Виды обработки металла: Виды обработки металлов
alexxlab | 16.07.2020 | 0 | Разное
Виды обработки металлов
Металлообработка – это технологический процесс, при котором на металлы или сплавы оказывается физическое воздействие специальными инструментами. В итоге меняются геометрические параметры материалов или их физико-механические характеристики. Результатами металлообработки становятся детали, сборочные узлы и металлоконструкции для строительства, бытовой сферы и всевозможных отраслей промышленности.
Технологии металлообработки
Для придания материалам заданных размеров, форм и свойств используются разные виды металлообработки:
- Механическая обработка давлением или резанием – воздействие при помощи пресса или режущего инструмента.
- Литье – отлив деталей заданной формы из расплавленного материала.
- Сварка – соединение нескольких металлических элементов при помощи сварочной технологии.
- Термическая обработка – нагрев цветных металлов или стали, их выдержка при определенной температуре и охлаждение с целью изменения характеристик.
- Художественная обработка – ковка, художественное литье или чеканка. Создание металлоизделий с высокими декоративными качествами.
- Электрообработка, пример – прокалка. Подразумевает прохождение через металл электрического разряда. Различают электроискровую и электрохимическую обработку, которая делает поверхность блестящей.
- Резка – разделение заготовок на составляющие определенных размеров и формы. К категории металлорежущего оборудования относятся лазерная резка, газокислородные и плазменные установки, буровые прессы и гильотины, сверлильные и гидроабразивные, расточные и отрезные, токарные и фрезеровочные станки. На современных производствах доминирует бесконтактная тепловая резка.
В зависимости от поставленных задач разные способы обработки металлов применяются самостоятельно или сочетаются друг с другом.
Виды механической обработки металлов
Мехобработка – это
воздействие на заготовку фрезой, сверлом, резцом или другим инструментом для придания ей заданных размеров.
- Операции резания – снятие с заготовки припусков материала с помощью режущего инструмента металлообрабатывающего станка. Тип механической обработки металлических изделий зависит от особенностей обрабатываемой поверхности, заданного класса точности, размеров детали и значений шероховатости. По технологии резания обрабатывается сортовой прокат черных и цветных металлов.
- Воздействие давлением или ударом, в результате которого заготовка подвергается пластической деформации и приобретает нужную форму с сохранением целостности. Часто перед воздействием давлением материал нагревается для снижения прочности и твердости. Металлообработка давлением используется для улучшения структуры и физико-механических характеристик материала, уменьшения его усадочной пористости и химической неоднородности, повышения прочности и эластичности. Это в нашем случае гибка металла или штамповка металла.
Методы мехобработки резанием
Метод |
Особенности |
Используемое оборудование |
Точение, токарные работы |
Закрепленная в шпинделе заготовка вращается с определенной скоростью, а установленный в суппорте резец выполняет продольно-поперечные движения. Так обрабатываются тела вращения в форме конуса или цилиндра, спиральные и винтовые поверхности. Кроме строгания (срезания стружки), к токарным работам относятся торцевание, отрезание, снятие фасок, выполнение канавок и обработка галтелей. |
Станки токарной группы. |
Сверление |
Выполнение в заготовках глухих или сквозных отверстий заданного диаметра и глубины, в т. ч. многогранных отверстий. Для сверления различных металлоизделий используются сверла из быстрорежущих сталей, сверла с твердыми сплавами, боразоном, алмазом. |
Станки сверлильной группы. |
Зенкерование |
Вид получистовой обработки материалов, при котором цилиндрические и конические отверстия в деталях доводятся до нужных размеров, гладкости и класса точности. Выполняется при помощи цельных или насадных зенкеров – многолезвийных инструментов с осью вращения. |
Сверлильные и токарные станки. Реже – расточные, фрезерные и агрегатные. |
Шлифование |
Технология чистовой и отделочной металлообработки, при которой с поверхности деталей снимается тонкий слой материала. В результате изделия доводятся до нужных размеров и заданного уровня шероховатости. |
Шлифовальные станки с абразивными кругами разной зернистости, для цветных металлов – алмазные инструменты. |
Фрезерование |
Бывает фасонным, концевым, периферийным и торцевым. |
Фрезерные станки с разнообразными фрезами. |
Зубофрезерование, зубонарезные работы |
Тип лезвийной металлообработки, в результате которого с высокой точностью, отличным качеством поверхности, одинаковым шагом и глубиной резьбы нарезаются зубчатые колеса эвольвентного профиля. Так производятся червячные колеса, всевозможные детали с прямыми и косыми зубьями, цилиндрические колеса внешнего зацепления. |
Зубофрезерные станки с червячными модульными фрезами. |
Долбление |
Вид металлообработки, близкий к строганию. |
Вертикально-долбежные станки, строгальные, универсально-фрезерные, вертикально-фрезерные с долбежными головками. |
Способы мехобработки давлением
Метод |
Особенности |
Используемое оборудование |
Прокатка |
Используется для производства листового металлопроката и трубопроката, валов, втулок, осей, гильз, профилей. Бывает продольной, поперечной и поперечно-винтовой. |
Прокатный стан с вращающимися валками. |
Штамповка – объемная и листовая |
Изменение формы и размеров заготовки под давлением штампа. |
Штамповочный пресс. Гидравлический или кривошипно-шатунный пресс. Для резки – гильотинные ножницы, вибрационные и дисковые станки. |
Прессование |
Выдавливание холодного или нагретого металла на оборудовании со сменной матрицей. Материал под давлением пресс-штемпеля выдавливается через отверстие в матрице, приобретает необходимую форму, плотность и характеристики. |
|
Волочение |
Создание изделий с заданной формой поперечного сечения. |
Волочильные станы. |
Ковка |
Подразумевает нагрев определенных участков заготовки и их механическую деформацию. Нагретый металлический прут деформируется и приобретает необходимую форму. В результате получаются уникальные изделия с высокими эстетическими качествами. |
При ручном методе – молот, на современных производствах – пресс. |
Технология литья
Эта технология обработки металлов и сплавов используется для получения изделий из чугуна, стали, сплавов на основе меди, магния, цинка и алюминия. При литье расплавленный металл заливается в литейные формы и застывает, превращаясь в отливки
заданных размеров и форм. Есть несколько технологий литья, включая методы с дополнительным использованием давления. Новые технологии литья позволяют создавать отливки миниатюрных размеров с превосходной точностью.
