Железо углерод таблица: Диаграмма железо-углерод | ООО КВАДРО
alexxlab | 03.07.1995 | 0 | Разное
Диаграмма состояния железо–углерод – презентация, доклад, проект
Вы можете изучить и скачать доклад-презентацию на тему Диаграмма состояния железо–углерод. Презентация на заданную тему содержит 11 слайдов. Для просмотра воспользуйтесь проигрывателем, если материал оказался полезным для Вас – поделитесь им с друзьями с помощью социальных кнопок и добавьте наш сайт презентаций в закладки!
Презентации» Химия» Диаграмма состояния железо–углерод
Слайды и текст этой презентации
Слайд 1
Описание слайда:
Автономное учреждение профессионального образования Ханты-Мансийского автономного округа – Югры «Сургутский политехнический колледж» Структурное подразделение – 4 Энергетическое отделение
Слайд 2
Описание слайда:
Содержание
Дмитрий Константинович Чернов
Диаграмме состояния железо–углерод
Критическая точка
Фазовый состав сплавов системы
Жидкий расплав
Аустенит
Феррит
Цементит.
Слайд 3
Описание слайда:
Дмитрий Константинович Чернов
Слайд 4
Описание слайда:
Структуры стали и чугуна представлены на диаграмме состояния железо–углерод, т.е. данная диаграмма является основой металловедения. Используя ее, можно определять структуру железоуглеродистых сплавов с любым содержанием углерода при любой заданной температуре. Структуры стали и чугуна представлены на диаграмме состояния железо–углерод, т.е. данная диаграмма является основой металловедения. Используя ее, можно определять структуру железоуглеродистых сплавов с любым содержанием углерода при любой заданной температуре.
Слайд 5
Описание слайда:
По оси абсцисс диаграммы отложено процентное содержание углерода в железе. Нулевое содержание углерода соответствует чистому железу, а 6,67% углерода содержится в химическом соединении железа с углеродом – карбиде железа Fe3C, который называют цементитом. Поэтому диаграмму железо–углерод называют также диаграммой железо–цементит.
По оси абсцисс диаграммы отложено процентное содержание углерода в железе. Нулевое содержание углерода соответствует чистому железу, а 6,67% углерода содержится в химическом соединении железа с углеродом – карбиде железа Fe3C, который называют цементитом. Поэтому диаграмму железо–углерод называют также диаграммой железо–цементит.
Слайд 6
Описание слайда:
Сплошные линии на диаграмме представляют собой геометрическое место критических точек.
Сплошные линии на диаграмме представляют собой геометрическое место критических точек.
Критическая точка – это температура, при которой происходит изменение кристаллической решетки вещества.
Слайд 7
Описание слайда:
Фазовый состав сплавов системы железо–углерод:
Слайд 8
Описание слайда:
Ж – жидкий раствор углерода в железе. При пересечении в процессе охлаждения температуры линии ACD фрагменты жидкого раствора превращаются в зародыши, наиболее устойчивые из них затем развиваются до размера кристаллов.
Ж – жидкий раствор углерода в железе. При пересечении в процессе охлаждения температуры линии ACD фрагменты жидкого раствора превращаются в зародыши, наиболее устойчивые из них затем развиваются до размера кристаллов.
Линию ACD называют линией ликвидуса Процесс выделения кристаллов из жидкости называют первичной кристаллизацией. Выше линии ликвидуса все сплавы находятся только в жидком состоянии.
Линия AECF называется линией солидуса, она характеризует температуру окончания процесса первичной кристаллизации.
Слайд 9
Описание слайда:
[А] – аустенит – твердый раствор Fe(C) внедрения атомов углерода в кристаллическую решетку -железа. В отличие от феррита аустенит немагнитен. Аустенит образуется только при температуре выше 727 °С. [А] – аустенит – твердый раствор Fe(C) внедрения атомов углерода в кристаллическую решетку -железа. В отличие от феррита аустенит немагнитен. Аустенит образуется только при температуре выше 727 °С. Твердость – около 2000 НВ.
Слайд 10
Описание слайда:
[Ф] – феррит сплав с небольшим содержанием углерода, по свойствам наиболее близкий железу. Феррит – твердый раствор Fe(C) внедрения атомов углерода в кристаллическую решетку -железа.
[Ф] – феррит сплав с небольшим содержанием углерода, по свойствам наиболее близкий железу. Феррит – твердый раствор Fe(C) внедрения атомов углерода в кристаллическую решетку -железа.
Слайд 11
Описание слайда:
[Ц] – цементит – химическое соединение с формулой Fe3C, имеет сложную кристаллическую решетку ромбической системы симметрии. Выделяется высокими твердостью и хрупкостью. [Ц] – цементит – химическое соединение с формулой Fe3C, имеет сложную кристаллическую решетку ромбической системы симметрии. Выделяется высокими твердостью и хрупкостью.
Tags Диаграмма состояния железо–углерод
Похожие презентации
Презентация успешно отправлена!
Ошибка! Введите корректный Email!
Сплавы на основе железа. Диаграмма состояния сплавов системы железо–углерод. Лекция 2. Тема 4
1. Модуль 2 сплавы на основе железа ТЕМА 4.
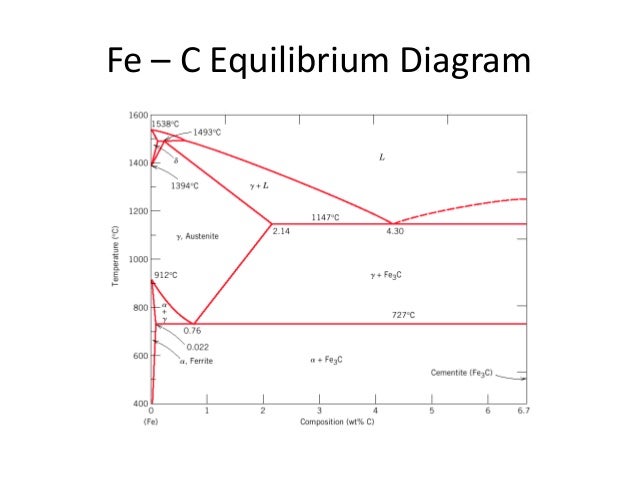
СПЛАВЫ НА ОСНОВЕ ЖЕЛЕЗА
ТЕМА 4.
ДИАГРАММА СОСТОЯНИЯ СПЛАВОВ
СИСТЕМЫ ЖЕЛЕЗО–УГЛЕРОД
Рис.1. Диаграмма состояния сплавов системы железо–углерод
Компоненты сплава
Железо. Чистое железо – серебристо-светлый
металл, имеющий температуру плавления 1539 ºС.
Обладает невысокой твердостью и прочностью и
хорошей пластичностью. Железо имеет несколько
аллотропических форм, а именно: α-железо с
объемно-центрированной кубической решеткой и γжелезо с гранецентрированной кубической решеткой.
Цементит.
Цементит
–
это
химическое
соединение железа с углеродом – карбид железа Fe3C.
В цементите содержится 6,67 % углерода. Цементит
имеет сложную ромбическую решетку с плотной
упаковкой атомов. Он обладает высокой твердостью
(HV1000) и очень малой пластичностью.
В системе существуют следующие фазы:
1. Жидкость (L) – (жидкий раствор углерода в
железе), существующая выше линии ликвидус.

2. Цементит Fe3C (Ц) – линия DFKL;
3. Феррит (Ф) – твердый раствор углерода в αжелезе. Область феррита в системе железо – углерод
расположена левее линий GPQ и AHN;
4. Аустенит (А) – твердый раствор углерода в γжелезе. Область аустенита на диаграмме – NJESG.
В системе протекают три нонвариантные реакции:
1. При 1499 ºС (линия HJB) протекает перитектическая
реакция:
LB + ФН → АJ.
В результате перитектической реакции образуется
аустенит.
2. При 1147 ºС (горизонталь ECF) протекает
эвтектическая реакция:
LC → AE + Ц.
В результате этой реакции образуется эвтектическая смесь
аустенита и цементита, которая называется ледебуритом.
3. При 727 ºС (горизонталь PSK) протекает эвтектоидная
реакция:
AS → ФP + Ц.
