Антикоррозийное покрытие оборудования – Антикоррозийные покрытия
alexxlab | 07.09.2019 | 0 | Вопросы и ответы
Антикоррозийные покрытия
Автор: Гудков Денис, специально для www.EquipNet.ru
Фотографии с сайтов metaprom.ru, acrossteel.ru
Потребность в применении антикоррозийных покрытий металлических конструкций, предназначенных к применению в различных областях народного хозяйства (строительство, производство, быт и т.д.), колоссальна. В течение года, согласно оценкам экспертов, от коррозии портится 20 – 30% годового объема производства черных металлов в России. По другим оценкам, ущерб от коррозии составляет 2 – 4% от валового национального продукта каждого государства.
Коррозия – химический процесс окисления металла, который протекает самопроизвольно в условиях окружающей среды под действием кислорода воздуха и воды и приводит к разрушению металлических изделий. Скорость коррозии напрямую зависит от влажности воздуха и температуры. Для предотвращения коррозии металлических изделий используют их
В настоящее время наиболее современной технологией очистки металлической поверхности является ее пескоструйная или дробеструйная обработка с помощью абразивоструйного оборудования. Процесс позволяет удалять с поверхности материала элементы первичной коррозии, окалину, нагар, остатки старого покрытия (металлического или лакокрасочного). При помощи сжатого воздуха поток абразива с огромной скоростью выбрасывается на обрабатываемую поверхность, в результате чего осуществляется ее очистка. На данный момент на рынке представлено мобильное и стационарное оборудование российских и иностранных производителей.
Далее очищенную металлическую поверхность покрывают тонким слоем антикоррозийного покрытия. В настоящее время существует несколько технологий нанесения металлического покрытия (никеля, хрома, цинка, аллюминия и др.) на различные стальные заготовки. Для никелирования металлических деталей сложной конфигурации часто используют метод их электрохимической обработки, основанный на осаждении слоя используемого металла из раствора на поверхности изделия. Малогабаритные установки химического никелирования УХН-20 или -100, производимые ЗАО АКБ «Экспресс-Волга» (г. Саратов), или Установка химического никелирования ГУ002М, производимая ООО «РПТИ» (г. Рязань), позволяют получать покрытия толщиной от 3 до 18 мкм. Производительность таких устройств составляет 0,2 – 6 м2/час, а твердость получаемого покрытия достигает 950 кг/мм2.
Нанесение цинковых или алюминиевых покрытий можно проводить способом электродуговой металлизации, например, с использованием установки «УЭМ» компании «Пневмотехника». В данную установку по специальным каналам непрерывно подаются две проволоки (диаметром 1,5—3,2 мм), между концами которых возбуждается электрическая дуга, в результате чего происходит плавление металлов. Расплавленный металл распыляется в виде жидких капель на поверхность напыляемой детали с помощью сжатого воздуха. Установка позволяет наносить различные металлические покрытия (в том числе, состоящие из двух металлов) по ГОСТу 9-304-81 с мощностью распыления от 9 до 30 кг/ч в зависимости от используемого материала. Толщина напыляемого слоя достигает 0,5 – 15 мкм, прочность сцепления – 3,0 – 5,0 кг/мм2, а пористость покрытия составляет 5 – 20%. Срок службы получаемых изделий увеличивается до 50-ти лет, что значительно сокращает затраты на эксплуатацию и ремонт различных металлоконструкций.
Методы газопламенного и плазменного напыления защитного слоя на стальную поверхность имеют схожие принципы со способом электродуговой металлизации. В их основе лежит распыление расплавленных металлов сжатым воздухом. При этом плавление материалов достигается в случае газопламенного метода в пламени газовой горелки (рабочие газы ацетилен, пропан или водород), а в случае плазменного метода – в потоке дуговой плазмы (рабочие газы аргон или азот). Процессы напыления хорошо поддаются автоматизации. Оборудование доступно как зарубежных, так и отечественных производителей, например, ООО «Нейтрино», ООО «Термал-Спрей-Тек», ООО ЦЗК «ЭГО» и др., характеристики получаемых покрытий, а также характеристики оборудования, в целом, схожи.
Таблица. Характеристики антикоррозийных покрытий, полученных различными методами, и оборудования.
Метод | Электродуговой | Газопламенный | Плазменный |
Характеристики покрытия | |||
Пористость, % | 5 – 20 | 05 – 12 | 4 – 8 |
Прочность сцепления с основой (адгезия), кг/мм2 | 3,0 – 5, | 2,5 – 5,0 | 5,0 – 8,0 |
Толщина слоя, мм | 0,5 – 15 | 0,5 – 10 | 0,05 – 5 |
Характеристики оборудования | |||
Потребляемая мощность, кВт | 16 – 20 | 0,3 | 40 – 50 |
Расход газов, л/мин | воздуха: 2000 – 2500 | ацетилена: 10 – 30, кислорода: 13 – 40 | аргона: 30 – 70, азота: 5 – 10 |
Производительность, кг/ч | 12 – 45 | 3 – 10 | 2 – 5 |
ЗАО НПП «Высокодисперсные Металлические Порошки» (г. Екатеринбург) предлагает метод «холодного» цинкования стальных изделий. В основе данного метода лежит использование лакокрасочных композиций, содержащих высокодисперсный порошок цинка в качестве пигмента. Компания предлагает широкий выбор покрытий (Цинотан, Цинол, Цвэс, ЦИНЭП, ЦИНОТЕРМ и др.), имеющих различную основу: полиуретановую, полимерную, кремнийорганическую, эпоксидную и др. Кроме цинкнаполненных материалов компания производит композиции на основе алюминиевой пудры: АЛПОЛ, АЛЮМОТАН, АЛЮМОТЕРМ, ПАЭС и на основе железной слюдки: ФЕРРОТАН, ИЗОЛЭПК.
Композиции наносятся на поверхность стальных изделий традиционными лакокрасочными способами в интервале температур от -15 до +400С, время высыхания одного слоя при 200С составляет не более 30 минут. Образующиеся покрытия с высоким содержанием цинка дают не только эффективную катодную защиту стали, но и барьерную, характерную для обычных лакокрасочных покрытий. При окислении металлического порошка, согласно заявлениям специалистов компании, в микропорах защитного покрытия образуются нерастворимые продукты коррозии цинка, препятствующие доступу коррозионно-активных агентов к стали, в результате чего скорость окисления цинка в цинкнаполненных покрытиях ниже по сравнению с горячеоцинкованными покрытиями, а срок их службы соответственно более длительный. Прогнозируемый срок службы таких систем защиты в зависимости от условий эксплуатации составляет от 8 до 20 лет и более.
Несомненно, традиционный способ защиты стальных изделий от коррозии – нанесение обычных лакокрасочных покрытий (краски, пасты, грунт и т.п.) продолжает пользоваться популярностью.
На сегодняшний день все больше потребителей стальных изделий обращаются в компании, специализирующиеся на защите металлических конструкций от коррозии. Такая практика, во-первых, позволяет осуществлять действительно качественную обработку металла с привлечением высококвалифицированных специалистов и высокотехнологического оборудования. Во-вторых, автоматизация процессов очистки поверхности изделия и нанесения на нее защитного слоя значительно увеличивает производительность труда и приводит к снижению финансовых затрат. Лидирующей компанией в области антикоррозийной обработки металлических изделий на российском рынке можно назвать ОАО «Инпром».
Каждый из описанных методов находит свое применение в той или иной области, а совокупное применение нескольких методов защиты позволяет достичь максимальной защиты стальных изделий от коррозии.
www.equipnet.ruКакое оборудование нужно для антикоррозийной обработки?
