Восстановление деталей металлизацией: Ремонт деталей металлизацией
alexxlab | 31.05.2023 | 0 | Разное
Восстановление деталей металлизацией
Металлизацией называется процесс нанесения на поверхность детали расплавленного и распыленного металла (рис. 17.5). Металл в виде проволоки расплавляется в специальных аппаратах-металлизаторах. Металли-зационные аппараты по способу получения тепловой энергии для нагрева распыляемого материала подразделяются на электродуговые, газовые, высокочастотные и плазменные.[ …]
Расплавленный металл распыляется струёй сжатого воздуха 0,5-0,6 МПа, выходящего из металлизатора, и мельчайшие частицы распыленного металла со скоростью 80- 200 м/с наносятся на поверхность детали. Толщина наносимого слоя колеблется от 0,3 до 10 мм.[ …]
Соединение распыленных частиц между собой и с поверхностью деталей происходит за счет механических и частично молекулярных связей. Для хорошего сцепления частиц с деталью поверхность под металлизацию тщательно подготавливают: очищают от влаги, окислов, придают шероховатость путем пескоструйной обработки, обдувки металлической крошкой, нарезания «рваной» резьбы и обезжиривают.
Поверхности деталей, не подлежащих металлизации, изолируют картоном, пергаментной бумагой, специальной пастой; отверстия, шпоночные канавки, пазы закрывают деревянными или резиновыми пробками. Воздух, необходимый для распыления металла, очищается от влаги и масла в специальных масловлагоотделителях.[ …]
Цилиндрические детали при металлизации устанавливают в патроне или центрах токарного станка, а металлизатор – на суппорте станка. Металлизация плоских деталей производится на столе, металлизатор при этом находится в руке рабочего.[ …]
Металлизационный слой обладает достаточно высокой износостойкостью при жидкостном и полужидкостном трении, но невысокой прочностью сцепления покрытия с напыляемой поверхностью. Поэтому металлизацией нельзя восстанавливать детали, работающие при больших удельных давлениях на сдвиг и сжатие (зубья шестерен, кулачки распредвалов и т. п.).[ …]
Электродуговая металлизация производится аппаратами, в которых плавление проволок осуществляется электрической дугой. Для электродуговой металлизации применяют аппараты ЭМ-3 А, ЭМ-9, ЭМ-10, ЭМ-12-67 (ручные) и ЭМ-6, ЭМ-12 и МЭС-1 (станочные), (рис. 17.5).[ …]
Г а з о в а я металлизация производится аппаратами ГИМ-2М, МГИ-1-57, МГИ-2-65 и др., в которых проволока плавится ацетилено-кислород-ным пламенем (рис. 17.6, а).[ …]
Высокочастотная металлизация основана на плавлении проволоки токами высокой частоты (рис. 17.6, б). В высокочастотном аппарате проволока специальным механизмом подается непрерывно в направлении конусного отверстия концентратора вихревых токов. Попадая в отверстие, проволока плавится и распыляется сжатым воздухом. Процесс ведется металлизаторами МВЧ-1, МВЧ-2 и МВЧ-3.[ …]
Рисунки к данной главе:
Схема устройства распылительных головок металлязатора |
Вернуться к оглавлению
Восстановление деталей металлизацией – презентация онлайн
Похожие презентации:
Восстановление корпусных деталей
Восстановление деталей сваркой и наплавкой
Восстановление деталей синтетическими материалами
Восстановление деталей. Гальваника
Техника транспорта, обслуживание и ремонт. Выбор рационального способа восстановления. (Тема 6.1)
Способы восстановления деталей
Ремонт деталей машин. (Тема 4.3)
Механическая обработка восстановленных деталей
Ремонт автомобилей. Восстановление деталей сваркой и наплавкой. (Тема 3.4)
Восстановление деталей пайкой
1. ВОССТАНОВЛЕНИЕ ДЕТАЛЕЙ
МЕТАЛЛИЗАЦИЕЙВосстановление деталей металлизацией.
Металлизация или газотермическое напыление — это
процесс нанесения расплавленного и распыленного
металла на восстанавливаемую поверхность детали с
целью компенсации ее износа.
Распыление – потоком воздуха или специального газа с
большой скоростью.
Напыляемые частицы:
– деформируются,
– внедряются в шероховатости и микронеровности,
– сцепляются механически с основным металлом,
в некоторых локальных точках отдельные частицы могут
свариться с основным металлом.
Достоинства:
– незначительное нагревание детали (до температуры
200°С),
– высокая производительность процесса,
-толщина напыленного металла (от 0,1 до 10 мм),
– простота технологического процесса.
