Цинкование электрохимическое – Гальваническое цинкование – технология, оборудование, электролиты + Видео
alexxlab | 08.12.2020 | 0 | Вопросы и ответы
Цинкование электролитическим способом
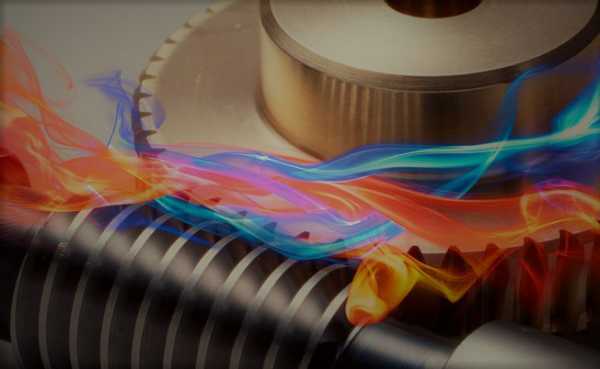
Процесс цинкования получает все большее распространение в промышленности. Это связано с тем, что цинк обладает наилучшими защитными свойствами и эффективно обеспечивает электрохимическую защиту сталей, медных и цинковых сплавов.
Гальванически осажденный цинк имеет светло-серый цвет с голубоватым оттенком. Его плотность равна 7,1 и температура плавления 419 °С. При 100-150 °С цинк легко может быть прокован и прокатан, но при повышении температуры до 200 °С он становится хрупким. Атомная масса цинка – 65,4, валентность – 2, стандартный электродный потенциал – 0,76 В и электрохимический эквивалент – 1,22 г/А-ч.
Так как стандартный электродный потенциал цинка более электроотрицателен, чем потенциал железа, то слой цинка в паре железо-цинк служит анодом и, следовательно, защищает железо от коррозии не только механически, но и электрохимически. Поэтому цинкование получило широкое применение для защиты железа в условиях атмосферной коррозии, а также для изделий, соприкасающихся с пресной водой.
По своим химическим свойствам цинк весьма активен и легко реагирует со всеми неорганическими и органическими кислотами, со щелочами и сернистыми соединениями. На воздухе легко тускнеет, покрываясь пленкой основных углекислых солей. Для повышения защитных свойств цинковых покрытий их подвергают специальной химической обработке в растворах хромовой кислоты и ее солей или в растворах солей фосфорной кислоты.
Покрытия применяют для защиты изделий из черных металлов (листов, труб, проволоки, деталей станков, автомобилей, приборов, крепежных изделий) от коррозии. В ремонтном производстве цинковые покрытия используют для защиты от коррозии крепежных деталей. Толщину цинковых покрытий выбирают в зависимости от условий эксплуатации и параметров изделий (табл. 5.6.)
Таблица 5.6. Толщина цинковых покрытий для изделий разных групп.
Условия эксплуатации |
Толщина цинкового покрытия, мкм |
Листовые детали |
|
Легкие (отапливаемые помещения |
24 |
Средние (неотапливаемые помещения) |
32 |
Жесткие (на открытом воздухе) |
|
Особо жесткие (в воде и тропиках) |
|
Крепежные изделия |
|
Шаг резьбы, мм |
|
|
6-9 |
Св. 0,8 |
9-12 |
Крупные и средние детали покрывают цинком, навешивая на подвесках в стационарных ваннах. Мелкие крепежные детали можно цинковать в колокольных или барабанных ваннах. Колокол (или барабан) вращается с частотой 8-15 оборотов в минуту в зависимости от его конструкции и обеспечивает постоянное взаимное перемешивание электролита и деталей.
Этот вид цинкования имеет свои особенности. Прежде всего, необходимо рассчитать продолжительность обработки деталей, исходя не из плотности тока, а из общей силы тока на барабанную ванну, заданной толщины слоя цинка и общей площади всех деталей, загруженных в барабан, или колокол. Известно, что электрохимический эквивалент цинка равен 1,22 г/А-ч, т.е. ток силой в 1 А осаждает в течение 1 ч 1,22 г цинка, при катодном выходе по току 100 %. Но выход по току в колокольных и барабанных ваннах при цинковании практически не превышает 50 %. Это связано с рядом причин, из которых одной из основных является истирание слоя цинка при вращении барабана и трении деталей между собой.
Возможно Вас так же заинтересуют следующие статьи: comments powered by HyperComments
ecm-zink.ru
Гальваническое цинкование — Цинковый портал
Гальваническое цинкование — технология основана на принципе работы гальванической пары. При гальваническом цинковании в качестве анода используется стальная или цинковая пластина, катодом является обрабатываемая деталь. Деталь при помощи технологических приспособлений погружается в солевой раствор цинковых соединений (электролит). Через раствор пропускается электрический ток. Происходит поляризация активных частиц (анионов, катионов). При гальваническом цинковании формирование поверхностного слоя детали производится из положительно заряженных ионов цинка, которые осаждаются на отрицательно заряженном катоде.
В зависимости от используемой соли цинка электролиты бывают:
· щелочными,
· нейтральными (слабощелочные),
· слабокислыми,
· кислыми.
Принципиальная схема гальванического цинкования
Каждый электролитический раствор при гальваническом цинковании обладает характерными специфическими признаками, поэтому при выборе рабочего состава для цинкования приоритетом служат окончательные технологические параметры изделия: толщина цинкового слоя, качество сцепления покрытия с металлической основой, стойкость защитного слоя к агрессивному воздействию.
Основной характеристикой при гальванической обработке (цинковании) считается толщина защитного слоя. Толщину цинкового покрытия (от 3 мкм до 40 мкм) можно регулировать путем изменения величины различных технологических параметров электролитического процесса:
· рабочей температуры электролита,
· концентрации активных составляющих рабочего раствора.
В конструкторской документации задается не только толщина цинкового покрытия, но и цвет финишной обработки (бесцветный, желтый, черный, хаки).
Преимущества гальванического цинкования
1. Высокая степень чистоты осаждаемого покрытия.
2. Большая химическая стойкость цинкового слоя.
3. Возможность регулирования толщины покрытия.
4. Высокие механические свойства защитного слоя.
5. Надежное сцепление осаждаемого цинка с покрываемым изделием.
6. Возможность цинкования деталей различной конфигурации.
7. Презентабельный внешний вид.
Сложности гальванического цинкования
При осаждении цинка на заданную поверхность потребляется значительное количество электроэнергии. Расход электроэнергии напрямую зависит от толщины наносимого слоя, от геометрических размеров обрабатываемых изделий и времени цинкования, технологических выходных параметров используемого оборудования (выпрямителей).
При гальваническом цинковании потребляется значительное количество воды. Это необходимо для увеличения степени чистоты обрабатываемой поверхности, улучшения процесса сцепления осаждаемого цинка со стальным основанием, придания изделию необходимого внешнего вида (согласно КД).
Дополнительная статья расходов при гальваническом цинковании связана с нейтрализацией вредных отходов, получаемых в процессе производства. Для решения этой проблемы строятся специальные очистные сооружения.
