Техпроцесс вала пример – 6.2.Типовые технологические процессы обработки валов
alexxlab | 21.10.2019 | 0 | Разное
6.2.Типовые технологические процессы обработки валов
Несмотря на большое разнообразие размеров и конструктивных форм, валы подвергаются одинаковым процессам изготовления. Типичными установочными базами для них являются центровые отверстия. На некоторых операциях обработки при воздействии изгибающие сил резания, например при фрезеровании плоскостей, сверлении радиальных отверстий, в качестве установочных баз используют обработанные шейки.
В зависимости от конструкций или программы выпуска изделий технологические процессы изготовления валов могут различаться только последовательностью обработки или введением дополнительных операций.
Типовую схему процесса изготовления валов можно представить следующим образом:
1) подготовка технологических баз — подрезание торцов и центрование. Эту операцию при серийном и массовом производстве выполняют на центровальных и фрезерно-центровальных станках двустороннего или барабанного типа;
2) черновая токарная обработка обоих концов вала, подрезание торцов и уступов;
3) чистовая токарная обработка, осуществляемая в той же последовательности, что и черновая. Наружные поверхности валов обтачивают на токарно-копировальных и многорезцовых одно- и многошпиндельных автоматах;
4) черновое шлифование шеек вала, служащих дополнительными базами при фрезеровании, сверлении, растачивании отверстий на одном из концов вала;
5) правка заготовки при изготовлении нежестких валов;
6) черновая и чистовая обработка фасонных поверхностей — нарезание шлицев, зубчатых венцов, фрезерование кулачков и т.д.;
7) выполнение последующих операций — сверления, развертывания, нарезания резьбы, фрезерования лысок, шпоночных канавок;
8) термическая обработка всей детали или отдельных ее поверхностей;
9) правка вала;
10) черновое и чистовое шлифование наружных поверхностей, торцов, отверстий;
11) доводка особо точных поверхностей.
Оборудование для выполнения типового процесса может быть разным, но порядок и характер операций при изготовлении валов должны оставаться неизменными.
При разработке технологических процессов изготовления валов необходимо руководствоваться типовыми технологическими процессами обработки различных поверхностей (таблица 6.1).
Таблица 6.1 – Типовые технологические процессы (операции) обработки различных поверхностей валов в условиях серийного производства
Поверхности | Точность | Шероховатость Ra, мкм | Характер и последовательность выполнения операций (переходов) |
Незакаливаемые цилиндрические и конические | Квалитет 11 и грубее Квалитет 9 и грубее Квалитеты 6…8 | 25 и грубее 3,2 и грубее 0,4…1,6 | Черновое точение на станках класса Н Черновое и чистовое точение на станках класса Н 1.Черновое, чистовое (получистовое) точение и круглое шлифование на станках класса Н 2.Предварительное и чистовое точение на станках класса П |
Закаливаемые цилиндрические и конические | Квалитеты 6…8 | 0,4…1,6 | 1.Черновое и получистовое точение, закалка и круглое шлифование на станках класса Н 2.Черновое, чистовое (получистовое) точение, закалка, чистовое точение на станках класса П с использованием сверхтвердых режущих материалов на основе нитрида бора (композит 01), карбонада (например марки АСПК) и др. |
Незакаливаемые шлицевые поверхности | Квалитет 6 наружнего диаметра | 0,4…1,6 | 1.Черновое и чистовое точение, круглое шлифование, шлицефрезерование 2.Черновое и чистовое точение, круглое шлифование, шлицефрезерование, круглое шлифование |
Закаливаемые шлицевые поверхности | Квалитет 6, 7 внутреннего диаметра | 0,4…1,6 | 1.Черновое и чистовое точение, шлицефрезерование, закалка, шлицешлифование 2.Получистовое точение, шлицефрезерование, закалка, шлицешлифование |
Цилиндрическая со шпоночной канавкой | Ширина канавки квалитетов 8, 9, точность диаметра квалитетов 8,9 | 1,6 0,4…0,8 | 1.Черновое и чистовое точение, шпоночное фрезерование, круглое шлифование 2.Получистовое точение, фрезерование шпоночного паза, круглое шлифование |
Резьбовая (крепёжная резьба) с нормальным и мелким шагом | 8h…8g | 1,6 | 1.Черновое и чистовое точение, нарезание резьбы плашками или резьбофрезерование 2.Получистовое точение, нарезание резьбы плашками или резцами 3.Получистовое точение, накатывание резьбы |
Резьбовая с нормальным и мелким шагом | 4h…6g | 0,8 | 1.Черновое и чистовое точение, нарезание резьбы резцами 2.Черновое и чистовое точение, резьбонакатывание, шлифование резьбы |
6.3. Изготовление вала в условиях среднесерийного производства
Получение исходной информации. В качестве примера принят вал (рисунок 6.2), материал — сталь 20Х, масса детали 4,9 кг, годовой объем выпуска 1250 шт., режим работы двухсменный при 40-часовой рабочей неделе.
