Виды термической обработки металлов: Термическая обработка | Компания Невские Ресурсы
alexxlab | 23.04.2023 | 0 | Разное
Термическая обработка металла и её виды
Термическая обработка металла и её виды
|
Термическая обработка металла — это изменение внутренней структуры металлов под воздействием изменяющихся температурных условий и в следствие этого, получение необходимых механических и физических свойств.
Термическая обработка металла применяется или в качестве промежуточной операции для улучшения обрабатываемости давлением и резанием, или в качестве окончательной операции технологического процесса, который обеспечивает заданный уровень свойств детали.
Общая длительность нагрева металла при термической обработке складывается из времени собственно нагрева до заданной температуры и времени выдержки при этой температуре.
1. Отжиг металла
Отжиг — термическая обработка (термообработка) металла, при которой производится нагревание металла, а затем медленное охлаждение. Эта термообработка (т. е. отжиг) бывает разных видов (вид отжига зависит от температуры нагрева, скорости охлаждения металла).
2. Закалка металла
Закалка — термическая обработка (термообработка) стали, сплавов, основанная на перекристаллизации стали (сплавов) при нагреве до температуры выше критической; после достаточной выдержки при критической температуре для завершения термической обработки следует быстрое охлаждение. Закаленная сталь (сплав) имеет неравновесную структуру, поэтому применим другой вид термообработки — отпуск.
3. Отпуск металла
Отпуск — термическая обработка (термообработка) стали, сплавов, проводимая после закалки для уменьшения или снятия остаточных напряжений в стали и сплавах, повышающая вязкость, уменьшающая твердость и хрупкость металла.
4. Нормализация сплавов
Нормализация — термическая обработка (термообработка), схожая с отжигом. Различия этих термообработок (нормализации и отжига) состоит в том, что при нормализации сталь охлаждается на воздухе (при отжиге — в печи).
5. Старение металла
Старение – это процесс изменения свойств сплавов без заметного изменения микроструктуры. Известны два вида старения: термическое и деформационное.
6. Обработка металла холодом
Новый вид термической обработки, для повышения твердости стали путем перевода остаточного аустенита закаленной стали в мартенсит. Это выполняется при охлаждении стали до температуры нижней мартенситной точки.
Методы поверхностного упрочнения металла
Поверхностная закалка — процесс термической обработки, представляющий собой нагрев поверхностного слоя стали до температуры выше критической и последующее охлаждение с целью получения в поверхностном слое структуры мартенсита.
Различают следующие виды закалки металла:
- индукционная закалка;
- закалка в электролите,
- закалка при нагреве токами высокой частоты(ТВЧ),
- закалка с газопламенным нагревом.
Термомеханическая обработка металла
Термомеханическая обработка – метод упрочнения металла или сплава при сохранении достаточной пластичности, совмещающий пластическую деформацию и упрочняющую термическую обработку (закалку и отпуск).
Литейный завод «Урал» выполнит термическую обработку металла (стали и чугуна) на заказ. Заказать термообработку деталей из чугуна, можно обратившись по телефонам в Бийске: 8 (3854) 43-08-23 или 8 (961) 989-90-85.
Термическая обработка металлов
Термическая обработка металлов
1. Общие сведения и виды термической обработки стали
Под термической обработкой металлов следует понимать изменение внутреннего строения (структуры) металла под воздействием изменяющихся температурных условий и, как следствие этого, получение необходимых механических и физических свойств металла.
Большая часть операций термической обработки проводится при критических температурах, при которых происходят структурные превращения в сплавах. Большинство превращений требует для своего полного завершения определенный промежуток времени.
Рекламные предложения на основе ваших интересов:
Дополнительные материалы по теме:
Поэтому процесс термической обработки металлов сводится, по существу, к трем последовательным операциям:
а) нагреву металла с определенной скоростью до необходимой температуры,
б) выдержке при этой температуре в течение некоторого времени,
в) охлаждению с заданной по процессу скоростью.
В зависимости от того, в каком направлении надо изменить свойства данного стального изделия, применяются различные виды термической обработки, отличающиеся максимальной температурой нагрева, продолжительностью выдержки и скоростью охлаждения. Термическая обработка широко применяется в современном машиностроении.
Основными видами термической обработки являются отжиг, нормализация, закалка и отпуск. Применение того или иного процесса термической обработки зависит от того, в каком направлении нужно изменить структуру и свойства данной стали. В практике часто применяются в определенной последовательности несколько процессов термической обработки к одному и тому же изделию или полуфабрикату для получения необходимых свойств.
Отжиг стальных изделий, поковок, слитков применяется в тех случаях, когда нужно изменить структуру крупнозернистой стали, т. е. измельчить зерно и сделать структуру мелкозернистой; улучшить обрабатываемость стали режущим инструментом; подготовить структуру стали к ‘последующей термической обработке; выровнять химическую неоднородность в крупных стальных отливках, слитках; устранить внутренние напряжения в стальных изделиях; освободить сталь от наклепа. Отжиг заключается в том, что стальное изделие нагревается до определенной температуры, выдерживается при этой температуре некоторое время и затем медленно охлаждается вместе с печью.
Отжиг подразделяется на несколько видов. В практике применяются следующие виды отжига: полный, неполный, изотермический; отжиг на зернистый перлит; диффузионный, низкотемпературный, рекристаллизационный.
Полным отжигом называется такой, при котором сталь нагревается до температуры, лежащей на 30—50° выше линии GSK по диаграмме состояния железоуглеродистых сплавов, выдерживается при этой температуре и затем медленно охлаждается-вместе с печью. После отжига сталь приобретает мелкозернистую структуру, становится мягкой, вязкой и освобождается от внутренних напряжений.
