Влияние азотирования на шероховатость поверхности – 7. Влияние технологических факторов на шероховатость поверхности.
alexxlab | 03.12.2019 | 0 | Разное
4.4.1 Влияние различных факторов на шероховатость поверхность
Формообразование в процессе резания новой (обработанной) поверхности зависит от следующих основных факторов: вида обработки, режимов резания, геометрии инструмента, свойств обрабатываемого материала, жесткости оборудования, состояния режущей кромки. Шероховатость (высота и шаг неровностей микропрофиля) поверхности зависит от способа резания, подачи, скорости резания, геометрии заточки инструмента, СОЖ, материала заготовки и других факторов.
При каждом виде обработки действует один или несколько преобладающих факторов.
Микрогеометрия вновь образованной поверхности может иметь самую разнообразную форму и размеры.
Так, например, при продольном точении, торцовом фрезеровании и строгании наибольшее влияние на шероховатость оказывают подача, углы в плане (φ и φ1) и радиус при вершине инструментов; при цилиндрическом фрезеровании—подача и диаметр фрезы; при фасонном точении—состояние режущей кромки. Схемы образования шероховатостей за счет перечисленных преобладающих факторов приведены на рис. 4.15.
а — резцом при продольном точении; б — торцовой фрезой; в — цилиндрической фрезой; г — фасонным резцом.
Рис. 4.15 – Схемы образования шероховатостей при обработке поверхностей различным инструментом
В первом и втором случае (рис. 4.15,а и б) в формировании микрогеометрии поверхности участвуют главная и вспомогательная режущие кромки с углами в плане φ и φ1. При перемещении резца на величину S за один оборот детали на образовавшейся поверхности остается гребешок высотой Н:
Н = S Sinφ Sin φ1 /Sin(φ + φ1),
Как видно из рисунка, чем меньше углы в плане и подача, тем меньше высота гребешков и лучше шероховатость поверхности.
Когда профиль неровностей получается от радиусного участка (r>0), фopмyлa для определения высоты неровностей Н имеет следующий вид:
½
H = r – (4r² – S²) /2,
Глубина резания на шероховатость поверхности влияет незначительно, и не как геометрический фактор, а как фактор, изменяющий температуру резания, условия наростообразования и деформацию срезаемого слоя.
Влияние скорости резания на шероховатость в наибольшей мере проявляется в области от 20 до 40 м/мин, где высота микронеровностей имеет наибольшее значение. С повышением скорости до 120—190 м/мин шероховатость постепенно уменьшается и затем практически не меняется. Ухудшение шероховатости при скоростях 20—40 м/мин объясняется интенсивным наростообразованием, а улучшение шероховатости при более высоких скоростях резания — повышением температуры в зоне резания и снижением трения между задней и обработанной поверхностями.
Твердость материала влияет на шероховатость в такой зависимости: с увеличением твердости шероховатость уменьшается.
С увеличением переднего угла уменьшается пластическая деформация срезаемого слоя, а следовательно и шероховатость.
Задний угол незначительно влияет на шероховатость обработанной поверхности. Если его изменение (уменьшение) увеличивает интенсивность износа по задней поверхности, то шероховатость при этом ухудшается, и наоборот.
Существенное влияние на шероховатость обработанной поверхности оказывает жесткость упругой технологической системы (станка, приспособления, детали, инструмента).
Известно, что возникновение вибраций резко увеличивает шероховатость. Однако даже при отсутствии визуально наблюдаемых вибраций колебания инструмента относительно детали имеются, и тем больше, чем меньше жесткость. Причиной таких колебаний являются динамический характер самого процесса стружкообразования, срыв нароста, неравномерность припуска, полученного на предшествующем переходе (за счет шероховатости большего значения), и др.
Смазочно-охлаждающие жидкости уменьшают трение и пластическое деформирование металла в зоне образования стружки и тем самым способствуют уменьшению высоты неровностей. Особенно эффективно применение масляных СОЖ.
Силы, действующие на инструмент. В процессе резания деформации подвергается не только срезаемый слой металла, но и слой основного металла детали. При этом на инструмент действует сила нормального давления стружки на переднюю поверхность, сила трения движущейся стружки об эту поверхность, сила упругой деформации основного металла, действующая на заднюю поверхность, и сила трения в точках контакта задней поверхности и обработанной поверхности.
Температура резания не сильно влияет на шероховатость поверхности, или влияет незначительно и не как геометрический фактор, а как фактор изменяющий температуру на условия наростообразования и деформацию срезаемого слоя.
studfiles.net
Термообработка по технологии TENIFER | Энциклопедия вооружения
Термообработка по технологии TENIFER QPQ
Азотирование и азоцементация деталей из стали, чугуна и металлокерамических сплавов на основе железа в солевых ваннах по технологии TENIFER® применяется на протяжении десятилетий во всём мире в самых различных отраслях промышленности. Технология используется для повышения износостойкости, усталостной прочности и, в особенности в сочетании с оксидированием, для увеличения коррозионной стойкости. Во многих случаях технология TENIFER® является альтернативой другим процессам термообработки поверхности деталей, например, закалке на мартенсит, гальваническим покрытиям (например, хромированию) и другим покрытиям (пластиковых, лаковых и т.д.) или азоцементации в плазме и газовой атмосфере, при этом обеспечивая более высокое качество и рентабельность.
Проведение процесса
Проведение процесса TENIFER Q, QP или QPQ является по сравнению с другими методами азоцементпации очень простым. Как это бывает обычным при термообработке деталей в солевых ваннах, их сначала нагревают на воздухе до температуры около 350°С, Азоцементация осуществляется в так называемой ванне TF1 при температуре 480-630°С, при этом в качестве стандартной температуры в большинстве случаев выбирают 580°С.
Солевой расплав состоит в основном из щелочного цианата а также щелочного карбоната и используется для работы в тигле из специального материала с вентиляционным устройством. Активной составной частью в ванне TF1 является щелочной цианат. В процессе азоцементации при реакции щелочного цианата с поверхностью деталей образуется щелочной карбонат. С помощью целенаправленного добавления неядовитого регенератора REG 1 в солевом расплаве снова создаётся нитрат и активность ванны TF 1 поддерживается с большой точностью (рис.1).
Поскольку регенерация ванны осуществляется без изменения объёма, не образуются избыточные количества солей, которые необходимо удалять. Потери пополняются добавочной солью TF 1. По сравнению с азоцементацией в атмосфере газа необходимые для процесса TENIFER QPQ вещества TF 1 и REG 1 не подпадают ни под категорию ядовитых, ни под категорию экологически опасных.
Оксидирование поверхности после азоцементации в солевой ванне осуществляется в специально разработанной охлаждающей ванне (ванна АВ1).При этом на поверхности обработанных деталей образуется слой оксида (магнетит) черного цвета, который обусловливает значительное увеличение коррозионной стойкости. Охлаждающая ванна имеет температуру 350-400°С. Кроме оксидирования наблюдается также благоприятное влияние на характерстику изменения размеров охлаждаемых деталей. Затем осуществляется дальнейшее охлаждение до комнатной температуры а также очистка обрабатываемого материала (процесс TENIFER-Q).
Если после проведения процесса поверхности деталей окажутся слишком шероховатыми, то, в зависимости от размеров и формы деталей, могут быть использованы самые различные методы полирования (процесс TENIFER-QP). Хорошо себя зарекомендовали:
- Притирка доводочной шкуркой с зернистостью 360 или мельче.
- Полирование или тонкое шлифование специальными полировочными кругами в непрерывном процессе подобно бесцентровому шлифованию или шлифованию на токарных автоматах.
- Скользящее шлифование в вибрационной ёмкости. Такая обработка применяется преимуществено для небольших и листовых деталей.
- Струйная обработка стеклянными шариками диаметром 40-70 микрон. Во избежание сильного закругления кромок или износа соединительного слоя рабочее давление должно составлять макс.4 атм.
- Автоматизированная струйная обработка металлическими шариками диаметром менее 1 мм.
Однако из-за промежуточной обработки может быть утеряна некоторая часть достигнутой антикоррозионной защиты. Поэтому после полирования часто проводится дополнительное оксидирование в ванне АВ 1.
Ход такого процесса показан на рис.2. Весь ход процесса с промежуточной обработкой отвечает технологии TENIFER-QPQ. QPQ означает Quench Polish Quench и заключает в себе термообработку TENIFER® с оксидированием, промежуточной полировкой и дополнительным оксидированием в солевом расплаве.
Структура и толщина азотированного слоя.
Соединительный слой.
При азоцементации в солевых ваннах по технологии TENIFER® образуется азотированный слой, состоящий из наружного соединительного слоя (эпсилон-слой) и примыкающего к нему диффузионного слоя. Образование, структура и свойства соединительного слоя зависят от использованного реагента.
Соединительный слой состоит из соединений железа, азота, углерода и кислорода. Благодаря его структуре он уже не обладает свойствами металла. Он характеризуется исключительно хорошим сопротивлением износу и коррозии и является стойким почти что до температуры парообразования. По сравнению с азоцементацией в плазме или в атмосфере газа технология TENIFER® позволяет получить соединительный слой с большим содержанием азота. Слои с высоким содержанием азота обеспечивают лучшую защиту от износа и, особенно, от коррозии, чем слои с более низким содержанем.
В соединительном слое, в зависимости от используемого материала, измерения показывают твёрдость примерно от 800 до 1500 единиц по Виккерсу. На рис.3 показаны для сравнения образованные различными методами граничные слои и соответствующие твёрдости.
При металлографическом исследовании поверхностного слоя детали, подверженной азоцементированию в солевой ванне соединительный слой чётко выделяется как слабо затравливаемая зона на фоне последующего диффузионного слоя. Соединительный слой образуется при проникновении атомарного азота в глубь поверхности. С увеличением поглощения азота превышается граница растворимости в граничной зоне и выделяются нитриды, образующие соединительный слой.