Технологический контроль чертежа. Деталь представляет собой ступенчатый вал. Точность изготовления основных поверхностей находится в пределах квалитетов 6…8. Отношение длины (325 мм) к диаметру (в среднем 50 мм) составляет 6,5. Вал можно считать достаточно жестким, что не вызывает трудностей в получении заданной точности. Шероховатость посадочных шеек находится в пределах 1,25 мкм, точность расположения поверхностей — в пределах 0,02 мм. Весьма мал допуск на погрешность формы шеек диаметром 45 мм. Диаметральные размеры шеек вала уменьшаются к концам. Конфигурация вала, размеры поперечных канавок позволяют производить обработку на токарных станках различного типа. Обеспечение точности и шероховатости диаметральных поверхностей не вызывает трудностей.
Необходимо отметить некоторые недостатки конструкции детали. На валу имеется три шпоночных паза: два закрытого типа и один полузакрытого на резьбовом конце. Вызывает сомнение правильность такого конструктивного решения. Для уменьшения номенклатуры инструментов целесообразно применять один размер: 14N9 или 16N9. Для шеек диаметром 45 мм рекомендуемым номинальным размером шпоночных пазов является размер 14. Поэтому в обоих случаях принимаем размер шпоночных пазов 14N9.
Определение типа производства. Пользуясь справочными таблицами, можно установить, что производство серийное. Величина партии деталей:
где N — годовая программа выпуска деталей одного наименования, шт.; а — необходимый запас деталей на складе, дней; m — количество рабочих дней в году (при пятидневной рабочей неделе m = 254).
.
По величине партии в 30 штук можно уточнить, что производство среднесерийное.
Выбор вида заготовки. В связи с небольшим объемом производства в качестве заготовки принимают прокат горячекатаный (ГОСТ 2590-91). Заготовки получают путем резки прутка дисковыми пилами. Диаметр прутка выбирают по наибольшему диаметру детали с учетом припуска на обработку и стандартного ряда диаметров согласно ГОСТ 2590-91. Длина заготовки принята равной 328-0,8.
Рисунок 6.2 – Вал быстроходный
Предварительная разработка технологического маршрута. Серийное производство в настоящее время имеет свои особенности. Широкое распространение в нем получили станки с ЧПУ и промышленные роботы. Использование станков с ЧПУ позволяет сконцентрировать ряд операций на одном рабочем месте.
Оборудование должно иметь возможность его быстрой переналадки на выпуск других деталей, сходных по технологическому процессу с рассматриваемой, т.е. обеспечивать возможность групповой обработки. В качестве оборудования используются в основном станки с ЧПУ.
Разработанный технологический маршрут обработки вала приведен в таблице 6.2. Маршрут и принятое оборудование позволяют обрабатывать ступенчатые валы различного назначения.
Таблица 6.2 – Технологический маршрут механической обработки вала (серийное производство)
Номер операции | Наименование и содержание операции | Эскиз обработки, базирование | Оборудование |
000 | Заготовительная | Круглопильный автомат 8Г642 | |
010 | Фрезерно-центровальная операция: фрезерование торцов и центрование | Фрезерно-центровальный полуавтомат МР-76М |
Продолжение таблицы 6.2
020 | Токарная операция: обработка со стороны выходного конца вала | Токарно-винторезный станок 16К20Т1 | |
030 | Токарная операция: обработка со стороны резьбового конца вала | Токарно-винторезный станок 16К20Т1 | |
040 | Фрезерная операция: фрезерование шпоночных пазов | Вертикально-фрезерный станок 6Р13Ф3 и револьверная головка |
Продолжение таблицы 6.2
045 | Термическая операция: цементация, закалка, отпуск | Печь цементационная Ц105, печь отпускная | |
050 | Шлифовальная операция: шлифовать поверхности Ø50к6, Ø45h8 и торец | Шлифовальный станок 3Т161Е | |
060 | Шлифовальная операция: шлифовать поверхности Ø45n7, Ø50k6 и торцы | Шлифовальный станок 3Т161Е | |
070 | Слесарная операция: калибрование резьбы | Верстак слесарный | |
075 | Моечная операция | Моечная машина | |
080 | Контрольная операция: контроль всех диаметров и длин и шпоночных пазов | Стол ОТК |
studfiles.net
6.4. Изготовление вала в условиях массового производства
Один из вариантов технологического маршрута изготовления вала в условиях массового производства, содержащий эскизы обработки с рассчитанными допусками, приведен в таблице 6.3.
Таблица 6.3 – Технологический маршрут механической обработки вала (массовое производство)
Номер операции | Наименование и содержание операции | Эскиз обработки, базирование | Оборудование |
000 | Заготовительная операция | Пресс штапмовочный | |
010 | Фрезерно-центровальная операция: фрезерование торцев и центрование | Фрезерно-центровальный полуавтомат МР-76М | |
020 | Токарная операция: черновая обработка со стороны выходного конца вала | Токарный многорезцовый полуавтомат 1Н713 |
Продолжение таблицы 6.3.
030 | Токарная операция: черновая обработка со стороны резьбового конца вала | Токарный многорезцовый полуавтомат 1Н713 | |
040 | Токарная операция: чистовое точение со стороны выходного конца вала | Токарный многорезцовый полуавтомат 1Н713 | |
050 | Токарная операция: чистовое точение со стороны резьбового конца вала | Токарный многорезцовый полуавтомат 1Н713 | |
060 | Фрезерная операция: фрезерование шпоночного паза на выходном конце вала | Шпоночно-фрезерный станок 692Р |
Продолжение таблицы 6.3.
