Твердость по роквеллу: таблица, шкала, обозначение и единицы измерения
alexxlab | 06.06.2023 | 0 | Разное
Измерение твердости по Роквеллу – Измерение твердости
Твердомеры Роквелла Qness сочетают в себе надежную конструкцию и интерфейсы для управления данными с оптимальным удобством для пользователя. При добавлении одного из дополнительных модулей в твердомер возможна детальная оптическая оценка и полная автоматизация.
НОВИНКА
- Методы измерений: Роквелл, Бринелль (HBT), Виккерс (HVT)
- Измерение: рама в виде буквы C с винтовым столом
- Подробное описание
НОВИНКА
- Методы измерений: Роквелл, Бринелль (HBT), Виккерс (HVT)
- Измерение: автоматическое с моторизованным столом
- Подробное описание
- Методы измерений: Роквелл, Бринелль (HBT), Виккерс (HVT)
- Измерение: неподвижный стол с моторизованной регулировкой высоты
- Подробное описание
- Методы измерений: Роквелл, Бринелль (HBT)
- Измерение: Siemens S7 PLC
- Оптимизированное время цикла
- Подробное описание
Справочный материал Измерение твердости по Роквеллу (DIN EN ISO 6508)
В 1907 году Людвик опубликовал предложение использовать глубину проникновения алмазного конуса для оценки твердости материала. Кроме того, влияние поверхности образца следует исключить путем приложения предварительного испытательного усилия. Только в 1922 году американцу Роквеллу, основанному на идее Людвика, удалось разработать полезный метод определения твердости. Благодаря простоте метода измерения твердости по Роквеллу, данный метод быстро нашел применение в промышленности.
Индентор для определения твердости по Роквеллу
Алмазный конус с углом при вершине 120° или два шарика из закаленной стали (диаметр 1/16 дюйма = 1,5875 мм или 1/8 дюйма = 3,175 мм) используются в качестве индентора в испытании Роквелла. Стальные шарики можно использовать только в том случае, если это явно требуется в спецификации продукта или оговаривается отдельно. Если требуется или согласовано, могут также использоваться твердосплавные шарики диаметром 6,356 или 12,70 мм.
120°
алмазный конус
HRA, HRC, HRD, HR 15 N,
HR 30 N, HR 45 N
Ø 3.175 мм
шарик из закаленной стали
HRE, HRH, HRK
Ø 1.
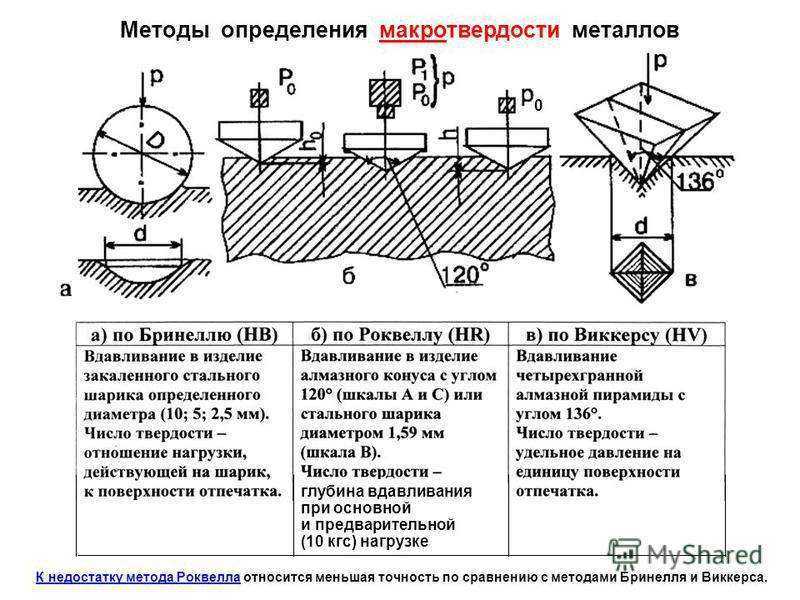
шарик из закаленной стали
HRB, HRF, HRG, HR 15 T, HR 30 T, HR 45 T, HR Bm, HR Fm
3 этапа измерения твердости по Роквеллу
- Сначала индентор вдавливается в поверхность образца с определенной предварительной нагрузкой F0. Это сделано для того, чтобы исключить влияние поверхности на значение твердости, такое как слои окалины, упрочнения и т.д. Под этой предварительной нагрузкой индентор первоначально проникает в образец на расстояние t0. Для создания предварительного испытательного усилия образец обычно прижимают к индентору до тех пор, пока не будет приложена заданная испытательная нагрузка.
