Твердость после закалки стали 45: Закалка и отпуск стали 45. Как закалить сталь 45 в домашних условиях?
alexxlab | 21.03.2023 | 0 | Разное
Марка: 45ГЛ (заменитель: 40ХЛ) Класс: Сталь для отливок обыкновенная Вид поставки: отливки: ТУ 24-1-12-181-75. Использование в промышленности: блоки, колеса, звездочки, кулачковые муфты, крупные зубчатые венцы и другие детали, требующие повышенной твердости и прочности. |
Химический состав в % стали 45ГЛ | ||
C | 0,42 — 0,5 | |
Si | 0,2 — 0,45 | |
Mn | 0,9 — 1,2 | |
Ni | до 0,45 | |
S | до 0,04 | |
P | до 0,04 | |
Cr | до 0,04 | |
Cu | до 0,3 | |
Fe | ~97 |
Свойства и полезная информация: |
Термообработка: Закалка 860 — 880oC, вода, Отпуск 580 — 630oC, вода.![]() Температура критических точек: Ac1 = 724 , Ac3(Acm) = 775 , Ar1 = 675 Свариваемость материала: ограниченно свариваемая. Флокеночувствительность: не чувствительна. Склонность к отпускной хрупкости: не склонна. Обрабатываемость резанием: после закалки и отпуска при HB 241-278 и σв=850-980 МПа, К υ тв. спл=0,63 и Кυ б.ст=0,5 Температура начала затвердевания, °С: 1490-1501 Показатель трещиноустойчивости, Кт.у.: 0,9. Склонность к образованию усадочной раковины, Ку.р.:1,1. Жидкотекучесть, Кж.т: 0,8. Линейная усадка, %: 2.2 Склонность к образованию усадочной пористости, Ку.п.:1,0. |
Механические свойства стали 45ГЛ | |||||||
Режим термообработки | Сечение, мм | σ0,2 (МПа) | σв(МПа) | δ5 (%) | ψ % | KCU (Дж/см2) | НВ, не более |
Закалка 860-880 °С, вода.![]() | До 100 | 490 | 690 | 10 | 25 | 39 | 217-269 |
Твёрдость стали 45ГЛ после закалки ТВЧ | |
Режим термообработки | НRCЭ поверхности |
Закалка ТВЧ, охлаждение в водном растворе глицирина. Низкий отпуск | 42-56 |
Поверхностная закалка с нагревом газовым пламенем, охлаждение на воздухе, затем в воде | 42 |
Опубликовано: 2010.11.02
Краткие обозначения: | ||||
σв | — временное сопротивление разрыву (предел прочности при растяжении), МПа | ε | — относительная осадка при появлении первой трещины, % | |
σ0,05 | — предел упругости, МПа | Jк | — предел прочности при кручении, максимальное касательное напряжение, МПа | |
σ0,2 | — предел текучести условный, МПа | σизг | — предел прочности при изгибе, МПа | |
δ5,δ4,δ10 | — относительное удлинение после разрыва, % | σ-1 | — предел выносливости при испытании на изгиб с симметричным циклом нагружения, МПа | |
σсж0,05 и σсж | — предел текучести при сжатии, МПа | J-1 | — предел выносливости при испытание на кручение с симметричным циклом нагружения, МПа | |
ν | — относительный сдвиг, % | n | — количество циклов нагружения | |
sв | — предел кратковременной прочности, МПа | R и ρ | — удельное электросопротивление, Ом·м | |
ψ | — относительное сужение, % | E | — модуль упругости нормальный, ГПа | |
KCU и KCV | — ударная вязкость, определенная на образце с концентраторами соответственно вида U и V, Дж/см2 | T | — температура, при которой получены свойства, Град | |
sT | — предел пропорциональности (предел текучести для остаточной деформации), МПа | l и λ | — коэффициент теплопроводности (теплоХотСтилость материала), Вт/(м·°С) | |
HB | — твердость по Бринеллю | C | — удельная теплоХотСтилость материала (диапазон 20o — T ), [Дж/(кг·град)] | |
HV | — твердость по Виккерсу | pn и r | — плотность кг/м3 | |
HRCэ | — твердость по Роквеллу, шкала С | а | — коэффициент температурного (линейного) расширения (диапазон 20o — T ), 1/°С | |
HRB | — твердость по Роквеллу, шкала В | σt | — предел длительной прочности, МПа | |
HSD | — твердость по Шору | G | — модуль упругости при сдвиге кручением, ГПа |
_ _ _ _ _ _ _ _ _ _ _ _ _ _ _ _ _ _ _ _ _ _ _ _ _ _ _ _ _ _ _ _ _ _ _ _ _ _ _ _ _ _ _ _ _ _ _ _ _ _ _ _ _ _ _ _ _ _ _ _ _ _ _ _ _ _ _ _ _ _ _ _ _ _ _ _ _ _ _ _ _ _ _ _ _ _ _ _ _ _ _ _ _ _ _ _ _ _ _ _ _ _ _ _ _ _ _ _ _ _ _ _ _ _ _ _ _ _ _ _ _ _ _ _ _ _ _ _ _ _ _ _ _ _ _ _ _ _ _ _ _ _ _ _ _ _ _ _ _ _ _ _ _ _ _ _ _ _ _ _ _ _ _ _ _ _ _ _ _ _ _ _ _ _ _ _ _ _ _ _ _ _ _ _ _ _ _ _ _ _ _ _ _ _ _ _ _ _ _ _ _ _ _ _ _ _ _ _ _ _ _ _ _ _ _ _ _ _ _ _ _ _ _ _ _ _ _ _ _ _ _ _ _ _ _ _ _ _ _ _ _ _ _ _ _ _ _ _ _ _ _ _ _ _ _ _ _ _ _ _ _ _ _ _ _ _ _ _ _ _ _ _ _ _ _ _ _ _ _ |
Химический состав, механические, физические и технологические характеристики
2. 3.15. Прокат с качеством поверхности группы 2ГП с испытанием на горячую осадку (65).
Испытание проката размером св. 80 мм изготовитель может не проводить.
2.3.16. Прокат из стали марок 45, 50, 50А с контролем твердости (ТВ4) на закаленных образцах в соответствии с требованиями, указанными в табл. 8а.
2.3.17. Массовая доля азота не более 0,008 % в кислородно-конвертерной стали для тонколистового проката.
2.3.13-2.3.17. (Введены дополнительно, Изм. № 1).
2.4. Допускается в технических условиях на конкретную продукцию предусматривать дополнительные или повышенные характеристики, не предусмотренные настоящим стандартом.
Перечень дополнительных характеристик приведен в приложении 5.
2.5. Маркировка и упаковка проката — по ГОСТ 7566.
2.5.1. Упаковка калиброванного проката — по ГОСТ 1051, со специальной отделкой поверхности — по ГОСТ 14955.