Гальваническое цинкование
– распространенный и востребованный способ нанесения защитного покрытия на стальные изделия. Технология гальванического цинкования хорошо изучена и постоянно модифицируется.www.zinkportal.ru
Гальваническое цинкование: виды и характеристики электролитов
При комнатной температуре цинк почти не реагирует с химическими элементами, при нагреве более +225°С скорость окисления критически возрастает. По мере увеличения толщины коррозионной пленки окислительные процессы замедляются. Гальваническое цинкование защищает от коррозии изделия из железа, никеля, меди и прочих металлов.
Виды и технологии цинкования
В настоящее время антикоррозионное цинкование производится несколькими способами. Конкретный метод выбирается с учетом назначения и размеров деталей и технологических возможностей предприятия и наличия оборудования.
- Холодное цинкование. Процесс покрытия осуществляется в результате электрохимических реакций, адгезия обеспечивается за счет молекулярного притяжения. Для защиты от коррозии поверхности покрываются специальными красками большим процентным содержанием высокодисперсного цинка. Наиболее простотой и доступный метод, имеет широкое распространение во время изготовления товаров народного потребления и металлоконструкций быстровозводимых зданий.
- Горячее цинкование. По частоте использования располагается на втором месте среди всех способов, а по качеству покрытия занимает лидирующие позиции. Недостатки – большие энергетические потери, вредное влияние на окружающую среду. Подготовленные детали погружаются в специальные ванны с расплавленным цинком, после выдержки вынимаются и оставляются в подвешенном состоянии для удаления излишков и остывания.
- Гальваническое цинкование. Технические параметры отвечают требованиям ГОСТ301-86, толщина покрытия до 30 мкм. Во время процесса цинк переходит из анода на поверхность изделия, для придания заданных свойств для покрытия применяются различные по химическому составу электролиты. Недостаток метода – сложность очистки технологических составов.
- Газо-термическое цинкование. Один из сложных методов, цинк расплавляется в нагретом газовом потоке и направляется на поверхность обрабатываемых деталей. Используется для обработки элементов промышленного назначения с большими линейными размерами. Осадки пористые, для увеличения защиты от коррозионных процессов требуется дополнительное покрытие слоя цинка.
- Термодиффузионное цинкование. Один из разновидностей горячего цинкования. Покрытие происходит за счет проникновения атомов цинка в сталь, образуется сложная структура железоцинкового сплава. Преимущества: детали обрабатываются в замкнутых пространствах, что минимизирует вредное воздействие на окружающую среду, покрытие ровное без микропор, толщина нанесения цинкового покрытия колеблется в широких пределах.
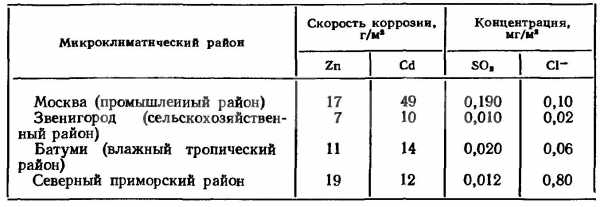
Скорость коррозии гальванического цинкования и кадмирования
На сегодняшний день для цинкования используется до 40% общей добычи металла, это наиболее используемый метод антикоррозионной защиты металлических поверхностей. В связи с тем, что потенциал цинка отрицательнее, чем имеет сталь, чугун и железо, защита происходит электрохимическим путем. При воздействии летучих продуктов синтетических смол, олиф и хлоридсодержащих углеводородов покрытия гальванического цинкования быстро разрушаются.
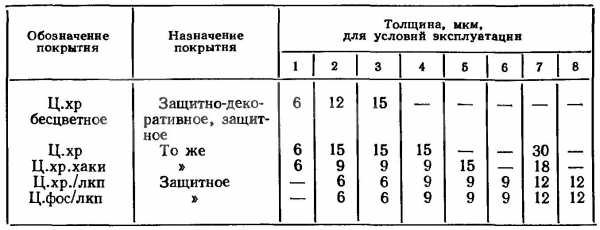
Используемая толщина цинкования
Для увеличения коррозионной стойкости после цинкования изделий выполняется специальная химическая дополнительная обработка в растворах хромовой или фосфорной кислоты.
Сравнительная характеристика применяемых электролитов
Для гальванического цинкования применяются простые и сложные электролиты. К первым относятся хлоридные, сульфатные, борфторидные и прочие. Ко вторым относятся аммонийные, цианидные, аминонокомплексные и цинкатные электролиты, для улучшения могут добавляться различные добавки и присадки. Цинкование гальваническое в простых электролитах происходит при довольно низкой поляризации катода, в сложных электролитах поляризация имеет значительные величины. Осадки цинкования в кислых растворах с крупнокристаллической структурой. Качество улучшается после введения различных добавок. В сложных электролитах покрытие мелкокристаллическое, плотное, имеет повышенные эксплуатационные показатели. Конкретный способ цинкования подбирается с учетом условий эксплуатации изделий и технических возможностей предприятия.
Низкие показатели рассеивающей способности простых электролитов ограничивают цинкование деталей со сложными геометрическими формами. Осаждение цинка из сложных растворов происходит при высокой рассеивающей способности, они дают равномерное покрытие на сложных поверхностях.
Кислые (простые) электролитыДля процесса требуется специальное оборудование гальванического цинкования, ванны изготавливаются из устойчивых пластиков, размеры ванн регламентируются государственными стандартами, при желании заказчика могут корректироваться с учетом особенностей производственных помещений. В зависимости от того, какие размеры и планировку имеет цех гальваники, предусматривается возможность монтажа линий или отдельных рабочих зон для гальванического цинкования.
- Сульфатные электролиты. Главный компонент – сульфат цинка, оптимальная концентрация не менее 200 мг/л. Для непрерывно двигающихся деталей цинкования концентрация может повышаться до 700 мг/л. Сульфатные растворы просты в работе, нетоксичны, отличаются высоким выходом по току. За счет этих показателей цинкование гальваническое в сульфатных электролитах получило широкое распространение во время обработки деталей простой конструкции. Для стабилизации кислотности в состав добавляются специальные добавки.
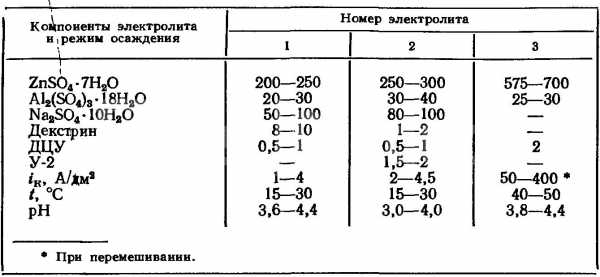
Режим цинкования и состав хлоридных электролитов
Первый электролит применяется для цинкования во вращающихся установках, второй для гальванического цинкования с блестящими покрытиями, третий для покрытия цинком листового проката и проволоки.
- Хлоридные электролиты для гальванического цинкования. Несмотря на высокую проводимость по току применяются намного реже. Причина – получить химически чистый хлорид цинка технологически трудно, а в остальных марках соли присутствует большое количество недопустимых примесей.
Режим цинкования и состав хлоридных электролитов
- Борфторидные электролиты цинкования. Главный компонент – борфторид свинца, для повышения показателей электропроводности добавляются соли натрия, структура поверхности улучшается за счет добавок состав ПВА. На выход по току большое влияние оказывает режим работы оборудования. Нанесение цинкового покрытия должно производиться при температуре +20°С. Масса цинка зависит от времени осаждения и концентрации раствора.
