Формула скорости резания – Скорость резания
alexxlab | 30.03.2020 | 0 | Вопросы и ответы
Особенности режимов резания, формулы скорости и глубины резания
Одной из операций, сопровождающих изготовление деталей на токарных станках, является фрезерование. Важное значение в этом процессе имеют такие параметры, как глубина и скорость резания. Необходимые значения ищутся с помощью формул и подбираемых под каждую деталь или изделие режимов. Далее, подробно разберем, что представляют собой режимы резания при фрезеровании.
Этапы обработки
Детали изготавливаются из прутков, имеющих разное сечение и форму: квадратные, шестигранные, круглые и другие. Если необходимо снять слой материала, который превышает по объему саму деталь, то стараются использовать заготовки в виде отливок или поковок.
Обработка деталей на станках производится в несколько этапов:
- Первой стадией является черновая обдирка будущей детали;
- Снимается значительный по объему слой материала;
- Далее, следует сделать чистовую обработку материала.
Важный момент при обработке деталей: в зависимости от того, насколько высокая точность требуется для изготовления детали, черновую обработку можно произвести на очень мощном и не самом точном станке, а вот уже чистовую обдирку можно делать на прецизионном станке, хоть и менее мощном.
Глубина резания
При черновой обдирке материалов производят снятие значительного объема с поверхности заготовки. Толщина снимаемого слоя при обработке цилиндрических поверхностей есть глубина резания. Вычислить же ее можно по формуле вида t=(D-d)/2. Когда идет подрезание торцевых поверхностей, то значение глубины резания такая же, как и толщина материала, снимаемого с поверхности заготовки.
При этом глубина отрезки мало влияет на скорость. Выбирается она в соответствии с износостойкостью резца, мощностью резцового механизма и при условии отсутствия паразитных вибраций. Если же они возникают, то следует уменьшить скорость подачи режущего инструмента до полного успокоения конструкции.
Скорость резания
Черновая обдирка заготовки предполагает вычисление скорости отрезки. Для этого применяют формулу скорости резания: Vc=(pi*Dm*n)/1000. В этой формуле следующие обозначения:
- Vc — скорость отрезки, измеряется как метры в минуту;
- Pi — постоянная, равняется 3,14;
- Dm — максимальный диаметр заготовки, рассчитываемый в миллиметрах;
- n — число оборотов шпинделя в оборотах за одну минуту.
В этой формуле является очевидным, что с ростом диаметра заготовки растет и скорость резания при условии постоянного числа оборотов шпинделя. При токарной обработке также важно учитывать твердость материала обработки и самого резца. Пример: имеется углеродистая сталь с твердостью порядка 200 H. B. Резцы твердого сплава требуют скорости резания 200 метров в минуту.
Согласно формуле для оборотов шпинделя
Правила черновой обработки
Как и любая технологическая операция, черновая обработка материалов требует соблюдения определенных правил. Перечислим основные правила чернового точения:
- При выборе глубины резания следует помнить, что ее значение не превышает 2/3 ширины режущей кромки;
- Черновая обдирка производится в несколько этапов;
- Обдирочным должен быть проходной резец;
- Первый проход по длине должен составлять размер поверхности детали без учета одного миллиметра;
- Как только произвели обдирку проходным резцом, необходимо с помощью подрезного резца поработать с торцом.
Соблюдая эти несложные правила, вы сможете произвести качественную первую обработку деталей и быть уверенными в качестве производства.
Контроль размеров
Токарная обработка сопровождается контролем линейных и диаметральных размеров детали. При обоих видах обработки чаще всего используют штангенциркуль. Также для диаметральных размеров при чистовой обработке необходимо воспользоваться микрометром и мерными скобами. В зависимости от того, насколько сложное производство, могут применяться и другие инструменты, уровни, специальные линейки, динамометры и другие. Производить контроль размеров необходимо несколько раз, чтобы определить отклонения и на этом основании решить вопрос о дальнейшей судьбе изделия.
Обработка детали является очень важным моментом в производстве изделия. Данная операция должна производиться со всей тщательностью и согласно нормам. При черновой и чистовой обработке важно учитывать формулы для скорости и глубины резания. Это позволит изготовить качественную и надежную деталь, которая обработана по всем правилам и нормам.
tokar.guru
4.5 Вывод формулы для расчёта скорости резания
Частные стойкостные зависимости от скорости, подачи и глубины резания выводятся аналогично температурным зависимостям. При постоянных условиях определяют зависимость стойкости инструмента от скорости резания. Проводят опыты при различных скоростях резания и строят кривые износа для каждой скорости резания.
Рисунок 59
При принятом критерии износа hз по графику (рис. 59) определяют стойкость инструмента, соответствующую каждой скорости
V | V1 | V2 | …. Vn |
T | T1 | T2 | …. Tn |
и в логарифмической системе координат строят график зависимости стойкости от скорости резания.
Записывают уравнение частной зависимости от скорости:
,
где
.
