная 9Cr-сталь P91, представленная на заводах в 1988-х годах, модифицированная вольфрамом 9Cr-сталь P92, представленная в 2001 году, и E911, представленная в 2002 году. разработана и применяется для крупногабаритных поковок и отливок паровых турбин. Стали 9-12Cr с более низким содержанием углерода (не более 0,1 %) и добавками Mo, W, V, Nb, N2 и других элементов, обладающие более высокими показателями длительной прочности в сочетании с хорошей стойкостью к окислению и коррозии при высоких температурах, в дальнейшем получили широкое распространение. развитый. Эти стали использовались на электростанциях, нефтехимических и химических заводах, в газотурбинном машиностроении, авиационной и аэрокосмической промышленности, а также в качестве компонентов ядерных и термоядерных реакторов.
Для разработки новых легированных сталей с улучшенными характеристиками было предпринято много усилий для изучения металлургических аспектов механизмов упрочнения для объяснения улучшенного сопротивления ползучести. Также были изучены эффекты различных добавок. Например, при разработке сталей 12CrMoV для улучшения ударных свойств и подавления присутствия дельта-феррита в микроструктуре добавляли Ni. Это было связано с твердением на твердый раствор и пониженной растворимостью C. Однако избыточное количество Ni, превышающее 0,6 %, вызвало ускоренное снижение предела прочности при ползучести, что может быть частично связано с пониженной стабильностью M2X. фаза и осаждение частиц M6X
Модифицированные стали 9Cr-1Mo достигли своей высокой прочности на ползучести за счет добавления V, Nb и N2, которые образуют мелкие выделения MX, а предел ползучести мартенситных сталей с высоким содержанием Cr был дополнительно повышен за счет замены части Mo на W. легированные стали этого класса обычно включают мартенситные стали с содержанием 12 % Cr и 9 % Cr. Одной из известных сталей с содержанием 12 % Cr является сталь марки X20CrMoV12.1. С тех пор, как в 1950-х годах была разработана сталь марки X20CrMoV12.1, она уже несколько десятилетий успешно используется на электростанциях при температуре около 560°С. Сопротивление ползучести этой марки стали основано на упрочнении твердого раствора и осаждении M23C6. и карбиды MX.
В течение десятилетий разработка жаропрочных сталей была сосредоточена на улучшении ползучести сталей 9-12Cr. На основе марки 9 цель улучшения сопротивления ползучести привела к разработке новых легированных сталей, таких как стали марок 91, 92, E911, 122 и TAF. На рис. 3 показана экстраполированная прочность на разрыв при ползучести через 100 000 часов для некоторых мартенситных сталей 9-12Cr в зависимости от температуры. Очевидно, что свойство P92 на разрыв при ползучести было улучшено.
Рис. 3 Сопротивление ползучести открытых материалов в зависимости от температуры
Выдающееся положение занимает сталь с относительно высоким содержанием Cr 10,5 % и содержанием B от 0,027 % до 0,04 %. Однако другие попытки разработать высокопрочные легированные стали этого типа для повышения сопротивления ползучести не увенчались успехом из-за отсутствия долговременной стабильности при гораздо более высоких температурах. Считается, что стойкость к окислению паром может ограничивать максимальную рабочую температуру этих материалов, поэтому разработка легированных сталей в настоящее время сосредоточена на разработке материалов с более высоким содержанием Cr с сопротивлением ползучести, эквивалентным классу 9. 2.
Несколько исследований показали, что добавление легирующих элементов является эффективным способом улучшения сопротивления ползучести сталей 9-12Cr. Было обнаружено значительное улучшение сопротивления ползучести при добавлении В. Помимо B, Cr является ключевым элементом, влияющим как на стойкость к окислению, так и на сопротивление ползучести. Опыт показал, что для повышения стойкости к окислению до ожидаемого уровня требуется 12 % Cr.
Различные исследования показали, что улучшенный 9Легированная сталь % Cr и легированная сталь 12 % Cr могут использоваться для деталей толстого сечения, предназначенных для использования в рабочем диапазоне от 565 ° C до 620 ° C. Жаропрочные стали марок 92 и 122 используются в приложениях, где их более высокие прочности позволяют использовать более тонкие секции, тем самым снижая угрозу усталости из-за термоциклирования. Уменьшение веса, вызванное более тонкими стенками, также приводит к снижению напряжений в соединениях котла и турбины, а также в стальных конструкциях, что способствует увеличению срока службы компонентов и снижению затрат.
Результаты разработки и улучшения качества сталей с 10 % Cr показали, что усталостные свойства материала с 10 % Cr улучшаются по сравнению с обычными сталями с содержанием 11–12 % Cr. Дополнительным преимуществом стали с 10 % Cr по сравнению с обычными низколегированными сталями является то, что более низкий коэффициент теплового расширения позволяет выдерживать большее повышение температуры при запуске. Другой целью опытно-конструкторских работ была разработка сталей 9-12Cr для применения при температурах до 650°C.
Обширное исследование развития микроструктуры этих легированных сталей во время термического воздействия показало начальную микроструктуру удлиненных дислокационных ячеек и субзерен, выровненных с частицами M23C6, вместе с более мелкими частицами VN (нитрид ванадия) и M2X внутри субзерен. . При длительных испытаниях на ползучесть в образце произошло некоторое разупрочнение материала за счет термического воздействия. Частично это размягчение было связано с освальдовским созреванием существующих частиц, но наблюдалось осаждение новых частиц, в частности фазы Лавеса. Параллельно плотность дислокаций уменьшилась, так что внутри субзерен наблюдалось мало дислокаций. Все эти микроструктурные изменения происходят медленнее в сталях, содержащих В.
Микроструктура этих сталей 9-12Cr представляет собой мартенсит отпуска с сопротивлением ползучести, обеспечиваемым контролируемым выделением карбидов и нитридов. В основном стали 9-12Cr также применяют в нормализованном и отпущенном состоянии. Мартенсит образуется при нормализации изделий аустенитизацией выше температуры А1 и последующем охлаждении на воздухе. Во время этого процесса следует избегать образования дельта-феррита, так как это может привести к охрупчиванию, что приведет к проблемам при изготовлении. При последующем отпуске выше 700 град в течение часа образуются упрочняющие выделения. Виды выделений, образующихся в мартенситных жаропрочных сталях, также зависят от состава, температурной предыстории при изготовлении, времени и температуры эксплуатации.
Основным осадком в сталях 9-12Cr является карбид M23C6, состоящий из Cr, Fe, Mo, W и C. Этот карбид обеспечивает базовую прочность на ползучесть сталей 9-12Cr за счет осаждения на границах субзерен во время отпуска. Карбиды M23C6 повышают сопротивление ползучести за счет замедления роста субзерен, что является основным источником деформации ползучести в сталях с 12 % Cr. Термическая стабильность M23C6 относительно высока. Выделения MX в сталях с 12 % Cr состоят в основном из V, Nb и N2, которые выделяются внутри субзерен, где они закрепляют свободные дислокации и увеличивают сопротивление ползучести. Термическая стабильность преципитатов MX очень высока, что приводит к высокой прочности ползучести. Интересно отметить, что равновесные расчеты показывают, что упрочняющий эффект V в мартенсите обусловлен выделением VN. Это означает, что даже несмотря на то, что N2 не является указанным легирующим элементом в этих сталях, захваченный N2 способствует высокой прочности.
Аустенитные стали – Когда к сталям Fe-Cr добавляется достаточное количество Ni (более 8%), структура стали превращается в аустенитную структуру, которая имеет гранецентрированную кубическую кристаллическую структуру. Аустенитные стали – это нержавеющие стали. Они обладают более высокой прочностью, пластичностью и пределом прочности при ползучести, чем ферритно-мартенситные стали. Высокая прочность делает их нечувствительными к ударным нагрузкам и резким перепадам температуры. Аустенитные стали не склонны к укрупнению зерна при высоких температурах. Эти стали имеют более высокую прочность при повышенных температурах, а также сопротивление ползучести, чем ферритные стали. При комнатной температуре аустенитные стали более пластичны, обладают хорошей формуемостью и, как правило, легче поддаются обработке. Эти стали чувствительны к сернистым газам. Механическая обработка этих сталей более сложна по сравнению с ферритными сталями.
Аустенитные стали — это стали, легированные FeCrNi, с содержанием хрома более 13 %, имеющие аустенитную структуру при комнатной температуре. Аустенитные стали дороже ферритных из-за высокого содержания легирующих элементов. Традиционно применение аустенитных сталей ограничивается областями с более высокими температурами, где существуют суровые коррозионные условия. Аустенитные стали часто используются в качестве наплавки на ферритные материалы для ремонта корродированных участков или для обеспечения защиты в местах, где коррозия может быть проблемой.
Аустенитные стали разработаны на основе стали 18Cr-8Ni, полученной из стали марки AISI 302. Для достижения необходимых свойств добавляются другие легирующие элементы. Кроме элементов внедрения, таких как C и N2, добавляются некоторые замещающие элементы, такие как Mn, Mo, W, Cu, Al, Ti, Nb, V и т.д. Эти легирующие элементы классифицируются как стабилизаторы феррита или стабилизаторы аустенита по их влиянию на формирование ферритной или аустенитной структуры. Их вклад можно оценить, используя обозначения эквивалентов Cr и Ni. Creq (эквивалент Cr) представляет собой Cr + 2Si + 1,5Mo + 1,75Nb + 1,5Ti + 5,5Al + 0,75W (%), тогда как Nieq (эквивалент Ni) представляет собой Ni + Co + 0,5Mn + 0,3Cu + 30C + 23N2 (%) .
Различные типы аустенитных сталей были получены путем увеличения прочности с добавлением легирующих элементов. Nb, Ti и V могут значительно улучшить сопротивление ползучести аустенитных сталей за счет выделения мелких карбидов или карбонитридов. Кроме того, добавление этих элементов может стабилизировать легированную сталь против межкристаллитной коррозии. С металлургической точки зрения развитие аустенита заключается в увеличении объемной доли упрочняющих выделений за счет замены карбидов Cr другими, более стабильными карбидами, что в то же время высвобождает Cr обратно в матрицу, повышая коррозионную стойкость. Тем не менее, различные исследования показали, что присутствие частиц вторичной фазы может упрочнять аустенитные стали, но также было замечено, что эти частицы вторичной фазы влияют на усталостные характеристики.
Аустенитные стали, такие как марки AISI 316 и AISI 304, широко используются в качестве конструкционных материалов в нескольких областях применения. Фактически, аустенитные стали используются во многих областях, которые подвергаются воздействию различных температур и температурных градиентов. Аустенитные стали обычно имеют низкую теплопроводность и высокие коэффициенты теплового расширения. Замечено, что могут развиваться высокие термические напряжения, приводящие к усталостному растрескиванию.
«Недостабилизация» — это один из методов повышения сопротивления ползучести сталей 18–8 Cr-Ni. Этот метод улучшает сопротивление ползучести за счет улучшения морфологии выделений за счет фиксации углерода в легированных сталях и уменьшения содержания карбидообразующих элементов, таких как Ti и Nb, которые препятствуют образованию карбида Cr, до уровня, при котором их содержания недостаточно для фиксации углерода.
Хотя добавление меди не приводит к значительным изменениям вплоть до примерно 2 %, можно наблюдать существенное повышение сопротивления ползучести за счет добавления меди в количестве примерно 3 % или более. Однако, поскольку прочность имеет тенденцию к насыщению, и снижение пластичности при ползучести может произойти, когда добавка Cu превышает 3 %, добавка Cu в количестве 3 % должна быть ограничена.
