Чем зенкер отличается от зенковки – Чем отличается зенкование от зенкерования
alexxlab | 24.12.2016 | 0 | Вопросы и ответы
Чем отличается зенкование от зенкерования – сверление, инструмент, особенности зенкования
Зенкование и зенкерование, несмотря на схожесть названий, являются разными операциями металлообработки с соответствующим инструментом. Схожесть операций в типе обработки и обрабатываемой поверхности. И зенкование, и зенкерование подразумевает механическую обработку резанием внутренней поверхности отверстий. Различия в характере обработки и, соответственно, получаемом результате.
Зенкерование: инструмент и особенности
Зенкерование – это промежуточный процесс обработки отверстий располагаемый, как правило, между сверлением и разверткой. Это получистовая обработка отверстия с целью:
- повышения точности отверстия до 4-го и даже 5-го класса;
- улучшения шероховатости;
- придания строгой геометрической формы.
Также зенкерование применяется при обработке отверстий полученных литьём или обработкой давлением.
Обработка производится с помощью зенкера, инструмента внешне похожего на сверло, но имеющего ряд конструктивных отличий. Основные отличия – это увеличенная перемычка между режущими кромками, увеличенное количество рабочих кромок и срезанный угол. Всё это обеспечивает высокую устойчивость зенкера и его соосность с обрабатываемым отверстием. Так, наличие 3-4 режущих кромок обеспечивает плавное распределение сил в зоне контакта зенкера с обрабатываемой деталью. Геометрия режущей части обеспечивает обработку отверстия без съема металла в продольном направлении.
Зенкеры различаются по количеству зубьев (3 или 4) и конструкции – насадные, цельные и вставные. Выбор инструмента зависит от диаметра отверстия. Так, применение вставных зенкеров (с вставными ножами) рекомендуется для отверстий диаметром от 20 мм., цельные применяются для малых диаметров (от 12 мм.).
Для получения более точных и сложных поверхностей используются комбинированные типы инструмента с большим количеством режущих кромок (до 8). При этом сборные зенкеры применяются совместно с другим металлорежущим инструментом – сверлами, развертками и т. д.
Особенности зенкования
Зенкование – это механическая обработка отверстий с целью создания различных геометрических углублений для потайного размещения крепежных изделий. Также она применяется для нарезки внутренних фасок. Для этих целей есть специальный инструмент – зенковка, имеющие различную форму. Выбор зенковки зависит от необходимого конечного результата.
Основные виды зенковок
- Цилиндрические зенковки. Применяются для получения цилиндрических выемок в просверленных отверстиях под установку болтов и винтов.
- Конические зенковки. Используются для вырезания отверстий конусной формы внутри детали, а также для зачистки острых кромок, снятия фасок и подготовки углублений под крепежные элементы. Чаще всего применяется инструмент с конусным углом 90° и 120°.
- Плоские или торцевые зенковки, также можно встретить название цековки. Преимущественно применяются для зачистки и обработки углублений перед установкой крепежных изделий.
Зенковка состоит из рабочей части и хвостовика со специальной цапфой выполняющей функцию направляющего пояса. Цапфа необходима для контроля соосности в процессе нарезки углублений.
Оборудование
Для зенкования и зенкерования используется, чаще всего, сверлильные станки различного типа. Также может быть использован обрабатывающий центр или токарный станок – практически тоже самое оборудование, на котором выполняются и операции сверления. Для обеих операций не рекомендуется использовать ручной инструмент из-за недостаточной точности позиционирования.
mekkain.ru
Зенкование и зенкерование – как обработать металлические детали? + Видео
Зенкование и зенкерование – это два разных технологических процесса, которые применяются при обработке металлических отверстий и поверхностей. Вам пригодятся специальные инструменты различной конструкции. В первом случае используются зенковки, во втором – зенкеры. Далее разберем их особенности и отличия.
1 Зенкование и зенковки – как использовать режущий инструмент?
После завершения сверления металлической детали возникает необходимость сделать сложные геометрические углубления внутри детали для последующей установки в них различных крепежных элементов – болтов, винтов, заклепок. Для этого, а также при необходимости качественно обработать поверхность и снять фаски внутри детали берем зенковку. Данный инструмент может быть различной формы. Ее можно подбирать, ориентируясь на конечный результат. На сегодняшний день различают конические, цилиндрические или торцевые (плоские) зенковки. Последние иногда носят названия цековки, а зенкование отверстий, как технологический процесс, может называться цекованием.

Работа зенковки
Рекомендуем ознакомиться
Зенковки цилиндрического типа необходимы для получения отверстий соответствующей формы в просверленных гнездах для последующей установки в них болтов и винтов различного типа. Зенковка имеет две части – рабочую поверхность и хвостовик, а также специальный направляющий пояс (цапфу), который необходим, чтобы обеспечивать контроль соосности инструмента в процессе работы над поверхностью металлической детали.
Конические зенковки имеют аналогичную составляющую, которая включает в себя хвостовик и рабочую часть с поясами, они обеспечивают соосность при работе.
Такие зенковки, как правило, используют при создании отверстий в виде конуса внутри детали, снятия фасок и для углублений под болты, различные плоские шайбы или упорные кольца. Наибольшее распространение получили зенковки с конусным углом в 90 или 120 градусов. Торцевые или плоские цековки применяются преимущественно для зачистки и обработки металлических углублений для установки крепежных элементов. Все зенковки различаются между собой диаметром, углом и режимами работы. Зенкование, как и зенкерование, осуществляется на сверлильных, агрегатных, фрезерных и токарно-фрезерных станках.
2 Промежуточный процесс обработки – повышаем класс точности
Зенкерование – это процесс расширения и обработки просверленных металлических отверстий штампованного или литого типа, который позволяет придать им строгую геометрическую форму. Зенкерование отверстий является промежуточным процессом, который чаще всего нужен после сверления и до металлического развертывания. С помощью качественного оборудования и инструмента можно добиться получения геометрических отверстий четвертого, а иногда и пятого класса точности. Инструмент для зенкерования называется зенкером.
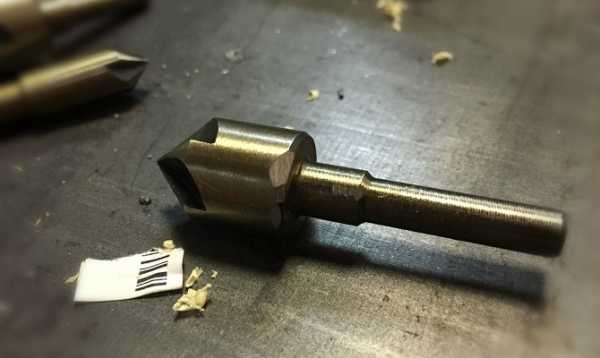
Зенкер по металлу
Зенкеры бывают нескольких типов и различаются по количеству зубьев (трех- или четырехперые), а по конструкции могут быть цельными, вставными или насадными. От обычного сверла зенкеры отличаются увеличенной перемычкой, которая соединяет режущие кромки, срезанным углом, а также наличием большего количества режущих зубьев-кромок. Они позволяют обеспечить устойчивость инструмента в процессе работы и максимально точную соосность зенкера и обрабатываемого отверстия.
