Закалка лезвия ножа графитом: Как закалить нож в домашних условиях: видео, инструкция, советы
alexxlab | 22.02.2023 | 0 | Разное
Как сделать нож из железнодорожного костыля
Профильные форумы содержат немало негативных высказываний о ножах из железнодорожного костыля. Якобы они имеют малую твёрдость и резать ножом позволительно лишь масло. Отчасти высказывания верны. Но, не изучив тему окончательно – делать выводы, неблагородное занятие. Закалка клинка с помощью цементирования – даёт потрясающие результаты. Попробуем разобраться с процессом в статье.
Нож из костыля своими руками.Содержание
- Процесс изготовления ножа из костыля своими руками
- Свойства стали ж/д костылей и как увеличить её прочность
- Закалка режущей кромки ножа графитом
- Закалка клинка твёрдой термической обработкой
Процесс изготовления ножа из костыля своими руками
Отрицательные отзывы о ножах из костыля не безосновательны, металл из которого делают костыли, фактически непригоден для изготовления ножей. Но есть секреты закалки стали. С их помощью легко добиться хорошей твёрдости клинка или лезвия. Начнём с изготовления:
- Необходимые материалы и инструменты, практически ничем неотличимы от обычной ковки: молоты 2 шт., горн (печь), наковальня, тиски, клещи.
- Мастера предпочитают изготавливать клинок и рукоять из костыля, без дополнительных элементов типа дерева, пластика, оргстекла. Изготовление начинается с ручки, ею является сторона изделия со шляпкой. Разогрев докрасна эту часть, заготовку зажимают в тиски, и производят вращение металла вокруг оси в пару оборотов. Рукоять примет интересный закрученный вид.
- Немного поправив ручку небольшим молотом, мастер куёт клинок. Расплющив обратную сторону заготовки и придав спуски. Одновременно выполняется подъём и остриё клинка. Металл легко поддаётся ковке, при невысоких температурах. Спецы выполняют эти процедуры за 30-40 минут.
- Охладив на воздухе изделие и доведя спуски до нужного уровня, мастер приступает к специальной закалке клинка.
- По окончании процедуры шлифуется всё изделие до блеска.
- Делается заточка режущей кромки, клинок готов.
В следующем разделе будет рассказано, о процедуре способной «оживить» почти любой металл. Советы опытных сталеваров придутся по вкусу, профессионалам и новичкам.
Свойства стали ж/д костылей и как увеличить её прочность
О свойствах стали железнодорожного костыля выдумывать небылицы нет смысла. Обыкновенная железяка под номером 3. Существует два способа придать клинку улучшенную твёрдость.
Пригодны они для определённых марок стали. Информация свободно доступна в интернете, загадка – почему ею люди боятся воспользоваться?
Неужели, проще написать негативный отзыв, чем изучить дополнительный метод закалки стали. Начнём со способа попроще.
Железнодорожный костыль.Закалка режущей кромки ножа графитом
Способ позволяет увеличить твёрдость режущей кромки. Понадобится: графит, металлическое основание и импульсный сварочный аппарат. Графит добыть проще из щёточного электродвигателя или пальчиковых батареек. От карандаша не вариант, содержит много добавок:
- Графит необходимо довести до порошкового состояния.
- В качестве металлического основания используйте плоскую ёмкость с небольшим углублением. Кусок строительного профиля – нормальный вариант.
- Необходимо засыпать в него графит и подключить плюс сварочного аппарата. К клинку – минус.
- Процесс заключается в проведении РК по кучке графита. Он будет искрить, возгорания допускать нельзя. Запрещено касание клинком профиля.
- Сильно опускать РК в графит не нужно, необходимо аккуратно поводить лезвием по кучке.
Процесс занимает немного времени, 5-7 минут. За это время необходимо успеть провести ножом несколько раз. Такой процесс называют – цементирование. Режущая кромка будет иметь твёрдость в 60-62 HRC.
Закалка клинка твёрдой термической обработкой
Принцип заключается в насыщении поверхности металла необходимым количеством углерода.
Процесс изменяет фазовый состав и атомарную решётку изделия. Такую процедуру производят с различными изделиями. Ножи не исключение.
Для цементации потребуется специальный порошок, состоящий из: бария, кальция и древесного угля. Все ингредиенты следует просеять через сито и тщательно перемешать:
- Для цементации клинка необходима огнеупорная форма, напоминающая ножны. В неё насыпается смесь.
- Клинок целиком погружаем в подготовленный порошок и у рукояти замазываем глиной. Она предотвратит утечку газов, и позволит детали нагреваться равномерно.
- Разогрев печь до 600-700 °C, туда помещается форма с клинком, постепенно повышая температуру до 1000-1100 °C.
Благодаря смеси солей и требуемому нагреву, происходят диффузные изменения в кристаллической решётке стали на атомном уровне. Держать при такой температуре следует 2-3 часа, для хорошего насыщения углеродом этого достаточно.
Достать изделие из печи и дать остыть на воздухе. Способ реально наилучший, не только РК пройдёт цементацию, но и весь клинок целиком. Минус процесса – время. Но результат превзойдёт все ожидания.
Старение сплавов. Закалочное и деформационное старение. Назначение, типы, виды режимов, структура и получаемые свойства
Отпуск и старение металла
Часто путём закалки повышается не только твёрдость металла, но и его хрупкость, поэтому необходимо выполнять ещё один этап — отпуск, при котором прочность и твёрдость несколько снижаются, но материал становится более пластичным. Делают отпуск при температуре, ниже, чем в предыдущем процессе, и охлаждают металл постепенно.
