Алюминий входит в состав сплава – Алюминиевые сплавы — марки, свойства и применение
alexxlab | 07.11.2019 | 21 | Вопросы и ответы
Характеристики, свойства и применение алюминиевых сплавов
Алюминий имеет колоссальное значение в промышленности вследствие повышенной пластичности, высокого уровня тепло- и электропроводности, низкой коррозии, поскольку образующаяся на поверхности пленка Al2O3 выступает защитником от окисления. Из алюминия получается отличный тонкий прокат, фольга, любой формы профиль при помощи прессования и других видов обработки давления. Из него создают разного типа провода, применяемые в электроаппаратуре.
Алюминий, как и железо очень редко применяется в чистом виде. Чтобы придать им заданные полезные качества на производстве добавляют небольшие количества (не больше 1 %) иных элементов, называемых легирующими. Таким образом получают сплавы железа, алюминия и других металлов.
Физические параметры алюминиевых сплавов
Алюминиевые сплавы имеют плотность, которая незначительно отличается от плотности чистого металла (2.7 г/см3). Она колеблется от 2.65 г/см3 для сплава АМг6 до 2.85 г/см3 для сплава В95.
Процедура легирования почти не оказывает влияния на величину модуля упругости и модуля сдвига. К примеру, модуль упругости упрочненного дюралюминия Д16Т почти такой же, как модуль упругости чистого металла А5 (Е=7100 кгс/мм2). Тем не менее, за счет того, что максимум текучести сплавов на несколько единиц превышает максимум текучести чистого алюминия, сплавы алюминия уже можно использовать в качестве конструкционного материала с различным уровнем нагрузок (все зависит от марки сплава и его состояния).
Большая часть алюминиевых сплавов отличается худшей электро- и теплопроводностью, коррозионной стойкостью и свариваемостью в сравнении с чистым алюминием.
Известно, что сплавы с более высокой степенью легирования характеризуются существенно меньшей электро- и теплопроводностью. Эти показатели находятся в непосредственной зависимости от состояния сплава.
Самые лучшие коррозионные свойства алюминиевых сплавов наблюдаются у сплавов АМц, АМг, АД31, а худшие – у высоко-прочных сплавов Д16, В95, АК. Помимо этого, коррозионные показатели термоупрочняемых сплавов в значительной степени зависят от режима закалки и старения. К примеру, сплав Д16 чаще всего используется в естественно-состаренном состоянии. Тем не менее, при температуре более 80оС его коррозионные показатели существенно снижаются и для использования в условиях более высоких температур зачастую применяют искусственное старение.
Хорошо поддаются всем видам сварки сплавы АМц и Амг. В процессе сварки нагартованного проката в области сварочного шва осуществляется отжиг, по этой причине прочность шва приравнивается к прочности основного материала в отожженном состоянии.
Виды алюминиевых сплавов
Сегодня очень развито производство алюминиевых сплавов. Существует два типа алюминиевых сплавов:
- деформируемые, из которых создают листы, трубы, профиль, паковки, штамповки
- литейные, из которых осуществляется фасонное литье.
Широкое применение алюминиевых сплавов обусловлено их свойствами. Такие сплавы очень популярны в авиации, автомобилестроении, судостроении и прочих сферах народного хозяйства.
Неупрочняемые сплавы Al – Mn (АМц) и Al – Mg (АМг) являются коррозионностойкими материалами, из которых изготавливают бензобаки, маслобаки, корпуса судов.
Упрочняемые сплавы Al -Mg – Si (АВ, АД31, АД33) применяются для создания лопастей и деталей кабин вертолетов, барабанов колес гидросамолетов.
Сплав алюминия и меди – дюралюминий или дюраль. Сплав с кремнием называют силумином. Сплав с марганцем – АМц имеет повышенную коррозионную стойкость. Такие элементы, как Ni, Ti, Cr, Fe в сплаве способствуют повышению жаропрочности сплавов, затормаживанию процесса диффузии, а присутствие лития и бериллия повышают модуль упругости.
Литейные алюминиевые сплавы используют для создания литых заготовок. Это сплавы Al – Si (силумины), Al – Cu (дюрали), Al – Mg (Амг). В числе силуминов стоит отметить сплавы Al – Si (AЛ – 2), Al – Si – Mg (АЛ – 4, АЛ – 9, АЛ – 34), упрочняемые при помощи термообработки. Силумины отлично поддаются литью, а также обработке резанием, свариванием, также их можно анодировать и даже пропитывать лаками.
Высокопрочные и жаропрочные литейные сплавы систем Аl – Cu – Mn (АЛ – 19), Al – Cu – Mn – Ni (АЛ – 33), Al – Si – Cu – Mg (АЛ – 3, АЛ – 5). Прошедшие процесс легирования хромом, никелем, хлором или цинком выдерживают температуру до 300°С. Из них создают поршни, головки блока, цилиндров.
Марки алюминиевых сплавов
Определенные характеристики алюминиевых сплавов соответствуют конкретным маркам этих сплавов. Признанные международные и национальные нормативы (раньше были немецкие DIN, а сегодня европейские EN, американские ASTM и международные ISO) также как и российские ГОСТы рассматривают по отдельности чистый алюминий и его сплавы. Чистый алюминий согласно этим документам делят на марки (grades), а не на сплавы (alloys).
Все марки алюминия делят на:
- алюминий высокой чистоты (99,95 %)
- технический алюминий, имеющий около 1 % примесей или добавок.
Стандарт EN 573-3 определяет разные по чистоте версии алюминия, к примеру, «алюминий EN AW 1050A», и алюминиевые сплавы, к примеру, «сплав EN AW 6060». В тоже время, достаточно часто алюминий называют сплавом, к примеру, «алюминиевый сплав 1050А».
В российских стандартах, к примеру, в документе ГОСТ 4784-97 «Алюминий и сплавы алюминиевые деформируемые» и иных документах по алюминию и алюминиевым сплавам, вместо термина «обозначения» используется близкие термин «марка», только в английском эквиваленте «grade». По существующим стандартам нужно использовать фразы типа «алюминий марки АД0» и «алюминиевый сплав марки АД31».
Однако зачастую термин «марка» используют лишь для алюминия, а алюминиевые сплавы называют просто «алюминиевыми сплавами» без всяких марок, к примеру, «алюминиевый сплав АД31».
Иногда люди путают термин «марка» с термином «маркировка». ГОСТ 2.314-68 определяет термин маркировка, как совокупность знаков, характеризующих продукт, к примеру, обозначение, шифр, номер партии (серии), дата изготовления, товарный знак фирмы. При этом марка – это монтажные или транспортные обозначения. Следовательно, обозначение или марка сплава – это всего лишь небольшая часть маркировки, но не сама маркировка.
Согласно документу ГОСТ 11069-2001 марки алюминия обозначаются цифрам после запятой в процентном содержании алюминия: А999, А995, А99, А85, А8, А7, А6, А5 и А0. При этом самый чистый алюминий – А999, в нем содержится 99,999 % алюминия. Он используется для лабораторных опытов. В промышленной отрасли используют алюминий высокой чистоты – от 99,95 до 99,995 % и технической чистоты – от 99,0 до 99,85 %.
