Твердость по роквеллу и бринеллю – Перевод твердости по Бринеллю (HB), Роквеллу (HRC), Виккерсу (HV) и Шору (HSD)
alexxlab | 22.07.2020 | 0 | Разное
Твердость Бринелла и Роквелла 2019
Испытание на твердость является одним из наиболее широко используемых методов испытаний материалов. Измерения статической твердости удобны для точного определения твердости.
Что такое твердость Бринелла?
Твердость по Бринеллю (HBW) представляет собой отношение между приложенной силой и поверхностью отпечатка. Индентор представляет собой шарик из твердого металла с диаметром D, который запечатлен силой F в поверхностные слои материала. Диаметр мяча стандартизирован и составляет: 10; 5; 2,5; 1мм.
При импринтинг материала для испытаний генерируется отпечаток формы кубического диаметра базового диаметра дБ и глубины hB. Измеритель твердости Бринелла использует импульсную силу от 9,807 н. До 29420 Н в зависимости от материала испытания и диаметра шарика рабочего колеса.
Нагрузка обычно применяется в течение 10-15 секунд в случае испытания стальных или стальных материалов, а для других более мягких материалов нагрузка должна наноситься не менее 30 секунд. Испытуемый должен быть очищен и обезжирен, а поверхность гладкая, чтобы измерение было максимально точным, чтобы определить диаметр чаши калота.
Во время измерения вибрации не должно быть, поскольку они могут чрезмерно влиять на значения измеренной твердости. Твердость Бринелла – безразмерный размер. По сравнению с другими методами испытаний на твердость, мяч Бринелла оставляет самую глубокую и самую большую печать и, следовательно, функционально и / или эстетически обезображает поверхность (если твердость измеряется на продукте, а не на образце).
Что такое твердость по Роквеллу?
В отличие от методов Бринелла и Виккерса метод Роквелла не измерял размер отпечатка, а глубину проникновения индентора. Поэтому в случае Rockwell твердость считывается по шкале твердости после ее выпуска.
Индукторы изготовлены из алмазного стержня или шара из акации. У бриллиантов стержня есть пиковый угол 1200 и радиус 0,2 мм вокруг, а диаметр шарика – 1/16 “и 1/8”. Тест HRB (ball) используется для мягких и средних твердых металлов, тогда как HRC (конус) используется для лиственных пород и обычно термически обработанных материалов.
Общая возможная глубина проникновения индентеров составляет 0,2 мм (HRC) или 0,26 мм (HRB) и делится на 100 частей методом HRC или 130 для метода HRB, поэтому твердость по методу Роквелла составляет: 1e = 0,002 м. В методе HRC индентор имеет форму алмазного ствола, который загружается с предварительной нагрузкой F0 = 98,07 N в течение 3 секунд, таким образом получая начальную точку, из которой измеряется глубина проникновения.