Продуктом превращения является эвтектоидная смесь.
феррита и цементита, которая называется перлитом.
ТЕМА 6. УГЛЕРОДИСТЫЕ СТАЛИ
Железоуглеродистые сплавы, содержащие углерода
от 0,02 до 2,14 %, называются сталями.

равновесном
состоянии
стали
делятся
на
доэвтектоидные, эвтектоидные и заэвтектоидные.
Сплавы железа с углеродом, содержащие углерода
до 0,02 %, называют технически чистым железом.
Железоуглеродистые сплавы с содержанием
углерода от 2,14 % до 6, 67 % называются чугунами. По
структуре в равновесном состоянии чугуны делятся на
доэвтектические, эвтектические и заэвтектические.
Рис. 2. Микроструктура доэвтектоидной стали
(0,2 % С), × 200
Рис. 3. Микроструктура эвтектоидной стали
(перлит пластинчатый), × 2000
Рис. 4. Микроструктура заэвтектоидной стали
(1,2 % С), × 200
5.1. Влияние углерода и постоянных
примесей на свойства сталей
С увеличением содержания углерода в
углеродистых
сталях,
находящихся
в
равновесном
состоянии,
меняются
их
структура и фазовый состав: уменьшается
количество
феррита
(НВ
80…100),
увеличивается количество цементита (НВ 800).

В соответствии с этим в сталях возрастают
твердость
НВ,
предел
прочности
σв,
уменьшаются пластичность δ и ударная
вязкость KSU.
Марганец и кремний – полезные примеси,
повышают прочность сталей. Попадают в сталь при
ее раскислении. Углеродистые стали содержат около
0,8 % Mn и 0,5 % Si.
Сера и фосфор – вредные примеси. Они
попадают в сталь с исходным сырьем.
Содержание серы в сталях допускают не более
0,05 %, большее ее количество придает сплавам
красноломкость.
Содержание фосфора в углеродистой стали
допускается до 0,05 %, большее его количество
повышает хладноломкость сплавов.
Азот (N2), кислород (О2) и водород (Н2) –
вредные примеси. Повышают хрупкость сталей.
5.2. Классификация углеродистых
сталей
Углеродистые стали классифицируют по
содержанию углерода, назначению, качеству,
степени раскисления и структуре в
равновесном состоянии.
По
содержанию
углерода
стали
подразделяются на:
1.
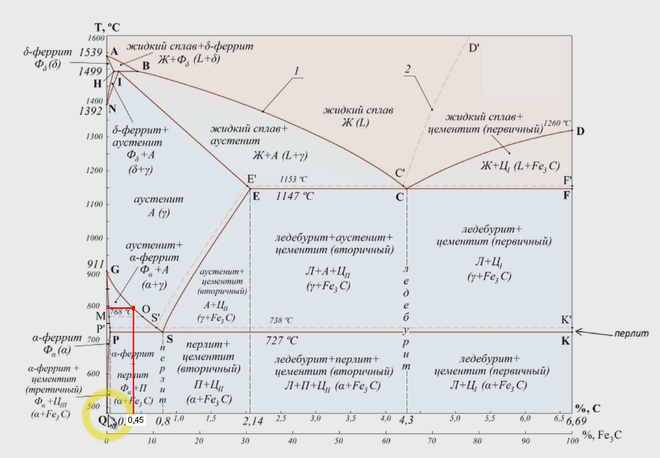
2. Среднеуглеродистые (0,3…0,7 % С)
3. Высокоуглеродистые (С > 0,7 %).
По назначению стали классифицируют на:
1. Конструкционные
2. Инструментальные.
Конструкционные стали предназначены для
изготовления строительных сооружений, деталей
машин и приборов. К этим сталям относят
цементуемые, улучшаемые, высокопрочные и
рессорно-пружинные.
Инструментальные стали подразделяют на стали
для режущего, измерительного инструмента,
штампов холодного и горячего деформирования.
По качеству стали подразделяют на:
1. Стали обыкновенного качества (до 0,06 % S и
0,07 % P)
2. Стали качественные (не более 0,04 % S и 0,035
% P)
3. Стали высококачественные (не более 0,025 % S
и 0,025 % P)
Стали обыкновенного качества бывают только
углеродистыми (до 0,5 % С), качественные и
высококачественные
–
углеродистыми
и
легированными.
По
степени
классифицируют на:
раскисления
стали
1.
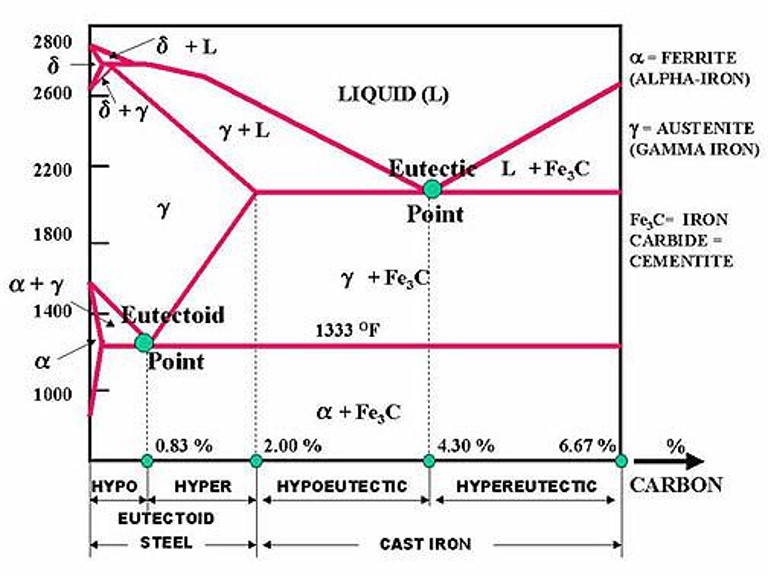
2. Полуспокойные стали
3. Кипящие стали
Раскисление – процесс удаления из жидкого
металла кислорода и оксидов, проводимый с
целью предотвращения хрупкого разрушения
стали при горячей деформации.
5.3. Углеродистые стали
обыкновенного качества
Стали обыкновенного качества выпускают в виде
проката (прутки, балки, листы, уголки, швеллеры и т.п.) в
нормализованном состоянии и в зависимости от
назначения и комплекса свойств подразделяют на группы:
А, Б, В.
Группа А – это стали, поставляемые по механическим
свойствам без уточнения их химического состава. Их
обозначают
буквами
Ст
(сталь)
и
цифрами,
обозначающими порядковый номер стали, – 0, 1, 2, 3,…, 6
(то есть Ст0, Ст1, Ст2,…, Ст6). Чем больше цифра, тем
больше содержание углерода, и, следовательно, выше
прочность и ниже пластичность.
Группа Б – это стали, поставляемые с гарантируемым
химическим составом, в обозначении марки сталей впереди
ставится буква Б– БСт0, БСт1,…, БСт6.
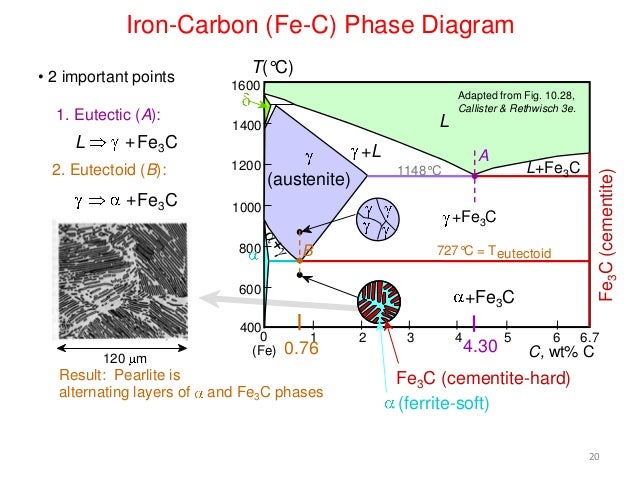
при этом не гарантируются.
Стали этой группы применяют для изделий,
изготавливаемых с применением горячей обработки. Для
таких сталей важны сведения о химическом составе,
необходимые для определения режима горячей обработки.
