Устройство рейсмуса: Рейсмусовый станок своими руками | Строительный портал
alexxlab | 02.09.1991 | 0 | Разное
Рейсмусовый станок своими руками | Строительный портал
0 votes
+
Голос за!
–
Голос против!
Часто мастера, которые любят работать с деревом, или хозяева дачных домиков, сталкиваются с необходимостью строгания множества досок, чтобы придать им визуальной привлекательности. Нужно выровнять толщину материала, вывести размеры досок и щитов, получить гладкую поверхность заготовок, из которых впоследствии предстоит смастерить мебель, или использовать их для отделки пола или помещения. Решением проблемы может стать покупка рейсмуса или изготовление рейсмусового станка своими руками, ведь аппарат с автоматической подачей заготовок и ножевыми валами из быстрорежущей стали значительно ускоряет и облегчает процесс строгания древесины.
Содержание:
- Предназначение рейсмусового станка
- Конструкция рейсмусового станка
- Принцип работы рейсмусового станка
- Изготовление рейсмусового станка
- Наладка рейсмусового станка
Предназначение рейсмусового станка
Рейсмусовые станки предназначаются для плоскостного строгания заготовок – щитов, брусков и досок по толщине в заданный размер, поэтому и являются основными на деревообрабатывающих предприятиях. К тому же рейсмусы имеются практически у каждого столяра. Главное назначение рейсмусовых станков состоит в равномерном обслуживании досок и прочих деревянных изделий по всей площади и получении заготовок, что имеют равную толщину по всей ширине и длине.
Рейсмусы при использовании в строительстве за один проход способны обрабатывать в большом количестве широкие доски. В отличие от промышленных аппаратов, бытовые рейсмусы являются небольшими по размерам и намного легче, что облегчает их транспортировку. К тому же современные модели имеют облегченную систему смены рабочих ножей и увеличенный контроль глубины резания, чтобы точно выверивать толщину снимаемой стружки.
Как правило, перед проведением данной процедуры деревянные поверхности подвергают предварительной обработке на фуговальном станке. Для нестандартных разновидностей материала (полимеры, мягкие пластики, утеплители на вспененной основе) предназначаются рейсмусовые станки с обрезиненными металлическими подающими вальцами, которые не способны портить поверхности заготовок.
Секционные подающие вальцы, которыми оснащено деревообрабатывающее оборудование, позволяют на входе в станок одновременно подавать разнотолщинные заготовки. Рейсмусовый станок является одним из важных установок в плотницком деле и строительстве, а также в мебельной промышленности, позволяя изготовить точные планки для гарнитуров из древесины или рейки для обшивки кухни.
На самодельном рейсмусовом станке нельзя строгать очень тонкие заготовки, потому что возникают вибрации, что сказываются на качестве обрабатываемой поверхности. Наименьшая длина обрабатываемой заготовки должна на 100 миллиметров быть большей расстояния от переднего до заднего подающего валка. При возникновении необходимости фрезеровать более короткий материал, то его нужно надежно закреплять на основании. С помощью соответствующих приспособлений на рейсмусовых станках получится обработать даже клинообразные заготовки и выровнять непараллельные плоскости.
Глубина пропила показывает срез рейсмуса за один проход: этот показатель колеблется в пределах 1 – 3 миллиметров, зависимо от ширины материала. Ширина заготовки характеризует возможности обработки изделий, что имеют определенный размер: оптимальное решение – 30 – 330 миллиметров. На производительность работы влияет мощность станка. Для частных мастерских подходит рейсмусовый станок в 1,9 кВт. Аппараты, мощность которых выше 1,8 кВт, пригодятся для строгания твердых пород древесины – ели, бука, груши, вяза, ясеня.
Конструкция рейсмусового станка
Рейсмусовым станком называют специальное устройство, которое относится к категории деревообрабатывающих станков, которые успешно справляются с плоскостным, объемным и профильным фрезерованием прямо- и криволинейных заготовок, выполненных из массивного дерева.
По конструкции различают:
- Односторонние рейсмусовые станки, на которых производится строгание только с верхней стороны;
- Двухсторонние рейсмусовые станки, где строгаются одновременно две противоположные стороны – нижняя и верхняя;
- Специальные рейсмусы – трех-, четырех- и много-ножевые.
Наибольшее распространение получили односторонние рейсмусовые станки, которые являются более простыми по конструкции и соответственно в эксплуатации. Их устройство мы сегодня и будем рассматривать.
Стол рейсмусового станка в отличие от фуговального станка кроется из одной сплошной плиты, что точно выстрогана и отшлифована, а также он не имеет в своей конструкции направляющей линейки. Кроме горизонтального стола, на котором регулируется толщина снимаемого слоя, рейсмус состоит из таких основных элементов, как специальная фреза, что представлена несколькими отдельными ножами и системы автоматической подачи деревянной заготовки по роликовым направляющим.
Станина для рейсмусового станка чугунная, пустотелая, цельнолитая, на ней крепят все детали и механизмы станка. Опорным столиком может служить металлический уголок размерами 100 на 100 миллиметров и длиной не меньше 1000 миллиметров. Эта длина объясняется мерами безопасности. Опорный столик навешивают на технологические уголки станка, крепят с одной стороны болтами, с другой – струбцинами. По высоте стол можно перемещать по направляющим салазкам с помощью подъемного механизма.
Над столом размещен ножевой вал. Механизм подачи заготовки представлен двумя парами валиков. Первая из них располагается перед ножевым валом, другая – за валом. Нижние валики устанавливают точно под верхними. Вращаются верхние валики от электрического двигателя через зубчатую передачу, поэтому они называются приводными, питающими или подающими. Нижние валики устанавливаются свободно и приводятся во вращение подаваемым материалом. Эти валики – поддерживающие или направляющие. В двусторонних рейсмусовых станках ножевые валы располагаются в столе и над рабочим столом.
Назначение нижних валиков состоит в облегчении подачи на ножи материала, они выступают над поверхностью рабочего стола на 0,2—0,3 миллиметра. Строгаемый материал при более высоком расположении нижних вальцев вибрирует от ударов ножей, тонкий будет прогибаться, и строгание получится неровным. Передний верхний валик принято делать рифленым для лучшего сцепления с нестроганой поверхностью заготовки.
Верхний задний валик необходимо делать гладким, потому что рифление способно портить строганную поверхность дерева. Размещают его ниже на 1 миллиметр режущих кромок ножей. Валики механизма подачи располагаются параллельно, поэтому в рейсмусовый станок одновременно можно подавать исключительно детали одинаковой толщины. Изделия меньшей толщины, даже на 2—3 миллиметра, дойдя до ножевого вала, получат сильный удар в торец ножом и вылетят обратно.
Для одновременного строгания пиломатериалов, что имеют разную толщину, в схему рейсмусового станка вводят рифленый валец секционный, что позволяет применять всю ширину станка и резко увеличивать его производительность. Состоит секционный валик из 12 рифленых колец, которые насажены на общую ось и соединены с ней пружинами. При прохождении под валиком изделия, толщина которого больше толщины других, что одновременно обрабатываются, секции, что надавливают на него, смещаются кверху и сохраняют сцепление с материалом под действием пружин.
Перед подобным рифленым валиком располагаются подвески, предназначение которых кроется в том, чтобы не допустить обратного вылета детали из станка. Сверху ножевой вал закрыт подъемным массивным колпаком, который служит надежным ограждением и является качественным приспособлением, что направляет стружку в воронку эксгаустера. Помимо этого, колпак совершает подпор волокон при строгании, нижняя его кромка для этого подведена к самым ножам.
Сменные ножи вы можете увеличить от двух до четырех. В качестве инструмента кроме фрезы можно применять гладкий барабан, что обтянут шлифовальной шкуркой. Выточить барабан получится из термостойкого пластика, алюминия или твердой древесины. Подходящие размеры: диаметр 80 миллиметров, длина 100 миллиметров. На одном из торцов делают проточку под гайку с шайбой. На боковой поверхности для прикрепления шкурки прорезан продольный паз, что имеет трапециевидную форму, под прижимную планку аналогичной формы. Просверливают в планке три отверстия для винтов с потайными головками.
Подача проводится верхними вальцами — задним гладким и передним рифленым. Два гладких вальца, которые свободно вращаются в подшипниках, способны уменьшать трение при движении по столу материала. Типовая максимальная ширина обрабатываемого изделия 315 – 1250 миллиметров, толщина — 5 – 160 миллиметров, диаметр ножевого вала 100 – 165 миллиметров, имеется на валу 2 – 4 ножа. Мощность электрического мотора достигает 1 – 44 кВт.