Кроме условий термообработки (температура, время, состав ванны) на толщину азотированного слоя влияет также содержание углерода и легирующих элементов. С увеличением доли легирующих элементов снижается толщина слоя, но в такой же степени увеличивается и твёрдость.
Показанные на рис.4 графики зависимости построены по результатам испытаний в ванне TF 1 при температуре 580°С. При обычной продолжительности термообработки 60 -120 минут толщина соединительного слоя на большинстве материалов 10-20 микрон.
Диффузионный слой
Глубина и твёрдость диффузионного слоя зависят в основном от материала. Чем более высоколегированная сталь, тем меньше глубина азотирования при одинаковой продолжительности обработки. С увеличением доли легирующих элементов возрастает твёрдость.
На нелегированных сталях на образование структуры диффузионного слоя оказывает влияние скорость охлаждения после азоцементации. После быстрого охлаждения в воде азот остаётся в составе твердого раствора. Из-за медленного охлаждения или последующего отпуска в наружной области диффузионного слоя на нелегированных сталях часть азота может выделяться в виде прожилок нитрида железа. Благодаря этому выделению улучшается ковкость детали после азоцементации.
На высоколегированных материалах диффузионный слой хорошо различается при металлографическом исследовании из-за большей чувствительности к травлению в отличие от сердцевинной структуры. Но фактическая глубина азотирования является также значительно большей, чем видимая при металлографическом исследовании затемненная область.
Существенное влияние охлаждения на образование диффузионного слоя не наблюдается. На рис.5 показана глубина азотирования для различных материалов в зависимости от продолжительности процесса.
Поверхностная твёрдость и сердцевинная прочность.
Достигаемая с помощью термообработки по технологии TENIFER® поверхностная твёрдость в значительной степени определяется составом материала. С увеличением содержания образующих нитрид легирующих элементов (Сг, Мо, А1, V, Mn, Ti, W) увеличивается поверхностная твёрдость. На рис.6 показаны ориентировочные значения сердцевинной прочности и поверхностной твёрдости азотированных в солевых ваннах сталей.
Изменение свойств деталей из-за обработки по технологии QPQ.
Коррозионная стойкость
Для определения коррозионной стойкости образцов и деталей проводятся исследования распылением соли (DIN 50021) или длительным погружением (DIN 50905/часть4).
При простом испытании распылением соли испытуемые детали подвергаются воздействию аэрозоли 5%-ного раствора поваренной соли при температуре 35°С.Это испытание обозначено в нормативном документе сокращением SS,
На рис.7 показаны результаты испытания распылением соли согласно DIN 50021 SS твёрдохромированных и азотированных по технологии TENIFER® поршневых штоков из нелегированной стали С35. Для получения толщины соединительного слоя 15-20 микрон на поршневых штоках требуется или твёрдое хромирование на толщину 15-20 микрон или азоцементация в солевой ванне в течение 90 минут. В отношении азотированных в солевой ванне поршневых штоков были испытаны различные варианты, например, азоцементация с оксидированием с промежуточной полировкой и без неё а также термообработка QPQ. Через 40 часов распыления соли на хромированных штоках появились первые признаки точечной коррозии. Спустя 180 часов на штоках было обнаружено очень сильное коррозионное разъедание на большой поверхности. По сравнению с этим ни один из азотированных штоков не был через 40 часов подвержен коррозии и даже через 180 часов обработанные по техноогии QPQ штоки оставались без признаков коррозии.
На рис.8 показана коррозионная стойкость образцов из материала С45, достигаемая после соответствующих ступеней огбработки согласно DIN 50021 SS.
Рис.9 демонстрирует соответствующую шероховатость поверхности образцов. В отшлифованном состоянии коррозия появляется уже через короткое время. Через 90 минут азоцементации в солевой ванне с оксидированием в охлаждающей ванне коррозионная стойкость составляет более 200 часов. Полировка не изменяет стойкости образцов. После последующего оксидирования в охлаждающей ванне (25 мин.при 370°С) достигаются значения более коррозионной стойкости 400 часов,
Наиболее жёстким испытанием на коррозию согласно DIN 50021 является тест CASS, где испытательный раствор дополнительно содержит уксусную кислоту и хлористую медь, а температура повышается до50°С. Результат сравнительных испытаний деталей, обработанных по методу QPQ, а также твёрдохромированных поршневых штоков с толщиной слоя 10-12 и соответственно 30-35 микрон показан на рис.10.
Испытание проводилось Институтом металловедения в Дармштадте в следующих условиях:
- Солевой раствор для распыления 5%NaCl + 0,26 г CuCh/l;
- рН 3,11-3,3;
- Температура 50°С (1 испытательный цикл == 1 час).
После обработки по технологии QPQ также наблюдается лучшая коррозионная стойкость, чем после твёрдого хромирования.Обработанные по технологии QPQ образцы показывают через 16 часов коррозионное разъедание лишь примерно 10% поверхности образца.
Для испытания длительным погружением (DIN 50905/часть 4) в качестве коррозионной среды применяется 3-ый раствор поваренной соли и 0,1%-ый раствор перекиси водорода (НзОз). Погружение образцов в испытательный раствор происходит в обезжиренном состоянии.
На рис. 11 представлены результаты различной поверхностной обработки образцов из термически улучшенной стали С45 после двухнедельного испытания погружением в соответствии с нормативами DIN.
В первой горизонтальной колонке приведены данные по термообработке и средняя потеря веса на м2 за 24 часа для образца QPQ.
С уменьшением веса 0,34 г/м2 этот образец выглядит значительно лучше чем образцы с гальваническим или химическим нанесением слоя.
При толщине твёрдого хрома 12 микрон и даже 45 микрон двойного хрома потеря веса составляла около 7 г/м и была таким образом более чем в 20 раз выше потери веса на образце после азоцементации.
Слой никеля 20 микрон показывает после дисперсионного твердения потерю веса 2,9 г/м . Только тройной слой с 37 микронами меди, 45 микронами никеля и 1,3 микрона хрома может сравниться с обработанным по технологии TENIFER-QPQ образцом.
Износостойкость и антифрикционные свойства
За счёт неметаллического строения соединительного слоя снижается трение и склонность к свариванию с ответной металлической поверхностью. Исключительные скользящие и антифрикционые качества а также высокая износостойкость являются известными и хорошо себя зарекомендовавшими качествами обработанных по технологии TENIFER® деталей.
Проведённые испытания на износ а также практическое применение снова и снова подтверждают высокую износостойкость узлов и деталей после азоцементации в солевых ваннах по сравнению с закалёнными обычным или индуктивным способом а также хромированными поверхностями. В очень многих случаях износостойкость соединительного слоя ещё более улучшается за счёт дополнительной окисляющей обработки. Например, обработанные по технологии TENIFER® такие узлы как валы редукторов, контрольные оправки и гидроагрегаты имеют более длительный срок службы чем твёрдохромированные узлы.
Часто возникают вопросы в отношении износостойкости диффузионного слоя. На рис.12 показано сравнение характеристики износа перекидных рычагов после различной термообработки. Мы видим износ поверхности рычага, который работал на распределительном валу из азотированного в солевой ванне отбелённого чугуна. Хотя из-за азоцементации твёрдость поверхности закалённого на мартенсит перекидного рычага несколько снижается, всё же чётко просматривается значительно улучшенная износостойкость за счёт соединительного слоя при работе в режиме трения продолжительностью до 80 часов,
Через 70-80 часов кривая износа проходит затем параллельно кривой перекидного рычага, подвергнутого только закалке на мартенсит, что объясняется защитным действием диффузионного слоя. Самопроизвольное увеличение износа после потери соедиительного слоя не наблюдалось.
Это исследование ещё раз очень наглядно показывает,что высокая поверхностная твёрдость автоматически не означает и высокую износостойкость. Как оценивать материал или парное сочетание материалов, зависит от соответствующего механизма износа. Особенно хорошо себя зарекомендовали азотированные рабочие пары материалов против адгезионного износа. Так, например, склонность к задиранию очень существенно снижается по сравнению с другими граничными слоями.
На рис.13 показаны результаты предельной несущей способности задирания на шестернях по Ниману-Реттигу. Она определялась увеличением налагаемого на профиль зуба изгибающего момента до тех пор, пока не появилось задирание. Благодаря азотированию с науглероживанием по технологии TENIFER®, прочность против задирания на исследованных материалах была увеличена в 2 – 5 раз.
В связи с вопросом об износостойкости и антифрикционых свойствах, интерес представляет также и коэффициент трения наружного граничного слоя. Возникающие при скольжении реации на граничной поверхности менее зависят от абсолютной твёрдости рабочих пар материалов, нежели от самих рабочих пар, их структуры, геометрии поверхности и используемого смазочного материала.
Для определения коэффициентов трения исследования проводились в нашей лаборатории на установке Амслер.
Во время испытаний вращался диск со скоростью 200 оборотов/мин в соприкосновении с неподвижным диском. Оба образца подвергались одинаковой обработке. Нагрузка составляла 5 – 30 Н во избежание адгезионного износа. В то время, как при более высоких нагрузках коэффициент трения с увеличением нагрузки возрастает, в диапазоне 5 – 30 Н он оставался постоянным.
На рис.14 представлен обзор полученных коэффициентов трения для различных сочетаний пар материалов в режиме сухого хода и после смазки маслом типа SAE 30.