Режим цинкования и состав борфторидных электролитов.
Цианидные электролиты для гальванического цинкования
Большое влияние на качество осадков оказывает режим работы гальванических ванн. Температурные параметры электрохимических процессов контролируются автоматических, процентное содержание цинка проверяется по окончании каждой рабочей смены. Добавление в растворы органических веществ позволяет получать блестящее гальваническое цинкование. Работы на оборудовании разбиваются на отдельные этапы, соблюдение рекомендованных параметров каждого из них обеспечивает надлежащее качество покрытий.
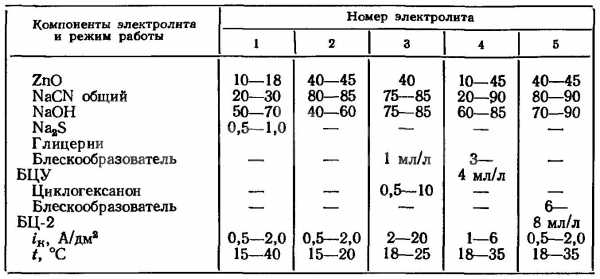
Состав цианидных электролитов для промышленного оборудования
Раствор цианида натрия готовится отдельно при обязательном соблюдении правил техники безопасности производства работ на промышленном оборудовании. После подготовки цианида натрия в раствор небольшими порциями при постоянном перемешивании вводится гидроксид натрия. На завершающем этапе приготовления электролит разводится дистиллированной водой до получения расчетной концентрации цинка. Цинкование гальваническое в растворе производит значительно меньше примесей, при необходимости они удаляются электрохимическим путем по мере накопления.
Цинкатные электролитыПринципы гальванического цинкования в цинкатных электролитах отличаются по показателям плотности тока. Диссоциация компонентов происходит ступенчато, для осаждения необходимы высокие значения катодной поляризации. Поверхность изделия имеет губчатую структуру и темный цвет из-за микрочастиц, появляющихся за счет электрохимического растворения в щелочной среде цинковых анодов. Для устранения проблемы в раствор добавляются соединения четырехвалентного олова. Допускается в тех же целях использовать трилон Б, полиэтиленполиамин и др. Добавки дают возможность получать более полное цинкование гальваническое при увеличенных параметрах плотности тока.
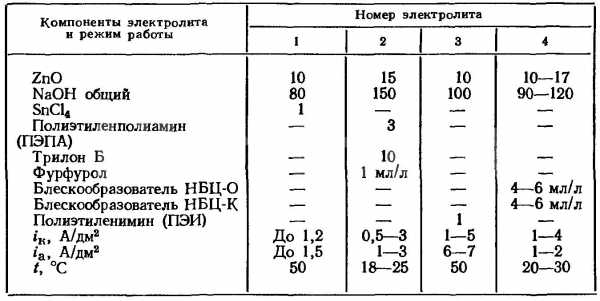
Состав и режим цинкатных электролитов
- Хлораммонийные электролиты. За счет высокой катодной поляризации и электропроводности достигается оптимальная рассеивающая способность. Цинкование гальваническое получается гладким и блестящим, покрытия равномерные на сложных профилях. Оборудование не требует дополнительных механизмов перемешивания раствора, для стабилизации показателей кислотности используются буферные добавки. Для получения блеска во время гальванического цинкования применяются блескообразователи. В промышленности широко применяются хлораммонийно-уротропные электролиты, для депассивации анодов добавляется ацетат аммония.
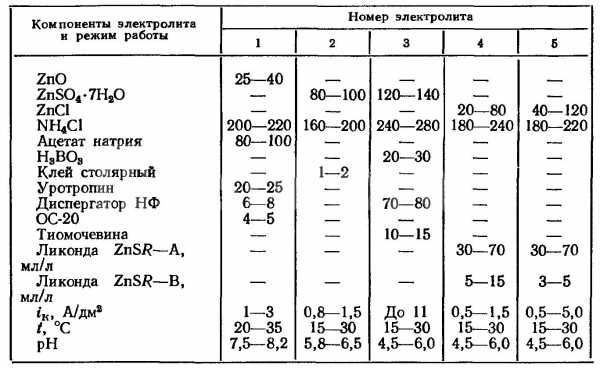
Состав и режимы хлораммонийных электролитов для гальванического цинкования
- Аминокомплексные электролиты для гальванического цинкования. Получают за счет добавки к хлораммонийным различных органических соединений, имеют высокую поляризацию цинка. Осадки мелкокристаллические, при использовании специальных дополнительных компонентов блестящие. Оборудование для производства работ обыкновенное,
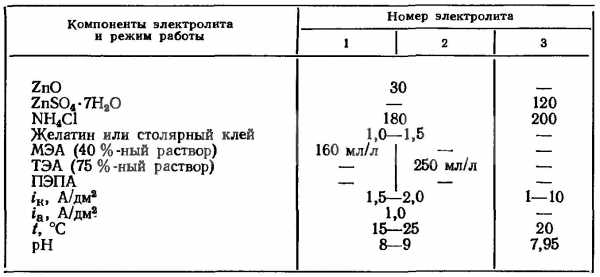
Состав электролитов для гальванического цинкования с использованием аминокомплексных соединений
- Пирофосфатные электролиты для гальванического цинкования. Для оборудования технологических линий применяются емкости из пластиков, подготовка деталей производится в отдельных ваннах. В результате химического взаимодействия исходных компонентов выпадает осадок пирофосфата цинка, в дальнейшем он растворяется с образованием комплексных соединений цинка.
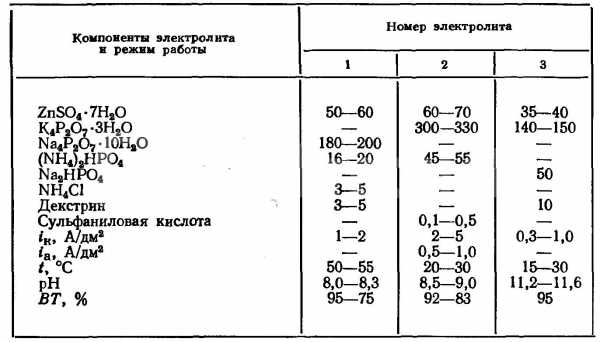
Состав пирофосфатных электролитов для гальванического цинкования
Для повышения качества и устойчивости цинковых покрытий дополнительно может выполняться финишное осаждение верхнего слоя. Чаще всего в промышленности в этих целях используется хроматирование.
Цинкование в домашних условиях своими руками
Небольшие по размерам изделия можно цинковать своими руками. Для гальванического цинкования применяется простой кислый электролит, приготавливаемый из 200 г сернокислого цинка, 50 г сернокислого аммония, 15 г уксуснокислого натрия. Компоненты растворяются в одном литре воды, температура электролита во время нанесения цинкового покрытия 18 ÷ 25°С, плотность по току 1,5 А/дм2.
