Ультразвуковая дефектоскопия это: Ультразвуковая дефектоскопия | это… Что такое Ультразвуковая дефектоскопия?
alexxlab | 03.06.1996 | 0 | Разное
Ультразвуковая дефектоскопия | это… Что такое Ультразвуковая дефектоскопия?
|
Ультразвукова́я дефектоскопи́я — метод основанный С.Я. Соколовым, позволяющий осуществлять поиск дефектов в материале изделия путём излучения и принятия ультразвуковых колебаний, отраженных от внутренних несплошностей (дефектов), и дальнейшего анализа их амплитуды, времени прихода, формы и других характеристик с помощью специального оборудования — ультразвукового дефектоскопа.
Принцип работы
Звуковые волны не изменяют траектории движения в однородном материале. Отражение акустических волн происходит от раздела сред с различными удельными акустическими сопротивлениями. Чем больше различаются акустические сопротивления, тем большая часть звуковых волн отражается от границы раздела сред. Так как включения в металле часто содержат воздух, имеющий на несколько порядков большее удельное акустическое сопротивление, чем сам металл, то отражение будет практически полное.
Разрешающая способность акустического исследования определяется длиной используемой звуковой волны. Это ограничение накладывается тем фактом, что при размере препятствия меньше четверти длины волны, волна от него практически не отражается. Это определяет использование высокочастотных колебаний — ультразвука. С другой стороны, при повышении частоты колебаний быстро растет их затухание, что ограничивает доступную глубину контроля. Для контроля металла наиболее часто используются частоты от 0.5 до 10 МГц.
Возбуждение и прием ультразвука
Существует несколько методов возбуждения ультразвуковых волн в исследуемом объекте. Наиболее распространенным является использование пьезоэлектрического эффекта. В этом случае излучение ультразвука производится с помощью преобразователя, который преобразует электрические колебания в акустические с помощью обратного пьезоэлектрического эффекта. Отраженные сигналы попавшие на пьезопластину из-за прямого пьезоэлектрического эффекта преобразуются в электрические, которые и регистрируются измерительными цепями.
Также используются электромагнитно-акустический (ЭМА) метод, основанный на приложении сильных переменных магнитных полей к металлу. КПД этого метода гораздо ниже, чем у пьезоэлектрического, но зато может работать через воздушный зазор и не предъявляет особых требований к качеству поверхности.
Классификация методов исследования
Существующие акустические методы неразрушающего контроля подразделяют на две большие группы – активные и пассивные.
Активные
Активные методы контроля подразумевают под собой излучение и приём акустических волн.
Отражения
Эхо-импульсный метод контроля сварного соединения без дефекта (сверху) и с дефектом (снизу). В правой части изображения представлен экран дефектоскопа с изображённым на нём зондирующим импульсом (сверху) и импульсом от дефекта (снизу).
- Эхо-метод или эхо-импульсный метод — наиболее распространенный: преобразователь генерирует колебания (т.е. выступает в роли генератора) и он же принимает отражённые от дефектов эхо-сигналы (приёмник). Данный способ получил широкое распространение за счёт своей простоты, т.к. для проведения контроля требуется только один преобразователь, следовательно при ручном контроле отсутствует необходимость в специальный приспособлениях для его фиксации (как, например, в дифракционно-временном методе) и совмещении акустических осей при использовании двух преобразователей. Кроме того, это один из немногих методов ультразвуковой дефектоскопии, позволяющий достаточно точно определить координаты дефекта, такие как глубину залегания и положение в исследуемом объекте (относительно преобразователя).
- Зеркальный или Эхо-зеркальный метод — используются два преобразователя с одной стороны детали: сгенерированные колебания отражаются от дефекта в сторону приемника. На практике используется для поиска дефектов расположенных перпендикулярно поверхности контроля, например трещин.
Трещина в угловом сварном шве, выявляемая дифракцинно-временным методом контроля.
- Дифракционно-временной метод
Кроме того, дифрагированные сигналы достаточно слабые.
- Дельта-метод — разновидность зеркального метода — отличаются механизм отражения волны от дефекта и способ принятия. На практике не используется.
Ревербационный метод контроля двухслойной конструкции.
- Ревербационный метод – основан на постепенном затухании сигнала в объекте контроля. При контроле двухслойной конструкции, в случае качественного соединения слоёв, часть энергии из первого слоя будет уходить во второй, поэтому ревербация будет меньше. В обратном случае будут наблюдаться многократные отражения от первого слоя, так называемый лес. Метод используется для контроля сцепления различных видов наплавок, например баббитовой наплавки с чугунным основанием. Основным недостатком данного метода является регистрация дефектоскопом эхо-сигналов от границы соединения двух слоёв. Причиной этих эхо-сигналов является разница скоростей упругих колебаний в материалах соединения и их различное удельное акустическое сопротивление.
- Акустическая микроскопия благодаря повышенной частоте ввода ультразвукового пучка и применению его фокусировки, позволяет обнаруживать дефекты, размеры которых не превышают десятых долей миллиметра.
- Когерентный метод – помимо двух основных параметров эхо-сигнала, таких как амплитуда и время прихода, используется дополнительно фаза эхо-сигнала. Использование когерентного метода, а точнее нескольких идентичных преобразователей, работающих синфазно, позволяет получить изображение дефекта, близкое к реальному. При использовании специальных преобразователей, таких как преобразователь бегущей волны или его современный аналог – преобразователь с фазированной решёткой, метод позволяет значительно уменьшить время, затрачиваемое на контроль изделия.
Прохождения
Методы прохождения подразумевают под собой наблюдение за изменением параметров ультразвуковых колебаний, прошедших через объект контроля, так называемых сквозных колебаний. Изначально для контроля применялось непрерывное излучение, а изменение его амплитуды сквозных колебаний расценивалось как наличие дефекта в контролируемом объекте, так называемой звуковой тени. Отсюда появилось название теневой метод. Со временем непрерывное излучение сменилось импульсным, а к фиксируемым параметрам помимо амплитуды добавились также фаза, спектр и время прихода импульса и появились другие методы прохождения. Термин теневой потерял свой первоначальный смысл и стал означать один из методов прохождения. В англоязычной литературе

- Теневой — используются два преобразователя, которые находятся по две стороны от исследуемой детали на одной акустической оси. В данном случае один из преобразователей генерирует колебания (генератор), а второй принимает их (приёмник). Признаком наличия дефекта будет являться значительное уменьшение амплитуды принятого сигнала, или его пропадание (дефект создает акустическую тень).
