Термообработка инструментальных сталей: Инструментальные стали и сплавы :: Технология металлов
alexxlab | 19.01.2023 | 0 | Разное
Глава V термическая обработка инструментальных сталей
Инструментальные стали по назначению подразделяются на три группы: стали для режущего инструмента, стали для измерительного инструмента и стали для штампов и пресс-форм.
Стали для режущего инструмента (резцов, сверл, метчиков, фрез и др.) должны обладать высокой твердостью, износостойкостью и теплостойкостью.
Режущий инструмент изготовляют из углеродистых, легированных и быстрорежущих сталей.
Углеродистые
стали маркируются буквой У (углеродистая) и
цифрами, показывающими среднее содержание
углерода в десятых долях процента. Буква
А, стоящая за цифрами, указывает, что
сталь высококачественная, содержащая
серы и фосфора не более 0,025%. Углеродистые
инструментальные стали подразделяются
на марки: У7, У8, У9, У10, У11, У12, У13. Для
улучшения обрабатываемости эти стали
отжигают на зернистый перлит при
температуре несколько выше точки Ас3 т.
Структура сталей У7 – У9 в закаленном состоянии состоит из мартенсита, сталей У10А – У13А – из мартенсита и избыточных карбидов.
Для уменьшения коробления углеродистые стали подвергают ступенчатой закалке. Отпускают инструмент из углеродистых сталей при разных температурах в зависимости от назначения и требуемой твердости.
Сталь
У7 применяется для изготовления
инструментов, подвергающихся ударам и
требующих повышенной вязкости при
умеренной твердости (зубила, кузнечные
штампы, клейма). Температура отпуска
250 – 325 °С, твердость HRC 48 – 55.
Легированные стали по сравнению с углеродистыми имеют следующие преимущества: большую прокаливаемость, меньший рост зерна при нагреве под закалку, возможность применения при закалке масла и горячих сред. Критический диаметр достигает40 – 80 мм.
Меньшая
скорость охлаждения при закалке уменьшает
опасность образования трещин, деформации
и коробления. Химический состав некоторых
легированных сталей, применяемых для
изготовления режущих инструментов,
приведен в табл.
Сталь X применяют для изготовления токарных, строгальных и долбежных резцов. Прокаливается в сечении до 25 мм. Сталь 9ХС применяют для изготовления сверл, фрез, метчиков, плашек, разверток. Прокаливается в сечении до 35 мм. Сталь 13Х применяется для изготовления мелких инструментов, бритвенных ножей, лезвий, острых хирургических инструментов, шаберов, гравировальных инструментов. Критический диаметр при закалке в масле 10 – 15 мм. Сталь 11ХФ применяется для изготовления метчиков и других режущих инструментов диаметром до 30 мм. Сталь 9ХФ применяется для изготовления пил, ножей, кернеров, пуансонов для холодной обрезки заусенцев. Сталь ХВГ применяется для изготовления плашек, клейм, разверток.
0,2 0,4 0,6 0,8 1,0 1,2 1,4 С,%
Рис 5.1. Температура закалки углеродистых сталей
Таблица
5. 1.
Химический состав некоторых легированных сталей для режущих инструментов (ГОСТ 5950 – 73), %
Марка стали | Элементы | ||||
С | Mn | Si | Cr | W – V | |
Х 9ХС 13Х 11ХФ 9ХФ ХВГ ХВСГ | 0,85 – 0,95 1,25 – 1,40 1,05– 1,15 0,80 – 0,90 0,90 – 1,05 0,95 – 1,05 | 0,30 – 0,60 0,30 – 0,60 0,40 – 0,70 0,30 – 0,60 0,80 – 1,10 0,60 – 0,90 | 1,20 –1,60 <0,35 <0,35 <0,35 <0,35 0,65 – 1,10 | 0,95 – 1,25 0,40 – 0,70 0,40 – 0,70 0,40 – 0,70 0,90 – 1,20 0,60 – 1,10 | ВЗЯТЬ С ГОСТА |
Таблица
5. 2.
Режимы термической обработки инструментальных легированных сталей
Марка стали | Отжиг | Закалка | Отпуск | |||||
Т, °С | НВ, не более | Т, °С | Среда охлаждения | HRC | Т, °С | HRC | ||
Х 9ХС 13Х 11ХФ 9ХФ ХВГ ХВСГ | 790 – 810 750 – 790 750 –790 760 – 790 780 – 800 790 – 810 | 241 241 229 255 255241 | 840 – 860 810 – 830 840 – 860 850 – 880 830 – 850 840 – 860 | Масло Масло Масло Масло Масло Масло | 62 – 63 62 – 64 62 – 64 61 – 64 62 – 63 62 – 63 | 180 – 250 150 – 170 150 – 170 200 – 2150 150 – 200 | 58 – 62 62 – 65 62 – 65 58 – 60 60 – 62 60 – 62 |
Таблица
5. 3.