Суммарная нагрузка F следует, добавив основную на
ru.esdifferent.com
Соотношение чисел твердости по Бринеллю, Роквеллу и Виккерсу
Твердость по Виккерсу | Твердость по Бринеллю Dш=10 мм, Р=3000 кг | Твердость по Роквеллу | |||
Шкал | |||||
Диаметр отпечатка, мм | Число твердости | C | B | A | |
(150 кг) | (100 кг) | (60 кг) | |||
1 | 2 | 3 | 4 | 5 | 6 |
1224 | 2,20 | 780 | 72 | – | 84 |
1116 | 2,25 | 745 | 70 | – | 83 |
1022 | 2,30 | 712 | 68 | – | 82 |
941 | 2,35 | 682 | 66 | – | 81 |
868 | 2,40 | 653 | 64 | – | 80 |
804 | 627 | 62 | – | 79 | |
746 | 2,50 | 601 | 60 | – | 78 |
694 | 2,55 | 578 | 58 | – | 78 |
650 | 2,60 | 555 | 56 | – | 77 |
606 | 2,65 | 534 | 54 | – | 76 |
1 | 2 | 3 | 4 | 5 | 6 |
587 | 2,70 | 514 | 52 | – | 75 |
551 | 2,75 | 495 | 50 | 74 | |
1 | 2 | 3 | 4 | 5 | 6 |
534 | 2,80 | 477 | 49 | – | 74 |
502 | 2,85 | 461 | 48 | – | 73 |
472 | 2,90 | 444 | 46 | – | 73 |
460 | 2,95 | 429 | 45 | – | 72 |
435 | 3,00 | 415 | 43 | – | 72 |
423 | 3,05 | 401 | 42 | – | 71 |
401 | 3,10 | 388 | 41 | – | 71 |
390 | 3,15 | 375 | 40 | – | 70 |
380 | 3,20 | 363 | 39 | – | 70 |
361 | 3,25 | 352 | 38 | – | 69 |
344 | 3,30 | 341 | 36 | – | 68 |
334 | 3,35 | 331 | 35 | – | 67 |
320 | 3,40 | 321 | 33 | – | 67 |
311 | 3,45 | 311 | – | 66 | |
303 | 3,50 | 302 | 31 | – | 66 |
292 | 3,55 | 293 | 30 | – | 65 |
285 | 3,60 | 285 | 29 | – | 65 |
278 | 3,65 | 277 | 28 | – | 64 |
270 | 3,70 | 269 | 27 | – | 64 |
261 | 3,75 | 262 | 26 | – | 63 |
255 | 3,80 | 255 | 25 | – | 63 |
249 | 3,85 | 248 | 24 | – | 62 |
240 | 3,90 | 241 | 23 | 102 | 62 |
235 | 3,95 | 235 | 21 | 101 | 61 |
228 | 4,00 | 229 | 20 | 100 | 61 |
222 | 4,05 | 223 | 19 | 99 | 60 |
217 | 4,10 | 217 | 17 | 98 | 60 |
213 | 4,15 | 212 | 15 | 97 | 59 |
208 | 4,20 | 207 | 14 | 95 | 59 |
1 | 2 | 3 | 4 | 5 | 6 |
201 | 4,25 | 201 | 13 | 94 | 58 |
197 | 4,30 | 197 | 12 | 93 | 58 |
192 | 4,35 | 192 | 11 | 92 | 57 |
186 | 4,40 | 187 | 9 | 91 | 57 |
183 | 4,45 | 183 | 8 | 90 | 56 |
178 | 4,50 | 179 | 7 | 90 | 56 |
174 | 4,55 | 174 | 6 | 89 | 55 |
171 | 4,60 | 170 | 4 | 88 | 55 |
166 | 4,65 | 167 | 3 | 87 | 54 |
162 | 4,70 | 163 | 2 | 86 | 53 |
159 | 4,75 | 159 | 1 | 85 | 53 |
155 | 4,80 | 156 | 0 | 84 | 52 |
152 | 4,85 | 152 | – | 83 | – |
149 | 4,90 | 149 | – | 82 | – |
148 | 4,95 | 146 | – | 81 | – |
143 | 5,00 | 143 | – | 80 | – |
140 | 5,05 | 140 | – | 79 | – |
138 | 5,10 | 137 | – | 78 | – |
134 | 5,15 | 134 | – | 77 | – |
131 | 5,20 | 131 | – | 76 | – |
129 | 5,25 | 128 | – | 75 | – |
127 | 5,30 | 126 | – | 74 | – |
123 | 5,35 | 123 | – | 73 | – |
121 | 5,40 | 121 | – | 72 | – |
118 | 5,45 | 118 | – | 71 | – |
116 | 5,50 | 116 | – | 70 | – |
115 | 5,55 | 114 | – | 68 | – |
113 | 5,60 | 111 | – | 66 | – |
РЕКОМЕНДАТЕЛЬНЫЙ БИБЛИОГРАФИЧЕСКИЙ СПИСОК
1. Солнцев Ю.П. Металловедение и технология металлов / Ю.П.Солнцев, В.А.Веселов, В.П.Демянцевич и др. М.: Металлургия, 1988, 512с.