Чем быстрее будут вращаться валовые ножи, тем чище и ровнее получается поверхность заготовок после строгания. Выбирать для использования можно аппараты со скоростью вращения 6 – 10 тысяч оборотов в минуту. Вес, устройство рейсмусового станка, а также компактность рейсмуса характеризуют напрямую возможность перемещения оборудования. Компактные станки, что имеют вес 27 – 39 килограммов, являются самым хорошим выбором.
При определенном расстоянии рабочего стола от ножевого вала строгают заготовку в размер, который показан на шкале, укрепленной на станине станка. Прижимы устанавливают по двум сторонам ножевого вала, они способны предотвратить вибрацию заготовок. Стружколоматель, что расположен перед ножевым валом, способствует надламыванию стружки и заготовку прижимает к столу, образуя полость для накопления стружек вместе с прижимом.
Принцип работы рейсмусового станка
В принцип работы рейсмуса заложена методика плоского строгания доски. Главным рабочим инструментом у рейсмусового станка является ножевой вал. Заготовки для обработки подаются на горизонтальный рабочий стол вручную или вальцами, которые прижимают их к столу и тянут в область обработки. Материал строгается сверху ножами, и в результате получаются детали, абсолютно идентичные по размеру. Многие рейсмусовые станки имеют автоматическую систему подачи заготовок с определенной скоростью, чтобы аккуратно и точно снимать необходимый слой.
Можно приобрести односторонний или двусторонний рейсмус. У первых рейсмусовых станках присутствует один ножевой вал, в двусторонних есть ещё и дополнительный ножевой вал на рабочем столе. Перед обработкой деталей рейсмусом они должны быть уже подструганными в фуговальном станке. По конструкции, в принципе два станка очень схожи между собой. Зачастую двусторонний рейсмус и фуганку комбинируют в один механизм. Такое оборудование имеет два стола – для фуганка сверху и для рейсмуса снизу.
Обычно на рейсмусовом станке строгают заготовки длиной чуть больше расстояния, что сформировалось между подающими вальцами, как на видео о рейсмусовом станке. В случае использования подкладных шаблонов (цулаги) можно строгать на рейсмусовом станке заготовки (щиты, бруски, доски) с непараллельными противоположными гранями. Поверхность данного шаблона должна наклоняется таким способом, чтобы при процедуре горизонтального строгания изделий можно было получить нужную конусность.
В некоторых моделях рейсмусовых станков для удобства производителями увеличена длина стола. Поэтому брус или имеют значительную площадь опоры, а изделия обрабатываются точнее. Чтобы заготовка по столу оптимально скользила, в них делают специальные канавки, уменьшающие силу трения. Подобные модели раньше использовались преимущественно на производстве, а сегодня эти принципы широко внедряются и в бытовые рейсмусовые аппараты.
Одним из основных преимуществ рейсмусового станка выступает высокое качество обработанных поверхностей. Толщина получаемых деталей задается с помощью подъемного механизма, когда стол перемещается по отношению к ножевому валу вверх. Но стоит учитывать то, что при высокой скорости резания заготовок и большой глубине резания ухудшается качество обработанной поверхности. Поэтому чтобы добиться гладкой поверхности, необходимо делать финишные проходы при малой глубине и небольшой скорости вращения ножевого вала, если станком предусмотрена регулировка.
Рейсмусовый станок является одним из наиболее высокопроизводительных деревообрабатывающих станков. Стоит один раз настроить размеры обрабатываемой заготовки с помощью линейки и подъемника, и вся партия изделий будет одинаковой, в пределе допустимого показателя. На рейсмусовых станках вы можете обрабатывать детали с шириной до 1250 миллиметров и с толщиной 5 – 160 миллиметров, кроме специальных станков, предназначенных для определенных работ.
Изготовление рейсмусового станка
Все хозяева, которые сталкиваются с изготовлением строительной столярки, вагонки и мебели из древесины, пришли к выводу о необходимости иметь в своем пользовании хотя бы самый примитивный рейсмус. Без такой установки крайне сложно получить откалиброванные заготовки по толщине заготовки, кроме того процедура займет кучу времени. Не всем по карману купить оборудование промышленного изготовления, цены рейсмусовых станков «кусаются», поэтому умельцы приходят к решению своими руками изготовить установку.
Перед тем, как приступить к изготовлению рейсмусового станка, стоит изучить процесс использования и хранения рейсмуса. Миниатюрные станки много места не требуют. Конструкция должна располагаться таким способом, чтобы её получалось обойти вокруг для удобного произведения подачи материала. Подобную технику вы можете установить перед гаражом или домом: главное, чтобы поверхность под станком была ровной для избегания возникновения вибраций. Габариты рейсмуса зачастую не больше метра в ширину и толщину, поэтому оборудование легко сможет поместиться в сарае или гараже.
Для домашнего создания предлагается следующая конструкция. Рама и рабочий стол станка являются сварными, выполненными из уголка 50 на 50 миллиметров и квадратной трубы 40 на 40 миллиметров, можно использовать и материал больших размеров. Помните, что излишняя массивность только увеличивает устойчивость рейсмусового станка и уменьшает вибрации, возникающие при работе. Для изготовления станка необходимы: токарный и сверлильный станки, болгарка, сварочный аппарат и дрель.
Следующим обязательным элементом конструкции выступает ножевой вал. Его желательно приобрести готовым с буксами, потому что самодельные валы абсолютно не всегда являются хорошо сбалансированными. В варианте, что приведён нами, использовался трехсотмиллиметровый вал с тремя ножами. Шкивы двигателя и вала следует взять ступенчатые, для выбора оптимальных оборотов вала, в границах 4000-7000 оборотов в минуту.
Для подобного размера вала вполне подходит асинхронный мотор, что имеет мощность 4-5 кВт, нет надобности использовать шкивы большего размера, кроме того двигатель подобной мощности вполне запускается от одной фазы известными способами. Прижимные ролики рекомендуется выточить или использовать готовые из выжимки старых советских стиральных машин. Рама роликов – сварная, крепят её с одной стороны на подпружиненных болтах, с другой – для крепления используется кусок рулевой тяги от «Москвича». Опыт показывает, что неплохо два таких крепления применить на один ролик.
Стол согласно чертежу рейсмусового стола устанавливается на регулировочных болтах. Болты для избегания потребности регулировки каждого оснащены приваренными велосипедными звездочками, что соединены цепью. Пружины возьмите с клапанов мотора грузовика. К сожалению, в данном рейсмусовом станке предусмотрена ручная подача заготовок. В перспективе при наличии желания можно применить механическую.
До начала работы необходимо проверить правильность расположения ножей, а также остроту их заточки. Помните, что огражденным должен быть ножевой вал. Не допускается обработка заготовки длиной меньше расстояния между задними и передними валами. Запрещается чистить, ремонтировать и налаживать рейсмусовый станок на ходу.
Подавать заготовки необходимо торец в торец, используя при этом всю ширину стола. Помните, что материал после обработки не должен иметь вырывов, заколов, а также рисок. Ворсистость и мшистость получаются при обработке сырого материала или строгании тупыми ножами, непрострожка наблюдается при неплотном прижатии заготовки валиками к столу, неодинаковой толщине заготовки и неодинаковом выступе лезвий ножей из вала.
Наладка рейсмусового станка
Рейсмусовые станки перед работой должны быть тщательно налажены. Любая неточность наладки спровоцирует дефекты обработки или приведет к уменьшению производительности станка.
- Перекос на рабочем столе. Строгаемая поверхность не будет получаться параллельной фугованной стороне.
- Рифленый валик располагается очень низко и нажимает слишком сильно на поверхность деталей при малой глубине строгания. Строганные поверхности получаются с поперечными вмятинами.
- Нижние валики подачи размещаются над уровнем стола выше, чем нужно, на 0,1—0,2 миллиметра. Вследствие этого имеет место вибрация обрабатываемого изделия под ударами ножей, а более тонкие детали прогибаются. Строгание выходит непрямолинейным и не таким гладким, концы изделий больше прострагиваются.
- Задняя нажимная колодка на обрабатываемую деталь давит. По этой причине изделие при выходе из передних подающих валиков благодаря уменьшению силы подачи останавливается. Так как ножи будут продолжать вращаться, строгается на поверхности детали одно место, и в итоге здесь возникает во всю ширину строгания желобок.Вообще желобки формируются при всякой, даже наиболее короткой остановке изделия.