- На втором этапе прилагается дополнительная испытательная нагрузка F1 . Теперь индентор проникает в образец еще на величину Dt. Дополнительное испытательное усилие должно быть приложено (начиная с предварительной нагрузки) без ударов или вибрации и без перескоков в течение 2-8 с и должно поддерживаться постоянным в течение 4 ± 2 с.
- На третьем этапе нагрузка снова разгружается до предварительной F0. Индентор перемещается вверх за упругую часть деформации tel, так что остающаяся глубина вдавливания составляет tbl. Значение твердости либо отображается непосредственно на твердомере, либо может быть рассчитано по измеренной глубине вдавливания.
t0 = глубина вдавливания за счет предварительного нагружения при нагрузке F0
Δt = дополнительная глубина вдавливания за счет дополнительной приложенной нагрузки F1
tel = упругая деформация за счет предварительного нагружения при нагрузке F0
tbl = остаточная глубина вдавливания после снятия испытательной предварительной нагрузки F0
Результаты измерения твердости по Роквеллу
Результат измерения твердости по Роквеллу определяется следующим образом:
В методе HRC Z равно 100, а деление шкалы Skt составляет 0,002 мм. Если измеренная глубина постоянного вдавливания составляет 0,12 мм, твердость C по Роквеллу составляет 40 HRC.
Согласно DIN EN ISO 6508-1 результат измерения твердости по Роквеллу отображается следующим образом:
60 HRC W ⇒ Значение твердости по Роквеллу
60 HRC W ⇒ Универсальный маркер для твердости по Роквеллу
60 HRC W ⇒ Маркировка шкалы твердости
60 HRC W ⇒ Значения с указанием материала индентора в случае использования шарика (не показана для алмазного конуса)
Что такое твердость по Роквеллу и почему она важна для ножей?
Содержание
- 1 Принципы испытания на твердость по Роквеллу
- 2 Процедура испытания на твердость по Роквеллу
- 3 применения теста на твердость по Роквеллу
- 4 преимущества теста на твердость по Роквеллу
- 5 ограничений теста на твердость по Роквеллу
- 6 Использование этого теста для ножей
- 7 ограничений теста на твердость по Роквеллу для ножей
- 8 будущих разработок в области технологий определения твердости
- 9 Что такое хорошая твердость по Роквеллу для ножа?
- 10 Подходит ли твердость 58 HRC для ножа?
- 11 Какая твердость по Роквеллу у дешевых ножей?
- Заключение 12
Испытание на твердость по Роквеллу является широко используемым методом измерения твердости материала. Испытание включает приложение определенной нагрузки к индентору, который вдавливается в материал, и измеряется глубина полученного отпечатка. Этот тест широко используется при контроле качества, выборе материалов, исследованиях и разработках и является важным инструментом для определения механических свойств материала.
В этом сообщении блога мы обсудим принципы измерения твердости по Роквеллу, его применение, преимущества и ограничения, а также его будущие разработки.
Принципы испытания на твердость по РоквеллуИспытание на твердость по Роквеллу основано на измерении глубины проникновения индентора в материал под определенной нагрузкой. В тесте используется стандартная нагрузка для каждой шкалы, а твердость определяется глубиной проникновения после снятия нагрузки. В нем используется либо алмазный конус, либо индентор из стального шарика. Факторы, влияющие на измерения твердости, включают тип материала, размер и форму индентора, а также нагрузку, приложенную к индентору. Существуют различные шкалы Роквелла, каждая из которых предназначена для определенного типа материала, например стали, алюминий и пластик.