070 | Фрезерная операция: фрезерование шпоночного паза на ступени под шестерню | Шпоночно-фрезерный станок 692Р | |
080 | Фрезерная операция: фрезерование резьбы М42х1,5-7h | Резьбофрезерный полуавтомат 5К63 | |
090 | Фрезерная операция: фрезерование паза 6+0,1 | Шпоночно-фрезерный станок 692Р | |
095 | Гальваническая операция: меднение резьбового конца вала | Ванна гальваническая | |
100 | Термическая операция: цементация+закалка+отпуск | Безмуфельный агрегат |
Продолжение таблицы 6.3.
110 | Шлифовальная операция: шлифование ступени вала и торца | Торцекруглошлифовальный полуавтомат 3Т161Е | |
120 | Шлифовальная операция: шлифование ступеней вала и торцов | Торцекруглошлифовальный полуавтомат 3Т161Е | |
130 | Шлифовальная операция: шлифование ступени вала | Круглошлифовальный станок 3М153Е | |
140 | Резьбонарезная операция: калибрование резьбы | Резьбонарезной станок 5Д07 | |
145 | Моечная операция: промывка детали | Моечная машина | |
150 | Контрольная операция | Стол ОТК |
Заготовки деталей обрабатываются на автоматической линии. Планировка линии приведена на рисунке 6.3.
Автоматическая линия обработки вала редуктора состоит из двух участков: участка обработки вала до термообработки и участка обработки вала после термообработки. Металлорежущие станки 2 установлены по ходу технологического процесса. Для загрузки заготовок и разгрузки деталей использованы магазины 3, в которых заготовки и детали находятся в ориентированном положении. Загрузка магазинов в начале линии производится оператором, а передача деталей от станка к станку — с помощью шагового транспортера 5. Непосредственная загрузка станков осуществляется двурукими автооператорами 4. Уборку стружки обеспечивает шнековый транспортер 1. В связи с тем, что обработка вала ведется с двух сторон, для исключения кантователей, усложняющих линию, применен следующий подход: токарные и шлифовальные станки, обрабатывающие деталь с различных сторон, установлены по принципу «фронт к фронту».
В таблице 6.4 приведены схемы технологических процессов изготовления первичного вала коробки передач, вторичного вала и промежуточного вала. Анализ таблицы показывает, что ступенчатые шлицевые валы и валы с зубчатыми венцами обрабатываются по единой технологической схеме. Основное различие при изготовлении заключается в том, что у шлицевого вала фрезеруют или накатывают шлицы, у вала- шестерни нарезают зубчатый венец.
Для обеспечения заданных точности и шероховатости отдельных поверхностей детали вводят доводочные операции: микрофиниширование или полирование.
studfiles.net
1. Технология изготовления валов
1.1. Способы получения заготовок валов
В мелкосерийном и единичном производстве, а также при изготовлении валов с незначительными перепадами ступеней, заготовки валов получают разрезанием прутков. При увеличении объема производства, а также при изготовлении валов со сложной конфигурацией и значительными перепадами диаметров ступеней заготовки целесообразно получать литьем и методами пластической деформации (ковка, штамповка, периодическая прокатка и т.п.). Это позволяет уменьшить припуски на обработку, трудоемкость и стоимость обработки резанием.
Выбор способа получения заготовки производится на основании технико-экономического анализа. Иногда применение кованых и штампованных заготовок объясняется повышенными требованиями к механическим свойствам сплавов.
В заготовительных цехах и отделениях обычно выполняют правку заготовок, обработку (обдирку) прутков по наружной поверхности и разрезание.
Правка устраняет искривление оси заготовки, она производится на прессах или специальных станках. Для обработки наружной поверхности прутков применяют специальные станки.
В кузнечно-прессовых цехах применяется резка прутков на прессах и ножницах. Эти способы высокопроизводительны, но не обеспечивают высокой точности. Торец заготовки оказывается неровным.
Дисковые пилы (рис. 1.1.,а,б) режут прутки по одному и в пакете.
Рис. 1.1. – Схема разрезки прутков дисковой пилой.
Приводные ножовки режут прутки ножовочным полотном, которое совершает возвратно-поступательное движение. Ширина реза меньше, чем при использовании дисковых пил, что важно при разрезании дорогостоящих материалов, однако, производительность ножовок ниже.
Ленточные пилы (рис. 1.2.) имеют высокую производительность, но отличаются сравнительно высокой стоимостью режущей ленты.
Рис. 1.2. – Схема разрезки прутка ленточной пилой.
1.2. Типовой техпроцесс обработки ступенчатых валов в крупносерийном или массовом производстве
Этот ТП включает следующие операции:
Обработка торцов, центрирование
Токарная обработка (точение) шеек валов
Предварительное шлифование
Фрезерование шпоночных пазов
Фрезерование шлицев
Обработка резьбы
Термообработка
Исправление центровых отверстий
Чистовое шлифование шеек вала
Шлифование шлицев
Калибрование резьбы и зачистка заусенцев
Промывка
Контроль
1.2.1. Обработка торцов вала и центрирование
В единичном и мелкосерийном производствах торцы обрабатывают на токарных и фрезерных станках. Центрирование выполняется на сверлильных, токарных, револьверных и горизонтально-расточных станках.
Центрирование может производиться или двумя инструментами (спиральным сверлом и зенкером), или же одним комбинированным центровочным сверлом. Угол конуса сверла обычно равен 600, однако, для тяжелых заготовок валов его увеличивают до 750 или 900.
