Взаимодействие нержавейки и черного металла: Можно ли приварить нержавейку к черному металлу
alexxlab | 13.05.1991 | 0 | Разное
Взаимодействие оцинкованных покрытий с другими металлами
Когда два разнородных металла вступают в контакт, и присутствует электролит, такой как влага, то возникает вероятность биметаллической коррозии у более электроотрицательного или анодного металла, как определено в электрохимическом ряду, который корродирует в первую очередь, предотвращая коррозию другого металла.
Биметаллический эффект является основой для защиты, которую цинковое покрытие (горячее цинкование) обеспечивает для малых зон незащищённой стали, если покрытие повреждено. Цинковые покрытия корродируют в первую очередь, защищая металл, который ниже его в электрохимическом ряду. Степень биметаллической коррозии будет зависеть от числа таких факторов, как контактируют металлы, соотношение площадей контактирующих металлов и условий эксплуатации. Как правило уровень биметаллической коррозии будет увеличиваться с увеличением разницы потенциалов между двумя металлами, например, как далеко расположены друг от друга два металла в гальваническом ряду напряжений. Однако потенциал может изменяться вследствие образования оксидного слоя и не может быть использован для определения степени возникновения биметаллической коррозии, так как другие факторы, которые приведены ниже, также важны. Соотношение площадей контактирующих металлов имеет существенное значение, и в идеале соотношение металлов анод-катод должно быть высоким. Если соотношение уменьшается, то могут возникнуть проблемы вследствие высокого уровня восстановления кислорода, которое может привести к увеличению коррозии анодного металла. Воздействующие условия имеют большое значение, т.к. для биметаллической коррозии электролит должен связать два имеющихся металла. В результате, в сухой окружающей среде (внутри помещения) вероятность биметаллической коррозии очень низкая, в то время как во внешних атмосферных условиях вероятность увеличивается, вследствие наличия влаги в виде дождя и конденсации. Наиболее худшими условиями является погружение в раствор, где электролит постоянно соединяет два металла.
Обычно любая возможность биметаллической коррозии может быть ослаблена электрической изоляцией двух металлов друг от друга. Для болтовых соединения могут быть обеспечены при использовании неопреновых или пластиковых шайб, в то время как для перекрытых поверхностей это может быть достигнуто использованием пластиковых прокладок или окрашиванием одной из поверхностей подходящей системы лакокрасочного покрытия. Обычно горячеоцинованная сталь хорошо функционирует в контакте с наиболее распространенными конструкционными металлами, когда в атмосферных условиях, обеспечивается высокое отношение площадей оцинкованной стали к другому металлу. И наоборот, в условиях погружения эффект биметаллической коррозии существенно увеличивается, и обычно требуется изоляция.
Медь и латунь
Если установка требует, чтобы контакт между гальванизированными материалами и медью или латунью в сырой или влажной окружающей среде, может произойти быстрая коррозия цинка. Даже сточные воды могут содержать достаточное количество растворенной меди, чтобы вызвать быструю коррозию.
Если использование меди или латуни в контакте с гальванизированными покрытиями неизбежно, должны быть приняты меры предосторожности, чтобы предотвратить электрический контакт между этими двумя металлами. Поверхность разъема должна быть изолирована непроводящими прокладками; соединения должны быть выполнены с изолирующим крепежом и уплотняющей втулкой. Это должно гарантировать, что вода повторно не распространиться и потоки воды от гальванизированной поверхности к медной или латунной не реверсирует.
Алюминиевая и нержавеющая сталь
В умеренных атмосферных условиях умеренной влажности, контакт между оцинкованной поверхностью и алюминия или нержавеющей стали, вряд ли вызовет существенную инкрементную коррозию. Тем не менее, при очень влажных условиях, оцинкованной поверхности может потребоваться электрическая изоляция от алюминия или нержавеющей стали.
Нержавеющая сталь
Когда гальванизированные болты используются на нержавеющей стали, цинк первоначально жертвует собой, пока защитный слой ржавчины не разовьется на нержавеющей стали. Как только этот слой ржавчины разовьется, он формирует слой изоляции, который предотвращает дальнейшую защиту цинка. Цинковое покрытие должно быть достаточно толстым, чтобы продлить защиту от ржавчины в течение несколько лет. У гальванизированных болтов выполненных горячим методом хватает цинкового покрытия, чтобы продлить защиту с минимальной потерей в эксплуатации покрытия.
Металл Воздействие атмосферы Погруженное состояние
Сельская местность Промышленные/городские районы Прибрежная зона Пресная вода Морская вода
Аллюминий а а-б а-б б б-в
Латунь б б а-в б-в в-г
Бронза б б б-в б-в в-г
Литейный чугун б б б-в б-в в-г
Медь б б-в б-в б-в в-г
Свинец а а-в а-б а-в а-в
Нержавеющая сталь а-б а-б а-б б б-в
a — Цинковое покрытие будет испытывать или дополнительную коррозию, или только незначительную. дополни- тельную коррозию, которая обычно допускается при эксплуатации.
Б — Цинковое покрытие будет испытывать незначительную или умеренную дополнительную коррозию, которая может быть допустимой в некоторых случаях эксплуатации.
В — Цинковое покрытие будет испытывать сильную дополнительную коррозию, необходимы защитные меры.
Г — Цинковое покрытие будет испытывать сильную дополнительную коррозию, контакта рекомендуется избегать.
Руководство, связанное с конкретным применением, касающимся оцинкованных стальных изделий в контакте с указанным металлом или сплавом.
а) Алюминий – Вероятность увеличения биметаллической коррозии вследствие атмосферного кон- такта с алюминием относительно низкая. Применение оцинкованной стали и алюминия, используемые в сочетании друг с другом, является плакирование алюминием. В этом случае рекомендуется изоляция вследствие большой площади поверхности алюминиевых пластин.
б) Медь – Вследствие большого потенциала, установившегося при контакте между сталью с цинковым покрытием, и медью и медьсодержащими сплавами, рекомендуется применение электроизоляции (даже в атмосферных условиях). При конструировании рекомендуется избегать стока воды с меди на оцинкованные изделия, так как малые количества меди, растворенной в воде, могут откладываться на изделии, что приведет к биметаллической коррозии.
в) Свинец – Вероятность биметаллической коррозии со свинцом в атмосферной среде низкая и нет информации о проблемах, касающихся, например, применения свинцовой гидроизоляции оцинкованных изделий и использование свинца в опорах с цинковым покрытием.
г) Нержавеющая сталь – Применение нержавеющей стали с оцинкованной сталью используется в виде гаек и болтов в атмосферных условиях. Учитывая низкий потенциал для биметаллической коррозии и малую площадь поверхности крепежных изделий из нержавеющей стали, биметаллическая коррозия обычно отсутствует, практика показывает необходимость сохранения изоляции, используя изолирующие шайбы. Практический опыт показывает, что там, где отношение площади поверхности цинка к площади другого металла большое, и указана категория «а» или «а – б», дополнительная коррозия как результат контакта будет незначительной или будет отсутствовать. Если соотношение площадей поверхностей уменьшено или выше, может потребоваться изоляция.
Свойства нержавейки и применяемость.

Свойства нержавейки и применяемость. Обозначение нагрузок на такелаж и крепеж из нержавейки
– Почему нержавейка не ржавеет
– Обозначение нагрузок на такелаж
– Нагрузки на болты и гайки из нержавейки
– Измерение химического состава нержавейки
Нержавеющая сталь – это сложнолегированный сплав с низким содержанием углерода и хромом не менее 10%. Она не ржавеет благодаря “ржавчине” окисла хрома на поверхности металла. Этот окисел на самом деле идеально прозрачный и очень стойкий к воздействию влаги и других агрессивных сред — фактически броня. Ржавление нержавеющей стали является результатом образования оксида, гидроксида или карбоната железа от воздействия внешних источников или разрушения пассивирующего слоя. Варианты цвета ржавчины от оранжевого до бурого и черного, зависят от типа оксида, гидроксида или карбоната и особенностей воды, участвующей в образовании молекул.