Процедура проведения испытания на твердость по Роквеллу включает подготовку образца, размещение его на плоской поверхности и приложение нагрузки к индентору. Индентор вдавливается в материал в течение определенного времени, а глубина вдавливания косвенно измеряется с помощью циферблата или цифрового считывателя на испытательной машине. Результат выражается числом по шкале твердости Роквелла. Тест является неразрушающим и может использоваться как на малых, так и на больших образцах. На точность теста на твердость по Роквеллу могут влиять чистота поверхности, размер и геометрия образца.
Применение теста на твердость по РоквеллуИспытание на твердость по Роквеллу широко используется в обрабатывающей промышленности для контроля качества. Он используется для обеспечения того, чтобы материалы соответствовали требуемым характеристикам твердости для конкретного применения. Тест также используется при выборе материала для определения пригодности материала для конкретного применения. В исследованиях и разработках испытание на твердость по Роквеллу используется для изучения влияния различных методов обработки на свойства материала.
Этот тест имеет ряд преимуществ перед другими тестами на твердость. Его легко выполнить, и он обеспечивает быстрые и точные результаты. Испытание является неразрушающим и не повреждает тестируемый материал. Кроме того, тест можно проводить как на малых, так и на больших образцах.
Ограничения теста на твердость по РоквеллуИспытание на твердость по Роквеллу имеет некоторые ограничения. Тест ограничен некоторыми материалами, такими как металлы, и может не подходить для других материалов, таких как керамика и композиты. На испытание влияют условия поверхности, такие как шероховатость и неровности поверхности, и оно может не дать полной картины свойств материала. На тест также влияет размер и геометрия образца, что может повлиять на точность результатов.
Твердость лезвия ножа является важным фактором его производительности. Слишком мягкое лезвие не будет держать лезвие, а слишком твердое лезвие может быть хрупким и склонным к сколам или поломке. Твердость лезвия определяется типом используемой стали и процессом термической обработки, используемым для упрочнения лезвия. Тест Роквелла используется для измерения твердости лезвия и проверки его соответствия требованиям для использования по назначению.
В ножевой промышленности испытание на твердость по Роквеллу обычно используется для измерения твердости лезвия на обухе и кромке. Шкала Роквелла, используемая для ножей, обычно представляет собой шкалу C, которая измеряет твердость закаленной стали.
Для проведения теста на твердость по Роквеллу в лезвие вдавливается алмазный или карбид вольфрамовый шарик с определенной нагрузкой. Измеряют глубину вдавливания и определяют твердость по шкале Роквелла. Результат выражается числом по шкале С Роквелла, которая для большинства ножевых лезвий находится в диапазоне от 50 до 65.
Хотя тест Роквелла является полезным инструментом для измерения твердость лезвия, он имеет некоторые ограничения. Тест не учитывает качество процесса термообработки, что может повлиять на твердость лезвия. Тест также не учитывает геометрию лезвия, что может повлиять на твердость на кромке. Наконец, тест не учитывает ударную вязкость лезвия, что важно для сопротивления сколам и поломкам.
Будущие разработки в технологии определения твердости
Испытание на твердость по Роквеллу — это хорошо зарекомендовавший себя метод измерения твердости материалов, который используется уже более 90 лет. Однако у теста на твердость по Роквеллу есть ограничения, а достижения в области технологий привели к разработке других методов определения твердости.
Например, тест на твердость по Виккерсу, в котором используется алмазный индентор, может использоваться для измерения твердости широкого спектра материалов, включая керамику и композиты. Тест на твердость по Кнупу, в котором используется пирамидальный индентор, используется для измерения твердости тонких покрытий и поверхностных слоев. Тест на твердость по Бринеллю, в котором используется шариковый индентор большего диаметра, используется для измерения твердости мягких материалов и крупных отливок.
В последние годы возрос интерес к разработке методы определения микротвердости, которые используются для измерения твердости небольших или тонких образцов. В этих тестах используется очень маленькая нагрузка, обычно менее 1 кг, и небольшой индентор, что позволяет проводить точные измерения твердости на небольших участках.
Еще одна область развития заключается в использовании цифровой обработки изображений для повышения точности и прецизионности измерений твердости. Эта технология использует передовые алгоритмы для анализа изображений отпечатка, сделанного индентором, и для расчета твердости материала на основе размеров отпечатка.