2.5.2. Маркировку наносят непосредственно на продукцию, если продукция не подлежит упаковке, и на ярлык, если продукция упакована в связки, мотки и бухты.
3.1. Прокат принимают партиями, состоящими из стали одной плавки, одного размера и одного режима термической обработки (при изготовлении в термически обработанном состоянии).
По согласованию изготовителя с потребителем партии формируются из стали одной марки нескольких плавок одного размера.
Каждую партию сопровождают документом о качестве по ГОСТ 7566.
При использовании для полуспокойной стали других (кроме кремния) раскислителей делается соответствующее указание в документе о качестве.
Для проката, принимаемого с характеристиками, устанавливаемыми потребителем в соответствии с пп. 2.2 и 2.3, в документе о качестве указывают результаты испытаний по заказываемым показателям.
3.2. Прокат подвергают приемо-сдаточным испытаниям.
3.3. Для проверки качества от партии проката отбирают:
1) для химического анализа — пробы по ГОСТ 7565. Контроль остаточных меди, никеля, хрома, мышьяка и азота изготовитель проводит периодически не реже раза в квартал. При изготовлении стали с учетом марганцевого эквивалента контроль остаточных меди, никеля и хрома проводят на каждой плавке;
2) для контроля качества поверхности и размеров — все прутки, полосы и мотки;
3) для контроля макроструктуры по излому или травлением, для испытания на ударный изгиб, определения глубины обезуглероженного слоя — два прутка, полосы или мотка;
4) для проверки твердости — 2 % прутков, полос или мотков, но не менее 3 штук;
5) для испытания на растяжение — один пруток, полосу или моток для контроля в нормализованном состоянии, два прутка, две полосы или два мотка для контроля в нагартованном, отожженном, высокоотпущенном или закаленном с отпуском состоянии;
6) для определения прокаливаемости — один пруток, полосу или моток от плавки-ковша стали всех марок, не содержащих бор, и два прутка, две полосы или два мотка от плавки — ковша стали марок, содержащих бор;
7) для определения величины зерна — один пруток, полосу или моток от плавки-ковша;
для испытания на осадку — три прутка, полосы или мотка;
9) для определения твердости после закалки — два продольных образца от плавки.
(Измененная редакция, Изм. № 1).
3.4. При получении неудовлетворительных результатов испытаний хотя бы по одному из показателей по нему проводят повторные испытания по ГОСТ 7566.
Результаты повторных испытаний распространяют на всю партию.
4.1. Химический анализ стали проводят по ГОСТ 22536.0 — ГОСТ 22536.9, ГОСТ 27809, ГОСТ 12359 или другими методами по точности, не уступающими стандартным. При возникновении разногласий химический анализ проводят по ГОСТ 22536.0-ГОСТ 22536.9, ГОСТ 27809, ГОСТ 12359.
4.2. Качество поверхности проверяют осмотром проката без применения увеличительных приборов. При необходимости проводят светление или травление поверхности, а для проката со специальной отделкой поверхности диаметром до 3 мм включительно осмотр проводят при увеличении до 10х. Глубину залегания дефектов на поверхности проката определяют контрольной зачисткой или запиловкой напильником.
4.3. Геометрические размеры и форму определяют при помощи измерительных инструментов по ГОСТ 26877, ГОСТ 162, ГОСТ 166, ГОСТ 427, ГОСТ 3749, ГОСТ 5378, ГОСТ 6507, ГОСТ 7502, или инструментов, аттестованных по ГОСТ 8. 001 или ГОСТ 8.326.
4.4. Отбор проб от мотков для всех видов испытаний проводят на расстоянии не менее 1,5 витка от конца раската.
4.5. От каждого отобранного для контроля прутка, полосы или мотка отбирают: для испытания на растяжение и осадку, для определения величины зерна, прокаливаемости и глубины обезуглероженного слоя — по одному образцу;
для испытания на ударный изгиб — по одному образцу каждого типа;
для контроля макроструктуры — один темплет.
4.6. Отбор проб для испытаний на осадку — по ГОСТ 7564.
4.7. Отбор проб для испытания механических свойств по табл. и проводят по ГОСТ 7564 (вариант 1), по табл. и — по ГОСТ 7564 (вариант 2).
(Измененная редакция, Изм. № 1).
4.7а. Отбор образцов для определения твердости после закалки проводят по схеме, приведенной в приложении 8.
Пробы для контроля могут быть вырезаны из готового проката или передельной заготовки (в плавочном контроле).
(Введен дополнительно, Изм. № 1).
4.8. Рекомендуемая температура нагрева образцов при испытании на горячую осадку 850-1000 °C. Температуру нагрева образцов указывают в документе о качестве.
Образцы нагревают до температуры ковки 850-1000 °С и осаживают на 65 % относительно первоначальной высоты. На осаженных образцах не должно быть раскрывшихся трещин и закатов.
4.9. Твердость по Бринеллю определяют по ГОСТ 9012. Твердость проката диаметром или толщиной менее 5 мм не определяют.
4.9а. Твердость по Роквеллу после закалки определяют по ГОСТ 9013 на площадке, расположенной на середине длины образца. Поверхность площадки для замера твердости подвергается зачистке; при этом шероховатость поверхности Ra должна быть не более 1,25 мкм по ГОСТ 2789.
(Введен дополнительно, Изм. № 1).
4.10. Испытание на растяжение проводят по ГОСТ 1497 на образцах пятикратной длины диаметром 5 или 10 мм.
Для проката диаметром или толщиной до 25 мм включительно испытание допускается проводить на образцах без механической обработки.
Испытание на ударную вязкость проводят по ГОСТ 9454 на образцах типа 1.
Направление оси образца — вдоль направления прокатки.
4.11. Образцы для испытаний на растяжение проката в соответствии с требованиями табл. 3 вырезают из нормализованных заготовок диаметром или стороной квадрата 25 мм.
Для прутков диаметром менее 25 мм нормализация проводится в готовом сечении прутка (без вырезки заготовки).
Примечание. От прутков размером более 120 мм отбор проб для механических испытаний может проводиться от перекованных или перекатанных заготовок сечением 90-100 мм.
4.12. Образцы для испытаний на растяжение проката в соответствии с требованиями табл. 8 вырезают из термически обработанных заготовок размером, указанным потребителем.
4.13. Режимы термической обработки заготовок (образцов) для проведения испытаний механических свойств приведены в приложениях и , для контроля твердости после закалки — в приложении 9.
(Измененная редакция, Изм. № 1).
4. 14. Контроль макроструктуры на излом или протравленных темплетах проводят без применения увеличительных приборов по ГОСТ 10243.
Допускается применять методы ультразвукового контроля (УЗК) и другие неразрушающие методы контроля, согласованные в установленном порядке.
4.15. Глубину обезуглероженного слоя определяют по ГОСТ 1763.
