Видео литье в землю: Литье алюминия в песчаные формы с подогревом смотреть онлайн видео от Folk Craft в хорошем качестве.
alexxlab | 15.08.2023 | 0 | Разное
Оборудование для песчано-глинистых смесей (ПГС)
Оборудование для песчано-глинистых смесей (ПГС) – УралИндуктор
Оборудование для
песчано-глинистых смесей
(ПГС)
Компания “УралИндуктор” предлагает весь спектр номенклатуры для процесса литья в песчано-глинистые смеси(ПГС).
Главным отличием нашей компании является собственный инженерный центр, который позволяет квалифицированно сопровождать поставку оборудования на всех этапах, от проектирования до ввода в эксплуатацию.
Описание
Литье в песчано-глинистые формы (литье в землю) – технология получения отливок литьем в «отпечатки», оставленные моделями в формовочной смеси. Изготовление «сырых» песчано-глинистых форм (ПГC) является самым распространенным процессом изготовления разовых песчаных форм в мире, составляет от 60 до 90% от общего объёма производства литых заготовок. Процесс изготовления таких форм характеризуется, прежде всего, высокими объемами производства, низкими производственными затратами, а также легкостью в управлении процессом. Так как снижение цен и в дальнейшем будет оставаться важной тенденцией в литейной промышленности процесс изготовления сырых песчаных форм и далее останется основным в области литейного производства.
В настоящее время литейные предприятия используют различные варианты технических решений формовочных машин и способов уплотнения на ПГС. Выбор оборудования зависит от вида отливок, объемов производства, экологических норм и т.д.
ТЕХНОЛОГИЯ ЛИТЬЯ В ПЕСЧАНО-ГЛИНИСТЫЕ ФОРМЫ
• Изготовление модельного комплекта из дерева, стали и т.д., в зависимости от серийности отливки.
• Изготовление сухой формовочной смеси из песка (преимущественно кварцевого) и связующего (глины).
• Изготовление стержней, литниковой системы.
• Размещение модельного полукомплекта на подмодельных плитах в опоках, засыпка формовочной смеси.
• Увлажнение смеси в полуформе, уплотнение ручным или механическим способом.
• Проставка стержней, установка второй опоки, установка второго полумодельного комплекта, литниковой системы.
• Засыпка и уплотнение формовочной смеси.
• Удаление модельного комплекта, сушка и сборка готовых полуформ.
Преимущества
• Низкая себестоимость производства. Материалы и оборудование для стержней и форм имеют сравнительно невысокую стоимость. А трудозатраты на эксплуатацию этих агрегатов и установок невелики.
• Универсальность процесса, т.е. возможность получать отливки из любых сплавов, любых размеров и массы, любой геометрической сложности в условиях индивидуального, серийного или массового производства.
• Возможность механизации (литейные конвейеры) и полной автоматизации процесса (автоматические литейные линии).
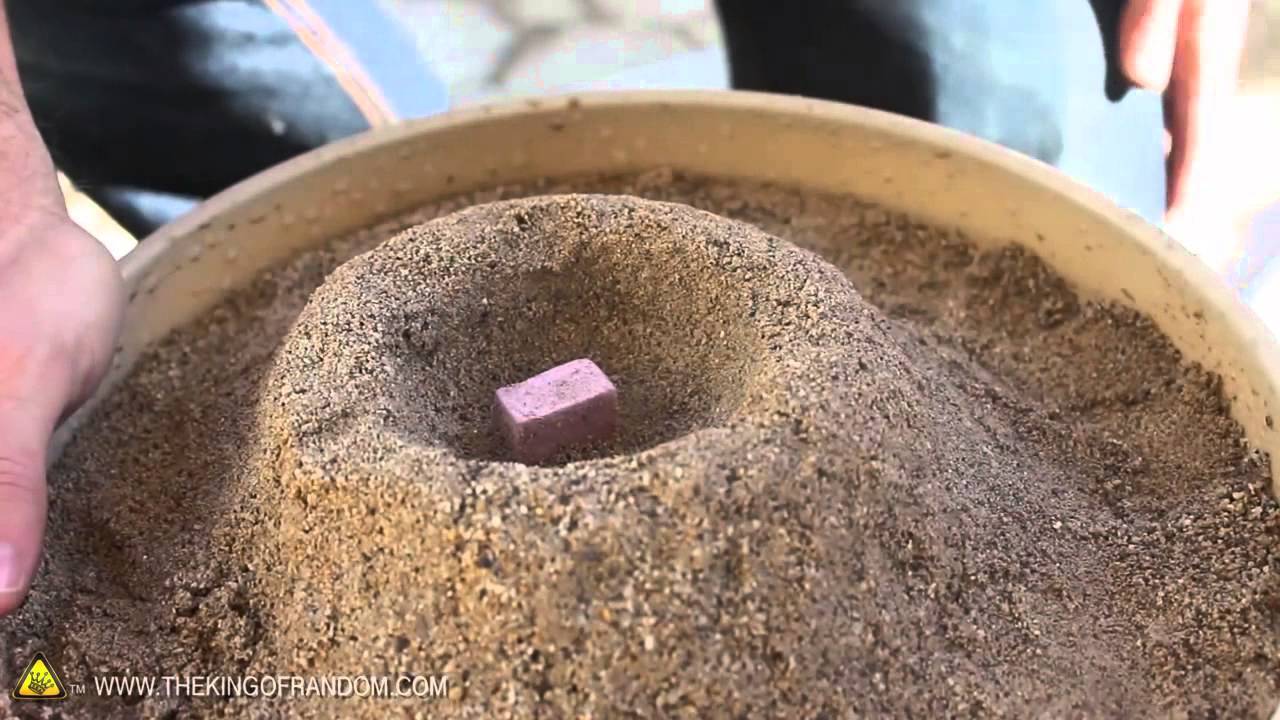
• Простой и доступный производственный процесс. В отличие от изготовления песчано-смоляных смесей ненужно рассчитывать сложную процедуру отверждения состава.