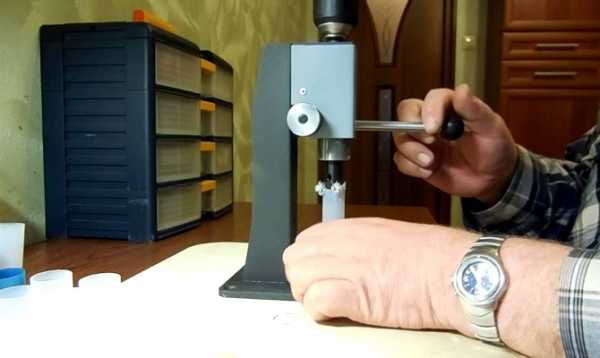
Зенкерование
Применение зенкеров определенного типа напрямую зависит от диаметра отверстия в обрабатываемой заготовке. Так, для отверстий, диаметр которых менее 12 мм, нужны цельные зенкеры, для отверстий свыше 20 мм – зенкеры вставного типа (со вставными ножами). При необходимости получить более точные и сложные поверхности используются комбинированные типы, в которых может быть до восьми режущих кромок, при этом зенкеры сборного типа могут дополнительно комбинироваться со сверлами, развертками и другими инструментами.
3 Развертывание – для обеспечения максимальной точности поверхности
Развертывание отверстий – это сложный технологический процесс чистовой обработки металлических отверстий на фрезерном оборудовании, который выполняется после процессов сверления и зенкерования. С помощью развертывания удается добиться высокого класса точности. Оно производится на ручных и автоматизированных сверлильных или токарно-фрезерных станках с ЧПУ или с ручным управлением. Инструмент, который применяется при развертывании, называется развертка.
При развертывании также широко применяется комбинированный тип инструмента, в который входит зенкер, зенковка, развертка, сверло и другие элементы. Комбинация инструментов позволяет существенно сократить время на получение отверстие нужной формы, класса точности и шероховатости. Сверление, как и зенкерование, и развертывание, можно называть схожими технологическими процессами в определенных режимах работы. Они выполняются на схожих видах ручного и механического оборудования.
tutmet.ru
Что такое зенкер и зенкование отверстий: технология операций
Среди металлообрабатывающего инструментария, применяемого для создания отверстий, особое значение заслуживает зенковка и зенкер. С их помощью выполняют проемы с заданными характеристиками, например, стабильность важных геометрических параметров, шершавость, сужение цилиндрического отверстия. Рассмотрим, что такое зенкер и зенковка.
Терминология
Зенковка – является многолезвийным инструментом для резки, используемая при обрабатывании отверстий в металлических деталях. После обработки получаются углубления конического/цилиндрического типа, можно создать опорную плоскость около отверстий, снять фаску на центровом отверстии.
Раззенковка отверстий – это вторичная подготовка готовых отверстий для размещения головок метизов – болты, винты, заклепки
Зенкер – инструмент для резки с многолезвийной поверхностью. Применяется в обработке отверстий цилиндрического/конического типа в заготовках для расширения диаметра, улучшения характеристик поверхностей и точностей. Этот тип обработки называется зенкерованием. Это получистовая обработка резанием.
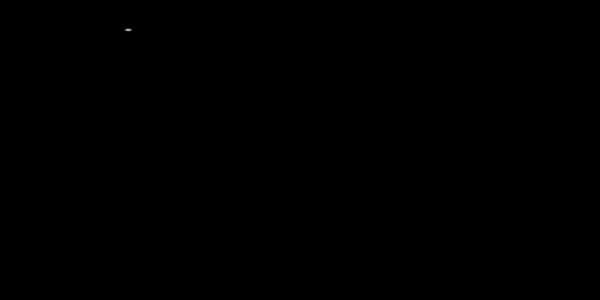
А — сверление сверлом В — растачивание на токарном станке С — зенкерование зенкером D — развёртывание развёрткой E,F — цекование цековкой G — зенкование зенковкой H — нарезка резьбы метчиком
Зенкование отверстий – процесс возделывания верхней части проема, чтобы, например, снять заусенцы с края отверстия или создать углубления, чтобы спрятать шляпку заклепок либо шурупа и сравнять с поверхностью детали. Приспособление, используемое для этой задачи, называется зенковкой.
Виды зенкеров и зенковок
Производство режущего инструментария по металлу подчиняется основной категории стандартов страны (ГОСТ) и техническими регламентами использования готового изделия. На агрегатах с частичным автоматизированным управлением используют следующие типы зенкеров:
- Цилиндрические, с диаметрами от 10 до 20 мм. Этот комплект с лезвиями производится с напылением из износостойких элементов. Регламентируется ГОСТ 12489-71.
- Неделимые конические, от 10 до 40 мм. Вырабатываются из легированной стали с устойчивым к износу напылением. Подчиняется ТУ 2-035-923-83.
- Целые, в виде насадок, с поперечником от 32 до 80 мм. Регламентируется ГОСТ 12489-71.
- Конический либо насадной, подчиняются ГОСТ 3231-71. Отмечаются присутствием специальных пластин, получаемых из твердых сплавов железа.
Зенковка – это также средство с многочисленными лезвиями, но обладает явными отличиями от зенкера по сфере использования. Эти приспособления подразделяются на некоторые типы:
- Коническая зенковка. Имеет эксплуатируемую головку с угловым коэффициентом конуса в 60,90, 120 градусов. В основном реализовывается для возделывания оснований под крепеж и удаления фасок, то есть затупить острые грани. Регламентируется ГОСТ 14953-80 Е.
- Округленная зенковка (цилиндрическая). Приспособление может обладать округленным либо коническим концом, имея износостойкое покрытие основания. В основном реализовывается в качестве обрабатывания опорных оснований.
Что такое зенкер, систематизация
Прорезывающий инструмент по металлу (зенкер) позволяет раззенковывать проем в детали до 5 группы меткости. Он массово используется для получистовой отделки деталей перед механическим развертыванием. По строению его разделяют на типы:
- целостные;
- насадочные;
- хвостовые;
- соединенные.
Внешне металлорежущие приспособления смахивают на простой небольшой бур, но обладают увеличенной численностью режущих краев. Правильность размеров проема обрабатываемой заготовки устанавливается за счет калибра. Крепеж инструментария в патроне агрегата выполняется с поддержкой хвостовика.
Для возделывания проемов, с поперечником до 10 см используются насадные приспособления с 4 остриями. Их главной особенностью считается крепеж через оправку. Достичь правильной регулировки реза позволило присутствие фаски на зубах элемента.
Конструкция конусного зенкера
Это приспособление предназначается для пропуска конусовидных проемов небольшой глубины. Главной особенностью в конструкции элемента считается присутствие зубьев прямого типа и абсолютно плоского внешнего основания. Численность элементов реза, в соответствии с калибровкой, может варьироваться в значении 6 – 12 единиц.