4.16. Прокаливаемость определяют методом торцевой закалки по ГОСТ 5657.
4.17. Величину зерна определяют по ГОСТ 5639.
4.18. На стали одной плавки, прошедшей испытания на макроструктуру, прокаливаемость и механические свойства на крупных профилях проката, при изготовлении более мелких профилей проката перечисленные испытания у изготовителя допускается не проводить.
4.19. Допускается у изготовителя применять статистические и неразрушающие методы контроля по методике, согласованной в установленном порядке. При возникновении разногласий и при периодических проверках качества продукции применяются методы контроля, предусмотренные настоящим стандартом.
5.1. Транспортирование и хранение — по ГОСТ 7566 со следующим дополнением.
5.1.1. Транспортирование продукции проводится транспортом всех видов в соответствии с правилами перевозки грузов, действующими на транспорте данного вида. По железным дорогам перевозка осуществляется в зависимости от массы и габаритных размеров в крытых или открытых вагонах. Масса грузового места не должна превышать при механизированной погрузке в открытые транспортные средства 10000 кг, в крытые — 1250 кг. Упаковка, средства и способы формирования пакетов — по ГОСТ 7566.
При отправке двух и более грузовых мест, размеры которых позволяют оформить транспортный пакет с габаритными размерами по ГОСТ 24597, грузовые места должны быть сформированы в транспортные пакеты. Средства крепления — по ГОСТ 21650.
Маркировка сплава
Конструкционные углеродистые качественные стали, по стандарту маркируются двузначным числом: сталь 05, 08…80, 85, которое указывает на усредненное значение, содержания углерода выраженное в сотых долях процента. Три цифры маркировки указывает на то что в сплаве содержится более чем 1% углерода, буква Л на отсутствие легировки — 45л, буквы Ст на его обыкновенное качество — Ст5.
Металлургическая промышленность производит стандартные стали марок от 05кп до 60, средний показатель углерода которых 0,05—0,60 процента, соответственно маркировки. Расшифровка марки стали 45 (фран. аналог С45) показывает содержание 0,45% С.
Сталь 45 и ее аналоги
Такой материал могут заменить следующие три марки стали: 50, 50 Г 2 и 40 Х.
Из них также создаются зубчатые колеса, цилиндры, эксцентрические насадки на вал, валы вращающиеся, коленчатые и распределительные, а также другие товары, применяемые в промышленности.
Марка стали 45 может именоваться по-разному в других странах и иметь несколько аналогов. К примеру, в США ей по свойствам равны 8 марок стали, в Германии – 10, во Франции – 14. В Польше аналог только один и он называется просто 45, в Австрии — C45SW.
Основные характеристики стали 45
Любой сплав имеет свои отличительные характеристики, определенный химический состав, ряд заменителей, функциональное предназначение.
Марки 40, 45, 50 выделяются высокими показателями прочности, имея при этом небольшую вязкость и пластичность. Поскольку механические свойства марки и 45 идентичны маркам 40 и 50, эти стали являются взаимозаменяемыми.
Химический состав и свойства
Химическими составляющими сплава помимо железа и углерода являются и ряд других элементов, количество которых малосущественно. Процентное отношение химических составляющих стали 45:
- Железо (Fe) — около 97%.
- Углерод (C) — 0,42—0,5%.
- Марганец (Mn) — 0,5—0,8%.
- Кремний (Si) — 0,17—0,37%.
- Никель (Ni) — не больше 0,25%.
- Хром (Cr) — не больше 0,25%.
- Медь (Cu) — не больше 0,25%.
- Мышьяк (As) — не больше 0,08%.
- Сера (S) — не больше 0,04%.
- Фосфор (P) — не больше 0,035%.
От химического состава стали и структуры напрямую зависят ее химические свойства. Все элементы входящие в состав условно делятся на полезные и вредные. Процесс добавления полезных примесей носит название легирование. Если расшифровать маркировку 45х, то становится ясно что сплав содержит добавление хрома, 45 г — марганца.
Основные химические свойства материала:
- степень окисления:
- устойчивость к коррозии;
- жароустойчивость;
- жаропрочность.
Механические характеристики
Для анализа и контролирования свойств стали используют различные методы их определения. К примеру, критерии прочности и пластичность определяют опытным путем, образцы растягивают до разрыва. Твердость сплавов фиксируют измеряя противодействие материала при влиянии на его поверхность твердого элемента, например, алмазного наконечника. Вязкость — ударными испытаниями специальных образцов.
Механические свойства и характеристики стали 45 (при t=20C).
Прочность — способность сплава выносить внешние нагрузки, не подвергаясь при этом разрушениям внутри. Характеризуется величинами: предел прочности, sв [МПа] и предел текучести стали 45, sT [МПа].
- труба — ГОСТ 8731–87 , sв =588 МПа, sT =323 МПа;
- прокат — ГОСТ 1050–88 , sв=600 МПа, sT =355 МПа;
- прокат отожженный — ГОСТ 1050–88 , sв =540 МПа.
Твердость — способность сплава оказывать сопротивление при воздействии твердых тел. Характеризуется величинами: твердость по Н. В. Бринеллю 10—1 [МПа], по Роквеллу HRC [МПа]. Для марки 45 в состоянии поставки:
- труба — ГОСТ 8731–87 , HB 10—1 = 207 МПа;
- прокат — ГОСТ 1050–88 , HB 10—1 = 229 МПа;
- прокат отожженка — ГОСТ 1050–88 , HB 10—1 = 207 МПа.
Пластичность — возможность сплава видоизменять свою форму под влиянием нагрузки и восстанавливать ее по окончании воздействия. Характеризуется величиной, относительное удлинение при разрыве, δ5 [ % ]:
- труба — ГОСТ 8731–87 , δ5 =14%;
- прокат — ГОСТ 1050–88 , δ5 =16%;
- прокат отожженка — ГОСТ 1050–88 — δ5 =13%.
Ударная вязкость — способность материала сопротивляться динамическим воздействиям нагрузки, KCU [ кДж / м2].
Физические свойства
К физическим характеристикам стали относятся: плотность, коэффициент теплового расширения, теплопроводность, модуль упругости, удельная теплоемкость и электропроводность.
Металлические сплавы имеют высокие показатели плотности, теплоемкости и электрической проводимости. Рассмотрим физические свойства марки 45 (при t=20C).
Плотность или удельный вес — масса вещества на единицу объема, плотность стали 45 ГОСТ 1050–88 ρ=7826—7595 кг/м3.
Коэффициент линейного теплового расширения количественно равен относительной перемене линейных размеров вещества при росте (понижении) температуры в сплаве на 1 градус Цельсия, α (1/град).
Теплопроводность вещества — способность отдавать количество тепла от более прогретого участка к менее прогретому. Характеризуется величиной коэффициента теплопроводности, λ [Вт/(м·град)].
