Виды дефектов металла: Производственные дефекты металла, металлопроката. Виды
alexxlab | 08.03.2023 | 0 | Разное
Фотоальбом дефектов основного металла
В фотоальбоме дефектов металла представлено более 200 фотографий и схематических изображений дефектов поверхности металла, выявляемых при визуальном и измерительном контроле. Помимо фотографий каждый дефект имеет определение из нормативной документации. Название каждого дефекта продублировано на английском, немецком и французском языках. В конце альбома содержится список рекомендуемой литературы и средств для проведения визуального контроля.
Материал альбома основан на следующих документах:
- ГОСТ 21014-88 «Прокат чёрных металлов. Термины и определения дефектов поверхности»;
- ГОСТ 19200-80 «Отливки из чугуна и стали. Термины и определения дефектов»;
- РД 03-606-03 «Инструкция по визуальному и измерительному контролю».
Фотоальбом дефектов металла может быть использован при подготовке и аттестации сварщиков и дефектоскопистов по визуально-измерительному контролю, а также представляет интерес для научных работников по направлению металлургия.
Содержание фотоальбома дефектов металла
Дефекты по ГОСТ 19200-80:
1. Дефекты несоответствия по геометрии отливки:
- Недолив
- Неслитина
- Обжим
- Подутость
- Перекос
- Стержневой перекос
- Разностенность
- Стержневой залив
- Коробление
- Незалив
- Вылом
- Зарез
- Прорыв металла
- Уход металла
2. Дефекты поверхности отливки:
- Пригар
- Спай
- Ужимина
- Нарост
- Залив
- Засор
- Плена
- Просечка
- Поверхностное повреждение
- Складчатость
- Газовая шероховатость
- Грубая поверхность
3. Дефекты несплошности в теле отливки:
- Горячая трещина
- Холодная трещина
- Межкристалическая трещина
- Газовая раковина
- Ситовидная раковина
- Усадочная раковина
- Песчаная раковина
- Шлаковая раковина
- Залитый шлак
- Графитовая пористость
- Усадочная пористость
- Газовая пористость
- Рыхлота
- Вскип
- Утяжина
4. Дефекты включений:
- Металлические включения
- Неметаллические включения
- Королек
5. Дефекты несоответствия по структуре:
- Отбел
- Половинчатость
- Ликвация
- Флокен
Видео презентация фотоальбома Дефекты основного металла
Дефекты по ГОСТ 21014-88:
1. Дефекты поверхности, обусловленные качеством слитка и литой заготовки:
- Раскатанное (раскованное) загрязнение
- Волосовина
- Раскатанный (раскованный) пузырь
- Пузырь-вздутие
- Расслоение
- Слиточная рванина
- Слиточная плена
- Раскатанный пригар
- Раскатанная (раскованная) трещина
2. Дефекты поверхности, образовавшиеся в процессе деформации:
- Деформационная рванина
- Рванина на кромках
- Затянутая кромка
- Заков
- Прокатная плена
- Трещина напряжения
- Скворечник
- Ус
- Подрез
- Порез
- Морщины
- Закат
- Риска
- Сквозные разрывы
- Надрывы
- Продир
- Наколы-проколы
- Раскатанные отпечатки
- Отпечатки
- Чешуйчатость
- Вкатанная окалина
- Рябизна
- Раковины от окалины
- Вкатанные металлические частицы
- Раковина-вдав
- Отстающая окалина
- Вкатанные инородные частицы
- Заплески
- Серые пятна
- Пятна загрязнения
- Пятна слипания сварки
- Заусенец
- Зазубрины
- Торцевая трещина
- Полосы-линии скольжения
- Полосы нагартовки
- Цвета побежалости
3. Дефекты поверхности, образовавшиеся при отделочных операциях:
- Травильные трещины
- Налет шлама
- Недотрав
- Перетрав
- Остатки окалины
- Оттенки травления
- Пятна ржавчины
- Вмятины
- Царапины
- Шлифовочные трещины
- Матовая поверхность
Смотрите так же разделы – Шаблоны сварщика, Комплекты для визуального контроля, Образцы для аттестации по визуальному контролю, Аттестация специалистов по ВИК, Аттестация лабораторий по визуальному методу.
Фотоальбом с различными видами поверхностных дефектов основного металла можно купить с доставкой до двери или до терминалов транспортной компании в следующих городах: Москва, Санкт-Петербург, Екатеринбург, Саратов. Амурск, Ангарск, Архангельск, Астрахань, Барнаул, Белгород, Бийск, Брянск, Воронеж, Великий Новгород, Владивосток, Владикавказ, Владимир, Волгоград, Волгодонск, Вологда, Иваново, Ижевск, Йошкар-Ола, Казань, Калининград, Калуга, Кемерово, Киров, Кострома, Краснодар, Красноярск, Курск, Липецк, Магадан, Магнитогорск, Мурманск, Муром, Набережные Челны, Нальчик, Новокузнецк, Нарьян-Мар, Новороссийск, Новосибирск, Нефтекамск, Нефтеюганск, Новочеркасск, Нижнекамск, Норильск, Нижний Новгород, Обнинск, Омск, Орёл, Оренбург, Оха, Пенза, Пермь, Петрозаводск, Петропавловск-Камчатский, Псков, Ржев, Ростов, Рязань, Самара, Саранск, Смоленск, Сочи, Сыктывкар, Таганрог, Тамбов, Тверь, Тобольск, Тольятти, Томск, Тула, Тюмень, Ульяновск, Уфа, Ханты-Мансийск, Чебоксары, Челябинск, Череповец, Элиста, Ярославль и другие города, кроме того, в Республике Крым.
причина возникновения и методика поиска
Из этого материала вы узнаете:
- Какие бывают типы дефектов металлических изделий
- Как можно обнаружить дефекты металлических изделий
- Какие бывают дефекты металлических изделий при литье
- Какие дефекты вызывает пластическая деформация
Производство предметов из металла представляет собой сложный технологический цикл. Некоторые операции могут как исключаться из этой цепочки, так и проводиться повторно. В процессе обработки металл претерпевает изменения, на нем могут появляться изъяны. Далее вы узнаете, какие бывают дефекты металлических изделий, а также как их можно выявить.
Типы дефектов металлических изделий
Из-за дефектов ухудшаются физико-механические свойства металлов, такие как электропроводность, магнитная проницаемость, прочность, плотность, пластичность.
Еще более грубыми считаются микро- и макроскопические дефекты металлических изделий, предполагающие нарушение сплошности или однородности. Они появляются по двум причинам: из-за несовершенства используемой технологии и низкой технологичности многокомпонентных сплавов. Дело в том, что при работе с подобными сплавами необходимо особенно точно соблюдать режимы, установленные для всех этапов изготовления и обработки.
