Ультразвуковой контроль сварных соединений трубопроводов: ОСТ 36-75-83 Контроль неразрушающий. Сварные соединения трубопроводов. Ультразвуковой метод
alexxlab | 24.04.2023 | 0 | Разное
Ультразвуковой контроль сварных соединений | Неразрушающий метод контроля сварки
Ультразвуковой контроль качества сварных соединений трубопроводов проводят для выявления дефектов соединений металлов – пор, раковин, неметаллических включений, непроваров в корне шва, трещин. При исследованиях определяют нарушения геометрии сварного шва, повреждения многослойных конструкций, проводится контроль толщины соединяемых материалов.
В аккредитованной строительной лаборатории С-Тест Калуга Вы сможете заказать ультразвуковой контроль качества сварных соединений по Государственным расценкам согласно ФЕР и СБЦ.
Обследование сварного соединения ультразвуком базируется на проводимости звуковых волн исследуемыми материалами. Благодаря своим уникальным физическим свойствам, каждый объект исследования (материал) взаимодействует с ультразвуковыми волнами только с присущими непосредственно ему характеристиками. Находящиеся в образце посторонние включения, трещины, имеют другие параметры взаимодействия, их состав и локализация выявляются при лабораторных исследованиях.
Ультразвуковой контроль сварных швов проводится лабораторией С-Тест Калуга согласно ГОСТ 14782-86. Введение объекта в эксплуатацию, невозможно без определения качества поверхности сварных соединений и внутренней структуры шва несущих конструкций, соединений трубопроводов, армирующих конструкций и других.
Методы ультразвуковой дефектоскопии в лаборатории С-Тест
Ультразвуковой контроль качества сварных соединений – неразрушающий метод контроля качества, определения локализации дефектов (ГОСТ 14782-86).
Наиболее востребованным методов ультразвуковых испытаний швов трубопроводов является эхо-метод. При ультразвуковой дефектоскопии сварных швов фиксируются отраженные от дефекта сигналы. Физико-механические характеристики материалов определяют по затуханию и преломлению отраженного от дна объекта импульса.
Эхо-метод – наш полевой метод ультразвуковой дефектоскопии сварных швов трубопроводов – применяется перед запуском трубопровода, когда доступ к исследуемому объекту есть только с одной стороны.
Оборудование для ультразвуковой дефектоскопии сварных соединений
В полевых исследованиях, проводимых нашей лабораторией контроля качества швов сварных, используется мобильный ультразвуковой дефектоскоп А1212 МАСТЕР ЛАЙТ. Прибор предназначен для локализации различных дефектов сварного соединения (структура сварного шва, прожоги сварных швов), трещин, внутренних расслоений, определения однородности объекта.
Достоинства ультразвукового контроля качества сварных соединений
Метод ультразвукового контроля качества, который применяет испытательная лаборатория С-Тест Калуга, имеет ряд достоинств:
· Безопасный;
· Быстрый;
· Высокая точность диагностики;
· Мобильный– портативность прибора позволяет применять метод в полевых условиях, непосредственно на объекте;
· Неразрушаемый – исследуемому объекту не наносятся повреждения;
· Автономный – проводится без остановки оборудования или объекта;
· Универсальный – контроль качества черных, нержавеющих, цветных металлов, пластмасс.
Об опасной ошибке при ультразвуковом контроле сварных соединений технологических труб
Об опасной ошибке при ультразвуковом контроле сварных соединений технологических трубопроводов
А.А. Сельский, канд. техн. наук, вед. специалист, [email protected] (ЧОУ ДПО НУЦ «Регионтехсервис», Красноярск, Россия),
Е.Е. Мельчикова, специалист (ООО «РТС-НК», Красноярск, Россия),
В.А. Сельский, специалист (ООО «ИКЦ «Индустрия», Красноярск, Россия)
В условиях, когда владельцы опасных производственных объектов при техническом диагностировании технологических трубопроводов с толщиной стенки менее 8 мм по объективным причинам не разрешают применять рентгенографию сварных соединений, требуя заменить ее ультразвуковым контролем, специалисты встают перед проблемой выбора стандарта, в котором определены нормы чувствительности и разбраковки результатов. Часто дефектоскописты ошибочно применяют единую норму предельно допустимой эквивалентной площади 1,6 кв. мм для всех вариантов толщины менее 10 мм, в том числе и менее 8 мм. Это приводит к тому, что безопасность многих таких трубопроводов после их обследования остается негарантированной. Поэтому назрела необходимость внесения изменений в ГОСТ 32569—2013 в части нормирования ультразвукового контроля сварных соединений технологических трубопроводов с толщиной стенки от 2 до 8 мм.