Под модулем Юнга подразумевается физическая величина, которая косвенно отображает возможности стали противостоять продольным деформациям (растяжению или сжатию). Эта величина указывает на жесткость материала и является важной физической особенностью, E 10—5=2 МПа;
Удельная теплоемкость — количество тепла, необходимое для нагрева 1 килограмма вещества на 1 градус Цельсия, Ϲ [Дж/(кг·град).
Электропроводность — способность материала быть проводником электрического тока. Характеризуется величиной удельного электрического сопротивления, Ṛ [Ом·м].
Технологические характеристики применение стали 45
Технологические характеристики стали указывают на пригодность сплава к различным методам обработки. Материал имеет следующие технологические характеристики:
- Температура процесса ковки, градус — 1250 вначале, 700 в конце. Охлаждение сечений до 400 мм производится при нормальных условиях окружающей среды.
- Свариваемость — трудно поддается процессу сварки. Виды сварки: РДС и КТС, с использованием подогрева и последующей термообработки.
- Условия для резания — в горячекатаном состоянии при НВ 170—179 МПа и sB = 640 МПа.
- Не склонна к отпускной способности после отжига.
- Имеет малую флокеночувствительность.
Формирование метода термообработки материала, обусловлено эксплуатационными требованиями относительно деталей и механизмов. В металлообрабатывающей промышленности применяют такие виды обработки: нормализация, улучшение, закалка ТВЧ, закалка с низким отпуском и др.
Среднеуглеродистые стали нашли применение в изготовлении деталей, отличающихся повышенной прочностью материала с повышенным воздействием циклических нагрузок (зубчатые колеса редукторов, шатунные механизмы). Сталь марки 45 применяется при производстве:
- шестерен, вал-шестерней, коленчатых и распределительных валов, бандажей, цилиндров, кулачков; шпинделей;
- бесшовных труб и каркасных элементов трубопровода, требуют закалки и отпуска стали;
- ряда запчастей и конструкций в отрасли мотовелостроения.
Технологический пример. Тиски, круглогубцы и плоскогубцы, выполняют на основе сталей 45 и 50. Производя термическую закалку, в собранном виде, нагревать следует только губки изделия для предохранения от образования закалочных трещин. Для подобного нагрева предназначены свинцовые и соляные ванны. При обработке в камерной печи остывание области с резким переходом (шарнир) должно происходить медленно, опусканием и перемещением в жидкости только поверхности губок инструмента (до потускнения остальной части). Температурный режим процесса отпуска 220—320 градусов в интервале 30—40 минут.
Сталь 45 и ее характеристики
- Малая чувствительность к флокенам.
- Сталь 45 и ее удельный вес: показатель равен 7826 кг/м3.
- К отпускной хрупкости не склонна.
- Термообработка: Состояние поставки.
- Твердость стали 45: показатель равен следующим значениям: HB 10 -1 = 170 МПа
Прочность у данного материала повышенный. Именно поэтому из него изготавливаются предметы, которые можно нормализовать, улучшать, чьи поверхности можно подвергать термической обработке.
В данном материале имеется 0,45 процента углерода. Другие примеси крайне незначительны.
Сталь относится к трудносвариваемым материалам. Чтобы произвести процедуру сварки, требуется сначала подогреть сталь, а затем обработать термически. При ковке температура сначала должна быть 1250 градусов по Цельсию, а в конце снизиться до 700 градусов.
Если изделие имеет сечение, которое меньше или равно 400 миллиметрам, то его можно охлаждать на воздухе.
Другие ГОСТы
ГОСТ ISO 2081-2017 Металлические и другие неорганические покрытия. Электролитические покрытия цинком с дополнительной обработкой по чугуну и стали ГОСТ Р 51736-2001 Металлокерамика стоматологическая для зубного протезирования. Технические требования. Методы испытаний ГОСТ 31575-2012 Металлокерамика стоматологическая для зубного протезирования. Технические требования. Методы испытаний ГОСТ 14311-85 Металлокорд. Технические условия ГОСТ Р 54908-2012 Металлопродукция из жаростойкой стали. Технические условия ГОСТ 4543-2016 Металлопродукция из конструкционной легированной стали. Технические условия ГОСТ Р 54909-2012 Металлопродукция из легированной стали и сплавов для клапанов двигателей внутреннего сгорания. Технические условия ГОСТ 7566-2018 Металлопродукция. Правила приемки, маркировка, упаковка, транспортирование и хранение ГОСТ 26877-91 Металлопродукция. Методы измерения отклонений формы ГОСТ 26877-2008 Металлопродукция. Методы измерений отклонений формы ГОСТ 33439-2015 Металлопродукция из черных металлов и сплавов на железоникелевой и никелевой основе. Термины и определения по термической обработке ГОСТ Р 58765-2019 Металлопродукция из стали и сплавов. Термины и определения ГОСТ 5949-2018 Металлопродукция из сталей нержавеющих и сплавов на железоникелевой основе коррозионно-стойких, жаростойких и жаропрочных. Технические условия ГОСТ 14959-2016 Металлопродукция из рессорно-пружинной нелегированной и легированной стали. Технические условия
Точный химический состав сплава 45
Условия эксплуатации изделий из этого материала, а также данные по химическому составу и процентному соотношению веществ, представленных в стали марки 45, регламентируются нормами ГОСТ 1050-88.
В данный сплав входит 9 элементов. Основными и наиболее значимыми здесь являются марганец и углерод. Дополнительными считаются:
- Кремний
- Никель
- Медь
- Хром
- Мышьяк
- Сера
- Фосфор
Полная информация по процентному соотношению всех веществ, входящих в состав стали марки 45, представлено в таблице ниже и на диаграмме.
Mn | C | Si | Ni | Cu | Cr | As | S | Р |
от 0,5 до 0,8 | от 0,42 до 0,5 | 0,17 – 0,37 | менее 0,3 | меньше 0,3 | до 0,25 | менее 0,08 | до 0,04 | меньше 0,035 |
Как решить проблему недостаточной твердости при закалке?
В производстве иногда наблюдается недостаточная твердость после закалки, что является распространенным дефектом в процессе термической закалки. «Недостаточная твердость» имеет два проявления: 1) Вся заготовка имеет низкое значение твердости 2) Эта часть твердости недостаточна или появляются мягкие пятна.Когда возникает явление недостаточной твердости, следует использовать испытание на твердость или металлографический анализ, чтобы проанализировать, какая «твердость недостаточна», а затем найти причину в сырье, процессе нагрева, охлаждающей среде, методе охлаждения.