Сплав 800HT представляет собой аустенитный сплав Ni-Fe-Cr (21 % Cr-32 % Ni-1 % Si-Al-Ti). Этот сплав характеризуется высоким сопротивлением ползучести и очень хорошей стойкостью к окислению. Супераустенитные нержавеющие стали 253MA или UNS S30815 и 353MA или UNS S35315 представляют собой аустенитные хромоникелевые стали, легированные азотом и редкоземельными металлами. Они обладают высоким сопротивлением ползучести и очень хорошей стойкостью к изотермическому и, прежде всего, циклическому окислению.
В настоящее время вместо аустенитных сталей ведется разработка высокопрочных ферритных сталей из-за их экономичности, хорошей свариваемости и вязкости разрушения, но все еще есть место для этих аустенитных сталей, которые в основном используются вместо аустенитных сталей. где стойкость к окислению и ползучесть у огня становятся более важными.
Ожидается, что следующее поколение жаропрочных сталей будет иметь еще более высокий предел текучести при высоких температурах, сопротивление ползучести (обычно предел прочности при разрыве в течение 100 000 часов составляет около 100 МПа) и коррозионную стойкость при высоких температурах. Однако ни один современный жаропрочный сплав не может удовлетворить этим требованиям. Таким образом, в настоящее время проводятся опытно-конструкторские работы по разработке сталей для использования при температурах до 700°С. Одной из успешно разработанных сталей является аустенитная нержавеющая сталь марки UNS S31035. Эта сталь обеспечивает очень высокий предел ползучести и хорошую коррозионную стойкость при высоких температурах. Alloy 800HT — еще один материал, разработанный для использования при температурах до 700 °C.
Основная проблема, связанная с использованием аустенитных сталей, заключается в том, как соединить материалы с компонентами, изготовленными из других классов материалов. Были проведены исследования методов и процессов сварки, а также поведения переходных соединений между аустенитными и мартенситно-ферритными сталями. Было обнаружено, что местоположение отказа варьировалось в зависимости от параметра испытания. При высоком напряжении при относительно низкотемпературном режиме разрушение обычно происходит в основном ферритном материале или металле сварного шва, а разрушение происходит вблизи границы раздела сварного шва (зона термического влияния), когда прикладывались низкие напряжения в диапазоне температур.
Относительно высокая стоимость аустенитных сталей в сочетании с такими недостатками, как высокий коэффициент теплового расширения и плохая теплопроводность, вероятно, продолжает ограничивать их применение. Есть две возможности дальнейшего развития. Во-первых, может иметь смысл разработка недорогой аустенитной стали, возможно, на основе Mn, а не Ni. Во-вторых, модифицированные аустенитные материалы, разработанные в ORNL (Национальная лаборатория Ок-Риджа), могут быть внедрены в коммерческую эксплуатацию. Высокая прочность этих сплавов может дать преимущества с точки зрения более тонких сечений и улучшенных характеристик теплопередачи.
Из других жаропрочных сплавов, которые могут быть использованы в будущем, обещают «оксидно-дисперсно-упрочненные» (ODS) сплавы, которые характеризуются хорошим сопротивлением ползучести при высоких температурах (т.е. выше 1000°С). Следовательно, эти сплавы рассматриваются как пригодные для применения при более высоких температурах, где прочность суперсплавов недостаточна. Эти сплавы обычно получают механическим легированием. Поскольку технологический процесс сложен и трудно поддается контролю при крупномасштабной переработке, в результате эти сплавы характеризуются плохой воспроизводимостью микроструктуры и непостоянством механических свойств. Сплавы ODS могут быть классифицированы на основе железа и на основе никеля по разнице в основном составе. Исследования показали, что их хорошая стойкость к высокотемпературному окислению коррелирует с диспергирующим оксидом, таким как Y2O3. Считается, что сплавы ODS наиболее выгодны в таких областях, как трубы теплообменников, где обычно встречаются высокие температуры, но нагрузка низка по сравнению с другими областями. Усилия по повышению прочности и разработке более совершенных методов изготовления продолжаются, и другие основные усилия направлены на создание надежных методов соединения.
Эволюция микроструктуры материалов, находящихся в эксплуатации
Микроструктуры сталей 9-12Cr, которые в настоящее время разрабатываются или уже имеются в продаже, состоят из одной фазы отпущенного мартенсита, за некоторыми исключениями. В этой структуре существуют дислокации высокой плотности, и на плотность дислокаций в основном влияет температура отпуска. Она становится высокой, когда температура отпуска низкая.
Считается, что ползучесть и эволюция структуры материала тесно связаны. Компоненты, подвергающиеся напряжению ползучести, имеют ограниченный срок службы. На самом деле было проведено большое количество исследований, чтобы связать исследования микроструктуры с эксплуатационным воздействием или остаточным сроком службы.
Свойства ползучести жаропрочных сталей определяются химическим составом и микроструктурой этих сталей. Если дан химический состав, то микроструктура этих сталей зависит от термической обработки, температуры и времени воздействия ползучести. Важнейшими механизмами упрочнения в этих сталях, работающих в условиях высокотемпературной ползучести, являются дисперсионное упрочнение и упрочнение на твердый раствор. На дисперсионное упрочнение ферритных сталей в основном влияют дисперсионные частицы MX. Показано, что как предел текучести при комнатной температуре, так и предел прочности при ползучести увеличиваются при увеличении плотности вторых фаз. При этом снижается скорость ползучести.
Если температура отпуска низкая, предел прочности при ползучести в краткосрочной области, как правило, высок, тогда как в долговременной области он быстро снижается, и кривая времени до разрушения пересекается с кривой времени до разрушения для высокотемпературных отпущенных сталей. Вероятно, это вызвано тем, что в низкотемпературных отпущенных сталях во время ползучести происходит рекристаллизация из мартенсита в равноосный феррит, что приводит к быстрому падению прочности, тогда как высокотемпературные отпущенные стали имеют микроструктуру, в которой плотность дислокаций мартенсита слишком мала с точки зрения условий отпуска. провести восстановление и перекристаллизацию. Из этих микроструктурных наблюдений следует, что ослабление из-за изменения микроструктуры менее вероятно во время ползучести в случае неустойчивых структур. То же самое, как известно, справедливо и для сталей с 12 % Cr, поэтому отпуск в последние годы проводился при температуре около 700°С, хотя ранее температура отпуска для этих сталей составляла около 650°С.0021
Очевидно, что механические свойства жаропрочных сталей ухудшаются при длительном воздействии высоких температур. Соответственно, их микроструктура также явно деградирует. Что касается характеристики эволюции микроструктуры, то ключевыми явлениями деградации являются (i) укрупнение выделений и фазовое превращение, (ii) распад исходной микроструктуры и (iii) образование микропустот на границах зерен. Эти микроструктурные изменения напрямую связаны с ухудшением сопротивления ползучести и других свойств, поэтому их часто рассматривают как демонстрацию воздействия перегрева и обычно принимают в качестве качественного показателя термической деградации. Исследования, проведенные в последние десятилетия, показали, что разные классы материалов имеют разные характеристики в эволюции микроструктуры.
Эволюция микроструктуры в ферритных сталях – Низколегированные стали или стали с перлитом/бейнитом проявляют тенденцию к сфероидизации перлита/бейнита после длительного воздействия высокой температуры. Типичная пластинчатая структура в перлите CrMoV меняется на структуру частиц. Служебное воздействие оказывает значительное влияние на прочность и пластичность. Также установлена и стандартизирована классификация микроструктурного износа сталей. На основании развития карбидной сфероидизации выделено пять степеней деградации. Классификация определяет уровень 1 как отсутствие сфероидизации, уровень 2 как наличие незначительной сфероидизации, уровень 3 как наличие средней сфероидизации, уровень 4 как наличие полной сфероидизации и уровень 5 как наличие серьезной сфероидизации. От уровня 1 до уровня 5 пластинчатая структура в перлите меняется на структуру частиц. Перлитная структура исчезает на уровне 4 и уровне 5, что приводит к ухудшению механических свойств. Таким образом, классификация микроструктурного износа низколегированных сталей устанавливается по степени сфероидизации.
Было проведено несколько исследований эволюции карбидов, присутствующих в стали, из-за воздействия ползучести. Разделение и укрупнение карбидов рассматриваются как показатель деградации материала из-за воздействия ползучести. Эволюция микроструктуры мартенситных сталей 9-12Cr имеет очень сложные характеристики при длительном воздействии высоких температур. Различные исследования показали, что значительно большее внимание уделяется укрупнению выделений, превращению мартенситной субструктуры и образованию микропустот на стадии деструкции стали. В этих исследованиях представлена оценка среднего размера частиц и доли остаточного ресурса для ферритных сталей. В этих исследованиях больше внимания уделялось M23C6, VC, фазе Лавеса и их составам. Однако в разных исследованиях были получены разные результаты по размеру и составу частиц с точки зрения абсолютного размера. Статистические показатели имеют хорошее соответствие в отношении зависимости среднего размера частиц от температурного воздействия или от времени выдержки при определенной температуре. На эту существенную разницу в абсолютных значениях (размер, содержание, межчастичное пространство и т. д.) сильное влияние оказывает не только статистический подход к оценке среднего качества, точность измерения при большом увеличении и выбранная методика отбора проб, история экспонирования испытуемого. компонент и его металлургические факторы и процесс формирования являются существенными действиями.
В отличие от низколегированных сталей, мартенсит редко менее чувствителен к образованию межкристаллитных полостей, и факторы воздействия на образование полостей намного сложнее, но в субструктуре можно увидеть некоторые признаки повреждения ползучести. Формы реек изменены, в частности, границы реек выглядят как бамбуковые сучки, называемые ячеистой структурой, что является типичной морфологией микроструктуры, вызванной ползучестью. В реечной структуре появилось много областей с низкой плотностью дислокаций, и можно увидеть некоторые типичные субструктуры. Субструктура, по-видимому, развивается по мере того, как границы субзерен формируются в результате движения дислокаций в процессе ползучести. Наблюдается существенное уменьшение плотности дислокаций, и можно увидеть несколько областей, свободных от дислокаций. Обширные выделения карбида можно увидеть на границах предшествующих аустенитных и мартенситных реек, с более мелкими выделениями в мартенситных пластинах. По границам образовались крупные укрупняющиеся карбиды в виде неправильного сфероида. По сравнению с исходным материалом карбидная морфология заметно огрубела.
Наблюдения во время исследования показали, что матрица отпущенного мартенсита претерпела ухудшение во время длительной ползучести. Дислокации взбирались или скользили и оканчивались на границах. По мере увеличения числа дислокаций на границах формируются сети и развиваются субструктуры. Морфология карбидов в границах отчетливо укрупняется, и большая часть упрочняющей фазы растворяется или укрупняется. За исключением характеристики укрупнения, мартенситные стали показали нормальную эволюцию микроструктуры, которая представляет собой распад мартенсита и изменение субструктуры во время длительного воздействия высокой температуры.
Принято считать, что мартенситная структура находится в стадии вырождения с увеличением времени ползучести. При длительном воздействии уменьшается плотность дислокаций, укрупняются выделения и уменьшается плотность мелких частиц в матрице. Границы мартенситной рейки нечеткие или даже исчезают, так как рейка подверглась вырождению. Огрубение реек происходит из-за двух путей, а именно (i) восстановления дислокаций внутри границ реек и (ii) рекомбинации двух границ субзерен, которая в основном происходит вблизи тройной точки границ реек при движении и вызывает исчезновение реечные границы. Также при смещении границ реек, вызывающем прогрессирующую локальную коалесценцию, неоднократно происходит растворение и переосаждение карбидов М23С6, распределяющихся по границам реек. Однако не подтверждено, что выделения MX выделяются во время ползучести или термического воздействия.
