Восстановление металла напылением – Восстановление деталей напылением
alexxlab | 17.11.2019 | 0 | Разное
Восстановление деталей c использованием оборудования Димет
Восстановление утраченных объемов металла
Применяемое оборудование при газодинамическом напылении по технологии Димет является эффективным и экономичным средством при восстановлении сработавшейся поверхности. В большей степени это обусловлено отсутствием деформации изделия, возникновения внутренних напряжений, структурных превращений металла изделия в виду того, что при устранении дефекта не происходит влияние на деталь высокой температуры. Используемый метод основан на локализованном восстановлении, т.е. участки без дефектов не подвергаются температурному воздействию, что сохраняет геометрические размеры детали и его первоначальную структуру материала.
Стоит обратить внимание на условия применения данного метода – требований к нагрузке на деталь по твердости и износостойкости быть не должно.
Восстановление посадочных мест подшипников на валу
Дефект вала – износ посадочных мест подшипников с двух сторон.
Для восстановления номинального размера было использовано напыление металлизированного слоя. Перед восстановлением поверхности, необходима обработка дефектного участка абразивом для лучшей адгезии. Далее в режиме «2» наносится состав С-01-11 тонким слоем, после включается режим «3» или «4» для наращивания слоя металла с запасом на токарную обработку.
Финальная стадия ремонта заключается в формировании поверхности, согласно чертежу детали. Во время этой операции необходимо учитывать особенность крупнозернистой структуры покрытия. Для получения качественной поверхности устанавливаются большие обороты и используется минимальная подача резца. Хорошая заточка инструмента обеспечивает высокое качество обработанной поверхности.
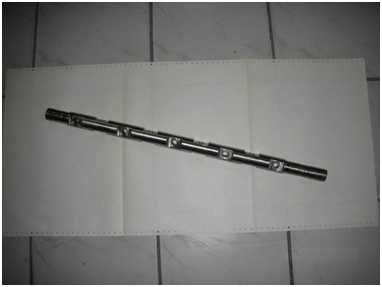
Изображение 1. Вал с изношенными хвостовиками.
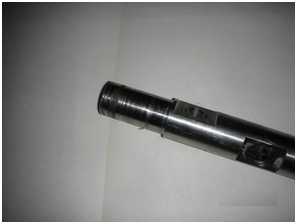
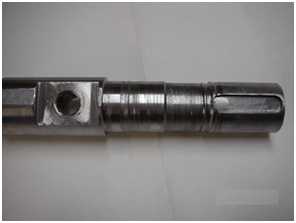
Изображение 2. Изношенные участки на валу.
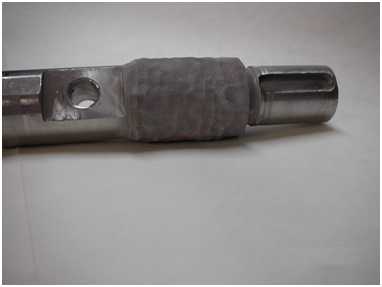
Изображение 3. Восстановленная поверхность с помощью технологии Димет.
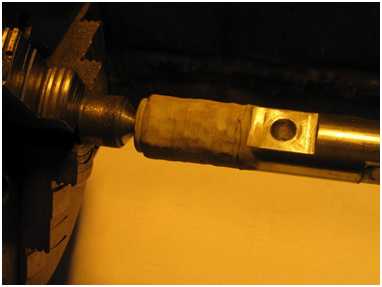
Изображение 4. Процесс проточки напыленной поверхности.
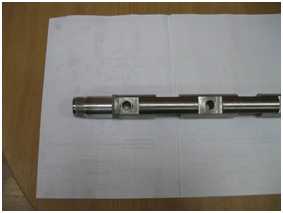
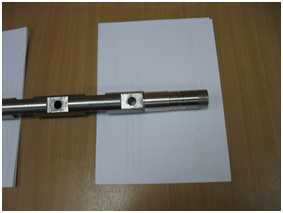
Изображение 5. Восстановленные участки на валу.
dimet.info
Димет официальный представитель Россия – Восстановление деталей
Современное оборудование «Димет» поможет восстановить утраченный объем металла на любых автозапчастях. Эта технология довольно эффективна и популярна. С ее помощью можно восстановить любые повреждения и дефекты на металлических поверхностях в короткие сроки, качественно и не прилагая особых усилий. Благодаря современным инновационным технологиям восстановить металлическую поверхность можно самым аккуратным способом, не подвергая ее особому нагреву. То есть восстановление металлических поверхностей при помощи «Димет» проходит при температуре 100–150 градусов Цельсия.
Удобство работы с «Димет»
Работа с этим оборудованием отличается удобством, простотой и безопасностью. При работе с «Димет» затрагивается только обрабатываемый участок, другие части поверхности не затрагиваются и не деформируются. Имейте в виду: восстановление деталей должны проводить только высококвалифицированные специалисты с опытом работы.
Способы восстановления деталей установкой «Димет» разнообразны. Это оборудование может работать с разными сплавами. Благодаря удобству и безопасности работы установки «Димет» пользуются большим спросом и популярностью. Их приобретают владельцы автомастерских и различных предприятий.