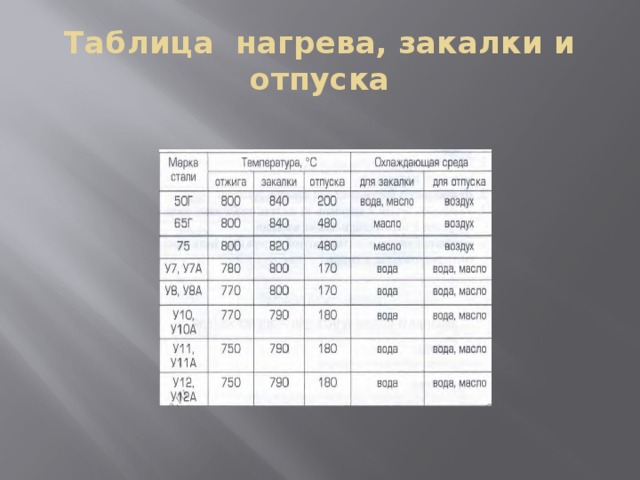
1.1 Неправильный выбор сырья или неподходящие материалы
Для изготовления деталей следует использовать среднеуглеродистую или высокоуглеродистую сталь, но неправильно использовать низкоуглеродистую сталь.
В заготовках должна использоваться легированная инструментальная сталь, но неправильное использование обычной высокоуглеродистой стали может привести к недостаточной твердости или размягчению.
Пример 1: Следует использовать зубчатое колесо из стали 45, а его твердость при закалке должна быть около 60HRC, и выбрать неправильный материал из стали 25. Таким образом, результирующая твердость может достигать только около 380HBS.
Пример 2: Вместо стали Т8 следует использовать форму из 9Мн2В. В связи с тем, что искры стали 9Мн2В и Т8 трудно различить, за процессом гашения ошибочно следовал процесс гашения 9Мн2В и применялось масляное охлаждение.

Вышеуказанные два случая относятся к недостаточной общей твердости, вы можете использовать тест на твердость или металлографический тест (закалка стали 25 для получения низкоуглеродистого мартенсита, как показано на рисунке 1, закалка стали 45 для получения мартенсита со средним содержанием углерода, как показано на картинке 2) судить.
Решение:1) При проектировании выберите соответствующие материалы;
2) Укрепление управления материалами. Химический анализ проводится до того, как материалы помещаются на склад, а затем они классифицируются для маркировки, что позволяет эффективно избежать отправки неправильных материалов;
3) Оператор термообработки должен перед операцией провести искровой анализ, чтобы примерно определить, соответствует ли материал детали требованиям чертежа;
4) Когда поперечное сечение заготовки большое или поперечное сечение заготовки толстое и тонкое, если используется инструментальная сталь, из-за ее плохой прокаливаемости это приведет к низкой внутренней твердости при большом поперечном сечении.

2.1 Низкая температура закалочного нагрева, недостаточное время выдержки температура нагрева при закалке стали ниже 860 ℃), так как феррит не полностью растворяется в аустените, после закалки не может быть получен однородный мартенсит, который является ферритом и мартенситом, влияет на твердость заготовки. Металлографический анализ показывает наличие нерастворенного феррита (как показано на рисунке 3).
Для высокоуглеродистой стали, особенно высоколегированной стали, если время нагрева или выдержки недостаточно, перлит не может превратиться в аустенит и не может быть получен мартенсит. В реальном производстве вышеуказанная ситуация часто возникает из-за отклонения показаний прибора (температура показаний слишком высока) или неравномерной температуры печи, что делает фактическую температуру заготовки низкой; Неправильная оценка толщины заготовки, из-за чего время выдержки оказывается слишком коротким.
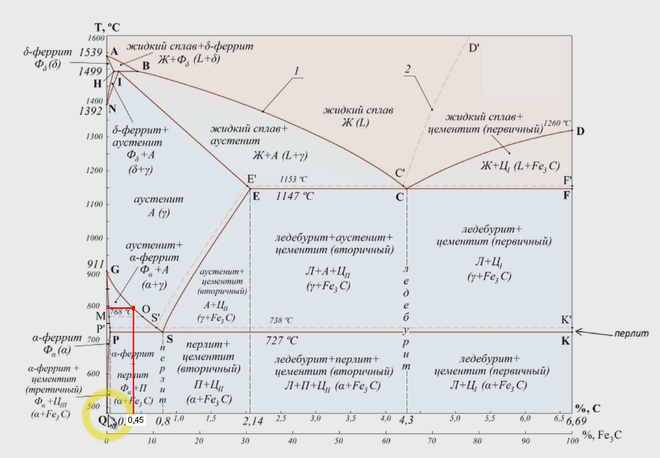
1) Контролируйте скорость нагрева, чтобы избежать слишком высокой скорости нагрева, что приводит к неравномерной температуре печи, в то же время вызывает преждевременное время изоляции, делая время изоляции недостаточным;
2) Всегда проверяйте исправность и точность показаний прибора, чтобы избежать явления, когда прибор показывает достигнутую температуру, а фактическая температура недостаточна;
3) Определяйте скорость нагрева и температуру нагрева строго в соответствии с руководством по материалу, чтобы температура охлаждения не была слишком низкой или слишком высокой;
4) Правильно оценить толщину материала, особенно фасонных частей.
3. При закалке и нагреве поверхность заготовки обезуглероживаетсяПосле закалки стали 45#, согласно металлографическому анализу, поверхность представляет собой феррит и низкоуглеродистый мартенсит, а после удаления поверхности обезуглероженный слой, твердость которого соответствует требованиям.
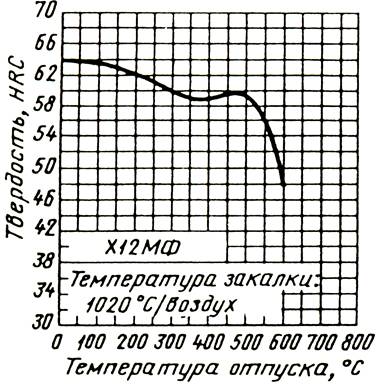
Такая ситуация часто возникает в камерной печи без защиты. Либо плохая защита, либо нагревание в соляной ванне с плохим раскислением, вызывающее реакцию кислорода с атомами углерода в заготовке с образованием СО, что снижает содержание углерода на поверхности заготовки, делая ее поверхностную твердость недостаточной.
Решение:1) Используйте неокислительную нагревательную печь
с защитной атмосферой , например защитная атмосфера для крекинга со спиртом и метанолом;2) Использовать закалку в вакууме;
3) Для обычных коробчатых печей для герметизации короба можно использовать железный лом или древесный уголь; поверхность заготовки покрыта антиокислительным покрытием; в топку помещается древесный уголь; заготовку покрывают раствором борной кислоты и спирта, а затем нагревают.