Можно проводить закалку без изменения структуры металла (полиморфного превращения). В этом случае не возникнет проблем с хрупкостью, но необходимая твёрдость не будет достигнута. А повысить её удастся путём ещё одного процесса термообработки, называемого старением. При старении происходит распад пересыщенного твёрдого раствора, в результате которого увеличивается прочность и твёрдость материала.
Отпуск стали — это разновидность термообработки, используемая для деталей, закалённых до критической точки, при которой происходит полиморфное изменение кристаллической решётки. Он заключается в выдерживании металла определённый промежуток времени в нагретом состоянии и медленном охлаждении на открытом воздухе. Делают отпуск, чтобы снизить внутреннее напряжение, а также исключить хрупкость металла и увеличить его пластичность.
При помощи старения достигается необходимая твёрдость закалённой стали. Старение может быть:
- естественным, при котором самопроизвольно повышается прочность закалённого металла и снижается его пластичность. Происходит данный процесс при выдержке в естественной среде;
- термическим.
Такое старение — это процесс повышения твёрдости металла посредством выдержки при высоких температурах. По сравнению с первым видом, в данном случае может произойти перестаривание — это когда твёрдость, пределы прочности и текучести, достигая максимальной величины, начинают снижаться;
- деформационным. Такое старение достигается при помощи пластической деформации закалённого сплава, имеющего структуру пересыщенного твёрдого раствора.
Что такое кузнечные краски
В последнее время большой популярностью пользуются кузнечные краски, специально оптимизированные для работы с кованными материалами. Такие краски наносятся на ковку с декоративными целями, что позволяет имитировать самые различные поверхности, начиная от золота и заканчивая чугуном.
Стоимость таких красок выше, чем у обычных. Однако это объясняется их повышенным сроком годности, который достигает 5 лет и более. При этом такие краски еще и действительно эффектно смотрятся, позволяя придать требуемый визуальный эффект уже самым фактом своего присутствия. Без необходимости применять различные способы окраски.
Сегодня имеется немало видов подобного покрытия, однако самым востребованным по праву считается немецкая краска WS-Plast, производимая Weigel & Schmidt GmbH. Данные краски позволяют придавать металлической поверхности множество различенных цветов и текстур. Тут вам и изумрудный цвет, и отличающийся красными тонами графит, и различные виды окраски под старину. При этом такое покрытие не только украшает, но еще и защищает металлическую поверхность от коррозии и прочих неприятностей, вызванных воздействием природы.
Также популярностью обладает молотковая краска (Hammerite), которая в настоящее время становится все более востребованной. Причина заключается в том, что такая краска не требует нанесения грунтовки, и даже может быть использована непосредственно на поверхностях, поврежденных коррозионными процессами. Впрочем, если ржавчина рыхлая, то ее все же придется удалить. Поверхность, обработанная данным покрытием, становится однотонной с эффектом узоров неравномерной формы и алюминиевых хлопьев.
Нанесение данной краски в основном практикуется с черными металлами, такими, как сталь и чугун. Впрочем, ей можно обрабатывать и некоторые цветные металлы.
Способы закалки
Суть любой закалки — превращение аустенита в мартенсит (диаграмма «железо-углерод»). В зависимости от температурного режима, закалка может быть полной или неполной. Первым способом закаливают инструментальную сталь, а вторым — цветную.
При закалке могут использоваться один или несколько охладителей. От этого также зависит способ термообработки. В зависимости от охлаждающей среды, термическая обработка металла может быть:
- с использованием одного охладителя;
- с подстуживанием;
- прерывистой;
- ступенчатой;
- изотермической.
Закалка в одном охладителе
Данный метод применяется для термообработки простых деталей, изготовленных из легированной и углеродистой стали. Деталь нагревается до необходимой температуры, а затем охлаждается в жидкости. Углеродистую сталь диаметром от 2 до 5 мм охлаждают в воде, детали меньшего диаметра и всю легированную сталь — в масле.
Закалка с подстуживанием
При термообработке с одним охладителем часто возникают состояния термического и структурного внутреннего напряжения. Развиваются они в том случае, когда разность температур достигает минимума. На поверхности металла образуется напряжение растяжения, в центре — напряжение сжатия. Чтобы данные напряжения уменьшить, перед тем, как опустить нагретую деталь в жидкость, её недолго держат на открытом воздухе. Температура детали в данном случае не должна быть ниже линии 0,8К по диаграмме «железо-углерод».
Прерывистая
Эту закалку проводят в двух средах — воде и масле или воде и воздухе. Нагретую до критической точки деталь сначала быстро охлаждают в воде, а потом медленно в масле или на открытом воздухе. Такой способ термообработки применяют для высокоуглеродистой стали. Этот метод — сложный, так как время охлаждения в первой среде очень мало и определить его сможет лишь специалист высокой квалификации.
Ступенчатая
При прерывистой термообработке деталь охлаждается неравномерно — более тонкие поверхности быстрее, чем все остальные. К тому же очень трудно отрегулировать время нахождения детали в первой среде (воде). Поэтому лучше использовать ступенчатую закалку. Данный метод позволяет охлаждать деталь в среде при температуре, превышающей мартенситную точку. Первая ступень — охлаждение и выдержка детали в данной среде до того момента, когда все сечения детали достигнут одной и той же температуры. Вторая ступень — окончательное медленное охлаждение (преобразование аустенита в мартенсит).