Степень устойчивости нержавеющей стали к коррозии частично зависит от обработки поверхности — шероховатая и царапанная может корродировать, а полированная до блеска сохраняет коррозионную стойкость. Причиной этого служит то, что ионы хлора могут проникать гораздо глубже под грязь, чем более объемные молекулы кислорода. Это явление также известно как «
глубинная коррозия». Хороший пример этого явления можно увидеть на пассажирских судах с перилами из полированной нержавеющей стали AISI 316. Еще про свойства нержавейки тут и тут.
Первый, самый распространенный тип нержавейки, обозначается A2 или AISI 304. Российское обозначение 12X18H9.
Когда мы встречаем в интернете в описании материала на товаре “нержавеющая сталь”, то, прежде всего, надо понять какой марки она? Если не указана марка, скорей всего имеется ввиду дешевая AISI 304.
В морском же деле следует использовать “морскую нержавейку”. Она и прослужит дольше, но и стоит подороже. Обозначается она как A4 или AISI 316. Российское обозначение 03Х17Н14М2. Предпоследняя буква указывает на наличие молибдена. Ее также называют кислотостойкой. Именно A4 широко используется для изготовления такелажа, дельных вещей и судовой оснастки. Более “породистые” сорта кислотостойкой нержавейки с низким содержанием углерода обозначают AISI 316L.
Существует несколько видов коррозии нержавеющей стали:
1. Общая коррозия, когда наблюдается разрушение окисной пленки на всей поверхности. При проникновении галогенов (фтора, хлора, брома и йода) через пассивирующую пленку происходит активный процесс коррозии. Именно поэтому при чистке нержавеющих поверхностей нельзя использовать хлорсодержащие вещества, например, белизну. Хлориды являются главным врагом нержавеющей стали.
2. Щелевая коррозия. Она возникает при наличии небольшого зазора в конструкциях из нержавеющей стали. Процесс ярко проявляется на примере крепежных элементов, эксплуатирующихся в морской воде. Хлориды, содержащиеся в воде, способствуют удалению окисного слоя. При отсутствии доступа кислорода и движущихся потоков воды коррозия продолжается.
3. Точечная. Она аналогична гальванической коррозии при точечном поражении защитного оксидного слоя и одновременном воздействии агрессивной среды. Нержавеющая сталь в поврежденном месте становится анодом, а пассивированная часть металла — катодом, в результате анод начинает быстрее растворяться, вызывая питтинговую коррозию.
4. Гальваническая коррозия, возникающая в результате прямого контакта разнородных металлов в агрессивной токопроводящей среде, например, в морской воде. При проектировании нержавеющих конструкций должны учитываться внешнее воздействие среды и взаимодействие в этих условиях нержавейки с другими металлами.
5. Межкристаллитная коррозия, возникающая при очень высокой температуре, например, при сварке.
6. Эрозивная коррозия, возникающая в результате воздействия абразивной жидкости с большой скоростью, постоянно разрушающей оксидную пленку.
Каков же самый простой и эффективный метод борьбы с коррозией нержавеющей стали? Чистота, чистота, и еще раз чистота. Посмотрите на нержавеющую кухонную раковину в любом доме — она подвергается воздействию самых различных химических веществ, но ее поверхность всегда остается яркой. Почему? Потому что постоянный поток свежей воды и протирка удаляют вредные химические вещества, которые могут повредить окисную пленку. Чистота имеет важнейшее значение для максимальной устойчивости нержавеющих сталей к коррозии.
Необходимо соблюдать несколько несложных правил и технологических приемов при использовании изделий из нержавейки:
1. Поскольку для образования прозрачного окисла нужен кислород, нержавейку надо сушить, а из карабинов с пружинками просто вытряхивать воду, иначе пружинка “умрет” со временем.
2. Наружные элементы на борту в обязательном порядке ставить на герметик, чтобы не затекала вода в щели и не возникало щелевой коррозии и “ржавых” подтеков.
3. Избегать глубоких царапин. В общем ничего страшного – царапина сама “заростет” окислом, но лучше помочь ей и обработать слишком глубокие “ямы” и заполировать до блеска. В крайнем случае применять “нулевку”.
4. Ничем не красить. В этом нет никакого смысла. Причина та же – без кислорода будет ржаветь.
5. Не применять ниже ватерлинии, иначе получите аккумуляторную батарею в соленой воде. Смотреть тут и тут чем это грозит. Если используете нержавеющий гребной винт на моторе или триммер, в обязательном порядке их вынимать из воды на время длительной стоянки или использовать анодную защиту в случае невозможности снять подводные нержавеющие части.
6. Техническое: чтобы не “закусывало” резьбу на талрепах 8245, похожих на них 4065 и прочих, рекомендуется смазывать специальной водоотталкивающей смазкой.
7. Избегать контактов изделий из нержавейки с металлами, способными образовать с ней гальваническую пару.
Например, нержавейка с цинком – практически 100% аккумулятор, если будет использоваться во влажной среде.
Однако крепеж из нержавейки часто используют для монтажа алюминиевых конструкций. В этом случае ставят влагозащитные EPDM-шайбы и герметизируют стыки.
8. И последнее — не экономить на A2, там, где требуется применение кислотостойкой A4 — потом дороже выйдет. Это уже проверено на чужом опыте.
Нержавейка абсолютно пригодна для сварки по причине низкого содержания углерода и отсутствия искусcтвенного покрытия, как в оцинкованных деталях. В месте сварки не образуется неприятной окалины. Остается только обработать место соединения, зашкурить и отполировать до блеска.
Более подробно свойства нержавейки описаны тут.
Химический состав нержавейки – здесь.
Расчет нагрузок на болты из нержавейки – по этой ссылке.
Не знакомым с терминами электрохимическая, гальваническая и щелевая коррозия рекомендуем ознакомиться с полезным материалом на rostfrei.
Обозначение нагрузок на такелаж
> Здравствуйте. Подскажите пожалуйста: на сайте в таблице на талрепы
> допустим есть графы WL/kg и BL. Что они значат?
WL – рабочая нагрузка.
BL – разрывная нагрузка. Обозначают в кило-Ньютонах (kN).
Обычно на такелаж применяют коэффициент запаса 4, т.е. разрывную делят на 4 для понимания рабочего диапазона. Иногда встречается коеффициент запаса 3 или 2, но это – кто как рискует.
> Как перевести из Ньютонов в килограммы?
Идем назад, к школьному курсу физики. Вспоминаем Второй закон Ньютона, из которого F=m*g, где g – ускорение свободного падения – равна 9,8. Соответственно m=F/g.
Обычно, на практике, совершенно точное вычисление нагрузок не требуется, поэтому, чтобы не усложнять себе жизнь, можно просто
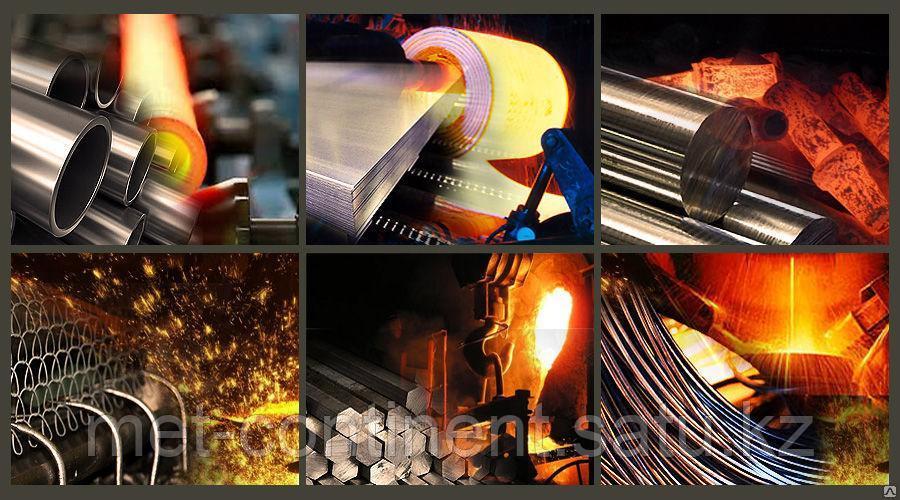
Например, #8382-4-08 DIN 3060 Трос мягкий 7X19 A4 8MM – BL= 41.7kN. Следовательно разрывная нагрузка составит около 4 тонн, а рабочая – 1 тонну.