Зенкерование отверстий считается ручной процедурой, осуществляемой через токарный агрегат, на котором крепится зенкер. Возделываемая деталь зажимается в патронаже агрегата, проверяется верное ее расположение в углублении. Осевые центры электрошпинделя и заднего узла станка должны находиться на одном уровне. Это дает снизить риск вылета технически подвижной гильзе (пиноль). В отделываемое отверстие наконечник инструментария дается вручную.
Чтобы получить после операции зенкерования проем нужного поперечника, при сверлении производится припуск 2-3 мм. Точные значения припуска зависят от калибровки углубления в возделываемой заготовке. Труднее реализовать процесс зенкеровки выкованных и плотных изделий. Чтобы упростить себе задачу следует заблаговременно расточить раззенкованное отверстие на 5-9 мм.
Зенкеровка может выполняться в порядке резания. В этой ситуации подача инструментария увеличивается вдвое, чем при сверловке, а скорость хода остается прежней. Углубление резания зенкером закладывается примерно в 50 процентов припуска на поперечник. Раззенковка отверстий инструментом, реализовывается с применением охлаждающих материалов. Механизм из твердых сплавов не требует внесения вспомогательного хладоносителя.
Зенкер при обрабатывании проемов гарантирует высокую точность, но избежать брака совсем нельзя. Самыми распространенными пороками обработки считаются:
- Увеличенный поперечник проема. Главная причина возникновения подобного изъяна считается применение приспособления с неверной заточкой.
- Уменьшенный поперечник углубления. Случается, что для работы был выбран ошибочный инструментарий либо применялся испорченный зенкер.
- Вызывающая чистота. Этот изъян может быть вызван рядом причин. Обычно, уменьшение чистоты кроется в неважной заточке приспособления. На практике также причиной порока может служить чрезмерная вязкость материала изделия. Поэтому элемент налипает на ленты инструмента. Повреждение также вызывается погрешностью токаря, сделавшего неверную подачу и ускорение реза.
- Частичная обработка проема. Эта причина обычно возникает в результате неверной фиксации детали либо неправильным припуском под зенкеровку, сохраненным после сверления.
Разновидности и предназначение зенковок
Зенковка напоминает вид сверла, которая используется для зенкования. Операция схожа с зенкерованием, но отличаются конечной задачей. Процедура зенкования нужна в ситуациях, когда существует необходимость в формировании округленных углублений, чтобы скрыть следы головок крепежа.
Возделывание деталей зенковкой причисляется к получистовому методу, и осуществляется перед операцией развертывания.
По конструкции зенковки подразделяются:
- Округленные;
- Конические.
Под самостоятельной категорией выделяют зенковки, состоящие из твердых сплавов. Они используются в качестве шлифовальных действ. Для обрабатывания проемов и удаления фасок в трудных зонах используют еще один тип инструментария – оборотная зенковка. Чтобы обеспечить необходимую обработку металлических изделий и дерева рекомендуется покупать зенковочный комплект, а не индивидуальными приспособлениями.
В структуру зенковок конусного типа укладываются хвостовик и эксплуатируемый элемент, с угловым показателем 60, 75, 90 и 120 градусов. Число зубьев варьируется в пределе 6 – 12 единиц, это зависит от поперечника инструмента. Чтобы обеспечить соосность возделываемого проема используется цапфа.
Округленная зенковка обладает устойчивым к износу напылением. Используется этот механизм для подреза фаски. По конструкции оно смахивает на сверло, но обладает большим количеством лезвий – от 4 до 10, все зависит от поперечника устройства. На торцевой части элемента присутствует наводящая цапфа. С ее помощью фиксируется позиция инструментария в период эксплуатирования. Цапфа бывает разъемной либо целостной. На практике используются устройства с разъемными цапфами, из-за удобства использования. На зенковку также можно надеть насадный резак.
Чтобы обработать несколько проемов на равное углубление следует применять зенковку с держателями, включающее в свой состав различные ограничители. При обрабатывании изделия элемент реза устанавливается в державке и выходит из упора на величину, равную углублению проема.
Зенковки производятся из различных сортов сталей, включая твердосплавную. Инструменты, выполненные из твердых сплавов, отлично подходят для обрабатывания деталей из металла, так как способны выдержать экстремальные нагрузки долгое время. Для обработки изделий из цветного металлического сплава либо дерева применяют устройства из быстрорежущей стали, так как она подвергается незначительным нагрузкам. Стоит отметить, что при обрабатывании, например, чугунных изделий, необходимо внести дополнительное охлаждение инструментария. Для этого используются специальные эмульсионные составы.
Принцип зенкерования металлических изделий
Во время обрабатывания проема, созданного в детали в период его литья, рекомендуется расточить его разом на несколько миллиметров вглубь, чтобы зенкер выбрал верную начальную направленность.
В период осуществления работ при обработке стальных заготовок рекомендуется использовать эмульсионные охлаждающие составы. Процедура зенкерования цветных металлов и чугуна дополнительного внесения хладоносителя не требуется. Очень важным этапом считается верный подбор инструментария для осуществления работ. В связи с этим концентрируют внимание на аспекты:
- Разновидность инструментария выбирается в соответствии с материалами заготовки и характера возделывания. Учитываются факторы расположения отверстия и численность процессов.
- Зенковки и устройство для зенкерования выбираются в зависимости от заданных параметров: величина углубления, диаметр, точность работы.
- Конструкцию металлорежущего инструмента устанавливают, исходя из метода его крепежа на станке.
Выбор зенкера производят по справочной литературе или пользуясь нормативным актом стандарта ГОСТ 12489-71:
- Заготовки, созданные из конструкционной стали, с проемами до 40 мм в поперечнике возделываются зенкером, произведенного из быстрорежущего железа, включающий 3-4 зубья и диаметр 10-40 мм. В отверстиях до 80 мм используются насадки диаметром 32-80 мм.
- Для закаленного железа при расточке предусмотрена оснастка с пластинами из твердых сплавов, с поперечником 14-50 мм и 3-4 зубьями.
- Для расточки глухих проемов чугунных изделий и деталей из цветного металла используют перовой зенкер.
Нужным условием при процедуре зенкерования считается соблюдение припусков. Поперечник выбранного инструментария в результате обязан совпасть с окончательным диаметром проема после обрабатывания. Если после зенкерования предусмотрено выполнение развертывания проема, то поперечник устройства снижают на 0,15-0,3 мм. Если же намечено растачивание черновым вариантом или сверловка под зенкерование, то следует сохранять припуск на край от 0,5 до 2 мм.
Скачать ГОСТ
ГОСТ 12489-71 Зенкеры цельные. Конструкция и размеры
ГОСТ 14953-80 Зенковки конические. Технические условия
oxmetall.ru
Зенкеры, зенкерование и зенковки. Виды зенковки.
