Электроды для плазмореза – Электроды для плазменной резки
alexxlab | 01.09.2019 | 0 | Вопросы и ответы
Расход электродов для плазменной резки. Характеристики, нормы – Мои статьи – Каталог статей
Помимо затрат на закупку металла, важнейшей частью эксплуатационных расходов на плазменную резку является покупка расходных материалов. Именно необходимость частой замены расходников и составляет львиную долю себестоимости данного вида технологических операций. Соответственно, добившись оптимального использования расходных материалов, можно заметно снизить издержки на плазменную резку.
Нормы расхода материалов
Не существует единого показателя «нормального» расхода электродов и других материалов для плазморежущих станков. Каждый такой станок имеет собственные характеристики (рабочий ток, диаметр сопла, интенсивность расхода газа, скорость резки и т.д.), поэтому для каждой модели норма расхода будет своя собственная.
Однако и это лишь начало. На скорость сгорания расходников также влияет множество других факторов, связанных с характеристиками обрабатываемого материала — вид и марка разрезаемого металла, его толщина, ширина разреза и т.д.
На норму расхода влияет также и мощность режущей дуги. По умолчанию она всегда принимается равной 40 кВт, однако при использовании аргоно-водородной смеси и дополнительной стабилизации режущей дуги при помощи сжатого воздуха, ее мощность принимается равной 80 кВт.
Когда менять электрод?
Следует отметить, что на практике мало кто вообще обращает внимание на формулы с нормами расхода электродов. На большинстве предприятий для их замены существуют собственные достаточно грубые нормативы. В частности электроды меняют по умолчанию либо после определенного количества пробивок, либо после каждой смены, если интенсивность работы станка позволяет данному расходнику прожить целую смену.
Соль в том, что в большинстве случаев замена электродов происходит слишком рано, когда данный расходник еще мог бы поработать. Иными словами предприятие банально теряет деньги, выбрасывая в мусор то, что способно приносить прибыль еще некоторое время.
На самом же деле поводом заменить электрод должен служить вполне конкретный признак, о котором будет сказано чуть ниже. Но чтобы понимать, что это за признак, следует в двух словах сказать о конструкции электрода и его рабочих задачах.Электрод плазморежущего станка имеет две составные части — корпус и вставку. Именно вставка обеспечивает формирование электрической дуги, поджигающей газ, из которого в итоге получается плазма. Корпус в свою очередь отвечает за отвод избыточной тепловой энергии, неизбежно генерируемой при создании плазмы.
Материалом для изготовления корпуса служит медь, так как она обладает высокой теплопроводностью. Однако этот металл характеризуется низким электрическим сопротивлением, что создает опасность «соскакивания» электрической дуги на сам корпус. Разумеется, допускать такое нельзя, поскольку тогда сгорят другие элементы плазмотрона, а может и сам плазмотрон.
Так вот, чтобы максимально эффективно использовать электрод, не допустив при этом «соскакивания» дуги на корпус, менять этот расходник следует ровно в тот момент, когда на вставке появится ямка по размерам равная диаметру самой вставки.
Причины ускоренного расхода электродов
Своевременная (а не ранняя) замена электрода — это лишь первый шаг на пути к разумной экономии при осуществлении плазменной резки. Второе, на что следует обратить внимание — фактический расход электрода на погонный метр реза или час работы станка. Необходимо сравнить данный показатель с установленной нормой для данной модели источника. Если показатели не совпадают, придется искать и устранять причину повышенного расхода.
Самих причин существует не так уж много:
1. Посторонние примеси в воздухе. Для нормальной работы станка ему нужен атмосферный воздух, чтобы формировать правильную газовую смесь. Если же в воздух, который нагнетается компрессором, загрязнен фракциями масла и воды, качественную газовую смесь не получить. Проверяя воздушный фильтр с отделителем воды в начале каждой смены, можно избежать данной проблемы.
2. Низкое качество рабочего газа. Крайне важно строго соблюдать рекомендации производителя станка во всем, что касается выбора расходников, особенно в вопросах плазмообразующего газа. Абсолютно недопустимо использовать неподходящий газ, или смесь, загрязненную кислородом либо атмосферным воздухом.
3. Низкое давление газа. Если отклониться от рекомендуемых показателей давления, низкий поток газа вызовет не только ускоренное выгорание электрода, но также будут обильно появляться искры, а рез получится низкого качества.
4. Нехватка охлаждающей жидкости. Для охлаждения в станках используется деионизированная вода либо ее смесь с чистым этиленгликолем. Обычно станки оснащены предохранителем, который выключает аппарат при сбое в работе системы охлаждения. Но если предохранителя нет, либо он сломался, то при перегреве плазмотрона срок службы электрода заметно сокращается.