Скорость нагрева, максимальная температура нагрева, выдержка и скорость охлаждения оказывают большое влияние на конечный результат отжига. В зависимости от химического состава стали и размеров изделия изменяется и скорость нагрева. Например, при отжиге легированных сталей, изделий сложной формы и изделий крупного размера нагрев производится мед-тленно. Выдержка при максимальной температуре нагрева должна обеспечить равномерный прогрев изделия до заданной температуры и произвести превращение в структуре стали.
Температура максимального нагрева углеродистых сталей зависит в основном от содержания углерода в стали. Ниже приводится табл. 3 температур отжига углеродистых сталей с различным содержанием углерода.
При проведении полного отжига нужно следить за максимально допустимой температурой нагрева, так как превышение температуры приводит к сильному росту зерна, в связи с чем сталь становится хрупкой. Такая сталь называется перегретой. Структуру перегретой стали можно исправить повторным отжигом. Структуры нормально отожженной стали и перегретой показаны на рис. 22. При нагреве стали до очень высоких температур ее можно испортить, так как при этом кислород, проникая в сталь, окисляет железо, в результате чего окислы железа располагаются по границам зерен.
Такая сталь называется пережженной и обладает очень низкими механическими свойствами. Исправить структуру пережженной стали повторными процессами термической обработки невозможно. Скорость охлаждения после тепловой выдержки оказывает большое влияние на механические свойства стали. При быстром охлаждении структурные составляющие стали получаются мельче, что ведет к повышению прочности и упругости стали. При медленном охлаждении металл становится мягче. Скорость охлаждения зависит от требований, предъявляемых к стали.
Отжиг на зернистый перлит применяется для уменьшения твердости, повышения вязкости и улучшения обработки заэв-тектоидных и эвтектоидных сталей. Практически он осуществляется нагревом стали до температуры 740—760°, т. е. немного выше критической точки. После выдержки сталь медленно охлаждается.
Диффузионный отжиг преследует устранение неоднородности химического состава крупных слитков высоколегированной стали. Характеризуется он медленным нагревом стали до высоких температур, порядка 1100—1150°, выдержкой при этих температурах от 10 до 15 часов и последующим охлаждением. Нагрев стали до таких температур ускоряет диффузионные процессы в аустените, в результате чего происходит выравнивание химического состава стали. После диффузионного отжига сталь обычно подвергается обыкновенному отжигу, или нормализации.
Рекристаллизационный отжиг применяется для уничтожения наклепа. При холодной обработке стали, прокатке, волочении проволоки, штамповке сталь получает холодное деформирование (наклёпывается). Наклеп выражается в том, что сталь после холодной обработки приобретает жесткость и становится малопластичной. Такую сталь трудно обрабатывать. Рекристаллизационный отжиг снимает эти деформации, и сталь приобретает свои первоначальные свойства. Структура наклепанной и отожженной стали показана на рис. 23. При рекристаллизационном отжиге сталь нагревается до температуры 680—700°, дается небольшая выдержка при этой температуре, после чего она охлаждается на воздухе.
Нормализация преследует те же цели, что и отжиг. При нормализации стальные изделия нагреваются на 30—50° выше линии GSE, выдерживаются при этих температурах и затем охлаждаются на воздухе.
Рис 22. Структура стали:
а — нормально отожженной; б — перегретой при отжиге
Нормализация способствует образованию в стали более мелкого зерна (рис. 24, а), чем оно получается при отжиге (рис. 24, б) и самый процесс нормализации протекает быстрее отжига. В настоящее время нормализация получила широкое применение и во многих случаях вытеснила отжиг.
Рис. 23. Структура стали:
а — наклепанной; б — отожженной
Закалкой стали называется такой процесс термической обработки, при котором сталь нагревается выше линии GSK на 30—50°, выдерживается при закалочной температуре и затем быстро охлаждается в воде, масле или на воздухе. Закалка применяется в тех случаях, когда нужно повысить прочность, упругость и твердость стали. Сущность закалки заключается в том, что в стали при нагреве выше линии GSK происходят структурные превращения, в результате которых образуются зерна аустенита. При быстром охлаждении аустенит при переходе через линию PSK распадается и в зависимости от скорости охлаждения в стали образуются новые структуры, т. е. сорбит, троостит или мартенсит, которые обладают большей прочностью по сравнению с перлитом.
Рис. 24. Структура стали:
а — нормализованной; б — отожженной
В зависимости от характера охлаждения закалка имеет несколько разновидностей. В производственной практике существуют следующие способы закалки.
Обыкновенная закалка (закалка в одной среде). Этот вид закалки применяется главным образом для простых деталей, изготовленных из углеродистых и легированных сталей. Детали после нагрева до закалочных температур и небольшой выдержки погружаются в охлаждающую среду и держатся в ней до тех пор, пока совершенно не охладятся. В качестве охлаждающей среды применяется вода или масло. Среда выбирается в зависимости от размеров изделий и химического состава стали.
Прерывистая закалка (закалка в двух средах) применяется преимущественно для закалки инструмента, изготовленного из высокоуглеродистых сталей. Этот способ заключается в том, что нагретое изделие после некоторой выдержки охлаждают в воде до температуры порядка 400—300°, после чего извлекают его из воды и дальнейшее охлаждение проводят в масле. Так как масляная среда дает меньшую скорость охлаждения, то образование в стали мартенсит-ной структуры происходит спокойнее, благодаря чему уменьшаются внутренние напряжения.
Рис. 25. Закалка зубила с самоотпуском
Закалка с самоотпуском. Отпуск изделий после закалки обычно производится повторным нагревом холодных закаленных изделий до необходимой температуры. В этом случае вся деталь подвергается одному и тому же режиму закалки и отпуска,
в результате чего твердость и вязкость во всех ее точках будут одинаковы. При закалке с самоотпуском к повторному нагреву не прибегают, и отпуск производят за счет тепла той части изделия, которая не погружена в закалочную жидкость, или за счет тепла, сохранившегося во внутренних слоях изделия. Закалка с самоотпуском широко применяется в случаях термической обработки ударных инструментов, так как для них создание одинаковой твердости во всех точках является нецелесообразным. Наоборот, постепенное и равномерное уменьшение твердости от рабочей части к центру и хвостовой части обеспечивает высокую стойкость инструмента в работе.