Ремонт автозапчастей с «Димет»
Ремонт деталей стоит начать с подготовительного процесса. Их не надо тщательным образом подготавливать и очищать от пыли. Сделать все это можно при помощи функции «абразивная чистка» на самом оборудовании. Восстановление деталей автомобиля оборудованием «Димет» довольно простое. Сначала надо извлечь деталь, провести ее диагностику, определить степень поврежденности. С помощью установки можно произвести напыление металла на детали. После этой процедуры на поврежденном участке не останется и следа от былой трещины.
«Димет» пользуется спросом и при восстановлении чугунных деталей. Всем владельцам авто известно, что чугунные детали плохо поддаются сварке — они очень деликатные. А вот с оборудованием «Димет» можно произвести восстановление наплавкой на самом высоком уровне. Технология нанесения металла на различные поверхности практически ничем не отличается.
Сфера применения «Димет» в автомастерских
Имея такое оборудование под рукой в своих автомастерских, владельцы могут предложить клиентам довольно широкий спектр обслуживания. С оборудованием «Димет» можно выполнять:
Это далеко не весь перечень услуг автомастерских, работающих с оборудованием «Димет».
Простыми словами об уникальной технологии. Посмотрите этот ролик сейчас.
dymet.org
восстановление деталей — Центр защитных покрытий — Урал
Восстановление баббитовых подшипников на производственной площадке ООО ЦЗПУ методом газопламенного напыления позволяет получить изделия с высокой адгезией баббитового слоя. Толщина напыленного баббитового слоя может составлять от 1,5 до 30 мм. Баббит это антифрикционный сплав на основе олова или свинца, предназначенный для использования в виде слоя, залитого или напыленного по корпусу вкладыша подшипника. У такого сплава получаются отличные свойства скольжения, и минимальный показатель по трению.
Вкладыши подшипников изготавливаются из стали, чугуна или бронзы, а внутренние части вкладышей лудятся и производится заливка баббитом. При заливке вкладышей баббитом выполняются следующие операции: выплавление из вкладыша старого баббита, обезжиривание, травление, облуживание, плавление баббита заливка подшипника, определение качества заливки, шабрение. Только при точном соблюдении всех технологических требований получаем подшипник скольжения высокого качества. Основными дефектами подшипников скольжения являются: износ и искажение формы рабочих поверхностей, отслоение, выкрошивание или частичное выплавление баббита. Следствием износа рабочих поверхностей подшипника является увеличение зазора, появление овальности, конусообразности и бочкообразности.
Восстановление баббитовых подшипников напыление баббита
Восстановление баббитовых подшипников является дорогим и трудоемким процессом при заливке. Срок службы подшипника, напыленного баббитом, в среднем в полтора, два раза больше, чем подшипника, изготовленного методом наплавки, благодаря микропористости около пяти процентов и удержанию масляной пленки после длительной остановки оборудования. При помощи газопламенного напыления производятся покрытия с повышенными качественными характеристиками.
Тонкостенный вкладыш подшипника скольжения в оснастке, напыление баббит — технология газопламенное напылениеПреимущества газопламенного напыления:
- это меньший припуск на предварительную механическую обработку детали
- отсутствие канавок «ласточкин хвост» на новых вкладышах
- возможность напыления баббита по слою залитого баббита на ремонтируемых вкладышах
- мы пылим не только баббит, но и бронзу, медь, латунь
Таким образом сокращается расход дорогостоящего баббита и уменьшается стоимость изготовления или ремонта вкладышей подшипников примерно на двадцать процентов по сравнению с заливкой.
ООО ЦЗПУ производит восстановление баббитовых подшипников методом газопламенного напыления. Газопламенное напыление при восстановлении баббитовых подшипников полностью исключает вероятность возникновения каверн или твердых включений. При газопламенном напылении равномерно распределяется баббит по поверхности подшипника — это позволяет снизить общую толщину баббитового слоя.
Технология, газопламенное напыление, позволяет ремонтировать и восстанавливать местный износ баббитового слоя подшипника после предварительного обезжиривания и механической обработки. При напылении невозможно использование бывшего в употреблении баббита. Заказывая газопламенное напыление в ООО ЦЗПУ, вы гарантированно получаете новый баббит в качестве антифрикционного слоя. Преимуществом нашей технологии при восстановлении подшипников скольжения, является тот факт, что в баббитовом слое в результате напыления образуются микропоры, что позволяет осуществлять пропитку маслом и удерживание масляной пленки в случае нарушения подачи масла и после длительной остановки машины, в результате чего исключается режим сухого трения.
При нанесении баббита напылением достигается более однородная прочность сцепления напыляемых слоев с основой подшипника скольжения, а величина адгезии покрытия к стали составляет 20 МПа, к баббиту — 15 МПа. Восстановление баббитовых подшипников скольжения напылением дает повышенные антифрикционные свойства и высокое сопротивление усталостным разрушениям. При применении очень мягких легкоплавких подшипниковых сплавов обеспечивается меньший износ шейки вала. Баббит, кроме того, имеет и минимальный коэффициент трения со сталью и хорошо удерживают смазку.