Короче говоря, часто возникает явление недостаточного гашения, и оператор должен проанализировать его в зависимости от различных ситуаций и выяснить причины, которые можно устранить.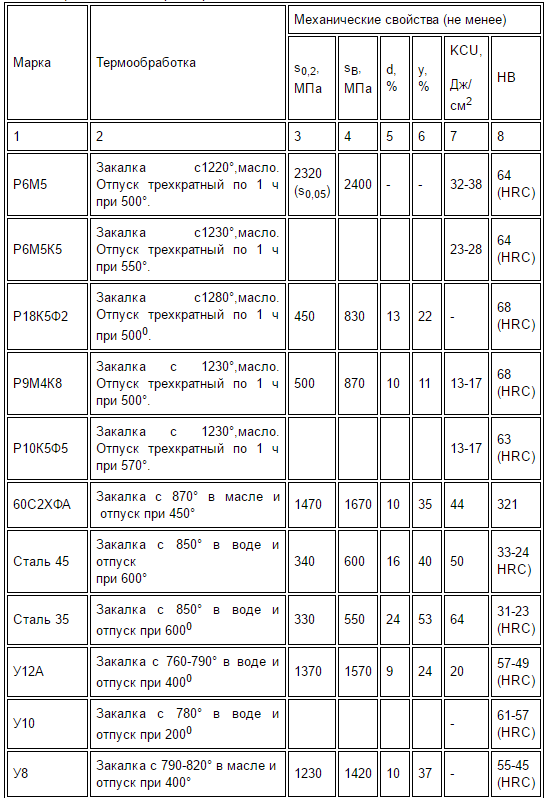
Я думаю, вы знаете это лучше меня, поэтому, если у вас есть какие-либо идеи об этой статье, пожалуйста, свяжитесь со мной, не стесняйтесь. Спасибо за чтение, и хорошего дня!
Закалка деталей EN8 / EN9. Вопросы и ответы, проблемы и решения
Где весь мир собирается для гальванического покрытия, анодирования и отделки
—–
См. также —
• Тема 20589«Стальные сплавы серии EN / EN8 по сравнению с EN9»
Q. EN 8 МАТЕРИАЛ ДИАМ. 7 ММ ТВЕРДОСТЬ 190 МАКС. Хотите добиться твердости до 350-400. Пожалуйста, порекомендуйте.
SATCHIT BASU
– ДЕЛИ, Индия
10 августа 2022 г.
Предыдущие тесно связанные вопросы и ответы, самые старые сначала:
2 марта 2009 г.
В. С материалом en9 я могу получить твердость 44-48 часов по всей детали. Если да, то можете ли вы предложить цикл h/t. Поскольку мы производим один продукт, который имеет эллиптическую протяжку посередине, в которой мы не можем получить твердость 44-48 часов, мы также обнаружили, что размеры нашей протяжки также изменились после окончательной термообработки. Так вы можете помочь получить твердость 44-48 часов?
Вишал Сачде
– Бхавнагар, Индия
6 марта 2009 г.
A. En9 — обычная нелегированная среднеуглеродистая сталь. Поэтому требуется очень сильное охлаждение в цикле термообработки, чтобы получить желаемую твердость, а толщина сечения, в свою очередь, сильно влияет на скорость охлаждения, которую можно достичь.
Информация, которую вы должны предоставить для дальнейшего ответа на ваш запрос:
1. Какая толщина сечения вашего компонента?
2. На какую глубину от поверхности вам нужна твердость 44-48 HRc?
3. Относительно Q2, хотите ли вы сквозное упрочнение?
4. Есть ли у вас оборудование для замачивания и закалки водой?
В зависимости от ответов на вышеприведенные вопросы может существовать цикл термической обработки, который даст вам то, что вы хотите получить на En9, или вам может потребоваться изменить марку на такую, которая имеет соответствующее содержание сплава, чтобы обеспечить закалку менее жестким закалка.
Билл Рейнольдс [умерший]
консультант-металлург – Балларат, Виктория, Австралия
Мы с прискорбием сообщаем, что Билл скончался 29 января 2010 года.
9 марта 2009 г.
A. Добрый день:
Учитывая ограниченную информацию, трудно сказать, возможна ли твердость 44-48 HRC. Размеры детали, толщина, закалка, перемешивание закалки, изменение химического состава от нагрева к нагреванию… вот некоторые из переменных, которые следует учитывать.
Поскольку это углеродный материал 0,50-0,60, при слишком высокой скорости закалки возможно коробление или растрескивание при закалке. Это может объяснить изменение размера протяжки. Если это тонкие детали, вы можете подвергнуть их аустенитной или маркировочной закалке, чтобы уменьшить коробление.
Если вы покупаете сталь с гарантированным диапазоном прокаливаемости, вы можете лучше предсказать реакцию на термообработку.
Если деталь слишком толстая для достижения достаточной твердости после закалки, может потребоваться замена материала.
Извините, быстрого ответа нет. Удачи.
Стив Бизуб
– Сент-Луис, Миссури
12 марта 2009 г.
A. Очевидно, что в EN 9 можно получить твердость 44-49 HRc, но, пожалуйста, укажите толщину сечения?
Пожалуйста, укажите, является ли dwg. требуется сквозная закалка и/или поверхностная закалка?
Делаем аналогичные компоненты; также укажите, является ли dwg. также указывает твердость сердцевины?
Я бы посоветовал больше закалки, чтобы избежать проблемы деформации
Просто для обмена, были изготовлены шкворни EN, которые были закалены до 25 Rc в сердцевине, затем поверхность была подвергнута индукционной закалке в полимерной закалке, чтобы придать твердость 55 hrc на поверхности на глубину 0,5 мм. таким образом достигается прочность, а также износостойкость, улучшается срок службы поверхности.
С уважением,
Викас
Викас Каушал
– Чандигарх, Индия
6 октября 2011 г.
В. В материалах EN9, C45 Flats and Bars мы не смогли получить требуемую твердость выше 50 HRC в закаленном состоянии при закалке в масле.
DEVA RAJAN
Менеджер по термообработке – COIMBATORE, Тамилнаду, Индия
10 марта 2012 г.
В. Наши компоненты имеют следующие размеры:
ДЛИНА: от 50 до 150 мм
ШИРИНА: от 07 до 20 мм
ТОЛЩИНА: от 0,8 до 1,5 мм
ИСПОЛЬЗУЕМЫЙ МАТЕРИАЛ — EN9
Может ли кто-нибудь предложить соответствующий процесс термообработки для достижения твердости по шкале Роквелла до 40-48?
Викас Мура
– ЧЕННАИ, Тамил Наду, ИНДИЯ
2 января 2013 г.
A. Да, если не считать моего опыта, материал EN 9 толщиной 0,75 ~ 1,50 мм может легко получить твердость 40 ~ 48 HRC путем изготовления компонентов в печи для закалки с сетчатой лентой, которая не будет иметь большого % обогащения углеродом и обезуглероживания из-за к непрерывному твердению. В условиях закалки твердость будет составлять 55 ~ 60 HRC, затем ее необходимо отпустить при 320 ~ 340 ° C в течение одного часа. Обычно это не вызывает больших искажений. В противном случае та же самая сетчатая ленточная печь с аустемперированием (закалка при 350 °C) даст 42 ~ 48 HRC, и дальнейший отпуск не потребуется.