2. Гуляев А.П. Металловедение. М.: Металлургия, 1986, 544 с.
3. Худокормова Р.Н. Материаловедение. Лабораторный практикум / Р.Н.Худокормова, Ф.И. Пантелеенко. Минск: Высшая школа, 1988, 224 с.
4. Лахтин Ю.М. Материаловедение / Ю.М. Лахтин, В.П. Леонтьева М.: Машиностроение, 1990, 528с.
5. Солнцев Ю.П.. Материаловедение / Ю.П.Солнцев, Е.И.Пряхин, Ф.И,Войткун. М.: МИСИС, 1999, 600с.
studfiles.net
Измерение твердости по Роквеллу HRC: методика, единицы измерения
Металлы обладают достаточно большим количеством физико-механических свойств, которые следует учитывать при их использовании для изготовления различных изделий. Твердость – способность одного материала препятствовать проникновению в него другого, более твердого. Для измерения этого показателя были разработаны самые различные методики тестирования. Часто проводится измерение твердости по Роквеллу (HRC). Этот метод имеет довольно большое количество особенностей, о которых далее поговорим подробнее.
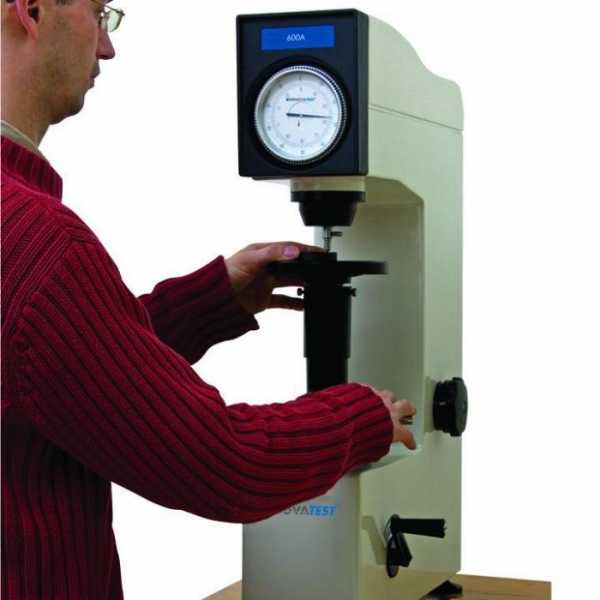
Методика измерения
Метод определения твердости металла по Роквеллу применяется в случае, когда нужно протестировать заготовку небольшой толщины. Кроме этого, подобным образом проверяется твердость поверхностного слоя изделия, к примеру, прошедшего закалку или процесс цементирования.
Проводится определение твердости металлов методом Роквелла следующим образом:
- Метод основан на вдавливании более твердого объекта в испытуемый. Для этого используется специальный алмазный наконечник, который имеет форму правильной пирамиды.
- Нагрузка прикладывается к наконечнику на протяжении определенного времени. При этом время выдержки и величина нагрузки могут существенно различаться. Согласно установленным стандартам в ГОСТ 9013-59, нагрузка может быть от 1 до 100 кгс. При этом уточняются конкретные значения из этого промежутка.
- Полученные отпечатки алмазного конуса измеряются. Наиболее важными показателями в этом случае можно назвать размер диагоналей оставшегося отпечатка.
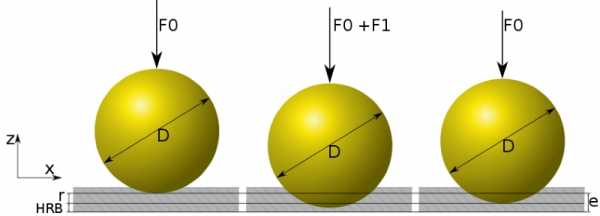
Принцип измерения твердости по Роквеллу
Полученные данные сверяются с табличными значениями, в которых учитывается величина приложенной силы и время выдержки. Рассматриваемая методика позволяет получить показатель твердости в своих условных единицах.
