Термообработка твч: Технология термообработки ТВЧ
alexxlab | 26.02.2023 | 0 | Разное
Термическая обработка (ТВЧ и объемная закалка)
Термическая обработка металла представляет собой эффективный процесс, включающий в себя несколько операций нагрева, выдержи и охлаждения металлов и сплавов.
Термической обработке подвергают заготовки для получения требуемой твердости металла, улучшения его свойств и прочности.
На нашем термическом участке возможно проведение различных видов термической обработки.
Для чугунов СЧ, ВЧ, КЧ:
- графитизирующий отжиг,
- искусственное старение,
- нормализация,
- закалка,
- отпуск.
Для специальных чугунов ЧХ, ЧС, ЧЮ, ЧГ, ЧН:
- различная термообработка по ГОСТ 7769-82.
Размеры деталей и садки ограничены рабочим пространством печи 400 x 400 x 800 мм.
Для сталей конструкционных, некоторых видов специальных, нержавеющих сталей (мартенситного и аустенитного класса), стальных отливок:
- нормализация,
- отжиг,
- сфероидезирующий отжиг,
- улучшение,
- отпуск (высокий, средний, низкий),
- обезводораживание,
- поверхностная закалка с нагревом ТВЧ.
Размеры деталей и садки ограничены рабочим пространством печи 400 x 400 x 800 мм.
Для алюминиевых сплавов АЛ1, АЛ4, АЛ9, АЛ12, В93, В95, В96Ц, В300, АК4, АК5, АК6, АК7, АК8, Д16, Д19 и других:
- закалка,
- старение,
- отпуск (по режимам Т1, Т2, Т4, Т6, Т7).
Размеры деталей и садки ограничены рабочим пространством печи 800 x 800 x 1000 мм.
Стоимость термической обработки
Стоимость термической обработки методами объемной закалки и поверхностным нагревом ТВЧ рассчитывается индивидуально в каждом конкретном случае и зависит от веса и размеров изделия, типа обрабатываемого материала, формы и сложности детали, количества, требованиям к твердости и вида термической обработки.
Получаемая твердость
Максимальная 63 HRC или 630 HB
Отпуск (средний и высокий)
- Максимальная температура: 700°С
- Максимальная масса: 500 кг
- Рабочее пространство: диаметр 700 мм, высота 1000 мм
Нагрев, закалка, улучшение
- Максимальная температура: 1500°С
- Максимальная масса: 650 кг
- Рабочее пространство: ширина 400 мм, высота 400 мм, глубина 800 мм
Отпуск (низкий)
- Максимальная температура: 250°С
- Максимальная масса: 250 кг
- Рабочее пространство: диаметр 630 мм, высота 800 мм
Закалка деталей типа вал
- Максимальная длина: 1800 мм
- Максимальная масса: 100 кг
Закалка деталей типа колес, катков, колец, шестерен
- закалка шестерен – максимальный модуль m=14
- закалка колец – максимальный диаметр 2000 мм
- максимальная масса: до 1000 кг
Закалочные среды: вода, масло.
Возможные виды деталей
Валы, пальцы, фланцы, торсионы, втулки, шкивы, колёса, шестерни, кольца, секторы, зубчатые колеса и многое другое.
Требования к конструкторско-чертежной документации
- Чертежи в формате PDF
- Размер бумаги А4-А0
- Разрешение от 1200 dpi и более
- Оформление чертежа согласно Единой Системе Конструкторской Документации (ЕСКД) с указанием технических требований и материала
- Спецификация на сборочные узлы в формате PDF
- Технические требования
- Марка материала
- Необходимость термообработки, твердость HB, HRC
Для заказа термической обработки и расчета стоимости изготовления отправляйте чертежи с указанием количества и материала на почту [email protected]
Обратитесь к нам
Заполните форму и мы оперативно проработаем ваш запрос
Просим ввести немного вводных данных для того чтобы первое общение прошло продуктивно и конструктивно.
If you are a human, ignore this field
Фотографии процесса
Термообработка (ТВЧ и объемная) | Уралпроммаш
Вы здесь
Термообработка (ТВЧ и объемная)
вс, 31/01/2021 – 22:23
Немного теории
Одним из методов изменения характеристик сталей является термообработка. Для повышения твердости применяется закалка. При этом заготовку нагревают до определенной температуры, а затем резко охлаждают. Более подробно о режимах закалки написано в марочниках сталей и специализированной литературе.
По типу термообработки различают поверхностную и объемную. Объемная термообработка производится в нагревательных печах. Поверхностная термообработка выполняется различными установками поверхностного нагрева. Наибольшее распространение в промышленности получила закалка сталей токами высокой частоты (ТВЧ).
Закалке подвергаются стали с содержанием углерода более 0,4%. Температурный интервал 800-850°С. При резком охлаждении аустенит превращается в мартенсит, который обладает высокой твердостью и прочностью.