С точки зрения прикладного, технического понимания, дефектами называют отклонения от установленной нормы, при которых ухудшаются рабочие характеристики металла или металлического изделия, происходит снижение сортности или отбраковка продукции. Но нужно понимать, что не любой изъян металла распространяется на изделие.
Отклонения, признанные дефектами для изделий, эксплуатируемых в определенных условиях (допустим, при усталостном нагружении), могут не приниматься во внимание при других условиях работы (например, при статическом нагружении).
Литьевые дефекты металлических изделий
Сегодня в металлургии принято использовать несколько классификаций брака, получаемого при литье.
Дефекты делятся на типы по месту нахождения. Так, если брак выявлен внутри участка, его считают внутренним. Если же проблема проявилась при дальнейшей обработке, ее относят к внешнему браку.
С точки зрения внешнего проявления, выделяют такие основные виды дефектов отливок, как пригар, при котором слой формовочных материалов, спекшихся с металлом, крепко присоединился к поверхности заготовки, и приливы, которые представляют собой отклонение размеров отливок от проекта в большую сторону.
Приливы делят на:
- Заливы, которые образуются вдоль стыка частей формы. Причина их появления кроется в несоблюдении размеров моделей и плохом соединении элементов опок.
- Подутость (распор) – возникает из-за давления расплава на рыхлую смесь.
- Нарост, который появляется, когда поток расплава размывает форму при заливке.
- Просечки (гребешки, заусенцы), образующиеся при затекании расплава в повреждения формы или стержня.
Нередко дефекты при литье проявляются в виде пороков поверхности. Сюда относятся:
- Засоры. Массы зерен земли или шлаков. Эта проблема появляется из-за ошибок, допущенных при проектировании форм, непродуманного расположения литников, несоблюдения технологии складирования и перевозки.
- Ужимины – образуются при сырой формовке, когда слой земли разрывается в месте конденсации жидкости и расплав заполняет образовавшуюся пустоту.
- Спаи, или неслитины, возникают, когда происходит контакт между слоями охладившегося расплава. Поскольку не достигнута необходимая температура, потоки не могут правильно сплавиться.
- Плены – появляются, когда окисляются легирующие добавки.
- Морщинистость, или складчатость. Данный дефект выглядят как разнонаправленные складки на поверхности металлического изделия. Такой изъян связан со скоплением большого объема углерода в металле.
- Выпот – провоцирует взрывообразное выделение скоплений графита, поэтому он похож на множество лопнувших пузырьков.
- Корольки появляются и из-за разбрызгивания расплава при заливке. В этом случае шарик металла кристаллизуется отдельно от отливки, не соединяясь с ней.
- Коробление отливки возникает по причине внутренних напряжений, провоцируемых неравномерным остыванием.
Также среди распространенных пороков литья стоит назвать трещины. Подобные дефекты металлических изделий также делятся на виды:
- Горячие.
Возникают, когда металл достигает температуры кристаллизации, обычно вызваны усадочным напряжением. Имеют неровные формы.
- Холодные. Появляются при более низких температурах, чем горячие, при этом отличаются ровным, прямым профилем.
- Межкристаллические. Образуются на металлических изделиях из легированных сталей в тех зонах, где имеются неметаллические включения.
Помимо прочего, нередко на предметах из металла появляются газовые дефекты:
- Ситовидная пористость, то есть большое количество мелких пузырьков в теле детали.
- Газовые раковины, которые представляют собой крупные каверны, возникшие после выхода и объединения мелких пузырьков.
Пластические дефекты металлических изделий
При отбраковке заготовок достаточно часто приходится сталкиваться с включениями инородных металлических или неметаллических тел, причем последние бывают различной величины, формы.
Надрыв представляет собой местные несквозные разрывы, находящиеся поперек или под углом к направлению обработки материла. Такие дефекты образуются из-за раскрытия внутренних несплошностей материала, а также несоблюдения норм, установленных для процесса обработки.
Сквозной разрыв отличается от предыдущего вида тем, что на металлическом изделии наблюдаются сквозные несплошности. Они образовываются при деформации плоской заготовки, имеющей неравномерную толщину, либо причиной появления сквозного разрыва могут стать вкатанные инородные тела.
Накол выглядит как несквозные единичные или групповые точечные углубления. Они появляются при использовании загрязненных смазочно-охлаждающих жидкостей, попадании на заготовку мелких металлических и инородных элементов. Еще одной причиной для образования накола могут стать выступы и налипшие частицы на валках.
Рекомендуем статьи по металлообработке
- Марки сталей: классификация и расшифровка
- Марки алюминия и области их применения
- Дефекты металлический изделий: причины и методика поиска
Вмятинами называют отдельные единичные углубления различных размеров, форм, имеющие пологие края. Вмятины появляются из-за повреждения металла в процессе производства, перевозки, хранения.
Забоина представляет собой углубление неправильной формы. Обычно такой дефект имеет острые края, поскольку появляется при ударе металлического изделия.
Отпечаток – периодически повторяющиеся углубления, выступы, расположенные по всему металлическому изделию или на некоторых его участках. Отпечатки появляются под действием неровностей на прокатных и правильных валках.
Задир выглядит как широкое продольное углубление с неровным дном и краями. Причина его появления состоит в резком трении заготовки о детали оборудования, при помощи которого осуществляется обработка.
Риска – это продольное узкое углубление, дно которого может быть закругленным либо плоским. Образуется при царапании заготовки металлического изделия выступами на поверхности оборудования.
Царапина представляет собой углубление неправильной формы, имеющее произвольное направление. Появляется из-за механических повреждений, например, во время складирования, перевозки металлических изделий.
Потертостью называют нарушение блеска на отдельно взятом участке металлического изделия, а также скопление мелких разнонаправленных царапин. Такие дефекты появляются из-за трения металлических изделий между собой.
Налип появляется в результате прилипания к металлическому изделию частиц или слоя металла с инструмента.
Закат образуется за счет вдавливания в изделие частиц обрабатываемого металла, заусенцев, выступов и других дефектов, появившихся в процессе обработки.
Пережог проявляется в виде темных, оплавленных или окисленных пятен на металлическом изделии, которые образуются, если была превышена температура, время нагрева материала.
Расслоение выглядит как отделение слоя материала на торцах, кромках металлического изделия, заготовки. Причина для расслоения одна – изначально внутри металла были дефекты, такие как рыхлости, включения, внутренние разрывы, пережог.
Плена представляет собой расслоение, обычно имеет форму языка, идущего по направлению обработки и одним краем соединенного с основным металлом. Подобное расслоение появляется, если в металле изначально были надрывы, трещины, пузыри, либо при нагреве материала был допущен его пережог, оплавление.