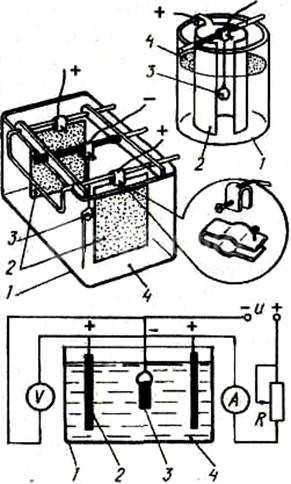
Оборудование своими руками для цинкования
1 – емкость под электролит. Можно изготовить своими руками из пластиков.
2 – аноды из цинка. Размеры должны отвечать размерам емкости, количество подбирается в зависимости от размещения обрабатываемых деталей.
3 – изделия цинкования. Размеры и количество должны учитывать технические характеристики ванны.
4 – электролит. Раствор приготавливается согласно существующих рекомендаций по химическому составу.
Толщина цинкового покрытия своими руками регулируется временем выдержки, плотностью тока и концентрацией электролита. Цинкование гальваническое должно производиться с соблюдением техники безопасности, размеры оборудования обеспечивать благоприятные параметры процесса.
plast-product.ru
Электролитическое цинкование | Защитные покрытия металлов
Различают два основных типа электролитов, применяемых для цинкования: кислые и щелочные. В кислых электролитах цинк находится в виде простых гидратированных ионов, разряжающихся на катодах с незначительной поляризацией. В щелочных электролитах цинк находится в виде комплексных ионов, разряд которых сопровождается значительной катодной поляризацией.
Кислые электролиты достаточно устойчивы, допускают применение высоких плотностей тока, особенно при перемешивании, при высоком выходе по току (даже при большой концентрации кислоты в электролите). Щелочные электролиты менее устойчивы; допустимая плотность тока в них ограничена и с повышением плотности тока заметно снижается выход по току.
Вследствие незначительной катодной поляризации в кислых электролитах структура цинковых покрытий грубее, чем в щелочных. Однако при введении коллоидов удается и в кислых электролитах получать цинковые покрытия с удовлетворительной структурой. Главным недостатком кислых электролитов является неравномерное распределение тока и металла на сложнопрофилированных изделиях. В результате этого толщина покрытия на выступах и других участках с повышенной плотностью тока значительно больше, чем в углублениях. Между тем защитные свойства как цинковых, так и других металлических покрытий определяются не средней толщиной на всей поверхности изделий, а фактической толщиной на том или ином участке. По этой причине кислые электролиты не рекомендуется применять для цинкования изделий сложной формы. Они успешно применяются для покрытия проволоки, ленты, полосы, т. е. изделий, не имеющих выступов и углублений. В этом случае при интенсивном перемешивании электролита можно применять высокую плотность тока, т. е. форсировать процесс.
Изделия сложной формы цинкуют в щелочных — комплексных электролитах, где катодная поляризация больше и, следовательно, происходит более равномерное распределение тока и металла.
Из кислых цинковых электролитов наибольшее распространение имеют сернокислые, из щелочных — цианистые, точнее щелочноцианистые. Реже применяют кислые хлористые и фторборатные цинковые электролиты.
www.stroitelstvo-new.ru
Гальваническое цинкование, линия цинкования, ванна для цинкования
В современном мире используется большое количество методов для защиты металлических поверхностей от образования слоя коррозии, который приводит к тому, что металлическое покрытие начинает становиться более хрупким и разрушается. На сегодняшний день для эффективной защиты от коррозии используется гальванический метод обработки металлов цинком.
Гальваническое цинкование металла
Гальваническое цинкование представляет собой процесс нанесения на поверхность металла цинка в растворе электролита. Данный метод относится к разряду наиболее эффективных для борьбы с появлением каррозии на металлических изделиях. Цинковый сплав покрывает металла тонкой пленкой, которая обладает отличными защитными свойствами. Она дает возможность после обработки использовать металлы в агрессивной среде. Она не дает различным веществам проникнуть в структуру металла для изменения его свойств. В результате использования цинка и электролита металлы становятся более прочными и устойчивыми к условиям окружающей среды.
Цинк является подходящим металлом для обработки других видов металлических материалов. После проведения процедуры гальванического цинкования на поверхности обработанного металла появляется слой пленки, которая придает ему серебристый оттенок, который имеет голубоватый подтон. Благодаря изделие из такого материала приобретает более эстетический внешний вид.
Гальваническое цинкование металла обладает достоинствами и недостатками.
К достоинствам данной процедуры относятся:
- высокий уровень производительности. За короткое время раствором из цинкового сплава и электролита покрывается большое количество металлических изделий.
- Аккуратность проведения процедуры. После обработки таким образом металлических изделий образуется равномерное покрытие, которое охватывает все изделий целиком. Практически не образуется ни подтеков, ни сколов.
- Улучшение внешних качеств отдельных металлических предметов. данный метод отлично подходит не только для защиты от коррозии, но и для придания изделиям из разных металлов эстетического внешнего вида. Поверхность покрывается тонким слоем пленки серебристого оттенка. Изделие приобретает блеск.
Главным недостатком проведения данной процедуры является низкий уровень сцепления с разными видами металлов. В результате защитный эффект от коррозии длится не долго. К тому же в результате анодирования может образоваться хрупкость металла, что приводит к разрушению конструкции.
Сегодня гальваническое цинкование используется для покрытия отдельных элементов цинковым сплавом для защиты их от коррозии и для придания им эстетического внешнего вида. Таким методом обрабатываются гвозди, метизы и крепежные инструменты.
Таблица 1. Гальваническая совместимость металлов
Металл | Сталь | Алюминий | Дюраль | Медь | Латунь | Бронза | Хром | Никель | Цинк | Олово | Припой ПОС |
---|---|---|---|---|---|---|---|---|---|---|---|
Сталь | + | + | + | – | – | – | + | + | + | + | + |
Алюминий | + | + | + | – | – | – | + | – | + | П | П |
Дюраль | + | + | + | – | – | – | + | – | + | П | П |
Медь | – | – | – | + | + | + | + | + | – | П | П |
Латунь | – | – | – | + | + | + | + | + | – | П | П |
Бронза | – | – | – | + | + | + | + | + | – | П | П |
Хром | + | + | + | + | + | + | + | + | + | П | П |
Никель | + | – | – | + | + | + | + | + | + | П | П |
Цинк | + | + | + | – | – | – | + | + | + | + | + |
Олово | + | П | П | П | П | П | П | П | + | + | + |
Припой ПОС | + | П | П | П | П | П | П | П | + | + | + |
Гальваническое покрытие металла
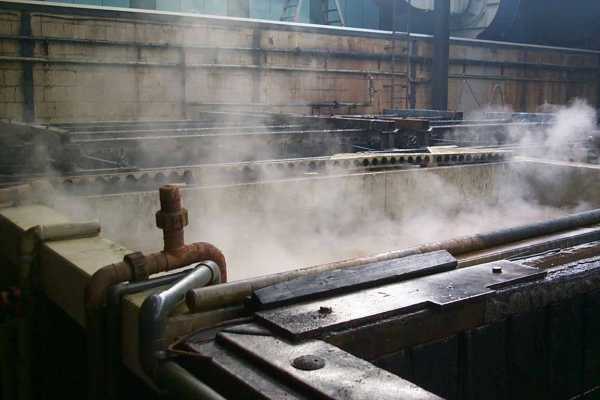
Цинкование гальваническое технология представляет собой электролитический химический процесс, который заключается в следующем:
- К двум металлам, которые находятся в ванне для гальванической обработки подводится электрический ток. Для этого применяются специальные электроды.