Закалка с самоотпуском практически производится следующим образом. После нагрева изделия до закалочной температуры и соответствующей выдержки при этой температуре рабочая часть инструмента погружается в воду (рис. 25, а). После неполного охлаждения в воде отпускаемую поверхность быстро-зачищают напильником (рис. 25, б) и наблюдают за цветами побежалости, которые появляются на зачищенной поверхности стали. Появляющиеся цвета побежалости являются результатом возникновения тонких слоев окислов на поверхности стали. Цвет слоя окисла зависит от его толщины. Цвета побежалости появляются при нагревании стали в интервале температур 200—325°. При появлении цвета побежалости, который соответствует требуемой температуре отпуска, рабочую часть инструмента быстро-окончательно охлаждают в воде (рис. 25, в).
2. Виды поверхностной закалки стали
Ряд деталей автомобиля и других машин, испытывая в процессе работы большие динамические нагрузки, одновременно подвергается поверхностному истиранию. В таких случаях возникает необходимость придавать высокую твердость поверхностному слою деталей, сохраняя их сердцевину вязкой. В последнее время в промышленности получили широкое распространение различные виды поверхностной закалки изделий.
В практике поверхностная закалка изделий производится следующими способами:
а) индукционным нагревом изделий токами высокой частоты,
б) контактным электронагревом изделий,
в) нагревом кислородно-ацетиленовым пламенем,
г) нагревом металлов и сплавов в электролите.
Поверхностная закалка токами высокой частоты производится с помощью индукционного нагрева металла токами высокой частоты. Этот метод разработан и применен в 1936 г. в Советском Союзе профессором В. П. Вологдиным.
Индукционный нагрев металлических изделий основан на использовании явлений электромагнитной индукции, теплового действия электрического тока и поверхностного эффекта. Нагрев изделий, подлежащих закалке, осуществляется при помощи специальной установки (рис. 26), которая состоит из следующих основных элементов: генератора высокой частоты, электродвигателя, трансформатора, индуктора, батареи конденсаторов. Сущность закалки токами высокой частоты заключается в том, что изделие, подвергающееся закалке, помещается в индуктор с таким расчетом, чтобы между ним и индуктором был воздушный зазор в 2—4 мм. Ток высокой частоты от машинного генератора поступает в индуктор. Вокруг индуктора создается переменное магнитное поле, под воздействием которого в закаливаемом изделии индуктируются вихревые токи. Благодаря явлению поверхностного эффекта максимальная плотность тока будет сосредоточена на поверхностном слое изделия. Толщина слоя, по которому идет ток максимальной плотности, называется глубиной проникновения тока. Под действием индукционного тока поверхностный слой изделия быстро нагревается до закалочных температур, а сердцевина изделия нагревается до температур, лежащих ниже линии PSK, благодаря чему в ней не происходит никаких структурных превращений и изменений механических свойств.
Нагрев изделий происходит в течение нескольких секунд, так как скорость нагрева равна 320—400° в секунду. По окончании нагрева изделия охлаждаются водяным душем. Вода поступает (из индуктора, изготовляемого в виде медной трубки и имеющей с внутренней стороны специальные отверстия для выхода воды. В индуктор вода подается под давлением от специальной
Рис. 26. Схема установки для закалки изделий токами высокой частоты
установки. Глубина закалки зависит в основном от частоты применяемого тока и может получаться от сотых долей миллиметра до нескольких миллиметров. Закалка’ токами высокой частоты отличается от обычной закалки высокой производительностью; кроме того, она обеспечивает получение более высокой поверхностной твердости закаленных изделий.
туры отпуска твердость стали уменьшается, а ударная вязкость увеличивается. Продолжительность выдержки при отпуске закаленной стали должна быть достаточной для того, чтобы обеспечить сквозной прогрев изделия и завершение структурных изменений. В зависимости от размеров отпускаемых изделий, их веса, конструкции печи, температуры отпуска время выдержки может быть различным — от нескольких минут до 4—5 часов. Охлаждение нагретых изделий может производиться в воздушной или в жидкой среде, преимущественно в воде, или на воздухе. Скорость охлаждения после нагрева и выдержки углеродистых сталей может быть различной, так как она не оказывает влияния на механические свойства отпускаемых изделий. При отпуске легированных сталей, главным образом хромистых, охлаждение должно производиться быстро. При медленном охлаждении ударная вязкость понижается и сталь может получиться хрупкой. Отпуск, в зависимости от температуры нагрева, бывает трех видов: низкий, средний и высокий.
Низкий отпуск производится при температуре 150—200°. Такой отпуск главным образом снимает внутренние напряжения, а высокая твердость и износоустойчивость изделия сохраняются. Низкий отпуск применяется для инструментальных стадей, а также после закалки деталей, подвергнутых цементации, цианированию и поверхностной закалке.
Средний отпуск осуществляется путем нагрева стали в интервале температур от 200 до 500°. Целью среднего отпуска является создание высоких пределов прочности и упругости при хорошей вязкости. Он применяется обычно при обработке пружин, рессор, штампов, а также ударного инструмента.
Высокий отпуск производится нагревом стали от 500 до 7002и применяется для деталей, изготовленных из улучшенной конструкционной стали. Высокий отпуск имеет своей целью получить наибольшую вязкость стали при достаточном пределе прочности и упругости. Этот вид отпуска применяется для обработки деталей,- подвергающихся действию ударных нагрузок, для создания у них однородной структуры сорбита отпуска. Такому отпуску подвергаются шатуны, шатунные болты, передние оси автомобиля и т. п.