Качество напыления баббита проверяют после того, как подшипник совсем остынет. При внешнем осмотре следят за тем, чтобы поверхность была без пор, трещин, раковин и имела серебристый цвет.
Восстановление баббитовых подшипников технология
Как ООО ЦЗПУ производит восстановление баббитовых подшипников методом газопламенного напыления:
- удаляется старый баббит, токарной обработкой или выплавляется. Старый баббит в дело больше не идет
- если есть ласточкины гнезда, то они вскрываются так, чтобы можно было дотянуться струей, т.е. подшипник, восстановленный напылением — под наплавку уже не годится
- если подшипник чугунный и ранее работал, то он подвергается термообработке для выжигания остатков масла в порах
- на подготовленную поверхность напыляется ХХХХХХХ (секрет фирмы). У него отличная адгезия, что дает гарантированное равномерное сцепление баббитового покрытия с корпусом подшипника
- производится напыление подшипника баббитом, либо в сборе, либо по частям, в зависимости от габаритов
- если пылили в сборе, подшипники разрезаются, притираются, при необходимости
- подшипники растачиваются, если заказчик требует, то производится расточка
- . ООО ЦЗПУ не шабрит подшипники, так как это надо делать по месту, а место от нас может находиться в сотнях и тысячах километров.
czpu.ru
Ремонт и восстановление валов напылением или наплавкой — Центр защитных покрытий — Урал
Центр защитных покрытий — Урал (ЦЗПУ) предлагает ремонт и восстановление валов напылением или наплавкой. Изношенные валы восстанавливаются различными способами, основными из которых являются наращивание изношенной поверхности слоем металла наплавкой или напылением (металлизацией).
Специалисты ООО ЦЗПУ напыляют рабочий слой и механической обработкой доводят посадочное место до требуемого размера. Предварительную и заключительную механические обработки мест под посадку производят на соответствующих токарно-винторезных и шлифовальных станках. Наше предприятие производит ремонт и восстановление валов напылением или наплавкой с восстановлением посадочных мест под полумуфты и подшипники, в том числе имеющие сплошную выработку по диаметру до 1,5—3 мм. Восстановление валов производится с учётом условий их эксплуатации, физического состояния. Восстановление напылением или наплавкой поможет вернуть деталь в рабочее состояние, повысить коррозийную и термическую стойкость поверхности, увеличить прочность. Во внимание берётся также характер повреждений и дефектов.
Напыление годится для восстановления любых посадочных мест на валах, где не нужно передавать большой вращающий момент через контакт с поверхностью. С помощью методики напыления мы успешно восстанавливаем валы редукторов, мотор редукторов, насосов.
Ремонт и восстановление валов напылением или наплавкой
Газотермическое напыление придает полное и принципиальное отсутствие термических структурных превращений и тепловых деформаций в детали вследствие низких температур нагрева при данной технологии восстановления не выше 250 градусов С, наличие открытых микропор в покрытии благоприятно влияет на условия работы пар трения, так как в порах постоянно удерживается незначительное количество смазки. Отличительной особенностью таких покрытий является однородная структура, низкая около 1,5 % и ниже пористость, что предотвращает усадку покрытия при эксплуатации деталей, равномерное распределение антифрикционных включений. Благодаря этому покрытие выдерживает длительные высокие цикличные нагрузки и перегрузки. Изношенные поверхности валов — шейки, цапфы должны быть подготовлены так, что бы наплавленный слой получался одинаковой толщины, иначе этот слой легко отслаивается, особенно при конической и овальной форме износа.
При ремонте и восстановлении валов напылением или наплавкой, изношенные участки вала предварительно обрабатывают для придания поверхностям шероховатости, обезжиривают, затем напыляют подслой, обеспечивающий прочную связь основного металла с рабочим слоем покрытия и защиту основного металла от окисления.
Износу и смятию у валов подвергаются цапфы, шпоночные канавки, шлицы, поверхности под посадку шестерён, шкивов и других деталей, резьбовые участки. Ремонт и восстановление валов напылением или наплавкой производится тогда, когда трущиеся поверхности приобретают коническую, овальную, бочкообразную или седлообразную форму, шлицевые и шпоночные канавки становятся шире, из-за чего шпоночное соединение ослабляется, а в шлицевых соединениях возникают удары, резьба срезается, сминается и вытягивается. При неправильной эксплуатации изделий и износе эти участки подвергаются сколам, царапинам, выбоинам, задирам и другим повреждениям.