- Такой металл, как цинк может быть использован в любой своей форме. Его помещают в специальные контейнеры сетчатого типа.
- В процессе электролиза заряженные частицы цинк распадаются на ионы и оседают на обрабатываемой поверхности. При этом слой покрытия является достаточно небольшим.
- Под действием электрического тока происходит расщепление цинковых анодных частиц.
- Для обработки металлов в производственных условиях таким методом используются три вида раствора: кислотный, щелочной, цианидный. Их выбор зависит от того, какой металл подвергается обработке цинковым сплавом.
Внимание: Гальваническую обработку металлов цинком лучше всего осуществлять в слабой кислой среде. Благодаря этому есть возможность получить более плотное покрытие и ровный защитный слой.
Гальваническая ванна цинкования
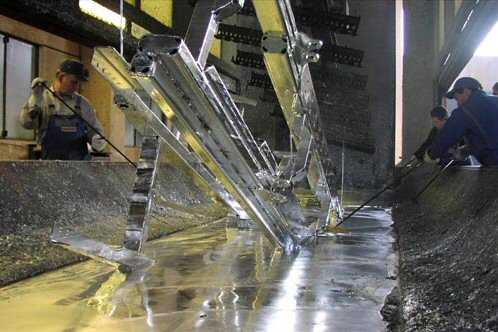
В современном мире для гальванической обработки металлов в растворе цинкового сплава необходимо специализированное оборудование. На производственных предприятиях используются производственные линии, которые состоят из элементов, позволяющих в промышленных масштабах осуществлять гальваническую обработку металлических изделий.
Оборудование для гальванического цинкования представлено специализированными ваннами. Они производятся из материалов, которые не разрушаются под воздействием агрессивной среды.
Гальванические ванны цинкования могут быть нескольких видов:
- мелкогабаритная ванна. Она предназначена для обработки небольших металлических изделий.
- Среднегабаритная ванна. В ней может с легкостью поместиться один предмет из металла, который состоит из металлических деталей. Для полной обработки изделия их нет необходимости отсоединять.
- Крупногабаритная ванна. Она используется для обработки цинковым сплавом крупных предметов. В ней даже размещаются трубы небольшой длины.
Основным недостатком гальванического оборудования является то, что оно не подходит для обработки изделий нестандартных изделий.
Также к оборудованию для проведения данного процесса обработки металлических изделий является приспособление для подведения электрического тока. Без него оседание частиц цинка на поверхность металлов практически невозможно. Оно должно иметь электроды для подключения к металлу и сплаву цинка.
Линия гальванического цинкования
Видео. Гальваническое покрытие металлов.
lkmprom.ru
Электрохимическое цинкование – Справочник химика 21
РАБОТА 3. ЭЛЕКТРОХИМИЧЕСКОЕ ЦИНКОВАНИЕ Введение [c.20]Цель работы — ознакомление с процессом электрохимического цинкования в стационарном и колокольном электролизерах. Изучение влияния состава электролита и режима электролиза, а также осаждения в нестационарном режиме — при реверсировании тока на качество покрытий, структуру и выход по току металла. [c.24]
Электрохимическое цинкование щироко распространено на машиностроительных и приборостроительных заводах для защиты от коррозии разнообразных деталей машин, в том числе различного крепежа (болты, гайки, шайбы) и пружин. Многие детали, подвергаемые цинкованию, испытывают при работе значительные статические и динамические нагрузки и нередки поломки стальных цинкованных деталей вследствие их наводороживания. [c.299]
Влияние цинковых покрытий на механические свойства сталей зависит от способа их нанесения. При электрохимическом цинковании наиболее сильное наводороживание и связанное с этим охрупчивание основного металла происходит в цианистых электролитах. Электролитическое цинкование не допускается для деталей, изготовленных из сталей с прочностью более 140 кгс/мм . [c.699]
Для покрытия мелких деталей при электрохимическом никелировании, так же как п при цинковании, широко применяют электролизеры с вращающимися колоколами или барабанами. [c.39]
Для получения металлических защитных покрытий применяются различные способы электрохимический (гальванические покрытия), погружение в расплавленный металл, металлизация, термодиффузионный и химический (см. 52). Из расплава получают покрытие цинка (горячее цинкование) и олова (горячее лужение). [c.219]
Главнейшими в настоящее время являются процессы никелирования, хромирования, цинкования, меднения, покрытия серебром, золотом и др. Наряду с этим разработаны способы осаждения некоторых редких металлов и сплавов. К гальванотехнике относится и первый промышленный электрохимический процесс воспроизведения художественных и технических рельефных предметов, получивший название гальванопластики. [c.4]
При работе ванны цианистого цинкования в автомате барабанного типа концентрация карбонатов в растворе постепенно увеличивается вследствие поглощения диоксида углерода из воздуха и электрохимического окисления цианидов на транспассивных цинковых анодах. [c.219]
Митрофанов Э. В., Флёров В. Н. Кинетика электрохимических процессов на пассивных анодах в цианистом электролите цинкования, // ЖПХ, 1972, 45, № 7, 1497. [c.314]
К электрохимическим — получение покрытий на катоде (цинкование, кадмирование, хромирование, никелирование, лужение), анодное оксидирование (анодирование алюминия и других легких сплавов), электрофоретическое осаждение порошковых материалов. [c.51]
Ограничениями в использовании кадмия является его высокая стоимость и дефицитность. В последние годы на ряде производств ограничено применение кадмиевых покрытий (вплоть до полного их исключения) вследствие высокой токсичности соединений кадмия. Поскольку кадмиевые покрытия более стойки в среде, содержащей ионы хлора, кадмирование используют для защиты черных и цветных металлов, соприкасающихся с морской водой, растворами солей. Кадмий более пластичный металл, чем цинк, поэтому кадмирование используется для защиты наиболее ответственных резьбовых изделий. Однако в последнее время все шире используют и цинковые покрытия. В промышленных условиях для создания электрохимической защиты предпочитают цинковые покрытия. Цинкованию подвергают не только готовые изделия, но и стальные листы, ленту. Цинковое покрытие часто применяют для защиты от коррозии водопроводных труб и запасных емкостей. В мягкой воде цинковое покрытие защищает сталь хуже, чем в жесткой. В горячей непроточной воде (свыше 70 °С) цинковое покрытие не обеспечивает надежной защиты стали от коррозии, так как в этих условиях цинк защищает сталь лишь механически. [c.281]
Применение цинковых или кадмиевых прокладок, покрытие цинком или кадмием медных сплавов при контакте их со сталью, а также цинкование или кадмирование стальных деталей при контакте с алюминиевыми сплавами, по-существу, также основано на принципе электрохимической защиты. В обоих случаях в систему медь — железо и железо — алюминий включают третий анод (цинк или кадмий), смещающий потенциал к таким значениям, при которых коррозия контактирующих анодов уменьшается или оказывается равной нулю . Этим методом широко пользуются в технике, что было иллюстрировано выше на конкретных примерах защиты магниевых и алюминиевых сплавов, а также судостроительных конструкций. В частности сообщается, что металлизация судостроительных сталей цинком обеспечивает надежную их эксплуатацию в контакте с алюминиевыми сплавами в течение длительного времени (5—8 лет). [c.198]