В ряде случаев у режущих инструментов выполняют дополнительную фаску с углом 1200, которая предохраняет центровое отверстие от забоин при случайном повреждении торцов вала.
В серийном и массовом производствах применяют фрезерно-центровальные полуавтоматы, на которых одновременно фрезеруются 2 торца (позиция 2 на рис. 1.3.), затем центруются 2 отверстия (позиция 3).
Рис. 1.3. – Схема обработки вала на фрезерно-центровальном полуавтомате.
studfiles.net
2.1.10. Пример технологического процесса изготовления корпусной детали
Общая структура технологического процесса при обработке корпусных деталей приведена в разделе 2.1.5. Пример технологического процесса изготовления корпусной детали, представленной на рис.2.36, приведен в таблице 2.2.
2.2. Технология изготовления ступенчатых валов
2.2.1. Служебное назначение, конструктивное исполнение, требования к точности, методы получения заготовок, материалы, базирование
Валы предназначены для передачи крутящего момента и монтажа на них различных деталей. Конструктивно валы подразделяются на гладкие, ступенчатые, фланцевые и валы-шестерни. Одной из основных характеристик валов является жесткость. Вал считается жестким, если отношение длины к диаметру менее 12-15. При большем отношении вал является нежестким.
Геометрически, валы представляют собой сочетание цилиндрических, конических, резьбовых, зубчатых, шлицевых, шпоночных поверхностей. При переходе от одной ступени к другой предусматриваются канавки или галтели. Обработка галтелей является более сложной операцией, чем обработка канавок. Поэтому для повышения технологичности изготовления поверхности перехода между ступенями рекомендуется оформлять в виде канавок. В то же время, с точки зрения повышения усталостной прочности, применение галтелей более предпочтительно.
Сопрягаемые цилиндрические (посадочные) поверхности валов выполняют по 6 – 8 квалитетам с шероховатостью поверхности 0,63 – 2,5 мкм. Отклонения формы и расположения поверхностей определяются служебным назначением изделия и назначаются при конструировании.
Заготовки для валов получают из проката, ковкой, штамповкой, высадкой на горизонтально-ковочных машинах (ГКМ), обжатием на ротационно-ковочных машинах, поперечно-винтовой и поперечно-клиновой прокаткой.
Валы изготавливают из углеродистых и легированных сталей: 45, 40Х, 45ХНМ, 38Х2МЮА и пр. В зависимости от назначения валы подвергают различным видам термической и химико-термической обработки: нормализации, улучшению, закалке, цементации, азотированию и пр.
Базами при обработке валов являются центровые отверстия и посадочные поверхности. Для исключения погрешности базирования ступеней вала по длине используют плавающий передний центр. В этом случае базой является торец заготовки, опорой которого является планшайба поводкового патрона.
2.2.2. Структура технологического процесса
Типовой технологический процесс изготовления валов из проката включает в различном сочетании следующие операции: правку, обдирку и резку проката; обработку центровых отверстий; черновое и чистовое точение; сверление и растачивание центрального отверстия; нарезание резьб; фрезерование шлицев, шпоночных пазов и лысок; нарезание зубьев для вал-шестерни; сверление радиальных отверстий; термообработку; черновое и чистовое шлифование шеек, зубьев, шлицев и резьб; отделочную обработку посадочных поверхностей: суперфиниширование, притирку и полирование; контроль размеров.
2.2.3. Правка, резка и обдирка проката
Правка прокатадиаметром свыше 50 мм осуществляется на прессах пластическим знакопеременным изгибом. Прутки меньшего диаметра правят на роликовых машинах с продольной подачей проката без его вращения (рис. 2.37, а) или с винтовой подачей проката (рис. 2.37, б). В последнем случае правка производится роликами глобоидальной формы, которые расположены под углом к оси проката. При вращении роликов заготовка получает поступательное и вращательное (винтовое движение).
Обдирка проката(грубое точение) производится с целью удаления дефектного слоя. Обдирка производится на бесцентрово-токарных станках. Схема станка представлена на рис. 2.38. Станок работает следующим образом. Заготовка без вращения подается роликами 1 в резцовые головки с резцами 2, 4 и сухарями 5, которые исключают прогиб заготовки от силы резания. Головки установлены на планшайбе на входе и на выходе для черновой и чистовой обдирки. Планшайба вращается вместе с зубчатым колесом 3. Процесс резания осуществляется за счет вращения резцов вокруг заготовки.
Резку прокатаосуществляют на приводных ножовках; пилах: дисковых, ленточных, фрикционных, электрофрикционных, с абразивным кругом; на токарно-отрезных станках; ножницах, прессах. Приводные ножовки разрезают прокат ножовочным полотном, которое прижимается режущей частью к прокату и совершает возвратно-поступательные движения от механического привода. Схемы резки проката дисковой и ленточными пилами представлены на рис. 2.39. Ленточная пила представляет собой бесконечную ленту с зубьями, натянутую на диски, один из которых является приводным. Резка фрикционной пилой производится за счет сил трения. Пила представляет собой тонкий стальной диск, который вращается со скоростью до 150 м/сек. При контакте с металлом он от трения нагревается и плавится. Резка электро-фрикционной пилой осуществляется за счет совместного действия трения и вольтовой дуги, которая зажигается при подключении пилы и проката к разным полюсам источника электрического тока. Схема резки проката на токарном сверлильно-отрезном станке представлена на рис. 2.39, г.
studfiles.net
Маршрутная технология изготовления детали
ФЕДЕРАЛЬНОЕ АГЕНСТВО ПО ОБРАЗОВАНИЮ
Государственное общеобразовательное учреждение высшего профессионального образования
Контрольная работа по дисциплине
“Основы технологии машиностроения”
Выполнил: студент гр.