Процесс измерения можно разделить на несколько этапов:
- Определяется тип шкалы.
- Устанавливается подходящий индикатор. Важно выбрать индикатор, который будет соответствовать типу установленной шкалы.
- Проводится два пробных теста, которые необходимы для корректирования работы применяемого оборудования.
- Прикладывается предварительная нагрузка, равная 10 кгс.
- Прикладывается основная нагрузка и выдерживается определенный период, который позволяет получить максимальное значение.
- Убирается нагрузка и считывается полученный результат.
Скачать ГОСТ 9013-59
Современное оборудование позволяет существенно упростить процесс и повысить точность получаемых результатов в ходе проводимых измерений.
Шкалы твердости
Мера твердости по Роквеллу обозначается HRC. За время проведения тестирования различных металлов было разработано 11 шкал, которые отличаются по соотношению геометрических размеров наконечника и прилагаемой нагрузки. Стоит учитывать, что сегодня в качестве вдавливаемого тела сегодня используются не только алмазные наконечники. Распространение получили:
- сферы, изготавливаемые из закаленной стали;
- шарики из сплава карбида и вольфрама.
Обозначение проводится с использованием заглавных букв латинского алфавита.

Шкалы для определения твердости по Роквеллу
Прочему так важно учитывать тип применяемой шкалы? Причин довольно много:
- От нее зависит вид вдавливаемого индикатора. При этом есть определенная связь между геометрической формой и размерами индикатора и получаемыми данными.
- У каждого типа вдавливаемого объекта есть свое ограничение по показателю максимальной нагрузки.
Получаемые результаты важны при изготовлении подшипников и прочих ответственных элементов, используемых при создании автомобилей или авиатехники. Размерность твердости, определяемой по Роквеллу, учитывается и при выборе изделий из закаленной стали.
Оборудование для проведения измерения
На момент разработки рассматриваемой методики измерения твердости специального оборудования не было. После того, как в машиностроительной и других областях промышленности установили важность этой физико-механической характеристики, было разработано специальное оборудование, которое основано также на вдавливании шарика или конуса в тестируемый объект. Современное оборудование позволяет с высокой точностью контролировать величину прилагаемой силы и времени выдержки. Твердомером измеряется твердость, как правило, небольших объектов, являющимися образцами получаемой заготовки. Это связано с весьма компактными размерами большинства моделей рассматриваемых устройств.
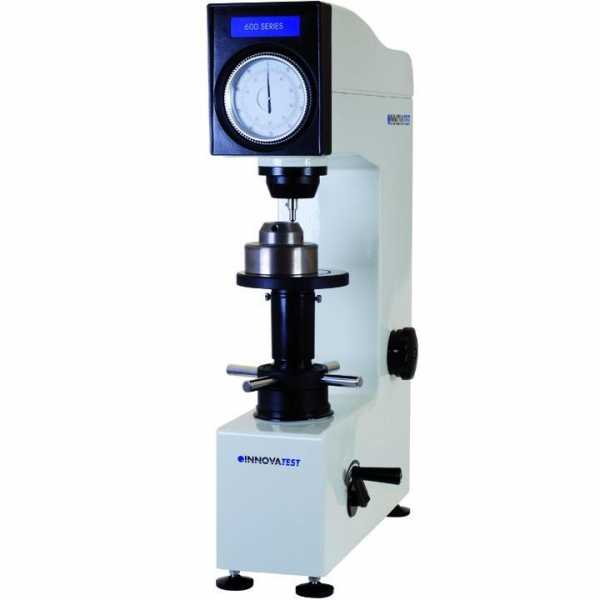
Твердомер Роквелла
К особенностям применяемого оборудования можно отнести нижеприведенные моменты:
- Испытуемый образец, как правило, располагается на столике.
- Алмазный наконечник опускается с помощью грузового рычага.
- Важным моментом является то, что наконечник опускается плавно. Это достигается при применении рукоятки с масленым амортизатором.
