Высоколегированные марки стали: Сталь высоколегированная и сплавы КОРРОЗОННОСТОЙКИЕ ЖАРОСТОЙКИЕ И ЖАРОПРОЧНЫЕ (ГОСТ 5632-72)
alexxlab | 04.06.2023 | 0 | Разное
Сталь высоколегированная и сплавы КОРРОЗОННОСТОЙКИЕ ЖАРОСТОЙКИЕ И ЖАРОПРОЧНЫЕ (ГОСТ 5632-72)
Стали высоколегированные и сплавы коррозионностойкие жаростойкие и жаропрочные (ГОСТ 5632-72) изготавливают марок: 40Х9С2, 40Х10С2М, 08X13, 12X13, 20X13, 30X13, 40X13, 10Х14АГ15, 12X17, 08X17Т, 95X18, 08Х18Т1, 15Х25Т, 15X28, 25Х13Н2, 20Х23Н13, 20Х23Н18, 10Х23Н18, 20Х25Н20С2, 15Х12ВНМФ, 20Х12ВНМФ, 37Х12Н8Г8МФБ, 13Х11Н2В2МФ, 45Х14Н14В2М, 40Х15Н7Г7Ф2МС, 08Х17Н13М2Т, 10Х17Н13М2Т, 31Х19Н9МВБТ, 10Х14Г14Н4Т, 14Х17Н2, 12Х18Н9, 17Х18Н9, 08Х18Н10, 12Х18Н9Т, 12Х18Н10Т, 08Х18Н10Т, 12Х18Н12Т, 08Х18Г8Н2Т, 20Х20Н14С2, 08Х22Н6Т, 12Х25Н16Г7АР.Сплавы по (ГОСТ 5632-72) изготавливают марок:06ХН28МДТ, ХН35ВТ, ХН35ВТЮ, ХН70Ю, ХН70ВМЮТ, ХН77ТЮР, ХН78Т, ХН80ТБЮ. ГОСТ 5632-72 содержит и другие марки сталей и сплавов. | |||
Марки, область применения и свариваемость сталей (ГОСТ 5632-72) | |||
МАРКА СТАЛИ |
ЗАМЕНИТЕЛЬ
|
ПРИМЕНЕНИЕ
|
СВАРИВАЕМОСТЬ
|
---|---|---|---|
40Х9С2 | Выпускные клапана двигателей, крепежные детали | Не применяется для сварных конструкций | |
40X1 ОС2М | Клапана двигателей, крепежные детали | Трудносвариваемая | |
08X13 12X13 20X13 25X1 ЗН2 |
Стали: 12X13 12Х18Н9Т Сталь: 20X13 Стали: 12X13 14X1 7Н2 |
Детали с повышенной пластичностью, подвергающиеся ударным нагрузкам | Ограниченно свариваемая |
30X13 40X13 |
Сталь: 40X13 Сталь: 30X13 |
Режущий инструмент, предметы домашнего обихода | Не применяется для сварных конструкций |
10Х14АП6 | Стали: 12Х18Н9, 08X1 8Н10, 12Х18Н9Т, 12Н18Н10Т |
Для немагнитных деталей, работающих в слабоагрессивных средах |
Сваривается без ограничений |
12X17 | Сталь: 12Х18Н9Т |
Крепежные детали, работающие в кислых растворах |
Трудносвариваемая |
08X1 7Т 08X1 8Т1 | Стали: 12X17, 08X1 8Т1 Стали: 12X17, 08X1 7Т |
Для конструкций, подвергающихся ударным нагрузкам и работающих в кислых средах |
Ограниченно свариваемая |
95X18 |
|
Не применяется для сварных конструкций |
|
15Х25Т | Сталь: 12Х18Н10Т |
Для сварных конструкций, не подвергающихся воздействию ударных нагрузок |
Трудносвариваемая |
15X28 | Стали: 15Х25Т, 20Х23Н18 |
Для сварных конструкций, не подвергающихся воздействию ударных нагрузок |
Трудносвариваемая |
20Х23Н13 |
Трубы и детали, работающие при высоких температурах |
Трудносвариваемая |
|
20Н23Н18 | Стали: 10Х25Т 20Х23Н13 |
Детали, работающие при температуре до 1100°С |
Ограниченно свариваемая |
10Х23Н18 |
Листовые детали, работающие при температуре до 1 100 °С |
Ограниченно свариваемая |
|
20Х25Н20С2 |
Детали печей, работающие при температуре до 1100°С |
Ограниченно свариваемая |
|
15Х12ВНМФ |
Детали, работающие при температуре до 780 °С |
Трудносвариваемая |
|
20Х12ВНМФ | Стали: 15Х12ВНМФ, 18Х11МНФБ |
Высоконагруженные детали |
Трудносвариваемая |
08Х17Н13М21 | Сталь: 10Х17Н13М21 |