Сварка
Сварка металлических элементов – это технология их прочного соединения в единую конструкцию. Все способы сварки делятся на 2 группы:
- Сварка плавлением – электрическая (дуговая или контактная), с использованием электродуговых аппаратов с электродами или полуавтоматов с присадочной проволокой.
В месте соединения детали разогреваются до температуры плавления материалов, их жидкие фазы смешиваются и после остывания создают прочный сварной шов. Для защиты области сваривания от окисления используются электроды со специальной обсыпкой, сварка с подачей инертного газа и сварка под флюсом. Этот гранулированный порошок при нагреве расплавляется и защищает область сваривания образовавшейся пленкой. После процесса обработки металла оставшийся шлак легко убирается шлифовкой. - Сварка пластическим деформированием, в т. ч. холодная – детали сдавливаются (с предварительным местным нагревом или без него) и формируют сварной шов. Нагрев осуществляется газом, электротоком или другим способом.
Виды термической обработки
Технология |
Процесс |
Результат |
Отжиг |
Нагрев до предела пластичности, выдержка и постепенное охлаждение вместе с печью. |
Улучшенная ковкость, вязкость и пластичность, уменьшенная прочность и твердость, устранение внутренних напряжений, получение равновесной структуры. |
Закалка |
Нагрев и выдержка при высокой температуре, затем стремительное охлаждение в воде или масле. |
Повышенная прочность, твердость из-за неравновесной структуры, устойчивость к сжатиям и растяжениям. |
Отпуск |
Вторичный нагрев, выдержка и охлаждение после закалки. Применяется для прочных сталей и закаленных сплавов. |
Компенсация нежелательных эффектов. |
Старение |
Медленная и длительная смена температуры. Применяется для сплавов, закаленных без полиморфного превращения. |
Усиление прочности и твердости сталей с содержанием Mg, Al, Ni, Cu. |
Нормализация |
Аналог отжига с остыванием на открытом воздухе. |
Изменение зернистости, улучшение ковкости. |
Химико-термическая обработка |
Изменение химического состава, структуры деталей и свойств их поверхности. Насыщение другими элементами. Сильный нагрев и длительная выдержка. |
Придание сплаву однородной структуры. Повышение износостойкости, твердости, устойчивости к коррозии, контактной выносливости и сопротивления усталости. |
Термомеханическая обработка |
Пластическая деформация, применяемая для сплавов магния и алюминия. |
Повышение плотности дислокации кристаллического строения, улучшение механических характеристик. |
Типы резки металла
Технология |
Особенности |
Преимущества |
Лазерная резка |
Сфокусированный лазерный луч расплавляет лист четко по линии реза. |
Экономичность, универсальность, высокое качество кромок, точная и тонкая линия реза, экономия материала, автоматическое выполнение раскроя любой сложности. |
Плазменная резка |
Сжатая режущая дуга эффективно режет токопроводные материалы: высоко- и низкоуглеродистые, высоколегированные и конструкционные стали, нержавейку, чугун, титан, биметаллы, цветметы. |
Быстрота и качество резки, широкие возможности применения, экономичность. |
Газокислородная резка |
Направленная струя технически чистого кислорода с температурой выше 1000 °С прожигает материал по линии реза и выдувает продукты сгорания. |
Эффективная резка металла толщиной от 5 до 200 см, включая углеродистые средне- и низколегированные стали толщиной 1–200 мм. |
Гидроабразивная резка |
Водная струя с примесью абразивных частиц подается на материал под давлением до 5000 атм. и режет его на молекулярном уровне. |
Создание деталей сложной формы с точным соблюдением размеров. |
Выбор технологий металлообработки
Методы обработки деталей выбираются в зависимости от поставленных задач, необходимых изменений в структуре или свойствах металла, размеров заготовок и конечных изделий, заданного класса точности и других факторов. На нашем производстве в Федоровском, в 40 км от Санкт-Петербурга, работает большой парк высокотехнологичного оборудования для разных видов металлообработки. Это станки с ЧПУ управлением, в которых львиная доля операций выполняется автоматически по введенным в компьютер чертежам и параметрам.
Способы обработки металла: расскажем о наиболее популярных
Вопросы, рассмотренные в материале:
- Почему так популярна обработка металлов
- Какие существуют основные способы обработки металла литьем и давлением
- Каковы особенности обработки металла термическим способом
- Чем хороши сварка, электрическая и механическая обработка металлов
С давних времен люди научились использовать металлы и их сплавы для улучшения условий своей жизни. Сейчас в обиходе человека много металлической посуды, украшений и разного рода инструментов. Большинство приборов и механизмов собраны из металлических деталей. Для создания этих предметов люди изобрели разные способы обработки металла. В зависимости от того, какие характеристики материала интересуют, можно подобрать наиболее подходящий метод его обработки.
Почему так популярна обработка металла
Уровень развития нашей цивилизации во многом определяется способностью людей работать с металлом. Еще в древности люди поняли, что если обработать медный или золотой самородок, то можно сделать разные полезные предметы и приспособления.
Этот период получил название «медный век». Постепенно люди изобрели новые технологии работы с металлическими заготовками, научились пользоваться такими способами, как литье и ковка. В результате из медной руды начали появляться все более совершенные предметы.
Люди разных стран и континентов постепенно развивали свои навыки работы с медью. На основе этого пластичного материала мастера по всему миру научились делать много красивых и полезных вещей. Спустя какое-то время началась и работа со сплавами, в результате чего стали появляться прочные инструменты и оружие. В каждой стране металлообработка развивалась своими темпами, способствуя всестороннему развитию государства.