Маркировка |
Состояние, назначение | |
---|---|---|
Россия |
США |
|
Без ТО |
F |
После изготовления, без дополнительной термической обработки. Степень нагартовки и механические свойства не контролируются |
ГК |
– |
Горячекатаное |
ГП |
– |
Горячепрессованное |
М |
О |
Отожженное (мягкое). Наиболее высокая пластичность и стабильность размеров |
Н |
– |
Нагартованное (холоднодеформированное) |
Н4 |
Н18 |
Усиленно нагартованное (прокаткой листов около 20 %, для максимального упрочнения) |
Н3 |
Н16 |
Нагартованное на три четверти (3/4), повышение прочности |
Н2 (П) |
Н14 |
Полунагартованное (1/2), повышение прочности |
Н1 |
Н12 |
Нагартованное на одну четверть (1/4), повышение прочности |
З |
W |
Закаленное* (нестабильное, обычно указывается длительность естественного старения после закалки), повышение прочности |
Т |
Т3, Т4 |
Закаленное + естественно состаренное. Получение достаточно высокой прочности, повышенной пластичности, трещиностойкостии, сопротивления усталости |
Т1 |
Т6 |
Закаленное + искусственно состаренное на максимальную прочность |
Т12 |
Т77 |
Закаленное + искусственно состаренное. Улучшение характеристик сопротивления коррозии, трещиностойкости, пластичности при некотором снижении прочности. В русской маркировке возрастание первой цифры при букве указывает на увеличение степени перестаривания и разупрочнения |
Т2 |
Т76 |
|
Т3 |
Т73 |
|
ТН** |
Т31, Т36, |
Закаленное + естественно состаренное + нагартованное. На степень деформации нагартовки указывает вторая цифра. Повышение прочности при снижении характеристик пластичности, трещиностойкости |
Т1Н** |
Т81, Т83, |
Закаленное + нагартованное + искусственно состаренное. На степень деформации (нагартовки) указывает вторая цифра. Повышение прочности |
Т1Н1** |
Т9 |
Закаленное + искусственно состаренное + нагартованное. Повышение прочности особенно при совмещении с процессом формообразования детали |
mining-prom.ru
Алюминиевыми сплавами на основе алюминия являются металлы, в состав которых помимо алюминия входят такие металлы, как медь, магний, литий, цинк, марганец, кремний и другие материалы. Алюминий характеризует малая плотность и низкая температура плавления. Также он обладает малой прочностью и высокой пластичностью. Из-за малой прочности чистый алюминий практически не применяется в технике и по этой причине в основном используются сплавы из алюминия, которые отличаются такими свойствами, как устойчивость к коррозии, пластичность, отсутствие магнитности, свариваемость, малая плотность и отсутствие искрообразования. Современное производство практически невозможно представить без использования алюминия. Когда-то данный металл был равен серебру по стоимости и применялся для создания ювелирных украшений и предметов роскоши. Это было связано со сложностью и трудоемкостью получения алюминия, который был упрощен только в начале 20-го века. Научившись получать чистый алюминий, появилась возможность создания сплавов, которые сегодня широко используются в промышленности. Сплавы из алюминия делятся на деформируемые и литейные. Литейные сплавы изготавливают в форме листов, труб, профилей, лент и прутков. Они упрочняются при холодном деформировании или закалке. Деформируемые сплавы используются для производства проката и поковок. Ниже мы рассмотрим несколько сплавов алюминия, которые наиболее часто используются в производстве деталей разного типа. Сплав ад 31 – это деформируемый сплав, который используется в производстве прутьев, профилей, проволоки, радиаторов, труб, строительных конструкций, от которых не требуется высокой прочности. Сплав ад 31 иногда обозначается под цифровым обозначением – 1310 или как сплав 6063. Сплав ад 16 является деформируемым алюминиевым сплавом, который применяется для создания силовых элементов транспортного и авиапроизводства. Также данный сплав используется для изготовления труб, выдерживающих высокие температуры (до 230 градусов по Цельсию). Ад 16 в некоторых случаях называется цифровым обозначением – 1160. Литейные алюминиевые сплавы ак 7п, ак 7ч и ак 9ч используются для изготовления фасонных отливок, чушек из алюминия, которые широко используются в литейном производстве. Алюминиевый сплав ак 12 является литейным и применяется для производства различных деталей и элементов трубопроводного и металлургического оборудования. Сплав из алюминия иногда называется, как ал 2. Наилучшими коррозионными свойствами обладают сплавы АМц, АМг и АД31. Помимо этого, свойства сплавов зависят от режима закалки и старения. К примеру, сплав Д16 применяется в состаренном состоянии, но при температуре выше 80 градусов по Цельсию, его коррозионные свойства становятся хуже и для работы при больших температурах применяется искусственное старение, несмотря на то, что прочность и пластичность в этом случае значительно пострадают. Многие сплавы сильно подвергаются коррозии под напряжением. |
3g-svarka.ru
Алюминий и алюминиевые сплавы — Материалы и свойства
К цветным металлам, имеющим наибольшее применение в технике, относятся: алюминий, медь, олово, свинец, цинк, магний, никель, титан, тантал и различные сплавы на их основе или с их сравнительно небольшим содержанием.
Алюминий (от латинского алумен – алюминиевые квасцы) – мягкий пластичный металл серебристо-белого цвета, обычно покрытый тонким слоем оксидов, защищающих его от дальнейшего окисления. Алюминий примерно в 2,9 раза легче железа, легко поддается прокатке, ковке, штамповке, волочению, имеет высокие электро- и теплопроводность. Он обладает коррозионной стойкостью в атмосфере, пресной воде, в нейтральных растворах, бензине и в других органических средах, но быстро разъедается щелочами.
Свойства алюминия связаны с содержанием примесей, по наличию которых его подразделяют на алюминий особый, высокой и технической чистоты. В начале марок алюминия стоит буква А, за которой следуют цифры, указывающие на чистоту металла, например для алюминия технической чистоты обозначение марки А85 показывает, что в металле содержится 99,85 % алюминия. Из алюминия изготавливают теплообменную и химическую аппаратуру, емкости, токоведущие жилы и провода. Его используют для защиты других металлов от коррозии.
В производстве металлических изделий более широко применяют сплавы алюминия, которые по сравнению со сплавами из других цветных металлов не только дешевы и просты в получении и обработке, но и имеют лучшие механические и антикоррозионные свойства.
Деформируемые алюминиевые сплавы
Алюминиевые сплавы по способу изготовления из них изделий подразделяют на деформируемые и литейные.
Деформируемые сплавы используют для изготовления листов, профилей, труб и т. п. Различают сплавы, упрочняемые термической обработкой и неупрочняемые. В зависимости от прочности упрочняемые сплавы подразделяют на сплавы обычной прочности и высокопрочные. Среди первых наиболее распространены дуралюмины.
Дуралюмины (не считая алюминия) состоят из меди, марганца, магния, кремния, железа ) В начале марок дуралюмина стоит буква Д, за которой следуют цифры, указывающие номер сплава, соответствующий его определенным свойствам. Так, например, дуралюмин Д6 имеет повышенную прочность, а Д18 – высокую пластичность.
К высокопрочным алюминиевым сплавам относят сплавы марок В93, В94, В95 и др. Здесь буква В означает высокопрочный, а цифры – номер сплава. В состав этих сплавов, кроме алюминия, входят цинк, медь, магний и марганец. Неупрочняемые сплавы получают на основе системы алюминий— марганец (АМц) или алюминий – магний (АМг), а также при совместном вводе в алюминий марганца и магния (до 1 — 2 % каждого).
Литейные алюминиевые сплавы
Литейные сплавы предназначены для получения фасонных отливок. Из них наиболее распространены сплавы алюминия с кремнием (6—13%) —силумины, имеющие марки АЛ2, АЛ4, АЛ9, где А означает алюминиевый, Л – литейный, а цифры – номер сплава.