Сварные конструкции, крепежные детали |
Трудносвариваемая |
10Х17НЗМ2Т |
Сварные конструкции |
Трудносвариваемая |
|
31Х19Н9МВБТ |
Крепежные детали |
Трудносвариваемая |
|
10Х14П4Н4Т | Стали: 20Х13Н4Г9, 12Х18Н9Т, 12Х18Н10Т, 08Х18Н10Т |
Для изготовления сварного оборудования и криогенной техники до темп.![]() |
Трудносвариваемая |
14Х17Н2 | Сталь: 20X1 7Н2 |
Детали компрессорных машин |
Трудносвариваемая |
12Х18Н9 17Х18Н9 | Стали: 20Х13Н4Г9, 10Х14Г14Н4Т Сталь: 20Х13Н4Г9 |
Холоднокатаный лист и лента повышенной прочности |
Сваривается без ограничений |
08X1 8Н10 08Х18Н10Т 12Х18Н9Т12Х18Н10Т | Сталь: 12Х18Н10Т Стали: 15Х25Т, 08Х18Г8Н2Т, 10Х14Г14Н4Т, |
Трубы, детали печной арматуры |
|
Высоколегированная сталь
Легирующие элементы образуют с железом химические связи, что существенно влияет на свойства материала и улучшает его качество. Химические добавки вводятся в сплав с учетом его назначения и необходимых характеристик, например:
- жаростойкость увеличивают Al, Si, Co;
- красностойкость – Mo;
- плотность – Ti, V;
- кислотоупорность – Si;
- прочность, износостойкость – Cr, V, Ti, Ni, Mn;
- твердость – Cr, V;
- упругость – Cr;
- стойкость к температурным расширениям – W;
- антикоррозионные качества – Ni, Mo, Ti, Cr;
- устойчивость перед ударными нагрузками – Mn, Co;
- прочность молекулярной решетки – W.
Сферы применения
Сложно переоценить, что значит высоколегированная сталь для нефтяной и химической промышленности, энергетики, машино- и авиастроения. Из таких сплавов производятся конструкции, используемые в агрессивных средах и при температурных перепадах. В газовой промышленности применяются коррозиестойкие легированные стали с содержанием углерода, уменьшенным до 0,12%. Элементы из окалиностойких сплавов используются в печах и в роли нагревательных элементов.
Классификация
Такие сплавы классифицируются:- По структуре – бывают аустенитные, аустенитно-ферритные и ферритные, аустенитно-мартенситные и мартенситные. Наиболее популярные аустенитные составы. Содержание легирующих веществ у них достигает 55%. В качестве основных компонентов используются хром (18%) и никель (до 8%). Остальные примеси вводятся в зависимости от необходимых свойств материала.
- По преобладающей составляющей – сплавы на никелевой основе (50% Ni или более) и на железоникелевой (свыше 65% Fe и Ni в соотношении 1,5:1).
- По свойствам – коррозиестойкие, жаростойкие, жаропрочные.
- По доминирующему компоненту, которым легировали сплав, – хромистые, хромомарганцевые, хромоникелевые.
- По тепловым характеристикам:
- элинвар (Х8Н36) – имеет стабильный модуль упругости и рабочий температурный диапазон от -50 до +100 °С, используется для изготовления часовых пружин и деталей измерительных приборов;
- платинит (ЭН42) – по тепловому расширению идентичен стеклу, используется для производства электродов ламп накаливания.
- По магнитным свойствам – магнитные (магнитомягкие и магнитотвердые) и немагнитные.
