Закалка 45 стали: Закалка и отпуск стали 45. Как закалить сталь 45 в домашних условиях?
alexxlab | 06.05.2023 | 0 | Разное
Влияние скорости лазерной обработки на структуру и свойства стали 45
Шатиков И.Р., Костромин С.В. // ПРОГРЕССИВНЫЕ ТЕХНОЛОГИИ И ПРОЦЕССЫ, Сборник научных статей Международной молодежной научно-практической конференции (25-26 сентября 2014 года), в 2-х томах, Том 2, Юго-Зап. гос. ун-т.,Курск, 2014, с: 261-265
Сталь 45 уже десятилетия используется в машиностроении для изготовления различных деталей. В основном для деталей, подвергаемых упрочняющей поверхностной обработке. Появившиеся лазерные методы обработки поверхности позволили еще эффективнее использовать детали из этой стали. В данной работе рассмотрены результаты лазерного поверхностного упрочнения стали 45 с различной исходной структурой: закалка + высокий отпуск, закалка, отжиг. Особое внимание уделяется образцам с исходной структурой после отжига и закалки
Методика эксперимента
Образцы из стали 45 подвергались предварительной термообработке по стандартным режимам для этой стали: закалке, закалке с последующим высоким отпуском при 600Ԩ, отжигу. После чего каждый образец прошел лазерную закалку CO2-лазером на установке ЛАТУС-31 с мощностью излучения 1100 Вт диаметром пучка 3 мм, которые дают плотность энергии 15,71 Вт/см2 и скоростями обработки 5, 10, 15, 20 мм/с. Изучение полученных свойств, производилось при помощи измерений микротвердости методом Виккерса и металлографических исследований.
Экспериментальные результаты
Полученные результаты согласуются с литературными данными. [1] При наиболее распространенном режиме закалка + высокий отпуск и последующая лазерная закалка. Единственным оптимальным режимом обработки из рассматриваемых является режим со скоростью 20 мм/с. Дающий увеличение микротвердости до 6200 МПа, по сравнению с основой 3200 МПа и на глубину 0,55 мм. (рис.1) При скорости в 15 мм/с испаряется до 262 ISBN 978-5-9905749-5-3 (Том 2) 25-26 сентября 2014 года 0,2 мм металла. Более подробно результаты с этим режимом обработки рассмотрены в [2].
Если в образцах после отжига и закалки с высоким отпуском было повышение уровня микротвердости и последующее быстрое снижение значений микротвердости до уровня основного металла.
То в образцах после закалки в небольшом верхнем слое 0,4-0,8 мм, проходила повторная закалка, дающая небольшое повышение микротвердости 1000-1500 МПа. После начинается зона лазерного отпуска с глубиной 1,8-2 мм и значительным и быстрым падением микротвердости до 4000 МПа что примерно соответствует уровню стали 45 после закалки и высокого отпуска. Еще глубже уровень микротвердости выравнивался до значений не обработанного металла. (рис.2) На фотографиях микроструктуры видно сложное строение ЗЛВ (рис.3) Для скоростей обработки 5 и 10 мм/с, имеются очень большие зоны испарившегося металла 0,8 и 0,4 мм соответственно. Скорости 15 и 20 мм/с практически не показали испарения металла. После идет тонкий обезуглероженный слой 50-70 мкм, образовавшийся при закалке из жидкого состояния, он характерен для всех скоростей. И далее идет повторно закаленный слой, который выделяется сильно выраженным градиентом дисперсности структуры мартенсита. В поверхностных слоях закалённых из жидкого состояния зерна очень крупные и по мере углубления дисперсность возрастает. Далее возникает ярко выраженная переходная зона, где уже тепловой энергии не хватает для повторной закалки и начинается зона отпуска с характерной для высоко отпущенной стали троостомартенситной структурой.