Введение
В России изначально принята система, в которой технологию неразрушающего контроля (НК) определяет общий стандарт. Например, для ультразвукового контроля (УК) сварных соединений — ГОСТ Р 55724-2013 [1]. А нормы чувствительности и браковки для конкретных видов объектов устанавливают ведомственные руководящие документы, например [2–4]. Зарубежные системы НК принципиально отличаются от российских. Так, документы [5, 6] представляют технологию и уровни контроля сварных соединений ультразвуком, а [7, 8] содержат уровни приемки, которые для конкретных объектов либо устанавливаются надзорным органом, либо выбираются заказчиком контроля или страховой компанией.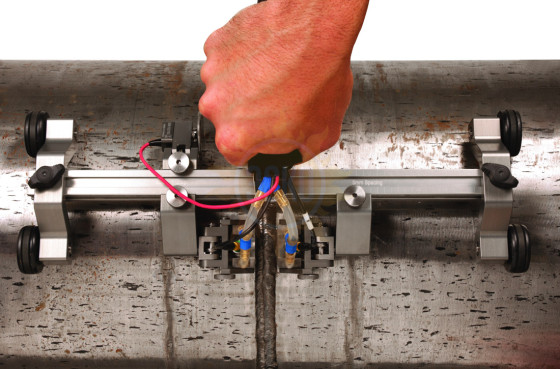
соединений технологических трубопроводов с толщиной стенки менее 8 мм. Российский стандарт [1] не ограничивает применение УК по значению толщины соединения, и для ряда подобных объектов в нашей стране действуют нормативные документы, регламентирующие УК при толщине стенки от 4 [9, 10] и даже от 2 мм [3, 11]. С одной стороны, это говорит о том, что российская система УК более маневренна, но с другой — это подчас ставит дефектоскопистов перед необходимостью логического выбора стандарта, в котором определены нормы браковки, что чревато ошибками, чему и посвящена данная статья.
Цели работы: изыскание, обоснование и популяризация логического выбора параметров УК сварных соединений технологических трубопроводов с толщиной стенки менее 8 мм в условиях отказа от радиографического метода.
Основная часть
Согласно требованиям ГОСТ 32569—2013 [2] УК сварных соединений технологических трубопроводов регламентирован, начиная от толщины стенки 8 мм. А для более тонких стенок предусмотрен только рентген. Но некоторые крупные организации — владельцы оборудования предпочитают отказываться от радиационных методов и настаивают на замене рентгена ультразвуком. Это требование, например, со стороны руководства предприятий ПАО «НК «Роснефть» представляется вполне оправданным: работы по диагностированию большого числа трубопроводов наряду с другими мероприятиями проводятся, как правило, в период капитальных ремонтов нефтеперерабатывающих установок в круглосуточном режиме и в сжатые сроки, и требование вывода посторонних лиц из зоны контроля на время рентгеновских съемок сильно замедляет работу других подразделений, участвующих в ремонтных работах. Но при этом у дефектоскопистов-акустиков нет специального нормативного документа, четко регламентирующего нормы чувствительности и разбраковки результатов УК трубопроводов с малыми значениями толщины стенки.
Для изложения сути проблемы рассмотрим п. 12.3.11 ГОСТ 32569—2013 [2], касающийся оценки качества сварных соединений по результатам УК, включая табл. 12.5.
Отметим, что в последнем абзаце данного пункта перед таблицей в скобках допущена опечатка: вместо союза «или» должна стоять запятая, как в документах [12, 13], предшествовавших данному стандарту. Молодых специалистов, не заставших периоды действия указанных документов, такая опечатка вводит в недоумение: в отношении трубопроводов I категории сказанное в скобках противоречит основному смыслу абзаца. Но главное — не в этом.
Вынужденный отказ от применения рентгена ставит специалистов УК перед необходимостью выбора норм чувствительности и браковки. Согласно ПБ 03-440—02 [14] и соответствующим международным документам [15, 16] у специалиста II и даже III уровня нет полномочий на самостоятельную разработку таких норм, они должны быть предоставлены ему документально. По результатам анализа около 150 заключений, выполненного при экспертизе промышленной безопасности технологических трубопроводов на одном из предприятий ПАО «НК «Роснефть», в зависимости от вариантов выбранных норм специалистов УК можно разделить на три группы.