Марки высоколегированных сталей
Марка | Содержание химических компонентов, % | ||||||
---|---|---|---|---|---|---|---|
C | Mn | Si | S | P | B | Al | |
СН1А | |||||||
1006АК | 0,25–0,4 | ˃0,02 | |||||
1008АК | 0,3–0,5 | ˃0,02 | |||||
1010АК | 0,08–0,13 | 0,3–0,6 | ˃0,02 | ||||
1012АК | 0,1–0,15 | 0,3–0,6 | ˃0,02 | ||||
1015АК | 0,13–0,18 | 0,3–0,6 | ˃0,02 | ||||
1018АК | 0,15–0,2 | 0,7–0,9 | ˃0,02 | ||||
1018SK | 0,15–0,2 | 0,7–0,9 | 0,1–0,35 | ||||
1022AK | 0,18–0,23 | 0,7–1 | ˃0,02 | ||||
1022SK | 0,18–0,23 | 0,7–1 | 0,1–0,35 | ||||
S25C | 0,22–0,28 | 0,22–0,28 | 0,15–0,35 | ||||
10B21 | 0,18–0,23 | 0,7–1 | ˃0,0005 | ||||
10B33 | 0,32–0,36 | 0,7–1 | 0,15–0,35 | ˃0,0005 | |||
1541 | 0,36–0,44 | 1,35–1,65 |
Характеристики
Свойства высоколегированных сталей зависят от марки, формулы сплава, легирующих веществ и их процентного содержания. При помощи термообработки и легирования определенными компонентами материалам придаются необходимые характеристики:
- прочность;
- твердость;
- сопротивление ползучести при нагреве;
- упругость;
- пластичность;
- устойчивость к деформации, истиранию, коррозии, износу;
- жаростойкость;
- жаропрочность;
- другие требуемые качества.
Например, по технологии штампосварки из таких сплавов производят изделия, выдерживающие сверхнизкие температуры до -253 °С. При обработке кремнием получают ферросилиды, устойчивые к кислотным средам.
Компания «Металлист» выполняет комплекс услуг по обработке высоколегированной стали:
- лазерная резка металла;
- плазменная резка металла;
- гибка металла;
- слесарные работы по металлу;
- порошковая покраска изделий из металла.
Похожие статьи
Инструментальная углеродистая сталь. Состав и применение
В производственной промышленности часто используют углеродистые инструментальные стали.
Читать дальше
В чём цель легирования стали и как оно влияет на характеристики материала
Классическая сталь состоит из углерода и железа. К сожалению, свойство данного металла не всегда подходит к предъявляемым требованиям в промышленных отраслях.
Читать дальше
Виды и марки листовой стали
Под сталью понимают сплав железа, углерода и других элементов. Как правило, процент углерода не превышает показатель в 2,14%.
Читать дальше
Высоколегированная сталь
Перейти к основному содержанию
| ||||
|
Сложный клиент……
8 марта 2023 г.
Решения для управления проектами
4 марта 2023 г.
Когда работа идет медленно
1 марта 2023 г.
Стратегия управления проектами
13 января 2023 г.
Управление рисками
6 января 2023 г.
Операции и прогнозирование в проекте Управление
3 января 2023 г.
Лидерство и навыки в проекте Управление
27 декабря 2022 г.
Управление проектом Основы
26 декабря 2022 г.
Испытание давлением
16 июля 2019 г.
Процедуры термообработки
11 июля 2019 г.
Все о легированной стали: определение, типы и применение
Легированная сталь — это тип стали, в который для улучшения свойств добавляются легирующие элементы, отличные от углерода. Некоторые из распространенных добавок к легированной стали включают: хром, кобальт, колумбий, молибден, марганец, никель, титан, вольфрам, кремний и ванадий. Легированные стали известны своими улучшенными свойствами по сравнению с обычной углеродистой сталью, такими как: коррозионная стойкость, твердость, прочность, износостойкость и ударная вязкость. Легированные стали используются для изготовления производственной оснастки и конечной продукции практически во всех отраслях промышленности. Точная марка и состав легированной стали могут быть адаптированы к требованиям применения.
В этой статье обсуждаются различные классы легированных сталей, включая их составы, свойства и области применения.
Что такое легированная сталь?