Такое же строение имеют и ЗЛВ у стали 30ХГСА, [3]
Образец после отжига показывает такие же зависимости микротвердости от глубины, что и образец после закалки и высокого
отпуска. Но глубина зон с высокой твердостью у образцов с исходной структурой после отжига немного меньше 0,1-0,3 мм. Уровни микротвердости отличаются не сильно (рис.4) Но интересно, что у этого образца не проявляется зависимости убывания значения микротвердости от скорости.
При изучении микростуктуры просматривается заметное отличие, а именно переходная зона является не тонкой полоской. Она выглядит как плавный переход от одной структуры к другой. То есть проявляется карбидная сетка. (рис.4а) Это можно объяснить тем что на определенной глубине энергии уже не хватает чтобы растворить карбиды. В образце после закалки и высокого отпуска это явление выражено не так и зона перехода очень тонкая. Так как предыдущая термообработка измельчила зерно.
Выводы.
Для стали 45 очень важен точный подбор режима обработки. Потому
что даже небольшие изменение, находит сильное отражение в строении и свойствах полученной поверхности. Получение максимально возможной глубины не всегда оправданно, из-за получения более неоднородной структуры по ЗЛВ по глубине. Что в свою очередь может свести к нулю усилия, затраченные на увеличение глубины упрочненного слоя.
Полное содержание статьи: http://regionika.ru/konf/%CC%CB-05%20%CC%E0%EA%E5%F2%20%D2%EE%EC2.pdf
Главная :: ООО «Политерм-Тюмень»
Главная :: ООО «Политерм-Тюмень»НАЗАД
ВПЕРЕД
Улучшенная модификация известной среды ПК-2
ЗАКАЛОЧНАЯ ЖИДКОСТЬ ПКМ ®
Среда ПКМ является нетоксичной, негорючей, неагрессивной в коррозионном отношении жидкостью, поэтому ее эксплуатация не требует специальных средств защиты обслуживающего персонала и оборудования.
Подробнее
ООО “Политерм-Тюмень” оказывает услуги
ТЕРМООБРАБОТКИ
Термообработка осуществляется в закалочном баке с рабочим раствором закалочной среды ПКМ нашего производства.
Подробнее
ООО “Политерм-Тюмень” оказывает услуги
КАРБОНИТРИРОВАНИЯ
Низкотемпературный химико-термический процесс упрочнения деталей и инструмента в продуктах пиролиза углерод-азотсодержащих соединений.
Подробнее
О ПРЕДПРИЯТИИ
Политерм-Тюмень
Сегодня, в условиях рынка, изготовление и реализация продукции немыслимы без применения производителями эффективных и экономичных технологий и материалов.
ООО «Политерм-Тюмень» является единственным в России производителем и прямым поставщиком высокотехнологичного продукта – универсальной водополимерной закалочной среды ПКМ®, являющейся полноценным заменителем нефтяных и иных закалочных масел при термообработке заготовок, деталей и инструмента.
Наш продукт применяют на постоянной основе более 200 промышленных предприятий в почти 50 регионах России, а также предприятия Беларуси, Казахстана и Украины.
ПОДРОБНЕЕ
Наша продукция
Закалочная жидкость ПКМ®Негорючая
Концентрат и его водные растворы абсолютно пожаробезопасны (содержание полимера в концентрате ~ 6,0%, в рабочем растворе ~ 0,5%, остальное – вода).
Нетоксичная
Концентрат закалочной жидкости ПКМ и его водные растворы не представляют опасности для человека и окружающей среды.
Неагрессивная
Концентрат и его водные растворы обладают пассивирующим воздействием на черные металлы и сплавы, поскольку их рН > 7,5. Замечена некоторая консервирующая способность при межоперационном пролеживании деталей.
Физические свойства
Физические характеристики рабочих растворов, такие как плотность, удельная теплоемкость очень близки к свойствам воды. Температура кипения ≈ 97-98°С, температура замерзания ≈ – 1,7°С. При замерзании концентрата он не теряет своих свойств.