Изотермическая
При изотермической термообработке деталь нагревают до критической точки, а затем опускают в масляную или соляную ванну температурой 250 градусов. Выдерживают полчаса, а далее остужают на открытом воздухе. Такая закалка обеспечивает высокую конструкционную прочность и применяется для легированных и конструкционных сталей, у которых распад аустенита в промежуточной области не происходит до конца. В дальнейшем он превращается не в мартенсит, а в бейнит + 20% остаточный аустенит, обогащённый углеродом. Такой закалкой можно достичь высокой прочности при хорошей вязкости.
Другие методы
Такие методы подходят для состаривания других видов металла. К примеру, если нужно состарить латунь, достаточно взять яблочный уксус (3 части) и соль (1 часть). Из компонентов готовят раствор и наливают его во флакон для распыления. В течение получаса изделие следует равномерно орошать полученным раствором. В конце работы предмет нужно отполировать парафином.
Также металлическое изделие можно покрасить, и для этого нужно подготовить наждачную бумагу, растворитель, черную акриловую краску, кисть-губку, другой оттенок акриловой краски (это будет акцентный цвет). Перед тем как приступить к работе над изделием, нужно обработать его наждачной бумагой, а после следует обезжирить поверхность предмета. Затем нужно взять кисть, смочить ее водой и окунуть в краску черного цвета. Изделие окрашивают и оставляют его высыхать на ночь. После предмет нужно неравномерными мазками окрасить краской акцентного цвета. Слой краски должен сохнуть минимум двое суток.
Какой бы метод состаривания металла ни был выбран, человек, работающий над изделием, должен позаботиться о соблюдении правил техники безопасности. Нельзя допускать попадания каких-либо средств на кожу и слизистые оболочки!
Температурный режим
Закалка — это превращение аустенита в мартенсит. На производстве при выборе температур термообработки пользуются диаграммой «железо-углерод». Температуру закалки углеродистых сталей определить очень легко. Нагрев конструкционной стали с содержанием углерода менее 0,8% доводят до температур, расположенных над линией GS и выше точки Ас3 на 30-50 градусов. Нагрев сталей, содержащих более 0,8% углерода, проводят при температурах на 30-50 градусов выше тех, которые расположены выше линии PSK. Температуру закалки легированной стали также выбирают, исходя из критических точек, но данный процесс много сложнее, так как помимо углерода такие стали содержат и другие компоненты.
Выбор охлаждающей среды
От выбора зависит качество детали:
- для охлаждения простых деталей и изделий, изготовленных из углеродистых сталей применяют чистую воду;
- для изделий сложных форм в качестве охладителя используют каустическую соду, смешанную с водой в соотношении 1:1. Приготовленный раствор нагревают до 50-60 градусов;
- закалка металла в масле применима к тонкостенным деталям из легированных или углеродистых сталей.
Углеродистую сталь, имеющую сложный состав, остужают в двух охладителях — сначала быстро в чистой воде, а затем медленно в ванне, наполненной маслом. Перемещать детали из воды в масло нужно очень быстро.
Покраска под старинную латунь
Декоративная краска для ковки может имитировать и другой красивый сплав – латунь. Как и бронза, он имеет теплый золотистый оттенок. Технология окрашивания под латунь напоминает декорирование под бронзу с патиной.
Можно применять следующий способ:
- на очищенный и загрунтованный металл наносят 1 слой латунной краски;
- после высушивания покрывают изделие кракелюрным лаком: покрытие образует мелкие трещинки;
- чтобы усилить выразительность покрытия, поверх лака окрашивают жженой умброй или полупрозрачным темным лаком, нанося тонкий слой и стараясь втереть его в потрескавшуюся поверхность;
- после высыхания изделие покрывают прозрачным акриловым лаком.
Подобным способом отделывают и поверхности под старинную медь, используя для первичного окрашивания состав с медной пудрой. В отличие от золотистых латуни и бронзы металлизированная краска имеет красноватый оттенок.
Читайте далее:
Как и чем красить изделия из гипса
Способы окраски изделий под дерево
Покраска дерева под старину для имитации антиквариата: секреты декорирования
Технология покраски декоративной штукатурки: выбор краски и колера, создание различных эффектов
Чем покрасить изделия из ДВП: особенности обработки материала
Какую сталь подвергают закалке
Термически обрабатывают только такой металл, в котором содержится не менее 0,45% углерода, а также инструментальную и легированную стали, твёрдость которых после закалки становится в несколько раз выше. Тот металл, в котором содержание углерода не превышает 0,45%, не обрабатывается термически. Ниже приведена таблица режимов термообработки для некоторых видов сталей.