В наши дни высокий уровень прогресса позволил достичь больших успехов во всех сферах жизни, включая металлообработку. Благодаря ей современные изделия отличаются высокой функциональностью и совершенством. Кроме этого, с помощью металлического оборудования создаются уникальные вещи из других материалов. Процесс металлообработки в современной промышленности имеет большое значение. Постоянно повышающийся уровень развития технологий позволяет улучшать процесс работы с металлом, достигая все новых успехов. Благодаря различным действиям и операциям он может быть любой формы с максимальной функциональностью.
Сфера металлообработки важна не только для производства, но и для повседневного быта. Спектр ее применения просто огромен. Сюда входит создание различных приборов и механизмов, ювелирных изделий, предметов быта, инструментов, оружия, станков, промышленного оборудования и многое другое. Простая металлическая болванка может принимать любую форму и размер, необходимый человеку. Сложно отрицать ту роль, которую занимает металлообработка в современном технологическом развитии.
Приведем наиболее распространенные способы обработки металлов:
- Литье.
- Воздействие давлением.
- Термическая обработка.
- Электрическая.
- Сварка.
- Механическое воздействие.
Все эти способы имеют свои особенности и определенную область применения. Для изготовления какой-то конкретной детали может понадобиться их комбинация или последовательное использование.
Литье как один из древних способов обработки металла
Еще в древнейшие времена человек заметил способность железа застывать в рамках предложенной формы. Возможно, именно с метеоритов началось знакомство человека с металлом. Метеоритное железо отличается высокой плавкостью. Его гораздо проще обрабатывать, поэтому в некоторых цивилизациях начинали с литья этого материала.
На Руси литье относилось к очень почетным профессиям, имеющим большое значение. Одними из самых знаменитых шедевров литейного дела считаются Царь-пушка и Царь-колокол. И пусть они никогда не использовались по своему прямому назначению, но слава о них идет по всему миру.
Петр Первый отдавал должное мастерству уральских литейщиков. Именно их он всецело поддерживал и назначил главными поставщиками оружия для всей армии. Они до сих пор сохраняют за собой этот титул. Выделяется несколько основных способов литья, которые используют большинство литейщиков:
- Литье в землю.
Представляет собой классический способ обработки цветных металлов. Для этого понадобится простая или составная модель, по которой будет делаться матрица. Модель может быть деревянной или из любого другого подходящего материала. Матрица выполняется из смеси песка и глины. Литниковая система состоит из полностью собранной модели. С целью газоотведения обязательно предусматривают возможность прокалывания формы тонкими острыми иглами. После выполненной отливки необходимо дождаться полного остывания.
- Литье в металлическую форму.
Кокиль – это разъемная форма, в которой выполняется отливка. Ее делают из металлических частей. Чаще всего матрица изготавливается в процессе отливки. Но если необходимо очень высокое качество поверхности и точность размеров, то выбирают способ фрезерования. Предварительно формы обрабатывают антипригарным составом. Затем выполняется заливка.
Когда кокиль остыл, его можно разобрать и достать отливку. Кокиль необходимо чистить после каждой заливки. Если он сделан качественно, то может прослужить до 300 рабочих циклов.
- Литье по газифицируемым моделям.
VT-metall предлагает услуги:
Современным способом обработки металла является тот, когда модель изготавливают из легкоплавкого и газифицируемого материала. Хорошо подходит для этих целей полистирол. Газифицируемая модель не удаляется и остается в форме. В процессе заливки она испаряется. Перечислим достоинства этого способа:
– модель не надо удалять из матрицы;
– можно создать любые сложные модели, при этом не понадобится делать составные формы;
– процессы моделирования и формования в этом случае выполнять гораздо легче.
Многие ультрасовременные металлургические комбинаты перешли на литье по газифицируемым моделям.
Благодаря особенностям каждого способа литья можно выделить определенные сферы применения для каждого метода. Например, для разовых отливок или малых серий подойдет литье в песчаные формы. Эта технология практически исчезла из сферы интересов промышленных предприятий, но по-прежнему популярна в небольших скульптурных мастерских и у любителей художественных промыслов. Отдать предпочтение литью в металлические формы следует в тех случаях, когда необходимы:
- большие тиражи отливок;
- высокая точность размеров;
- высокое качество поверхности.
Различные ювелирные производства также используют литье в металлические формы.
Для больших тиражей отливок с высокой точностью и малыми трудозатратами больше подойдет литье по газифицируемым моделям.
Основные способы обработки металла давлением
Металлические материалы могут менять свою форму и размер под действием давления. При этом изменяется не только сама форма детали, но и физические и механические свойства материала. В связи с этим способ обработки металла при помощи давления стал активно использоваться во многих производствах и разных отраслях промышленности.
Вид пластической деформации материала путем давления зависит от применяемой температуры:
- Горячая. Если температура рекристаллизации ниже температуры заготовки.
- Холодная. Если температура рекристаллизации выше температуры заготовки.
В современной промышленности могут использовать следующие способы обработки черных и цветных металлов давлением:
- ковка;
- прокатка;
- волочение;
- прессование;
- объемная или листовая штамповка.
Поговорим о них более подробно.
- Ковка.
Одним из самых простых способов обработки металла является ковка. Она выполняется универсальными инструментами простой формы (плоскими бойками). Кроме этого используется гидравлический пресс. Для проведения операции деталь предварительно нагревают. Уровень нагрева определяется характеристиками самого материала.
Разогретую деталь размещают между двумя бойками. Если конструкция представляет собой молот и наковальню, то нижний боек неподвижен. В таком случае молот с силой опускается на деталь. Если при ковке используется гидравлический пресс, то деталь подвергается одновременному сжатию с двух сторон. Для выравнивания со всех сторон деталь можно поместить на ребро и повторить процесс заново.
Рекомендуем статьи по металлообработке
- Марки сталей: классификация и расшифровка
- Марки алюминия и области их применения
- Дефекты металлический изделий: причины и методика поиска
- Прокатка.