Эффект упрочнения твердого раствора легирующими элементами ослаблен, но оказался незначительным. Выделение фаз Лавеса не оказывает сильного влияния на стойкость этой стали к деформации ползучести, однако рядом с фазами Лавеса часто обнаруживаются полости повреждений, так что фазы Лавеса могут влиять на сопротивление стали разрушению при ползучести. Принято считать, что в случае ферритных сталей наблюдается увеличение содержания Cr в выделениях М23С6, а в эвтектоидных карбидах – увеличение содержания Мо, как М3С, так и М6С. Изменение состава выделений и уменьшение расстояния между частицами при укрупнении карбидов являются результатом проявления ползучести и деградации микроструктуры.
Однако существует заметная трудность в сопоставлении эволюции микроструктуры (например, вторых фаз) с оценкой остаточного ресурса. Необходимо знать не только фактическое состояние исходного материала, которое для одного и того же типа материала может значительно варьироваться от нагревания к нагреванию или от продукта к продукту, но и условия воздействия и историю, поскольку они также являются факторами, влияющими на ход эволюции. Более того, не установлено количественной зависимости, связывающей параметры микроструктурной эволюции с истощением жизни.
Образование микропустот на границах зерен – Концепция образования микропустот или микрополостей на границах зерен изучалась и развивалась в 1970-х годах. Обычно он признается и применяется с классификацией Нойбауэра и производными методами на протяжении десятилетий. Принцип основан на том, что развитие ползучести жаропрочных сталей связано с появлением полостей за некоторое время до разрыва. Эти полости постепенно образуют микротрещины за счет взаимосвязей и в конце концов начинают инициировать разрыв. Появление микропустот означает, что сталь в процессе эксплуатации сильно повреждена.
Схематическая оценка микроструктуры по Нойбауэру имеет ряд классов, а именно (i) класс 0, который соответствует полученному, без тепловой эксплуатационной нагрузки, (ii) класс 1, который подвергается ползучести, без полостей, (iii) класс 2а, который является усовершенствованным воздействие ползучести, изолированные полости, (iv) класс 2b, который представляет собой более сильное воздействие ползучести, многочисленные полости без предпочтительной ориентации, (v) класс 3a, который представляет собой повреждение ползучести, многочисленные ориентированные полости, (vi) класс 3b, который представляет собой серьезное повреждение ползучести, цепи полостей и / или разделения по границам зерен, (vii) класс 4, который представляет собой серьезное повреждение ползучести, микротрещины, и (viii) класс 5, который представляет собой большое повреждение ползучести, макротрещины.
Еще один важный аспект взаимосвязи наличия полостей с развитием ползучести можно найти в документах Нойбауэра, где утверждается, что «заметное образование полостей происходит на границе зерен в конце вторичной ползучести». Поскольку примеры распределения степеней поврежденности кажутся не вполне соответствующими кривой ползучести, можно считать, что 4-й и 5-й классы можно принять как репрезентативные для разных стадий третичной ползучести, а 3-й класс принять как точку перехода между вторичными а третичный и класс 2 считаются представителями вторичной ползучести.
Размер и плотность полостей обычно увеличиваются по мере ползучести. Размер и плотность полостей также зависят от типа материала, однако обычно считается, что образование микропустот и характер их эволюции являются важным показателем для оценки степени повреждения. Исследования образования микропустот указывают на то, что зарождение полости связано с границей зерна и частицами второй фазы в ней, а также наличием поверхностно-активных элементов, таких как P и Sn, в границе зерна, что облегчает зарождение полости. Плотность полостей (количество полостей на единицу площади границы зерна) увеличивается с увеличением времени ползучести и температуры, а приложенное напряжение также увеличивает плотность полостей. Рост полостей контролируется двумя механизмами: диффузионным ростом и ростом ограничения, первый преобладает при высоком уровне напряжений, а второй – при значительно меньших напряжениях.
Размер микропустот находится в диапазоне микрометров, и они не могут быть обнаружены с помощью обычных методов неразрушающего контроля (НК), поэтому необходимо металлографическое исследование для наблюдения за их морфологией и распределением.
Некоторые важные моменты, касающиеся жаропрочных сталей
Выбор жаропрочных сталей для конкретного применения основывается на требуемом уровне жаростойкости и требуемых механических свойствах стали. Использование более высоких легирующих элементов и, следовательно, более жаростойких может быть невыгодным из-за охрупчивания, помимо более высокой стоимости. Жаропрочная сталь не должна подвергаться воздействию пламени, и следует избегать прямого контакта с С, чтобы предотвратить снижение жаростойкости из-за науглероживания.
Жаропрочные стали используются в промышленных печах, паровых котлах, паровых трубах, паровых турбинах, рекуператорах, металлургической, химической и нефтяной промышленности, газо- и топливопроводах, топках, нагревателях, резисторах, теплообменниках и мусоросжигательных заводах и т. д.
Термообработка гомогенизацией для снижения разрушения отливок из жаропрочной стали
- Панель авторов Войти
Что такое открытый доступ?
Открытый доступ — это инициатива, направленная на то, чтобы сделать научные исследования бесплатными для всех. На сегодняшний день наше сообщество сделало более 100 миллионов загрузок. Он основан на принципах сотрудничества, беспрепятственного открытия и, самое главное, научного прогресса. Будучи аспирантами, нам было трудно получить доступ к нужным нам исследованиям, поэтому мы решили создать новое издательство с открытым доступом, которое уравняет правила игры для ученых со всего мира. Как? Упрощая доступ к исследованиям и ставя академические потребности исследователей выше деловых интересов издателей.
Наши авторы и редакторы
Мы являемся сообществом из более чем 103 000 авторов и редакторов из 3 291 учреждения в 160 странах, в том числе лауреатов Нобелевской премии и самых цитируемых исследователей мира. Публикация на IntechOpen позволяет авторам получать цитирование и находить новых соавторов, а это означает, что больше людей увидят вашу работу не только из вашей собственной области исследования, но и из других смежных областей.
Оповещения о содержимом
Краткое введение в этот раздел, посвященный открытому доступу, особенно с точки зрения IntechOpen
Как это работаетУправление предпочтениями
Контакты
Хотите связаться? Свяжитесь с нашим головным офисом в Лондоне или командой по работе со СМИ здесь
Карьера
Наша команда постоянно растет, поэтому мы всегда ищем умных людей, которые хотят помочь нам изменить мир научных публикаций.
Открытый доступ
Автор:
Мохаммад Хосейн Бина
Представлено: 18 января 2012 г. Опубликовано: 19 сентября 2012 г.
DOI: 10.5772/50312
Скачать бесплатноиз отредактированного тома
Под редакцией Yogiraj Pardhi
Заказ о заказах. В этой главе исследуется влияние гомогенизационной термической обработки на разрушение отливок из жаропрочных сталей. Во-первых, описаны литые нержавеющие стали и факторы, влияющие на разрушение этих сталей. Одним из наиболее важных факторов является сигма-фазовое охрупчивание, которое подробно изучено. Наконец, обсуждается влияние гомогенизационной термической обработки на растворение карбидов и уменьшение сигма-фазы и разрушения. Настоящая глава представляет собой сборник моего промышленного опыта и других исследований разрушения валков печи непрерывного отжига, подготовленный для использования практиками и исследователями. Глава также может быть полезна аспирантам, исследующим неудачи.
Объявление
2. Классификация и обозначение литых нержавеющих сталей
Литые нержавеющие стали обычно классифицируют как отливки из коррозионно-стойкой стали (которые используются в водных средах при температуре ниже 650°C) или отливки из жаропрочной стали (которые подходят для рабочая температура выше 650 °C). Литые нержавеющие стали чаще всего указываются на основе химического состава с использованием системы обозначений Группы высоколегированных продуктов Американского общества производителей стали [1].
2.1. Отливки из коррозионностойкой стали
Отливки из коррозионностойкой стали широко используются в химических процессах и электрооборудовании, где требуется коррозионная стойкость в водной или парожидкостной среде при температурах ниже 315°C. Работоспособность литых коррозионно-стойких сталей во многом зависит от отсутствия в микроструктуре сплава углерода и особенно выделенных карбидов. Поэтому литые коррозионно-стойкие сплавы обычно имеют низкое содержание углерода (обычно менее 0,20 %, а иногда и менее 0,03 %). Все литые коррозионно-стойкие стали содержат более 11 % хрома [1].
Рис. 1.
Содержание хрома и никеля в отливках из жаростойких и коррозионностойких сталей стандартных марок ACI [1].
2.2. Отливки из жаропрочной стали
Отливки из нержавеющей стали классифицируются как жаропрочные, если они способны длительно работать при непрерывном или периодическом воздействии рабочих температур, при которых температура металла превышает 650°C. Отливки из жаропрочных сталей напоминают высоколегированные коррозионно-стойкие стали, за исключением более высокого содержания углерода, что придает им большую прочность при повышенной температуре [1]. Три основные категории литейных сталей Н-типа в зависимости от состава [1–4]:
Железо-хромовые сплавы, содержащие от 10 до 30% Cr и мало никеля или совсем без него.
Эти сплавы имеют низкую прочность при повышенных температурах и полезны в основном благодаря своей стойкости к окислению. Использование этих сплавов ограничено условиями, либо окислительными, либо восстановительными, которые предполагают низкие статические нагрузки и равномерный нагрев. Содержание хрома зависит от предполагаемой температуры эксплуатации [1].
Железохромоникелевые сплавы содержат более 13 % Cr и 7 % Ni (хрома всегда больше, чем никеля) [1]. Эти аустенитные сплавы обычно используются в окислительных или восстановительных условиях, подобных тем, которым выдерживают ферритные железо-хромовые сплавы, но в эксплуатации они обладают большей прочностью и пластичностью, чем прямые хромовые сплавы. Поэтому они используются, чтобы выдерживать большие нагрузки и умеренные перепады температур. Эти сплавы также используются в присутствии окисляющих и восстановительных газов с высоким содержанием серы.
Железо-никель-хромовые сплавы содержат более 25 % Ni и более 10 % Cr (никеля всегда больше, чем хрома) [1].
Эти аустенитные сплавы используются для выдерживания восстановительных, а также окислительных атмосфер, за исключением случаев, когда содержание серы заметно. (В атмосферах, содержащих 0,05% или более сероводорода, например, рекомендуются железо-хромо-никелевые сплавы [1].) В отличие от железо-хромо-никелевых сплавов, железо-никель-хромовые сплавы не науглероживаются быстро и не становятся хрупкими. и не поглощают азот в азотирующих атмосферах. Эти характеристики улучшаются с увеличением содержания никеля, а в науглероживающих и азотирующих средах срок службы отливок увеличивается с увеличением содержания никеля [1]. Аустенитные сплавы железа, никеля и хрома широко применяются в условиях сильных колебаний температуры, например, в приспособлениях, используемых при закалке, и в деталях, которые нагреваются неравномерно или периодически нагреваются и охлаждаются. Кроме того, эти сплавы обладают характеристиками, которые делают их подходящими для нагревательных элементов электрического сопротивления.