Смеситель литейный чашечный (бегуны)
Область применения: изготовление формовочной и стержневой смеси в литейном производстве. Основные элементы оборудования: вертикальные катки, скребки (отвалы), электропривод, выпускной люк с пневмоприводом.
Приготовление смеси:
– включить привод вращения катков (скребков)
– загрузить сухие компоненты смеси – (в процессе перемешивания катки уплотняют смесь, а скребки (отвалы) разрыхляют её; время перемешивания 1-2 минуты)
– после образования однородной массы добавить жидкие компоненты (процесс перемешивания продолжать в течение 5-10 минут)
– после достижения необходимых свойств выпустить готовую смесь через выпускной люк.
Время перемешивания зависит от типа смеси и требуемых свойств.
Технические характеристики
Модель | Ø чаши, мм | Замес мах, кг | Производительность, т/ч | Скорость вращения, об/мин | Мощность, кВт |
---|---|---|---|---|---|
УИ-СБ 1110 | 1000 | 110 | 1.5-2 | 44 | 4 |
УИ-СБ 1110А | 1220 | 130 | 2-4 | 27 | 4 |
УИ-СБ 1114 | 1820 | 500 | 5-6 | 25 | 15 |
* – для прокрутки таблицы, нажмите пальцем и ведите вправо.
В представленной таблице указаны технические характеристики для базовых моделей. Наша компания спроектирует и изготовит оборудование согласно вашему ТЗ.
Смеситель вихревой
Область применения: изготовление формовочной и стержневой смеси в литейном производстве
Основные элементы оборудования: активатор со сменными ножами из износостойкого материала, вихревые головки со сменными лопатками из износостойкого материала, электроприводы активатора и вихревых головок, выпускной люк с пневмоприводом.
Приготовление смеси: – включить привод вращения активатора – загрузить сухие компоненты смеси – (в процессе вращения активатора компоненты смеси начинают образовывать однородную массу; время перемешивания 1-2 минуты) – после образования однородной массы включить приводы вихревых головок и добавить жидкие компоненты (процесс перемешивания продолжать в течение 3-6 минут) – после достижения необходимых свойств выпустить готовую смесь через выпускной люк. Время перемешивания зависит от типа смеси и требуемых свойств.
Преимущества: – меньше длительность перемешивания – более равномерное распределение компонентов по всему объему смеси – лучшая текучесть и формуемость смеси в процессе изготовления форм – минимальные затраты времени на замену быстро изнашиваемых деталей
Технические характеристики
Характеристика | УИ-СВ 160-22 | УИ-СВ 190-37 | УИ-СВ 190-45 | УИ-СВ 190-55 |
---|---|---|---|---|
Производительность, т/ч | 12 | 15 | 20 | 25 |
Мощность, квт/ч | 33 | 59.![]() |
89.55 | 99.55 |
Замес мах, кг | 500-600 | 600 | 800 | 1250 |
Мощность двигателя, кВт | 22 | 37 | 45 | 55 |
Количество роторов, шт | 1 или 2 | 1 или 2 | 2 | 2 |
Мощность привода ротора, кВт | 11 или 2х22 | 22 или 2х22 | 2х22 | 2х22 |
Скорость вращения шпинделя, об/мин | 34,2 | 34,2 | 34,2 | 34,2 |
Диаметр диска, | 1600 | 1950 | 1950 | 1950 |
* – для прокрутки таблицы, нажмите пальцем и ведите вправо.
В представленной таблице указаны технические характеристики для базовых моделей.
Наша компания спроектирует и изготовит оборудование согласно вашему ТЗ.
Формовочные машины для песчано-глинистых смесей серии УИФ-14
Описание
Формовочные машины для песчано-глинистых смесей серии УИФ-14 предназначены для работы в литейном производстве с использованием песчано-глинистых смесей. Установки производят уплотнение смеси в небольших полуопоках. Уплотнение смеси происходит с помощью микровстряски, и не требует предварительного ручного уплотнения смеси. Процесс формовки происходит в несколько этапов, отдельно формуется верхняя и нижняя полуопоки, затем полуопоки переворачиваются (вручную, или с помощью переворотной установки) и стыкуются.
Основные части
Станина. Станина, стальная, с верхним поворотным рычагом (траверсой), а также посадочными местами для приводов и вспомогательного оборудования.
Система выемки. Состоит из двух пар цилиндров, шатуна, вала синхронизации, кронштейна и толкателя. Система для удобной и аккуратной выемки выталкивает готовую полуопоку одновременно с четырех углов.