ПОДРОБНЕЕ
УСЛУГИ ПРЕДПРИЯТИЯ
УСЛУГИ ПРЕДПРИЯТИЯ
Термообработка
ООО «Политерм-Тюмень» оказывает услуги термообработки сторонним организациям. Термообработка осуществляется в закалочном баке с рабочим раствором закалочной среды ПКМ нашего производства.
ПОДРОБНЕЕ
Карбонитрирование
Предлагаем свои услуги по низкотемпературному химико-термическому процессу упрочнения деталей и инструмента в продуктах пиролиза углерод-азотсодержащих соединений.
ПОДРОБНЕЕ
СЕРТИФИКАТЫ
Сертификаты и награды
Профессиональная работа и активная позиция в своем сегменте российского бизнеса не прошли незамеченными для компании ООО «Политерм-Тюмень».
Помимо отличной репутации и удачных партнерских отношений с крупнейшими отечественными компаниями, деятельность предприятия была отмечена премиями, рейтингами, памятными знаками и сертификатами.
Руководство по выбору сталей сквозной закалки
Сравнительную таблицу твердости стали см. ниже
Нагрев | Растяжение | Твердость | Постановление Раздел | ||||||
<=13 мм | >13 <=19 мм | >19 <=29 мм | >29 <=63мм | >63 <=100мм | > | >150 <=250 мм | |||
В | 625-775 н/мм2 | 179-229 | 080М40 | 080М40 | 080М40 | 080М40 | 708М40 | ||
Р | 700-850 Н/мм2 45-55 ТСИ | 201-255 | 080М40 | 080М40 | 070М55 | 070М55 | 070M55 | 605М36 | 605М36 |
С | 775-925 Н/мм2 50-60 ТСИ | 223-277 | 070M55 | 070М55 | 070М55 | 070М55 | 605М36 | 709М40 | 709М40 |
Т | 850-1000 Н/мм2 55-65 ТСИ | 248-302 | 070М55 | 070М55 | 605M36 | 605М36 | 605M36 | 817М40 | 817М40 |
У | 925-1075 н/мм2 60-70 ТСИ | 269-331 | 605М36 | 605М36 709М40 | 605М36 | 709М40 | 709M40 | 826М40 | 826М40 |
В | 1000-1150 Н/мм2 75-80 ТСИ | 293-352 | 605М36 | 605M36 | 709М40 | 817М40 | 826М40 | 826М40 | 826М40 |
Вт | 1075-1225 Н/мм2 80-85 ТСИ | 311-375 | 708М40 | 709М40 | 817М40 | 826М40 | 826M40 | 826М40 | 826М40 |
Следует сделать ссылку на соответствующие стандарты текучести и ударопрочности.
По поводу сталей, требуемых для условий X, Y или Z, обращайтесь в наш технический отдел.
Перечисленные выше стали представляют наиболее распространенные марки.
Существуют и другие спецификации, соответствующие этим требованиям. Пожалуйста, запросите другие оценки.
№ твердости ХБ | № твердости ХВ | Твердость HRC | Эквивалент. UTS н/мм2 | № твердости ХБ | № твердости ХВ | Твердость HRC | Эквивалент. UTS н/мм2 | |
899 856 817 780 745 712 682 653 627 601 578 555 534 514 495 477 461 444 429 415 401 388 375 363 352 341 331 321 311 302 293 285 277 269 262 255 248 241 235 229 |
1150 1050 960 885 820 765 717 675 633 598 567 540 515 494 472 454 437 420 404 389 375 363 350 339 327 316 305 296 287 279 270 263 256 248 241 235 229 |
70 68 66 64 62 60 58 57 55 53 52 50 49 47 46 45 44 42 41 40 38 37 36 35 34 33 32 31 30 29 28 26 25 24 23 22 21 | 3027 2888 2749 2641 2517 2409 2286 2193 2116 2023 1946 1869 1792 1730 1668 1606 1544 1498 1452 1406 1359 1297 1266 1220 1174 1143 1112 1081 1050 1019 988 958 927 911 880 849 834 803 788 772 | 223 217 212 207 201 197 192 187 183 179 174 170 167 163 159 156 152 149 146 143 140 137 134 131 128 126 123 121 118 116 114 111 109 107 105 103 101 99,2 97,3 95,5 | 223 217 212 207 202 197 192 187 183 179 174 170 166 163 159 156 153 149 146 143 140 137 134 131 128 126 124 121 118 116 114 112 109 107 105 103 101 99 97 95 | 20 18 17 16 15 13 12 10 9 8 7 6 4 3 2 1 0 | 757 726 710 695 680 664 649 633 618 610 602 595 587 579 564 556 541 526 517 510 494 486 479 463 456 448 440 432 417 409 402 394 386 378 371 363 355 351 347 340 | |
Сравнительная таблица твердости стали.![]() |
Эта сравнительная таблица предназначена только для справки. Эквиваленты следует рассматривать с осторожностью.