Легированная сталь представляет собой материал на основе железа, который помимо углерода содержит один или несколько преднамеренно добавленных элементов. Легирующие элементы добавляются в сталь для улучшения одного или нескольких ее физических и/или механических свойств, таких как: твердость, прочность, ударная вязкость, жаростойкость, коррозионная стойкость и износостойкость. Эти элементы обычно составляют 1-50% массы металла. Существует множество способов группировки легированных сталей. Их можно сгруппировать по основным легирующим элементам (например, нержавеющая сталь содержит значительное количество хрома) или по процентному содержанию всех легирующих элементов, содержащихся в стали (например, высоколегированная сталь обычно содержит более 8 % легирующих элементов, тогда как в низколегированной стали менее 8 %).
Каков состав легированной стали?
В зависимости от желаемых свойств материала легированная сталь может содержать большое разнообразие легирующих элементов в различных количествах. Каждый из этих элементов добавляется для улучшения некоторых свойств стали, таких как твердость или коррозионная стойкость. Типичные легирующие элементы включают: бор, хром, молибден, марганец, никель, кремний, вольфрам и ванадий. Другие менее распространенные элементы, которые могут быть добавлены: алюминий, кобальт, медь, свинец, олово, титан и цирконий.
Сколько углерода содержится в легированной стали?
Содержание углерода в легированной стали зависит от типа используемой легированной стали. Большинство сталей имеют содержание углерода ниже 0,35% углерода по весу. Например, низкоуглеродистая сталь, предназначенная для сварки, имеет содержание углерода ниже 0,25% масс., а часто содержание углерода составляет менее 0,15% масс. Однако инструментальные стали представляют собой тип легированной стали с высоким содержанием углерода, обычно от 0,7 до 1,5.
Как изготавливают легированную сталь?
Легированная сталь производится путем плавки основных сплавов в электропечи при температуре свыше 1600 °С в течение 8-12 часов. Затем его отжигают при температуре более 500 ° C, чтобы изменить химические и физические свойства и удалить примеси. Прокатная окалина (полученная в результате отжига) удаляется с поверхности плавиковой кислотой. Отжиг и удаление окалины повторяются до тех пор, пока сталь не расплавится. Расплавленная сталь отливается для прокатки и придания окончательной формы в зависимости от требуемых размеров.
Как правило, сталь производится с использованием одного из двух процессов: в электродуговой печи (ЭДП) или в доменной печи. Доменная печь — это начальный процесс превращения оксидов железа в сталь. Чугун производится в доменной печи из кокса, железной руды и известняка. ЭДП отличается от доменной печи тем, что она создает расплавленную сталь путем плавления стального лома, железа прямого восстановления и/или чугуна с использованием электрического тока.
Где используется легированная сталь?
Применение легированной стали очень широко и зависит от типа легированной стали. Некоторые легированные стали используются для производства труб, особенно для использования в энергетике. В то время как другие используются в производстве коррозионно-стойких контейнеров, столового серебра, кастрюль, сковородок и нагревательных компонентов для тостеров и другого кухонного оборудования. Легированные стали можно разделить на две основные категории: низколегированные стали и высоколегированные стали. Применение легированных сталей в основном определяется категорией, к которой они относятся.
Низколегированные стали используются в различных отраслях промышленности благодаря их прочности, обрабатываемости и доступности. Их можно найти на кораблях, трубопроводах, сосудах под давлением, буровых платформах, военной технике и строительной технике.
Высоколегированные стали, с другой стороны, могут быть дорогими в производстве и сложными в работе. Тем не менее, они идеально подходят для автомобильной промышленности, химической обработки и оборудования для производства электроэнергии благодаря своей высокой прочности, ударной вязкости и коррозионной стойкости.
Каковы свойства легированной стали?
Легированная сталь может иметь широкий диапазон свойств в зависимости от конкретных легирующих элементов и их количества, добавленного в сталь. Некоторые из ключевых свойств, связанных с некоторыми легированными сталями: высокая производительность, долговечность, высокая прочность, хорошие характеристики в жестких условиях и коррозионная стойкость.
Какая температура требуется для закалки легированной стали?
Не все легированные стали поддаются термообработке. Примеры легированных сталей, которые нельзя подвергать термообработке, включают ферритные и аустенитные нержавеющие стали. Чтобы сталь была достаточно закаливаемой, для ее упрочнения необходим углерод. Стали, такие как мартенситные стали, например, могут быть закалены до относительно высокого содержания углерода. Для легированных сталей с достаточным содержанием углерода для закалки температура, необходимая для закалки легированной стали, обычно составляет 760-1300 °C (в зависимости от содержания углерода). Как и в случае с другими типами стали, закалка легированной стали включает контролируемый нагрев при критических температурах с последующим регулируемым охлаждением.