Технические характеристики
Наименование | УИФ-143 | УИФ-144 | УИФ-145 | УИФ-146 | УИФ-148 | УИФ-148М | |||
---|---|---|---|---|---|---|---|---|---|
Максимальный размер опоки, мм | 500x400x160 | 500x400x180 | 500×400×200 | 600x500x200 | 800x630x320 | 800х700х320 | |||
Размер рабочего стола, Д/Ш мм | 560×420 | 560×465 | 600×460 | 700×555 | 900х730 | ||||
Рабочее давление воздуха, MPа | 0.![]() |
||||||||
Сила сжатия, кгс | 4200 | 6300 | 6800 | 12700 | 16900 | ||||
Сила встряски, кгс | 800 | 750 | 750 | 1000 | 2700 | 4200 | |||
Ход поршня сжатия, мм | 100 | 120 | 200 | 160 | 180 | ||||
Ход штока верхней плиты, мм | 150 | 160 | 200 | 350 | |||||
Расстояние между верхней и нижней плитой, мм | 200-370 | 300-400 | 350-450 | 500-680 | |||||
Габаритные размеры, Д/Ш/В мм | 1000х600х1350 | 900x600x1400 | 900x600x1400 | 1100x700x1600 | 1339x1038x2200 | 1152x1162x2292 |
* – для прокрутки таблицы, нажмите пальцем и ведите вправо.
Мультиконтактная формовочная машина для песчано-глинистых смесей серии УИФ-0806
Описание
Мультиконтактная формовочная машина для песчано-глинистых смесей серии УИФ-0806 предназначена для работы в литейном производстве с использованием песчано-глинистых смесей. Установка предназначена для уплотнение смеси в небольших полуопоках. Уплотнение смеси происходит с помощью микровстряски, и не требует предварительного ручного уплотнения смеси.
Процесс формовки происходит в несколько этапов, отдельно формуется верхняя и нижняя полуопоки, затем полуопоки переворачиваются (вручную, или с помощью переворотной установки) и стыкуются.
Данная установка предназначена как для отдельного использования, так и для эксплуатации в автоматических или полуавтоматических линиях.
В данной серии верхняя уплотнительная плита наборная, и состоит из 48 независимых плит с отдельными пневматическими цилиндрами, что позволяет использовать различные размеры опок без дополнительной подстройки оборудования.
Формовочная машина не требовательна к месту установки.
Основные части
Станина. Стальная рама с верхним поворотным рычагом (траверсой), а также посадочными местами для приводов и вспомогательного оборудования. Система выемки. Состоит из двух пар цилиндров, шатуна, вала синхронизации, кронштейна и толкателя. Система для удобной и аккуратной выемки выталкивает готовую полуопоку одновременно с четырех углов. Система уплотнения.В данном механизме используется пружинная система с пневматическим приводом с регулируемой силой сжатия, для обеспечения наилучшего результата под различные требования. Пневмосистема. Предназначена для предварительной фильтрации и дегидрации подключаемого сжатого воздуха для обеспечения нужного качества воздуха для механизма уплотнения.
Технические характеристики
Наименование | УИФ-0806 |
---|---|
Максимальный размер опоки, мм | 800x630x300 |
Размер рабочего стола, Д/Ш мм | 950×370 |
Ход верхней плиты, мм | 200 |
Сила уплотнения, 4 кг/см2 | 4 |
Максимальная нагрезка на рабочий стол, кг | 650 |
Ход поршня сжатия, мм | 300 |
Потребление воздуха, м3 | 2.![]() |
Габаритные размеры, ДхШхВ мм | 2175x1600x2380 |
Вес установки, т | 5 |
* – для прокрутки таблицы, нажмите пальцем и ведите вправо.
Стержневая машина по горячей оснастке серии УИФ-86
Описание
Установка предназначена для создания форм из горяче-твердеющих смесей на основе смол. Отвердение смесей происходит с помощью нагрева формующей оснастки, и выдержкой модели в нагретом состоянии. Готовые модели используются как составная часть для литья в песчано-глинистые смеси (ПГС), горяче-твердеющие смеси (ГТС) и т.п. Данная серия может быть модифицирована под необходимые требования производства.
Основные функции установки
Механизм разделения оснастки: вертикальный Способ подачи смеси: автоматический Способы выбора и контроля температуры нагрева: автоматический/ручной Встроенный датчик контроля температуры: да Способ установки пресс-форм: крайние половины пресс-форм подвижные, центральные фиксированные Способ нагрева: электрический (возможен вариант исполнения газового нагрева)
Технические характеристики
Наименование | УИФ-8612 |
---|---|
Максимальный размер формы (ДхШхВ мм) | 540x400x300 |
Максимальный вес форм (кг) | 12×2 |
Габариты установки (Д/Ш/В мм) | 2800x1600x2760 |
Общая мощность установки (кВт) | 35 |
Мощность нагрева (кВт) | 18 |
* – для прокрутки таблицы, нажмите пальцем и ведите вправо.
Видео работы установки
Полигональное сито
Область применения: подготовка отработанной песчано-глинистой формовочной смеси в литейном производстве (просеивание, удаление пыли и инородных включений) Основные элементы оборудования: приемный желоб с вибратором для предотвращения зависания смеси, барабан полигональный конический, электропривод барабана, корпус сита.