Прокатка представляет собой пропуск заготовки через вращающиеся валки. Этот способ обработки металла позволяет придать детали определенную форму, а также уменьшить ее поперечное сечение. Деталь в процессе трения втягивается между валками и под их давлением деформируется до определенного состояния. Специальное устройство для прокатки материала называется прокатный стан.
- Волочение.
Является процессом протягивания через фильеру обрабатываемого материала. В некоторых случаях материал перед обработкой нагревается. Бывает однократное волочение или целый комплекс фильер, проходя которые поперечное сечение заготовки существенно уменьшается.
Очень часто способом волочения обрабатывают материалы проката. Для изготовления волоков используют инструментальную сталь, твердые сплавы и алмазы. Специальные клещи захватывают заостренный конец прутка и протягивают его через фильеру. Этот способ применяется для изготовления тонкостенных труб, проволоки разного размера и любых пустотелых профилей.
- Прессование.
В основе прессования лежит технология выдавливания материала через отверстие матрицы. Сам материал располагается в закрытой форме. После выдавливания ему придается необходимая форма. Способ обработки металла прессованием часто используют в цветной металлургии и в области авиастроения.
- Штамповка.
Другим вариантом работы с продукцией прокатного стана является объемная штамповка. В ходе нее заготовка деформируется в полости штампов, принимая форму будущей поковки. Таким способом достигается высокая точность изделия. Объемную штамповку можно делать на специализированных машинах, на молотах или с использованием пресса.
Приведенные выше способы обработки металла посредством давления получили широкое распространение для создания металлических конструкций и различных заготовок в сфере промышленности. При этом используется как холодная обработка, так и предварительный нагрев. Самым простым способом воздействия на металлическое изделие считается ковка, а самым продуктивным признан прокатный метод.
Особенности обработки металла термическим способом
Очень эффективным способом считается использование термической обработки. При этом металл проходит несколько последовательных операций: нагрев, выдержку и охлаждение. В результате этих процессов меняются физико-химические характеристики материала, а под воздействием высоких температур изменяется его структура.
Термическую обработку применяют в тех случаях, когда необходимо повысить твердость материала, обеспечить ему большую прочность.
Воздействие высокой температурой на заготовку должно длиться определенное количество времени. Продолжительность процесса зависит от длительности нагрева металла до нужной температуры и времени, на протяжении которого должна действовать эта температура. Скорость нагрева может зависеть не только от характеристик самого металла, но и от особенностей используемой печи и размера заготовки.
В некоторых случаях при использовании термического способа обработки металла происходит обезуглероживание поверхности вплоть до появления окалины. Такая проблема возникает тогда, когда высокая температура слишком долго действует на поверхность материала. В результате снижается его прочность, что может привести к хрупкости всего изделия.
Выделяются три вида термической обработки металла в зависимости от воздействующего фактора: термическая, термомеханическая и химико-термическая.
- Термическая обработка – воздействие только температур на металл.
- Термомеханическая – воздействие температур и пластических деформаций детали.
- Химико-термическая – наиболее сильный метод, сочетает в себе воздействие температур и химических веществ.
Кроме этого можно выделить разные виды термической обработки по структуре полученного материала: закалка, отпуск и отжиг.
- Закалка.
Ее используют с целью придания большей прочности различным сплавам. Так, можно придать большую твердость инструментальной, углеродистой, легированной стали (она сама по себе является соединением железа и углерода) и сплавам цветных металлов (дюралюминия, бронзы и пр. ). Невозможно произвести закалку таких материалов, как чистое железо и низкоуглеродистые стали.
Этот способ обработки металлов и сплавов подразумевает нагрев изделия до таких температур, когда происходит разрушение кристаллической структуры материала, но твердое состояние все еще сохраняется. После этого следует быстрое охлаждение при помощи воздуха, воды или масла. В результате кристаллическая структура не восстанавливается и остается хаотичной (фаза т. н. мартенсита).
Процедура закаливания приводит к тому, что материал становится более твердым. Определенные сорта стали в закаленном состоянии тверже в три-четыре раза, чем незакаленные аналоги. С другой стороны, повышение твердости приводит к усилению хрупкости изделия, так как сохраняется внутреннее напряжение.
В зависимости от глубины закалки увеличивается термоупрочненный слой. Максимально твердая деталь получается в результате объемной закалки, но это придает ей и наибольшую хрупкость. Правильное сочетание разных слоев закаленного и незакаленного материала позволяет значительно повысить эксплуатационные характеристики изделия.
- Отпуск.
Отпуск по-другому называют искусственным старением. Он повышает прочность изделия на сжатие, растяжение и изгиб, снижая хрупкость закаленного материала. Эти процессы приводят к некоторому уменьшению твердости изделия, полученному в результате закалки. Широкое применение отпуск нашел в обработке сварочных швов с целью снижения сварочного напряжения.
В процессе отпуска заготовка нагревается до определенной температуры, в зависимости от сорта материала. В ходе нагрева кристаллическая структура аустенита частично восстанавливается. Затем деталь медленно охлаждают на воздухе (нормализация). После этого следует самый медленный процесс охлаждения вместе с печью (отпуск).
- Отжиг.
Отжиг используется с целью кратковременного уменьшения твердости и повышения вязкости изделия, что является промежуточной технологической операцией. Это может понадобиться в том случае, когда необходимо гнуть или резать металлическую заготовку. В дальнейшем такая деталь проходит повторную закалку.
Суть отжига заключается в нагревании детали до температуры, при которой кристаллическая структура восстанавливается (для стали – от мартенсита к аустениту). После этого следует медленное восстановительное охлаждение. В процессе отжига сталь может нагреваться до +500…+600 °С (низкотемпературный отжиг), до +750 °С (неполный отжиг) или до +900 °С (полный отжиг).
Электрические способы обработки металла
Существует целый ряд сплавов и хрупких непластичных металлов, которые не поддаются механическому воздействию. Но современные технологии позволяют изготавливать из них сложные изделия, полностью совпадающие с чертежами.