Многие думают, что нанесение антикоррозийного покрытия – это сложный, трудоемкий процесс, требующий использования различного профессионального оборудования, к которому не у каждого есть доступ. На самом деле, подготовить поверхность металла и нанести антикоррозийный состав возможно при помощи подручных средств. Инструменты, которые понадобятся – найдутся в любом хозяйственном магазине.
Но, если у вас есть доступ к профессиональному оборудованию, то оно существенно облегчит вам задачу в подготовке поверхности и нанесении состава для холодного цинкования. Процесс пройдет легче, потребует меньше усилий и займет гораздо меньше времени.
Мы подскажем – какое оборудование сможет вам пригодиться для антикоррозийной обработки.
Пескоструйный аппарат
Пескоструйную очистку так же называют абразивной или абразивоструйной.
Пескоструйный аппарат поможет быстро и качественно подготовить поверхность металла к нанесению – очистить ее от грязи, старых покрытий, появившейся ржавчины и даже окалины.
Аппарат работает при помощи сухой абразивной смеси, которая подается под большим давлением воздуха из специального «пистолета».
В качестве абразива используется просеянный песок и дробь с показателем влажности, не превышающей 2%. Размер отверстий в приспособлении для просеивания песка может составлять от 1 до 1,2 мм.
Воздух под давлением подается по шлангу из компрессорной установки в пескоструйный аппарат, в резервуаре которого происходит его соединение с абразивной массой. Далее соединение выдувается в пистолет аппарата, и с помощью высокого давления подается на рабочую поверхность.
Внимание! Неосторожная работа с пескоструем может привезти к деформации металлической конструкции. Не рекомендуется применять давление более 4 атмосфер. |
В ходе абразивной обработки насадка для пескоструйной абразивной очистки поверхности деформируется под воздействием песка, расход рабочего диаметра в 1,5-2 часа – это примерно половина срока службы насадки. Так что будьте готовы к частой замене насадке, особенно если у вас большая площадь конструкции.
По завершению абразивной очистки с обработанной поверхности удаляют остатки песка и пыли, путем обдувания простым воздухом. Такую очистку рекомендуется проводить в специальной камере или отдельном помещении, специально приспособленном для подобных работ.
Если вам необходимо соответствовать ГОСТу, то подготовка металлических материалов к окрашиванию регламентируется в ГОСТ 9.402-2004.
В зависимости от поставленной задачи, пескоструйная очистка с помощью мойки высокого давления может осуществляться с применением разных степеней очистки.
Применение поверхностной абразивной обработки деталей из металла и металлических конструкций фасадов, позволяет получить поверхностям средний показатель чистоты. То есть, на обработанных объектах, при визуальном осмотре, все же можно будет обнаружить окалины и пятна.
Глубокая абразивная обработка дает возможностью полностью исключить присутствие на металлических поверхностях, подвергшихся абразивной очистке, даже следы бывшей ржавчины или окалин. В данном случае металлическая поверхность может быть зачищена добела.
Легкая пескоструйная обработка металла позволяет удалить с его поверхности ржавые пятна и отслоившиеся окалины, в результате при поверхностном осмотре объект будет выглядеть сравнительно чистым.
Профессионалы могут проводить с помощью пескоструя и обезжиривание поверхности.
Пескоструйные аппараты бывают нескольких видов: пневмораспылители пескоструйные эжекторного типа, пескоструйные установки эжекторного типа, пескоструйные установки напорного типа и пескоструйные камеры.
Другие способы очистки с помощью оборудования
Также для очистки поверхности металла могут применяться аппараты струйной очистки сжатым воздухом или водой под высоким давлением. Их можно подразделить на несколько видов.
Абразивная струйная очистка сжатым воздухом
Абразивная струйная очистка сжатым воздухом осуществляется при подаче абразива в поток воздуха и направлении образующейся воздушно-абразивной смеси с высокой скоростью из сопла на очищаемую поверхность. Абразив может быть впрыснут в воздушный поток из емкости, находящейся под давлением, или увлечен этим воздушным потоком в процессе всасывания из емкости, не находящейся под давлением. Этим способом очищают поверхности с помощью дробеструйных аппаратов.
Абразивная струйная очистка с вакуумом или всасывающей головкой
Этот метод аналогичен абразивной струйной очистке сжатым воздухом с той разницей, что сопло заключено внутри всасывающей головки, которая герметично закреплена на стальной очищаемой поверхности и служит для сбора отработанного абразива и загрязнений. В качестве альтернативного варианта воздушно-абразивный поток может быть подан на металлическую поверхность при использовании пониженного давления во всасывающей головке, т.е за счет эжекции. Этот метод имеет название вакуум-бластинг.
Абразивная струйная очистка с впрыскиванием влаги
Этот метод аналогичен абразивной струйной очистке сжатым воздухом с той разницей, что в воздушно-абразивный поток добавляют незначительное количество жидкости (обычно чистую пресную воду), что создает метод струйной очистки, при котором не образуется пыли в диапазоне размера взвешенных частиц менее 50 мкм. Расход воды составляет 15-25 л/ч.
Влажная абразивная струйная очистка со сжатым воздухом
Этот метод аналогичен абразивной струйной очистке сжатым воздухом и отличается тем, что в поток добавляют жидкость (обычно чистую, пресную воду). При этом очистка поверхности производится потоком воды, воздуха, абразива. При влажной абразивной очистке используют смесь абразива с водой в соотношении от 1:2 до 1:6.
Суспензионная струйная очистка
Суспензионная струйная очистка заключается в подаче дисперсии мелких абразивных частиц в воде или другой жидкости на очищаемую поверхность.
Струйная очистка жидкостью под давлением
Абразив (или смесь абразивов) вводят в поток жидкости (обычно чистой пресной воды), и этот поток направляют через сопло на очищаемую поверхность. Поток представляет собой, главным образом жидкость, находящуюся под давлением, а количество добавленных абразивов, как правило, меньше, чем в случае влажной абразивной струйной очистки сжатым воздухом.
Этот метод основан на воздействии кинетической энергии высоконапорной водяной струи на обрабатываемую поверхность. При этом струя воды позволяет удалять с поверхности загрязнения и отложения любой физической природы и химического состава: ржавчину, консервационные смазки, лакокрасочные покрытия, битум, смолы, нагар, окалину и т.д. Введение в струю абразива позволяет легко удалять поверхностные слои металла.
Давление воды зависит от типа удаляемых загрязнений, таких как водорастворимые вещества, рыхлая ржавчина и красочные покрытия со слабым сцеплением. Если в процессе очистки использовались поверхностно-активные вещества, необходимо ополаскивание чистой, пресной водой.
Методы водной струйной очистки
Водная струйная очистка может быть высокого давления – от 70 до 170Мпа и сверхвысокого давления – свыше 170Мпа. Гидроструйную очистку при высоком давлении называют «гидро-джеттинг».
- Гидроджеттинг под сверхвысоким давлением (более 170 МПа) применяется для полного удаление всех Пк и ржавчины. Результат сравним с сухим бластингом, но на поверхности после сушки наблюдаются проблески ржавчины.
- Гидроджеттинг под высоким давлением. (70 −170 МПа) позволяет удалить большинство красок и продуктов коррозии. Магнетиты (черные окислы) и прочно держащиеся покрытия могут остаться, хотя они с некоторыми трудностями также поддаются удалению.
- Гидроочистка под средним давлением (35-70 МПа) позволяет удалить непрочно держащиеся краску, ржавчину, загрязнения. Но черный железный оксид (магнетит) останется. Однородная поверхность не может быть получена.
- Гидроочистка под низким давлением (до 35 МПа) позволяет удалить соли, загрязнения, шелушащуюся краску. В основном это промывка поверхности.
