Формула глубина резания – 211
alexxlab | 27.10.2020 | 0 | Вопросы и ответы
Расчет режимов резания при токарной обработке
I.Определить глубину резания, при обтачивании, если обработка идет за один проход Ø25мм до Ø20мм.
Воспользуемся формулой для определения глубины резания:
где D – диаметр заготовки, d – диаметр детали, i – число проходов.
II. Определить продольной подачу s, при точении.
Исходя из требований, предъявляемых к шероховатости обрабатываемых поверхностей, по справочнику находим подходящую величину подачи s = 0,1-0,3 мм/об.
III. Определить скорость резания v при обработке внешних цилиндрических поверхностей.
Для найденных значений подачи и глубины резания, скорость резания v = 80 м/мин
IV. Расчет числа оборотов шпинделя. Из формулы скорости резания:
где D – наиболее удаленная точка от оси вращения шпинделя, находим число оборотов n
Ближайшее значение n согласно паспортным данным n=1000об/мин
Фрезерная обработка
I.Вычисление ширины и глубины резания при фрезеровании. Воспользуемся формулой для определения глубины резания:
где D – диаметр обрабатываемой поверхности, d – диаметр обработанной поверхности.
II. Расчет скорости фрезерования.
По таблице скоростей фрезерования для инструмента из быстрорежущей стали v=20м/мин
III. Расчет числа оборотов шпинделя. Из формулы скорости резания:
где D – диаметр инструмента, находим число оборотов n
Ближайшее значение n согласно паспортным данным n=1250об/мин
Сверление.
I.Вычисление глубины сверления для отверстия Ø5мм
Воспользуемся формулой для определения глубины резания при сверлении:
где D – диаметр сверла,
II. Определение скорости сверления .
Формула скорости резания при сверлении
2.7 Виды возможного брака и способы его устранения
1. Повышенная шероховатость – настроить подачу и обороты; проверить заточку резца.
2.Неправильные продольные размеры обточенной заготовки – выбрать люфт при пользовании лимбом.
3. Недостаточная точность при фрезеровании закрытого паза – использовать фрезу несколько меньшего диаметра и обрабатывать паз за два прохода
3. Организация рабочего места
Рабочим местом называется участок производственной площади цеха, на котором расположен станок с комплектом приспособлений, вспомогательного и режущего инструмента, технической документации и других предметов и материалов, находящихся непосредственно в распоряжении токаря. Оснащенность рабочего места и организация труда на нем в значительной мере определяют производительность труда токаря. Рабочее место оснащается: одним или несколькими станками с постоянным комплектом принадлежностей; комплектом технологической оснастки постоянного пользования, состоящим из приспособлений, режущего, измерительного и вспомогательного инструмента; комплектом технической документации, постоянно находящейся на рабочем месте; комплектом предметов ухода за станком и рабочим местом; инструментальными шкафами, подставками, планшетами, стеллажами и т. п.; передвижной и переносной тарой для заготовок и изготовленных деталей; подножными решетками, табуретками или стульями. Комплект технологической оснастки и комплект предметов ухода за станком и рабочим местом постоянного пользования устанавливаются в зависимости от характера выполняемых работ, типа станка и принятой схемы инструментального хозяйства в цехе. Количество такой оснастки определяет размеры, внутреннее устройство и число шкафов, тумбочек и стеллажей.
studfiles.net
Определение режимов резания
при основных видах лезвийной обработки
Лабораторная работа №
9Основные понятия
1.1. Режимы резания
При назначении элементов режимов резания учитывают характер обработки, тип и размеры инструмента, материал его режущей части, материал и состояние заготовки, тип и состояние оборудования.
Элементы режима резания обычно устанавливают в следующем порядке:
Глубина резания t: при черновой (предварительной обработке) назначают по возможности максимальную t, равную всему припуску на обработку или большей части его; при чистовой (окончательной) обработке – в зависимости от требований точности размеров и шероховатости обработанной поверхности.
Подача S: при черновой обработке выбирают максимально возможную подачу, исходя из жесткости и прочности системы СПИД, мощности привода станка, прочности твердосплавной пластинки и других ограничивающих факторов; при чистовой обработке – в зависимости от требуемой степени точности и шероховатости обработанной поверхности.
Скорость резания V рассчитывают по эмпирическим формулам, установленным для каждого вида обработки.
Стойкость Т – период работы инструмента до затупления, приводимый для различных видов обработки.
Сила резания. Под силой резания обычно подразумевают ее главную составляющую Рz, определяющую расходуемую на резание мощность Ne и крутящий момент на шпинделе станка. Силовые зависимости рассчитывают по эмпирическим формулам, значения коэффициентов и показателей степени в которых для различных видов обработки приведены в соответствующих таблицах.
1.2. Определение режимов резания при точении
Определим режимы резания для чернового наружного точения цилиндрической поверхности на токарном станке в следующей последовательности:
1.2.1. Определить глубину резания t, мм:
, (9.1)
где D – диаметр заготовки, мм;
d – диаметр детали, мм;
i – число проходов.
1.2.2. Назначить подачу S, мм/об, в зависимости от вида
обработки, режима обработки (черновой, чистовой),
жесткости системы СПИД и др. факторов, согласно
таблицы 9.1 приложения Д.
Выбирают модель токарного станка, на котором будет выполняться точение, и корректируют значение выбранной подачи S по паспортным данным этого станка.
2.2.3. Рассчитать теоретическую скорость резания VД, м/мин, допускаемую режущим инструментом по формуле:
, (9.2)
где Т – стойкость инструмента, при одноинструментальной
обработке принимают в пределах 30÷60 мин;
Сv ,m, х, у – коэффициенты, значения которых определяются
по таблице 9.2 приложения Д.
t – глубина резания, мм;
S – подача, мм/об;
Кv– поправочный коэффициент, который определяется
по формуле:
, (9.3)
где Kmv – коэффициент, учитывающий влияние материала
заготовки, определяется по таблице 9.3
приложения Д ;
Knv – коэффициент, учитывающий состояние поверхности
заготовки:
– для стальной заготовки Knv=0,9;
– для чугунной заготовки Knv=0,8;
Kиv – коэффициент, учитывающий влияние материала
инструмента, определяется по таблице 9.5
приложения Д.
studfiles.net
7.Расчёт режимов резания при механической обработке.
Глубина резания
При черновой обработке глубина резания вычисляется по формуле:
Где Z —припуск;
К — число проходов.
мкм.
При чистовой обработке глубина резания зависит от качества обработанной поверхности и выбирается по таблицам: t = 0.5мм.
Подача.
При черновом точении выбирается по таблицам: S=0.5мм/об
Скорость резания.
При наружном продольном точении скорость резания вычисляется по формуле:
Где :
Т- среднее значение стойкости инструмента;
,
,x,
у,-
коэффициенты , учитывающие качество
материала;
t— глубина резания;
S —подача.
Коэффициент вычисляется
по формуле:
Где
—коэффициент,
учитывающий влияние материала заготовки;
— коэффициент,
учитывающий состояние поверхности ;
Скорость резания при черновом точении.
=мм/мин
Скорость резания при чистовом точении.
=мм/мин
Частота вращения шпинделя вычисляется по формуле
– При черновом точении:
– При чистовом точении:
Сила резания вычисляется по формуле:
Где:
,х
,у, n-
постоянные, которые зависят от расчётных
условий.
Сила резания при черновом точении:
=10*200**0,5
*0,84=1658Н.
Сила резания при чистовом точении:
=10*200*0,3*0,165*1*0,9=122Н.
2.Расчет режимов резания для подрезания фасок.
Подача выбирается из справочника S = 0.1 MM/ОБ
Скорость резания при точении фаски.
м/мин
Сила резания.
Мощность резания
Вт
3.Расчет режимов резания для нарезки резьбы.