Объявление
3. Микроструктура жаропрочных сталей
Микроструктура той или иной марки в первую очередь определяется составом. Хром, молибден и кремний способствуют образованию феррита (магнитного), тогда как углерод, никель, азот и марганец способствуют образованию аустенита (немагнитного). Хром (промотор феррита и мартенсита), никель и углерод (промоторы аустенита) особенно важны для определения микроструктуры [1]. Жаропрочные литейные сплавы (кроме типа HA) содержат большое количество хрома и никеля, которые обычно являются аустенитными и немагнитными. Аустенит в матрице обеспечивает полезную жаропрочность, если он надлежащим образом армирован частицами карбида и нитрида. Для достижения максимальной прочности аустенит не должен содержать феррита [5]. Микроструктура отливок из аустенитной нержавеющей стали типа HH (25Cr-12Ni), используемых в валках печи непрерывного отжига в необработанном состоянии, представлена на рис. 2. Идеальная микроструктура сплава HH составляет
Рис. 2.
Микроструктура валика в необработанном состоянии (2% нитала).
аустенитная, тогда как на рис. 2 исходная микроструктура состояла из частиц аустенита, феррита, а также черных карбидов. Присутствие феррита объяснялось неконтролируемым затвердеванием и, следовательно, возникновением явления сегрегации в образце.
Наличие феррита в микроструктуре может быть полезным или вредным (особенно при высоких температурах) в зависимости от применения. Феррит может быть полезен с точки зрения свариваемости, поскольку полностью аустенитные нержавеющие стали подвержены проблеме свариваемости, известной как горячее растрескивание или образование микротрещин. Но при 540 °С и выше ферритная фаза может трансформироваться в комплексное железо-хром-никель-молибденовое интерметаллическое соединение, известное как σ-фаза, что снижает ударную вязкость, коррозионную стойкость и пластичность при ползучести [1]. Степень снижения прочности увеличивается со временем и при температуре примерно до 815°С и может сохраняться до 9°С.25°С [1].
Реклама
4. Сигма-фазовое охрупчивание
Несколько факторов вызывают разрушение отливок из жаропрочной стали, такие как окисление, сульфидирование, науглероживание, ползучесть, термическая усталость и сигма-фазовое охрупчивание. Интерметаллиды, такие как сигма-фаза, являются важными источниками разрушения высокотемпературных материалов.
Существование σ-фазы в железо-хромовых сплавах впервые было обнаружено в 1907 г. при наблюдении термической остановки на кривых охлаждения [6]. Первое фактическое наблюдение σизг в сплавах железа с хромом было сообщено в 19 г.27 [7]. σ-фаза была идентифицирована методом рентгеновской дифракции в 1927 г. [8] и в 1931 г. [9]. После того, как существование σ было твердо установлено, были проведены многочисленные исследования для определения составов и температур, при которых может образовываться σ. В целом, σизг образуется при длительной выдержке в диапазоне от 565 до 980°С, хотя этот диапазон несколько меняется в зависимости от состава и обработки [1]. Сигма-фаза имеет тетрагональную кристаллическую структуру с 30 атомами в элементарной ячейке и отношением c/a , равным примерно 0,52 [10]. Сигма также образуется в аустенитных сплавах. В полностью аустенитных сплавах σ образуется из аустенита по границам зерен. При наличии в аустенитном сплаве δ-феррита образование σ происходит быстрее и происходит в δ-феррите [1].
Эта фаза представляет собой уникальную комбинацию железа и хрома, образующую твердую и хрупкую вторую фазу. Наличие сигма-фазы не только оказывает вредное влияние на механические свойства материала, но и снижает его коррозионную стойкость за счет удаления хрома и молибдена из аустенитной матрицы. Относительно небольшое количество сигма-фазы, когда она почти непрерывна на границе зерен, может привести к очень раннему выходу деталей из строя [11]. На рис. 3(а) показан неисправный ролик (типа HH), который использовался для перемещения металлической полосы в печах непрерывного отжига. Аустенитная матрица и сеть выделений сигма-фазы на границах аустенитных зерен в неисправном ролике показаны на рис. 3(б). Образование сигма-фазы при длительном нагреве при температурах выше 650°С приводит к неблагоприятному снижению ударной вязкости роликов при более низких температурах и в периоды простоя. Поэтому в периоды остановки, правки или прогрева распространение трещины по сигма-фазе на границах зерен приводит к выходу из строя роликов [12,13].
Рис. 3.
а) Вид вышедшего из строя печного ролика, (б) микроструктура аустенитной матрицы и сеть выделений сигма-фазы на границе зерен (электролитическое травление) [13].
Все ферритные стабилизирующие элементы способствуют образованию σизг [1]. В промышленных сплавах кремний даже в небольших количествах заметно ускоряет образование σизг. В целом все элементы, стабилизирующие феррит, способствуют образованию σизг. Молибден оказывает такое же влияние, как кремний, а алюминий оказывает меньшее влияние. Увеличение содержания хрома также способствует образованию σизг. Небольшие количества никеля и марганца увеличивают скорость образования σизг, хотя большие количества, которые стабилизируют аустенит, замедляют образование σизг. Добавки углерода уменьшают образование σизг за счет образования карбидов хрома, тем самым уменьшая количество хрома в твердом растворе [14,15]. Добавки вольфрама, ванадия, титана и ниобия также способствуют образованию σизг. Как и следовало ожидать, σ образуется легче в ферритных, чем в аустенитных нержавеющих сталях [14-17].
4.1. Механизм образования сигма-фазы в жаропрочных сталях
На рис. 4 показан механизм образования сигма-фазы в вышедшем из строя ролике. Наличие дельта-феррита в аустенитной матрице приводит к ускоренному образованию сигма-фазы. Как правило, эта фаза зарождается внутри дельта-феррита. Превращение дельта-феррита можно описать двумя эвтектоидными реакциями [1]:
δ→M23C6+γ2E1
δ→σ+γ2E2
Рис. 4.
. Стрелками показаны крупные перлитоподобные колонии.
По реакции (1) образуются карбиды М 23 С 6 пластинчатой морфологии, а также вторичный аустенит (рис. 4). Механизм этой реакции можно обобщить следующим образом: во-первых, рост карбидных выделений внутри дельта-феррита приводит к образованию вторичного аустенита [18]. Содержание хрома вблизи выделений высокое и приводит к увеличению содержания хрома вблизи соседнего дельта-феррита. Поэтому внутри дельта-феррита развивается рост карбидов и формируется пластинчатая структура, включающая карбиды и вторичный аустенит [19]. ]. Наконец, после завершения пластинчатой преципитации на передней стороне преципитатов формируется сигма-фаза [19].
Рис. 5.
Различные морфологии сигма-фазы в нержавеющей стали [20].
4.2. Морфология сигма-фазы
Морфологию сигма-фазы можно разделить на дендритные и глобулярные структуры [17,20,21]. На рис. 5 показана морфология сигма-фазы в нержавеющей стали (19Cr-9Ni-2Mn). Сигма-фаза образовалась путем превращения дельта-феррита в охрупчивающую сигма-фазу и вторичный аустенит из-за неподходящих условий работы. Лин и др. [20] указали, что дендритоподобная сигма-фаза нестабильна, а глобулярная сигма-фаза стабильна. Кроме того, вокруг частиц δ-феррита наблюдалась дендритоподобная σ-морфология, что означало частичное фазовое превращение δ→σ [20]. Гилл и др. [21] также предположили, что сфероидальная σ-фаза является результатом неустойчивости дендритной сигма-фазы к любому локализованному уменьшению ширины.
4.3. Места выделения сигма-фазы
Места выделения сигма-фазы состоят из границы раздела δ/γ, тройной конъюнкции, угла зерна и ячейки, которые показаны на рис. 6 [22]. Местами начального выделения является межфазная граница δ/γ, так как она имеет более высокую граничную энергию и здесь сосредоточено много дефектов. Следовательно, выделение сигма-фазы происходит преимущественно на границе δ/γ, а затем выделяется ближе к внутренней части зерна дельта-феррита [19].,22]. Другие места осаждения были сконцентрированы в δ-феррите, поскольку σ-фаза предпочитала осаждаться в области с более высоким содержанием Cr [20,22]. Выделение в углу зерна означает, что сигма-фаза была сильно сконцентрирована и образовалась в углу дельта-феррита. Осаждение при тройном соединении означало, что σ-фаза выделяется вокруг δ-феррита. Выделение ячеистой формы представляло собой эвтектоидный распад дельта-феррита на сигма- и вторичную аустенитную фазы, который отчетливо наблюдался при 800°С [22].
4.

Одним из наиболее подверженных влиянию образования сигма-фазы механических свойств сталей является энергия удара. Влияние сигма-фазы на энергию удара аустенитной стали Fe-25Cr-20Ni показано на рис. 8 [23]. При увеличении времени выдержки в интервале температур формирования сигма-фазы (760–870°С) значение ударной вязкости снижается на 85 %.
Влияние высокотемпературного воздействия на ударную вязкость с низким междоузлием 29Ферритная нержавеющая сталь Cr-4Mo была исследована (рис. 9) Aggen et al. [24]. На этом рисунке кривая С показывает время охрупчивания в зависимости от температуры старения. Для образования σ охрупчивание было наиболее быстрым примерно при 775°C, тогда как охрупчивание при 475°C было медленнее с максимальной скоростью примерно при 480°C. В целом для этого сплава сигма-фаза образуется в интервале температур от 595 до 925°С. Охрупчивание наиболее выражено при образовании межкристаллитных σ-пленок, что приводит к межкристаллитному растяжению и ударному разрушению [1].
Рис. 6.
Выделение сигма-фазы на: (а) границе раздела δ/γ и (б) тройной конъюнкции, угловой и ячеистой [22].
Рис. 7.
Влияние времени и температуры старения на энергию удара аустенитной стали Fe-25Cr-20Ni [23].
Рис. 8.
Зависимости время-температура для получения DBTT при 25 и 100°C для ферритной нержавеющей стали 29Cr-4Mo в зависимости от времени старения, которые охватывают как диапазон охрупчивания при 475°C, так и диапазон охрупчивания σ-фазы [24]. ].
Твердость сигма-фазы в сплавах Fe-Cr составляет примерно 68 HRC [1]. На рис. 10 показана микроструктура аустенитной матрицы и сеть выделений сигма-фазы на границе зерна, а также инденторные эффекты на поверхности в нескольких местах. Видно, что из-за хрупкости и большей твердости сигма-фазы по отношению к аустенитной матрице эта фаза часто разрушается при вдавливании.
Рис. 9.
Микроструктура аустенитной матрицы и сеть выделений сигма-фазы на границе зерна. Видно, что из-за того, что сигма является хрупкой фазой, часто происходит разрушение при вдавливании (указано стрелками) [12].
Поэтому относительно небольшое количество σ-фазы, когда она почти сплошная на границе зерен, может привести к очень раннему выходу из строя высокотемпературных деталей [12].
Объявление
5.

Для устранения расслоения в литой структуре часто необходимо гомогенизировать деталь перед использованием, чтобы обеспечить однородность химического состава и микроструктуры. Эта обработка также может быть использована для полного растворения карбидов и хрупких и вредных фаз, таких как сигма, которые образуются в условиях эксплуатации. В этом методе сталь нагревается в течение достаточно длительного периода времени, чтобы завершить растворение карбидов, а затем начинается охлаждение с соответствующей скоростью, чтобы избежать образования вредных фаз [12].