- Зеркально-теневой — используется для контроля деталей с двумя параллельными сторонами, развитие теневого метода: анализируются отражения от противоположной грани детали. Признаком дефекта, как и при теневом методе, будет считаться пропадание отраженных колебаний. Основное достоинство этого метода в отличие от теневого заключается в доступе к детали с одной стороны.
Вертикально ориентированная трещина, выявляемая зеркальным методом.
- Временной теневой основан на запаздывании импульса во времени, затраченного на огибание дефекта.
Используется для контроля бетона или огнеупорного кирпича.
- Метод многократной тени аналогичен теневому, с тем исключением, что ультразвуковая волна несколько раз проходит через параллельные поверхности изделия.
- При эхо-сквозном методе используют два преобразователя, расположенные по разные стороны объекта контроля друг напротив друга. В случае отсутствия дефекта, на экране дефектоскопа наблюдают сквозной сигнал и сигнал, двукратно отражённый от стенок объекта контроля. При наличии полупрозрачного дефекта, также наблюдают отражённые сквозные сигналы от дефекта.
Эхо-сквозной метод контроля. При отсутствии дефекта на экране дефектоскопа наблюдаются только 1 и 2 импульсы. При наличии полупрозрачного дефекта, дополнительно 3 и 4-й. На рисунке для наглядности отражения ультразвуковых волн, неверно показаны направления их распространения. Ультразвуковые волны распространяются вдоль акустической оси передатчика (верхнего преобразователя).
- Ревербационно-сквозной метод включает в себя элементы ревербационного метода и метода многократной тени. На небольшом расстоянии друг от друга, как правило с одной стороны изделия, устанавливают два преобразователя – передатчик и приёмник. Ультразвуковые волны, посылаемые в объект контроля после многократных отражений, в конечном счете попадают на приёмник. Отсутствие дефекта позволяет наблюдать стабильные отраженные сигналы. При наличии дефекта изменяется распространение ультразвуковых волн – изменяется амплитуда и спектр принятых импульсов. Метод применяется для контроля многослойных конструкций и полимерных композитных материалов.
- Велосиметрический метод основан на регистрации изменения скорости упругих волн в зоне дефекта. Применяется для контроля многослойных конструкций и для изделий из полимерных композиционных материалов.
Собственных колебаний
Вынужденных колебаний
- Интегральный
- Локальный
- Акустико-топографический
Свободных колебаний
- Интегральный
- Локальный
Импендансные
- Изгибных волн
- Продольных волн
- Контактного импенданса
Пассивные
Пассивные методы контроля заключаются в приёме волн, источником которых является сам объект контроля.
- Акустико-эмиссионный
- Вибрационно-диагностический
- Шумодиагностический
Современные дефектоскопы точно замеряют время, прошедшее от момента излучения до приёма эхо-сигнала, тем самым измеряя расстояние до отражателя. Это позволяет добиться высокого лучевого разрешения исследования. Компьютеризированные системы позволяют провести анализ большого числа импульсов и получить трёхмерную визуализацию отражателей в металле.
Преимущества
Ультразвуковой контроль изделий в ГДР, 1977 год
Ультразвуковое исследование не разрушает и не повреждает исследуемый образец, что является его главным преимуществом. Возможно проводить контроль изделий из разнообразных материалов, как металлов, так и неметаллов. Кроме того можно выделить высокую скорость исследования при низкой стоимости и опасности для человека (по сравнению с рентгеновской дефектоскопией) и высокую мобильность ультразвукового дефектоскопа.
Недостатки
Использование пъезоэлектрических преобразователей требует подготовки поверхности для ввода ультразвука в металл, в частности создания шероховатости поверхности не ниже класса 5, в случае со сварными соединениям ещё и направления шероховатости (перпендикулярно шву). Ввиду большого акустического сопротивления воздуха, малейший воздушный зазор может стать неодолимой преградой для ультразвуковых колебаний. Для устранения воздушного зазора, на контролируемый участок изделия предварительно наносят контактные жидкости, такие как вода, масло, клейстер. При контроле вертикальных или сильно наклоненных поверхностей необходимо применять густые контактные жидкости с целью предотвращения их быстрого стекания.
Для контроля изделий с внешним диаметром менее 200мм, необходимо использовать преобразователи, с радиусом кривизны подошвы R, равным 0,9-1,1R радиуса контролируемого объекта, так называемые притертые преобразователи, которые в таком виде непригодны для контроля изделий с плоскими поверхностями. Например для контроля цилиндрической поковки, необходимо производить перемещение преобразователя в двух взаимно перпендикулярных направлениях, что подразумевает под собой использование двух притёртых преобразователей – по одному для каждого из направлений.
Как правило ультразвуковая дефектоскопия не может дать ответ на вопрос о реальных размерах дефекта, лишь о его отражательной способности в направлении приемника. Эти величины коррелируют, но не для всех типов дефектов. Кроме того, некоторые дефекты практически невозможно выявить ультразвуковым методом в силу их характера, формы или расположения в объекте контроля.
Практически невозможно производить достоверный ультразвуковой контроль металлов с крупнозернистой структурой, таких как чугун или аустенитный сварной шов (толщиной свыше 60 мм)[1][2] из-за большого рассеяния и сильного затухания ультразвука. Кроме того, затруднителен контроль малых деталей или деталей со сложной формой.