Тип | Инструмент | Температура закалки | Температура отпуска | Чем охлаждают после закалки | Чем охлаждают после отпуска |
У7, У7А | Инструмент плотника, отвёртки, топоры, зубила и др.![]() | 800 | 170 | водой | водой маслом |
У8, У8А | Слесарный инструмент, пилы, ножовки, стамески и др. | 800 | 170 | водой | водой маслом |
У10, У10А | Ручные метчики, надфили, рашпили, пилы по дереву, инструмент без нагрева режущей кромки | 790 | 180 | водой | водой маслом |
У11, У11А | Деревообрабатывающий инструмент, ручные метчики, надфили и др. | 780 | 180 | водой | водой маслом |
У12, У12А | Слесарный инструмент | 780 | 180 | водой | водой маслом |
У13, У13А | Режущий и измерительный инструмент, детали машин | 780 | 180 | водой | вода масло |
У9ГА | Режущий инструмент — метчики, свёрла, фрезы | 800 | 180 | вода | водой маслом |
Р9 | Режущий инструмент — метчики, свёрла, зенкера, фрезы, протяжки и др.![]() | 1250 | 580 | маслом | воздухом печи |
Р18 | Режущий инструмент для обработки металлов различной твёрдости | 1300 | 580 | маслом | воздухом печи |
ШХ6 | Шарики и ролики для подшипников | 810 | 200 | маслом | воздухом |
ШХ9 | Шарики и ролики для подшипников | 830 | 280 | маслом | воздухом |
ШХ15 | Шарики и ролики для подшипников | 845 | 400 | маслом | воздухом |
9ХС | Свёрла, фрезы, развёртки, метчики, гребёнки и др. | 860 | 170 | маслом | воздухом |
9Х5ВФ | Ножи для фрезерования древесины | 950 | 270 | маслом | воздухом |
50ХГСА | Пружины, рессоры | 840 | 315 | водой | воздухом |
60С2 | Торсионные валы, высоконагружаемые пружины | 870 | 325 | водой | воздухом |
60С2ХА | Высоконагружаемые пружины и рессоры | 870 | 315 | водой | воздухом |
60С2ВА | Пружины и рессоры | 850 | 330 | водой | воздухом |
85ХВ | Пружины, фрикционные диски | 830 | 250 | водой | воздухом |
Какие бывают дефекты при закалке металла
При несоблюдении режимов закалки могут появляться следующие дефекты:
- трещины или коробление.
Причина — внутреннее напряжение. Если коробление поддаётся рихтовке и выпрямлению, то трещины исправить никак нельзя. Это — окончательный брак;
- пережог, который представляет из себя окислы по границам зёрен, возникающие из-за проникновения внутрь металлических изделий кислорода. Пережог возможен при нагреве металла до температуры, близкой к температуре плавления. Такой металл не подлежит исправлению;
- перегрев. При нагреве металла свыше температуры каления происходит его перегрев, в результате которого образуется крупная структура. Такой металл обладает повышенной хрупкостью. Исправляется при помощи отжига и новой закалки;
- низкая твёрдость. Недостаточная твёрдость получается при низкой температуре нагревания, недостаточной выдержке при необходимой температуре и маленькой скорости охлаждения. Данный дефект легко исправить при помощи отжига и ещё одной закалки;
- окисление и обезуглероживание, которое происходит при воздействии металла с воздухом и печными газами.
Окисленный слой, окалина, наносит непоправимый вред производству, ибо такой дефект исправить нельзя. Чтобы избежать проблемы, необходимо использовать печи с защитной атмосферой.
Технология изготовления
Патенированные изделия производятся в заводских условиях и в мастерских. Ассортимент может быть ограничен, но есть возможность сделать индивидуальный заказ. Ретро-зеркала изготавливаются по уникальным методикам искусственного состаривания. В результате получается интересный рисунок и оригинальные эффекты.
Важно! Винтажные изделия декорируются вручную. Применяются следующие техники:
Применяются следующие техники:
- состаривание с использованием щелочей;
- техника «Гламизе»;
- нанесение рисунка в стиле ретро.
Чтобы получить винтажное изделие, определенные участки вытравливаются при помощи химического раствора. Процесс проводится вручную. На поверхности выступает рисунок, у которого нет аналогов. Обработка щелочами помогает создать эффект состаренности.
Французская техника «Гламизе» состоит в том, что мастер процарапывает иглой на зеркале узоры и рисунки. Затем изделие покрывается слоем краски. Оно хорошо смотрится в винтажном багете. На поверхность наносят узоры, имитирующие «потрепанность временем». Для усиления эффекта используют поталь. Это листы металла, имитирующие сусальное золото.
Закалка стали в условиях дома или дачи
Иногда случается такое, что необходима термообработка металла дома или на даче. Это происходит, если купленный инструмент оказался недокаленным или вообще незакалённым. Часто возникает необходимость закалить ножик, топор или сверло. Конечно, хорошую закалку можно провести только в условиях производства, но мужчины-умельцы отлично умеют это делать и на обыкновенном костре. Последовательность домашней закалки:
- готовим две ёмкости. В одну наливаем минеральное масло, в другую — воду;
- также нужно подготовить инструмент, при помощи которого будем класть закаливаемый металл в костёр и вынимать из него.
Для этой процедуры подойдут клещи;
- далее разводим костёр и ждём когда образуются угли. На них и кладём металлический предмет, который нужно закалить;
- следим за цветом углей и окраской пламени. Раскалённые угли имеют белый цвет. А пламя не должно быть белым. Малиновый цвет пламени — оптимальный для процесса закалки в домашних условиях. Белое пламя говорит о слишком высокой температуре внутри костра, и деталь наша может просто сгореть;
- также необходимо следить, чтобы на металлическом изделии не появлялись чёрные или синие пятна, которые говорят о деформации металла в результате чрезмерного размягчения. А если металл стал белым, то такую деталь можно смело выкидывать.
- как только металлический предмет нагреется до нужной нам температуры, вытаскиваем его и опускаем сначала в масло. Делаем это трижды, первый раз на три секунды. Каждый раз время увеличиваем на столько же. Опускаем и вынимаем резко;
- далее опускаем металлический инструмент в ёмкость с водой и оставляем там до тех пор, пока он полностью не остынет.
Детали или предметы, имеющие вытянутую форму в воду помещаем вертикально. Для оценки температуры закалки в костре используем таблицу цветов. Вместо костра можно использовать любую печку.
СТАРЕ́НИЕ МЕТА́ЛЛОВ
Авторы: М. А. Штремель
СТАРЕ́НИЕ МЕТА́ЛЛОВ, изменение свойств металлов и сплавов, протекающее самопроизвольно в процессе длительной выдержки при комнатной темп-ре (естественное старение) либо при умеренном нагреве (искусственное старение). С. м. проводится как спец. окончательная операция термической обработки для большого числа сплавов, которая обеспечивает получение комплекса необходимых механич. или физич. свойств.