Часто задаваемые вопросы
Что такое хорошая твердость по Роквеллу для ножа?Хороший ассортимент для большинства ножи находится между 56 и 62 по шкале С Роквелла (HRC).
Низкий HRC (56-58) обычно означает, что сталь более мягкая и пластичная, что облегчает ее заточку и делает ее более устойчивой к сколам. Однако он также может не удержать своего края. Этот диапазон более характерен для тяжелых ножей, таких как тесаки или мачете.
Более высокое значение HRC (58-60) указывает на более твердую и износостойкую сталь, способную удерживать острую кромку в течение более длительного времени. Этот диапазон предпочтителен для многих ножей для повседневного ношения (EDC), кухонных ножей и складных ножей. Однако более твердые стали могут быть более хрупкими и склонными к сколам.
Подходит ли 58 HRC для ножа?Твердость по Роквеллу 58 HRC можно считать хорошей для определенных типов ножей. Этот уровень твердости предлагает баланс между прочностью и сохранением края. Ножи с твердостью 58 HRC легче затачивать, они более устойчивы к сколам и достаточно долговечны.
Однако пригодность ножа твердостью 58 HRC также зависит от его предполагаемого использования и предпочтений пользователя. Эта твердость подходит для тяжелых работ или использования на открытом воздухе. Для ножей, которым требуется более острый край в течение длительного времени, таких как высокопроизводительные кухонные ножи или некоторые ножи для повседневного ношения (EDC), может быть предпочтительнее более высокий HRC (59-62).
Дешевые ножи часто имеют более низкую твердость по Роквеллу, обычно от 52 до 56 HRC. Эти ножи сделаны из менее дорогой и более мягкой стали, что делает их более простыми в производстве и более доступными. Однако более низкая твердость означает, что они могут не удерживать остроту лезвия долго, и им может потребоваться более частая заточка.
Важно отметить, что, хотя эти ножи могут подходить для легких задач, они могут не работать должным образом для тяжелых или точных задач резки. Кроме того, качество стали и процесс термообработки у недорогих ножей могут значительно различаться, что приводит к несоответствиям в производительности и долговечности.
В заключение, испытание на твердость по Роквеллу является широко используемым методом измерения твердости материалов. Это неразрушающий и простой в выполнении тест, который дает быстрые и точные результаты. Тест имеет ограничения, такие как его пригодность для определенных материалов и влияние состояния поверхности на точность результатов.
Однако достижения в технологии определения твердости привели к разработке других методов определения твердости, которые можно использовать для более широкого круга материалов и областей применения.
Будущие разработки в области технологий, такие как измерение микротвердости и цифровая обработка изображений, продолжат повышать точность и точность методов определения твердости. Испытание на твердость по Роквеллу останется важным инструментом контроля качества, выбора материалов, а также исследований и разработок, но оно будет дополняться другими методами испытаний по мере появления новых материалов и приложений.