Принцип работы:
Отработанная формовочная смесь посредством ленточного транспортера подается на приемный желоб сита и далее в барабан. Выбранная частота вращения барабана обеспечивает за счет центробежной силы и силы трения подъем смеси на гранях барабана и соскальзывание ее вниз. Во время соскальзывания и перекатывания слоев смеси происходит частичное измельчение комьев и просеивание. Благодаря конической форме барабана не просеявшиеся комья смеси, а также инородные включения (остатки стержней) продвигаются вдоль оси барабана к противоположному его торцу и там выпадают отдельно от просеянной смеси в тару с отходам. Основная масса смеси просыпается сквозь сетчатые стенки барабана вниз на ленточный транспортер или в тару (размер ячеек сетки выбирается в соответствие с требованиями заказчика). В верхней части корпуса сита имеется отверстие с фланцем для присоединения вытяжной установки. При прохождении смеси через сито кроме измельчения и очистки происходит также удаление пыли и частичное охлаждение за счет испарения влаги. На боковой части корпуса сита сделаны люки для обслуживания барабана (очистка от налипания).
Технические характеристики
Тип | УИ-П310 | УИ-П4313 | УИ-П4315 |
---|---|---|---|
Продуктивность Т | 14-25 | 40-70 | 70-100 |
* – для прокрутки таблицы, нажмите пальцем и ведите вправо.
В представленной таблице указаны технические характеристики для базовых моделей.
Наша компания спроектирует и изготовит оборудование согласно вашему ТЗ.
Воздушный охладитель
Область применения: подготовка отработанной песчано-глинистой формовочной смеси в литейном производстве (охлаждение и удаление пыли) Основные элементы оборудования: приемное отверстие, установка подачи воздуха (воздуходувка), полотно для просеивания и перемещения смеси, вибродвигатели, форсунки для распыления воды, инфракрасный пирометр, разгрузочное отверстие.
Принцип работы: Горячая отработанная смесь, поступающая в охладитель, за счет вдуваемого воздуха находится во взвешенном состоянии (в «кипящем» слое), увлажняется через форсунки водой и охлаждается за счет скрытой теплоты парообразования. Охлажденная смесь движется по полотну посредством вибродвигателей к разгрузочному отверстию. Температура смеси в охладителе контролируется инфракрасным пирометром. Для удаления пыли в верхней части корпуса охладителя предусмотрены отверстия для подключения систем пылеулавливания.
Технические характеристики
Наименование | Производительность, т |
---|---|
УИВО-8607 | 15-20 |
УИВО-8610 | 20-30 |
УИВО-8614 | 30-50 |
УИВО-8618 | 50-80 |
УИВО-8623 | 80-120 |
* – для прокрутки таблицы, нажмите пальцем и ведите вправо.
В представленной таблице указаны технические характеристики для базовых моделей. Наша компания спроектирует и изготовит оборудование согласно вашему ТЗ.
УСТАНОВКА ДРОБЛЕНИЯ КОМЬЕВ
Предназначена для дробления и измельчения комьев песка после произведения отливки. Установка представляет собой ленту, с установленными на ней износостойкими пластинами для дробления комьев, приводным механизмом с электромотором. Для удобства эксплуатации, установка размещается около места выбивки изделий из форм.
Ленточный Магнитный сепаратор
Область применения: подготовка отработанной песчано-глинистой формовочной смеси в литейном производстве (отделение инородных металлических частиц) Основные элементы оборудования: приводной и натяжной барабаны, транспортерная лента, электромагнит, электропривод.
Принцип работы:
Сепаратор устанавливается над ленточным транспортером между выбивной решеткой и полигональным ситом; направление движения ленты сепаратора перпендикулярно направлению движения транспортера; под действием магнита металлические включения вытягиваются из смеси и «прилипают» к ленте сепаратора; лента сепаратора перемещает «прилипшие» частицы за пределы действия магнита, где происходит их отделение от ленты в тару с отходами.
Технические характеристики
Модель | Ширина ленты, мм | Производительность, м3/ч | Скорость ленты, м/с | Толщина слоя смеси, мм | Магнитное поле, Гс |
---|---|---|---|---|---|
УИ-ЛМ954 | 400 | 35 | 0.64 | 1.1*2 | ≥2500 |
УИ-ЛМ955 | 500 | 50 | 0.64 | 2.2*2 | ≥2500 |
УИ-ЛМ957 | 650 | 70 | 0.64 | 3.7*2 | ≥2500 |
УИ-ЛМ958 | 800 | 90 | 0.85 | 5.5*2 | ≥2500 |
УИ-ЛМ9510 | 1000 | 120 | 0.85 | 1.5*2 | ≥2500 |
УИ-ЛМ9512 | 1200 | 150 | 1.06 | 11 | ≥2500 |
* – для прокрутки таблицы, нажмите пальцем и ведите вправо.
В представленной таблице указаны технические характеристики для базовых моделей. Наша компания спроектирует и изготовит оборудование согласно вашему ТЗ.
При обращении в компанию «УралИндуктор» вы гарантированно получаете:
Кратчайшие сроки поставки
Консультацию инженерного центра
Качественное обслуживание
Помощь в подборе оборудования
Квалифицированную техническую поддержку
Большой ассортимент оборудования в наличии
Остались вопросы?