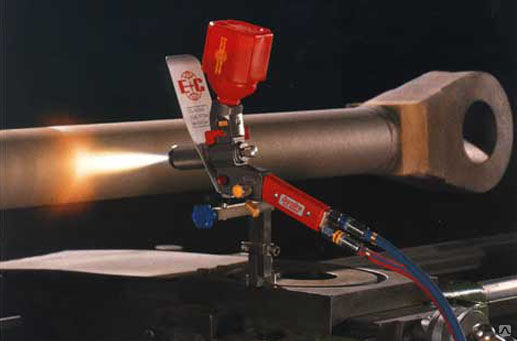
Недостатки:
– более низкая сцепляемость;
– частицы напыленного металла, связанны друг с другом
механическими связями;
– необходимость подготовки поверхности к нанесению
покрытия
и
сложность
обработки
нанесенного
покрытия;
– напыленный металл не выдерживает ударные
нагрузки.
Известны следующие виды металлизации:
– газопламенная,
– электродуговая,
– высокочастотная
– плазменная и др.
Последовательность металлизации.
Механическая обработка изделий. Создание на
поверхности требуемой шероховатости (нарезка «рваной»
резьбы, насечка поверхности, нарезка резьбы роликом).
Обезжиривание. Чугунные детали кроме обезжиривания,
подвергают обжигу (260…5300С)
Струйная
обработка.
Покрываемую
поверхность
подвергают дробеструйной обработке.
Напыление.
Окончательная механическая обработка, в том числе
лезвийным инструментом, или шлифование, требует
особых решений новых проблем, так как при шлифовании
нет привычной искры, шлифовальные круги быстро
засаливаются и т.
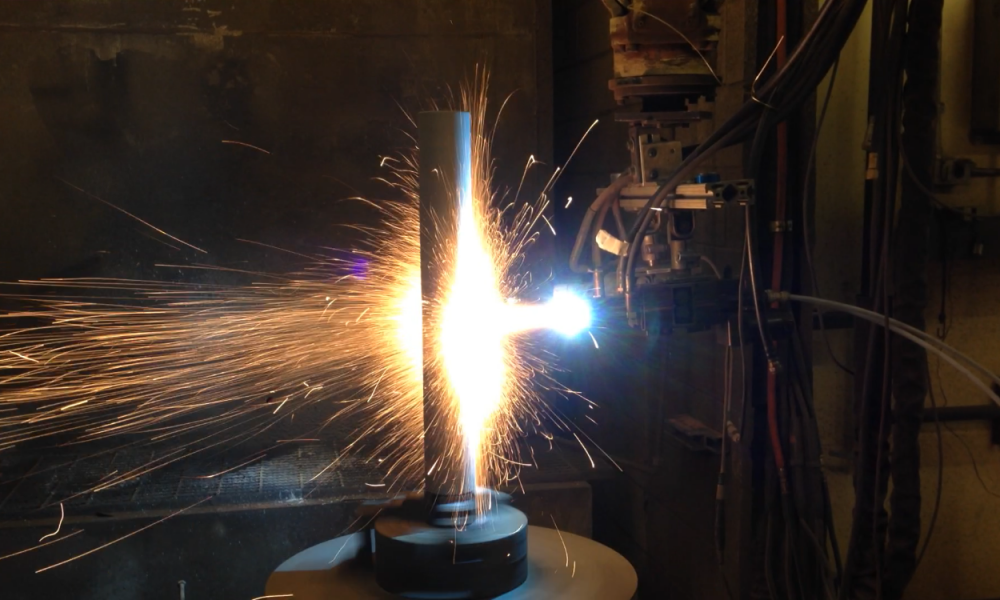
Электродуговое напыление.
Процесс расплавления металла осуществляется
посредством горения электрической дуги между двумя
электродными проволоками,
распыление осуществляется струей сжатого воздуха
(0,6 МПа)
Расстояние от сопла до детали 80… 100 мм;
Толщина наносимого слоя до 5 мм,
Высокочастотное напыление.
При этом способе вместо проволоки используются
стержни из углеродистой стали, которые помещают в
высокочастотный индуктор.
Стержни расплавляются токами высокой частоты,
распыляются и напыляются струей сжатого воздуха
Преимущества:
– выгорание основных химических элементов снижается
в 4…6 раз,
2…3 раза, что увеличивает прочность сцепления и
уменьшает расход материала.
Недостатком этого процесса являются
– сложность
– высокая стоимость высокочастотных установок,
– сравнительно невысокая производительность по
сравнению с другими способами металлизации.
