Дорнирование отверстий – назначение, виды и технологические схемы
alexxlab | 05.04.2020 | 0 | Вопросы и ответы
назначение, виды и технологические схемы
Дорнование, которое часто называют дорнированием, позволяет создать на поверхности металлического изделия защитный слой, способный эффективно противостоять воспринимаемым нагрузкам.
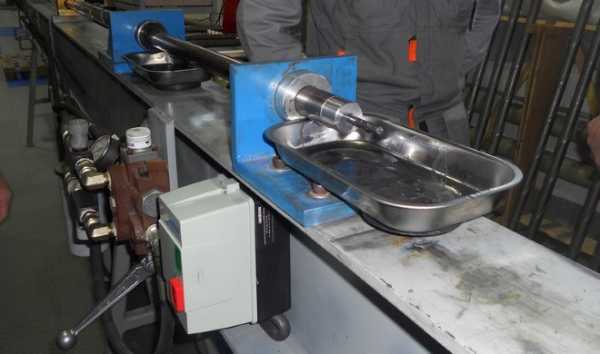
Дорнирование оружейного ствола
Назначение и технологические особенности
В процессе эксплуатации любого изделия, в том числе и изготовленного из металла, основную нагрузку воспринимает его наружная поверхность, в то время как внутренние слои остаются практически нетронутыми. В качестве такой нагрузки, в частности, может выступать термическое воздействие, а также внешние факторы, приводящие к коррозии или интенсивному износу металла.
Основная задача, которую решает дорнование, являющееся методом обработки металлического изделия, заключается в том, чтобы обеспечить его надежную защиту от вышеуказанных негативных факторов. Дорнование – это инновационная технология, суть которой заключается в том, что внутреннюю поверхность отверстий, выполненных в металлических деталях, подвергают пластической деформации в холодном состоянии, за счет чего на них и формируется слой, отличающийся исключительными механическими характеристиками.
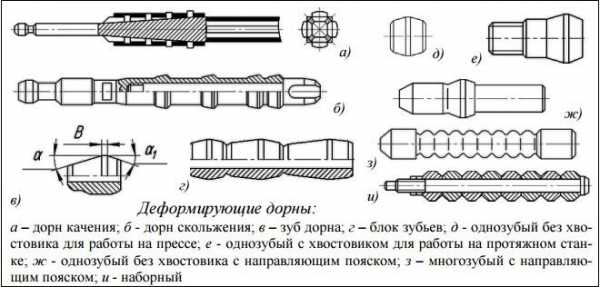
Дорн – инструмент для дорнования. Различают дорны качения и дорны скольжения
Дорнование, выполняемое при помощи специального инструмента, который передвигается по внутренней поверхности отверстия с определенной степенью натяга, позволяет решить следующие задачи:
- приведение размеров внутреннего сечения обрабатываемого изделия в соответствие с требуемыми значениями;
- устранение шероховатостей, имеющихся на внутренней поверхности обрабатываемого отверстия;
- улучшение прочностных характеристик металла, формирующего внутреннюю поверхность отверстия.
Если вы планируете выполнить дорнование, следует иметь в виду, что диаметр обрабатываемого отверстия должен быть всегда меньше поперечного сечения используемого инструмента на величину натяга.
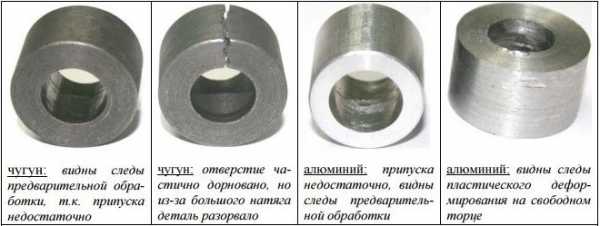
Примеры деталей после дорнования
Объемное и поверхностное дорнование
Существует два вида дорнирования стволов и труб, при котором не образуется стружка, – объемное или поверхностное. При выполнении объемного дорнования обработка осуществляется по всему поперечному сечению заготовки. В результате такой технологической операции, выполняемой при помощи инструмента, оснащенного несколькими зубьями, можно сформировать поверхность, шероховатость которой будет находиться в интервале 0,04–0,63 мкм, а точность – соответствовать 11 единицам по шкале IT.
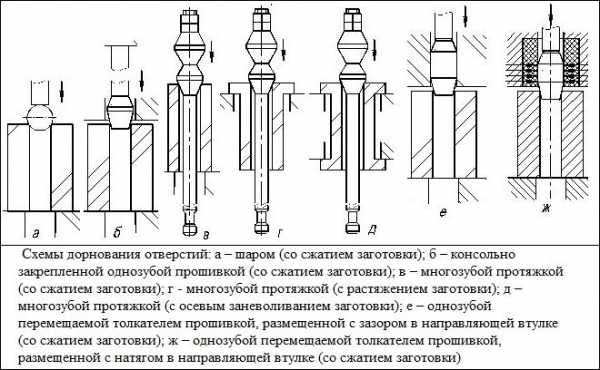
Схема объемного дорнования отверстий малого диаметра
При помощи объемного дорнования обрабатываются отверстия большой длины, трубные заготовки или изделия, выполненные в виде гильз. Такая операция, которой можно подвергать отверстия практически любой длины, сохраняя их прямолинейность, является хорошей альтернативой черновому растачиванию.
Схема обработки детали поверхностным дорнованием
При выполнении поверхностного дорнования можно получить внутреннюю поверхность, шероховатость которой будет находиться в пределах 0,04–0,32 мкм, а точность – соответствовать 6–9 единицам. При поверхностном дорновании отверстия на внутренней поверхности последнего создается упрочненный слой металла, поэтому эту технологию обработки с успехом можно применять в качестве альтернативы таким сложным операциям, как:
- шлифование;
- хонингование;
- развертывание;
- выглаживание.
Разновидности и технологические особенности
По технологическим особенностям выполнения дорнирование может быть свободным и несвободным. При свободном дорновании, которому преимущественно подвергаются бесшовные и электросварные трубы со стенками средней толщины, величина деформирования наружных поверхностей обрабатываемых изделий не оговаривается.
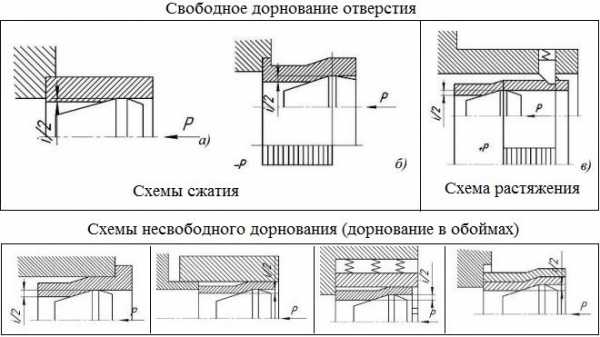
В зависимости от способа закрепления детали дорнование может быть свободным или в обоймах
Несвободному дорнованию преимущественно подвергаются внутренние отверстия в тонкостенных трубных изделиях. При выполнении такой технологической операции гарантируется отсутствие следующих последствий обработки:
- искривление оси обрабатываемой заготовки;
- снижение устойчивости заготовки в ее продольном направлении;
- наличие участков поверхности, выглаживание которых выполнено некачественно.
Чтобы обеспечить такое высокое качество обработки, при несвободном дорновании изделие закрепляют в специальных обоймах, отличающихся высокой жесткостью и упругостью. Нередко такую операцию совмещают с холодным редуцированием, в процессе которого диаметр обрабатываемого отверстия и инструмента уменьшаются под воздействием низких температур.
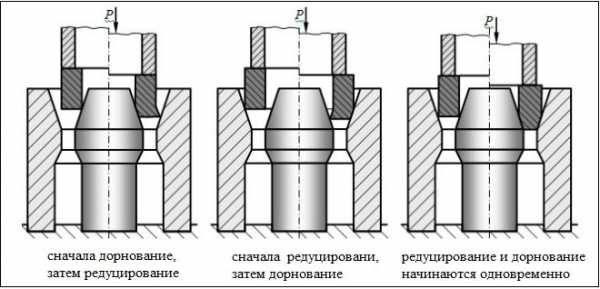
Варианты совмещенного процесса дорнования-редуцирования
Основные параметры
Специалисты руководствуются такими параметрами дорнования, как:
- обычный и относительный натяг;
- скорость выполнения;
- сила выполнения;
- относительная деформация.
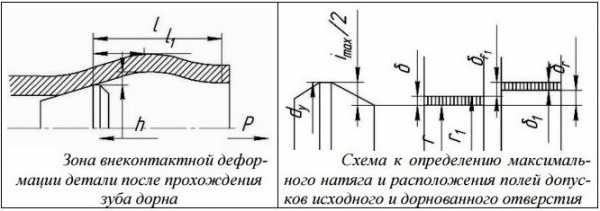
Для нормального дорнования допуск на размеры обрабатываемого отверстия должен быть в несколько раз меньше половины натяга
Натяг, который является одним из основных параметров дорнования, представляет собой разницу между диаметрами обрабатываемого отверстия и размером поперечного сечения используемого инструмента. Если данный показатель слишком велик, то в процессе обработки не получится сформировать поверхность с требуемым уровнем шероховатости. Выбирая данный параметр, следует учитывать как степень пластичности обрабатываемого изделия, так и его прочностные характеристики. Под относительным натягом дорнования понимают величину, получаемую отношением размера обработанного или необработанного отверстия к величине обычного натяга.
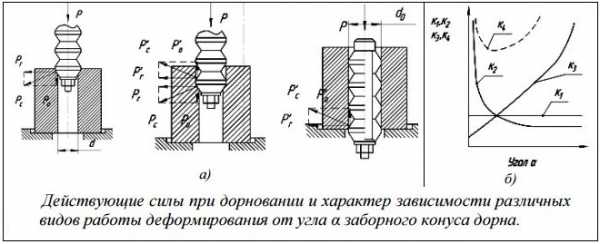
При дорновании прикладываемая к инструменту сила раскладывается на осевую и радиальную составляющие
Под силой, с которой выполняется дорнирование, подразумеваются усилия, которые инструмент оказывает на стенки отверстия в радиальном и осевом направлениях. При помощи усилия, оказываемого инструментом в радиальном направлении, увеличивается поперечное сечение обрабатываемого отверстия, а сила, создаваемая дорном в направлении оси обрабатываемой заготовки, позволяет удалить мельчайшие неровности с ее внутренней поверхности.
Относительная деформация, измеряемая в процентах, дает возможность определить, насколько изменился при дорновании наружный диаметр обрабатываемого изделия.
Технологические схемы
Дорнирование, которое при наличии соответствующего оборудования и инструмента можно выполнить и в домашних условиях, осуществляется:
- методом растяжения;
- сжатием;
- путем комбинирования двух вышеуказанных методик.