Чешуйчатость представляет собой пластическую деформацию, вызванную пережогом или недостаточной пластичностью металла периферийной зоны. В соответствии с названием, такие разрывы на металлическом изделии больше всего похожи на чешую или сетку.
Рябизна выглядит как скопление углублений, появившихся на металлическом изделии во время проката или плавки.
Смятой поверхностью называют тип деформации, при котором на металлическом изделии появляются складки, изгибы, волны, при этом не вызывающие разрыва металла.
Излом представляет собой полосу поперек направления прокатки или под углом к нему. Изломы появляются из-за резкого перегиба в процессе сматывания, разматывания рулонов, либо при перекладке тонких листов.
Недотрав выглядит как пятна, полосы, появившиеся на металлическом изделии из-за неравномерного травления.
Перетрав – это местное или общее разъедание поверхности изделия, которое проявляется как точечные либо контурные углубления. Образуется, так же как и недотрав, при несоблюдении режима травления.
Пятна загрязнения могут иметь форму полос, натеков, разводов. Их оставляют на поверхности металлического изделия технологическая эмульсия, загрязненное масло, мазут.
Коррозионные пятна могут быть светлыми или темными, обычно имеют шероховатую текстуру, так как появляются под действием коррозии.
Цвета побежалости проявляются в виде окисленных участков, то есть пятен и полос различной окраски и формы. Такие пятна отличаются гладкой поверхностью, так как проявляются при нарушении норм термической обработки и травления.
Кольцеватость характерна только для круглых металлических заготовок – на их поверхности появляются повторяющиеся кольцеобразные выступы, углубления. Виной тому пластическая деформация, плавка.
Следы плавки несколько похожи на кольцеватость, они выглядят как повторяющиеся светлые и темные полосы. Однако в данном случае полосы идут по заготовке в любом направлении: могут быть продольными, поперечными либо спиралеобразными. Образуются при плавке.
Омеднение проявляется как покраснение некоторых участков поверхности металлического изделия. Такие пятна образуются после контактного выделения меди, что связано с нарушением режимов термической обработки и травления.
Серповидность полос и лент – это отклонение формы металлического изделия от поверочной линейки. Такой дефект измеряют в миллиметрах на метр длины полуфабриката.
Овальностью называют отклонение поперечного сечения изделия от формы круга. Если с – максимальный, d – минимальный и т – средний диаметр сечения, то по формуле c – d/m × 100 можно рассчитать отклонение от идеальной формы в процентах.
Разностенность – несовпадение толщины стенки по длине трубы с номинальной толщиной либо разница в толщине заготовки по ее площади.
Разнотолщинность – отклонение толщины плоского изделия по длине и ширине от установленных параметров либо разница толщины стенки вдоль длины металлической трубы.
Фестонистость представляет собой появление выступов по краю металлического изделия при глубокой штамповке листов и лент. Направление выступов соответствует направлению оси прокатки.
Способы обнаружения дефектов металлических изделий
Существует несколько уровней исследования, которые используются для разных глубин и размеров дефектов:
- Субмикроскопическое исследование.
- Микроанализ.
- Макроанализ.
Под дефектами кристаллического строения металлов принято понимать отклонения от структуры идеального, то есть бездефектного, кристалла.
Дефекты кристаллической структуры делят на типы в соответствии с их формой и размерами:
- Дислокации, то есть отсутствие полуплоскости кристаллической решетки.
- Вакансии или пустоты в узлах кристаллической решетки.
- Атомы внедрения, предполагающие присутствие в решетке дополнительных атомов между узлами.
- Атомы замещения, то есть атомы другого элемента, находящиеся в узлах кристаллической решетки обрабатываемого металла.
1. Субмикроскопическое исследование
Цель его состоит в выявлении дефектов на границах кристаллов или зерен. Дело в том, что из-за неравномерности кристаллизации или недостаточного питания зародышей жидким раствором появляются тонкие прослойки между блоками кристаллов. Либо причина может скрываться в выделении на поверхности кристаллов твердой фазы нерастворимых соединений и элементов. Так, фосфор и целый ряд тугоплавких металлов не способны образовывать соединения с железом в сталях, поэтому они откладываются на границах зерен.
В число субмикроскопических дефектов входят сколы в стали 38Х2МЮА. Причина их появления проста: во время легирования стали алюминием по границам зерен выделяются локальные плоскости, которые и становятся слабым местом металла во время дальнейшей обработки.
2. Микроанализ
При подобном исследовании для выявления дефектов используют микроскопы с увеличением более 100 крат. Именно микроанализ применяется чаще всего при поиске литейных дефектов. Этот метод позволяет определить балл зерна, наличие и количество включений неметаллической природы, меди, серы и фосфора, структуру металла.
От доли углерода и легирующих элементов, содержащихся в стали, зависит, какие твердые фазы выделятся при кристаллизации. Отметим, что данные стадии имеют различную прочность, твердость и пластичность. В стойких к коррозии марках стали при разных температурных режимах охлаждения формируются фазы аустенита, мартенсита или ледобурита.
Также к ключевым характеристикам, определяющим качество металла, относится балл зерна. Дело в том, что при снижении данного показателя повышается пластичность металла, но снижается его прочность. Однако легирование карбидообразователями или тугоплавкими материалами позволяет добиться упрочнения стали, сохраняя при этом ее изначальную пластичность.
Одним из главных направлений исследования микроанализа считается определение доли вредных примесей и неметаллических включений (в процентах). Чаще всего роль вредной примеси играют сера и фосфор, из-за которых сталь приобретает такие свойства, как красноломкость и хладноломкость.
Чтобы металл мог применяться для производства изделий, доля этих двух элементов должна укладываться в установленные нормы. Благодаря контролю неметаллических включений удается установить содержание в стали оксидов, сульфидов, нитридов и других соединений. Отметим, что такие примеси могут влиять на металл как положительным, так и отрицательным образом.
3. Макроанализ
Данный способ изучения представляет собой визуальное выявление дефектов металлических изделий, иными словами, с его помощью поверхность рассматривается при увеличении до 30 крат. Такое исследование позволяет обнаружить крупные дефекты поверхности или глубинных слоев металла. Нужно понимать, что макроскопические изъяны могут образовываться на любом этапе производства металлического изделия – от выплавки и до хранения. Чаще всего после выявления подобных деформаций металл забраковывают или возвращают на доработку.
Понимание их причин и средств устранения
Литье металлов – это сложный процесс, включающий приложение высокого давления к расплавленному металлу, что делает возможным несколько нежелательных явлений, которые могут поставить под угрозу качество конечной продукции. Это дефекты литья, и они вызывают серьезные опасения у производителей.