Химический состав (%) и теплостойкость быстрорежущих сталей (ГОСТ 19265 – 73)
Марка стали | Элементы | ||||||
C | Cr | W | V | Mo | Co | Теплостойкость | |
Р18 Р9 Р6М5 Р14Ф4 Р10К5Ф5 | 0,7 – 0,8 0,85–0,95 0,80–0,88 1,20-1,30 1,45-1,55 | 3,8-4,4 3,5-4,4 3,8-4,4 4,0-4,6 4,0-4,6 | 17,0-18,5 8,5-10,0 5,5-6,5 13,0-14,5 10,0-11,5 | 1,0-1,4 2,0-2,6 3,4-4,1 4,3-5,1 | 1,0 1,0 5,0-5,5 1,0 1,0 | – – – – 5,0-6,0 | 620 620 620 630 640 |
Рис. 5.2. Схема режимов термической обработки
инструментов из быстрорежущей стали:
а) – без обработки холодом, б) – с
обработкой холодом.
изготовления протяжек, длинных метчиков, разверток и других изделий. Сталь ХВСГ применяется для изготовления плашек, клейм, разверток.
Легированные инструментальные стали, так же как и углеродистые, не обладают теплостойкостью, и инструменты, изготовленные из них, могут быть использованы только для резания с небольшой скоростью.
Быстрорежущие стали обозначают буквой Р (рапид – скорость), цифры после этой буквы указывают содержание основного легирующего элемента – вольфрама в процентах.
Дополнительное легирование быстрорежущих сталей молибденом, кобальтом, ванадием обозначается в марке буквами М, К, Ф и цифрами, показывающими их количество.
Содержание ванадия (до 2%) и хрома (примерно 4% во всех сталях) в марке не указывается.
Быстрорежущие
стали предназначены для изготовления
высокопроизводительного режущего
инструмента, работающего при высоких
скоростях резания. Имеют высокую
теплостойкость (красностойкость) (до
620 – 640 °С) и износостойкость.
Теплостойкость (сохранение высокой твердости при нагреве до температуры 500 – 620 °С) достигается легированием стали карбидообразующими элементами (вольфрамом, молибденом, хромом, ванадием).
В литом состоянии в быстрорежущей стали имеются три типа карбидов: первичные (ледебуритная эвтектика), вторичные, выделившиеся при охлаждении из аустенита, и эвтектоидные в результате перлитного превращения, т. е. распада аустенита на легированный феррит и мелкие (эвтектоидные) карбиды.
Для разрушения эвтектики на отдельные карбиды и устранения хрупкости литую быстрорежущую сталь подвергают горячей обработке (ковке, прокатке) и отжигу при температуре 830 – 850 °С. Твердость после отжига 207 – 255 НВ.
При закалке быстрорежущие стали нагреваются до высоких температур (значительно выше Ас3), что обеспечивает получение высоколегированного аустенита, который при закалке превращается в мартенсит с тем же содержанием легирующих элементов,
Закалка
осуществляется таким образом: медленный
нагрев до 800 – 850 °С, выдержка при этой
температуре (для выравнивания температуры
по сечению), быстрый нагрев до температуры
закалки, кратковременная выдержка и
охлаждение в масле.
Структура после закалки: мартенсит + карбиды + остаточный аустенит, количество которого весьма значительно – до 30%, так как при столь высоких температурах нагрева его устойчивость растет. Твердость после закалки HRC ~ 62.
После закалки быстрорежущую сталь подвергают отпуску при температуре 560 – 580 °С. При этом происходит превращение остаточного аустенита в мартенсит и выделение из мартенсита мелкодисперсных карбидов ванадия и вольфрама. Твердость быстрорежущей стали повышается до HRC ~ 64.
Для наиболее полного превращения аустенита в мартенсит дается двух-трехкратный отпуск по 1 ч (рис. 5.2, а)
Микроструктура быстрорежущей стали после закалки и отпуска показана на рис. 5.3.
Температура
конца превращения аустенита в мартенсит
(Мк)
быстрорежущей стали ниже нуля. Поэтому
для более полного превращения аустенита
в мартенсит сталь можно обрабатывать
холодом при температуре 198 – 193 К (от –75
до – 80 °С) (рис. 5.2, б).
Применение
обработки холодом сокращает длительность
цикла термической обработки.
В плохо отожженной быстрорежущей стали после закалки при нормальной твердости и нормальном количестве остаточного аустенита наблюдается грубозернистый чешуйчатый излом, напоминающий по виду нафталин. Сталь оказывается очень хрупкой. Этот вид брака называется нафталиновым изломом.
При недостаточной проковке наблюдается карбидная ликвация, что увеличивает хрупкость стали и понижает стойкость инструмента.
Для
улучшения режущих свойств некоторые
инструменты дополнительно обрабатывают
в жидких цианистых солях при температуре
520 – 580 °С. На поверхности быстрорежущей
стали образуется цианированный тонкий
слой 0,02 – 0,07 мм, имеющий высокую твердость
(1000 – 1100 НV)
и повышенную теплостойкость ~ 650 °С.
Иногда после шлифования и заточки
инструмента из быстрорежущей стали для
повышения режущих свойств, антикоррозионной
стойкости и улучшение товарного вида
применяется обработка паром при
температуре отпуска 550 – 570 °С. При такой
обработке в результате реакции железа
с паром на поверхности образуется пленка
окиси железа Fe3O4 темно-синего цвета, имеющая большую
прочность сцепления с металлом. Эффект
повышения стойкости инструмента при
этом объясняется добавочным отпуском
и снятием
напряжений, возникших при заточке и шлифовании.