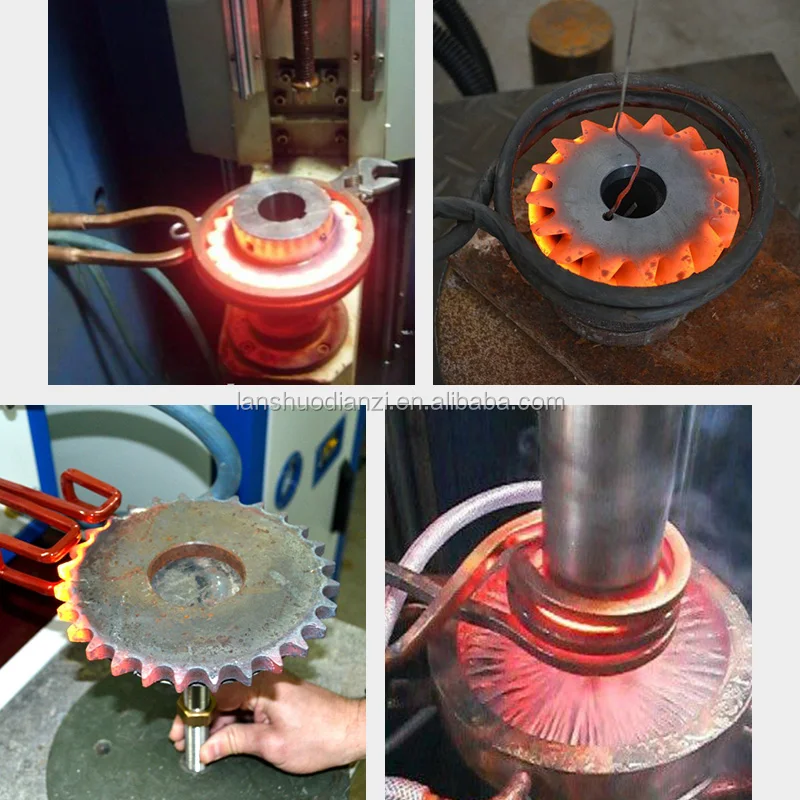
Матчасть
В распоряжении ЗАО «Уралпроммаш» имеется установка мощностью 350 кВт, которая позволяет эффективно обрабатывать массивные детали и заготовки, начиная от пальцев гусеничных траков, заканчивая шкивами и паровозными колесами. Также на предприятии освоена закалка зубчатых колес с большим и малым модулем.
При поверхностной закалке особе значение имеет обеспечение стабильных режимов подачи, нагрева и охлаждения.

В распоряжении ЗАО «Уралпроммаш» имеется закалочный станок. За счет регулировки скорости подачи заготовки, регулирования силы тока ТПЧ и температуры охлаждающей эмульсии обеспечивается подбор оптимальных режимов ведения процесса и обеспечивается равномерность термообработки.
Дополнительно закалочный станок имеет возможность вращения заготовки в центрах, что позволяет обеспечить сплошность поверхности нагрева, и, как следствие, одинаковую структуру и твердость поверхности заготовки.
Для эффективной работы установки ТВЧ имеет большое значение правильная конфигурация индуктора. ЗАО «Уралпроммаш» располагает парком из 30 индукторов, охватывающих весь размерный ряд наиболее ходовых деталей. Более того предприятие имеет опыт проектирования, изготовления и ремонта индукторов.
И так основными достоинствами поверхностной закалки ТВЧ являются:
• После закалки ТВЧ у детали сохраняется мягкой середина, что существенно повышает ее сопротивление пластической деформации.

• Быстрый нагрев и охлаждение не дают большого коробления и поводок, что позволяет уменьшить припуск на чистовую обработку.
• Возможность точно рассчитать и регулировать глубину закаленного слоя.
• Обработку ТВЧ можно выполнять после окончательной механической обработки.
ЗАО «Уралпроммаш» занимается термообработкой более 10 лет и имеет богатый опыт.
Обратитесь к нашим специалистам за консультацией.
Tags:
ТВЧ
закалка
термообработка
объемная закалка
Оборудование для термической обработки
ОБЩИЕ СВЕДЕНИЯ О ТЕРМИЧЕСКОЙ ОБРАБОТКЕ НЕПРЕРЫВНАЯ ПЕЧЬ ДЛЯ КРЕПЕЖНЫХ СОЕДИНЕНИЙ ШАХТНАЯ ПЕЧЬ ДЛЯ ОТЖИГА ПРОВОЛОКИ ПЕЧЬ КОЛПАКОВОГО ТИПА ДЛЯ ОТЖИГА ПРОВОЛОКИ КАМЕРНЫЕ ПЕЧИ ДЛЯ ОТЖИГА ПРОВОЛОКИ ВАКУУМНАЯ ПЕЧЬ ТИГЕЛЬНАЯ ПЕЧЬ ГЕНЕРАТОРЫ ДЛЯ СИСТЕМ ТЕРМООБРАБОТКИ
КОМПЛЕКСНЫЙ ПРОЦЕСС ТЕРМИЧЕСКОЙ ОБРАБОТКИ
Термическая обработка (термическая обработка) стали и сплавов может быть следующих видов: отжиг, нормализация, закалка, отпуск.