Применение
Ультразвуковой дефектоскоп для контроля железнодорожных рельс
Применяется для поиска дефектов материала (поры, волосовины, различные включения, неоднородная структура и пр. ) и контроля качества проведения работ — сварка, пайка, склейка и пр. Ультразвуковой контроль является обязательной процедурой при изготовлении и эксплуатации многих ответственных изделий, таких как части авиационных двигателей, трубопроводы атомных реакторов или железнодорожные рельсы.
Ультразвуковой контроль сварных швов
Сварные швы являются самой массовой областью применения ультразвуковой дефектоскопии. Это достигается за счёт мобильности ультразвуковой установки, высокой производительности контроля, высокой точности, высокой чувствительности к любым внутренним (объёмным – поры, металлические и неметаллические включения; плоскостным – непровары, трещины), а также внешним, т.е. поверхностным дефектам сварных швов (подрезы, обнижения валика усиления и т.п.).
Многие ведомственные документы подразумевают обязательный ультразвуковой контроль сварных швов, либо альтернативный выбор ультразвукового или радиационного контроля, либо контроль обоими методами.
Основным документом в России по ультразвуковому контролю сварных швов является ГОСТ 14782-86, в котором рассмотрены в полном объёме методы контроля стыковых, тавровых, нахлесточных и угловых сварных швов, выполненных различными способами сварки. Также в нём подробно описаны стандартные образцы (эталоны) СО-1, СО-2 (СО-2А), СО-3 и СО-4 и стандартные образцы предприятия, необходимые для настройки дефектоскопа, а также их параметры для их изготовления.
Объёмы контроля и нормы оценки качества сварного соединения устанавливаются различными нормативными документами в соответствии с требованиями прочности к конкретной сварной конструкции. На предприятиях, изготавливающих особо ответственные изделия, а также различными надзорными органами могут выпускаться собственные методические материалы для оценки качества сварных швов. Примером может служить РД РОСЭК-001-96, разработанный Ростехнадзором для оценки качества сварных соединений для грузоподъёмных машин.
Литература и нормативно-техническая документация
Литература
- Клюев В.В. Неразрушающий контроль. Том 3.: Справочник. В 7-и книгах / Под ред. Клюева В.В. — М. Машиностроение 2004
- Гурвич А. К., Ермолов И. Н. Ультразвуковая дефектоскопия сварных швов — Киев: Техшка, 1972
- Выборнов Б.
И. Ультразвуковая дефектоскопия – М.: Металлургия, 1985
Нормативно-техническая документация
- ГОСТ 14782-86 Контроль неразрушающий. Соединения сварные. Методы ультразвуковые.
- ГОСТ 24507-80 Контроль неразрушающий. Поковки из черных и цветных металлов. Методы ультразвуковой дефектоскопии.
- ГОСТ 22727-88 Прокат листовой. Методы ультразвукового контроля.
- ГОСТ 21120-75 Прутки и заготовки круглого и прямоугольного сечения. Методы ультразвуковой дефектоскопии.
- РД РОСЭК-001-96 Машины грузоподъемные. Конструкции металлические. Контроль ультразвуковой. Основные положения.
- ОП 501 ЦД-97 Энергетическое оборудование. Сосуды давления. Трубопроводы пара, воды.
- ПНАЭ Г-7-010-89 Оборудование и трубопроводы атомных энергетических установок. Сварные соединения и наплавки. Правила контроля.
- ПНАЭ Г-10-032-92 Правила контроля сварных соединений элементов локализующих систем безопасности атомных станций.
- ПНАЭ Г-7-032-91 Унифицированные методики контроля основных материалов полуфабрикатов), сварных соединений и наплавки оборудования и трубопроводов атомных энергетических установок.
Ультразвуковой контроль. Часть IV. Контроль сварных соединений из сталей аустенитного класса.
См. также
- Ультразвуковое исследование
- Дефектоскоп
- Электронный архив журнала “Дефектоскопия” по ультразвуковым методам
Примечания
- ↑ ПНАЭ Г-7-032-91 Ультразвуковой контроль. Часть IV. Контроль сварных соединений из сталей аустенитного класса. П.1.4.
- ↑ Клюев В.В. Неразрушающий контроль. Том 3. П.5.1.3.1.
Ультразвуковая дефектоскопия | это… Что такое Ультразвуковая дефектоскопия?
|
Ультразвукова́я дефектоскопи́я — метод основанный С.Я. Соколовым, позволяющий осуществлять поиск дефектов в материале изделия путём излучения и принятия ультразвуковых колебаний, отраженных от внутренних несплошностей (дефектов), и дальнейшего анализа их амплитуды, времени прихода, формы и других характеристик с помощью специального оборудования — ультразвукового дефектоскопа. Является одним из самых распространенных методов неразрушающего контроля.
Принцип работы
Звуковые волны не изменяют траектории движения в однородном материале. Отражение акустических волн происходит от раздела сред с различными удельными акустическими сопротивлениями. Чем больше различаются акустические сопротивления, тем большая часть звуковых волн отражается от границы раздела сред. Так как включения в металле часто содержат воздух, имеющий на несколько порядков большее удельное акустическое сопротивление, чем сам металл, то отражение будет практически полное.
Разрешающая способность акустического исследования определяется длиной используемой звуковой волны. Это ограничение накладывается тем фактом, что при размере препятствия меньше четверти длины волны, волна от него практически не отражается. Это определяет использование высокочастотных колебаний — ультразвука. С другой стороны, при повышении частоты колебаний быстро растет их затухание, что ограничивает доступную глубину контроля. Для контроля металла наиболее часто используются частоты от 0.5 до 10 МГц.
Возбуждение и прием ультразвука
Существует несколько методов возбуждения ультразвуковых волн в исследуемом объекте. Наиболее распространенным является использование пьезоэлектрического эффекта. В этом случае излучение ультразвука производится с помощью преобразователя, который преобразует электрические колебания в акустические с помощью обратного пьезоэлектрического эффекта. Отраженные сигналы попавшие на пьезопластину из-за прямого пьезоэлектрического эффекта преобразуются в электрические, которые и регистрируются измерительными цепями.