Оставьте заявку и мы перезвоним© 2014-2023
— ООО «МТПК» Производство оборудования для металлургии
Основные виды литья для изготовления отливок armtorg.ru
Основные виды литья для изготовления отливокЛитьё в песчаные формы
Литьё в песчаные формы — дешёвый, самый грубый, но самый массовый (до 75-80 % по массе получаемых в мире отливок) вид литья. Вначале изготовляется литейная модель (ранее — деревянная, в настоящее время часто используются пластиковые модели, полученные методами быстрого прототипирования), копирующая будущую деталь. Модель засыпается песком или формовочной смесью (обычно песок и связующее), заполняющей пространство между ею и двумя открытыми ящиками (опоками). Отверстия в детали образуются с помощью размещённых в форме литейных песчаных стержней, копирующих форму будущего отверстия. Насыпанная в опоки смесь уплотняется встряхиванием, прессованием или же затвердевает в термическом шкафу (сушильной печи). Образовавшиеся полости заливаются расплавом металла через специальные отверстия — литники. После остывания форму разбивают и извлекают отливку. После чего отделяют литниковую систему (обычно это обрубка), удаляют облой и проводят термообработку.
Новым направлением технологии литья в песчаные формы является применение вакуумируемых форм из сухого песка без связующего. Для получения отливки данным методом могут применяться различные формовочные материалы, например песчано-глинистая смесь или песок в смеси со смолой и т. д. Для формирования формы используют опоку (металлический короб без дна и крышки). Опока имеет две полуформы, то есть состоит из двух коробов. Плоскость соприкосновения двух полуформ — поверхность разъёма. В полуформу засыпают формовочную смесь и утрамбовывают её. На поверхности разъёма делают отпечаток промодели (промодель соответствует форме отливки). Также выполняют вторую полуформу. Соединяют две полуформы по поверхности разъёма и производят заливку металла.
Литьё в кокиль
Литьё металлов в кокиль — более качественный способ. Изготавливается кокиль — разборная форма (чаще всего металлическая), в которую производится литьё. После застывания и охлаждения, кокиль раскрывается и из него извлекается изделие. Затем кокиль можно повторно использовать для отливки такой же детали.
Литьё в кокиль, кокильное литьё, способ получения фасонных отливок в металлических формах — кокилях. В отличие от других способов литья в металлические формы (литьё под давлением, центробежное литьё и др. ), при литьё в кокиль заполнение формы жидким сплавом и его затвердевание происходят без какого-либо внешнего воздействия на жидкий металл, а лишь под действием силы тяжести. Основные операции и процессы: очистка кокиля от старой облицовки, прогрев его до 200—300°С, покрытие рабочей полости новым слоем облицовки, простановка стержней, закрывание частей кокиля, заливка металла, охлаждение и удаление полученной отливки. Процесс кристаллизации сплава при литье в кокиль ускоряется, что способствует получению отливок с плотным и мелкозернистым строением, а следовательно, с хорошей герметичностью и высокими физико-механическими свойствами. Однако отливки из чугуна из-за образующихся на поверхности карбидов требуют последующего отжига. При многократном использовании кокиль коробится и размеры отливок в направлениях, перпендикулярных плоскости разъёма, увеличиваются.
В кокилях получают отливки из чугуна, стали, алюминиевых, магниевых и др. сплавов. Особенно эффективно применение кокильного литья при изготовлении отливок из алюминиевых и магниевых сплавов. Эти сплавы имеют относительно невысокую температуру плавления, поэтому один кокиль можно использовать до 10000 раз (с простановкой металлических стержней). До 45 % всех отливок из этих сплавов получают в кокилях. При литье в кокиль расширяется диапазон скоростей охлаждения сплавов и образования различных структур. Сталь имеет относительно высокую температуру плавления, стойкость кокилей при получении стальных отливок резко снижается, большинство поверхностей образуют стержни, поэтому метод кокильного литья для стали находит меньшее применение, чем для цветных сплавов. Данный метод широко применяется при серийном и крупносерийном производстве.
Литьё под давлением
ЛПД занимает одно из ведущих мест в литейном производстве. Производство отливок из алюминиевых сплавов в различных странах составляет 30—50 % общего выпуска (по массе) продукции ЛПД. Следующую по количеству и разнообразию номенклатуры группу отливок представляют отливки из цинковых сплавов. Магниевые сплавы для литья под давлением применяют реже, что объясняется их склонностью к образованию горячих трещин и более сложными технологическими условиями изготовления отливок. Получение отливок из медных сплавов ограничено низкой стойкостью пресс-форм.
Номенклатура выпускаемых отечественной промышленностью отливок очень разнообразна. Этим способом изготовляют литые заготовки самой различной конфигурации массой от нескольких граммов до нескольких десятков килограммов. Выделяются следующие положительные стороны процесса ЛПД:
- Высокая производительность и автоматизация производства, наряду с низкой трудоёмкостью на изготовление одной отливки, делает процесс ЛПД наиболее оптимальным в условия массового и крупносерийного производств.
- Минимальные припуски на мехобработку или не требующие оной, минимальная шероховатость необрабатываемых поверхностей и точность размеров, позволяющая добиваться допусков до ±0,075 мм на сторону.
- Чёткость получаемого рельефа, позволяющая получать отливки с минимальной толщиной стенки до 0,6 мм, а также литые резьбовые профили.
- Чистота поверхности на необрабатываемых поверхностях, позволяет придать отливке товарный эстетический вид.
Также выделяют следующие негативное влияние особенностей ЛПД, приводящие к потере герметичности отливок и невозможности их дальнейшей термообработки:
- Воздушная пористость, причиной образования которой являются воздух и газы от выгорающей смазки, захваченные потоком металла при заполнении формы. Что вызвано неоптимальными режимами заполнения, а также низкой газопроницаемостью формы.