- Отжиг – термическая обработка металла, при которой металл нагревают, а затем медленно охлаждают. Отжиг бывает разных видов (вид отжига зависит от температуры нагрева, скорости охлаждения металла).
- Закалка – термическая обработка стали и сплавов, основанная на рекристаллизации стали (сплава) при нагреве выше критической температуры; после достаточной выдержки при критической температуре для завершения термической обработки следует быстрое охлаждение. Закаленная сталь (сплав) имеет неравновесную структуру, поэтому может применяться другой вид термической обработки – отпуск.
- Отпуск – термическая обработка стали, сплавов проводится после закалки для уменьшения или снятия остаточных напряжений в стали и сплавах, повышает вязкость, что снижает твердость и хрупкость металла.
- Нормализация – термическая обработка, аналогичная отжигу.
Отличие этих видов термической обработки (нормализации и отжига) состоит в том, что при нормализации сталь охлаждают на воздухе (при отжиге – в печи).
ОТЖИГ СТАЛИ
Отжиг – процесс термической обработки металла, который производится при нагреве, а затем медленном охлаждении металла. Перемещение структуры из неравновесного состояния в более равновесное. Отжиг первого рода, его виды: восстановление металлов, рекристаллизационный отжиг, отжиг для снятия напряжений, отжиг на раствор (называемый также гомогенизирующим). Отжиг второго рода – изменение структуры сплава рекристаллизацией вблизи критических точек для получения равновесной структуры. Отжиг второго рода, его виды: полный, неполный, изотермический отжиг. Отожженная, ее виды применительно к стали показаны ниже.
- Восстановление стали – нагрев до 200 – 400°С, отжиг для уменьшения или устранения наклепа. В результате отжига происходит уменьшение искажения кристаллических решеток кристаллитов и частичное восстановление физико-химических свойств стали.
- Рекристаллизационный отжиг стали – нагретой до температуры 500 – 550°С; отжиг для снятия внутренних напряжений – нагрев до температур 600 – 700°С. Эти виды отжига снимают внутренние напряжения металлической отливки от неравномерного охлаждения ее деталей и заготовок, обрабатываемых давлением (прокаткой, волочением, ковкой) при температурах ниже критических. За счет рекристаллизации деформированных зерен новые кристаллы вырастают ближе к равновесию, поэтому твердость стали снижается, а пластичность и ударная вязкость возрастают. Для полного снятия внутренних напряжений из стали необходимая температура должна быть не менее 600°С. Охлаждение после выдержки при заданной температуре должно быть достаточно медленным: из-за ускоренного охлаждения вновь возникают внутренние напряжения.
- Диффузионный отжиг стали (гомогенизация) применяется при наличии в стали внутрикристаллитной ликвации. Выравнивание состава в зернах аустенита достигается за счет диффузии углерода и других примесей в твердом состоянии наряду с самодиффузией железа.
В результате отжига сталь становится однородной по составу (гомогенной), так называемый диффузионный отжиг и гомогенизация. Температура гомогенизации должна быть достаточно высокой, однако нельзя допускать перегорания, плавления зерен. Предполагая выгорание, кислород воздуха окисляет железо, проникая вглубь его, образуются фрагментированные оксидными оболочками кристаллиты. Прогар устранить невозможно, поэтому бракуются перегретые заготовки. Диффузионный отжиг стали обычно приводит к чрезмерному укрупнению зерна, которое следует исправить с последующим полным отжигом (до мелкого зерна).
- Полный отжиг стали связан с фазой рекристаллизации, измельчением зерна при температурах точек АС1 и АС2. Его назначение – улучшение структуры стали для облегчения последующей механической обработки, штамповки и закалки, а также получение равновесной мелкоперлитной структуры готовой детали. Для полного отжига сталь нагревают при температуре на 30-50°С выше линии ГСК и медленно охлаждают.
После отжига избыточный цемент (в заэвтектоидной стали) и эвтектоидный цементит имеют форму пластин, так называемого пластинчатого перлита
- При отжиге стали на пластинчатый перлит заготовки оставляют для охлаждения в печи, обычно при частичном подогреве печи топливом, скорость охлаждения не более 10-20°С в час. Отжиг также достигается за счет измельчения зерна. Грубая структура, как у доэвтектоидной стали, получается при затвердевании за счет свободного роста зерен (при медленном охлаждении отливки) и в результате перегревается. Эта структура называется видманштеттеновой структурой (по имени австрийского астронома А. Видманштеттена, открывшего в 1808 г. структуру такого метеоритного железа). Такая структура придает бланку низкую прочность. Структура характеризуется включениями феррита (белые участки) и перлита (темные участки), расположенных в виде вытянутых пластин под разными углами друг к другу. В структуре заэвтектоидной стали видманштеттова структура характеризуется избытком цементита с линейным расположением.