Необходимо войти для просмотра
Первая группа напрямую или через методический документ [11] ориентируется на нормы [3], действующие на объектах котлонадзора и предусматривающие УК при толщине стенки трубопровода h от 2 мм. При оформлении заключений они добавляют соответствующий документ в перечень использованных. Такой вариант представляется наиболее логичным, так как нормы [3] — очень жесткие и достаточно подробно проградуированы по значениям толщины.
Вторая группа опирается на нормы СТО 00220256-005—2005 [10], которые для малых толщин практически совпадают с нормами [3]. Но, во-первых, это другой тип объектов, потому ссылка в заключениях на данный документ формально не оправдана; во-вторых, нормы [10] регламентируют УК при толщине от 4 мм, поэтому значения толщины 2,5 и 3,5 мм остаются неохваченными.
Специалисты первой и второй групп понимают, что с переходом к более тонким стенкам трубопроводов предельно допустимая эквивалентная площадь дефекта Sэ должна снижаться как по соображениям обеспечения прочности и безопасности объекта, так и по чисто геометрическим условиям. Для примера на рис. 1 показана усредненная кривая, связывающая
Необходимо войти для просмотра
где ΔА — надбавка к чувствительности прибора, дБ, которая должна вводиться при переходе от некоторого исходного значения предельно допустимой эквивалентной площади Sэ0 к меньшему Sэi. На рис. 1 она показана отдельной шкалой.
Третья группа дефектоскопистов, выделяя из контекста документов [2], [12] либо [13] фразу “1,6 кв. мм — при толщине стенки трубы до 10 мм включительно”, применяет эту норму Sэ для всех вариантов толщины менее 10 мм. Но это — грубая ошибка.
Необходимо войти для просмотра
Дефектоскописты третьей группы не учитывают, что при переходе ко все более малым значениям h (рис. 2, здесь 1 — возможные значения толщины стенки трубопровода h, мм; 2 — точки ввода УК; 3 — остаточная толщина “живого” металла hост, мм; 4 — дисковый отражатель с эквивалентной площадью Sэ = 1,6 кв. мм) с неизменным значением Sэ = 1,6hост также пойдет на снижение и на определенном этапе станет меньше нижнего предела h, который указан в конструкторской документации и регулярно пересчитывается при экспертизах промышленной безопасности. Иными словами, для толщинометрии область такой модели дефекта недопустима, а для дефектоскопии — нормальна. И такое противоречие явно неприемлемо.
Вызывает тревогу тот факт, что только на одном предприятии и в отношении только одной нефтеперерабатывающей установки обнаружено несколько десятков таких заключений, выданных в разные годы различными диагностическими организациями. Это, к сожалению, свидетельствует о весьма широком распространении такого опасного заблуждения.
Выводы
Для обеспечения единого и однозначного подхода к оценке качества сварных соединений технологических трубопроводов с h до 8 мм необходимо внести изменения или дополнения в ГОСТ 32569—2013 [2] в части нормирования УК в этой области (с исправлением вышеуказанной опечатки).
До внесения этих изменений (дополнений) учебным центрам и независимым органам по аттестации персонала в области НК при подготовке специалистов УК для контроля технологических трубопроводов рекомендуется уделять особое внимание вопросу важности дифференцированного подхода к нормам браковки в зависимости от толщины стенки объекта и логического выбора этих норм.
Независимым органам по аттестации лабораторий НК при проверках служб контроля и консультациях также рекомендуется уделять внимание логическому выбору норм УК сварных соединений технологических трубопроводов с h до 8 мм в тех условиях, когда рентген запрещен или невозможен.
Отмечена еще одна область разногласий в части УК технологических трубопроводов — касательно контроля соединений из аустенитной стали. Но это — специфическая проблема, требующая отдельного рассмотрения.
Список литературы
1. ГОСТ Р 55724—2013. Контроль неразрушающий. Соединения сварные. Методы ультразвуковые. URL: http://docs.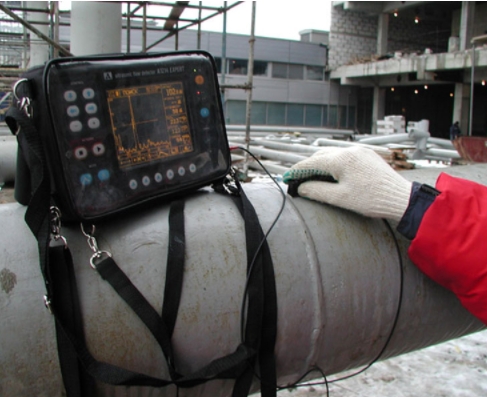
2. ГОСТ 32569—2013. Трубопроводы технологические стальные. Требования к устройству и эксплуатации на взрывопожароопасных и химически опасных производствах. URL: http://docs.cntd.ru/document/1200111138 (дата обращения: 08.10.2018).