Схемы дорнования отверстий
Выбор технологической схемы для дорнования влияет на величину осевой нагрузки, которой будет подвергаться обрабатываемое изделие. Если такая нагрузка будет слишком большой, она может стать причиной возникновения в обрабатываемой детали осевых напряжений.
При использовании схемы растяжения или сжатия нагрузка, создаваемая дорном, приходится на отдельные участки обрабатываемой поверхности, а комбинированный метод позволяет распределять нагрузку равномерно.
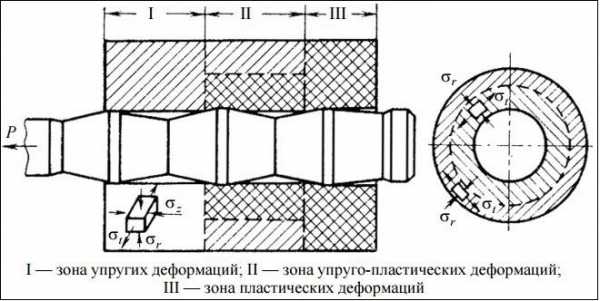
Схема деформации при обработке поверхности многозубым дорном
В последнее время объемное дорнирование все чаще выполняется по инновационным схемам, предполагающим использование пассивного, нейтрального и активного противонатяжения. Такие схемы, которые достаточно сложно реализовать в домашних условиях, предполагают применение специальных опор, выполняющих функции натяжных подвижных механизмов.
Чтобы в результате дорнования получить отверстие с меньшей шероховатостью стенок, необходимо выполнять такую технологическую операцию с более высоким натягом или провести предварительную механическую обработку отверстия.
Оценка статьи:
Загрузка…met-all.org
Дорнование – что представляет собой и как выполняется? + Видео
Способ обработки металлических изделий без удаления стружки – это дорнование, его также достаточно часто называют дорнированием.
1 Что представляет собой дорнование?
Во время эксплуатации поверхности металлических деталей испытывают серьезные нагрузки, которые практически не воспринимаются внутренними слоями изделий. Именно слои, находящиеся сверху, противодействуют разнообразным негативным влияниям, начиная от теплового воздействия и коррозии, и заканчивая изнашиванием деталей.
Дорнование, как процесс эффективной обработки поверхностей, как раз и был создан для того, чтобы нивелировать все указанные проявления, увеличивая тем самым уровень износостойкости и надежности изделий из металла.
Рекомендуем ознакомиться
Дорнирование представляет собой инновационный вариант обработки отверстий деталей методом локального холодного деформирования, выполняемого по пластической технологии. Его суть следующая: дорн (специальное рабочее приспособление) передвигается внутри ствола изделия и за счет натяга обеспечивает:- модификацию геометрических параметров и форм детали в целом и ее поперечного сечения в частности;
- качественное нивелирование имеющихся шероховатостей;
- упрочнение поверхностного слоя металла.
Величина поперечного диаметра отверстия обрабатываемой детали всегда меньше показателя сечения дорна на показатель натяга.
2 Дорнирование ствола – объемное и поверхностное
Процесс обработки отверстий без удаления стружки в настоящее время может выполняться объемно либо поверхностно. В первом случае процедура ведется по всему сечению (поперечному) заготовки. Она позволяет получать за один проход рабочего инструмента, оснащенного несколькими зубьями, величину шероховатости от 0,04 до 0,63 микрометров при точности отверстий на уровне 11 единиц по шкале IT.
Объемное дорнование рекомендовано для обработки длинных цилиндров, трубных изделий, изготовленных в виде гильз. Оно с успехом заменяет собой менее эффективную операцию чернового растачивания таких деталей. Объемное деформирование дает возможность работать с любыми по длине трубами, обеспечивая необходимый показатель их прямолинейности.
Дорнование поверхностного типа гарантирует получение шероховатости в пределах 0,04–0,32 микрометра при точности не менее 6 и не более 9 квалитетов. При таком способе деформирования на поверхности создается прочный слой, поэтому эта методика может заменить ряд сложных процедур, в частности:
3 Описание разновидностей дорнования
Существует несвободный и свободный вид выполнения описываемой операции. При свободном дорнировании внешние поверхности изделий не имеют каких-либо ограничений на деформирование. По этой причине оно обычно используется для выполнения объемных работ с бесшовными и электросварными трубами, которые характеризуются средними величинами толщины стенки.
Несвободное дорнирование больше подходит для тонкостенных труб, так как оно гарантирует отсутствие после обработки таких явлений:
- искривление заготовки по оси;
- снижение устойчивости в продольном направлении;
- некачественное выглаживание металла.
Как правило, данный вид пластичного деформирования производится в упругих и жестких обоймах. Также достаточно часто несвободное дорнование выполняется в комбинации с холодным редуцированием деталей (процесс сужения сечения отверстий и прутков).
4 Главные показатели процедуры пластичного деформирования заготовок
К основным параметрам этой обработки относят такие величины:
- относительный натяг;
- натяг;
- скорость;
- сила;
- относительная деформация.
Под натягом, как было сказано выше, понимают разницу между номинальными сечениями отверстия и дорна. Чересчур высокий натяг может стать причиной снижения конечного показателя шероховатости, что, конечно же, нежелательно. Поэтому к выбору величины натяга относятся максимально ответственно, принимая во внимание характеристики пластичности и начальной прочности деталей.
Относительный же натяг является параметром без размерности. Под ним подразумевают отношение величины обработанного либо начального отверстия к показателю натяга дорнирования.
Сила процесса обработки отверстий подразделяется на два компонента:
- радиальный;
- осевой.
Первая требуется для повышения сечения заготовки, которая подвергается деформированию. Данный компонент обеспечивает объемную обработку. А вот осевая сила удаляет мельчайшие неровности. Она нужна для работы трения.
Относительной деформацией называют такой показатель, который определяет реальную деформацию детали по ее наружному сечению. Выражается данный параметр в процентах.
Последний показатель процесса – сила дорнования. Существенного воздействия на величину износа рабочего инструмента и качество выполнения операции он не имеет.
5 Основные схемы выполнения пластичного деформирования отверстий
Дорнирование выполняется по следующим схемам:
- растяжение;
- сжатие;
- комбинирование первых двух методик.
Подбор правильной схемы обработки очень важен, так как она устанавливает параметры осевого нагружения изделий, которое является причиной возникновения осевых напряжений.
При применении схемы растяжения либо сжатия на деталь воздействуют напряжения на каком-либо конкретном участке. А вот смешанная схема подразумевает, что нагрузку воспринимает вся длина заготовки.
Объемное дорнование в последнее время все чаще осуществляется по новым схемам – с пассивным, нейтральным и активным видом противонатяжения. Для выполнения процедуры с их использованием требуются специальные опоры – натяжные подвижные механизмы, которые ограничивают укорачивание деталей при их обработке дорном.
Добавим, что описанная методика обеспечивает тем меньший показатель шероховатости, чем более высокий натяг используется. Кроме того, оптимальные величины шероховатости отверстий после деформирования отмечаются тогда, когда заготовки подвергаются перед выполнением операции механической обработке.
tutmet.ru
что это такое, обработка стволов и труб
Работа механических узлов машин сопровождается серьезной нагрузкой на поверхность деталей, особенно это касается различных отверстий. Верхний контактный слой металла берет на себя львиную долю механических воздействий и усилий, предотвращая разрушающее влияние на внутренние слои. Чем прочнее будет этот внешний слой, тем общая износостойкость изделия будет выше. Чтобы искусственно укрепить поверхность отверстий, применяют такой технологический прием, как дорнирование отверстий.
В машиностроении дорнование – это применение процесса укрепления поверхности отверстия методом калибрования или протягивания деформирующего. Кроме этого, дорнирование позволяет получить формообразующую либо чистовую обработку ствола отверстий. Слой, который укрепляется, может быть разной толщины, это зависит от величины натяжения.
Назначение и сферы применения дорнирования
Как вкратце говорилось выше, дорнирование необходимо, чтобы укрепить поверхность стволов отверстий, придать им большую прочность, таким образом повышая износостойкость изделия. Все это осуществляется за счет возможности пластически деформировать металл на протяжении зоны контакта при помощи дорна. Дорны бывают двух типов: скольжения и качения. Чаще всего процесс протекает при холодном состоянии заготовки.
Когда инструмент дорн с определенным уровнем натяга движется по стволу, вместе с укреплением стенок решаются и другие задачи:
- подгонка диаметра отверстия под нужные параметры, стволов отверстий прямоугольного сечения до нужных размеров;
- избавление от неровностей, любых шероховатостей, которые были допущены предыдущей обработкой ствола;
- возможность сформировать определенную форму сечения, например, создать шлицы, борозды или оригинальный рисунок на внутренней поверхности.
Дорнирование применяется не только в гражданском машиностроении, но и на оружейном производстве. С его помощью укрепляют оружейные стволы танковых и других машин, используют при изготовлении гильз.
Когда планируется применить дорнирование к тому или иному отверстию, важно, чтобы дорн имел диаметр больший, чем поперечное сечение ствола отверстия на толщину натяжения. Все это очень точно рассчитывается, чтобы не было разрыва заготовки.
Технологический процесс дорнования
Особенность процесса дорнирования технически будет зависеть от выбора схемы обработки металла, которых бывает три:
- когда применяют растяжение;
- используют сжатие;
- комбинируют процесс сжатия и растяжения.
При использовании любой из двух первых схем воздействие на изделие проходит на конкретном отрезке. Дорнирование по комбинированному принципу предполагает, что нагрузка будет распределена по всей поверхности детали с внутренней стороны ствола.
Если нужно обработать ствол детали в объемном виде, технологические схемы выбирают следующие:
- нейтральное противонатяжение;
- активное;
- пассивное.
Применение этих схем связано с использованием осевого напряжения, и нужны дополнительные элементы – опоры подвижного типа, чтобы укорачивание изделия не выходило за допустимые пределы.
Использование разных типов дорнов в любом случае предполагает, что инструмент будет двигаться внутри канала ствола под воздействием специального протяжного механизма или суппорта вибрационного на гидроприводе. При этом происходит постоянная смазка канала с целью уменьшения трения о слой металла и более плавного прохода.
Разновидности
Под разновидностями дорнирования понимают свободный и несвободный процесс проведения операции. Когда дорнирование свободное, изделие, а именно его поверхность, не ограничивается в возможности деформирования. Приемлем такой вид процесса при объемных работах с трубами электросварными либо при бесшовном литье, где толщина стенки ствола определяется как усредненная величина.
Дорнирование свободное не подходит для таких заготовок, как, например, трубы с тонкими стенками ствола. Здесь применяют несвободное дорнирование, которое позволяет избежать следующих последствий:
- осевого смещения заготовки;
- понижения устойчивости вдоль направления ствола;
- выглаживания металла с недостаточным качеством.