Specimen | Homogenization temperature (°C) | 5″ border-bottom=”.5″ border-left=”.5″ border-right=”.5″ bgcolor=”auto” dir=”btLr” valign=”center” align=”center”> Cooling environment | Microstructures (etched electrolytically by 10 M KOH solution) | Microstructures (etched by Marble’s reagent) |
Hh2 | – | – | 5″ bgcolor=”auto” valign=”center” align=”center”> | |
Hh3 | 950 | Air | ||
HH8 | 5″ border-bottom=”.5″ border-left=”.5″ border-right=”.5″ bgcolor=”auto” dir=”btLr” valign=”center” align=”center”> 1050 | Air | ||
Hh21 | 1100 | Air | 5″ border-left=”.5″ border-right=”.5″ bgcolor=”auto” valign=”center” align=”center”> | |
Hh24 | 1100 | Furnace |
Table 1.
Микроструктуры выбранной разрушенной роликовой стали до и после термообработки гомогенизацией в течение 2 часов.
Микроструктуры выбранной разрушенной прокатной стали до и после гомогенизирующей термической обработки при различных температурах в течение 2 ч представлены в таблице 1. В микроструктуре образца Hh24 отчетливо видно образование хрупкой сигма-фазы и выделение карбидов по сравнению с микроструктура образца Hh21. В результате медленного охлаждения в печи все желаемые изменения в гомогенизированной структуре обращаются вспять. Другими словами, образование карбидных выделений в зернах, неоднородность аустенита в качестве матричной фазы и образование интерметаллических хрупких фаз типа сигма-фазы — все это результаты медленного охлаждения при температурах от 650 до 9°С.50°C, сильно снижает ударную вязкость стали. Поскольку образование сигма-фазы является трудоемким процессом, образование этой фазы было сведено к минимуму за счет охлаждения на воздухе. Наименьшее количество сигма-фазы и карбидов наблюдается в образце Hh21, который показывает однородность микроструктуры и уменьшение микроскопической сегрегации. Поэтому для роликовой правки и получения хорошей ударной вязкости следует проводить гомогенизирующую термообработку при 1100°С в течение не менее 2 ч с последующим охлаждением на воздухе [12].
На рис. 11 показаны участки выделения сигма-фазы в неисправном валке до и после гомогенизирующей термообработки при 1100 °С в течение 2 ч с последующим охлаждением на воздухе. Рис. 12 и табл. 2 иллюстрируют химический состав в трех точках сканирования, указанных на рис. 11 (а), (б) и (в). Как видно на рис. 11, точки 1, 2 и 3 представляли собой аустенитную матрицу, дельта-феррит и сигма-фазу соответственно. Таблица 2 показывает, что содержание хрома, молибдена и кремния в сигма-фазе выше, чем в аустенитной фазе. Как правило, дельта-феррит и сигма-фаза богаты хромом. Но массовый процент кремния и молибдена в дельта-феррите выше, чем в других фазах (аустените и сигме). Кремний и молибден играют важную роль в фазовом превращении δ→σ+γ2 и действуют как сильные стабилизаторы дельта-феррита [5,20].
Как видно из рис. 11, термообработка при 1100°С с последующим охлаждением на воздухе привела к изменению морфологии сигма-фазы с дендритной структуры (рис. 11(а) и (б)) на глобулярную структуру ( Рис. 11(в)). Дендритная сигма-фаза указывает на нестабильную форму, а глобулярная сигма-фаза демонстрирует стабильную форму. Кроме того, дендритная структура хрупкая, а шаровидная структура пластична. Таким образом, можно сделать вывод, что для завершения превращения дельта-феррита в сигма-фазу необходимо повысить температуру гомогенизационной термообработки до 1100°С и преобразовать морфологию сигма-фазы в стабильную глобулярную структуру. Эта структура приводит к заметному увеличению энергии удара и пластичности ролика печи непрерывного отжига. Напротив, образование сигма-фазы с дендритной морфологией приводит к снижению пластичности и разрушению ролика.
Рисунок 10.
w3.org/2001/XMLSchema-instance” xmlns:sym=”http://www.w3.org/2012/symbol”> Морфология сигма-фазы. (а) и (б) после разрушения и до обработки гомогенизацией соответственно и (в) после термообработки гомогенизацией при 1100 °С в течение 2 ч с последующим охлаждением на воздухе.Рис. 11.
Анализ ЭДС: (а) аустенитной фазы (точка 1 на рис. 11(а)), (б) ферритной фазы (точка 2 на рис. 11(б)) и (в) сигма-фаза (точка 3 на рис. 11(в)).
Точка | Element (wt.![]() | ||
Cr | Si | Mo | |
1 (gamma) | 22.125 | 1.353 | 0.227 |
5″ border-right=”.5″ bgcolor=”auto” valign=”center” align=”left”> 2 (delta) | 27.639 | 2.896 | 1,341 |
3 (Sigma) | 34.641 | 2,544 | 1.![]() |
Table 2.
Table 2.
.
.
. неудавшийся образец до гомогенизации, (б) образец после гомогенизационной термообработки при 1100 °С в течение 2 ч с последующим охлаждением в печи и (в) с последующим охлаждением на воздухе.
На рис. 13 представлены поверхности излома разрушенного образца до гомогенизации (рис. 13(а)), образца после гомогенизационной термообработки при 1100 °С в течение 2 ч с последующим охлаждением в печи (рис. 13(б) ), и образец после гомогенизационной термообработки при 1100 °С в течение 2 ч с последующим охлаждением на воздухе (рис. 13(в)). Анализ ЭДС точек 1 и 2 на рис. 13(а) и 13(б), соответственно, указывают на наличие сигма-фазы в определенных кристаллографических плоскостях. Фактически поверхность разрушения разрушенного образца (рис. 13, а) содержала характерное для хрупкого разрушения случайное расположение плоских поверхностей и поверхностей со ступенями. Поверхность излома образца после гомогенизационной термообработки при 1100 °С в течение 2 ч с последующим охлаждением в печи (рис. 13, б) представляла собой смесь мелких ямочек и слоистых поверхностей, свидетельствующих о хрупком и вязком изломе в этом образце. ЭДС-анализ точки 3 на рис. 13(б) показал наличие хрома в виде карбидных частиц. Частицы карбида находились в центре небольших ямочек. По данным ЭДС-анализа точек 2 и 3 можно сказать, что из-за медленной скорости охлаждения в печи все желаемые изменения, происходящие в гомогенизированных структурах, обращаются вспять и происходит новое образование сигма-фазы и выделений в образце. при переходе от вязкого к почти хрупкому разрушению. Как видно на рис. 13 (с), образование глубоких ямок является основной характеристикой вязкого разрушения. ЭДС-анализ точки 4 был аналогичен основному металлу. Эта цифра указывает на значительное уменьшение количества сигма-фазы и осадков после гомогенизации.
Следовательно, перед роликовой правкой необходимо провести гомогенизирующую термическую обработку для растворения вредных фаз в аустените в качестве матричной фазы и получения хорошей ударной вязкости. Во многих случаях микроструктурная неоднородность может быть устранена выдержкой образца при высоких температурах в течение достаточного времени и охлаждением с соответствующей скоростью. В противном случае очень высока возможность образования мелких трещин при роликовой правке. Эти трещины могут привести к поломке ролика в процессе правки и/или в печи непрерывного отжига.
Реклама
6. Выводы
Сигма-фаза имеет тенденцию выделяться в областях с высоким содержанием хрома, таких как карбиды хрома в зерне. Относительно небольшое количество σ-фазы, когда она почти непрерывна на границе зерен, может привести к очень раннему выходу из строя высокотемпературных деталей. Важно понимать, что сигма-фаза не может подвергаться значительной пластической деформации; вместо этого он ломается даже при относительно низких уровнях деформации. Это верно при повышенных температурах, но тем более при температуре окружающей среды. Там, где прочность и пластичность являются важной частью конструкции системы, сигма-фаза недопустима. Образование сигма-фазы с дендритной морфологией приводит к снижению пластичности и разрушению жаропрочных сталей. Микроструктурная неоднородность (сигма-фаза и карбиды) может быть устранена выдержкой образца при высоких температурах в течение достаточного времени и охлаждением с соответствующей скоростью. Гомогенизационная термообработка в соответствующих условиях может привести к изменению морфологии сигма-фазы с дендритной структуры на глобулярную. Эта структура приводит к значительному увеличению энергии удара и пластичности жаропрочных сталей.
Ссылки
- 1. СправочникA. S.M.Volume.PropertiesSelectionIrons.SteelsHigh PerformanceAlloys. A.S.M.InternationalMaterials.ParkOhio, 2005
- 2. Lamb, S., Практическое руководство по нержавеющим сталям и никелевым сплавам, ASM International, Materials Park, Ohio, 1999.
- 3. ASM Handbook, Volume 15, Casting, ASM International, Materials Парк, Огайо, 2005
- 4.
ШиС.Липпольд Дж. C.Микроструктура «.Эволюция во время.эксплуатации.двух.литых жаростойких.нержавеющих сталей HP-Nb.модифицированных 20-32nb»материалов.ХарактеристикаТом.810292008
- 5. Прагер М. и Свобода Дж. Литейная металлургия высоколегированных металлов, Металлургия стального литья, Американское общество основателей стали, Роки Ривер, Огайо, 1984.
- . Анорг. Chem., 5512
- 7. E.C. Bain and W.E. Griffiths, An Introduction to the Iron-Chromium-Nickel Alloys, Trans.AIME, 751927166
- 8. Chevenard P.Experimental ResearchofIron.NickelChromiumAlloys.TravMem., Bur. Междунар. Poids et Mesures, 17192790
- 9. Wever F.JellinghausW.The-ComponentTwo.System-ChromiumIron.Mitt-WilhelmKaiser.InstVol1.1931143
- 10. HallE. О.ЭлджиС. H.TheSigma.PhaseMetall.RevVol1.196661
- 11. Справочник по ASM, Том 11, Анализ и предотвращение отказов, ASM International, Materials Park, Ohio, 2002.
- 12. BinaM. Х.ДиниГ.Вагефис. М. М. Саатчи, А. Раиси, К. Наваби, М. Применение «.Гомогенизации.
- 13. ДиниГ.БинаМ. Х.Вагефис. М.М.РаисиК.Сафаей-РадМ.НавабиМ.Отказ“.печи непрерывного отжига.Роллер.МобаракеСтил.компания”Инженерный.Анализ отказов.Том78562008
- 14. А.Дж. Лена и В.Е. Карри, Влияние холодной обработки и рекристаллизации на образование сигма-фазы в высокостабильных аустенитных нержавеющих сталях, Trans.ASM, 471955193
- 15. Справочник по ASM, том 19, усталость и разрушение, ASM International, Materials Park, Ohio, 2005
- 16. Справочник по ASM, Том 12, Фрактография, ASM International, Materials Park, Ohio, 2005
- 17. Лин Д.Ю., Лю Г.Л., Чанг Т.К. и Хси Х.К., «Развитие микроструктуры нержавеющей стали 24Cr-14Ni-2Mn после старения при различных соотношениях азот/воздух», Journal of Alloys and Compounds, Vol.1-21501542004
- 18.