3. РД 153-34.1-003-01. Сварка, термообработка и контроль трубных систем котлов и трубопроводов при монтаже и ремонте энергетического оборудования. РТМ-1с. URL: http://docs.cntd.ru/document/1200026674 (дата обращения: 08.10.2018).
4. ПНАЭ Г-7-032—91. Унифицированные методики контроля основных материалов (полуфабрикатов), сварных соединений и наплавки оборудования и трубопроводов атомных энергетических установок. Ультразвуковой контроль. Часть IV. Контроль сварных соединений из сталей аустенитного класса. URL: https://meganorm.ru/Index2/1/4293842/4293842254.htm (дата обращения: 08.10.2018).
5. ISO 17640:2017. Non-destructive testing of welds. Ultrasonic testing. Techniques, testing levels, and assessment.

6. DIN EN 1714—2002. Non-destructive testing of welds. Ultrasonic testing of welded joints. URL: https://docslide.us/documents/dinen-1714092002 ultrasonic-testing-of-weldedjoints.html (дата обращения: 08.10.2018).
7. ISO 11666:2010. Non-destructive testing of welds. Ultrasonic testing. Acceptance levels. URL: http://www. studmed.ru/iso-11666-2010-non-destructive-testing-of-weldsultrasonic-testing-acceptance levels_d93c3ee64df.html (дата обращения: 08.10.2018).
8. DIN EN 1712—2002. Non-destructive testing of welds. Ultrasonic testing of welded joints. Acceptance levels. URL: http://nd.gostinfo.ru/print.aspx?control=27&id=4041994&print=yes (дата обращения: 08.10.2018).
9. СТО Газпром 2-2.4-083—2006. Инструкция по неразрушающим методам контроля качества сварных соединений при строительстве и ремонте промысловых и магистральных газопроводов. URL: https://standartgost.ru/id/1072446 (дата обращения: 08.
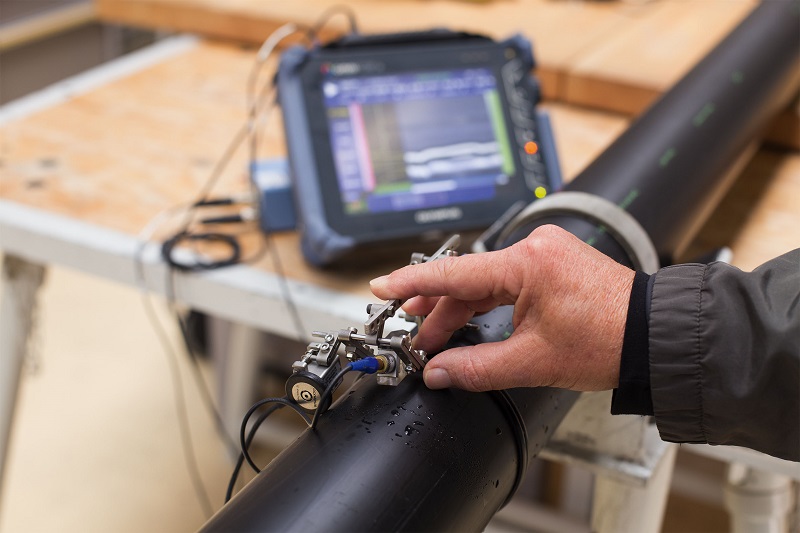
10. СТО 00220256-005—2005. Швы стыковых, угловых и тавровых сварных соединений сосудов и аппаратов, работающих под давлением. Методика ультразвукового контроля. URL: https://standartgost.ru/id/1069715 (дата обращения: 08.10.2018).
11. РД 34.17.302—97 (ОП 501 ЦД—97). Котлы паровые и водогрейные. Трубопроводы пара и горячей воды, сосуды. Сварные соединения. Контроль качества. Ультразвуковой контроль. Основные положения. URL: http://files.stroyinf.ru/Data2/1/4294817/4294817159.htm (дата обращения: 08.10.2018).
12. Рекомендации по устройству и безопасной эксплуатации технологических трубопроводов: рук. по безопасности. — Сер. 03. — Вып. 67. — М.: ЗАО НТЦ ПБ, 2018. — 194 с.
13. ПБ 03-585—03. Правила устройства и безопасной эксплуатации технологических трубопроводов. — Сер. 03. — Вып. 25. — М.: ЗАО НТЦ ПБ, 2012. — 152 с.