Для реализации операции несвободного дорнирования деталь перед прохождением дорна закрепляют в специальных обоймах жесткой и упругой конструкции.
Использование любого из способов дорнирования требует применения смазочных материалов, чтобы уменьшить трение, ускорить процесс обработки, избежать порчи заготовки или инструмента.
Объемное и поверхностное дорнование
Дорнирование как способ обработки ствола отверстия, когда отсутствует процесс удаления стружки, можно выполнить поверхностным образом либо объемно. При объемном методе операция захватывает всю заготовку (имеется в виду поперечное сечение). Совершая один проход инструментом, рабочая часть которого оснащена несколькими зубьями, добиваются фактической шероховатости в пределах 0.63–0.04 микрон с большой точностью отверстия.
Объемное дорнирование ввиду своей эффективности призвано заменять менее эффективный метод, когда заготовки подвергают растачиванию черновому. Применяют объемную деформацию для обработки любых типов труб, цилиндров с длинным стволом, при этом прямолинейность изделий сохраняется в нужных границах.
Применение поверхностного дорнирования позволяет получить в канале ствола шероховатость в пределах 0.32–0.04 микрон. Основное назначение метода – упрочнить поверхностный слой и, возможно, избежать сложных технологических приемов: развертывания, шлифования, выглаживания и хонингования металла.
Пластическое деформирование и калибровка
Суть пластического деформирования заключается в том, что дорн с диаметром рабочей части больше, чем ствол отверстия, вдавливается в последний под воздействием силы станка. Калибровка же внутренней поверхности труб протекает при воздействии на обрабатываемый участок источника тепловой энергии для разогрева и последующего внедрения в область инструмента дорна. Недостаток калибровки – в возможном изменении параметров заготовки и в большей сложности процесса относительно пластической деформации.
Метод ударных импульсов
Способ, при котором подача инструмента дорна по каналу отверстия ствола проходит не в постоянном поступательном режиме, а толчками с одинаковой частотой, называется методом ударных импульсов. Такой процесс очень эффективен, так как снижает нагрузку на инструмент, на канал и позволяет достичь максимальной точности обработки.
Специалисты-практики в области обработки металла и все, кто имеет непосредственный опыт проведения процесса дорнирования отверстий, поддержите тему в комментариях. Для начинающих умельцев ваши знания имеют неоценимое значение!
wikimetall.ru
назначение, виды и технологические схемы
Дорнование, которое часто называют дорнированием, позволяет создать на поверхности металлического изделия защитный слой, способный эффективно противостоять воспринимаемым нагрузкам.
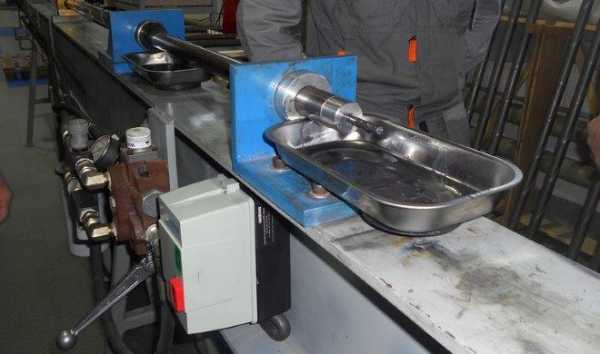
Дорнирование оружейного ствола
Назначение и технологические особенности
В процессе эксплуатации любого изделия, в том числе и изготовленного из металла, основную нагрузку воспринимает его наружная поверхность, в то время как внутренние слои остаются практически нетронутыми. В качестве такой нагрузки, в частности, может выступать термическое воздействие, а также внешние факторы, приводящие к коррозии или интенсивному износу металла.
Основная задача, которую решает дорнование, являющееся методом обработки металлического изделия, заключается в том, чтобы обеспечить его надежную защиту от вышеуказанных негативных факторов. Дорнование – это инновационная технология, суть которой заключается в том, что внутреннюю поверхность отверстий, выполненных в металлических деталях, подвергают пластической деформации в холодном состоянии, за счет чего на них и формируется слой, отличающийся исключительными механическими характеристиками.
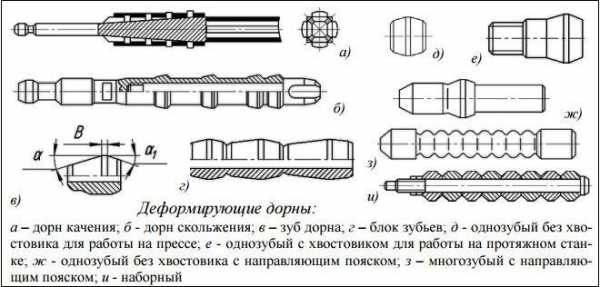
Дорн – инструмент для дорнования. Различают дорны качения и дорны скольжения
Дорнование, выполняемое при помощи специального инструмента, который передвигается по внутренней поверхности отверстия с определенной степенью натяга, позволяет решить следующие задачи:
- приведение размеров внутреннего сечения обрабатываемого изделия в соответствие с требуемыми значениями;
- устранение шероховатостей, имеющихся на внутренней поверхности обрабатываемого отверстия;
- улучшение прочностных характеристик металла, формирующего внутреннюю поверхность отверстия.
Если вы планируете выполнить дорнование, следует иметь в виду, что диаметр обрабатываемого отверстия должен быть всегда меньше поперечного сечения используемого инструмента на величину натяга.
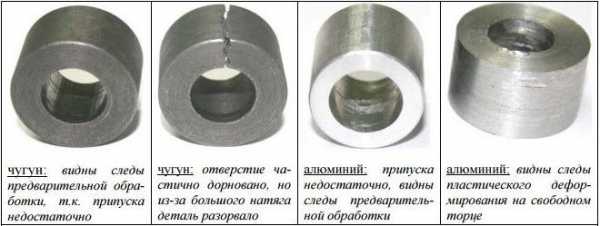
Примеры деталей после дорнования
Объемное и поверхностное дорнование
Существует два вида дорнирования стволов и труб, при котором не образуется стружка, – объемное или поверхностное. При выполнении объемного дорнования обработка осуществляется по всему поперечному сечению заготовки. В результате такой технологической операции, выполняемой при помощи инструмента, оснащенного несколькими зубьями, можно сформировать поверхность, шероховатость которой будет находиться в интервале 0,04–0,63 мкм, а точность – соответствовать 11 единицам по шкале IT.
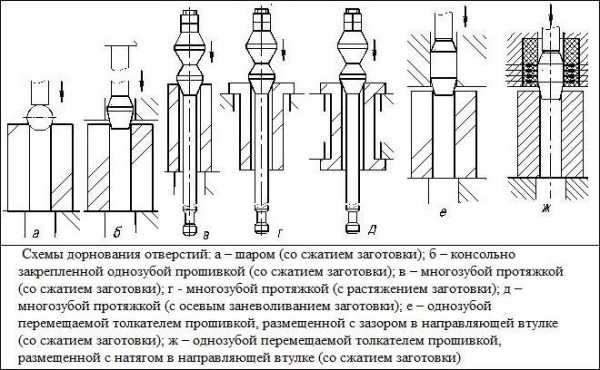
Схема объемного дорнования отверстий малого диаметра
При помощи объемного дорнования обрабатываются отверстия большой длины, трубные заготовки или изделия, выполненные в виде гильз. Такая операция, которой можно подвергать отверстия практически любой длины, сохраняя их прямолинейность, является хорошей альтернативой черновому растачиванию.
Схема обработки детали поверхностным дорнованием
При выполнении поверхностного дорнования можно получить внутреннюю поверхность, шероховатость которой будет находиться в пределах 0,04–0,32 мкм, а точность – соответствовать 6–9 единицам. При поверхностном дорновании отверстия на внутренней поверхности последнего создается упрочненный слой металла, поэтому эту технологию обработки с успехом можно применять в качестве альтернативы таким сложным операциям, как:
- шлифование;
- хонингование;
- развертывание;
- выглаживание.
Разновидности и технологические особенности
По технологическим особенностям выполнения дорнирование может быть свободным и несвободным. При свободном дорновании, которому преимущественно подвергаются бесшовные и электросварные трубы со стенками средней толщины, величина деформирования наружных поверхностей обрабатываемых изделий не оговаривается.
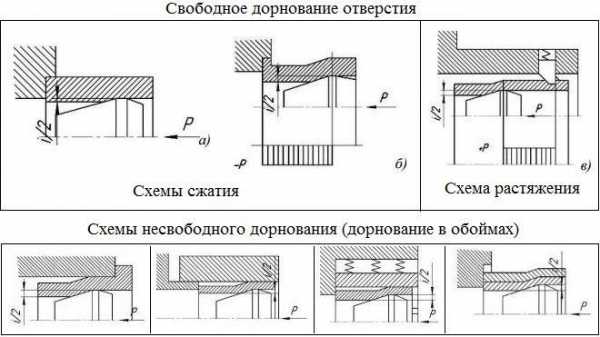
В зависимости от способа закрепления детали дорнование может быть свободным или в обоймах
Несвободному дорнованию преимущественно подвергаются внутренние отверстия в тонкостенных трубных изделиях. При выполнении такой технологической операции гарантируется отсутствие следующих последствий обработки:
- искривление оси обрабатываемой заготовки;
- снижение устойчивости заготовки в ее продольном направлении;
- наличие участков поверхности, выглаживание которых выполнено некачественно.
Чтобы обеспечить такое высокое качество обработки, при несвободном дорновании изделие закрепляют в специальных обоймах, отличающихся высокой жесткостью и упругостью. Нередко такую операцию совмещают с холодным редуцированием, в процессе которого диаметр обрабатываемого отверстия и инструмента уменьшаются под воздействием низких температур.
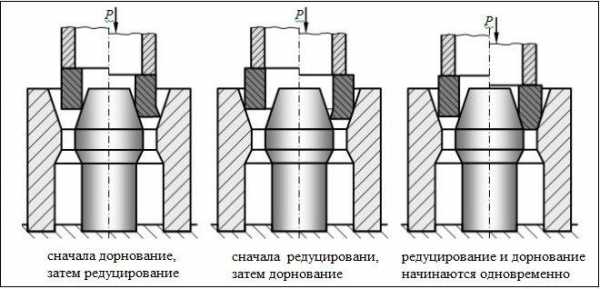
Варианты совмещенного процесса дорнования-редуцирования
Основные параметры
Специалисты руководствуются такими параметрами дорнования, как:
- обычный и относительный натяг;
- скорость выполнения;
- сила выполнения;
- относительная деформация.