В современных технологиях по производству изделий или деталей, особое место занимает обработка отверстий. Это довольно сложный и ответственный технологический процесс, в котором необходимы специальные инструменты. Это, в основном, металлорежущие инструменты, предназначенные для промышленного применения станочного и ручного типа. Для выполнения отверстий пользуются сверлами. А для обработки подготовленных сверлами отверстий применяются зенковки и зенкеры.
Зенкер (нем. senker), относится к металлорежущим инструментам, использующимся для предварительной и окончательной обработки стенок отверстий. Такой вид работ по металлу называется зенкерованием. Зенкер, в отличие от сверла, оснащен большим числом режущих кромок (от 3 до 6, есть и больше). Часто, при выполнении зенкерования, используют смазочно-охлаждающие вещества (СОЖ).
Материалы, из которых изготавливаются зенкеры, должны быть более прочными и износостойкими, чем обрабатываемый материал, обычно высокопрочные металлы и сплавы.
Основные виды зенкеров:
- Машинные цельные, с коническим хвостовиком. Предназначены они для предварительной обработки отверстий конической формы.
- Насадные, которые по своей сути являются насадками, имеют напаянные пластины из твердого сплава. Предназначены для окончательной обработки стенок отверстия в чугунных и стальных деталях.
Зенкерование выполняют на различных металлообрабатывающих станках:
- Токарные
- Сверлильные
- Фрезерные с ЧПУ
- Расточные
- Агрегатные
Зенковка-это металлорежущий, многолезвийный инструмент. Она используется для выполнения отверстий различной формы и величины. Также зенковка используется для корректировки уже подготовленных отверстий, для выполнения опорных поверхностей вокруг отверстий. Отличаются зенковки от зенкеров тем, что имеют направляющие цапфы и зубья на торцах.
Зенковки делятся по форме режущей части на следующие виды:
- Цилиндрические. Имеют направляющую цапфу для обеспечения соосности.
- Конические. Имеют направляющую цапфу для обеспечения соосности.
- Торцовые, используют для зачистки внешней поверхности под потайные головки крепежных инструментов.
Так как зенковки изготавливаются по определенным стандартам, то они делятся по диаметру отверстий, которые обрабатывают:
- Простые (от 0,5 до 1,5 мм)
- С предохранительным конусом или без него (от 0,5 до 6 мм)
- С конусным хвостовиком (от 8 до 12 мм)
Зенкование осуществляется на металлообрабатывающих станках:
- Сверлильных
- Токарных
- Токарно-револьверных
- Агрегатных
Оба процесса, и зенкерование и зенкование, близки по значениям в режимах работы. Они осуществляются на одинаковых видах оборудования. Оба метода обработки могут найти применение в условиях единичного, серийного и массового производства.
mekkain.ru
Зенкеры, зенковки, цековки, развертки. Слесарное дело |
Зенкеры
Зенкеры (рис. 3.34, а) предназначены для обработки отверстий в заготовках, полученных отливкой, штамповкой или предварительным сверлением. В отличие от сверла зенкер имеет большее число режущих кромок (три или четыре), что обеспечивает получение поверхностей с более высокими показателями точности и шероховатости.
По конструкции зенкеры бывают насадные и цельные и могут иметь различное направление угла спирали (правое, левое, прямое). Зенкеры изготавливают из быстрорежущей стали или оснащают пластинами из твердого сплава марок ВК6, ВК8, BKbM, ВК8В, Т5К10, Т15К6. Пластины из твердого сплава закрепляются в зенкере при помощи пайки или клинового крепление, что позволяет многократно использовать корпус зенкера. Рабочая часть зенкеров, изготовленных из быстрорежущей стали, имеет обратную конусность (по направлению к хвостовику) порядка 0,05… 0,1 на 100 мм длины рабочей части и соединяется с хвостовиком так же, как и у сверл, шейкой. Цельные зенкеры закрепляются непосредственно в коническом отверстии шпинделя станка, а насадные устанавливаются на специальную оправку, также имеющую конический хвостовик для установки в шпинделе станка.
В качестве режущей части насадных зенкеров используются многогранные твердосплавные пластины. Крепление таких пластин в корпусе насадного зенкера осуществляют механическим путем (рис. 3.35). Режущие пластины 1 закрепляются в корпусе 2 при помощи тяги 3, что позволяет производить замену пластин непосредственно на станке. Для этого достаточно сместить тягу 3, повернуть пластину следующей гранью или заменить ее на новую, снова закрепить тягу и продолжать работу. Возможность оснащения таких зенкеров пластинами из различных инструментальных материалов позволяет существенно расширить технологические возможности и производительность при зенкеровании.
Геометрические параметры режущей части зенкеров (см. рис. 3.34, б) выбираются в зависимости от условий обработки: главный угол в плане ф = 30… 60 передний угол у = 3… 30 ° для зенкеров из быстрорежущей стали,для зенкеров, оснащенных пластинами твердого сплава, этот угол составляет от 5 до -5°; задний угол а на главных режущих кромках составляет 8… 15 Выбор конструкции зенкера и материала рабочей части в значительной степени зависит от обрабатываемого материала и параметров обрабатываемого отверстия:
• зенкеры из быстрорежущей стали, имеющие три-четыре зуба и диаметр от 10 до 40 мм, применяются для обработки отверстий в заготовках из конструкционной стали;
• зенкеры, оснащенные пластинами из твердого сплава, имеющие три-четыре зуба и номинальный диаметр от 14 до 50 мм, используются при обработке отверстий в заготовках из труднообрабатываемых и закаленных сталей;
• зенкеры с насадными головками из быстрорежущей стали номинальным диаметром от 32 до 80 мм предназначены для обработки отверстий в заготовках из конструкционной стали;
• перовые зенкеры служат для обработки глухих отверстий в заготовках из чугуна и цветных металлов;
• для обработки глухих отверстий диаметром от 15 до 25 мм применяется специальный зенкер, у которого в корпусе выполнено специальное отверстие для подачи СОЖ в зону резания (рис. 3.36).
Изнашивание зенкеров (рис. 3.37) происходит по задним поверхностям, где образуются площадки с задним углом, равным нулю, и шириной h4; по передним поверхностям с образованием лунки; по ленточке с образованием поперечных проточин на длине Лл; по уголкам с образованием конических или цилиндрических участков hy. В качестве критерия износа зенкеров при обработке заготовок из стали принят износ зенкера по уголкам, равный 1,2… 1,5 мм, а при обработке заготовок из чугуна — 0,8… 1,5 мм. Затачивание и перетачивание изношенных зенкеров осуществляется, как правило, на специальном оборудовании в заточных цехах.
Зенковки и цековки
Зенковки и цековки (рис. 3.38) для обработки опорных поверхностей под крепежные винты в отличие от зенкеров имеют режущие зубья на торце и направляющие цапфы, которые обеспечивают нужное направление зенковок и цековок в процессе обработки. Цапфа вводится в предварительно просверленное отверстие, при этом оси отверстия и образованного зенковкой углубления совпадают. Зенковки для обработки отверстий под цилиндрические головки винтов изготавливаются с цилиндрическим и коническим хвостовиком. Зенковки с ципиндрическим хвостовиком (рис. 3.38, и) выпускаются диаметром 15; 18; 20; 22 и 24 мм: а зенковки с коническим хвостовиком (рис. 3.38, б) — диаметром 15; 18; 20; 22; 24; 26; 30; 32; 33; 34; 36 и 40 мм.