Операции, при которых образуются растворы или промывные воды, содержащие цианистые соединения к ним относятся основные процессы Электрохимического выделения металла из их цианистых солей (цинкование, кадмирование, меднение, серебрение), а также операции промывки после этих процессов. [c.18]
При работе с цианистыми электролитами и солями вследствие их большой ядовитости соблюдают особые меры предосторожности к работе на ваннах допускаются лица, прошедшие дополнительный инструктаж в местах хранения цианистых веществ не разрешается хранить кислоты, а на участках цианистых ванн нежелательно устанавливать кислые ванны (меднения, цинкования и др.) категорически запрещается принимать пишу, воду и курить в помещениях, где имеются ванны перед едой, курением и пользованием туалетом необходимо снять спецодежду, промыть руки раствором сернокислого железа и затем тщательно вымыть их теплой водой с мылом спецодежду работающих с цианистыми ваннами следует хранить отдельно от общей спецодежды и личной одежды лица, имеющие повреждения кожи на руках, к работе не допускаются отработанные цианистые растворы и сточные воды, содержащие цианиды, должны обезвреживаться в специальных емкостях путем обработки сильными окислителями (гипохлоритами), после чего стоки могут направляться в общий нейтрализатор электрохимического участка. При малых объемах сточных вод их следует обезвредить раствором сернокислого железа. [c.744]
От агрессивных воздействий среды стальные конструкции защищают окрашиванием лакокрасочными материалами, горячим цинкованием, газотермическим напылением цинка или алюминия, электрохимической защитой, облицовкой химически стойкими неметаллическими материалами и т. д. [c.439]
Кадмирование. Кадмий по свойствам весьма сходен с цинком, но в качестве гальванического покрытия имеет много преимуществ. Цвет й внешний вид кадмиевого осадка красивее, чем цинкового, коррозионная стойкость и, в частности, защита железного изделия — совершеннее (потенциал кадмия лишь немного отрицательнее потенциала железа). В отличие от цинка кадмий не растворяется в щелочах. Кадмиевые покрытия эластичнее цинковых. Электрохимический эквивалент кадмия почти вдвое больше, чем цинка (ат. вес кадмия 112,41, цинка 65,38), поэтому кадмирование протекает быстрее, чем цинкование. Все это привело к довольно широкому распространению кадмирования, несмотря на высокую стоимость кадмия. [c.554]
Металлические горячие (цинкование, лужение, свинцевание, алю-минирование из расплавленных металлов) диффузионные (алитирование — насыщение поверхности алюминием, азотирование, силицирование и др.) металлизация путем распыления металлов (алюминием, цинком, свинцом, оловом, медью, бронзой и т. д.) контактные, в результате электрохимического вытеснения, без наложения внешнего тока (лужение стали и латуни, золочение серебра, меднение стали и-др.) гальванические—получаемые электрокристаллизацией (никелирование, меднение, цинкование, лужение, хромирование и т. д.) химические — получаемые в результате химических реакций на поверхности металла, например, химическое никелирование, серебрение и т. п. [c.333]
На заводах, выпускающих серебряно-цинковые источники тока применяются никелирование, кадмирование, цинкование и серебрение. Первые три вида покрытия наносятся на токоотводы отрицательных электродов некоторых типов серебряно-цинковых источников тока, причем никель и кадмий служат для предотвращения растворения токоотвода, а цинк наносится в качестве электрохимически активного материала. [c.30]
Рассмотрим более подробно роль защитного покрытия на примере лужения и цинкования железа. Оловянные и цинковые покрытия по своей электрохимической природе различны, так как цинк в ряду напряжения металлов стоит левее железа, а олово — правее нормальный потенциал железа по водородной шкале равен — 0,4Л цинка — 0,7Г>, олова — 0,14. Следовательно, по активности эти мета.илы можно расположить в следующий ряд Zn > Ре > Sп. [c.350]
Автомат имеет 26 рабочих позиций и состоит из следующих нормализованных узлов двух автооператоров 1 четырех основных секций 2 (см. рис. 27) с направляющими четырех основных секций 3 без направляющих двух секций загрузки и разгрузки 4] двух барабанов 5 четырех ванн 6 для химических операций (декапирования, осветления, пассивирования, улавливания) пяти ванн 7 для электролитических операций (цинкования) двух ванн никелирования 8 шести ванн холодной промывки 9 трех ванн горячей промывки 10 двух ванн электрохимического обезжиривания 11 пяти бортовых отсосов 12 сушила шнекового 13-, сушила камерного 14 козырька /5 двух бортовых отсосов крайних 16 и трех бортовых отсосов односторонних 17. [c.77]
Разработаны технологические процессы нанесения на поверхность алюминиевых деталей различных гальванических покрытий. Развитие электрохимических методов обработки проката в черной металлургии с целью защиты от коррозии неизмеримо увеличило масштабы производства, мощности генераторов постоянного тока низкого напряжения и регулирующей аппаратуры, внедрения автоматического контроля и регулирования основных технологических параметров различных процессов. К этим процессам относятся катодное и анодное обезжиривание, травление и электрополировка металлов, а также нанесение различных покрытий, в том числе лужение и цинкование листового металла, полосы и проволоки, и, наконец, оксидирование алюминия, магния и их сплавов. [c.10]
Электрохимическое цинкование и кадмирование алюминия и его сплавов в цианидных электролитах можно осуществлять и без предварительного меднения. Тонкие пленки никеля или железа наносят на поверхность алюминиевых сплавов погружением изделий на 1—2 мин в подкисленные соляной кислотой (10—20 мл/л НС1) растворы хлоридов этих металлов (например, 20—30 г/л РеС1з) при 90—95 °С. [c.332]
Электрохимическое цинкование вызывает потерю пластичносш сталей вследствие наводороживания. Сгали с пределом прочности выше 1380 МПа цинковаршю не подлежат. [c.899]
Использование цинка, кадмия и ртути в технике. Около 40% добываемого цинка используется на цинкование, т. е. покрытие поверхности черных металлов для защиты нх от коррозии. Сам цинк, как у.же указывалось, будучи электрохимически более активным, чем железо, к коррозии вполне. устойчив благодаря образованию на его поверхностп прочной оксидной пленки. Покрытие черных металлов цинком производится различными способами горячим цинкованием, т. е. погружением металла в расплавленный цинк распылением расплавленного циика но поверхности черного металла действием нарами цинка на поверхность черного металла электролитически. Цинковое покрытие даже в случае нарушения его целостности продолжает оказывать на железо защитное действие уже ио электрохимическому ирипиину (см. гл. XX, 12). [c.333]