14. ПБ 03-440—02. Правила аттестации персонала в области неразрушающего контроля. — Сер. 28. — Вып. 3. — М.: ЗАО НТЦ ПБ, 2018. — 60 с.
15. ISO 9712:2012.

NDT personnel. URL: https://www.iso.org/ru/standard/57037.html (дата обращения: 08.10.2018).
16. EN 473:2000. Non-destructive testing. Qualification and certification of NDT personnel. General principles. URL: https:// shop.bsigroup.com/ProductDetail/?pid=000000000030147320 (дата обращения: 08.10.2018).
Ультразвуковой контроль кольцевых сварных швов трубопроводов
Глава: Ультразвуковой контроль кольцевых сварных швов трубопроводовУльтразвуковой контроль 2 – Обучение неразрушающему контролю
Глава: Ультразвуковой контроль кольцевых сварных швов трубопроводов
Вернуться к главной странице статьи
Глава |
Ультразвуковой контроль кольцевых сварных швов трубопроводов
- До недавнего времени контроль сварных швов трубопроводов традиционно был исключительно прерогативой радиографии.
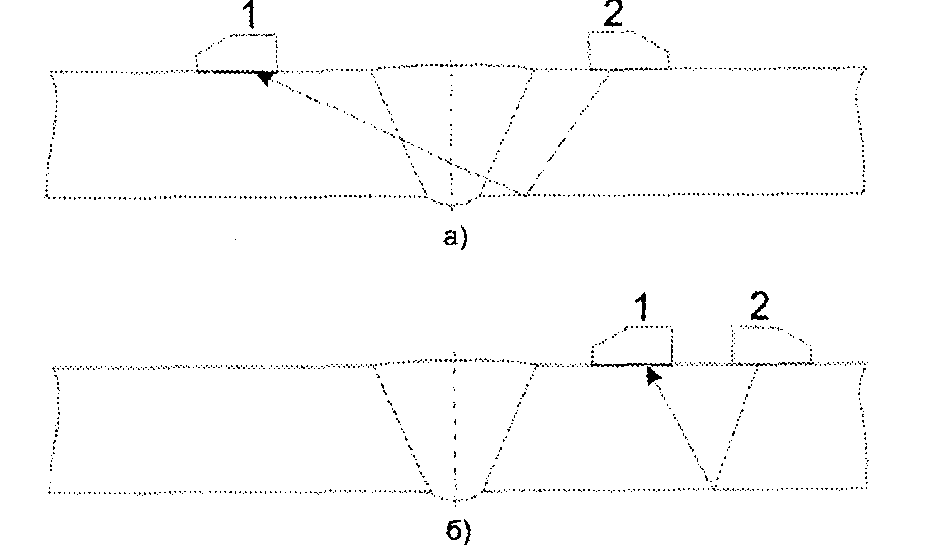
В настоящее время несколько компаний обеспечивают механизированный контроль кольцевых сварных швов трубопроводов с помощью ультразвукового контроля. Методы для этого приложения используют многие достижения в области оборудования и компьютеризации, которые стали возможны лишь недавно. Эти системы включают в себя многие аспекты технологии, обсуждаемые в этой книге, и их описание здесь дает подходящее краткое описание технологий, применяемых в данной области.
Основы систем
Рисунок 23 |
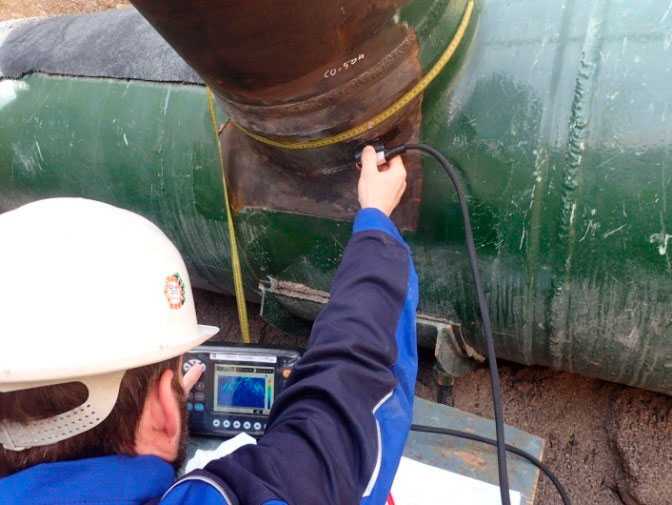
При оценке результатов сканирования оператор принимает решение о приемлемости сварки на основании длины сигнала, превышающей пороговое значение, указанное в Спецификации компании.