Особенности технологии термической обработки инструментальных сталей в вакуумных электропечах торговой марки
Вы можете скачать(открыть) полный текст статьи в PDF-версии
В.М. Шулаев, к.ф.-м.н., В. Ю. Жорняк, Д.А. Листопад, к.т.н.
Неукоснительное и точное соблюдение всех параметров термообработки способствует высокому качеству стального инструмента. Поэтому для закалки наилучшим образом подходят вакуумные электропечи благодаря их автоматизации и системе контроля.
Вакуумная термическая обработка является современной альтернативой классической технологии термической обработки инструмента в соляных ваннах по ряду причин. Отпадает необходимость в проведении трудоемкой операции очистки поверхности от остатков солей и последующей подготовки к нанесению упрочняющих покрытий типа нитрида титана. Повышенная скорость нагрева изделий в смеси солей приводит к возникновению максимального градиента температур между поверхностью и сердцевиной, что определяет высокий уровень термических напряжений и, как следствие, деформацию инструмента. Большая скорость нагрева обуславливает также разнозернистость микроструктуры при аустенизации и последующей закалке. При термообработке изделий в смеси солей происходит частичное обезуглероживание и потеря легирующих элементов в поверхностном слое. В вакуумных электропечах эти явления можно практически полностью исключить. Возможность полного контроля процесса и точность поддержания режимов термообработки — одна из важнейших причин популярности вакуумных электропечей при термической обработке инструментальных сталей.
Каждый специалист, связанный с термообработкой инструментальных сталей, должен помнить о возможностях оптимизации этого процесса. При этом обязательно использовать наиболее подходящие режимы нагрева, аустенизации, закалки и отпуска. И в соответствии с этим осуществлять правильный выбор оборудования.
НАГРЕВ
Процесс термообработки инструментальных сталей в вакуумных печах начинается с многоступенчатого нагрева. Для инструмента из низколегированной стали рекомендуется двухступенчатый нагрев, для быстрорежущего инструмента — трехступенчатый, а для крупногабаритного инструмента или инструмента переменного поперечного сечения — четырехступенчатый.
Медленный прогрев с необходимым количеством ступенек дает определенные преимущества. Большая часть инструментальных сталей чувствительна к тепловым ударам из-за низкой теплопроводности. Уменьшение термических градиентов снижает склонность сталей к растрескиванию. Для большинства инструментальных сталей следует подбирать температуру предварительного разогрева, чуть ниже критической температуры превращения материала (Ас1), и выдерживать по времени столько, чтобы по всему поперечному сечению достигалась однородность температуры. Нагрев инструмента с выдержкой над критической температурой обеспечивает однородные изменения в объеме материала, что уменьшает его деформацию.
Первую ступень подогрева для инструмента из низколегированной стали рекомендуется проводить при 600°С, а для инструмента из быстрорежущей стали — при 850°С. Тепло распространяется от поверхности к сердцевине, и за счет этого температура поверхности инструмента удерживается ниже температуры нагревателей до полного прогрева сердцевины инструмента. При этом длительность выдержки должна обеспечивать выравнивание температуры сердцевины и поверхности инструмента, а также нагревателей. Время выдержки при первом подогреве в 2 раза превышает время выдержки при аустенизации. Первый подогрев инструмента из быстрорежущей стали до 850°С и последующая выдержка при этой температуре осуществляется с целью уменьшения напряжений и сокращения времени нагрева при высоких температурах.
Вторую ступень нагрева при 1050°С для инструмента из быстрорежущей стали необходимо использовать в следующих случаях:
- для плотноупакованной садки из изделий малых размеров;
- для термической обработки изделий с поперечным сечением более 20 мм.
Второй подогрев позволяет сократить время выдержки при окончательном нагреве.
Кроме того, инструментальные стали претерпевают объемные изменения при переходе от отожженной микроструктуры (в состоянии поставки) к аустениту в ходе разогрева. При нагреве в соляных ваннах возникают неоднородные объемные превращения, возможны неконтролируемые деформации, особенно в случае деталей переменного поперечного сечения. При нагреве в вакуумных электропечах подобного явления можно избежать. Крупногабаритный инструмент переменного поперечного сечения в этом случае дополнительно подогревают при температуре 400–500°С.
АУСТЕНИЗАЦИЯ
Цель аустенизации — обеспечение полного или частичного растворения карбидных частиц с последующей диффузией легирующих элементов в железной матрице. Разные типы карбидов растворяются с разной скоростью, в зависимости от температуры. Таким образом, подбор температуры аустенизации определяется, главным образом, составом инструментальной стали. Кроме того, температура аустенизации может слегка варьироваться для получения необходимых механических свойств инструмента с учетом конкретных применений.
Условия аустенизации в вакуумной печи также отличаются от условий аустенизации в соляной ванне. Установлено, что медленный нагрев в вакуумных печах создает благоприятные условия для более полного растворения первичных карбидов и получения высоколегированного аустенита.
