Твердость алмаза по роквеллу – Алмаз самый твердый из всех минералов, по Роквеллу, шкала Мооса
alexxlab | 11.08.2020 | 0 | Разное
Рекордная твердость: 10 самых твердых материалов на Земле
Алмаз до сих пор остается эталоном твердости: в различных методиках измерения механической твердости материалов он выступает в роли индентора (методы Роквелла, Виккерса) или эталонной поверхности (метод Мооса). Однако есть материалы, твердость которых выходит за «алмазный предел» или вплотную к нему приближается.
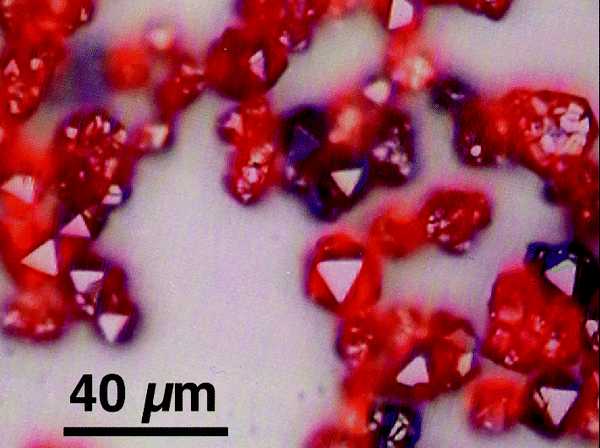
Субоксид бора образует кристаллы-двойники в форме тетраэдров

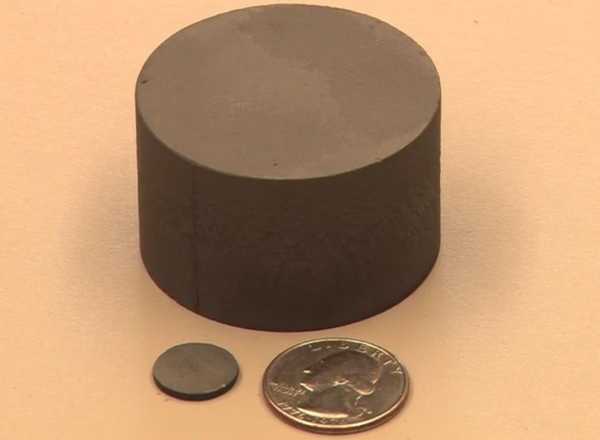

Бор-углерод-кремниевый сплав
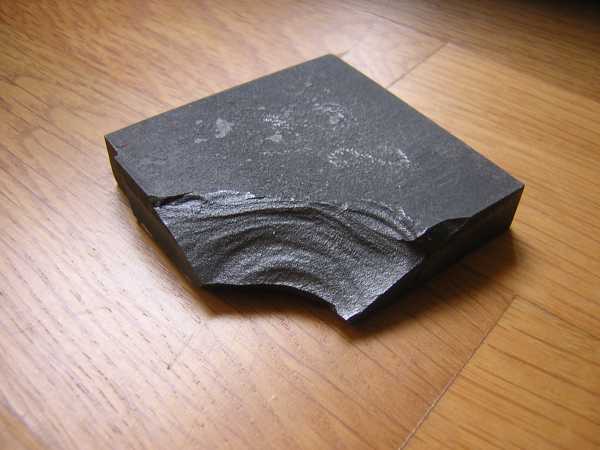
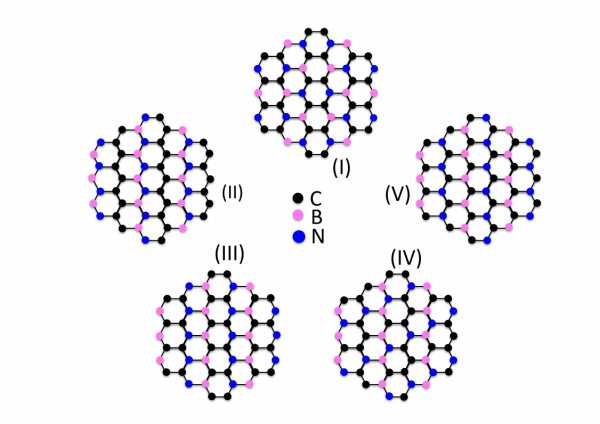

Наноструктурированный кубонит

Плотная гексагональная (вюртцитная) структура нитрида бора

Образец лонсдейлита, обнаруженный в сибирском кратере Попигай — четвертой по размеру астроблеме в мире
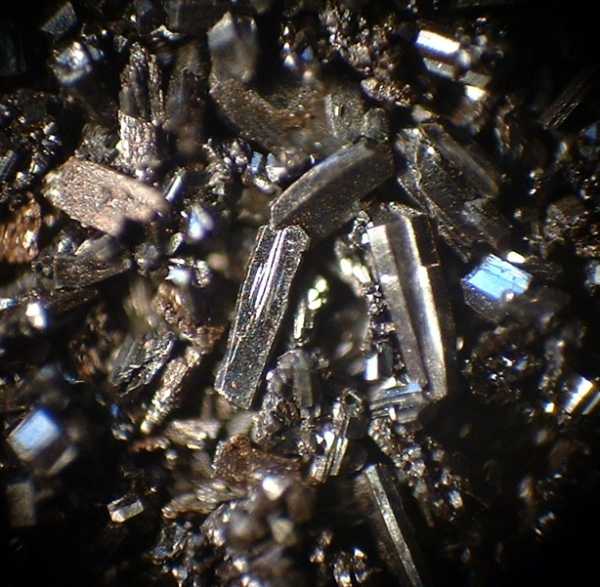
www.popmech.ru
Измерение твердости вдавливанием алмазной по Роквеллу
Рис. 103. Схема прибора для измерения твердости вдавливанием алмазного конуса или стального шарика (измерение по Роквеллу) /—столик для установки образца 2 — маховик 3 — груз 4 — шкала-индикатор, 5—масляный регуля тор 5 — шток с алмазным конусом (шариком) 7 — рукоятка | ![]() |
Измерение твердости вдавливанием алмазного конуса или стального шарика (метод Роквелла) по ГОСТу 9013—59. Твердость по методу Роквелла определяют по глубине вдавливания в испытуемую поверхность стального шарика диаметром 1,588 мм при нагрузке 100 кГ или [c.16]
Содержание задания. Измерить твердость по Бринеллю (шариком 10 мм) и Роквеллу (по шкале С) и указать примерное значение предела прочности испытуемой стали. Объяснить принцип измерения твердости вдавливанием шарика или алмазного конуса. [c.186]
Существует несколько способов измерения твердости вдавливанием по Бринеллю (НВ, мерой твердости служит отношение нагрузки к площади поверхности сферического отпечатка шарика) по Роквеллу (НКА, НКВ, яле – условная величина, обратная глубине вдавливания шарика или алмазного конуса в зависимости от твердости испытуемого металла, с соответствующим отсчетом на приборе Роквелла) по Виккерсу (НУ – определяется отношением нагрузки к квадрату средней длины диагоналей отпечатка от вдавливания четырехгранной алмазной пирамидки).