Хотя неплавление является наиболее вероятным дефектом в GMAW, это, безусловно, не единственный дефект. Поэтому оператор не может назвать все сигналы выше порогового значения отсутствием слияния. Для более достоверной оценки характера сигнала оператор должен использовать всю возможную информацию, доступную на дисплеях. На рис. 10-23 представлена блок-схема системы ультразвукового контроля кольцевых сварных швов трубопровода.
Датчики
- Точность определения зоны стала возможной благодаря разработке ультразвуковых преобразователей с контактной фокусировкой луча (также называемых преобразователями с внутренней фокусировкой). (см. главу 3).
Информация закрытого типа
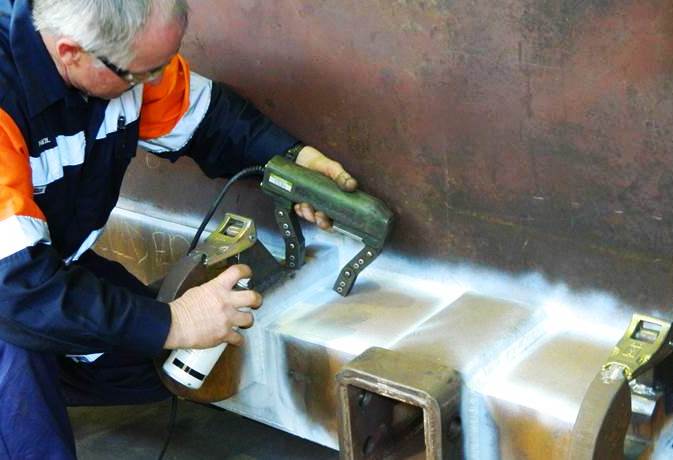
Амплитуда сигнала — это смещение от базовой линии, которое сигнал делает в УЗ-сканере. Это смещение выводится как напряжение, от нуля при отсутствии сигнала в затворе до максимум 10, 12 или 15 вольт (в зависимости от производителя) для полного смещения экрана. Затем выходное напряжение преобразуется в точку на ленточной диаграмме с положением на диаграмме, пропорциональным высоте сигнала.
Точно так же время можно отображать, используя длину затвора в качестве переменной напряжения. Самая ранняя точка на затворе — ноль вольт, а самая длинная (самая поздняя по времени) — 10 вольт. Снова «временное напряжение» преобразуется в сигнал ленточной диаграммы, положение которого пропорционально времени, в течение которого сигнал появляется в затворе. В дополнение к отображению ленточной диаграммы амплитуды и время (или эквивалентное пройденное расстояние) могут быть представлены в виде цветов. Цветной дисплей используется оператором для более быстрой оценки. Отображение диаграммы стробируемой информации поясняется рис. 10-24. Два сигнала показаны так, как они могут появиться на осциллографе. Амплитуды и времена в стробируемой области показаны как повышенные напряжения на диаграмме. Сигнал S1 составляет около 80% высоты экрана и появляется в начале строба. О раннем приходе свидетельствует низкое напряжение на временной трассе, около 2 вольт. Второй сигнал, S2, имеет меньшую амплитуду и появляется позже в затворе. На это указывает меньшее (4 вольта) амплитудное смещение на графике и большее временное смещение (около 8 вольт).
Рисунок 10-24
Требования к подготовке поверхности
- Для того, чтобы датчики располагались правильно, чтобы луч пересекал зональные мишени, их располагают на разном расстоянии от осевой линии сварного шва. Для этого необходимо, чтобы на поверхности, по которой перемещается зонд, не было материалов, препятствующих звуку или препятствующих его движению по поверхности трубы.

Калибровка
- Калибровка УЗК включает в себя настройку системы для приема сигналов от целей известного размера и в известном местоположении. Основными мишенями для дефектов несплавленного типа являются отверстия с плоским дном диаметром 2 мм. Их располагают на образце трубы в точках, соответствующих геометрии подготовки под сварку. В дополнение к основным мишеням есть мишени для подреза (глубина надрезов 1 мм) и еще одна мишень для подтверждения диапазона, чтобы гарантировать, что сварной шов проверяется сразу за центральной линией (центральной прорезью или сквозным отверстием).