Обработка стальных изделий холодом была впервые применена русским ученым П. П. Аносовым в 1827 г. Широкое применение этот метод получил в наше время благодаря Исследованиям профессора А. П. Гуляева. Сущность обработки стальных изделий холодом заключается в том, что закаленная сталь непосредственно после закалки охлаждается до температур, лежащих значительно ниже 0 (минус 80—190°). При низких температурах остаточный аустенит закаленной стали, распадаясь, превращается в мартенсит. Благодаря этому твердость стали повышается, структура стали становится однородной, повышается ее прочность. Охлаждение закаленных изделий до низких температур производится различными способами: твердой углекислотой, которая дает возможность понизить температуру стали до — 75°, жидким воздухом, кислородом или азотом до — 180—190° в холодильных машинах. Обработке холодом подвергаются режущий инструмент, измерительный инструмент и различные цементованные ответственные детали.
4. Термическая обработка чугуна
Отливки и изделия из серого и белого чугунов подвергаются различным видам термической обработки с целью уничтожения внутренних напряжений, снижения твердости, повышения прочности, улучшения антифрикционных и других свойств.
Отжиг чугунных отливок производится для уничтожения внутренних напряжений и для снижения твердости. Нагрев их делается медленный, так как при быстром нагреве в силу плохой теплопроводности чугуна в нем могут появляться трещины. Скорость нагрева производится в пределах 80—160° в час. Максимальная температура нагрева 500—550°. При такой температуре отливки выдерживаются в течение 2—8 часов. После выдержки производится медленное охлаждение со скоростью от 20 до 50° в час. В результате отжига отливки из серого чугуна освобождаются от внутренних напряжений. Такому отжигу подвергаются отливки блока цилиндров двигателя и поршневых колец. В тех случаях, когда на поверхности отливок образуется слой отбеленного чугуна, отливки также подвергаются отжигу, но с целью снижения твердости.
При отжиге для снижения твердости отливки нагреваются до более высоких температур, порядка 800—950°.
Закалка чугунных изделий производится с целью повышения их твердости, прочности и износоустойчивости. Чугунные изделия, подлежащие закалке, нагревают до 900—950°, выдерживают при этой температуре и затем подвергают охлаждению в масле. Вода для охлаждения не применяется во избежание коробления изделий и образования трещин. После закалки производится отпуск при температурах порядка 200— 300°.
Наиболее распространенным видом закалки чугунных изделий является изотермическая закалка, при которой изделие, нагретое до 850—950°, после выдержки переносится в соляную ванну, температура которой обычно бывает от 250 до 400°. После выдержки в соляной ванне изделия охлаждают на воздухе.
Охлаждающая среда и ее правильный выбор оказывают большое влияние на качество закалки. В. интервале температур 650—400° аустенит очень неустойчив и при медленном охлаждении распадается на феррит и цементит. Следовательно, для того, чтобы предотвратить распад аустенита и переохладить его, необходима большая скорость охлаждения, особенно в интервале температур 650—400°. Аустенит в углеродистых сталях при температурах ниже 400° делается относительно устойчивым, и при процессе превращения его в мартенсит охлаждение желательно проводить медленно, что связано с уменьшением внутренних термических напряжений. Что касается легированных сталей, то охлаждение их ниже 400° должно проводиться быстро. В качестве охлаждающей среды при закалке могут применяться: вода различной температуры, как чистая так и с примесями некоторых солей, минеральные и растительные масла, расплавленные соли, расплавленные металлы.
Скорость охлаждения нагретого металла в этих средах различна.
Различные скорости охлаждения в закалочных средах объясняются тем, что при погружении нагретого металла в жидкость на его поверхности образуется пленка перегретого пара, которая прочно держится вокруг изделия и способствует образованию паровой рубашки. Паровая рубашка плохо проводит тепло, вследствие чего происходит снижение скорости охлаждения. При закалке в масле паровая рубашка разрывается медленно, а в воде она разрывается быстрее, этим объясняются различные скорости охлаждения. Вода повторно, применяемая для закалки, закаливает сильнее, чем свежая. В воде с примесью едкого натра охлаждение происходит очень быстро в связи с тем, что частички едкого натра при попадании на поверхность раскаленного металла взрываются и способствуют разрушению паровой рубашки.
5. Определение температуры нагрева изделий
Температура нагрева изделий при термической обработке металлов имеет исключительно важное значение. Качество изделий после термической обработки в основном зависит от точного соблюдения и выполнения температурного режима того или иного вида термообработки. Поэтому для измерения и регулирования температурного режима термической обработки пользуются специальными приборами, которые называются пирометрами. Пирометры бывают термоэлектрические и оптические.
Термоэлектрический пирометр состоит из термопары и милливольтметра (.рис. 27, а). Термопара состоит из двух тонких проволочек, изготовленных из разных металлов. Концы проволочек спаяны, два других остаются свободными, которыми термопара присоединяется к милливольтметру. При нагревании спаяных концов между свободными концами термопары появляется разность потенциалов, электрический ток при этом регистрируется отклонением стрелки милливольтметра. Величина отклонения стрелки милливольтметра зависит от температуры нагрева спаянных концов термопары. Милливольтметр имеет две шкалы. На одной нанесены милливольты, а на другой — градусы. Для измерения температур, не превышающих 1000°, одна проволочка термопары делается из хромеля (сплав никеля с хромом), а другая из алюминия (сплав никеля с алюминием, марганцем и кремнием). Для предохранения проволочек термопары от повреждений они вставлены в защитные трубки (рис. 27, б). Внутренняя трубка делается из фарфора, а внешняя из стали.