Кроме метода Бринелля, в СССР стандартизованы еще два метода измерения твердости — метод Роквелла (ГОСТ 9013—59 ) иметод Виккерса (ГОСТ 2999—59). По методу Роквелла о твердости судят по разности глубин, на которые проникает алмазный конус или стальной шарик диаметром 1,5875 мм при действии двух последовательно приложенных нагрузок (предварительной — 10 кГ и общей — 60, 100 или 150 кГ). Для определения числа твердости применяют две шкалы. Шкала В соответствует вдавливанию стального шарика и число твердости при этом обозначается HRB. Для более твердых материалов применяется шкала С (вдавливание алмазного конуса) и число твердости обозначается HR . [c.138]
Для испытаний материалов с низкой твердостью и для измерения твердости мелких деталей и тонких слоев применяются методы измерения твердости при малых нагрузках, например метод Супер-Роквелла (ГОСТ 22975—78). Микротвердость замеряют вдавливанием алмазных наконечников при минимальных нагрузках (до 5 Н). обработка данных производится по методу Виккерса (ГОСТ 9450—76). [c.39]
В технике применяются методы определения твердости, основанные на измерении размеров лунок, получаемых при вдавливании в поверхность испытуемого материала стальных шариков, алмазных конусов или призм (твердость по Бринеллю, по Роквеллу, по Виккерсу). [c.171]
Приборы, работаюш,пе ио методу Роквелла (вдавливание алмазного конуса), применяют в основном для измерения высокой твердости. Недостаток этого метода — относительно невысокая точность измерения, но этот метод позволяет получить числовое значенпе твердости испытываемого изделия в 3—4 раза быстрее, чем на приборах, работающих по методам вдавливания стального шарика или пирамиды.
Твердость по Роквеллу (шкала А) образцов определяют по ГОСТ 20017-74 вдавливанием алмазного конического наконечника (радиус сферы при вершине конуса 0,2 мм) в испытуемый образец под действием двух нагрузок – предварительной в 100 Н и общей в 590 Н, равной сумме предварительной и дополнительной (490Н) нагрузок число твердости в единицах HRA зависит от глубины внедрения наконечника (чем она больше, тем число твердости меньше). Поверхность или участок поверхности образца, на которых проводят измерение твердости, должны быть отшлифованы. Каждый образец испытывают в трех точках, расположенных по диагонали или наибольшему размеру, на равном расстоянии друг от друга ( 2 мм) и от вершин углов или краев образца (5= 0,5 мм). За показатель твердости партии принимают среднее арифметическое значение твердости образцов, отобранных от партии, округленное до 0,5 единицы HRA. [c.118]
Измерение твердости методом Роквелла. Измерение осуществляют путем вдавливания в испытуемый металл стального шарика диаметром 1,59 мм или конусного алмазного наконечника с углом при вершине 120° (рис. 1.11, б). В отличие от метода Бринелля твердость по Роквеллу определяют не по диаметру отпечатка, а по глубине вдавливания шарика или конуса. [c.39]
Вдавливание производится под действием двух последовательно приложенных нагрузок — предварительной, равной 98,1 Н, и окончательной (общей) нагрузки, равной 981,588,6,1471,5 Н. Твердость определяют по разности глубин вдавливания отпечатков. Для испытания твердых металлов необходима нагрузка 1471,5 Н, а вдавливание стальным шариком нагрузкой 981 Н производят для определения твердости незакаленной стали, бронзы, латуни и других мягких материалов. Испытание сверхтвердых материалов производят алмазным наконечником нагрузкой 588,6 Н. Глубина вдавливания измеряется автоматически, а твердость после измерения отсчитывается по трем шкалам А, В, С. Твердость (число твердости) по Роквеллу обозначается следующим образом
Широко известно измерение твердости по глубине отпечатка, получаемого при вдавливании алмазного конуса или стального шарика — метод Роквелла. Определение твердости осуществляется с помощью конусного твердомера (ТР) по ГОСТ 9013-59. Этот метод позволяет изменять нагрузку в широких пределах без изменения значений твердости. Прибор, предназначенный для измерения твердости по Роквеллу (рис. 2.8), имеет столик 4, установленный в нижней части неподвижной станины. В верхней части станины укреплены индикатор 8 и шпиндельный узел 7, в котором имеется наконечник с алмазным конусом 6 (с углом при вершине 120°) или со стальным шариком. На индикаторе 8 нанесены две шкалы (черная и красная) и имеются две стрелки — большая (указатель твердости), вращающаяся по шкале, и маленькая, предназначенная для контроля предварительного нагружения, сообщаемого вращением маховика 3. [c.29]
Твердость следует измерять не менее чем в трех точках (особенно алмазным конусом), т. е. не менее трех раз на одном образце. Для расчета лучше принимать среднее значение результатов второго и третьего измерений и не учитывать результат первого измерения. Для определения твердости по Роквеллу требуется меньше времени (30-60 с), чем по Бринеллю, причем результат измерения виден на шкале (указан стрелкой). При измерении твердости по Роквеллу остается меньший отпечаток на поверхности детали. Твердость очень тонких слоев металла (толщиной менее 0,3 мм) при нагрузках 588,4 и 1471 Н (60 и 150 кгс) измерять нельзя, так как алмазный конус проникает на глубину, превышающую толщину этих слоев. Вместе с тем с увеличением твердости измеряемого материала глубина отпечатка уменьшается, вследствие чего снижается точность измерения (особенно металлов твердостью более 60 HR ). Для этих целей иногда применяют приборы типа суперроквелл (тип ТРС) по ГОСТ 22975-78 или Виккерс (тип ТВ) по ГОСТ 2999-75, с помощью которых измеряют твердость при меньшей нагрузке и с меньшей глубиной вдавливания. Предварительная нагрузка при этом составляет 29,42 И (3 кгс). Каждое деление шкалы индикатора такого прибора соответствует глубине вдавливания, равной 1 мкм. Поэтому чувствительность данного прибора заметно выше.
Твердость по Роквеллу. Этот метод измерения твердости (ГОСТ 9013-59) наиболее универсален и наименее трудоемок. Здесь не нужно измерять размеры отпечатка, так как число твердости отсчитывают непосредственно по шкале твердомера. Число твердости зависит от глубины вдавливания наконечника, в качестве которого используют алмазный конус с углом при вершине 120° или стальной шарик диаметром 1,588 мм. Нагрузку выбирают в зависимости от материала наконечника. Для различных комбинаций нагрузок и наконечников прибор Роквелла имеет три измерительных шкалы А, В, С. Твердость по Роквеллу обозначают цифрами, определяюш ими уровень твердости, и буквами HR с указанием шкалы твердости, например 70 HRA, 58 HR , 50 HRB. [c.54]
Поверочная схема для средств измерений твердости металлов, утвержденная ВНИИМ (рис. 60), предусматривает наличие эталонных приборов для измерений твердости металлов тремя стандартизированными методами статического вдавливания наконечников стального шарика (по Бринеллю) алмазного конуса и стального шарика (по Роквеллу) и алмазной пирамиды (по Виккерсу). [c.121]
Требования к приборам для определения твердости металлов вдавливанием алмазной пирамиды (по методу Виккерса) и правила их поверки изложены в ГОСТ 7038—63, ГОСТ 2999—59, ГОСТ 9377—63 и в инструкции 235—56 По поверке приборов для измерения твердости металлов по методам Бринелля, Роквелла и Виккерса .