Электрический способ обработки металла востребован при создании электронных и бытовых приборов, а также в машиностроительной отрасли. На многих крупнейших заводах установлены специальные станки для электрической обработки материала. Выделяется несколько методов воздействия на металл при помощи электрического тока:
- Электроэрозионная обработка.
Она используется в том случае, если нужно сделать гравировку, отверстие или сложный паз, создать пресс-форму, штамп или кокиль. На поверхность заготовки воздействуют электрическим током, вызывая процесс электроэрозии. В результате разрушается поверхность электродов.
В процессе используется электрод такой формы, которую и нужно придать обрабатываемой заготовке. Существуют как электроискровые, так и электроимпульсные станки. В ходе обработки деталь размещается в ванне, заполненной жидкостью, не проводящей ток. Сама заготовка является анодом, а инструмент воздействия – катодом. На него подается ток и его сближают с анодом.
Когда искровой промежуток сокращается до минимума, то электрический разряд, возникший между анодом и катодом, вызывает моментальный нагрев материала до +10 000 °С. Материал начинает плавиться. Этот процесс сопровождается выбросом микрочастиц с поверхности металла, которые сразу же застывают в жидкости, опускаясь на дно. Это очень экономичный и безотходный способ обработки изделий, не требующий больших затрат энергии.
- Электрохимическая обработка.
Электрохимическая обработка позволяет оказывать точное воздействие на поверхность изделия. Основой процесса является жидкость, проводящая электрический ток (электролит). В нее погружается деталь, требующая обработки. Электролит приводит к растворению внешних слоев металла. В результате можно делать гравировку на поверхности изделия, профилировать заготовки или наносить специальное покрытие.
Кроме этого, электрохимический способ обработки металла позволяет создавать изделия с минимальной толщиной или изменять размеры деталей. Для этого существуют специальные режущие механизмы, способные снимать верхний слой растворенной пленки металла.
- Анодно-механическая обработка.
Для работы с материалами, обладающими повышенной вязкостью, или очень твердыми сплавами был разработан способ анодно-механической обработки. В нем соединены воедино электромеханическая и электроэрозионная технология. В данном случае деталь является анодом, а вращающийся инструмент – катодом.
После погружения в электролит пускают ток. В результате деталь плавится. При этом на ее поверхности появляется пленка, которая не способна проводить электричество. В определенных местах эту пленку снимает вращающийся инструмент.
Основные способы обработки металлов при помощи сварки
Несмотря на то, что сварку люди научились применять довольно давно, только в последние десятилетия разработали основные методы сварочных работ. В процессе сварки две детали нагреваются до температуры, при которой начинает плавиться их кромка. Тогда их и соединяют в единое неразъемное целое. Выделяется несколько групп сварочных технологий:
- Химическая. В результате химической реакции выделяется тепло, которое нагревает металл. Этот вариант используется для работы в труднодоступных местах, куда невозможно подвести электричество или подтащить газовые баллоны, в том числе под водой.
- Газовая. С помощью газовой горелки нагревают металл до необходимой температуры. Благодаря смене формы факела возможна не только сварка, но и резка металлов.
- Электросварка. Этот способ является самым популярным. Специальным аппаратом создается электрическая дуга, которая нагревает и плавит рабочую зону. Для сваривания деталей понадобятся обсыпные электроды или специальная сварочная проволока, а также обязательным условием является атмосфера инертных газов.
При контактной сварке нагрев осуществляется проходящим через точку соприкосновения соединяемых заготовок сильным электротоком. Существует точечная и роликовая сварка. При точечной детали соединяются в определенных точках. Роликовый способ подразумевает прокатку проводящего ролика по поверхности деталей, в результате чего формируется непрерывный шов.
Сварочные работы выполняют, когда необходимо соединить какие-либо строительные конструкции, детали механизмов, трубопроводы, корпуса судов и автомобилей и т. д. Также сварку можно сочетать с другими видами металлообработки.
Механическая обработка металла: виды и способы
Все виды механической обработки материалов объединяет один основной принцип, на котором строится работа: берется острый и твердый по отношению к заготовке инструмент, к которому прикладывают механическое усилие. Под воздействием инструмента изменяется форма или размер заготовки. Величина, на которую заготовка превышает размер конечного изделия, называется «припуск».
Выделяется несколько видов обработки материала посредством резания. Все зависит от целей, преследуемых мастером, и формы будущего изделия. Перечислим основные способы обработки металлов резанием:
- Точение. Осуществляется на станке, оборудованном резцом (например, на токарном). Чтобы обработать деталь, ее необходимо закрепить на станке, где она будет вращаться вокруг своей оси, а в это время резец снимет слой металла с поверхности заготовки. С помощью точения можно обработать цилиндрические, конические и торцевые поверхности как внутри, так и снаружи.
- Сверление. Осуществляется на станке, оборудованном сверлом. Основная цель заключается в проделывании отверстий в заготовке. С этой целью деталь жестко фиксируют с помощью тисков, и в ней сверлится отверстие определенного диаметра, который зависит от параметров сверла.
Кроме этого, сверло может отличаться как размером, так и формой. Иногда для работы требуется перовое, спиральное или центровочное сверло.
- Фрезерование. Специальный станок для фрезеровки оборудован инструментом с резцами (фрезой). Фреза быстро вращается вокруг своей оси, а деталь, закрепленная на столе, движется продольно. В зависимости от того, как закреплены заготовка и фреза, выделяют горизонтальную, вертикальную и диагональную фрезеровки. Для мастеров, занимающихся фрезеровкой, выпускают и компактные ручные электрические фрезеры. Они очень удобны в том случае, когда необходимо сделать какую-то работу на месте, не устанавливая деталь в стационарном станке. И пусть спектр их возможностей ограничен, но как мобильная версия они достаточно удобны.
- Строгание. Осуществляется на специальном станке, который может быть продольно-строгальным, поперечно-строгальным и строгально-долбежным. Операция строгания может понадобится при изготовлении рам, штанг, станин и пр.