Группа В – это стали повышенного качества. Их
поставляют с гарантированными химическим составом и
механическими свойствами. В обозначение марки вводится
буква В (ВСт1,…, ВСт5). Стали группы В дороже, чем стали
групп А и Б, их применяют для ответственных деталей (для
производства сварных конструкций).
При маркировке сталей обыкновенного
качества степень раскисления обозначается
добавлением индексов: в спокойных сталях –
“сп”, полуспокойных – «пс», кипящих – «кп»,
например, Ст3сп, БСт3пс или ВСт4кп. Спокойными
и полуспокойными производят стали Ст1-Ст6,
кипящими – Ст1-Ст4 всех групп. Сталь Ст0 по
степени раскисления не разделяют.
5.4. Углеродистые качественные стали
Маркируют
эти
стали
(ГОСТ
1050-88)
двузначными цифрами 05, 08, 10, 15, 20, …, 75, 80,
85, обозначающими среднее содержание углерода в
сотых долях процента.

Например, сталь 20 содержит в среднем 0,20 % С,
сталь 70 – 0,70 % С и т.д.
ТЕМА 6. ЧУГУНЫ
Чугуны – более дешевый материал, чем стали.
Содержание углерода в них больше 2,14 %. Они
обладают пониженной температурой плавления и
хорошими литейными свойствами. За счет этого из
чугунов можно делать отливки более сложной
формы, чем из сталей.
В зависимости от того, в каком виде и форме
присутствует углерод в сплавах, различают белые,
серые, высокопрочные и ковкие чугуны.
6.1. Белые чугуны
Весь углерод в этом чугуне находится в
связанном состоянии в виде цементита.
Эти чугуны имеют большую твердость (НВ
450…550) из-за присутствия в них большого
количества цементита; они очень хрупкие и для
изготовления деталей машин не используются.
Отливки из белого чугуна служат для получения
с помощью графитизирующего отжига деталей из
ковкого чугуна.
6.2. Серые чугуны
В структуре серого чугуна практически весь
углерод находится в свободном состоянии – в
виде графита.

включения имеют форму пластин.
По структуре металлической основы серые
чугуны разделяют на три вида.
1. Серый перлитный со структурой перлит +
графит.
2. Серый феррито-перлитный со структурой
феррит + перлит + графит.
3. Серый ферритный со структурой феррит +
графит.
Рис. 5. Микроструктура серого перлитного чугуна
Таблица 1
Механические свойства серых чугунов
Чугун
σв ,
МПа
НВ
СЧ 15
СЧ 25
150 163…229
250 180…250
СЧ 40
СЧ 45
400 207…285
450 229…289
Структура
металлической
основы
Феррит
Феррит +
перлит
Перлит
Перлит
Из серых чугунов изготавливают блоки
цилиндров, картеры, маховики и др.
В
автотракторостроении
и
сельскохозяйственном машиностроении часто
применяют следующие марки серых чугунов:
СЧ18, СЧ20, СЧ25 (немодифицированные) и CЧ30 и
СЧ35 (модифицированные).
6.3. Высокопрочные чугуны
Высокопрочными называют чугуны, в которых
графит имеет шаровидную форму.
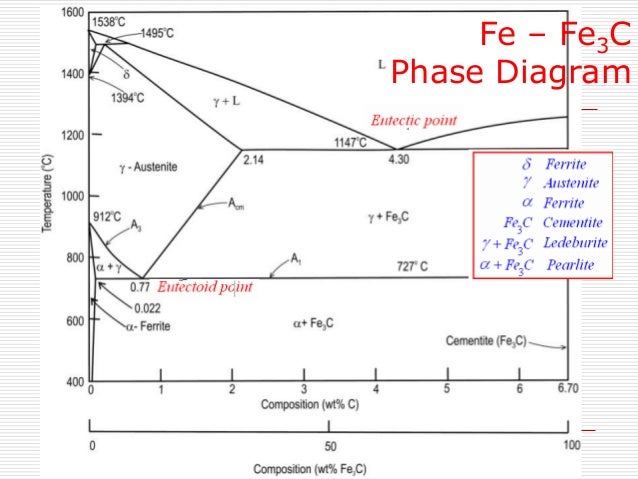
Высокопрочные
чугуны
получают
модифицированием жидкого чугуна небольшими
добавками магния.
Маркируют высокопрочный чугун буквами ВЧ, затем
следуют цифры, которые показывают среднее значение
временного сопротивления при растяжении – σв
(кгс/мм2).
Высокопрочный чугун – хороший заменитель литой
стали (применяется для изготовления коленчатых и
распределительных
валов,
гильз
цилиндров,
автомобильных двигателей).
Рис. 6. Микроструктура феррито-перлитного
высокопрочного чугуна
6.4. Ковкие чугуны
Ковкими называют чугуны, в которых графит имеет
хлопьевидную форму. Их получают в результате
специального графитизирующего отжига отливок
белого доэвтектического чугуна.
Ковкий чугун маркируют буквами КЧ и цифрами.
Первые цифры марки показывают среднее значение
временного сопротивления при растяжении – σв
(кгс/мм2), вторые – относительное удлинение – δ (%).
В автотранспортном и сельскохозяйственном
машиностроении применяют ковкие чугуны марок
КЧ37-12, КЧ35-10, КЧ50-4.

картеры редукторов, рулевых механизмов, ступицы
колес, педали и др.
Таблица 2
Механические свойства ковких чугунов
Чугун
КЧ 30-6
КЧ 37-12
КЧ 60-3
КЧ 80-1,5
σв, δ,
МПа %
НВ
300 6 100…163
370 12 110…163
600 3 200…269
800 1,5 270…320
Структура
металличес
кой основы
феррит
феррит
перлит
перлит
Рис. 7. Микроструктура ферритного ковкого чугуна
Carbon Steels and the Iron-Carbon Phase Diagram – IspatGuru
Carbon Steels and the Iron-Carbon Phase Diagram
- satyendra
- March 6, 2016
- 1 Comment
- austenite, carbon steel, cementite, охлаждение, феррит, нагрев, диаграмма железо-углерод, микроструктура, перлит, сталь,
Углеродистые стали и фазовая диаграмма железо-углерод
Стали представляют собой сплавы, содержащие элементы железа (Fe) и углерода (C). C растворяется в Fe при производстве сталей. Чистое Fe плавится при температуре 1540°C, и при этой температуре C легко растворяется в жидком железе, образуя жидкий раствор. Когда этот жидкий раствор затвердевает, он образует твердый раствор, в котором атомы C растворяются в твердом железе. Отдельные атомы С располагаются в пустотах между атомами Fe кристаллических зерен аустенита (при высоких температурах) или феррита (при низких температурах). Аустенит имеет гранецентрированную кубическую (ГЦК) структуру, тогда как феррит имеет объемноцентрированную кубическую (ОЦК) структуру (рис. 1). Если количество С, растворенного в жидком чугуне, поддерживается ниже 2,1 %, продукт представляет собой сталь, а если выше этого значения, то продукт представляет собой чугун. Хотя жидкое железо может растворять углерод при содержании значительно выше 2,1 % углерода, твердое железо не может. Это приводит к другой твердой структуре чугуна (железо с общим содержанием углерода более 2,1 %).
Помимо C, все типы сталей содержат элемент марганец (Mn) и небольшое количество примесных атомов фосфора (P) и серы (S). Следовательно, стали можно рассматривать как сплавы трех и более элементов. Этими элементами являются Fe, C, добавки других элементов/элементов и примеси. Обычно состав стали подразделяют на две категории, а именно (i) простые стали C и (ii) легированные стали. В простых углеродистых сталях другие элементы состоят только из Mn, P и S, тогда как в легированных сталях добавляются один или несколько дополнительных легирующих элементов.