Подача:
Продольная (t=1,5 мм)
Поперечная (t=2.5 мм)
Скорость резания при нарезании резьбы вычисляется по формуле:
=1*1,15*0,65=0,78
мм/мин.
Сила резания:
Н
4.Расчёт режимов резания при шлифовании.
Скорость окружности:
-чистовое
шлифование = 35 м/с
Глубина шлифования:
– черновое точение t=0.025 мм
-чистовое точение t=0.013 мм
Продольная подача:
–черновое шлифование S=7мм
–чистовое шлифование S=4мм
Мощность (эффективная) при шлифовании
– черновое шлифование
=5,2 кВт
– чистовое шлифование
=2,9квт
Техническая норма времени.
Расчет основного времени.
Основное время на чистовое точение рассчитывается по формуле:
Где:
-расчетная
длина рабочего хода режущего инструмента;
–
число рабочих ходов режущего инструмента;
-частота
вращения шпинделя ,принятая по паспорту
станка;
–
подача по паспортным данным станка.
Где
–
длина резания;
–
длина подвода режущего
инструмента;
–
длина врезания инструмента;
–
длина перебега режущего инструмента;
-дополнительная
длина хода инструмента, вызванная
особенностями наладки конструкции
обрабатываемых заготовок.
Черновое
точение d= 28*205
мм
Чистовое
точение d= 24*205
мм
Аналогично производится расчет основного времени для каждого точения.
studfiles.net
Формула для расчета скорости резания
На основании изложенного скорость резания, допускаемая резцом, подсчитывается по следующей общей формуле.
С – постоянный коэффициент, характеризующий обрабатываемый материал и условия обработки,
Кv – обобщающий поправочный коэффициент на измененные условия обработки.
.
Методика назначения режимов резания
При назначении режимов резания следует соблюдать следующую последовательность:
1. Выбрать рациональную марку инструментального материала.
2. Выбрать оптимальные геометрические параметры резца.
3. Задаться максимально возможной глубиной резания.
4. По выбранной глубине резания назначают максимальную возможную подачу.
5. Назначают оптимальное значение периода стойкости.
6. Производят расчет допускаемой скорости резания (с учетом поправочных коэффициентов).
7. Корректировка скорости резания по числу оборотов станка. (По паспортным данным станка).
8. Проверка выбранных элементов режимов резания по мощности станка.
9. Подсчет машинного времени обработки.
Конструкции токарных резцов
Токарные резцы являются самым распространенным видом инструментов, применяемых в отрасли.
По направлению подачи резцы делятся на правые и левые.
Основные типы токарных резцов следующие: (рис. 38.)
а) Проходной прямой,
б) проходной отогнутый,
в) проходной упорный,
г) проходной упорный отогнутый,
д) подрезной отогнутый,
е) прорезной (канавочный),
ж) отрезной,
з) расточной для сквозных отверстий,
и) расточной для глухих отверстий.
По форме сечения державки резцы делятся на прямоугольные и круглые.
Круглая форма сечения применяется для расточных резцов и резьбовых резцов для внутренних резьб.
Размеры сечения державки определяют из условия прочности
,
,
кгсмм
– изгибающий момент
(рис. 39.)
W – момент сопротивления, мм3
Рис. 38. Основные типы токарных резцов.
Рис. 39. Схема к расчету державки резца на прочность.
Для прямоугольного сечения
;
обычно Н = 1,6B, тогда
,
мм.
Для державок круглого сечения
,
мм.
Размеры сечений резцов стандартизованы и приведены в соответствующих стандартах. По способу крепления режущих пластин к державке резцы делятся на напайные и механическим креплением. Припаивание твердосплавных пластин осуществляется на установках ТВЧ. В качестве припоя служит медь, латунь или специальные сплавы. В качестве флюса используется техническая бура или специальные флюсы, например: Ф100. (рис. 40.).
Для твердосплавных напайных резцов рекомендуются следующие формы передней поверхности. (рис. 41.)
а) = – 3-5°; f = 0,2-0,5 мм.
б) Для обработки пластичных материалов с в 80 кгс/мм2 с s < 0,3 мм/об; l =2-2,5 мм; R 2l.
в) Для обработки пластинных хрупких материалов при прерывистом резании.
г) Для обработки хрупких материалов и пластичных материалов с в 80 кгс/мм2 при чистовых режимах работы.
д) Для обработки пластичных материалов с в > 80 кгс/мм2 и для работы в условиях прерывистого резания. Формы твердосплавных режущих пластин для напайных инструментов определены ГОСТ 2209-69.
Припаивание пластин к державкам и последующие охлаждения и заточка инструментов зачастую приводит к образованию трещин в плаcтинах. Этих недостатков лишены инструменты с механическим
Рис. 40. Крепление режущих пластин припаиванием.
Рис. 41. Формы передней поверхности твердосплавных резцов.
креплением многогранных неперетачиваемых пластин (МНТ).
В зависимости от способа крепления пластины бывают без отверстия и с отверстием.
Формы режущих пластин определены ГОСТ 19042 – 80, – ГОСТ 19086 – 80. Формы пластин из сплавов МС регламентированы ТУ – 48 – 19 – 307 – 80.
Основные схемы механического крепления пластинок следующие (Рис. 42).
а) Прижим пластин к опорной плоскости со стороны передней поверхности (для пластин без отверстия).
б) Прижим пластины через отверстие к боковым (упорным) поверхностям.
в) Одновременный прижим пластины к опорной и боковым поверхностям.
Наиболее распространены следующие формы пластин: (Рис. 43).
Формы пластин характеризуются следующими размерами:
D – Диаметр вписанной окружности,
l – длина режущей кромки,
R – радиус закругления переходного лезвия,
S – толщина пластины.
В зависимости от точности основных размеров пластин различают четыре степени точности:
1. Нормальная (U) – шлифованные по ленточке и опорным поверхностям.
2. Повышенная степень точности (М), то же, что и U , но с более жесткими допусками.
3, Высокая степень точности (G ) – шлифованные по опорным и боковым поверхностям.
4. Особо высокая степень точности (С) то же, что G, но с более жесткими допусками.
Рис. 42. Схемы механического крепления режущих пластинок
Рис. 43. Основные формы многогранных неперетачиваемых пластин
Рис. 44. Схема построения обозначений режущих неперетачиваемых пластин
Обозначаются пластины следующим образом: (Рис. 44).
Важным конструктивным элементом резцов являются опорные пластины, которые служат для увеличения срока службы державки резца. Опорные пластины изготавливают из твердых сплавов группы ВК (BKI5) или закаленных сталей и предохраняют державку в случае поломки режущей пластины.
Дробление стружки при точении
В последнее время в массовом производстве большое значение приобретают вопросы дробления стружки. Дробление стружки являются необходимым требованием, предъявляемым к работе автоматических линий. Дело в том, что сливная путаная стружка затрудняет процесс автоматизации, может ухудшать шероховатость обработанной поверхности и вызывать случайные поломки инструментов. С другой стороны дробленая стружка более компактная и транспортабельная, что весьма важно при удалении стружки из цехов и при перевозке ее на переплавку.
При выполнении токарных операций дробление стружки можно достигнуть следующими способами:
1. Кинематическое дробление. Этот способ заключается в том, что на движение подачи накладывается осциллирующее движение с определенной частотой и амплитудой. Частота колебания будет определять размеры стружки. В результате этого стружка будет иметь различную толщину, что вызовет ее, разрушение в более тонком месте. Такой способ в отрасли реализуется на ПЦО при отрезании прибыли (Рис. 45).
2. Накладные стружколомы. При точении резцами с плоской передней поверхностью применяют накладные стружколомы. Накладные стружколомы стандартизованы, изготавливаются централизованно, как и режущие пластины. Материалом служит твердый сплав марки ВК8. Изменяя расстояние l, можно добиться получения стружки требуемой формы и размеров (Рис. 46).