5. Грязь в газопроводе. Пыль и влага, которых в избытке в заводском цеху, легко оседают внутри газопроводов, нарушая тем самым формирование нормальной плазменной массы. По этой причине даже после недолгого простоя газопроводы нужно чистить. А прямое попадание влаги на электрод и вовсе способно вывести его из строя.
6. Неисправность завихрителя. С данной деталью могут приключиться самые различные неприятности. Обычно он либо лопается, либо частично оплавляется. Нередки также случаи банального засорения грязью. Так или иначе, но любые изменения в количестве воздуха, расходуемого в процессе работы станка, равно как и нарушения в направлении воздушного потока, неизбежно приводят к очень скорому сгоранию электрода.
В заключение нам остается лишь порекомендовать вам, как можно чаще заглядывать в руководство по эксплуатации вашего плазморежущего станка. Там вы найдете решение многих проблем, которые могут возникнуть в процессе использования данного аппарата.
Сезонность работ по плазменной резке
Услуги плазменной резки — достаточно перспективный вид малого бизнеса, который найдет своего клиента и в крупном мегаполисе, и в небольшом райцентре. Однако многих предпринимателей, начинающих деятельность в данной сфере, интересует, насколько велик фактор сезонности в данном бизнесе и следует ли ожидать просадок спроса в определенное время года.
…Читать подробнее
Сравнение лазерной и плазменной резки. Преимущества и недостатки
Часто, при покупке оборудования для резки металла, мы встаем перед выбором, какой вид резки лучше, плазменный или лазерный? У каждого есть свои преимущества и недостатки и для того, чтобы вы сделали правильный выбор, в этой статье мы подробно разберем каждый.
…Читать подробнее
Важные навыки оператора по плазменной резке
Все более востребованной сегодня становится плазменная резка металла, которая стала современной альтернативой обычной газовой. Производительность работы существенно возрастает, а рабочий процесс упрощается. Однако для правильного и эффективного использования плазмотрона специалист должен обладать всеми необходимыми навыками.
…Читать подробнее
www.perfect-cut.ru
Износ электродов в системах воздушно-плазменной и кислородно-плазменной резки
Электроды — это конструктивно cложные расходные детали для систем плазменной резки. Их конструкция, материал и принцип работы схож с характеристикам автомобильных свечей зажигания. Электроды, как и свечи зажигания, проводят электричество высокого напряжения в среде c высокой температурой. Поэтому материалы, из которых состоит электрод, должны быть устойчивы к воздействию образующихся при температуре веществ плазменной дуги, и высокоскоростных струй вихревого газа. Помимо этого, такие материалы должны обеспечивать надежное уплотнение, не допускающее утечек газов и жидкостей под высоким давлением. Как и свеча зажигания, электрод — это самая прочная рабочая часть в системе.
Электрод проводит питание постоянного тока от источника тока плазменной резки к металлическому листу. Стандартная конструкция электрода — это держатель из меди или композитного материала медь-серебро c эмиттером из гафния — тугоплавкого металла, устойчивого к воздействию дуги в средах воздушно-плазменной или кислородно-плазменной резки. Эмиттер постепенно приходит в негодность под воздействием высоких температур дуги и высокоскоростных потоков газа. Основной износ электрода приходится на запуск и остановку резки, когда гафниевый материал плавитcя и отвердевает, при быстром нагреве и остывании.
При нормальном использовании на краю детали образуется небольшой дефект вогнутой формы, постепенно увеличиваясь в размере (на несколько тысячных см за один раз) до 0,10–0,31 см в зависимости от конструкции, материалов резака и расходных деталей. (См. данные таблицы ниже). Когда этот дефект становится слишком глубоким, дуга цепляется за материал держателя и расплавляет его. Если электрод не может зажечь или поддержать дугу — значит, он пришел в негодность. Если расплавленный материал с электрода стекает вниз и скапливается в отверстии сопла, это приводит к стремительному и непоправимому отказу электрода и сопла.