В колокольную ванну цинкования заливают цианистый электролит с концентрацией общего цианида 85 г/л (в расчете на Na N). Необходимая толщина цинкового покрытия 10 мкм. Для цинк-цианистого электролита данного состава выход по току в стационарных ваннах составляет около 80 %. В колоколах общая расчетная продолжительность процесса должна быть увеличена на 15 % с учетом механического истирания покрытий и неравномерности пересыпания деталей. Удельные потери раствора при процессе около 115 см на 1 м поверхности деталей. Проектная норма расхода цианидов на электрохимическое разложение 0,8 г/(А-ч) [24]. [c.220]
Важнейшая область прикладной электрохимии — гальванотехника. Этим названием объединяются два направления гальваностегия — получение гальванических покрытий иа металлах и гальванопластика — электрохимическое получение точных металлических копий с рельефных поверхностей (Якоби). Сейчас гальваиоиластика находит применение для нанесения металлических рисунков на полупроводники и непроводящие материалы (например, в производстве печатных радиосхем для миниатюрных радиоирпемииков). Гальванические покрытия наносят для защиты металлов от коррозии, а также в декоративных и специальных целях (увеличение отрамсопротивления электрических контактов и т. д.). Покрытие осуществляют электролизом растворов как с растворимым анодом (никелирование, кадмирование, цинкование, лужение, серебрение и др.), так и с нерастворимым (хромирование, золочение). Покрываемое изделие всегда является катодо . [c.264]
К электрохимическим относятся методы получения покрытий под действием электрического поля на катоде (цинкование, кадмирование, хромирование, никелирование, осаждение сплавов различного состава), анодное и анодно-катодное оксидирование (анодирование алюминия и его сплавов, микродуговая обработка) электрофоретическое и электростатическое осаждение порошковых материалов, нанесение комбинированных покрытий за счет сочетания процессов электролитического и электрофоретического осаждения. [c.50]
Для помещений, где выполняют дробеструйную, гидроабразивную и дробеметную очистку, обезжиривание органическими растворителями, химическую и электрохимическую обработку, горячее цинкование, консервацию, лакокрасочные и моечные работы, должна предусматриваться приточно-вытяжная вентиляция, которая обеспечивает удаление вредных примесей до концентраций не превышающих нормы. Очистку дробью и металлическим песком п оводят в помещениях и на установках, изолированных от других производственных участков. [c.742]
Повышение эффективности холодного фосфатирования и получение новых качественных характеристик покрытия может быть достигнуто при катодной поляризации стали в процессе ее обработки в ванне. В этом случае, если плотность тока превышает 0,15 а/дм , количество образующегося фосфата оказывается пропорциональным времени и плотности тока, а потенциал фосфати-руемой стали достигает значений, отвечающих потенциалу выделения цинка. Электрохимический эквивалент осадка в ванне фосфатирования составляет примерно 3 г/а – ч в свежеприготовленном растворе и снижается по мере проработки ванны. Таким образом, здесь происходит одновременное цинкование и фосфатирование. Потенциал отфосфатированной стали, обработанной при плотности тока 0,5 а/дм за 10 мин, в 3%-ном растворе НаС1 сохраняет значение около—1,0 в (по медно-сульфатному электроду) в течение 80 ч. [c.92]
Исследовано [72] влияние добавки цетилтриаммоний-бромида, предложенной в [73, 74], на диффузию водорода через сталь при цинковании в различных электролитах, в том числе и в цианистом. Диффузия водорода изучалась электрохимическим методом [10]. Авторы установили, что введение в цианистый электролит 1 г/л цетилтриаммоний-бромида оказывает незначительное влияние на диффузию водорода при цинковании. [c.202]
Для нанесения электрохимических и химических покрытий мелких деталей в барабанах применяется автомат типа УТ5 (фирмы Гальванотехника ). В нем производится цинкование, кадмирование, никелирование и другие гальванические покрытия (УТЗ), оксидирование (УТ513) и фосфатированне (УТ512). Техническая характеристика автоматов типа УТЗ приведена в табл. 3.10. Автомат овальной формы, возвратного типа. Он состоит из металлоконструкции, расположенной внутри рядов ванн автомата, механизма подъема, опускания и передвижения и транспортного устройства с 36 каретками (тележками). Подъемный ме- [c.102]
Автоматические линии оснащаются вспомогательным оборудованием ваннами селективной очистки, установками БРП (бесконтактный переключатель), буферными и запасными ваннами. Ванны селективной очистки предназначены для электрохимической очистки никелевых электролитов от металлических загрязнений. Они изготовлены из стального футерованного корпуса, двух катодных и четырех анодных рядов. Установка БРП устанавливается на ванне для включения и выключения реле времени, технологического тока и воздуха. Буферные ванны используются при очистке зеркала электролита в ваннах обезжиривания и состоят из корпуса со сливным карманом и крышки с люком. Запасные ванны служат для приготовления или хранения электролитов при ремонте ванн или фильтрации растворов и состоят из сварного корпуса и крышки с люком. Эти ванны имеют три модификации для цианистых и кислых электролитов, для электролитов фосфатирования и хромирования и электролитов щелочного лужения и оксидирования стали. Автооператорные линии для цинкования на подвесках модели АЛГ-35М разработаны ЦКБ ГП (рис. 3 38 и 3.39). [c.125]
Основные задачи, стоящие перед народным хозяйством в период строительства коммунизма сформулированы в программе КПСС, принятой XXII Съездом, и пре-/ дусматривают осуществление в массовом масштабе авл томатизации производства, находящей в последние годы все большее применение. Эта тенденция характерна н для цехов электрохимической обработки металлов, в которых осуществляется электрохимическое нанесение металлических покрытий на детали машин или такие виды электрохимической обработки, как обезжиривание и травление, а также лужение, цинкование или меднение рулонной стали, листов, труб, проволоки. [c.3]
chem21.info
Цинковые покрытия – сравнение методов цинкования и их характеристики
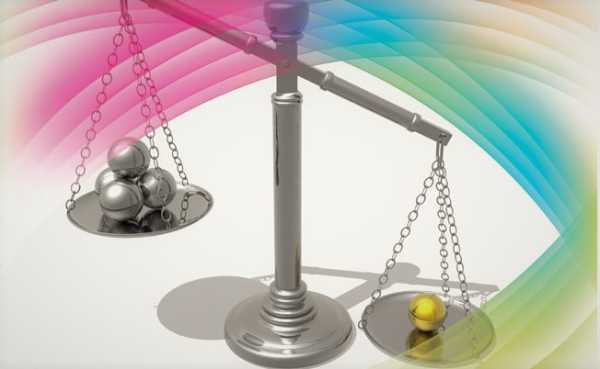
Глубокий анализ-сравнение различных методов нанесения цинковых покрытий!
Как уже говорилось, горячее цинковое покрытие представляет из себя систему железо-цинковых сплавов с различным отношением содержания железа и цинка с постепенно уменьшающимся содержанием железа по мере приближения к внешней стороне покрытия.
Все железо-цинковые сплавы прочнее, чем сталь основы, что придает покрытию высокую устойчивость к истиранию. Наоборот, внешний ή-слой мягче, чем сталь, что создает хорошие условия для устойчивости к удару.
Таким образом, совокупность этих слоев создает устойчивость к разрушению при перевозках, монтаже и при обслуживании.