youtube.com/embed/vimOi2iz2r4?controls=0&modestbranding=1&rel=0&iv_load_policy=3&autoplay=1″ src=”data:text/html;https://www.youtube.com/embed/vimOi2iz2r4?controls=0&modestbranding=1&rel=0&iv_load_policy=3&autoplay=1;base64,PGJvZHkgc3R5bGU9J3dpZHRoOjEwMCU7aGVpZ2h0OjEwMCU7bWFyZ2luOjA7cGFkZGluZzowO2JhY2tncm91bmQ6dXJsKGh0dHBzOi8vaW1nLnlvdXR1YmUuY29tL3ZpL3ZpbU9pMml6MnI0LzAuanBnKSBjZW50ZXIvMTAwJSBuby1yZXBlYXQnPjxzdHlsZT5ib2R5ey0tYnRuQmFja2dyb3VuZDpyZ2JhKDAsMCwwLC42NSk7fWJvZHk6aG92ZXJ7LS1idG5CYWNrZ3JvdW5kOnJnYmEoMCwwLDApO2N1cnNvcjpwb2ludGVyO30jcGxheUJ0bntkaXNwbGF5OmZsZXg7YWxpZ24taXRlbXM6Y2VudGVyO2p1c3RpZnktY29udGVudDpjZW50ZXI7Y2xlYXI6Ym90aDt3aWR0aDoxMDBweDtoZWlnaHQ6NzBweDtsaW5lLWhlaWdodDo3MHB4O2ZvbnQtc2l6ZTo0NXB4O2JhY2tncm91bmQ6dmFyKC0tYnRuQmFja2dyb3VuZCk7dGV4dC1hbGlnbjpjZW50ZXI7Y29sb3I6I2ZmZjtib3JkZXItcmFkaXVzOjE4cHg7dmVydGljYWwtYWxpZ246bWlkZGxlO3Bvc2l0aW9uOmFic29sdXRlO3RvcDo1MCU7bGVmdDo1MCU7bWFyZ2luLWxlZnQ6LTUwcHg7bWFyZ2luLXRvcDotMzVweH0jcGxheUFycm93e3dpZHRoOjA7aGVpZ2h0OjA7Ym9yZGVyLXRvcDoxNXB4IHNvbGlkIHRyYW5zcGFyZW50O2JvcmRlci1ib3R0b206MTVweCBzb2xpZCB0cmFuc3BhcmVudDtib3JkZXItbGVmdDoyNXB4IHNvbGlkICNmZmY7fTwvc3R5bGU+PGRpdiBpZD0ncGxheUJ0bic+PGRpdiBpZD0ncGxheUFycm93Jz48L2Rpdj48L2Rpdj48c2NyaXB0PmRvY3VtZW50LmJvZHkuYWRkRXZlbnRMaXN0ZW5lcignY2xpY2snLCBmdW5jdGlvbigpe3dpbmRvdy5wYXJlbnQucG9zdE1lc3NhZ2Uoe2FjdGlvbjogJ3BsYXlCdG5DbGlja2VkJ30sICcqJyk7fSk7PC9zY3JpcHQ+PC9ib2R5Pg==”>
Шкалы твердости по Роквеллу
Шкалы твердости по Роквеллу Шкала, показывающая твердость материалов, впервые использованная в 1919 году, когда ее изобрел Стэнли П.
Как и шкала твердости по Бринеллю, шкала Роквелла основана на измерении глубины отпечатка, сделанного путем вдавливания алмазного наконечника или шарика в материал. Однако, в отличие от теста Бринелля, тест Роквелла выполняет два измерения глубины. Мяч (скажем) приводится в контакт с тестируемым материалом. Предварительное усилие прикладывается в течение заданного промежутка времени, а затем измеряется глубина вдавливания. Затем сила увеличивается с заданной скоростью, пока не достигнет полной силы. Эта сила сохраняется постоянной в течение заданного периода времени, после чего сила снижается до предварительного уровня силы. Через заданный период времени глубину отпечатка измеряют второй раз.
Твердость по Роквеллу рассчитывается как разница между глубиной вмятины после того, как испытуемый материал «отскочил» от приложения полной силы, и ее начальной глубиной под действием предварительной силы. Назовите эту разницу в миллиметрах ч. Затем
Если в тесте используется сфероконический алмаз:
Если в тесте используется мяч:
Обычные весы Роквелла | ||||
---|---|---|---|---|
Символ шкалы | Индентор типа (если шарик, диаметр) | Предварительное усилие | Общая сила | Типичное использование |
HRA | Алмаз сфероконической формы | 98,07 Н (10 кгс) | 588,4 Н (60 кгс) | Твердые сплавы, тонкая сталь и мелкозернистая цементируемая сталь. |
ХРБ | Шар, 1,588 мм (¹⁄₁₆″) | 98,07 Н (10 кгс) | 980,7 Н (100 кгс) | Медные сплавы, мягкие стали, алюминиевые сплавы, ковкий чугун и т.![]() |