Старение, или «дисперсионное твердение», – осн. способ упрочняющей термич. обработки сплавов на основе цветных металлов – Al, Mg, Cu, Ni и др.; проводится при выдержке сплава ниже темп-ры предшествующей закалки с целью выделения из твёрдого раствора дисперсных (0,01–1 мкм) включений, что приводит к повышению прочности.
В сплавах на основе железа при старении (при 20–300 °C и выдержке от нескольких часов до нескольких лет) происходит повышение предела текучести по мере перехода содержащихся в сплавах N и C в сегрегации (химич. неоднородности) и выделения на дислокациях. В зависимости от предшествующей обработки сплава старение может быть двух осн. типов – закалочное и деформационное. Наибольшее практич. значение имеет деформац. старение, которое в отличие от закалочного может происходить при низком содержании примесных атомов в твёрдом растворе; оно наблюдается практически для всего диапазона содержания С в стали, в то время как закалочное даёт заметный эффект в осн. только для низкоуглеродистых сталей. В случае когда деформац. старению предшествует холодная пластич. деформация, упрочнение стали повышается, но несколько снижается пластичность. Динамич. деформац. С. м. – процесс старения, протекающий непосредственно в ходе пластич. деформации; такую «тёплую деформацию» ниже температур рекристаллизации используют для дополнит. упрочнения, напр., пружинной проволоки и ленты.
Старение стали может проявляться в ухудшении пластичности и вязкости за время длительной эксплуатации при климатич. темп-рах. К процессу собственно С. м., в т. ч. деформационного, добавляется деградация поверхностного слоя за счёт износа, коррозии и пр. Для предотвращения отрицат. эффекта С. м. в «нестареющих сталях» понижают содержание C и N (до 10–3% по массе) или связывают их в соединения (TiC, AlN и др.). Экспресс-контроль стали на возможное С. м. – сравнение ударной вязкости до и после холодной деформации и выдержки при 250 °C.
Проверка металла на наличие термообработки
Перед тем, как начать каление, нам необходимо убедиться, что материал приобретённого нами инструмента не термообработан. Делаем проверку с помощью обыкновенного паяльника. Нагреваем инструмент и проводим им по интересующей нас металлической поверхности. Если паяльник прилипает к металлу, то значит ни о какой его термообработке не может быть и речи. Плавное прохождение паяльника по поверхности стали или отскакивание от неё говорят о том, что проверяемый нами предмет либо хорошо термообработан либо обработан слишком сильно. При отсутствии термообработки делаем её самостоятельно.
Технологии состаривания горных пород
Технологии декоративного преображения горных пород достаточно разнообразны и связаны с физико-техническими характеристиками обрабатываемой поверхности. Мягкие образцы (туф, травертин, мрамор) чаще всего подвергают кислотному травлению либо механическому воздействию средних по твердости абразивов.
Для особо прочных горных пород (классический гранит, габбро диабаз и прочие интрузивы) применяют технологии искусственного старения двух типов:
- Механические представляют собой бучардирование – ударно-вращательное воздействие на камень зубчатыми молотками-бучардами, закрепленными на вращающихся дисках.
В результате твердосплавные иглы создают на гранитной поверхности оригинальный рельефный рисунок.
- Термические предполагают использование высокотемпературных газовых горелок, выжигающих из поверхностного слоя породы кристаллы наименее тугоплавких минералов. Отличие такой технологии от первого метода состоит в том, что поверхность камня после обработки может немного изменить цвет, став более светлой.
Закалка ножа графитом
Термическая обработка металла графитом хороша тогда, когда нужно закалить не весь предмет, а только его часть. У ножа — это кромка. Последовательность процесса термообработки ножа в домашних условиях:
- острие ножа проверяем на твёрдость при помощи надфиля. Если металл легко стачивается, а надфиль издаёт глухой звук, значит нож не термообработан;
- для данного процесса понадобится графит, который можно добыть из круглых батареек, взять стержни простого карандаша или воспользоваться графитовыми щётками генератора;
- добытый графит превращаем в порошок;
- в качестве источника питания используем сварочный аппарат постоянного тока.
Выставляем на минимум;
- делаем подложку из оцинкованного листа. На неё насыпаем графитовый порошок;
- к подложке подсоединяем «плюс» сварочного прибора, а ручке ножа — «минус»;
- далее лезвием ножа аккуратно водим по графиту так, чтобы оно не касалось подложки. А ещё следим, чтобы графит не воспламенился, иначе ножик наш будет испорчен;
- при движении лезвия по графиту последний будет выдавать искры. Как только увидим, что остриё ножика нагрелось, процесс прекращаем. Приблизительное время закалки — не более 5 минут;
- даём ножу остыть естественным путём, затем берём надфиль и проверяем твёрдость. Если звук, издаваемый надфилем при контакте с ножом звонкий, а остриё не поддаётся затачиванию, значит твёрдость лезвия высокая.
Процесс закалки на производстве провести намного легче, чем дома. При необходимости можно попробовать закалить нужный предмет или инструмент «топорными» способами с применением подручных средств.
Используемая литература и источники:
- Поверхностные явления в металлах и сплавах / В.
К. Семенченко. — М.: Гостехиздат
- Сверхбыстрая закалка жидких сплавов. — Москва: Машиностроение
- Статья на Википедии
Как закалить и закалить лезвия ножей
Этот пост ответит на вопрос, как закалить лезвия ножей, а также закалить их. Также ответим, зачем закаливать и отжигать лезвие ножа.