Определение твердости по методу Роквелла основано на вдавливании в исследуемый материал стального шарика или алмазного конуса и последующем измерении глубины вдавливания (рис. 3.3). В зависимости от величины нагрузки и формы индентора используют две шкалы красную В или черную С. Стрелка циферблата указывает величину ЮО-Л по красной шкале при измерении шариком, где h -глубина вдавливания индентора, 100 и 130 число делений на щкалах С и В соответственно. Величину твердости определяют по индикаторной шкале, каждое деление которой соответствует глубине вдавливания в 2 мкм. [c.72]
В технике применяются методы определения твердости, основанные на измерении размеров лудок, получаемых при вдавливании в поверхность испытуемого материала стальных шариков, алмазных конусов или призм (твердость по Бринеллю, по Роквеллу, по Виккерсу). Соответственно для иллюстрации приведем метод определения твердости по Бринеллю, в котором [c.138]
Измерение твердости. Контроль твердости колец и тел качения проводится по Роквеллу HR и HRA (ГОСТ 9013) при нагрузках соответственно 1500 и 600 И, по Виккерсу HV (ГОСТ 2999) при нагрузках 10, 20, 50 и 100 Н и Суппер-Роквеллу 40. .. 86 HRN 30 при нагрузке 3(Ю Н путем вдавливания алмазного наконечника в поверхность испытуемой детали. Основной мерой твердости, указываемой в технической документации на производство подшипников, является характеристика HR измерения по Роквеллу при нагрузке 1500 Н считаются прямым методом, остальные методы относятся к косвенным. Перевод чисел твердости, полученных в результате косвенных измерений, на значения по шкале HR приведены в табл. 4.12. [c.330]
Измерение твердости колец производится на их торцах. Минимальное расстояние от центра отпечатка до края кольца и минимальная ширина торцовой поверхности колец должны быть не менее указанной в табл. 4.13. Если из-за недостаточной ширины кольца контроль твердости по Роквеллу невозможен, то измерения выполняют по методу Виккерса. Минимальная толщина детали или упрочненного слоя в точке вдавливания алмазного конуса приведена в табл. 4.14. [c.330]
При методе Роквелла твердость испытываемого образца считается обратно пропорциональной глубине вдавливания, т. е. чем глубже получается вдавливание, тем меньше твердость. Твердость по Роквеллу измеряется глубиной вдавливания маленького стального шарика диаметром 1,59 мм (Vie дюйма) при нагрузке 100 кг или же алмазного конуса с углом у вершины 120° и радиусом закругления конуса у вершины, равным 0,2 мм, при нагрузке 150 кг. В некоторых приборах алмазный конус заменен алмазной пирамидой с углом при вершине в 136° между двумя противолежащими гранями. Это дает возможность заменить измерение глубины отпечатка измерением его диагонали результат получается точнее. [c.93]
Приборы для измерения твердости по Роквеллу могут быть стационарными и переносными. Основным типом стационарной установки является прибор ТК. Твердость определяется путем вдавливания в образец индентора (шарика диаметром 1,588 мм или алмазного конуса с углом при вершине 120°) под действием двух нагрузок — предварительной и рабочей. Определение числа твердости производится после снятия рабочей нагрузки при остающейся предварительной. Поэтому в конструкции прибора предусмотрен механизм предварительного нагружения, создающий нагрузку 1СЮ0 н (10 кГ), постоянную для всех шкал. Прибор ТК имеет следующие шкалы шкала А — полная нагрузка 600 н ( 60 кГ) индентор — алмазный конус шкала — полная нагрузка 1000 (100 к/), индентор — стальной шарик шкала С — полная нагрузка 1500 (150 кГ), индентор — алмазный конус. Предварительная нагрузка осуществляется поджатием образца к индентору до установки стрелки индикатора в вертикальное положение, рабочая нагрузка прилагается через рычажную систему с отношением плеч 1 20. Глубина отпечатка фиксируется индикатором с увеличением 500. Работа на приборе проста и не требует особой квалификации, производительность высокая. [c.10]
Сущность метода Роквелла (рис. 145, б) заключается в том, что в испытуемый образец вдавливается наконечник (стальной шарик или алмазный конус). Твердость по Роквеллу измеряется в условных единицах, что упрощает расчеты. При этом методе совмещаются операции вдавливания измерительного наконечника и измерения величины отпечатка. [c.159]
Твердость основного металла определяют по ГОСТ 9012—59, ГОСТ 9013—59 или ГОСТ 2999—59, а сварного соединения по ГОСТ 6996—66 на шлифах поперечного сечения шва по линиям, параллельным границе проплавления основного металла, а также пересекающим ось симметрии шва. Для измерения твердости используют приборы типа Виккерса (ГОСТ 2999 — 59), Бринеля (ГОСТ 9012—59 ) или Роквелла (ГОСТ 9013—59), твердомеры микротвердости вдавливанием алмазной пирамиды (ГОСТ 9450—60). [c.109]
Испытание на твердость по Роквеллу проводят вдавливанием алмазного конуса или закаленного стального шарика. Затем измеряют глубину лунки после снятия нагрузки к. Твердость по Роквеллу отсчитывается в отвлеченных единицах по шкале прибора. Прибор имеет три шкалы А, В, С. Твердость закаленной среднеуглеродистой стали, определенная по шкале С, равна приблизительно 62. При измерении твердости по шкалам С и А ис- [c.71]
Измерение твердости по Роквеллу основано на вдавливании в испытуемый материал алмазного конуса с углом при вершине 120°. Вдавливание осуществляется нагрузкой в 60 (шкала А), в 100 (шкала В) или 150 кг (шкала С), соответственно толщине проверяемого образца или твердости поверхностного слоя металла. Приложение основной нагрузки производится уже после то го, как индикатор зафиксирует предварительную нагрузку 10 кг. Число твердости вычисляется по разности глубины предварительного и окончательного вдавливания и обозначается соответственно буквенными символами или Няс- [c.9]
Измерение твердости по Роквеллу требует меньше времени (30—60 с), чем по Бринеллю, причем результат измерения виден на шкале (он указан стрелкой). Кроме того, измерение твердости по Роквеллу оставляет меньший отпечаток на поверхности детали. Твердость очень тонких слоев металла (толщиной менее 0,3 мм) с указанными нагрузками 60 и 150 кгс измерять нельзя, так как алмазный конус проникает на глубину, превышающую толщину этих слоев, и указывает, следовательно, твердость нижележащих областей. Вместе с тем с увеличением твердости измеряемого материала глубина отпечатка уменьшается, вследствие чего понижается точность измерения (особенно для металлов с твердостью более NR 60). Для этих же целей иногда применяют приборы типа супер-роквелл, у которых твердость измеряют с меньшей нагрузкой и с меньшей глубиной вдавливания. Предварительная нагрузка со- [c.178]