Например, верхний предел закалочных температур при этом можно понизить на 20–30°С и на 15–20% уменьшить разнозернистость в микроструктуре быстрорежущей стали по сравнению с нагревом в соляной ванне.
ЗАКАЛКА
При достижении необходимого перераспределения легирующих элементов в ходе аустенизации инструментальную сталь следует достаточно быстро охлаждать для обеспечения мартенситного превращения. Большинство инструментальных сталей, как правило, приобретают мартенситную структуру в температурном интервале 315–95°С. Скорость охлаждения инструментальной стали в каждой конкретной охлаждающей среде (вакуум, газ — азот, закалочное масло) для полного упрочнения определяется ее химическим составом. Сильно легированные инструментальные стали достигают предельной прочности при небольших скоростях охлаждения. Как правило, небольшие скорости охлаждения обеспечивают оптимизированную микроструктуру и твердость инструмента при минимальных искажениях и склонности к растрескиванию. В случае сильнолегированных инструментальных сталей, полученных при температурах более 1095°С, скорость охлаждения с 980 до 650°С критична для оптимизации термообработки и вязкости материала.
Независимо от способа охлаждения инструментальных сталей, конечная мартенситная структура чрезвычайно хрупка и напряжена. Сталь может содержать нерастворенные избыточные карбиды и остаточный аустенит в заметных количествах. Присутствие в структуре инструментальной стали остаточного аустенита нежелательно, так как он ухудшает механические свойства и нарушает стабильность геометрических размеров инструмента. Использование инструментальной стали в таком состоянии создает существенный риск порчи инструмента. Поэтому сразу же после окончания охлаждения инструментальных сталей каким-либо способом до температуры последующей обработки (65°С) следует проводить «немедленный отпуск», как правило, не позднее чем через 15–30 минут.
ОТПУСК
После закалки проводится отпуск как для снятия напряжений в хрупком мартенсите, образующемся в ходе закалки, так и для уменьшения содержания остаточного аустенита. Большинство инструментальных сталей имеют достаточно широкую область температур отпуска. Рекомендуется использовать наивысшую температуру отпуска, которая обеспечивает необходимую твердость инструмента. Скорость нагрева и охлаждения от температуры отпуска обычно не критичны. Материалу следует дать остыть до 65°С и часто окончательно до комнатной температуры между и после отпусков.
Существует хорошее эмпирическое правило — одночасовая выдержка на каждые 2,5 см самого большого поперечного сечения после того, как инструмент полностью достигнет необходимой температуры, но не менее двух часов, независимо от размера.
Многократный отпуск типичен для многих сложнолегированных инструментальных сталей. Они требуют двух- и даже трехкратного отпуска для полного перехода остаточного аустенита в мартенсит, а также максимального снятия внутренних напряжений, возникших при закалке. Эти стали достигают максимальной твердости уже после первого отпуска и именуются вторично-упрочняемыми сталями. Однако однократный отпуск не обеспечивает эффективного превращения всего остаточного аустенит в мартенсит. Цель второго или третьего отпуска — интенсификация этого превращения, а также понижение твердости до необходимого рабочего уровня.
ОБОРУДОВАНИЕ ДЛЯ ВАКУУМНОЙ ТЕРМООБРАБОТКИ ИНСТРУМЕНТА
Исходя из вышеизложенного очевидно, что вакуумные электропечи категорически необходимы для решения задач высококачественной термической обработки инструмента. Правда, процесс термообработки всегда связан с неконтролируемым возникновением деформаций. Они могут быть больше или меньше за счет изменений микроструктуры инструмента, но они всегда присутствуют. Однако при термообработке в вакуумных электропечах деформация инструмента существенно меньше, чем при термообработке в соляных ваннах. Вклад в деформацию инструмента вносят многие факторы: высокое содержание легирующих элементов в инструментальной стали, слишком высокая скорость нагрева инструмента, продолжительная изотермическая выдержка, неоптимальная температура аустенизации, неудачный выбор условий закалки и другие.
В первую очередь для обеспечения требуемых свойств изделий при термической обработке в вакуумных печах необходимо правильно выбрать условия охлаждения. Длительное время наиболее распространенными способами закалки в вакуумных печах были: охлаждение в масле и охлаждение газом — азотом при давлениях меньше 0,17 МПа. Для сильнолегированных сталей используется также охлаждение в вакууме. Эти способы охлаждения продолжают эффективно использовать и в настоящее время. Для обеспечения полной прокаливаемости инструмента большого сечения в настоящее время используются вакуумные печи с давлением инертного газа от 0,17 МПа до 2,0 МПа и еще больших давлениях (вакуум- компрессионные электропечи). Для ускоренного нагрева садки при температурах ниже 800°С в вакуумных печах последнего поколения используют конвекционную передачу тепла за счет циркуляции газа — азота от нагревательного модуля к садке. Данное техническое решение позволило заметно сократить время цикла термической обработки садки.