Обозначение нагрузок на болты и гайки из нержавейки
> Что такое предел прочности?
> Предел текучести – что это?
> Что прочнее, нержавеющий болт или оцинкованный?
> A2-70 и A4-80 – что обозначают на головке нержавеющего болта?
А вот тут все подробно описано. С картинками и табличками.
Коротко:
– Предел прочности – когда ломается, предел текучести – когда гнется.
– Нержавеющий болт менее прочный. Весьма приблизительно соответствует КП 4.6 – 5.8.
– A4-80 приблизительно на 20% прочнее, чем A2-70, а A2-50 – вообще “пластилиновый”.
Как измерить химический состав нержавейки?
Например, вот так.
Электрохимическая и щелевая коррозия. Справочник ROSTFREI. Петербург +7(812)297-73-38 ПРОТЕХ
- Общие сведения о нержавеющей стали
- Виды и свойства нержавеющей стали
- Химический состав нержавеющей стали и соответствие стандартов
- Технические характеристики аустенитной нержавеющей стали
- Электрохимическая и щелевая коррозия
- Практическое использование крепежа на судне
- Нержавейка в производстве ножей
- Измерение химического состава нержавеющей стали ручным прибором
Одна из лучших статей о электрохимических реакциях с нержавеющией сталью и о коррозии нержавейки была опубликована в 2004 году в журнале КАТЕРА И ЯХТЫ по материалам фирмы Quicksilver Marine Parts & Accessories. Приведем здесь частично текст и изображения из этой статьи…
Спустя некоторое время мы наткнулись на тренд обсуждение этого материала на форуме о подводной охоте. Статья не претендует на “глубину” познания процессов, а скорее отвечает на вопрос: что же делать, и как не наступить на грабли? Истина где-то рядом с кислородом 🙂 и по теме топика там есть много здравых мыслей. Еще ветка есть тут.
ЩЕЛЕВАЯ КОРРОЗИЯ
Нержавеющая сталь — это сложнолегированный сплав, в который входят хром и никель. Не ржавеет она благодаря образующейся на поверхности изделия тонкой пленке оксида хрома. Этот окисел хрома на самом деле идеально прозрачний и прочный как броня. Именно он защищает поверхность от ржавчины. При отсутствии кислорода оксидный слой разрушается, и нержавеющая сталь покрывается ржавчиной не хуже обычной. Иными словами, “нержавейка” не ржавеет только до тех пор, пока имеется доступ кислорода и покрывающие ее окисел хрома не разрушен. Вот именно понимание этого процесса позволит ответить на много вопросов о применяемости нержавейки.
Самый простой способ предотвратить данную разновидность коррозии (щелевой) — ограничить доступ влаги в “щели” с использованием герметика, вовремя удалять образующиеся отложения и обеспечить хорошую вентиляцию “сомнительных” мест. Краткие рекомендации по работе с нержавеющим крепежом также описаны на сайте интернет-магазина deel.ru дельных вещей и такелажа их нержавейки.
ВИДЫ МОРСКОЙ КОРРОЗИИ
Гальваническая коррозия представляет собой электрохимическую реакцию между двумя и более различными (или разнородными) металлами. Различными, потому что для того, чтобы началась реакция, один должен быть более химически активным (или менее стабильным), чем другой или другие. Когда мы говорим про гальваническую коррозию, то имеем в виду электрообмен. Все металлы обладают электрическим потенциалом, поскольку у всех атомов есть электроны, движение которых и есть электричество.
Гальваническая коррозия более активного металла начинается в тот момент, когда две или более детали из разнородных металлов, имеющие взаимный контакт (благодаря обычному соприкосновению, или же посредством проводника) помещаются в электролит (любую жидкость, проводящую электричество). Электролитом может быть что угодно, за исключением химически чистой воды. Не только соленая морская, но и обычная вода из-под крана благодаря наличию минеральных веществ является превосходным электролитом, и с ростом температуры электропроводность ее только растет (по этой причине корпуса судов, эксплуатирующихся в жарком климате, заметно больше подвержены коррозии, чем на Севере).
Процесс гальванической коррозии можно наиболее наглядно проиллюстрировать на примере алюминиевой подводной части подвесного мотора и гребного винта из нержавеющей стали. Алюминий — более химически активный металл — является в данном случае анодом, а менее активная нержавеющая сталь — катодом.
Вот что происходит, когда эта пара помещается в воду, играющую роль электролита (рис. 1):1. На аноде:
a. Через место контакта (в нашем случае — через гребной вал) электроны перетекают с анода, металла более химически активного на катод — гребной винт. Происходит следующая реакция: Al ® Al+++ +3e.
b. При этом атомы более химически активного металла превращаются в ионы (этим термином обозначаются атомы с “недостатком“ или “избытком” электронов), которые устремляются в воду и связываются с ионами кислорода, обмениваясь с ними электронами и образуя оксид алюминия. (Процесс этот ничем не отличается от того, что происходит с ионами железа при образовании оксида железа).
c.

2. На катоде:
a. С анода поступают электроны, причем они не просто накапливаются, а вступают в реакцию с ионами электролита.
b. Реакция обычно происходит такая:
11/2 О2 + 3 Н2О + 6 е ® 6 ОН—.
c. Ион гидроокиси ОН— — щелочной, поэтому в районе катода образуется щелочная среда. (Следует отметить, что это обстоятельство надо обязательно иметь в виду владельцам деревянных корпусов — щелочь разрушает целлюлозу).
Очень важно понять, что следствием освобождения каждого позитивного иона металла на аноде обязательно является формирование негативного иона электролита, образующегося вследствие реакции электронов катода. Электрически анодные и катодные реакции должны быть эквивалентны. Рост или снижение уровня катодной реакции вызывает ответные рост или снижение уровня анодной реакции. Это ключевой факт для понимания процесса коррозии и управления им. Его можно проиллюстрировать эффектом влияния размеров анода и катода. Если к очень большому аноду подключить маленький катод, процесс коррозии анода пойдет медленно. А если поступить наоборот, то анод очень быстро разрушится.
Алюминиевых деталей на катере или мотолодке полным-полно. И если не контролировать процесс гальванической коррозии, все они быстро выйдут из строя.
Гальваническая коррозия может протекать даже в том случае, если на вашей лодке нет ни одной детали из нержавеющей стали. Предположим, что и подводная часть мотора, и винт алюминиевые, но лодку вы обычно ставите у пирса со стальной стенкой и подключаетесь при этом к береговой системе электроснабжения. Провод заземления (так называемый “третий” — дань безопасности) соединяет при этом алюминиевые детали лодки с погруженной в воду стальной стенкой (рис. 2). Если учесть внушительную массу стальной стенки, то и подводной части мотора, и винту грозят серьезные повреждения. Предотвратить их можно при помощи гальванического изолятора — своеобразного фильтра, отсекающего токи низкого напряжения и позволяющего при этом заземляющему проводу в случае пробоя изоляции или короткого замыкания выполнить свою функцию — отвести ток в землю и спасти вам жизнь.