Твердые растворы аналогичны жидким растворам; то есть после того, как твердое вещество растворилось, его присутствие больше не очевидно для наблюдателя, как это было до его растворения (рис. 1). Атомы C помещаются в отверстия, которые существуют между атомами Fe гранецентрированного кубического (ГЦК) аустенита, присутствующего при этой температуре. Этот твердый раствор C в Fe представляет собой углеродистую сталь. На рис. 1 показаны центры атомов Fe в ГЦК-решетке. Если позволить каждой из маленьких сплошных точек расшириться, пока они не соприкоснутся друг с другом, в результате получится модель ГЦК-железа, как показано на рис. 1 (справа). Расширенные атомы Fe соприкасаются друг с другом по диагоналям граней куба. Маленькие открытые кружки определяют центр пустот между атомами железа. Если эти кружочки расширить до соприкосновения с атомами железа, то их максимальный диаметр будет равен 41,4 % от диаметра атома Fe. Это означает, что атомы размером менее примерно 42 % от диаметра атома Fe могут поместиться в отверстия между атомами Fe. Атомы С малы, но диаметр атомов С оценивается в 56 % от диаметра атомов Fe в аустените. Следовательно, когда C растворяется в железе, он немного раздвигает атомы Fe. Чем больше C растворяется, тем дальше раздвигаются атомы Fe. Таким образом, существует предел тому, сколько C может быть растворено в железе.
Рис. 1 Структура железа и растворение углерода в гранецентрированном кубическом железе
В чистом железе разница между ферритом и аустенитом заключается в разнице их атомных структур. Атомы Fe имеют объемно-центрированную кубическую (ОЦК) кристаллическую структуру в феррите и ГЦК-кристаллическую структуру в аустените. Как в зернах феррита, так и в зернах аустенита эта атомная структура внутри зерна не изменяется. И феррит, и аустенит являются отдельными фазами. Когда C добавляется к аустениту для образования твердого раствора, твердый раствор имеет ту же самую ГЦК кристаллическую структуру, что и чистое железо. C от графита (рис. 1) как раз помещается между атомами железа. Кристаллическая структура остается ГЦК, единственное изменение заключается в том, что атомы Fe раздвинуты очень немного дальше друг от друга. И чистый аустенит, и аустенит с растворенным в нем С являются одной и той же фазой. Таким образом, аустенит (с растворенным в нем углеродом) и феррит (с растворенным в нем углеродом) — это две разные фазы, каждая из которых представляет собой сталь.
Низкоуглеродистые стали – гипоэвтектоидные стали
На фазовой диаграмме Fe-C представлена карта температурно-составного состава двух фаз (аустенита и феррита). Он также указывает, где можно ожидать смеси этих двух фаз. Фазовая диаграмма Fe-C представлена на рис. 2. В чистом железе аустенит превращается в феррит при охлаждении до 912°C.
Эту температуру перехода традиционно называют температурой A3, и диаграмма показывает, что добавление C к Fe Температура А3. В то время как максимальное снижение происходит в так называемой эвтектоидной точке, которая также известна как перлитная точка. Эвтектоидная точка представляет собой температуру и состав на фазовой диаграмме, при которых происходит эвтектоидная реакция, то есть реакция, при которой одно твердое вещество превращается в два твердых вещества. Эвтектоидная точка в системе Fe-C имеет состав около 0,76 % C, а стали с составом меньше этого значения называются доэвтектоидными сталями. Эвтектоидную температуру традиционно называют температурой А1. 9Рис. 2. Диаграмма состояния железа и углерода координаты в узкой области в левом нижнем углу фазовой диаграммы Fe-C. Максимальное количество С, которое растворяется в ферритном железе, составляет всего 0,022 %. Это происходит при эвтектоидной температуре 727°С. Это означает, что феррит по существу является чистым железом, потому что он всегда 99,978 % или чище по углероду. Однако видно, что аустенит может растворять гораздо больше углерода, чем феррит. При эвтектоидной температуре аустенит растворяет около 0,76 % С, что примерно в 38 раз больше С, чем феррит может удерживать при этой температуре. Аустенит содержит больше углерода, чем феррит, поскольку дырки между атомами железа в ГЦК-структуре больше, чем в ОЦК-структуре.
Центральная область в левой части фазовой диаграммы Fe-C отображает точки температура-состав, в которых сталь состоит из смеси феррита и аустенита. Предположим, что микроскоп с горячим столиком используется для изучения полированной стали с содержанием углерода 0,4 % после ее нагрева до 760°С. Поскольку эта точка температурного состава находится в центральной области, сталь должна представлять собой смесь феррита и аустенит, два примера которого показаны в левой части фазовой диаграммы Fe-C.
Часть фазовой диаграммы в доэвтектоидной области показана на рис. 3. Она дает информацию о составе двух фаз. Аустенитные зерна имеют состав, указанный как N , а состав феррита, указанный как M на рис. 3.
В качестве еще одного примера полезности фазовой диаграммы можно рассмотреть простой эксперимент. Сталь состава 0,4 % С сначала нагревают до 850°С и выдерживают примерно 10 минут. После такой кратковременной выдержки все зерна в этой стали будут состоять из зерен чистого аустенита (структура ГЦК) с содержанием углерода 0,4 %. и видя область всего из трех зерен, как показано на рис.3. Теперь температура горячей стадии снижена до 760°С, и образец медленно охлаждается до этой температуры. При охлаждении происходит изменение микроструктуры. Согласно фазовой диаграмме, сталь после охлаждения становится двухфазной, смесью аустенита и феррита. Эксперименты показывают, что феррит, образующийся в чистом аустените при его охлаждении, практически всегда образуется на границах аустенитных зерен. Это показано в микроструктуре на рис. 3 (справа), где феррит сформировался в виде ряда альфа-зерен вдоль границ предшествующих аустенитных зерен.
Рис. 3 Часть фазовой диаграммы в доэвтектоидной области
Сравнение этой микроструктуры на рис. 3 с микроструктурой в нижней части рис. 3 (слева) показывает сходства и различия. Они похожи тем, что оба содержат смесь ферритных и аустенитных зерен с одинаковой объемной долей каждого из них, но отличаются тем, что распределение ферритных зерен совершенно различно. Микроструктура в нижней части рис. 3 (слева) обычно формируется при нагреве стали от комнатной температуры до 760°С. Этот пример объясняет один из интересных аспектов сталей, заключающийся в том, что микроструктуру можно контролировать с помощью термической обработки, и она Известно, что механические свойства сталей контролируются микроструктурой. Микроструктура стали обычно относится к определенной форме, размеру, распределению и типам фаз зерен в стали.
Высокоуглеродистые стали – заэвтектоидные стали
По мере увеличения % C, растворенного в аустените, атомы железа раздвигаются дальше друг от друга. Это растягивает химические связи, которые удерживают атомы железа вместе, создавая форму энергии, называемую энергией деформации. Существует предел тому, какую энергию деформации может выдержать аустенит. Количество С, растворенного в аустените при достижении этого предела, называется пределом растворимости. Предел растворимости в аустените при 820°С составляет 1% С. Если сплав, содержащий 1,6% С, нагреть до 820°С, только 1% из этих 1,6% С растворится в аустените. Оставшиеся 0,6 % C включаются в новую фазу, называемую цементитом. Эта новая фаза, цементит, имеет одно существенное отличие от аустенита или феррита. Это химическое соединение, которое существует только в одном составе. Формула химического элемента для цементита – Fe3C. На каждый атом C в соединении приходится три атома Fe, что дает атомный состав 25 атомных % C. Соответствующий весовой процент C в цементите составляет 6,7 %.
Помимо ограничения одним составом, цементит имеет несколько сходств с аустенитом и ферритом. Это кристалл, атомы которого расположены в регулярно повторяющихся геометрических рядах. Кристаллическая структура немного сложнее, чем ОЦК феррита или ГЦК аустенита, и она хорошо известна. Кроме того, это отдельная фаза и присутствует в виде дискретных зерен. Так, весь избыток 0,6 % С в этом примере при 820 град С присутствует в виде отдельных зерен цементита вперемешку с зернами аустенита, то есть микроструктура представляет собой двухфазную смесь аустенита и цементита.