Рис. 45. Метод кинематического дробления стружки
Рис. 46. Дробление стружки при точении при помощи накладных стружколомов
Недостатком этого метода является то, что для каждого конкретного случая режима резания и обрабатываемого материала необходимо подбирать расстояние l опытным путем. С уменьшением l эффект дробления стружки увеличивается.
3. Заточка лунок, канавок и уступов на передней поверхности.
Этим способом пользуются при работе с напайными резцами с плоскими МНП. Подбором величины размеров l, τ, f, h, R (Рис. 47) добиваются получения необходимой формы стружки. Недостатком этого метода является трудоемкость заточки. Большое влияние на дробление оказывает размер фаски f , которое улучшается с его уменьшением.
4. МНП со сложным профилем передней поверхности. Этот способ является универсальным и наиболее перспективным в настоящее время. На передней поверхности пластин методом прессования получают двойные и тройные канавки, размеры которых обеспечивают дробление стружки в широком диапазоне изменения глубины резания и подачи. Геометрические параметры таких пластин регламентированы ТУ – 48 – 19 – 308 – 80, (Рис. 47). Увеличение подачи и главного угла в плане приводит к увеличению толщины срезаемого слоя, что усиливает эффект дробления стружки.
Фасонные резцы
Фасонные резцы имеют режущие кромки, соответствующие профилю обрабатываемой детали. Обработка такими резцами производительна и точна. Однако, фасонные резцы трудоемки в изготовлении, поэтому их применение оправдано в массовом производстве.
В зависимости от конструкции различают призматические и круглые резцы.
Стойкость призматических резцов выше, их крепление жестче. Круглые резцы проще в приготовлении и допускают большее число переточек.
Проектирование фасонных резцов заключается з следующем:
Рис. 47. Заточка стружколомающих канавок (I) и лунок (II) на режущих пластинах
Рис. 48. Многогранные режущие пластины с двойными стружколомающими канавками, полученные методом прессования
1. Назначают передний γ и задний α углы резца. Для круглых резцов α = 10 – 15°, для призматических α = 12 – 17°. Передний угол γ выбирается в зависимости от обрабатываемого материала (γ =0 – 30°).
Размеры резцов принимают из достижения прочности и жесткости по нормалям.
Задние углы у ревущих кромок, обрабатывающих наклонные участки профиля детали, уменьшаются в зависимости от угла наклона. Задний угол на этих участках не должен быть < 2°.
При установке круглого резца на станок при заточке необходимо выдержать размер h между осями детали и резца (Рис. 47).
Размер H, называемый смещением передней поверхности резца относительно оси, определяется:
Размер
Профили фасонного резца и детали отличаются. Глубина профиля резца определяется в сечении, перпендикулярном к задним поверхностям (в технологической плоскости).
tp – у призматического резца,
tp׀ – у дискового резца.
Размеры профиля резца по ширине (вдоль оси), как правило, совпадает с размерами детали и расчету не подлежат.
Сначала определяют профиль резца в плоскости передней поверхности. Затем определяют профиль резца в сечении, перпендикулярном к задней поверхности для призматических резцов и в осевой плоскости дискового резца. Полученные размеры профиля округляют до 0,01 мм. Допуск на профиль резца принимают равным 0,3…0,4 от допуска на профиль детали.
Заточка фасонных резцов осуществляется только по передней
Рис. 49. Схема расчета профиля фасонных резцов
поверхности (Рис. 50).
Фасонные резцы имеют достаточно широкое применение в отрасли. Так, для профилирования МВП применяются призматические фасонные резцы.
При обработке ряда деталей на многошпиндельных горизонтальных полуавтоматах часто применяют фасонные круглые (дисковые) резцы, устанавливаемые на поперечник суппорта этих станков.
Рис. 50. Схема заточки фасонных резцов
studfiles.net
Элементы режима резания
Элементы режима резания
Режимом резания называется совокупность элементов, определяющих условия протекания процесса резания.
К элементам режима резания относятся – глубина резания, подача, период стойкости режущего инструмента, скорость резания, частота вращения шпинделя, сила и мощность резания.
При проектировании технологических процессов механической обработки или режущих инструментов возникает необходимость в определении и назначении элементов режима резания. Отечественная практика механической обработки накопила огромный нормативно – справочный материал, с помощью которого можно назначить любой режим резания для любого вида механической обработки. Однако, табличный метод назначения режимов резания является весьма громоздким, так как требует анализа большого количества справочной информации. Более того, все режимные параметры взаимосвязаны и при изменении хотя бы одного из них автоматически изменяются и другие, что еще более усложняет процесс назначения режимов резания.
Аналитический (расчетный) метод определения режима резания менее трудоёмок и более предпочтителен при учебном проектировании технологических процессов механической обработки резанием. Он сводится к определению, по эмпирическим формулам, скорости, сил и мощности резания по выбранным значениям глубины резания и подачи.
Для проведения расчетов необходимо иметь паспортные данные выбранного станка, а именно – значения подач и частот вращения шпинделя, мощности электродвигателя главного движения. При отсутствии паспортных данных расчет выполняется приблизительно, в проделах тех подач и частот вращения шпинделя, которые указаны в справочной литературе.
Выбор режущего инструмента
Его следует начинать с анализа шероховатости поверхностей детали, которая задана на чертеже. В зависимости от параметра шероховатости выбирается метод обработки данной поверхности, которому соответствует свой специфический режущий инструмент. В табл. 1 приведена зависимость шероховатости поверхности от различных методов обработки.
Немаловажное значение для расчета режимов резания имеет выбор материала инструмента. При его выборе следует руководствоваться рекомендациями табл. 2. Для тонких (отделочных) методов обработки материалов с высокими скоростями резания (свыше 500 м/мин) рекомендуется применение сверхтвердых инструментальных материалов.
Наиболее распространенными среди них являются материалы, полученные на основе кубического нитрида бора.
Выбор и назначение глубины резания
Рис. 1.Схема к определению глубины резания при точении
Глубиной резания называется расстояние между обрабатываемой и обработанной поверхностями, измеренное по нормали к последней.
При черновых методах обработки назначают по возможности максимальную глубину резанияt, равную всему припуску или большей части его. При чистовом резании припуск срезается за два прохода и более. На каждом следующем проходе следует назначать меньшую глубину резания, чем на предшествующем. Глубину последнего прохода назначают в зависимости от требований точности и шероховатости обработанной поверхности.
В данной работе рекомендуются следующие глубины резания t, мм:
черновая обработка t >2;
получистовая и чистовая обработка t = 2,0 – 0,5;
отделочная обработка (3,2 мкм і Ra > 0,8 мкм) t = 0,5 – 0,1.
При сверлении глубина резания t=0,5·D, при рассверливании, зенкеровании и развертывании t=0,5·(D-d) мм, где
D – диаметр осевого инструмента,
d – диаметр предварительно полученного отверстия, мм.
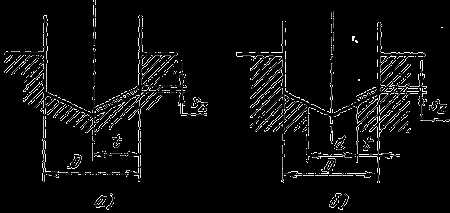
Рис. 2.Схемы для определения глубины резания при сверлении (а) и рассверливании (б) отверстий.
При отрезании, точении канавок и фасонном точении глубина резания приравнивается длине лезвия резца (см. рис. 3).
Рис. 3. Схема к определению глубины резания при отрезании
Выбор величины подачи
Подачей называется путь, пройденный какой-либо точкой режущей кромки инструмента, относительно заготовки, за один оборот заготовки (режущего инструмента), либо за один двойной ход режущего инструмента.