Проверил преподаватель:
Томск 2011 г.
Анализ технологического процесса
и технологичности детали
В результате анализа можно сказать, что для данного типа производства (мелкосерийное) заготовка выбрана правильно – круглый прокат Ø54 ГОСТ 2590-88. Данный вид заготовки, является оптимальным в мелкосерийном типе производства, не усложняет заготовительную операцию и является экономически обоснованным.
Черновые, чистовые и промежуточные базы выбраны с соблюдением принципа единства баз. На одной из первых операций изготавливаются центровые отверстия, которые и обеспечивают принцип единства баз.
Для достижения заданной точности детали последовательность операций и переходов выбрана рационально. Параметры установленного оборудования соответствует требованиям операций. В основном применяется универсальное оборудование и оснастка, что и подтверждает правильность выбора в мелкосерийном или в единичном производстве.
Применяемый режущий инструмент технологичность детали обеспечивает. Технологический процесс на операциях соблюдается, но качество обработки напрямую связан с квалификацией персонала.
Деталь изготавливается из стали 40Х ГОСТ 4543-71. Для обработки заготовки применяем режущий инструмент с твердосплавными пластинами из ВК8, ВК6.
Этот материал используется для деталей, которые имеют высокую прочность и вязкость, износостойкость. Также данная сталь имеет хорошие пластические свойства и хорошо переносит ударные нагрузки на изгиб.
Деталь в целом является достаточно технологичной, имеет хорошие базовые поверхности. Обрабатываемые поверхности являются легкодоступными.
Выбор заготовки
Выбор заготовки осуществляется исходя из назначения и конструкции детали, материала, технических требований, масштаба и серийности выпуска, а также экономичности изготовления. Выбрать заготовку – значит установить способ ее получения, наметить припуски на обработку каждой поверхности, рассчитать ее размеры и указать допуски на неточность изготовления.
Так как тип производства мелкосерийный или единичный, а деталь имеет небольшие габариты и массу, то нам необходимо использовать круглый прокат нормальной точности.
Прокат разрезается на заготовки необходимой длины на токарном универсальном станке.
разработка операционных
технологических карт
Проектирование технологических процессов (ТП) механической обработки начинается с изучения служебного назначения детали, технических требований к ней, норм точности и программы выпуска, анализа возможности предприятия по обработке данной детали.
Проектирование ТП представляет собой многовариантную задачу, правильное решение которой требует проведения ряда расчетов. В начале проектирования предварительно устанавливаются виды обработки отдельных поверхностей заготовки и методы достижения их точности, соответствующие требованиям чертежа, серийности производства и существующего на предприятии оборудования.
При низкой точности исходных заготовок ТП начинается с черновой обработки поверхности, имеющей наибольшие припуски. При этом в самую первую очередь снимается припуск с тех поверхностей, на которых возможны дефекты с целью скорейшего отсеивания брака.
Дальнейший маршрут строится по принципу обработки сначала грубых, а затем более точных поверхностей. Наиболее точные поверхности обрабатываются в последнюю очередь.
В конце маршрута выполняются и второстепенные операции (сверление малых отверстий, нарезание крепежной резьбы, снятие фасок, заусениц и т.д.). Наиболее легко повреждаемые поверхности обрабатываются на заключительной стадии ТП.
При требовании закалки детали все второстепенные поверхности обязательно обрабатываются окончательно до закалки, точные поверхности – предварительно, но не грубее девятого квалитета. Окончательная обработка поверхностей с точными размерами производится после термических операций.
Маршрутная технология изготовления детали «Вал» представлена ниже, где подробно описана вся последовательность обработки детали в цехе ремонтно-механического завода. На каждую операцию указана технологическая оснастка (приспособления, мерительный инструмент) и технологическое оборудование. Приведем маршрут обработки в таблице:
Операция | Содержание и наименование операций | Станок, оборудование | Оснастка |
005 Заготовительная. | Отрезать заготовку от прутка Ø 54 мм l=302 мм. | Абразивно-отрезной 8В262 | Тиски |
010 Токарная | Подрезать и центровать торец, точить Ø40h6 под шлифование, Ø45h6 под шлифование, Ø52 окончательно, проточить две канавки b=3мм и одну канавку b=1,9+0,25 и Ø42,5-0,34; точить фаску 1×45°. Сверлить отверстие Ø30Н7 под шлифование. | Токарный 16Т02П | |
015 Токарная | Подрезать и центровать второй торец, выдерживая размер 300h22, точить Ø40r6 под шлифование, Ø45h6 под шлифование, Ø52 окончательно и точить фаску 1×45°; проточить 2 канавки b=3мм, канавку b=1,9+0,25 и Ø37,5-0,34, канавку b=1,9+0,25 и Ø42,5-0,34. Сверлить отверстие Ø 30Н7 под шлифование. | Токарный 16Т02П | |
020 Слесарная | Зачистить заусенцы, острые кромки притупить | Шабер, напильник | |
025 Термическая | Закалить до твердости 28..32HRC | Печь | |
030 Шлифовальная | Шлифовать наружные участки вала Ø40r6, Ø40h8, Ø45h6 и внутренние участки вала Ø30Н7 выдерживая размеры окончательно. | Круглошлифовальный 3У10В | Центры, хомутик, поводок |
035 Слесарная | Зачистить заусенцы | Шабер, напильник | |
040 Фрезерная | Фрезеровать два шпоночных паза b=12 мм, выдерживая размер 4+0,12 окончательно. | Шпоночно-фрезерный 6930 | Станочные тиски |
045 Слесарная | Зачистить заусенцы | Шабер, напильник | |
050 Промывочная | Промыть деталь по типовому тех.процессу | Моечная машина | |
055 Гальвоническая | Химическое оксидирование | Ванна | |
060 Контрольная | Технический контроль | Плита | Штангельциркуль ШЦ-1, микрометр, КИМ типа ВЕ155 |
Список литературы
Должиков В.П. Разработка технологических процессов механообработки в мелкосерийном производстве:Учебное пособие.-Томск: Изд-во ТПУ, 2003.-324с.