Охлаждению при непрерывной закалке в масле подвергаются инструменты простой формы толщиной или диаметром 30–40 мм из низко- и среднелегированных сталей. Для термообработки инструмента с закалкой в масло и «немедленного отпуска» в одном цикле нами предлагается новая вакуумная электропечь модели СЭВФ 3.3/11,5 ИЗМ-ОТТОМ (фото 1). В этой печи садка вначале нагревается в вакууме до температуры закалки. После изотермической выдержки при заданной температуре садка погружается в закалочную среду (вакуумное масло (ВМ 3) или Нетоксол). После этого садка извлекается из закалочной среды в зону загрузки (среднюю зону). Выдержка садки после закалки обеспечивает стекание остатков закалочной жидкости и понижение температуры нагревательного модуля до температуры отпуска, в течение времени исключающем закалочное растрескивание. После этого садка поднимается обратно в нагревательный модуль (при температуре отпуска). Нагревается и выдерживается при заданной температуре. Охлаждение садки после отпуска можно производить в закалочной среде или в вакууме вместе с печью.
Печь СЭВФ 3.3/11,5 ИЗМ-ОТТОМ является экологически чистой. В ней отсутствует выброс химически активных газов в атмосферу помещения, что обеспечивает ее взрыво и пожаробезопасность в процессе эксплуатации. Печь может применяться как общепромышленная в авиационной, электронной, радиотехнической, электротехнической, машиностроительной и других отраслях промышленности.
Таким образом, промышленным предприятиям для проведения закалки в масло и «немедленного отпуска» инструмента из низко- и среднелегированных сталей в одном производственном цикле, с промежуточным циклом вакуумного обезжиривания, предлагается вакуумная электропечь сопротивления нового поколения модели СЭВФ 3.3/11,5 ИЗМ-ОТТОМ, которая относится к современному высокотехнологичному термическому оборудованию. Детали из такой печи вынимают светлыми и сухими.
Для нагрева и охлаждения в вакууме мелкоразмерного инструмента из высоколегированных сталей предлагается новая вакуумная электропечь модели СЭВЭ 3.3/13 ИВ ОТТОМ (фото 2). Конструкция печи допускает использование систем ускоренного охлаждения на базе статических атмосфер газа — азота или аргона.
Вакуумная элеваторная электропечь сопротивления модели СЭВГ 3.3/13 ИЗГ-ОТТОМ (фото 3) предназначена для закалки мелкого инструмента (диаметром или толщиной менее 100 мм) из различных марок быстрорежущих (Р18, Р9, Р6 М5, Р6 М5 Ф3, Р5 М5 К5 и др.) и высоколегированных сталей в потоке охлаждающего газа (азот или аргон) при давлениях меньше 0,17 МПа.
В зоне ускоренного охлаждения располагается газовый спрейер. К зоне ускоренного охлаждения пристыковывается наружная система циркуляции газа (фото 3), которая оборудована теплообменниками для понижения температуры охлаждающего газа и мощной газодувкой.
ЗАКЛЮЧЕНИЕ
К настоящему времени разработка новых инструментальных материалов с более высоким уровнем физико-механических свойств путем использования постоянно уссложняющихся составов оказался исчерпанным. Поэтому повышение служебных характеристик инструмента возможно благодаря разработке новых технологий:
- производства инструментальных материалов традиционного состава;
- нанесения упрочняющих покрытий;
- объемного упрочнения с помощью термической обработки, которое неразрывно связано с использованием новейшего вакуумного печного оборудования.
Термическая обработка инструментальных сталей
Инструментальная сталь относится к различным углеродистым и легированным сталям, которые особенно хорошо подходят для изготовления инструментов. Их пригодность обусловлена их особой твердостью, стойкостью к истиранию, способностью удерживать режущую кромку и/или устойчивостью к деформации при повышенных температурах (красная твердость). Инструментальная сталь обычно используется в термически обработанном состоянии.
Схематическое дерево группировки металлов
Инструментальные стали с содержанием углерода от 0,7% до 1,5% производятся в тщательно контролируемых условиях для обеспечения требуемого качества. Содержание марганца часто поддерживается на низком уровне, чтобы свести к минимуму возможность растрескивания при закалке водой. Тем не менее, правильная термическая обработка этих сталей важна для адекватной производительности, и есть много поставщиков, которые поставляют инструментальные заготовки, предназначенные для закалки в масле.
Инструментальные стали изготавливаются нескольких марок для различных применений. Выбор сплава зависит, среди прочего, от того, требуется ли острая режущая кромка, как в штампах, или от того, должен ли инструмент выдерживать ударную нагрузку и условия эксплуатации, характерные для таких ручных инструментов, как топоры, кирки и инструменты для добычи полезных ископаемых. В общем, температура края при предполагаемом использовании является важным фактором, определяющим как состав, так и требуемую термическую обработку. Марки с более высоким содержанием углерода обычно используются для таких применений, как штампы для штамповки, металлорежущие инструменты и т. д.