Исследованные образцы после хромирования, закалки на мартенсит и азотирования с науглероживанием с водяным охладением или окисляющим охлаждением в охлаждающей ванне имели значения шероховатости около 4 микрон. Лишь на образцах после термообработки по технологии QPQ шероховатость поверхности была снижена за счёт полирования примерно до Rm = 1 микрон. В режиме сухого хода азотированные образцы показывают гораздо более низкие коэффициенты трения, чем образцы с закалёнными на мартенсит или хромированными граничными слоями. Благодаря окислению соединительного слоя, на азотированных образцах увеличивается коэффициент трения.
В смазанном состоянии необходимо учитывать гидродинамическую долю несущей способности. За исключением азотированных по технологии QPQ образцов, в результате имеющейся шероховатости поверхности присутствует крупная доля твёрдого тела, так что результаты относятся, по-видимому, к области смешанного (полусухого) трения. Азотированные по технологии QPQ образцы имеют в этих условиях проведения экспериментов минимальный коэффициент трения из всех вариантов.
Термообработка TENIFER® увеличивает усталостную прочность при круговом изгибе а также контактную прочность. На них оказывают главным образом влияние:
Содержание азота в соединительном и диффузионном слоях, ” Толщина диффузионого слоя. ” На нелегированных сталях состояние раствора азота.
Кроме того, необходимо учитывать ещё состояние структуры и прочность. В то время, как на нелегированных сталях повышение усталостной прочности зависит от скорости охлаждения, на легированных материалах достойное упоминания влияние охлаждения отсутствует. Возможное повышение усталостной прочности после 1-2 -часовой термообработки по технологии TENIFER® составляет на деталях из нелегированных и низколегированных сталей около 100%.
В этой связи следует ещё указать на то, что из-за хромирования снижается усталостная прочность при циклическом изгибе основного материала. Подобное явление известно по гальваническому цинкованию. По сравнению с этим, при азотировании с науглерожванием всегда увеличивается усталостная прочность.
На рис.15 показаны результаты исследования усталостной прочности образцов с надрезами из материала C45N. После термообработки по технологии QPQ повышение усталостной прочности составляет более 50%. После твёрдого хромирования усталостная прочность наоборот снижается на 20%.
Практическое применение технологии TENIFER-QPQ
Коррозионная, усталостная прочность а также износостойкость обработанных деталей по экологически чистой технологии азотирования с науглероживанием QPQ в солевых ваннах исследовались по самым различным методикам. При этом было установлено превосходство по сравнению с хромированными, никелированными и другими азотированными граничными слоями.
Показанные на рис.16 детали быстродействующих муфт для соединения шлангов, по которым подаются жидкие и газообразные среды, раньше изготовлялись из коррозионностойких сталей. Благодаря применению технологии для азотирования с науглероживанием в солевых ваннах QPQ появилась возможность замены дорогостоящего основного материала на нелегированную цементируемую сталь. В исполнении с термообработкой по технологии QPQ достигается требуемая коррозионная стойкость и износостойкость.
На рис.17 показан фрагмент коленчатого вала из материала 42СгМо4 для высокомощных двухтактных двигателей. Благодаря термообработке QP были выполнены требования в отношении износостойкости, усталостной прочности и антифрикционных свойств.
Детали подвергаются автоматической промежуточной полировке металлическими шариками на монорельсовой струйной установке. Опыты с азотированными в атмосфере газа или в плазме деталями не принесли желаемого результата.
На рис.18 показаны амортизаторы давления газа и обработанные по технологии QPQ поршневые штоки. Их устанавливают главным образом на капотах двигателей и багажников автомобилей а также на грузовых люках и салонных дверях в самолётах.
По сравнению с ранее проводившимся хромированием поступают сообщения о значительном улучшении коррозионной стойкости и износостойкости. Затраты на термообработку этих деталей были снижены примерно на одну треть.
На рис.19 показаны такие мелкие детали, как фурнитура для чемоданов и решётки для фенов. Их обрабатывают по технологии QPQ в качестве навалочного груза в очень больших количествах. 60 минут для азоцементации, оксидирование, промежуточная полировка и дополнительное оксидирование являются достаточными для достижения требуемых коррозионной стойкости и износостойкости.
Примеры применения можно было бы сколько угодно продолжать. О широких возможностях применения технологии QPQ свидетельствуют представленные на рис.20 некоторые типичные узлы и детали, обрабатываемые сегодня в серийном производстве с помощью комбинированного метода азоцементации в солевых ваннах. Здесь речь идёт, главным образом, о деталях из области автомобильной промышленности, как напимер, оси приводов для стеклоочистителей, натяжные устройства для клиновых ремней и клапаны.
Технология QPQ применяется также для термообработки деталей в авиации, на морских нефтяных платформах, в аппарате- и машиностроении, энергетике, пищевой промышленности, а также в технологии изготовления текстильного оборудования, гидроагрегатов и оптических приборов.
Установки TENIFER® и соображения рентабельности.
При выборе технологического процесса главными критериями являются его экономичность, достигаемое качество и экологическая безопасность. Весьма важной также является простота в применении процесса. По сравнению с другими процессами нитроцементации, процесс TENIFER® прост в применении. Обработка может выполняться как на обслуживаемых вручную, так и на полностью автоматизированных установках.
Современные установки с компьютерным управлением – очень гибкие. Они не только могут быть отрегулированы в зависимости от колебаний потребности в обработке деталей, но также позволяют одновременно проводить обработку по нескольким различным программам.
Автоматическая установка солевых ванн, показанная на рис. 21, идеально подходит для использования процесса TENIFER® в массовом производстве (в составе производственной конвейерной линии), а также для коммерческой термообработки, где из-за различных потребностей клиентов процесс нужно часто переналаживать.
На рис. 22 приведена схема установки TENIFER®, которая, в соответствии с новейшими технологическими требованиями, работает без сточных вод и оснащена эффективной системой отделения отходов и установкой по очистке воздуха. С такой технологией легко могут быть выполнены требования, предъявляемые в промышленно развитых странах к установкам с точки зрения экологии и охраны труда.
Cравнительный анализ процесса TENIFER® и других технологических процессов с точки зрения экономичности также показывает преимущества процесса
worldweapon.info
Азотирование 5—686 — Влияние – Энциклопедия по машиностроению XXL
Сталь — Азотирование — Влияние на предел выносливости 466, 467 [c.557]Длительность азотирования — Влияние на глубину азотированного слоя 287, 288 –хромоникелевая — Характеристика 124 [c.555]
Коэффициент Yz учитывает влияние двустороннего приложения нагрузки (реверса). При одностороннем приложении нагрузки = 1. При реверсивном нагружении и одинаковых нагрузке и числе циклов нагружения в прямом и обратном направлении (например, зубья сателлита в планетарной передаче) Y = 0,65 — для нормализованных и улучшенных сталей = 0,75—для закаленных и цементованных Y = 0,9 —для азотированных. [c.15]
Рис. 10.И. Влияние температуры и длительности азотирования на твердость (а) и глубину (б) азотированного | ![]() |
Уменьшить влияние состояния поверхности на усталость можно соответствующими технологическими методами обработки, приводящими к Упрочнению поверхностных слоев. К числу таких методов относятся наклеп поверхностного слоя путем накатки роликом, обдувки дробью и т. п. химико-термические методы — азотирование, цементация, цианирование термические — поверхностная закалка токами высокой частоты или газовым пламенем. Указанные методы обработки приводят к увеличению прочности поверхностного слоя и созданию в нем значительных сжимающих остаточных напряжений, затрудняющих образование усталостной трещины, а потому влияющих на повышение предела выносливости. [c.608]
Длина дуги оказывает существенное влияние на качество сварного шва и его геометрическую форму. Длинная дуга способствует более интенсивному окислению и азотированию расплавляемого металла, увеличивает разбрызгивание, а при сварке электродами основного типа приводит к пористости металла. [c.67]
Различные способы поверхностного упрочнения (наклеп, цементация, азотирование, поверхностная закалка токами высокой частоты ИТ. п.) сильно повышают значения предела выносливости. Это учитывается введением коэффициента влияния поверхностного упрочнения /С . Путем поверхностного упрочнения деталей можно в 2—3 раза повысить сопротивление усталости деталей машин. [c.318]
Коэффициенты ра и 3 учитывают шероховатость поверхности. Для шлифованных и полированных поверхностей принимают Ра = 3т = 1 при чистовой обточке Ра = Ра = 1,05. . . 1,25 при обдирке ра = Р- = 1,2… 1,5. На значение коэффициента р влияет упрочнение поверхности (цементация, азотирование и т. д.). Влияние этих факторов подробно излагается в литературе [26]. [c.316]
Для азотированных зубчатых колес величину [а/у] надо назначать с осторожностью, поскольку методы расчета не полностью отражают влияние неравномерности распределения удельных контактных нагрузок. Ориентировочно можно принять [С нг] = 40 кгс/см . [c.633]
Решить задачу 15.17 прц условии, что после шлифовки поверхность детали была подвергнута азотированию, причем коэффициент влияния упрочнения = 1,7. [c.300]
Упрочняющее влияние поверхностного наклепа, поверхностной закалки, цементации, азотирования и других технологических факторов оценивается коэффициентом р, взятым из справочной литературы, который вводится сомножителем к коэффициенту [c.423]
ТАБЛИЦА 40. ВЛИЯНИЕ УСЛОВИЙ АЗОТИРОВАНИЯ ПРИ 0,1 МПа НА СВОЙСТВА ХОЛОДНОКАТАНОГО (0,5 мм) ТАНТАЛА ЭЛЕКТРОННОЛУЧЕВОЙ ПЛАВКИ (II [c.110]