Система плазменно-дуговой резки | Медные электроды, износ в дюймах | Электроды из композита медь-серебро, износ в дюймах |
Прецизионная система плазменно-дуговой резки (кислородно-плазменная резка) | 0,07–0,12 см | 0,15–0,20 см |
Система плазменно-дуговой резки с впрыском воды (кислородно-плазменная резка) | 0,10–0,20 см | 0,25–0,35 см |
Стандартная система плазменно-дуговой резки с использованием двухкомпонентной газовой смеси (кислородно-плазменная резка) | 0,10–0,20 см | 0,25–0,35 см |
Стандартная система плазменно-дуговой резки с использованием двухкомпонентной газовой смеси | 0,22–0,30 см | 0,25–0,35 см |
В самых современных системах кислородно-плазменной резки срок службы деталей обычно составляет 1–2 часа фактического времени «на дуге» или 200–300 прожигов. В системах воздушно-плазменной резки этот срок может в два раза превышать указанный, достигая тем самым 400–600 запусков. Это объясняется тем, что содержащийся в воздухе азот понижает интенсивность реакции воздуха с электродами. В системах кислородно-плазменной резки с инертными пусковыми газами и плавным изменением тока срок службы электрода может достигать 1000 или более запусков.
| Новое состояние Новый электрод. Представленный в этом примере электрод имеет конструкцию из сварного композитного материала медь-серебро с серебром в передней части электрода и медью в его задней части. В центре детали расположен неиспользованный гафниевый элемент. |
| Естественный износ Электрод с естественным износом. Дефект гафниевой вставки образован в ее центре и однородно по форме, что свидетельствует о правильном выравнивании расходных деталей и соответствующей скорости потока вихревого плазмообразующего газа. Глубина дефекта составляет приблизительно 0,25 см. Передние края детали ровные и четкие. Цвет серебра существенно не изменился. На передней части детали заметны оксидные образования серого оттенка, что является нормой.
|
| Естественный износ на половину от полного износа Электрод с обычными признаками естественного износа. Данный электрод сняли с системы до окончания срока службы по другой причине, например: скольжение резака по листу, удар резака, изменение напряжения, изменение качества резки и т.д. Глубина дефекта составляет 0,19 см. Несмотря на то, что этот электрод выглядит как отработанный, он еще сможет выполнить 100 или более прожигов, а его дефект может увеличиться до 0,25 см или даже до 0,35 см, прежде чем он выйдет из строя.
|
| Дефект не по центру Электрод с дефектом, смещенным относительно центра. Эту проблему легко обнаружить, так как такое расположение дефекта говорит о серьезной проблеме с потоком газа (неисправный или закупоренный завихритель) или о разбалансировке деталей резака (вследствие ошибок при сборке и проблем с подгонкой деталей). Если эту проблему не удается устранить путем полной замены деталей резака, тогда это может свидетельствовать о неисправности самого резака.
|
| Влага при запуске Наличие влаги при запуске дуги. Такие детали имеют неровные следы воздействия вихревой дуги от выточки под ключ до контактной поверхности электрода. Влага в газе, который подается до возбуждения дуги, приводит к тому, что серебро подвергается воздействию высоких частот. Передние края серебра нечеткие; качество поверхности, как при обработке пескоструйным аппаратом. Проверьте газ, который подается до возбуждения дуги, на наличие влаги. Быструю проверку можно выполнить с помощью бумажного полотенца или листа бумаги. Поместите чистое бумажное полотенце под резак и включите подачу газа в системе (только в режимах TEST (ТЕСТ) или GAS CHECK (ПРОВЕРКА ГАЗА)!). На полотенце не должно быть признаков наличия влаги или загрязнений.
|
| Утечка охлаждающей жидкости Проще всего обнаружить проблему утечки охлаждающей жидкости.
Эта проблема часто происходит из-за разреза или недостаточной смазки уплотнительных колец или по причине ненадежно закрепленных или разбалансированных деталей. |
| Недостаточная подача газа Недостаточная подача газа при возбуждении дуги обусловливает медленное зажигание. Перенос дуги с начальной точки (как правило, это острый угол, наподобие выточки под ключ) на эмиттер длится слишком долго. На этих деталях будет достаточно однородное кольцо расплавленного материала держателя вокруг дефекта. Поверхность может выглядеть, как спаянные брызги металла, или вдоль передней части детали может образоваться сварочная ванна.
|
| Эксплуатация до отказа Электрод, который эксплуатировался до непоправимого отказа. Поскольку электрод расположен выше, то при его работе повреждается сопло, когда расплавленный материал выдувается с наконечника электрода и скапливается на внутренней поверхности сопла. При длительной эксплуатации, в работе всех деталей наступает такой отказ. |
| Эксплуатация до отказа
Все это говорит о недостаточной скорости потока газа, что приводит к неконтролируемому зажиганию дуги между соплом и электродом. Проверьте скорость потока газа, подаваемого на резак. Лучше всего это сделать, используя расходомер (0–400 куб.фут/ч) со шлангом, надетым на выпускное отверстие резака тестируемой системы. При отсутствии такой возможности, можно выполнить тест на тактильное ощущение потока газа на выпускном отверстии резака, когда включена подача только плазмообразующего газа. Должен ощущаться вихревой поток газа, который действует как всасывающая сила.