Совершенно аналогично находят частные зависимости стойкости от подачи и глубины резания
,
,
где
,
Рисунок
60 – Частные зависимости стойкости отV,
S
и t
На основании частных зависимостей записывают общую зависимость
,
откуда
,
приняв: , получим:
– формула справедлива
в интервале V1 – V2 (рис. 63),
где V – расчётная допустимая скорость резания, рассчитывается для конкретных условий обработки;
CV – постоянный коэффициент, зависящий от условий обработки;
KΣ – суммарный поправочный коэффициент на изменённые условия обработки, – берутся по справочникам;
T – период стойкости инструмента. Он задаётся технологом и зависит от стоимости и сложности инструмента;
S – подача;
t – глубина;
– показатель
относительной стойкости;
YV, XV – показатели при подаче и глубине резания, характеризуют степень влияния на скорость резания соответственно подачи и глубины резания.
Рисунок
61
Для увеличения производительности труда при одинаковой стойкости целесообразнее работать с большим отношением t/S или b/a.
4.6 Упрочнение (наклёп) в зоне резания
В процессе превращения срезаемого слоя в стружку благодаря пластической деформации происходит упрочнение материала (наклёп). Упрочняется стружка, особенно её контактный слой. В случае образования нароста он упрочняется в ещё большей степени, примерно в 2-3 раза по отношению к микротвёрдости обрабатываемого материала. Упрочняется и обработанная поверхность.
Упрочнение характеризуется глубиной h и степенью наклёпа обработанной поверхности.
Степень наклёпа H равна:
,
где H2 – микротвёрдость обработанной поверхности;
H1 – микротвёрдость обрабатываемой заготовки.
С увеличением скорости резания происходит некоторое снижение глубины и степени наклёпа. Это связано с уменьшением зоны первичной пластической деформации.
С увеличением подачи или толщины срезаемого слоя глубина и степень наклёпа увеличиваются. Это связано с увеличением сил резания.
Глубина
резания влияния практически не оказывает.
Рисунок 62
Рисунок 63
Влияние геометрии резца на h и H
Сувеличением переднего угла и угла в плане степень и глубина уменьшаются, а с увеличениемR и, особенно, радиуса округления режущей кромки r – увеличиваются.
Рисунок 64
С применением СОЖ H и h снижаются.
5 Основные операции механической обработки
5.1 Точение
Черновое точение – 12 квалитет (13 – экономический).
Получистовое – 10…11 квалитет, Rz40…20
Рисунок 67 – Токарно-винторезный станок
studfiles.net
Вид обработки | Инструментальный материал | Подача, мм/об | Cv | xv | yv | mv | |||
Обработка конструкционной стали, sв=750 МПа | |||||||||
Наружное продольное точение | Т15К6 | SЈ0,3 | 420 | 0,15 | 0,2 | 0,2 | |||
0,3<SЈ0,7 | 350 | 0,35 | |||||||
S>0,7 | 340 | 0,45 | |||||||
Отрезание | Т5К10 | – | 47 | 0 | 0,8 | 0,2 | |||
Р18* | 23,7 | 0 | 0,66 | 0,25 | |||||
Фасонное | Р18* | 22,7 | 0 | 0,5 | 0,3 | ||||
Нарезание резьбы | Т15К6 | 244 | 0,23 | 0,3 | 0,2 | ||||
Р6М5 | SЈ2 | 14,8 | 0,7 | 0,3 | 0,11 | ||||
S>2 | 30 | 0,6 | 0,25 | 0,08 | |||||
Обработка серого чугуна , НВ 150 | |||||||||
Наружное точение | ВК6 | SЈ0,4 | 292 | 0,15 | 0,2 | 0,2 | |||
S>0,4 | 243 | 0,15 | 0,4 | 0,2 | |||||
Отрезание | – | 68,5 | 0 | 0,4 | 0,2 | ||||
Резьба | – | 83 | 0,45 | – | 0,33 | ||||
Обработка медных сплавов, НВ 100 – 140 | |||||||||
Наружное точение | Р18 | SЈ0,2 | 270 | 0,12 | 0,25 | 0,23 | |||