*Некоторые условия могут повлиять на соотношение между твердостью и пределом прочности при растяжении.
KV Steel Services является поставщиком качественной стали для предприятий точного машиностроения.
Термическая обработка обычных сталей. Машиностроение
Термическая обработка обычных сталей Таблица температур и закалочных сред
Закалочные среды : Закалочные растворы действуют только благодаря своей способности охлаждать сталь. Они не оказывают благотворного химического воздействия на закаленную сталь и сами по себе не придают никаких необычных свойств. Большинству требований к закалочным средам удовлетворительно удовлетворяет вода или водные растворы неорганических солей, таких как поваренная соль или каустическая сода, или какое-либо масло. Скорость охлаждения относительно высокая при закалке в рассоле, несколько менее быстрая в воде и медленная в масле.
Закалка : Отпуск уменьшает хрупкость, придаваемую закалкой, и придает стали определенные физические свойства. Закалка всегда следует за закалкой, а не предшествует ей. Помимо снижения хрупкости, отпуск размягчает сталь. Отпуск всегда проводят при температурах ниже нижней критической точки стали. В этом отношении отпуск отличается от отжига, нормализации или закалки, которые требуют температуры выше верхней критической точки.
Отжиг : Отжиг стали позволяет получить мелкозернистый, мягкий, пластичный металл без внутренних напряжений или деформаций. В отожженном состоянии сталь имеет наименьшую прочность. Как правило, отжиг противоположен закалке. Нагрев металла чуть выше верхней критической точки, выдержка при этой температуре и очень медленное охлаждение в печи завершают отжиг стали.
Нормализация : Нормализация стали устраняет внутренние напряжения, возникающие при термической обработке, сварке, литье, формовании или механической обработке. Стресс, если его не контролировать, приводит к неудаче. Из-за лучших физических свойств стали часто используются в нормализованном состоянии, но редко, если вообще когда-либо, в отожженном состоянии. Одним из наиболее важных применений нормализации является сварка деталей. Сварка вызывает деформации в соседнем материале. Кроме того, сам сварной шов представляет собой литую структуру, в отличие от кованой структуры остального материала. Эти два типа структур имеют разную зернистость, и для измельчения зерна, а также для снятия внутренних напряжений после изготовления все сварные детали должны быть нормализованы.