HRc | Алмаз сфероконической формы | 98,07 Н (10 кгс) | 1471 Н (150 кгс) | Сталь, твердый чугун, перлитный ковкий чугун, титан, сталь с глубокой поверхностной закалкой и другие материалы твердостью более 100 по шкале Роквелла B. |
ХРД | Алмаз сфероконический | 98,07 Н (10 кгс) | 980,7 Н (100 кгс) | Тонкая сталь и сталь средней поверхностной закалки, а также перлитный ковкий чугун. |
ПЧ | Шар, 3,175 мм (⅛″) | 98,07 Н (10 кгс) | 980,7 Н (100 кгс) | Чугун, алюминиевые и магниевые сплавы и подшипниковые металлы. |
хорватских рупий | Шар, 1,588 мм (¹⁄₁₆″) | 98,07 Н (10 кгс) | 588,4 Н (60 кгс) | Отожженные медные сплавы и тонкий мягкий листовой металл. |
ХРГ | Шар, 1,588 мм (¹⁄₁₆″) | 98,07 Н (10 кгс) | 1471 Н (150 кгс) | Чугуны ковкие, медно-никелево-цинковые и мельхиоровые сплавы.![]() |
HRH | Шар, 3,175 мм (⅛″) | 98,07 Н (10 кгс) | 588,4 Н (60 кгс) | Алюминий, цинк и свинец. |
кун | Шар, 3,175 мм (⅛″) | 98,07 Н (10 кгс) | 1471 Н (150 кгс) | Подшипниковые металлы и другие очень мягкие или тонкие материалы. Используйте самый маленький шар и самый тяжелый груз, который не дает эффекта наковальни. |
ХРЛ | Шар, 6,350 мм (¼′) | 98,07 Н (10 кгс) | 588,4 Н (60 кгс) | |
HR | Шар, 6,350 мм (¼″) | 98,07 Н (10 кгс) | 980,7 Н (100 кгс) | |
ХРП | Шар, 6,350 мм (¼″) | 98,07 Н (10 кгс) | 1471 Н (150 кгс) | |
Рубль | Шар, 12,70 мм (½″) | 98,07 Н (10 кгс) | 588,4 Н (60 кгс) | |
ХРС | Шар, 12,70 мм (½″) | 98,07 Н (10 кгс) | 980,7 Н (100 кгс) | |
ВСР | Шар, 12,70 мм (½″) | 98,07 Н (10 кгс) | 1471 Н (150 кгс) |
Поверхностные весы Роквелла | ||||
---|---|---|---|---|
Шкала Символ | Тип индентора Если шарик, диаметр в (дюймы) | Предварительная сила в ньютонах (кг-сила) | Суммарная сила ньютонов (кгс) | Типичные Приложения |
15Н | Алмаз сфероконической формы | 29,42 (3) | 147,1 (15) | Аналогичен шкалам A, C и D , , но для более тонкого калибровочного материала или глубины корпуса. ![]() |
30Н | Алмаз сфероконической формы | 29,42 (3) | 294,2 (30) | |
45Н | Алмаз сфероконической формы | 29,42 (3) | 441,3 (45) | |
15Т | Шар 1,588 (1/16) | 29,42 (3) | 147,1 (15) | Аналогичен шкалам B, F и G, , но для более тонкого калибровочного материала . |
30Т | Шар 1,588 (1/16) | 29,42 (3) | 294,2 (30) | |
45Т | Шар 1,588 (1/16) | 29,42 (3) | 441,3 (45) | |
15 Вт | Шар 3,175 (⅛) | 29,42 (3) | 147,1 (15) | Очень мягкий материал. |
30 Вт | Шар 3,175 (⅛) | 29,42 (3) | 294,2 (30) | |
45 Вт | Шар 3,175 (1/8) | 29,42 (3) | 441,3 (45) | |
15X | Мяч 6. ![]() (¼) | 29,42 (3) | 147,1 (15) | |
30Х | Шар 6.350 (¼) | 29,42 (3) | 294,2 (30) | |
45Х | Шар 6.350 (¼) | 29,42 (3) | 441,3 (45) | |
15 лет | Шар 12,70 (½) | 29,42 (3) | 147,1 (15) | |
30 лет | Шар 12,70 (½) | 29,42 (3) | 294,2 (30) | |
45 лет | Шар 12,70 (½) | 29,42 (3) | 441,3 (45) |
Таблица адаптирована из Таблицы 1
Сэмюэл Р. Лоу.
Измерение твердости металлических материалов по Роквеллу.
Рекомендованное практическое руководство NIST.
Специальная публикация 960-5.
Вашингтон: USGPO. 2001.
стандарты
ASTM E 18-05, Стандартные методы испытаний по Роквеллу
Твердость и поверхностная твердость по Роквеллу металлических материалов.