При измерении материалов большой твердости проба по Бринелю не дает надежных чисел. В этом случае твердость определяют вдавливанием алмазного конуса на специальном приборе, сконструированном Роквеллом, откуда метод и получил свое название. Числа твердости по Роквеллу имеют своеобразное значение (величина, обратная глубине погружения конуса в материал) и отсчитываются по индикатору, имеющемуся на приборе. Эту твердость условлено обозначать буквой (пли [c.124]
При измерении твердости по Роквеллу наконечник стандартного типа (алмазный конус с углом при вершине 120° или стальной шарик диаметром 1,588 мм) вдавливается в испытуемый образец (деталь). Вдавливание конуса или шарика производится под действием двух последовательно прилагаемых нагрузок — предварительной и основной. Предварительная нагрузка при конусе и шарике равна 10 кгс. Величина основной нагрузки при вдавливании конуса 140 кгс, а шарика 90 кгс. Таким образом полная (общая) нагрузка на конус составляет 10 + 140 = 150 кгс, а на шарик 10 + 90 = 100 кгс. Происходящее при этом углубление наконечника прибора отсчитывается по шкале С, если наконечник — алмазный конус, [c.32]
Измерение твердости алмазным конусом методом Роквелла проводится на специальном приборе путем вдавливания в испытуемую поверхность стального шарика диаметром 1,588 мм (1/16″) или алмазного конусного наконечника с углом при вершине 120°. Твердость определяется по глубине вдавливания под действием двух последовательно прилагаемых нагрузок предварительной — 10 кгс и общей [c.205]
Твердость по Роквеллу измеряют на специальном приборе вдавливанием в испытываемый образец стандартного алмазного конуса с углом при вершине 120° или стандартного стального шарика диаметром 1,588 мм. Прн измерении твердости по Роквеллу образец нагружают в две стадии сначала прикладывают пред- [c.59]
Наиболее простым методом испытания свойств является измерение твердости. Твердостью называют свойство материала оказывать сопротивление деформации в поверхностном слое при местных контактных воздействиях. Различают методы определения твердости по Брпнелю (по диаметру отпечатка шарика) по Роквеллу (по глубине вдавливания алмазного конуса или закаленного шарика) по Виккерсу (для деталей малой толщины или тонких поверхностных слоев твердость определяют по диагонали отпечатка алмазной пирамиды). Схемы этих методов приведены на рис. 47. В некоторых случаях определяют микротвердость отдельных участков металла. Этот метод используют для измерения твердости отдельных зерен или очень тонких слоев. [c.87]
Контроль твердости тел качения. Твердость тел качения диаметром более 4,76 мм контролируют по Роквеллу при нагрузке 150 кГ. При вдавливании алмазного конуса в криволинейные поверхности шариков и роликов измеренные числа твердости HR x имеют относительное значение. Действительная твердость HR с учетом искажающего влияния кривизны шариков и роликов вычисляется по фор.муле [c.411]
Определение твердости металлов по методу Роквелла основано на вдавливании алмазного наконечника конической формы (угол конуса 120°) или стального закаленного шарика диаметром 1,59 мм (1/16″) а поверхность испытуемого образца или изделия. Значения твердости по Роквеллу — отвлеченные числа. Прн испытании твердость отсчитывают по шкалам С, Л и В прибора. Число твердости, измеренной алмазным наконечником под нагрузкой [c.29]
Твердость по Роквеллу измеряется по шкалам А, В, С в условных единицах. Измерение твердости по шкалам А ъ С производится путем вдавливания в испытуемый образец алмазного [c.49]
Твердость по Роквеллу (HRA, HRB и HR ) определяют вдавливанием алмазного индентора (шкалы А и С) или стального закаленного шарика (шкала В) в испытуемую поверхность. Твердость измеряют в условных единицах. В обозначении твердости 50 HR число 50 — твердость, измеренная по шкале С. Методика и условия проведения испытания стандартизованы (ГОСТ 9013—59). [c.93]
Испытание по способу Роквелла (рис. 10, 6) заключается в том, что с помощью пресса в поверхность образца 2 вдавливают стальной закаленный шарик 1 диаметром 1,588 мм кт алмазный конус 3 с углом при вершине 120°. О величине твердости судят по глубине вдавливания шарика или конуса. Числа твердости по Роквеллу HR измеряются в условных единицах и отсчитываются по шкалам прибора, укрепленного на прессе и имеющего три шкалы. Если испытание проводится стальным шариком, то отсчет ведут по шкале В, а твердость обозначают НРВ. При испытании алмазным конусом отсчет вед>т либо по шкале А (твердость обозначается НЯА), либо по шкале С (твердость обозначается НРС). Способ Роквелла удобен простотой отсчета и дает большую точность измерений. [c.25]
Используют следующие методы определения твердости металла проба напильником (метод неточен), проба по цвету искры (заточка изделия ка шлифовальном круге, измерение также неточное), а также определение по Бри-неллю (ГОСТ 9012—59, вдавливание стального шарика в исследуемый металл), по Роквеллу (ГОСТ 9013—59, вдавливание в исследуемый металл алмазного конуса) и по Викерсу (ГОСТ 2999—75, вдавливание в исследуемый материал алмазной пирамиды), а также определение твердости по метолу упругой отдачи по Шору (по высоте отскакивания шарика или бойка от обработанной поверхности). [c.142]
mash-xxl.info
Алмазная пирамида по Роквеллу. Rockwell C-Scal eHardness Number |
Алмазная пирамида по Викерсу. Diamond Pyramid Hardness Number Vickers |
По Бринеллю шарик 10 мм, 3000 кгс. / Brinell Hardness Number 10-mm Ball, 3000-kgf Load |
Твердость по Роквеллу / Rockwell Hardness Number |
Поверхностная твердость по Роквеллу / Rockwell Superficial Hardness Number Superficial Diamond Indenter |
Склероскоп Шора / Shore Scleroscope Hardness Number |
Стандартный шарик / Standard Ball |
Шарик Холтгрина / Hultgren Ball |
Шарик из карбида вольфрама/ Tungsten Carbide Ball |
Шкала А, 60 кгс нагрузки, Алмазный индентер / A-Scale 60-kgf Load Diamond Indenter |
Шкала D, 100 кгс нагрузки, Алмазный индентер / D-Scale 100-kgf Load Diamond Indenter |
Шкала 15-N Scale 15-kgf (кгс) Load |
Шкала 30-N Scale 30kgf (кгс) Load |
Шкала 45-N Scale Нагрузка 45-kgf (кгс) Load |
dpva.ru
Измерение твердости вдавливанием алмазного конуса или стального шарика (метод Роквелла)
По методу Роквелла твердость металлов определяют вдавливанием в испытуемый образец (изделие) стального шарика диаметром 1,588 мм при нагрузке 100 кг или алмазного конуса с углом при вершине 1200 при нагрузке 60 и 150 кг. Схема определения твердости по Роквеллу приведена на рис. 3.
При испытании сначала прикладывают предварительную нагрузку Р0, равную 10 кг, а затем нормальную Р, равную 60, 100 или 150 кг (ГОСТ 9013-59). Разность глубин проникновения шарика или алмаза под нагрузками Р0 и Р (h-h0) характеризует твердость. Чем меньше эта разность, тем тверже испытуемый материал, и, наоборот, чем больше эта разность, тем мягче материал.
Числа твердости по Роквеллу обозначают HR и вычисляют по формуле.