- Стружка попадает под задний гладкий валик из-за неправильного монтажа накидного козырька или неисправностей эксгаустера. По этим причинам на строганной поверхности возникают вмятины, иногда задержка детали.
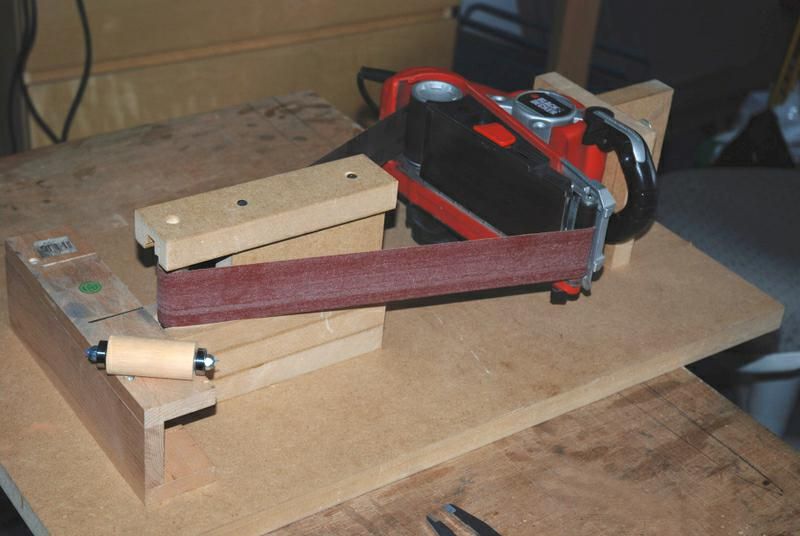
К наиболее распространенным в деревообрабатывающем деле относятся фуговальные, фрезерные, строгальные и рейсмусовые станки, которые предназначаются для плоскостного, объемного и профильного фрезерования прямо- и криволинейных заготовок из массивного дерева и древесных материалов, для нарезания проушин и шипов в брусках дверных коробок и оконных блоков. Если вы планируете заниматься только плоскостным строганием, то вам стоит отдать предпочтение рейсмусу. Вы можете приобрести этот станок в торговой точке или собрать своими руками, используя информацию, представленную на нашем сайте, и нашу пошаговую инструкцию.
Рейсмусовый станок своими руками | Строительный портал
0 votes
+
Голос за!
–
Голос против!
Часто мастера, которые любят работать с деревом, или хозяева дачных домиков, сталкиваются с необходимостью строгания множества досок, чтобы придать им визуальной привлекательности. Нужно выровнять толщину материала, вывести размеры досок и щитов, получить гладкую поверхность заготовок, из которых впоследствии предстоит смастерить мебель, или использовать их для отделки пола или помещения. Решением проблемы может стать покупка рейсмуса или изготовление рейсмусового станка своими руками, ведь аппарат с автоматической подачей заготовок и ножевыми валами из быстрорежущей стали значительно ускоряет и облегчает процесс строгания древесины.
Содержание:
- Предназначение рейсмусового станка
- Конструкция рейсмусового станка
- Принцип работы рейсмусового станка
- Изготовление рейсмусового станка
- Наладка рейсмусового станка
Предназначение рейсмусового станка
Рейсмусовые станки предназначаются для плоскостного строгания заготовок – щитов, брусков и досок по толщине в заданный размер, поэтому и являются основными на деревообрабатывающих предприятиях. К тому же рейсмусы имеются практически у каждого столяра. Главное назначение рейсмусовых станков состоит в равномерном обслуживании досок и прочих деревянных изделий по всей площади и получении заготовок, что имеют равную толщину по всей ширине и длине.
Рейсмусы при использовании в строительстве за один проход способны обрабатывать в большом количестве широкие доски. В отличие от промышленных аппаратов, бытовые рейсмусы являются небольшими по размерам и намного легче, что облегчает их транспортировку. К тому же современные модели имеют облегченную систему смены рабочих ножей и увеличенный контроль глубины резания, чтобы точно выверивать толщину снимаемой стружки.
Как правило, перед проведением данной процедуры деревянные поверхности подвергают предварительной обработке на фуговальном станке. Для нестандартных разновидностей материала (полимеры, мягкие пластики, утеплители на вспененной основе) предназначаются рейсмусовые станки с обрезиненными металлическими подающими вальцами, которые не способны портить поверхности заготовок.
Секционные подающие вальцы, которыми оснащено деревообрабатывающее оборудование, позволяют на входе в станок одновременно подавать разнотолщинные заготовки. Рейсмусовый станок является одним из важных установок в плотницком деле и строительстве, а также в мебельной промышленности, позволяя изготовить точные планки для гарнитуров из древесины или рейки для обшивки кухни.
На самодельном рейсмусовом станке нельзя строгать очень тонкие заготовки, потому что возникают вибрации, что сказываются на качестве обрабатываемой поверхности. Наименьшая длина обрабатываемой заготовки должна на 100 миллиметров быть большей расстояния от переднего до заднего подающего валка. При возникновении необходимости фрезеровать более короткий материал, то его нужно надежно закреплять на основании. С помощью соответствующих приспособлений на рейсмусовых станках получится обработать даже клинообразные заготовки и выровнять непараллельные плоскости.
Глубина пропила показывает срез рейсмуса за один проход: этот показатель колеблется в пределах 1 – 3 миллиметров, зависимо от ширины материала. Ширина заготовки характеризует возможности обработки изделий, что имеют определенный размер: оптимальное решение – 30 – 330 миллиметров. На производительность работы влияет мощность станка. Для частных мастерских подходит рейсмусовый станок в 1,9 кВт. Аппараты, мощность которых выше 1,8 кВт, пригодятся для строгания твердых пород древесины – ели, бука, груши, вяза, ясеня.
Конструкция рейсмусового станка
Рейсмусовым станком называют специальное устройство, которое относится к категории деревообрабатывающих станков, которые успешно справляются с плоскостным, объемным и профильным фрезерованием прямо- и криволинейных заготовок, выполненных из массивного дерева.
По конструкции различают:
- Односторонние рейсмусовые станки, на которых производится строгание только с верхней стороны;
- Двухсторонние рейсмусовые станки, где строгаются одновременно две противоположные стороны – нижняя и верхняя;
- Специальные рейсмусы – трех-, четырех- и много-ножевые.
Наибольшее распространение получили односторонние рейсмусовые станки, которые являются более простыми по конструкции и соответственно в эксплуатации. Их устройство мы сегодня и будем рассматривать.
Стол рейсмусового станка в отличие от фуговального станка кроется из одной сплошной плиты, что точно выстрогана и отшлифована, а также он не имеет в своей конструкции направляющей линейки. Кроме горизонтального стола, на котором регулируется толщина снимаемого слоя, рейсмус состоит из таких основных элементов, как специальная фреза, что представлена несколькими отдельными ножами и системы автоматической подачи деревянной заготовки по роликовым направляющим.
Станина для рейсмусового станка чугунная, пустотелая, цельнолитая, на ней крепят все детали и механизмы станка. Опорным столиком может служить металлический уголок размерами 100 на 100 миллиметров и длиной не меньше 1000 миллиметров. Эта длина объясняется мерами безопасности. Опорный столик навешивают на технологические уголки станка, крепят с одной стороны болтами, с другой – струбцинами. По высоте стол можно перемещать по направляющим салазкам с помощью подъемного механизма.
Над столом размещен ножевой вал. Механизм подачи заготовки представлен двумя парами валиков. Первая из них располагается перед ножевым валом, другая – за валом. Нижние валики устанавливают точно под верхними. Вращаются верхние валики от электрического двигателя через зубчатую передачу, поэтому они называются приводными, питающими или подающими. Нижние валики устанавливаются свободно и приводятся во вращение подаваемым материалом. Эти валики – поддерживающие или направляющие. В двусторонних рейсмусовых станках ножевые валы располагаются в столе и над рабочим столом.
Назначение нижних валиков состоит в облегчении подачи на ножи материала, они выступают над поверхностью рабочего стола на 0,2—0,3 миллиметра. Строгаемый материал при более высоком расположении нижних вальцев вибрирует от ударов ножей, тонкий будет прогибаться, и строгание получится неровным. Передний верхний валик принято делать рифленым для лучшего сцепления с нестроганой поверхностью заготовки. Такой валик устанавливается на 2—3 миллиметра ниже поверхности материала, что подается на ножи.
Верхний задний валик необходимо делать гладким, потому что рифление способно портить строганную поверхность дерева. Размещают его ниже на 1 миллиметр режущих кромок ножей. Валики механизма подачи располагаются параллельно, поэтому в рейсмусовый станок одновременно можно подавать исключительно детали одинаковой толщины. Изделия меньшей толщины, даже на 2—3 миллиметра, дойдя до ножевого вала, получат сильный удар в торец ножом и вылетят обратно.