Рис. 27. Термоэлектрический пирометр:
а — схема пирометра; б— термопара в защитной трубке
Оптический пирометр с исчезающей нитью работает по принципу изменения степени яркости излучения раскаленных тел. С помощью такого пирометра измерение температуры нагретого металла производится на некотором расстоянии от него путем сравнения яркости световых лучей, излучаемых нагретым металлом, с яркостью нити лампы, помещенной в пирометре. Определение температуры нагретого металла производится через окуляр. Путем перемещения объектива прибора получают четкое изображение рассматриваемого предмета. После установки пирометра путем пропускания тока накаливают нить лампы. Накал нити регулируется реостатом и производится до тех пор, пока ее изображение не исчезнет на фоне раскаленного металла. Изображение нигги исчезает при ее нагреве, соответствующем нагреву раскаленного металла, т. е. когда температуры у них будут одинаковы. Температура нити измеряется гальванометром, на шкале которого нанесены градусы. Оптическим пирометром можно измерять температуры до 2000°.
Цвета каления и побежалости при отсутствии описанных приборов дают возможность определить температуру нагретых металлов довольно точно на глаз.
При определении температур нагретой стали на глаз в интервале 220—325° пользуются цветами побежалости.
6. Термическая обработка основных деталей автомобиля
Значительная часть автомобильных деталей подвергается различным видам термической обработки с целью сообщения им физических и механических свойств, обеспечивающих необходимую прочность. Для подготовки структуры металла к последующим видам термической обработки применяются главным образом нормализация и отжиг. Улучшение углеродистых сталей производится закалкой и отпуском. Основные детали автомобиля, как, например, коленчатые валы, после штамповки подвергаются нормализации, затем механической обработке, после чего шейки их закаливаются токами высокой частоты.
Распределительные валы, изготовленные из стали марки 40, подвергаются закалке токами высокой частоты и отпуску. Шестерни коробок передач цементируются и закаливаются в масле с последующим отпуском. Шестерни главной передачи подвергаются закалке и обработке холодом, впускные клапаны — закалке с последующим охлаждением в масле и отпуску. Выпускные клапаны закаливаются при нагреве до 1050—1100°, охлаждаются в масле или воде после чего их отжигают и охлаждают вместе с печью. Полуоси ведущих колес автомобиля после штамповки подвергают нормализации, а после механической их обработки улучшают закалкой и отпуском.
Термическая обработка металла: сердце промышленности
Ничто не может быть изготовлено без термической обработки. Термическая обработка металла необходима, так как необходима для осей, подшипников, шестерен, крепежных деталей и коленчатых валов.
Услуги по термообработке увеличивают стоимость металлических изделий примерно на 15 миллиардов долларов в год, придавая определенные свойства, необходимые для успешного функционирования деталей.
Что такое термообработка?
Термическая обработка – это процесс нагревания и охлаждения металла в твердом состоянии для получения желаемых свойств и долговечности без изменения его формы.
Процесс термообработки используется для упрочнения металла, смягчения металла, повышения износостойкости металла или повышения прочности хрупких изделий.
Термически обработанные металлы
Черные металлы составляют большую часть термически обработанных металлов. 80% черных металлов – это нагретая сталь , включая чугун, нержавеющую сталь и инструментальную сталь.
Сплавы алюминия, меди, магния, никеля и титана также можно подвергать термообработке.
Зачем термическая обработка металлов?
- Для повышения твердости металла. Поверхность термообработанных деталей тверже сердцевины не менее чем на 30-40 %.
- Для улучшения пластичности и обрабатываемости, делая металл пригодным для холодной прокатки, волочения проволоки и т. д.
- Для повышения стойкости к износу и коррозии. Положите твердую поверхность на относительно мягкие детали, срок службы изделия увеличится.
- Для улучшения ломкости.
- Для снятия внутренних напряжений, возникающих при литье, сварке, горячей и холодной обработке.
- Для улучшения электрических и магнитных свойств.
Как работает термообработка?
Хотя разные процессы термообработки приводят к разным результатам в металле, все они включают три этапа: нагрев, выдержку и охлаждение.
1.
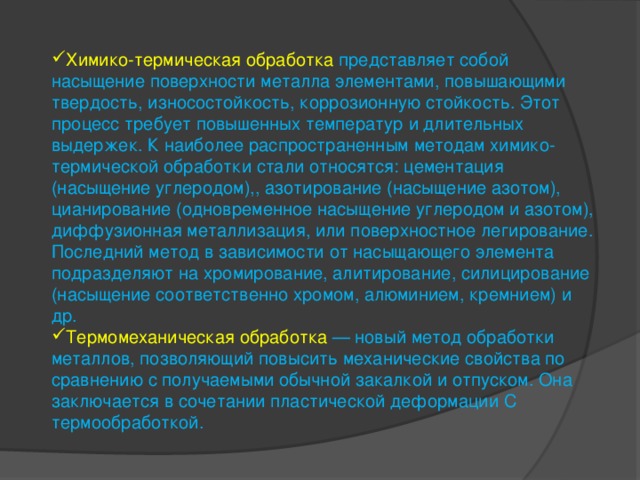
Медленно нагрейте металл до верхней критической температуры, чтобы поддерживать постоянную температуру.
Термообработанные металлы находятся в защитной атмосфере. Для нагрева используется расплавленная соль, вакуум, покрытие или метод упаковки. Если металл подвергнут термообработке неравномерно, один участок будет расширяться быстрее, чем другой, что приведет к деформации или растрескиванию участка металла.
Разные металлы имеют разную температуру термообработки. Скорость нагрева основана на следующих факторах:
- Теплопроводность металлов. Металлы с высокой теплопроводностью нагреваются быстрее, чем металлы с низкой теплопроводностью.
- Состояние металлов. Инструменты и детали, подвергнутые закалке или напряжению, нагреваются медленнее, чем необработанные.
- Размер и сечение металлов. Более крупные детали или детали с неровным поперечным сечением нагреваются медленнее, чем мелкие детали.