Начнем с того, зачем закалять сталь. когда вы закаляете сталь, вы заключаете углерод и железо в более прочные, но более хрупкие структуры. Когда вы закаляете его, вы позволяете углероду растворяться в железе и формировать более прочные структуры за счет некоторой твердости.
Что касается того, как закалить лезвие ножа для резьбы по дереву, вам нужно нагреть его до красной температуры, а затем быстро охладить лезвие. Точная температура называется критической температурой и варьируется в зависимости от конкретного сплава стали. Именно при температуре происходит аустенитное фазовое превращение.
На простых углеродистых сталях вы можете грубо проверить, достаточно ли высока температура, используя магнит: когда он достигает достаточно высокой температуры, магнит больше не будет прилипать к стали, обычно он достигает критической температуры и готов к закалке. . При этой температуре сталь будет светиться тусклым красным цветом, если смотреть в условиях низкой освещенности, в то время как при более высокой температуре вы можете в конечном итоге сжечь углерод в стали, что сделает ее неспособной достичь полной твердости и потенциально расплавит края вашего лезвия.
Более экзотические сплавы могут иметь критические температуры, которые варьируются от точки, при которой сталь больше не притягивается к магниту, и более сложные требования к термообработке. В этой статье мы предполагаем, что вы работаете с простой высокоуглеродистой сталью. Если вы имеете дело с более причудливыми стальными сплавами, вам следует выяснить точную температуру для использования и рассмотреть возможность использования кузницы с регулируемой температурой, чтобы получить все преимущества более совершенного сплава.
Для закалки небольших лезвий можно использовать кислородно-ацетиленовую горелку. Для более крупных предметов, таких как тесло, мачете или мечи, вам понадобится подходящая горн, чтобы нагреть все лезвие до равномерного красного каления, или кислородно-пропановый бутон розы, чтобы иметь возможность производить достаточно тепла, поскольку ацетилен имеет очень низкий предел скорости.
При использовании кислородно-ацетиленовой горелки я рекомендую использовать пламя с небольшим количеством топлива, чтобы вы могли видеть небольшое оранжевое перо в пламени. это поможет покрыть лезвие углеродом и предотвратит выгорание углерода и железа на поверхности стали, что может привести к окислительной атмосфере.
- Нагрейте лезвие ножа для резьбы по дереву до тускло-красного каления. Начните с кончика лезвия и продвигайте тепло к кончику. Он больше не будет притягиваться к магнитам, его температура чуть ниже критической. Нагрейте лезвие немного сильнее, чем это.
- Когда лезвие достигнет желаемой температуры по всему лезвию, быстро погрузите лезвие в большой металлический контейнер с жидкостью, чтобы охладить его и затвердеть.
Убедитесь, что раскалённое докрасна состояние немного проникает в хвостовик, чтобы хвостовик имел достаточную прочность и не сгибался на вас. Также перед закалкой убедитесь, что режущая кромка лезвия не остыла. Вы должны быть очень быстрыми, чтобы погасить после удаления от источника тепла.
- Закалка лезвия ножа для резьбы по дереву путем нагревания ножа в среде с регулируемой температурой, такой как домашняя духовка (еще одна веская причина использовать безопасное для пищевых продуктов масло, такое как рапсовое, вместо моторного масла) при температуре от 350 до 450f в течение от 1/2 до 2 часов. Я рекомендую вам, по крайней мере, очистить лезвия от масла перед этим шагом и использовать моющее средство/обезжириватель, например простой зеленый, если вы использовали моторное масло, чтобы предотвратить загрязнение духовки.
Что касается жидкостей, которые следует использовать для тушения, то масло канолы лучше, чем моторное масло, из-за гораздо меньшего количества выделяемого дыма и, вероятно, менее опасного дыма по сравнению с присадками в моторном масле. Существуют и другие лучшие закаливающие масла, но масло канолы можно легко купить в местном продуктовом магазине, оно имеет очень высокую температуру дымообразования и стоит очень дешево. Можно использовать воду, и она будет остывать намного быстрее, чем масло, но может вызвать большую деформацию и даже привести к растрескиванию некоторых сталей.
Для разных сталей рекомендованы разные жидкости для закалки, и если вы точно не знаете, какой раствор вы используете, масла с большей вероятностью дадут желаемый результат, чем вода.
Если вы закаляете очень большое лезвие в масле, вы все равно можете получить немного дыма, особенно если вы используете моторное масло. Я рекомендую использовать горелку, чтобы поджечь дым, поднимающийся от масла, так как его сжигание уменьшит количество дыма и запаха.
Что касается закалки, я лично закаляю свои ножи для резьбы по дереву при 400f (204c) в течение 30 минут, но вы можете найти более высокие температуры до 450f (232c) для большей долговечности некоторых лезвий или до 350f (176c) для более твердость/способность удержания лезвия в зависимости от ножа.
Нормализация лезвия ножа для резьбы по дереву — еще один важный шаг. Перед закалкой, но после шлифовки и ковки следует подумать о нормализации. Нормализация – это процесс нагрева стали выше критической температуры и медленное охлаждение от этой температуры. Это помогает снять напряжение в лезвии, придаваемое ковкой и шлифовкой. Для прямых ножей очень важно, чтобы они не коробились при термической обработке, чтобы сначала нормализовать их. Это также может улучшить структуру зерна в окончательной закалке, чтобы нормализовать их перед закалкой, что дает немного более прочные лезвия после закалки.