Для одновременного строгания пиломатериалов, что имеют разную толщину, в схему рейсмусового станка вводят рифленый валец секционный, что позволяет применять всю ширину станка и резко увеличивать его производительность. Состоит секционный валик из 12 рифленых колец, которые насажены на общую ось и соединены с ней пружинами. При прохождении под валиком изделия, толщина которого больше толщины других, что одновременно обрабатываются, секции, что надавливают на него, смещаются кверху и сохраняют сцепление с материалом под действием пружин.
Перед подобным рифленым валиком располагаются подвески, предназначение которых кроется в том, чтобы не допустить обратного вылета детали из станка. Сверху ножевой вал закрыт подъемным массивным колпаком, который служит надежным ограждением и является качественным приспособлением, что направляет стружку в воронку эксгаустера. Помимо этого, колпак совершает подпор волокон при строгании, нижняя его кромка для этого подведена к самым ножам.
Сменные ножи вы можете увеличить от двух до четырех. В качестве инструмента кроме фрезы можно применять гладкий барабан, что обтянут шлифовальной шкуркой. Выточить барабан получится из термостойкого пластика, алюминия или твердой древесины. Подходящие размеры: диаметр 80 миллиметров, длина 100 миллиметров. На одном из торцов делают проточку под гайку с шайбой. На боковой поверхности для прикрепления шкурки прорезан продольный паз, что имеет трапециевидную форму, под прижимную планку аналогичной формы. Просверливают в планке три отверстия для винтов с потайными головками.
Подача проводится верхними вальцами — задним гладким и передним рифленым. Два гладких вальца, которые свободно вращаются в подшипниках, способны уменьшать трение при движении по столу материала. Типовая максимальная ширина обрабатываемого изделия 315 – 1250 миллиметров, толщина — 5 – 160 миллиметров, диаметр ножевого вала 100 – 165 миллиметров, имеется на валу 2 – 4 ножа. Мощность электрического мотора достигает 1 – 44 кВт.
Чем быстрее будут вращаться валовые ножи, тем чище и ровнее получается поверхность заготовок после строгания. Выбирать для использования можно аппараты со скоростью вращения 6 – 10 тысяч оборотов в минуту. Вес, устройство рейсмусового станка, а также компактность рейсмуса характеризуют напрямую возможность перемещения оборудования. Компактные станки, что имеют вес 27 – 39 килограммов, являются самым хорошим выбором.
При определенном расстоянии рабочего стола от ножевого вала строгают заготовку в размер, который показан на шкале, укрепленной на станине станка. Прижимы устанавливают по двум сторонам ножевого вала, они способны предотвратить вибрацию заготовок. Стружколоматель, что расположен перед ножевым валом, способствует надламыванию стружки и заготовку прижимает к столу, образуя полость для накопления стружек вместе с прижимом.
Принцип работы рейсмусового станка
В принцип работы рейсмуса заложена методика плоского строгания доски. Главным рабочим инструментом у рейсмусового станка является ножевой вал. Заготовки для обработки подаются на горизонтальный рабочий стол вручную или вальцами, которые прижимают их к столу и тянут в область обработки. Материал строгается сверху ножами, и в результате получаются детали, абсолютно идентичные по размеру. Многие рейсмусовые станки имеют автоматическую систему подачи заготовок с определенной скоростью, чтобы аккуратно и точно снимать необходимый слой.
Можно приобрести односторонний или двусторонний рейсмус. У первых рейсмусовых станках присутствует один ножевой вал, в двусторонних есть ещё и дополнительный ножевой вал на рабочем столе. Перед обработкой деталей рейсмусом они должны быть уже подструганными в фуговальном станке. По конструкции, в принципе два станка очень схожи между собой. Зачастую двусторонний рейсмус и фуганку комбинируют в один механизм. Такое оборудование имеет два стола – для фуганка сверху и для рейсмуса снизу.
Обычно на рейсмусовом станке строгают заготовки длиной чуть больше расстояния, что сформировалось между подающими вальцами, как на видео о рейсмусовом станке. В случае использования подкладных шаблонов (цулаги) можно строгать на рейсмусовом станке заготовки (щиты, бруски, доски) с непараллельными противоположными гранями. Поверхность данного шаблона должна наклоняется таким способом, чтобы при процедуре горизонтального строгания изделий можно было получить нужную конусность.
В некоторых моделях рейсмусовых станков для удобства производителями увеличена длина стола. Поэтому брус или имеют значительную площадь опоры, а изделия обрабатываются точнее. Чтобы заготовка по столу оптимально скользила, в них делают специальные канавки, уменьшающие силу трения. Подобные модели раньше использовались преимущественно на производстве, а сегодня эти принципы широко внедряются и в бытовые рейсмусовые аппараты.
Одним из основных преимуществ рейсмусового станка выступает высокое качество обработанных поверхностей. Толщина получаемых деталей задается с помощью подъемного механизма, когда стол перемещается по отношению к ножевому валу вверх. Но стоит учитывать то, что при высокой скорости резания заготовок и большой глубине резания ухудшается качество обработанной поверхности. Поэтому чтобы добиться гладкой поверхности, необходимо делать финишные проходы при малой глубине и небольшой скорости вращения ножевого вала, если станком предусмотрена регулировка.
Рейсмусовый станок является одним из наиболее высокопроизводительных деревообрабатывающих станков. Стоит один раз настроить размеры обрабатываемой заготовки с помощью линейки и подъемника, и вся партия изделий будет одинаковой, в пределе допустимого показателя. На рейсмусовых станках вы можете обрабатывать детали с шириной до 1250 миллиметров и с толщиной 5 – 160 миллиметров, кроме специальных станков, предназначенных для определенных работ.
Изготовление рейсмусового станка
Все хозяева, которые сталкиваются с изготовлением строительной столярки, вагонки и мебели из древесины, пришли к выводу о необходимости иметь в своем пользовании хотя бы самый примитивный рейсмус. Без такой установки крайне сложно получить откалиброванные заготовки по толщине заготовки, кроме того процедура займет кучу времени. Не всем по карману купить оборудование промышленного изготовления, цены рейсмусовых станков «кусаются», поэтому умельцы приходят к решению своими руками изготовить установку.
Перед тем, как приступить к изготовлению рейсмусового станка, стоит изучить процесс использования и хранения рейсмуса. Миниатюрные станки много места не требуют. Конструкция должна располагаться таким способом, чтобы её получалось обойти вокруг для удобного произведения подачи материала. Подобную технику вы можете установить перед гаражом или домом: главное, чтобы поверхность под станком была ровной для избегания возникновения вибраций. Габариты рейсмуса зачастую не больше метра в ширину и толщину, поэтому оборудование легко сможет поместиться в сарае или гараже.
Для домашнего создания предлагается следующая конструкция. Рама и рабочий стол станка являются сварными, выполненными из уголка 50 на 50 миллиметров и квадратной трубы 40 на 40 миллиметров, можно использовать и материал больших размеров. Помните, что излишняя массивность только увеличивает устойчивость рейсмусового станка и уменьшает вибрации, возникающие при работе. Для изготовления станка необходимы: токарный и сверлильный станки, болгарка, сварочный аппарат и дрель.
Следующим обязательным элементом конструкции выступает ножевой вал. Его желательно приобрести готовым с буксами, потому что самодельные валы абсолютно не всегда являются хорошо сбалансированными. В варианте, что приведён нами, использовался трехсотмиллиметровый вал с тремя ножами. Шкивы двигателя и вала следует взять ступенчатые, для выбора оптимальных оборотов вала, в границах 4000-7000 оборотов в минуту.
Для подобного размера вала вполне подходит асинхронный мотор, что имеет мощность 4-5 кВт, нет надобности использовать шкивы большего размера, кроме того двигатель подобной мощности вполне запускается от одной фазы известными способами. Прижимные ролики рекомендуется выточить или использовать готовые из выжимки старых советских стиральных машин. Рама роликов – сварная, крепят её с одной стороны на подпружиненных болтах, с другой – для крепления используется кусок рулевой тяги от «Москвича». Опыт показывает, что неплохо два таких крепления применить на один ролик.
Стол согласно чертежу рейсмусового стола устанавливается на регулировочных болтах. Болты для избегания потребности регулировки каждого оснащены приваренными велосипедными звездочками, что соединены цепью. Пружины возьмите с клапанов мотора грузовика. К сожалению, в данном рейсмусовом станке предусмотрена ручная подача заготовок. В перспективе при наличии желания можно применить механическую.