Скворцов В.Ф. Выбор технологических баз при изготовлении деталей: Учебное пособие.-Томск: Изд-во ТПУ, 2007.-56с.
Справочник технолога – машиностроителя. В 2 – х т./Под ред. А. Г.
Косиловой и Р. К. Мещерякова.- М.: Машиностроение, 1985 г.
studfiles.net
Разработка технологического процесса обработки ступенчатого вала
Курсовой проект
По дисциплине Технология машиностроения
На тему
Разработка технологического процесса обработки ступенчатого вала
Студент Михайлов А.С.
Москва, 2010г
Содержание
Введение
1. Служебное назначение и технические требования детали
2. Технологический контроль чертежа и анализ технологичности конструкции
3. Определение типа производства
4. Выбор способа получения заготовки
5. Проектирование маршрутной технологии обработки детали
6. Выбор технологических баз для механической обработки
7. Выбор оборудования, оснастки и средств автоматизации
8. Расчет припусков на механическую обработку
9. Расчет режимов резания и норм времени
10. Маршрутная технологическая карта
11. Обоснование эффективности технологического процесса
Список использованной литературы
Введение
В современном машиностроительном комплексе, когда качество продукции является стабильным показателем работы большинства предприятий, ввиду использования ими однотипного оборудования и инструмента, на первый план стратегических целей компаний выходят скорость производства продукции, и ее конкурентоспособная себестоимостью.
Данные цели достигаются применением комплексных мероприятий направленных на снижение затрат предприятия среди которых можно выделить такие как:
-применение высокопроизводительного инструмента повышенной твердости, комбинированного инструмента и инструмента со сменными многогранными пластинами, позволяющих снизить затраты на изготовление изделий;
-применение принципа Just-in-time (точно вовремя), заключающегося в том, что во время производственного процесса необходимые детали оказываются на производственной линии строго в тот момент, когда это нужно и в строго необходимом количестве, что позволяет снизить складские расходы;
– применения принципа «автономизации», или автоматизации с использованием интеллекта, когда процесс настроен таким образом, что обработка изделия ведется до тех пор, пока оборудование не подаст сигнал об ошибке и не остановит процесс, что позволяет одному оператору обслуживать одновременно несколько станков сводя к минимуму риск производства бракованной продукции;
– также в последнее время все большую популярность приобретают система канбан, позволяющая снизить перепроизводство; система poka-yoke(пока-ёкэ) или защита от ошибок, исключающая влияние человеческого фактора; 5S – правильная и удобная организация рабочего места, исключающая лишние предметы и требующая строго поддерживаемого порядка. А также многие другие.
В данной курсовой работе рассмотрен технологический процесс обработки изделия – «Вал ступенчатый». Валы различны по служебному назначению, конструктивной форме, размерам и материалу. Несмотря на это, при разработке технологического процесса изготовления валов приходится решать многие однотипные задачи, поэтому целесообразно пользоваться типовыми процессами, которые созданы на основе проведенной классификации.
Целью курсовой работы является разработка технологического процесса производства конкурентоспособного изделия с применением современного точного оборудования и высокопроизводительного инструмента, с требуемой годовой программой производства.
Задание
Материал изделия – сталь 35; твердость 207 HB; годовая программа выпуска N= 20 000 , L= 240-0,46 ; l1 = 145-0,4 ; l4 = 25-0,21 ; l5 = 58-0.3 ; l6 = 89-0.35 ; l7 = 39-0.25 ; d1 = 86-0.035 ; d2 = 69-0.03 ; d3 = 47-0.025 ;
; .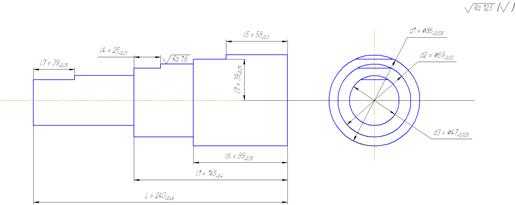
Рис. 1. Схема вала с данными задания
mirznanii.com
Технологический процесс изготовления валов.
В зависимости от конструкции и размера, требуемой точности и объема выпуска строится маршрут обработки вала. Валы, размером до 150 мм длиной обрабатываются полностью на токарно-револьверных станках или автоматах до их отрезки после выполнения всех черновых и чистовых операций.