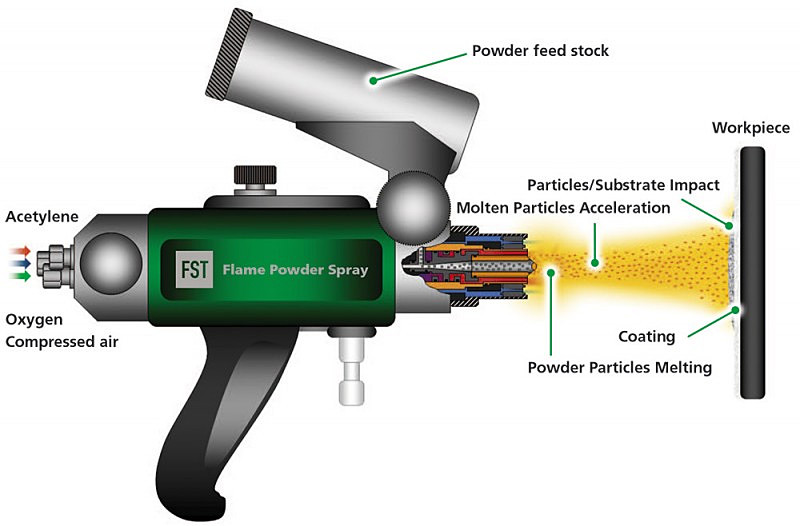
Плазменное напыление.
Основные отличия:
– более высокая температура по сравнению с другими
источниками расплавления и большая мощность,
– значительное повышение производительности
процесса,
– возможность наносить и расплавлять любые
жаростойкие и износостойкие материалы
Благодаря более высокой температуре наносимого
материала и большей скорости полета, прочность
соединения покрытия с деталью выше, чем при других
способах металлизации.
Порошок в зону дуги
подается
транспортирующим газом
(азотом), расплавляется и
переносится на деталь.
Газопламенное напыление.
При газопламенном напылении расплавление электродной
проволоки производится струей ацетилено-кислородного
пламени.
Распыление расплавленного металла и нанесение его на
изношенную деталь производится струей сжатого воздуха
Газопламенное нанесение порошковых материалов.
Методы газопламенного нанесения покрытий:
напыление без последующего оплавления,
-применяемое для получения покрытий, которые не
подвергаются знакопеременным нагрузкам, сильному
нагреванию при толщине покрытий до 2 мм на сторону;
напыление с одновременным оплавлением,
-используемое для восстановления деталей с износом до
3.

серого чугуна, конструкционных
напыление с последующим оплавлением,
для восстановления деталей с износом до 2,5 мм на
Процесс
нанесения
покрытий
производится
с
использованием специальных установок УПТР-1-78М,
снабженных сварочными горелками, которые служат для
смешивания горючего газа (ацетилена или пропана) с
кислородом и получения газового пламени.
Технологический процесс состоит из следующих этапов:
– нагревание детали до температуры 200…250°С;
– нанесение подслоя;
-нанесение слоев, позволяющих получить покрытие с
необходимыми физико-механическими свойствами.
Газопламенному напылению подвергаются маховики,
валы КПП, опоры коренных подшипников, посадочные
пояски и опорные буртик гильзы цилиндров, нижняя
головка шатуна, шейки под подшипник, шейки коленвала
и др.
Детонационное напыление
Детонационные покрытия формируются с помощью
ударных
волн,
периодически
инициируемых
микровзрывами смеси кислорода и ацетилена.
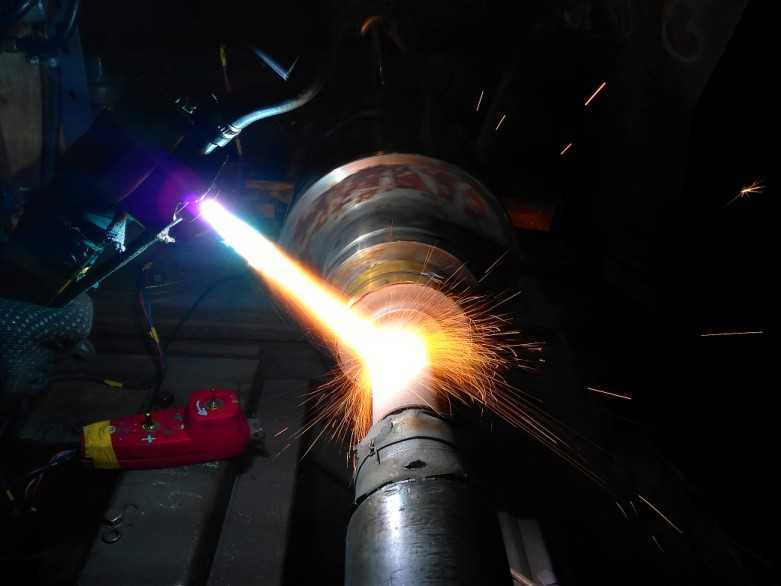
Установка состоит из камеры сгорания, выполненной
совместно с водоохлаждаемой трубкой-створом 5,
электрической свечи 2, газопроводом по кислороду и
ацетилену 1, порошкового дозатора 4 и источника тока 3.