Зенковки для обработки конических углублений с углами 60, 90 и 120° (рис. 3.38, в, г) такие», изготавливают и с цилиндрическим, и с коническим хвостовиком. Зенковки с цилиндрическим хвостовиком изготавливают диаметром 8; 10; 12; 16; 20; 25 мм, а с коническим хвостовиком — диаметром 16; 20; 25; 31,5; 40; 50; 63 и 80 мм.
Для подрезания торцев приливов и бобышек в литых корпусных деталях применяются одно- и двухсторонние пековки (рис. 3.38, д, е) из быстрорежущей стали или оснащенные пластинами твердого сплава. Они крепятся на специальных оправках с помощью байонетного замка. Выпускаются цековки диаметром 25; 32; 40; 50; ЬЗ; 80 и 10С мм.
Развертки
Развертки (рис. 3.39) изготовляются цельными и насадными с коническим и цилиндрическим хвостовиком, оснащаются вставными ножами, впаянными пластинами из твердого сплава либо изготовляются из быстрорежущей стали. Развертки в отличие от сверла и зенкера имеют большее количество режущих кромок, что позволяет при обработке снимать слой материала небольшой толщины, составляющий десятые и даже сотые доли миллиметра. Припуски на развертывание выбираются по таблицам в зависимости от диаметра обрабатываемого отверстия Различают развертки для ручного и машинного развертывания, цилиндрические и конические. Развертки для ручного развертывания на конце цилиндрического хвостовика имеют квадратную часть, на которую устанавливают вороток для вращения развертки в обрабатываемом отверстии.
Конструктивно развертка для ручного развертывания состоит из рабочей части, хвостовика и шейки. Рабочая часть конуса включает в себя режущую часть (заборный конус и направляющий конус, который обеспечивает центрирование развертки в отверстии) и калибрующую часть, обеспечивающую получение отверстия с заданной точностью и шероховатостью обработанной поверхности.
Режущая часть заборного конуса развертки имеет угол при вершине 2ф. Для обработки вязких металлов этот угол составляет 12… 15°, а для обработки хрупких и твердых материалов — от 3 до 5°.
Твердосплавные развертки имеют угол при вершине 30… 45 Направляющий конус рабочей части развертки расположен под углом 45 э к ее оси. Задний угол а на режущей части составляет от 6 до 15°, на калибрующей части этот угол обычно равен нулю, а передний угол у — 0… 15 . Для хрупких материалов передний угол равен нулю, а для твердосплавных разверток он составляет от 0 до -5°. Ручные развертки используют, как правило, при обработке отверстий диаметром от 3 до 50 мм в материала;, невысокой твердости (конструкционные стали, цветные металлы). Конические развертки (рис. 3.40) применяются для развертывания конических отверстий и, как правило, работают в комплекте из двух трех штук.
Машинные развертки бывают цилиндрическими и коническими, насадными и цельными. Цельные машинные развертки предназначены для обработки отверстий диаметром от 3 до 100 мм, а для развертывания отверстий диаметром от 25 до 300 мм используются насадные развертки. И цельные (рис. 3.41, а, б), и насадные (рис. 3.41, в, г) развертки изготавливают из быстрорежущей стали или оснащают пластинами из твердого сплава. Конструкция и материал машинной развертки выбирается в зависимости от характера выполняемых работ, материала обрабатываемой заготовки и требований, предъявляемых к качеству обработанной поверхности.
dlja-mashinostroitelja.info
Чем отличается зенкование от зенкерования?
Зенкование и зенкерование, несмотря на схожесть названий, являются разными операциями металлообработки с соответствующим инструментом. Схожесть операций в типе обработки и обрабатываемой поверхности. И зенкование, и зенкерование подразумевает механическую обработку резанием внутренней поверхности отверстий. Различия в характере обработки и, соответственно, получаемом результате.
Зенкерование: инструмент и особенности
Зенкерование – это промежуточный процесс обработки отверстий располагаемый, как правило, между сверлением и разверткой.
Это получистовая обработка отверстия с целью:повышения точности отверстия до 4-го и даже 5-го класса;
- улучшения шероховатости;
- придания строгой геометрической формы.
Также зенкерование применяется при обработке отверстий полученных литьём или обработкой давлением.
Обработка производится с помощью зенкера, инструмента внешне похожего на сверло, но имеющего ряд конструктивных отличий. Основные отличия – это увеличенная перемычка между режущими кромками, увеличенное количество рабочих кромок и срезанный угол. Всё это обеспечивает высокую устойчивость зенкера и его соосность с обрабатываемым отверстием. Так, наличие 3-4 режущих кромок обеспечивает плавное распределение сил в зоне контакта зенкера с обрабатываемой деталью. Геометрия режущей части обеспечивает обработку отверстия без съема металла в продольном направлении.Зенкеры различаются по количеству зубьев (3 или 4) и конструкции – насадные, цельные и вставные. Выбор инструмента зависит от диаметра отверстия. Так, применение вставных зенкеров (с вставными ножами) рекомендуется для отверстий диаметром от 20 мм., цельные применяются для малых диаметров (от 12 мм.). Для получения более точных и сложных поверхностей используются комбинированные типы инструмента с большим количеством режущих кромок (до 8). При этом сборные зенкеры применяются совместно с другим металлорежущим инструментом – сверлами, развертками и т. д.
Особенности зенкования
Зенкование – это механическая обработка отверстий с целью создания различных геометрических углублений для потайного размещения крепежных изделий. Также она применяется для нарезки внутренних фасок. Для этих целей есть специальный инструмент – зенковка, имеющие различную форму. Выбор зенковки зависит от необходимого конечного результата.
tdfrezer.ru
Раззенковка — studvesna73.ru
Слово раззенковка английскими буквами(транслитом) — razzenkovka
Слово раззенковка состоит из 11 букв: а а в е з з к к н о р
Значения слова раззенковка. Что такое раззенковка?
РАЗЗЕНКОВКА рассверливание конических заклепочных отверстий в крайних элементах склепываемых частей конструкции для постановки потайных и полупотайных заклепок.
Технический железнодорожный словарь. — 1941
РАЗЗЕНКОВКА — рассверливание конических заклепочных отверстий в крайних элементах склепываемых частей конструкции для постановки потайных и полупотайных заклепок.
Технический железнодорожный словарь. — 1941
Зенкерование и зенкование представляют собой технологические операции, предназначенные для обработки отверстий. Несмотря на схожесть названий, данные операции отличаются по своему назначению и применяемому технологическому инструменту.
Зенкерование и зенкование представляют собой различные операции по обработке отверстий. Зенкерование предназначено для улучшения качества поверхности отверстий, выполненных методами сверления, литья или обработки давлением. В отличие от зенкерования, зенкованием получают углубления в отверстиях под потайные крепежные элементы. Инструментом для операций зенкерования служат зенкеры, а для зенкования — конические и цилиндрические зенковки.