НА ЧТО ОБРАЩАТЬ ВНИМАНИЕ
Гальваническую коррозию подводных частей подвесных моторов и угловых колонок — или любых алюминиевых частей лодки — значительно ускоряет наличие деталей из нержавеющей стали, таких, как гребные винты, триммеры (особенно если они “заземлены” на двигатель), узлы дистанционного управления.

Другая причина, способная ускорить процесс гальванической коррозии — это уменьшение полезной площади анодных протекторов (о них тоже будет рассказано позже). Но и без наличия нержавеющей стали расположенные под водой алюминиевые детали все равно подвергаются воздействию гальванической коррозии — хотя и не столь интенсивной, как при контакте с иным металлом. При наличии электролита на большинстве однородных, вроде бы, металлических поверхностей все равно образуются крошечные аноды и катоды — в тех местах, где состав сплава неоднороден или имеются посторонние вкрапления или примеси — например, частицы металла с форм или штампов.
Нержавеющую сталь в качестве катода и алюминий в качестве анода мы использовали лишь в качестве одного из примеров; образовать “батарею” для запуска гальванической коррозии в паре с алюминием способен любой другой металл. К примеру, такая пара образуется и при контакте алюминия с цинком, только на сей раз катодом становится алюминий, а подвергается коррозии цинк — металл более химически активный. Один из худших врагов алюминия при образовании гальванической пары — это медь или медные сплавы (бронза).
Резюмируя сказанное, рекомендуется всегда обращать внимание при монтаже на ряд активности металлов: золото, нержавейка, бронза, медь, латунь, сталь, чугун, алюминий, цинк, магний. Чем дальше друг от друга стоят металлы в этом ряду активности, тем больше вероятность возникновения между ними электрохимической коррозии.
Например, категорически не рекомендуется использовать нержавеющий крепеж в контакте с алюминием, если этот узел подвергается интенсивному влиянию влаги. Вот тут нужно сделать оговорку. Именно нельзя, если нержавейка с алюминием будет в воде постоянно. Скажем ниже ватерлинии. Как раз наоборот, при монтаже деталей на корпусе лодки или на фасадных конструкциях, надо применять нержавейку по алюминию. Только использовать герметик для борьбы с щелями и затеканием. Оцинкованные детали для этого не годны совсем.
Еще один пример на основе таблицы активности металлов – соединение электрических алюминиевых и медных проводов между собой. Для соединения всегда рекомендуется использовать переходные клеммные колодки, которые есть в продаже в любом электротехническом магазине.
Другая причина гальванической коррозии — подключение к береговой электросети. При этом алюминиевая подводная часть вашего мотора или колонки посредством заземляющего вывода подключается к подводным частям других лодок и становится частью огромной гальванической батареи, связанной с погруженным в воду береговым металлом. При этом не только на вашей лодке, но и на соседних коррозия значительно ускоряется.
КОРРОЗИЯ ОТ БЛУЖДАЮЩИХ ТОКОВ
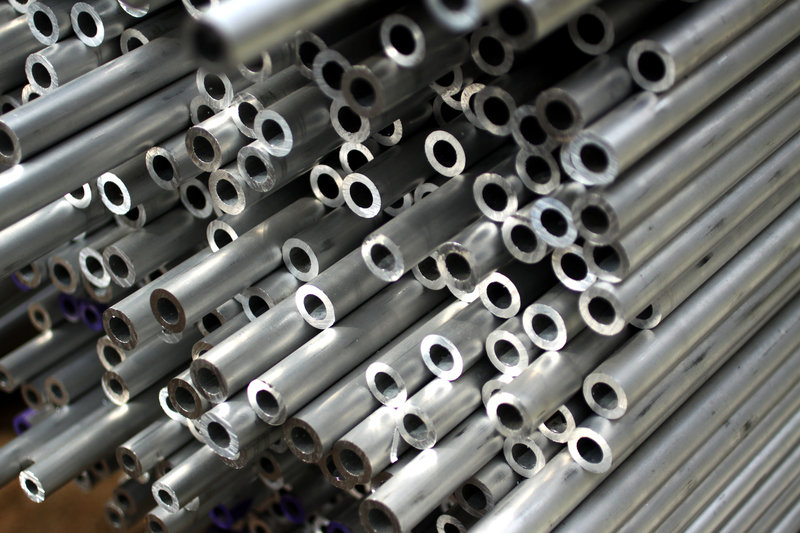
Данная разновидность коррозии отличается от гальванической, хотя природа у них одна. Гальваническая коррозия вызывается соединением двух разнородных металлов и происходит за счет их электрических потенциалов. Один металл выступает в роли анода, другой — в роли катода. Здесь же электрический ток попадает на подводную часть лодки из внешнего источника и через воду уходит в землю.
К примеру, ваша лодка расположена между лодкой с утечкой постоянного тока и местом, являющимся хорошим заземлением для этого тока. Хотя ток могут уходить в землю и через воду, ваша лодка может явиться проводником со значительно меньшим сопротивлением. Таким образом, ток будет уходить в землю и с нее. Наиболее интенсивно коррозия будет развиваться в том месте лодки, откуда ток уходит в воду.Блуждающие токи могут вызываться не только внешними, но и внутренними источниками — коротким замыканием в сети лодки, плохой изоляцией проводки, подмокшим контактом или неправильным подключением какого-либо элемента электрооборудования.
Наиболее распространенный внешний источник блуждающих токов — береговая сеть электроснабжения. Лодка с внутренним источником блуждающих токов (например, по причине повреждения изоляции одного из проводов) может стать причиной усиленной коррозии множества соседних лодок, подключенных к той же береговой электросети, если они обеспечивают лучшее заземление. Ток при этом передается на другие лодки посредством все того же “третьего” заземляющего провода.
Гораздо более неуловимый — но потенциально более опасный — случай коррозии блуждающих токов может происходить безо всяких проблем с электрооборудованием (и вашей лодки, и соседних). Предположим, что вы возвращаетесь на стоянку после выходных на воде, подсоединяетесь к береговому источнику, чтобы подзарядить аккумулятор, и спокойно уходите домой — автоматическое зарядное устройство само отключит зарядившуюся батарею. В понедельник по соседству с вашей лодкой причаливает большой стальной катер (с ободранной и поцарапанной краской). Владелец его тоже подключается к береговой сети и тоже оставляет свою посудину на несколько дней. Электрическая батарея готова — большой стальной корпус и небольшая подводная часть вашего мотора, соединенные заземляющим проводом. В зависимости от разделяющего их расстояния, разницы размеров и времени, которое ваш сосед решил провести на берегу, в следующие выходные вы можете обнаружить, что подводная часть вашего мотора либо просто покрыта белесым налетом, либо разрушилась чуть ли не полностью.
Ветка обсуждения тут и тут.
Нержавеющая сталь – черные металлы
Одной из характеристик, характеризующих нержавеющие стали, является минимальное содержание хрома 10,5% в качестве основного легирующего элемента. Четыре основные категории кованой нержавеющей стали в зависимости от металлургической структуры: аустенитная, ферритная, мартенситная и дисперсионно-твердеющая. Литые марки нержавеющей стали обычно обозначаются как жаропрочные или коррозионностойкие.
Аустенитная кованая нержавеющая сталь подразделяются на три группы:
- Серия AISI 200 (сплавы железо-хром-никель-марганец)
- Серия AISI 300 (сплавы железо-хром-никель)
- Сплавы, упрочненные азотом
Содержание углерода обычно низкое (0,15% или менее), а сплавы содержат не менее 16% хрома с достаточным количеством никеля и марганца для обеспечения аустенитной структуры при всех температурах от криогенной области до точки плавления сплава.
Аустенитные нержавеющие стали, упрочненные азотом, представляют собой сплавы хрома, марганца и азота; некоторые сорта также содержат никель. Пределы текучести этих сплавов (отожженных) обычно на 50% выше, чем у неазотсодержащих марок. Они немагнитны и большинство из них остаются таковыми даже после тяжелой холодной обработки.