Одним из результатов отжига для пластинчатого перлита является мелкозернистая структура.
- Неполный отжиг стали связан с фазой рекристаллизации только в точках А и С1; неполный отжиг применяется после горячей штамповки при мелкозернистой структуре заготовки.
- Отжиг стали на гранулированный перлит обычно применяют для эвтектоидных, заэвтектоидных сталей для повышения пластичности, ударной вязкости стали и снижения ее твердости. Для гранулированного перлита сталь нагревают выше AC1, а затем кратковременно выдерживают до полного растворения цементита в аустените. Затем сталь охлаждают до температуры несколько ниже Ar1, выдерживают при этой температуре несколько часов. Частицы оставшегося цементита служат зародышами кристаллизации всего оставшегося цементита, который растет в виде округлых (глобулярных) кристаллитов, рассеянных в феррите. По сравнению с пластинчатым перлитом гранулированный перлит имеет существенно иные свойства, такие как меньшая твердость, но более высокая пластинчатость и вязкость.
Особенно это относится к заэвтектоидной стали, где весь цемент (как эвтектоидный, так и избыток) получается в виде глобул.
- Изотермический отжиг – после нагрева и выдержки сталь быстро охлаждают до температуры ниже точки А 1 , затем выдерживают при этой температуре до полного распада аустенита до перлита, после чего охлаждают на воздухе. Применение изотермического отжига значительно сокращает время и увеличивает производительность. Например, обычная процедура отжига нержавеющей стали длится 13-15 часов, а изотермическая – всего 4-7 часов.
ЗАКАЛКА СТАЛИ
Различают виды закалки с полиморфными превращениями сталей и без полиморфных превращений, для большинства цветных металлов. Материал, подвергшийся закалке, становится более твердым, но хрупким, менее эластичным и вязким, если производить большее количество повторов нагревания и охлаждения. Для снижения хрупкости и повышения ударной вязкости и пластичности после закалки применяют полиморфное превращение. После закалки без полиморфного превращения применяется старение. Когда вы покидаете материал, можно заметить некоторое снижение твердости и прочности.
В зависимости от температуры нагрева отпуск делится на полный и неполный. В случае полного твердения материал нагревают на 30 – 50°С выше ГС для доэвтектоидной, эвтектоидной стали, как и для заэвтектоидной линейки ПСК, в этом случае структура стали становится аустенит + цементит и аустенит. При неполном твердении осуществляется нагрев по диаграмме ПСК, что приводит к образованию избыточной фазы. Неполная закалка обычно используется для инструментальной стали. Закалку снимают отпуском материала. Для некоторых изделий закалка производится частично, например при изготовлении японской катаны закаливается только режущая кромка меча.
Закалочные среды
При закалке на переохлаждение аустенита до мартенситного превращения требуется температура быстрого охлаждения, но не во всем интервале температур, а только в пределах 650-400°С, т. е. в интервале температур, при котором аустенита меньше всего стабильнее всего превращается в ферритно-цементитную смесь. Выше 650 °С скорость превращения аустенита невелика, и поэтому смесь можно охлаждать закалкой в интервале температур медленно, но, конечно, недостаточно, чтобы инициировать потерю феррита или превращение аустенита в перлит.
Механизм действия закалочной среды (вода, масло, акваполимерная закалочная среда (Термат) и охлаждение в растворах солей) заключается в следующем. В момент погружения изделий в закалочную среду вокруг образовавшейся пленки возникает перегретый пар, охлаждение осуществляется через паровую рубашку, т.е. относительно медленно. Когда температура поверхности достигает определенного значения (определяемого составом закалочной жидкости), при котором паровая рубашка разрывается, жидкость начинает кипеть у поверхности детали и быстро остывать.
Первую стадию относительно медленного кипения называют стадией пленочного кипения, вторую стадию быстрого охлаждения – стадией пузырькового кипения. Когда температура поверхности металла ниже точки кипения жидкости, жидкость не может кипеть и медленно остывать. Эта стадия называется конвективным теплообменом.
Способы закалки
- Закалка в охладителе – нагретая до определенной температуры деталь погружается в закалочную жидкость, где остается до полного охлаждения. Этот метод применяют для упрочнения простых деталей из углеродистых и легированных сталей.
- Прерывистая закалка в двух средах – метод применяется для закалки высокоуглеродистых сталей. Деталь сначала быстро охлаждают в быстродействующей охлаждающей среде (например, в воде), а затем медленно охлаждают (в масле).