Основными преимуществами ремонта и восстановления валов в ООО ЦЗПУ является большой опыт работы по приданию компонентам дополнительных качественных характеристик, которые позволяют значительно повысить эффективность работы деталей машин и оборудования.
czpu.ru
Ремонт деталей машин металлизацией
Строительные машины и оборудование, справочник
Категория:
Ремонтирование строительных машин
Публикация:
Ремонт деталей машин металлизацией
Читать далее:
Ремонт деталей машин металлизацией
Металлизацией называется напыление расплавленного металла на поверхность восстанавливаемых изделий. Металл, расплавленный в специальном приборе — ме-таллизаторе, распыляется сжатым воздухом на мельчайшие частицы (0,01…0,015 мм) и в таком виде перекосится на поверхность ремонтируемой детали. Большая скорость движения частиц (120…300 м/с) и незначительное время полета, исчисляемое тысячными долями секунды, обусловливают в момент удара их пластическую деформацию, заполнение неровностей и пор поверхности детали, сцепление с ней и между собой, образование сплошного покрытия.
После образования первого слоя покрытия снова наслаивают расплавленный металл, в результате чего удается получить покрытия с толщиной слоя 0,03… 10 мм и даже более. Обычно покрытия из тугоплавких металлов наносят толщиной 1…1.5 мм, а из легкоплавких—2,5…3 мм. По способу плавления металла различают дуговую, газовую, высокочастотную и плазменную металлизацию.
Рис. 1. Схема дуговой металлизационной установки
1 — расплавляемые проволоки; 2 — токопроводы; 3 — подающий механизм; 4 — направляющие наконечники; 5 —сопло, подающее сжатый воздух; б —зона плавления; 7 — поверхность металлизуе-мой детали
Дуговая металлизация (рис. 1) заключается в расплавлении электрической дугой исходного материала и напылении его струей сжатого воздуха на поверхность детали. Электрическая дуга горит между двумя проволоками, протягиваемыми роликами. Струя сжатого воздуха вытягивает дугу. Размер распыляемых частиц колеблется в пределах 10…50мкм. Скорость напыления с расстояния 30 мм от сопла 250 м/с. Толщина напыленного слоя составляет 20 мкм…10 мм. Для электродуговой металлизации используют аппараты ЭМ-ЗА, ЭМ-6, ЭМ-9, ЭМ-10.
Газопламенную металлизацию осуществляют с помощью аппаратов, в которых металлическая проволока или порошковые материалы распыляются ацетилено-кислородным пламенем пли пламенем других горючих газов в смеси с кислородом. При этом способе повышается прочность сцепления, уменьшаются размеры рас-пыливаемых частиц металла и снижается его окисление. Недостатки: низкая производительность и сложность установки Для газопламенной металлизации применяют аппараты ГИМ-1М, ГИМ-2М, МГИ-1-57, МГИ-2-65.
Высокочастотная металлизация основана на принципе расплавления проволоки в зоне индуктора, состоящего из нескольких витков медной трубки, к которому подается ток высокой частоты (200…50 кГц) от лампового генератора. Высокочастотная металлизация обеспечивает быстрый нагрев конца электродной проволоки, что уменьшает выгорание углерода и других элементов, делает покрытие однородным с пределом прочности на разрыв в 2,5 раза выше, чем при электродуговой металлизации. Недостатки: сложность и высокая стоимость оборудования. В качестве источников питания применяют ламповые генераторы токов высокой частоты ГЗ-46, ЛГП-30, Л1ПЗ-60.
Плазменную металлизацию осуществляют с помощью плазматронов, в которых плазмообразующий газ (аргон) протекает сквозь столб электрического разряда, частично или полностью ионизируется и превращается в плазму. Плазматрон состоит из катода и анода, охлаждаемых водой. От источника постоянного тока между катодом и анодом возбуждается электрическая дуга. Плазмообразующий газ, введенный в зону горения, ионизируется и выходит из анода плазматрона в виде струи небольшого сечения. Высокая электропроводность плазменной струи значительно повышает плотность тока, температуру газа и скорость его истечения. Рабочая температура струи достигает 7000…15000 °С при скорости истечения до 1500 м/с.
Для плазменной металлизации используют установки УПУ-ЗМ, УМП-4-64, УМП-5-68, которые обеспечивают более высокие, чем при других способах металлизации, механические свойства покрытия и более прочное его соединение с поверхностью детали. Покрытие обладает высокой износостойкостью и не снижает усталостной прочности детали. За счет высокой температуры плазменной струи можно наносить покрытия практически из любых материалов. Процесс полностью автоматизирован, что повышает производительность труда. При плазменной металлизации проволокой можно использовать газопорошковую среду, а порошок — в качестве присадочного материала. В качестве плазмообразующего газа при распылении порошка кроме аргона применяют азот, водород, гелий.
Описанные способы металлизация применяют для восстановления начальных размеров и формы поверхностей изношенных деталей, а также для нанесения анти-фрикционных и износоустойчивых покрытий, создания декоративных антикоррозионных и жаропрочных покрытий, исправления дефектов черного и цветного литья, заделки наружных раковин, устранения пористо-стей, течей, трещин различного происхождения.
Применению металлизации для этих целей способствуют: низкая температура нагрева поверхности изделия, не превышающая 50…70°С, при которой основной металл не претерпевает никаких структурных изменений, полностью сохраняя свои механические свойства. Это дает возможность наносить слой покрытия на любые материалы: металл, дерево, резину, пластмассы и т. п.;
высокая твердость покрытия, превышающая твердость исходного материала.