Различают подачу на один зуб Sz, подачу на один оборот S и подачу минутную Sм, мм/мин, которые находятся в следующей зависимости:
(1)
где: – частота вращения режущего инструмента, мин-1;
– число зубьев режущего инструмента.
При черновой обработке выбирают максимально возможную подачу, исходя из жесткости и прочности системы, мощности привода станка, периода стойкости режущего инструмента и других ограничивающих факторов. При чистовой обработке – в зависимости от требуемого параметра шероховатости обработанной поверхности.
При черновом точении выполняется вариантный расчёт режимов резания для нескольких значений подач в диапазоне, ограниченном чистовой (табл. 3) и максимальной подачей, допустимой прочностью режущей пластины (табл. 4).
При обработке отверстий осевым режущим инструментом выбирают рекомендуемую подачу, допустимую по прочности инструмента (табл.5).
Исходной величиной подачи при фрезеровании является подача Sz – на зуб. Рекомендуемые подачи для чистового фрезерования приведены в табл. 6.
В учебных целях рекомендуется значения подач выбирать из наиболее распространённого диапазона: 0,05- 0,5 мм/об.
Меньшие значения назначать для чистовой обработки, большие – для черновой.
Выбор значения периода стойкости
Периодом стойкости (стойкостью) режущего инструмента называется время его непрерывной работы между двумя смежными переточками.
Выбор значения периода стойкости режущего инструмента рекомендуется сделать из следующего ряда:
15;30;45;60;90;120 мин.
Меньшие значения периода стойкости следует назначать для мелких инструментов.
Расчёт режимов резания при сверлении, рассверливании, зенкеровании и развёртывании
Расчёт режимов резания при резьбонарезании
Расчёт режима резания при шлифовании
Расчёт режимов резания при строгании и долблении
Расчёт режимов резания при фрезеровании
osntm.ru
Режимы резания при токарной обработке: расчет, таблица
Точение – один из многофункциональных методов обработки деталей разного типа. Он используется для чистовой и черновой работы с изделиями в процессе выполнения их ремонта или изготовления. Внимательный подход к подбору режимов резанья обеспечивает существенное повышение продуктивности данного процесса.
Что это такое
Под режимом резания чаще всего подразумевают характеристики, которые находят расчетным путем. Это глубина, скорость и подача. Данные величины являются очень важными. Без них качественно выточить любую деталь просто невозможно.
При расчете режимов работы учитывают и другие характеристики производимых рабочих манипуляций:
- допустимые припуски;
- вес заготовок;
- частота вращения шпинделя станка.
При необходимости учитываются много других характеристик тех элементов, которые влияют на процесс обработки деталей.
Характеристика режимов работы
Расчет операции резания выполняется с использованием специальных справочных и нормативных документов, которых на данный момент существует немало. Необходимо тщательно изучить представленные таблицы и выбрать в них подходящие значения. Правильно выполненный расчет гарантирует высокую эффективность применяемого режима обработки детали и обеспечивает достижение лучшего результата.
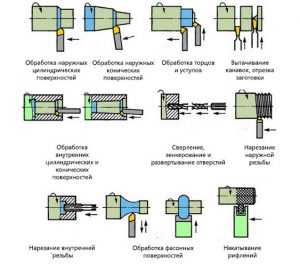
Основные виды токарных работ по металлу
Но такой метод расчета является не всегда удачным, особенно в условиях производства, когда нецелесообразно тратить много времени на изучение таблиц с огромным числом значений. Установлено, что все величины режимов резания взаимосвязаны между собой. Если изменить одно значение, закономерно, что все остальные характеристики обработки станут иными.
Поэтому очень часто специалисты предпочитают применять расчетную или аналитическую методику определения режимов резания. Используются специальные эмпирические формулы, при помощи которых определяются все необходимые нормы. Чтобы расчеты по данной методике были абсолютно точными, необходимо знать следующие параметры токарного станка:
- частота вращения шпинделя;
- величины подач;
- мощность.
На современных производствах для выполнения подобных расчетов используют специальное программное обеспечение. Специалисту достаточно ввести известные данные, после чего компьютер выдаст вычисляемые величины. Применение программ для расчетов существенно облегчает работу специалистов и делает производство более эффективным.
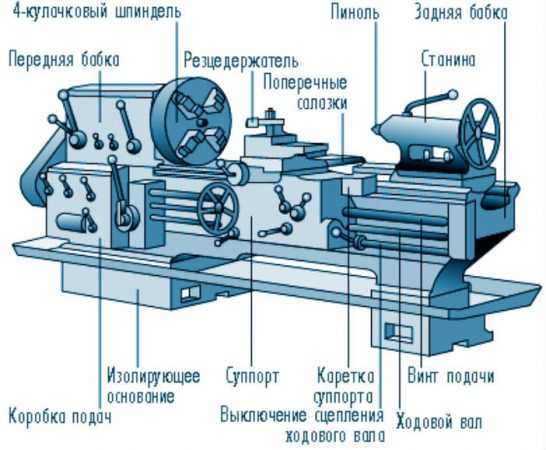
Устройство токарного станка
Схема расчетов
Перед выполнением расчетов операции резания необходимо определить, какой тип режущего инструмента будет использоваться в данном случае. При токарной или абразивной обработке хрупких материалов выбирают оснащение с минимальными показателями. Следует не забывать, что во время работы деталь обычно довольно сильно нагревается. Если скорость обработки будет очень высокая, она может деформироваться, что приведет к ее непригодности.
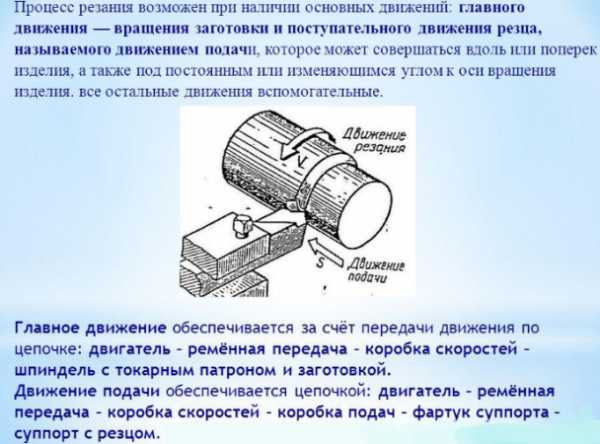
Процесс резания металла
Обязательно учитывается, какая обработка будет осуществляться – чистовая или черновая. В первом случае подбирают рабочие параметры, которые обеспечат максимальную точность. Специалисты обращают внимание и на толщину срезаемого слоя. В зависимости от данной характеристики выбирается количество проходок для выполнения обрезки на специальном оборудовании.
Глубина
Глубина является одним из важнейших параметров для обеспечения качества изготовленных заготовок. Она определяет толщину срезаемого слоя за одну проходку. При выполнении подрезки торца за глубину принимают диаметр детали.
Учитывается количество проходов, что определяется припусками на обработку:
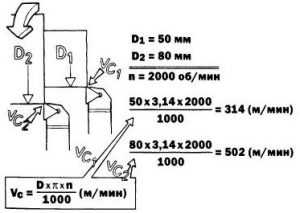
Изменение обрабатываемого диаметра
- 60% на черновую;
- 20–30% на получистовую;
- 10–20% на чистовую.
Для определения глубины обрезки цилиндрических заготовок используется следующая формула:
k=(D-d)/2, где к – глубина обрезки, D – первоначальный диаметр, d – получаемый диаметр.
При определении режимов резания при работе с плоскими деталями вместо диаметров используют длину. Принято считать, что при черновой обработке глубина должна составлять больше 2 мм, получистовой – 1–2 мм, чистовой – меньше 1 мм. Данный параметр зависит от требований к качеству деталей. Чем меньше класс точности, тем больше проходов необходимо выполнить для достижения необходимых свойств изделий.