DEVARAJ [фамилия удалена редактором из соображений конфиденциальности]
– KARUR, TN, India
4 января 2013 г.
В. Какова максимальная прокаливаемость материала EN9 при закалке в масле. Химический состав: C – 0,55, Si – 0,15, Mn – 0,75, P – 0,003, S – 0,005.
ДЕВАРАДЖАН ЛАКШМАНАН
– КОИМБАТУР, Индия
7 мая 2014 г.
В. Здравствуйте, сэр
. Мне нужны подробности о твердости стали EN8, и она используется для испытания на износ аустенизированного ковкого чугуна, и у меня твердость материала 33 HRC.
гопи натх
студент – Мадурай, Тамил Наду, Индия
3 июля 2014 г.
В. Я занимаюсь термообработкой в коммерческих целях.
Мы получили один валок трубной мельницы для термообработки
Размер 520 мм в диаметре. X 320 мм
Какую максимальную твердость можно получить с помощью закалки в масле?
Bharat V Shah
Услуги по обработке металлов – Ахмадабад, Гуджарат, ИНДИЯ
Привет, Девараджан, Гопи, Бхарат. С уважением, Тед Муни, ЧП Стремление жить Алоха Finishing.com – Пайн-Бич, Нью-Джерси |
10 апреля 2016 г.
В. Здравствуйте, сэр,
Я хочу узнать о процедуре термической обработки материала EN-9 для получения 36-47 HRC путем закалки. на самом деле мы делаем закалку с температурой 820/840 °C, но получаем очень низкую твердость при закалке (18-20 RC). Пожалуйста, дайте решение для этого.
Мадхави Редди
– Пуна, Индия
17 апреля 2017 г.
В. Материал EN9, требуемая твердость от 300 до 350 BHN, диаметр диаметра 680 мм, толщина 200 мм, диаметр отверстия 135 мм. Вес около 300 кг. Предложите возможность достижения требуемой твердости и параметры процесса.
Vijayendra T R
– Бангалор, Индия
Как добиться твердости до 45-50 HRC на C45?
8 мая 2017 г.
В. Можно ли при цементировании материала C45 получить твердость 44-50 HRC?
Длина 91 мм. Диаметр штифта 25 мм. И две ступеньки на обоих концах диаметром 12g6. А обработка поверхности – твердое хромирование. Требуемая глубина корпуса 0,8-1,2 мм.
Rajkumar w
покупатель – Пуна, Махараштра, Индия
17 мая 2017 г.
А. Привет, Раджкумар!
Вам нужно цементировать C45 до 44-50 HRC, я должен сказать, что вы можете достичь этой твердости без труда.
Твердость корпуса или сердцевины? Если это твердость корпуса, есть ли какие-либо спецификации для твердости сердцевины?
Если вы уже решили эту проблему, сообщите нам об этом! С уважением,
Daniel Montañés
TEL – N FERRARIS – Cañuelas, Буэнос-Айрес, Аргентина
Июнь 2017 г. Привет, Раджкумар. Где ты? Дэниел ответил и отправил запрос на разъяснения! Спасибо! С уважением, Тед Муни, ЧП RET Стремление жить Алоха finish. ![]() |
17 июня 2017 г.
В. Здравствуйте,
Я хотел бы узнать об объемной закалке En9 для достижения твердости сердцевины 330-355 BHN. Кованый вал диаметром 45 мм и длиной 400 мм с одним торцевым диском диаметром 250 мм и длиной 30 мм. Если да, пожалуйста, предложите цикл H/t.
MUTHUSAMY PALANISAMY
Lakshmi Machine Works Limited – Коимбатур, Тамилнаду, Индия
27 октября 2017 г.
В. У нас есть цилиндрический (твердый) материал EN8, длина = 300 мм, диаметр = 60 мм. Представитель нашей компании по закалке обещает закалить его при 55°С, но диаметр после закалки сильно различается. Это из-за непрерывной закалки больше, чем его возможности? Какова оптимальная твердость, которую мы можем ожидать?
САУРАБ КУМАР
– Нойда, Индия
8 ноября 2017 г.
А. Привет, Саурабх!
EN8, по моему опыту, не является хорошим материалом для упрочнения. При толщине 60 мм вам нужно, по крайней мере, немного бора и хрома в вашем составе, чтобы улучшить глубину закалки.
Прокаливаемость менее 50 HRC на расстоянии более 6 мм от поверхности, возможно, вы можете получить это число выше при закалке в рассоле, но не 30 мм (расстояние от поверхности до центра).
Удачи!
Daniel Montañés
TEL – N FERRARIS – Cañuelas, Буэнос-Айрес, Аргентина
24 марта 2018 г.
В. Здравствуйте, мы производим штифты диаметром от 3 мм до 16 мм. и длиной от 8 мм до 150 мм, только из материала EN8D. Делаем процесс закалки со стыковкой и охлаждением в подсоленной воде. Тем не менее, мы получаем вариации в закалке. Нам нужна твердость 48-52. Но очень редко мы достигаем цели. Так может ли кто-нибудь помочь мне с точной формулой, чтобы получить правильную твердость?
Минимальный размер:- 3 диам. x 8 длина до 60 мм
Максимальный размер:- 16 диаметр x 40 длина до 100 мм
ПОЖАЛУЙСТА, ОТВЕТИТЕ МНЕ. СПАСИБО.
Ketankumar Patel
Vijay Engineering Works, Ахмадабад. – Ахмадабад, Гуджарат, Индия
11 мая 2018 г.
В. Привет.
Я хочу знать, как добиться упрочнения материала EN8D.
Мы сделали дуговую закалку и закалку в масле. Но нам это не помогло.
Если кто знает помогите пожалуйста.
Район,
Прашант
Прашант Парсана
– Раджкот. Индия
19 июля 2018 г.
В. Здравствуйте, сэр,
Мы столкнулись с той же проблемой. твердость в круглом стержне EN8. Поверхность материала достигает 34-35 HRC, а сердцевина материала достигает только 25-26. Пожалуйста, предложите, как исправить проблему.
Dinesh Venugopalsamy
Контроль качества – Коимбатур, Тамилнаду, Индия
Недостаточная твердость, достигнутая при термообработке C45 Материал
24 июля 2018 г.
В. Моя ситуация: Для закалки мы взяли материал марки С45 толщиной 4,00 мм и шириной 70 мм. Углерод % 0,425 и Mn % 0,66. В последней партии, использованной с таким же нагревательным материалом, твердость достигла от 46 до 48 HRC, в партии этого месяца твердость достигла только от 37 до 38 HRC. Каковы вероятные причины недостижения твердости?