Алюминиевые сплавы широко используют в ракетной технике, авиастроении, при создании других средств транспорта, в химическом машиностроении, строительстве и др.
arxipedia.ru
Состав – алюминиевый сплав – Большая Энциклопедия Нефти и Газа, статья, страница 1
Состав – алюминиевый сплав
Cтраница 1
Состав алюминиевых сплавов играет скромную, но все же важную роль в процессе КР. При обсуждении этой проблемы будет необходимо обращаться к вопросам физического металловедения некоторых важных классов сплавов. Здесь в основном ограничимся описанием морфологии и процесса образования выделений применительно к КР. [1]
В состав алюминиевых сплавов входят медь, цинк, магний, марганец, кремний, железо и другие элементы. [2]
В состав алюминиевых сплавов, помимо основного компонента ( алюминия), входят: медь, кремний, магний, марганец и другие элементы, значительно повышающие механические свойства сплавов. [3]
В состав алюминиевых сплавов кобальт входит только в редких случаях, большей частью в экспериментальных сплавах. Встречающиеся количества кобальта не превышают десятых долей процента и легко могут быть определены одним из колориметрических методов. [4]
В состав алюминиевых сплавов входят кремний, магний, медь, цинк, марганец, железо и другие элементы. По технологическим свойствам алюминиевые сплавы подразделяются на литейные, обладающие хорошими литейными технологическими свойствами, и деформируемые, сравнительно легко поддающиеся обработке давлением, резко повышающей их прочность. [5]
В составы алюминиевых сплавов входят также многочисленные мелкие добавки, с которыми связаны в основном два типа эффектов. К элементам этого типа относятся Mn, Zr и Сг, влияющие на форму зерна в сплавах всех четырех основных типов. Форма зерна играет, как будет показано ниже, важную роль в КР алюминиевых сплавов, поэтому к результатам многих исследований, выполненных на модельных сплавах с равноосной структурой, следует относиться с осторожностью. Подобные сплавы можно исследовать с целью выявления роли добавок отдельных элементов, но они не моделируют промышленные сплавы, более сложные с точки зрения как химического состава, так и микроструктуры. Поэтому следует полагать, что отдельные ( а возможно, и многие) выводы, сделанные на основании изучения модельных сплавов, не применимы к сложным промышленным материалам с деформированной формой зерна. [7]
Разработка составов алюминиевых сплавов проводится с учетом создания материалов, обладающих комплексом необходимых антифрикционных свойств. Отличительной особенностью алюминиевых сплавов, содержащих мягкие структурные составляющие в виде включений почти чистых олова, свинца или кадмия ( рис. 173), является своеобразная реакция этих составляющих на режимах сухого или полужидкостного трения. [9]
Для исследования состава алюминиевых сплавов применяют часто еще следующий способ разложения и анализа. Ввиду того что реакция растворения протекает очень бурно, следует иметь наготове сосуд с холодной водой для охлаждения содержимого колбы с целью замедлить реакцию. После прекращения реакции дают раствору постоять 3 – 5 мин. Осадок, содержащий соединения меди, железа, никеля, марганца, магния и кальция, отфильтровывают от раствора, в котором находятся алюминий, цинк, олово и большая часть кремневой кислоты. Затем в осадке и растворе определяют вышеперечисленные элементы. [10]
Магний входит в состав алюминиевых сплавов, устойчивых к воздействию морской воды, и ряда сплавов на основе цинка. [11]
Хром входит в состав алюминиевых сплавов некоторых марок в качестве легирующего компонента, содержание которого не превышает десятых долей процента. [12]
Что входит в состав алюминиевых сплавов. [13]
В зависимости от состава алюминиевого сплава и степени охлаждения режим уточняется. [14]
Страницы: 1 2 3
www.ngpedia.ru
Алюминий и его сплавы | Учебные материалы
Алюминий — металл серебристо-белого цвета, порядковый номер в Периодической системе Д.И. Менделеева — 13, атомный вес 26,97. Кристаллическая решетка ГЦК с периодом а = 4,0414 Å, атомный радиус 1,43 Å. Плотность — 2,7 г/см3, температура плавления 660 0С. Имеет высокую тепло- и электропроводность. Удельное электросопротивление 0,027 мкОм×м. Предел прочности sв = 100 МПа, относительное сужение y = 40 %.
В зависимости от чистоты различают алюминий особой чистоты А999 (99,999 % Аl), высокой чистоты: А995,А99, А97, А95 и технической чистоты: А85, А8, А7, А6, А5 (99,5 % Аl), АО (99,0 % Аl).
Алюминий обладает высокой коррозионной стойкостью вследствие образования на его поверхности тонкой прочной пленки Аl2О3. Алюминий легко обрабатывается давлением, обработка резанием затруднена, сваривается всеми видами сварки.
Ввиду низкой прочности алюминий применяют для ненагруженных деталей и элементов конструкций, когда от металла требуется легкость, высокая электропроводность. Из него изготовляют трубопроводы, фольгу, цистерны для перевозки нефти и нефтепродуктов, посуду теплообменники, провода, кабели. Алюминий имеет большую усадку затвердевания (6 %).
Как конструкционный материал значительно чаще применяются алюминиевые сплавы. Они характеризуются высокой удельной прочностью, способностью сопротивляться инерционным и динамическим нагрузкам, хорошей технологичностью. Предел прочности достигает 500…700 МПа. Большинство обладают высокой коррозионной стойкостью (за исключением сплавов с медью). Основными легирующими элементами алюминиевых сплавов являются Сu, Mg, Si, Mn, Zn, реже Li, Ni, Ti. Многие образуют с алюминием твердые растворы ограниченной переменной растворимости и промежуточные фазы СuAl2, Mg2Si и др. Это дает возможность подвергать сплавы упрочняющей термической обработке. Она состоит из закалки на пересыщенный твердый раствор и естественного или искусственного старения.
По технологическому признаку алюминиевые сплавы подразделяются на две группы (рисунок 52): деформируемые, литейные.
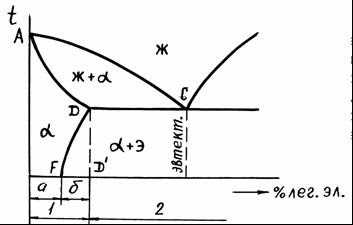
- деформируемые: а — не упрочняемые ТО; б — упрочняемые ТО;
- литейные
Рисунок 52 — Диаграмма состояния сплавов алюминий — легирующий элемент
Сплавы левее точки F имеют структуру однофазного a — твердого раствора, который имеет высокую пластичность и не упрочняются термической обработкой. Упрочнить эти сплавы можно холодной пластической деформацией (наклепом). На участке FD’ сплавы имеют предельную растворимость легирующего элемента в алюминии и поэтому упрочняются термической обработкой. Сплавы правее точки D’ имеют в структуре эвтектику, которая придает сплавам высокую жидкотекучесть. Поэтому эти сплавы относятся к литейным.
Старение закаленных сплавов. После закалки алюминиевые сплавы подвергаются старению, которое приводит к дополнительному повышению прочности сплава при некотором снижении пластичности и вязкости.
В зависимости от условий проведения, различают два вида старения:
- естественное, при котором сплав выдерживают при нормальной температуре несколько суток;
- искусственное, при котором сплав выдерживается при повышенной температуре в течение 10…24 ч.
В процессе старения происходит распад пересыщенного твердого раствора, в решетке которого атомы меди располагаются статистически равномерно. В зависимости от температуры и продолжительности, старение протекает в несколько стадий.
Так, например, в сплавах Аl — Сu при естественном или низкотемпературном искусственном старении (ниже 100…150 0С) образуются зоны Гинье-Престона 1 (ГП-1). На начальной стадии в пересыщенном a — твердом растворе образуются объемы (сегрегации), обогащенные атомами меди. Они представляют собой пластинчатые или дисковые образования диаметром 4…6 нм и толщиной несколько атомных слоев.