Инструментальная сталь обычно поставляется в отожженном состоянии, около 200/250 по Бринеллю (около 20 HRC), для облегчения механической обработки. В этом состоянии большая часть содержания сплава существует в виде карбидов сплава, рассеянных по мягкой матрице. Эти стали должны быть подвергнуты термообработке, чтобы развить их характерные свойства. Процесс термической обработки изменяет распределение сплава и превращает мягкую матрицу в твердую матрицу, способную выдерживать давление, истирание и удары, присущие формовке металла. Каждый этап цикла термообработки предназначен для выполнения определенной функции, и, подобно звеньям в цепи, конечный продукт хорош настолько, насколько хорош его самый слабый компонент. Хотя это может составлять только 10% или меньше стоимости инструмента, процесс термообработки, вероятно, является единственным наиболее важным фактором, определяющим производительность инструмента. При термообработке инструментальных сталей не существует такой вещи, как приемлемый короткий путь.
Предварительный нагрев
Предварительный нагрев или медленный нагрев инструментальных сталей обеспечивает два важных преимущества. Во-первых, большинство инструментальных сталей чувствительны к термическому удару. Внезапное повышение температуры до 1500/2000°F может привести к растрескиванию инструментальной стали. Во-вторых, инструментальные стали претерпевают изменение плотности или объема, когда они превращаются из исходной отожженной микроструктуры в высокотемпературную структуру аустенита.
Если это изменение объема происходит неравномерно, это может вызвать ненужную деформацию инструментов, особенно когда различия в сечении вызывают трансформацию некоторых частей инструмента до того, как другие части достигнут требуемой температуры. Инструментальные стали должны быть предварительно нагреты чуть ниже этой критической температуры превращения, а затем выдержаны достаточно долго, чтобы все поперечное сечение достигло однородной температуры. Эта проблема особенно очевидна, когда различия в геометрии или размере сечения могут привести к трансформации некоторых частей инструмента до того, как другие части достигнут заданной температуры.
Аустенитизация
Как правило, более высокие температуры позволяют диффундировать большему количеству сплава, что обеспечивает немного более высокую твердость и прочность. Время выдержки при температуре аустенизации обычно очень короткое – от одной до пяти минут после того, как инструмент достиг температуры. Полезное содержание сплава в большинстве инструментальных сталей существует в виде частиц карбида в отожженной стали. Это содержание сплава по меньшей мере частично диффундирует в матрицу при температуре закалки или аустенизации.
Инструментальная сталь
Фактическая используемая температура в основном зависит от химического состава стали. Высокие температуры позволяют диффундировать большему количеству сплава, обеспечивая немного более высокую твердость или прочность на сжатие. Используемое время выдержки зависит от температуры. Диффузия сплава происходит быстрее при более высоких температурах, и время выдержки соответственно уменьшается.
Инструментальная сталь Цвет в зависимости от температуры
Выбранная температура аустенизации сильно зависит от содержания легирующих элементов в стали. Целевые свойства, включая твердость, предел прочности при растяжении, размер зерна и т. д., также влияют на выбранную температуру. Более высокие температуры позволяют диффундировать большему количеству сплава, что обычно обеспечивает более высокую твердость. (Это верно до тех пор, пока температура не превышает начальную температуру плавления стали.) Если используются более низкие температуры аустенизации, то происходит меньшая диффузия сплава в матрицу.
Закалка
Скорость охлаждения инструментальной стали и тип закалочной среды для ее полного затвердевания зависит от химического состава. Высоколегированные инструментальные стали приобретают полностью закаленные свойства с более медленной скоростью закалки. Как бы инструментальные стали не закалялись, получаемая мартенситная структура чрезвычайно хрупкая и испытывает большие напряжения. Некоторые инструментальные стали в таких условиях самопроизвольно трескаются, даже если их не трогать при комнатной температуре. Скорость охлаждения стали для полного затвердевания зависит от химического состава. Как правило, низколегированные стали необходимо закаливать в масле для достаточно быстрого охлаждения. Более высокое содержание легирующих элементов позволяет стали приобретать полностью закаленные свойства с более низкой скоростью закалки. Стали с воздушной закалкой охлаждаются более равномерно, поэтому деформация и риск растрескивания меньше, чем у сталей с закалкой в масле.
Упрощенная фазовая диаграмма Fe-C
Независимо от способа закалки инструментальной стали образующаяся структура, мартенсит, становится чрезвычайно хрупкой и подвергается большим нагрузкам. При эксплуатации в таких условиях большинство инструментальных сталей разрушится. Некоторые инструментальные стали в таких условиях самопроизвольно трескаются, даже если их не трогать при комнатной температуре. Этот процесс называется закалкой. Как правило, низколегированные стали, такие как 01, должны быть закалены в масле, чтобы охладиться достаточно быстро. Стали с более высоким содержанием легирующих элементов могут приобретать полностью закаленные свойства за счет более медленного процесса закалки.
Отпуск
Отпуск проводится для снятия напряжения с хрупкого мартенсита, образовавшегося во время закалки. Большинство сталей имеют довольно широкий диапазон допустимых температур отпуска. Как правило, используйте самую высокую температуру отпуска, которая обеспечит необходимую твердость инструмента. Скорость нагрева до и охлаждения от температуры отпуска не имеет решающего значения. Материал должен полностью остыть до комнатной температуры (50/75°F) или ниже между и после отпуска. Большинство сталей имеют довольно широкий диапазон допустимых температур отпуска. В общем, используйте самую высокую температуру отпуска, которая обеспечит необходимую твердость инструмента.