До начала работы необходимо проверить правильность расположения ножей, а также остроту их заточки. Помните, что огражденным должен быть ножевой вал. Не допускается обработка заготовки длиной меньше расстояния между задними и передними валами. Запрещается чистить, ремонтировать и налаживать рейсмусовый станок на ходу.
Подавать заготовки необходимо торец в торец, используя при этом всю ширину стола. Помните, что материал после обработки не должен иметь вырывов, заколов, а также рисок. Ворсистость и мшистость получаются при обработке сырого материала или строгании тупыми ножами, непрострожка наблюдается при неплотном прижатии заготовки валиками к столу, неодинаковой толщине заготовки и неодинаковом выступе лезвий ножей из вала.
Наладка рейсмусового станка
Рейсмусовые станки перед работой должны быть тщательно налажены. Любая неточность наладки спровоцирует дефекты обработки или приведет к уменьшению производительности станка. Чаще всего наблюдаются такие упущения в наладке рейсмусов:
- Перекос на рабочем столе. Строгаемая поверхность не будет получаться параллельной фугованной стороне.
- Рифленый валик располагается очень низко и нажимает слишком сильно на поверхность деталей при малой глубине строгания. Строганные поверхности получаются с поперечными вмятинами.
- Нижние валики подачи размещаются над уровнем стола выше, чем нужно, на 0,1—0,2 миллиметра. Вследствие этого имеет место вибрация обрабатываемого изделия под ударами ножей, а более тонкие детали прогибаются. Строгание выходит непрямолинейным и не таким гладким, концы изделий больше прострагиваются.
- Задняя нажимная колодка на обрабатываемую деталь давит. По этой причине изделие при выходе из передних подающих валиков благодаря уменьшению силы подачи останавливается. Так как ножи будут продолжать вращаться, строгается на поверхности детали одно место, и в итоге здесь возникает во всю ширину строгания желобок.Вообще желобки формируются при всякой, даже наиболее короткой остановке изделия.
Остановки часто случаются во время, когда детали поступают в задние валики. Это случается при очень низком размещении верхнего заднего валика и при его слишком большом нажиме на материал. Причинами кратковременной задержки или остановки детали бывает также недостаточный нажим на изделие подающих валиков, чрезмерно высокое расположение нижних валиков, сильное загрязнение стола при обработке сосновых деталей смолой.
- Стружка попадает под задний гладкий валик из-за неправильного монтажа накидного козырька или неисправностей эксгаустера. По этим причинам на строганной поверхности возникают вмятины, иногда задержка детали.
Поэтому при наладке рейсмусового станка следует помнить, что при значительном заполнении стола, к примеру, при строгании широкого щи¬та или одновременной подаче изделий во всю ширину рабочего стола, повышенным должно быть давление подающих вальцов, потому что в этих случаях сопротивление резанию сильно увеличивается. При строгании узких деталей или при небольшом заполнении стола нужно уменьшить давление подающих вальцов, чтобы избежать смятия дерева.
К наиболее распространенным в деревообрабатывающем деле относятся фуговальные, фрезерные, строгальные и рейсмусовые станки, которые предназначаются для плоскостного, объемного и профильного фрезерования прямо- и криволинейных заготовок из массивного дерева и древесных материалов, для нарезания проушин и шипов в брусках дверных коробок и оконных блоков. Если вы планируете заниматься только плоскостным строганием, то вам стоит отдать предпочтение рейсмусу. Вы можете приобрести этот станок в торговой точке или собрать своими руками, используя информацию, представленную на нашем сайте, и нашу пошаговую инструкцию.
Рейсмусовый станок своими руками | Строительный портал
0 votes
+
Голос за!
–
Голос против!
Часто мастера, которые любят работать с деревом, или хозяева дачных домиков, сталкиваются с необходимостью строгания множества досок, чтобы придать им визуальной привлекательности. Нужно выровнять толщину материала, вывести размеры досок и щитов, получить гладкую поверхность заготовок, из которых впоследствии предстоит смастерить мебель, или использовать их для отделки пола или помещения. Решением проблемы может стать покупка рейсмуса или изготовление рейсмусового станка своими руками, ведь аппарат с автоматической подачей заготовок и ножевыми валами из быстрорежущей стали значительно ускоряет и облегчает процесс строгания древесины.
Содержание:
- Предназначение рейсмусового станка
- Конструкция рейсмусового станка
- Принцип работы рейсмусового станка
- Изготовление рейсмусового станка
- Наладка рейсмусового станка
Предназначение рейсмусового станка
Рейсмусовые станки предназначаются для плоскостного строгания заготовок – щитов, брусков и досок по толщине в заданный размер, поэтому и являются основными на деревообрабатывающих предприятиях. К тому же рейсмусы имеются практически у каждого столяра. Главное назначение рейсмусовых станков состоит в равномерном обслуживании досок и прочих деревянных изделий по всей площади и получении заготовок, что имеют равную толщину по всей ширине и длине.
Рейсмусы при использовании в строительстве за один проход способны обрабатывать в большом количестве широкие доски. В отличие от промышленных аппаратов, бытовые рейсмусы являются небольшими по размерам и намного легче, что облегчает их транспортировку. К тому же современные модели имеют облегченную систему смены рабочих ножей и увеличенный контроль глубины резания, чтобы точно выверивать толщину снимаемой стружки.
Как правило, перед проведением данной процедуры деревянные поверхности подвергают предварительной обработке на фуговальном станке. Для нестандартных разновидностей материала (полимеры, мягкие пластики, утеплители на вспененной основе) предназначаются рейсмусовые станки с обрезиненными металлическими подающими вальцами, которые не способны портить поверхности заготовок.
Секционные подающие вальцы, которыми оснащено деревообрабатывающее оборудование, позволяют на входе в станок одновременно подавать разнотолщинные заготовки. Рейсмусовый станок является одним из важных установок в плотницком деле и строительстве, а также в мебельной промышленности, позволяя изготовить точные планки для гарнитуров из древесины или рейки для обшивки кухни.
На самодельном рейсмусовом станке нельзя строгать очень тонкие заготовки, потому что возникают вибрации, что сказываются на качестве обрабатываемой поверхности. Наименьшая длина обрабатываемой заготовки должна на 100 миллиметров быть большей расстояния от переднего до заднего подающего валка. При возникновении необходимости фрезеровать более короткий материал, то его нужно надежно закреплять на основании. С помощью соответствующих приспособлений на рейсмусовых станках получится обработать даже клинообразные заготовки и выровнять непараллельные плоскости.
Глубина пропила показывает срез рейсмуса за один проход: этот показатель колеблется в пределах 1 – 3 миллиметров, зависимо от ширины материала. Ширина заготовки характеризует возможности обработки изделий, что имеют определенный размер: оптимальное решение – 30 – 330 миллиметров. На производительность работы влияет мощность станка. Для частных мастерских подходит рейсмусовый станок в 1,9 кВт. Аппараты, мощность которых выше 1,8 кВт, пригодятся для строгания твердых пород древесины – ели, бука, груши, вяза, ясеня.
Конструкция рейсмусового станка
Рейсмусовым станком называют специальное устройство, которое относится к категории деревообрабатывающих станков, которые успешно справляются с плоскостным, объемным и профильным фрезерованием прямо- и криволинейных заготовок, выполненных из массивного дерева.
По конструкции различают:
- Односторонние рейсмусовые станки, на которых производится строгание только с верхней стороны;
- Двухсторонние рейсмусовые станки, где строгаются одновременно две противоположные стороны – нижняя и верхняя;
- Специальные рейсмусы – трех-, четырех- и много-ножевые.
Наибольшее распространение получили односторонние рейсмусовые станки, которые являются более простыми по конструкции и соответственно в эксплуатации. Их устройство мы сегодня и будем рассматривать.
Стол рейсмусового станка в отличие от фуговального станка кроется из одной сплошной плиты, что точно выстрогана и отшлифована, а также он не имеет в своей конструкции направляющей линейки. Кроме горизонтального стола, на котором регулируется толщина снимаемого слоя, рейсмус состоит из таких основных элементов, как специальная фреза, что представлена несколькими отдельными ножами и системы автоматической подачи деревянной заготовки по роликовым направляющим.