Влияние упрочнения поверхности. Для повышения несущей способности деталей широко используют разные способы поверхностного упрочнения цементацию, нитроцементацию, азотирование, поверхностную закалку токами высокой частоты (т. в. ч.), деформационное упрочнение (наклеп) накаткой роликами или дробеструйной обработкой. Упрочнение поверхности деталей значительно повышает предел выносливости, что и учитывается к оэффициентом влияния поверхностного упрочнения Км (табл. 0.4). [c.15]
Сильное влияние на усталостную прочность титановых сплавов оказывает химико-термическая обработка поверхности, проводимая для улучшения антифрикционных свойств. Наиболее простые и распространенные методы химико-термической обработки—термическое оксидирование на воздухе и азотирование. [c.184]
Изменение состояния поверхностного слоя. Положительное влияние на стойкость против КР стали типа 18-8 в хлоридах оказывает азотирование [59]. Диффузионное хромирование, сплошные никелевые покрытия также повышают сопротивление КР в различных средах [22, 59]. Хорошие защитные свойства показало алюминиевое покрытие [22]. Обезуглероживание поверхностного слоя коррозионно-стойких сталей также вызывало повышение стойкости против КР. Перспективным способом защиты от КР является создание белого слоя (15—30 мкм) на поверхности стали. Это объясняется более высокой коррозионной стойкостью белого слоя, большой гомогенностью его свойств, а также значительными остаточными напряжениями сжатия в нем [22]. [c.75]
Влияние геометрических характеристик на работу узла трения можно проследить на следующих примерах. Поршень из алюминиевого сплава оказался неработоспособным в азотированном цилиндре. После некоторого времени работы на юбке поршня возникали задиры, происходил перенос материала поршня на зеркало цилиндра. После того как на поверхность поршня были нанесены небольшие канавки для удержания смазки, пара цилиндр—поршень за весь период эксплуатации двигателя не имела каких-либо неполадок в работе. [c.197]
Рис, 27. Влияние легирующих элементен на общую глубину азотированного слоя [c.109]
Рис, 29. Влияние легирующих элементов на твердость азотированного слоя. Азотирование при 550 С в течение 24 ч (для сплава с алюминием 8 ч) [c.109]
Рис. 33. Влияние длительности выдержки при 600° С на твердость азотированной поверхности стали с различным содержанием элементов (в %) — 0,07 С 18,0 Сг 8,3 N1 0,2 Мо 0,5 Т1 2 —0,06 С 16,0 Сг 14,3 N1 2,0 Мо 1,3 Т1 Л 0,30 С 1,5 Сг 1,1 А1 4 — 0,20 С 1,4 Сг 0,4 Мо 0,3 V | ![]() |
Напряжения остаточные—Пример определения 288 Автоскрепленные цилиндры—см. Цилиндры автоскрепленные Азотирование — Влияние на предел выносливости 469, 470 Аистова тензометры 491 Алюминиевые сплавы — см. Сплавы алюминиевые Амортизаторы 352 [c.537]
Прини.мая во внимание влияние температуры процесса, можно заключить, что для получения детали с максимальной твердостью и минимальной деформацией следует применять низкую температуру азотирования (500— 520°С), при которой глубина будет невелика (до 0,5 мм, обычно 0,2—0,3 мм). [c.335]
Если в одном сечении действует нисколько концентраторов, учитывают влияние наиболее опасного и них и — масштабные факторы, т. е. коэффициенты, учитыЕиющие влияние поперечных размеров вала (принимаются по таб, [. 3.7) Р — коэффициент поверхностного упрочнения, вводится при поверхностной закалке ТВЧ, азотировании, дробеструйном наклепа и в ряде других случаев (принимается по табл. 3.8). [c.57]
Шероховатость оказывает влияние la равномерность и качество слоя цементации, азотирования, циан рования. При определенных высоте неровностей, глубине термообработанного слоя и припуск, снимаемом при шлифовании, может появиться пятнистая твердость поверхности. Качество гальванич ских, лакокрасочных и ины 4 покрытий также зависит от шероховатости поверхностей. Коррозия возникает и распространяется быстре> на грубообработанных поверхностях. [c.226]
Из перечисленных выше способов наиболее эффективно азотирование, которое практически полностью устраняет влияние концентраторов напряжений. Для азотированных деталей коэффициент д чувствительности к концентрации напряжений близок к нулю (т. е. эффективный коэффициент концентрации напряжений к йй 1). Азотирование почти не вызывает изменения формы и размеров деталей. Это позволяет во многих случаях устранить заключительное шлифование и бв,кгс1ммг сопутствующие ему дефекты, снижающие прочность. Кроме того, азотированный слой обладает повышенной коррозие- и термостойкостью. Твердость и упрочняющий эффект в противоположность обычной термообработке сохраняются до высоких температур (500—60б°С). Сочетание этих качеств делает азотирование ценным способом обработки деталей, работающих при повышенных температурах и подвергающихся высоким циклическим нагрузкам и [c.317]
Влияние химической обработки на прочностные свойства зависит от марки стали. Так, химико-термическая обработка деталей из стали 18Х2Н4ВА (азотирование, нитродементация и цементация) существенно не изменяет предела выносливости при симметричном цикле растяжения—сжатия и пульсирующем растяжении. [c.131]
Аналогичные опыты были проделаны на образцах из стали 18Х2Н4ВА. Коленчатые валы двигателей из этой стали азотируются на глубину 0,3—0,4 мм. Показания высокочастотного прибора определяются поверхностной твердостью. Влияние химического состава и повторного азотирования незначительно. [c.142]
Прижоги и шлифовочные трещины характерны для цементированной или азотированной поверхности. Для сталей, цементированных на глубину 1,3 мм, с концентрацией углерода на поверхности 1,2% установлена пропорциональная зависимость между толщиной стружки за один проход и показаниями амплитудно-фазового дефектоскопа ДНМ-500. Для изучения влияния шлифовки цементированной поверхности использовались клинья из стали 18ХНВА. Бруски цементировались при температуре 950°С в твердом карбюризаторе (13% ВаСОз). После цементации они проходили высокий отпуск (/=650 °С, выдержка 3 ч), закалку (при /=780°С, охлаждение в масле), низкий отпуск (при /=170° С, охлаждение на воздухе) и затем шлифовались под наклоном. Характерные зависимости, полученные при испытаниях этих клиньев, показаны на рис. 7-18. [c.144]
При поверхностном азотировании стали вследствие насыщения металла азотом с последующей закалкой и образования химических соединений твердость поверхностного слоя возрастает до HR (58-65). При этом, очевидно, особенно важное влияние на износ набивки может оказьшать геометрия микронеровностей. Результаты обработки профилограмм показывают, что шероховатость поверхности после азотирования снижается почти на два класса, что приводит к весьма интенсивному износу материала сальниковой набивки. С уменьшением высоты микронеровностей ресурс работы сальника увеличивается. [c.85]Проектирование звездочек с вогнутым профилем зубьев, повышение класса чистоты, закалка или цементация рабочих поверхностей зубьев Уменьшение влияния концентраторов напряжений (увеличение радиусов галтелей, исполнение шпоночных канавок с плавным выходом и т. п.), шлифование цапф (тяже-лонагруженных валов по всей длине), поверхностный наклеп галтелей, поверхностная закалка, азотирование Обеспечение условий жидкостного трения, увеличение жесткости опоры, высокая точность изготовления и высокий класс чистоты обработки рабочей поверхности цапфы, нанесение на поверхности опор специальных покрытий для улуч-шения приработки [c.231]
Влияние глубины азотированного слоя на предел выносливости азотированных деталей с концентраторами напряжений и без концентраторов напряжений подобно влиянию глубины цементованного слоя. Цементация, а особенно азотирование резко повышают предел выносливости стальных деталей с концентраторами напряжений, если упрочненный слой непрерывно проходит и по опасным зонам (галтели, отверстия, шпоночные пазы, места проходов отверстий и др.). Применение местного предохранения от азотирования или цементации или удаление упрочненного слоя в местах концентрации напряжений приведет к тому, что в результате химико-термической обработки упрочнения не будет. [c.304]
Рис. 31. Влияние продолжительности проц,есса на глубину слоя (Л) и поверхностную твердость (/7Р) азотированного слоя У сталь марки 38ХМЮА, азотированная при 500° С 2 — сталь марки 34ХНЗМФА, азотированная при 480° С — сталь марки 4Х14Н14В2М, азотированная при 560-630°С. | ![]() |
Рис. 40. Влияние режима азотирования на кавитационную стойкость стали / — сталь марки 38ХМЮА, азотирование по режиму | ![]() |
Для оценки влияния метода азотирования на усталость исследовали образцы, подвергнутые ионному и га овому азотированию ею режимам, обеспечивающим образование диффузионного слоя толщиной 0,13 мм. При газовом азотировании в этом случае необходима выдержка в тече- [c.172]
mash-xxl.info
11.4. Влияние качества поверхности на эксплуатационные свойства деталей
Основные эксплуатационные характеристики деталей. Важнейшими эксплуатационными характеристиками деталей машин являются износостойкость и сопротивление усталости.
Износостойкость определяет сопротивление поверхности детали изнашиванию в процессе эксплуатации. При изнашивании изменяются размеры и геометрическая форма поверхностей, что приводит к изменению характера сопряжении деталей, потере точности относительного расположения деталей и узлов и нарушениям в работе машины.
Сопротивление усталости характеризует способность детали противостоять многократно повторяющимся знакопеременным нагрузкам в процессе эксплуатации. Недостаточное сопротивление усталости приводит к быстрой поломке деталей, вызывая отказ в работе машины.
Условия эксплуатации деталей разнообразны, в связи с чем в некоторых случаях к деталям предъявляют дополнительные требования, такие как коррозионная стойкость, отражательная способность, электрические, магнитные, эстетические свойства и т. д.
При конструировании и в процессе изготовления деталей важно знать, как влияют характеристики поверхностей деталей на их эксплуатационные свойства. Это дает возможность правильно регламентировать требования к поверхностям деталей, избежать необоснованных затрат на их изготовление и уменьшить потери от брака.