|
| Высокая cкорость потока газа Если сопло в хорошем состоянии, но при этом электрод имеет достаточно глубокий дефект, тогда это может говорить о том, что скорость потока плазмообразующего газа может быть слишком высокой. При интенсивном воздействии вихрей плазмообразующего газа элемент быстро разрушается. Это приводит к стремительному глубокому износу. Проверьте объемную скорость потока плазмообразующего газа.
|
При возникновении вопросов звоните:
8-800-333-09-71 — звонок бесплатный
Чтобы не подорвать налаженный процесс работы Вашего предприятия и обезопасить Ваш бизнес от непредвиденных потерь, приобретайте только оригинальные расходные детали у авторизованных дистрибьюторов, имеющих сертификат на право реализации оборудования и расходных материалов.
Источник статьи: Hypertherm Inc.
c-avt.com
Электроды для плазмореза | TMDL мотор
Электрод плазменной резки переносит ток от горелки к пластине. Это тонкая деталь из меди или серебра и содержит гафний или вольфрам. Эти материалы оказались отличными проводниками электричества. Электричество подается от машины к факелу и переходит в катодный блок, с которым электрод контактирует, и затем фокусирует этот заряд на конце электрода через вставку гафния / вольфрама, которая затем дуги к пластине. Сопло принимает эту дугу и действительно фокусирует ее таким образом, что режет металл, но электрод несет ток.Сопло электрода имеет тенденцию сильно нагреваться, потому что он находится прямо посреди перегретого газа. Таким образом, задняя часть электрода имеет присоединенное охлаждающее устройство, которое помогает переносить тепло от электрода.
Когда вы используете электрод, гафний / вольфрам становится расплавленным, и куски его начинают выдуваться через сопло по мере вырезания. Он развивает яму на передней поверхности электрода. Когда глубина углубления превышает 1/32, пришло время изменить расход. Если вы не измените электрод и вместо этого запустите его в режим отказа, а это означает, что он действительно больше не будет вырезать, вы фактически горите через медь, потому что гафний ушел. Дуга выглядит как уродливое зеленое свечение, если вы даже можете вообще срезать. Вся вершина электрода будет сожжена. Вы никогда не хотите добираться до этого момента, потому что он вводит огромное количество тепла в этот факел, что может нанести большой урон.
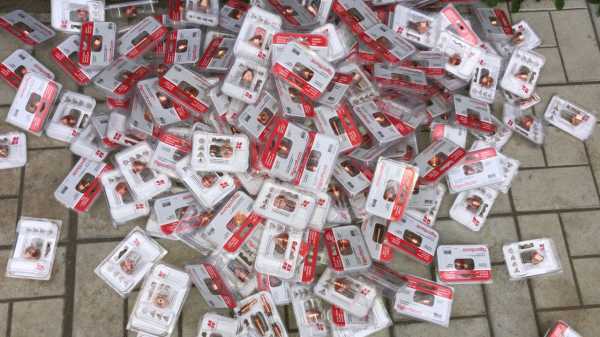
Мы всегда рекомендуем вам сменить электрод и насадку вместе. Таким образом, когда вы бросаете новый набор расходных материалов, у вас есть идеальное отверстие и идеальная глубина ямы каждый раз. Если вы склонны просто менять их индивидуально, вы можете поставить под угрозу качество резки. Вы можете установить новый электрод, но если ваше отверстие сопла шире, чем должно быть, вы отказались от некоторых характеристик.
Ничто действительно не ухудшается в вихревом кольце, хотя оно может треснуть в результате падения или от нагревания и охлаждения с течением времени. Как только он взломан, он не может направлять газ так, как должен, поэтому пришло время его изменить. На каждые 5-10 комплектов электродов / форсунок вы должны изменить вихревое кольцо.
tmdl.ru
Комплектующие для плазменной резки, плазмотрона, к плазморезу
Главная страница » Плазменная резка » Оборудование » Комплектующие для плазменной резки
Плазменная резка – это самый современный способ раскроя не только металла, но и некоторых других, не проводящих электрический ток материалов. Осуществляется она при помощи плазмореза высокотемпературной ионизированной струёй воздуха – плазмой. Качество работы плазмореза (скорость реза и техническое состояние кромок) зависит от многих факторов. Большое значение играют комплектующие для плазменной резки: детали и расходные материалы. Для плазмореза расходными материалами являются: сопла, электроды и т.д.
Устройство плазмореза — детали
Аппарат плазменной резки состоит из следующих блоков:
Источник питания обеспечивает определённые параметры тока и напряжения, компрессор – качество и давление воздуха и вихревую форму воздушного потока. Режущим инструментом является плазмотрон: он генерирует и формирует струю плазмы. Кабель-шланги обеспечивают подачу электрического тока и воздуха от источника в плазмотрон.