Эти цели показаны на рис. 10-25 вместе с траекторией, по которой проходит центр звукового луча. Следует отметить, что путь, выбранный для проверки 1-й насыпи, отличается. Это предполагает использование тандемной пары зондов. Один датчик передает луч, который отражается от внутренней и наружной поверхностей, а также от цели. Поскольку его путь не возвращается к передающему зонду, другой зонд используется в качестве приемника для обнаружения любых сигналов, связанных с дефектами на пути передаваемого луча. Осмотр траектории Засыпки 2 показывает, что датчик находится далеко от центральной линии сварного шва, что является результатом режима эхо-импульса, в котором используется датчик.
Рисунок 10-25 | |
Горячий проход 1 и 2 | |
Земельный участок (LCP) | |
Заполнители 1 и 2 и выточка наружного диаметра | |
Корневая область | |
Спасибо RTD Quality Services Ltd.![]() |
|
Таблицы калибровки
- Различия в оборудовании и дисплеях существуют. Однако хороший пример принципов показан на рис. 10-27 (любезно предоставлено Shaw Pipeline Services). Диаграмма разделена на четыре области.

Оценка сигналов
- При ультразвуковом контроле соединений GMAW могут возникать несколько источников сигналов.

РИСУНОК 28: СХЕМАТИЧЕСКОЕ ПРЕДСТАВЛЕНИЕ РАЗРЫВОВ GMAW | ||
На схеме показаны основные неоднородности, встречающиеся в сварных соединениях GMAW. Последующие описания являются основой для оценки сигналов оператором. Открыть эту схему как карту изображения вместе с таблицей Отдельная страница |
Трубы разных производителей (т. е. отличные от калибровочного образца):
Исследования показали, что скорость звука варьируется от одного типа трубы к другому (хотя все они называются сталью X70). Отношение скорости пластикового клина, на котором установлен ультразвуковой датчик, к скорости тестируемой стали определяет угол преломления луча в стали. Если скорость звука в стали изменяется, соотношение изменяется, поэтому изменяется угол преломления. Это может означать, что если сталь с более высокой акустической скоростью, чем у калибровочного образца, должна быть испытана (без изменения настроек датчика или прибора), то исследуемые зоны не будут откалиброваны. например луч зондов LCP теперь может быть изогнут и направлен на область Fill 1.
Влияние температуры
- Во время зимних работ было обнаружено, что в калибровки были внесены многочисленные коррективы. Исследования показали, что очень важно поддерживать температуру в узком диапазоне (+/- 10°C). Причиной этого беспокойства является изменение скорости звука в зависимости от температуры. Для пластмасс эффект изменения температуры намного быстрее, чем для стали. В рабочем диапазоне контроля (от +40°C до -40°C) изменения скорости в стали пренебрежимо малы по сравнению с изменением скорости в пластике в том же диапазоне температур.
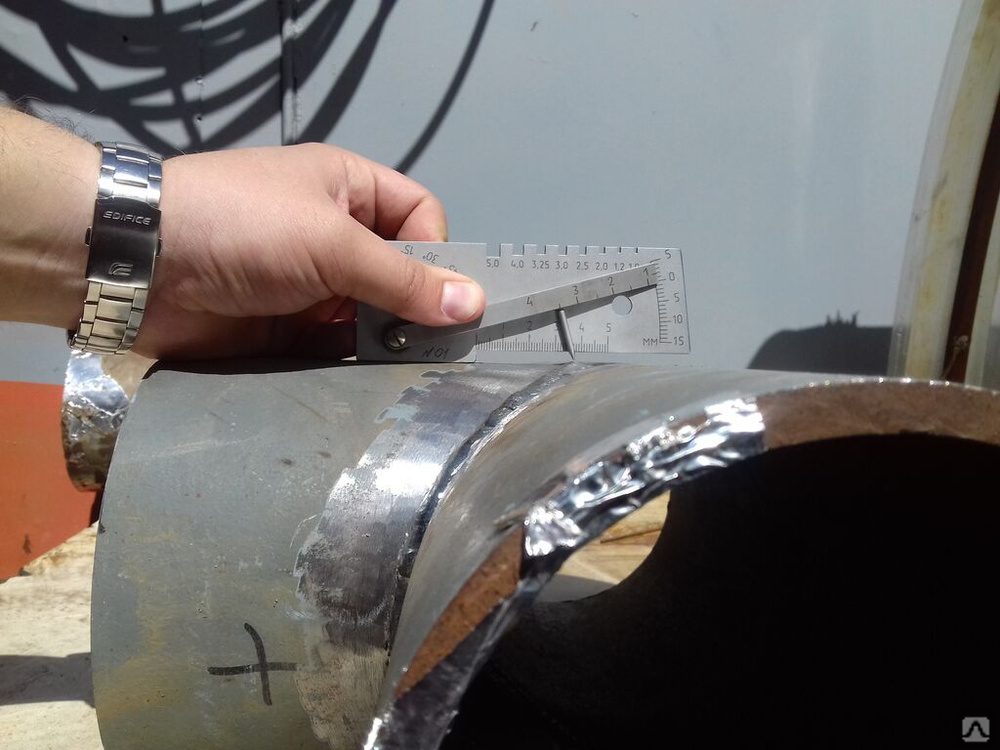
Для обеспечения контроля температурных режимов требуется ряд мер предосторожности. Термопары размещаются в клиньях, чтобы гарантировать, что рабочая температура находится в пределах допусков, разрешенных спецификацией. Регулирование температуры осуществляется либо с помощью грелки под калибровочным блоком, либо путем циркуляции нагретой контактной жидкости через датчики. Грелка несколько аккуратнее, поскольку контактная жидкость не течет все время, но если датчики не центрированы на калибровочном блоке, нагрев может быть неравномерным. Кроме того, когда датчики снимаются с площадки, они начинают остывать. От начала сканирования до его конца пластик может остыть ниже допуска. Повторное выполнение сварки дважды подряд может потребовать повторного размещения датчиков на грелке для повторного прогрева перед вторым проходом.