Как и углерод, азот повышает прочность стали. Но, в отличие от углерода, в нержавеющей стали азот практически не соединяется с хромом. Эта комбинация, образующая карбид хрома, снижает прочность и коррозионную стойкость сплава.
До недавнего времени металлурги сталкивались с трудностями при добавлении контролируемых количеств азота в сплав. Развитие метода аргонно-кислородного обезуглероживания (AOD) сделало возможными уровни прочности, ранее недостижимые для обычных отожженных нержавеющих сплавов.
Аустенитные нержавеющие стали обычно используются там, где основными требованиями являются коррозионная стойкость и ударная вязкость. Типичные области применения включают валы, насосы, крепежные детали и трубопроводы в морской воде, а также оборудование для обработки химикатов, продуктов питания и молочных продуктов.
Ферритные деформируемые сплавы (серия AISI 400) содержат от 10,5 до 27% хрома. Кроме того, использование аргонно-кислородного обезуглероживания и вакуумно-индукционной плавки позволило получить несколько новых марок феррита, в том числе 18Cr-2Mo, 26Cr-1Mo, 29Cr-4Mo и 29Cr-4Mo-2Ni. С низким содержанием углерода, но, как правило, с более высоким содержанием хрома, чем мартенситные марки, эти стали не упрочняются термической обработкой и лишь умеренно упрочняются холодной обработкой. Ферритные нержавеющие стали являются магнитными и сохраняют свою основную микроструктуру до точки плавления, если в них присутствует достаточное количество Cr и Mo. В отожженном состоянии прочность этих марок примерно на 50 % выше, чем у углеродистых сталей.
Ферритные нержавеющие стали обычно используются там, где требуется умеренная коррозионная стойкость и где ударная вязкость не является основным требованием. Они также используются там, где коррозионное растрескивание под напряжением хлоридов может быть проблемой, поскольку они обладают высокой устойчивостью к этому типу коррозионного разрушения. В тяжелых сечениях трудно достичь достаточной ударной вязкости при использовании высоколегированных ферритных марок. Типичные области применения включают автомобильные отделочные и выхлопные системы, а также теплообменное оборудование для химической и нефтехимической промышленности.
Мартенситные стали также относятся к серии AISI 400. Эти кованые высокоуглеродистые стали содержат от 11,5 до 18% хрома и могут иметь небольшое количество дополнительных легирующих элементов. Они магнитны, упрочняются термической обработкой, обладают высокой прочностью и умеренной ударной вязкостью в закаленном состоянии. Формовка должна производиться в отожженном состоянии. Мартенситные нержавеющие стали менее устойчивы к коррозии, чем аустенитные или ферритные марки. Два типа мартенситных сталей — 416 и 420F — были разработаны специально для хорошей обрабатываемости.
Мартенситные нержавеющие стали используются там, где прочность и/или твердость имеют первостепенное значение, и где среда относительно мягкая с коррозионной точки зрения. Эти сплавы обычно используются для подшипников, пресс-форм, столовых приборов, медицинских инструментов, конструкционных деталей самолетов и компонентов турбин. Тип 420 все чаще используется для пресс-форм для пластмасс и промышленных компонентов, требующих твердости и коррозионной стойкости.
Дисперсионно-твердеющие нержавеющие стали приобретают очень высокую прочность благодаря низкотемпературной термической обработке, которая не приводит к существенной деформации прецизионных деталей. Составы большинства дисперсионно-твердеющих нержавеющих сталей сбалансированы для обеспечения упрочнения за счет обработки старением, при которой выделяются твердые интерметаллические соединения и одновременно происходит отпуск мартенсита. Начальная микроструктура сплавов PH – аустенитная или мартенситная. Аустенитные сплавы должны быть подвергнуты термической обработке для превращения аустенита в мартенсит, прежде чем можно будет осуществить дисперсионное твердение.
Эти сплавы используются там, где требуется высокая прочность, умеренная коррозионная стойкость и хорошая технологичность. Типичные области применения включают валы, насосы высокого давления, детали самолетов, высокопрочные пружины и крепежные детали.
Литая нержавеющая сталь обычно имеет соответствующие марки деформируемой стали с аналогичным составом и свойствами. Однако между литыми и деформируемыми марками есть небольшие, но важные различия в составе. Отливки из нержавеющей стали должны иметь обозначения, установленные ACI (Институт литья сплавов), а не обозначения аналогичных деформируемых сплавов.
Рабочая температура обеспечивает основу для различия между жаростойкими и коррозионностойкими марками литья. Серия C марок ACI обозначает коррозионно-стойкие стали; серия H обозначает жаропрочные стали, которые можно использовать для конструкционных применений при рабочих температурах от 1200 до 2200°F. Содержание углерода и никеля в сплавах серии H значительно выше, чем в сплавах серии C. Стали серии Н не защищены от коррозии, но коррозия происходит медленно — даже при воздействии продуктов сгорания топлива или атмосферы, подготовленной для науглероживания и азотирования. Марки серии C используются в клапанах, насосах и фитингах. Марки серии H используются для деталей печей и компонентов турбин.
Истирание и износ являются видами отказов, требующими особого внимания при работе с нержавеющими сталями, поскольку эти материалы служат во многих суровых условиях. Они часто работают, например, при высоких температурах, в приложениях, контактирующих с пищевыми продуктами, и там, где доступ ограничен. Такие ограничения препятствуют использованию смазочных материалов, что приводит к контакту металла с металлом, что способствует истиранию и ускоренному износу.
В ситуации износа скольжения сначала происходит разрушение из-за истирания, за которым следует потеря размеров из-за износа, за которым, в свою очередь, обычно следует коррозия. Истирание — это серьезная форма адгезионного износа, проявляющаяся в виде порванных участков металлической поверхности. Истирание можно свести к минимуму за счет снижения контактных напряжений или использования защитных поверхностных слоев, таких как смазочные материалы (где это приемлемо), наплавки, гальванические покрытия и азотирование или науглероживание поверхности.
Результаты испытаний пар из нержавеющей стали (таблица) указывают на относительно низкую стойкость к истиранию аустенитных марок и даже сплава 17-4 РН, несмотря на его высокую твердость. Среди стандартных марок только AISI 416 и 440C показали хорошие результаты. Стойкость к истиранию от хорошей до отличной продемонстрировали сплавы Armco Nitronic 32 и 60 (последние были разработаны специально для защиты от заедания).
Результаты недавних исследований доказывают, что добавление кремния в аустенитный нержавеющий сплав с высоким содержанием марганца, упрочненный азотом, позволяет получить износостойкую нержавеющую сталь. Износостойкость и коррозионная стойкость по-прежнему считаются неизбежным компромиссом при использовании нержавеющей стали, но новая формула обещает противостоять обоим условиям.
Сильнейшая коррозия — причина номер один для выбора нержавеющей стали. Но в тех случаях, когда детали трудно смазывать, большинство нержавеющих сталей не могут сопротивляться износу. При высоких нагрузках и недостаточной смазке нержавеющая сталь часто имеет тип повреждения поверхности, известный как истирание. В критических частях истирание может привести к заклиниванию или замерзанию, что может привести к остановке оборудования.
Конструкторы обычно решают проблему истирания, используя литые сплавы или нанося кобальтовое покрытие на детали из нержавеющей стали. В любом случае исправления могут быть дорогостоящими и могут создать новые проблемы, сопровождающие процесс жесткой облицовки. К ним относятся поддержание одинаковой толщины облицовки и обеспечение надлежащей адгезии между облицовкой и основанием. Новая формула нержавеющей стали призвана обойти эти трудности, предлагая альтернативу дорогим износостойким материалам.
В поисках рентабельной альтернативы исследователи из Carpenter Technology, Рединг, Пенсильвания, изучили элементное влияние кремния, марганца и никеля на сопротивление истиранию упрочненных азотом аустенитных нержавеющих сталей. Результаты первоначальной программы испытаний показали, что кремний является катализатором стойкости к истиранию, а никель и марганец – нет.