Конструкция плазмотрона
Самыми важными элементами конструкции плазмотрона являются сопло и электрод. Их состояние определяет глубину реза и качество кромок.
Сопла
Сопла для плазмотрона (узнать больше про них можно здесь)
Основная функция сопла – формирование струи плазмы, и именно для этого оно сужается к выходному отверстию. Применяются керамические и медные сопла. Чаще используются медные, так как у них выше механическая прочность, и они имеют воздушное охлаждение.
От геометрических размеров сопла зависят возможности плазмореза. Его диаметр определяет скорость и объём проходящего воздуха, а эти два параметра влияют на:
- ширину реза;
- скорость выполнения работы;
- степень охлаждения плазмотрона.
Электроды
Электроды для плазменного резака (узнать про них подробнее можно тут)
Электрод служит для поджига и поддержания дуги. Материалом для него могут служить:
- медь;
- вольфрам;
- гафний;
- цирконий.
Самые популярные – электроды из гафния. Не желательно использование электродов из бериллия и тория, так как оксид первого – радиоактивен, а второго – токсичен.
Необходим систематический контроль за техническим состоянием (не допускать изношенности) этих двух деталей. Своевременная и одновременная замена электрода и сопла позволят получить качественный раскрой материала.
Прочие расходники
К другим расходным материалам относятся:
- защитные насадки и колпаки;
- изоляторы;
- пружины;
- наконечники;
- диффузоры;
- насадки для строжки.
Где можно приобрести комплектующие и расходные материалы для плазмореза
Мы уже рассказывали, что развитие плазменной обработки материалов привело к большому разнообразию технологических процессов и конструктивных решений самого плазмотрона. Но, в существующем изобилии постоянно повторяются одни и те же функциональные узлы (например, в плазмотроне — это электрод и сопло). Они в процессе обработки материала выполняют роли катода и анода (в настоящей статье рассмотрим анод — катод рассмотрен в… Далее »
Большое количество областей применения и требований к плазменной обработке материалов привело к большому разнообразию, как в организации технологических процессов, так и в конструктивном оформлении самого плазмотрона. В существующем изобилии конструкций плазморезов, имеются одни и те же функциональные узлы. Например, в плазмотроне — это электрод и сопло, которые в процессе обработки материала выполняют роли катода и анода… Далее »
Шланг для плазмотрона входит в состав кабель-шлангового пакета. Он служит для подключения плазмотрона к блоку питания, источникам сжатого воздуха (компрессору) и вспомогательного газа (газораспределительной рампе). Подключение шланга к газораспределительной рампе Через шланг подаются плазмообразующие газы от батареи баллонов, которые устанавливаются в газораспределительные рампы. В рампе может быть любое количество… Далее »
Кабель-пакет для плазмореза (его полное название: кабель-шланговый пакет) предназначен для соединения между собой источника питания, компрессора и плазмотрона. По электрическому кабелю подается ток от трансформатора или инвертора (в зависимости от модели плазменного оборудования) для возбуждения или горения электрической дуги (режим зависит от вида обработки: резка плазменной струёй или плазменно-дуговая). По шлангу идет сжатый… Далее »
Для работы плазмореза необходим блок электропитания, который обеспечивает режущий узел строго заданными по амплитуде электрическими током и напряжением. Основополагающим узлом блока питания для аппарата плазменной резки могут быть: трансформатор; инвертор. Трансформатор Сварочный трансформатор не чувствителен к перепадам напряжения, что существенно при наличии маломощной электросети (например, в сельской местности)…. Далее »
О плазменной резке и о том, как работает плазмотрон, мы рассказывали в статье «Плазменная резка. Принцип работы». В ней рассказано, что важнейшими узлами и деталями, влияющими на формирование струи и качество реза, являются электроды и сопла. Про электроды мы рассказывали и дали некоторые рекомендации по их правильной эксплуатации в статье «Электроды для плазменной резки». Здесь расскажем про сопло для плазменной… Далее »
Как происходит плазменная резка и работает плазмотрон, мы рассматривали на нашем сайте в статье «Плазменная резка. Принцип работы». Из этой статьи понятна функция электрода в процессе плазменной резки, поэтому на этом останавливаться не будем. Сегодня рассмотрим, что влияет на преждевременный выход из строя электрода. Признаки необходимости замены электрода Напомним, что электрод состоит из двух… Далее »
Плазменная резка сегодня нашла широкое применение в промышленности и быту, как удобный, технологичный и достаточно простой метод плазменной обработки различных материалов, при котором используется в качестве рабочего инструмента струя плазмы. Одним из важных условий работы плазменного оборудования является наличие плотного воздушного потока, которым обеспечивается сжатие электрической дуги и устранение, образующихся при… Далее »
Плазменная установка состоит из источника питания и плазмотрона. Для соединения с компрессором используется кабель-шланговый пакет. Рассмотрим один из главных составляющих аппарата – плазмотрон (резак). Устройство плазмотрона Под резаком подразумевается плазмотрон. Это устройство, которое подключается к источнику тока, и в процессе резки образует плазму. Состоит оно из следующих основных узлов: системы газо- и… Далее »
plazmen.ru
Расходные материалы для плазменной резки: выбираем расходники
Расходные материалы для плазменной резки требуют своевременной замены, что позволяет гарантировать высокое качество изготавливаемых изделий и надежную работу станка.