Цинковое покрытие, нанесенное электрохимическим способом, по механическим свойствам подобно обычному цинку, то есть является относительно мягким. Кроме того, электрохимическое цинкование осуществляется при обычной температуре, поэтому, кроме очень узкой переходной области, в системе не наблюдается железо-цинковых сплавов, и адгезия цинкового слоя к металлу основы относительно невелика. Сам процесс нанесения покрытия представляет определенные сложности с точки зрения равномерности нанесения покрытия, поскольку ток стремится избегать полостей. Приходится изощряться при пространственном расположении анодов. Метод является достаточно дорогостоящим, и поэтому ограничиваются нанесением покрытия на мелкие, в том числе резьбовые детали. Он не может конкурировать с методом горячего цинкования при защите цинком крупных, средних и даже большинства относительно мелких деталей.
Рис. 2. 11. Часть ассортимента деталей, которые могут быть механически оцинкованы.
Наоборот, метод шерардизации в модификации “Дистек” постепенно начинает отвоевывать пространство как у электрохимического, так и горячего цинкования. Достаточная толщина покрытия (до 60-120 мкм), его равномерность и плотность с последующей защитой методом фосфатирования позволяет изделиям выдерживать в солевом тумане (одним из основных методов определения коррозионной устойчивости изделий) до 1500 часов, что является очень хорошим показателем. Поскольку нанесение покрытия производится при 380-400°С на поверхности изделия, образующиеся железо- цинковые слои на данных изделиях получаются более твердыми, чем в случае электрохимического нанесения покрытий. Поступают сообщения о создании новых установок, позволяющих обрабатывать все более крупные изделия.
Сравнение свойств различных видов цинковых покрытий очень наглядно видно из таблицы № 2.12.
Поскольку, как видно из таблицы, все виды цинковых покрытий имеют как свои преимущества, так и недостатки, очевидно, что каждый тип покрытия имеет свою нишу применения. Встает вопрос, насколько долговечны покрытия различного типа, и имеется ли в этом вопросе преимущество одного типа покрытия перед другим. Ответ на этот вопрос дает рис. № 2.12, где приведены времена жизни покрытий, нанесенных различными способами и различной толщины. Из рисунка видно, что практически все точки для покрытий, полученных самыми разнообразными способами (горячее цинкование, электрохимическое, шерардизация, окрашивание в координатах “длительность службы” – “толщина покрытия” с очень малым разбросом укладываются на единую кривую, что говорит об отсутствии связи времени службы изделия с типом нанесения покрытия, основной фактор – это толщина покрытия. Однако надо иметь в виду, что красочное покрытие ограничено в сроке службы из-за подверженности его истиранию.
Рис. 2.12. Зависимость времени жизни покрытия от его толщины при разных способах нанесения.
Таблица № 12.2. Сравнение различных методов нанесения цинковых покрытий на функциональные свойства изделий (механическое цинкование в таблице не рассматривается, но по характеристикам оно ближе всего к методу шерардизации).
Характеристика покрытия |
Горячее цинкование |
Электрохимическое нанесение |
Шерардизация (механич. цинкование) |
Напыление цинка |
Окраска цинк-содержащими красками |
Адгезия |
Покрытие, сросшееся со сталью, из-за наличия различных железосодержащих слоев |
Хорошая, сравнимая с таковой для покрытий из других металлов |
Хорошая, сравнимая с таковой для электрохимического покрытия |
Хорошая механическая подготовка под окраску при условии, что дробеструйная подготовка проведена нормально |
При хорошей дробеструйной обработке дает наилучшие результаты |
Непрерывность и однородность |
Хорошие – любая непроцинковка хорошо видна в виде “черных пятен”. Некоторый избыток цинка на точках слива |
Однородная в пределах возможности ванны. Поры не представляют проблемы, поскольку сталь защищается прилегающим цинком |
Покрытие тонкое на углах – в противоположность горячему цинкованию |
Зависит от опытности оператора. Покрытие пористое, но поры вскоре заполняются продуктами коррозии цинка |
Хорошая – любые поры заполняются продуктами реакции |
Толщина |
Обычно 50-125 мкм на трубах и другой продукции; более толстые покрытия до 250 мкм получаются на сталях, раскисленных кремнием или после дробеструйной очистки перед цинкованием. Покрытия толщиной 10-30 мкм применяются на проволоке и листе. |
Толщина в пределах 3-15 мкм. Более толстые слои возможны, но невыгодны экономически |
Изменяются по желанию, обычно в пределах 10-80 мкм |
Толщина изменяется в интервале 100-150 мкм, но покрытия до 500 мкм могут использоваться |
До 40 мкм краски (или более в специальных случаях) при окраске в один слой |
Формуемость и механические свойства |
Обычные покрытия, на конечных изделиях не пригодны к изменению формы; слой сплава устойчив к абразивному воздействию, но хрупкий при гибке. Специальные покрытия с тонким слоем сплава или при его отсутствии хорошо формуются (на листах) и устойчивы к сварке |
Сталь с электрохимическим покрытием обладает превосходной формуемостью и может быть сварена точечной сваркой. Небольшие детали обычно подвергаются такой обработке перед окраской |
Хорошие. Не наблюдается охрупчивания высокопрочных сталей |
При применении конечной продукции формовка не нужна. Можно осуществлять сварку через тонкое покрытие, если это необходимо, но обычно экранируют края, которые необходимо сварить, и после сварки эти места покрывают слоем цинка |
Сопротивление к истиранию лучше, чем у обычных красок. Окрашенные листы могут быть подвергнуты формовке и сварке с небольшими нарушениями покрытия |
Последующая обработка |
Конверсионные покрытия – хроматы предотвращают белую ржавчину; фосфатирование на новых листах является хорошей основой для последующей окраски |
Конверсионные покрытия (например, хроматы) для предотвращения белой ржавчины. Часто используются как основа для последующего окрашивания |
Могут быть применены конверсионные покрытия |
Возможно нанесение защитных покрытий, которые становятся основой для окрашивания, давая более долгую жизнь изделиям |
Может быть использова на отдельно или в качестве грунтовки под обычные красочные покрытия |
Другие свойства |
Доступны ванны различных размеров. Части изделий до 25 метров могут быть оцинкованы в некоторых случаях. Требуется внимательное отношение к дизайну изделия.Имеются непрерывные процессы цинкования листов и проволоки |
Любые размеры ванн доступны. Процесс обычно используется для простых, в основном, малых изделий, пригодных для цинкованиях в барабанах или при непрерывном цинковании листов и проволоки. Никакого нагревания, за исключением случая уменьшения водородной хрупкости для высокопрочных сталей |
Идеально для малых изделий, включая шайбы и пружины (примерно до 15 см или 250 г). Трудности при нанесении, например, внутри полых изделий |
Нет ограничений на размер или форму, очень экономичен для изделий с высоким отношением массы к поверхности. Неэкономичен при окрашивании сетчатых изделий. Наличие дополнительных трудностей (например, внутри труб) могут ограничить применение. Наилучший метод для нанесения очень толстых покрытий. Малое нагревание стали |
Пригоден для всего, что может быть окрашено, хотя могут быть трудности при окрашивании трубчатых структур. Не требуется никакого нагревания |
ecm-zink.ru