Увеличение твердости объясняется микрозакалкой и наклоном частиц металла, деформирующихся при ударе о поверхность детали.
В сочетании с высокой пористостью напыленного слоя, хорошо удерживающего смазку, твердость покрытия способствует увеличению сроков службы восстанавливаемых изделий;
возможность напыления разнообразных металлов, в том числе и разнородных, образующих механическую смесь мельчайших частиц, что позволяет создавать новые типы материалов, отличающихся весьма высокими антифрикционными свойствами. Например, металлизация подшипников биметаллической проволокой из алюминия и свинца позволяет не только заменять дорогостоящие оловянистые баббиты и бронзы, но и значительно увеличить срок службы подшипников.
При рассмотрении целесообразности применения металлизации для восстановления изношенных деталей следует учитывать, что металлизованный слой не повышает их прочности, а следовательно, металлизация неприменима для восстановления деталей с ослабленным сечением. Ограниченно применяется металлизация при восстановлении деталей, находящихся под действием динамической нагрузки, а также деталей, работающих при сухом трении, так как сцепляемость напыленного слоя с основным металлом детали недостаточна.
Получение качественных покрытий возможно лишь при строгом соблюдении режимов и тщательной подготовке поверхностей. Подготовку поверхности для металлизации производят в такой последовательности: – очистка деталей от загрязнений, пленок, оксидов, жировых пятен, влаги и ржавчины; – предварительная механическая обработка поверхности с целью придания ей правильной геометрической формы; – создание шероховатой поверхности для удержания нанесенного слоя металла; – защита смежных поверхностей, не подлежащих металлизации.
Очищают поверхности от загрязнений щетками, промывают в бензине или растворителях, очищают также, нагревая в печах над пламенем газовой горелки или паяльной лампы.
Механической обработкой исправляют геометрическую форму детали и доводят до размеров, при которых возможно нанесение покрытия заданной толщины. На концах цилиндрических поверхностей оставляют буртики и протачивают замки в виде кольцевых канавок, предохраняющие покрытие от разрушения с торца.
Шероховатость на поверхностях деталей, подлежащих металлизации, получают различными способами. Для деталей сложной формы для заделки трещин и раковин и для плоских деталей применяют пескоструйную обработку сухим кварцевым песком с размером частиц 1,5…2 мм. Шероховатость закаленных тяжелонагруженных деталей создается наплавкой вибрирующими электродами в сочетании с пескоструйной обработкой (обдувкой). В отдельных случаях шероховатость создают, наматывая на деталь очищенную от окалины проволоку диаметром 0,5… 1,5 мм с шагом 2…5 этого диаметра. Намотанная проволока закрепляется сваркой, после чего производится пескоструйная обработка.
На поверхности термически необработанной круглой детали нарезается рваная резьба резцом, установленным с большим вылетом ниже оси детали на 3…6 мм.
После очистки и подготовки к металлизации не рекомендуется брать деталь голыми руками, класть ее на загрязненные поверхности и выносить во влажные помещения. Время между концом подготовки и нанесением слоя металла не должно превышать 1 ч во избежание окисления подготовленной поверхности.
Поверхности детали, не подлежащие металлизации, защищают картоном, листовой сталью или изоляционной лентой, а пазы и отверстия — деревянными пробками.
Нанесение слоя металла выполняется в специальных камерах, оборудованных пылеприемниками, или на месте ремонта машины. Поверхности, имеющие форму тел вращения, металлизуют на токарном станке, при этом металлизатору, закрепленному на суппорте с помощью специального приспособления, сообщают движения подачи, и скорость вращения детали выбирают в зависимости от размеров детали и типа металлизатора.
Для получения высокого качества покрытий струю распыленного металла следует направлять перпендикулярно обрабатываемой поверхности и выдержать расстояние от сопла металлизатора до изделия в пределах 100…150 мм. Вначале следует напылять металл на участки, имеющие резкие переходы: углы, галтели, уступы, а затем переходить к металлизации всей поверхности, равномерно наращивая металл.
Требуемые размеры, качество отделки и правильная геометрическая форма поверхностей, покрытых распыленным металлом, достигаются механической обработкой.
Реклама:
Читать далее: Электролитическое наращивание металла
Категория: – Ремонтирование строительных машин
Главная → Справочник → Статьи → Форум
stroy-technics.ru
Восстановление деталей припеканием
8. Восстановление деталей электрохимическими и химическими покрытиями
15. Восстановление деталей способом дополнительных ремонтных деталей
Этим способом восстанавливают блоки цилиндров, гнёзда клапанов, посадочные отверстия под подшипники качения в картерах коробок передач, задних мостов, ступиц, корпуса масляных и водяных насосов, отверстия с изношенной резьбой в корпусных деталях и другие детали. Крепление дополнительной детали осуществляют за счёт гарантированного натяга, привариванием в нескольких точках или по всему сечению торцовой поверхности, установкой стопорных винтов либо шпилек (для крепления втулок, резьбовых ввёртышей).