Также используются электромагнитно-акустический (ЭМА) метод, основанный на приложении сильных переменных магнитных полей к металлу. КПД этого метода гораздо ниже, чем у пьезоэлектрического, но зато может работать через воздушный зазор и не предъявляет особых требований к качеству поверхности.
Классификация методов исследования
Существующие акустические методы неразрушающего контроля подразделяют на две большие группы – активные и пассивные.
Активные
Активные методы контроля подразумевают под собой излучение и приём акустических волн.
Отражения
Эхо-импульсный метод контроля сварного соединения без дефекта (сверху) и с дефектом (снизу). В правой части изображения представлен экран дефектоскопа с изображённым на нём зондирующим импульсом (сверху) и импульсом от дефекта (снизу).
- Эхо-метод или эхо-импульсный метод — наиболее распространенный: преобразователь генерирует колебания (т.е. выступает в роли генератора) и он же принимает отражённые от дефектов эхо-сигналы (приёмник). Данный способ получил широкое распространение за счёт своей простоты, т.к. для проведения контроля требуется только один преобразователь, следовательно при ручном контроле отсутствует необходимость в специальный приспособлениях для его фиксации (как, например, в дифракционно-временном методе) и совмещении акустических осей при использовании двух преобразователей. Кроме того, это один из немногих методов ультразвуковой дефектоскопии, позволяющий достаточно точно определить координаты дефекта, такие как глубину залегания и положение в исследуемом объекте (относительно преобразователя).
- Зеркальный или Эхо-зеркальный метод — используются два преобразователя с одной стороны детали: сгенерированные колебания отражаются от дефекта в сторону приемника.
На практике используется для поиска дефектов расположенных перпендикулярно поверхности контроля, например трещин.
Трещина в угловом сварном шве, выявляемая дифракцинно-временным методом контроля.
- Дифракционно-временной метод — используется два преобразователя с одной стороны детали, расположенные друг напротив друга. Если дефект имеет острые кромки (как, например, трещины) то колебания дифрагируют на концах дефекта и отражаются во все стороны, в том числе и в сторону приёмника. Дефектоскоп регистрирует время прихода обоих импульсов при их достаточной амплитуде. На экране дефектоскопа одновременно отображаются оба сигнала от верхней и от нижней границ дефекта, тем самым можно достаточно точно определить условную высоту дефекта. Способ достаточно универсален, позволяет производить ультразвуковой контроль на швах любой сложности, но требует специального оборудования для фиксации преобразователей, а также дефектоскоп, способный работать в таком режиме.
Кроме того, дифрагированные сигналы достаточно слабые.
- Дельта-метод — разновидность зеркального метода — отличаются механизм отражения волны от дефекта и способ принятия. На практике не используется.
Ревербационный метод контроля двухслойной конструкции.
- Ревербационный метод – основан на постепенном затухании сигнала в объекте контроля. При контроле двухслойной конструкции, в случае качественного соединения слоёв, часть энергии из первого слоя будет уходить во второй, поэтому ревербация будет меньше. В обратном случае будут наблюдаться многократные отражения от первого слоя, так называемый лес. Метод используется для контроля сцепления различных видов наплавок, например баббитовой наплавки с чугунным основанием. Основным недостатком данного метода является регистрация дефектоскопом эхо-сигналов от границы соединения двух слоёв. Причиной этих эхо-сигналов является разница скоростей упругих колебаний в материалах соединения и их различное удельное акустическое сопротивление.
Например на границе баббит-сталь возникает постоянный эхо-сигнал даже в местах качественного сцепления. В силу конструкционных особенностей некоторых изделий, контроль качества соединения материалов ревербационным методом может быть невозможен именно из-за наличия на экране дефектоскопа эхо-сигналов от границы соединения.
- Акустическая микроскопия благодаря повышенной частоте ввода ультразвукового пучка и применению его фокусировки, позволяет обнаруживать дефекты, размеры которых не превышают десятых долей миллиметра.
- Когерентный метод – помимо двух основных параметров эхо-сигнала, таких как амплитуда и время прихода, используется дополнительно фаза эхо-сигнала. Использование когерентного метода, а точнее нескольких идентичных преобразователей, работающих синфазно, позволяет получить изображение дефекта, близкое к реальному. При использовании специальных преобразователей, таких как преобразователь бегущей волны или его современный аналог – преобразователь с фазированной решёткой, метод позволяет значительно уменьшить время, затрачиваемое на контроль изделия.
Прохождения
Методы прохождения подразумевают под собой наблюдение за изменением параметров ультразвуковых колебаний, прошедших через объект контроля, так называемых сквозных колебаний. Изначально для контроля применялось непрерывное излучение, а изменение его амплитуды сквозных колебаний расценивалось как наличие дефекта в контролируемом объекте, так называемой звуковой тени. Отсюда появилось название теневой метод. Со временем непрерывное излучение сменилось импульсным, а к фиксируемым параметрам помимо амплитуды добавились также фаза, спектр и время прихода импульса и появились другие методы прохождения. Термин теневой потерял свой первоначальный смысл и стал означать один из методов прохождения. В англоязычной литературе метод прохождения называется through transmission technique или through transmission method, что полностью соответствует его российскому названию. Термин теневой в англоязычной литературе не применяется.
- Теневой — используются два преобразователя, которые находятся по две стороны от исследуемой детали на одной акустической оси. В данном случае один из преобразователей генерирует колебания (генератор), а второй принимает их (приёмник). Признаком наличия дефекта будет являться значительное уменьшение амплитуды принятого сигнала, или его пропадание (дефект создает акустическую тень).
- Зеркально-теневой — используется для контроля деталей с двумя параллельными сторонами, развитие теневого метода: анализируются отражения от противоположной грани детали. Признаком дефекта, как и при теневом методе, будет считаться пропадание отраженных колебаний. Основное достоинство этого метода в отличие от теневого заключается в доступе к детали с одной стороны.
Вертикально ориентированная трещина, выявляемая зеркальным методом.
- Временной теневой основан на запаздывании импульса во времени, затраченного на огибание дефекта.
Используется для контроля бетона или огнеупорного кирпича.