Содержание кремния в недавно разработанном устойчивом к истиранию нержавеющем сплаве составляет от 3 до 4%. Уровни кремния должны оставаться ниже 5% для поддержания надлежащей металлургической структуры. Кроме того, слишком много кремния снижает растворимость азота. Для поддержания прочности необходимо было бы добавить большее количество дорогостоящего никеля.
Исследователи теперь могут определить предельные значения оптимального состава устойчивой к коррозии нержавеющей стали. Чтобы доказать пригодность новой стали, ее свойства, такие как истирание, износ и коррозия, оцениваются и сравниваются с имеющимися в продаже нержавеющими сталями. В сравнение включены четыре сплава, коррозионностойкий аустенитный сплав под названием Gall-Tough, другие аустенитные сплавы с более высоким содержанием никеля и марганца (16Cr-8Ni-4Si-8Mn) и нержавеющие стали типов 304 и 430.
Результаты показывают, что порог истирания для коррозионностойкой нержавеющей стали более чем в 15 раз выше, чем для обычных нержавеющих сталей. Кроме того, коррозионностойкая нержавеющая сталь выдерживает более чем в два раза большую нагрузку без образования истираний по сравнению со сплавом 16Cr-8Ni-4Si-8Mn. Тем не менее, новая формула лишь немного жертвует коррозионной стойкостью.
По прочности и твердости коррозионностойкая нержавеющая сталь и сплав 16Cr-8Ni-4Si-8Mn превосходят сплавы типов 304 и 430. Новый сплав также демонстрирует уникально высокий предел прочности при растяжении, возможно, из-за образования мартенсита во время испытаний на растяжение. Пластичность всех четырех сплавов превосходна. Эти результаты показывают, что стойкие к истиранию сплавы могут экономически сократить разрыв между коррозионной стойкостью, истиранием и износостойкостью металла по металлу.
Является ли нержавеющая сталь черным металлом? – АМАРИН
Этот вопрос задавался каждый год, когда инженеры интересовались черными или цветными металлами во время выполнения процедуры сварки, оценки неразъемных соединений или расчета коррозии.
В этой статье дается обзор черных металлов , что они из себя представляют и как они производятся . Существует несколько распространенных типов черных металлов, таких как мягкая сталь , нержавеющая сталь и чугун . Черные металлы очень универсальны. Прочтите эту статью, чтобы узнать об их применении, преимуществах и недостатках черных металлов
Знаете ли вы? Железо — самый распространенный элемент на Земле. Земное ядро состоит из сплава железа и никеля, составляющего около 35% массы Земли.
Чистое железо очень мягкое, имеет серовато-белый цвет и имеет ограниченное применение. Железо редко встречается в чистом виде (за исключением метеоритов). Он существует в природе вместе с другими элементами, в виде полезных ископаемых. Наиболее распространенным минералом является оксид железа. Минералы со значительным содержанием железа называются железными рудами – обычно встречаются железные руды – гематит и магнетит.
Как производят железо и другие черные металлы?
Железо получают из железной руды путем плавки в доменной печи. Полученное таким образом железо называется чугуном , в состав которого входит 92-94% железа и 3-5% углерода , наряду с небольшими количествами других элементов. Чугун является хрупким и имеет ограниченное применение. Поэтому он используется для производства различных видов черных металлов.
Доменная печь, в которой железо получают из железной руды путем плавки Расплавленный чугун обычно заливают в печи (электродуговые, индукционные, мартеновские или доменные) и соединяют с другими элементами для получения различных черных металлов. Расплавленному материалу либо непосредственно отливается необходимая форма, либо прокатывается ( в горячем, теплом или холодном состоянии, в зависимости от применения ). Затем он подвергается термической обработке (отжиг , отпуск, закалка и т. д. ) для улучшения механических свойств и предотвращения коррозии.
Черные металлы обладают улучшенными физическими свойствами, такими как высокая прочность, пластичность и высокая прочность на растяжение, и находят широкое применение в коммерческих и промышленных целях. Наиболее распространенными черными металлами являются мягкая сталь, углеродистая сталь, легированная сталь, нержавеющая сталь, кованое железо и чугун.
Типы черных металлов
Мягкая сталь и углеродистая сталь: Железо соединяется с углеродом для получения мягкой и углеродистой стали. Мягкая сталь имеет меньшее количество углерода (от 0,16% до 0,3% по весу), тогда как углеродистая сталь имеет относительно большее количество углерода (до 2%). Как правило, чем больше углерода, тем тверже металл.
Мягкая сталь, будучи относительно более мягкой, используется для изготовления стальных листов, а углеродистая сталь, будучи более твердой, используется для изготовления валов и шкивов. Кроме того, углеродистая сталь используется для резки других металлов и используется в станках, лезвиях и сверлах.
Легированная сталь: Легированная сталь получается путем добавления в чугун таких элементов, как никель, титан, хром, вольфрам и ванадий. В основном это делается для повышения прочности, долговечности, пластичности, коррозионной стойкости и т. д. Легированная сталь используется в электрических компонентах и в строительстве. Применение легированной высокопрочной стали
Нержавеющая сталь: Это разновидность легированной стали с высоким содержанием хрома (где-то от 10,5% до 27% ). Количество c Наличие хрома влияет на его ударную вязкость и устойчивость к коррозии . В зависимости от количества присутствующего хрома нержавеющая сталь подразделяется на различные категории ( аустенитная, ферритная, мартенситная и дисперсионно-твердеющая мартенситная ) и имеет различные применения, включая насосы, трубы, выхлопные системы, подшипники, столовые приборы, медицинские инструменты, турбины. и компонентов самолетов.
Чугун: Чугун получают путем добавления кремния в расплавленный чугун и его охлаждения. Он твердый и хрупкий, обладает высокой износостойкостью. Чаще всего используются в двигателях, поршнях, станках, печах и трубах.
Литье по сравнению с кованой стальюКованое железо: Кованое железо представляет собой почти чистое железо, поскольку в нем очень мало углерода (менее 0,08%). Чугун смешивают со шлаком в печи для получения кованого железа. Шлак, добавленный во время производства, помогает сделать металл более устойчивым к окислению (ржавчине) и коррозии. Он легко сваривается и легко гнется в горячем или холодном состоянии. Типичные области применения включают перила, гвозди, цепи, мебель, украшения и сельскохозяйственное оборудование.
Преимущества
В дополнение к разнообразным применениям, перечисленным выше, черные металлы имеют ряд преимуществ перед цветными металлами.
- Обладают магнитными свойствами и поэтому используются в электроприборах и больших двигателях. Это особенно важно, так как магнитные свойства статора притягивают ротор, облегчая правильную работу двигателя.
- Обладают термостойкостью, т. е. способны выдерживать большее количество тепла по сравнению с цветными металлами. Это особенно полезно в станках, чтобы помочь увеличить срок службы инструмента и предотвратить повреждение.
- Черные металлы можно легко сделать менее коррозионно-активными путем добавления других элементов или катодной защиты.
Недостатки
По сравнению с цветными металлами (например, алюминием ), которые не содержат железа , черные металлы подвержены ржавчине при воздействии даже небольшого количества влаги. Однако некоторые марки нержавеющей стали являются исключением из-за присутствия хрома.
Резюме
Черные металлы легко сочетаются с другими элементами до улучшают их коррозионную стойкость . Это свойство в сочетании с большой долговечностью, высокой прочностью и пластичностью делает черные металлы очень универсальными и подходящими для широкого спектра применений в различных отраслях промышленности.
Нравится:
Нравится Загрузка…
Взаимодействие поверхности с белками на различных марках нержавеющей стали: эффекты адсорбции белка, изменения поверхности и высвобождение металла
. 2013 апр; 24(4):1015-33.
дои: 10.1007/s10856-013-4859-8. Epub 2013 2 февраля.