Цикл взрыва длится 0,23 с, т.е. в секунду производится
3…4 взрыва.
При каждом взрыве на ограниченный участок
поверхности наносится покрытие толщиной 6,3 мкм.
Во взрывной волне газ сжимается до давления десятков
атмосфер с температурой несколько тысяч градусов.
Несмотря на высокие температуры, развивающиеся в
месте контакта частиц порошка с подложкой, деталь не
нагревается до температуры более 200″С.
Уровень шума при работе детонационной установки —
140 дБ, что выше предела допустимого техникой
безопасности (80 дБ).
Газодинамическое напыление металла
Газодинамическое напыление металлов основано
на эффекте закрепления частиц металла,
если они движутся со сверхзвуковой скоростью,

К настоящему времени технология ДИМЕТ® позволяет
наносить покрытия из алюминия, цинка, меди, олова,
свинца, баббитов, никеля и наносить их не только
на металлы, но и на стекло, керамику, бетон.
Температура при нанесении покрытий не превышает
150 градусов, т.е. температуры работающего двигателя,
что позволяет широко применять в авторемонтных
работах, а именно:
Основные элементы технологии холодного
газодинамического напыления
Технология газодинамического напыления металлов
ДИМЕТ® включает в себя нагрев сжатого газа (воздуха),
дальнейшее поступление его в сверхзвуковое сопло с
формированием в сопле воздушного потока сверхзвуковой
скорости.
—Ремонт головки блока цилиндров двигателя;
—Герметизация топливных баков;
—Ремонт радиаторов;
—Ремонт и восстановление кондиционеров автомобиля;
—Ремонт посадочных мест коленвалов и постелей
распредвалов;
—Ремонт обогревателей заднего стекла;
—Цинкование, антикоррозийная обработка и многое
другое.

Техника безопасности при выполнении газотермических работ
К работе на установках для напыления допускаются лица не
моложе 18 лет, обученные приемам работы на оборудовании.
При плазменном и детонационном напылении наиболее вредными
для здоровья работающих являются шум, загрязнение воздуха,
ультрафиолетовые и инфракрасные излучения.
Для защиты оператора от шума и загрязнений рекомендуется
покрытия наносить в специальных камерах с местным отсосом
воздуха.
Плазменная
струя
является
интенсивным
источником
инфракрасного и ультрафиолетового излучения, поэтому оператор
должен работать в защитной маске со светофильтром.
Камеры для напыления также оборудуют соответствующими
светофильтрами. Руки от излучения защищаются рукавицами из
асбестовой ткани.
Требования к технике безопасности при газопламенном и
электродуговом напылении предъявляются те же, что и при
выполнении работ по газовой и электродуговой сварке.
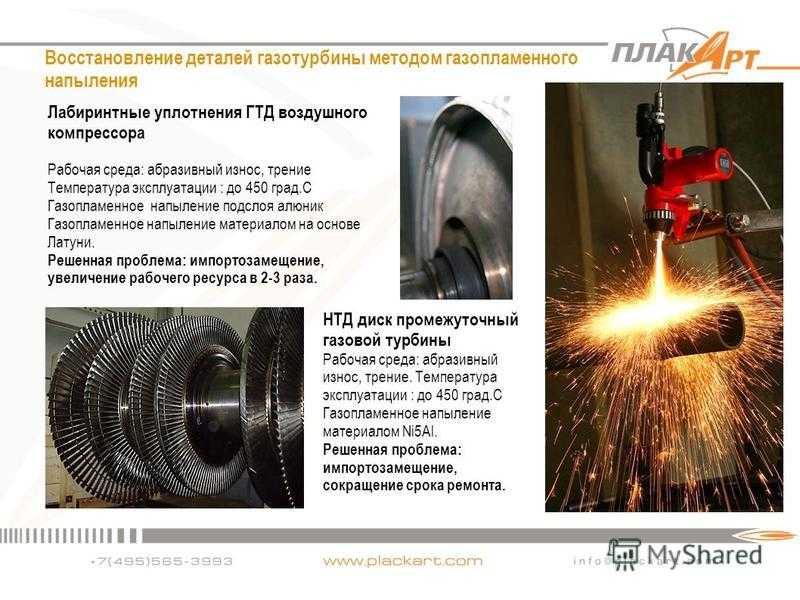
English Русский Правила
Что такое вакуумная металлизация и почему это важно?