Для нормального дорнования допуск на размеры обрабатываемого отверстия должен быть в несколько раз меньше половины натяга
Натяг, который является одним из основных параметров дорнования, представляет собой разницу между диаметрами обрабатываемого отверстия и размером поперечного сечения используемого инструмента. Если данный показатель слишком велик, то в процессе обработки не получится сформировать поверхность с требуемым уровнем шероховатости. Выбирая данный параметр, следует учитывать как степень пластичности обрабатываемого изделия, так и его прочностные характеристики. Под относительным натягом дорнования понимают величину, получаемую отношением размера обработанного или необработанного отверстия к величине обычного натяга.
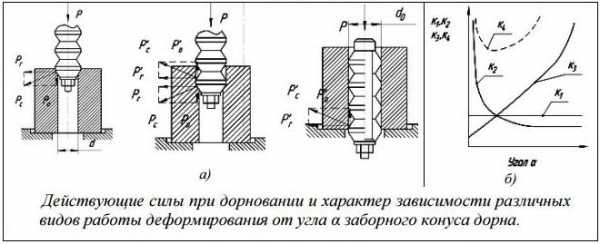
При дорновании прикладываемая к инструменту сила раскладывается на осевую и радиальную составляющие
Под силой, с которой выполняется дорнирование, подразумеваются усилия, которые инструмент оказывает на стенки отверстия в радиальном и осевом направлениях. При помощи усилия, оказываемого инструментом в радиальном направлении, увеличивается поперечное сечение обрабатываемого отверстия, а сила, создаваемая дорном в направлении оси обрабатываемой заготовки, позволяет удалить мельчайшие неровности с ее внутренней поверхности.
Относительная деформация, измеряемая в процентах, дает возможность определить, насколько изменился при дорновании наружный диаметр обрабатываемого изделия.
Технологические схемы
Дорнирование, которое при наличии соответствующего оборудования и инструмента можно выполнить и в домашних условиях, осуществляется:
- методом растяжения;
- сжатием;
- путем комбинирования двух вышеуказанных методик.
Схемы дорнования отверстий
Выбор технологической схемы для дорнования влияет на величину осевой нагрузки, которой будет подвергаться обрабатываемое изделие. Если такая нагрузка будет слишком большой, она может стать причиной возникновения в обрабатываемой детали осевых напряжений.
При использовании схемы растяжения или сжатия нагрузка, создаваемая дорном, приходится на отдельные участки обрабатываемой поверхности, а комбинированный метод позволяет распределять нагрузку равномерно.
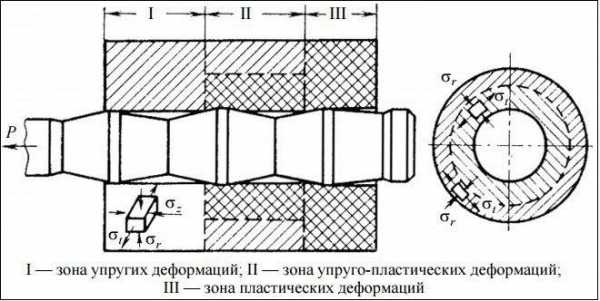
Схема деформации при обработке поверхности многозубым дорном
В последнее время объемное дорнирование все чаще выполняется по инновационным схемам, предполагающим использование пассивного, нейтрального и активного противонатяжения. Такие схемы, которые достаточно сложно реализовать в домашних условиях, предполагают применение специальных опор, выполняющих функции натяжных подвижных механизмов.
Чтобы в результате дорнования получить отверстие с меньшей шероховатостью стенок, необходимо выполнять такую технологическую операцию с более высоким натягом или провести предварительную механическую обработку отверстия.
Оценка статьи:
Загрузка…Поделиться с друзьями:
moy-metall.ru
4 Ствол. Развитие технологии получения нарезов. Дорнирование
4
Ствол. Развитие технологии получения нарезов. Дорнирование
Ствол является основной деталью оружия, определяющей его боевые качества, его стабильную меткость стрельбы, высокую поражаемость целей и эффективное действие пуль.
Эти качества ствола обеспечиваются обоснованно выбранным рациональным геометрическим профилем нарезов канала и высокой точностью его исполнения в производстве технологическими средствами.
Многолетний опыт производства нарезного стрелкового оружия показывает, что с уменьшением его калибра технологические трудности по изготовлению канальной части ствола независимо от способа получения нарезов возрастают. Не менее сложным были поиски рациональных способов получения нарезов. Эта тенденция пронизывает все ствольные технологии, смена которых происходит в соответствии с требованиями экономики и общего технического прогресса оружейного производства.
В начале 40-х годов на Ижевском заводе для стволов катибра 7,62 мм наиболее приемлемым с технологической и экономической точки зрения был признан высокопроизводительный способ получения нарезов методом дорнирования. В отличие от весьма продолжительной строжки с помощью специального режущего инструмента, именуемого шпалером, образование нарезов по этому методу происходит за счет пластической деформации металла в процессе проталкивания через гладкий канал термически обработанной заготовки конического пуансона (дорна) со спиральными выступами на поверхности. Для ствола калибра 7,62 мм длина инструмента около 30 мм.
Наружный профиль этого инструмента по своей форме (в поперечном разрезе) представляет собой изображение профиля канала ствола.
После окончания процесса дорнирования внутренние, наиболее деформированные слои металла удерживают наружные в растянутом состоянии и в то же время сами сжимаются ими. Появление этой технологии в ствольном производстве также связано с Ижевским заводом.
В середине 30-х годов исследователи технологической лаборатории В.Н. Новиков, А.Я. Фишер, С.С. Пенкин разработали технологию дорнирования, чертежи дорнов, станок и приспособления для проталкивания инструмента в «напор». В 1936 году изготовлена первая опытная партия дорнированных заготовок стволов пулемета «ДП» для Ковровского завода им. Киркиж (арх. 272-47).
Дальнейшее развитие в пулеметном производстве Ковровского завода эта технология получила с участием М. С. Лазарева.
Освоение технологии дорнирования на Ижевском заводе было начато в предвоенные годы на винтовочных стволах. На ствольном производстве завода за год до начала Великой Отечественной войны был организован специальный участок по освоению новой технологии, который возглавлял в то время исследователь лаборатории резания металлов Б. Ф. Файзулин.
А с началом войны усилиями этой же бригады ствольщиков осуществлен массовый переход на нарезание винтовочных стволов методом дорнирования вместо малопроизводительной строжки шпалером.
Новая технология оказалась несравненно производительнее. Затраты машинного времени снизились более чем в 40 раз (вместо 50 примерно 1 минута). Если при строжке шпалером в течение одной рабочей смены со станка снималось 6–7 стволов, то при дорнировании — 240–250 стволов за это же время. При этом обеспечивалось вполне приемлемое качество каналов стволов по состоянию поверхности и соблюдению точности получаемых канальных размеров.
Обеспечивались также приемлемые меткость стрельбы и живучесть стволов. Все это имело особо важное значение для организации выпуска винтовок образца 1891/30 годов в больших количествах.
Новая механическая технология нарезания каналов стволов в условиях военного времени оказалась просто находкой для оружейного производства. И не только для Ижевского завода.
«Что бы мы делали в войну, когда Ижевскому заводу поставили задачу выпускать двенадцать тысяч винтовок в сутки, сколько бы тогда станков потребовалось?» — отмечает в своей книге («Накануне и в дни испытаний») инициатор и один из авторов разработки технологии дорнирования, исследователь лаборатории резания металлов, главный инженер, директор завода, а в годы войны и зам. Наркома вооружения — Владимир Николаевич Новиков.
С этого времени дорнирование стало основной технологией для стволов калибра 7,62 мм на ижевском оружейном производстве. Получение нарезного профиля канала ствола методом дорнирования гладкого отверстия в годы войны получило широкое распространение и на других оружейных заводах, как самая производительная и наиболее экономичная технология по сравнению с другими, известными в то время способами получения нарезов. В том числе и методом протягивания через гладкое канальное отверстие специальной режущей протяжки.
Однако метод дорнирования имел свои предельные технологические возможности. С увеличением диаметра канала и веса заготовки значительно усложнялись все вспомогательные операции, сопровождающие дорнирование, с резким возрастанием усилия проталкивания инструмента.
По опыту того же завода им. Киркиж стволы калибра 30 мм в середине 50-х годов изготовлять дорнированием было невозможно (арх. 454-55).
Требовалась разработка специального прессового оборудования большой мощности. Наряду с этим с увеличением калибра ствола расширялись возможности применения специальных нарезательных инструментальных головок повышенной производительности (типа Уайт, Рейнметал, Борзинг и др.), но этот завод пошел по пути освоения электрогидравлического метода получения нарезов, возможность применения которого тогда изучалась и на Ижевском заводе.
По экономической эффективности с дорнированием как технологическим методом получения нарезов в 40-х годах могла соревноваться только режущая протяжка.
Возникнув на рубеже XIX и XX веков, протяжные станки примерно с 1905 года стали известны по применению при изготовлении шпоночных и шли-цевых отверстий, а затем и в других областях обработки металла резанием.
В конце 40-х годов исследовалась возможность применения протяжек для нарезания стволов калибра 12,7 мм на шестипозиционном протяжном полуавтоматическом станке «Лапойнт» (арх. 673-48) в порядке изучения перспективы автоматизации всего технологического процесса обработки ствола с созданием непрерывной технологической цепочки. Результаты исследований были положительные.
Однако метод протягивания, несмотря на высокую точность процесса и хорошее качество канальной поверхности, не получил распространения в отечественном оружейном производстве ввиду сложности и дороговизны инструмента (протяжек), а в применении к стволам калибра 7,62 мм и в связи с другими технологическими трудностями, обусловленными малым диаметром обрабатываемого отверстия (арх. 271-46).
Технология нарезания стволов методом дорнирования, ставшая уже традиционной для нормального калибра, оказалась наиболее приемлемой и для системы АК, вступившей в сферу массового производства в конце 40-х годов. Она сохранилась и при переходе АК-47 в начале 60-х годов в новую модификацию — АКМ.
Эта технология по своей относительной простоте и высокой производительности долгое время вполне устраивала оружейное производство. До тех пор пока не назрела постановка вопроса о максимальном повышении уровня его автоматизации. На заводах, применявших эту технологию, проводились исследования по улучшению чистоты канальной поверхности стволов и устранению причин образования дефектов, свойственных процессу дорнирования: «серость», «сыпь», «волнистость», «переломы полей и нарезов», «пересечки» и т. п. (арх. 2356-53, стр. 165).
Обычно после дорнирования канал ствола не нуждается в полировке поверхности, так как получаемая при этом его чистота достаточно высокая. Но операция его полирования свинцовыми шустами с использованием наждачной пыли определенной зернистости применялась не для улучшения чистоты, а для выравнивания диаметральных размеров канала после наружной обточки ствола, порождая одновременно такие дефекты, как «сыпь» и «непросвинцовка».