- Усадочные пороки, проявляющиеся из-за высокой теплопроводности форм наряду с затрудненными условиями питания в процессе затвердевания.
- Неметаллические и газовые включения, появляющиеся из-за нетщательной очистки сплава в раздаточной печи, а также выделяющиеся из твёрдого раствора.
Задавшись целью получения отливки заданной конфигурации, необходимо чётко определить её назначение: будут ли к ней предъявляться высокие требования по прочности, герметичности или же её использование ограничится декоративной областью. От правильного сочетания технологических режимов ЛПД, зависит качество изделий, а также затраты на их производство. Соблюдение условий технологичности литых деталей, подразумевает такое их конструктивное оформление, которое, не снижая основных требований к конструкции, способствует получению заданных физико-механических свойств, размерной точности и шероховатости поверхности при минимальной трудоёмкости изготовления и ограниченном использовании дефицитных материалов. Всегда необходимо учитывать, что качество отливок, получаемых ЛПД, зависит от большого числа переменных технологических факторов, связь между которыми установить чрезвычайно сложно из-за быстроты заполнения формы.
Основные параметры, влияющие на процесс заполнения и формирования отливки, следующие:
- давление на металл во время заполнения и подпрессовки;
- скорость прессования;
- конструкция литниково-вентиляционной системы;
- температура заливаемого сплава и формы;
- режимы смазки и вакуумирования.
Сочетанием и варьированием этих основных параметров, добиваются снижения негативных влияний особенностей процесса ЛПД. Исторически выделяются следующие традиционные конструкторско-технологические решения по снижению брака:
- регулирование температуры заливаемого сплава и формы;
- повышение давление на металл во время заполнения и подпрессовки;
- рафинирование и очистка сплава;
- вакуумирование;
- конструирование литниково-вентиляционной системы;
Также, существует ряд нетрадиционных решений, направленных на устранение негативного влияние особенностей ЛПД:
- заполнение формы и камеры активными газами;
- использование двойного хода запирающего механизма;
- использование двойного поршня особой конструкции;
- установка заменяемой диафрагмы;
- проточка для отвода воздуха в камере прессования;
Литьё по выплавляемой модели
Ещё один способ литья металлов — по выплавляемой модели — применяется в случаях изготовления деталей высокой точности (например лопатки турбин и т. п.) Из легкоплавкого материала: парафин, стеарин и др. , (в простейшем случае — из воска) изготавливается точная модель изделия и литниковая система. Наиболее широкое применение нашёл модельный состав П50С50 состоящий из 50 % стеарина и 50 % парафина, для крупногобаритных изделий применяются солевые составы менее склонные к короблению. Затем модель окунается в жидкую суспензию на основе связующего и огнеупорного наполнителя. В качестве связующего применяют гидролизованный этилсиликат марок ЭТС 32 и ЭТС 40, гидролиз ведут в растворе кислоты, воды и растворителя (спирт, ацетон). В настоящее время в ЛВМ нашли применения кремнезоли не нуждающиеся в гидролизе в цеховых условиях и являющиеся экологически безопасными. В качестве огнеупорного наполнителя применяют: электрокорунд, дистенсилиманит, кварц и т. д. На модельный блок (модель и ЛПС) наносят суспензию и производят обсыпку, так наносят от 6 до 10 слоёв. С каждым последующим слоем фракция зерна обсыпки меняются для формирования плотной поверхности оболочковой формы. Сушка каждого слоя занимает не менее получаса, для ускорения процесса используют специальные сушильные шкафы, в которые закачивается аммиачный газ.
Из сформировавшейся оболочки выплавляют модельный состав: в воде, в модельном составе, выжиганием, паром высокого давления. После сушки и вытопки блок прокаливают при температуре примерно 1000 для удаления из оболочковой формы веществ способных к газообразованию. После чего оболочки поступают на заливку. Перед заливкой блоки нагревают в печах до 1000. Нагретый блок устанавливают в печь и разогретый металл заливают в оболочку. Залитый блок охлаждают в термостате или на воздухе. Когда блок полностью охладится его отправляют на выбивку. Ударами молота по литниковой чаше производится отбивка керамики, далее отрезка ЛПС.Таким образом получаем отливку.
В силу большого расхода металла и дороговизны процесса ЛВМ применяют только для ответственных деталей.
Процесс литья по выплавляемым моделям базируется на следующем основном принципе:
• Копия или модель конечного изделия изготавливаются из легкоплавкого материала.
• Эта модель окружается керамической массой, которая затвердевает и образует форму.
• При последующем нагревании (прокалке) формы модель отливки расплавляется и удаляется.
• Затем в оставшуюся на месте удалённого воска полость заливается металл, который точно воспроизводит исходную модель отливки.