Станина для рейсмусового станка чугунная, пустотелая, цельнолитая, на ней крепят все детали и механизмы станка. Опорным столиком может служить металлический уголок размерами 100 на 100 миллиметров и длиной не меньше 1000 миллиметров. Эта длина объясняется мерами безопасности. Опорный столик навешивают на технологические уголки станка, крепят с одной стороны болтами, с другой – струбцинами. По высоте стол можно перемещать по направляющим салазкам с помощью подъемного механизма.
Над столом размещен ножевой вал. Механизм подачи заготовки представлен двумя парами валиков. Первая из них располагается перед ножевым валом, другая – за валом. Нижние валики устанавливают точно под верхними. Вращаются верхние валики от электрического двигателя через зубчатую передачу, поэтому они называются приводными, питающими или подающими. Нижние валики устанавливаются свободно и приводятся во вращение подаваемым материалом. Эти валики – поддерживающие или направляющие. В двусторонних рейсмусовых станках ножевые валы располагаются в столе и над рабочим столом.
Назначение нижних валиков состоит в облегчении подачи на ножи материала, они выступают над поверхностью рабочего стола на 0,2—0,3 миллиметра. Строгаемый материал при более высоком расположении нижних вальцев вибрирует от ударов ножей, тонкий будет прогибаться, и строгание получится неровным. Передний верхний валик принято делать рифленым для лучшего сцепления с нестроганой поверхностью заготовки. Такой валик устанавливается на 2—3 миллиметра ниже поверхности материала, что подается на ножи.
Верхний задний валик необходимо делать гладким, потому что рифление способно портить строганную поверхность дерева. Размещают его ниже на 1 миллиметр режущих кромок ножей. Валики механизма подачи располагаются параллельно, поэтому в рейсмусовый станок одновременно можно подавать исключительно детали одинаковой толщины. Изделия меньшей толщины, даже на 2—3 миллиметра, дойдя до ножевого вала, получат сильный удар в торец ножом и вылетят обратно.
Для одновременного строгания пиломатериалов, что имеют разную толщину, в схему рейсмусового станка вводят рифленый валец секционный, что позволяет применять всю ширину станка и резко увеличивать его производительность. Состоит секционный валик из 12 рифленых колец, которые насажены на общую ось и соединены с ней пружинами. При прохождении под валиком изделия, толщина которого больше толщины других, что одновременно обрабатываются, секции, что надавливают на него, смещаются кверху и сохраняют сцепление с материалом под действием пружин.
Перед подобным рифленым валиком располагаются подвески, предназначение которых кроется в том, чтобы не допустить обратного вылета детали из станка. Сверху ножевой вал закрыт подъемным массивным колпаком, который служит надежным ограждением и является качественным приспособлением, что направляет стружку в воронку эксгаустера. Помимо этого, колпак совершает подпор волокон при строгании, нижняя его кромка для этого подведена к самым ножам.
Сменные ножи вы можете увеличить от двух до четырех. В качестве инструмента кроме фрезы можно применять гладкий барабан, что обтянут шлифовальной шкуркой. Выточить барабан получится из термостойкого пластика, алюминия или твердой древесины. Подходящие размеры: диаметр 80 миллиметров, длина 100 миллиметров. На одном из торцов делают проточку под гайку с шайбой. На боковой поверхности для прикрепления шкурки прорезан продольный паз, что имеет трапециевидную форму, под прижимную планку аналогичной формы. Просверливают в планке три отверстия для винтов с потайными головками.
Подача проводится верхними вальцами — задним гладким и передним рифленым. Два гладких вальца, которые свободно вращаются в подшипниках, способны уменьшать трение при движении по столу материала. Типовая максимальная ширина обрабатываемого изделия 315 – 1250 миллиметров, толщина — 5 – 160 миллиметров, диаметр ножевого вала 100 – 165 миллиметров, имеется на валу 2 – 4 ножа. Мощность электрического мотора достигает 1 – 44 кВт.
Чем быстрее будут вращаться валовые ножи, тем чище и ровнее получается поверхность заготовок после строгания. Выбирать для использования можно аппараты со скоростью вращения 6 – 10 тысяч оборотов в минуту. Вес, устройство рейсмусового станка, а также компактность рейсмуса характеризуют напрямую возможность перемещения оборудования. Компактные станки, что имеют вес 27 – 39 килограммов, являются самым хорошим выбором.
При определенном расстоянии рабочего стола от ножевого вала строгают заготовку в размер, который показан на шкале, укрепленной на станине станка. Прижимы устанавливают по двум сторонам ножевого вала, они способны предотвратить вибрацию заготовок. Стружколоматель, что расположен перед ножевым валом, способствует надламыванию стружки и заготовку прижимает к столу, образуя полость для накопления стружек вместе с прижимом.
Принцип работы рейсмусового станка
В принцип работы рейсмуса заложена методика плоского строгания доски. Главным рабочим инструментом у рейсмусового станка является ножевой вал. Заготовки для обработки подаются на горизонтальный рабочий стол вручную или вальцами, которые прижимают их к столу и тянут в область обработки. Материал строгается сверху ножами, и в результате получаются детали, абсолютно идентичные по размеру. Многие рейсмусовые станки имеют автоматическую систему подачи заготовок с определенной скоростью, чтобы аккуратно и точно снимать необходимый слой.
Можно приобрести односторонний или двусторонний рейсмус. У первых рейсмусовых станках присутствует один ножевой вал, в двусторонних есть ещё и дополнительный ножевой вал на рабочем столе. Перед обработкой деталей рейсмусом они должны быть уже подструганными в фуговальном станке. По конструкции, в принципе два станка очень схожи между собой. Зачастую двусторонний рейсмус и фуганку комбинируют в один механизм. Такое оборудование имеет два стола – для фуганка сверху и для рейсмуса снизу.
Обычно на рейсмусовом станке строгают заготовки длиной чуть больше расстояния, что сформировалось между подающими вальцами, как на видео о рейсмусовом станке. В случае использования подкладных шаблонов (цулаги) можно строгать на рейсмусовом станке заготовки (щиты, бруски, доски) с непараллельными противоположными гранями. Поверхность данного шаблона должна наклоняется таким способом, чтобы при процедуре горизонтального строгания изделий можно было получить нужную конусность.
В некоторых моделях рейсмусовых станков для удобства производителями увеличена длина стола. Поэтому брус или имеют значительную площадь опоры, а изделия обрабатываются точнее. Чтобы заготовка по столу оптимально скользила, в них делают специальные канавки, уменьшающие силу трения. Подобные модели раньше использовались преимущественно на производстве, а сегодня эти принципы широко внедряются и в бытовые рейсмусовые аппараты.
Одним из основных преимуществ рейсмусового станка выступает высокое качество обработанных поверхностей. Толщина получаемых деталей задается с помощью подъемного механизма, когда стол перемещается по отношению к ножевому валу вверх. Но стоит учитывать то, что при высокой скорости резания заготовок и большой глубине резания ухудшается качество обработанной поверхности. Поэтому чтобы добиться гладкой поверхности, необходимо делать финишные проходы при малой глубине и небольшой скорости вращения ножевого вала, если станком предусмотрена регулировка.
Рейсмусовый станок является одним из наиболее высокопроизводительных деревообрабатывающих станков. Стоит один раз настроить размеры обрабатываемой заготовки с помощью линейки и подъемника, и вся партия изделий будет одинаковой, в пределе допустимого показателя. На рейсмусовых станках вы можете обрабатывать детали с шириной до 1250 миллиметров и с толщиной 5 – 160 миллиметров, кроме специальных станков, предназначенных для определенных работ.
Изготовление рейсмусового станка
Все хозяева, которые сталкиваются с изготовлением строительной столярки, вагонки и мебели из древесины, пришли к выводу о необходимости иметь в своем пользовании хотя бы самый примитивный рейсмус. Без такой установки крайне сложно получить откалиброванные заготовки по толщине заготовки, кроме того процедура займет кучу времени. Не всем по карману купить оборудование промышленного изготовления, цены рейсмусовых станков «кусаются», поэтому умельцы приходят к решению своими руками изготовить установку.
Перед тем, как приступить к изготовлению рейсмусового станка, стоит изучить процесс использования и хранения рейсмуса. Миниатюрные станки много места не требуют. Конструкция должна располагаться таким способом, чтобы её получалось обойти вокруг для удобного произведения подачи материала. Подобную технику вы можете установить перед гаражом или домом: главное, чтобы поверхность под станком была ровной для избегания возникновения вибраций. Габариты рейсмуса зачастую не больше метра в ширину и толщину, поэтому оборудование легко сможет поместиться в сарае или гараже.