Часть фазовой диаграммы Fe-C, расширенная до более высоких составов C, где цементит становится важным, показана на рис. 4. Область на карте температура-состав, соответствующая аустениту, показана как центральная темная область. Поскольку цементит существует только в одном составе, он показан на фазовой диаграмме в виде вертикальной линии, расположенной на его составе, 6,7 % С. Можно видеть, что ось состава в нижней части диаграммы имеет излом сразу после 1,2. %, а значение 6,7 % расположено рядом с изломом. Если бы разрыв не был вставлен, состав 6,7 % появился бы примерно на 300 мм вправо. Чтобы представить настоящую диаграмму, можно представить, что правая часть расширяется примерно на 300 мм, что расширяет отмеченную заштрихованную двухфазную область на гораздо большую площадь.
Рис. 4 Часть фазовой диаграммы Fe-C в заэвтектоидной области
Линия на диаграмме с названием «Acm» определяет предел растворимости C в аустените. Видно, что при 820°С эта линия дает точку при 1 % С, что является максимальным количеством С, которое может быть растворено в аустените при 820°С. Сплавы с процентным составом С справа от линии Acm находятся в заштрихованной двухфазной области и состоят из смеси зерен аустенита и цементита. Например, сталь с 0,95 % С нагревают до 760°С, точка температура-состав будет находиться в незаштрихованном кружке на рис. 4, через который проходит горизонтальная линия со стрелкой. Поскольку точка температура-состав находится в заштрихованной двухфазной области, эта сталь состоит из смеси аустенита состава О (0,85 % С) и цементита состава Р (6,7 % С). Диаграмма не описывает, как будет выглядеть микроструктура. Тем не менее, эксперименты показывают, что микроструктура будет такой, как показано в нижней части рис. 4. Весь цементит представлен в виде мелких зерен сферической формы, довольно беспорядочно распределенных по аустенитным зернам, которые имеют гораздо большие размеры и типичные изогнутые границы зерен.
Чтобы дополнительно продемонстрировать использование фазовой диаграммы для понимания того, как изменяется микроструктура во время термообработки, можно рассмотреть эксперимент, в котором сталь с 0,95 % C нагревают до 850 ° C и выдерживают в течение 20 минут или около того. Как показано на фазовой диаграмме на рис. 4, эта точка температура-состав соответствует однофазной аустенитной области. Если предположить, что структуру можно наблюдать в микроскоп с подогревом столика, то небольшая область, наблюдаемая при большом увеличении, может состоять всего из трех зерен, что будет иметь вид, подобный показанному на рис. 4.9.0021
Если температуру горячей ступени понизить до 760 град С, то эта температурно-составная точка лежит в двухфазной области аустенит-цементит, а значит, при охлаждении должны образовываться зерна цементита. Как и в случае доэвтектоидной стали на рис. 3, где феррит образуется на границах аустенитных зерен во время охлаждения, здесь во время охлаждения на границах аустенитных зерен образуется цементит. Как показано на рис. 4, окончательная микроструктура имеет все прежние границы аустенитных зерен из структуры при 850°C, заполненные тонкими пластинчатыми зернами цементита. Отличие микроструктуры от показанной на рис. 4 (внизу слева), где сталь с 0,95 % С нагревали непосредственно от комнатной температуры до 760°С. Обе микроструктуры содержат одинаковую объемную долю цементита и аустенита, но распределение цементита совершенно различно. В отличие от аустенита и феррита цементит очень хрупок. Следовательно, структура стали 0f 0,95 % C на рис. 4 с ее соединенными между собой цементитными пластинами не такая прочная, как структура на рис. 4 (нижняя левая сторона) с ее мелкими изолированными зернами цементита. Опять же, это пример того, как термическая обработка может изменить микроструктуру, что, в свою очередь, изменяет механические свойства.
Эвтектоидная сталь – перлит
Стали с содержанием углерода около 0,76 % образуют уникальную микроструктуру, называемую перлитом. На рис. 5 представлена фазовая диаграмма Fe-C, на которой область ниже линии A1, равная 727°C, заштрихована темным цветом. Вся эта область представляет собой двухфазную область. Стали, медленно охлаждаемые до температурных координат этой области, состоят из смеси двух фаз, феррита и цементита. Микроструктуры сталей в этой двухфазной области сильно различаются, и перлит является лишь одной из многих микроструктур, которые могут встречаться.
Чтобы понять перлитную микроструктуру, сталь, имеющую С около 0,76 %, нагревают в микроскопе с горячим столиком до 800°С. Как показано на рис. 5, сталь состоит из всех аустенитных зерен всего через одну или две минуты при температуре 800°. C. После охлаждения до температуры ниже А1 и выдержки от 5 до 10 минут или около того аустенитные зерна полностью замещаются новым набором перлитных зерен, как показано на рисунке. В отличие от всех структур зерен, описанных до сих пор, зерна перлита не являются одной фазой. Скорее, они состоят из смеси двух фаз, феррита и цементита, имеющих уникальную микроструктуру. Чтобы увидеть истинные детали микроструктуры, можно рассмотреть небольшую область внутри зерна перлита при очень большом увеличении, как показано на рис. 5 (слева). Структура состоит из чередующихся пластин феррита и цементита. Ферритовые пластины намного толще цементитных и занимают 90 % объема по сравнению с 10 % для цементита. На границах зерен перлита происходит резкое изменение ориентации пластин, как это показано для реального образца на рис. 5 (справа). Эта микроструктура получена с помощью просвечивающего электронного микроскопа при увеличении в 11 000 раз.
Рис. 5 Часть диаграммы Fe-c в эвтектоидной точке и изображение перлита
На этом электронно-микроскопическом изображении пластины цементита представляют собой светлую фазу, а пластины феррита – темную фазу. Цементитные пластины имеют толщину всего 0,1 микрометра и слишком тонкие, чтобы их можно было рассмотреть в оптический микроскоп. Хотя цементит является хрупким, перлит – нет, в основном из-за мелкого размера цементитных пластин. Если теперь эту сталь охладить от температуры 700°C до комнатной температуры, микроструктура существенно не изменится, независимо от того, насколько медленно или быстро сталь охлаждается. Феррит остается почти чистым ОЦК-железом с растворенным в нем менее 0,02 % С, а цементит остается с 6,7 % С с неизменной кристаллической структурой.
Согласно фазовой диаграмме, при охлаждении аустенита ниже температуры А1 и кратковременной выдержке аустенит полностью замещается какой-либо формой феррито-цементита, а при охлаждении до комнатной температуры никаких дальнейших изменений в образующемся феррите не происходит. -происходит цементитная микроструктура. Аустенит никогда не встречается в простых углеродистых сталях при комнатной температуре. Исключением из этого правила являются закаленные стали с высоким содержанием углерода, которые содержат смеси мартенсита и остаточного аустенита. Это означает, что микроструктуры, содержащие аустенит, можно увидеть только в микроскоп с горячим предметным столиком, поскольку при охлаждении аустенит заменяется другими структурами. При высоких скоростях охлаждения (например, при закалке в воде и масле) к ним относятся мартенситная и бейнитная структуры. При скоростях охлаждения на воздухе и медленнее (например, при охлаждении в печи) аустенит превращается в некоторую форму ферритоцемента.
Номенклатура A1, Ae1, Ac1 и Ar1
Фазовая диаграмма Fe-C, показанная на рис. 2, называется равновесной фазовой диаграммой. Это означает, что температуры превращения, указанные линиями «А», были определены при чрезвычайно низких скоростях охлаждения или нагревания, при которых достигаются равновесные условия. Линии A3, Acm и A1, которые появляются на равновесных фазовых диаграммах, часто изображаются как линии Ae3, Aecm и Ae1 соответственно, где буква «e» указывает на условия равновесия. Отсутствие буквы «е» подразумевает условия равновесия.
Рассмотрим снова процесс, объясненный для понимания микроструктуры перлита. Диаграмма на рис. 5 показывает, что при охлаждении аустенитных зерен примерно до 727°С из аустенита начинает формироваться перлит. Это происходит только в том случае, если аустенит охлаждается очень медленно. Даже при небольших скоростях охлаждения, таких как 3°С в минуту, температура превращения снижается примерно на 20°С. Это означает, что фазовую диаграмму Fe-C можно использовать только в качестве приблизительного ориентира для оценки температур превращения. Мало того, что превращение аустенита в перлит при охлаждении смещается вниз по температуре, обратное превращение перлита в аустенит при нагревании смещается вверх по температуре. Величину этого сдвига при охлаждении и нагревании можно продемонстрировать на простом опыте.