- Метод многократной тени аналогичен теневому, с тем исключением, что ультразвуковая волна несколько раз проходит через параллельные поверхности изделия.
- При эхо-сквозном методе используют два преобразователя, расположенные по разные стороны объекта контроля друг напротив друга. В случае отсутствия дефекта, на экране дефектоскопа наблюдают сквозной сигнал и сигнал, двукратно отражённый от стенок объекта контроля. При наличии полупрозрачного дефекта, также наблюдают отражённые сквозные сигналы от дефекта.
Эхо-сквозной метод контроля. При отсутствии дефекта на экране дефектоскопа наблюдаются только 1 и 2 импульсы. При наличии полупрозрачного дефекта, дополнительно 3 и 4-й. На рисунке для наглядности отражения ультразвуковых волн, неверно показаны направления их распространения. Ультразвуковые волны распространяются вдоль акустической оси передатчика (верхнего преобразователя).
- Ревербационно-сквозной метод включает в себя элементы ревербационного метода и метода многократной тени. На небольшом расстоянии друг от друга, как правило с одной стороны изделия, устанавливают два преобразователя – передатчик и приёмник. Ультразвуковые волны, посылаемые в объект контроля после многократных отражений, в конечном счете попадают на приёмник. Отсутствие дефекта позволяет наблюдать стабильные отраженные сигналы. При наличии дефекта изменяется распространение ультразвуковых волн – изменяется амплитуда и спектр принятых импульсов. Метод применяется для контроля многослойных конструкций и полимерных композитных материалов.
- Велосиметрический метод основан на регистрации изменения скорости упругих волн в зоне дефекта. Применяется для контроля многослойных конструкций и для изделий из полимерных композиционных материалов.
Собственных колебаний
Вынужденных колебаний
- Интегральный
- Локальный
- Акустико-топографический
Свободных колебаний
- Интегральный
- Локальный
Импендансные
- Изгибных волн
- Продольных волн
- Контактного импенданса
Пассивные
Пассивные методы контроля заключаются в приёме волн, источником которых является сам объект контроля.
- Акустико-эмиссионный
- Вибрационно-диагностический
- Шумодиагностический
Современные дефектоскопы точно замеряют время, прошедшее от момента излучения до приёма эхо-сигнала, тем самым измеряя расстояние до отражателя. Это позволяет добиться высокого лучевого разрешения исследования. Компьютеризированные системы позволяют провести анализ большого числа импульсов и получить трёхмерную визуализацию отражателей в металле.
Преимущества
Ультразвуковой контроль изделий в ГДР, 1977 год
Ультразвуковое исследование не разрушает и не повреждает исследуемый образец, что является его главным преимуществом. Возможно проводить контроль изделий из разнообразных материалов, как металлов, так и неметаллов. Кроме того можно выделить высокую скорость исследования при низкой стоимости и опасности для человека (по сравнению с рентгеновской дефектоскопией) и высокую мобильность ультразвукового дефектоскопа.
Недостатки
Использование пъезоэлектрических преобразователей требует подготовки поверхности для ввода ультразвука в металл, в частности создания шероховатости поверхности не ниже класса 5, в случае со сварными соединениям ещё и направления шероховатости (перпендикулярно шву). Ввиду большого акустического сопротивления воздуха, малейший воздушный зазор может стать неодолимой преградой для ультразвуковых колебаний. Для устранения воздушного зазора, на контролируемый участок изделия предварительно наносят контактные жидкости, такие как вода, масло, клейстер. При контроле вертикальных или сильно наклоненных поверхностей необходимо применять густые контактные жидкости с целью предотвращения их быстрого стекания.
Для контроля изделий с внешним диаметром менее 200мм, необходимо использовать преобразователи, с радиусом кривизны подошвы R, равным 0,9-1,1R радиуса контролируемого объекта, так называемые притертые преобразователи, которые в таком виде непригодны для контроля изделий с плоскими поверхностями. Например для контроля цилиндрической поковки, необходимо производить перемещение преобразователя в двух взаимно перпендикулярных направлениях, что подразумевает под собой использование двух притёртых преобразователей – по одному для каждого из направлений.
Как правило ультразвуковая дефектоскопия не может дать ответ на вопрос о реальных размерах дефекта, лишь о его отражательной способности в направлении приемника. Эти величины коррелируют, но не для всех типов дефектов. Кроме того, некоторые дефекты практически невозможно выявить ультразвуковым методом в силу их характера, формы или расположения в объекте контроля.
Практически невозможно производить достоверный ультразвуковой контроль металлов с крупнозернистой структурой, таких как чугун или аустенитный сварной шов (толщиной свыше 60 мм)[1][2] из-за большого рассеяния и сильного затухания ультразвука. Кроме того, затруднителен контроль малых деталей или деталей со сложной формой.
Применение
Ультразвуковой дефектоскоп для контроля железнодорожных рельс
Применяется для поиска дефектов материала (поры, волосовины, различные включения, неоднородная структура и пр. ) и контроля качества проведения работ — сварка, пайка, склейка и пр. Ультразвуковой контроль является обязательной процедурой при изготовлении и эксплуатации многих ответственных изделий, таких как части авиационных двигателей, трубопроводы атомных реакторов или железнодорожные рельсы.
Ультразвуковой контроль сварных швов
Сварные швы являются самой массовой областью применения ультразвуковой дефектоскопии. Это достигается за счёт мобильности ультразвуковой установки, высокой производительности контроля, высокой точности, высокой чувствительности к любым внутренним (объёмным – поры, металлические и неметаллические включения; плоскостным – непровары, трещины), а также внешним, т.е. поверхностным дефектам сварных швов (подрезы, обнижения валика усиления и т.п.).
Многие ведомственные документы подразумевают обязательный ультразвуковой контроль сварных швов, либо альтернативный выбор ультразвукового или радиационного контроля, либо контроль обоими методами.