- Ламинарная закалка осуществляется путем интенсивного орошения детали струей воды и обычно применяется при необходимости упрочнения детали. В этом методе формируется паровая рубашка, обеспечивающая лучшую прокаливаемость, чем простая закалка в воде. Такая закалка обычно выполняется в катушках индуктивности на объектах ТВЧ.
- Ступенчатая закалка – закалка, при которой изделие охлаждается в закалочной среде, имеющей температуру выше мартенситной точки стали. При охлаждении и выдержке в этой среде закаленная сталь должна иметь температуру закалочной ванны во всех точках сечения. Затем следует окончательное, обычно медленное охлаждение, во время которого происходит закалка, т. е. превращение аустенита в мартенсит.
- Изотермическая закалка. В отличие от ступенчатой закалки изотермическая закалка требует выдержки стали в закалочной среде до полного изотермического превращения аустенита.
ОТПУСК СТАЛИ
Закалка стали смягчает эффект закалки, снижает или устраняет остаточное напряжение, повышает вязкость, снижает твердость и хрупкость стали. Размещение производится путем нагрева деталей на закаленном мартенсите до температуры ниже критической. Таким образом, в зависимости от температурного режима нагрева могут быть приготовлены мартенситный, трооститный или сорбитный отпуск. Эти условия отличаются от соответствующих состояний отпуска строением и свойствами: при твердении цементит (в троостите и сорбите) получается в виде вытянутых пластинок в виде пластинчатого перлита. А при закалке становится зернистым, как в зернистом перлите.
Преимуществом точечной структуры является более выгодное сочетание прочности и пластичности. При одинаковом химическом составе и твердости сталь с одинаковой точечной структурой имеет значительно более высокие относительные сужение y, ударную вязкость n, повышенное удлинение d, предел текучести s t по сравнению со сталью с пластинчатой структурой.
Мартенсит закалки имеет неустойчивую тетрагональную решетку, мартенсит отпуска – устойчивую центрированную кубическую решетку альфа-железа.
Жилье делится на низкое, среднее и высокое в зависимости от температуры нагрева.
Для определения температуры отпуска-отжига изделий используется таблица цветов. Тонкая пленка оксидов железа придает металлу разнообразные быстро меняющиеся цвета — от светло-желтого до серого. Эта пленка появляется, если очищенный от окалины стальной продукт нагревают до 220°С; при увеличении времени нагрева или температуры оксидная пленка утолщается и изменяется ее цвет. Цвета отжига проявляются как на сырой, так и на закаленной стали.
При низкотемпературном отпуске (нагрев до температуры 200-300°С) в структуре стали в основном присутствует мартенсит, у которого, однако, меняется решетка. Также осаждение карбидов железа начинается из твердого раствора углерода в альфа-железе и первоначального накопления мелких групп. Это влечет за собой снижение твердости и повышение пластических и вязких свойств стали, а также снижение внутренних напряжений в деталях. Для низкотемпературного отпуска изделия выдерживают определенное время, как правило, в масляных или солевых ваннах. Если при низком отпуске изделия нагревают на воздухе, то регулирование температуры осуществляют с помощью цветов отжига, возникающих на поверхности изделия. Появление этих цветов связано с интерференцией белого света в пленках оксида железа на поверхности деталей при нагреве. В диапазоне температур от 220 до 330°С в зависимости от толщины пленки цвет меняется от светло-желтого до серого. Низкий отпуск применяют для режущего, мерительного инструмента и зубчатых колес.
При среднем (нагрев в интервале 300-500°С) и высоком (500-700°С) отпуске мартенситное состояние переходит соответственно в трооститное или сорбитное состояние. Чем выше отпуск, тем меньше твердость закаленной стали и тем выше ее пластичность и ударная вязкость. Когда закаленная сталь получает наилучшее сочетание механических свойств, улучшая такие показатели, как прочность, пластичность и ударная вязкость, именно поэтому высокий отпуск после закалки ее на мартенсит применяют для термической обработки штампов, пружин, листовых рессор, а высший – для многих детали, подверженные высоким нагрузкам (например, оси автомобилей, шатуны двигателя).
Для некоторых марок стали отпуск проводят после нормализации. Это относится к мелкозернистому сплаву доэвтектоидной стали (особенно никеля), имеющей высокую вязкость и, следовательно, плохую обрабатываемость режущим инструментом. Для улучшения обрабатываемости стали проводят нормализацию стали при повышенной температуре (до 950-970°С), при которой она приобретает крупную структуру (обусловливающую лучшую технологичность) и одновременно повышенную твердость (из-за низкой критической скорости твердения никелевой стали). Для снижения твердости проводят высокий отпуск этой стали.