где h0 – глубина внедрения в мм наконечника под действием предварительной нагрузки Р0; h – глубина внедрения наконечника под действием общей нагрузки; К – постоянная величина; для шарика К=0,26 и для конуса К=0,2; С – цена деления циферблата индикатора прибора, соответствующая углублению наконечника на 0,002 мм.
Таким образом, твердость по Роквеллу выражается в условных единицах.
На практике числа твердости по Роквеллу обычно не вычисляют по приведенной выше формуле, а отсчитывают по шкале индикатора прибора типа ТК непосредственно в процессе испытания.
Нулевое деление черной шкалы совпадает с начальным положением стрелки. Красная шкала смещена относительно нулевого деления черной шкалы на 30 делений в направлении, противоположном движению стрелки индикатора при внедрении наконечником. Следовательно, начальное деление красной шкалы совпадает с делением 30 на циферблате индикатора. Это смещение сделано по той причине, что глубина вдавливания шарика часто превышает 0,2 мм, и тогда стрелка при вдавливании делала бы поворот более чем на 100 делений, т.е. значение твердости могли бы получаться отрицательными. Большая стрелка служит для указания твердости, а малая – для контроля величины предварительного нагружения.
Твердость на приборе ТК можно измерить:
Алмазным конусом с общей нагрузкой 150 кг (предварительная – 10 кг и основная 140 кг). Значение твердости определяют по черной шкале С и обозначают НRC. Эта шкала применяется для испытания закаленных сталей, обладающих твердостью до 67HRC , и для определения твердости тонких поверхностных слоев толщиной более 0,5 мм;
Алмазным конусом с общей нагрузкой 60 кг (предварительная – 10 кг и основная 50 кг). Значение твердости определяют по черной шкале С и обозначают HRA. Эта шкала применяется для испытания сверхтвердых сплавов (например, карбидов вольфрама), тонкого листового материала и для измерения твердости тонких поверхностных слоев (0,3-0,5 мм) или тонких пластинок;
Стальным шариком 1/16 дюйма с общей нагрузкой 100 кг (предварительная – 10 кг и основная 90 кг). Значение твердости определяют по красной шкале В и обозначают HRB. Шкала В служит для испытаний металлов средней твердости и для испытаний изделий толщиной от 0,8 до 2 мм.
На основании опытных работ установлена связь между числами твердости по Роквеллу (при HRC>20) и по Бринеллю
НВ≈10·HRC
К достоинствам метода Роквелла следует отнести высокую производительность, простоту обслуживания, точность измерения и сохранение качественной поверхности после испытаний. Не рекомендуется применять этот метод для определения твердости неоднородных по структуре сплавов (чугуна), для испытания криволинейных поверхностей с радиусом кривизны менее 5 мм и для испытания деталей которые под действием нагрузки могут деформироваться.
studfiles.net
Измерение твердости вдавливанием алмазного конуса (твердость по Роквеллу)
Рис. 103. Схема прибора для измерения твердости вдавливанием алмазного конуса или стального шарика (измерение по Роквеллу) /—столик для установки образца 2 — маховик 3 — груз 4 — шкала-индикатор, 5—масляный регуля тор 5 — шток с алмазным конусом (шариком) 7 — рукоятка | ![]() |
Измерение твердости вдавливанием алмазного конуса или стального шарика (метод Роквелла) по ГОСТу 9013—59. Твердость по методу Роквелла определяют по глубине вдавливания в испытуемую поверхность стального шарика диаметром 1,588 мм при нагрузке 100 кГ или [c.16]
Кроме метода Бринелля, в СССР стандартизованы еще два метода измерения твердости — метод Роквелла (ГОСТ 9013—59 ) иметод Виккерса (ГОСТ 2999—59). По методу Роквелла о твердости судят по разности глубин, на которые проникает алмазный конус или стальной шарик диаметром 1,5875 мм при действии двух последовательно приложенных нагрузок (предварительной — 10 кГ и общей — 60, 100 или 150 кГ). Для определения числа твердости применяют две шкалы. Шкала В соответствует вдавливанию стального шарика и число твердости при этом обозначается HRB. Для более твердых материалов применяется шкала С (вдавливание алмазного конуса) и число твердости обозначается HR . [c.138]
Приборы, работаюш,пе ио методу Роквелла (вдавливание алмазного конуса), применяют в основном для измерения высокой твердости. Недостаток этого метода — относительно невысокая точность измерения, но этот метод позволяет получить числовое значенпе твердости испытываемого изделия в 3—4 раза быстрее, чем на приборах, работающих по методам вдавливания стального шарика или пирамиды. [c.227]
Широко известно измерение твердости по глубине отпечатка, получаемого при вдавливании алмазного конуса или стального шарика — метод Роквелла. Определение твердости осуществляется с помощью конусного твердомера (ТР) по ГОСТ 9013-59. Этот метод позволяет изменять нагрузку в широких пределах без изменения значений твердости. Прибор, предназначенный для измерения твердости по Роквеллу (рис. 2.8), имеет столик 4, установленный в нижней части неподвижной станины. В верхней части станины укреплены индикатор 8 и шпиндельный узел 7, в котором имеется наконечник с алмазным конусом 6 (с углом при вершине 120°) или со стальным шариком. На индикаторе 8 нанесены две шкалы (черная и красная) и имеются две стрелки — большая (указатель твердости), вращающаяся по шкале, и маленькая, предназначенная для контроля предварительного нагружения, сообщаемого вращением маховика 3. [c.29]
Измерение твердости колец производится на их торцах. Минимальное расстояние от центра отпечатка до края кольца и минимальная ширина торцовой поверхности колец должны быть не менее указанной в табл. 4.13. Если из-за недостаточной ширины кольца контроль твердости по Роквеллу невозможен, то измерения выполняют по методу Виккерса. Минимальная толщина детали или упрочненного слоя в точке вдавливания алмазного конуса приведена в табл. 4.14. [c.330]
Сущность метода Роквелла (рис. 145, б) заключается в том, что в испытуемый образец вдавливается наконечник (стальной шарик или алмазный конус). Твердость по Роквеллу измеряется в условных единицах, что упрощает расчеты. При этом методе совмещаются операции вдавливания измерительного наконечника и измерения величины отпечатка. [c.159]
Испытание на твердость по Роквеллу проводят вдавливанием алмазного конуса или закаленного стального шарика. Затем измеряют глубину лунки после снятия нагрузки к. Твердость по Роквеллу отсчитывается в отвлеченных единицах по шкале прибора. Прибор имеет три шкалы А, В, С. Твердость закаленной среднеуглеродистой стали, определенная по шкале С, равна приблизительно 62. При измерении твердости по шкалам С и А ис- [c.71]
При измерении материалов большой твердости проба по Бринелю не дает надежных чисел. В этом случае твердость определяют вдавливанием алмазного конуса на специальном приборе, сконструированном Роквеллом, откуда метод и получил свое название. Числа твердости по Роквеллу имеют своеобразное значение (величина, обратная глубине погружения конуса в материал) и отсчитываются по индикатору, имеющемуся на приборе. Эту твердость условлено обозначать буквой (пли [c.124]