- Время выдержки применимой нагрузки зависит от размеров испытуемого образца. Как правило, показатель составляет 3-6 секунд. Сила воздействия определяется также величиной заготовки.
- Важные параметры вводятся при помощи специального пульта программирования. За счет того, что контроль прилагаемой силы и время выдержки проводит оборудование, точность получаемых результатов довольно высока.
Рассматриваемое оборудование производится достаточно большим количеством различных компаний. При этом стоимость предложения может колебаться в достаточно большом диапазоне.
Преимущества и недостатки метода
Каждый метод вычисления твердости поверхности обладает своими определенными достоинствами и недостатками. Принято считать, что испытание на твердость по Роквеллу и Бринеллю являются основными, так как позволяют получить наиболее точный результат.
К достоинствам метода измерения твердости по Роквеллу HRC можно отнести нижеприведенные моменты:
- Технология определяет возможность тестирования поверхностей с повышенной твердостью.
- При тестировании поверхность повреждается несущественно, что позволяет исследовать уже готовые изделия.
- Существенно упрощается процесс расчетов показателя твердости, так как нет необходимости в замере диаметра получаемого отпечатка после снятия прилагаемой нагрузки.
- На проведение измерений по Роквеллу уходит всего несколько секунд.
Однако есть и несколько существенных недостатков, которые также нужно учитывать:
- В сравнении с методом по Бринеллю, получаемый результат не так точен.
- Для повышения точности проводимых измерений следует тщательно подготовить поверхность.
Несмотря на то, что получаемые результаты могут иметь достаточно высокую погрешность, этот метод получил широкое распространение в машиностроительной и других отраслях промышленности, так как на тестирование уходит мало времени.
Показатель твердости зависит от достаточно большого количества моментов, к примеру, химического состава. Кроме этого, металлы могут улучшаться закалкой и другими видами термической обработки. Сегодня можно встретить довольно много методической литературы с таблицами, в которых указывается твердость для распространенных материалов. Принимаются эти значения зачастую при выполнении расчетов или проектировании.
Твердость некоторых материалов, получаемая при проведении тестов по Роквеллу, сравнивается с соответствующим показателем алмаза. Этот материал считается одним из самых твердых. Поэтому твердость алмаза по Роквеллу составляет 100 HRC. Аналогичные показатели стекла и вольфрама будут существенно ниже.
На точность проводимых измерений может оказывать влияние:
- Толщина испытуемого образца. Согласно принятым нормам при проникновении алмазного наконечника на 0,2 мм толщина испытуемого образца должна быть не меньше 2 см. В противном случае, полученные данные будут считаться искаженными.
- Если один образец применяется для проведения нескольких тестов, то расстояние между отпечатками должно быть не менее трех их диаметров. Соблюдение этого правила также позволяет получить более точные результаты.
- Результаты на циферблате могут отличаться в зависимости от положения исследователя. Повторные тестирования должны проводиться с одной точки обзора, иначе полученные результаты могут отличаться.
В заключение отметим, что сегодня подобные исследования проводятся все реже. Это связано с тем, что при изготовлении заготовок достигают высокой точности химического состава и физико-механических свойств. Поэтому каждой марке металла соответствует определенный показатель твердости по Роквеллу. Измерения зачастую проводятся после выполнения химико-термической обработки, когда от соблюдения применяемой технологии зависит конечный результат.
Если вы нашли ошибку, пожалуйста, выделите фрагмент текста и нажмите Ctrl+Enter.
stankiexpert.ru
1. Определение твердости по Бринеллю
Метод Бринелля заключается во вдавливании стального закаленного (иногда твердосплавного) шарика диаметром D(10,0; 5,0; 2,5; 2,0 или 1,0 мм) в испытуемый материал под фиксированной нагрузкойР(3000, 1500, 1000, 750, 500, 250, … 1 кгс)12в течение заранее выбранного времени (10…180 с) – см. рис. 10.1.
Мерой твердости по Бринеллю является диаметр отпечатка d, который измеряется с помощью оптического устройства, входящего в комплект прибора.