Назначение и особенности зенкерования
Назначением зенкерования является улучшение точности и шероховатости отверстий. Данная операция относится к этапу получистовой обработки и располагается в технологическом процессе между сверлением и развертыванием. Кроме улучшения качества поверхности, выполненной сверлением, зенкерование применяют также для обработки отверстий, полученных в результате литья и обработки давлением. Инструментом для операций зенкерования является зенкер, вид которого внешне напоминает сверло.
Благодаря большему по сравнению со сверлом количеству режущих кромок, с помощью зенкера достигается повышенная чистота обрабатываемой поверхности. Наличие 3-4 режущих кромок обеспечивает плавное распределение усилий в зоне контакта инструмента и обрабатываемой детали. Также зенкер отличается от сверла оригинальной геометрией режущей части, что обусловлено необходимостью обработки уже существующих отверстий без съема материала в продольном направлении.
Назначение и особенности зенкования
Зенкование предназначено для получения на торцах отверстий гнезд для потайного размещения головок крепежных элементов. Данные углубления, которые могут иметь цилиндрическую либо коническую форму, обрабатываются соответственно коническими или цилиндрическими зенковками.
Геометрия цилиндрической зенковки напоминает зенкер, а рабочая часть конической зенковки вместо спиральных режущих кромок имеет зубчатые. В конструкции цилиндрической зенковки должен быть предусмотрен направляющий поясок. Конические зенковки также применяются для зачистки острых кромок и снятия фасок.
Оборудование
Операции зенкерования и зенкования выполняются на том же технологическом оборудовании, что и сверление. Таким оборудованием может выступать сверлильный станок или универсальный обрабатывающий центр. Также существует возможность зенкования и зенкерования с использованием токарного станка. Выполнять данные операции с помощью ручного инструмента не рекомендуется в связи с невозможностью обеспечения необходимой точности его позиционирования.
Среди металлообрабатывающего инструментария, применяемого для создания отверстий, особое значение заслуживает зенковка и зенкер. С их помощью выполняют проемы с заданными характеристиками, например, стабильность важных геометрических параметров, шершавость, сужение цилиндрического отверстия. Рассмотрим, что такое зенкер и зенковка.
Терминология
Зенковка – является многолезвийным инструментом для резки, используемая при обрабатывании отверстий в металлических деталях. После обработки получаются углубления конического/цилиндрического типа, можно создать опорную плоскость около отверстий, снять фаску на центровом отверстии.
Раззенковка отверстий – это вторичная подготовка готовых отверстий для размещения головок метизов – болты, винты, заклепки
Зенкер – инструмент для резки с многолезвийной поверхностью. Применяется в обработке отверстий цилиндрического/конического типа в заготовках для расширения диаметра, улучшения характеристик поверхностей и точностей. Этот тип обработки называется зенкерованием. Это получистовая обработка резанием.
А — сверление сверлом В — растачивание на токарном станке С — зенкерование зенкером D — развёртывание развёрткой E,F — цекование цековкой G — зенкование зенковкой H — нарезка резьбы метчиком
Зенкование отверстий – процесс возделывания верхней части проема, чтобы, например, снять заусенцы с края отверстия или создать углубления, чтобы спрятать шляпку заклепок либо шурупа и сравнять с поверхностью детали. Приспособление, используемое для этой задачи, называется зенковкой.
Виды зенкеров и зенковок
Производство режущего инструментария по металлу подчиняется основной категории стандартов страны (ГОСТ) и техническими регламентами использования готового изделия. На агрегатах с частичным автоматизированным управлением используют следующие типы зенкеров:
- Цилиндрические, с диаметрами от 10 до 20 мм. Этот комплект с лезвиями производится с напылением из износостойких элементов. Регламентируется ГОСТ 12489-71.
- Неделимые конические, от 10 до 40 мм. Вырабатываются из легированной стали с устойчивым к износу напылением. Подчиняется ТУ 2-035-923-83.
- Целые, в виде насадок, с поперечником от 32 до 80 мм. Регламентируется ГОСТ 12489-71.
- Конический либо насадной, подчиняются ГОСТ 3231-71. Отмечаются присутствием специальных пластин, получаемых из твердых сплавов железа.
Зенковка – это также средство с многочисленными лезвиями, но обладает явными отличиями от зенкера по сфере использования. Эти приспособления подразделяются на некоторые типы:
- Коническая зенковка. Имеет эксплуатируемую головку с угловым коэффициентом конуса в 60,90, 120 градусов. В основном реализовывается для возделывания оснований под крепеж и удаления фасок, то есть затупить острые грани. Регламентируется ГОСТ 14953-80 Е.
- Округленная зенковка (цилиндрическая). Приспособление может обладать округленным либо коническим концом, имея износостойкое покрытие основания. В основном реализовывается в качестве обрабатывания опорных оснований.
Что такое зенкер, систематизация
Прорезывающий инструмент по металлу (зенкер) позволяет раззенковывать проем в детали до 5 группы меткости. Он массово используется для получистовой отделки деталей перед механическим развертыванием. По строению его разделяют на типы:
Внешне металлорежущие приспособления смахивают на простой небольшой бур, но обладают увеличенной численностью режущих краев. Правильность размеров проема обрабатываемой заготовки устанавливается за счет калибра. Крепеж инструментария в патроне агрегата выполняется с поддержкой хвостовика.
Для возделывания проемов, с поперечником до 10 см используются насадные приспособления с 4 остриями. Их главной особенностью считается крепеж через оправку. Достичь правильной регулировки реза позволило присутствие фаски на зубах элемента.
Конструкция конусного зенкера
Это приспособление предназначается для пропуска конусовидных проемов небольшой глубины. Главной особенностью в конструкции элемента считается присутствие зубьев прямого типа и абсолютно плоского внешнего основания. Численность элементов реза, в соответствии с калибровкой, может варьироваться в значении 6 – 12 единиц.
Зенкерование отверстий считается ручной процедурой, осуществляемой через токарный агрегат, на котором крепится зенкер. Возделываемая деталь зажимается в патронаже агрегата, проверяется верное ее расположение в углублении. Осевые центры электрошпинделя и заднего узла станка должны находиться на одном уровне. Это дает снизить риск вылета технически подвижной гильзе (пиноль). В отделываемое отверстие наконечник инструментария дается вручную.
Чтобы получить после операции зенкерования проем нужного поперечника, при сверлении производится припуск 2-3 мм. Точные значения припуска зависят от калибровки углубления в возделываемой заготовке. Труднее реализовать процесс зенкеровки выкованных и плотных изделий. Чтобы упростить себе задачу следует заблаговременно расточить раззенкованное отверстие на 5-9 мм.