Наиболее простым методом испытания свойств является измерение твердости. Твердостью называют свойство материала оказывать сопротивление деформации в поверхностном слое при местных контактных воздействиях. Различают методы определения твердости по Брпнелю (по диаметру отпечатка шарика) по Роквеллу (по глубине вдавливания алмазного конуса или закаленного шарика) по Виккерсу (для деталей малой толщины или тонких поверхностных слоев твердость определяют по диагонали отпечатка алмазной пирамиды). Схемы этих методов приведены на рис. 47. В некоторых случаях определяют микротвердость отдельных участков металла. Этот метод используют для измерения твердости отдельных зерен или очень тонких слоев. [c.87]
Контроль твердости тел качения. Твердость тел качения диаметром более 4,76 мм контролируют по Роквеллу при нагрузке 150 кГ. При вдавливании алмазного конуса в криволинейные поверхности шариков и роликов измеренные числа твердости HR x имеют относительное значение. Действительная твердость HR с учетом искажающего влияния кривизны шариков и роликов вычисляется по фор.муле [c.411]
Используют следующие методы определения твердости металла проба напильником (метод неточен), проба по цвету искры (заточка изделия ка шлифовальном круге, измерение также неточное), а также определение по Бри-неллю (ГОСТ 9012—59, вдавливание стального шарика в исследуемый металл), по Роквеллу (ГОСТ 9013—59, вдавливание в исследуемый металл алмазного конуса) и по Викерсу (ГОСТ 2999—75, вдавливание в исследуемый материал алмазной пирамиды), а также определение твердости по метолу упругой отдачи по Шору (по высоте отскакивания шарика или бойка от обработанной поверхности). [c.142]
В технике применяются методы определения твердости, основанные на измерении размеров лунок, получаемых при вдавливании в поверхность испытуемого материала стальных шариков, алмазных конусов или призм (твердость по Бринеллю, по Роквеллу, по Виккерсу). [c.171]
Твердость по Роквеллу (шкала А) образцов определяют по ГОСТ 20017-74 вдавливанием алмазного конического наконечника (радиус сферы при вершине конуса 0,2 мм) в испытуемый образец под действием двух нагрузок – предварительной в 100 Н и общей в 590 Н, равной сумме предварительной и дополнительной (490Н) нагрузок число твердости в единицах HRA зависит от глубины внедрения наконечника (чем она больше, тем число твердости меньше). Поверхность или участок поверхности образца, на которых проводят измерение твердости, должны быть отшлифованы. Каждый образец испытывают в трех точках, расположенных по диагонали или наибольшему размеру, на равном расстоянии друг от друга ( 2 мм) и от вершин углов или краев образца (5= 0,5 мм). За показатель твердости партии принимают среднее арифметическое значение твердости образцов, отобранных от партии, округленное до 0,5 единицы HRA. [c.118]
Измерение твердости методом Роквелла. Измерение осуществляют путем вдавливания в испытуемый металл стального шарика диаметром 1,59 мм или конусного алмазного наконечника с углом при вершине 120° (рис. 1.11, б). В отличие от метода Бринелля твердость по Роквеллу определяют не по диаметру отпечатка, а по глубине вдавливания шарика или конуса. [c.39]
Твердость следует измерять не менее чем в трех точках (особенно алмазным конусом), т. е. не менее трех раз на одном образце. Для расчета лучше принимать среднее значение результатов второго и третьего измерений и не учитывать результат первого измерения. Для определения твердости по Роквеллу требуется меньше времени (30-60 с), чем по Бринеллю, причем результат измерения виден на шкале (указан стрелкой). При измерении твердости по Роквеллу остается меньший отпечаток на поверхности детали. Твердость очень тонких слоев металла (толщиной менее 0,3 мм) при нагрузках 588,4 и 1471 Н (60 и 150 кгс) измерять нельзя, так как алмазный конус проникает на глубину, превышающую толщину этих слоев. Вместе с тем с увеличением твердости измеряемого материала глубина отпечатка уменьшается, вследствие чего снижается точность измерения (особенно металлов твердостью более 60 HR ). Для этих целей иногда применяют приборы типа суперроквелл (тип ТРС) по ГОСТ 22975-78 или Виккерс (тип ТВ) по ГОСТ 2999-75, с помощью которых измеряют твердость при меньшей нагрузке и с меньшей глубиной вдавливания. Предварительная нагрузка при этом составляет 29,42 И (3 кгс). Каждое деление шкалы индикатора такого прибора соответствует глубине вдавливания, равной 1 мкм. Поэтому чувствительность данного прибора заметно выше. [c.32]
Твердость по Роквеллу. Этот метод измерения твердости (ГОСТ 9013-59) наиболее универсален и наименее трудоемок. Здесь не нужно измерять размеры отпечатка, так как число твердости отсчитывают непосредственно по шкале твердомера. Число твердости зависит от глубины вдавливания наконечника, в качестве которого используют алмазный конус с углом при вершине 120° или стальной шарик диаметром 1,588 мм. Нагрузку выбирают в зависимости от материала наконечника. Для различных комбинаций нагрузок и наконечников прибор Роквелла имеет три измерительных шкалы А, В, С. Твердость по Роквеллу обозначают цифрами, определяюш ими уровень твердости, и буквами HR с указанием шкалы твердости, например 70 HRA, 58 HR , 50 HRB. [c.54]
Поверочная схема для средств измерений твердости металлов, утвержденная ВНИИМ (рис. 60), предусматривает наличие эталонных приборов для измерений твердости металлов тремя стандартизированными методами статического вдавливания наконечников стального шарика (по Бринеллю) алмазного конуса и стального шарика (по Роквеллу) и алмазной пирамиды (по Виккерсу). [c.121]
Определение твердости по методу Роквелла основано на вдавливании в исследуемый материал стального шарика или алмазного конуса и последующем измерении глубины вдавливания (рис. 3.3). В зависимости от величины нагрузки и формы индентора используют две шкалы красную В или черную С. Стрелка циферблата указывает величину ЮО-Л по красной шкале при измерении шариком, где h -глубина вдавливания индентора, 100 и 130 число делений на щкалах С и В соответственно. Величину твердости определяют по индикаторной шкале, каждое деление которой соответствует глубине вдавливания в 2 мкм. [c.72]
В технике применяются методы определения твердости, основанные на измерении размеров лудок, получаемых при вдавливании в поверхность испытуемого материала стальных шариков, алмазных конусов или призм (твердость по Бринеллю, по Роквеллу, по Виккерсу). Соответственно для иллюстрации приведем метод определения твердости по Бринеллю, в котором [c.138]
При методе Роквелла твердость испытываемого образца считается обратно пропорциональной глубине вдавливания, т. е. чем глубже получается вдавливание, тем меньше твердость. Твердость по Роквеллу измеряется глубиной вдавливания маленького стального шарика диаметром 1,59 мм (Vie дюйма) при нагрузке 100 кг или же алмазного конуса с углом у вершины 120° и радиусом закругления конуса у вершины, равным 0,2 мм, при нагрузке 150 кг. В некоторых приборах алмазный конус заменен алмазной пирамидой с углом при вершине в 136° между двумя противолежащими гранями. Это дает возможность заменить измерение глубины отпечатка измерением его диагонали результат получается точнее. [c.93]