Чистота поверхности ухудшалась также наличием следов обработки канала гладкой строжкой шпалером перед операцией дорнирования. Образовывались местные надрывы металла на канальной поверхности. Наличием указанных и других свойственных технологий дорнирования недостатков создавались трудности по дальнейшему развитию оружейного производства в направлении автоматизации технологических процессов. Необходимость создания новой, более совершенной ствольной технологии ощущалась уже в 50-х годах.
Электрогидравлическая обработка каналов стволов (ЭГО и ЭГН)
Автоматизация ствольного производства требовала снижения веса заготовки и сокращения операций по механической обработке детали с исключением свойственных дорнированию напряжений в металле, и что не менее важно, исключения необходимости многочисленных исправлений кривизны ствола ручными правками, обусловленной, в первую очередь, деформацией металла заготовки в процессе проталкивания дорна. В этом отношении преимущество перед дорнированием имел новый метод получения нарезов, разработанный в технологическом институте Ф.А. Куприянова (арх. 296-51). Инженеры-технологи этого института Н.Н. Гусев и В.Н. Гусев в 1948 году предложили оружейному производству способ получения нарезов в стволах путем электрогидравлической обработки металла (ЭГО).
Вместо обычных приемов обработки металла резанием или деформации продавливанием пуансона (дорна), предложен процесс направленного анодного растворения металла при высоких скоростях протока электролита с образованием профиля нарезов в канальном отверстии ствола.
Этот способ позволял также производить обработку гладкого отверстия ствола с равномерным съемом металла по всей поверхности в порядке подготовки отверстия к электрогидравлическому нарезанию (ЭГН) или дорнированию. Наименование электрогидравлического он получил ввиду существенного значения в этом процессе скорости протока электролита.
Первыми исследованиями ЭГН на Ижевском заводе (арх. 251-51; 1077-53), проведенными в 50-х годах И.А. Самойловым, выявлена технологическая сложность практического внедрения этого процесса в массовое производство стволов системы АК. Трудности возникли в обеспечении необходимой точности канальных размеров и качества обрабатываемой поверхности.
Сложным в изготовлении был инструмент-катод с высокими требованиями по точности размеров и чистоте поверхности, от которой зависела и чистота обрабатываемого отверстия.
Наибольшие трудности возникли при попытках применения подвижного катода, являвшегося по сравнению с неподвижным более удобным инструментом при разработке автоматизированной технологии, в связи с особой сложностью инструмента, оборудования и технологии в целом. Малый диаметр обрабатываемого отверстия создавал трудности в обеспечении надежного центрирования катода, обеспечении стабильной скорости протока электролита, а также постоянства электропроводности электролита и плотности тока.
Трудным было получение одинаковой глубины нарезов по длине ствола, в связи с чем потребовалась разработка стабилизатора тока для обеспечения стабильной его плотности (арх. 2623-57, стр. 7).
Отработка технологии электрогидравлического нарезания стволов среднего калибра с изучением специфических ее особенностей, оказывающих влияние на качество обработки канальной поверхности, потребовала значительною времени, которое захватило и 60-е годы. Большой объем исследований в этом направлении был проведен технологической лабораторией Ижевского завода, возглавляемой Н.Г. Виноградовым, а затем Н.М. Дмитриевым.
Много хлопот доставила исследователям «рябь» под кромками полей — цепочка бугорков и углублений в металле, производящая зрительное впечатление местной рябизны поверхности. Длительное изучение и экспериментальное воспроизведение этого дефекта показали, что причина его образования связана с наличием шероховатостей, зарезов и местных мелких повреждений на изоляционных планках катода, что приводило к возникновению стационарных местных завихрений электролита и нарушению равномерности стравливания металла (арх. 1077-53). Устранение причин этого дефекта стало сложным проблемным вопросом.
Не свойственно было прежним технологиям и столь большое скругление профиля нарезов, как при ЭГН. При механическом способе обработки нарезы имеют форму с более острыми углами перехода, чем при ЭГН, где радиус скругления углов полей и места перехода от боковой грани поля ко дну нареза находился в пределах 0,3–0,5 мм (арх. 1131-58).
Первоначально эта особенность расценивалась как дефект, характеризующий отступление от требований чертежа. В дальнейшем этот «дефект» стал рассматриваться как положительное качество, способствующее лучшему наложению и удерживанию хрома, а следовательно, и повышению живучести ствола. Баллистические качества стволов со скруглениями профиля нарезов в пределах 0,5 мм не нарушались.
Метод ЭГН, несмотря на незаконченность технологической отработки, сохранял перспективы возможного использования вместо дорнирования и к началу 60-х годов.
Именно в расчете на ЭГН сотрудником Ижевского филиала технологического института И.Л. Заваловым в конце 50-х годов была разработана технология механической обработки ствола АК-47, полностью исключающая его правки в связи с отсутствием кривизны (арх. 2732-59, стр. 50).
Эта технология привлекла к себе большое внимание специалистов оружейного производства, так как создавала благоприятные условия для решения проблемы максимальной его автоматизации.
Исследования показали, что основное искривление стволов происходит на операции дорнирования, нарушение их прямизны при дальнейшей механической обработке является уже результатом перераспределения напряжений в металле, первоисточником которых также является операция дорнирования. Большое количество правок приводило к появлению в стволе дополнительных дефектов: («переломы полей и нарезов», «пузыри» и т. п.).
Процесс правки ствола является ручной операцией, требующей высокой квалификации рабочего и длительного профессионального обучения правщика. Только меткий глаз в сочетании с накопленным опытом и профессиональным мастерством другой раз по едва заметному теневому обозначению в канале может определить место и направление искривления ствола, а затем соразмерить силу удара, способного исправить дефект.
Такими мастерами своего дела, обладающими высоким искусством правщика, были Е.П. Старков, А.И. Якимов, В.К. Валеев.
Профессия правщика стволов была одной из престижных и дефицитных на оружейном производстве. По точности выполнения своей работы высококвалифицированный правщик стволов ценился на уровне искусных заправщиков режущих инструментов, например разверток для окончательной доводки патронников стволов до нужного размера, какими являлись Н.В. Чернышев и В.В. Ардашев. В рабочем «сейфе» Николая Васильевича Чернышева хранились калибры изготовления 1915 года для контроля размеров патронников винтовочных стволов, которые подтверждали высокую точность работы большого мастера.
В предложенном Заваловым техпроцессе, практически исключающем правки, были и свои недостатки.
Применение электрогидравлической обработки не приводило к изгибу ствола, но при этом не происходило и выравнивания канала по диаметральным размерам, как при дорнировании за счет деформации металла при проталкивании пуансона.
Искажение геометрии отверстия, полученное на предшествующих операциях механической обработки (конусность, эллипсность, винтообразность и т. п.), после операции ЭГО гладкого отверстия и нарезания канала в лучшем случае могли оставаться неизменными, являясь в дальнейшем браковочными признаками по канальным размерам в дополнение к «ряби», «волнистости» и другим свойственным этому процессу дефектам (арх. 2732-59, стр. 61).
Искажения геометрии канала ствола с местными «провалами» диаметральных размеров при оценке в сравнении с допускными эталонами и проверке специальными гладкими калибрами — пробками не обнаруживались. Они регистрировались специальными приборами технологической лаборатории, позволяющими производить замеры по всей длине нарезной части ствола через любые интервалы и в любой точке с микрометрической точностью.
Но этот лабораторный способ контроля геометрии канала ствола был пригоден только для исследовательских целей, использование его в массовом производстве стволов было весьма сложным и неприемлемым.
Выравнивание канального отверстия ствола перед электрогидравлическим нарезанием требовало чистовой механической обработки с применением гладкой строжки, развертывания или других способов, что существенно усложняло ствольный технологический процесс и полностью поглощало экономический выигрыш, даваемый бесправочной технологией, предложенной И.Л. Заваловым. Вследствие указанных причин внедрение комплексного процесса электрогидравлической обработки гладкого отверстия и получения нарезов таким же способом на уровне технологической отработанности начала 60-х годов оказалось невозможным. Ижевский завод признал целесообразным автоматизацию производства стволов системы АК проводить на базе существующего технологического процесса с применением дорнирования.
Совершенствования по технологии дорнирования
Вопрос о конечной операции по подготовке гладкого отверстия ствола к нарезанию был одним из узловых и в применении к технологии дорнирования, так как гладкая строжка шпалером не вполне устраивала оружейное производство.
Она требовала больших затрат времени, уступала другим технологиям по чистоте обработки отверстия. Из всех проверявшихся способов обработки гладкого отверстия наиболее рациональным для замены шпалерной строжки признан электрогидравлический (арх. 2395-54, стр. 42). Режущая протяжка уступала ЭГО по экономической эффективности (дорогой и малостойкий инструмент), а скоростное развертывание не гарантировало повышения чистоты обработки по сравнению с обычным развертыванием.
ЭГО по сравнению с гладкой строжкой обеспечивала лучшую, примерно на 2 класса, чистоту поверхности, а без учета дефектов, обусловленных специфическими особенностями ЭГН, обеспечивалась и лучшая чистота хромированного канала ствола. При анодном травлении металла в первую очередь снимались неровности поверхности (шероховатость, гребешки, мелкие порезки и т. н.), оставшиеся от предыдущей грубой механической обработки. Но и как скоростное развертывание ЭГО не обеспечивала полной чистоты поверхности в случае наличия глубоких кольцевых порезок металла — следов инструмента после предварительного развертывания отверстия, если их глубина превышала припуск металла на этот вид обработки. Не выведенные при чистовой обработке перед дорнированием глубокие порезки металла «высвечивались» на поверхности хромированного ствола как «пересечки полей и нарезов».
Искажения геометрии канального отверстия на предшествующих операциях механической обработки в данном случае не препятствовали внедрению электрогидравлической обработки гладкого отверстия в производство, поскольку они поглошались операцией дорнирования (арх. 2995-54, стр. 190–200).
Однако с внедрением ЭГО в производство (арх. 2448-55, стр. 10) стали обнаруживаться ранее не замечавшиеся некоторые особенности этой технологии. Основной из них была высокая чувствительность ЭГО к качеству металла по неметаллическим включениям, что выражалось в появлении нового дефекта в каналах хромированных стволов
Это «черные продольные полосы» различной интенсивности и оттенков длиною до 200 мм — новый вид брака, ранее не встречавшийся при гладкой строжке (арх. 2716-59.стр. 66). Они обозначали выступающие над поверхностью канала бугорки металла темного цвета с легкой шероховатостью неровной поверхности, вытянутые, как правило, вдоль оси ствола. Полосы более светлого цвета, имеющие блестящую поверхность, обозначали неоднородность металла по неметаллическим включениям (сере и фосфору).