Зенкеровка может выполняться в порядке резания. В этой ситуации подача инструментария увеличивается вдвое, чем при сверловке, а скорость хода остается прежней. Углубление резания зенкером закладывается примерно в 50 процентов припуска на поперечник. Раззенковка отверстий инструментом, реализовывается с применением охлаждающих материалов. Механизм из твердых сплавов не требует внесения вспомогательного хладоносителя.
Зенкер при обрабатывании проемов гарантирует высокую точность, но избежать брака совсем нельзя. Самыми распространенными пороками обработки считаются:
- Увеличенный поперечник проема. Главная причина возникновения подобного изъяна считается применение приспособления с неверной заточкой.
- Уменьшенный поперечник углубления. Случается, что для работы был выбран ошибочный инструментарий либо применялся испорченный зенкер.
- Вызывающая чистота. Этот изъян может быть вызван рядом причин. Обычно, уменьшение чистоты кроется в неважной заточке приспособления. На практике также причиной порока может служить чрезмерная вязкость материала изделия. Поэтому элемент налипает на ленты инструмента. Повреждение также вызывается погрешностью токаря, сделавшего неверную подачу и ускорение реза.
- Частичная обработка проема. Эта причина обычно возникает в результате неверной фиксации детали либо неправильным припуском под зенкеровку, сохраненным после сверления.
Разновидности и предназначение зенковок
Зенковка напоминает вид сверла, которая используется для зенкования. Операция схожа с зенкерованием, но отличаются конечной задачей. Процедура зенкования нужна в ситуациях, когда существует необходимость в формировании округленных углублений, чтобы скрыть следы головок крепежа.
Возделывание деталей зенковкой причисляется к получистовому методу, и осуществляется перед операцией развертывания.
По конструкции зенковки подразделяются:
Под самостоятельной категорией выделяют зенковки, состоящие из твердых сплавов. Они используются в качестве шлифовальных действ. Для обрабатывания проемов и удаления фасок в трудных зонах используют еще один тип инструментария – оборотная зенковка. Чтобы обеспечить необходимую обработку металлических изделий и дерева рекомендуется покупать зенковочный комплект, а не индивидуальными приспособлениями.
В структуру зенковок конусного типа укладываются хвостовик и эксплуатируемый элемент, с угловым показателем 60, 75, 90 и 120 градусов. Число зубьев варьируется в пределе 6 – 12 единиц, это зависит от поперечника инструмента. Чтобы обеспечить соосность возделываемого проема используется цапфа.
Округленная зенковка обладает устойчивым к износу напылением. Используется этот механизм для подреза фаски. По конструкции оно смахивает на сверло, но обладает большим количеством лезвий – от 4 до 10, все зависит от поперечника устройства. На торцевой части элемента присутствует наводящая цапфа. С ее помощью фиксируется позиция инструментария в период эксплуатирования. Цапфа бывает разъемной либо целостной. На практике используются устройства с разъемными цапфами, из-за удобства использования. На зенковку также можно надеть насадный резак.
Чтобы обработать несколько проемов на равное углубление следует применять зенковку с держателями, включающее в свой состав различные ограничители. При обрабатывании изделия элемент реза устанавливается в державке и выходит из упора на величину, равную углублению проема.
Зенковки производятся из различных сортов сталей, включая твердосплавную. Инструменты, выполненные из твердых сплавов, отлично подходят для обрабатывания деталей из металла, так как способны выдержать экстремальные нагрузки долгое время. Для обработки изделий из цветного металлического сплава либо дерева применяют устройства из быстрорежущей стали, так как она подвергается незначительным нагрузкам. Стоит отметить, что при обрабатывании, например, чугунных изделий, необходимо внести дополнительное охлаждение инструментария. Для этого используются специальные эмульсионные составы.
Принцип зенкерования металлических изделий
Во время обрабатывания проема, созданного в детали в период его литья, рекомендуется расточить его разом на несколько миллиметров вглубь, чтобы зенкер выбрал верную начальную направленность.
В период осуществления работ при обработке стальных заготовок рекомендуется использовать эмульсионные охлаждающие составы. Процедура зенкерования цветных металлов и чугуна дополнительного внесения хладоносителя не требуется. Очень важным этапом считается верный подбор инструментария для осуществления работ. В связи с этим концентрируют внимание на аспекты:
- Разновидность инструментария выбирается в соответствии с материалами заготовки и характера возделывания. Учитываются факторы расположения отверстия и численность процессов.
- Зенковки и устройство для зенкерования выбираются в зависимости от заданных параметров: величина углубления, диаметр, точность работы.
- Конструкцию металлорежущего инструмента устанавливают, исходя из метода его крепежа на станке.
Выбор зенкера производят по справочной литературе или пользуясь нормативным актом стандарта ГОСТ 12489-71:
- Заготовки, созданные из конструкционной стали, с проемами до 40 мм в поперечнике возделываются зенкером, произведенного из быстрорежущего железа, включающий 3-4 зубья и диаметр 10-40 мм. В отверстиях до 80 мм используются насадки диаметром 32-80 мм.
- Для закаленного железа при расточке предусмотрена оснастка с пластинами из твердых сплавов, с поперечником 14-50 мм и 3-4 зубьями.
- Для расточки глухих проемов чугунных изделий и деталей из цветного металла используют перовой зенкер.
Нужным условием при процедуре зенкерования считается соблюдение припусков. Поперечник выбранного инструментария в результате обязан совпасть с окончательным диаметром проема после обрабатывания. Если после зенкерования предусмотрено выполнение развертывания проема, то поперечник устройства снижают на 0,15-0,3 мм. Если же намечено растачивание черновым вариантом или сверловка под зенкерование, то следует сохранять припуск на край от 0,5 до 2 мм.
Скачать ГОСТ
ГОСТ 12489-71 Зенкеры цельные. Конструкция и размеры –
ГОСТ 14953-80 Зенковки конические. Технические условия –
Зенкование и зенкерование – это два разных технологических процесса, которые применяются при обработке металлических отверстий и поверхностей. Вам пригодятся специальные инструменты различной конструкции. В первом случае используются зенковки, во втором – зенкеры. Далее разберем их особенности и отличия.
Содержание
- Зенкование и зенковки – как использовать режущий инструмент?
- Промежуточный процесс обработки – повышаем класс точности
- Развертывание – для обеспечения максимальной точности поверхности
1 Зенкование и зенковки – как использовать режущий инструмент?
После завершения сверления металлической детали возникает необходимость сделать сложные геометрические углубления внутри детали для последующей установки в них различных крепежных элементов – болтов, винтов, заклепок. Для этого, а также при необходимости качественно обработать поверхность и снять фаски внутри детали берем зенковку. Данный инструмент может быть различной формы. Ее можно подбирать, ориентируясь на конечный результат. На сегодняшний день различают конические, цилиндрические или торцевые (плоские) зенковки. Последние иногда носят названия цековки, а зенкование отверстий, как технологический процесс, может называться цекованием.
Зенковки цилиндрического типа необходимы для получения отверстий соответствующей формы в просверленных гнездах для последующей установки в них болтов и винтов различного типа. Зенковка имеет две части – рабочую поверхность и хвостовик, а также специальный направляющий пояс (цапфу), который необходим, чтобы обеспечивать контроль соосности инструмента в процессе работы над поверхностью металлической детали.