Приборы для измерения твердости по Роквеллу могут быть стационарными и переносными. Основным типом стационарной установки является прибор ТК. Твердость определяется путем вдавливания в образец индентора (шарика диаметром 1,588 мм или алмазного конуса с углом при вершине 120°) под действием двух нагрузок — предварительной и рабочей. Определение числа твердости производится после снятия рабочей нагрузки при остающейся предварительной. Поэтому в конструкции прибора предусмотрен механизм предварительного нагружения, создающий нагрузку 1СЮ0 н (10 кГ), постоянную для всех шкал. Прибор ТК имеет следующие шкалы шкала А — полная нагрузка 600 н ( 60 кГ) индентор — алмазный конус шкала — полная нагрузка 1000 (100 к/), индентор — стальной шарик шкала С — полная нагрузка 1500 (150 кГ), индентор — алмазный конус. Предварительная нагрузка осуществляется поджатием образца к индентору до установки стрелки индикатора в вертикальное положение, рабочая нагрузка прилагается через рычажную систему с отношением плеч 1 20. Глубина отпечатка фиксируется индикатором с увеличением 500. Работа на приборе проста и не требует особой квалификации, производительность высокая. [c.10]
Измерение твердости по Роквеллу основано на вдавливании в испытуемый материал алмазного конуса с углом при вершине 120°. Вдавливание осуществляется нагрузкой в 60 (шкала А), в 100 (шкала В) или 150 кг (шкала С), соответственно толщине проверяемого образца или твердости поверхностного слоя металла. Приложение основной нагрузки производится уже после то го, как индикатор зафиксирует предварительную нагрузку 10 кг. Число твердости вычисляется по разности глубины предварительного и окончательного вдавливания и обозначается соответственно буквенными символами или Няс- [c.9]
Измерения алмазным конусом с нагрузкой 150 кгс (HR ) проводят а) для закаленной или низкоотпущенной стали (с твердостью более НВ 450), т. е. в условиях, когда вдавливание стального шарика (по Бринеллю или Роквеллу по шкале В) в твердый материал может вызвать деформацию шарика и искажение результатов [c.177]
Измерение твердости по Роквеллу требует меньше времени (30—60 с), чем по Бринеллю, причем результат измерения виден на шкале (он указан стрелкой). Кроме того, измерение твердости по Роквеллу оставляет меньший отпечаток на поверхности детали. Твердость очень тонких слоев металла (толщиной менее 0,3 мм) с указанными нагрузками 60 и 150 кгс измерять нельзя, так как алмазный конус проникает на глубину, превышающую толщину этих слоев, и указывает, следовательно, твердость нижележащих областей. Вместе с тем с увеличением твердости измеряемого материала глубина отпечатка уменьшается, вследствие чего понижается точность измерения (особенно для металлов с твердостью более NR 60). Для этих же целей иногда применяют приборы типа супер-роквелл, у которых твердость измеряют с меньшей нагрузкой и с меньшей глубиной вдавливания. Предварительная нагрузка со- [c.178]
Содержание задания. Измерить твердость по Бринеллю (шариком 10 мм) и Роквеллу (по шкале С) и указать примерное значение предела прочности испытуемой стали. Объяснить принцип измерения твердости вдавливанием шарика или алмазного конуса. [c.186]
Более часто измеряют твердость алмазным конусом с нагрузкой 150 кГ (HR ). Эти измерения проводят а) для определения твердости закаленной или низкоотпущенной стали (с твердостью более 450 НВ), т. е. в условиях, когда вдавливание стального шарика (по Бринелю или Роквеллу по шкале В) в твердый материал может вызвать деформацию шарика и искажение результатов б) для материалов средней твердости (более 230 НВ) как более быстрым способом определения, оставляющим, кроме того, меньший след на измеряемой поверхности, чем при испытании по Бринелю в) для определения твердости тонких поверхностных слоев, но толщиной более 0,5 мм (например, цементованного слоя) применение шарика может вызвать продавливание поверхностного слоя. [c.156]
При измерении твердости по Роквеллу наконечник стандартного типа (алмазный конус с углом при вершине 120° или стальной шарик диаметром 1,588 мм) вдавливается в испытуемый образец (деталь). Вдавливание конуса или шарика производится под действием двух последовательно прилагаемых нагрузок — предварительной и основной. Предварительная нагрузка при конусе и шарике равна 10 кгс. Величина основной нагрузки при вдавливании конуса 140 кгс, а шарика 90 кгс. Таким образом полная (общая) нагрузка на конус составляет 10 + 140 = 150 кгс, а на шарик 10 + 90 = 100 кгс. Происходящее при этом углубление наконечника прибора отсчитывается по шкале С, если наконечник — алмазный конус, [c.32]
Измерение твердости алмазным конусом методом Роквелла проводится на специальном приборе путем вдавливания в испытуемую поверхность стального шарика диаметром 1,588 мм (1/16″) или алмазного конусного наконечника с углом при вершине 120°. Твердость определяется по глубине вдавливания под действием двух последовательно прилагаемых нагрузок предварительной — 10 кгс и общей [c.205]
Твердость по Роквеллу измеряют на специальном приборе вдавливанием в испытываемый образец стандартного алмазного конуса с углом при вершине 120° или стандартного стального шарика диаметром 1,588 мм. Прн измерении твердости по Роквеллу образец нагружают в две стадии сначала прикладывают пред- [c.59]
Существует несколько способов измерения твердости вдавливанием по Бринеллю (НВ, мерой твердости служит отношение нагрузки к площади поверхности сферического отпечатка шарика) по Роквеллу (НКА, НКВ, яле – условная величина, обратная глубине вдавливания шарика или алмазного конуса в зависимости от твердости испытуемого металла, с соответствующим отсчетом на приборе Роквелла) по Виккерсу (НУ – определяется отношением нагрузки к квадрату средней длины диагоналей отпечатка от вдавливания четырехгранной алмазной пирамидки). [c.193]
Определение твердости металлов по методу Роквелла основано на вдавливании алмазного наконечника конической формы (угол конуса 120°) или стального закаленного шарика диаметром 1,59 мм (1/16″) а поверхность испытуемого образца или изделия. Значения твердости по Роквеллу — отвлеченные числа. Прн испытании твердость отсчитывают по шкалам С, Л и В прибора. Число твердости, измеренной алмазным наконечником под нагрузкой [c.29]
Испытание по способу Роквелла (рис. 10, 6) заключается в том, что с помощью пресса в поверхность образца 2 вдавливают стальной закаленный шарик 1 диаметром 1,588 мм кт алмазный конус 3 с углом при вершине 120°. О величине твердости судят по глубине вдавливания шарика или конуса. Числа твердости по Роквеллу HR измеряются в условных единицах и отсчитываются по шкалам прибора, укрепленного на прессе и имеющего три шкалы. Если испытание проводится стальным шариком, то отсчет ведут по шкале В, а твердость обозначают НРВ. При испытании алмазным конусом отсчет вед>т либо по шкале А (твердость обозначается НЯА), либо по шкале С (твердость обозначается НРС). Способ Роквелла удобен простотой отсчета и дает большую точность измерений. [c.25]
mash-xxl.info
Твёрдость по Роквеллу – это… Что такое Твёрдость по Роквеллу?