Вакуумная металлизация является обычной практикой в обрабатывающей промышленности. Детали всех типов и назначений обычно покрываются металлом по разным причинам. Вакуумная металлизация не только придает изделию приятный внешний вид, но и обеспечивает физическую защиту от повреждений.
Mueller предлагает услуги УФ-вакуумной металлизации широкого спектра деталей. Но что такое вакуумная металлизация и как она работает?
Что такое вакуумная металлизация?Вакуумная металлизация детали включает процесс нанесения металлического покрытия на деталь. Металлическое покрытие наносится в вакуумной зоне и равномерно покрывает всю деталь. Это покрытие обеспечивает множество преимуществ, как визуальных, так и физических.
Многие компоненты устройства и пластиковые детали требуют вакуумной металлизации для обеспечения надлежащего функционирования устройства. Без надлежащего покрытия надлежащей толщины детали могут быть повреждены, и устройство может работать неправильно. С подходящим покрытием из подходящего металла эти важные детали могут служить годами.
Существует множество различных причин, по которым компаниям может потребоваться вакуумная металлизация компонентов, в том числе:
- Добавление отражающих свойств к деталям- Некоторые детали должны иметь отражающую поверхность для эстетических целей или для надлежащего функционирования устройства.
- Защита от кислорода и влаги – Многие детали должны быть защищены от жидкостей и кислорода во избежание повреждений и выхода из строя.
- Создание или ограничение электропроводности – В зависимости от части устройства может потребоваться усиление или ограничение количества проходящего через него электричества. Правильная вакуумная металлизация может помочь контролировать поток электричества.
В процессе вакуумной металлизации можно использовать такие металлы, как алюминий, медь и никель. Каждый металл имеет свои преимущества, как физические, так и эстетические. Прежде чем выбирать металл, который будет использоваться для покрытия, важно понять функцию детали.
Как выполняется вакуумная металлизация?Компания Mueller предоставляет услуги УФ-вакуумной металлизации любых необходимых деталей. Сочетая распыление жидкости и металлизацию, наш процесс создает как физические, так и эстетические преимущества для деталей.
Наш процесс включает в себя нанесение УФ-отверждаемой грунтовки для обеспечения надлежащей адгезии. Затем в вакууме на поверхность детали наносится испаренный металл. Наконец, для защиты и визуальной привлекательности добавляется прочный УФ-лак или тонированное покрытие.
Этот процесс физического осаждения из паровой фазы (PVD) обеспечивает полное покрытие детали равномерным количеством металла. Благодаря равномерному покрытию деталь будет хорошо приспособлена к нагрузкам, связанным с работой устройства, будь то нагревание, шлифование, резка или трение.
Вакуумная металлизация обеспечивает защитный барьер от повреждений для любой части устройства. Он также предлагает красивую отделку для деталей, которые будут представлены на внешней стороне устройства. Этот процесс прост и эффективен, обеспечивая множество преимуществ как для производителей, так и для потребителей.
Компания Mueller готова предоставить вашему бизнесу услуги по вакуумной металлизации, необходимые для вашей продукции. Позвоните нам сегодня, чтобы узнать больше о нашем процессе и обсудить ваши потребности с нашей командой.
О компании Mueller Corporation
Компания Mueller Corporation, основанная в 1955 году, предлагает клиентам широкий выбор вакуумных металлизированных и промышленных покрытий для удовлетворения любых потребностей в декоративной или функциональной отделке. Корпорация Mueller поддерживает высочайший уровень удовлетворенности клиентов и гарантии качества, постоянно инвестируя в свою продукцию и своих сотрудников. Уделяя особое внимание разработке инновационных покрытий посредством исследований и разработок, а также постоянному совершенствованию нашего процесса с помощью новых технологий и приложений, корпорация Mueller остается лидером в области функциональных и декоративных покрытий для брендов по всему миру.
Стационарные и переносные кинетические системы металлизации для объемного восстановления
Стационарные и переносные кинетические системы металлизации для объемного восстановления ремонта Стационарные и портативные системы кинетической металлизации для восстановления размеров
|