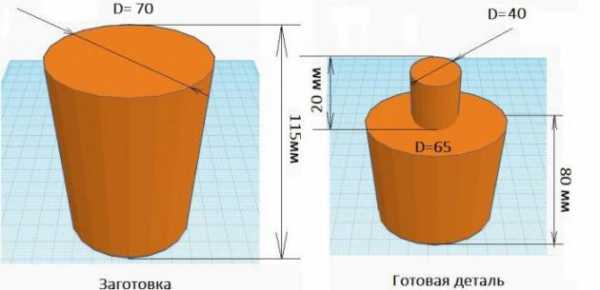
Схема черновой обработки металла
Подача
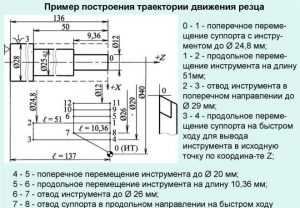
Пример построения траектории движения резца
Под подачей подразумевают величину перемещения резца за один оборот заготовки. При выполнении черновой обработки данный параметр может иметь максимально возможные значения. На завершительном этапе работ значение подачи определяется с учетом квалитета шероховатости. Данная характеристика зависит от глубины обрезки и габаритов заготовки. Чем меньше размеры, тем она ниже. При большой толщине срезаемого слоя выбираются минимальные параметры подачи.
Чтобы облегчить работу специалистам, разработаны специальные таблицы. Там указаны значения подачи при разных условиях режима резанья. Для выполнения точных расчетов иногда необходимо знать размер державки резца.
Если резанье выполняется с существенными ударными нагрузками, значения с таблицы необходимо умножать на коэффициент 0,85. При работе с жаропрочной конструкционной сталью подача не должна быть больше 1 мм/об.
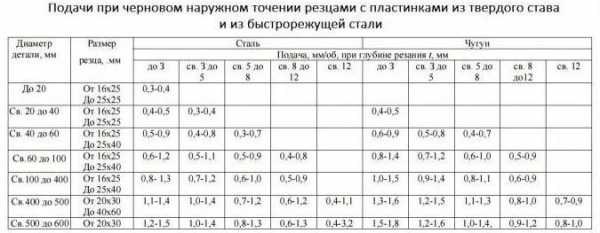
Подачи при черновом наружном точении
Скорость
Скорость резания – это один из важнейших показателей, который определяется на этапе расчетов перед выполнением основных работ. Ее значения зависят от проводимых операций. Обычно отрезание торцов происходит при максимально возможной скорости. Сверление или точение имеют совсем иные требования к данному рабочему параметру. Поэтому для качественного выполнения поставленных задач необходимо знать следующее:
Таблица для расчета режимов резания
- тип выполняемой слесарной операции;
- вид применяемого токарного инструмента;
- материал, из которого изготовлена заготовка.
При традиционной токарной обработке скорость определяется путем умножения диаметра заготовки на количество ее оборотов за минуту и на π. Полученное значение необходимо разделить на 1000. Также скорость резанья можно определить, используя стандартные таблицы для режимов резанья.
Проверка выбранных рабочих характеристик
Когда глубина, подача и скорость определены, их необходимо проверить. Полученные рабочие параметры не должны быть больше нормативных значений, которые указаны в паспорте эксплуатируемого токарного станка.
Обязательно необходимо определить мощность оборудования. Для этого силу обрезки умножают на ее скорость и делят на 1000. Полученное значение сравнивают с тем, что указано в паспорте станка. Если рассчитанные по формулам параметры больше, необходимо корректировать глубину, подачу и скорость, чтобы избежать повреждения оборудования и инструментов.
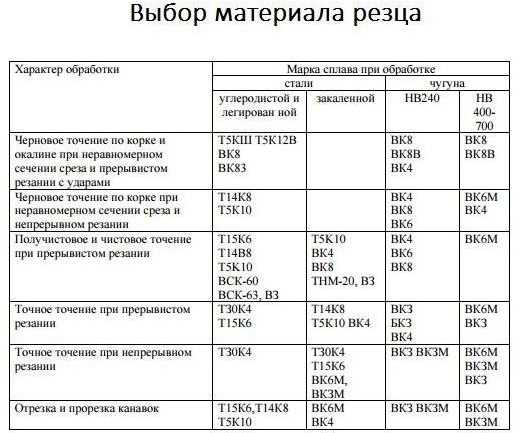
Выбор материала резца при токарной обработке
Какой режущий инструмент использовать
Изготовление деталей на подобных станках осуществляется при помощи специальных токарных резцов. Они должны обеспечивать следующее:
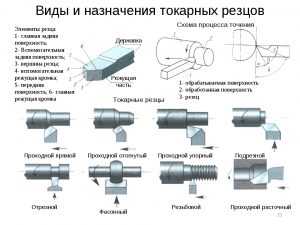
Виды и назначения токарных резцов
- качественную обработку деталей с получением нужной формы и размеров;
- достижение высокого качества обрабатываемой поверхности;
- высокую производительность при минимальных энергетических затратах;
- технологичность в изготовлении;
- ремонтоспособность;
- минимальный расход дорогих материалов для их изготовления.
Токарные резцы классифицируют по разным параметрам. По виду производимых работ они могут быть отрезными, проходными, фасонными, подрезными и т. д. Резцы изготовляются из различных материалов – алмазов, вольфрама, титан-вольфрама и других. В зависимости от конструктивного исполнения данные инструменты бывают цельными, сборными и комбинированными.
Выбор конкретного типа инструмента осуществляется с учетом режимов проводимых рабочих операций, твердости заготовки, геометрических параметров режущей части и других характеристик.
Видео по теме: Токарная обработка металла
vtorexpo.ru
Скорость резания определяется по формуле
1) F = t · s;
2) F = t · ;
3) F = · s;
4) F = D · S;
5) F = . D.
6. Скорость резания определяется по формуле:
1) = ;
2) = ;
3) = πD п ·1000;
4) = πRп;
5) = πD п.
7. Данная формула υ = , м/мин определяет :
1) скорость резания;
2) подачу;
3) глубину резания;
4) машинное время;
5) момент резания.
8. Глубина фрезерования – это толщина слоя материала, снимаемого с заготовки:
1) за один проход фрезы;
2) за два прохода фрезы;
3) за три прохода фрезы;
4) за четыре прохода фрезы;
5) за пять проходов фрезы.
9. По какой формуле находится глубина резания?
1. .
2. .
3. .
4. .
5. .
10. Как понизить скорость резания?
1. Переточить резец.
2. Уменьшить частоту вращения шпинделя.
3. Устранить вибрацию.
4. Уменьшить вылет резца.
5. Уменьшить вылет пиноли.
11. Режимы резания – это:
1) скорость подачи, глубина резания;
2) глубина подачи, величина резания, скорость резания;
3) скорость резания, величина подачи, глубина резания;
4) частота вращения шпинделя, скорость резания;
5) чистота обработки, глубина резания.
12. Формула машинного времени:
1) t = ;
2) = ;
3) T0 = ;
4) n = ;
5) F = t . s.
13. Частота вращения шпинделя токарно-винторезного станка вычисляется по формуле:
1) n = ;
2) n = t;
3) n = ;
4) n = ;
5) n = .
14 Для чернового прохода глубину резания обычно принимают:
1) 0,2 – 0,3 мм;
2) 0,3 – 0,4 мм;
3) 0,4- 0,5 мм;
4) 1,5- 2 мм;
5) 4 – 6 мм.
15. Для получистового прохода глубину резания обычно принимают:
1) 0,2 – 0,3 мм;
2) 2- 4 мм;
3) 0,4- 0,5 мм;
4) 1,5- 2 мм;
5) 4 – 6 мм.
16. Для чистового прохода глубину резания обычно принимают:
1) 0,2 – 0,3 мм;
2) 0,3 – 0,4 мм;
3) 0,4- 0,5 мм;
4) 0,5- 2 мм;
5) 4 – 6 мм.