Ashish kekre
Покупатель – Dombivli, Thane, Maharashtra, INDIA
4 ноября 2018 г.
Лазерная закалка
A. Мы можем достичь поверхностной твердости 52-54 HRC в материале C45 путем лазерной закалки. Мы в этом уверены.
АШОК РЕДДИ
– Пуна МАХАРАШТРА, ИНДИЯ
2 августа 2019 г.
В. Здравствуйте, сэр, я Гадж Днянешвар.
Мы используем EN8 для омывателя, но поточечное изменение в 1 штуке (32-44 часа) при проверке направления 180 на работе. В чем проблема?
Dnyaneshwar Ghadge
KANAL ENTERPRISES – INDORE, MADHYPRADESH INDIA
17 января 2020 г.
В. Я хочу добиться твердости от 28 до 32 HRC С ПОМОЩЬЮ МАТЕРИАЛА en8 d С СОДЕРЖАНИЕМ УГЛЕРОДА ОТ 40% ДО 45% И mn ДО 0,6 И ВЫШЕ, НО НЕ МОГУ ПОЛУЧИТЬ ЖЕЛАЕМУЮ ТВЕРДОСТЬ, ИНОГДА СОСТАВЛЯЮЩУЮ 18 HRC ИЛИ 22 HRC ИЛИ 38 HRC
НЕ ПОНИМАЮ, КАК ПОДДЕРЖИВАТЬ HRC.
A Singh
— Мумбаи, МАХАРАШТРА, ИНДИЯ
Кузнечные молотки EN9 неправильно закаляются
12 марта 2020 г.
В. Здравствуйте, мне нужен совет. Я кузнец, который начинает делать свои собственные молоты. Я выбрал EN9. Я выковал головки и закалил их, но результаты были неоднозначными. Я начал с масляной закалки, и конечный результат показался мне мягким, оставляя вмятины на лице при ударах по высокоуглеродистым долотам и тому подобному.
Так что я пошел на закалку водой: первая была успешной, и в итоге у меня было прекрасное твердое лицо, которое не помялось. Все три, которые я сделал после этого, страдали от трещин в щеках молотка. Поэтому я попробовал закалку водой, чередуя лицо и ручку, оставляя щеки остывать медленнее, и это оставило то, что я чувствовал, все еще слишком мягким.
Итак, мой вопрос: какой твердости следует ожидать от молота EN9, и есть ли какие-либо подсказки или рекомендации по процессу термообработки для изготовления молотков. Заранее спасибо.
Дэвид Бейнс
Fire Monkey Forge — SPALDING
15 марта 2020 г.
В. Здравствуйте,
Мы являемся производителями стальных стержней для обуви из материала EN9.
У нас всегда были проблемы с процессом закалки, а также проблемы с закалкой и ржавлением через несколько недель.
Пожалуйста, дайте нам квалифицированный совет для решения наших проблем.
Спасибо
Сардхар
Сардхар Латиф
Генеральный менеджер – Веллор, Тамил Наду, Индия
март 2020
(любезно предоставленоcompositetoeboots.org)
А. Привет, Сардхар. Я не разбираюсь в термообработке и не могу вам в этом помочь, но если читатели не направят вас к технической библиотеке, я уверен, что вам придется начать со специфики вашей технологической последовательности, а не только с . “были проблемы в процессе закалки, закалки и коррозии” 🙂
Пожалуйста, расскажите нам, что вы в настоящее время делаете для термической обработки и закалки. Вы не наносите никаких антикоррозионных средств? Вам не разрешено? Спасибо!
С уважением,
Тед Муни, ЧП RET
Стремление жить Алоха
finish.com – Пайн-Бич, Нью-Джерси
19 августа 2020 г.
A. Просто чтобы ответить на пару вопросов о материалах EN9. Это то, что мы, специалисты по термообработке, называем ****. Он имеет очень и очень переменную твердость от основной закалки и отпуска. Вы бы выиграли от цементации материала; однако я не думаю, что это было бы здорово для молотков.
Вам необходимо обратить внимание на высокоуглеродистые стали (0,6% и выше) и закалить и отпустить их до твердого и прочного состояния.
Надеюсь, это поможет!
Джеймс Бейли
– Соединенное Королевство
21 декабря 2020 г.
В. Мы столкнулись с той же проблемой. твердость в круглом стержне EN8. Поверхность материала достигает 34-35 HRC, а сердцевина материала достигает только 25-26. Пожалуйста, предложите, как исправить проблему.
Панди Каттусами
– Ченнаи Тамилнад, Индия
Декабрь 2020 г.
А. Привет Панди. “Та же проблема” означает, что великое наследие Билла Рейнольдса на этой странице должно быть большим подспорьем. Но, пожалуйста, начните с размеров круглого стержня и того, что вы делаете в настоящее время, чтобы достичь твердости, о которой вы сообщаете.
EN8 содержит немного меньше углерода, чем EN9, поэтому из-за моего невежества в термической обработке я предполагаю, что он менее упрочняемый. Спасибо!
Удачи и С уважением,
Тед Муни, ЧП RET
Стремление жить Алоха
finish.com – Пайн-Бич, Нью-Джерси
18 февраля 2021 г.
В. Сэр, мне нужна ваша помощь, чтобы узнать достижимую твердость материала en8d с содержанием углерода 0,40-0,41 и марганца 0,60 %
Мне нужно достичь 56-60 HRC при индукционной закалке
Но мы не получаем более 48-52 часов
Пожалуйста, предложите, достижимо ли это или нет
Или какой материал из углеродистой стали мы должны выбрать, чтобы достичь выше HRC
С уважением,
Ashish
Ашиш Бансал
– Лудхияна/ Пенджаб/ Индия
<- Ред. примечание: пожалуйста, опишите свою ситуацию, а не публикуйте в аннотации
Какие? Хм?
21 июня 2021 г.
В. Есть ли какой-либо паспорт для другого материала с этим диапазоном твердости?
Бхавеш Домадия
Старший инженер по исследованиям и разработкам – Ахмадабад, Индия
<- Ред. примечание: пожалуйста, опишите свою ситуацию, а не публикуйте в аннотации Какие? Хм?
12 декабря 2021 г.
В. МАТЕРИАЛ C45 ПОЛУЧАЕТ БОЛЬШЕ ВАРИАНТОВ ЗАТУШЕНИЯ В ВОДУ – КАК ЕГО ЗАДЕРЖАТЬ?
Мани Ваннан
– Хайдарабад, Индия
1 апреля 2022 г.
В. Здравствуйте, сэр, я ТАВАМАНИ с завода по термической обработке в Меце. Мой клиент, которому была предоставлена твердость материала EN8D, требовал от 27 до 32 HRC (сердцевина и поверхность) с одинаковыми характеристиками.