Для домашнего создания предлагается следующая конструкция. Рама и рабочий стол станка являются сварными, выполненными из уголка 50 на 50 миллиметров и квадратной трубы 40 на 40 миллиметров, можно использовать и материал больших размеров. Помните, что излишняя массивность только увеличивает устойчивость рейсмусового станка и уменьшает вибрации, возникающие при работе. Для изготовления станка необходимы: токарный и сверлильный станки, болгарка, сварочный аппарат и дрель.
Следующим обязательным элементом конструкции выступает ножевой вал. Его желательно приобрести готовым с буксами, потому что самодельные валы абсолютно не всегда являются хорошо сбалансированными. В варианте, что приведён нами, использовался трехсотмиллиметровый вал с тремя ножами. Шкивы двигателя и вала следует взять ступенчатые, для выбора оптимальных оборотов вала, в границах 4000-7000 оборотов в минуту.
Для подобного размера вала вполне подходит асинхронный мотор, что имеет мощность 4-5 кВт, нет надобности использовать шкивы большего размера, кроме того двигатель подобной мощности вполне запускается от одной фазы известными способами. Прижимные ролики рекомендуется выточить или использовать готовые из выжимки старых советских стиральных машин. Рама роликов – сварная, крепят её с одной стороны на подпружиненных болтах, с другой – для крепления используется кусок рулевой тяги от «Москвича». Опыт показывает, что неплохо два таких крепления применить на один ролик.
Стол согласно чертежу рейсмусового стола устанавливается на регулировочных болтах. Болты для избегания потребности регулировки каждого оснащены приваренными велосипедными звездочками, что соединены цепью. Пружины возьмите с клапанов мотора грузовика. К сожалению, в данном рейсмусовом станке предусмотрена ручная подача заготовок. В перспективе при наличии желания можно применить механическую.
До начала работы необходимо проверить правильность расположения ножей, а также остроту их заточки. Помните, что огражденным должен быть ножевой вал. Не допускается обработка заготовки длиной меньше расстояния между задними и передними валами. Запрещается чистить, ремонтировать и налаживать рейсмусовый станок на ходу.
Подавать заготовки необходимо торец в торец, используя при этом всю ширину стола. Помните, что материал после обработки не должен иметь вырывов, заколов, а также рисок. Ворсистость и мшистость получаются при обработке сырого материала или строгании тупыми ножами, непрострожка наблюдается при неплотном прижатии заготовки валиками к столу, неодинаковой толщине заготовки и неодинаковом выступе лезвий ножей из вала.
Наладка рейсмусового станка
Рейсмусовые станки перед работой должны быть тщательно налажены. Любая неточность наладки спровоцирует дефекты обработки или приведет к уменьшению производительности станка. Чаще всего наблюдаются такие упущения в наладке рейсмусов:
- Перекос на рабочем столе. Строгаемая поверхность не будет получаться параллельной фугованной стороне.
- Рифленый валик располагается очень низко и нажимает слишком сильно на поверхность деталей при малой глубине строгания. Строганные поверхности получаются с поперечными вмятинами.
- Нижние валики подачи размещаются над уровнем стола выше, чем нужно, на 0,1—0,2 миллиметра. Вследствие этого имеет место вибрация обрабатываемого изделия под ударами ножей, а более тонкие детали прогибаются. Строгание выходит непрямолинейным и не таким гладким, концы изделий больше прострагиваются.
- Задняя нажимная колодка на обрабатываемую деталь давит. По этой причине изделие при выходе из передних подающих валиков благодаря уменьшению силы подачи останавливается. Так как ножи будут продолжать вращаться, строгается на поверхности детали одно место, и в итоге здесь возникает во всю ширину строгания желобок.Вообще желобки формируются при всякой, даже наиболее короткой остановке изделия.
Остановки часто случаются во время, когда детали поступают в задние валики. Это случается при очень низком размещении верхнего заднего валика и при его слишком большом нажиме на материал. Причинами кратковременной задержки или остановки детали бывает также недостаточный нажим на изделие подающих валиков, чрезмерно высокое расположение нижних валиков, сильное загрязнение стола при обработке сосновых деталей смолой.
- Стружка попадает под задний гладкий валик из-за неправильного монтажа накидного козырька или неисправностей эксгаустера. По этим причинам на строганной поверхности возникают вмятины, иногда задержка детали.
Поэтому при наладке рейсмусового станка следует помнить, что при значительном заполнении стола, к примеру, при строгании широкого щи¬та или одновременной подаче изделий во всю ширину рабочего стола, повышенным должно быть давление подающих вальцов, потому что в этих случаях сопротивление резанию сильно увеличивается. При строгании узких деталей или при небольшом заполнении стола нужно уменьшить давление подающих вальцов, чтобы избежать смятия дерева.
К наиболее распространенным в деревообрабатывающем деле относятся фуговальные, фрезерные, строгальные и рейсмусовые станки, которые предназначаются для плоскостного, объемного и профильного фрезерования прямо- и криволинейных заготовок из массивного дерева и древесных материалов, для нарезания проушин и шипов в брусках дверных коробок и оконных блоков. Если вы планируете заниматься только плоскостным строганием, то вам стоит отдать предпочтение рейсмусу. Вы можете приобрести этот станок в торговой точке или собрать своими руками, используя информацию, представленную на нашем сайте, и нашу пошаговую инструкцию.
Ультразвуковой толщиномер | Ультразвуковое испытательное оборудование
Принцип мультиэхо-ультразвуковой толщинометрии с использованием ультразвукового мульти-эхо-инструмента для измерения толщины прост и может быть проиллюстрирован на рисунке ниже.
Все звуки — это физические вибрации, которые проходят через материал, а в случае со звуком, к которому мы привыкли, вибрации проходят через воздух. Ультразвук такой же, как звук, который мы слышим, но его частота превышает ту, которую люди способны слышать. В то время как самая высокая частота, которую может слышать человек, составляет около 20 000 Гц, все устройства Portagauge используют звук на частоте 2,25 МГц, 2,5 МГц или 5 МГц в зависимости от конкретного используемого датчика.
Все устройства Portagauge® используют ультразвук для измерения толщины материала. Устройство посылает на датчик сильный электрический сигнал, заставляя его излучать ультразвуковой импульс высокой энергии. Передаваемый ультразвуковой импульс проходит через покрытие и металл и отражается от задней стенки. Затем отраженные звуковые волны отражаются внутри металла, и каждый раз лишь небольшая часть эха проходит обратно через покрытие. Время между небольшими эхо-сигналами дает синхронизацию эхо-сигналов внутри металла, которые относятся к толщине металла. Возвращаемые эхосигналы не обязательно должны быть последовательными, так как толщиномер автоматически интерпретирует их и рассчитает толщину. Для каждого импульса, посылаемого в металл, проверяются как минимум три эхо-сигнала, чтобы его можно было квалифицировать как ультразвуковой толщиномер с несколькими эхо-сигналами.
С помощью линейки Portagauge® можно измерять толщину различных металлов и твердых пластиков. Существуют различные варианты ультразвуковых датчиков с разными частотами для работы с разными материалами.
В Portagauge® 5 есть база данных, содержащая данные о скорости звука для 12+ различных материалов, предварительно загруженных в устройство для удобства. Примеры материалов в базе данных: углеродистая сталь, нержавеющая сталь 304, нержавеющая сталь 316, чугун, ковкий чугун, медь, ПВХ, свинец, нейлон, полиэтилен, алюминий, асбест и стекловолокно. Существует также ввод для пользовательских материалов, чтобы вы могли вводить тестовый материал, которого нет в списке.
Если есть конкретный материал, который вы хотите протестировать, но не уверены, сможет ли наша линейка Portagauge® это сделать, свяжитесь с нами, отправив запрос.
Нам известно, что наши клиенты занимаются неразрушающим контролем с использованием ультразвуковых толщиномеров для измерения толщины материалов в различных условиях. Мы разработали список рекомендаций по передовой практике, чтобы убедиться, что у вас есть знания, необходимые для успешного измерения.
Удалите любой поверхностный мусор, который может помешать измерению будут устранены. Воздушные карманы будут влиять на ультразвуковой сигнал, снижая надежность полученных измерений
Убедитесь, что при выполнении измерения к датчику приложено достаточное давление
Нет необходимости удалять слой краски с материала при работе с Portagauge® 4 и Portagauge® 5, так как ультразвуковая технология мультиэхо будет учитывать дополнительное отражение звука и определять правильное обратное эхо, которое представляет истинную стену толщина материала
Как работает линейка Portagauge® для обнаружения коррозии и толщины материала? В наших Portagauge® 3 и Portagauge® 5 используются двухэлементные датчики, которые обычно используются для контроля коррозии. Они очень чувствительны к обнаружению коррозии в виде точечной коррозии и почти любых других форм коррозии. Точечная коррозия – это, в частности, локализованная форма коррозии, при которой в материале образуются полости, которые могут повредить материал.