TsengC. C.ShenY.ThompsonS. В.МатаяМ. C.KraussG.Разрушение «.Формирование.сигма-фазы M.C.аустенита из.дельта-феррита в. I. S. I. 3.StainlessL.Steel»Металлургические.МатериалыСделки. A.Vol6114711581994
- 19. MartinsM.CastelettiL. Материалы C.Sigma «.PhaseMorphologies.inCast.Aged.Super.Duplex.Stainless.Steel.CharacterizationVol.87927952009
- 20. HsiehC. К.ЛинД. Y.WuW.Осадки“.Поведение. σ.Phasein. .CrNiMn.Cr-0.SiНержавеющие.стали, горячекатаный.при.8.с°. C.VariousReduction.Ratios» Materials.ScienceEngineeringA.Vol1-21811892007
- 21. GillT. П. С. Виджаялкшми М. Родригес П. Падманабхан К. A.О «корреляции.микроструктуры-свойств.термально.стареющего типа». 3.StainlessL.SteelWeld.Metal» Metallurgical.TransactionsA.Vol6111511241989
- 22. HsiehC. К.ЛинД. Ю.ЧангТ. Материалы.ScienceEngineeringA.Vol1-21281352008
- 23. Г.Н. Эмануэль, Сигма-фаза и другие эффекты длительного нагрева при повышенных температурах на 25-процентной хромистой-20-процентной никелевой стали, на Симпозиуме о природе, возникновении и влиянии сигма-фазы, STP 110, Американское общество испытаний и материалов, 195182
- 24.
AggenG.et al.Microstructures Versus.Propertiesof.29FerriticStainless.Steelin.MiCon. 7. Оптимизация свойств обработки. производительности службы. T. P.67Американское общество.испытаний.материалов1979334
Разделы
Информация о авторе
- 1. Введение
- 2. Классификация и обозначение литых нержавеющих сталей
- 6.Выводы
Ссылки
Реклама
Автор:
Мохаммад Хосейн Бина
Представлено: 18 января 2012 г. Опубликовано: 19 сентябряth, 2012
СКАЧАТЬ БЕСПЛАТНО © 2012 Автор(ы). Лицензиат IntechOpen. Эта глава распространяется в соответствии с условиями лицензии Creative Commons Attribution 3.0, которая разрешает неограниченное использование, распространение и воспроизведение на любом носителе при условии надлежащего цитирования оригинальной работы.
В рамках нашей миссии по поддержке распространения знаний мы путешествуем по всему миру, чтобы представить наши публикации и поддержать наших авторов и академических редакторов. Мы посещаем международные симпозиумы, конференции, семинары, книжные ярмарки, а также деловые встречи с профессионалами в области науки, образования и издательского дела. Ознакомьтесь с предстоящими и прошедшими мероприятиями.
\r\n\tОбразование и развитие человека — это междисциплинарная область исследований, целью которой является пролить свет на темы, связанные как с обучением, так и с развитием. Эта серия предназначена для исследователей, практиков и студентов, которые хотят больше узнать об этих областях и их приложениях.
Жаропрочная сталь | Специальные стали и магнитные материалы | Ассортимент продукции | Бизнес и продукция
Tohoku Steel может похвастаться самой большой долей внутреннего рынка жаростойкой стали для клапанов двигателей и производством очень надежной, высококачественной жаропрочной стали.
Жаропрочная сталь для впускных клапанов
Наименование и состав стали
Наименование стали | С | Си | Кр | Пн |
---|---|---|---|---|
СУх2 | 0,45 | 3 | 8 | ― |
СУх4 | 0,40 | 2 | 11 | 1 |
СУх21 | 0,50 | 1,5 | 8 | ― |
〔масс.%〕
Физическое свойство
Плотность 〔г/см ~{3} 〕 | Коэффициент теплового расширения 〔X10 ~{-6}/ ℃〕 | Теплопроводность 〔W/m・K〕 | Электрическое сопротивление 〔мкОм・㎝〕 | |
---|---|---|---|---|
СУх2 | 7,70 | 20-600℃ 12,5 | 20℃ 16,7 800℃ 23 | 20℃ 79 |
СУх4 | 7,65 | 20-800℃ 12,2 | 20℃ 15,2 800℃ 22,7 | 20℃ 84 |
СУх21 | 7,70 | 20-600℃ 13,4 | 20℃ 25 | 20℃ 73 |
Температурный режим термообработки
Закалка | Закалка | |
---|---|---|
СУх2 | 980~1080℃, закалка в масле | 700~850℃, воздушное охлаждение |
СУх4 | 980~1080℃, закалка в масле | 700~800℃, воздушное охлаждение |
СУх21 | 1000~1050℃, закалка в масле | 650~750℃, воздушное охлаждение |
Механические свойства при высоких температурах
Тепловая обработка испытательного образца
SUH2: 1030 ℃, OQ / 750 ℃, AC , SUH4: 1050 ℃, OQ / 750 ℃, AC
SUH21: 1030 ℃, OQ / 750 ℃, AC
9 21: 1030 ℃, OQ / 750 ℃, AC
1189 21: 1030 ℃, OQ / 750 ℃, AC
9189 21: 1030: 1030 ℃, 750 ℃, AC
18: 1030 ℃, 750 ℃, AC.

Жаропрочная сталь для выпускных клапанов (на основе железа)
Состав
Наименование стали | C | Mn | Ni | Cr | N |
---|---|---|---|---|---|
21-2Н | 0,5 | 8 | 2 | 20 | 0,3 |
СУх45 | 0,5 | 9 | 3,5 | 21 | 0,4 |
23-8Н | 0,3 | 2 | 8 | 23 | 0,3 |
Материальное имущество
Плотность 〔г/см ~{3} 〕 | Коэффициент теплового расширения 〔X10 ~{-6} /℃〕 | Теплопроводность 〔W/m・K〕 | Электрическое сопротивление 〔мкОм・㎝〕 | |
---|---|---|---|---|
21-2Н | 7,73 | 20-400℃ 16,5 20-760℃ 18,4 | 20℃ 18.![]() | 20℃ 79 |
СУх45 | 7,75 | 20-500℃ 17,5 20-760℃ 18,4 | 20℃ 18.0 | 20℃ 75 |
23-8Н | 7,85 | 20-500℃ 17,8 20-800℃ 19,5 | 20℃ 18.0 | 20℃ 75 |
Состояние температуры термообработки
Обработка раствором | Старение | |
---|---|---|
21-2Н | 1100~1150℃, быстрое охлаждение | 730~780℃, воздушное охлаждение |
СУх45 | 1100~1200℃, быстрое охлаждение | 730~780℃, воздушное охлаждение |
23-8Н | 1100~1180℃, быстрое охлаждение | 750~800℃, воздушное охлаждение |
.0792 23-8N:1100℃,WQ/800℃,AC
High temperature corrosion resistance
Heat-resistant steel for exhaust valves (high alloy)
Composition summary
Steel Имя | Ni | Кр | Фе | Ал | Ти | Другие дополнительные элементы |
---|---|---|---|---|---|---|
NCF751* | ≧70 | 15 | 6 | 1 | 2,5 | Nb+Ta |
NCF80A* | Бал | 20 | ≦1,5 | 1,5 | 2 | C |
Недвижимое имущество
Плотность 〔г/см ~{3} 〕 | Коэффициент теплового расширения 〔X10 ~{-6} /℃〕 | Теплопроводность 〔W/m・К〕 | Электрическое сопротивление 〔мкОм・㎝〕 | |
---|---|---|---|---|
NCF751* | 8,24 | 20-760℃ 14,9 20-820℃ 16,6 | 20℃ 13,6 800℃ 31,4 | 20℃ 121,5 |
NCF80A* | 8,17 | 20-760℃ 14,9 20-900℃ 17,0 | 20℃ 11,0 800℃ 29,5 | 20℃ 124 |
Состояние термической обработки
Обработка раствором | Старение | ||
---|---|---|---|
NCF751* | 1135~1165℃, быстрое охлаждение | 800~830℃, воздушное охлаждение 690~720℃, быстрое охлаждение | Ссылка условие |
NCF80A* | 1120~1150℃, быстрое охлаждение | 730~760℃, воздушное охлаждение | Ссылка условие |
.

Стойкость к высокотемпературной коррозии
*NCF751 эквивалентен Inconel 751.
*NCF80A эквивалентен Nimonic 80A.
*Inconel и Nimonic являются зарегистрированными торговыми марками Special Metals Corporation.
Термический центр – Металлургические основы термической обработки
Термическая обработка нержавеющих сталей в значительной степени зависит от типа (деформируемая или литая) и марки нержавеющей стали, а также от причины обработки, чаще всего для обеспечения восстановления свойств, измененных во время изготовления (например, коррозионная стойкость, пластичность или твердость), чтобы компонент из нержавеющей стали мог работать в предполагаемых условиях эксплуатации. Существует довольно много различных термообработок.
Очистка
Очистка, которую часто упускают из виду, необходима перед выполнением каких-либо операций по термообработке нержавеющей стали для удаления масел, жиров и других видов остатков. Оставшись на поверхности нержавеющей стали во время термообработки, может произойти локализованное науглероживание, ухудшающее коррозионную стойкость или другие свойства материала.
Отжиг
Для нержавеющей стали обычно используется ряд различных методов отжига (полный, изотермический, подкритический). Аустенитные нержавеющие стали нельзя упрочнять термической обработкой, но они упрочняются холодной обработкой. Отжиг не только позволяет рекристаллизовать упрочненные зерна, но также переводит карбиды хрома (осаждающиеся на границах зерен) обратно в раствор. Отжиг также можно использовать для гомогенизации отливок или сварных швов и для снятия напряжений от холодной обработки.
Температура отжига обычно выше 1900°F (1040°C), хотя некоторые типы нержавеющей стали можно отжигать при строго контролируемых температурах вплоть до 1850°F (1010°C), когда желателен мелкий размер зерна. Время при температуре часто поддерживается коротким, чтобы свести к минимуму окисление поверхности и контролировать рост зерен, что может привести к поверхностному явлению, называемому «апельсиновой коркой».
Закалочный отжиг
Отжиг аустенитной нержавеющей стали иногда называют закалочным отжигом, поскольку металл необходимо быстро охладить в диапазоне температур 19от 00°F (1040°C) до ниже 1100°F (600°C) и предпочтительно ниже 900°F (480°C), чтобы предотвратить осаждение карбидов на границах зерен (сенсибилизация). Исключение составляют стабилизированные и сверхнизкоуглеродистые сорта. Это может быть достигнуто очень быстрым охлаждением газом или водой с ускорением вентилятора.
Докритический (технологический) отжиг
Подкритический отжиг рекомендуется для всех применений, не требующих максимальной мягкости. Все мартенситные и большинство ферритных нержавеющих сталей могут подвергаться докритическому отжигу путем нагревания до верхней части диапазона температур феррита или полному отжигу путем нагрева выше критической температуры до диапазона аустенита с последующим медленным охлаждением. Типичные температуры для докритического отжига составляют от 1400°F (760°C) до 1525°F (830°C).
Когда материал был предварительно нагрет выше критической температуры, например, при горячей обработке, по крайней мере некоторое количество мартенсита присутствует, даже в ферритных нержавеющих сталях (например, 430). Относительно медленное охлаждение со скоростью 75 ° F (25 ° C) в час от полной температуры отжига или выдержка в течение одного часа или более при докритической температуре отжига требуется для получения желаемой мягкой структуры феррита и сфероидизированных карбидов. Однако детали, подвергнутые только холодной обработке давлением после полного отжига, могут быть удовлетворительно подвергнуты подкритическому отжигу менее чем за 30 минут.
Ферритные типы сохраняют преимущественно однофазные структуры во всем диапазоне рабочих температур (например, 409, 442, 446) и требуют только короткого рекристаллизационного отжига в диапазоне 1400°F (760°C) – 1750°F (955°C). ).