При более высоких температурах нагрева образуются крупные зоны ГП-2. Выдержка в течение нескольких часов приводит к образованию в зонах ГП-2 дисперсных частиц q — фазы (СuAl2). Образование зон ГП-1, ГП-2 и q- фазы приводит к повышению прочности и твердости закаленных алюминиевых сплавов.
Деформируемые сплавы, не упрочняемые термообработкой. Эти сплавы отличаются высокой пластичностью, хорошей свариваемостью и высокой коррозионной стойкостью. Пластическая деформация упрочняет сплавы почти в 2 раза.
К этой группе сплавов относятся марки АМц (1,1…1,6 % Мn), АМг2, АМг3, АМг5, АМг6 (цифра показывает содержание магния в процентах).
Они применяются для сварных элементов конструкций, испытывающих сравнительно небольшие нагрузки и требующие высокого сопротивления коррозии. Из сплавов АМц, АМг2, АМг3 изготовляют емкости для хранения нефтепродуктов, трубопроводы для масла и бензина, палубные надстройки, в строительстве — витражи, перегородки, двери, оконные рамы и др. Сплавы АМг5, АМг6 применяются для средненагруженных деталей и конструкций: рамы и кузова вагонов, перегородки зданий переборки судов, кабины лифтов.
Деформируемые сплавы, упрочняемые термообработкой. Наиболее распространенными представителями группы алюминиевых сплавов, применяемыми в деформированном виде и упрочняемыми термической обработкой, являются дуралюмины (от французского dur- твердый). К ним относятся сплавы системы Al — Cu – Mg — Mn. Типичными дуралюминами являются марки Д1 и Д16. Их химический состав приведен в таблице 18.
Таблица 18 — Химический состав дуралюминов, %
Марка | Cu | Mn | Mg | Si | Fe |
Д1 Д16 | 3,8…4,8 3,8…4,5 | 0,4…0,8 0,3…0,9 | 0,4…0,8 1,2…1,8 | <0,7 <0,5 | <0,7 <0,5 |
Предел прочности Д1 sв = 410 МПа и d = 15%, у Д16 sв = 520 МПа и d= 11 %. Они хорошо деформируются в холодном и горячем состояниях. Для закалки сплав Д1 нагревается до 495…510 0С, а Д16 — до 485…503 0С. Нагрев до более высоких температур вызывает пережог. Охлаждение производится в воде.
Дуралюмины после закалки подвергают естественному старению, т.к. при этом обеспечивается более высокая коррозионная стойкость. Время старения 4…5 суток. Иногда применяют искусственное старение при температуре 185…195 0С. Из сплава Д16 изготовляют обшивки, силовые каркасы, строительные конструкции, кузова грузовых автомобилей, шпангоуты, стрингера, лонжероны самолетов и т.д.
Сплавы авиаль (АВ) уступают дуралюминам по прочности, но обладают лучшей пластичностью в холодном и горячем состояниях, хорошо свариваются и сопротивляются коррозии, имеют высокий предел усталости. Упрочняющей фазой является соединение Мg2Si.
Авиаль закаливается при 515…525 0С с охлаждением в воде, а затем подвергается естественному старению (АВТ) или искусственному при температуре 160 0С в течение 12 часов (АВТ1). Изготовляют листы, трубы, лопасти винтов вертолетов, кованые детали двигателей, рамы, двери.
Высокопрочные алюминиевые сплавы. Прочность этих сплавов достигает 550…700 МПа, но при меньшей пластичности, чем у дуралюминов. Они, кроме Сu и Mg содержат Zn. К ним относятся сплавы В95, В96. Упрочняющими фазами являются MgZn2, Al3Mg3Zn3, Al2CuMg. С увеличением содержания цинка прочность повышается, но снижается пластичность и коррозионная стойкость.
Сплавы закаливают при 465…475 0С с охлаждением в воде и подвергают искусственному старению при 135…145 0С в течение 16 ч. Они более чувствительны к концентратам напряжений и имеют пониженную коррозионную стойкость под напряжением. Применяются там же, где и дуралюмины.
Ковочные алюминиевые сплавы отличаются высокой пластичностью при температурах ковки и штамповки (450…475 0С) и удовлетворительными литейными свойствами. Закалка проводится при 515…525 0С с охлаждением в воде, старение при 150…160 0С в течение 4…12 ч. Упрочняющими фазами являются Mg2Si, CuAl2.
Сплав АК6 используют для деталей сложной формы и средней прочности (sв = 360 МПа) — крыльчатки, качалки, крепежные детали.
Сплав АК8 с повышенным содержанием Сu хуже обрабатываются давлением, но более прочный и применяется для изготовления подмоторных рам, лопастей винтов вертолетов и др.
Жаропрочные сплавы. Эти сплавы применяются для деталей, работающих до 300 0С (поршни, головки цилиндров, обшивка самолетов, лопатки и диски осевых компрессоров, крыльчатки и т.д.). Эти сплавы дополнительно легируют Fe, Ni, Ti.
Сплав АК4-1 закаливают при 525…535 0С, а сплав Д20 — при 535 0С в воде и подвергают старению при 200…220 0С. Упрочняющими фазами являются СuAl2, Mg2Si, Al2CuMg, Al9FeNi. При частичном распаде твердого раствора они выделяются в виде дисперсных частиц, устойчивых к коагуляции, что обеспечивает повышенную жаропрочность.
Литейные алюминиевые сплавы. Сплавы для фасонного литья должны обладать высокой жидкотекучестью, сравнительно небольшой усадкой, малой склонностью к образованию горячих трещин и пористости в сочетании с хорошими механическими свойствами, сопротивлением коррозии.
Высокие литейные свойства имеют сплавы, содержащие в структуре эвтектику. Содержание легирующих элементов в этих сплавах больше предельной растворимости их в алюминии и больше, чем в деформируемых. Чаще применяют сплавы Al — Si, Al — Cu, Al — Mg. Для измельчения зерна, а следовательно улучшения механических свойств, в сплавы вводят модифицирующие добавки (Ti, Zr, B, V, Na и др.). Многие отливки из алюминиевых сплавов подвергают термической обработке. Например: отжиг при 300 0С в течение 5…10 ч; закалка и естественное старение tзак = 510…520 0С и охлаждение в горячей воде (40…100 0С) выдержка до 20 часов.
Сплавы Al — Si (силумины) содержат много эвтектики, поэтому обладают высокими литейными свойствами отливки, более плотные. К ним относятся сплавы АЛ2, АЛ4, АЛ9.
АЛ2 содержит 10-13% Si и является эвтектическим сплавом, упрочняющей термической обработке не подвергается.
АЛ4, АЛ9 — доэвтектические и дополнительно легированы Мg. Могут упрочняться термообработкой. Упрочняющей фазой служат Mg2Si. Эти сплавы применяют для изготовления крупных нагруженных деталей: корпуса компрессоров, картеры и блоки цилиндров двигателей.
Сплавы Al — Cu. Эти сплавы (АЛ7, АЛ19) имеют более низкие литейные свойства, чем силумины. Поэтому их применяют, как правило, для отливок небольших деталей простой формы (арматура, кронштейны и т.д.). Имеют большую усадку, склонность к образованию горячих трещин и к хрупкому разрушению.
Сплавы Аl — Mg. Эти сплавы (АЛ8, АЛ27) имеют низкие литейные свойства, так как не содержат эвтектики. Характерной особенностью этих сплавов является хорошая коррозионная стойкость, повышенные механические свойства и обрабатываемость резанием. Они предназначены для отливок, работающих во влажной атмосфере. Сплавы марок АЛ13 и АЛ22 имеют более высокие литейные свойства в результате образования тройной эвтектики.