Каковы основные типы легированной стали?
Легированная сталь может быть разделена на семь основных категорий, как показано в Таблице 1 ниже:
1. Низколегированная сталь
Низколегированная сталь – это стали с легирующими элементами, составляющими менее 8% состава стали. металл. Эти легирующие элементы добавляются для улучшения механических свойств стали. Например: молибден повышает прочность; никель увеличивает ударную вязкость металла, хром добавляет жаропрочность, коррозионную стойкость и твердость.
Сталь низколегированная широко применяется в производстве и строительстве. Обычно эта сталь используется в военных транспортных средствах, строительной технике, кораблях, трубопроводах, сосудах под давлением, конструкционной стали и платформах для бурения нефтяных скважин.
2.
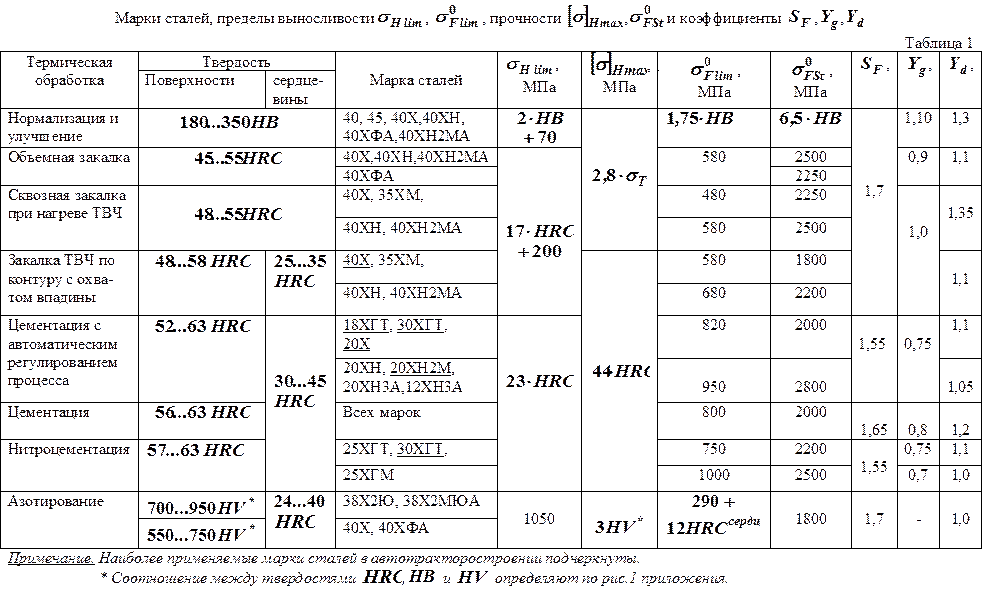
Высокопрочная низколегированная (HSLA) сталь или микролегированная сталь обеспечивает как высокую прочность, так и хорошую устойчивость к атмосферной коррозии. Существует шесть основных категорий стали HSLA: атмосферостойкая сталь, игольчатая ферритная сталь, сталь с уменьшенным перлитом, двухфазная сталь, сталь с контрольным прокатом и микролегированная ферритно-перлитная сталь. Как правило, медь, хром, фосфор и кремний используются для повышения коррозионной стойкости, а ванадий, ниобий, титан и медь — для увеличения прочности. Высокая прочность сталей HSLA может затруднить их формование. В определенных ситуациях добавляют цирконий или кальций, чтобы облегчить их формирование.
HSLA широко используется в автомобильной промышленности. Горячекатаная сталь HSLA может использоваться для систем подвески, шасси, колес и механизмов сидений. Принимая во внимание, что холоднокатаные стали HSLA могут использоваться для усиления и кронштейнов сидений.
3. Высоколегированная сталь
Высоколегированная сталь отличается высоким содержанием легирующих элементов более 8% от общего состава стали. Производство высоколегированной стали может быть дорогим, и с ней может быть сложно работать. Тем не менее, эти марки идеально подходят для автомобильной промышленности, конструкционных компонентов, оборудования для химической обработки и производства электроэнергии благодаря их твердости, коррозионной стойкости и ударной вязкости.