НОРМАЛИЗАЦИЯ СТАЛИ
Нормализация является более дешевой операцией, чем отжиг, т.к. печи используются только для нагрева и выдержки изделия при температуре нагрева, а охлаждение производится вне печи. Кроме того, нормализация ускоряет процесс термообработки. Таким образом, отжиг выгодно заменить нормализацией. Однако это не всегда возможно, так как твердость некоторых сталей увеличивается после нормализации более значительно, чем при отжиге. Мягкую сталь рекомендуется подвергать нормализации, так как она почти не имеет разницы в свойствах после отжига и нормализации.
Стали, содержащие более 0,4% углерода, приобретают повышенную твердость после нормализации. Эти стали лучше отжигать. На практике также такие стали часто подвергают нормализационному отжигу на месте, а затем отпуску при высокой температуре 650 – 700°С для снижения твердости. Нормализация применяется для получения мелкозернистой структуры в отливках и поковках, для устранения внутренних напряжений при подготовке структуры стали к закалке.
Термическая обработка инструментов из быстрорежущей стали
Для обеспечения высокой прочности и производительности инструментов, необходимых для работы, часть из них имела достаточную твердость и износостойкость. Это возможно за счет создания сердечника мелкозернистой мартенситной структуры, что достигается предварительной ковкой и изотермическим отжигом перед механической обработкой, а после механической обработки — закалкой и отпуском. Для этих термических процессов характерно следующее:
1) нагрев инструмента при ковке, отжиге и закалке должен быть быстрым, чтобы весь материал был равномерно прогрет; в то же время слишком медленный нагрев вызывает появление накипи;
2) выдержка инструмента в печи должна быть достаточной для структурных превращений, но во избежание выгорания углерода с поверхности инструмента и роста зерен аустенита не переусердствовать при высокой температуре;
3) охлаждение инструмента необходимо производить в зависимости от химического состава стали с определенной интенсивностью
.
Данные операции термической обработки применяются ко всем классам инструментальной стали. Однако температурные режимы этих процессов во многом зависят от марки стали и размеров инструмента. Учитывая относительно широкое применение быстрорежущих сталей для изготовления режущего инструмента, рассмотрим специфику операций термической обработки.
Быстрорежущая сталь обычно поставляемая в отожженном состоянии со структурой мелкозернистого (сарбатосодержащего) перлита с избытком карбидов. Твердость стали обычного исполнения Р9 и Р18 по ГОСТу должна быть не более НВ = 207-255, а сталей повышенного качества – до НВ = 269-293. Толщина безоперационного слоя на боку для стержней диаметром 5—100 мм не должна превышать 0,45—1,3 мм.
Полированная сталь (чешуйница) с обеспложенным слоем обычно не допускается. Запас пластичности быстрорежущей стали определяют по механическим свойствам, при необходимости проверяют технологическими испытаниями пробной резки, штамповки, а также образцов на изгиб.
по мере карбидной неоднородности на ТВД диаметром более 50 мм, обычно более 3 цилиндров, заготовки из прутков, стержней большого диаметра для уменьшения карбидной неоднородности следует подвергать дополнительной ковке. Поковкой бывают также прутки из быстрорежущей стали. Таким образом, термическая обработка быстрорежущих сталей включает, кроме основных операций закалки и отпуска, операции ковки и последующего отжига. При выборе видов и режимов термической обработки следует учитывать получение необходимой зернистости, ударной вязкости (не менее HRC = 62-65), прочности и жаростойкости стали. Также необходимо отомстить за то, что смена режимов нагрева, замачивания и охлаждения по-разному влияет на получение оптимальных значений вышеуказанных характеристик. Таким образом, твердость закаленной стали с повышением температуры закалки сначала увеличивается, а затем снижается. Жаростойкость зависит также от твердого раствора сплава™ и увеличивается с повышением температуры закалки, а прочность — от структурных факторов и преде<л<де только от размера зерен и условий распределения карбидов. Поэтому при повышении температуры закалки обеспечивается равномерный рост зерна, но при этом обеспечивается растворение мелких карбидов, в том числе присутствующих в отожженной стали по границам зерен, для повышения прочности. Кроме того, температура закалки, обеспечивающая наибольшую красную твердость, не совпадает с температурами, способствующими максимальной твердости.
Нагрев под ковку из-за плохой теплопроводности быстрорежущей стали следует отложить. Заготовки из стали Р18 диаметром 50—60 мм сначала помещают в печь с температурой 400—600°С и медленно нагревают из расчета 7—8 минут на каждые 10 мм толщины, а затем нагревают до 780—820°С. °С и выдерживают при этой температуре, т.е. в области превращения перлита в аустенит, также из расчета 7-8 мин на каждые 10 мм диаметра. Заготовку меньшего размера следует помещать в печь с температурой 780-820°С. Дальнейший нагрев до температуры начала ковки /= 1140-1180°С, а слитки до /=1150-1200°С производят сравнительно быстро. . Для предотвращения чрезмерного твердения и растрескивания ковка (прокатка) прекращается при температуре 875-900°С, а слитки при температуре 975-1000°С. По мере закалки быстрорежущей стали охлаждением на воздухе, для предотвращения растрескивания крупные заготовки медленно охлаждают в горячем песке, а затем проводят изотермический отжиг.