Чтобы нормализовать лезвие ножа для резьбы по дереву, нагрейте его выше критической температуры, а затем дайте ему остыть на воздухе до комнатной температуры. Обычно рекомендуется повторять несколько раз, так как каждый раз снимается больше стресса. 3 раза обычно считается хорошим, и в идеале каждый раз следует проводить при более низкой пиковой температуре, чем в последний раз, хотя этого может быть трудно достичь без кузницы с регулируемой температурой.
Разница между нормализацией и отжигом вашего ножа для резьбы по дереву заключается в том, что нормализация остывает быстрее и не производит мертвую мягкую сталь, как при отжиге. Некоторые стали могут даже значительно затвердевать при простом охлаждении на воздухе, но, как правило, для ножей нужна более жесткая сталь.
Лезвие с мягкой подкладкой – Журнал BLADE
Нож Шона Эллиса украшен изящным узором из дамасской стали с четырьмя витками и оленьим оленем Sambar. (Изображение Калеба Ройера)На протяжении веков кузнецы из разных культур осознавали необходимость лезвий, которые выполняли бы свою работу без критических поломок. Некоторые восточные культуры специализировались на дифференциальной закалке, особенно японцы. Европейские культуры, как правило, приваривали закаливаемый край к более мягкому стержню. В каждом случае конечным результатом является достаточно твердая кромка, чтобы ее можно было хорошо резать, и корешок, прочный и устойчивый к поломке.
Одним из показателей современного производителя ножей является готовность и способность успешно проходить процессы сертификации мира ножей, такие как сертификаты подмастерья и мастера-кузнеца Американского общества кузнецов (ABS). Точно так же одним из показателей лезвия ножа является его способность выполнять различные задачи, которые подвергают испытанию геометрию лезвия и термообработку.
Если вы когда-либо были связаны с производством ножей за последние 40 лет или около того, вы, несомненно, видели истории о лезвиях, демонстрирующих способность удерживать лезвие, а также прочность и гибкость, чтобы сгибаться, не ломаясь. Ключом к такой производительности является то, что лезвие имеет твердую кромку и мягкую спинку. Простите за каламбур, но давайте немного сломаем это.
Перво-наперво — нож должен резать. Одним из ключей к превосходным режущим характеристикам является хорошо закаленная кромка. Правильно закаленная кромка достигается за счет использования стали с достаточным количеством углерода, доведенной до надлежащей температуры закалки, закаленной в надлежащей закалочной среде и отпущенной до надлежащей твердости.
Каждая из этих переменных имеет значение, но в конце концов, если производитель все сделает правильно, кромка хорошо работающего лезвия будет закалена и отпущена на мартенсит с твердостью в диапазоне от 58 до 60 HRC по Роквеллу плюс или минус точка или две в зависимости от геометрии. Если край оставить слишком мягким, лезвие не будет резать должным образом.
А как же острие лезвия? Должен ли он быть таким же твердым, как край? Ответ: «Это зависит». Твердость как металлургическое свойство прямо противоположна ударной вязкости, поскольку чем тверже лезвие, тем оно более хрупкое. В то же время незакаленный клинок из отожженной стали очень трудно сломать, но зато не держит заточку. Если производитель полностью закалит лезвие от края до острия, нож с большей вероятностью сломается при рубке или изгибе.
Позвольте мне говорить о «более вероятном» в данном случае. Вы больше подвержены удару молнии или укусу акулы? Как оказалось, вероятность того, что вас ударит молния, примерно в 7,5 раз выше, чем укушенная акулой, но вероятность того, что вас ударит, составляет всего 1 к 500 000. В любом случае, ни то, ни другое маловероятно. Я утверждаю это, потому что, хотя эмпирически верно, что полностью закаленное лезвие «более вероятно» сломается, чем лезвие с мягкой тыльной стороной и закаленной кромкой, если производитель правильно выполняет термообработку и пользователь правильно использует лезвие, либо работают очень хорошо с очень низким риском катастрофического сбоя.
Bennies с мягкой подкладкой
Даже если общий риск поломки при нормальном использовании невелик, все же есть смысл в том, что некоторые производители хотят добиться последней части производительности, используя преимущества прочности лезвия с мягкой подкладкой. Так что же делает лезвие с мягкой подкладкой? Каковы преимущества? Благодаря упрочнению края, но преднамеренному смягчению стержня, лезвие более устойчиво к поломке при воздействии экстремальной силы. Это остается верным независимо от того, прикладывается ли сила к лезвию параллельно, как при рубке, или перпендикулярно, как при сгибании.
Кузнец-подмастерье из ABS и бывший чемпион Forged in Fire Шон Эллис является сторонником лезвия с мягкой оболочкой. Первоначально он изучил процесс упрочнения кромок у мастера ABS Джима Кроуэлла в начале 1990-х годов, когда Джим продемонстрировал упрочнение кромок с помощью ацетиленовой горелки.
Он нагрел только лезвие, закалил лезвие, а затем воспользовался факелом, чтобы вернуть закалку. Чтобы закалить, он начал с факела у позвоночника и использовал мокрую тряпку, чтобы край оставался прохладным. Когда он закончил, край стал светло-бронзовым, а корешок синим.
Несмотря на то, что это было несколько лет назад, метод, которому Кроуэлл научил Эллиса, остается жизнеспособным. Нагрев только кромки оставляет стержень мягким и отожженным, но превращает кромку в отпущенный мартенсит, необходимый для резки. Использование горелки для последующей «синировки» лезвия снимает любые внутренние напряжения, которые могут возникнуть при нагреве только кромки до критической температуры, то есть до немагнитного состояния.