Сборку дополнительной и ремонтируемой деталей выполняют обычно за счёт посадки с гарантированным натягом, при этом происходит изменение размеров втулки. При напрессовке её на вал наружный диаметр увеличивается, а при запрессовке в отверстие уменьшается внутренний диаметр. Независимо от способа соединения посадка втулки с натягом должна гарантировать прочность соединения (от проворачивания, перемещений).
Путём замены части детали восстанавливают дорогостоящие элементы конструкции. Изношенная часть детали удаляется, а вновь изготовленная соединяется с деталью с помощью сборочных операций (напрессовки, сварки, пайки). Этот вид ремонта может привести к появлению пространственных отклонений взаимосвязанных поверхностей. Он применяется при ремонте кузовов, рам, кабин.
16. Сварка в процессах создания ремонтных заготовок
Сварка – это процесс получения неразъёмных соединений установлением межатомных связей между свариваемыми частями при их местном нагреве, пластическом деформировании или совместном действии того и другого. От вида энергии сварочные процессы разделяют: термические, механические и термомеханические. Сварка термического класса использовании тепловой энергии: электродуговая, электрошлаковая, газовая, индукционная, плазменная, Механического класса (сварка трением, ультразвуковая и др.) Термомеханического класса (контактная, диффузионная, взрывом )
Сварка стали. Низкоуглеродистые стали хорошо свариваются всеми видами сварки, не подвержены существенной закалке при сварке. При сварке высокоуглеродистых и среднелегированных сталей во избежание закалки и образования трещин применяют предварительный нагрев до 300°С с последующим отжигом или отпуском. Ограниченно свариваются стали 45 и 50 и низколегированные стали с содержанием углерода до 0,45 %.
Сварка чугуна. Сварка чугуна усложнена его низкой пластичностью и склонностью к отбеливанию. Последнее объясняется большим содержанием углерода, выгоранием кремния и быстрым охлаждением металла. При этом углерод не успевает выделиться в виде графита и остается в химически связанном состоянии в виде цементита Fe3C. При усадке чугуна возникают значительные внутренние напряжения.
Сварка цветных металлов. Алюминиевые сплавы характеризуются плохой свариваемостью. На поверхности нагреваемой заготовки образуется пленка штатного, химически стойкого и тугоплавкого оксида. Свинец. Его сварка сопровождается образованием сравнительно тугоплавких оксидов. Сварку ведут нейтральным ацетиленокислородным пламенем или с применением газов – заменителей ацетилена. Присадочным материалом служит свинцовая проволока или полоса.
Оборудование для сварки. Технологическое оборудование для сварки включает источники питания, ацетиленовые генераторы, вращатели и столы. Для дуговой сварки применяют ток силой 1–3000А и напряжением8–140В.
17. Восстановление деталей пайкой.
Пайка – процесс соединения металлов или неметаллических материалов посредством расплавленного присадочного металла, называемого припоем и имеющего температуру плавления ниже температуры плавления основного металла. В процессе пайки происходят взаимное растворение и диффузия припоя и основного металла, чем и обеспечиваются прочность, герметичность, электропроводность и теплопроводность паяного соединения. Для получения качественного соединения температура нагрева спаиваемых деталей в зоне шва должна быть на 50–100°С выше температуры плавления припоя. Для защиты поверхностей спаиваемых деталей от интенсивного окисления в результате нагрева место пайки покрывают флюсом, который образует жидкую и газообразную преграды между поверхностями спаиваемых деталей и окружающим воздухом. Процесс пайки заключается в следующем: при нагревании припой расплавляется и, соприкасаясь с нагретым, но свободным от окисной пленки основным металлом, смачивает его, и растекается по его поверхности. Способность припоя заполнять швы зависит от степени смачивания припоем основного металла, его капиллярных свойств и шероховатости поверхности спаиваемых деталей. Пайка, как способ восстановления деталей, имеет следующие преимущества: простота технологического процесса и применяемого оборудования; высокая производительность процесса; сохранение точной формы, размеров и химического состава деталей; простота и лёгкость последующей обработки ;небольшой нагрев деталей; возможность соединения деталей, изготовленных из разнородных металлов; достаточно высокая прочность соединения деталей; низкая себестоимость восстановления детали.
Припои для пайки. В зависимости от температуры плавления и прочности применяемых припоев различают пайку мягкими припоями и пайку твёрдыми припоями. При пайке мягкими припоями используют припои с температурами плавления ниже 400ºС, обеспечивающие получение паяных швов с пределами прочности до 90 МПа. Применяют следующие мягкие припои: оловянно-свинцовые, малооловянистые, легкоплавкие и специальные. При пайке твёрдыми припоями применяют припои с температурами плавления выше 400°С: медные , медно-цинковые , меднофосфористые, серебряные.Перед пайкой поверхности деталей очищают от пыли, жира, краски, ржавчины, окалины и окисной плёнки.
18. Заливка жидким металлом.