Французский ученый Флорис Осмонд, ответственный за название мартенсита, также несет ответственность за использование букв «r» и «c» для сдвига линий «A» при охлаждении и нагреве. В конце 19 века он был первым ученым, который использовал термопары для измерения влияния скорости нагрева и охлаждения. Буква «r» происходит от французского слова «охлаждение», «refroidissement», а буква «с» происходит от французского слова «обогрев», «шофаж».
В «чистом железе», когда аустенит превращается в феррит при охлаждении, выделяется тепло, а когда феррит превращается в аустенит при нагревании, тепло поглощается. Линии A3 и A1 диаграммы чистого Fe-C смещены вниз по температуре из-за марганца (Mn) и кремния (Si), присутствующих в типичной стали, имеющей состав C-0,18 %, Mn-0,75 % и Si. – 0,2 % к значениям А1 как 725°С и А3 как 824°С. Данные нагрева показывают, что около 737°С скорость повышения температуры резко снижается. Это происходит из-за тепла, поглощаемого образцом, когда перлитная часть стали превращается в аустенит. Это означает, что линия А1 сместилась вверх на 12°С, с 725°С до 737°С. Фактическую температуру превращения при нагреве принято обозначать как Ас1. Величина сдвига вверх зависит от скорости нагрева. Если скорость нагрева увеличивается выше значения 40 град С в минуту, значение Ac1 увеличивается.
При охлаждении происходит обратный эффект. Тепло, выделяющееся в типичной стали с составом C-0,18 %, Mn-0,75 % и Si-0,2 % при превращении аустенита в феррит или перлит, замедляет скорость снижения. Этот эффект виден как для превращения аустенита в феррит ниже температуры A3, так и для превращения аустенита в перлит ниже температуры A1. Первое превращение начинается при 762 °С, что на 62 °С ниже температуры А3, равной 824 °С, а второе происходит при 652 °С, что на 73 °С ниже температуры А1, равной 725 °С. чтобы отметить фактические температуры превращения, которые происходят при охлаждении, как температуры Ar3 и Ar1. Видно, что скорость охлаждения, показанная на рис. 6, в три раза больше скорости нагрева. Эта более высокая скорость объясняет повышенный сдвиг температуры А1 от -73°С при охлаждении до всего лишь +12°С при нагревании. Температурный диапазон на рис. 6 не расширен настолько, чтобы можно было измерить повышенную температуру A3, которая называется температурой Ac3. 9Рис. 6. Сдвиг линий «А» при нагреве и охлаждении стали с добавлением нижнего индекса «с» и смещением вниз при охлаждении, с маркировкой добавленным индексом «r». Эти сдвиги температур превращения могут стать важными в производственных операциях, связанных с быстрым нагревом и охлаждением. Примером может служить сдвиг температуры превращения вверх при нагреве в таких процессах, как пламенная и индукционная закалка.
Диаграмма равновесия железа и углерода | Металлургия
ОБЪЯВЛЕНИЯ:
В этой статье мы обсудим: 1. Введение в диаграмму равновесия железо-углерод 2. Фазы в диаграмме Fe-Fe 3 C 3. Критические температуры 4. Превращения и микроструктуры медленно охлаждаемых сталей 5. Методы, используемые для Различие между свободным ферритом и свободным цементитом 6.
Комплектация:
- Знакомство с Fe-Fe 3 C Диаграмма равновесия
- Фазы в Fe-Fe 3 C Диаграмма
- Критические температуры в Fe-Fe 3 C Диаграмма равновесия
- Превращения и микроструктуры медленно охлаждаемых сталей в Fe-Fe 3 C Диаграмма равновесия
- Методы, используемые для различения свободного феррита и свободного цементита в Fe-Fe 3 C Диаграмма равновесия
- Ограничения Fe-Fe 3 C Диаграмма равновесия
1. Знакомство с Fe-Fe 3 C Диаграмма равновесия:
ОБЪЯВЛЕНИЯ:
Углерод является наиболее важным легирующим элементом железа, который существенно влияет на аллотропию, структуру и свойства железа. Таким образом, изучение системы Fe-C важно еще и потому, что она составляет основу промышленных сталей и чугунов, и многие из основных особенностей этой системы влияют на поведение даже самых сложных легированных сталей.
Способность интерпретировать эту диаграмму важна для правильной оценки фазовых изменений. Диаграмма Fe-C на самом деле обеспечивает ценную основу для построения знаний о большом разнообразии как простых углеродистых, так и легированных сталей.
Железо образует соединение с углеродом, называемое цементитом, когда содержание углерода превышает пределы растворимости железа. Хотя углерод в виде графита должен из-за того, что он имеет меньшую свободную энергию, чем цементит, тем не менее цементит образуется, потому что образование цементита более вероятно кинетически, т. образуют цементит, тогда как для зародышеобразования графита требуется 100% сегрегация углерода.
ОБЪЯВЛЕНИЙ:
Цементит, химическая формула Fe3C, имеет фиксированное содержание углерода 6,67 %, т. е. когда железо имеет 6,67 % углерода, то получается 100 % цементит. Таким образом, эту диаграмму (см. самую нижнюю горизонтальную линию на рис. 1.22), в которой есть компоненты железа и цементита (100 % Fe на одном конце и 100 % цементита на другом конце диаграммы), можно по праву назвать диаграммой железо-цементит.
Диаграмма железо-цементит не является истинной диаграммой равновесия, поскольку равновесие означает отсутствие изменения фазы во времени, каким бы продолжительным оно ни было. Графит является более стабильной формой углерода. Цементит представляет собой метастабильную фазу, которая при длительном воздействии распадается на графит. Графитизация, однако, редко происходит в сталях и может занять годы. Таким образом, цементит, хотя и является метастабильной фазой, можно считать практически стабильным.
Таким образом, диаграмма Fe – Fe 3 C, хотя и представляет метастабильные условия, можно предположить, что она представляет состояние равновесия, имеющее отношение к поведению большинства сталей на практике. В чугунах высокое содержание углерода и высокие добавки кремния способствуют образованию графита, и, таким образом, в чугунах (за исключением белого чугуна) превращения в большей степени основаны на диаграмме Fe-графит. Диаграмма Fe-C строго справедлива только при одном атмосферном давлении. Условно композиции указаны в весовых %.
РЕКЛАМА:
2. Фазы в Fe-Fe 3 C Диаграмма равновесия:
(i) Альфа-феррит, или сокращенно просто феррит:
Феррит представляет собой твердый раствор углерода внедрения в альфа-железе и, таким образом, имеет структуру ОЦК. Он получил свое название от латинского слова «феррум», означающего железо. Максимальная растворимость углерода в феррите составляет 0,02 % при 727°С (точка Т на рис. 1.22), которая уменьшается с понижением температуры до незначительной величины при 0°С (< 0,00005% при 20°С). Это мягкая и пластичная фаза.
ферромагнитен при низких температурах, но теряет свои магнитные свойства при повышении температуры с большими потерями при температуре Кюри, 768°С, а выше этой температуры становится немагнитным (парамагнетиком). Рис. 1.21 (б) иллюстрирует микроструктуру феррита с многогранными зернами. Каждое зерно имеет разную ориентацию атомов, выделяется элементарная ячейка одного зерна.
(ii) Аустенит:
Представляет собой твердый раствор внедрения углерода в гамма-железе и имеет структуру ГЦК. Он получил свое название от «сэр Остин». Максимальная растворимость углерода в аустените составляет 2,11 % при 1147 °С (точка Q на рис. 1.22), которая снижается до 0,77 % углерода при 727 °С. Аустенит мягкий, пластичный, вязкий и ковкий (структура FCC) и немагнитный (парамагнитный). Стали обычно прокатывают и куют при температуре выше 1100 °C, когда они находятся в аустенитном состоянии из-за их высокой пластичности и ковкости, что также связано с их структурой FCC.