Эллис обнаружил, что нагрев лезвия не менее чем на треть пути от лезвия к обуху приводит к повышению производительности. Впоследствии он перешел на термообработку в кузне, а затем и в печи.
Хотя закалка кромок возможна в кузне или печи, методология меняется. Таким образом, закалка кромок приводит к образованию мартенситной кромки и стержня, сохраняющего прежнюю микроструктуру. Если бы лезвие было выковано и нормализовано, то обух был бы из мягкого перлита. Если бы лезвие было отшлифовано из пруткового проката, стержень был бы из карбида сфероидальной формы.
Еще один способ получить твердую кромку с мягкой тыльной стороной — закалить только кромку. Можно весь клинок прогреть в горне или печи, а затем поместить в масло для закалки только край клинка. Этот метод в настоящее время преподается в школах ABS.
В этом случае вам потребуется достаточное количество масла для надлежащего охлаждения стали, поэтому вы не можете просто заполнить закалочный бак маслом до уровня в полдюйма. Вместо этого используйте ограничительную пластину, чтобы удерживать край на нужной глубине, позволяя баку иметь увеличенный объем масла. Вы качаете лезвие в масле таким образом, чтобы кромка хорошо закалилась, а корень медленно остыл.
Медленное охлаждение стержня приводит к образованию перлитной микроструктуры, а закалка края приводит к образованию мартенсита. В результате снова получается жесткий край и мягкая спина, и снова рекомендуется рисовать «синюю спину». Лезвия с закаленной кромкой устойчивы к поломке, хотя мягкий стержень может гнуться и оставаться согнутым.
Последний способ получить нож с мягкой оболочкой — самый трудный, но он дает наилучшие результаты. В этом методе лезвие полностью закаливается, при этом все лезвие доводится до критической температуры и все лезвие полностью закаливается. После регулярной закалки в печи лезвие проходит закалку на обухе.
В этом сценарии корешок проталкивается от синего до серого, но не до того момента, когда он начинает показывать теплый цвет. По сути, в этом случае вы применяете дифференциальный отпуск, а не дифференциальную закалку, добавляя тепло в диапазоне 650-800 ° F только к стержню, в результате чего получается мартенсит с высоким отпуском. Поскольку вы работаете с более высокими температурами, необходимо проявлять особую осторожность, чтобы край оставался прохладным, оставляя его погруженным в воду или мокрый песок.
Мастер-кузнец ABS Скотт МакГи ведет курс «Введение в кузнечное дело» в муниципальном колледже Хейвуда в Хейвуде, Северная Каролина. Студенты узнают у МакГи, как сделать нож, который пройдет тест производительности ABS, используя полную закалку и вытягивание горелки. Он предпочитает углеродистую сталь 1075 и использует две пропановые горелки, чтобы равномерно вытянуть корешок, сохраняя край прохладным на мокром песке.
КОНСТРУКЦИОННЫЕ РЕЗУЛЬТАТЫ
Я попросил металлурга Ларрина Томаса рассказать о структурных результатах различных подходов к упрочнению кромок. По словам Ларрина, «когда дело доходит до твердости по Роквеллу, отпуск полностью закаленного лезвия в горелке до температуры 650–800 °F приводит к твердости в диапазоне твердости по Роквеллу от 45 до 55 HRC, в зависимости от стали и времени, проведенного при температуре отпуска. . Медленное охлаждение корешка путем закалки кромки приведет к мягкому перлиту, аналогичному воздушному охлаждению при нормализации и измельчении зерна. Это ставит позвоночник в диапазоне от 20 до 40 HRC, в зависимости от стали. Некоторые стали обладают настолько высокой прокаливаемостью, что частично затвердевают при охлаждении на воздухе, например стали для закалки в масле O1 или L6, и могут даже достигать 60 HRC, если поперечное сечение достаточно тонкое.
«Чем мягче обух, тем более устойчиво лезвие к поломке, но тем больше вероятность того, что оно «схватится» при изгибе. Другими словами, потребуется меньшее изгибание более мягкого стержня, чтобы лезвие оставалось постоянно согнутым. Идеальным условием было бы такое, при котором сталь имеет достаточную твердость, чтобы избежать изгиба, но достаточную прочность, при которой она не разрушается. Это сочетание свойств лучше всего достигается за счет полной закалки и отпуска с прокалкой».
На протяжении многих лет сертифицированные кузнецы ABS демонстрировали компетентность в этих процессах. Если вы хотите подняться по лестнице навыков изготовления ножей и сертификатов или если вы хотите подняться по лестнице высокопроизводительных ножей для тяжелых условий эксплуатации, термическая обработка ножа с мягкой спинкой — это навык, которым вы должны овладеть. Если вы относитесь к ножеделу или покупателю ножей, который хочет получить 100% прочности лезвия, не жертвуя режущей кромкой, подумайте о лезвии с мягкой подкладкой.
Читать Подробнее
- Hallmark of the Hamon
- Кована в Fame
- San-Mai: Steel Trinity
Следующий шаг: скачать бесплатный нож.
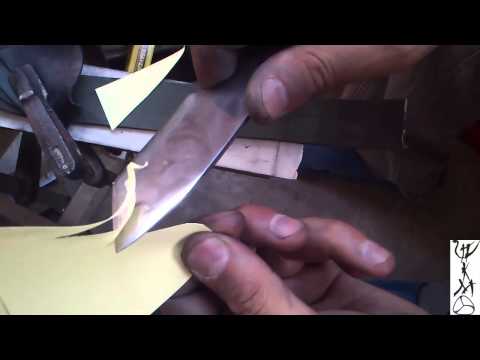