Жаропрочные сплавы. Наибольшее применение получил сплав АЛ1, из которого изготовляют поршни, головки цилиндров и другие детали, работающие при температуре 275…300 0С. Структура литого сплава АЛ1 состоит из a- твердого раствора, содержащего Cu, Mg, Ni, и избыточных фаз Al2CuMg, Al6CuNi.
Более жаропрочными являются сплавы АЛ19 и АЛ33. Это достигается добавками в сплавы Mn, Ti, Ni, Zn, Ce и образованием нерастворимых интерметаллидных фаз Al6Cu3, Al2Ce, Al2Zr и др.
Для крупногабаритных деталей работающих при 300…350 0С применяют сплав АЛ21.
dprm.ru
Алюминий и его сплавы: все об этом металле
На сегодняшний день практическое применение нашли почти все известные человеку металлы и их сплавы. У каждого из них есть свои специфические особенности, которые и определяют сферу их использования в тех или иных отраслях промышленности. Наибольшее распространение получили железо и всевозможные соединения на его основе, а также алюминий и его сплавы. Это можно объяснить, прежде всего, большими природными запасами, а также прекрасными химическими, физическими и механическими характеристиками.
Немного истории
Согласно древней легенде, описанной в трактате «Естественная история» Гая Плиния Старшего, составленной примерно в 77 году н.э., однажды к императору Рима Тиберию подошел незнакомый мастер и сделал ему подарок в виде чаши из серебристого и очень легкого металла. Когда Тиберий спросил его, из чего он ее сделал, тот ответил, что из глины. Удивившись, император приказал умертвить невинного ремесленника и уничтожить его мастерскую, чтобы это изобретение не привело к обесцениванию металлов римской казны. Жаль, что он в то время не смог оценить все перспективы открытия, ведь алюминий и его сплавы в будущем совершили прямо-таки настоящий прорыв.
Почему алюминий и его сплавы так популярны?
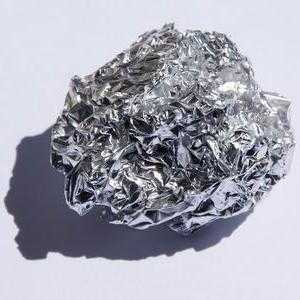
Основные сплавы на основе алюминия
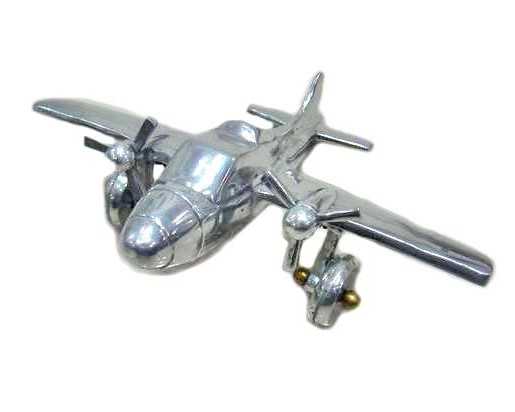
Дюралюмин (дюралюминий, или просто дюраль)
Название этого соединения произошло от слова Дюрен – именно так назывался немецкий город, в котором в 1911г. начали производить этот сплав в промышленных масштабах. Получают его добавлением к алюминию меди (2,2 – 5,2 %), магния (0,2 – 2,7%) и марганца (0,2 – 0,1%). После термообработки металл становится очень прочным (статическая прочность достигает 450-500 МПа). Для того чтобы повысить антикоррозийную стойкость, его нередко плакируют алюминием. Используют в качестве конструкционного материала в транспортном и авиационном машиностроении.
Магналии
Это различные сплавы алюминия с магнием и прочими элементами (содержание магния – 1-13%). Для них характерна высокая пластичность, хорошая свариваемость и коррозийная стойкость. Используются для изготовления фасонных отливок, проволоки, листов, заклепок и т.д.
Силумин
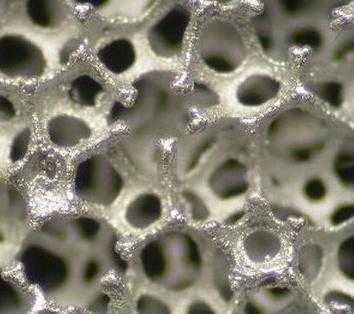
Алюминий и его сплавы еще долго будут служить на благо человечества. Доказательство тому новое изобретение – пеноалюминий или, как его еще называют, «металлический поролон». Многие эксперты считают, что у пористого алюминия есть отличные перспективы.
fb.ru
: Металлургия: образование, работа, бизнес :: MarkMet.ru
СВОЙСТВА И ПРИМЕНЕНИЕ АЛЮМИНИЯ
По объему производства и масштабам применения алюминий (Аl) является самым распространенным цветным металлом. Он открыт в 1826 г. Его название происходит от латинского слова «алюмен» —название квасцов (соединения, содержащего алюминий).
Алюминий имеет относительно малую плотность, низкую температуру плавления (658°С) и очень высокую скрытую теплоту плавления. Он хорошо поддается механической обработке: прокатке, ковке, волочению, резанию и т. п., а также обладает высокой теплопроводностью и электропроводностью. Электропроводность алюминия составляет 60—65% от электропроводности меди. Алюминий в три раза легче меди, поэтому алюминиевый провод с таким электросопротивлением легче, чем медный. Обладая большим сродством к кислороду, алюминий имеет одновременно и высокую коррозионную стойкость на воздухе и в ряде других сред.
Чистый алюминий имеет малую прочность и не может быть использован в качестве конструкционного материала. Однако прочность его резко возрастает под влиянием добавок других элементов, термической и механической обработки. Многие сплавы на основе алюминия обладают достаточно высокой механической прочностью, сочетающейся с малой плотностью, что делает их весьма ценным конструкционным материалом.
Алюминий и алюминиевые сплавы служат весьма эффективными заменителями свинца, меди, олова, цинка, а в ряде случаев их успешно используют вместо стали. В электротехнике алюминий применяют для изготовления проводов, кабелей, шинопроводов, конденсаторов, выпрямителей переменного тока и т. д. Алюминиевые сплавы широко применяют в литом и деформированном состояниях в различных авиаконструкциях, в транспортном машиностроении и автомобильной промышленности. Благодаря высокой коррозионной стойкости алюминий применяют в химическом машиностроении при изготовлении аппаратуры для производства азотной кислоты, органических веществ, пищевых продуктов и т. д. Возрастает использование алюминия при строительстве жилых и общественных зданий, сооружений, мостов и т. д. Широко применяют алюминий для защиты поверхности металлов от коррозии, при изготовлении полупроводниковых приборов, в радиолокации, электротехнике, ядерной технике.
Высокую химическую активность алюминия используют в металлургии для получения трудновосстановимых тугоплавких металлов (хрома, вольфрама, марганца и др.), а также щелочноземельных и щелочных металлов, для раскисления и легирования стали. Тонкоизмельченный алюминий при нагревании на воздухе сгорает с выделением большого количества тепла. Эту алюминотермическую реакцию используют для получения чистых металлов и других целей. В пищевой промышленности алюминий применяют в виде фольги для упаковки, консервных банок и т. а. Из алюминия изготовляют предметы домашнего обихода, художественные и декоративные изделия.
Литейные свойства алюминия невысоки из-за большой усадки, малой жидкотекучести и высокой пористости получаемого литья. Значительные затруднения имеют место при сварке алюминия, что связано с большой тугоплавкостью окислов алюминия, образующихся на поверхности при сварке.