Механические свойства приведены в таблице 1.9. Он стабилен при температуре выше 727°C в простых углеродистых сталях, но может быть получен при комнатной температуре, скажем, путем добавления в стали таких элементов, как Ni или Mn. Микроструктура показана на рис. зерно полиэдрической структуры.
(iii) Дельта-феррит:
ОБЪЯВЛЕНИЯ:
Представляет собой твердый раствор внедрения углерода в дельта-железе, имеющий структуру ОЦК. Максимальная растворимость углерода 0,09.% при 1495°С. Это высокотемпературная фаза и высокотемпературное проявление а-феррита.
(iv) Цементит, карбид железа, Fe 3 C:
Это интерстициальное промежуточное соединение с фиксированным содержанием углерода 6,67%. Он имеет сложную орторомбическую кристаллическую структуру с 12 атомами железа и 4 атомами углерода на элементарную ячейку. Это состав с высокой твердостью ( ~ 800 VPN), который легко царапает стекло. Это хрупкая фаза с низкой прочностью на растяжение и высокой прочностью на сжатие. Он слабоферромагнитен до 210°C и парамагнетичен выше. Температура плавления составляет около 1227°C.
Цементит может образовывать твердый раствор замещения, т. е. его атомы углерода могут быть замещены неметаллическими элементами, такими как N или O. Его атомы железа могут быть замещены атомами Mn, Cr, W и т. д., когда он называется легированным цементитом. и может быть представлен как (Fe, M) 3 C, где M обозначает символ металла. Цементит является метастабильным соединением и при определенных условиях разлагается с образованием свободного углерода, то есть графита.
3. Критические температуры в Fe-Fe 3 C Диаграмма равновесия :
Стали испытывают также остановку температур при охлаждении или нагреве, когда в них происходят превращения, как фазовые, так и магнитные. Температуры, при которых происходят превращения (происходят остановки) в твердом состоянии, называются критическими температурами, или критическими точками. Для их обозначения используются аналогичные символы, как и для чистого железа.
Критические точки при нагреве сталей:
А 0 :
210 °C — это температура Кюри (преобразование магнитного поля в немагнитное при нагревании) цементита, как показано пунктирной линией, A 0 на рис. 1.22.
А 1 :
Добавление углерода в количестве более 0,02% к железу приводит к этой критической точке из-за инвариантного эвтектоидного превращения при постоянной температуре 727°C, когда перлит превращается в аустенит (0,77% C) при нагревании и наоборот. При охлаждении выделяется тепло, вызывающее термическую остановку, и фактически, если сталь с содержанием углерода более 0,6 % охлаждается в темноте, тепло, выделяющееся в точке A1, может поднять температуру образца до такой степени, что снова на мгновение появляется красное свечение. , наблюдаемое до возобновления охлаждения. Эта точка термической остановки A1 также называется точкой рекалесценции или углеродной точкой. Хотя A1 обязан своим существованием углероду, на него не влияет содержание углерода, как показано горизонтальной линией TUT’ на рис. 1.22. А1 также называется нижней критической температурой.
А 2 :
Называется температурой Кюри (феррита), при которой ферромагнитный феррит при нагревании переходит в парамагнитный, т.е. при 768°С. Она показана горизонтальной линией от 768°С до точки V (рис. 1.25). Потеря ферромагнетизма феррита (т. е. A 2 ) в сплавах Fe-C с более высоким содержанием углерода, чем точка V (≈ 0,5% C), следует линии ВУТ в зависимости от углерода сплава, хотя изменение происходит в сторону парамагнитного тогда аустенит.
А 3 :
Это температура, при которой феррит только начинает формироваться из аустенита при охлаждении доэвтектоидной стали или последние следы свободного феррита превращаются в аустенит при нагреве. Таким образом, это температура, соответствующая границе раздела фаз γ + α/γ для доэвтектоидных сталей, и является функцией содержания углерода в сплавах, поскольку она снижается от 910 °С при 0 % С до 727 °С при 0,77 % С. Она также называется верхней критической температурой доэвтектоидных сталей.
Температурный интервал между A1 и A3 называется критическим диапазоном, в котором аустенит находится в равновесии с ферритом. На рис. 1.25 видно, что кривая UV является общей (при нагреве) как для исчезновения феррита (А3), так и для исчезновения ферромагнетизма (А2) и, таким образом, эта часть кривой представляет температуры А3,2. Для заэвтектоидных сталей А2 , A3 совпадают с эвтектоидной температурой, поэтому правее 0,77 % C нижнюю критическую температуру часто обозначают как A3,2,1.
А см :
Это температура в заэвтектоидной стали, при которой доэвтектоидный цементит только начинает формироваться (при охлаждении) из аустенита. Он представляет собой температуру границы раздела фаз γ/γ + Fe3C и является функцией углерода. Изменение этой температуры с углеродом представлено QU, как на рис. 1.22. Линия Acm показывает состав аустенита в равновесии с цементитом.
Линия см показывает, что растворимость углерода в твердом состоянии в аустените очень быстро снижается с максимума 2,11 % при 1147°C до максимума 0,77 % при 727°C из-за большей стабильности цементита при более низких температурах. Дополнительный углерод выделяется из аустенита в виде доэвтектоидного цементита в заэвтектоидных сталях (также называемый вторичным цементитом в чугунах). Отделение цементита от аустенита (при охлаждении) также сопровождается выделением тепла.
Линия см намного круче, чем линия A3, что хотя и означает, что количество доэвтектоидного цементита в товарных сталях очень мало, но это также означает, что для растворения этого цементита необходимо нагревание, слишком высокие температуры. для полной гомогенизации аустенита. Такой нагрев до высоких температур на практике нежелателен.
4. Превращения и микроструктуры медленно охлаждаемых сталей в Fe-Fe 3 C Диаграмма равновесия:
На диаграмме Fe-Fe 3 C (рис. 1.22) ABCD представляет собой ликвидус, выше которого каждый сплав находится в жидком состоянии. AOPQCRD представляет собой солидус, ниже которого каждый сплав является полностью твердым. Чтобы понять происходящие превращения, рассмотрим медленное охлаждение некоторых сплавов из жидкого состояния до комнатной температуры. На рис. 1.27 показана часть диаграммы Fe-Fe3C вместе с кривыми термического охлаждения некоторых сталей, которые обсуждаются ниже. Для обсуждения проведена вертикальная линия, обозначающая состав стали.
1. Доэвтектоидные стали:
Рассмотрим медленное охлаждение стали Fe-0,4 % C в равновесных условиях, скажем, от 1600°C до комнатной температуры. При температуре «а» на рис. 1.27 затвердевание начинается с образования твердого δ-феррита. По мере охлаждения продолжает образовываться больше δ-феррита, пока не будет достигнута температура B (1495°C).
В этот момент (до начала перитектической реакции) количество фаз составляет:
При этой температуре происходит перитектическая реакция, но количество жидкости превышает необходимое для полной перитектической реакции (δ-феррит/жидкость = 4,5).
Таким образом, когда эта реакция завершена, количества присутствующих фаз составляют:
При дальнейшем охлаждении жидкость превращается в твердый аустенит до тех пор, пока не будет достигнута температура С, при которой затвердевание завершается, т. е. при температуре С твердое тело полностью состоит из зерен аустенита (одна фаза) с содержанием углерода 0,4%. По мере продолжения охлаждения аустенит сохраняется до тех пор, пока не будет достигнута температура, соответствующая N, которая представляет собой температуру сплава А3, после чего на границах зерен аустенита начинает формироваться феррит.
Доэвтектоидный феррит (также цементит в заэвтектоидных сталях) всегда образуется на границах зерен аустенита при медленном охлаждении. Поскольку атомы на границах зерен не находятся в узлах решетки, а находятся в метастабильном состоянии, то есть в высокоэнергетическом состоянии, они могут легко образовать там феррит. Феррит продолжает образовываться при понижении температуры до тех пор, пока не будет достигнута эвтектоидная температура.
На данный момент пропорции фаз таковы:
Эти 50,67 % аустенита (0,77 % С) при эвтектоидной температуре должны вступить в эвтектоидную реакцию с образованием смеси феррита и цементита, называемой перлитом в количестве 50,67 %. Так, в стали с содержанием углерода 0,4 % содержится 49,33 % доэвтектоидного феррита и 50,67 % перлита. См. схему охлаждения на рис. 1.25 и схематические микроструктуры этой стали.