Конические зенковки имеют аналогичную составляющую, которая включает в себя хвостовик и рабочую часть с поясами, они обеспечивают соосность при работе.
Такие зенковки, как правило, используют при создании отверстий в виде конуса внутри детали, снятия фасок и для углублений под болты, различные плоские шайбы или упорные кольца. Наибольшее распространение получили зенковки с конусным углом в 90 или 120 градусов. Торцевые или плоские цековки применяются преимущественно для зачистки и обработки металлических углублений для установки крепежных элементов. Все зенковки различаются между собой диаметром, углом и режимами работы. Зенкование, как и зенкерование, осуществляется на сверлильных, агрегатных, фрезерных и токарно-фрезерных станках .
2 Промежуточный процесс обработки – повышаем класс точности
Зенкерование– это процесс расширения и обработки просверленных металлических отверстий штампованного или литого типа, который позволяет придать им строгую геометрическую форму. Зенкерование отверстий является промежуточным процессом, который чаще всего нужен после сверления и до металлического развертывания. С помощью качественного оборудования и инструмента можно добиться получения геометрических отверстий четвертого, а иногда и пятого класса точности. Инструмент для зенкерования называется зенкером.
Зенкер по металлу
Зенкеры бывают нескольких типов и различаются по количеству зубьев (трех- или четырехперые), а по конструкции могут быть цельными, вставными или насадными. От обычного сверла зенкеры отличаются увеличенной перемычкой, которая соединяет режущие кромки, срезанным углом, а также наличием большего количества режущих зубьев-кромок. Они позволяют обеспечить устойчивость инструмента в процессе работы и максимально точную соосность зенкера и обрабатываемого отверстия.
Применение зенкеров определенного типа напрямую зависит от диаметра отверстия в обрабатываемой заготовке. Так, для отверстий, диаметр которых менее 12 мм, нужны цельные зенкеры, для отверстий свыше 20 мм – зенкеры вставного типа (со вставными ножами). При необходимости получить более точные и сложные поверхности используются комбинированные типы, в которых может быть до восьми режущих кромок, при этом зенкеры сборного типа могут дополнительно комбинироваться со сверлами, развертками и другими инструментами.
3 Развертывание – для обеспечения максимальной точности поверхности
Развертывание отверстий – это сложный технологический процесс чистовой обработки металлических отверстий на фрезерном оборудовании, который выполняется после процессов сверления и зенкерования. С помощью развертывания удается добиться высокого класса точности. Оно производится на ручных и автоматизированных сверлильных или токарно-фрезерных станках с ЧПУ или с ручным управлением. Инструмент, который применяется при развертывании, называется развертка.
По типу обработку развертки могут быть ручными или механическими (машинными), а по форме – конусообразными или цилиндрическими. Инструмент состоит из трех частей с калибрующей частью и режущими кромками, которые равномерно или неравномерно распределяются по окружности. Как правило, развертки используются комплектом по три штуки, это необходимо для выполнения поочередно черновой, получистовой и чистовой обработки. В таком случае удается добиться максимального эффекта при обработке поверхности.
При развертывании также широко применяется комбинированный тип инструмента, в который входит зенкер, зенковка, развертка, сверло и другие элементы. Комбинация инструментов позволяет существенно сократить время на получение отверстие нужной формы, класса точности и шероховатости. Сверление, как и зенкерование, и развертывание, можно называть схожими технологическими процессами в определенных режимах работы. Они выполняются на схожих видах ручного и механического оборудования.
Трубогиб ручной ТР и другие марки – рассматриваем типы этого приспособления
В этой статье мы рассмотрим различные механические трубогибы, которые можно использовать руками, применяя только мускульную.
Виды сварочных аппаратов – обзор популярных моделей
Статья подскажет вам, какое специальное оборудование имеет смысл приобрести, если вы планируете производить работы по.
Ленточнопильный станок (ленточные пилы)
Цветные металлы и сплавы
Конструкционные стали и сплавы
Зенкованием называется обработка выходной части отверстия, например снятие заусенцев с краев отверстия, расширение центровых отверстий, образование углублений под потайные головки винтов и заклепок. Инструмент, применяемый для этой цели, называется зенковкой. Зенковки по форме режущей части подразделяются на конические и цилиндрические, имеющие торцовые зубья и снабженные цапфой.
Конические зенковки предназначены для снятия заусенцев в выходной части отверстия, получения конического углубления в отверстии под опоры конических головок винтов и заклепок и для центрования отверстий. Наибольшее распространение получили конические зенковки с углом конуса при вершине 30, 60, 90 и 120°.
Цилиндрические зенковки с торцовыми зубьями1 применяются для расширения выходной части цилиндрических отверстий под головки винтов, под плоские шайбы, а также для подрезания торцов, плоскостей бобышек, для выборки уступов и углов. Число зубьев у этих зенковок от 4 до 8.
На рис. 190 показаны зенковки различных видов и примеры обработки ими отверстий.
Зенкерованием называется обработка готовых отверстий, полученных отливкой, штамповкой или сверлением, с целью придать им строго цилиндрическую форму, большую точность и лучшую чистоту поверхности. После зенкера отверстие получается 4 и 5-го классов точности.
Отверстия 2 и 3-го классов точности получают развертыванием. Следовательно, зенкерование может быть и промежуточной операцией между сверлением и развертыванием.
Зенкеры (рис. 191) разделяются на цельные и насадные, а по количеству зубьев (перьев) — на трехперые и четырехперые. Цельный зенкер имеет три или четыре режущие кромки, а насадной — четыре режущие кромки. Для обработки отверстий диаметром 12—35 мм применяют зенкеры цельной конструкции, а для обработки отверстий диаметром в пределах 24—100 мм — насадные зенкеры.
Зенкование и зенкерование, как и процесс сверления, происходит при двух совместных относительных движениях инструмента — вращательном и поступательном вдоль оси. Сверло, выбираемое для сверления отверстия под обработку зенкером, должно иметь диаметр, уменьшенный против диаметра окончательно обработанного отверстия на величину припуска. В табл. 12 приводятся диаметры зенкеров и рекомендуемые припуски (на сторону) под зенкерование.
Рис. 1. Зенковки: а — для обработки отверстия под коническую головку винта, б — примеры работы коническими зенковками, в — зенковки для обработки отверстий под цилиндрические головки и шейки, г —отверстие, раззенкованное под цилиндрическую головку винта, д — отверстие, раззенкованное под шейку винта, е — соединение деталей винтом через раззенкованное отверстие
Рис. 2. Зенкеры: а — цельный, б — насадной, в — стержень для насадки головки зенкера
Рис. 3. Ручная (слева) и машинная развертки: Л — рабочая (заходная) часть развертки, Б — калибрующая часть, В — шейка, Г — хвостовик, Д — квадратная головка для захвата развертки воротком при развертывании вручную
Читать далее:
studvesna73.ru