ISO 6508-1 Металлические материалы. Испытание на твердость по Роквеллу (шкала A, B, C, D, E, F, G, H, K, N, T) – Часть 1: Метод испытания, 1999-09-01
ISO 6508-2 Металлические материалы. Испытание на твердость по Роквеллу (шкала A, B, C, D, E, F, G, H, K, N, T) – Часть 2: Проверка испытательных машин, 1999-09-01
ISO 6508-3 Металлические материалы. Испытание на твердость по Роквеллу (шкала A, B, C, D, E, F, G, H, K, N, T) – Часть 3: Калибровка эталонных мер, 1999-09-01
хотите еще?
http://classes.mst.edu/civeng120/lessons/hardness/equipment/rockwell/index.html
Copyright © Sizes, Inc., 2008, 2021. Все права защищены.
Последняя редакция: 14 ноября 2021 г.
Понимание твердости металлов
Основы инженерного дела
Михал Ярмолюк с Pixabay
Твердость — шаткое понятие, и существует так много различных широко используемых методов определения твердости, что легко запутаться. Здесь мы устраняем путаницу.
Дэйв Палмер | 12 октября 2021 г.
При проектировании металлических деталей важно указывать их твердость. Однако многие инженеры имеют лишь шаткое представление о том, что такое твердость на самом деле или как ее измеряют. Для этого есть веские причины. Как мы увидим, твердость — довольно шаткое понятие, и существует так много различных широко используемых методов определения твердости, что легко запутаться. Цель этой статьи — помочь прояснить эту путаницу.
Сначала поговорим о том, чем твердость не является. Жесткость не имеет ничего общего с жесткостью. Стальная деталь может иметь высокую или низкую твердость, но она всегда будет иметь одинаковую жесткость. Титановая деталь может иметь ту же твердость, что и стальная, но ее жесткость всегда будет вдвое меньше, чем у стали. Твердость сама по себе также не имеет ничего общего с тем, является ли материал хрупким или пластичным. Из двух материалов с одинаковой твердостью один может быть хрупким, а другой пластичным.
Что такое твердость? Чтобы дать несколько круговое и не очень полезное определение, это мера того, как материал ведет себя в тесте на твердость. Это подводит нас к теме испытаний на твердость.
Один из тестов на твердость, наиболее часто используемый в США, был разработан Хью Роквеллом и Стэнли Роквеллом в 1914 году. Хотя они не были ни братьями, ни даже родственниками, наличие одной фамилии значительно облегчало придумывание имени. для теста. В тесте Роквелла индентор вдавливается в металлическую поверхность с заданной силой. Твердость обратно пропорциональна глубине проникновения.
Существует множество шкал твердости по Роквеллу, в зависимости от типа используемого индентора и нагрузки. Например, в шкале Роквелла С используется конусообразный индентор с алмазным наконечником, рассчитанный на нагрузку 150 кг. В шкале Rockwell B используется шариковый индентор диаметром 1/16 дюйма с нагрузкой 100 кг. Шкала Роквелла C обычно обозначается аббревиатурой HRC (твердость по Роквеллу C), а шкала Роквелла B обозначается аббревиатурой HRB (твердость по Роквеллу B). Чем выше число, тем тверже материал, но только относительно других чисел в данной шкале. Например, очень твердая сталь может иметь твердость 64 HRC, а достаточно мягкая сталь может иметь твердость 70 HRB.
Какие весы лучше использовать? Это зависит от того, что вы измеряете. Шкала Rockwell C хороша для измерения закаленной стали. Rockwell B лучше подходит для более мягкой стали или относительно твердого алюминия. Для более мягкого алюминия вам может понадобиться шкала Rockwell E (шар диаметром 1/8 дюйма с нагрузкой 100 кг) или шкала Rockwell F (шар диаметром 1/16 дюйма с нагрузкой 60 кг). Как правило, чем больше индентор или чем меньше нагрузка, тем лучше будет шкала для мягких материалов.
Толщина материала также имеет значение. Если вы пытаетесь измерить твердость тонкой полоски материала, вам не следует использовать нагрузку, которая будет проталкивать индентор через материал на другую сторону.