Физические и механические свойства алюминия характеризуются следующими данными:
Атомная масса | 26,98 |
Плотность при 20°С, г/см3 | 2,7 |
Температура, °С: |
|
плавления | 658,9 |
кипения | 2497 |
Удельная теплоемкость, кал/г | 0,222 |
Теплопроводность кал/(см·сек·град) | 0,52 |
Скрытая теплота плавления, кал/г | 92,7 |
Коэффициент линейного расширения, 1 /град | 23,8*10-6 |
Удельное электросопротивление, ом-мм2/м | 0,025-0,03 |
Временное сопротивление алюминия, кГ/мм2 |
|
деформированной | 15 |
отожженной | 8 |
Предел текучести алюминия, кГ/мм2, при температуре, °С |
|
отожженного | 5-8 |
деформированного | 12 |
Относительное удлинение алюминия, %: |
|
Деформированной | 5-10 |
отожженной | 30-40 |
Предел упругости алюминия, кГ/мм2: |
|
отожженного | 3-4 |
Модуль упругости, кГ/мм2 | 5500-7000 |
Модуль сдвига, кГ/мм2 | 2760 |
Твердость НВ алюминия, кГ/мм2 |
|
Деформированного | 25-35 |
Отожженного | 13-20 |
Литого | 13-25 |
Алюминий и его сплавы характеризуются высокой коррозионной стойкостью в атмосферных условиях, в том числе и загрязненных промышленными газами. Сероводород, сернистый газ, аммиак и другие газы, находящиеся в воздухе, не влияют на скорость коррозии алюминия и его сплавов при комнатной температуре, а пар, дистиллированная и чистая пресная вода — и при высоких температурах. Практически не действуют на алюминий сернокислые нейтральные соли магния, натрия, аммония. Высокой коррозионной стойкостью обладает алюминий в органических кислотах: уксусной, лимонной, винной, пропиновой, яблочной.
Алюминий и его сплавы устойчивы в концентрированной азотной кислоте при комнатной температуре и сильно разрушаются в разбавленной кислоте. Он устойчив против коррозии в 100%-ной серной кислоте и в растворах этой кислоты до 10%. С повышением температуры раствора и концентрации кислоты >10% скорость коррозии алюминия резко возрастает.
Соляная кислота, а также растворы плавиковой и бромистоводородной кислот быстро разрушают алюминий и его сплавы. Алюминий и его сплавы обладают значительной коррозионной стойкостью в растворах аммиака, но разрушаются под действием едких щелочей.
В контакте с большинством металлов, являющихся более благородными по ряду напряжений, алюминий является анодом, и в таких случаях коррозия его в электролитах ускоряется. При работе в морской воде или в растворах хлористого натрия при контакте с обычной или нержавеющей сталью коррозия алюминия увеличивается.
АЛЮМИНИЕВЫЕ СПЛАВЫ
Все технические сплавы на алюминиевой основе принято разделять на деформируемые (после прессования, прокатки, ковки) и литые.
Деформируемые сплавы. Эти сплавы делят на упрочняемые и не упрочняемые термической обработкой.
Термическая обработка сплавов основана на изменении растворимости различных промежуточных соединений в основном алюминиевом растворе. Например, растворимость меди в алюминии при комнатной температуре составляет 0,5%, а при температуре образования эвтектики (548°С) 5,7%. При понижении температуры раствор становится пересыщенным промежуточным соединением, которое должно выделиться из него в виде отдельной составляющей (для алюминиевомедных сплавов промежуточным соединением является СuАl2). Процесс выделения избыточной фазы можно затормозить быстрым охлаждением и получить таким путем при обычной температуре состояние сплава, в котором он находился при высоких температурах. Полученный таким образом пересыщенный раствор будет находиться в неустойчивом состоянии и в нем с течением времени будут происходить внутренние процессы, сопровождающиеся изменением механических свойств сплава (старение).
Если старение происходит при комнатной температуре, то его называют естественным; если при повышенной температуре — то искусственным. При старении значительно возрастает временное сопротивление сплава по сравнению с временным сопротивлением свежезакаленного и отожженного сплавов.
В начальный (инкубационный) период старения повышение временного сопротивления сплавов незначительно. В этот период сплавы обладают большой пластичностью и закаленные изделия могут подвергаться разным видам пластической деформации. При дальнейшем старении пластичность сплавов уменьшается и эти операции становятся невозможными. Для придания сплаву пластичности после старения его необходимо вновь вернуть в свежезакаленное состояние.
Алюминиевые сплавы, содержащие только элементы, не образующие промежуточных соединений с изменяющейся растворимостью, не упрочняются при термической обработке. К сплавам, не упрочняемым термической обработкой, относятся сплавы алюминия с марганцем и магнием (марки АМц, АМг, АМг5П).
Алюминиевомарганцовистые сплавы превосходят чистый алюминий по прочности и коррозионной стойкости.
Сплавы алюминия с магнием имеют меньшую плотность, более высокие прочность и коррозионную стойкость, чем чистый алюминий. Благодаря этим свойствам алюминиевомагниевые сплавы широко применяют в авиаконструкциях вместо чистого алюминия. Кроме того, алюминиевомагниевые сплавы в значительной степени упрочняются при обработке давлением в холодном состоянии (нагартовкой).
Наиболее распространенной труппой деформируемых алюминиевых сплавов являются дуралюмины (дюралюминий).
Дуралюмин представляет собой сплав на алюминиевой основе, в который в качестве специальных добавок обычно вводят медь, магний, марганец. Остальные элементы, присутствующие в этих сплавах, являются случайными примесями, попадающими в сплав в процессе производства. В наиболее значительных количествах в качестве примесей в дуралюмине находятся железо и кремний (примерно 0,5%). Марганец вводят в состав дуралюмина главным образом для повышения коррозионной стойкости и прочности сплава. Однако марганец ухудшает пластичность алюминия, поэтому содержание его должно быть не более 1%.
Медь и магний с кремнием способствуют упрочнению сплава при термообработке, так как они образуют соединения, растворимые в алюминии (например,Mg2Si). Повышение содержания магния в алюминии уменьшает пластичность сплава в горячем состоянии и затрудняет обработку его давлением. Поэтому и большинстве случаев дуралюмин содержит не более 0,8% Mg. У высокопрочного специального дуралюмина содержание магния достигает 1,8%. Ухудшение технологических свойств сплава в этом случае компенсируется более высокими механическими свойствами. Наиболее заметное влияние меди на повышение прочности сплава наблюдается при содержании ее в сплаве 4,5—5,0%· Дальнейшее повышение содержания меди не приводит к эффективному повышению прочности и одновременно резко снижает пластичность.
Железо при комнатной температуре практически нерастворимо в алюминии и присутствует в нем в виде самостоятельной фазы (Al3Fe). В жаропрочных алюминиевых сплавах железо в сочетании с никелем оказывает положительное влияние. В большинстве же случаев железо относится к вредным примесям в алюминии. (Кремний на механические и физико-химические свойства алюминия влияет так же, как и железо. Значительное влияние на свойства ряда алюминиевых сплавов оказывают даже незначительные добавки титана, натрия, церия.
К числу дуралюминов относятся сплавы Д1, Д1П, Д16, Д16П, Д18, Д19, Д19П. Механические свойства дуралюминов значительно повышаются под влиянием термической обработки, искусственного и естественного старения. Сплавы этой группы обладают и хорошими литейными свойствами и могут с успехом применяться при изготовлении крупных поковок и штамповок.