А вот использование в ходе рабочего процесса изношенных расходников: сопел, электродов, вихревых колец и других элементов, непременно приведет к браку.
Как определить время замены расходных материалов?
Узнать, что пришло время менять расходные материалы, опытному оператору не составит труда, ведь плазморез сам выдает наличие изношенных элементов:
- качество реза ухудшилось – значит, необходимо проверить на износ электрод и сопло;
- когда пламя электрической дуги становится зеленоватым – начинает выгорать вставка на торце электрода;
- когда процесс пробивки требует снизить высоту плазмотрона – результатом становится деформация внешних и внутренних стенок сопла, так как в процессе функционирования его обрызгивает горячий металл.
Определить, требуется ли в настоящий момент замена электрода, также позволит визуальная оценка расходного материала.
С этой целью необходимо осмотреть серебристую вставку, находящуюся на торце электрода. Она может быть выполнена из вольфрамового, циркониевого или гафниевого сплава.
При этом электрод можно считать рабочим, если выработка вставки не превышает глубину в 2 мм, при условии эксплуатации кислородно- или воздушно-плазменной резки.
Видео:
Для плазменной резки с использованием аргоновой или азотной среды допустимая глубина выработки составляет 2,2 мм.
Такие расходники плазменной резки, как вихревые кольца, требуют замены реже, чем другие расходные материалы.
Как правило, срок службы завихрителей истекает после износа 50 электродов.
Продлить время их эксплуатации позволяет правильная смазка уплотнительных колец.
При недостаточном ее количестве вихревые элементы могут деформироваться.
Но если применить смазку в слишком большом количестве, может произойти блокировка вихревых каналов, в результате возникнут проблемы с охлаждением электрода, понизится качество резки.
Правильная технология смазывания завихрителей предусматривает нанесение смазки на пучки пальцев в малом количестве, после чего их складывают вместе, трут друг о друга, затем только смазку наносят на поверхность уплотнительного элемента.
Чтобы своевременно производить замену расходных материалов для плазменной резки, рекомендуется вести специальный журнал.
Его применение позволит фиксировать среднее время работы расходников.
Исходя из чего, впоследствии, можно будет провести плановую замену материалов, тем самым предотвратить ухудшение качества резки и, что самое важное, поломку плазмореза.
Как правильно выбрать расходные материалы?
Выбирая расходники для плазменной резки, необходимо учитывать технические возможности материалов, что позволит их полноценно эксплуатировать длительное время.
К примеру, при выборе сопла и электрода рекомендуется руководствоваться характеристиками металла, используемого для резки.
К примеру, от типа металла и его толщины зависит число пробивок, которое могут выдержать сопло и электрод. Также учитывается применяемая величина тока.
При выборе на тип необходимых расходных металлов для плазменной резки также оказывает влияние вид металлических изделий, особенно это касается цветных металлов и их сплавов.
Обработке подвергают углеродистую и нержавеющую сталь, но для последнего типа изделия при резе под углом применяется конкретная категория расходных материалов.
Какие именно нужно использовать расходники при разных рабочих режимах, как правило, описывается в справочной книге оператора, специально созданной под оборудование плазменной резки.
Точно следуя инструкции производителя плазморезов, можно продлить срок эксплуатации установки.
Иначе использование расходников, несоответствующих выбранному режиму, приведет к понижению качества среза и поломке расходных материалов.
При этом рекомендуется проводить плазменную обработку материалов, обеспечив рабочий процесс с такой силой тока дуги, на величину которой изначально были запланированы расходные элементы.
Значит, если сопло плазмореза оборудовано на 40А, нельзя проводить резку плазмой с применением 100А.
Обычно чтобы достичь идеального качества реза, выставляют величину тока на 95% с учетом номинального значения, на котором может эксплуатироваться сопло.
При режиме резки с пониженной силой тока дуги, рез получается неудовлетворительный – с обратной стороны вырезанной детали можно наблюдать излишки метала.
При большой силе тока значительно снижается период эксплуатации сопла.