Инструментальная сталь – зависимость твердости от температуры отпуска
Скорость нагрева до температуры отпуска и охлаждения после нее обычно не имеет решающего значения. Многократный отпуск является типичным, особенно для многих более сложных инструментальных сталей (например, серии M и серии H), требующих двойного или даже тройного отпуска для полного превращения остаточного аустенита в мартенсит. Эти стали достигают максимальной твердости после первого отпуска и называются сталями вторичной закалки. Целью второго или третьего отпуска является снижение твердости до желаемого рабочего уровня и обеспечение эффективного отпуска любого нового мартенсита, образовавшегося в результате превращения аустенита при отпуске. Отпуск проводится для размягчения мартенсита, образовавшегося во время закалки. . Выполняя второй отпуск, этот новый мартенсит размягчается, что снижает вероятность растрескивания.
Отжиг
Инструментальные стали обычно поставляются клиентам в отожженном состоянии с типичными значениями твердости около 200-250 по Бринеллю (» 20 HRC) для облегчения механической обработки и других операций. Это особенно важно для кованых инструментов и штампов, где происходит частичная или полная закалка на воздухе, что приводит к накоплению внутренних напряжений. Штампы и инструменты, которые могут нуждаться в повторной закалке, должны быть отожжены. Полный отжиг включает в себя медленный и равномерный нагрев стали до температуры выше верхней критической температуры (Ac3) и до аустенитного диапазона с последующей выдержкой до полной гомогенизации. Охлаждение после нагрева тщательно контролируется с определенной скоростью, рекомендованной производителем стали для используемой марки инструментальной стали. Охлаждение обычно продолжается примерно до 1000°F (540°C), после чего сталь можно вынуть из печи и охладить на воздухе до комнатной температуры.
Изменение размера
Процесс термообработки приводит к неизбежному увеличению размера инструментальных сталей из-за изменений в их микроструктуре. Рост большинства инструментальных сталей составляет примерно от 0,0005 до 0,002 дюйма на дюйм исходной длины во время термообработки. Это несколько варьируется в зависимости от ряда теоретических и практических факторов. Большинство термообработчиков понимают, чего ожидать от типичных процессов.
В некоторых случаях сочетание переменных факторов, включая высокое содержание сплава, длительное время аустенизации или высокую температуру, слишком раннее прекращение процесса закалки, недостаточное охлаждение между отпусками или другие факторы в процессе, может вызвать некоторые из высокотемпературных структура, аустенит, чтобы сохраниться при комнатной температуре. Другими словами, при нормальной закалке структура полностью не превращается в мартенситную.
Это состояние остаточного аустенита обычно сопровождается неожиданной усадкой в размере и иногда меньшей способностью удерживать магнит. Это состояние часто можно исправить, просто подвергая инструменты воздействию низких температур, например, при криогенной или холодильной обработке, чтобы стимулировать завершение превращения в мартенсит.
Глубокая заморозка
Для большинства инструментальных сталей наличие остаточного аустенита крайне нежелательно, поскольку его последующее превращение в мартенсит приводит к увеличению размера (объема), создавая внутреннее напряжение, и приводит к преждевременному выходу из строя. Путем глубокой заморозки до -120°F (-85°C) или, в некоторых случаях, криогенного охлаждения до -320°F (-195°С) трансформируется остаточный аустенит. Новообразованный мартенсит подобен исходной структуре после закалки и должен быть отпущен. Часто глубокая заморозка выполняется перед темперированием из-за опасений по поводу растрескивания, но иногда это делается между несколькими темперациями.
Остаточный аустенит может быть нежелательным по ряду причин. При охлаждении стали до криогенных (минусовых) температур этот остаточный аустенит может быть преобразован в мартенсит. Новообразованный мартенсит подобен исходной структуре после закалки и должен быть отпущен. Криогенные обработки должны включать закалку после замораживания.
Вам также может понравиться
Термическая обработка стали Термическая обработка – это группа промышленных… | Что из нержавеющей стали? Скульптура в стиле ар-деко из нержавеющей стали… | Аустенит (гамма-железо) Аустенит, также известный как гамма-фаза… | Экструзия Экструзия – это процесс, при котором… |
Термическая обработка инструментальных сталей Дэвид Пай
Термообработка инструментальных сталей в действительности очень похожа на обработку легированных сталей. Однако различие в методах обработки требует большой осторожности при выборе технологических методов с точки зрения однородности температуры процесса. Это критический вопрос с точки зрения обеспечения хорошей однородности температуры в технологической камере печи. Значительные колебания температуры в технологической камере, скорее всего, вызовут серьезные металлургические фазы внутри инструмента.
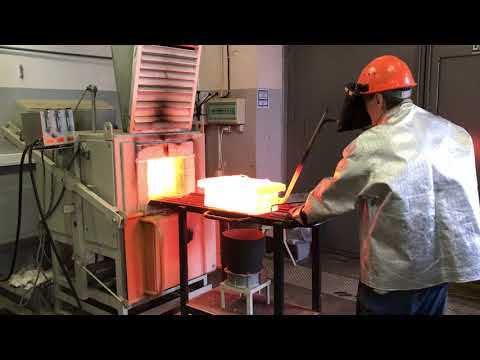
Теперь мы переходим к доступным методам для успешной термической обработки инструментальных сталей и полученной металлургии. Пожалуйста, не недооценивайте значение снятия напряжения на этапе производства инструментальной стали.