Влияние шероховатости поверхности на эксплуатационные свойства деталей. Исследованиями установлено, что шероховатость поверхностей оказывает большое влияние на изнашивание деталей в процессе эксплуатации.
В процессе трения рабочих поверхностей в машинах и механизмах наблюдается начальный, более интенсивный период изнашивания, когда поверхности прирабатываются. Трущиеся поверхности вначале контактируют по вершинам микронеровностей, в результате чего происходят их срезание и пластическое деформирование. К концу приработки высота исходной шероховатости уменьшается на 65…75 %, а площадь фактического контакта возрастает, что приводит к уменьшению контактных давлений. Поэтому интенсивность изнашивания резко падает, и в дальнейшем происходит равномерное изнашивание, определяющее срок службы детали.
Рис. 11.14. Характерная зависимость износа I поверхности детали от шероховатости Rа:
1, 2 –Соответственно при легких
и тяжелых условиях работы
Установлено, что в результате приработки на трущихся поверхностях образуется оптимальная шероховатость, характерная для конкретных условий работы соединения (давление, скорость скольжения, наличие смазочного материала, физико-механические свойства материалов деталей и т.д.). Поэтому, если в процессе обработки деталей на их поверхностях обеспечить шероховатость, близкую к оптимальной, длительность приработки и изнашивание будут наименьшими. Это положение подтверждается зависимостью интенсивности из-нашивания от исходной шероховатости трущихся поверхностей (рис. 11.14).Существование оптимальной шероховатости объясняется следующими обстоятельствами. При наличии на трущихся поверхностях неровностей, высота которых превышает оптимальные значения, возрастают их механическое зацепление, скалывание и срез, в результате чего происходит повышенное изнашивание деталей. При высоте неровностей меньше оптимального значения изнашивание возрастает вследствие более плотного соприкос-новения трущихся поверхностей, приводящего к выдавливанию смазочного вещества, молекулярному сцеплению и схватыванию.
Как отмечалось, оптимальная по износостойкости шероховатость поверхности деталей зависит от вида соединения и конкретных условий их эксплуатации. Эта зависимость определяется путем специальных исследований. Так, для рабочих поверхнос-тей беговых дорожек подшипников качения оптимальна шероховатость Rа = 0,04…0,08 мкм, для зеркала цилиндров двигателей Rа = 0,08…0,32 мкм, для пальца в соединении его с поршнем Rа = 0,16…0,63 мкм, для отверстия в бобышке поршня Rа = = 0,63…1,25 мкм.
На интенсивность изнашивания деталей оказывает влияние не только высота, но и направление неровностей исходной шероховатости трущихся поверхностей. По данным исследований следует, что при легких условиях работы и жидкостном трении лучшие результаты получаются при совпадении направления следов неровностей с направлением перемещения трущихся деталей. В этих условиях имеет место большая площадь контакта поверхностей, разделенных слоем смазочного вещества.
При тяжелых условиях работы, когда давления значительны и смазка недостаточна, рекомендуется создавать на поверхностях пересекающиеся следы неровностей, при которых не происходит полного выдавливания смазочного материала, уменьшается вероятность схватывания и появления задиров.
От шероховатости поверхности существенно зависит сопротивление усталости деталей. Усталостному разрушению металла способствуют отдельные дефекты и неровности на поверхности детали, которые являются источниками концентрации напряжений. При грубой обработке, когда на поверхности имеются глубокие риски, последние выступают в роли первичных очагов концентрации напряжений. Во впадинах неровностей при циклических и знакопеременных нагрузках возникают субмикроскопические трещины, которые в дальнейшем разрастаются и приводят к образованию усталостных трещин и разрушению детали. Имеется общая закономерность, показывающая, что сопротивление усталости выше у деталей, поверхности которых обработаны более тонкими способами и имеют меньшую высоту микронеровностей. Чем грубее шероховатость, тем больше на ней впадин и глубоких рисок, на дне которых концентрируются и собираются корродирующие вещества, и поэтому здесь коррозия поверхности происходит интенсивнее. С уменьшением шероховатости коррозионная стойкость деталей повышается.
Исследованиями установлено, что шероховатость и волнистость поверхностей деталей влияют на точность сопряжений, прочность соединений с натягом, контактную жесткость, герметичность соединений и другие эксплуатационные характеристики отдельных деталей и узлов. Так, например, наличие волнистости в 5…10 раз уменьшает опорную площадь трущихся поверхностей и, следовательно, снижает их износостойкость. Волнистость желобов подшипников качения увеличивает уровень вибраций.
Влияние микротвердости на эксплуатационные свойства деталей. В процессе трения происходит механическое (внедрение) и молекулярное (притяжение, схватывание) взаимодействие поверхностей. Молекулярное взаимодействие сопутствует механическому, и степень их относительного проявления зависит от конкретных условий изнашивания. Но для снижения изнашивания деталей необходимо уменьшить взаимное внедрение трущихся поверхностей, чтобы предотвратить их схватывание. Поэтому повышение микротвердости при механической обработке способствует уменьшению внедрения и контактного схватывания, а следовательно, увеличивает износостойкость трущихся поверхностей.
У
τ, мин
становлено, что в процессе изнашивания исходная микротвердость поверхностного слоя деталей изменяется. В период приработки на трущихся поверхностях не только формируется оптимальная шероховатость, но и создается оптимальная микротвердость поверхностного слоя детали. Исследования показали, что при трении в образцах с более высокой микротвердостью в процессе приработки она снижается до определенного значения (рис. 11.15, кривая1), а в образцах с низкой исходной микротвердостью возрастает примерно до такого же значения (кривая 2). Оптимальная микротвердость трущихся поверхностей зависит от конкретных условий изнашивания.Рис. 11.15. Изменение микротвердости образцов из стали 20 в процессе изнашивания: 1,2 – соответственно исходная микротвердость Н = 4,0 и 1,2 ГПа
Наличие наклепа повышает эксплуатационные свойства трущихся деталей при небольших скоростях и нормальных давлениях. При высоких скоростях скольжения и давлениях наклеп незначительно влияет на износостойкость деталей, хотя в отдельных случаях может и снижать ее.
Теоретическими и экспериментальными исследованиями установлено, что при наклепе деформация поверхностного слоя детали уменьшается главным образом за счет снижения ее пластической составляющей. Поэтому наклеп поверхностного слоя металла, полученный в результате механической обработки, приводит к увеличению контактной жесткости и контактной выносливости деталей, что повышает эксплуатационные характеристики соединений.
Упрочнение поверхностного слоя оказывает большое влияние на сопротивление усталости деталей машин. При этом наклепанный слой препятствует развитию существующих и возникновению новых усталостных трещин. Возникновение новых усталостных трещин в деталях с наклепанным поверхностным слоем происходит под этим слоем, и развитие их наблюдается при более высоких напряжениях и большем числе циклов нагружения по сравнению с деталями, не имеющими наклепа. Следовательно, наклепанный слой уменьшает интенсивность влияния всевозможных геометрических и структурных концентраторов напряжений, повышая тем самым сопротивление усталости.
Наклеп поверхностного слоя деталей при механической обработке снижает в большинстве случаев их коррозионную стойкость. При пластическом деформировании поликристаллического металла в нем создаются микронеоднородности, способствующие возникновению большого количества гальванических микроэлементов. В результате неоднородного деформирования зерен металла накопленная энергия повышается неравномерно и по-разному изменяется электродный потенциал. Ферритные зерна как более наклепанные становятся анодами, а менее наклепанные перлитные зерна – катодами. При этом ускоряется адсорбция и более интенсивно развиваются коррозионные и диффузионные процессы.
Однако при некоторых видах обработки и определенных условиях протекания процесса резания происходит завальцовывание пластически деформируемым ферритом путей проникновения коррозионных сред внутрь металла. В этих условиях наклепанный поверхностный слой может обладать достаточно высокой коррозионной стойкостью.
Влияние остаточных напряжений на эксплуатационные свойства деталей. В настоящее время на основании ряда исследований установлено, что остаточные напряжения в поверхностном слое деталей независимо от их знака не оказывают заметного влияния на износостойкость деталей при трении. Объясняется это тем, что в процессе трения происходит интенсивное пластическое деформирование трущихся поверхностей. Остаточные напряжения, созданные механической обработкой, снимаются в начальном периоде изнашивания, а затем в процессе трения постепенно возникают остаточные напряжения сжатия, которые не зависят от остаточных напряжений в поверхностном слое металла, действовавших до начала трения.
Наиболее заметное влияние остаточные напряжения оказывают на сопротивление деталей усталости. При циклическом нагружении металлов наблюдается пластическая деформация отдельных, наиболее слабых зерен поверхностного слоя. Она сопровождается упрочнением металла и искажением кристаллической решетки. Если напряжения превышают предел выносливости, искажение атомной кристаллической решетки становится столь значительным, что наступает разрыв междуатомных связей по плоскостям скольжения. При этом наблюдаются субмикроскопические нарушения сплошности, т.е. разрыхление металла, которое приводит к возникновению усталостных трещин, а затем и к разрушению деталей.
Исследования показывают, что сжимающие напряжения повышают предел выносливости, а растягивающие – уменьшают его.
Рис. 11.16. Влияние СОТС и методов их подвода при точении на усталостную прочность образцов из титанового сплава ВТ4: – полив СОТС; – распыление СОТС;1– резание всухую;2– сжатый воздух;3– масло «Индустриальное 20»;4– сульфофрезол;5– Г3-3Х
И
МПа)
меются данные о том, что сжимающие остаточные напряжения в поверхностных слоях деталей повышают также надежность соединений с натягом. Нагревание деталей до сравнительно невысоких температур приводит к релаксации остаточных напряжений, и тогда они уже не оказывают влияния на предел выносливости. Из рис. 11.16 следует, что составы СОТС и методы подвода их в зону резания при точении титановых сплавов оказывают заметное влияние на предел выносливости при испытаниях на изгиб вращающихся образцов.При температуре испытаний 20 °С применение СОТС повышает предел выносливости, выраженный числом циклов нагружений N при –1 = 305 МПа:
масляные СОТС – полив в 1,7…2,3 раза, распыление в 1,4…1,9 раза;
эмульсия Р3-СОЖ8 – полив в 3,6 раза, распыление в 3,1 раза;
СОТС НИАТ – полив в 4,3 раза, распыление в 3,8 раза.