Термическая обработка стали Таблица температуры и закалочной среды
Сталь | Температура | Закалочная среда | ||
Воздушное нормализующее охлаждение | Отжиг | Закалка | ||
1020 | 1 650–1 750 | 1 600–1 700 | 1 575–1 675 | Вода |
1022 (x1020) | 1 650–1 750 | 1 600–1 700 | 1 575–1 675 | Вода |
1025 | 1 600–1 700 | 1 575–1 650 | 1 575–1 675 | Вода |
1035 | 1 575–1 650 | 1 575–1 625 | 1 525–1 600 | Вода |
1045 | 1 550–1 600 | 1 550–1 600 | 1 475–1 550 | Масло или вода |
1095 | 1 475–1 550 | 1 450–1 500 | 1 425–1 500 | Масло |
2330 | 1 475–1 525 | 1 425–1 475 | 1 450–1 500 | Масло или вода |
3135 | 1 600–1 650 | 1 500–1 550 | 1 475–1 525 | Масло |
3140 | 1 600–1 650 | 1 500–1 550 | 1 475–1 525 | Масло |
4037 | 1 600 | 1 525–1 575 | 1 525–1 575 | Масло или вода |
4130 (x4130) | 1 600–1 700 | 1 525–1 575 | 1 525–1 625 | Масло (с) |
4140 | 1 600–1 650 | 1 525–1 575 | 1 525–1 575 | Масло |
4150 | 1 550–1 600 | 1 475–1 525 | 1 550–1 550 | Масло |
4340 (x4340) | 1 550–1 625 | 1 525–1 575 | 1 475–1 550 | Масло |
4640 | 1 675–1 700 | 1 525–1 575 | 1 500–1 550 | Масло |
6135 | 1 600–1 700 | 1 550–1 600 | 1 575–1 625 | Масло |
6150 | 1 600–1 650 | 1 525–1 575 | 1 550–1 625 | Масло |
6195 | 1 600–1 650 | 1 525–1 575 | 1 500–1 550 | Масло |
NE8620 | — | — | 1 525–1 575 | Масло |
NE8630 | 1 650 | 1 525–1 575 | 1 525–1 575 | Масло |
NE8735 | 1 650 | 1 525–1 575 | 1 525–1 575 | Масло |
NE8740 | 1 625 | 1 500–1 550 | 1 500–1 550 | Масло |
30905 | — | (г) (з) | (и) | — |
51210 | 1 525–1 575 | 1 525–1 575 | 1 775–1 825 (к) | Масло |
51335 | — | 1 525–1 575 | 1 775–1 850 | Масло |
52100 | 1 625–1 700 | 1 400–1 450 | 1 525–1 550 | Масло |
Коррозионностойкий (16-2)(1) | — | — | — | — |
Хром кремний (для пружин) | — | — | 1 700–1 725 | Масло |
Сталь | Отпуск (волочение) Температура для | ||||
100 000 | 125 000 | 150 000 | 180 000 | 200 000 | |
1020 | — | — | — | — | — |
1022 (x1020) | — | — | — | — | — |
1025 | (а) | — | — | — | — |
1035 | 875 | — | — | — | — |
1045 | 1 150 | — | — | (н) | — |
1095 | (б) | — | 1 100 | 850 | 750 |
2330 | 1 100 | 950 | 800 | — | — |
3135 | 1 250 | 1 050 | 900 | 750 | 650 |
3140 | 1 325 | 1 075 | 925 | 775 | 700 |
4037 | 1 225 | 1 100 | 975 | — | — |
4130 (x4130) | (г) | 1 050 | 900 | 700 | 575 |
4140 | 1 350 | 1 100 | 1 025 | 825 | 675 |
4150 | — | 1 275 | 1 175 | 1 050 | 950 |
4340 (x4340) | — | 1 200 | 1 050 | 950 | 850 |
4640 | — | 1 200 | 1 050 | 750 | 625 |
6135 | 1 300 | 1 075 | 925 | 800 | 750 |
6150 | (г) (д) | 1 200 | 1000 | 900 | 800 |
6195 | (ф) | — | — | — | — |
NE8620 | — | 1000 | — | — | — |
NE8630 | — | 1 125 | 975 | 775 | 675 |
NE8735 | — | 1 175 | 1 025 | 875 | 775 |
NE8740 | — | 1 200 | 1 075 | 925 | 850 |
30905 | — | — | — | — | — |
51210 | 1 200 | 1 100 | (к) | 750 | — |
51335 | — | — | — | — | — |
52100 | (ф) | — | — | — | — |
Коррозионностойкий (16-2)(1) | (м) | — | — | — | — |
Хром кремний (для пружин) | — | — | — | — | — |
Примечания:
(a) Натяжение при 1150 °F для прочности на растяжение 70 000 фунтов на квадратный дюйм.