17. Для черновых проходов принимают подачу:
1) 0,5 – 1,2 мм/об;
2) 0,3 – 0,4 мм/об;
3) 0,4- 0,5 мм/об;
4) 1,5- 2 мм/об;
5) 4 – 6 мм/об.
18. Для чистовых проходов принимают подачу:
1) 0,5 – 1,2 мм/об;
2) 0,08 – 0,4 мм/об;
3) 0,4- 0,5 мм/об;
4) 1,5- 2 мм/об;
5) 4 – 6 мм/об.
19. Глубокими называются отверстия, длина которых превышает диаметр в:
1) 2 раза;
2) 3 раза;
3) 4 раза;
4) 4,5 раза;
5) 5 и более.
20. Подача при сверлении – это путь сверла в мм за:
1) 0,5 оборот заготовки;
2) 1 оборот заготовки;
3) 2 оборота заготовки;
4) 3 оборота заготовки;
5) 4 оборот заготовки.
21. Глубиной резания при сверлении является:
1) t = мм;
2) t = 3 мм;
3) t = – мм;
4) t = мм;
5) t = D – d мм.
Тема 4. Виды и назначение токарных резцов
1. Основной режущий инструмент, применяемый при обработке заготовок на
токарно-винторезных станках, называется:
1) сверло;
2) метчик;
3) резец;
4) фреза;
5) зенкер.
2. Обтачивание наружных цилиндрических поверхностей производится:
1) проходным упорным резцом;
2) проходными резцами;
3) подрезными резцами;
4) отрезными резцами;
5) фасонными резцами.
3. Подрезные резцы применяют для:
1) обработки наружных поверхностей;
2) обработки уступов;
3) обработки торцов;
4) отрезания заготовок;
5) обработки внутренних поверхностей.
4. Токарные резцы по конструкции головки бывают:
1) прямые, отогнутые;
2) только правые;
3) составные;
4) только подрезные;
5) только прямые.
5. Отрезание заготовок осуществляется с помощью:
1) подрезных резцов;
2) упорных резцов;
3) проходных резцов;
4) отрезных резцов;
5) фасонных резцов.
6. Какие резцы применяют при обработке заготовки малой жесткостью на проход?
1. Все типы резцов.
2. Проходные, упорные.
3. Отрезные.
4. Подрезные.
5. Алмазные.
7. Какие резцы применяют при черновом точении труднообработаемых металлов и сплавов?
1.Быстрорежущие.
2.Твердосплавные.
3.Минералокерамические.
4.Алмазные.
Тема 5. Части и элементы резца. Геометрия токарного резца
1. Угол между передней поверхностью и плоскостью, перпендикулярной плоскости резания и проходящей через главную режущую кромку называется:
1) угол при вершине ε;
2) угол заострения ;
3) угол резания ;
4) передний угол ;
5) задний угол .
2. Угол между главной задней поверхностью резца и плоскостью резания называется:
1) угол резания;
2) вспомогательный угол в плане φ;
3) главный угол в плане φ;
4) главный задний угол λ;
5) угол при вершине ε.
3. Кромка, образованная пересечением передней и главной задней поверхностями называется:
1) вспомогательной режущей кромкой;
2) главной режущей кромкой;
3) вспомогательной задней поверхностью;
4) главной задней поверхностью;
5) передняя поверхность.
4. Величина угла резания обозначается буквой:
1) ; 2) ; 3) ; 4) ; 5) .
5. Вспомогательный угол в плане 1 обычно принимают:
1) 5-10 градусов;
2) 12-14 градусов;
3) 15-20 градусов;
4) 20-25 градусов;
5) 25-30 градусов.
6. Рабочей частью резца называется:
1) острие;
2) головка;
3) упор;
4) торец;
5) тело.
7. Как называется угол, образованный проекцией главной режущей кромки на
основную плоскость и направлением подачи?
1. Угол при вершине ε.
2. Главный задний угол .
3. Передний угол .
4. Главный угол в плане .
5. Вспомогательный угол в плане 1.
8. Как называется линия пересечения передней и главной задней поверхностью у проходного резца?
1. Вершина резца.
2. Главная режущая кромка.
3. Задние поверхности.
4. Передняя поверхность.
5. Режущая вершина резца.
9. Угол между главной задней поверхностью резца и плоскостью резания составляет:
1) 50 – 100;
2) 60 – 120;
3) 100 – 200;
4) 120 – 300;
5) 320.
10. При токарной обработке главным движением является:
1) Вращение резца;
2) Вращение заготовки;
3) Поступательное движение резца;
4) Поступательное движение заготовки;
11. Как называется линия пересечения передней и главной задней поверхностей?
1. Вершина резца.
2. Главная режущая кромка.
3. Задние поверхности.
4. Передняя поверхность.
5. Режущая вершина резца.
12. Как называется плоскость, параллельная продольной и поперечной подачам?
1. Плоскость резания.
2. Поверхность резания.
3. Основной плоскостью.
4. Обрабатываемая поверхность.
5. Обработанная поверхность.
13. Поверхность, с которой срезается материал, называется:
1) обрабатываемой;
2) обработанной;
3) поверхность резания;
4) срезанная поверхность;
5) готовая поверхность.
14. Поступательное движение резца, обеспечивающее срезание материала
по спирали это:
1) главное движение;
2) движение подачи;
3) точение;
4) вспомогательное движение;
5) движение по спирали.
15. Поверхность, проходящая через главную режущую кромку инструмента и
касательная к поверхности резания, называется:
1) поверхность резания;
2) поверхность точения;
3) поверхность обработанная;
4) поверхность необработанная;
5) основная поверхность.
16. Для осуществления процесса резания необходимы движения:
1) главное и вспомогательное;
2) вспомогательное и поступательное;
3) главное;
4) движения подачи;
5) движение по спирали.
17. Необходимые движения для осуществления процесса резания:
1) главное и вспомогательное;
2) вертикальное и горизонтальное;
3) главное и вертикальное;
4) радиальное и осевое;
5) вертикальное и вспомогательное.
18. Главный угол в плане для проходных упорных резцов:
1) 400;
2) 500;
3) 550;
4) 600;
5) 900.
Тема 6. Сверление и нарезание резьбы на токарно-винторезном станке
1. Шаг нарезаемой резьбы на станка модели ТВ-6, мм:
1) 0,8; 1; 1,25;
2) 1,5; 2; 2,5;
3) 1,5; 2;
4) 2; 2,5; 3;
5) 1,5; 3.
2. Как устранить смещение центров шпинделя и задней бабки?
1. Зацентровать заготовку.
2. Отрегулировать зазор в подшипнике.
3. Выставить заднюю бабку на соосность.
4. Устранить люфт пиноли.
5. Устранить люфт шпинделя.
3. Каким должен быть диаметр стержня, если диаметр резьбы 8 мм?
1. 7 мм;
2. 7,2 мм;
3. 7,5 мм;
4. 7,8 мм;
5. 8 мм.
4. Для нарезания метрических резьб угол профиля должен составлять:
1) 400;
2) 500;
3) 600;
4) 700;
5) 750.
5. Для нарезания дюймовой и трубной резьбы угол профиля должен составлять:
1) 400;
2) 500;
3) 550;
4) 600;
5) 650.
6. Глубокими называются отверстия, длина которых превышает диаметр в:
1) 2 раза;
2) 3 раза;
3) 4 раза;
4) 4,5 раз;
5) 5 и более раз.
7. Подача при сверлении – это путь сверла за:
1) 0,5 оборот заготовки;
2) 1 оборот заготовки;
3) 2 оборота заготовки;
4) 3 оборота заготовки;
5) 4 оборот заготовки.
8. Глубиной резания при сверлении является:
1) t = мм;
2) t = 3 мм;
3) t = – мм;
4) t = мм;
5) t = D – d мм.