2. Холдинг
Выдержать некоторое время металл при достигнутой температуре.
Время зависит от требований, которые варьируются от нескольких секунд до 60 часов и более.
Время также зависит от типа материала и размера детали. Большие детали требуют больше времени. Для неравномерных поперечных сечений вы можете использовать самое большое сечение для определения времени.
3. Охлаждение
Охладить металл до комнатной температуры. Скорость охлаждения зависит от самого металла и охлаждающей среды.
Охлаждающая среда включает рассол, воду, масло и воздух, которые расположены в порядке убывания скорости охлаждения. Рассол поглощает тепло быстрее всего, а воздух медленнее всего. Как правило, мы используем воду для закалки углеродистой стали, масло для закалки легированной стали и воду для закалки цветных металлов.
Также возможно использование термических печей для охлаждения . Контролируемая среда обеспечивает высокую точность, когда необходимо медленное охлаждение.
Виды термической обработки
1. Термическая обработка отжигом
Термическая обработка отжигом используется для размягчения металлов при холодной обработке и штамповке, придавая им высокую пластичность и ударную вязкость. В нем меньше внутренних напряжений, деформаций и трещин, но за счет твердости.
Процесс , при котором отжигаемый металл нагревается выше его верхней критической температуры, выдерживается при этой температуре в течение определенного периода времени, а затем очень медленно охлаждается в печи или на воздухе.
Типы отжига в основном включают полный отжиг, диффузионный отжиг, сфероидизирующий отжиг и технологический отжиг.
Технологический отжиг , также называемый докритическим отжигом, нагревает металл до температуры чуть ниже нижней критической температуры стали. Он в основном используется для низкоуглеродистой стали для восстановления пластичности. Диапазон температур составляет от 260 ° C (500 ° F) до 760 ° C (1400 ° F).
Применение: Отожженные металлы включают медь, алюминий, серебро, сталь и латунь. Отжиг меди заставляет ее прокатываться или гнуться. Отожженная сталь, такая как полутвердая сталь, твердая сталь и легированная сталь, легко режется.
2. Нормализующая термическая обработка
Между отжигом и нормализующей термической обработкой нет никакой разницы, за исключением того, что нормализация подвергается воздушному охлаждению. Нормализация снимает внутренние напряжения, вызванные сваркой, литьем или закалкой, чтобы облегчить резку металла.
Нормализация заключается в том, что металл нагревают до температуры, которая на 40°С выше его верхней критической температуры, выдерживают в течение определенного периода времени, затем охлаждают на воздухе с несколько большей скоростью.
Применение: Нормализация применяется после холодной обработки, такой как прокатка, штамповка и ковка. Нормализованная сталь тверже отожженной. Нормализация стали делает сталь более прочной, чем в любом другом состоянии.
3. Закалочная термообработка
Закалка подготавливает структуру к отпуску. Это может повысить высокую твердость и износостойкость, но за счет низкой пластичности.
Закалочная термическая обработка заключается в том, что металл нагревают до соответствующей температуры аустенизации и выдерживают в течение некоторого времени. Затем металл быстро охлаждают в воде, масле или рассоле.
Применение: Сталь нагревают до температуры от 800 до 850 °C для осуществления аустенизации. Затем его быстро охлаждают с образованием мартенсита. Эта сталь для закалки в масле довольно прочная, но более хрупкая.
4.
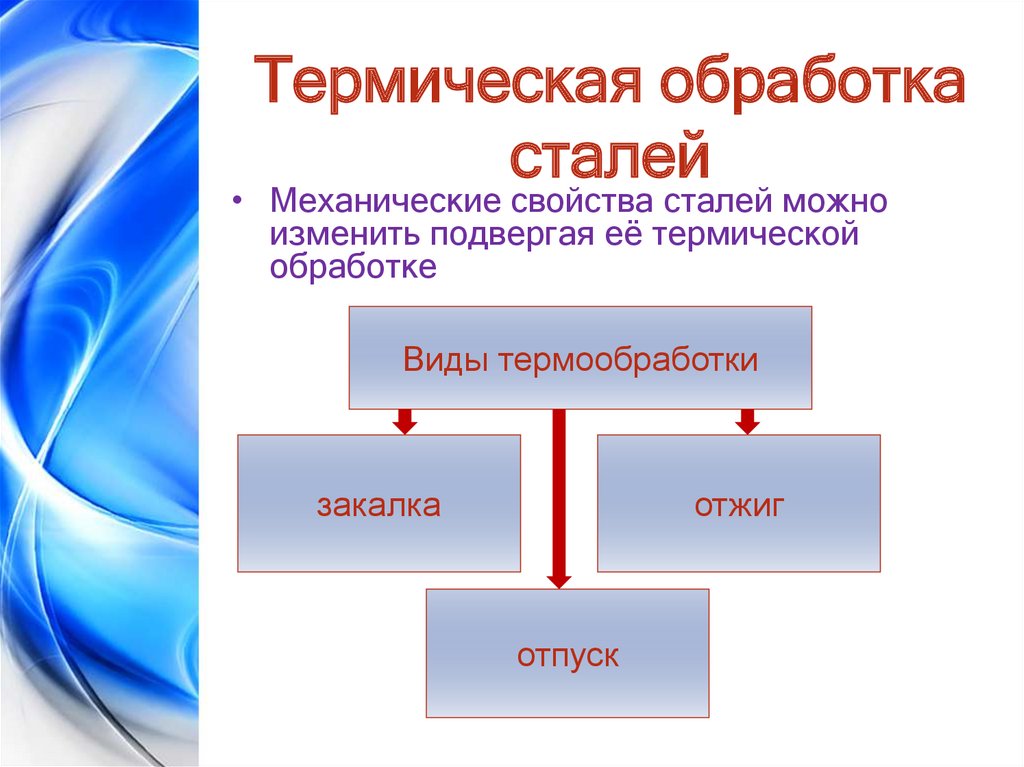
Отпуск Термическая обработка проводится после отпуска. Повышает эластичность, прочность и износостойкость металла.