Дефекты, связанные с литьем, бывают разных видов. Каждый из них имеет свои особенности, причины и меры профилактики. Ключом к освоению литья является понимание различных сопутствующих дефектов и причин. Следовательно, вы можете активно избегать этих недостатков и поставлять клиентам высококачественные продукты.
Здесь мы рассмотрим основные дефекты, которые могут возникнуть во время различных типов процесса литья , включая конкретные примеры дефектов, которые могут появиться в ваших отливках. Вы также узнаете о различных причинах этих дефектов литья и способах устранения каждой из них.
Что такое Дефекты литья ? Дефекты литья — это дефекты или неровности, которые ставят под угрозу характеристики качества компонента. Существуют различные причины и источники дефектов литья, начиная от отказа материала и заканчивая литейным оборудованием или неоптимизированной процедурой.
Хотя с некоторыми из этих дефектов можно мириться или ими можно пренебречь, некоторые дефекты поверхности отливки приводят к слабому отливке, нестандартным формам и плохой функциональности. Следовательно, они должны быть удалены или предотвращены, чтобы обеспечить лучшее функционирование конечного продукта.
Существуют различные типы дефектов литья, но обычно они сгруппированы в четыре категории, а именно:
- Металлургические дефекты
- Дефекты, вызванные нагреванием
- Дефекты материала литейной формы
- Дефекты формы отливки
Давайте рассмотрим различные дефекты в каждой группе, их причины и способы устранения.
Металлургические дефектыЭти дефекты возникают в основном из-за проблем, связанных с металлическим материалом. Существует пять различных типов металлургических дефектов, в том числе:
1.
Дефекты пористости Это внутренние дефекты литья под давлением , которые обычно трудно обнаружить. Обычно вы найдете их там, где на металле есть небольшие отверстия, пустоты или воздушные карманы. Как правило, пористость возникает всякий раз, когда в процессе литья в металл попадает воздух. В результате этого в верхней части матрицы могут возникать зазоры, или форма может заполняться слишком медленно. Таким образом, полученный компонент может иметь ослабленную структурную прочность. Есть два основных дефекта пористости:
Когда отлитый металл затвердевает внутри формы, он не может удерживать столько газа, как когда он был в жидкой форме. Поэтому металл имеет тенденцию выделять газ. Неспособность газа пройти через форму легко приводит к захвату пузырьков внутри металла. Эти пузырьки выглядят как:
- Пинхолы. Это небольшие отверстия в верхней части литой детали. Обычно вы видите их (при визуальном осмотре) группами у поверхности отливки.
- Дыры. Это более крупные отверстия внутри литой заготовки.
В отличие от пинхолов, они не видны невооруженным глазом. Поэтому для их обнаружения вам понадобится рентгеновский, ультразвуковой, гармонический или магнитный анализ.
- Открытые отверстия. Это типы пузырей, которые появляются на поверхности заготовки. Они возникают из-за захвата воздуха при заливке металла в форму. Рубцы представляют собой неглубокие формы открытых отверстий.
Эти дефекты имеют круглую или овальную форму на поверхности отливок. Часто они имеют гладкую поверхность ярко-желтого или ярко-белого цвета. В результате вы можете выявить дефект газовой пористости в литье путем визуального осмотра после процесса литья. С другой стороны, вам нужен рентгеновский аппарат для проверки этого дефекта на необработанных поверхностях.
Причины- Газы, присутствующие в металлическом сплаве. Литье металлов включает заполнение штампов расплавленным металлическим сплавом при высоком давлении и скорости.
Следовательно, неспособность расплавленного сплава течь стабильно и упорядоченно может вызвать турбулентность с участием газов. Завихрения часто возникают из-за глухих зон в литниковой системе, неразумных параметров разливки, неправильной конструкции желобов. Таким образом, вы можете заметить некоторые дефекты пористости из-за этих турбулентностей.
- Выделенный водород из расплавленного сплава. Это одна из основных причин пористости литья. Влага из воздуха или плавильных инструментов может попасть в расплавленный металл или сплав стали , тем самым дополнительно разлагаясь на водород. При охлаждении и затвердевании отливки растворимость водорода снижается, что приводит к его выделению и образованию газовых пор.
- Газы от разделительных составов для форм. При контакте с расплавленным металлическим сплавом часто нагреваются смазки для форм. В результате они разлагаются и выделяют газ, который в конечном итоге вызывает дефекты пористости.
Аналогичным образом, использование слишком большого количества разделительных составов для форм может вызвать улетучивание газа.
- Убедитесь, что используются чистые и сухие слитки металлических сплавов для предотвращения образования водорода.
- Используйте подходящие параметры литья, включая скорость впрыска и давление.
- Контролируйте температуру плавки, чтобы предотвратить перегрев.
- Используйте литник и направляющую достаточной длины более 50 мм. Таким образом, вы обеспечите стабильный и адекватный поток газов.
- Смазка для форм должна быть самого высокого качества и в контролируемом количестве.
Усадочная пористость отличается от круглых, гладких поверхностей газовой пористостью; они встречаются в виде зазубренных угловатых краев. Металлы обычно дают усадку при охлаждении и затвердевании. Однако, если усадочная полость неровная, искажает форму детали или создает внутренние отверстия, она становится дефектом. Распространенными усадочными дефектами пористости являются:
- Открытые усадочные дефекты. Они возникают на поверхности отливки в виде углублений (выемки) или отверстий (труб). Воздух втягивается внутрь формы, когда металлический сплав сжимается неравномерно, что создает открытую усадку.
- Закрытые усадочные дефекты. Появляются в виде отверстий внутри отливки, где происходит неравномерный нагрев расплавленного металла. Они могут встречаться в микро- или макроформах. Макроусадки выглядят как зубчатые линии или метки и видны невооруженным глазом. С другой стороны, микроотверстия выглядят угловатыми и их можно увидеть в микроскоп.
- Деформация. Эта усадка происходит во время или после затвердевания металла, изменяя форму и размеры компонента. Они заставляют металл искривляться плоскими или большими участками.
- Высокая концентрация металла в определенных зонах формы.
- Слишком низкое давление впрыска.
- Плохая конструкция направляющей и литника.
- Неравномерный рисунок затвердевания металла.
- Разность температур в разных частях расплавленного металла.
- Чрезвычайно высокая температура заливки.
- Используйте простую геометрию отливки с улучшенной конструкцией рабочего колеса и литника.
- Обеспечьте оптимальное заполнение полостей, улучшив желоб с помощью программного обеспечения для моделирования.
- Увеличьте давление впрыска металла.
- Вставьте охлаждающие змеевики, ребра или внутренние охладители, чтобы обеспечить надлежащий отвод тепла.