При восстановлении сильно изношенных деталей или при заделке
крупных местных дефектов в отливках используют заливку жидким металлом. Для получения прочной связи заливаемого металла с металлом восстанавливаемой детали поверхность детали подвергают специальной обработке. В процессе восстановления детали способом раздельной тепловой подготовки и заливки наращиваемую поверхность детали оплавляют с помощью мощной угольной дуги, газовых горелок или индукционного нагрева. Заливкой жидким металлом целесообразно восстанавливать крупногабаритные изделия или значительное количество мелких однотипных деталей. Этот способ обеспечивает высокие производительность и качество.
Изношенные детали можно заливать различными металлами и сплавами. Для восстановления крупных партий дефектных деталей используют плавильную печь и специальный металлосборник с разливочным приспособлением. Из плавильной печи жидкий металл периодически поступает в металлосборник, откуда он подается для непрерывной наплавки деталей. Иногда применяют способ центробежной наплавки с предварительным расплавлением присадочного металла и последующей его заливкой внутрь вращающихся заготовок. При этом наплавляемые втулки вращаются в центробежных машинах, патронах станков или спец. приспособлениях. Нагрев заготовок и плавление заливаемого материала производят в высокочастотных, электродуговых и других печах. Для расплавления легкоплавких антифрикционных материалов можно использовать обычные горны. Такой способ обеспечивает получение плотного беспористого слоя металла, однако производит. низка. Метод восстановления вкладышей подшипников опрессовкой и последующей заливкой баббитом основан на перераспределении оставшегося вкладыше материала. При восстановлении с рабочей поверхн. снимают тонкую стружку, устанавливают вкладыши в приспособлении для выдавливания углублений, затем их извлекают оттуда и заливают баббитом.
19. Восстановление деталей с примен. синтетических матер.
Пластмассы в ремонтной практике наносят на поверхности деталей для восстановления их размеров, повышения износостойкости и улучшения герметизации. Одновременно покрытие из пластмассы снижает шум от трения и повышает коррозион. стойкость изделия.
Акриловые пластмассы. При ремонте широко применяют акриловые пластмассы, содержащие в качестве связующих материалов акриловые смолы – продукты полимеризации метилметакрилата и сополимеризации метилметакрилата со стиролом.
Пластмассы класса полиамидов. В ремонтной практике наибольшее распространение получил капрон марок А и В. Это» твердый материал белого цвета с желтым оттенком, имеющий высокую прочность, износостойкость, масло- и бензостойкость, а также хорошие антифрикционные свойства. Поставляется он в виде гранул размером 7–8 мм. Основными недостатками капрона являются низкая теплопроводность, теплостойкость и усталостная прочность. Максимально допустимая рабочая температура капроновых покрытий не должна превышать плюс 70–80°С и минус 20–30°С.
Ремонт деталей с применением составов на основе эпоксидной смолы. Главный связующий компонент этих составов – эпоксидная смола марки ЭД-6 или ЭД-5. Чаще применяют смолу ЭД-6. Это прозрачная вязкая масса светло-коричневого цвета. Для приготовления состава на основе смолы ЭД-6 на 100 частей (по массе) смолы вводят 10–15 частей дибутилфталата (пластификатор), до 160 частей наполнителя и 7–8 частей полиэтиленполиамина (отвердитель).
Ремонт деталей с применением клеев. В ремонтной практике наибольшее применение получили клеи ВС-10Т, ВС-350 и № 88Н. Клей ВС-10Т – прозрачная однородная жидкость тёмно-красного цвета. Им можно склеивать между собой и в любом сочетании различные металлы и неметаллические материалы (сталь, чугун, алюминий, медь, стеклотекстолит, асбоцементные материалы и др.), работающие при температуре 200°С втечение 200 ч и при температуре 300°С в течение 5 ч. Клеевой шов устойчив против воды, нефтепродуктов, холода.
20. Восстановление деталей наплавкой.
Наплавка широко применяется при восстановлении цилиндрических поверхностей деталей, шлицевых поверхностей, изношенных зубьев шестерён и т. д.
Дуговая наплавка под флюсом заключается в том, что электрическая дуга горит между электродом и заготовкой под слоем гранулированного флюса толщиной 10–40 мм. Наплавка под флюсом обеспечивает высокое качество наплавленного металла, так как сварочная ванна защищена от вредного влияния кислорода и азота воздуха. Флюсы содержат стабилизирующие, газообразующие, шлакообразующие, раскисляющие, легирующие и связующие вещества.
Наплавка в среде защитных газов состоит в том, что в зону электрической дуги через газоэлектрическую горелку подаётся под давлением защитный газ, который, оттесняя воздух, защищает расплавленный металл сварочной ванны от вредного воздействия на него кислорода и азота воздуха
Вибродуговая наплавка осуществляется автоматической головкой вибрирующим электродом с частотой 50–100 Гц и амплитудой 1–3 мм. Цикл наплавки состоит из короткого замыкания, дугового разряда и холостого хода. Во время дугового разряда электрод и заготовка оплавляются, при этом на конце электрода образуется капля металла, которая переносится на заготовку преимущественно во время короткого замыкания.
Плазменная наплавка осуществляется с использованием плазменной струи, представляющей собой частично или полностью ионизированный газ, обладающий свойствами электропроводности и имеющий высокую температуру. Она создаётся дуговым разрядом, размещённым в узком канале специального устройства, при обдуве электрической дуги потоком плазмообразующего газа.