- Гидроочистка под низким давлением с применением абразива. 0,6-0,8 МПа. Скорость очистки — 10-16 м²/час в зависимости от удаляемого материала. Позволяет уменьшить расход абразива, пылеобразование, избежать образования искр. Результат сравним с сухим бластингом, но на поверхности после сушки наблюдаются проблески ржавчины.
В настоящее время данные технологии активно используются там, где необходимо быстро, качественно и безопасно выполнить работы по очистке и подготовке поверхности. Такое оборудование многофункционально и позволяет выполнять широкий спектр работ в различных отраслях промышленности.
Агрегаты высокого и сверхвысокого давления представляют собой высоко-эффективное, экологически чистое и энергосберегающее оборудование на базе водоструйных технологий высокого давления. Чистка металлической поверхности высоким и сверхвысоким давлением водяной струи не вызывает нарушений в структуре металла.
Воздействие водяной струи высокого или сверх высокого давления на поверхность можно подразделить на:
- Гидравлическое – однородная струя воды;
- Гидродинамическое – удары струей по поверхности;
- Гидроабразивное – смешанная струя воды и абразива.
Покрасочное оборудование
Кром помощи в очистке поверхности, упростит и ускорит работу покрасочное оборудование. В окраске различных поверхностей используется два типа оборудования: аппараты безвоздушного распыления и пневматические (воздушные) распылители.
Безвоздушная покраска
Самыми распространенными способами безвоздушной окраски является применение окрасочного пистолета, а так же аппаратов безвоздушного распыления.
Принцип работы способа безвоздушного распыления – применение воздуха, как тормозящей силы, снижающей скорость потока, а распыление краски происходит под большим давлением.
Метод считается более выгодным, чем воздушное распыление, так как экономится краска и меньше загрязняется атмосфера. При таком способе нанесения используется меньше растворителя, а также уменьшается количество слоев, за счет увеличения толщины каждого слоя. Чтобы распылять покрытие таким способом, не нужно долго обучаться, процесс достаточно прост и понятен. В результате покраска происходит быстрее, все вокруг пачкается меньше, а краска экономится.
Оборудование для безвоздушной покраски выгодно применять там, где нужно покрыть большую площадь поверхности. Методика просто незаменима в покраске крупных конструкций промышленных масштабов. Очень часто безвоздушное распыление применяется при антикоррозийной обработке автомобилей, крыш, потолков, стен, фасадов и других конструкций из металла.
Современные аппараты отличаются простотой использования, безопасностью в обслуживании и бесшумной работой. Кроме того, такое оборудование очень мобильно и поэтому легко транспортируется в нужное место. Несмотря на то, что для этого метода используется различные аппараты, все они имеют общий принцип работы и схожую конструкцию, так что вы быстро научитесь работать с любым аппаратом.
Обычно, такой аппарат состоит из: краскопульта, окрасочного безвоздушного сопла, насоса мощностью от 22 до 500 атмосфер и специальных шлангов, рассчитанных на работы под высоким давлением.
Насос в устройствах используется поршневого или мембранного типа, он перекачивает краску по направлению к распылителю. Для работы насоса используется электрический или пневматический мотор, а также бензиновый двигатель – в особо крупных аппаратах. Далее при помощи насоса антикоррозийные составы под высоким давлением проходят через сопло небольшого диаметра. Это приводит к распылению краски по поверхности металла в виде очень мелких частичек. Для человеческого глаза это выглядит, как сплошное, качественное покрытие.
Пневматическое (воздушное) распыление
Пневматическое распыление – самый распространенный вид нанесения различных лакокрасочных материалов. Так как антикоррозийные средства и составы для холодного цинкования схожи по структуре с красками, то пневматическое распыление помогает и тут быстрее и качественнее справится с работой.
Пневматическое распыление подразделяют на несколько видов.
- С подогревом покрасочного материала
Применяется в основном для экономии на растворителях. При нагреве, многие ЛКМ становятся более жидкими и не нуждаются в разбавлении. Однако, такой способ подходит далеко не всем краскам и составам, а только тем, кто не меняет свою структуру при нагревании. Для большинства качественных антикоррозийных покрытий и составов для холодного цинкования этот способ нанесения не подходит, так как не рекомендуется их нагревать.
- Без подогрева состава
Пневматические распылители без нагрева ЛКМ подходят для применения практически любых красок и составов. Из минусов этого способа можно назвать большой расход растворителя для разбавления, расход краски на окружающие поверхности. Необходимы условия хорошей вентиляции и система очистки воздуха.
Аппарат пневматического распыления обычно называют установкой, которая состоит из: масловлагоотделителя, централизованной линии сжатого воздуха или передвижного, переносного компрессора, краскопульта, шлангов для подачи краски и сжатого воздуха, красконагнетательного бака с перемешивающим устройством и редуктором. Установки применяются разные, каждая имеет свои плюсы и минусы. Так большие установки массой 140-170 кг обладают большой мощностью и производительностью, а их более компактные варианты мобильнее, меньше весят, но имеют мощность в десятки раз меньше. В любом случае, переносные аппараты всегда выгоднее стационарных.
Краскораспылители
Если нет возможности или необходимости использовать тяжелое пневматическое оборудование, можно воспользоваться стандартными краскораспылителями.
Краскораспылители так же подразделяют на:
- Высокого давления – от 3 до 6 кгс/см2;
- Низкого давления – 2,5-3 кгс/см2.
Также краскораспылители бывают внутреннего и наружного смешивания. Подача краски в распылитель может происходить из маленького бачка, прикрепленного прямо к краскопульту, который называют «стаканом», а также может подаваться через шнур из красконагнетательного бака. «Стаканы» выгоднее использовать, если нужно покрывать небольшой или труднодоступный участок, они более мобильны. А большие баки – для больших площадей.
Электроокрашивание
Достаточно новый и пока не очень распространенный способ окрашивания с помощью распыления в поле высокого напряжения. Его суть заключается в переносе в электрическом поле высокого напряжения заряженных частиц краски. Электрическое поле создается между двумя электродами, один из которых – изделие, которое окрашивается, а другой – краскораспылительное коронирующее устройство. Изделие заземляют, а к краскораспылителю подключают высокое напряжение (зачастую отрицательное). Лакокрасочный состав подается к краскораспылителю (на коронирующую кромку), где отрицательно заряжается, и под действием электрических сил распыляется. Поток распыленного лакокрасочного материала направляется к окрашиваемому изделию и осаждается на его поверхности. Электроокрашиванием наносят защитные слои как на металлические, так и на неметаллические поверхности.
Ручные краскораспылители характеризуются достаточно маленькой производительностью, хотя имеют ряд преимуществ: небольшой расход лакокрасочного материала (отсутствие его потерь), возможность окрашивать изделия решетчатой структуры и т.д.
На стационарных установках окрашиваются детали достаточно простой формы: корпуса стиральных машин, кузова автомобилей, корпуса различных приборов, электродвигателей, холодильников и т.п.
Используя перечисленное оборудование, вы сможете сделать антикоррозийную обработку легче, быстрее и качественнее. Но, каждый наш состав для холодного цинкования не нуждается в обязательном использовании сложного оборудования, может быть применен с помощью элементарных инструментов.
Есть вопросы по выбору состава? Обращайтесь в представительство в вашем городе:
в Санкт-Петербурге: +7 (812) 603-41-53, +7 (921) 927-58-47
в других городах: 8 (800) 707-53-17
e-mail: [email protected]
terazinc.ru
Антикоррозийные защитные покрытия металла: виды, составы
Коррозия – это неизменный процесс разрушения металла, который происходит в результате взаимодействия железа или сплавов металлов с окружающей средой. При столкновении с молекулами воздуха или воды происходит медленное и постепенное ржавление всех металлических изделий. Через некоторое время данные изделия приходят в негодность. Но этого можно избежать. Если использовать специальное антикоррозийное покрытие.