Ю Хедберг 1 , X Wang, J Hedberg, M Lundin, E Blomberg, I Odnevall Wallinder
Принадлежности
принадлежность
- 1 Отделение изучения поверхности и коррозии, кафедра химии, Школа химических наук и инженерии, Королевский технологический институт KTH, Стокгольм, Швеция.
[email protected]
- PMID: 23378148
- PMCID: PMC3620448
- DOI: 10.1007/s10856-013-4859-8
Бесплатная статья ЧВК
Y Hedberg et al. J Mater Sci Mater Med. 2013 9 апр.0003
Бесплатная статья ЧВК
. 2013 апр; 24(4):1015-33.
doi: 10.1007/s10856-013-4859-8. Epub 2013 2 февраля.
Авторы
Ю Хедберг 1 , X Wang, J Hedberg, M Lundin, E Blomberg, I Odneval Wallinder
принадлежность
- 1 Отделение изучения поверхности и коррозии, Химический факультет, Школа химических наук и инженерии, Королевский технологический институт KTH, Стокгольм, Швеция.
[email protected]
- PMID: 23378148
- PMCID: PMC3620448
- DOI: 10.1007/s10856-013-4859-8
Абстрактный
Имплантация с использованием нержавеющей стали (НС) является примером, когда понимание вызываемого белком высвобождения металла из НС важно при оценке потенциальных токсикологических рисков. Здесь было исследовано высвобождение металлов, вызванное белком, для аустенитных (AISI 304, 310 и 316L), ферритных (AISI 430) и дуплексных (AISI 2205) сортов в растворе фосфатно-солевого буфера (PBS, pH 7,4), содержащем либо бычий сывороточный альбумин (BSA) или лизоцим (LSZ). Результаты показывают, что как BSA, так и LSZ вызывают значительное обогащение хромом поверхностного оксида всех марок нержавеющей стали. Оба белка индуцировали повышенную степень высвобождения железа, хрома, никеля и марганца, очень значительную в случае БСА (увеличение до 40 раз), тогда как оба белка снижали коррозионную стойкость НС, с обратной ситуацией для металлического железа ( снижение скорости коррозии и уменьшение высвобождения металла в присутствии белков). Для достижения наблюдаемых эффектов необходимо полное покрытие монослоя.
Цифры
Рис. 1
Количество (мкг/см 2 )…
Рис. 1
Количество (мкг/см 2 ) металлов (Fe, Cr, Ni и Mn), выброшенных из…
Рисунок 1 Количество (мкг/см 2 ) металлов (Fe, Cr, Ni и Mn), выделяемых из аустенитной нержавеющей стали марок 304 ( a , b ) и 316L ( c , d ), подвергавшихся воздействию до 168 часов в PBS, PBS + BSA и PBS + LSZ. Звездочки указывают на значительное увеличение общего высвобождения металлов (Fe + Cr + Ni + Mn) в белковом растворе (PBS + BSA и PBS + LSZ соответственно) по сравнению с PBS, рассчитанное с помощью теста Стьюдента t (непарные данные с неравная дисперсия), * P < 0,05, ** P < 0,01 и *** P < 0,001. Вставка графики увеличены без Fe
Рис. 2
Количество (мкг/см 2 )…
Рис. 2
Количество (мкг/см 2 ) металлов (Fe, Cr, Ni и Mn), выброшенных из…
Рис. 2 Количество (мкг/см 2 ) металлов (Fe, Cr, Ni и Mn), выделяемых из ферритной нержавеющей стали марки 430 ( a , b ) подвергались воздействию до 168 часов в PBS, PBS + BSA и PBS + LSZ. Звездочки указывают на значительное увеличение общего высвобождения металлов (Fe + Cr + Ni + Mn) в белковом растворе (PBS + BSA и PBS + LSZ соответственно) по сравнению с PBS, рассчитанное с помощью теста Стьюдента t (непарные данные с неравная дисперсия), * P < 0,05, ** P < 0,01 и *** P < 0,001. На вставке графики увеличены, за исключением Fe
Рис. 3
Нормы выделения железа из…
Рис. 3
Скорость выделения железа из нержавеющей стали марок 430, 304 и 316L,…
Рис. 3 Скорость выделения железа из нержавеющей стали марок 430, 304 и 316L, выраженная в мкг/(см 2 h), для воздействия в PBS, PBS + BSA и PBS + LSZ до 168 ч. Столбики ошибок представляют собой стандартное отклонение между тройными образцами (за вычетом пустой концентрации)
Рис. 4
Относительное массовое отношение окисленных…
Рис. 4
Относительное массовое соотношение между окисленным хромом и окисленным железом (Cr бык /(Cr бык…
Рис. 4Относительное массовое соотношение между окисленным хромом и окисленным железом (Cr ox / (Cr ox + Fe ox )) в поверхностном оксиде неэкспонированных и экспонированных материалов марки 430 ( верх ) и 304 ( низ ) в PBS, PBS + BSA и PBS + LSZ при периодах воздействия до 168 часов. Звездочки указывают на слишком плотный или слишком толстый адсорбированный слой LSZ, чтобы можно было проводить измерения методом XPS на этом повторном участке поверхности
Рис. 5
a Потенциал холостого хода свыше…
Рис. 5
a Потенциал холостого хода с течением времени для нержавеющей стали 304, подверженной воздействию PBS,…
Рис. 5a Потенциал разомкнутой цепи с течением времени для нержавеющей стали 304, подвергаемой воздействию PBS, PBS + LSZ и PBS + BSA. 9Показанные полосы ошибок 0271 указывают стандартное отклонение между двумя повторными измерениями. b Поляризационная (коррозионная) стойкость (Ом·см 2 ) нержавеющей стали марки 304 в PBS, PBS + BSA и PBS + LSZ после 18 ч воздействия ( планка погрешности : стандартное отклонение между тремя повторными измерениями)
Рис. 6
Измеренная масса (мг/м 2 )…
Рис. 6
Определяемая масса (мг/м 2 ) адсорбированного LSZ и BSA на нержавеющей стали…
Рис. 6Измеренная масса (мг/м 2 ) адсорбированных LSZ и BSA на нержавеющей стали марки 316, определенная с помощью QCM ( a ). Стрелки указывают момент времени введения белка и промывания (с PBS). Соответствующие толщины слоев ККМ по расчетам Фойгта для адсорбции ЛСЦ и БСА на 316 подложках в растворе ФСБ с рН 7,4 ( б ). Столбики ошибок показывают расхождение между двумя независимыми измерениями (только одно измерение для BSA). Примечание. Измерения адсорбции проводились при более низких концентрациях белка (BSA — в 10 раз, LSZ — в 2 раза) по сравнению с исследованием высвобождения металлов, как в [20]. Подробная информация о моделировании Фойгта и воспроизводимости дана в [20] для хромированных подложек по сравнению с 316 и другими подложками (цветной рисунок онлайн)
Рис. 7
Относительное атомное соотношение азота…
Рис. 7
Относительное атомное соотношение между азотом и окисленным углеродом на неэкспонированном и экспонированном 304…
Рис. 7Относительное атомное соотношение между азотом и окисленным углеродом на незащищенной и незащищенной нержавеющей стали 304 в PBS, PBS + BSA и PBS + LSZ
Рис. 8
Количество выброса металла в…
Рис. 8
Количество выделившегося металла в мкг/см 2 для разных концентраций БСА в ФБР…
Рис. 8Количество выделившегося металла в мкг/см 2 для различных концентраций БСА в PBS для 316 л после 168 ч воздействия: a выпуск железа, b выпуск хрома, c выпуск никеля, d выпуск марганца
Рис. 9
a Количество окисленного хрома…
Рис. 9
a Количество окисленного хрома на количество окисленного хрома и железа (отн.…
Рис. 9a Количество окисленного хрома на количество окисленного хрома и железа (относительная масса %) и b относительное атомное соотношение между азотом и окисленным углеродом, измеренное с помощью XPS; всего для 316L без воздействия и после воздействия растворов PBS с различными концентрациями BSA, в течение 168 ч соответственно
Рис. 10
Значения дзета-потенциала (ZP)…
Рис. 10
Значения дзета-потенциала (ZP) поверхности 316 QCM, измеренные в диапазоне 1…
Рис.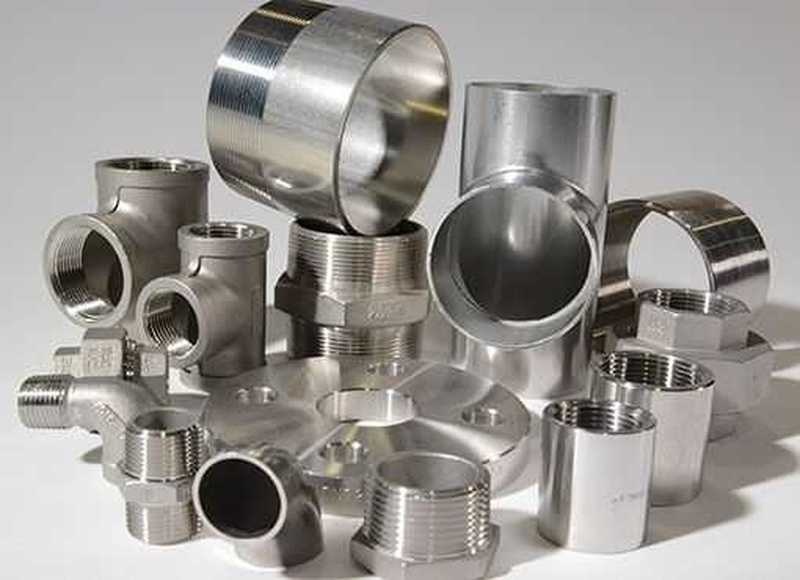
Значения дзета-потенциала (ZP) поверхности 316 QCM, измеренные в 1 мМ растворе KCl, в зависимости от pH раствора
См. это изображение и информацию об авторских правах в PMC
Похожие статьи
Адсорбция и вызванное белком высвобождение металла из металлического хрома и нержавеющей стали.