Как видно (см. рис. 11.16), водные СОТС увеличивают N в большей степени, чем масла, а полив СОТС – в большей степени, чем их распыление, т.е. наблюдается хорошая корреляция расположения СОТС по их воздействию на формирование благоприятных сжимающих остаточных напряжений и предел выносливости титановых образцов (см. рис. 11.13 и 11.16).
При температуре усталостных испытаний 300 °С воздействие СОТС, применявшихся при обработке, сказывается на повышении стойкости образцов значительно слабее, чем при нормальных температурах.
Ключевые слова и понятия
Обработанная поверхность (ОП), качество ОП, шероховатость ОП, номинальное сечение среза, действительное сечение среза, остаточное сечение среза, теоретический профиль ОП, расчетная высота неровностей поверхности, действительная высота микронеровностей, наклеп, упрочнение, разупрочнение, остаточные напряжения, износостойкость, предел выносливости.
Контрольные вопросы
Какими показателями характеризуется качество обработанной поверхности?
От каких факторов зависит расчетная высота микронеровностей?
В чем причины несоответствия расчетных и действительных значений микронеровностей обработанной поверхности?
Как режимы резания влияют на шероховатость обработанной поверхности?
Перечислите основные причины возникновения наклепа.
Каково воздействие силового и теплового факторов процесса резания на величину и знак остаточных напряжений?
На какие основные эксплуатационные характеристики детали оказывают влияние шероховатость обработанной поверхности, наклеп и остаточные напряжения?
298
studfiles.net
Влияние шероховатости поверхности на износ
В технологии ОМД бытует мнение «чем меньше шероховатость, тем лучше». С другой стороны на зеркальных поверхностях смазка не поддерживается. Как решить эту проблему? Например, иглы для прессования. Создавать оптимальную шероховатость. Получение управляемого рельефа.
Рисунок 23 – График зависимости величины износа
от шероховатости поверхности
Основные способы повышения износостойкости
1. Правильный подбор технологической смазки.
2. Уменьшение давления на поверхности трения.
3. Увеличение твердости металла инструмента.
4. Повышение качества поверхности инструмента.
5. Эффективные средства повышения поверхностной твердости:
Вид обработки | HV |
Цементация и обработка ТВЧ | 500-600 |
Азотирование | 800-1200 |
Хромирование | 1200-1400 |
Плазменное направление твердых сил | 1400-1600 |
Боросилицирование | 1800-2000 |
Эффект безизносности (Крагельский И.В., Гаркунов Д.Н.) избирательный перенос при трении. Самовосстанавливающиеся узлы.
Гидродинамический ввод смазки при волочении
Рисунок 24 – Гидродинамический ввод смазки при волочении
1 – Проволакиваемое изделие; 3 – напорная втулка; 5 – резервуар для смазки; 7 – уплотняющее кольцо.
2 – волоки; 4 – микрозазор; 6 – смазка;
При волочении изделия 1 в резервуаре для смазки происходит захват смазки шероховатой поверхностью изделия. При этом смазка затягивается в микрозазор 4. Внутренняя поверхность напорной втулки 3 выполнена с минимальной шероховатостью с целью снижения сопротивления движению смазки. По мере волочения микрозазор 4 будет заполнен смазкой так ,что в итоге в нем образуется давление смазки. Величину давления смазки рассчитывают так, чтобы на входе в зону деформации волоки 2 оно было равно величине рабочих контактных напряжений. Варьируют величиной зазора 4, длиной напорной втулки 3, скоростью волочения и вязкостью смазки 6. В этом случае смазка будет вытекать через зазор между волокой и поверхностью изделия, образуя, таким образом, гидродинамический эффект. Трущиеся поверхности будут полностью разделены слоем смазки.
Необратимые деформации
Виды необратимых деформаций
Смятие или локальная пластическая деформация элементов поверхности деформирующего инструмента — наиболее распространенный вид необратимых деформаций при эксплуатации инструмента. При смятии происходит изменение формы и размеров наиболее нагруженных инструментов сверх допускаемых. Процесс смятия наиболее интенсивно развивается в местах совместного действия максимальных температур и давлений, затрагивая значительные объемы металла инструмента.
При смятии уменьшается высота выступающих элементов инструмента, увеличиваются размеры полости ручьев в плане, искажается их конфигурация; наблюдается также изгиб пуансонов, игл, оправок, деформация хвостовиков и блоков под рабочие вставки. Например, при штамповке осадкой наблюдается смятие стенок матрицы, знака, выталкивателя и выступов матрицы и пуансона. «Поднутрение» знака неизбежно приводит к застреванию поковок.
Деформирующий инструмент выходит из строя не только из-за смятия, но и из-за образования единичных трещин и последующего хрупкого разрушения в связи с динамическим и циклическим воздействием сил. На рабочих поверхностях инструмента сложной конфигурации с глубокими вырезами обычно обнаруживаются единичные мелкие и глубокие трещины в углах, на вертикальных стенках, в основании углублений. Если трещины неглубокие, то работоспособность инструмента будет определяться скоростью их распределения в длину и глубину. Образование глубоких трещин и разрушение характерны для хрупкого инструмента. Образование единичных трещин и хрупкое разрушение инструмента вызывается главным образом концентрацией напряжений в местах резких переходов, неблагоприятной схемой напряженного состояния, наличием в металле инструмента металлургических дефектов. Например, молотовые штампы часто выходят из строя в результате образования усталостных трещин и последующего разрушения в местах сопряжения хвостовика с заплечиками под действием ударно-циклических нагрузок.
Современная теория разрушения металлов рассматривает разрушение не как мгновенный акт, а как процесс развития трещины под действием напряжений. Причем, хрупкое разрушение, вызываемое периодическими пластическими сдвигами, наступает тогда, когда исчерпан весь ресурс вязкости металла инструмента. Впервые такое предположение выдвинул Гриффитс. Он рассмотрел напряженное состояние плоской плиты единичной толщины со сквозной трещиной эллиптического сечения. Такая трещин обладает поверхностной энергией. Вблизи трещины упругой механической решетки снимается и освобождается упругая энергия.
Рисунок 25 – Пластинка единичной толщины с микротрещиной длиной 2L
Обладает поверхностной энергией
Растягивающие напряжения снижают упругую энергию поля на величину . Поможно найтиLкр трещины, после которой трещина начинает беспрепятственно расти при WУ > WП .
Найдем экстремум функции .
Рисунок 26 – График зависимости длины трещины от энергии.