Правила сборки элементов установки плазменной резки
При замене расходных элементов оборудование плазменной резки нужно собирать так, чтобы все детали с нужным усилием контактировали между собой.
Такой подход позволит обеспечить высокий уровень электроконтакта, необходимый оборот охлаждающего вещества и воздуха.
Разборку и сборку аппарата плазменной резки нужно проводить на чистом месте, необходимо полностью исключить попадание пыли в плазмотрон.
Видео:
Смазывая поверхность уплотнительных элементов силиконовым составом, нельзя применять его слишком много, так как это может обратиться закупоркой вихревых каналов.
А также вызвать загрязнение резака технической пылью, которая является токопроводящей, что в конечном итоге может стать причиной пробоев электродуги в камере, образующей плазму.
Также не рекомендуется смешивать отдельные типы смазок, что станет причиной воспламенения плазменного оборудования.
Особенности регулярного обслуживания плазмореза
Без регулярного обслуживания аппарат плазменной резки может функционировать не один год, но это неправильно.
Охлаждающие и газовые каналы имеют свойство постепенно забиваться металлической пылью, в то время как они должны постоянно содержаться в чистоте.
Эта проблема касается и посадочных мест расходников, которые нужно регулярно проверять на наличие загрязнений и деформаций.
Снятие пыли и грязи с элементов установки плазменной резки нужно проводить с использованием натуральной мягкой ткани и специального вещества для зачистки электроконтактов.
Также нужно выполнять ежедневно проверку давления и расхода охлаждающего состава и газа, образующего плазму.
Если не проконтролировать затраты охлаждающего вещества, а они могут оказаться заниженными, основные элементы плазмореза не будут должным образом охлаждаться, что приведет к снижению их срока службы.
Причина недостаточного поступления охлаждающего состава, может крыться в изношенном насосе или закупоренных фильтрах.
Очень важно осуществлять контроль стабильности давления, которое отвечает за стабильность режущей дуги и качество среза.
При излишнем давлении газа, образующего плазму, плохо зажигается плазменная дуга, такая проблема возникает, даже если все другие требования по техническим настройкам были выполнены правильно.
Видео:
По причине завышенного давления чаще всего приходится менять электроды.
Газ, за счет которого в аппарате образуется плазма, должен быть без каких-либо примесей, так как именно от него зависит срок эксплуатации расходных материалов.
Не менее важно вести контроль над рабочим расстоянием, которое находится между краем сопла и обрабатываемым изделием, так как от этого также зависит срок годности расходных элементов и качество реза.
rezhemmetall.ru
Электроды (катоды) для плазменной резки (плазмореза)
Катод для плазменной резки – одна из основных деталей плазмотрона , которая производится со вставками из тугоплавкого металла (вольфрама, циркония или же гафния). В компании «ПУРМ» вы можете купить подходящий для конкретного оборудования электрод по цене производителя, а с выбором вам помогут наши эксперты.
Назначение
Катод для плазмореза расположен в тыльной стороне дуговой камеры и выполняет важнейшую функцию – возбуждение плазмогенерирующей дуги. Изготовляется в виде гильз-вставок из материала с высокими теплопроводящими свойствами (медь и ее сплавы).
Посередине изделие имеет специальную вставку из материала с высокой термоэлектронной эмиссией (циркония либо гафния), которая и контактирует с плазменной дугой. В процессе эксплуатации она выгорает, поэтому время от времени нужно проверять ее выработку – при превышении значения в 2 мм элемент требуется заменить.
Электроды для плазмореза производятся разной длины и диаметра, поэтому подбираются исходя из разновидности оборудования. Конец катода-вставки выполняется плоским, а хвостовая часть активно охлаждается водой или воздухом, что значительно продлевает его срок эксплуатации. В плазмотроне он фиксируется с помощью специальных цанг или зажимов.
Особенности катода-вставки
Основная особенность электрода для плазменной резки основана на том, что закрученный газовый поток позволяет стабилизировать дугу и закрепить ее активное пятно по центру гильзы – т.е. непосредственно на вставке из тугоплавкого металла. Во всех аппаратах, работающих на сжатом воздухе, применяются именно такие изделия, поскольку путем создания оксидно-нитридной пленки они эффективно защищают расплав чистого металла от возможного испарения.
При работе в окислительных средах нередко используются пустотелые катоды из меди для плазмореза. Они обладают повышенной устойчивостью к разрушению при использовании вихревого метода стабилизирования дуги, создаваемого специализированным завихрительным приспособлением плазмотрона.