Лазерная наплавка представляет собой технологический метод получения покрытий с заданными физико-механическими свойствами путём нанесения на поверхность детали наплавочного материала с последующим оплавлением его лазерным лучом.
Индукционная наплавка основана на использовании токов высокой частоты (ТВЧ) для нагрева металла детали и присадочного материала. Индукционный нагрев обеспечивает высокую скорость роста температуры (до 200°С/с) и высокую производительность процесса.
21. Восстановление деталей напылением.
Сущность процесса состоит в напылении предварительно расплавленного металла на специально подготовленную поверхность деталейструёй сжатого воздуха или инертного газа. При этом мелкие частицырасплавленного металла (размером 0,002–0,2 мм), находясь в пластическомсостоянии с температурой 0,85–0,95 от температуры плавления исходногометалла, с большой скоростью (140–300 м/с) достигают поверхности детали.При ударе о поверхность детали они деформируются и, внедряясь в её порыи неровности, образуют покрытие.
В зависимости от вида энергии, используемой в аппаратах для
напыления, различают следующие способы напыления: газопламенное, дуговое, индукционное (токами высокой частоты), детонационное и плазменное.
Газопламенное напыление покрытий выполняется с помощью специальных аппаратов, в которых напыляемый металл плавится под воздействием ацетиленокислородного пламени, а распыляется струёй сжатого воздуха.
Дуговое напыление – процесс, с помощью которого металл расплавляется электрической дугой, горящей между двумя проволоками, изолированными друг от друга.
Детонационное напыление заключается в расплавлении металла, его распылении и переносе на поверхность детали за счёт энергии взрыва смеси ацетилена и кислорода.
Плазменное напылениеосновано на нанесении металлических покрытий на поверхность детали путём использования тепловых и динамических свойств плазменной струи. В качестве плазмообразующего газа применяют азот, гелий или аргон.
22. Восстановление деталей припеканием.
Припекание – технологический процесс получения покрытий, заключающийся в нанесении на поверхность детали порошковой формовки или слоя порошка и нагрева их до температуры, обеспечивающей спекание порошкового материала и образование прочной диффузионной связи с деталью.
Порошковые покрытия из металлов и сплавов относятся к перспективным из-за большого разнообразия способов образования этих покрытий для деталей различного функционального назначения. Такая универсальность обусловлена самой природой покрытия, состоящего из спечённого порошкового материала, состав которого может быть практически любым.
Термодиффузионным индукционным припеканиемспособом обмазки (рис. 4.21, а) можно получать покрытия большой пористости в основном для антифрикционных деталей.
Центробежное индукционное припекание (рис. 4.22) позволяет получать качественные покрытия на внутренних поверхностях цилиндрических деталей при вращении их в индукторе высокочастотной установки.
Электроконтактное припекание (рис. 4.24) металлических порошков может осуществляться с предварительным формованием порошкового слоя или в свободно насыпанном состоянии.
infopedia.su
Восстановление деталей напылением и наплавкой
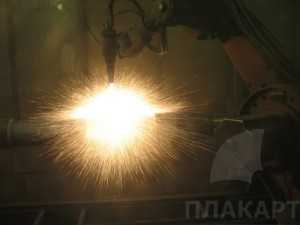
Восстановление штока напылением
Восстановление деталей наплавкой и напылением заменяет хромирование и имеет ряд неоспоримых преимуществ. Газотермическое напыление позволяет вернуть деталям их первоначальные характеристики, а порой и значительно увеличить их работоспособность. При этом износ должен быть не более 0,3 мм. С помощью напыления или наплавки создаётся покрытие твёрдостью более 60 HRC, адгезией более 30 Мпа, чего нельзя достигнуть методом хромирования. После такой обработки поверхность обладает высокой плотностью и надежно защищена от коррозии.
Восстановление деталей напылением, без покрытия хромом, позволяет избежать термических поводок благодаря небольшому нагреву поверхности изделия. Кроме того, отсутствие перемешивания с основой позволяет получить требуемые твердость и химический состав поверхности. Восстановление наплавкой может привести к термическим поводкам, однако результатом является покрытие, обладающее металлургической связью с основой, чего нельзя добиться при хромировании поверхности. При использовании покрытия хромом, детали быстрее изнашиваются и обеспечивается плохая прирабатываемость.
Восстановление вала наплавкой
Обработка деталей, так же, как при хромировании, осуществляется в несколько этапов: подготовка, непосредственное нанесение покрытия, дополнительная механическая обработка поверхности. Работу осуществляют сотрудники с солидным опытом работы.
Отказавшись от неэффективной технологии хромирования, мы восстанавливаем детали газопламенным и плазменным напылением, лазерной и плазменной наплавкой (без покрытия хрома), выполняем механическую обработку (токарную, шлифовальную, суперфиниш). Нанесение покрытий осуществляется в наших цехах по всей территории России.
Более подробную информацию о методе напыления и наплавки и его преимуществах перед хромированием Вы сможете получить по телефонам, указанным на сайте.
tspc.kz