Критическое значение длины трещины определиться по формуле:
Предельное значение напряжения по формуле:
Опуская промежуточные выводы удельную энергию S заменим на работу пластической деформации А, при которой происходит разрушение металла образца. Тогда и для сопоставления двух материалов
studfiles.net
Дефекты азотирования – Энциклопедия по машиностроению XXL
Важнейшим дефектом азотирования является повышенная хрупкость азотированного слоя. При азотировании возможна деформация изделий и в ряде случаев коробление. [c.153]ДЕФЕКТЫ АЗОТИРОВАНИЯ И ИХ ПРЕДУПРЕЖДЕНИЕ [c.108]
Рис. 9.46. Общий вид (a) разрушенного диска I ступени КНД двигателя НК-8-2у, (б) рельеф его усталостного излома, образованный от дефекта материала в виде включения TiN, и (в) структура материала в зоне нитридного включения. Цифры /, 2, 3 отвечают последовательно зонам дефекта, усталости и долома. Цифры I, II, ///характеризуют различные структуры азотированного слоя | ![]() |
Азотированные изделия — Дефекты 7 — 579 Аккумуляторные батареи — см. Батареи аккумуляторные [c.11]
Растрескивание (шелушение азотированного слоя изделий) Внутренние напряжения вследствие резкого перехода от азотированного слоя к сердце-вине Предупреждение дефекта медленное охлаждение после азотирования или азотирование с отпуском. Исправление дефекта отпуск при 570—580° С в течение 4—5 час. в печи с постоянной атмосферой аммиака [c.579]
Хрупкость (выкрашивание поверхности азотированного слоя) Чрезмерное насыщение нитридами тонкого слоя поверхности вследствие крупнозернистости структуры и обезуглероживания поверхности при предварительной термообработке Предупреждение дефекта ступенчатый процесс азотирования (1-я ступень — 510—520 С, б—10 час. 2-я ступень — 570—580° С, 15-20 час. и 3-я ступень — 510 -520° С, 2-4 часа). Исправление дефекта отпуск в атмосфере аммиака при температуре 570—580° С в течение 4 -5 час. или при 630—650° С в течение 2 час. [c.580]
Азотирование снижает вязкость стали и повышает ее прочность, ослабляет влияние поверхностных дефектов на предел выносливости и существенно повышает предел выносливости стали, особенно у тонких деталей и при работе в некоторых коррозионных средах. Азотирование повышает сопротивление задирам и налипанию металла под нагрузкой, особенно при повышенных температурах. [c.175]
Поверхность колец из азотированной стали устойчива против износа, но этим качеством обладает только верхний слой глубиной 0,3—0,5 мм. Поэтому при износе или дефектах общей глубиной более 0,15—0,2 мм кольца из азотированных сталей надо заменять, так как при их обработке основной азотированный слой будет снят. [c.390]
Фокусом излома называют малую зону вокруг места возникновения начальной микроскопической трещины усталости (рис. 20.5). Чаще всего фокус излома располагается на поверхности изделия в местах концентрации напряжений. Концентраторы напряжений могут быть как конструктивными, так и в виде поверхностных дефектов (царапины, трещины, неметаллические включения и т. п.). При наличии сильных внутренних дефектов или при поверхностном упрочнении (цементация, азотирование, наклеп и т. д.) фокус излома может располагаться и под поверхностью детали. [c.335]
Преимущества и недостатки азотирования. По сравнению с цементацией азотирование имеет ряд преимуществ и недостатков. Температура азотирования (480—540° С) гораздо ниже температуры цементации и закалки высокая твердость поверхностного слоя у азотированных деталей получается сразу, без последующей закалки, что позволяет избежать дефектов, обычно сопутствующих закалке после цементации. [c.286]
Дефекты поверхности (трещины, риски, следы коррозии, обезуглероживание) недопустимы, так как они сильно снижают усталостную прочность. Этим объясняются высокие требования к качеству поверхности пружинной проволоки и ленты. Поверхность пружин, работающих в тяжелых эксплуатационных условиях, обрабатывается обточкой, бесцентровой шлифовкой или полировкой. Ряд пружин подвергают цементации или азотированию поверхности. [c.230]
Нарушения температурного режима при азотировании также могут привести к возникновению ряда дефектов на насыщенной поверхности изделия. Так, слишком низкая температура процесса дает крайне малую толщину насыщенной пленки, причем такой дефект не выявить обычными методами контроля (проверкой твердости азотированного слоя), однако он крайне негативно отражается на эксплуатационных свойствах изделия. Подобный дефект может быть устранен повторным азотированием при правильной температуре процесса. Завышенные температуры азотирования применимы только для быстрорежущих и нержавеющих сталей, в других случаях они приводят к снижению твердости поверхности, которая уже не может быть восстановлена повторными азотированиями. [c.476]
Кроме того, при ионном азотировании химически активными центрами являются все многочисленные дефекты кристаллической структуры поверхностной зоны металла, образованные в результате радиационного воздействия ионной бомбардировки поверхности. Это способствует интенсификации реакций взаимодействия между газом и металлом и ускоряет диффузионный процесс. [c.108]
При исследовании макрошлифа можно определить форму и расположение зерен в литом металле (рис. 1, б) волокна (деформированные кристаллиты) в поковках и штамповках дефекты, нарушающие сплошность металла (усадочная рыхлость, газовые пузыри, раковины, трещины и т. д.) химическую неоднородность сплава, вызванную процессом кристаллизации или созданную термической или химикотермической (цементация, азотирование и т. д.) обработкой. [c.12]
При исследовании установлено, что при определенных условиях существует допустимый предел давления газовой смеси, превышение которого вызывает переход аномального тлеющего разряда в нормальный. При нормальном тлеющем разряде получаются дефекты при азотировании, так как в этом случае не вся поверхность детали охватывается свечением. [c.123]
Ускорение диффузии при ионном азотировании, так же, как и при ионном легировании кремния [91 ], видимо, связано с действием указанных ниже основных факторов, возникающих в результате ионной бомбардировки насыщаемой поверхности. Происходит локальный перегрев очень тонкого поверхностного слоя, в результате чего возникает температурный градиент. Если энергию, получаемую за счет ионной бомбардировки, преобразовать в тепловую, то она будет соответствовать крайне высокой температуре. В первые минуты насыщения в результате внедрения ионов азота в насыщаемую поверхность возникает высокий градиент концентрации. Это подтверждается сравнительным спектральным исследованием поверхности образцов технического железа [16]. На бомбардируемой поверхности образуется большое количество дефектов кристаллической решетки и градиент их в направлении [c.123]
Азотированные детали отличаются хорошей сопротивляемостью действию переменных напряжений и обладают высоким пределом выносливости, что объясняется не только увеличением твердости поверхности, но и созданием в ней напряжений сжатия, которые уменьшают напряжения растяжения и, создавая выгодную эпюру напряжений, понижают вредное действие концентраторов напряжений, — поверхностных дефектов, резких переходов сечений и т. д. Детали после азотирования приобретают значительную сопротивляемость коррозии на воздухе, а также в пресной и соленой воде. Следует отметить, что даже самое легкое шлифование (на 0,05 мм), удаляя сплошной слой нитридов, значительно понижает сопротивляемость азотированных деталей коррозии. [c.270]
Наиболее часто встречающийся дефект при шлифовании хромированных деталей — это появление шлифовочных трещин под слоем хрома на стальных закаленных и азотированных деталях. Появления таких трещин можно избежать только при строгом соблюдении определенных режимов обработки. [c.146]
При химико-термической обработке дефектами являются недостаточная степень насыщения поверхностного слоя (углеродом при цементации,азотом при азотировании и т. д.), а также недостаточная глубина насыщения. [c.181]
Дефекты механической обработки. Наиболее опасным дефектом механической обработки являются шлифовочные трещины как следствие шлифования изделий из некоторых марок сталей, склонных к их образованию закаленных высокоуглеродистых и легированных. Они возникают также на цементированных, азотированных и хромированных изделиях. [c.181]
При азотировании могут быть следующие дефекты а) коробление, б) растрескивание азотированного слоя, в) пятнистая и пониженная твёрдость, г) хрупкость азотированного слоя. [c.80]
Повышение усталостной изгибной прочности вала достигается накаткой роликами галтелей шеек после срезания азотированного слоя на галтелях. Для выявления поверхностных, и внутренних дефектов коленчатый вал подвергают гаммаграфированию и магнитному контролю. [c.26]
К дефектам, возникающим при азотировании, относятся шелушение азотированной поверхности на глубину до 0,01—0,05 мм дефект исправимый, так как при чистовом, отделочном шлифовании поверхности после азотирования слой поврежденного металла удаляют полностью [c.181]
На азотированном слое могут появиться цвета побежалости, что не является дефектом. Не следует удалять цвета побежалости, пескоструйной обработкой детали, так как это может привести к шелушению и пористости азотированного металла. [c.181]
Одним из наиболее часто встречающихся дефектов. азотированного слоя на стали типа 38ХМЮА является высокая поверхностная хрупкость. При этом найдено, что хрупкость распространяется на глубину 0,03—0,05 м.м. Основной причиной высокой хрупкости азотированного слоя является сильное пересыщение поверхностного слоя азотом. Борьба с хрупкостью ведется следующими методами. [c.222]
Дефектом азотированного слоя является высокая поверхностная хрупкость наружной кромки на глубину 0,03 — 0,05 мм. Высокая хрупкость может являться следствием больщой концентрации азота (10 — 12%) и скопления в поверхностном слое значительного количества нитридов. [c.80]
Из перечисленных выше способов наиболее эффективно азотирование, которое практически полностью устраняет влияние концентраторов напряжений. Для азотированных деталей коэффициент д чувствительности к концентрации напряжений близок к нулю (т. е. эффективный коэффициент концентрации напряжений к йй 1). Азотирование почти не вызывает изменения формы и размеров деталей. Это позволяет во многих случаях устранить заключительное шлифование и бв,кгс1ммг сопутствующие ему дефекты, снижающие прочность. Кроме того, азотированный слой обладает повышенной коррозие- и термостойкостью. Твердость и упрочняющий эффект в противоположность обычной термообработке сохраняются до высоких температур (500—60б°С). Сочетание этих качеств делает азотирование ценным способом обработки деталей, работающих при повышенных температурах и подвергающихся высоким циклическим нагрузкам и [c.317]
Некачественная термическая и химико-термическая обработка поверхности зубьев иногда приводит к отслаивамию поверхностных частиц металла. Отслаивание возможно из-за дефектов поверхностного слоя азотированных или цементованных с последующей поверхностной закалкой зубьев или из-за недостаточной прочности сердцевины, вследствие чего при больших нагрузках происходит продавливаиие хрупкой кромки. Наличие перегрузок способствует отслаиванию. [c.287]
Вздутия иа поверхности Шлаковые включения, рвспо ложенные у поверхности азотированного изделия Предупреждение дефекта тщательный контроль стали на шлаковые включения [c.579]
Неравномерная (пятнистая) твёрдость (мягкие места на поверхности азотированного изделия) Наличие отдельных участков, покрытых оловом, на азотируемой поверхности изделия Предупреждение дефекта фосфатирова-ние перед азотированием и тщательная подготовка поверхности изделия [c.580]
ПИЯ развития отпускной хрупкости стали в процессе азотирования. Ввиду того что легирование стали алюминием насто приводит. к металлургия, дефектам (неметал-лич. включения, волосовины, шиферный излом), разработана сталь ЗОХЗВА, не содержащая алюминия. Хим. сост. и механич. св-ва С. к. а, приведены в табл. 1 и 2. [c.199]
mash-xxl.info
Влияние шероховатости.
11
Поверхность реальных твердых тел никогда не бывает идеально гладкой, а покрыта многочисленными неровностями различной формы. Размеры неровностей изменяются в очень широких пределах – от нескольких межатомных расстояний до десятков микрон, а в отдельных случаях – до нескольких миллиметров. Влияние шероховатости на смачивание изучено наиболее подробно для поверхностей с неровностями (выступами, впадинами), средняя глубина или высота которых составляет от десятых долей до нескольких десятков микрометров.
Шероховатость твердой поверхности характеризуется ее микрорельефом, который обычно представляет сложное хаотическое чередование разнообразных выступов и впадин. Измеряют микрорельеф с помощью профилографов, которые могут выявлять неровности примерно до 1 мкм. Более тонкие детали выявляются другими методами, в частности с помощью интерференционных и электронных микроскопов.