Повторный процесс (стабилизирующий) отжиг
Стабилизирующий отжиг иногда проводят после обычного отжига для сплавов, содержащих титан или ниобий (например, 321 и 347). Большая часть углерода связана с титаном марки 321 или с ниобием марки 347 при их отжиге обычным способом.
Второй отжиг между 1600°F (870°C) и 1650°F (900°C) в течение нескольких часов с последующим быстрым охлаждением осаждает весь возможный углерод в виде карбида титана или ниобия и предотвращает последующее осаждение карбида хрома. Эта специальная защитная обработка иногда полезна в чрезвычайно коррозионных условиях эксплуатации, особенно когда работа также включает температуры в диапазоне от 750°F (400°C) до 1600°F (870°C).
Светлый отжиг
Все марки нержавеющей стали могут подвергаться светлому отжигу в высоко восстановительных печах с регулируемой атмосферой, работающих в атмосфере водорода, диссоциированного аммиака или азота/водорода при точке росы ниже -60°F (-50°C) или при вакуумные печи для предотвращения или сведения к минимуму окисления поверхности. Мартенситные марки (в зависимости от содержания углерода) и даже некоторые ферритные марки подвержены водородному охрупчиванию.
Закалка, закалка и отпуск
Мартенситные нержавеющие стали закаляются путем аустенизации, закалки и отпуска, как и низколегированные стали. Типичными являются температуры аустенизации от 1800°F (980°C) до 1850°F (1010°C). Твердость после закалки увеличивается с температурой аустенизации примерно до 1800°F (980°C), а затем снижается из-за присутствия остаточного аустенита. Для некоторых марок оптимальная температура аустенизации может зависеть от температуры последующего отпуска.
Медленная скорость нагрева или предварительный нагрев перед аустенитизацией рекомендуется для предотвращения растрескивания в высокоуглеродистых сортах (например, 440°C) и в сложных сечениях низкоуглеродистых сортов. Предварительный нагрев до 1450°F (790°C) с последующим нагревом до температуры аустенизации является обычной практикой.
Воздушное охлаждение от температуры аустенизации обычно достаточно для получения полной твердости, но иногда используется закалка в масле, особенно для больших сечений. Детали следует подвергать отпуску, как только они остынут до комнатной температуры, особенно если использовалась закалка в масле, чтобы избежать замедленного растрескивания. Закалка при температуре выше 950°F (510°C) должно сопровождаться относительно быстрым охлаждением до температуры ниже 750°F (400°C), чтобы избежать охрупчивания при 885°F (475°C).
Дисперсионное твердение мартенситных марок (например, 17-4, 13-8) обычно требует полного отжига с последующим кондиционированием аустенита, трансформационным охлаждением и старением (дисперсионным твердением). Полуаустенитные типы дисперсионно-твердеющего твердения (например, 17-7, 15-7) могут потребовать отжига, триггерного отжига (для подготовки аустенита к превращению при охлаждении до комнатной температуры), охлаждения при отрицательных температурах (для завершения превращения аустенита) и старение (до полного упрочнения сплава). Закалка улучшает прочность и ударную вязкость и обычно происходит в 9Диапазон от 00°F (480°C) до 1150°F (620°C).
Обработка при температуре ниже нуля
Компоненты из нержавеющей стали могут подвергаться криогенной обработке перед отпуском для преобразования остаточного аустенита, особенно там, где важна стабильность размеров (например, 440°C). Температуры в диапазоне от -100°F (-75°C) до -150°F (-100°C) являются обычным явлением, и используется глубокое охлаждение ниже -300°F (-185°C).
Снятие напряжения
Аустенитные нержавеющие стали обычно нагревают от 800°F (425°C) до 1700°F (925°C) для достижения адекватного снятия напряжения. Один час при температуре 1600°F (870°C) обычно снимает около 85% остаточных напряжений. Однако снятие напряжения в этом температурном диапазоне может также привести к выделению карбидов на границах зерен, что приводит к сенсибилизации, которая серьезно снижает коррозионную стойкость. Чтобы избежать этих эффектов, настоятельно рекомендуется использовать стабилизированную нержавеющую сталь (например, 321 или 347) или сталь с очень низким содержанием углерода (например, 304L или 316L), особенно если требуется длительное время снятия напряжения.
Снятие напряжения снижает остаточные напряжения, предотвращает коррозионное растрескивание под напряжением, улучшает ударную вязкость и стабильность размеров при эксплуатации. Обработка полным раствором (отжиг), как правило, путем нагрева примерно до 1975 ° F (1080 ° C) с последующим быстрым охлаждением, снимает все остаточные напряжения, но не является практической обработкой для большинства крупных или сложных изделий.
При изготовлении сваривается большое количество нержавеющей стали. Когда полный отжиг невозможен, например, для крупных компонентов или сложных форм, сварные детали можно нагревать до промежуточной температуры, чтобы уменьшить высокие остаточные напряжения. Снятие напряжения выполняется при соединении разнородных металлов, таких как аустенитная нержавеющая сталь и низколегированная сталь. Снятие напряжений в сварных соединениях из мартенситной или ферритной нержавеющей стали закалит зоны термического влияния и восстановит некоторую коррозионную стойкость.
Низкотемпературное снятие напряжения
Когда аустенитные нержавеющие стали подвергаются холодной обработке давлением для достижения высокой прочности, низкотемпературное снятие напряжения увеличивает предел пропорциональности и предел текучести (особенно предел текучести при сжатии). Снятие напряжения при низких температурах в диапазоне от 325°F (160°C) до 775°F (415°C) уменьшит остаточное напряжение практически без влияния на коррозионную стойкость и/или механические свойства. Можно использовать температуры до 800°F (425°C), если не требуется устойчивость к межкристаллитной коррозии.
Науглероживание и азотирование
Процессы низкотемпературного азотирования и науглероживания были разработаны для аустенитных нержавеющих сталей и быстро завоевывают признание для повышения стойкости к износу и коррозии. Мягкая жесткость матрицы ограничивает эти процессы в высоконагруженных приложениях.
Покрытия
Наиболее часто применяемым покрытием является нитрид титана (TiN), который используется как для повышения прочности поверхности, так и для эстетических целей, имеет привлекательный золотой цвет и зеркальное покрытие.
сталь | Состав, свойства, типы, сорта и факты
производство
Посмотреть все СМИ
- Ключевые сотрудники:
- Эндрю Карнеги Генри Бессемер Сэр Уильям Сименс Джон Огастес Роблинг Чарльз М. Шваб
- Похожие темы:
- Дамасская сталь углеродистая сталь стальная промышленность перлит литая сталь
Просмотреть весь связанный контент →
Резюме
Прочтите краткий обзор этой темы
сталь , сплав железа и углерода, в котором содержание углерода колеблется до 2 процентов (при более высоком содержании углерода материал определяется как чугун). На сегодняшний день это наиболее широко используемый материал для строительства инфраструктуры и промышленности в мире, он используется для изготовления всего, от швейных иголок до нефтяных танкеров. Кроме того, инструменты, необходимые для изготовления таких изделий, также изготавливаются из стали. Как показатель относительной важности этого материала, в 2013 году мировое производство необработанной стали составило около 1,6 миллиарда тонн, а производство следующего по важности технического металла, алюминия, составило около 47 миллионов тонн. (Для списка производства стали по странам, см. ниже Мировое производство стали.) Основными причинами популярности стали являются относительно низкие затраты на ее производство, формовку и обработку, обилие двух сырьевых материалов (железной руды и металлолома) и беспрецедентный ассортимент механические свойства.
Свойства стали
Основной металл: железо
Изучение производства и структурных форм железа от феррита и аустенита до легированной стали
Посмотреть все видео к этой статье Основным компонентом стали является железо, металл, который в его чистое состояние ненамного тверже меди. За исключением самых крайних случаев, железо в твердом состоянии, как и все другие металлы, поликристаллично, т. е. состоит из многих кристаллов, смыкающихся друг с другом на своих границах. Кристалл — это хорошо упорядоченное расположение атомов, которые лучше всего можно представить в виде сфер, соприкасающихся друг с другом. Они упорядочены в плоскостях, называемых решетками, которые особым образом проникают друг в друга. Для железа расположение решетки лучше всего представить единичным кубом с восемью атомами железа в углах. Важным для уникальности стали является аллотропность железа, то есть его существование в двух кристаллических формах. В объемно-центрированной кубической (ОЦК) конфигурации в центре каждого куба находится дополнительный атом железа. В гранецентрированной кубической (ГЦК) конфигурации в центре каждой из шести граней единичного куба находится один дополнительный атом железа. Существенно, что стороны гранецентрированного куба или расстояния между соседними решетками в ГЦК конфигурации примерно на 25 процентов больше, чем в ОЦК компоновке; это означает, что в ГЦК-структуре больше места, чем в ОЦК-структуре, для удержания инородных ( , т.
е. сплава) атомов в твердом растворе.
Железо имеет аллотропию ОЦК ниже 912°C (1674°F) и от 1394°C (2541°F) до температуры плавления 1538°C (2800°F). Называемое ферритом, железо в его ОЦК-образовании также называется альфа-железом в диапазоне более низких температур и дельта-железом в зоне более высоких температур. Между 912° и 1394°С железо находится в ГЦК-порядке, который называется аустенитным или гамма-железом. Аллотропное поведение железа сохраняется, за немногими исключениями, в стали, даже когда сплав содержит значительное количество других элементов.
Существует также термин бета-железо, который относится не к механическим свойствам, а скорее к сильным магнитным характеристикам железа. Ниже 770 ° C (1420 ° F) железо является ферромагнитным; температуру, выше которой он теряет это свойство, часто называют точкой Кюри.
Викторина “Британника”
Строительные блоки предметов повседневного обихода
Из чего сделаны сигары? К какому материалу относится стекло? Посмотрите, на что вы действительно способны, ответив на вопросы этого теста.
В чистом виде железо мягкое и, как правило, не используется в качестве конструкционного материала; основной метод его упрочнения и превращения в сталь – добавление небольшого количества углерода. В твердой стали углерод обычно встречается в двух формах. Либо он находится в твердом растворе в аустените и феррите, либо находится в виде карбида. Форма карбида может быть карбидом железа (Fe 3 C, известным как цементит) или карбидом легирующего элемента, такого как титан. (С другой стороны, в сером чугуне углерод проявляется в виде чешуек или скоплений графита из-за присутствия кремния, подавляющего образование карбидов.)
Влияние углерода лучше всего иллюстрируется диаграммой равновесия железо-углерод. Линия A-B-C представляет точки ликвидуса (, т. е. температуры, при которых расплавленное железо начинает затвердевать), а линия H-J-E-C представляет точки солидуса (при которых затвердевание завершается). Линия A-B-C показывает, что температура затвердевания снижается по мере увеличения содержания углерода в расплаве железа. (Это объясняет, почему серый чугун, содержащий более 2 процентов углерода, обрабатывается при гораздо более низких температурах, чем сталь.) Расплавленная сталь, содержащая, например, 0,77 процента углерода (показана вертикальной пунктирной линией на рисунке), начинает затвердевает при температуре около 1475 ° C (2660 ° F) и полностью затвердевает при температуре около 1400 ° C (2550 ° F). С этой точки и ниже все кристаллы железа находятся в аустенитной — , т. е. ГЦК — компоновка и содержат весь углерод в твердом растворе. При дальнейшем охлаждении резкое изменение происходит примерно при 727 ° C (1341 ° F), когда кристаллы аустенита превращаются в тонкую пластинчатую структуру, состоящую из чередующихся пластинок феррита и карбида железа. Эта микроструктура называется перлитом, а изменение называется эвтектоидным превращением. Перлит имеет твердость алмазной пирамиды (DPH) примерно 200 кгс на квадратный миллиметр (285 000 фунтов на квадратный дюйм), по сравнению с DPH 70 кгс на квадратный миллиметр для чистого железа.