Станок оборудуют прямыми и изогнутыми резцами. Прямыми легко управлять, но большую точность в работе дают только изогнутые. Поэтому чаще всего на строгальные станки устанавливают резцы изогнутой формы.
- Долбление. Осуществляется посредством долбежного станка. Резец совершает прямолинейное возвратно-поступательное движение, а перпендикулярно ему двигается заготовка. Чаще всего долбление используется при изготовлении плоских деталей с небольшой высотой. Так, путем долбления можно получить очень точное зубчатое колесо.
- Шлифование. Осуществляется на станке, оборудованном шлифовальным кругом. Заготовка обрабатывается посредством воздействия этого круга, который вращается продольно, поперечно или вокруг заготовки. В результате получается высокоточная деталь. Важно понимать, что для качественной работы шлифовального станка необходимо предусмотреть те особенности, которые влечет за собой эта операция: нагревание детали во время обработки, возможная сильная вибрация и пр.
При изготовлении той или иной металлической детали может понадобиться различное оборудование. Зачастую все операции комбинируются и группируются для достижения наилучшего результата, снижения затрат и упрощения процессов.
Почему следует обращаться к нам
Мы с уважением относимся ко всем клиентам и одинаково скрупулезно выполняем задания любого объема.
Наши производственные мощности позволяют обрабатывать различные материалы:
- цветные металлы;
- чугун;
- нержавеющую сталь.
При выполнении заказа наши специалисты применяют все известные способы механической обработки металла. Современное оборудование последнего поколения дает возможность добиваться максимального соответствия изначальным чертежам.
Для того чтобы приблизить заготовку к предъявленному заказчиком эскизу, наши специалисты используют универсальное оборудование, предназначенное для ювелирной заточки инструмента для особо сложных операций. В наших производственных цехах металл становится пластичным материалом, из которого можно выполнить любую заготовку.
Преимуществом обращения к нашим специалистам является соблюдение ГОСТа и всех технологических нормативов. На каждом этапе работы ведется жесткий контроль качества, поэтому мы гарантируем клиентам добросовестно выполненный продукт.
Благодаря опыту наших мастеров на выходе получается образцовое изделие, отвечающее самым взыскательным требованиям. При этом мы отталкиваемся от мощной материальной базы и ориентируемся на инновационные технологические наработки.
Мы работаем с заказчиками со всех регионов России. Если вы хотите сделать заказ на металлообработку, наши менеджеры готовы выслушать все условия. В случае необходимости клиенту предоставляется бесплатная профильная консультация.
Типы процессов изготовления металла
Термин «изготовление металла» относится к процессам, используемым для создания готовой детали или продукта путем придания формы, добавления или удаления материала из необработанной металлической заготовки или полуфабриката. В следующей статье представлен обзор доступных типов производственных процессов с описанием того, что они влекут за собой, какие материалы они подходят и для каких приложений они подходят.
Запросить предложение
Резка
Резка — это процесс разделения металлической заготовки на более мелкие части. Существует несколько используемых методов резки, каждый из которых обладает уникальными характеристиками, которые делают его пригодным для различных применений.
Древнейший метод резки — пиление. В этом процессе используются режущие лезвия — прямые или вращающиеся — для резки материалов различных размеров и форм. Автоматические операции распиловки позволяют производителям добиваться большей точности и аккуратности при резке деталей без ущерба для скорости обработки.
Одним из новейших методов резки является лазерная резка. В этом процессе используется мощный лазер для резки материалов до желаемой формы и размера. По сравнению с другими процессами резки он обеспечивает более высокую точность и аккуратность резки, особенно для сложных и замысловатых конструкций деталей.
Механическая обработка
Механическая обработка является субтрактивным процессом, т. е. создает детали и изделия путем удаления материала с заготовки. В то время как некоторые производители продолжают использовать технологии ручной обработки, многие обращаются к обрабатывающему оборудованию с компьютерным управлением, которое обеспечивает более жесткие допуски, большую согласованность и более высокую скорость обработки.
Двумя наиболее распространенными процессами обработки с ЧПУ являются фрезерование с ЧПУ и токарная обработка с ЧПУ. Фрезерные операции с ЧПУ основаны на вращающихся многогранных режущих инструментах для удаления лишнего металла с заготовки. Хотя этот процесс часто используется в качестве завершающей процедуры, его можно использовать для завершения всего проекта. В токарных операциях с ЧПУ используются одноточечные режущие инструменты для удаления материала с поверхности вращающейся заготовки. Этот процесс идеально подходит для создания цилиндрических компонентов с точными внутренними и внешними элементами.
Сварка
Сварка относится к процессу соединения материалов — обычно таких металлов, как алюминий, чугун, сталь и нержавеющая сталь — вместе с использованием высокой температуры и давления. Существует множество доступных методов сварки, в том числе сварка вольфрамовым электродом в среде инертного газа (TIG), сварка металлическим электродом в среде инертного газа (MIG), дуговая сварка в среде защитного газа (SMAW) и дуговая сварка с флюсовой проволокой (FCAW). требования к навыкам. Производители могут использовать ресурсы компании, занимающейся ручной или роботизированной сваркой, в зависимости от размера и сложности сварочного проекта.
Пробивка отверстий
В операциях пробивки отверстий используются специализированные инструменты (т. е. наборы пуансонов и штампов) и оборудование (т. е. пробивные прессы) для вырезания секций из плоских заготовок средними и большими тиражами. Пробивное оборудование с ЧПУ используется для обработки легких и тяжелых металлов.
Формовка
Формовка включает формование и изменение формы твердого металла в желаемую деталь или изделие. Доступно несколько различных процессов формования, включая гибку, волочение, экструзию, ковку, вытягивание, прокатку и растяжение. Они обычно используются с листами и пластинами, а также с другими формами материалов для производства простых компонентов и сложных сборок.