- Очистите металлическую поверхность от загрязнений.
2.
Углубления Углубление – это воздействие прижима на поверхность отливки, которое не точно повторяет форму формы. Раковины появляются на поверхности отливки, когда имеется подповерхностная полость. Эти углубления возникают вдоль толстостенных участков на поверхности металла. Поскольку раковины отражают свет, вы можете легко определить эти дефекты поверхности отливки с помощью визуального осмотра.
- Неравномерная толщина стенок отливок часто приводит к неравномерной усадке при затвердевании.
- Частично перегретая форма вызывает медленное затвердевание отливки в этих перегретых областях.
- Недостаточная вентиляция полости матрицы, что приводит к сжатию газа между поверхностью жидкого металла и поверхностью полости.
- Низкое давление впрыска.
- Плохой эффект подачи из-за короткого времени удержания давления.
- Оптимизация конструкции отливки для обеспечения одинаковой толщины стенок.
- Улучшить вентиляцию полости штампа.
- Избегайте перегрева полости пресс-формы и дайте металлу больше времени выдерживать давление.
- Увеличьте давление впрыска металла.
3.
Шлаковые включенияШлаковые включения прочно прикрепляются к отливке, снижая механические характеристики конечного продукта. Обычно это происходит, когда неметаллические материалы образуют неравномерную корку на поверхности отливки. Дефект литья представляет собой лентовидный унос или карман с острыми краями и неправильной формой. Кроме того, другие формы включений включают песок, гвозди, грязь или оксиды. Хотя они имеют толщину всего несколько миллиметров, их можно увидеть невооруженным глазом.
Причины- Разлив и затвердевание жидкого металла, содержащего частицы шлака.
- Неправильная система литников.
- Образование нерастворимых интерметаллических соединений в процессе затвердевания; таким образом, вызывая их сегрегацию в остаточной жидкости.
- Добавление сплава, который не полностью растворился в расплаве.
- · Тщательная и регулярная очистка матрицы.
- Улучшить конструкцию системы ворот.
- Используйте чистый расплавленный металл.
- Нанесите небольшой кусочек сплава и наблюдайте за изменениями металлических сплавов.
4.
ОкалинаОкалина относится к потерям металла, возникающим при литье цветных металлов. Когда металл плавится, он окисляется, образуя слои примесей и накипи, которые всплывают на поверхность металла. Примеси возникают из-за смешения оксида основного металла и других металлов на поверхности.
Причины- · Термитная реакция.
- Слишком высокая температура металла.
- Образование оксидов в результате реакции, происходящей между воздухом в литейной форме и высокотемпературным жидким металлом.
- · Избегайте перемешивания, которое может привести к окислению и термитной реакции.
- Уменьшить температуру металла.
- Уменьшить время плавления.
5.
ПайкаПайка – распространенный дефект литья в процессе литья. Это происходит, когда расплавленный металл прилипает к поверхности полости формы и остается там после извлечения отливки. Следовательно, в некоторых областях отливок материала либо не хватает, либо избыток материала. Выявить пайку можно при визуальном осмотре.
Причины- Повреждения, недостаточная твердость или низкая шероховатость полости матрицы.
- Неправильный механизм выброса, вызывающий наклонный впрыск.
- Перегрев расплавленного металлического сплава или штампов.
- Использование антиадгезивов низкого качества.
- Недостаточное количество элемента железа в сплаве.
- Устраните любые повреждения полости штампа и улучшите ее шероховатость.
- Отрегулировать углы уклона и конструкцию ворот.
- Обеспечьте сбалансированный выброс за счет оптимизации механизма выброса.
- Мониторинг и контроль температуры штампа и расплавленного сплава
- Используйте высококачественные смазки для форм.
- Используйте соответствующий железный элемент с запасом от 0,8% до 1,1%.
Существует пять дефектов литья, вызванных нагреванием, в том числе горячие разрывы, закрытие в холодном состоянии и термическая усталость.
1.
Горячие разрывы Горячие разрывы являются одними из серьезных дефектов литья, возникающих из-за нагревания. Этот дефект возникает при затвердевании металлической отливки. На этой стадии в металле развиваются термические деформации растяжения и напряжения. Горячий разрыв возникает, когда металл сжимается при затвердевании. Обычно вы видите их в виде неправильных или линейных узоров на литых деталях.
- · Термическое сжатие на поверхности металла.
- Недостаточная температура заливки металла.
- Неправильный процесс затвердевания и размещение ворот.
- · Используйте хорошие галтели на стыках.
- Аккуратно поместите ворота рядом с матрицей.
- Использовать стандартные методы затвердевания.
- Обеспечьте равномерную толщину материала.
2.
Холодное закрытиеХолодное закрытие дефектов – это трещины с закругленными краями. Они возникают, когда металл поступает в форму более чем из одной точки. Однако металл слишком холодный и не может правильно слиться, чтобы сформировать идеальную деталь. Таким образом, возникает холодный затвор, так как трещины с закругленными краями, проходящие через середину заготовки, создают слабое место на отливке.
Причины- Неправильная конструкция литниковой системы.
- Низкие температуры жидкого металла.
- Снижение текучести расплавленного металла.
- Тонкие срезы отливки.
- Оптимизация литниковой системы для предотвращения узких поперечных путей и обеспечения надлежащего потока металла.
- Улучшение газопроницаемости формы.
- Увеличьте температуру заливки металла, чтобы предотвратить преждевременное затвердевание.
3.
Термическая усталость Этот дефект характерен для алюминиевого литья под давлением , так как штампы подвергаются высоким термическим нагрузкам. Термические напряжения возникают из-за температурных градиентов, возникающих при нагреве и охлаждении поверхности при впрыске, выбросе и распылении смазки. Поскольку штампы для литья под давлением подвержены высоким термическим и механическим нагрузкам, подвергание их повторяющимся циклам очень низких и высоких температур приведет к структурной слабости и трещинам внутри компонента.
- · Постоянное воздействие высокой температуры на штамп.
- Кромки и углы со слишком маленькими радиусами.
- Градиент температуры слишком близок к воротам.
- · Дайте углам и кромкам допустимые радиусы.
- Уменьшите градиент температуры вблизи ворот.
- Дайте матрице немного остыть.
Существует 7 типов дефектов литья, вызванных неподходящим материалом формы. Читай дальше.
1.
Порезы и промывки Это области избыточного металла, возникающие, когда расплавленный металл вымывает часть формовочной смеси. Когда это происходит, песку не хватает прочности, чтобы противостоять эрозии. Порезы и смывы проявляются в виде невысоких выпуклостей вдоль поверхности заготовки. Обычно они наклоняются к концу, где давление заливки жидкого металла больше.