- Твёрдость по Роквеллу
Роквелла метод [по имени американского металлурга С.Роквелла (S.Rockwell), разработавшего этод метод] – способ определения твёрдости материалов (главным образом металлов) вдавливанием в испытываемую поверхность алмазного индентора с углом при вершине 120° (шкалы А и С) или стального закалённого шарика диаметром 1/16 дюйма или 1,588 мм (шкала B. Твёрдость по Роквеллу выражается в условных единицах. За единицу твёрдости принята величина, соответствующая перемещению индентора на 0,002 мм. Испытание методои Роквелла проводят на специальном настольном приборе, снабжённом индикатором, который показывает число твёрдости. ГОСТ 23677-79.
Источник: Иванов В.Н. Словарь-справочник по литейному производству. – М.: Машиностроение, 1990. – 384 с.: ил.
ISBN 5-217-00241-1смотри также Твёрдость, Твёрдость по Бринеллю, Твёрдость по Виккерсу.
Металлургический словарь. 2003.
- Твёрдость по Виккерсу
Смотреть что такое “Твёрдость по Роквеллу” в других словарях:
твёрдость по Роквеллу — — [А.С.Гольдберг. Англо русский энергетический словарь. 2006 г.] Тематики энергетика в целом EN Rockwell hardnessHRRH … Справочник технического переводчика
твёрдость по Роквеллу по шкале В — — [http://slovarionline.ru/anglo russkiy slovar neftegazovoy promyishlennosti/] Тематики нефтегазовая промышленность EN Rockwell B hardness … Справочник технического переводчика
твёрдость по Роквеллу по шкале С — — [http://slovarionline.ru/anglo russkiy slovar neftegazovoy promyishlennosti/] Тематики нефтегазовая промышленность EN Rockwell C hardness … Справочник технического переводчика
число твёрдости по Роквеллу — твёрдость по Роквеллу — [А.С.Гольдберг. Англо русский энергетический словарь. 2006 г.] Тематики энергетика в целом Синонимы твёрдость по Роквеллу EN Rockwell numberRockwell hardness numberRoRHN … Справочник технического переводчика
твёрдость по шкале Роквелла — твёрдость по Роквеллу — [http://slovarionline.ru/anglo russkiy slovar neftegazovoy promyishlennosti/] Тематики нефтегазовая промышленность Синонимы твёрдость по Роквеллу EN Rockwell hardness … Справочник технического переводчика
Твёрдость — У этого термина существуют и другие значения, см. Твёрдость (значения). Твёрдость это способность материала сопротивляться проникновению в него другого, более твёрдого тела индентора во всем диапазоне нагружения: от момента касания с… … Википедия
Твёрдость по Бринеллю — Бринелля метод [по имени шведского инженера Ю.А.Бринелля (J.A.Brinell)] способ определения твёрдости материалов вдавливанием в испытываемую поверхность стального закалённого шарика диаметром 2,5; 5 и 10 мм пр нагрузке P от 625 H до 30 кН. Число… … Металлургический словарь
Твёрдость по Виккерсу — Виккерса метод [по названию английского военно промышленного концерна Виккерс ( Vickers Limited )] способ определения твёрдости материалов вдавливанием в поверхность образца или изделия алмазного индентора имеющего форму правильной четырёхгранной … Металлургический словарь
твёрдость алмаза — (твёрдость по Роквеллу, твёрдость по Виккерсу) [http://slovarionline.ru/anglo russkiy slovar neftegazovoy promyishlennosti/] Тематики нефтегазовая промышленность EN diamond hardness … Справочник технического переводчика
Твёрдость по Шору (Метод вдавливания) — У этого термина существует и другое значение, см. Твёрдость по Шору. При этом следует понимать, что хотя в другом значении этот метод также является методом измерения твёрдости, оба метода предложены одним и тем же автором, имеют совпадающие… … Википедия
metallurgy_dictionary.academic.ru
твёрдость алмаза – это… Что такое твёрдость алмаза?
- твёрдость алмаза
- diamond hardness
Большой англо-русский и русско-английский словарь. 2001.
- твёрдость
- твёрдость горной породы
Смотреть что такое “твёрдость алмаза” в других словарях:
твёрдость алмаза — (твёрдость по Роквеллу, твёрдость по Виккерсу) [http://slovarionline.ru/anglo russkiy slovar neftegazovoy promyishlennosti/] Тематики нефтегазовая промышленность EN diamond hardness … Справочник технического переводчика
Твёрдость по Шору (Метод отскока) — У этого термина существует и другое значение, см. Твёрдость по Шору. При этом следует понимать, что хотя в другом значении этот метод так же является методом измерения твёрдости, оба метода предложены одним и тем же автором, имеют совпадающие… … Википедия
Твёрдость — У этого термина существуют и другие значения, см. Твёрдость (значения). Твёрдость это способность материала сопротивляться проникновению в него другого, более твёрдого тела индентора во всем диапазоне нагружения: от момента касания с… … Википедия
ТВЁРДОСТЬ — ТВЁРДОСТЬ, сопротивление твердого тела вдавливанию или царапанию. При вдавливании твердость равна нагрузке, отнесенной к поверхности отпечатка. Вдавливается стальной шарик (Метод Бринелля) или алмазная пирамидка (методы Роквелла и Виккерса).… … Современная энциклопедия
Твёрдость — Твердость ТВЁРДОСТЬ, сопротивление твердого тела вдавливанию или царапанию. При вдавливании твердость равна нагрузке, отнесенной к поверхности отпечатка. Вдавливается стальной шарик (метод Бринелля) или алмазная пирамидка (методы Роквелла и… … Иллюстрированный энциклопедический словарь
МИКРОТВЁРДОСТЬ — сопротивление пластич. вдавливанию (обычно в плоскую поверхность) твёрдого индентора (обычно пирамиды из алмаза). Отличия испытаний на М. от обычных измерений твёрдости очень малые нагрузки и малые размеры отпечатка. М. позволяет оценивать св ва… … Большой энциклопедический политехнический словарь
Алмаз — У этого термина существуют и другие значения, см. Алмаз (значения). Алмаз Алмаз в материнской породе Формула C … Википедия
Изумруд — У этого термина существуют и другие значения, см. Изумруд (значения). Запрос «Смарагд» перенаправляется сюда; см. также другие значения. Изумруд … Википедия
Изумруды — Изумруд Изумруд из Бразилии Формула Be3(Al,Cr)2Si6O18 Сингония Гексагональная Цвет Зелёный, желтоватый Блеск … Википедия
Алмаз — [άδάμας (ΰдамас) первоначальное название стали, позднее алмаза) м л, С. Куб. модиф. К лы октаэдрические, куб. и тетраэдрические. Дв. прорастания по {111}; параллельные сростки. Сп. сов. по {111}. Тв. 10. Уд. в.… … Геологическая энциклопедия
Алмаз — минерал, кристаллическая модификация чистого углерода (С). А. обладает самой большой из всех известных в природе материалов твёрдостью, благодаря которой он применяется во многих важных отраслях промышленности. Известны три… … Большая советская энциклопедия
dic.academic.ru