Сотрудничайте с экспертами PDF, Inc. для удовлетворения ваших потребностей в производстве металлов
Производство металлов включает широкий спектр процессов, включая, помимо прочего, резку, механическую обработку, сварку, штамповку, резку и формование. В то время как большинство мастерских по изготовлению металлоконструкций не предлагают все эти процессы собственными силами, в PDF, Inc. мы предоставляем все эти возможности и многое другое под одной крышей. Для получения дополнительной информации о наших услугах по изготовлению металлоконструкций свяжитесь с нами или запросите расценки сегодня.
Процессы обработки металлов давлением: методы, отрасли и применение
6 Общие процессы обработки металлов давлениемТип процесса формовки металла, который вы выберете, будет зависеть от типа металла, который вы используете, что вы создаете и как он будет использоваться. Некоторые из наиболее распространенных методов обработки металлов давлением:
Читайте дальше, чтобы узнать больше об этих процессах: |
Процессы обработки металлов давлением являются неотъемлемой частью нашего общества, и без них наше общество остановилось бы.
Продукты и компоненты, созданные с помощью различных процессов обработки металлов , используются при создании всего, от строительных лесов и тяжелой техники до проектирования и создания микропроцессоров и искусственного интеллекта.
Вы когда-нибудь задумывались, как делают металл? Когда дело доходит до формовки металла, существует несколько производственных процессов на выбор, каждый из которых предлагает свой собственный список преимуществ и недостатков, каждый подходит для конкретных применений и подходит для разных типов металла.
Некоторые из наиболее распространенных методов обработки металлов давлением:
- Профилирование
- Экструзия
- Пресс-тормоз
- Штамповка
- Ковка
- Литье
Давайте рассмотрим некоторые из распространенных приложений, для которых используется каждый тип формовки, и некоторые отрасли, в которых используется каждый тип.
1. Профилегибочное производство
youtube.com/embed/cqbEuiNPEGY?feature=oembed” data-mce-style=”position: absolute; top: 0px; left: 0px; width: 100%; height: 100%; border: none;”>Короче говоря, профилирование включает в себя непрерывную подачу длинной полосы металла через барабанные ролики для достижения желаемого поперечного сечения.
Услуги по формованию профилей:
- Возможность расширенного встроенного добавления перфорированных элементов и тиснения
- Лучше всего подходят для больших объемов
- Выход сложных профилей со сложным изгибом
- Имеют жесткие воспроизводимые допуски
- Имеют гибкие размеры
- Создание деталей любой длины
- Требуют минимального обслуживания инструмента
- Способны формовать высокопрочные металлы
- Разрешение на владение инструментальным оборудованием
- Уменьшить место для ошибки
- Меньше брака
(Источник: Хотите узнать, подходит ли вам профилирование? Нажмите ниже, чтобы узнать больше.
)
Общие приложения и отрасли
Промышленность
- Аэрокосмическая промышленность
- Прибор
- Автомобилестроение
- Строительство
- Энергия
- Окно
- ОВКВ
- Металлические строительные изделия
- Солнечная
- Трубы и трубы
Общие области применения
- Строительное оборудование
- Компоненты двери
- Лифты
- Каркас
- ОВКВ
- Лестницы
- Крепления
- Перила
- Корабли
- Структурные компоненты
- Гусеницы
- Поезда
- Трубка
- Windows
2. Экструзия
Экструзия – это процесс формовки металла, при котором металл продавливается через матрицу желаемого поперечного сечения.
Если вы подумываете о формовании металла методом экструзии, вам следует иметь в виду, что:
- В первую очередь предпочтительным методом экструзии является алюминий, хотя можно использовать и большинство других металлов
- Матрицы (алюминиевые) относительно доступны по цене
- Штамповка или тиснение выполняются как дополнительная операция
- Может производить полые профили без сварки швов
- Может производить сложные поперечные сечения
Общие приложения и отрасли
Промышленность
- Сельское хозяйство
- Архитектура
- Строительство
- Производство потребительских товаров
- Производство электроники
- Гостеприимство
- Промышленное освещение
- Военный
- Ресторан или служба общественного питания
- Доставка и транспортировка
Общие приложения
- Алюминиевые банки
- Бары
- Цилиндры
- Электроды
- Фитинги
- Рамки
- Линии подачи топлива
- Технология впрыска
- Рельсы
- Стержни
- Структурные компоненты
- Гусеницы
- Трубка
3.

Прессовое торможение включает в себя обычное формование листового металла (обычно), изгибание металлической заготовки под заданным углом путем ее зажимания между пуансоном и матрицей.
Если вы заинтересованы в листогибочном прессе, имейте в виду, что это:
- Лучше всего подходит для коротких и небольших тиражей
- Производит более короткие детали
- Лучше всего подходит для совместимых форм с более простыми схемами изгиба
- Имеет высокие затраты на оплату труда
- Создает меньшее остаточное напряжение, чем профилирование
Общие приложения и отрасли
Отрасли
- Архитектура
- Строительство
- Производство электроники
- Промышленное производство
Общие приложения
- Декоративная или функциональная отделка
- Корпуса для электроники
- Корпуса
- Средства безопасности
4.