4. Нержавеющая сталь
Нержавеющая сталь является одной из самых известных легированных сталей и самой коррозионностойкой. Как правило, в качестве основных легирующих элементов она содержит некоторое сочетание никеля, хрома и молибдена, которые составляют около 11-30 % состава стали. Существует три типа нержавеющей стали: аустенитная, ферритная и мартенситная.
Аустенитные стали обычно используются для содержания агрессивных жидкостей и оборудования в горнодобывающей, химической, архитектурной или фармацевтической промышленности. В аустенитных сталях содержится большое количество никеля (до 35%), молибдена, хрома (16—26%), ниобия, углерода до 0,15%. Аустенитные стали часто обладают лучшей коррозионной стойкостью из всех нержавеющих сталей. Эти стали также обладают высокой формуемостью и прочностью и обычно востребованы благодаря своим свойствам при экстремальных температурах.
Ферритная сталь, используемая в промышленном оборудовании и автомобилях, представляет собой сорт нержавеющей стали с содержанием углерода менее 0,10% и более 12% углерода. Эта марка стали была разработана для защиты от коррозии и окисления, в частности от коррозии под напряжением. Эти стали практически не упрочняются термической обработкой и лишь слегка упрочняются холодной прокаткой.
Мартенситные стали, в основном используемые для изготовления столовых приборов, имеют типичное содержание хрома от 11,6 до 18% с добавлением 1,2% углерода и никеля. Как группа, самое высокое содержание хрома в мартенситных сталях ниже, чем самое высокое содержание хрома в ферритных и аустенитных сталях. Мартенситные стали известны своей исключительной прокаливаемостью при умеренной коррозионной стойкости. Это делает их идеальными для столовых приборов, гаечных ключей, хирургических инструментов и турбин.
5. Микролегированная сталь
Высокопрочные низколегированные стали (HSLA) часто называют микролегированными сталями.
6. Усовершенствованная высокопрочная сталь (AHSS)
Усовершенствованная высокопрочная сталь (AHSS) в основном используется в автомобильной промышленности. Этот металлический сплав играет ключевую роль в снижении общего веса транспортных средств. Он обладает уникальными свойствами, такими как: высокая прочность и оптимизированная формуемость, что делает его идеальным для применения в автомобилестроении.
7. Маржинальная сталь
Маржинальная сталь представляет собой особый вид стального сплава с низким содержанием углерода. Эта сверхвысокопрочная сталь обладает превосходной ударной вязкостью и хорошей пластичностью по сравнению с большинством сталей. В отличие от других стальных сплавов мартенситностареющая сталь упрочняется за счет осаждения интерметаллических соединений, а не за счет присутствия углерода. Мартенситно-стареющая сталь сочетает в себе высокую прочность и твердость с относительно высокой пластичностью благодаря отсутствию углерода и использованию интерметаллических осадков. Основными типами выделений являются Ni3Mo, Ni3Ti, Ni3Al и Fe2Mo, которые также встречаются в больших объемных фракциях. Мартенситно-стойкие стали в основном используются в аэрокосмической отрасли, а также в производстве инструментов и оружия.
8. Инструментальная сталь
Инструментальная сталь — термин, используемый для описания ряда углеродистых и легированных сталей, которые хорошо подходят для производства инструментов. Эти стали отличаются твердостью, износостойкостью, ударной вязкостью, устойчивостью к размягчению при высоких температурах. Инструментальная сталь идеально подходит для производства инструментов, включая (но не ограничиваясь) штампы для станков и ручные инструменты.
Подходит ли легированная сталь для литья под давлением?
Да, легированная сталь подходит для литья под давлением. Низколегированные стали являются одним из материалов, используемых в процессе литья под давлением. Легированная сталь марки Р20, например, используется для пресс-форм, которые используются для обычных пластмасс, поскольку они не вызывают коррозии или сильного износа.
Резюме
В этой статье представлена легированная сталь, объяснено, что это такое, и рассмотрена ее важная роль в производстве. Чтобы узнать больше о легированной стали, свяжитесь с представителем Xometry.
Xometry предоставляет широкий спектр производственных возможностей и других дополнительных услуг для всех ваших потребностей в прототипировании и производстве. Посетите наш веб-сайт, чтобы узнать больше или запросить бесплатное предложение без каких-либо обязательств.
Отказ от ответственности
Контент, отображаемый на этой веб-странице, предназначен только для информационных целей.