Термическая обработка в соляной ванне
Термическая обработка в солевой ванне является наименее дорогим методом термической обработки с точки зрения инвестиций в оборудование. Тем не менее, все еще следует учитывать предварительную и последующую очистку, особенно последнюю. Наконец, есть как хранение соли, так и утилизация сточных вод, которые необходимо учитывать и учитывать в стоимости переработки. Кроме того, необходимо (как и при всех методах термической обработки) предварительный нагрев для уменьшения теплового удара и поверхностной влаги на стали.
Также следует учитывать метод гашения и потенциальное загрязнение среды гашения. Существует также подготовка и проводка, чтобы иметь возможность поднимать и поддерживать работу в расплавленной соли и из нее. Соляные ванны обеспечивают защиту поверхности стали во время процесса от поверхностного обезуглероживания и поверхностного окисления (при условии, что анализ соляной ванны контролируется и поддерживается). Расплавленная соль также защищает рабочую поверхность с помощью кокон соли для снижения риска теплового удара Существует миф, что соляная ванна уменьшает искажения.
Это миф, принятый во всем мире. Применяется не только для термообработки соляных ванн; он также применяется для атмосферной и вакуумной термообработки. Деформация не обязательно возникает в результате термической обработки. Проявляется во время процедуры термической обработки, и предполагается, что это вызвано процедурой термической обработки. Это не обязательно верное предположение!! Необходимо разобраться во влиянии и причинах проявившегося искажения.
Каждый раз, когда сталь обрабатывается ковкой, прокаткой или механической обработкой, в стали возникают индуцированные поверхностные напряжения. Единственным эффективным способом получения индуцированного напряжения является применение тепла.
Таким образом, видно, что деформация вызвана не обязательно термообработкой, а агрессивностью, с которой она обрабатывается. Еще один миф заключается в том, что резкое точение уменьшает искажения из-за скорости резки. Чем быстрее вы режете, тем больше возникает трение и тем выше риск образования неотпущенного мартенсита на стальной поверхности. Неотпущенный мартенсит может привести к поверхностному растрескиванию.
Итак, в чем секрет уменьшения искажений?
Первое, что нужно понять, это то, что искажение невозможно устранить.
Что же делать?
- Меньше подача и скорость, медленнее сверление. Закалка после электроэрозионных операций. (Это будет обязательным для снижения риска растрескивания поверхности пресс-формы или штампа
- Промежуточное снятие напряжения является подходящим методом уменьшения деформации, но не устраняет ее.
Методы термической обработки инструментальных сталей в атмосфере и в псевдоожиженном слое
Атмосферная термообработка — это просто еще один метод защиты поверхности стали от поверхностного окисления и обезуглероживания.
Те же самые принципы, которые применяются как к термообработке в атмосфере, так и к термообработке в соляной ванне, применимы и к термообработке в псевдоожиженном слое.
Термическая обработка в кипящем слое основана на том же принципе, что и в кипящем слое, с той лишь разницей, что псевдоожиженный слой не увлажняет стальную поверхность.
Таким образом, сталь все равно будет окисляться и обезуглероживаться (очень незначительно) при извлечении из станины. Таким образом, изготовитель инструмента должен поддерживать связь с предприятием по термообработке.
Вакуумная термообработка.
Методы вакуумной термообработки становятся «рабочими лошадками» в термической промышленности.
Вакуумная печь используется в металлургической промышленности уже почти 75 лет. Они использовались до Первой мировой войны и, безусловно, использовались для большинства аспектов термической обработки.
Вакуумная печь находит применение в следующих процессах:
- Аустенитизация
- Решение
- Закалка
- Науглероживание
- Азотирование углеродом
- Азотирование
- Ферритная азотоцементация
- Тонкопленочные твердые покрытия
- Декоративное покрытие
- Пайка и многие другие термические процессы
Что особенного в вакуумной печи?
Вакуумная печь — это еще один источник тепла, вот и все. Принципы металлургического фазового превращения остаются неизменными независимо от типа печи. Существуют и другие важные преимущества вакуумной термообработки, которые показаны ниже. Вакуумная печь обычно представляет собой печь периодического действия. Процесс работает от холодного к горячему с возможностью введения задержек для выравнивания дисперсии поперечного сечения. Закалочная среда может представлять собой радиальное охлаждение на 360 градусов. Смесь закалочной среды может варьироваться в зависимости от обрабатываемой стали, а также от изменения давления. Скорость охлаждения также может быть изменена для работы с чувствительными сталями и переменными размерами поперечного сечения.
Предложен предварительный нагрев и выбор скорости охлаждения для соответствующих механических и металлургических свойств. На следующем рисунке показана классификация инструментальных сталей. Далее следует также помнить, что металлургия инструментальных сталей по-прежнему основана на металлургических принципах, которые обсуждались на первых курсах.