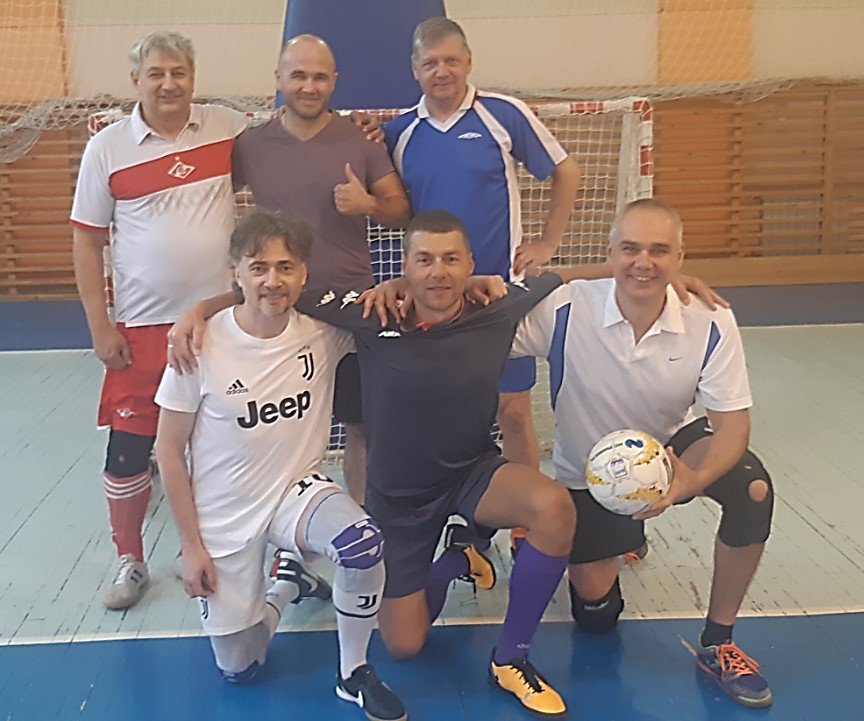
Штамповка включает размещение плоского металлического листа (или рулона) в штамповочном прессе, где инструмент и штамп оказывают давление, чтобы придать металлу новую форму или вырезать кусок металла.
Штамповка связана с:
- Штамповка одним нажатием
- Однородные детали с фиксированными размерами
- Более короткие детали
- Большие объемы
- Создание сложных деталей за короткое время
- Требуются высокотоннажные прессы
Общие приложения и отрасли
Отрасли
- Производство бытовой техники
- Строительство
- Электротехническое производство
- Производство оборудования
- Производство креплений
Общие области применения
- Детали самолетов
- Боеприпасы
- Бытовая техника
- Заглушка
- Электроника
- Двигатели
- Шестерни
- Оборудование
- Уход за газоном
- Освещение
- Фурнитура для замка
- Электроинструменты
- Прогрессивная штамповка
- Телекоммуникационная продукция
5.
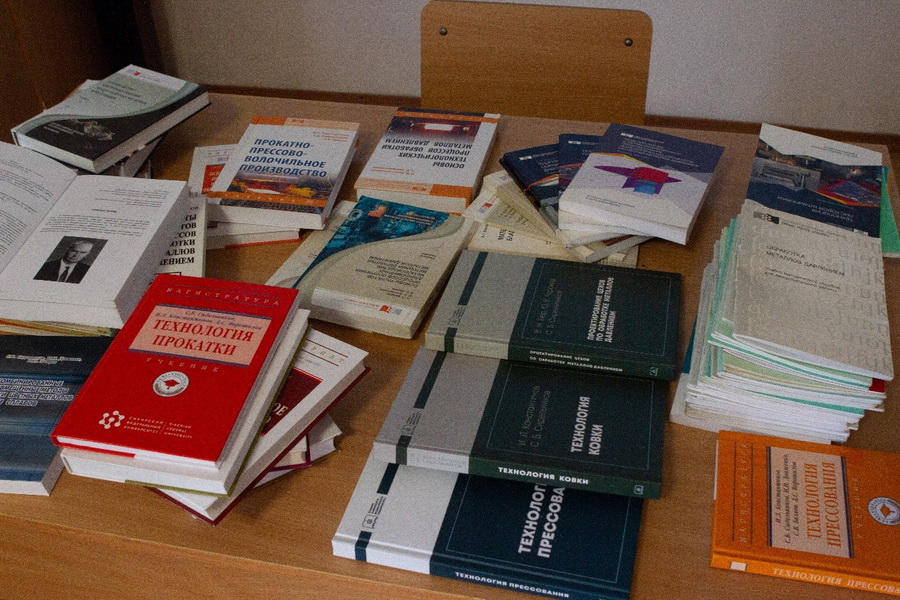
Ковка включает в себя формование металлов с использованием локальных сжимающих усилий после нагрева металла до состояния, при котором он становится ковким.
Если вы рассматриваете возможность ковки, имейте в виду, что:
- Прецизионная ковка сочетает в себе производство и изготовление путем придания исходному материалу желаемой формы с минимально возможным количеством вторичных операций
- Последующая обработка практически не требуется
- Требуются высокотоннажные прессы
- Дает более крепкий конечный продукт
- В результате получается продукт с высокой прочностью и твердостью
Общие приложения и отрасли
Промышленность
- Аэрокосмическая промышленность
- Автомобилестроение
- Медицинский
- Производство и передача электроэнергии
Применение
- Балки оси
- Шаровые шарниры
- Муфты
- Сверла
- Фланцы
- Шестерни
- Крючки
- Шкворни
- Шасси
- Ракеты
- Валы
- Розетки
- Рулевые рычаги
- Клапаны
6.

Литье — это процесс заливки жидкого металла в форму, содержащую полую полость желаемой формы.
Тем, кто рассматривает возможность использования процесса формовки литьем металла, следует помнить, что он:
- Можно использовать широкий спектр сплавов и сплавов по индивидуальному заказу
- Результат: недорогой инструмент для мелкосерийного производства
- Может привести к получению продуктов с высокой пористостью
- Лучше всего подходит для небольших тиражей
- Может создавать сложные детали
Общие приложения и отрасли
Промышленности
- Альтернативная энергетика
- Сельское хозяйство
- Автомобилестроение
- Строительство
- Кулинария
- Оборона и военные
- Здравоохранение
- Горное дело
- Производство бумаги
Общие приложения
- Бытовая техника
- Артиллерия
- Предметы искусства
- Корпуса камер
- Корпуса, крышки
- Диффузоры
- Тяжелое оборудование
- Двигатели
- Прототип
- Инструменты
- Клапаны
- Колеса
Выбор метода формовки металла
Вы ищете формовочную машину для своего проекта? Тип процесса формовки металла, который вы выберете, будет зависеть от многих факторов: Какой металл вы используете? Каков ваш бюджет? Что вам нужно создать и как это будет использоваться?
Каждая технология обработки металлов давлением имеет свои преимущества и недостатки.