Этот перлит или любой другой перлит состоит из феррита и цементита в следующей пропорции:
Как уже было сказано, феррит, образующийся до эвтектоидной реакции, называется доэвтектоидным ферритом. Феррит, входящий в состав перлита, называется эвтектоидным ферритом, тогда как цементит, присутствующий в перлите, называется эвтектоидным цементитом.
В этом сплаве (сталь с 0,4 % углерода) пропорции феррита и цементита (сразу после эвтектоидной реакции) можно получить непосредственно, применяя правило рычага:
Кривая TS’ на рис. 1.25 показывает, что растворимость углерода в твердом состоянии в феррите уменьшается с понижением температуры, т. е. от максимальной растворимости 0,02 % С при 727°С она уменьшается до < 0,00005 % при 20°С. Так, любой феррит, будь то свободный или эвтектоидный феррит в стали, при охлаждении от 727°С (эвтектоидная температура после завершения эвтектоидной реакции) до комнатной температуры, или, скажем, 20°С приводит к выделению небольшого количества цементит называется третичным цементитом.
Максимальное количество этого третичного цементита выделяется в сплаве, содержащем 100 % феррита, при 727°C, т. е. в стали с содержанием углерода 0,02 %, и это количество составляет (при 20°C):
В большинстве коммерческих сталей и чугунов количество третичного цементита намного меньше этого значения, и в большинстве случаев им пренебрегают. Таким образом, мы будем пренебрегать этим, обсуждая микроструктуры сталей и чугунов. Таким образом, в большинстве случаев за микроструктуру, полученную сразу после эвтектоидной реакции, принимают микроструктуру при комнатной температуре. Обсуждается важность третичного цементита при закалочном старении сталей.
Сталь с содержанием углерода 0,4 % имеет примерно 50 % феррита и 50 % перлита в микроструктуре в условиях медленного охлаждения.
2. Эвтектоидная сталь (0,77 % Сталь) :
Эвтектоидная сталь (рис. 1.27) при охлаждении, скажем, от 1600°С, начинает затвердевать при температуре J с образованием непосредственно из жидкости твердого аустенита и завершается в точке К, когда сплав имеет в микроструктуре зерна аустенита только (углерод 0,77 %). Дальнейшее охлаждение этого сплава до точки U или эвтектоидной температуры происходит без каких-либо изменений. Затем этот сплав при 727°C подвергается эвтектоидной реакции с образованием 100% перлита.
Количество эвтектоидного феррита и эвтектоидного цементита (т.е. в перлите) рассчитано по уравнениям 1.22 и 1.23. Таким образом, эвтектоидная сталь имеет 100% перлит в микроструктуре, как схематично показано на рис. 1.25.
3. Гиперэвтектоидные стали:
Заэвтектоидные стали содержат углерод от 0,77% до 2,11%. Рассмотрим охлаждение, скажем, 1,2% углеродистой стали из расплавленного состояния, скажем, от 1500°C. Затвердевание начинается при температуре d на рис. 1.27 с образованием твердого аустенита. При дальнейшем охлаждении твердый аустенит продолжает образовываться до тех пор, пока не будет достигнута температура e, при которой затвердевание завершается. При этой температуре твердая сталь полностью состоит из зерен аустенита с содержанием углерода 1,2 %. Эта фаза сохраняется при постоянном охлаждении до тех пор, пока не будет достигнута температура, соответствующая w, т. е. A см температура стали, и начинает образовываться цементит.
Цементит продолжает формироваться в виде сетки по границам зерен аустенита при понижении температуры (рис. 1.25), пока не будет достигнута эвтектоидная температура. Уравнения 1.26 и 1.27 дают количество аустенита и доэвтектоидного цементита соответственно в стали с содержанием углерода 1,2 % при только что достигнутой температуре 727°C.
Затем аустенит (0,77 % C) должен подвергнуться эвтектоидной реакции с образованием перлита. Таким образом, сталь с содержанием углерода 1,2 % имеет 7,29% доэвтектоидного цементита и 92,71 % перлита схематическая микроструктура.
5. Методы, используемые для различения свободного феррита и свободного цементита в Fe-Fe 3 C Диаграмма равновесия:
Когда содержание углерода в стали значительно отличается от эвтектоидного углерода, то можно легко провести различие между доэвтектоидной сталью и заэвтектоидной сталью. Нитал является распространенным реагентом для травления. Под световым микроскопом доэвтектоидный цементит выглядит белым, а доэвтектоидный феррит также кажется белым, но цементит присутствует в виде сетки на границах зерен перлита (при комнатной температуре), тогда как феррит присутствует в виде зерен (равноосных многогранных зерен) с границами зерен в между зернами феррита (при правильном травлении).
Коммерческие стали имеют содержание углерода до 1,5 %, поэтому количество доэвтектоидного цементита составляет менее 10 % в заэвтектоидных сталях. Вероятно, что микроструктуры этих медленно охлаждаемых заэвтектоидных сталей могут оказаться похожими на микроструктуры некоторых медленно охлаждаемых доэвтектоидных сталей, которые содержат доэвтектоидный феррит в количествах менее 10 % (то есть имеют содержание углерода от 0,7 до 0,77 %). потому что доэвтектоидные фазы (цементит в первом и феррит во втором) присутствуют на границах зерен перлита и кажутся белыми под оптическим микроскопом из-за травления ниталом.
Для различения свободного феррита и свободного цементита можно использовать один или несколько из следующих методов:
1. Формы фаз:
Проэвтектоидный феррит выглядит как зерна, которые являются довольно широкими, многогранными, и можно увидеть границы зерен между соседними зернами феррита (при правильном травлении). Пленки доэвтектоидного цементита обычно значительно тоньше, имеют неправильные очертания и ограничены резкими линиями. Они присутствуют в виде сети иголок или тромбоцитов. Цементит выглядит намного ярче и четче из-за его твердости и характеристик травления ниталом. См. рис. 1.29.(а) и (б).
Если исследовать топографию поверхности полированных и протравленных (нитал) образцов доэвтектоидной стали и заэвтектоидной стали, фокусируя кусок и слегка расфокусируя (или фокусируя верхнюю часть рельефной пластины цементита), цементит появляется стоять прямо над плоскостью травления, как показано на рис. 1.30 (а) и (б).
2. Относительная твердость:
Цементит очень твердый (~ 800 ВЧ), а феррит очень мягкий (~ 95 VPN), можно провести испытание на микротвердость, чтобы отличить феррит от цементита. Однако можно провести простой тест.
Сделайте царапину на полированной и протравленной поверхности стали, а затем осмотрите точку царапины, где она входит в белую доэвтектоидную фазу из перлита. См. рис. 1.31. Если царапина при входе расширяется, то это феррит мягкой фазы, а значит, сталь является доэвтектоидной сталью, если же она утончается в белой фазе, то белая фаза значительно тверже перлита, то есть это цементит заэвтектоидной фазы. стали.
3. Специальные травители:
Травление ниталомприводит к тому, что цементит и феррит под микроскопом выглядят белыми, что затрудняет их обнаружение в некоторых сталях. Классически раствор пикрата натрия, применяемый либо кипячением (что неудобно), либо электролитически, затемняет цементит, но не феррит, хотя пластинки цементита в перлите также затемняются, т. е. затемняются перлитные колонии.
См. рис. 1.32 микроструктуры заэвтектоидной стали, (а) протравленные ниталом, (б) протравленные раствором пикрата натрия. Другой травитель на основе тиосульфата натрия и нитрата аммония (разработанный Beraha) окрашивает феррит, но не цементит [Рис. 1.32 (с)]
6. Ограничения Fe-Fe 3 C Диаграмма равновесия:
В реальных циклах термообработки используются скорости охлаждения, намного превышающие равновесные скорости охлаждения, с помощью которых построена диаграмма Fe-Fe 3 C, и, таким образом, накладываются серьезные ограничения на интерпретацию диаграммы Fe-Fe 3 C, приведенной ниже A 1 Температура.