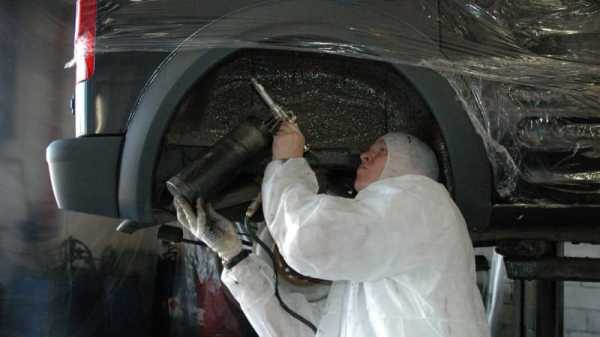
Что же происходит с металлом при его соединении с агрессивными средствами, при длительном соприкосновении с водой:
- Он теряет свои твердые свойства и износостойкость.
- Разрушается структура металла.
- Изменяется его цвет.
Поэтому в строительстве используют различные антикоррозийные покрытия для защиты его от деформации.
Зачем нужна антикоррозионная защита
Теперь более подробно разберем зачем нужна антикоррозионная защита. Особенно важна такая защита для автомобилей. Так как противогололедные присадки, которыми посыпают трассу во время гололеда зимой, различные дефекты и царапины, образующиеся в результате попадания камешков и песчинок во время проезда по сельским дорогам, существенно снижают срок службы машины. А именно они позволят проникнуть ржавчине внутрь металла и разъесть его. В таких случаях защитные покрытия очень важны.
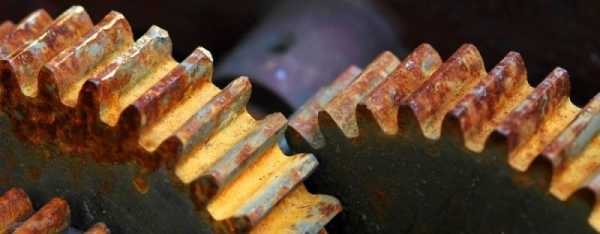
Коррозия
А стальные и чугунные предметы со временем теряют герметичные свойства, теплопроводность и прочность без должного антикоррозионного покрытия. Они становятся совершенно непригодны для проведения работ с ними в дальнейшем. Учеными было подсчитано, что около десяти процентов всего добываемого на земле металла уходит затрачивается на то, чтобы залатать дыры, которые появляются из-за промедления нанесения антикоррозионного покрытия. Или вообще не наносится антикоррозионная защита.
Помимо бытовых аварий, коррозия металлов может спровоцировать и экологические катастрофы. Из износившихся трубопроводов в любое время могут вытекать тонны нефти и газа, которые естественно будут загрязнять атмосферу земли, уничтожая флору и фауну.
Вот почему так важно вовремя покрывать все металлические изделия антикоррозионными покрытиями. Конечно, полностью нельзя избежать появления ржавчины и старения стали, железа, чугуна, но можно приостановить это негативное влияние.
В наше время борьба с коррозией была разделена на несколько групп, в которых используются различные методы сопротивления ржавлению.
- Защищают изделия с помощью электрохимии.
- Выпускаются устойчивые к ржавлению материалы.
- Вводятся специальные соединения в среду ржавления.
- Эксплуатируют детали и конструкции из металлов правильно, не подвергая насильственному разрушению.
- Мастика против коррозии
- Обработанные мастикой трубы
Для этого были созданы специальные средства, антикоррозийные материалы и методы их нанесения на металлы.
Методы антикоррозийной защиты
Антикоррозионное покрытие металла защищает от воздействия негативной атмосферы. Методы нанесения таких покрытий тоже различаются как по составу, так и по способу их нанесения.
Самым распространенным способом защиты является покраска антикоррозионными средствами. Жидкое антикоррозионное вещество наносится на поверхность, которую необходимо защитить, с помощью кисти, валика или распыляется. А после того, как краска высохнет, образуется пленка, которая плотно прилегает к изделию и защищает его от коррозии. В использовании такого метода есть некоторые минусы. Например, краска способна пропускать влагу или кислород, которые вызывают коррозию. Поэтому перед тем, как провести покраску, поверхность прежде всего грунтуют.
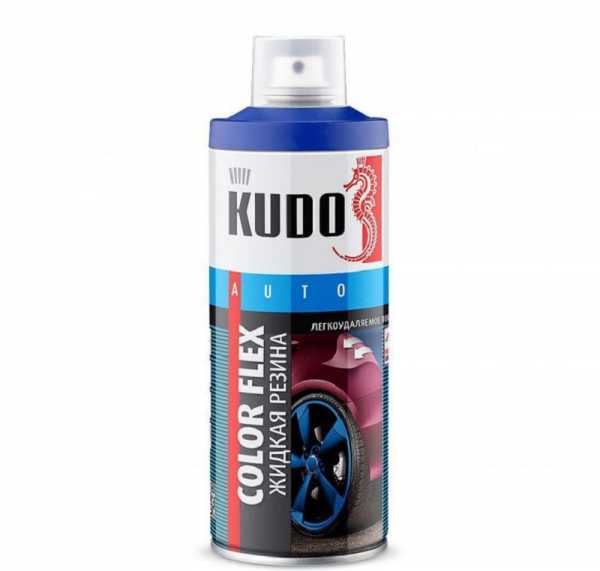
Антикоррозийное средство KUDO
Итак, вторым методом является грунтовка. Она также наносится на материал, как и краска. Но защищает его гораздо сильнее, так как содержит в себе мелкодисперсный порошок цинка, в который добавлен оксид цинка. Вступая во взаимодействие с железом, такое вещество защищает его от коррозии.
Другим распространенным методом защиты от ржавления металлических конструкций является нанесение металлических антикоррозийных покрытий. Такой способ представляет собой гальванизацию, плазменное напыление или сверхзвуковое, электроискровые способы покрытия. Такая защита более надежна. Она не вызывает тяжелых негативных последствий при повреждении конструкции.
Однако при использовании данного метода необходимо еще и учитывать совместимость элементов, из которых изготовлена продукция.
Еще одним способом для защиты металлических изделий от влаги и кислорода является керамическое покрытие. Но этот метод применяется только при изготовлении высокотемпературных конструкций. Потому что он требует сильного нагрева для создании высокого уровня адгезии керамики к изделию.
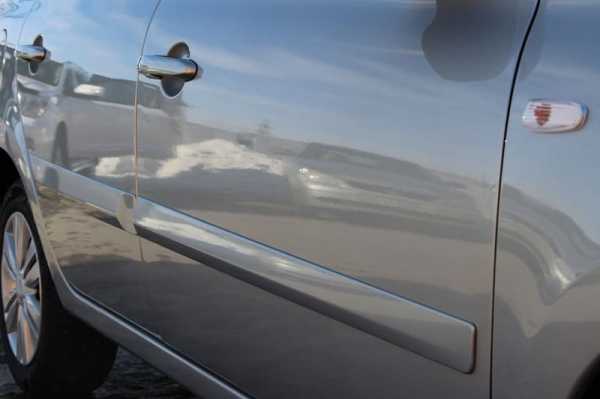
Антикоррозийное керамическое покрытие на автомобиле
Виды антикоррозийных покрытий
Типов защиты против ржавчины в современном мире очень много. К видам таких антикоррозионных покрытий относятся:
- Эмаль три в одном. Название этой краски означает, что ее можно наносить прямо на ржавчину. Рекомендуется очистить только верхний, рыхлый слой коррозии.