Изотермический отжиг быстрорежущей стали необходим для снятия напряжения, полученного при обработке давлением, и для снижения твердости, а также для создания структуры зернистого перлита или сарбатообразования с относительно хорошей обрабатываемостью.
Изотермический отжиг быстрорежущей стали Р18 получают путем нагрева до температуры 850-870°С с выдержкой до 12 часов при этой температуре. После окончания выдержки производят охлаждение стали до температуры 720-740°С с относительно небольшой скоростью (40-50°С в час), а затем при 720-740°С сталь снова старят в течение не менее 4 часы. Следует особо отметить, что быстрорежущие стали, содержащие молибден или кобальт и особо чувствительные к обезуглероживающему отжигу, целесообразно отжигать в печи с защитной атмосферой или в чугунной стружке.
При резании с большой скоростью вызывается неравномерный нагрев поверхностного слоя обрабатываемого инструмента, что является причиной создания поверхностных напряжений и образования участков с мартенситно-аустенитной структурой. В связи с этим для крупных инструментов сложной формы и большой длины, например протяжек, после механической обработки для снятия напряжений и подготовки стали к закалке рекомендуется производить высокий отпуск. Этот отпуск производят путем нагрева инструмента до температуры 650—680° С с выдержкой 2— 3 ч с последующим охлаждением на воздухе или в масле.
Высокая красная твердость и режущая способность быстрорежущей стали зависят не только от химического состава, исходной зернистой структуры с равномерным распределением карбидов, но и от конкретных условий закалки и отпуска. Поэтому нагрев при закалке таких сталей до высоких температур, отстоящих от температуры плавления, является специфической особенностью термической обработки этих сталей. Учитывая пониженную (в 2-3 раза) теплопроводность быстрорежущих сталей по сравнению с углеродистыми, для предотвращения возникновения высоких напряжений и трещин производят стадию нагрева под закалку. Первый нагрев, который производят только для крупных (диаметром более 30 мм) и сложных инструментов, производят при температуре 400—500°С в печи любой конструкции. Второй нагрев до 840°С, необходимый для превращения перлита в аустенит, избегая обезуглероживания, па и окисления, проводят в печах с защитной атмосферой или ваннах. Продолжительность выдержки при таком нагреве зависит от формы и размеров инструмента. При нагревании солей экспозиция составляет около 20 секунд, печки и 25-30 секунд на 1 мм шлиф инструмента. Такая большая выдержка необходима не только для прогрева инструмента по всему сечению до заданной температуры, но и для полного превращения перлита в аустенит. Окончательный нагрев до температуры закалки, необходимой для растворения карбидов легирующих элементов в аументе, производится относительно быстро, так как при длительной выдержке возможен рост зерна аустенита. Кроме того, по границам зерен аустенита может образовываться карбидная сетка, а также происходить обезуглероживание поверхностных слоев инструмента.
Кроме того, длительное воздействие вблизи температуры образования жидкой фазы изменяет форму карбидов. Они приобретают угловатую форму и сильно увеличиваются в размерах за счет растворения мелких карбидов.
Продолжительность нагрева до высоких температур, как установила практика, в определенной степени пропорциональна сечению инструмента и составляет 8-9 секунд на 1 мм диаметра или толщины при нагреве в соли и 10-12 секунд на нагрев в печи.
Следует отметить, что качество отпуска зависит от точности установки температур закалки, так как при незначительных изменениях химического состава стали температура закалки изменяется. При этом диапазон изменения температуры закалки для конкретной стали должен быть уменьшен до 10-5°С, что повышает режущую способность инструмента в 1,5 раза.
Окончательный нагрев инструмента из обыкновенных быстрорежущих сталей целесообразнее производить в солевом расплаве ВаС12, а из сталей, содержащих кобальт или более 1,5—2% молибдена, для наилучшей защиты от обезуглероживания — в контролируемых атмосферах или в солевом расплаве , но с уменьшенной выдержкой, с применением нагретого до 1100-1150°С.
охлаждения нагретого до закалки инструмента Температуру следует устанавливать в зависимости от его размеров и формы. Ускоренное охлаждение до 500-400°С задерживает выход карбидов из аустенита и способствует лучшей жаростойкости.
Непрерывная закалка с охлаждением в масле (30-100°С) может применяться для инструмента простых форм (резцы, сверла) диаметром (толщиной) до 30-40 мм. Инструменты малого диаметра или толщины 3-5 мм можно охлаждать сжатым воздухом или непосредственно на воздухе.