- · Излишки металла в некоторых местах формы.
- Высокоскоростной поток расплавленного металла заставляет избыточный металл проходить через ворота.
- Обеспечьте правильную конструкцию литниковой системы.
- Повышение прочности стержня и формы.
- Добавьте больше вяжущих в основной песок.
2.
ПлавлениеПлавление — еще один дефект литья в песчаные формы, возникающий при сплавлении песчинок с текущим жидким металлом. Это приводит к тонкому слою твердой стекловидной корки, прочно прикрепленной к отливке. Основной причиной этого дефекта является низкая огнеупорность песка. Из-за низкой огнеупорности песка он не может противостоять высокой температуре жидкого металла. Таким образом, возникает дефект сплавления.
Причины- · Низкая огнеупорность песка или глины.
- Смешивание металла с песчинками.
- Слишком высокая температура заливки металла.
- · Повышение огнеупорности формовочных материалов.
- Снижение температуры заливки расплавленного металла.
3.
Выход из формыВыход из формы происходит, когда расплавленный металл вытекает из формы. В результате полость формы не будет заполнена полностью. Таким образом, вы, как правило, получаете отсутствующие или неполные отлитые компоненты. В большинстве случаев внешний вид гладкий, но иногда вы можете получить неравномерные и грубые биения.
Причины- Неисправная форма или машина для литья под давлением.
- Точное проектирование литейных форм.
- Перед литьем осмотреть формы и заменить неисправные.
- Используйте для изготовления пресс-форм высококачественное сырье, способное выдерживать высокие температуры.
4.
ВздутияМеталлостатические силы часто заставляют стенку пресс-формы двигаться назад, вызывая вздутие размеров заготовки. Это означает, что отливка будет увеличиваться сверх желаемого объема, проявляясь в виде небольших гладких выпуклостей. В результате возрастут требования к его подаче и обработке, что может привести к потерям металла.
Причины- Плесень низкой прочности.
- Неправильная трамбовка песчаной формы.
- Спроектируйте формы так, чтобы они выдерживали давление расплавленного металла и предотвращали движение стенки формы назад.
- Используйте более прочные, хорошо утрамбованные формы.
5.
Капли Эти дефекты возникают, когда отливка еще находится в расплавленном состоянии. Они возникают, когда кусочки рыхлого формовочного песка или комки падают с поверхности валика в полость формы. В результате на поверхности отливки возникает аномальный выступ неправильной формы. Капли также могут сделать металлическую поверхность грязной и непригодной для использования.
- · Низкая прочность песка.
- Недостаточное флюсование расплавленного металла.
- Мягкая трамбовка.
- Отсутствие усиления выступа песка в своде.
- Используйте более прочный песок.
- Удаление примесей расплавленного металла с помощью надлежащего флюсования.
- Обеспечьте более жесткую трамбовку.
- Укрепите выступы песка с помощью кляпов или гвоздей.
6.
Проникновение металла Это происходит в ситуациях, когда расплавленный металл проникает в отверстия или зазоры в формовочной смеси. Основная причина этого заключается в том, что размер зерна формовочной смеси слишком крупный, что препятствует надлежащему течению жидкого металла. Следовательно, вы получите шероховатую и неровную поверхность отливки, что снизит ее эстетичность. Вы можете легко увидеть последствия проникновения металла невооруженным глазом.
- Использование песка с высокой проницаемостью и низкой прочностью.
- Мягкая трамбовка песка.
- Использование крупнозернистого или крупного песка приводит к более сильному проникновению металла.
- Отсутствие смывки формы.
- Используйте мелкие, высокопрочные зерна.
- Обеспечивают жесткое трамбование и низкую проницаемость песка.
7.
Крысиные хвосты Крысиные хвосты выглядят как неровные трещины или линии на отливках. Эти дефекты возникают из-за нарушения сжатия на поверхности полости формы, когда расплавленный металл чрезмерно горячий. Расплавленный песок расширяется под воздействием тепла, что приводит к тому, что стенки формы сдвигаются назад и прогибаются. В процессе на поверхности отливки появится небольшая отметка. Если такой сбой происходит несколько раз во время процедуры литья, вы можете заметить небольшие перекрещивающиеся линии на поверхности компонента.
- · Плохая расширяемость песка.
- Неправильная конструкция пресс-формы.
- Чрезмерная температура заливки металла.
- Добавить горючие добавки в формовочную смесь.
- Уменьшить температуру заливки металла.
- Форма должна быть менее твердой, чтобы обеспечить адекватное расширение.
Неправильная форма отливки может вызвать два типа дефектов: несоответствие и заусенцы.
1.
Несоответствия Несоответствия – это дефекты литья, возникающие из-за несоосности нижней и верхней частей формы. Это может произойти, если перед заливкой металла перед заливкой металла не выровнены верхняя часть и сопротивление формы. Существует два типа несовпадений, а именно смещение формы и смещение стержня. Смещение пресс-формы является результатом смещения пресс-формы и часто проявляется как горизонтальное смещение. С другой стороны, смещение ядра происходит из-за смещения ядра и проявляется как вертикальное смещение.
- Ослаблены штифты коробки.
- Штифты неправильной формы.
- Неправильное размещение верхней и нижней частей пресс-формы приводит к смещению.
- Обеспечьте надлежащее выравнивание и монтаж стыковочных пластин.
- Используйте правильную формовочную коробку и закрывающие штифты.
2.
Заусенец Заусенцы – это любой избыточный или нежелательный материал , который возникает в виде тонких образований неправильной формы на линии разъема литой под давлением детали. Как правило, это тонкий лист металла, образующийся на стыках и превращающийся в окалина после переплавки. Так как вспышки часто имеют более крупные размеры, их можно увидеть при визуальном осмотре.
- Недостаточное усилие зажима.
- Недостаточная очистка поверхности разъема.
- Слишком высокая скорость впрыска и температура наполнения.
- Недостаточная прочность материала матрицы.
- Деформированные или изношенные шарниры литейной машины.
- Отрегулируйте параметры литья, такие как скорость впрыска, температура заполнения и усилие зажима.
- Обеспечить регулярное техническое обслуживание литейных машин.
- Очистите полость штампа и поверхность разъема.
Теперь вы уже понимаете различные дефекты литья и способы их предотвращения. Если у вас есть потребность в литье под давлением, лучше всего выбрать опытного поставщика услуг, тогда RapidDirect — ваш лучший выбор.
Наши специалисты имеют опыт и навыки в процессе литья, например, литье под давлением. Поэтому вы можете быть уверены, что мы предоставляем Услуги по литью под давлением , которые превзойдут ваши ожидания.
Попробуйте RapidDirect прямо сейчас!