Основным документом в России по ультразвуковому контролю сварных швов является ГОСТ 14782-86, в котором рассмотрены в полном объёме методы контроля стыковых, тавровых, нахлесточных и угловых сварных швов, выполненных различными способами сварки. Также в нём подробно описаны стандартные образцы (эталоны) СО-1, СО-2 (СО-2А), СО-3 и СО-4 и стандартные образцы предприятия, необходимые для настройки дефектоскопа, а также их параметры для их изготовления.
Объёмы контроля и нормы оценки качества сварного соединения устанавливаются различными нормативными документами в соответствии с требованиями прочности к конкретной сварной конструкции. На предприятиях, изготавливающих особо ответственные изделия, а также различными надзорными органами могут выпускаться собственные методические материалы для оценки качества сварных швов. Примером может служить РД РОСЭК-001-96, разработанный Ростехнадзором для оценки качества сварных соединений для грузоподъёмных машин.
Литература и нормативно-техническая документация
Литература
- Клюев В.В. Неразрушающий контроль. Том 3.: Справочник. В 7-и книгах / Под ред. Клюева В.В. — М. Машиностроение 2004
- Гурвич А. К., Ермолов И. Н. Ультразвуковая дефектоскопия сварных швов — Киев: Техшка, 1972
- Выборнов Б.
И. Ультразвуковая дефектоскопия – М.: Металлургия, 1985
Нормативно-техническая документация
- ГОСТ 14782-86 Контроль неразрушающий. Соединения сварные. Методы ультразвуковые.
- ГОСТ 24507-80 Контроль неразрушающий. Поковки из черных и цветных металлов. Методы ультразвуковой дефектоскопии.
- ГОСТ 22727-88 Прокат листовой. Методы ультразвукового контроля.
- ГОСТ 21120-75 Прутки и заготовки круглого и прямоугольного сечения. Методы ультразвуковой дефектоскопии.
- РД РОСЭК-001-96 Машины грузоподъемные. Конструкции металлические. Контроль ультразвуковой. Основные положения.
- ОП 501 ЦД-97 Энергетическое оборудование. Сосуды давления. Трубопроводы пара, воды.
- ПНАЭ Г-7-010-89 Оборудование и трубопроводы атомных энергетических установок. Сварные соединения и наплавки. Правила контроля.
- ПНАЭ Г-10-032-92 Правила контроля сварных соединений элементов локализующих систем безопасности атомных станций.
- ПНАЭ Г-7-032-91 Унифицированные методики контроля основных материалов полуфабрикатов), сварных соединений и наплавки оборудования и трубопроводов атомных энергетических установок.
Ультразвуковой контроль. Часть IV. Контроль сварных соединений из сталей аустенитного класса.
См. также
- Ультразвуковое исследование
- Дефектоскоп
- Электронный архив журнала “Дефектоскопия” по ультразвуковым методам
Примечания
- ↑ ПНАЭ Г-7-032-91 Ультразвуковой контроль. Часть IV. Контроль сварных соединений из сталей аустенитного класса. П.1.4.
- ↑ Клюев В.В. Неразрушающий контроль. Том 3. П.5.1.3.1.
Полное руководство по методике ультразвуковой дефектоскопии
Ультразвуковой контроль или ультразвуковая дефектоскопия — это тип неразрушающего контроля, в котором для проведения проверок и измерений используются высокочастотные ультразвуковые волны. Ультразвуковой контроль часто используется для обнаружения и оценки дефектов, измерения размеров, характеристики материалов и многого другого.
Звуковые волны с частотой более 20 кГц и длиной волны 1,9 см или менее при атмосферном давлении известны как ультразвуковые волны. Проще говоря, ультразвук — это звуковые волны, частота которых превышает предел человеческого слуха.
Ультразвуковая дефектоскопия использует эти ультразвуковые звуковые волны для обнаружения дефектов внутри твердого металлического или бетонного объекта без какого-либо повреждения его исходной структуры.
В большинстве обычных УЗ-приложений ультразвуковые импульсы с центральной частотой в диапазоне от 0,1 до 15 МГц и граничными частотами до 50 МГц проходят через материалы для обнаружения внутренних дефектов или определения характеристик материалов. Одним из типичных примеров является ультразвуковое измерение толщины, при котором измеряется толщина испытуемого объекта путем контроля коррозии трубы.
Ультразвуковая дефектоскопия чаще всего проводится на стали и других металлах и сплавах, хотя она также может использоваться с более низким разрешением на бетоне, дереве и композитных материалах. Стальное и алюминиевое строительство, металлургия, производство, авиация, автомобили и другие виды транспорта входят в число отраслей, в которых он используется.
Ультразвуковая дефектоскопия основана на том принципе, что звуковые волны вызывают механические колебания в различных средах, таких как жидкости, твердые тела или газ. Распространенными видами распространения звуковых волн в твердых телах являются поперечные волны и продольные волны. Этот метод использует поток ультразвука в твердых металлических, бетонных или деревянных объектах.
Когда любая звуковая волна проходит через среду, она имеет определенную частоту, длину волны и скорость. Если волна сталкивается с краем другой среды (например, с дефектом), она немедленно передается обратно на тот же конец, где ее можно обнаружить. Это фундаментальная теория, лежащая в основе ультразвукового обнаружения потока.
Принципы ультразвуковой дефектоскопииУльтразвуковая дефектоскопия в целом основана на трех принципах: частоте, скорости и длине волны.
Частота (f) Частоты в диапазоне от 500 кГц до 10 МГц в секунду используются в большинстве приложений ультразвуковой дефектоскопии. Звуковая энергия эффективно проходит через самые распространенные твердые и жидкие тела на более высоких частотах.
Это расстояние между двумя последовательными точками, когда волна распространяется в среде и образует волновой цикл. Минимальный предел обнаружения для ультразвукового метода дефектоскопии составляет 1/2 длины волны.
Скорость (c)Скорость звуковой волны зависит от среды, в которой она распространяется, и зависит от плотности и упругости среды. Звуковые волны распространяются с различной скоростью. Удельная скорость ультразвука определяется при ультразвуковой дефектоскопии.