Литьё по газифицируемым (выжигаемым) моделям
Литьё по газифицируемым моделям (ЛГМ) из пенопласта по качеству фасонных отливок, экономичности, экологичности и высокой культуре производства наиболее выгодно. Мировая практика свидетельствует о постоянном росте производства отливок этим способом, которое в 2007 году превысило 1,5 млн т/год, особенно популярна она в США и Китае (в одной КНР работает более 1,5 тыс. таких участков), где всё больше льют отливок без ограничений по форме и размерам. В песчаной форме модель из пенопласта при заливке замещается расплавленным металлом, так получается высокоточная отливка. Чаще всего форма из сухого песка вакуумируется на уровне 50 кПа, но также применяют формовку в наливные и легкоуплотняемые песчаные смеси со связующим. Область применения ЛГМ — отливки массой 0,1—2000 кг и более, тенденция расширения применения в серийном и массовом производстве отливок с габаритными размерами 40—1000 мм, в частности, в двигателестроении для литья блоков и головок блоков цилиндров и др.
На 1 тонну годного литья расходуется 4 вида модельно-формовочных (неметаллических) материалов:
- кварцевого песка — 50 кг,
- противопригарного покрытия — 25 кг,
- пенополистирола — 6 кг,
- плёнки полиэтиленовой — 10 кв.м.
Отсутствие традиционных форм и стержней исключает применение формовочных и стержневых смесей, формовка состоит из засыпки модели песком с повторным его использованием на 95-97 %.
Центробежное литье и центробежный метод литья
Центробежный метод литья (центробежное литьё) используется при получении отливок, имеющих форму тел вращения. Подобные отливки отливаются из чугуна, стали, бронзы и алюминия. При этом расплав заливают в металлическую форму, вращающуюся со скоростью 3000 об/мин.
Под действием центробежной силы расплав распределяется по внутренней поверхности формы и, кристаллизуясь, образует отливку. Центробежным способом можно получить двухслойные заготовки, что достигается поочерёдной заливкой в форму различных сплавов. Кристаллизация расплава в металлической форме под действием центробежной силы обеспечивает получение плотных отливок.
При этом, как правило, в отливках не бывает газовых раковин и шлаковых включений. Особыми преимуществами центробежного литья является получение внутренних полостей без применения стержней и большая экономия сплава в виду отсутствия литниковой системы. Выход годных отливок повышается до 95 %.
В нашем производстве используют машины с горизонтальными осями вращения. Широким спросом пользуются отливки втулок, гильз и других заготовок, имеющих форму тела вращения, произведенные с помощью метода центробежного литья. Что такое центробежное литьё?
Центробежное литье — это способ получения отливок в металлических формах. При центробежном литье расплавленный металл, подвергаясь действию центробежных сил, отбрасывается к стенкам формы и затвердевает. Таким образом получается отливка. Этот способ литья широко используется в промышленности, особенно для получения пустотелых отливок (со свободной поверхностью).
Технология центробежного литья обеспечивает целый ряд преимуществ, зачастую недостижимых при других способах, к примеру:
- Высокая износостойкость.
- Высокая плотность металла.
- Отсутствие раковин.
- В продукции центробежного литья отсутствуют неметаллические включения и шлак.
Центробежным литьём получают литые заготовки, имеющие форму тел вращения:
- втулки;
- венцы червячных колёс;
- барабаны для бумагоделательных машин;
- роторы электродвигателей.
Наибольшее применение центробежное литьё находит при изготовлении втулок из медных сплавов, преимущественно оловянных бронз.
По сравнению с литьём в неподвижные формы центробежное литьё имеет ряд преимуществ: повышаются заполняемость форм, плотность и механические свойства отливок, выход годного. Однако для его организации необходимо специальное оборудование; недостатки, присущие этому способу литья: неточность размеров свободных поверхностей отливок, повышенная склонность к ликвации компонентов сплава, повышенные требования к прочности литейных форм.
Литьё в оболочковые формы
Литьё в оболочковые формы — способ получения фасонных отливок из металлических сплавов в формах, состоящих из смеси песчаных зёрен (обычно кварцевых) и синтетического порошка (обычно фенолоформальдегидной смолы и пульвер-бакелита). Предпочтительно применение плакированных песчаных зёрен (покрытых слоем синтетической смолы).
Оболочковую форму получают одним из двух методов. Смесь насыпают на металлическую модель, нагретую до 300°С, выдерживают в течение нескольких десятков секунд до образования тонкого упрочнённого слоя, избыток смеси удаляют. При использовании плакированной смеси её вдувают в зазор между нагретой моделью и наружной контурной плитой. В обоих случаях необходимо доупрочнение оболочки в печи (при температуре до 400°С) на модели. Полученные оболочковые полуформы скрепляют, и в них заливают жидкий сплав. Во избежание деформации форм под действием заливаемого сплава перед заливкой их помещают в металлический кожух, а пространство между его стенками и формой заполняют металлической дробью, наличие которой воздействует также на температурный режим охлаждающейся отливки.
Этим способом изготавливают различные отливки массой до 25 кг. Преимуществами способа являются значительные повышение производительности по сравнению с изготовлением отливок литьём в песчаные формы, управление тепловым режимом охлаждения отливки и возможность механизировать процесс.