Ступенчатый отжиг с опережающим подстугиванием на воздухе с выдержкой 2-5 мин в горячей охлаждающей среде (нитрат калия) при g = 450-500°С или 250-350°С, т.е. р-область наибольшей устойчивости аустенита, это целесообразно для контурных средних и очень длинных и тонких инструментов. После окончания выдержки инструмент охлаждают непосредственно воздухом. При отсутствии ванны с расплавленной смесью инструменты можно также охлаждать в масле до 300—450°, а затем на воздухе.
Изотермическая закалка, рекомендуемая для крупных и длинных инструментов, заключается в охлаждении в солевом расплаве с температурой 200-300°С с выдержкой 30-60 минут. Кроме того, для очень крупных инструментов с резкими переходами может применяться прерывистый отжиг, который проводят сначала в масле, нагретом до 90-100°С, при котором происходит частичное мартенситное превращение, а затем инструменты переносят в печь для отжига. каникулы. Также следует отметить затвердевание под давлением. Применяется для уменьшения деформации инструментов простой формы и очень малых размеров. При этом инструменты сначала охлаждают в соли до 500-600°С, а затем в масле под давлением.
Несмотря на высокую температуру, правильно закаленная быстрорежущая сталь должна иметь мелкозернистую структуру, состоящую из легированного мартенсита (около 50%), высоколегированного остаточного аустенита (около 30%) и сложных карбидов (около 20%). Для дальнейшего превращения остаточного аустенита во вторичный, более легированный мартенсит сразу после закалки производили многократный отпуск. Последним является для инструмента из быстрорежущих сталей нормальной работоспособности при температуре 560-570°С старение в течение 60-75 минут при нагреве в соляной ванне и старение в течение 60 минут при нагреве в печи. Затем следует охлаждение инструмента на воздухе до комнатной температуры. При выдержке из остаточного аустенита выделяются мелкодисперсные карбиды, в результате чего аустенит обедняется углеродом и легирующими примесями и становится менее устойчивым. При этом превращение остаточного аустенита во вторичный, более легированный мартенсит повышает твердость стали до HRC = 63-65. Такой отпуск для стали Р18 рекомендуется 2-3 раза, а для стали Р9—3—4 раза. Кроме того, инструмент подвергают изотермическим неполным или прерывистым закамкам, а также все основные инструменты диаметром более 80 мм подвергают греховному, четырехкратному отпуску.
Количество отпусков можно сократить до одного, если сразу закаленную быстрорежущую сталь подвергнуть однократному отпуску, а затем поместить в среду с отрицательными температурами (-75—120°С). При этом происходит более интенсивный процесс дальнейшего превращения остаточного аустенита во вторичный мартенсит.
Повышение температуры отпуска быстрорежущих сталей обычного исполнения до 580-600°С, как известно, снижает твердость и износостойкость, но мало повышает прочность и отпуск при температуре ниже 550е достаточно затруднен при полном превращении аустенита. Наоборот, стали повышенные характеристики, для получения твердости HRC = 65-66 необходимо выпускать при более высокой температуре (575-585°С). Это обеспечивает лучшие режущие свойства инструментов, применяемых в основном при чистовых операциях. Для инструментов же сложной формы на этих сталях применяют съем стружки большого сечения, выпуск производят при еще более высоких температурах (580-590′ ю.ш.).
Значительное увеличение стойкости высокоскоростного инструмента может также обеспечить дополнительный выпуск инструмента после заточки, если инструмент не подвергается таким химико-термическим методам рафинирования, как цианирование и обработка горячим паром.
Правку инструмента из быстрорежущих сталей в отличие от инструмента из других сталей лучше всего производить сразу после закалки или при нагреве, а сталь закаленную до 300-350°С, т.е. в условиях, когда сталь обладает низким сопротивлением пластической деформации. В связи с этим после отпуска делается по необходимости только правка.
Следует указать на некоторые особенности закалки наплавленного инструмента при нагреве, при закалке следует принимать в ванну, чтобы верхняя зона рабочей части инструмента находилась выше уровня соли в ванне, т.к. за счет тепла прогревается даже на некоторой части своей длины, выступая над поверхностью ванны. В связи с этим во избежание сильного нагрева сварной шов обычно располагают над рабочей частью на величину, примерно равную диаметру рабочей части.
Нагрев под закалку токами высокой частоты (ТВЧ) более мощный процесс, чем при нагреве в печи и солях. Скорость индукционного нагрева составляет от 20 до 1000 град/сек (иногда больше), при этом скорость нагрева в расплавах солей не превышает 10, а в печи 0,8 град/сек. Однако качество термической обработки инструментов из быстрорежущей стали, нагретых токами высокой частоты, зависит не только от температуры, но и от скорости. Известно, что увеличение скорости нагрева смещает начало и конец фазовых превращений в область более высоких температур.