(b) Для отпуска в состоянии пружины при температуре 800–900 °F. Твердость по Роквеллу С-40–45.
(c) Прутки или поковки можно закаливать в воде при температуре от 1500 до 1600 °F.
(d) Охлаждение на воздухе от температуры нормализации дает прочность на растяжение примерно
фунтов на квадратный дюйм.
(e) Для отпуска в состоянии пружины при температуре 850–950 °F. Твердость по Роквеллу С-40–45.
(f) Вытяжка при температуре 350–450 °F для удаления деформаций закалки. Твердость по Роквеллу С-60–65.
(g) Отжиг при 1600–1700 °F для снятия остаточных напряжений, вызванных сваркой или холодной обработкой. Может применяться только к стали, содержащей титан или ниобий.
(h) Отжиг при 1900–2100 °F для обеспечения максимальной мягкости и коррозионной стойкости. Охладить на воздухе или закалить в воде.
(i) Закаливать только холодной обработкой.
(j) Нижняя граница диапазона для листов толщиной 0,06 дюйма и менее. Средний диапазон для листа и проволоки 0,125 дюйма.
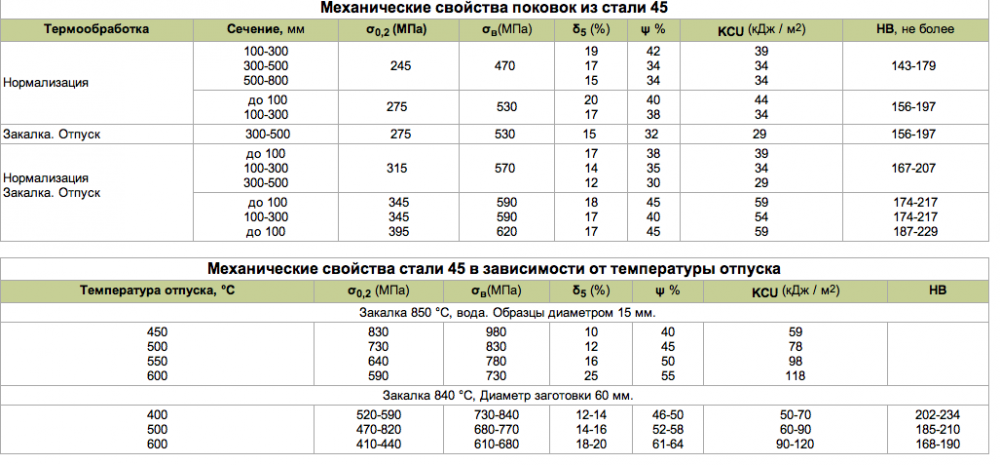
(k) Не рекомендуется для промежуточных пределов прочности на растяжение из-за низкой ударопрочности.
(l) AN-QQ-S-770 — рекомендуется, чтобы перед отпуском коррозионно-стойкая (16 Cr-2 Ni) сталь подвергалась закалке в масле при температуре 1875–1900 °F после периода выдержки в течение 30 минут при этой температуре. Чтобы получить прочность на разрыв при 115 000 фунтов на квадратный дюйм, температура отпуска должна быть примерно 525 ° F. Рекомендуется время выдержки при этих температурах около 2 часов. Температуры отпуска от 700 ° F до 1100 ° F не одобрены.
(m) Вытяжка при температуре приблизительно 800 °F и охлаждение на воздухе для твердости по Роквеллу C-50.
(n) Вода, используемая для закалки, должна иметь температуру 80–150 °F.
Рис. 1 Температурная диаграмма, показывающая преобразование градусов по Цельсию в градусы Фаренгейта или наоборот, шкала цветовой температуры для диапазона температур закалки и диапазона температур отпуска.