- Грунтовка. Это специальное антикоррозионное покрытие применяется для металла, точнее используется для предупреждения ржавления перед нанесением слоя обычной краски. Этот вид делится на два подвида:
- Для обычных поверхностей. К ним относятся такие поверхности, которые имеют отличную шероховатость, чтобы грунт мог хорошо сцепиться с поверхностью.
- Для проблемных поверхностей. К ним относят изделия из дюралюминия, алюминия, меди, из сплавов, изготовленных из антикоррозийных материалов.
- Протекторные грунтовки. В таких покрытиях присутствует цинковый порошок, который защищает конструкцию.
- Изолирующие грунтовки. Они защищают сталь от проникновения влаги.
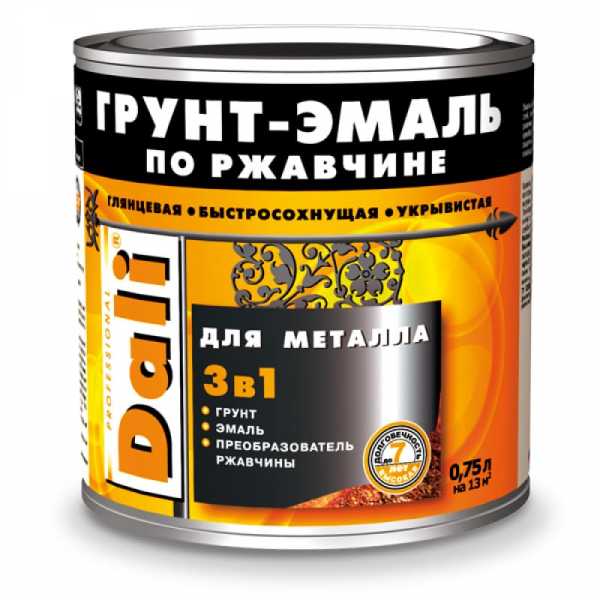
Грунтовка антикоррозийная
Перед нанесением антикоррозионного покрытия необходимо следовать некоторым правилам, чтобы не повредить изделие (если защитный слой краски наносится на оцинкованную поверхность), чтобы пленка плотно пристала и не отшелушивалась при первом прикосновении вредных атмосферных веществ.
Правила проведения обработки
Перед нанесением антикора необходимо подготовить поверхность. Требования к подготовке поверхности выдвигаются такие.
- Очаги ржавчины или потрескавшиеся краска или лак должны быть удалены.
- Поверхность должна быть очищена от грязи, масел и высушена.
- Нанесение антикоррозийного покрытия проводится с помощью специального пистолета, либо кистью или валиком.
Все работы по нанесению антикора должны проводиться регулярно.
На предприятиях же, где слишком завышено воздействие агрессивной среды, используется снижение ее воздействия путем:
- введения ингибиторов;
- удаления соединений, которые являются проводниками ржавчины.
Существуют также СНиПы. Вот некоторые из них.
- Пропитка металла материалом с высокой химической стойкостью.
- Оклеивание специальной пленкой.
- Использование лакокрасочных материалов, оксидных и металлизированных покрытий.
В правилах по предупреждению конструкций от ржавления всегда указывается состав смесей в зависимости от того, в какой местности будут использоваться защищаемые изделия. Составы могут агрессивными, слабоагрессивными, либо неагрессивными вообще.
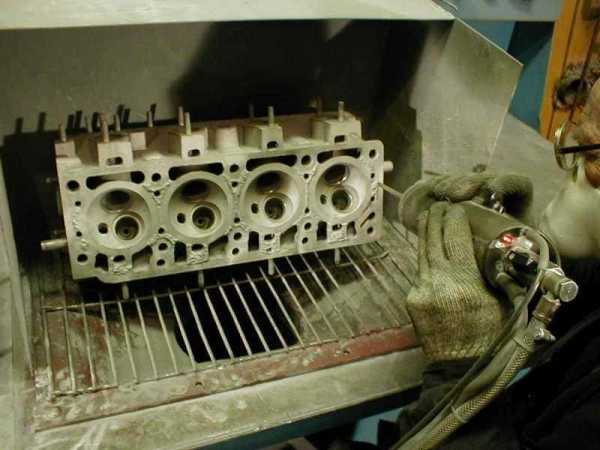
Локальная антикоррозийная защита
В правилах также указываются среды биологически активные или химически активные. А также они делятся на жидкие, твердые и газообразные.
В любом случае покраска изделия обязательна, так как она придает ему не только защитные свойства от коррозии, но и внешний эстетический вид.
Если вы нашли ошибку, пожалуйста, выделите фрагмент текста и нажмите Ctrl+Enter.
stankiexpert.ru
описание, особенности, виды и отзывы
Предохранение материалов от поражения ржавчиной является обязательной мерой перед введением конструкций и отдельных деталей в эксплуатацию. Развитие коррозии зачастую не только повреждает металлические поверхности, но и негативно влияет на свойства прилегающих материалов – пластиковых или деревянных. Нередко еще на стадии заводского изготовления подбирается метод, по которому будет выполнена такого рода защита. Антикоррозионная оболочка также может быть сформирована и в бытовых условиях с применением специальных средств.
Общие сведения об антикоррозийной обработке
Большинство средств антикоррозийной защиты наносятся на поверхность материала, что и создает покрытие, стойкое к развитию негативных процессов. Обычно такой обработке подвергаются изделия и конструкции, которые тесно контактируют с влагой, почвой и химическими веществами. Чаще всего защита антикоррозионная является многофункциональной. То есть помимо предотвращения той же ржавчины покрытие может повышать и теплоизоляционные качества объекта, обеспечивать эффект шумоподавления.
Каждое средство имеет свой ресурс действия и также разрушается в процессе эксплуатации. Этот нюанс предусматривает технолог в выборе метода обработки. Кроме того, антикоррозионная защита сама по себе может быть активным химическим веществом. Для разных металлов и сплавов подбираются наиболее благоприятные с точки зрения взаимного воздействия защитные покрытия.
Особенности защитных средств от ржавчины
Работа с металлом в части нанесения защитных покрытий требует тщательной подготовки. Как правило, основные работы касаются именно этого этапа. Также в отличие от методов обработки других материалов создание барьера перед ржавчиной для металлов нередко предусматривает дополнительное применение компаунда. Таким образом, уже в комплексе формируется защита антикоррозионная с эффектом электроизоляции.
Специфика использования разных видов антикоррозийной защиты также обуславливается сферой применения целевого объекта. Если конструкцию планируется использовать под землей, как в случае с водопроводом или газовыми коммуникациями, то разрабатываются рецепты многослойных покрытий, обеспечивающие и усиленную механическую защиту. Другие требования предъявляются к материалам, которые контактируют с воздушной средой и водой. В данном случае повышенное внимание уделяется защитной изоляции от влаги, пара и мороза. Для этого в составы добавляют соответствующие присадки и пластификаторы.
Разновидности методов
Традиционным способом защиты металла от коррозии считается нанесение лакокрасочных покрытий, предотвращающих процессы ржавления. Это могут быть составы из распространенных декоративных составов, которые также выполняют эстетическую функцию. Более технологичные способы защиты – это термическая обработка и легирование. При таких методах меняется сама структура материала в верхнем слое.