Прутковые и штампованные заготовки длиной более 150 мм обрабатывают по следующему маршруту:
1. Одновременное или поочередное фрезерование торцов.
2. Одновременная или поочередная зацентровка торцов.
3. Черновое обтачивание наружных поверхностей.
4. Чистовое обтачивание наружных поверхностей.
5. Предварительное шлифование шеек.
6. Нарезание шлицев и получение шпоночных пазов.
7. Сверление отверстий (если предусматривается конструкцией).
8. Нарезание резьбы.
9. Термическая обработка (если предусматривается).
10. Окончательное шлифование шеек.
При обработке нежестких валов в маршрут могут вводиться дополнительные операции, такие как протачивание и шлифование шейки под люнет или промежуточные правки заготовки, если они допускаются техническими требованиями.
Фрезерование торцов и их зацентровка в крупносерийном и массовом производстве может выполняться на фрезерно-центровальных полуавтоматах МР-71 и МР-73 или МР-77 и МР-78. На этих станках одновременно производится обработка двух заготовок.
Обработка торцов может производиться на двухсторонних торцефрезерных автоматах А-981М и на двухсторонних центровальных автоматах А-982М. Раздельная обработка торцов может производиться на горизонтально- и продольно-фрезерных станках, на одно- или двухсторонних центровальных станках.
В единичном или мелкосерийном производстве выполнение этих операций может производиться на токарных и револьверных станках.
Наружное черновое и чистовое обтачивание поверхности валов в зависимости от объема выпуска может производиться на токарных, токарно-копировальных, одношпиндельных горизонтальных многорезцовых станках (полуавтоматах), на одно- или многошпиндельных вертикальных полуавтоматах, на станках с ЧПУ.
Обработка на многорезцовых полуавтоматах обеспечивает точность в пределах 11 – 12 квалитетов. При тщательной наладке станка, правильном выборе инструмента точность может быть повышена до 6 – 8 квалитета.
Одновременное черновое и чистовое обтачивание допускается, если обеспечивается заданная точность и не увеличивается шероховатость обрабатываемой поверхности.
Многорезцовое обтачивание целесообразно применять при обработке длинных шеек валов и большом перепаде диаметров ступеней вала. Однако, при данном методе возрастает Тпз, время на техническое обслуживание, на настройку и поднастройку системы.
При увеличении количества резцов в наладке возможно возникновение вибрации, неравномерный износ режущего инструмента и др. Поэтому в ряде случаев целесообразнее производить обработку на гидрокопировальных полуавтоматах, позволяющих работать на более высоких скоростях резания и подачах. При небольших затратах Тпз и времени технического обслуживания затраты на настройку и под настройку сокращаются в 2 – 3 раза по сравнению с многорезцовым обтачиванием. Обработка на гидрокопировальных станках позволяет получить 6 – 8 квалитет и применяется обычно при чистовой обработке нежестких валов. Поэтому в каждом конкретном случае необходимо производить сравнение варианта обработки на многорезцовом и гидрокопировальном станках.
Обработка на вертикальных полуавтоматах производится в патроне или в центрах, при этом на каждой позиции может производиться или полная обработка заготовки или заготовка обрабатывается при перемещении ее из позиции в позицию. Точность обработки на вертикальных полуавтоматах – 11 квалитет.
Примеры наладок многорезцовых горизонтальных и вертикальных полуавтоматов приведены в [5].
Фрезерование шпоночных пазов на валах может производиться на шпоночно-фрезерных станках пальцевой фрезой или на горизонтально-фрезерных – дисковой фрезой в зависимости от конструкции паза.
Шпоночные пазы можно получать на вертикально- или горизонтально-фрезерных станках, работающих по маятниковому методу путем снятия пальцевой фрезой за каждый рабочий ход определенного слоя материала. При данном методе обеспечивается высокая точность обработки. Схема обработки приведена на рис, где t – припуск, снимаемый за один рабочий ход; n – общий припуск.
Сквозные шпоночные канавки наиболее эффективно обрабатывать дисковой фрезой напроход.
В единичном и мелкосерийном производстве сквозные шпоночные канавки могут обрабатывать на строгальных станках.
Нарезание шлицев на валах может производиться шлицефрезерованием, шлицестроганием, протягиванием, накатыванием. Фрезерование производится на шлицефрезерных или зубофрезерных станках червячными фрезами. При нарезании шлицев на валах диаметром до 60 мм их обработка производится за один переход, при большем диаметре – за два перехода – черновой и чистовой. Предварительное нарезание шлицев производится до термической обработки, окончательное – после термической обработки. При наличии термической обработки нарезание производится после предварительного шлифования шеек, а при отсутствии термической обработки – после чистового шлифования шеек. Нарезание шлицев может производиться фасонными дисковыми фрезами на горизонтально-фрезерных станках с применением делительных приспособлений. Данный способ производительнее в 3 – 4 раза способа шлицефрезерования.
Шлицепротягивание производится на горизонтально-протяжных станках с помощью специальных приспособлений и протяжек, профиль зубьев которых соответствует профилю протягиваемых шлицев. Каждый шлиц нарезается поочередно в двух диаметрально противоположных направлениях двумя блоками протяжек с последующим поворотом для нарезания следующих шлицев.