Вся информация и загрузки защищены и конфиденциальны.
Мы гордимся материалами высшего качества, передовыми технологиями и опытными специалистами. Мы занимаемся всеми проектами, направленными на достижение результатов высшего качества. Наши всесторонние отзывы об анализе DFM помогут вам решить проблемы конструкции, которые могут вызвать дефекты литья под давлением. С RapidDirect вы можете быть уверены в строгих производственных процессах и проверках для обеспечения высокого качества отливок.
Заключение Процесс литья металла сложен и может привести к различным поверхностным дефектам. Лучшее понимание этих дефектов литья даст вам больше возможностей для контроля качества литья. Знание всего о дефектах литья и способах их устранения обеспечит превосходное качество вашего литья.
Хотя в некоторых ситуациях эти дефекты могут быть нормальными, опытные специалисты по литью под давлением могут помочь вам предотвратить или исправить их. Поэтому вы должны работать с партнером, который обеспечивает контроль качества. Свяжитесь с RapidDirect сегодня для вопросов и запросов по литью под давлением.
Как решить их в различных процессах обработки листового металла
- 1 июля 2022 г.
Изготовление листового металла — один из самых популярных процессов создания прототипов и производственных деталей. Это помогает создавать несколько долговечных деталей, начиная от прототипов небольшого объема и заканчивая деталями массового производства. Этот процесс часто используется в самых разных отраслях промышленности, включая автомобильную, аэрокосмическую и строительную.
Существует множество различных процессов обработки листового металла, но каждый из них может иметь свой уникальный набор дефектов. В этом сообщении блога мы рассмотрим некоторые из наиболее распространенных дефектов листового металла и их решения в различных процессах.
Что такое процессы изготовления листового металла?
Процессы изготовления листового металла — это процессы, которые изменяют первоначальную форму листа для получения вытянутой детали желаемой толщины. Их можно разделить на три основные категории:
Резка
Процессы резки листового металла можно дополнительно разделить на те, которые используют силы сдвига (например, резка, штамповка, вырубка), и те, которые не используют (например, резка лазерным лучом, плазменная резка, гидроабразивная резка).
Формовка
В процессе формовки металлический лист изгибается в желаемую форму. Методы формования включают воздушную гибку, чеканку и профилирование.
Соединение
Это процесс сборки различных компонентов из листового металла для получения желаемого продукта. К процессам соединения относятся сварка, пайка, заклепка, болтовое соединение, а наиболее распространенный метод – шовное соединение.
Как и в любом другом производственном процессе, в получаемых продуктах могут возникнуть некоторые дефекты, которые могут повлиять на их производительность, качество и характеристики. Вот некоторые распространенные дефекты в процессе изготовления листового металла и способы их устранения.
Резка/резка листового металла Дефекты и решения
Резка листового металла относится к приложению значительной силы к листу, что в конечном итоге приводит к его разрыву на части. Наиболее распространенным методом резки является резка, при которой применяется усилие сдвига, превышающее предел прочности материала на сдвиг, что приводит к его разрушению и отделению в этом месте.
Общие дефекты включают:
1.
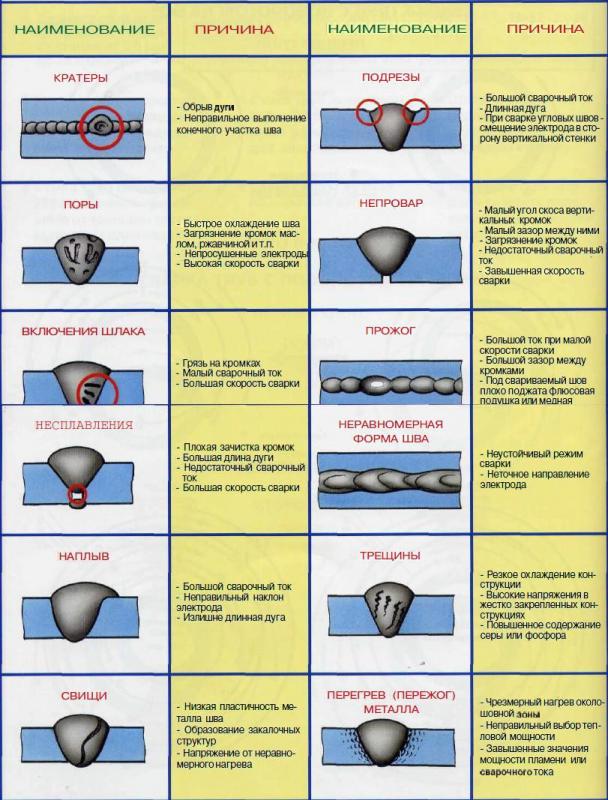
Заусенцы – это острые, неровные металлические детали, которые остаются прикрепленными к металлической заготовке. Обычно они возникают из-за затупления лезвий или их неправильного расположения. Слишком большой зазор между лезвиями приведет к их разрыву, а не к срезу, в то время как меньший зазор не позволит лезвиям прорезать материал, образуя заусенцы.
Аналогичным образом, деформированные кромки образуются из-за неправильного прижима зажима, а также из-за неправильного расположения лезвий.
Во избежание этого можно обратиться к руководству по эксплуатации ножниц, чтобы получить правильный зазор и давление зажима в зависимости от типа и толщины материала.
2. Скручивание
После завершения процесса резки металл мог испытывать некоторое скручивание вдоль своей оси. Это вызвано нарезкой слишком узких полос или использованием неправильного переднего угла. Этого можно избежать, регулируя передний угол в зависимости от свойств листового металла, геометрии и параметров резки.
3. Выпуклость
Выпуклость наблюдается, когда заготовка из листового металла имеет разную толщину по ширине. Это происходит, когда он движется в горизонтальном направлении, но не закручивается и не поднимается по краям. В результате получается металл вогнутой, выпуклой и треугольной формы. Этот дефект можно свести к минимуму на ранней стадии, изменив направление зерен металла и изменив передний угол.
4. Деформация
Деформация возникает, когда кромки слегка приподнимаются над плоскостью из-за неправильной обрезки. Это обычно наблюдается в длинных, узких, тонких листах. Чтобы преодолеть это, следует максимально уменьшить передний угол, а листовой металл должен удерживаться с помощью задней опоры.
Дефекты штамповки листового металла и решения
Процесс штамповки листового металла представляет собой производственный процесс холодной штамповки, при котором штамп используется на прессе для пробивки оттиска на металлической заготовке, что приводит к пластической деформации. Этот процесс также может сопровождаться другими формовочными инструментами для получения готовой детали или в качестве промежуточного этапа.