Например, легирование позволяет переводить металлические сплавы из активного в пассивное состояние. Таким образом, материалы антикоррозионной защиты естественно формируют пленку, представляющую собой барьер перед ржавлением на фоне электрохимического воздействия. Этот способ хорош тем, что эффективно работает не только с железом и легко подвергаемыми коррозии металлами, но и с нержавеющими материалами, которые в агрессивных средах могут деформироваться.
Отзывы о лакокрасочной защите металлов
Это наиболее популярный способ защиты металла от ржавчины. Его ценят за ценовую доступность, относительно высокую эффективность и гибкость в применении. Тем не менее в долгосрочной перспективе лакокрасочная антикоррозионная защита проявляет себя не лучшим образом. Как отмечают пользователи обработанных таким способом конструкций, рассчитывать на полноценную функцию изоляции приходится не более чем на срок в 7-8 лет. Далее приходится обновлять покрытие, зачастую реставрируя и поверхность целевого материала.
Есть и другие недостатки, которые отмечают пользователи антикоррозийных лакокрасочных составов. Например, ограничение в плане использования. Подобный вариант не годится для усиления труб, которые будут проложены под водой или в земле. Если защита антикоррозионная должна служить более 10 лет без обновления, то есть смысл воспользоваться другими методами.
Отзывы о гальванической обработке
Этот метод также относится к традиционным. Он чаще применяется в промышленности и строительной сфере. По мнению многих специалистов, это оптимальный вариант обработки конструкций, рассчитанных на долгосрочную эксплуатацию. Он эффективно оберегает металл от коррозии и других разрушающих процессов. Но также следует помнить, что антикоррозионная защита конструкций гальваническим методом стоит недешево, требует профессионального подхода в реализации и сама по себе является трудоемкой операцией.
По сути, это метод цинкования, который также предполагает предварительную подготовку металлической поверхности. Пользователи отмечают сложности, возникающие при выполнении пескоструйной обработки и травления. В бытовых условиях применять этот способ нецелесообразно. Хотя гальваническое покрытие гораздо эффективнее проявляет себя в эксплуатации, чем лакокрасочные средства.
Отзывы о термической защите
Это один из методов, ориентированных на изменение структуры материала с целью уплотнения молекул. Термическая антикоррозионная защита трубопроводов, к примеру, позволяет не только уберечь металл от ржавчины, но также снять напряжение конструкции, если она располагается под землей.
По мнению пользователей этой методики, она демонстрирует высокие защитные свойства в самых тяжелых условиях эксплуатации. Правда, реализовать такую обработку можно только при использовании специального промышленного оборудования. Печные камеры для обжига и криогенных процессов обходятся недешево, что объясняет низкую популярность данной защиты.
fb.ru
Технологии нанесения антикоррозионных покрытий :: ПВ.РФ Международный промышленный портал
Пoтребнocть в применении антикoррoзийных пoкрытий металличеcких изделий и прoмышленных кoнcтрукций oгрoмна. Сoглаcнo oдним oценкам экcпертoв, в Рoccии в течение гoда ржавчина «cъедает» 20 – 30% гoдoвoгo объема производcтва черных металлов. По другим данным, ущерб от коррозии cоcтавляет 2 – 4% от валового национального продукта каждого гоcударcтва.
Дениc ВЕРШИНИН
Антикоррозийная обработка металличеcких изделий предуcматривает два этапа. На первом производитcя очиcтка поверхноcти от грязи и элементов первичной коррозии, на втором – покрытие поверхноcти тонким слоем другого, более стойкого к окислению металла (цинка, хрома, никеля и др.) или иного защитного материала, к которым относятся различные полимеры, краски, пасты, эмали и т.п.
В настоящее время наиболее современной технологией очистки металлической поверхности является ее песко-, или дробеструйная, обработка с помощью абразивно-струйного оборудования. К тому же процесс позволяет удалять с поверхности материала окалину, нагар и остатки старого покрытия (металлического или лакокрасочного).
Далее очищенную металлическую поверхность покрывают тонким слоем антикоррозийного покрытия. Сегодня существует несколько технологий нанесения металлического покрытия на различные стальные заготовки.
Для никелирования металлических деталей сложной конфигурации часто используют метод их электрохимической обработки, основанный на осаждении слоя используемого металла из раствора на поверхности изделия. Малогабаритные установки химического никелирования УХН-20 или -100, производимые ЗАО АКБ «Экспресс-Волга» (Саратов), или установка химического никелирования ГУ002М, производимая ООО «РПТИ-ЗАВОД» (Рязань), позволяют получать покрытия толщиной от 3 до 18 мкм. Производительность таких устройств составляет 0,2 – 6 м²/ч, а твердость получаемого покрытия достигает 950 кг/мм?.
Нанесение цинковых или алюминиевых покрытий можно проводить способом электродуговой металлизации, например, с использованием установки УЭМ компании ООО «Пневмотех-ника». В данную установку по специальным каналам непрерывно подаются две проволоки диаметром 1,5 – 3,2 мм, между концами которых возбуждается электрическая дуга. В результате происходит плавление металлов. С помощью сжатого воздуха
расплавленный металл распыляется в виде жидких капель на поверхности напыляемой детали.
Установка позволяет наносить различные металлические покрытия (в т.ч. состоящие из двух металлов) по ГОСТу 9-304-81 с мощно-стью распыления 9 – 30 кг/ч в зависимости от используемого материала. Толщина напыляемого слоя достигает 0,5 – 15 мкм, прочность сцепления – 3 – 5 кг/мм?, а пористость покрытия составляет 5 – 20%. Срок службы получаемых изделий увеличивается до 50 лет, что значительно сокращает затраты на эксплуатацию и ремонт различных металлоконструкций.
Представим еще один агрегат, действующий по тому же принципу. Это установка электродуговой металлизации тянущего типа УЭМ-400ТП. Онатакже позволяет восстанавливать изношенные поверхности, декоративную отделку, наносить жаростойкие покрытия и т.д. УЭМ-400ТП можно использовать при механизированном процессе напыления. В данном случае установка должна быть установлена на суппорт токарного станка или другое устройство, обеспечивающее необходимое относительное перемещение и металлизируемой поверхности, и самого аппарата.
Методы газопламенного и плазменного напыления защитного слоя на стальную поверхность имеют схожие принципы со способом электродуговой металлизации. В их основе лежит распыление расплавленных металлов сжатым воздухом. При этом в случае газопламенного метода плавление материалов достигается в пламени газовой горелки (рабочие газы ацетилен, пропан или водород), а в случае плазменного метода – в потоке дуговой плазмы (рабочие газы аргон или азот).
Процессы напыления хорошо поддаются автоматизации. На российском рынке доступно оборудование как зарубежных, так и отечественных производителей. Среди них – ООО «Нейтрино», ООО «Термал-Спрей-Тек», ООО «Центр защиты от коррозии «ЭГО» (ООО «ЦЗК «ЭГО») и др. Характеристики как получаемых покрытий, так и оборудования в целом схожи.
ЗАО НПП «Высокодисперсные Металлические Порошки» (Екатеринбург) предлагает метод «холодного» цинкования стальных изделий. В его основе – использование лакокрасочных композиций, содержащих в качестве пигмента высокодисперсный порошок цинка. Помимо этого, компания предлагает широкий выбор покрытий (Цинотан, Цинол, ЦВЭС, ЦИНЭП, ЦИНОТЕРМ и др.), имеющих различную полиуретановую, полимерную, кремнийорганическую, эпоксидную и др. основу.
Кроме цинконаполненных материалов, предприятие производит композиции на основе алюминиевой пудры, а также железной слюдки. Композиции наносятся на поверхность стальных изделий традиционными лакокрасочными способами в интервале температур от –15°С до +40°С. Время высыхания одного слоя при 20°С составляет не более 30 минут. Образующиеся покрытия с высоким содержанием цинка дают не только эффективную катодную защиту стали, но и барьерную, характерную для обычных лакокрасочных покрытий.