Образование этого ярко выраженного дефекта связано с тем, что имеющиеся в стали неметаллические включения, шлаковины и т. п. при химической обработке металла анодному стравливанию не поддаются и остаются на поверхности канала, а при дорнировании вдавливаются в металл, создавая отличающийся от общего фона особый оттенок поверхности. Последующее хромирование поверхности канала ствола этого дефекта не скрывает.
В случае если глубина залегания неметаллического включения меньше припуска на обработку поверхности, то стравливание металла происходит под этим включением, которое после «впрессовывания» в металл пуансоном принимает более резко выраженный цветовой оттенок. «Черные полосы» как дефект отмечались на стволах независимо от процентного содержания неметаллических включений. Электрогидравлическая обработка ствола по канальному отверстию служила как бы дефектоскопом по выявлению в металле неметаллических включений.
Объективность подхода к оценке специфических особенностей электрогидравлической обработки гладкого канала (ЭГО) и нарезов ствола (ЭГН) и связанных с ними изменений по качественному состоянию канальной поверхности с учетом его влияния на служебные свойства детали требовала накопления соответствующего производственного и эксплуатационного опыта.
Но в процессе накопления этого опыта — в середине 60-х годов, когда доработка технологического процесса ЭГН для стволов калибра 7,62 мм стала обретать законченный вид, был начат технологический поиск более совершенных методов нарезания стволов, приемлемых и для стволов малого калибра, который стал уже объектом конструкторских исследований.
Необходимость этих поисков обуславливалась практической потребностью, так как нарезание стволов малого калибра с высокими требованиями по чистоте поверхности и точности канальных размеров применением существующих технологических методов значительно усложнялось. В особо резкой форме технологические трудности проявили себя при сверлении и последующей обработке глубоких отверстий малого диаметра.
Выход из положения открывал метод получения нарезов ротационной холодной ковкой (редуцированием) с применением специальных ковочных машин. В конце 60-х годов этот метод вступил в технологическое соревнование с электрохимическим способом нарезания стволов. Широкое применение редуцирования в массовом производстве стволов наступило в 70-х годах, когда малый калибр оружия стал уже практической реальностью.
Холодная ротационная ковка стволов (редуцирование)
Через каждые 4 минуты из горизонтально-ковочной машины SHK-10 с автоматизированным процессом ковки и подачи заготовок на обработку выходит ствол АКМ с готовым нарезным каналом и патронником, не требующими дополнительной механической обработки.
Не сложная по технологии обработки и заготовка, поступающая для загрузки бункера машины, длиною 311 мм, наружным диаметром 30 мм и с канальным отверстием диаметром 11,6 мм. Подготовка гладкого канала заготовки к редуцированию со сверлением первоначального отверстия диаметром 10,45 мм позволяла применять высокопроизводительные методы обработки, не создавая особых технологических трудностей.
После сверления производилась термическая обработка заготовки, 4-х разовое развертывание отверстия до размера 11,35 мм и на заключительном этапе — электрохимическая обработка до размера 11,6 мм.
Инструментом, обеспечивающим необходимый профиль канала ствола и патронника, является оправка, изготовленная из твердого сплава ВК-20, со спиральными выступами на цилиндрической поверхности и утолщением на конце с наружным профилем по форме патронника ствола. Цилиндрическая часть оправки длиною 40 мм в поперечном сечении представляет собою зеркальное изображение профиля канала ствола.
Нарезной канал и патронник при редуцировании образуются в результате обжатия металла вокруг инструмента — оправки при высокочастотной ковке ствольной заготовки двумя парами симметрично расположенных бойков. Число ударов в одну минуту — 1200. Максимальная степень обжатия металла по канальной части ствола около 40 %.
Регулируемая скорость подачи заготовки в ковочной машине SHK-10 обеспечивалась в пределах от 0 до 36 мм/сек. Осевое вращение заготовки — 40–60 об/мин. Оптимальный режим в пределах 52–56 об/мин.
Редуцированный канал ствола и патронник по своей чистоте не требовали дополнительной обработки перед хромированием. Включение на непродолжительное время «обратного тока» для очистки и некоторого разрыхления поверхности в целях повышения ее адгезионной способности при наложении хрома сливалось с операцией хромирования.
Первая партия ковочных машин SHK-10 группой специалистов Ижевского завода принималась у австрийской фирмы GFM в период с сентября по декабрь 1971 года. Зам. главного механика завода И.Ф. Зуев со своим помощником М. Мусиным, зам. главного технолога Б.Н. Андреев и ведущие специалисты этой службы В.С. Письменский, В.А. Никитин и Л.Ф. Мокрушин в течение этого времени производили не только техническую приемку машин, но и участвовали в отработке технологии ковки стволов АКМ. Одновременно производилось и уточнение чертежа на ствол с учетом технических возможностей ковочной машины, которая также в процессе сдачи заказчику дорабатывалась.
Был момент, когда фирма была не в состоянии удовлетворить требования Советской стороны в точности исполнения чертежных размеров по канальной части ствола и патроннику, считая их чрезмерно жесткими.
В разгар конфликта, когда был начат разговор о возможном расторжении контракта, В.А. Никитину — главному специалисту по канальной части ствола, пришлось возвращаться на свой завод для изучения возможностей изменения требований чертежа на ствол с учетом предложений австрийской стороны и согласования их со своим заказчиком.
Согласие заводских служб на изменение чертежа, не получившее пока еще одобрения внешних испытательных организаций, касалось изменения допусков на точность изготовления 4 и 5-го конусов патронника ствола в связи с местным непроковом в переходной части, (увеличения допуска примерно на 0,02 мм), а также скругления полей нарезов канальной части ствола.
После приемки первой партии ковочных машин SHK-10 руководители фирмы GFN отметили, что впервые встретились с такой строгой требовательностью приемщиков, вследствие чего конструкция машин будет улучшена.
Были также разговоры о том, что только в России существует строгий прямоугольный профиль нарезов оружейных стволов, что в других странах он делается более плавным.
После приемки в 1977 году второй партии ковочных машин у австрийцев на одной из них с согласия советской стороны была произведена опытная, ковка стволов калибра 4,5 мм для фирмы «Koval Arms» (Великобритания) с положительными результатами.
На Ижевском заводе австрийские ковочные машины стали осваиваться в 1972 году, первоначально на стволах калибра 7,62 мм для системы АКМ. Освоение производилось той же группой приемщиков машин у австрийцев под руководством главного инженера завода Б.Ф. Файзулина, являвшегося и главным инициатором внедрения ковочной ствольной технологии в массовое производство, его заместителя О.И. Собина и главного технолога М.И. Миллера.
Своевременное освоение нового прогрессивного метода нарезания стволов в массовой технологии имело весьма важное значение для дальнейшего технического развития оружейного производства.
Первые стволы, изготовленные по новой технологии, по боевым качествам показали вполне обнадеживающие результаты, однако в ходе освоения выявилась необходимость корректировки данного процесса и внесения некоторых дополнительных конструктивных изменений по стволу.
Для обеспечения возможности редуцирования произведено уточнение режима термообработки ствольной заготовки с учетом упразднения подкалки казенной части ствола на более высокую твердость. По длине ствола произведено выравнивание твердости. На утолщенной казенной части твердость понижена, а на остальном участке она несколько повышена. С учетом положительного опыта электрогидравлического нарезания стволов в чертеже произведено скругление внутренних и наружных углов нарезов радиусом 0,8 мм.
Процесс редуцирования в результате наружного обжатия заготовки при ковке оставляет в канале остаточные напряжения противоположной дорнированию реактивной направленности. Эта особенность редуцирования, как и при дорнировании, должна была учитываться при выполнении технологических операций по наружной механической обработке ствола.
Применение редуцирования, даже с учетом свойственной этому процессу недостаточно четкой проковки последних конусов патронника в зоне перехода к нарезной части, не сказалось на изменении прочностных, баллистических и боевых характеристик ствола, включая и большие перепады температур окружающей среды.
Но некоторые сомнения в этом все же возникали. Связанные с этим дополнительные сравнительные испытания автоматов с редуцированными и дорнированными стволами в специализированных исследовательских организациях подтвердили ранее сделанные выводы в пользу редуцирования (арх. 900-73).
Редуцирование каналов стволов с одновременным изготовлением патронника дало снижение трудоемкости изготовления этой детали по сравнению с дорнированием канала и изготовлением патронника путем обработки металла резанием примерно на 40 %. Не страдало при этом и качество изготовленных стволов, боевые свойства и эксплуатационная долговечность.
Применение редуцирования сокращало потребности в производственных площадях по ствольному участку, при этом повышалась и общая культура производства. Но не только в этом состоят преимущества данной технологии. Снижение трудоемкости изготовления ствола на 40 % не являлось высшим предельным достижением данного процесса в области технологий.
В условиях уменьшения калибра оружия, когда трудоемкость обработки канальной части ствола прежними методами резко возрастает, в не меньшей мере возрастает и преимущество редуцирования.
При определенных условиях оно может оказаться единственным методом изготовления стволов малого калибра без особых технологических сложностей.
Это показали предпринятые в конце 60-х годов поиски рациональной технологии изготовления стволов калибра 5,60 (5,45) мм. Полученный на Ижевском заводе при освоении редуцирования стволов АКМ технологический опыт, который был первым в отечественном оружейном производстве стволов среднего калибра, послужил базовой основой для проверки возможности применения этого метода и к стволам малого калибра.
Стволы калибра 5,45 мм. Первоначально этот калибр в перестволенных автоматах АКМ имел цифровое значение 5,60 мм, как диаметр канала, измеряемый по дну нарезов. В дальнейшем при перерасчете на диаметр по полям он перевоплотился в калибр 5,45 мм, каким он стал известен по автомату АК-74.
Многие оружейники и патронщики считали, что калибр 5,6 мм целесообразно было бы оставить без изменений, только считать его диаметром канала ствола не по нарезам, а по полям, как во всем оружии. Это создавало бы лучшие возможности для разработки пуль специального назначения.
Широкими технологическими исследованиями, проведенными на Ижевском заводе (И.А. Самойловым и В.А. Никитиным) в конце 60-х годов с участием организаций В.М. Сабельникова и В.И. Лазарева (инв. 5044-70), установлено, что из всех известных способов получения нарезов (строжка шпалером, дорнирование, редуцирование и ЭГН) лучшими и примерно равноценными между собой являются редуцирование и электрохимическое нарезание (ЭХН, ранее именовавшееся ЭГН). Поиски лучшей технологии и опыт изготовления первых партий стволов калибра 5,45 мм, предназначенных для новых автоматов различных конструкций, обнаружил резко возросшие по сравнению с калибром 7,62 мм технологические трудности выполнения операций по механической обработке глубокого канального отверстия.