Поделиться
Casting Crowns – Официальный сайт
Музыка
Новый альбом уже доступенВидео
Иисус на расстоянии (официальное музыкальное видео) No Hurt (официальное музыкальное видео) Crazy People (официальное лирик-видео) Шрамы на небесах (официальное видео) Пустынная дорога (официальное аудио) Все, кроме легкого (официальное аудио) Сумасшедшие (Официальное аудио) 2-е мнение (официальное аудио) Целитель (лирическое видео) Сила Креста (лирическое видео) Никто (Официальное музыкальное видео) при участии Мэтью Уэста Start Right Here (версия HGA) [Official Lyric Video] ft.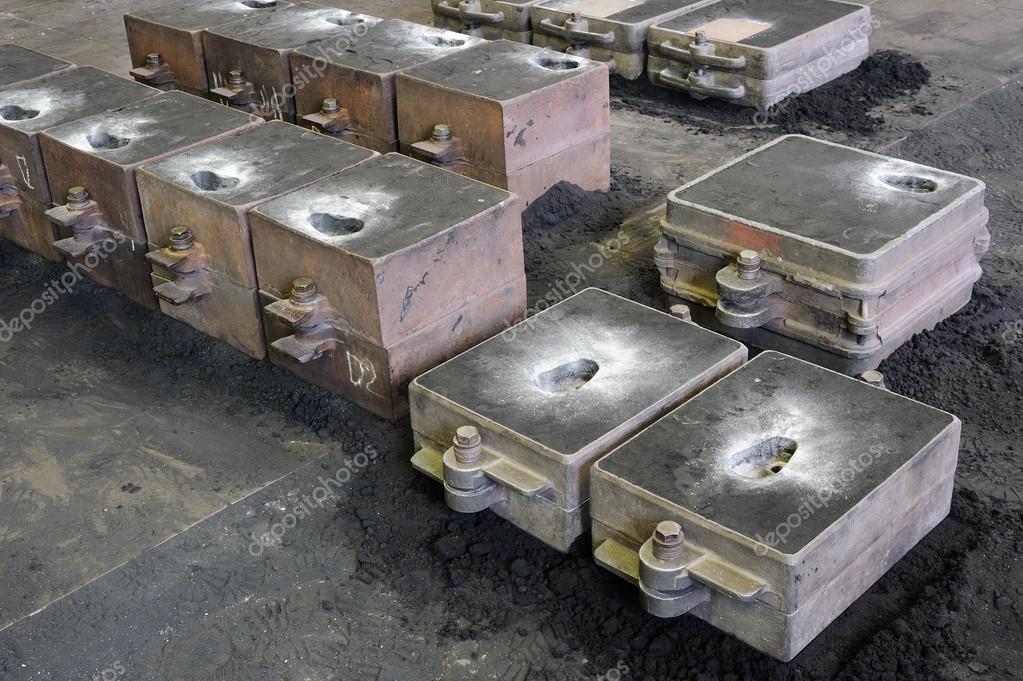
Кастинг талантов. Секреты успешного производства коммерческого или вещательного видео
Перейти к содержимому- Посмотреть увеличенное изображение
Каждый бренд хочет снять успешный рекламный ролик или видеоматериал. Привлечение талантов из авторитетного агентства по поиску талантов или компании по управлению талантами может сделать или разрушить ваше коммерческое видеопроизводство.
Актеры читают свои сценарии на сцене в театре Сегодняшние успешные маркетинговые усилия компании часто основываются на прочной базе интернет-маркетинга. В наш цифровой век цифровое видео двигает вперед иглу, когда дело доходит до взаимодействия с клиентами. Поэтому вполне естественно создавать корпоративные и коммерческие видеоролики, которые помогут рассказать историю вашего бренда. Вы можете сделать это разными способами. Самый популярный, хотя и самый дорогой, — это нанять группу обученных профессионалов, которые расскажут историю вашего бренда. Союз коммерческих актеров может стоить постановку от 1000 до более 100 000 долларов (за штуку) в зависимости от типа снимаемой рекламы. Один из самых известных вопросов: «Сколько нужно снять рекламный ролик?» И правда в том, что это зависит. Подробнее о стоимости рекламы читайте в этой статье. Короче говоря, чем крупнее покупка рекламы, тем больше вы должны платить талантам… за профсоюзную рекламу. Как вы понимаете, итоговый результат быстро увеличивается.
Если у вас недостаточно денег, чтобы платить обученным актерам, вы всегда можете привлечь генерального директора компании или сотрудников, чтобы записать более «приземленную» и полезную историю. Сегодня, особенно в социальных сетях, потребители любят ассоциировать людей с брендами. Они покупаются на вашу историю, и как только они связываются с вами, они связываются с тем, что вы продаете.
Преимущества найма профессиональных актеров
Самое большое преимущество найма обученного актера заключается в том, что вы можете гарантировать, что талант будет спокойным, уверенным и донесет сообщение вашего бренда таким образом, чтобы он был узнаваем и хорошо принят. Если вы или ваша команда раньше не снимались с камеры, может быть неприятно, когда все источники света и камеры направлены на вас. Обученные специалисты смогут донести ваше сообщение и внести коррективы по ходу дела.
Существуют также профессиональные реплики, которые актер узнает и поймет на съемочной площадке. Актеры знают свою цель, актеры знают, как найти свет, актеры знают, как представить себя и манипулировать тональностью голоса и языком тела, зрительным контактом и темпом. Обученные таланты знают, как дышать и доставлять.
Где найти профессиональных актеров
В каждом крупном городе есть агентства по работе с талантами и компании по управлению талантами.
Лучший способ найти надежных поставщиков — обратиться в местный офис SAG или просто воспользоваться поиском в Google. Посмотрите отзывы о каждой компании. Если у какой-либо компании отзыв ниже 4.0, я бы посоветовал не связываться с ними. Если у вас ограниченный бюджет и вы не можете нанять профессионала с представительством, Google — отличный ресурс.