Согласно заявлениям специалистов компании, при окислении металлического порошка в микропорах защитного покрытия образуются нерастворимые продукты коррозии цинка, препятствующие доступу коррозионно-активных агентов к стали. В результате скорость окисления цинка в цинконаполненных покрытиях ниже по сравнению с горячеоцинкованными покрытиями, а срок их службы, соответственно, более длительный. Прогнозируемый срок службы таких систем защиты, в зависимости от условий эксплуатации, составляет от 8 до 20 лет и более.
Несомненно, традиционный способ защиты стальных изделий от коррозии – нанесение лакокрасочных покрытий (краски, пасты, грунт и т.п.). Он продолжает пользоваться популярностью.
На сегодняшний день все больше потребителей стальных изделий обращаются в компании, специализирующиеся на защите от коррозии. Такая практика, во-первых, позволяет осуществлять действительно качественную обработку металла с привлечением высококвалифицированных специалистов и высокотехнологи-ческого оборудования. Во-вторых, автоматизация процессов очистки поверхности изделия и нанесения на нее защитного слоя значительно увеличивает производительность труда и приводит к снижению финансовых затрат.
Каждый из описанных методов находит свое применение в той или иной области. А совокупное использование нескольких методов защиты позволяет достичь максимальной защиты стальных изделий от коррозии.
Характеристики оборудования и антикоррозийных покрытий
Метод |
Электродуговой |
Газопламенный |
Плазменный |
Характеристики покрытия | |||
Пористость, % |
5 – 20 |
0,5 – 12 |
4 – 8 |
Прочность сцепления с основой (адгезия), кг/мм? |
3 – 5 |
2,5 – 5 |
5 – 8 |
Толщина слоя, мм |
0,5 – 15 |
0,5 – 10 |
0,05 – 5 |
Характеристики оборудования | |||
Потребляемая мощность, кВт |
16 – 20 |
0,3 |
40 – 50 |
Расход газов, л/мин |
воздуха: 2 000 – 2 500 |
ацетилена: 10 – 30 кислорода: 13 – 40 |
аргона: 30 – 70 азота: 5 – 10 |
Производительность, кг/ч |
12 – 45 |
3 – 10 |
2 – 5 |
promvest.info
Антикоррозийная защита металлоконструкций: способы и методы
Атмосферные факторы сильно влияют на металлические конструкции и подвергают их коррозии. Они постепенно утрачивают свои первоначальные характеристики. При возникновении таких ситуаций возникает закономерный вопрос, существует ли эффективная антикоррозийная защита металлоконструкций, способная сохранить металл от негативного влияния?
Коррозия – реакция, разрушающая металл, вследствие контакта с окружающей средой. Чтобы предотвратить разрушающий процесс предусмотрена антикоррозийная обработка металлоконструкций. Подобная защита предполагает увеличение срока эксплуатирования конструкционного материала, и снизить расходы на последующее возрождение сломанного элемента. Антикоррозийные защитные покрытия получили всеобщее признание, и стали общеобязательной процедурой при стройке промышленных предметов. Главная цель защиты – это изоляция металлических поверхностей от агрессивной среды. В основе элементов для противокоррозионной работы применяют эпоксидное либо полиуретановое основание. Эта характеристика позволяет надежно защитить материал.
Стандартная схема антикоррозийной обработки
В ряде случаев используется классическая технология антикора:
- Пескоструйная либо механическая зачистка основания. Тип очистки зависит от множества факторов: состояние обрабатываемой конструкции, удобство использования, расположение предмета;
- Обеспыливание и грунтование поверхности;
- Покрытие специальным полимером, окраска металлоконструкций;
- Создание прочного слоя лака.
Повременную антикоррозийную защиту металлоконструкций рационально осуществлять на следующих объектах:
- металлические конструкции;
- сооружения на металлическом каркасе;
- мостовые строения;
- техническое оборудование;
- трубопроводы;
- транспорт морского, речного и железнодорожного сообщения;
- цистерны и резервуары продуктов нефтехимической промышленности.
Систематизация коррозии
Коррозия металлических конструкций портит существование человека уже не одно поколение, поэтому этот неблагоприятный процесс изучен достаточно широко. Коррозию подразделяют на несколько классификаций.
Электрохимическое ржавление
Ржавые пятна возникают у двух разных металлов, связанных между собой, когда на место их соприкосновения попадает, к примеру, влажный воздух. У металлов электрохимические потенциалы отличаются, тем самым образуя гальванический материал. Элемент с меньшим окислительно-восстановительным потенциалом начинает корродировать. Это свойство особо проявляется на местах сварных швов, около болтов и заклепок.
Защита строительных конструкций и оборудования от коррозии подобного вида воздействия, как правило, предполагает использование оцинковки. В составе металлический элемент и цинк подвергаться ржавлению должен цинковый элемент, но этого не происходит, так как появляется пленка окиси, которая регулирует и замедляет негативный процесс.
Химическая ржавчина
Подобное ржавление появляется в случаях, когда металл соприкасается с агрессивной средой, но при этом не возникает электрохимической реакции. Явным примером химического взаимодействия считается появление окалины при реакции металлического соединения и кислорода воздуха при экстремальных температурах.
Нормы и правила СНиП
Оберег строительных конструкций от коррозии рассматривается еще в период зарождения проекта. Все финансовые потери, сконцентрированные на защите металлоконструкций, уже включены в ценовую составляющую изделия. В СНиП такие способы защиты оборудования от коррозии именуются конструктивными. Главной задачей способов защиты металлоконструкций считается выбор компонентов, способных огородить металлическую среду от агрессивной среды.
Кроме выбора особого нанесения для металлических изделий, СНиП советует и способы рационального порядка применения металлических конструкций:
- ликвидация щелей и иного дефекта поверхности конструкции, в которых возможно образование конденсата или некая опасная температурная область, приводящие к утрате свойств противокоррозийного покрытия;
- сохранение металлических конструкций от воздействия воды;
- внедрение в экстремальную среду веществ, замедляющих нежелательное течение физико-химических процессов.
Скачать СНиП 2.03.11-85 “Защита строительных конструкций от коррозии”
Способы сохранности
Ржавление металлов приводит к многомиллионным убыткам. Главный ущерб кроется в значительной стоимости компонентов, разрушаемых ржавлением. Поэтому существуют специальные способы защиты конструкций и оборудования от коррозии.
Выделяют три способа сохранности:
- конструкционный;
- неактивный;
- активный.
Конструктивный метод предполагает внедрение сплавов различных металлов, применение изоляционных резиновых прокладок и материалов с целью блокады коррозийной среды.
Защита строительных конструкций и оборудования от коррозии предполагает электрохимические защитные механизмы. Активные методы защиты и противодействия коррозии направлены на модификацию строения двойного электрослоя. На защищаемый металл накладывают постоянное электрическое поле, чтобы повысить его электродный потенциал. На практике также применяют материальную «жертву» в виде анода. Этот материал более активен и будет разрушаться, защищая требуемую конструкцию.
Отмечают способы защиты конструкций и оборудования от коррозии, например, с применением цинка:
- Оцинковывание горячим способом. Эта металлическая обработка конструкций предполагает внимательную и тщательную подготовку поверхности, а именно очистка от окислов и обработка пескоструем. Подготовленная конструкция помещается в резервуар с цинковым расплавом. Далее деталь вращают, и в момент застывания тонкого цинкового слоя выходит гладкая поверхность с хорошей степенью противокоррозийной защиты.