Рис. 10.1. Схема определения твердости по Бринеллю
Твердость по Бринеллю обозначается НВ и может быть рассчитана по формуле:
гдеF– площадь поверхности отпечатка
– шарового сегмента.
Метод Бринелля предназначен для измерения твердости особо мягких, мягких и средне твердых материалов (включая незакаленную сталь) с твердостью от 8 до 450 единиц НВ (кгс/мм2). Черные металлы имеют твердость выше 140 НВ; цветные металлы и сплавы – 8…130 НВ, в том числе алюминий, свинец и мягкие сплавы – 8…35 НВ.
2. Определение твердости по Роквеллу
Мерой твердости по Роквеллу является глубина вдавливания индентора, которая определяется с помощью индикатора часового типа, встроенного в прибор. Схема испытания показана на рис. 10.2.
Рис. 10.2. Схема определения твердости по Роквеллу:
а) по шкалам А и С; б) по шкале В
Измеренное
значение твердости считывается
непосредственно со шкалы индикатора.
Современные приборы позволяют использовать
9 шкал:A, B, C, D, E, F, G, H, K,рассчитанных
на применение разных нагрузок и
инденторов. В отечественной практике
обычно используют только три шкалы:А,
BиС.
Шкала Аиспользуется при испытаниях особо твердых материалов – твердых сплавов и деталей, подвергнутых химико-термической обработке (цементации, азотированию, борированию и т. п.). Здесь в качестве индентора используется алмазный конус с углом при вершине 120о, вдавливаемый под нагрузкой 60 кгс. Твердость, измеренная по этой шкале, обозначается HRA.
Шкала Виспользуется при испытаниях средне твердых материалов, включая цветные сплавы и незакаленную сталь. Здесь в качестве индентора используется стальной закаленный шарик диаметром 1,588 мм (1/16дюйма13), вдавливаемый под нагрузкой 100 кгс. Твердость, измеренная по этой шкале, обозначается HRВ.
Шкала Сиспользуется при испытаниях средне твердых и твердых материалов, включая незакаленную и закаленную сталь. Здесь в качестве индентора используется алмазный конус (тот же, что по шкале А), вдавливаемый под нагрузкой 150 кгс. Твердость, измеренная по этой шкале, обозначается HRС. Например, твердость закаленной стали составляет 60…65 HRС.
Метод Роквелла отличается особой простотой и оперативностью, при его использовании меньше повреждается поверхность испытуемого материала и поэтому он широко применяется для контроля качества термической обработки в цехах и лабораториях машиностроительных предприятий.
3. Определение твердости по Виккерсу
В методе Виккерса в качестве индентора используется правильная четырехгранная алмазная пирамида с углом между гранями 136о, которая вдавливается под нагрузкойРот 5 до 120 кгс.
Рис. 10.3. Схема определения твердости по Виккерсу
Мерой твердости является диагональ отпечатка, измеряемая с помощью микроскопа, встроенного в прибор. Схема определения твердости по Виккерсу показана на рис. 10.3.
Твердость по Виккерсу (HV) вычисляется по формуле:
гдеF– площадь отпечатка,d– диагональ отпечатка. Числа твердости по Виккерсу и Бринеллю имеют одинаковую размерность кгс/мм2(МПа) и для материалов с твердостью приблизительно до 340 НВ практически совпадают.
Метод Виккерса наиболее универсален и пригоден для измерения твердости любых металлов в лабораторных условиях, но отличается повышенной точностью при испытании высокотвердых материалов. При использовании небольших нагрузок (5…20 кгс) получаются микроскопические отпечатки, практически не повреждающие поверхность деталей.
Разновидностью прибора Виккерса является разработанный в нашей стране прибор для определения микротвердости ПМТ-3, в котором применен микроскоп с бóльшим увеличением (до 800), а для вдавливания алмазных инденторов используются очень малые нагрузки – 2…500 гс. Микротвердомер ПМТ-3 широко используется при изучении твердости деталей малых размеров и отдельных структурных составляющих сплавов14.
studfiles.net