Отпуск заключается в том, что закаленный металл повторно нагревают до температуры ниже нижней критической температуры с последующим экстремальным охлаждением на воздухе, в воде или масле.
Температуры отпуска колеблются от 300° до 1100°F, что обычно намного ниже температур закалки. Чем выше температура, тем мягче он становится.
Применение: Отпуск применяется к режущим инструментам, инструментам и зубчатым колесам, которые упрочняются в процессе упрочняющей термической обработки. Закаленная сталь (закаленная углеродистая сталь) может уменьшить хрупкость и сохранить ударную вязкость.
Скорость охлаждения при отжиге, нормализации и закалке увеличивается по очереди. Чем выше скорость охлаждения, тем тверже металл.
5. Закалка и закалка
(1) Аустенитная закалка
Austempering используется в заготовках из ковкого чугуна или стали. По сравнению с закалкой создает меньше трещин и деформаций, делая изделия более пластичными, прочными и ударопрочными. Тем не менее, закаленные металлы не могут иметь толщину более 1/2 дюйма.
Austempering направлен на получение бейнитной структуры в заготовке из прочного пластичного материала. Температура нагрева выше, чем у закаленных, обычно от 840 до 950 градусов Цельсия. Охлаждение происходит довольно быстро, и весь процесс не требует окончательного отпуска.
(2) Закалка
Закалка позволяет металлу лучше контролировать процессы обезуглероживания и науглероживания. Однако его нельзя использовать на больших заготовках или на всех типах стали.
Закалка заключается в нагреве металла до температуры выше верхней критической точки. Затем его охлаждают, чтобы снизить температуру до точки между 150 и 300 градусами Цельсия. Эта точка находится выше начальной точки мартенсита. В этой точке он удерживается до тех пор, пока вся заготовка не достигнет однородной температуры. Это позволяет аустениту превратиться в мартенсит. Наконец, он охлаждается на воздухе.
6. Термическая обработка раствора
Отжиг на твердый раствор, также называемый обработкой на твердый раствор, требуется перед старением.
Отжиг на твердый раствор — это для растворения выделений, присутствующих в металлических сплавах, и последующей быстрой закалки сплавов до комнатной температуры во избежание образования выделений во время охлаждения. После обработки сплавы будут в мягком состоянии.
Применение: Аустенитные нержавеющие стали, алюминиевые сплавы, сплавы с высоким содержанием никеля, сплавы титана и медные сплавы используют обработку раствором в качестве предварительной обработки для старения. Он обеспечивает термостойкость и коррозионную стойкость для применения детали.
Поверхностное упрочнение изменяет химический состав поверхностного слоя за счет поглощения углерода, азота или их смеси. Затвердевает только внешний слой заготовки, а внутренний остается мягким.
Обычно используемые процессы поверхностного упрочнения включают науглероживание и азотирование.
(1) Науглероживание: Это после закалки и низкотемпературного отпуска, добавление углерода на поверхность низкоуглеродистой стали для облегчения закалки, но ее центр по-прежнему сохраняет прочность и пластичность.
(2) Азотирование: Это до добавление азота на поверхность стали . Азотированная поверхность стали имеет повышенную твердость, износостойкость, усталостную прочность и коррозионную стойкость. В настоящее время в производстве в основном применяется газовое азотирование. Применяется для термической обработки зубчатых колес и термической обработки чугуна.
8. Индукционная закалка
Если деформация была проблемой для детали, предпочтительным методом является индукционная закалка. Это может быть важным фактором для круглых деталей, таких как шестерни. Поскольку время нагрева короткое, индукционная закалка может увеличить производительность и снизить трудозатраты.
Индукционная закалка использует электрический ток, передаваемый от медной катушки, расположенной вокруг детали. Направленный ток нагревает выбранные участки стальной детали до необходимой температуры и глубины. Затем деталь закаливают для достижения нужной твердости.
9. Закалка пламенем
Закалка пламенем нагревает только одну область детали. Этот процесс хорошо подходит для небольших объемов работ или очень глубоких случаев.
Пламенная закалка заключается в том, что металлическая часть нагревается пламенем, а затем гасится. Часто это можно сделать с помощью очень небольшого специализированного инструмента.
10. Термическая обработка для снятия напряжения
Термическая обработка для снятия напряжений предназначена для возврата металла как можно ближе к исходному состоянию текучести, предела прочности при растяжении и пластичности. Снятие напряжения металла при сварке может снизить опасность растрескивания сварных соединений сосудов.
Этот процесс заключается в нагревании металла до температуры чуть ниже его нижней критической границы с последующим медленным охлаждением.
Применение: Обычно используется для деталей котлов, баллонов с воздухом, аккумуляторов и т. д.
11. Вакуумная термообработка
Вакуумная термообработка может обеспечить наилучшую отделку поверхности и металлургию из всех методов термообработки , что не требует дополнительной очистки.
Он помещает стали в вакуумные печи для термообработки, содержащие только аргон. Камера нагревается до 2400 градусов по Фаренгейту с контролируемой скоростью, а затем температура снижается. Цикл вакуумной термообработки занимает от 3 до 24 часов. Процесс контролируется компьютером для обеспечения единообразия и повторяемости.
Применение: Вакуумная закалка применяется для крепежа, который является основой горнодобывающей, медицинской промышленности, аэрокосмической промышленности, строительства и т. д.
Рекомендации
1. Термическая обработка
2. Процессы термической обработки
3. Этапы термической обработки
Автор : Джордан Джордан — автор блога, хорошо разбирающийся в этой отрасли. Большинство главное, он искренне надеется помочь вам в ваших проектах.