Для повышения прочности дуралюмины подвергают закалке. Сплавы при этом нагревают обычно до 500° С, а охлаждают в воде. Процесс естественного старения после закалки длится пять-семь суток. Отжигают дуралюмины при 1340—1370°С.
Из дуралюминов изготовляют детали каркаса самолетов, шпангоуты, стрингеры, лонжероны, элероны, стойки, заклепки и пр.
(Сплав, сохраняющийся в закаленном состоянии сколько угодно времени, т. е. стареющий только при искусственном нагревании, должен содержать минимальное количество меди и не иметь в структуре таких фаз, как CuA12 и Al2CuMg. К сплавам, стареющим только при искусственном нагревании, относится сплав АВ (авиль), содержащий в качестве основных компонентов, кроме алюминия, магний и кремний. Прочность сплава АВ в термически обработанном состоянии ниже, чем у дуралюмина, а пластичность в отожженном состоянии выше. Поэтому сплав АВ с успехом применяется для изготовления деталей глубокой вытяжкой.
Наиболее прочные из алюминиевых сплавов содержат в качестве основных добавок цинк, магний и медь, например сплав В95. Сплавы этого типа широко применяются в ответственных конструкциях в виде кованых и прессованных изделий и листов. Они имеют несколько меньшую пластичность, чем дуралюмин, и обладают худшей коррозионной стойкостью и жаростойкостью. Эти сплавы рекомендуется применять в конструкциях, работающих при невысоких температурах нагрева (примерно до 120°С). Сплавы обычно подвергают закалке в воде с последующим искусственным старением при 120—140°С.
Детали, работающие под действием температур 200—300°С, изготовляют из жаропрочных алюминиевых сплавов. Эти сплавы в отличие от других алюминиевых сплавов содержат специально вводимые присадки никеля и железа. К таким сплавам относятся АК4, АК4-1. Термическая обработка их состоит в закалке от температур 510—520°С с последующим искусственным старением..
По технологическим особенностям, назначению, физическим и коррозионным свойствам различают алюминиевые деформируемые сплавы коррозионностойкие, декоративные, заклепочные, ковочные, жаропрочные, со специальными свойствами, самозакаливающиеся. В зависимости от уровня прочности различают алюминиевые деформируемые сплавы низкой, средней и высокой прочности.
Сплавы низкой прочности (временное сопротивление менее 30 кГ/мм2), как правило, не упрочняются термической обработкой; применяют их обычно в отожженном состоянии. В эту группу сплавов входят технический алюминий, сплавы типа магналий (АМг1, АМг2, АМгЗ, АМг4, АМг5, АМг6П). По коррозионным свойствам сплавы этой группы в большинстве случаев относятся к коррозионностойким.
Сплавы средней прочности (временое сопротивление 30—45 кГ/мм2) применяют после закалки и естественного или искусственного старения. К этой группе относятся ковочные сплавы (АК4, АК4-1, АК6, АК8), дуралюмин (Д1, Д15, БД 17, Д19), магналий АМг6, сплавы АВ, АД35, Д20.
Сплавы высокой прочности (временное сопротивление >45 кГ/мм2) эффективно упрочняются термической обработкой, которая состоит в закалке и искусственном старении. К этой группе сплавов относятся сплавы В93, В95, а также сплавы средней прочности ДШ, Д19 и АК8 после соответствующей обработки.
У катаных изделий из сплавов Д16 и Д19 временное сопротивление можно повысить до 45 кГ/мм2 и более нагартовкой, искусственным старением и снятием плакировки. Сплав АК8 обладает высокой прочностью лишь в виде прессованных полуфабрикатов определенного сечения.
Наибольшей прочностью при комнатной температуре обладают сплавы В93 и В95, но они разупрочняются в результате длительного воздействия температуры порядка 100°С и более. Сплавы ДШ и Д19 имеют более низкую прочность при комнатной температуре, но они менее чувствительны к действию надрезов при повторных нагрузках, чем сплавы В93 и В95. Кроме того, они обладают и большей жаропрочностью. Сплав В95 применяют для нагруженных конструкций, работающих длительное время при температурах не более 100—120°C (обшивка, стрингеры, шпангоуты, лонжероны самолетов, силовой каркас некоторых клепаных строительных сооружений и т. п.). Сплав ДГб применяют для средненагруженных конструкций, работающих длительное время при температуре до 150°С, а сплав Д19 — для средненагруженных конструкций, работающих длительное время при температурах до 250°С. Сплав АК8 используют для изготовления нагруженных конструкций, работающих длительное время при температуре до 100°С (подмоторные рамы, бандажи колес железнодорожных вагонов, лопасти винтов вертолетов и т. п.).
Ковочные сплавы обладают высокими пластическими свойствами при температурах горячей деформации и хорошими литейными качествами. Из этих сплавов изготовляют слитки, поковки и штамповки самых крупных размеров и наиболее сложной формы. К числу ковочных относятся сплавы АК6, AK8, АК4, АК4-1, В93 и В97. Кроме того, в качестве ковочных материалов могут применяться сплавы АД, АД1, АМц, АМг1, АМг2, АМг3, АМг4, АМг5,АМг6, АД31, АД33, АД35, АВ, Д1, В95,Д20.
Сплавы АК4 и AK4-I1 имеют среднюю прочность при нормальной температуре и сравнительно высокую прочность при температурах до 200—250°С. Из сплава АК6 получают сложные по форме штамповки. Сплав АК8 более прочен, чем сплав АК6, но труднее поддается термообработке. Сплавы АКб и АК8 обычно применяют в закаленном и искусственно состаренном состоянии. Для повышения пластичности их подвергают естественному старению. В этом случае заметно снижаются прочностные характеристики сплава, особенно предел текучести.
Сплав БД 17 обладает средней прочностью при нормальной температуре и высокой прочностью при 200—250°С.
Из сплавов АК4, АК4-1, БД 17 изготовляют лопатки компрессоров, крыльчатки, диски и кольца турбореактивных и турбовинтовых двигателей и другие детали, работающие при высоких температурах. Сплав АК4-1 может применяться в виде листов.
Из сплава АК6 производят штампованные и кованые детали сложной формы и средней прочности (подмоторные рамы, фитинги, качалки, крепежные детали).
Из сплавов АК8 и В93 изготовляют высоконагруженные штамповки и кованые детали —подмоторные рамы, стыковые узлы, пояса лонжеронов. Из сплава В93, кроме того, изготовляют детали самолетов.
Все сплавы ковочной группы удовлетворительно свариваются точечной и роликовой сваркой и неудовлетворительно сваркой плавлением, они хорошо обрабатываются резанием.
Заклепочные сплавы имеют высокое сопротивление срезу и обладают способностью выдерживать значительную холодную деформацию. К этой группе относятся сплавы Д18, В65, В94. В зависимости от состава заклепочный полуфабрикат может расклепываться либо в свежезакаленном, либо в состаренном состоянии. При массовом изготовлении предпочтение отдается заклепкам, которые можно ставить в состаренном состоянии. Для силовых конструкций наибольшее применение имеют заклепки из сплава В65, для менее нагруженных конструкций, требующих повышенной коррозионной стойкости, — из сплава АМг5П, а для конструкций, подвергающихся нагреву, —из сплава Д19П.
Жаропрочные сплавы отличаются высокими прочностными характеристиками при повышенных температурах. Их применяют в искусственно состаренном состоянии. К этой группе относятся сплавы ДГб, ДШ, БД 17, АК4, АК4-1, Д20.