В компании «ПУРМ» вы можете купить качественные электроды для плазменной резки, которые характеризуются продолжительным эксплуатационным ресурсом. Обращайтесь – мы гарантируем бесплатную помощь в выборе изделия, в зависимости от используемого оборудования и других аспектов.
www.purm.ru
Плазменная резка. Замена электродов для плазменной резки.
Обычно электрод для плазменной резки состоит из двух частей. Первая часть – „ вставка”, которая образует дугу. „Вставка” обычно выполняется из гафния или вольфрама, что зависит от выбранного плазменного газа. Вторая часть выполняется из меди. Медь имеет хорошую теплопроводность, она помогает отвести тепло от „вставки”. Нельзя допускать, чтобы дуга вступила в контакт с медью – это может испортить весь плазмотрон. Необходима обязательная замена электрода при появлении во „вставке” ямки такой же глубины, как и её диаметр.
Причины досрочного износа электрода
1. Низкое качество воздуха
Воздух, используемый в аппарате плазменной резки, должен быть чистым и очищенным от влаги или масла. Воздух, поставляемый посредством воздушного компрессора, может содержать влагу и масло. Плазменный аппарат должен иметь воздушный фильтр с влагоотделителем. Фильтр необходимо контролировать каждый день и по надобности менять.
Как узнать, что воздух чистый:
- Проверьте использованные сопла и электроды: если они чёрные от сожжённых веществ, то воздух плохого качества.
- Если аппарат в течение часа работает на холостом ходу, положите зеркало под отверстие сопла и направьте на него воздух: если воздух влажный, то зеркало запотеет.
2. Плазмообразующий газ низкого качества
Есть несколько плазмообразующих газов для использования в аппаратах плазменной резки. Выбор соответствующего газа очень важен. В инструкции обычно указывается, какой газ нужно применять при работе с определенным комплектом расходных материалов. В большинстве систем для ручной резки используется сжатый воздух.
Электроды для резки с помощью сжатого воздуха обычно содержат „вставку” из гафния. Резка не тем газом приведет к скорому износу или порче „вставки”.
Для резки в инертной атмосфере (с использованием азота и смеси аргона с водородом) применяются электроды с вольфрамовыми „вставками”. Присутствие кислорода или воздуха в плазменном потоке приведет к износу вольфрама.
3. Низкое давление газа
В инструкции прописаны рабочие величины давления для использования в аппаратах. Низкое давление во время резки приводит к уменьшению потока газа, выгоранию электрода, искрению, ограничению мощности источника питания, плохому качеству резки и т.п. И наоборот, повышение давления не увеличит мощность резки, а уменьшит срок службы. Всегда необходимо придерживаться требований инструкции при работе с аппаратом.
4. Недостаточное количество охлаждающей жидкости в плазмотронах, охлаждаемых жидкостью
В плазмотронах, охлаждаемых жидкостью, используют деионизированную воду или смесь деионизированной воды и чистого этиленгликоля. Корпус горелки имеет как катод, так и анод. Охлаждающая жидкость должна циркулировать между анодом и катодом Электропроводные вещества, в том числе ионизированная вода, могут стать причиной короткого замыкания в электропроводке.
Большинство аппаратов, охлаждаемых жидкостью, имеют предохранитель низкого давления и расхода охлаждающей жидкости. Он предотвращает перегрев плазмотрона в случае неисправности системы охлаждения или низкого расхода. Если вам кажется, что срок службы электрода короче обычного, проверьте значения расхода охлаждающей жидкости.
5. Недостаточно чистые газопроводы
Оборудование для плазменной резки и сварки требует очистки газопроводов после простоя (даже краткосрочного). Если аппарат работает в обстановке высокой влажности, то недостаточно короткой предочистки для устранения всей влаги из газопроводов.
Если электрод плохо зачищен, то влага из газопровода может осесть и испортить электрод.
6. Повреждённый завихритель
Завихритель служит для завихрения плазменного газа вокруг головки электрода, это концентрирует дугу по центру электрода. Если завихритель поврежден, лопнул, расплавился или забился грязью, изменятся направление и количество расходуемого воздуха, что быстро повреждает электрод. Необходима замена завихрителя.
7. Частое зажигание дуги
Большинство источников для плазменной резки и сварки способны зажечь дугу при высоком напряжении. Это главная причина износа электродов. Поэтому дугу надо зажигать непосредственно перед началом резки. Большинство аппаратов поддерживает функцию автоматического снижения напряжения после возникновения дуги. Лучше всего сразу подвести плазмотрон к месту реза, и, после зажигания дуги, как можно скорее начать резку.
Больший срок службы электродов в автоматической или машинной резке достигается за счет программирования на цепную резку всегда, когда это возможно. Благодаря этому можно вырезать несколько деталей, причём дугу потребуется зажечь только один раз.
svarnoy.ru