Отражение на краю дефекта Когда ультразвук, проходящий через материал, попадает в барьер с другой средой, часть энергии отражается обратно, а часть ее передается. Коэффициент отражения или количество отраженной энергии пропорционально относительному акустическому импедансу двух материалов.
Акустическое сопротивление — это характеристика материала, определяемая как произведение плотности на скорость звука в конкретном материале. Коэффициент отражения в процентах от давления падающей энергии может быть рассчитан для любых двух материалов по формуле.
Z2-Z1
R = ———-
Z2 + Z1
В этой формуле
R = отражение, представляя процент энергии, отраженной
R = отражение, представляя процент энергии
.0003
Z1 = акустическое сопротивление 1-го материала
Z2 = акустическое сопротивление 2-го материала
Методика ультразвуковой дефектоскопии Ультразвуковая дефектоскопия по сути является методом сравнения. Обученный оператор, выполняющий ультразвуковую дефектоскопию, идентифицирует определенные эхо-картины, соответствующие эхо-отклику от хороших деталей и от репрезентативных дефектов, используя соответствующие эталонные стандарты, знания о распространении звуковых волн и общепринятые процедуры испытаний. Чтобы определить состояние испытуемого образца, его эхо-картину можно сравнить с картинами этих калибровочных стандартов.
Ультразвуковая дефектоскопия с использованием прямого луча с контактными датчиками, датчиками с линией задержки, двойными элементами или погружными датчиками обычно используется для обнаружения трещин или расслоений, параллельных поверхности контролируемого образца, а также пустот и пористость. Он работает на основе основной предпосылки, что звуковая энергия, распространяющаяся через среду, будет продолжать распространяться до тех пор, пока она либо не рассеется, либо не отразится от границы с другим материалом, например, воздухом, окружающим дальнюю стену или находящимся внутри трещины.
Ультразвуковая дефектоскопия в режиме передачи В некоторых случаях ультразвуковая дефектоскопия завершается в режиме передачи. В этом методе ультразвуковой дефектоскопии звуковая энергия перемещается между двумя преобразователями, расположенными на противоположных сторонах контролируемого образца.
Если на пути звука имеется большой дефект, луч будет заблокирован, и звуковой импульс не достигнет приемника. испытание луча угла
для ультразвуковой дефектоскопииПри использовании контроля наклонным лучом для ультразвуковой дефектоскопии трещины или другие дефекты, перпендикулярные поверхности образца к этой поверхности, не могут быть обнаружены с помощью методов контроля прямым лучом.
Такие дефекты могут появляться в сварных швах, конструкционных металлических деталях и множестве других важных компонентов.
Ультразвуковые преобразователиПреобразователь — это устройство, которое может изменять состояние энергии с одного направления на другое. Электрическая энергия может быть преобразована в звуковую энергию с помощью ультразвуковых преобразователей и наоборот.
Стандартные преобразователи для ультразвуковой дефектоскопии используют динамический элемент, состоящий из полимеров, композитов или пьезокерамики. Когда на этот элемент подается электрический импульс высокого напряжения, он вибрирует в определенном диапазоне частот и создает звуковые волны. Электрический импульс генерируется, когда входящая звуковая волна вызывает вибрацию этого элемента.
Пять типов ультразвуковых преобразователей часто используются при обнаружении неисправностей.
- Контактные преобразователи
- Иммерсионные преобразователи
- Преобразователи с линией задержки
- Преобразователи с угловым лучом
- Преобразователи с двойным элементом
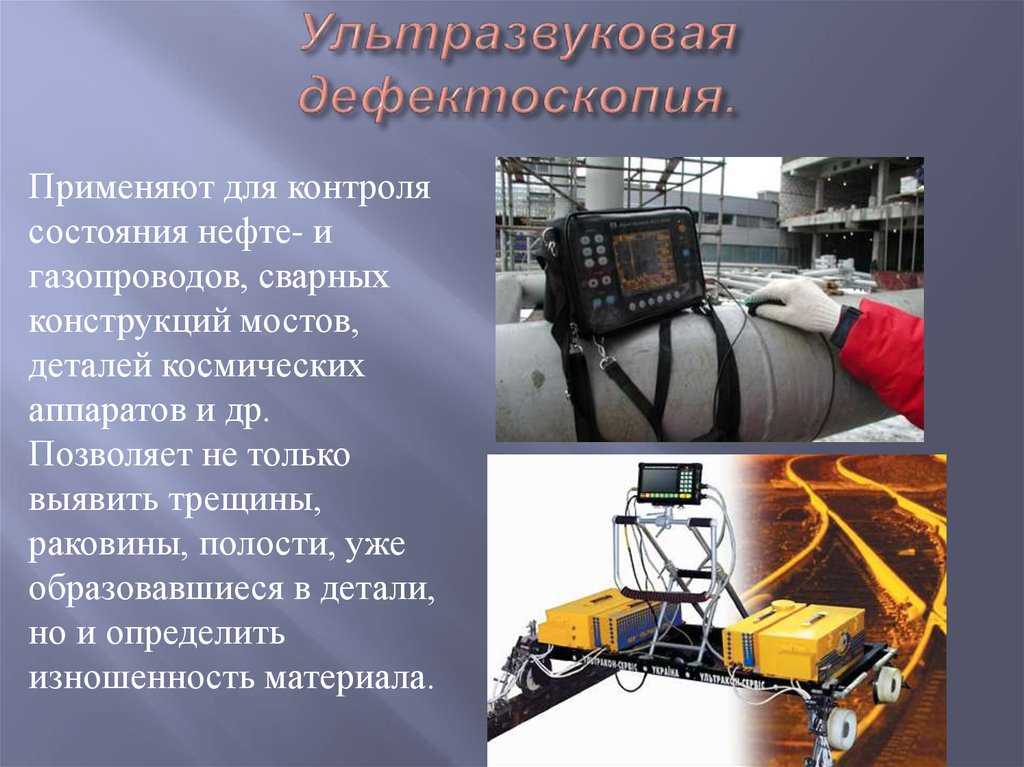
MODSONIC является ведущим индийским производителем, экспортером и продавцом компактного оборудования для ультразвуковой дефектоскопии. Линейка ультразвуковых дефектоскопов включает в себя множество моделей, которые могут применяться в различных отраслях промышленности.