9. Каким должен быть диаметр отверстия для нарезания резьб по стали, если резьба М 8 мм?
1) 5,0;
2) 5,5;
3) 6,0;
4) 6,5;
5) 6,7.
10. Каким должен быть диаметр стержня, если резьба М 8х1,25
1) 7 мм;
2) 7,2 мм;
3) 7,5 мм;
4) 7,9 мм;
5) 8 мм.
11. Метрическая резьба имеет профиль равностороннего треугольника с углом при вершине:
1) 200;
2) 300;
3) 400;
4) 500;
5) 600.
12. Дюймовая резьба имеет профиль равнобедренного треугольника с углом при
вершине:
1) 200;
2) 300;
3) 400;
4) 500;
5) 550.
13. Метчики диаметром до 20 мм обычно изготавливают с:
1) 2-я канавками;
2) 3-я канавками;
3) 4-я канавками;
4) 5-и канавок;
5) 6-и канавок.
15. Метчики диаметром от 20 до 40 мм обычно изготавливают с:
1) 2-я канавками;
2) 3-я канавками;
3) 4-я канавками;
4) 5-и канавок;
5) 6-и канавок.
16. Цельные плашки применяют при нарезании резьбы диаметром до:
1) 10мм;
2) 20мм;
3) 30мм;
4) 45мм;
5) 52мм.
17. Ручные (слесарные) метчики выполняют обычно в комплекте из:
1) 2-х штук;
2) 3-х штук;
3) 4-х штук;
4) 5-ти штук;
5) 6-ти штук.
3.3. Механическая обработка металлов (3 курс)
Тема 1. Горизонтально- фрезерный станок. Техническая характеристика станка модели НГФ-110 Ш4
1. Фрезерные станки относятся к группе металлорежущих станков:
1) 1-й;
2) 3-й;
3) 4-й;
4) 5-й;
5) 6-й.
2. Частота вращения шпинделя станка модели НГФ-110 Ш4:
1) 100-120 об/мин;
2) 125 об/мин;
3) 1000 об/мин;
4) 1250 об/мин;
5) 125…1250 об/мин.
3. Число ступеней частот вращения шпинделя станка модели НГФ-110 Ш4:
1) 2;
2) 3;
3) 4;
4) 5;
5) 6.
4. Внутренний конус шпинделя станка модели НГФ-110 Ш4:
1) Морзе 3;
2) Морзе 4;
3) Морзе 5;
4) Морзе 6;
5) Морзе 7.
5. Ширина фрезы, устанавливаемый на станке не более:
1) 110мм;
2) 115мм;
3) 120мм;
4) 125мм;
5) 130мм.
6. Размер рабочей поверхности стола станка модели НГФ-110 Ш4:
1) 25х50мм;
2) 50х100мм;
3) 200х100мм;
4) 400х100мм;
5) 500х100мм.
7. Расстояние от оси шпинделя до стола (мм) :
1) 10…100;
2) 20…150;
3) 30…200;
4) 40…250;
5) 50…300.
8. Перемещение стола продольное (мм):
1) 85;
2) 170;
3) 250;
4) 300;
5) 350.
9. Перемещение стола поперечное (мм):
1) 85;
2) 170;
3) 250;
4) 300;
5) 350.
10. Перемещение стола вертикальное (мм):
1) 85;
2) 170;
3) 250;
4) 300;
5) 350.
11. Цена одного деления лимба продольной и поперечной подачи (мм):
1) 0,1;
2) 0,025;
3) 0,05;
4) 1.25;
5) 1,75.
12. Цена одного деления лимба вертикальной подачи (мм):
1) 0,1;
2) 0,025;
3) 0,05;
4) 1.25;
5) 1,75.
13. Размер станка НГФ-110 Ш4 (мм):
1) 300х400х500;
2) 500х600х700;
3) 685х640х925;
4) 700х800х900;
5) 1000х1400х1800.
14. Термин «фреза» происхождения:
1) английского;
2) немецкого;
3) греческого;
4) русского;
5) французского.
Тема 2. Основные фрезерные операции. Режим резания при фрезеровании
1. Глубина фрезерования – это толщина слоя материала, снимаемого с заготовки:
1) за один проход фрезы;
2) за два прохода фрезы;
3) за три прохода фрезы;
4) за четыре прохода фрезы;
5) за пять проходов фрезы.
2. Назовите допустимые диаметры фрез от ширины стола станка?
t – ширина стола, d – диаметр
1.
Ширина стола (t) | 160 | 250 | 320 |
Диаметр (d) | 50 – 100 | 80 – 160 | 100 – 200 |
2.
Ширина стола (t) | 160 | 250 | 320 |
Диаметр (d) | 50 – 80 | 80 – 100 | 100 – 200 |
3.
Ширина стола (t) | 160 | 250 | 320 |
Диаметр (d) | 50 – 80 | 100 – 150 | 150 – 200 |
4.
Ширина стола (t) | 160 | 250 | 320 |
Диаметр (d) | 50 – 60 | 60 – 80 | 80 – 100 |
5.
Ширина стола (t) | 160 | 250 | 320 |
Диаметр (d) | 50 – 80 | 80 – 100 | 100 – 120 |
3. Слой металла, который снимается в процессе фрезерования, определяется:
1) шириной;
2) длиной;
3) высотой;
4) глубиной;
5) шириной и глубиной фрезерования.
4. Ширина фрезерования измеряется обработанной за один проход фрезы
поверхности:
1) шириной;
2) длиной;
3) высотой;
4) глубиной;
5) шириной и глубиной фрезерования.
5. Скорость резания при фрезеровании определяется по формуле:
1) = ;
2) = ;
3) = πD п ·100;
4) = πRп;
5) = πD п.
6. Частота вращения шпинделя вычисляется при фрезеровании по формуле:
1) n = ;
2) n = t;
3) n = ;
4) n = ;
5) n = .
7. Если нужно установить глубину фрезерования 0,5мм, а цена деления лимба 0,025мм, то маховичок поворачивают на:
1) 10 делений;
2) 15 делений;
3) 20 делений;
4) 25 делений;
5) 30 делений.
8. Фрезерование прямоугольных уступов выполняется фрезами:
1) цилиндрическими;
2) дисковыми;
3) отрезными;
4) дисковыми и отрезными;
5) цилиндрическими и отрезными.
9. Фрезерование скосов осуществляется фрезами:
1) угловыми;
2) цилиндрическими;
3) дисковыми;
4) отрезными;
5) дисковыми и отрезными
10. Фрезерование узких пазов выполняют фрезами:
1) угловыми;
2) цилиндрическими;
3) дисковыми;
4) отрезными;
11. Разрезания заготовок на фрезерных станках выполняется фрезами:
1) угловыми;
2) цилиндрическими;
3) дисковыми;
4) отрезными;
Составитель раздела
ст. преподаватель Гусейнов М.Д.
Заведующий кафедрой Харченко В.В.
«___»________200__г.
Федеральное агентство по образованию
Государственное образовательное учреждение высшего профессионального
образования
«Бийский педагогический государственный университет имени В.М. Шукшина»
Факультет технологии и профессионально-педагогического образования
Кафедра технология
4. ПЕРЕЧЕНЬ МЕТОДИЧЕСКИХ УКАЗАНИЙ ДЛЯ РАЗЛИЧНЫХ
РАЗДЕЛОВ УЧЕБНЫХ ЗАНЯТИЙ ПО ДИСЦИПЛИНЕ
«ТЕХНОЛОГИЧЕСКИЙ ПРАКТИКУМ (МЕТАЛЛООБРАБОТКА)»
4.1. Общие методические указания
Дисциплина «Технологический практикум» строится в соответствии с программой как единая, комплексная дисциплина, опирающаяся на теоретическую и общетехническую подготовку студентов, получаемая ими на протяжении первых 3-х лет обучения.