Шлицестрогание производится набором специальных фасонных резцов, устанавливаемых в резцовой головке. Количество резцов и их профиль соответствуют профилю получаемых шлицев. Все резцы одновременно нарезают шлицы, получая радиальную подачу. Метод высокопроизводителен и применяется в крупносерийном и массовом производстве. Производительность шлицепротягивания или шлицестрогания в 5 – 8 раз выше шлицефрезерования.
Накатывание шлицев может производиться на специальных станках и гидравлических прессах многороликовыми головками. Накатывают эвольвентные и треугольные шлицы модулем до 3, диаметром 20 – 100 мм, длина зуба или шлица – Lz = 120 мм. Накатывание в ряде случаев позволяет отказываться от термической обработки и последующей механической обработки. Шероховатость поверхности в пределах Ra = 0,40 – 0,20 мкм. Производительность метода приблизительно в 10 раз выше шлицефрезерования.
Сверление отверстий в валах может производиться на одно- или многошпиндельных сверлильных станках. Выбор станка определяется количеством отверстий и их расположением на валу.
Выбор метода нарезания резьбы на валах определяется типом производства и требуемой точностью. В крупносерийном и массовом производстве резьбы 6 квалитета могут быть получены на резьботокарных полуавтоматах. Резьбы 8 – 11 квалитетов могут быть получены на резьбофрезерных или резьбонакатных станках.
В условиях единичного и мелкосерийного производства резьбы 6 квалитета точности могут быть получены на токарно-винторезных станках с помощью резцов или вихревым методом с помощью специальных резцовых головок.
Резьбы на валах могут быть получены с помощью плашек различной конструкции, резьбонарезных головок, резьбовых резцов, гребенчатых фрез. Нарезание плашками обеспечивает 8 – 9 квалитет и ниже. Применение резьбонарезных головок обеспечивает повышение производительности в 3 – 4 раза по сравнению с нарезанием плашкой, а точность может быть получена в пределах 6 квалитета. Нарезание резьбы может производиться дисковыми или групповыми гребенчатыми фрезами, обеспечивая 8 –9 квалитет и выше.
В крупносерийном и массовом производстве резьбы 6 квалитета точности могут быть получены путем накатывания плоскими плашками или роликами. Производительность метода в 15 – 20 раз выше по сравнению с накатыванием головками.
Резьбошлифование применяется для труднообрабатываемых материалов или когда к резьбе предъявляются высокие требования по точности. Резьбы шлифуют на специальных резьбошлифовальных станках, а в единичном и мелкосерийном производстве можно производить на токарных станках с помощью специальных приспособлений.
В качестве чистового и окончательного метода обработки поверхности валов наиболее широко применяется шлифование с продольными или поперечными подачами. Шлифование закаленных шлицев может производиться фасонными кругами или отдельно шлифуют боковые поверхности и впадины шлицев. Шлифование фасонным кругом обеспечивает большую точность и производительность.
Обработка на бесцентрово-шлифовальных станках производится продольной подачей на проход или врезанием – поперечной. Жесткость бесцентрово-шлифовальных станков примерно в 1,5 – 2 раза выше круглошлифовальных и обеспечивает повышение производительности примерно в 1,5 – 2 раза. Бесцентровое шлифование эффективно исправляет некруглость (с исходной некруглости 0,3 мм может быть получена некруглость 0,0025 мм). Точность обработки – 5 – 6 квалитет, шероховатость Ra = 0,32 – 0,20 мкм.
1. Шлифующий круг. 2. Заготовка. 3. Ведущий круг. 4. Опорный нож. |
Рассмотрим схему бесцентрового шлифования.
В процессе обработки опорный нож должен регулироваться по высоте так, чтобы обеспечивать необходимое повышение h оси обрабатываемого вала (шейки вала) над центровой линией кругов. Это превышение составляет 0,35¸0,4 диаметра обрабатываемой заготовки, но не более 14 мм. Меньшая или большая величина h приводит к огранке шлифуемой поверхности.
При шлифовании торцев ступеней вала применяют торцокруглошлифовальные станки. Ось круга может располагаться под углом от 8° до 45°. Величина угла определяется в зависимости от снимаемого припуска и шлифуемого диаметра.
Отделочная обработка ступеней валов может производиться также абразивными и алмазными лентами на ленточно-шлифовальных станках, поверхностно-пластическим деформированием путем обкатывания шариками или роликами, алмазным выглаживанием, суперфинишем абразивными или алмазными брусками. При суперфинише брусок совершает осциллирующее движение, возвратно-поступательное и продольное перемещение вдоль оси обрабатываемой заготовки.
Контроль валов.
Контроль валов осуществляется с помощью универсальных измерительных средств, различных калибров и комплексных измерительных устройств.
Контролируются как размеры, так и форма и относительные повороты поверхностей вала.
Рассмотрим некоторые схемы контроля:
а) Отклонение от круглости контролируется с помощью рычажной двухконтактной скобы при установке вала в центрах.
в) Отклонение от соосности опорных шеек контролируется с помощью индикаторов при установке вала на ножевые опоры. |
б) Огранка контролируется с помощью индикатора при установке вала в призму.
г) Радиальное биение размера d относительно опорных шеек определяется индикатором при установке вала в призмы.
д) Торцевое биение вала контролируется индикатором при установке его на призме.
infopedia.su