Рис. ![]() |
Луч с левой стороны показывает предполагаемое положение луча для области LCP. Правая сторона указывает результирующий луч, когда скорость стали больше, чем прогнозируемая (например, трубы разных производителей).
И наоборот, правая сторона может показывать луч, предназначенный для попадания в зону заполнения 1 (как в тандемной технике, показанной в разделе калибровки). Если не будут внесены поправки, чтобы сохранить датчик при температуре, которая была разработана для холодных зимних температур, пластик может охладиться, и скорость звука возрастет. Это уменьшает угол преломления до чего-то вроде луча слева, тем самым помещая его в область LCP вместо предполагаемой заливки 1.
Назад на главную страницу статьи
|НДТнет| |
Ультразвуковой контроль сварных соединений
Ультразвуковой контроль включает использование ультразвуковых волн для обнаружения дефектов внутри материала.
Сварные соединения могут иметь дефекты внутри сварных швов или вблизи зоны сварки.
Немногие из дефектов, которые часто встречаются в сварных швах, это пористость,
Трещины, шлаковые включения, несплавление, непровар, корень
вогнутость, кратерные трубы, острые подрезы, прожоги, трещины ЗТВ и
гораздо более.
Эти дефекты, если они расположены глубоко и не могут быть просмотрены вручную, Для обнаружения этих разрывов используется ультразвуковое сканирование. обычный ультразвуковой метод контроля сварных соединений, который показан здесь полностью надежный оператор. Поэтому международные органы требует, чтобы оператор имел квалификацию в соответствии со стандартом, а машина используется также соответствует требованиям стандартов.
Где научиться неразрушающему контролю?
Сертификация может быть ASNT Level 1, Level II или Level III или PCN или квалификация ISO 9712. Есть много лучших учебных заведений по неразрушающему контролю. для сертификатов NDT, одним из них является AQC – Advanced Quality Center.
Как сканировать сварной шов?
Первоначально Выберите соответствующий датчик для сканирования сварных листов или труб.
Выберите доступную высокую частоту (например, 4 МГц или 6 МГц) для проверки с высокой чувствительностью.
Обычно сканируется от половины расстояния до полутора расстояния,
для полного сканирования толщины шва. Если не возможно, по крайней мере
сканируйте от ½ до 1 расстояния, но сканируйте с обеих сторон пластины
(Верх и низ).
Точное местоположение и глубину дефекта можно узнать во время выше метод сканирования. Но для оценки размера дефекта мы всегда нужен эталонный метод, такой как DAC-кривая амплитуды расстояния, DGS- Размер увеличения расстояния или любой другой.
Чтобы нарисовать кривую АРД, нам нужен эталонный блок с равной толщиной сварного шва. или мы также можем использовать эталонные блоки стандартного эквивалентного размера в качестве упомянутый ASME, раздел V, статья 4 (как показано здесь)
Как сканировать с эталонным блоком?
Чтобы установить эталонное усиление в децибелах (дБ), сначала установите диапазон развертки (например, диапазон = 3 rd длина участка).
Поместите угловой датчик в угол основного материала, чтобы получить отражение от задней стенки в точке 3 рд длина опоры (отражение задней стенки будет от угла основания
материал).