По всем разделам практикума программой предусмотрены: вводные беседы по каждому этапу, лабораторно-практические работы, во время выполнения которых студенты учатся разбираться в сложных чертежах и схемах, пользоваться справочной литературой, выполнять расчёты, составлять технологические карты и составлять отчет по лабораторным работам.
Приступая к выполнению лабораторной работы, в первую очередь проводится изучение методики работы, рассмотрение темы и основных вопросов по теме.
В ходе проведения работ, студент ведёт рабочие записи, оформляет расчёты и таблицы, анализирует полученный результат, делает выводы.
«Технологический практикум (металлообработка)» состоит из двух основных разделов: ручная обработка металла и механическая обработка металлов.
Ниже приведены методические рекомендации по каждому разделу.
4.2. Ручная обработка металлов
1. Перед работой ознакомиться с устройством и описанием используемых приборов и инструментов, изучить инструкцию по технике безопасности при работе с приборами и инструментами.
2. До начала работ надеть спецодежду, убрать всё лишнее с верстака.
Проверить прочность и устойчивость верстака, соответствие росту работающего. Слесарные тиски должны быть исправны и прочно закреплены.
Инструмент расположить на расстоянии вытянутой руки. Используемые наиболее часто инструменты кладут ближе, реже используемые – дальше.
Всё, что нужно брать правой рукой, расположить справа, что берут с левой – слева. Предметы, которые берут обеими руками, кладут перед работающими.
3. На лабораторных занятиях студенты должны научиться правильно выполнять основные слесарные операции: разметка, опиливание в размер, резку, рубку, правка и гибка металлов, резка металлов, опиливание, сверление, зенкование, зенкерование и развёртывание отверстий, нарезание резьбы, клёпка, притирка, доводка, пайка. Подбирать и использовать инструмент и приспособления по назначению.
Инструмент перед началом работы осмотреть, при осмотре убедиться в отсутствии следов коррозии, забоин, трещин, заусенцев. Убедиться в прочности насадки рукоятки инструмента.
Обработка ведётся по технологическим картам. Изучить по чертежу устройство и назначение изготовляемой детали (изделия), точности её размеров (допуски), шероховатость обрабатываемых поверхностей.
По окончанию лабораторной работы проводится самоконтроль, сдаются выполненные изделия и отчёт.
4.3. Механическая обработка металлов
В этом разделе рассматривается технология обработки металлов.
Основное оборудование механической мастерской по обработке металлов являются: токарно-винторезный станок модели ТВ – 4 и ТВ – 7, фрезерный станок модели НГФ – 110 , сверлильный станок модели НС – 12 М и точило ЭТ – 60.
Перед выполнением лабораторно-практических работ необходимо ознакомиться с правилами техники безопасности при работе на станках. Изучить назначение, устройство, управление и приемы наладки станка. Проверить исправность станка.
На рабочем месте должны находиться инструменты и принадлежности, необходимые для выполнения задания и ухода за станком. Ознакомиться с учебно-технологической документацией, чертежами, технологическими картами. При выполнении работ на станках пользоваться инструментами и технологическими картами.
Изучить выполнение основных технологических операций: точение, фрезерование и сверление. Выбрать режим и последовательности выполнения этих операций. Подобрать инструмент по назначению, по направлению, по конструкции и режиму обработки. Надежно закреплять заготовку и режущий инструмент. Работать только хорошо заточенным инструментом.
На лабораторно-практических занятиях студенты должны научиться выполнять токарные операции: обтачивание цилиндрических, конических поверхностей, подрезание уступов и торцов, отрезание заготовок, растачивание отверстий, сверление зенкерование и развертывание отверстий, нарезание резьбы, фасонное обтачивание, накатывание рифленых поверхностей.
Фрезерные операции: обработка плоских наружных поверхностей. Подробно конспектировать все этапы выполнения лабораторно – практических работ, провести анализ, составить план.
4.4. Методические указания к самостоятельной работе студентов
Самостоятельная работа студентов по изучению курса «Технологический практикум (металлообработка)» включает: работа с учебниками, справочниками, самостоятельную проработку теоретических знаний, полученных на занятиях, выполнения инструкционных и технологических карт, чертежей, изучение дополнительной литературы, рекомендуемой преподавателем, подготовка сообщений по темам дисциплины.
При всех формах самостоятельной работы студент может получить консультации у преподавателя согласно графика консультации. Самостоятельная работа студента позволит более глубоко усвоить изучаемый материал курса, дает возможность получения навыков поиска и обработки литературы, проанализировать различные подходы к решению поставленной задачи.
По самостоятельной работе проводится контрольный опрос, тестирование. Результаты учитываются при аттестации студента.
Составитель раздела
ст. преподаватель Гусейнов М.Д.
Заведующий кафедрой Харченко В.В.
«___»________200__г.
Федеральное агентство по образованию
Государственное образовательное учреждение высшего профессионального
образования
«Бийский педагогический государственный университет имени В.М. Шукшина»
Факультет технологии и профессионально-педагогического образования Кафедра технология
5. МАТЕРИАЛЬНО-ТЕХНИЧЕСКОЕ
ОБЕСПЕЧЕНИЕ ДИСЦИПЛИНЫ
По дисциплине «Технологический практикум (металлообработка)»
по направлению (специальности) 030600 (050502) «Технология
и предпринимательство»
Для проведения занятий по дисциплине используются аудитории № 66, №68
Сведения об оснащенности образовательного процесса
специализированным и лабораторным оборудованием
Наименование специализированных аудиторий и лабораторий | Перечень оборудования | Количес- тво | Примечание* |
1 | 2 | 3 | 4 |
Лаборатория № 68 |
| 1 6 30 30 12 20 20 80 30 20 20 20 50 20 20 20 20 20 1 1 12 20 2 1 1 2 2 1 100 1 | |
Лаборатория № 66 |
ЭТ-93-2
| 1 1 1 8 2 2 3 2 30 30 30 10 10 10 15 10 |
Составитель раздела
ст. преподаватель Гусейнов М.Д.
Заведующий кафедрой Харченко В.В.
«___»________200__г
Федеральное агентство по образованию
Государственное образовательное учреждение высшего профессионального
образования
«Бийский педагогический государственный университет имени В.М. Шукшина»
Факультет технологии и профессионально-педагогического образования Кафедра технология
6. ИННОВАЦИИ В ПРЕПОДАВАНИИ
По дисциплине «Технологический практикум (металлообработка)»
по направлению (специальности) 030600 (050502)
«Технология и предпринимательство»
Инновацией в преподавании дисциплины «Технологический практикум (металлообработка)» является внедрение компьютерного тестирования в процесс изучения дисциплины. С этой целью разработаны тесты по следующим разделам:
– ручная обработка металла;
– механическая обработка металлов.
Использование тестирования производиться для промежуточного и итогового контроля, а также в процессе самостоятельной работы студентов. Кроме того используется мультимедийное обеспечение программного материала занятий (презентации, слайды и др.).
Составитель раздела
ст. преподаватель Гусейнов М.Д.
Заведующий кафедрой Харченко В.В.
«___»________200__г.
Федеральное агентство по образованию
Государственное образовательное учреждение высшего профессионального
образования
«Бийский педагогический государственный университет имени В.М. Шукшина»
Факультет технологии и профессионально-педагогического образования
Кафедра технология
7. ПЕРЕЧЕНЬ УЧЕБНИКОВ И УЧЕБНЫХ ПОСОБИЙ, ИЗДАННЫХ СОТРУДНИКАМИ УНИВЕРСИТЕТА ПО ДИСЦИПЛИНЕ
Технологический практикум (металлообработка)
по направлению (специальности) 030600 (050502) «Технология предпринимательство»
Составитель раздела
ст. преподаватель Гусейнов М.Д.
Заведующий кафедрой Харченко В.В.
«___»________200__г.
refdb.ru