Сплав Д20 имеет относительно высокие прочностные характеристики при 200—ЗО0°С. Он не содержит в качестве легирующего элемента магний, что придает ему некоторые специфические свойства: высокий эффект упрочнения при закалке, практически постоянные свойства при вылеживании при комнатной температуре (отсутствует естественное старение). Поэтому его целесообразно применять в конструкциях в искусственно состаренном состоянии. В закаленном и отожженном состояниях сплав Д20 допускает сложные технологические деформации. Он может закаливаться в кипящей воде без потери свойств, что позволяет уменьшать внутренние напряжения в деталях и устранять их поводку в процессе механической обработки. Он не склонен к коррозии под напряжением в любых полуфабрикатах и в любых состояниях термической обработки. Однако этот сплав имеет пониженную общую коррозионную стойкость в связи с относительно высоким содержанием меди. Сплав Д20 обладает высокой пластичностью в горячем состоянии, подвергается ковке и штамповке при 400—460°С. Термическая обработка сплава состоит в закалке с температуры 535 ±5°С и искусственном старении при 165—175°С. Из него изготовляют поковки, а также штамповки сложной формы, катаные листы и прессованные полуфабрикаты.
Сплавы АК4 и АК4н1 применяют для кованых и штампованных деталей, работающих при температурах до 250°С.
Коррозионностойкие сплавы обладают высоким сопротивлением общей коррозии и коррозии под напряжением в атмосферных условиях и в морской воде. Они, как правило, имеют низкую и среднюю прочность. К коррозионностойким сплавам относятся технический алюминий (АД и АД 1), сплавы алюминия с магнием, с относительно низким содержанием магния (АМг1, АМ;г2, АМгЗ, АМг4), сплавы алюминия с магнием и кремнием (АДЭ1), сплавы алюминия с марганцем (АМц). При определенных условиях к коррозионностойким сплавам могут быть отнесены сплавы АМг6В. АМг6, АДЗЗ, АД35.
Технический алюминий марок АД и АД1 применяют в тех случаях, когда элементы конструкций не несут нагрузок и требуют материалов с высокими пластическими свойствами, хорошей свариваемостью, высоким сопротивлением коррозии и высокой тепло- и электропроводностью.
Сплавы АМг1, АМг2, АД31, АМг4 характеризуются высокой коррозионной стойкостью, хорошим декоративным видом и отличной полируемостью. Их применяют в мало- и средненагруженных сварных и клепаных конструкциях. Из указанных сплавов, а также из сплавав АД и АД1 изготовляют трубопроводы, витражи, электродро- воды, двери, оконные рамы, корпусы часов, ювелирные поделки, палубные надстройки морских и речных судов, баки и т. п.
Сплавы АМц и АМг3 применяют для сварных малонагруженных конструкций, которые должны характеризоваться высокой коррозионной стойкостью, например баки для хранения бензина и керосина.
Сплавы АМг5В и АМг6 используют в средненагруженных сварных и клепаных конструкциях, от которых требуется высокая коррозионная стойкость.
Сплавы АДЗЗ и АД35 применяют в средненагруженных конструкциях (преимущественно клепаных и клееных), от которых требуется повышенный предел текучести и высокая коррозионная стойкость, а также высокая сопротивляемость коррозионной усталости (лопасти вертолетов, рамы и кузовы вагонов, сварные баки, подвесные нагруженные потолки, перегородки судов, электромачты, трубопроводы, стрелы экскаваторов, лифты, узлы подъемных кранов и буровых установок, корпусы судов и др.).
Самозакаливающиеся сплавы обладают свойством закаливаться при охлаждении на воздухе. Это свойство обеспечивает возможность получения высокой прочности сварного шва без специальной закалки сварной конструкции. Самозакаливающимся является сплав типа В92. Максимальные механические свойства он приобретает после закалки и искусственного старения при 100°С в течение 96 ч. В качестве присадочного материала при сварке сплава рекомендуется применять проволоку В92св. Естественное старение шва без закалки продолжается 30 суток. Зону сварного шва рекомендуется сохранять несколько утолщенной.
Литейные алюминиевые сплавы. Эти сплавы условно могут быть высокой и средней прочности, жаропрочные и коррозионностойкие.
Высокопрочные и средней прочности алюминиевые литейные сплавы АЛ2, АЛ4, АЛ9, а также сплав АЛ41 применяют в модифицированном состоянии.
Сплав АЛ2 обладает очень хорошими литейными свойствами. По механическим свойствам он относится к сплавай средней прочности, обладает удовлетворительной коррозионной стойкостью во влажной атмосфере и морской воде, удовлетворительно сваривается аргоно-дуговой сваркой. Этот сплав используют для литья деталей сложной формы, не испытывающих больших нагрузок.
Сплав АЛ4 предназначен для изготовления крупных и средних деталей, по дергающихся значительным нагрузкам и работающих под давлением. Он обладает хорошими литейными свойствами, относительно высокими механическими свойствами и удовлетворительной коррозионной стойкостью во влажной атмосфере и морской воде, хорошо обрабатывается резанием и удовлетворительно сваривается газовой и аргоно-дуговой сваркой. Этот сплав обладает повышенной склонностью к образованию газовой пористости. Режим термической обработки сплава АЛ4 состоит в следующем: нагрев до 535 ±55С, охлаждение в воде при 500—100°С, старение при 175±5°С в течение 15 ч. Сплав АЛ9 относится к сплавам средней прочности, обладает хорошими литейными свойствами. Применяют его для деталей средней нагруженности, но сложной конфигурации, а также для деталей, работающих под давлением. Сплав склонен к естественному старению, через один-два месяца механические свойства закаленного сплава приближаются к свойствам закаленного и искусственно состаренного. Сплав обладает удовлетворительной коррозионной стойкостью в морской воде, удовлетворительной обрабатываемостью резанием, повышенной герметичностью. Он сваривается газовой и аргоно-дуговой сваркой.
Повышенной герметичностью обладают практически все сплавы рассматриваемой группы, т. е. они обладают способностью выдерживать гидравлическое давление 150—200 ат.
Литейные жаростойкие алюминиевые сплавы предназначены для работы при высоких температурах. Обычно в качестве литейных алюминиевых материалов, работающих при повышенных температурах, применяют сплавы АЛ1, АЛ4, АЛ6, АЛ 10В, АЛ25, АЛ 26, АЛ19, АЛ20, АЛ21. По степени возрастания жаропрочности сплавы для литых поршней располагаются в следующем порядке: АЛ10В, АЛ26, АЛ26, АЛ1, а по степени технологичности — АЛ1, АЛ10В, АЛ 26, АЛ25. Сплавы АЛ26 и АЛ26 характеризуются наиболее низким коэффициентом линейного расширения, что позволяет создавать при их применении малые зазоры между поршнем и цилиндром в поршневых двигателях.
Наиболее высокой жаропрочностью и повышенной герметичностью обладают сплавы типа AЛ21. Сплав АЛ19 обладает наиболее высокими механическими свойствами при комнатной температуре и повышенной жаропрочностью. Герметичность отливок из этого сплава пониженная.
Для кратковременного использования при высоких температурах могут быть применены сплавы типа АЛ8, обладающие высокой прочностью, так как за короткое время значительное разупрочнение этих сплавов не успевает произойти.
Большинство сплавов эвтектического типа или с содержанием эвтектики > 35% имеют более высокую жаропрочность в литом состоянии, чем в термически обработанном. Сплавы типа силумин обладают большей жаропрочностью в немодифициро- ванном состоянии, чем в модифицированном.
Литейные алюминиевые сплавы обычно имеют более высокое содержание легирующих элементов, чем деформируемые. Термическая обработка их, как правило, состоит в закалке с последующим искусственным старением. Температура нагрева литейных сплавов под закалку обычно выше, чем у деформируемых, а выдержка при температуре закалки более длительная.
markmet.ru