Более трудоемкой с увеличением затрат времени стала операция правки стволов вследствие ухудшения видимости теневого треугольника в узком канале, обозначающего нарушение прямизны детали. В связи с уменьшением диаметра обрабатываемого отверстия соответственно снизились и прочностные качества канального инструмента (сверл, разверток, шпалеров, шустов), его жесткость и эксплуатационная долговечность. Наиболее резкие проявления и связанные с этим технологические трудности имели место при сверлении первоначального отверстия диаметром 4,8 мм, где стойкость инструмента в связи с увеличением продольных и крутильных колебаний была особенно низкой.
Снижало это и рабочую подачу инструмента. Увеличилась опасность поломки сверл из-за закупорки отверстий стружкой, что требовало повышенного внимания при наблюдении за процессом сверления. Это исключало возможность многостаночного обслуживания. Частая смена инструмента, ухудшенные условия отвода стружки не только снижали производительность технологических операций, но и косвенно влияли на качество обработки отверстий.
Поломки инструмента были свойственны и технологии сверления глубоких отверстий диаметром 6,45 мм под операцию дорнирования стволов калибра 7,62 мм, где по технологии предусматривалась специальная операция по удалению поломавшихся сверл примерно у 5 % ствольных заготовок.
Но при диаметре отверстия 4,8 мм поломки сверл существенно участились с одновременным увеличением и затрат времени на извлечение обломков инструмента из ствола.
Гладкая строжка, применявшаяся для улучшения чистоты канала и выравнивания его геометрических размеров, отличалась крайне низкой производительностью для стволов любых калибров, а калибра 5,45 мм в особенности.
Сверление отверстия диаметром 9,1 мм с последующей обработкой гладкого канала до размера 10,2 мм под редуцирование было куда проще.
Трудоемкость канальных операций по стволам калибра 5,45 мм применительно к процессу редуцирования по сравнению с технологией дорнирования стволов АКМ калибра 7,62 мм была меньше примерно на 60 %.
Метод одновременного редуцирования канала ствола и патронника был признан наиболее приемлемым для массового производства стволов. Он обеспечивал достаточно высокую точность получаемых размеров, исключая некоторые погрешности по 4 и 5-му конусам патронника, не оказывающие влияния на эксплуатационные качества оружия.
Качественное состояние канального отверстия не уступало ЭХН. Снижение трудозатрат по сравнению с методом ЭХН обеспечивалось более чем в 1,5 раза.
Положительный опыт освоения редуцирования в ствольном производстве был использован Б.Ф. Файзулиным и В.С. Письменским при переводе на процесс редуцирования изготовление корпуса дульного тормоза автомата АК-74 из сортового трубчатого проката. Это снизило общие затраты массового производства на изготовление дульного тормоза примерно на 50 %.
Истории поисков рациональной технологии изготовления автоматных стволов начала 50-х годов известна также попытка применения прессованных заготовок с наличием гладкого канального отверстия, образованного методом прессования горячего металла. Применение такой заготовки исключало из технологического процесса глубокое сверление канального отверстия.
Способ получения прессованной заготовки разработан в технологическом институте инженером Залесским. Сущность ее прессования заключалась в продавливании горячего металла из закрытого объема через отверстие (очко) штампа. Для образования канального отверстия на конце пуансона имеется оправка, входящая в сечение очка до начала выдавливания из него металла.
Серией технологических опытов и проведенными испытаниями «установлена принципиальная возможность применения полых заготовок для изготовления стволов» (арх. 2224-51, стр. 230). Изготовленные из прессованных заготовок стволы на завершающем этапе отработки данной технологии по своим баллистическим характеристикам, прочности и живучести не уступали стволам, изготовленным по штатной технологии (арх. 2440-51, стр. 14).
Полигоном они были рекомендованы «для проверки технологичности (в процессе изготовления серийной партии) и более широких испытаний служебных качеств» (арх. 2771-53, стр. 138).
В ходе производства в стволах из прессованных заготовок обнаруживались отдельные дефекты по канальной части, трудноустранимые технологией.
С учетом этого фактора, а также в связи с развернувшимися работами по совершенствованию штатной и созданию других новых технологий, работы по прессованным заготовкам в то время не получили дальнейшего развития.
Поделитесь на страничкеСледующая глава >
document.wikireading.ru
Дорнование отверстий – Энциклопедия по машиностроению XXL
Применяется два основных метода обработки отверстий пластическим деформированием 1) дорнование отверстий одно- или много-зубыми прошивками или протяжками (дорнами), проталкиваемыми или протягиваемыми через отверстие в отдельных случаях эту же роль могут выполнять калибрующие шарики 2) раскатывание отверстий роликовыми или шариковыми вращающимися раскатками. [c.120]Дорнование отверстий многозубыми дорнами может выполняться с небольшими или большими натягами. Дорнование с небольшими [c.120]
Дорнование с большими натягами характерно для изготовления деталей типа втулок из бесшовных труб. Величина натяга при таком дорновании может достигать нескольких миллиметров. Процесс сопровождается значительным увеличением не только внутреннего, но наружного диаметра заготовки. С учетом этого заготовки можно нарезать из трубы, диаметр которой меньше диаметра изготовляемой из нее втулки. Устройство дорнов и распределение натяга между отдельными зубьями в данном случае такое же, как и при дорновании отверстий с небольшими натягами. [c.123]
Дорнование отверстий. В процессе калибрования отверстий инструмент (дорн) определенной формы проталкивается (протягивается) через обрабатываемое отверстие, имеющее несколько меньшие размеры, чем дорн, при этом за счет пластических деформаций диаметр отверстия увеличивается, а поверхностный слой металла в нем упрочняется. [c.375]
Ступицы катков, независимо от применяемого способа восстановления обода, восстанавливают осадкой в специальном штампе с последующим дорнованием отверстия и калибровкой шпоночного паза. Все операции по восстановлению ступицы производят на гидравлическом прессе. [c.376]
Обработка повышает несущую способность поверхности, уменьшает удельное давление в контакте трущейся пары, а образовавшийся рельеф с большими радиусами выступов и впадин способствует удержанию смазки между поверхностями. Давление на инструмент в зависимости от материала детали достигает 5…20 МПа, число ходов 2…4. Пластическое деформирование применяется и как отделочно-упрочняющая обработка в виде дорнования отверстий и алмазного выглаживания отверстий и шеек. В контакте детали и инструмента в этом случае имеет место трение скольжения. [c.484]
С целью повышения износостойкости и усталостной прочности деталей машин применяют накатывание и раскатывание роликами, дорнование отверстий, дробеструйный наклеп. [c.10]
В процессе дорнования отверстие кольца калибруется при каждом проходе дорна с двух сторон, этим самым удается исправить конусность, оставшуюся после токарной обработки отверстия. В качестве смазки применяют машинное масло (веретенное 2). [c.528]
При дорновании отверстий шарами, инструмент-шар, перемещаясь вдоль оси обрабатываемого отверстия, имеет местные угловые подвижности //, /у и //. В этом случае общая подвижность ТС, с учетом трех [c.59]
Обработка дорнованием отверстия запрессованной бронзовой втулки повышает прочность соединения с натягом в 1,5—3 раза Кроме того, при такой обработке достигается увеличением твердости внутренней поверхности втулки в 1,5—2 раза. [c.68]
Раскатывание отверстий выполняют многороликовыми инструментами на сверлильных, токарно-револьверных, горизонтально-расточных и агрегатных станках, а также на токарных автоматах. При раскатывании повышается твердость поверхностного слоя на 20—50% и его износостойкость в 1,5—2 раза. Такой же результат получают при дорновании отверстий шариками и калибрующими оправками. [c.138]
Отделку поверхностей производят накаткой наружных поверхностей уплотняющими роликами (или шариками), раскаткой цилиндрических отверстий роликовыми или шариковыми раскатками, дорнованием отверстий, калиброванием отверстий шариками или оправками, алмазным выглаживанием поверхностей вращения. Эти методы производительны и обеспечивают высокое качество поверх- [c.205]
Этот вид обработки отверстий заключается в их калибровании (дорновании) проглаживающими прошивками (дорнами) и шариками, а также в раскатывании отверстий. [c.229]
Стенки отверстий упрочняют с помощью раскатывания, Калибрования шариками и дорнования (прошивания уплотняющими прошивками). [c.323]
Для повышения сопротивления усталости пластин отверстия упрочняют дорнованием, путем обжатия в специальных матрицах и т. д. [c.402]
Заготовки перед обработкой необходимо подвергать травлению для очистки от окалины и ржавчины. В отверстии предварительно снимаются заходные фаски под углом 15—30°. Особое внимание обращается на перпендикулярность упорного торца обрабатываемому отверстию. Обработка производится на прессах или протяжных станках с применением СОЖ если деталь изготовляют из горячекатаной трубы с отношением диаметров 1,1—1,3, рекомендуются в качестве СОЖ веретенное масло, олеиновая кислота или сульфофрезол. При натягах более 0,5 мм обработка сопровождается образованием наплывов на торцах, которые приходится подрезать. При повышенных требованиях к точности диаметра после дорнования рекомендуется применять калибрующую прошивку, а для повышения чистоты (до 10-го класса) — роликовую раскатку. Они могут быть заменены чистовым растачиванием. Дорнование с большими натягами позволяет не только уменьшить трудоемкость изготовления деталей, но и упрочнить материал и поднять коэффициент его использования [c.123]
В настоящее время внедряется процесс доводки отверстия после развертывания — дорнование, обеспечивающее снижение припуска на последующую доводку до 0,03—0,05 мм вместо 0,07— 0,1 мм это позволило повысить производительность притирки, снизить расход паст, оснастки и притирочных станков. [c.407]
Схемы дорнования цилиндрических отверстий однозубыми и многозубыми дорнами и шариками показаны на рис. 215. [c.375]
Способы дорнования фасонных отверстий аналогичны рассмотренным выше. Фасонное дорнование часто применяется для исправления профильных отверстий, деформированных при термической обработке. [c.375]
Диаметр отверстия после дорнования й д получается несколько меньше диаметра инструмента d . Это связано [c.375]
Рис. 215. Схемы дорнования цилиндрических отверстий. | ![]() |
В процессе дорнования применяется смазка минеральное масло — при обработке стальных и бронзовых деталей и керосин — при обработке чугунных. При дорновании деталей из высокопрочной стали с очень большими натягами, а также при выдавливании в отверстии различного рода профилей целесообразно осуществлять предварительное покрытие поверхностей отверстий металлическими смазками — производить меднение или свинцевание их. [c.377]
Калибрование отверстий (дорнование) оправками и шариками применяется для повышения точности, чистоты поверхностей отверстий и микротвердости поверхностного слоя. Сообщая дополнительное [c.677]