Различные виды термической обработки
❮ Назад к блогу
Различные виды термической обработки
1 декабря 2021 г.
Возможно, вы видели слова «термообработка» в отношении изделий из стали, таких как ножи, ручные инструменты и другие изделия из стали. Но что именно на самом деле означает термин «термообработка»? Термическая обработка заключается в нагревании металла до заданной критической температуры или выше, а затем в охлаждении. Этот экстремальный нагрев изменит определенный химический состав в сплаве, а процесс охлаждения навсегда установит эти изменения в сплаве. Ниже мы рассмотрим различные виды термической обработки металлических сплавов.
Отжиг
Отжиг широко используется и является одним из самых популярных способов термообработки металлических сплавов. Типичная процедура отжига заключается в том, чтобы поместить металл в проходную печь или горячую камеру на заводе. Температура металла будет повышаться примерно на 50°C выше критической с постоянной скоростью. Как только металл достигает этой точки в течение установленного периода времени (2-3 часа), металл затем медленно охлаждается до своего нормального диапазона.
Эта процедура охлаждения выполняется путем постепенного понижения температуры горячей комнаты в течение определенного периода времени. Подумайте о термостате обогревателя, который включается и выключается в зависимости от температуры воздуха. В случае отжига температура этого термостата будет медленно снижаться, пока не будет достигнута конечная температура охлаждения. Этот процесс «смягчит» сталь, чтобы сделать ее более податливой для машинной обработки.
Этот процесс также удалит все газы, оставшиеся в составе стали, тем самым укрепив сталь. Еще одно преимущество отжига заключается в том, что он увеличивает магнитные и электрические свойства металла, что идеально подходит для порошкового покрытия и других электротехнических красок.
Нормализация
Нормализация имеет некоторое сходство с отжигом, поскольку они оба нагреваются до одной и той же температуры на 50°C выше критического порога. Основное отличие нормализации заключается в том, что время выдержки при этой температуре намного меньше, чем при отжиге. Процесс охлаждения также намного быстрее, так как металл переносится из горячей комнаты обратно в открытый цех для сушки на воздухе при нормальной температуре окружающей среды (комнатной температуре).
Этот процесс охлаждения (или закалка воздухом) закрепит изменения, сделанные ранее в точке нагрева. Нормализация снимает любые напряжения в металле и обычно применяется к холоднодеформированной стали, такой как штампованная, кованая или прокатная сталь.
Закалка
Закалка — это процесс повышения прочности стали, чтобы сделать ее более твердой и менее хрупкой. Если отжиг — это «инь», то закалка — это «ян», поскольку это полная противоположность отжига с точки зрения термической обработки. Если вы когда-нибудь видели, как кузнец делает меч или нож, вы видели закалку в действии, поскольку это важная часть процесса.
Металл нагревают на 40°C выше критической температуры, а затем быстро охлаждают, помещая его в масло или воду. Иногда вместо воды используется соляной раствор, так как вода иногда может вызывать образование пузырьков на поверхности металла. Вы можете увидеть конечные результаты закалки в таких предметах, как вышеупомянутые ножи и мечи, а также шестерни, метчики, штампы и долота.
Закалка
Закалка может привести к тому, что металл местами станет хрупким в зависимости от толщины закаливаемого металла. Типичным следующим шагом при использовании метода закалки для термической обработки тонких металлов, таких как лезвия, является их отпуск. Отпуск снижает хрупкость металла за счет снятия внутренних напряжений в металле, возникших в процессе закалки.
Обычный процесс закалки металла состоит в том, чтобы взять только что закаленный кусок и снова нагреть металл. Эта точка нагрева обычно находится в диапазоне между температурой окружающей среды и температурой критической точки. Эта температура может достигать 700°C, и как только эта температура будет достигнута, металл будет оставаться закрепленным в течение определенного периода времени. Отпуск обычно проводят в масляной ванне или ванне с расплавленным свинцом, а время выдержки при верхнем нагреве зависит от типа используемого металла и желаемой твердости металла.
Азотирование
Азотирование – это процесс формирования толстой «пленки» на поверхности металла, который обычно осуществляется с использованием газообразного азота, отсюда и название «азотирование». Этот тип термической обработки идеально подходит для тех, кто не хочет, чтобы вся металлическая деталь была закалена, а просто хочет укрепить поверхность. Этот метод иногда используется для инструментов, на которых со временем появляется много вмятин и царапин, таких как гаечные ключи.
Процесс азотирования заключается в помещении металла в герметичную камеру, в которую входят трубы. Трубки являются входом и выходом для газообразного аммиака, который будет циркулировать внутри камеры. Камера нагревается в печи до температуры 500°C, что приводит к выделению газообразного азота из циркулирующего внутри камеры аммиака. Газообразный азот образует атомарный азот из-за тепла, и это вызывает химическую реакцию с металлом, образуя нитрат железа на поверхности.
Чем дольше металл находится в этом состоянии нитрата железа при повышенных температурах, тем глубже нитрат железа проникнет в металл. После завершения процесса нет необходимости в охлаждении или закалке, поскольку нитрат железа будет постоянно связан с металлом.
Цианирование
Цианирование – это метод термической обработки мелких и средних кусков металла, который повышает предел усталости металла. Этот метод термической обработки также повышает поверхностную твердость металла. Название «цианирование» происходит от цианида натрия, который используется в процессе термической обработки.
Процесс цианирования начинается с помещения металла в ванну с расплавленной цианидной солью при температуре 950°C. Ванна с расплавленной солью состоит из цианида натрия, кальцинированной соды, карбоната натрия и хлорида натрия. Металл находится в этой расплавленной ванне около 20 минут, так как цианид натрия разрушается в нагретой среде. Это химическое разложение приведет к образованию азота, а также углерода из окиси углерода. Азот и углерод будут просачиваться на поверхность металла, заставляя его затвердевать в процессе.