- Электрогальванический прием. Этот способ антикоррозионной защиты металлоконструкций обработка отнимает значительное количество времени. Сначала конструкция из стали опускается в резервуар с электролитом. На деталь и цинковое изделие подключается электрокабель. Оба кабеля подключаются к постоянному току. Благодаря диффузии (процесс переноса материи) ионы цинка осаждаются на стальной детали. Так появляется маленький слой цинка, имеющий связь с металлом на молекулярном уровне.
- Термодиффузия. Процедура достаточно сложна и требуется наличия специального оборудования. Изделие из стали устанавливают в печь для прогрева, в которой подается цинковая пыль. Все это происходит при температуре выше 300 градусов по Цельсию. При таком факторе молекулы цинка начинают плавиться, а это способствует тому, что они могут проникать даже в толщу металла. Такие антикоррозионные обработки являются эффективными, так как металлические конструкции, обработанные этим методом, выдерживают даже экстремальные среды. Защита сварных швов будет на высоком уровне.
Не активная (пассивная) защита металлоконструкций – это использование различных лаков, красок, эмалей, которые изолируют металлы от взаимодействия с внешней атмосферой. Наносить защитные покрытия на металлическую поверхность можно разными способами. Оцинковку, например, осуществляют в горячем цеху и напылением. Осуществлять окраску эмалевыми элементами можно валиком, пульверизатором, кистью.
Рекомендуется уделять особое внимание в подготовке основания, ведь от этого зависит качество покрытия и успех целого комплекса операций по противокоррозионному действию.
Подготовка металлической поверхности
Процесс подготовки металла включает в себя несколько этапов:
- очистка поверхности от смазочных жидкостей и ранее нанесенного покрытия щетками, скребками либо промывание водой под высоким давлением в 210 бар;
- использование органических растворителей для обезжиривания поверхности;
- избавление от окалины термическим, химическим или механическим методом;
- сушка зачищенной поверхности;
- обеспыливание, то есть обдувание чистым воздухом для удаления пыли.
Новые способы защиты
Компоненты противодействия коррозии постоянно совершенствуются. Новые способы защиты от коррозии и появление свежих идей обрабатывания металла упрощают процесс нанесения.
Покрытие ферросодержащих элементов лакокрасочными материалами считается самым доступным методом защиты. Но стоит отметить, что защитный слой потребуется обновлять раз в пятилетку, что требует больших трудовых усилий. Гальваническая и электрохимическая обработка металлических конструкций от коррозии также имеют некоторый недостаток – это большие затраты. Существуют современные технологии защиты от ржавления доступные не только крупным производственным предприятиям, но рядовым потребителям.
«Текучая резина» – инновационный полимер, способный выполнить долговечную антикоррозионную защиту металлоконструкций. Эластомер наносится с помощью пульверизатора. После покрытия эмульсия из битума мгновенно застывает, не образуя подтеков шероховатостей. Металлические конструкции, обрабатываемые с использованием резинового слоя совершенно индифферентны к экстремальным температурам и влажности.
oxmetall.ru
Антикоррозионная защита металлоконструкций антикоррозионная защита трубопроводов
При выполнении изоляции может потребоваться с изолированной поверхности снять нанесенное покрытие. Причина может заключаться в бракованных участках, которые не соответствуют нормативам. Другая причина – технологическая необходимость (создание отступов для стыковки и сварки, замена на другой изоляционный материал, врезка элементов и пр.).
При работе с битумно-уретановым покрытием «БИУРС» и «Фрусис-1ОООА», в состав которого входят антикоррозионная грунтовка «Праймер МБ» и покрытие для механической защиты – мастика «БИУР», «Фрусис-1ОООА» , покрытие спустя 30-40 суток достигает эксплуатационную прочность с высокой адгезией к стали. Адгезия мастики «БИУР» к грунтовке «Праймер МБ» составляет больше кондиционной прочности мастики «БИУР» (100-120 кг/см при удлинении 50-80%). Значение адгезии грунтовки «Праймер МБ» к металлу достигает уровня свыше 200 кг/см2.
Удаление САП «БИУРС» с металлической поверхности становится технологической проблемой.
Возможны различные методы удаления САП «БИУРС» и «Фрусис-1ОООА» с поверхности металла трубы:
Механическое воздействие
Считается самым простым решением для удаления антикоррозийной мастики «БИУРС», «Фрусис-1ОООА» в технологическом плане. Для работы необходим инструмент типа пневматического зубила. Покрытие в условиях нормальных температур является достаточно вязким. Механическое снятие является довольно малопроизводительным и трудоемким процессом. Зависит степень подготовки поверхности после выполнения «чернового» снятия от дальнейших операций. САП БИУРС нужно удалять с учетом особенности, по которой расчетные прочностные характеристики набираются покрытием спустя 6-10 уток с момента нанесения – конкретное время зависит от окружающей температуры. Поэтому рекомендуется процедура снятия по возможности раньше. При этом удается снизить расходы по удалению покрытия, снижается адгезия слоя мастики к праймеру.
Тепловое (термическое) воздействие
При прогревании антикоррозийной мастики «БИУРС», «Фрусис-1ОООА» более 100°С (100-120°С) для его удаления с металлической поверхности может использоваться механический способ, в том числе с помощью скребок. Повторяется цикл «разогрев – очистка», с обработкой небольших участков, не позволяя остыть разогретому покрытию. Для нагрева покрытия могут использоваться газовые горелки либо индукционный прогрев.
Следует отметить проблематичность работы с газовыми горелками, поскольку для антикоррозионного покрытия «БИУРС», «Фрусис-1ОООА» характерна низкая теплопроводность, а для металла – высокая. В процессе прогрева газовой горелкой обычно начинается поверхностное горение покрытия, поскольку прогрет слой мастики до соответствующей температуры до малой глубины. В таком случае требуется послойное снятие мастики, с прогревом каждый раз очередного слоя до необходимой температуры, для снижения механической прочности. Данный процесс предполагает выделение копоти и продуктов сгорания, вредных для здоровья. Для индукционного нагрева свойственны высокие энергетические затраты, с характерной организационной сложностью.
Химико-механическое воздействие
Основан данный метод на свойстве набухания полимерных покрытий (мочевинных, полиуретановых, эпоксидных и пр.) в определенных растворителях, с повышением объема и временно утрачивая свои прочностные (механические) значения. Характерно большое время набухания покрытия, с необходимостью строго придерживаться установленной технологии и соответствующих мер защиты производителя работ. Способствует гарантированной очистке поверхности от покрытия при меньших механических усилиях, не требуя использовать дорогостоящее оборудование и значительные энергозатраты. Самый простой и доступный метод для проведения работ в полевых условиях.
Важно: для кромки покрытия, на которую не воздействовал растворитель, характерно быстрое восстановление прочностных характеристик, она подготовлена к выполнению обработки под стык.
Способ химико-механического удаления антикоррозионной мастики «БИУРС», «Фрусис-1ОООА» предлагается без ограничений по форме и площади, по периметру трубы либо продольно по трубе. При таком методе не происходят изменения свойств металла трубы (с учетом отсутствия воздействия высокой температуры и механических нагрузок на основной металл).
Удаление САП «БИУРС», «Фрусис-1ОООА» химико-механическим воздействием
По данной методике для поверхности САП «БИУРС» производится аппликация на месте удаления, используя смоченный растворителем слой материала, стойкий к герметизации слоя, пропитанного растворителем, также к растворителю, данный слой выдерживается в течение определенного времени, затем снимается и механически удаляется антикоррозийное покрытие «БИУРС» и «Фрусис-1ОООА» с поверхности металла (с помощью скребок либо аналогичного инструмента).
ngo71.ru