Охлаждающая сталь с более низким содержанием углерода ( , например, 0,25 процента) дает микроструктуру, содержащую около 50 процентов перлита и 50 процентов феррита; это мягче, чем перлит, с DPH около 130. Сталь с содержанием углерода более 0,77%, например, 1,05%, содержит в своей микроструктуре перлит и цементит; он тверже перлита и может иметь DPH 250.
Оформите подписку Britannica Premium и получите доступ к эксклюзивному контенту. Подписаться сейчас
Выделение осадка в аустенитной жаропрочной нержавеющей стали 22Cr25NiWCuCo(Nb) при термообработке при 1200 °C
. 2021 26 февраля; 14 (5): 1104.
дои: 10.3390/ma14051104.
Шэн-Мин Ян 1 , Цзин-Лин Ву 1 , Ён-Цуэн Пан 2 , Донг-И Линь 1
Принадлежности
- 1 Факультет химии и материаловедения, Национальный университет Гаосюн, город Гаосюн 811, Тайвань.
- 2 Офис генерального директора, ThinTech Materials Technology Co., LTD., город Гаосюн 811, Тайвань.
- PMID: 33652951
- PMCID: ПМС7956762
- DOI: 10.3390/ma14051104
Бесплатная статья ЧВК
Шэн-Мин Ян и др. Материалы (Базель). .
Бесплатная статья ЧВК
. 2021 26 февраля; 14 (5): 1104.
дои: 10. 3390/ma14051104.
Авторы
Шэн-Мин Ян 1 , Цзин-Лин Ву 1 , Ён-Цуэн Пан 2 , Донг-И Линь 1
Принадлежности
- 1 Факультет химии и материаловедения, Национальный университет Гаосюн, город Гаосюн 811, Тайвань.
- 2 Офис генерального директора, ThinTech Materials Technology Co., LTD., город Гаосюн 811, Тайвань.
- PMID: 33652951
- PMCID: PMC7956762
- DOI:
10.
3390/ma14051104
Абстрактный
В этом исследовании для исследования влияния содержания Nb на термические характеристики и поведение при осаждении использовались образцы из жаропрочной стали 22Cr25NiWCuCo(Nb) с высоким содержанием Cr и Ni. Профили дифференциальной сканирующей калориметрии показали, что температура плавления образцов стали 22Cr25NiWCuCo(Nb) несколько снижается с увеличением содержания Nb. После термообработки при 1200 °С в течение 2 ч осадки растворялись в стальной матрице, не содержащей ниобия. Кроме того, в образцах Nb-содержащих сталей можно было наблюдать Z-фазу (CrNb(C, N)) и MX (Nb(C, N), (Cr, Fe)(C, N) и NbC). Количество и объемная доля выделений увеличивались с увеличением содержания Nb, причем выделения распределялись неоднородно по границе зерна и внутри зерна. Даже при увеличении продолжительности термообработки до 6 ч размер аустенитного зерна и выделения становились более крупными; объемная доля выделений также увеличивалась при 1200 °С. Z-фаза, а не MX-фаза, стала доминирующим выделением при этой температуре.
Ключевые слова: МХ; Nb-допинг; фаза Z; жаропрочная сталь; осадки.
Заявление о конфликте интересов
Авторы заявляют об отсутствии конфликта интересов.
Цифры
Рисунок 1
Оптическая микроструктура и морфология осадка…
Рисунок 1
Оптическая микроструктура и морфология выделений образцов из стали 22Cr25NiWCuCo(Nb) после термической обработки при…
фигура 1 Оптическая микроструктура и морфология выделений образцов из стали 22Cr25NiWCuCo(Nb) после термообработки при 1200 °С в течение 2 ч: ( a ) без Nb, ( b ) Nb-0,3, ( c ) Nb-0,6 , и ( d ) Образцы из стали Нб-0,9.
Рисунок 2
ТЭМ – высокоугловое кольцеобразное наблюдение в темном поле и…
Рисунок 2
ПЭМ – высокоугловое кольцевое темное наблюдение и анализ образцов стали 22Cr25NiWCuCo(Nb) после обработки на твердый раствор…
фигура 2ПЭМ – высокоугловое кольцевое темнопольное наблюдение и анализ образцов стали 22Cr25NiWCuCo(Nb) после обработки на твердый раствор при 1200 °С в течение 2 ч: ( a ) Nb-0,3, ( b ) Nb-0,6 и ( c ) Образцы из стали Nb-0,9.
Рисунок 3
Профили ДСК из 22Cr25NiWCuCo(Nb)…
Рисунок 3
Профили ДСК образцов стали 22Cr25NiWCuCo(Nb), полученные в результате термического анализа: ( a…
Рисунок 3 Профили ДСК образцов стали 22Cr25NiWCuCo(Nb), полученные в результате термического анализа: ( a ) без Nb, ( b ) Nb-0,3, ( c ) Nb-0,6 и ( d ) Nb стальные образцы -0,9.
Рисунок 4
Микроструктура и морфология осадка…
Рисунок 4
Микроструктура и морфология выделений образцов из стали 22Cr25NiWCuCo(Nb) после термической обработки при…
Рисунок 4Микроструктура и морфология выделений образцов из стали 22Cr25NiWCuCo(Nb) после термообработки при 1200 °С в течение 6 ч: ( а ) Nb-0,3, ( б ) Nb-0,6 и ( c ) образцы из стали Nb-0,9. (Отмеченные точки 1–9 — анализ химического состава, соответствующий таблице 3.)
Рисунок 5
Средний размер зерна по…
Рисунок 5
Средний размер зерна в зависимости от содержания Nb в стали 22Cr25NiWCuCo(Nb)…
Рисунок 5 Зависимость среднего размера зерна от содержания Nb в образцах из стали 22Cr25NiWCuCo(Nb) после термообработки при 1200 °С в течение 2 и 6 ч.
Рисунок 6
Средний размер частиц осадков…
Рисунок 6
Средний размер частиц выделений в образцах стали 22Cr25NiWCuCo(Nb) с различным Nb…
Рисунок 6Средний размер частиц выделений в образцах из стали 22Cr25NiWCuCo(Nb) с различным содержанием Nb после термообработки при 1200 °С в течение 2 и 6 ч.
Рисунок 7
Объемная доля осадков в…
Рисунок 7
Объемная доля выделений в образцах из стали 22Cr25NiWCuCo(Nb) с различным содержанием Nb…
Рисунок 7 Объемная доля выделений в образцах из стали 22Cr25NiWCuCo(Nb) с различным содержанием Nb после термообработки при 1200 °С в течение 2 и 6 ч.
Рисунок 8
Гистограммы размера преципитата в…
Рисунок 8
Гистограммы размеров выделений в образцах стали 22Cr25NiWCuCo(Nb) с различным содержанием Nb…
Рисунок 8Гистограммы размеров выделений в образцах стали 22Х25NiWCuCo(Nb) с различным содержанием Nb после термообработки при 1200 °С в течение 2 ч: ( а ) Nb-0,3, ( б ) Nb-0,6 и ( в) ) Образцы из стали Nb-0,9.
Рисунок 9
Гистограммы размера преципитата в…
Рисунок 9
Гистограммы размеров выделений в образцах из стали 22Cr25NiWCuCo(Nb) с различным содержанием Nb после…
Рисунок 9 Гистограммы размеров выделений в образцах стали 22Cr25NiWCuCo(Nb) с различным содержанием Nb после термообработки при 1200 °С в течение 6 ч: ( и ) Nb-0,3, ( б ) Nb-0,6 и ( в ) ) Образцы из стали Нб-0,9.
См. это изображение и информацию об авторских правах в PMC
.Похожие статьи
Влияние размера зерна на горячую пластичность аустенитной нержавеющей стали с высоким содержанием азота в присутствии осадков.
Ван З., Ван И., Ван С. Ван Цзи и др. Материалы (Базель). 2018 15 июня; 11 (6): 1026. дои: 10.3390/ma11061026. Материалы (Базель). 2018. PMID: 291 Бесплатная статья ЧВК.
Поведение при рекристаллизации полностью аустенитной нержавеющей стали, стабилизированной ниобием.
Барчеллини К., Дамбилл С., Хименес-Мелеро Э. Барчеллини С. и др. Дж Микроск. 2019 апр; 274(1):3-12. дои: 10.1111/jmi.12776. Epub 2018 17 декабря. Дж Микроск. 2019. PMID: 30561019
Эволюция выделений в аустенитной жаропрочной стали HR3C при ползучести при 700 и 750 °С.
Сюй Л., Хе Ю., Кан Ю., Юнг Д.С., Шин К. Сюй Л. и др. Материалы (Базель). 2022 5 июля; 15 (13): 4704. дои: 10.3390/ma15134704. Материалы (Базель). 2022. PMID: 35806827 Бесплатная статья ЧВК.
Влияние эксплуатации на микроструктуру и механические свойства жаропрочной аустенитной нержавеющей стали HR3C.
Голанский Г., Зелинский А., Срока М., Сланя Ю. Голанский Г. и соавт. Материалы (Базель). 2020 13 марта; 13 (6): 1297. doi: 10.3390/ma13061297. Материалы (Базель). 2020. PMID: 32183009 Бесплатная статья ЧВК.
Прогресс в исследованиях аустенитных нержавеющих сталей, образующих оксид алюминия: обзор.
Лю Л., Фань С., Сун Х., Чен Ф., Го Дж., Хуан Т. Лю Л. и др. Материалы (Базель).
2022 13 мая; 15 (10): 3515. дои: 10.3390/ma15103515. Материалы (Базель). 2022. PMID: 35629544 Бесплатная статья ЧВК. Обзор.
Посмотреть все похожие статьи
использованная литература
- Суо Дж., Пэн З., Ян Х., Чай Г., Ю М. Формирование жидкой фазы в аустенитной стали Sanicro 25 во время испытания на ползучесть при 700 °C. Металлогр. Микроструктура. Анальный. 2019; 8: 281–286. doi: 10.1007/s13632-019-00529-0. – DOI
- Мазиас П. Дж. Разработка жаростойких и устойчивых к окислению аустенитных нержавеющих сталей для высокотемпературных применений. ДЖОМ. 2018;70:66–75.
doi: 10.1007/s11837-017-2642-x. – DOI
- Мазиас П. Дж. Разработка жаростойких и устойчивых к окислению аустенитных нержавеющих сталей для высокотемпературных применений. ДЖОМ. 2018;70:66–75.
- Зелинский А., Дудзяк Т.П., Голанский Г., Газдович Ю., Колодзей А. Влияние длительного старения при высоких температурах на развитие оксидной окалины и эволюцию микроструктуры аустенитных сталей. Сталь Рез. Междунар. 2020;91:15. doi: 10.1002/srin.2015. – DOI
- Семпура Г., Гил А., Агуэро А., Гутьеррес М., Крук А., Чирска-Филемонович А. Микроструктурные исследования отложений на Sanicro 25 после 25 000 часов окисления в паре с использованием передовых методов электронной микроскопии.
- Семпура Г., Гил А., Агуэро А., Гутьеррес М., Крук А., Чирска-Филемонович А. Микроструктурные исследования отложений на Sanicro 25 после 25 000 часов окисления в паре с использованием передовых методов электронной микроскопии.