Обработка отверстий в деталях машин производится тремя способами раскаткой (развальцовкой), дорнованием, калиброванием шариком. [c.484]
Технология располагает достаточными средствами, чтобы получать требуемую шероховатость. Кроме алмазов и кубического нитрида бора, широкое применение получили способы упрочняюще-чистовой обработки, такие как накатка, наружных поверхностей, раскатка (дорнование) отверстий. Эти процессы отличаются более высокой производительностью, чем шлифование, обеспечивают во многих случаях получение более высокого класса шероховатости поверхности, обладают целым рядом других преимуществ. [c.10]
Рис. 1.22. Схемы дорнования отверстий а — однозубым дорйом б — многозубым дорном в — многозубым составным дорном | ![]() |
При обработке отверстий, например, на токарно-винторезных станках (двухподвижная ТС) из-за пофешностей установки заготовок и мерного инструмента часто имеет место случай обработки эксцентрично вращающихся отверстий. При протягивании или дорновании отверстий (одноподвижная ТС), из-за пофещностей установки заготовок и других причин возможен случай обработки отверстий, ось которых не перпендикулярна к базовому торцу заготовки. Поэтому здесь в качестве количественной характеристики проявления эффекта самоустанавливаемости рекомендуется использовать значение коэффициента самоустанавливаемости. Выбор этой характеристики основан на известном из теории технологических цепей [60] положении о том, что на каждой операции между входной Аз и выходной Ад величинами погрешностей существует линейная взаимосвязь, выражаемая уравнением [c.60]
Проявления эффекта самоустанавливаемости при дорновании отверстий. Дорнование отверстий осуществлялось на прессе мод. УМЭ-ЮТС со скоростью 10 мм/мин. В качестве СОЖ использовалась жидкость на масляной основе марки МР-1у (ТУ 38 101731-80), а в качестве инструментов – многозубый дорн диаметром 15 мм, изготовленный из быстрорежущей стали марки Р6М5, и шар того же диаметра. В качестве обрабатываемых заготовок использовали втулки из стали 45 с соотношением диаметров 45/14,7 мм/мм и длиной 20 мм. Заготовки устанавливались по схемам (см. рис. 2.9, а – г). Схема установки заготовки и дорна на прессе (вариант обработки многозубым дорном жестко установленной заготовки) представлена на рис. 2.11 [95]. [c.67]
Дорнованием можно обрабатывать детали из стали, латуни, алюминия. Чем прочнее сталь, тем меньше, при одинаковом натяге, получается остаточная деформация у стали 20 она больше, чем у стали 45. Выглаживание деталей из алюминия сопровождается снятием небольшой стружки, в результате фактический натяг оказывается меньше расчетного. Иногда дорны изготовляют из стали 38ХМЮА с азотированной поверхностью. Применение многозубых дорнов при обработке отверстий небольшого диаметра, имеющих сопряжения с перпендикулярными им другими отверстиями, позволяет исключить прогиб инструмента, обычный, если в качестве последнего используется режущая прошивка. [c.123]
П р о v к у р я к о в Ю. Г.. Иссле дование процесса дорнования цилиндрических отверстий. Уральский политехнический им ститут имени С. М. Кирова, 1952. [c.589]
mash-xxl.info
Устройство для дорнования глубоких отверстий
Изобретение относится к области машиностроения и приборостроения, к обработке глубоких отверстий преимущественно малых диаметров. Устройство содержит корпус с отверстием для размещения дорна и толкателя его привода и закрепленное на корпусе направляющее устройство для толкателя, выполненное в виде нескольких пластин с центральным отверстием под толкатель и с расположенными по их концам бобышками с отверстиями, которыми каждая пластина установлена с возможностью взаимодействия с двумя возвратными пружинами, а направляющие разные пластины колонны размещены в различных проходящих через ось толкателя плоскостях. Для повышения надежности в эксплуатации устройство снабжено запрессованными в каждую пластину втулками из эластичного антифрикционного материала, отверстие которых совмещено с упомянутым центральным отверстием под толкатель, установленный в этом отверстии с натягом, при этом возвратные пружины смонтированы на двух штырях, один из которых закреплен на верхней части колонн, а другой – на бобышках пластин. 2 ил.
Изобретение относится к металлообработке, в частности к обработке глубоких отверстий дорнованием.
Известен станок для дорнования отверстий (авторское свидетельство СССР 360175, кл. В 23 D 37/04. БИ 36, 1972), содержащий станину с расположенной на ней подвижной кареткой для размещения деталей и дорна и неподвижно закрепленного на станине взаимодействующего с дорном стержня, который поддерживается несколькими люнетами, причем каждый люнет выполнен в виде двух несущих упорные ролики и кулачки рычагов, поворачиваемых посредством установленного на каретке толкателя, воздействующего на упорные ролики и кулачки соответственно при прямом и обратном ходах каретки. Известен станок для дорнования отверстий (авторское свидетельство СССР 428873, кл. В 23 D 37/04. БИ 19, 1974), содержащий станину, на которой размещен подвижный стол со штангой и люнет для поддержания последней, перемещающийся по направляющим, причем люнет выполнен в виде по крайней мере двух несущих упорные ролики замкнутых цепей, внутренние ветви которых взаимодействуют с направляющими, закрепленными на столе, а внешние – жестко связаны с кареткой, которая расположена между направляющими. Недостаток известных устройств – высокая сложность конструкций люнетов, состоящих из многих точных деталей. Известно устройство для дорнования глубоких отверстий (патент РФ 2127654, кл. В 23 D 37/10, В 23 Р 9/00, В 24 В 39/02. Бюл. 8, 1999), выбранное в качестве прототипа, содержащее корпус с отверстием для размещения дорна и толкателя его привода и закрепленное на корпусе направляющее устройство для толкателя, выполненное в виде нескольких пластин с центральным отверстием под толкатель и с расположенными по их концам бобышками с отверстиями, которыми каждая пластина свободно установлена на две жестко закрепленные на корпусе колонны бобышками от корпуса, причем направляющие разные пластины колонны размещены в различных проходящих через ось толкателя плоскостях, а на колоннах между корпусом и пластинами смонтированы пружины. Недостатком известного устройства является наличие зазоров между толкателем и центральными отверстиями пластин, что приводит, особенно при дорновании отверстий малого диаметра (1-3 мм), к прогибам толкателя, возрастанию сил трения в направляющем устройстве, увеличению износа его деталей и в целом к снижению надежности устройства в эксплуатации. Другим недостатком известного устройства является размещение возвратных пружин на колоннах между пластинами и корпусом, в котором выполнены выточки для этих пружин. Это обуславливает увеличение толщины верхней части корпуса, длины толкателя и уменьшение его жесткости, что также снижает надежность устройства в эксплуатации. Задача изобретения – повышение надежности устройства в эксплуатации. Решение указанной задачи достигается тем, что устройство для дорнования глубоких отверстий содержит корпус с отверстием для размещения дорна и толкателя его привода и закрепленное на корпусе направляющее устройство для толкателя, выполненное в виде нескольких пластин с центральным отверстием под толкатель и с расположенными по их концам бобышками с отверстиями, которыми каждая пластина установлена с возможностью взаимодействия с двумя возвратными пружинами, а направляющие разные пластины колонны размещены в различных проходящих через ось толкателя плоскостях. При этом оно снабжено запрессованными в каждую пластину втулками из эластичного антифрикционного материала, отверстие которых совмещено с упомянутым центральным отверстием под толкатель, установленный в этом отверстии с натягом, при этом возвратные пружины смонтированы на двух штырях, один из которых закреплен на верхней части колонн, а другой на – бобышках пластин. Сущность предлагаемого устройства поясняется чертежом, где на фиг.1 приведен его общий вид, а на фиг.2 – вид сверху. Устройство состоит из корпуса 1 с калиброванным отверстием для размещения дорна 2 и толкателя 3, закрепленного в штоке 4 его привода винтом 5. В корпусе 1 выполнена прорезь, в которую устанавливается обрабатываемая заготовка 6, и провальное отверстие для дорна 2. Для удержания дорна 2 в крайнем верхнем положении в корпусе предусмотрен подпружиненный фиксатор (не показан). Для направления толкателя 3 служат пластины 7 с запрессованными в них втулками 8 из эластичного антифрикционного материала, в котором толкатель установлен с натягом. Пластины 7 по концам содержат бобышки с отверстиями, которыми они свободно установлены на запрессованные в корпусе 1 колонны 9, 10, 11 и 12 (фиг. 2). Причем каждая пара этих колонн, несущая пластину 7, размещена в различных проходящих через ось толкателя 3 плоскостях. На штырях 13 и 14, запрессованных соответственно в верхнюю часть колонн 9, 10, 11 и 12 и бобышки пластин 7, смонтированы возвратные пружины 15, 16, 17 и 18. Устройство работает следующим образом. Обрабатываемая заготовка 6 устанавливается в прорезь корпуса 1 соосно с дорном 2. При включении привода шток 4, преодолевая сопротивление пружин 15, 16, 17 и 18 и небольшие силы трения, возникающие при перемещении толкателя 3 во втулках 8, своим торцом последовательно сдвигает размещенные на колоннах 9, 10, 11 и 12 пластины 7 со втулками 8 вниз, а толкатель проталкивает через отверстие заготовки дорн 2, который падает в провальное отверстие в корпусе 1. При перемещении штока 4 с толкателем 3 вверх под действием пружин 15, 16, 17 и 18 пластины 7 со втулками 8 возвращаются в исходное положение. Так как в предлагаемом устройстве толкатель установлен в центральном (направляющем) отверстии с натягом, а длина толкателя снижена, то прогибы его резко уменьшаются. Благодаря этому существенно возрастает надежность предлагаемого устройства в эксплуатации. На основе предлагаемого устройства разработано приспособление к пневматическому прессу для дорнования отверстия диаметром 2+0,025 мм во втулке из стали 40Х высотой 100 мм. Проведенные испытания свидетельствуют о высокой надежности приспособления в эксплуатации.Формула изобретения
Устройство для дорнования глубоких отверстий, содержащее корпус с отверстием для размещения дорна и толкателя его привода и закрепленное на корпусе направляющее устройство для толкателя, выполненное в виде нескольких пластин с центральным отверстием под толкатель и с расположенными по их концам бобышками с отверстиями, которыми каждая пластина установлена с возможностью взаимодействия с двумя возвратными пружинами, а направляющие разные пластины колонны размещены в различных проходящих через ось толкателя плоскостях, отличающееся тем, что оно снабжено запрессованными в каждую пластину втулками из эластичного антифрикционного материала, отверстие которых совмещено с упомянутым центральным отверстием под толкатель, установленный в этом отверстии с натягом, при этом возвратные пружины смонтированы на двух штырях, один из которых закреплен на верхней части колонн, а другой – на бобышках пластин.РИСУНКИ
Рисунок 1, Рисунок 2www.findpatent.ru