Двухэлементные датчики содержат два пьезоэлектрических кристалла, один из которых действует как ультразвуковой передатчик, а другой — как ультразвуковой приемник. Двухэлементная конструкция дает датчикам преимущество перед одноэлементными датчиками при работе с неровными поверхностями в сильно корродированных материалах из-за эффекта псевдофокусировки ультразвуковых лучей. Это позволяет двухэлементным датчикам быть более чувствительными к эхо-сигналам от основания ямок корродированного материала, которые представляют собой минимальную оставшуюся толщину стенки. Звуковые волны, отраженные от части хорошего материала, покажут, насколько сильно материал подвергся коррозии.
Измерение толщины стенки, отображаемое в диапазоне Portagauge®, представляет собой оставшуюся толщину стенки материала, находящегося в хорошем состоянии. Сравнивая толщину стенки, измеренную Portagauge®, с фактической толщиной стенки материала, когда он был в совершенно новом состоянии, оператор может определить серьезность коррозии.
В Portagauge® 3 используется технология одиночного эха, которая определяет количество времени, необходимое одиночному эху отраженного звука для прохождения через материал и обратно к датчику. Время, необходимое для прохождения через материал, а также скорость звука в материале позволяют устройству рассчитать толщину стенки.
В Portagauge® 4 и Portagauge® 5 используется технология мультиэхо, при которой передаваемый ультразвуковой импульс проходит как через покрытие, так и через металл и отражается от задней стенки. Отраженные звуковые волны отражаются внутри материала, и каждый раз только небольшая часть эха проходит обратно через покрытие. Время между небольшими эхо-сигналами дает синхронизацию эхо-сигналов внутри металла, которые относятся к толщине металла. Для каждого импульса, посылаемого в материал, проверяются как минимум три эхо-сигнала, чтобы их можно было квалифицировать как мультиэхо-технологию ультразвуковой толщинометрии.
Различные стандарты Классификационного общества требуют использования только ультразвуковых толщиномеров с несколькими эхосигналами для морской промышленности. Мы рекомендуем Portagauge® 5 для таких приложений. Примеры таких стандартов приведены ниже:
IACS: Особые требования процедурных требований IACS PR № 19 и № 77
DNVGL: DNVGL-CG-028 – Раздел 3 – Основные требования
5) Только несколько эхо-приборов могут использоваться для ТМ на борту всех судов
Серия ультразвуковых толщиномеров Portagauge® предназначена для измерения толщины стенок различных металлов и твердых пластиков. Технология мульти-эхо Portagauge® 4 и Portagauge® 5 предназначена для игнорирования лакокрасочного покрытия материала, что позволяет измерять истинную толщину материала. В результате линейка Portagauge® не подходит для использования в качестве измерителей глубины краски, толщиномера краски или тестера краски.
Ультразвуковой толщиномер — измерение толщины металла
Показаны 1-12 из 15
Страница
- Вы сейчас читаете страницу 1
- Страница 2
- Страница Следующий
Показывать
12 24 36
Сортировать по Должность наименование товара Цена Позиция
Установить нисходящее направление
Показаны 1-12 из 15
Страница
- Вы сейчас читаете страницу 1
- Страница 2
- Страница Следующий
Показывать
12 24 36
Сортировать по Должность наименование товара Цена Позиция
Установить нисходящее направление
Ультразвуковые толщиномеры, также известные как (NDT) Оборудование для неразрушающего контроля
Информация об ультразвуковых измерениях
измеряемый материал. Это достигается с использованием «связующей» жидкости, обычно называемой «связующей жидкостью». Эта жидкость служит для «связывания» или передачи ультразвуковых волн от преобразователя в материал и обратно. Перед проведением измерений на поверхность измеряемого материала следует нанести небольшое количество контактной жидкости. Как правило, достаточно одной капли контактного вещества.
При любом ультразвуковом измерении форма и шероховатость испытательной поверхности имеют первостепенное значение. Шероховатые, неровные поверхности могут ограничивать проникновение ультразвука через материал и приводить к нестабильным и, следовательно, ненадежным измерениям. Измеряемая поверхность должна быть чистой и не содержать мелких твердых частиц, ржавчины или окалины. Наличие таких препятствий будет препятствовать правильному прилеганию преобразователя к поверхности. Часто при очистке поверхностей помогают проволочная щетка или скребок. В более крайних случаях можно использовать роторные шлифовальные машины или шлифовальные круги, хотя необходимо соблюдать осторожность, чтобы предотвратить выемку поверхности, которая будет препятствовать правильному соединению преобразователя. Чрезвычайно шероховатые поверхности, такие как поверхность некоторых чугунов, напоминающая гальку, измерить труднее всего. Такие поверхности воздействуют на звуковой луч, как матовое стекло на свет, луч становится рассеянным и рассеивается во всех направлениях. Помимо создания препятствий для измерения, шероховатые поверхности способствуют чрезмерному износу датчика, особенно в ситуациях, когда датчик “скребет” по поверхности. Датчики следует регулярно осматривать на наличие признаков неравномерного износа рабочей поверхности. Если поверхность износа изнашивается с одной стороны больше, чем с другой, звуковой луч, проникающий в испытуемый материал, может больше не быть перпендикулярным поверхности материала. В этом случае будет сложно точно локализовать крошечные неровности в измеряемом материале, поскольку фокус звукового луча больше не находится непосредственно под преобразователем.
Несколько факторов влияют на силу распространения ультразвука. Они описаны ниже:
Сила исходного сигнала
Чем сильнее сигнал в начале, тем сильнее будет его эхо-сигнал. Начальная сила сигнала во многом зависит от размера ультразвукового излучателя в датчике. Большая излучающая площадь будет посылать больше энергии в измеряемый материал, чем малая излучающая площадь. Таким образом, так называемый «1/2-дюймовый» преобразователь будет излучать более сильный сигнал, чем «1/4-дюймовый» преобразователь.
Поглощение и рассеяние
Когда ультразвук проходит через любой материал, он частично поглощается. Если материал, через который он проходит, имеет зернистую структуру, звуковые волны также будут рассеиваться. Оба этих эффекта уменьшают силу волн и, следовательно, способность обнаруживать возвращающееся эхо. Ультразвук более высокой частоты поглощается и рассеивается больше, чем ультразвук более низкой частоты. Хотя может показаться, что использование более низкого
преобразователь частоты может быть лучше в каждом случае, низкие частоты менее направленны, чем высокие частоты. Таким образом, датчик с более высокой частотой будет лучшим выбором для обнаружения точного местоположения
небольших ямок или дефектов в измеряемом материале.
Геометрия преобразователя
Физические ограничения измерительной среды иногда определяют пригодность преобразователя для данной работы. Некоторые датчики могут быть просто слишком большими для использования в ограниченном пространстве. Кроме того, площадь поверхности, доступная для контакта с датчиком, может быть ограничена, что требует использования датчика с небольшой поверхностью износа. Измерение на криволинейной поверхности, такой как стенка цилиндра двигателя, может потребовать использования преобразователя с соответствующей изогнутой поверхностью износа.
Температура материала
При необходимости измерения на очень горячих поверхностях необходимо использовать высокотемпературные преобразователи. Эти датчики изготовлены с использованием специальных материалов и технологий, которые позволяют им выдерживать высокие температуры без повреждений. Кроме того, необходимо соблюдать осторожность при выполнении «обнуления зонда» или «калибровки по известной толщине» с высокотемпературным датчиком.
Толщиномер | Сосна экологическая
Сортировать по:
ПопулярныеЛучшие продажиПо алфавиту, A-ZПо алфавиту, Z-AЦена, от низкой к высокойЦена, от высокой к низкойДата, от старой к новойДата, от новой к старой
Оборудование, доступное как для аренды, так и для покупки
У нас есть усовершенствованные цифровые толщиномеры, сочетающие в себе мощные функции измерения со сложными возможностями сбора и вывода данных для приложений, включающих осмотр труб и резервуаров, а также других металлических конструкций, подверженных коррозии или эрозии, таких как котельные трубы, сосуды под давлением, паропроводы и приложения, требующие очень точных измерений толщины тонких или многослойных материалов с помощью одноэлементных преобразователей. Эти инструменты производятся такими производителями, как Danatronics, Olympus и GE.
Чтобы узнать больше, нажмите на продукт из списка.