1. Трещины
Иногда, когда металлические слои выходят за пределы их работоспособности, они начинают утончаться, пока плоский слой не порвется в самом слабом месте. Такие дефекты известны как «утяжка» или «расщепление» в процессе штамповки листового металла.
Чтобы этого не произошло, перед началом операции следует использовать программное обеспечение моделирования формообразования для анализа листа. Кроме того, изучение настроек радиуса формы и глубины, типа и толщины материала, а также методов термообработки также может помочь избежать этих дефектов.
2. Морщины
Когда условия деформации сжатия, применяемые обрабатывающим оборудованием, толкают листовой металл на себя, линейная сила сдавливает внутрь, пока не образуется морщинистый фланец, и внутренняя геометрия не повреждается.
С такими дефектами можно бороться, растягивая или вытягивая листы, а не формируя их. Кроме того, если лист имеет сложный геометрический профиль, можно использовать валики для вытягивания, связующие для вытягивания и прокладки. Кроме того, натяжные валики помогают контролировать поток металла в полость штампа.
3. Пружинящий возврат
Когда радиус изгиба падает ниже установленного значения, заданного гибочным оборудованием, желаемая форма не достигается. Это известно как пружинение или окончательное отклонение детали из-за неправильного процесса.
Чтобы исправить эти дефекты, включите регулировку перегиба или сверхкомпенсации. Однако это не устраняет ошибку упругой деформации, увеличивая жесткость детали за счет положительного растяжения.
Дефекты гибки листового металла и решения
Гибка листового металла является важным процессом обработки листового металла благодаря возможности вычерчивания деталей различной геометрии без инструментов, а также быстрому выполнению, высокой повторяемости и автоматизации. Это также позволяет изготавливать изделия из одного куска металла с использованием пластической деформации, а не из нескольких частей, соединенных вместе с помощью сварки или клепки, что приводит к снижению затрат, повышению прочности и упрощению сборки.
1. Трещины в уголке изгиба
Две основные причины появления трещин в вытянутой детали: плохая податливость металла и очень малый радиус изгиба.
Чтобы избежать появления этих дефектов, используйте более мягкие металлы или увеличьте их пластичность путем нагревания и последующего медленного охлаждения.
2. Нестабильный угол изгиба
Основными причинами таких дефектов являются недостаточное давление материала и неравномерное давление изгиба, вызывающее неравномерную потерю устойчивости при сжатии. Этой проблеме также может способствовать асимметричное выпукло-вогнутое скругление штампа.
Чтобы решить эту проблему, увеличьте усилие домкрата и сбалансируйте зазор в выпукло-вогнутой галтели штампа.
3. Деформация отверстия
Расположение отверстия может быть деформировано из-за трения между вогнутой поверхностью штампа и внешней поверхностью в процессе гибки.
Такие дефекты можно устранить, увеличив давление пластины эжектора или добавив на эту пластину твердое пятно, чтобы увеличить трение между вышеупомянутыми поверхностями, чтобы они не скользили.
4. Неровное вогнутое дно детали
Такие дефекты обычно вызваны использованием выталкивающего устройства из-за недостаточного усилия или неровного материала.
Поэтому перед началом процесса гибки убедитесь, что выталкивающее устройство настроено на правильную меру усилия или вообще снято, а материал ровно выровнен.
5. Непараллельный изгиб к середине отверстий
Этот дефект вызван тем, что высота изгиба меньше минимального предела высоты изгиба, что приводит к расширению и искажению кривой.
Простое увеличение высоты гибочного элемента или материала устраняет эти типы дефектов.
Дефекты сварки листового металла и решения
Сварка обычно используется для соединения двух или более частей листового металла вместе. Будь то сварка MIG (дуговая сварка металлическим электродом в газе), сварка TIG (дуговая сварка вольфрамовым электродом в газе), дуговая сварка с защитным металлом (SMAW) или дуговая сварка порошковой проволокой (FCAW), при несоблюдении надлежащей технологии можно столкнуться с рядом дефектов.
Общие дефекты в процессе сварки листового металла включают:
1. Брызги
Брызги возникают, когда вблизи сварочной дуги образуются капли расплавленного материала. Обычно это вызвано большими токами, неправильной полярностью или недостаточной газовой защитой.
Во избежание этого уменьшите ток и длину дуги и увеличьте угол между горелкой и пластиной. Очистка газового сопла также может помочь.
2. Пористость
Эти дефекты возникают, когда водород, азот и кислород поглощаются расплавленной сварочной ванной. При затвердевании они захватываются сварным швом. Жир, влага, краска и ржавчина также могут вызвать пористость.
Чтобы предотвратить эту проблему, убедитесь, что края пластины чистые и сухие, используйте свежие сварочные материалы и проверьте сварочную горелку на наличие утечек.
3. Подрез
Подрез возникает при использовании высокого напряжения или большой длины дуги. Использование неправильного электрода или слишком большого по отношению к толщине электрода, а также высокая скорость перемещения резака также могут вызвать эту проблему.
Таких дефектов можно избежать, используя электрод подходящего размера, обеспечив медленное перемещение горелки и избегая удержания вблизи вертикальной пластины, если выполняется горизонтальный угловой шов.
4. Трещины
Трещины могут образовываться на сварном шве, когда внутренние напряжения превышают прочность сварного шва или основного металла (или того и другого). Они могут распространяться с течением времени, и поэтому должны быть устранены немедленно.
Этих дефектов можно избежать путем тщательной очистки, опиливания, шлифовки и снятия заусенцев с краев металлических пластин, чтобы они хорошо подходили друг к другу. Также помогает обеспечение правильной температуры при повторном нагреве обеих сторон соединения.
Другие распространенные дефекты поверхностей из листового металла
Помимо процессов формовки листового металла, в процессе производства могут возникать и другие распространенные дефекты.
Например, к числу наиболее распространенных относятся царапины на поверхности, загрязнения, вмятины и проколы. Кроме того, неравномерность может возникать из-за высоких растягивающих напряжений или коробления при сжатии в процессе изготовления листового металла.
Иногда устранение этих дефектов может быть затруднено и часто требует особого внимания во время процесса.
Беспокоитесь о дефектах листового металла? WayKen здесь для вас
В заключение, очевидно, что листовой металл играет жизненно важную роль в обрабатывающей промышленности из-за его способности подвергаться различным процессам. При работе с ним можно столкнуться с рядом дефектов, влияющих на его полезность. Благодаря этой статье, если вы, вероятно, обладаете базовыми знаниями о дефектах листового металла, теперь пусть профессиональная служба позаботится обо всем остальном!
В WayKen мы специализируемся на быстром прототипировании и различных процессах изготовления листового металла, включая резку, штамповку, гибку и сварку. Мы также предлагаем нашим клиентам первоклассную инженерную поддержку.