Что такое ультразвуковой контроль и как он работает?
Ультразвуковой контроль (УЗК) включает ряд методов неразрушающего контроля (НК), при которых ультразвуковые волны проходят через объект или материал. Эти высокочастотные звуковые волны передаются в материалы для определения характеристик материала или обнаружения дефектов. В большинстве приложений ультразвукового контроля используются короткие импульсные волны с частотами в диапазоне от 0,1 до 15 МГц, хотя могут использоваться частоты до 50 МГц. Одним из распространенных применений этого метода испытаний является ультразвуковое измерение толщины, которое используется для определения толщины объекта, например, при оценке коррозии трубопровода.
Как это работает?
Ультразвуковой контроль использует пьезоэлектрический преобразователь, соединенный с дефектоскопом, который в своей основной форме представляет собой импульсный приемник и дисплей осциллографа. Преобразователь проходит над проверяемым объектом, который обычно связан с объектом контроля гелем, маслом или водой. Эта контактная жидкость необходима для эффективной передачи звуковой энергии от преобразователя в деталь, однако она не требуется при проведении испытаний с помощью бесконтактных методов, таких как электромагнитный акустический преобразователь (ЭМАП) или лазерное возбуждение.
Эхо-импульс и сквозное пропускание
Ультразвуковой контроль можно проводить двумя основными методами – эхо-импульсным и сквозным.
При импульсном эхо-контроле один и тот же преобразователь излучает и принимает энергию звуковой волны. В этом методе используются эхо-сигналы на границе раздела, например, на задней стороне объекта или дефекта, для отражения волн обратно к датчику. Результаты представлены в виде линейного графика, где амплитуда по оси ординат представляет интенсивность отражения, а расстояние или время по оси абсцисс показывает глубину прохождения сигнала через материал.
При тестировании сквозного пропускания используется излучатель для отправки ультразвуковых волн с одной поверхности и отдельный приемник для приема звуковой энергии, достигшей противоположной стороны объекта. Несовершенства материала уменьшают количество принимаемого звука, позволяя обнаружить дефекты.
Контактный и иммерсионный контроль
Ультразвуковой контроль также можно разделить на два основных типа: контактный или иммерсионный контроль .
Контактный ультразвуковой контроль обычно используется для проверки доступности или портативности на месте. Контактный ультразвуковой контроль можно проводить, когда доступна только одна сторона испытуемого образца, или когда испытуемые детали имеют большие размеры, неправильную форму или их трудно транспортировать.
Иммерсионный ультразвуковой контроль – это лабораторный или заводской неразрушающий контроль, который лучше всего подходит для изогнутых компонентов, сложной геометрии и для разработки ультразвуковой техники. В этом методе компонент или материал погружают в воду, которая действует как контактная жидкость вместо гелей, используемых для контактного ультразвука. Иммерсионный УЗ обычно использует метод эхо-импульса, а траектории роботизированного датчика можно использовать для проверки сложных поверхностей, которые было бы трудно покрыть контактными датчиками. Иммерсионный УЗК можно использовать для широкого диапазона толщин стенок и типов материалов, что делает его подходящим методом испытаний для различных областей применения и отраслей.
Для чего используется?
В качестве метода неразрушающего контроля ультразвуковой контроль идеально подходит для обнаружения недостатков и дефектов, не повреждая проверяемый объект или материал. Периодические ультразвуковые проверки также могут использоваться для проверки коррозии или роста известных дефектов и, таким образом, потенциально предотвращать выход из строя детали, компонента или всего актива. Он используется в различных отраслях промышленности, включая аэрокосмическую, автомобильную, строительную, медицинскую, металлургическую и обрабатывающую.
Какие материалы можно тестировать?
Ультразвуковой контроль используется в самых разных отраслях промышленности благодаря его пригодности для многих различных материалов. УЗ идеально подходит для контроля плотных кристаллических структур, таких как металлы. Керамика, пластмассы, композиты и бетон также могут успешно контролироваться, но с меньшим разрешением, поскольку затухание в этих материалах выше.
Ультразвуковая технология успешно используется в медицинском секторе на протяжении многих десятилетий и становится все более предпочтительным вариантом как для рутинной диагностической визуализации, так и для медицинских исследований из-за отсутствия ионизирующего излучения.
Преимущества
К преимуществам ультразвукового контроля относятся:
- Высокая проникающая способность, позволяющая обнаруживать дефекты глубоко внутри детали
- Высокая чувствительность, позволяющая обнаруживать очень маленькие дефекты
- Может использоваться для проверки, когда доступна только одна сторона объекта
- Более высокая по сравнению с другими методами неразрушающего контроля точность определения глубины внутренних дефектов и толщины деталей с параллельными поверхностями
- Способен оценить размер, форму, ориентацию и природу дефектов
- Способность оценивать структуру сплава компонентов с различными акустическими свойствами
- Неопасный для находящихся рядом людей, оборудования или материалов
- Возможны высокоавтоматизированные и портативные операции
- Можно получить немедленные результаты, что позволяет принимать незамедлительные решения
Ограничения
Однако есть несколько ограничений для ультразвукового контроля, а именно:
- Требуются опытные техники для осмотра и интерпретации данных
- Ложноположительные результаты, также известные как ложные сигналы, могут быть результатом допустимых аномалий, а также самой геометрии компонента
- Объекты шероховатые, неправильной формы, очень маленькие, тонкие или неоднородные, трудно поддающиеся контролю
- Перед началом испытания необходимо удалить отслоившуюся окалину или краску, хотя можно оставить чистую, надлежащим образом закрепленную краску
- Соединения, необходимые для испытаний с использованием обычного UT
- УЗК может иметь меньшую чувствительность к объемным дефектам, особенно металлическим включениям, чем рентгенографический контроль
Области применения
Ультразвуковой контроль имеет множество применений в различных отраслях промышленности, включая проверку целостности материала или компонента.