Для характеристики микрорельефа обычно используют коэффициент шероховатости К – отношение фактической площади поверхности (с учетом площади впадин и выступов) к проекции на горизонтальную плоскость. Площадь участка, выбираемого для расчета коэффициента шероховатости, должна быть достаточно велика по сравнению с размерами отдельных неровностей, иначе коэффициент шероховатости не будет усредненной характеристикой поверхности.
Из определения коэффициента шероховатости очевидно, что всегда
К > 1. После шлифовки металлов (алюминия, бронзы, некоторых марок стали и чугуна) К = 1,005. Для грубодисперсных структур, волокнистых и пористых материалов коэффициент шероховатости может быть значительно больше.
Обычные методы не позволяют измерить для шероховатой поверхности истинный краевой угол θ, т.е. угол наклона поверхности жидкости к поверхности твердого тела в точке на линии смачивания (угол ЕСF на рис.1). Фактически измеряют углы наклона поверхности жидкости к плоскости, на которую проецируется профиль твердой поверхности (угол GAC). Измеряемый статический краевой угол θш называют макроскопическим краевым углом (или макрокраевым углом).
.
При анализе смачивания необходимо прежде всего найти зависимость равновесного макрокраевого угла θш на шероховатой поверхности от коэффициента шероховатости К. Рассмотрим условия равновесия в трехфазной системе твердое тело – жидкость – газ с учетом шероховатости подложки. Примем, как и при выводе уравнения равновесного краевого угла на идеально гладкой поверхности, что при смачивании изменяется только свободная поверхностная энергия системы, а влиянием потенциальной энергии жидкости можно пренебречь. Примем также, что размеры капли значительно больше среднего размера неоднородностей λ; тогда можно считать, что поверхность жидкости на границе с газом сферическая. Это условие выполняется достаточно точно, если λ<< a, где a2 – капиллярная постоянная жидкости (a2 = H0 r = 2σLA /ρL g). Тогда при увеличении смоченной поверхности на бесконечно малую площадь dωSL изменение свободной поверхностной энергии . Здесь, как и ранее, ωSA, ωSL, ωLA – площади контакта соответствующих фаз (твердое тело, жидкость, газ). Из условия минимума свободной энергии находим, что равновесие достигается при. Для шероховатой поверхности, где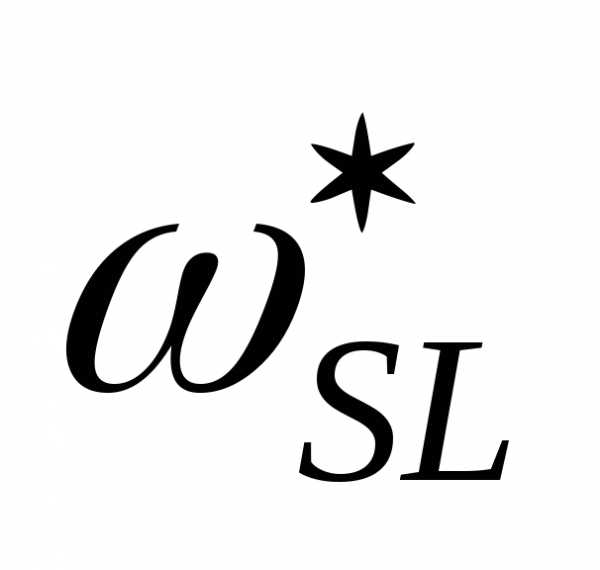
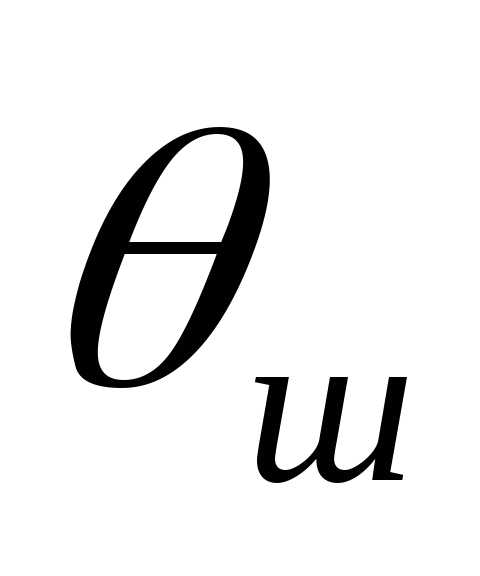
(1)
Соотношение (1) называется уравнением Венцеля – Дерягина.
Уравнение (1) позволяет сделать следующие выводы. В отсутствие смачивания (θ0 > 90˚) увеличение шероховатости приводит к увеличению макрокраевого угла. Если жидкость смачивает данный материал (90˚ > θ > 0˚), увеличение шероховатости вызывает уменьшение макрокраевого угла θш.
При достаточно
большом коэффициенте шероховатости и
выполняется термодинамическое условие
полного смачивания.
При
экспериментальном исследовании влияния
шероховатости на смачивание в ряде
случаев получено удовлетворительное
согласие с приведенными выше теоретическими
выводами.
Рис.2. Теоретические зависимости (по уравнению (1) ) краевых углов θш от коэффициента шероховатостиКдля равновесных краевых углов0˚: 1 – 120; 2–
100; 3 – 90; 4 – 75; 5 – 45˚.
При контакте воды с подложками, покрытыми сажей, триоксидом мышьяка или порошком ликоподия, наблюдалось заметное возрастание макрокраевых углов в соответствии с уравнением (1). Для краевых углов 90˚ > θ > 0˚ уменьшение макрокраевого угла θш при увеличении коэффициента шероховатости наблюдалось в ряде случаев. Например, раствор этилксантата калия образует на шлифованной поверхности пирита макрокраевой угол 18˚, а на полированной – 59˚; на тех же поверхностях раствор бутилксантата калия образует краевые углы 20˚ и 79˚. Полированный графит смачивается расплавами солей и оксидов (NaF, ZrF2, ZrO2) гораздо хуже, чем грубо обработанный.
При контакте воды с нержавеющей сталью макрокраевой угол при значительном изменении коэффициента шероховатости оставался постоянным – 90˚; в соответствии с уравнением (1) это единственный случай, когда шероховатость не должна влиять на макрокраевой угол.
Приведенные данные в целом согласуются с выводами, полученными на основе термодинамического анализа влияния шероховатости. Вместе с тем экспериментальные значения макрокраевых углов не всегда удовлетворительно согласуются с уравнением (1). Одна из причин этих расхождений заключается в следующем. На реальной твердой поверхности может быть сеть сообщающихся друг с другом микроканавок. Поместим на такую поверхность каплю, объем которой соизмерим с общим объемом канавок, пересекающих периметр смачивания. Если жидкость смачивает материал подложки (90˚ > θ), то жидкость под действием капиллярных сил будет вытекать из капли вдоль канавок. При неизменной площади основания капли ее объем уменьшится; в результате уменьшится и макрокраевой угол θш, который в данном случае является краевым углом отекания θR. Напротив, при θ > 90˚ капиллярные силы втягивают жидкость вдоль канавок в направлении от периметра смачивания к центру основания капли, что может привести к увеличению макрокраевого угла натекания θА.
Форму неровностей обычно характеризуют углом наклона α различных участков твердой поверхности к горизонтальной плоскости, точнее – к той плоскости, на которую проецируется реальная поверхность при расчете коэффициента шероховатости (рис.1). Угол наклона (крутизна микрорельефа) представляет локальную характеристику рельефа твердой поверхности. Крутизна может сильно меняться при переходе от одного участка поверхности к другому. В общем случае нет прямой зависимости между коэффициентом шероховатости и крутизной. В частном случае, когда микрорельеф представляет периодическое чередование параллельных гребней и канавок с поперечным сечением в виде одинаковых равнобедренных треугольников, .
Наряду с крутизной микрорельефа α большую роль играет расположение микроканавок и микровыступов. Течение жидкости вдоль канавок происходит беспрепятственно и быстрее, чем по гладкой твердой поверхности. Рассмотрим более сложный случай, когда параллельные канавки и выступы расположены перпендикулярно к направлению течения жидкости, слой жидкости на границе с воздухом ограничен цилиндрической поверхностью, причем образующая цилиндра параллельна направлению выступов и канавок. Макрорельеф поверхности не имеет изломов (см. рис.1). При движении линии смачивания по такому рельефу угол наклона жидкости к поверхности твердого тела, т.е. динамический краевой угол θd, периодически изменяется. На тех участках канавки, где поверхности жидкости и твердого тела наклонены в одну сторону (например, в точке С), θd = θш – αС (αС – крутизна наклона микрорельефа в точке С). Если поверхности жидкости и подложки наклонены в разные стороны (в точке А), то θd = θш + αА.
В отсутствие посторонних сил перемещение линии смачивания при натекании может происходить только в том случае, если при этом происходит непрерывное уменьшение динамического краевого угла. Перемещение прекратится, если в каких-либо двух положениях линии смачивания краевые углы больше, чем в промежуточном положении. Для каждой данной канавки имеется такое положение линии смачивания, при котором динамический краевой угол принимает минимальное значение (θd)min. Это значение достигается в тот момент, когда линия смачивания проходит через точку, в которой крутизна микрорельефа максимальна (αmax). При этом (θd)min = θш – αmax. Дальнейшее перемещение линии смачивания в пределах этой же канавки привело бы к увеличению динамического краевого угла. Такой процесс сопровождался бы увеличением свободной энергии системы, поэтому самопроизвольно (без дополнительных воздействий) он протекать не может.
Анализ экспериментальных данных показывает, что шероховатость влияет на макрокраевые углы при высоте неровностей не менее 0,5 мкм. Максимальный гистерезис краевых углов, обусловленный влиянием шероховатости, не может превышать 2αmax (αmax – максимальная крутизна).
studfiles.net