Лундин М., Хедберг Ю., Цзян Т., Хертинг Г., Ван Х., Торманн Э., Бломберг Э., Валлиндер И.О. Лундин М. и соавт. J Коллоидный интерфейс Sci. 2012 15 января; 366 (1): 155-164. doi: 10.1016/j.jcis.2011.09.068. Epub 2011 2 октября. J Коллоидный интерфейс Sci. 2012. PMID: 22014396
Взаимодействие бычьего сывороточного альбумина и лизоцима с нержавеющей сталью изучено методами времяпролетной масс-спектрометрии вторичных ионов и рентгеновской фотоэлектронной спектроскопии.
Хедберг Ю.С., Киллиан М.С., Бломберг Э., Виртанен С., Шмуки П., Одневалл Валлиндер И. Хедберг Ю.С. и соавт. Ленгмюр. 2012 27 ноября; 28 (47): 16306-17. doi: 10.1021/la3039279. Epub 2012 12 ноября. Ленгмюр. 2012. PMID: 23116183
Сравнение скорости выделения металла из нержавеющей стали AISI 316L и чистого Fe, Cr и Ni в синтетическую биологическую среду.
Гертинг Г., Валлиндер И.О., Лейграф К. Хертинг Г. и соавт. J Мониторинг окружающей среды. 2008 Сентябрь; 10 (9)): 1092-8. doi: 10.1039/b805075a. Epub 2008 5 августа. J Мониторинг окружающей среды. 2008. PMID: 18728903
Выделение никеля из нержавеющих сталей.
Одреши П., Манту Б., Фраппаз А., Руссо Д., Шабо Г., Фор М., Клоди А.
Ходреши П. и соавт. Контактный дерматит. 1997 г., сен; 37 (3): 113-7. doi: 10.1111/j.1600-0536.1997.tb00314.x. Контактный дерматит. 1997. PMID: 9330816
Выделение металлов из нержавеющей стали в биологических средах: обзор.
Хедберг Ю.С., Одновал Валлиндер И. Хедберг Ю.С. и соавт. Биоинтерфазы. 2015 29 марта; 11 (1): 018901. дои: 10.1116/1.4934628. Биоинтерфазы. 2015. PMID: 26514345 Обзор.
Посмотреть все похожие статьи
Цитируется
Активные формы кислорода, образованные наночастицами металлов и оксидов металлов в физиологических средах – обзор реакций, важных для нанотоксичности, и предложения по категоризации.
Кесслер А., Хедберг Дж.
, Бломберг Э., Одновалл И. Кесслер А. и др. Наноматериалы (Базель). 2022 4 июня; 12 (11): 1922. дои: 10.3390/nano12111922. Наноматериалы (Базель). 2022. PMID: 35683777 Бесплатная статья ЧВК. Обзор.
Адсорбция титана и белка: обзор механизмов и эффектов поверхностных особенностей.
Барбери Дж., Сприано С. Барбери Дж. и соавт. Материалы (Базель). 2021 24 марта; 14 (7): 1590. дои: 10.3390/ma14071590. Материалы (Базель). 2021. PMID: 33805137 Бесплатная статья ЧВК. Обзор.
Обзор взаимодействия сывороточного альбумина с биомедицинскими сплавами.
Клок О., Игуаль Муньос А., Мишлер С. Клок О и др. Материалы (Базель). 2020 29 октября; 13 (21): 4858. дои: 10.3390/ma13214858. Материалы (Базель).
2020. PMID: 33138286 Бесплатная статья ЧВК. Обзор.
Последние достижения в изучении межфазной адсорбции биоинженерных моноклональных антител.
Холлоуэлл П., Ли З., Ху Х., Руан С., Калония С., ван дер Валле С.Ф., Лу Младший. Холлоуэлл П. и др. Молекулы. 2020 28 апр;25(9)):2047. doi: 10,3390/молекулы25092047. Молекулы. 2020. PMID: 32353995 Бесплатная статья ЧВК. Обзор.
Влияние образования биокороны на превращение и растворение наночастиц кобальта в физиологических условиях.
Мей Н., Хедберг Дж., Одневалл Валлиндер И., Бломберг Э. Мей Н и др. АСУ Омега. 2019 12 декабря; 4(26):21778-21791. doi: 10.1021/acsomega.9b02641. электронная коллекция 201924 декабря. АСУ Омега. 2019. PMID: 31891055 Бесплатная статья ЧВК.
Просмотреть все статьи “Цитируется по”
использованная литература
- Suárez C, Vilar T, Gil J, Sevilla P. In vitro оценка топографических изменений поверхности и высвобождения никеля из лингвальных ортодонтических дуг. J Mater Sci Mater Med. 2010;21(2):675–683. doi: 10.1007/s10856-009-3898-7. – DOI – пабмед
- Гальван Дж., Салданья Л., Мультигнер М., Кальсадо-Мартин А., Ларреа М., Серра С. и др. Пескоструйная очистка медицинской нержавеющей стали: влияние на ее коррозионное поведение, выделение ионов и биосовместимость.
J Mater Sci Mater Med. 2012;23(3):657–666. doi: 10.1007/s10856-012-4549-y. – DOI – пабмед
- Гальван Дж., Салданья Л., Мультигнер М., Кальсадо-Мартин А., Ларреа М., Серра С. и др. Пескоструйная очистка медицинской нержавеющей стали: влияние на ее коррозионное поведение, выделение ионов и биосовместимость.
- Вонг АКЛ. Биопленки в пищевой промышленности. Дж. Молочная наука. 1998;81(10):2765–2770. doi: 10.3168/jds.S0022-0302(98)75834-5. – DOI – пабмед
- Седрикс А.
- Седрикс А.