S>0,2 | 182 | 0,3 | |||||||
Обработка алюминиевых сплавов | |||||||||
Наружное точение | Р18 | SЈ0,2 | 485 | 0,12 | 0,25 | 0,28 | |||
S>0,2 | 328 | 0,5 | |||||||
Обрабатываемый материал | Вид обработки | Инструментальный материал | Cv | qv | xv | yv | mv | ||
Сталь конструкционная, sв=750 МПа | Сверление | Р6М5 | 9,8 | 0,4 | – | 0,5 | 0,2 | ||
Рассверливание | Р6М5 | 16,2 | 0,4 | 0,2 | 0,5 | 0,2 | |||
ВК8 | 10,8 | 0,6 | 0,2 | 0,3 | 0,25 | ||||
Зенкерование | Р6М5 | 16,3 | 0,3 | 0,2 | 0,5 | 0,3 | |||
Т15К6 | 18 | 0,6 | 0,2 | 0,3 | 0,25 | ||||
Развёртывание | Р6М5 | 10,5 | 0,3 | 0,2 | 0,65 | 0,4 | |||
Т15К6 | 100,6 | 0,3 | 0 | 0,65 | 0,4 | ||||
Чугун серый НВ 190 | Сверление | Р6М5 | 14,7 | 0,25 | – | 0,55 | 0,125 | ||
ВК8 | 34,2 | 0,45 | – | 0,3 | 0,2 | ||||
Рассверливание | Р6М5 | 23,4 | 0,25 | 0,1 | 0,4 | 0,125 | |||
ВК8 | 56,9 | 0,5 | 0,15 | 0,45 | 0,4 | ||||
Зенкерование | Р6М5 | 18,8 | 0,2 | 0,1 | 0,4 | 0,125 | |||
ВК8 | 105 | 0,4 | 0,15 | 0,45 | 0,4 | ||||
Развёртывание | Р6М5 | 15,6 | 0,2 | 0,1 | 0,5 | 0,3 | |||
ВК8 | 109 | 0,2 | 0 | 0,5 | 0,45 | ||||
Медные сплавы | Сверление | Р6М5 | 28,1 | 0,25 | – | 0,55 | 0,125 | ||
Силумин и литейные алюминиевые сплавы | Сверление | Р6М5 | 36,3 | 0,25 | – | 0,55 | 0,125 | ||
Фрезы | Инструментальный материал | Sz | Cv | qv | xv | yv | uv | pv | mv |
Обработка серого чугуна, НВ 190 | |||||||||
Торцовые | ВК6 | – | 445 | 0,2 | 0,15 | 0,35 | 0,2 | 0 | 0,32 |
Р6М5 | – | 42 | 0,2 | 0,1 | 0,4 | 0,1 | 0,1 | 0,15 | |
Цилиндрические | ВК6 | Ј 0,2 | 923 | 0,37 | 0,13 | 0,19 | 0,23 | 0,1 | 0,42 |
>0,2 | 750 | 0,37 | 0,4 | 0,47 | 0,23 | 0,1 | 0,42 | ||
Р6М5 | Ј 0,15 | 57,6 | 0,7 | 0,5 | 0,2 | 0,3 | 0,3 | 0,25 | |
>0,15 | 27 | 0,6 | |||||||
Дисковые | Р6М5 | – | 78,5 | 0,2 | 0,5 | 0,4 | 0,1 | 0,1 | 0,15 |
Концевые | – | 72 | 0,7 | 0,5 | 0,2 | 0,3 | 0,3 | 0,25 | |
Отрезные | – | 30 | 0,2 | 0,5 | 0,4 | 0,2 | 0,1 | 0,15 | |
Обработка медных сплавов, НВ 100-140 | |||||||||
Торцовые | Р6М5* | Ј 0,1 | 136 | 0,25 | 0,1 | 0,2 | 0,15 | 0,1 | 0,2 |
>0,1 | 86,2 | 0,4 | |||||||
Цилиндрические | Ј 0,1 | 115,5 | 0,45 | 0,3 | 0,2 | 0,1 | 0,1 | 0,33 | |
>0,1 | 74,3 | 0,4 | |||||||
Дисковые | Ј 0,1 | 158,5 | 0,25 | 0,3 | 0,2 | 0,1 | 0,1 | 0,2 | |
>0,1 | 102 | 0,4 | |||||||
Отрезные | – | 111,3 | 0,25 | 0,3 | 0,2 | 0,2 | 0,1 | 0,2 | |
Концевые | – | 103 | 0,45 | 0,3 | 0,2 | 0,1 | 0,1 | 0,33 | |
Обработка алюминиевых сплавов, sв=100-200 МПа, НВ Ј 65 | |||||||||
Торцовые | Р6М5* | Ј 0,1 | 245 | 0,25 | 0,1 | 0,2 | 0,15 | 0,1 | 0,2 |
>0,1 | 155 | 0,4 | |||||||
Цилиндрические | Ј 0,1 | 208 | 0,45 | 0,3 | 0,2 | 0,1 | 0,1 | 0,33 | |
>0,1 | 133,5 | 0,4 | |||||||
Дисковые | Ј 0,1 | 285 | 0,25 | 0,3 | 0,2 | 0,1 | 0,1 | 0,2 | |
>0,1 | 183,4 | 0,4 | |||||||
Отрезные | – | 200 | 0,25 | 0,3 | 0,2 | 0,2 | 0,1 | 0,2 | |
Концевые | – | 185,5 | 0,45 | 0,3 | 0,2 | 0,1 | 0,1 | 0,33 | |
Обрабатываемый материал | Нарезание резьбы | Материал режущей части | Условия резания или конструкции инструмента | Коэффициент и показатели степени | Среднее значение периода стойкости Т, мин | ||||
СV | x | у | q | т | |||||
Сталь конструкционная углеродистая, s в= 750 МПа | Крепежной резцами | Т15К6 | – | 244,0 | 0,23 | 0,30 | – | 0,20 | 70 |
Р6М5 | Черновые ходы: Р < 2 мм Р > 1 мм | 14,8 30.0 | 0,70 0,60 | 0,30 0,25 | – | 0,11 0,08 | 80 | ||
Чистовые ходы | 41,8 | 0,45 | 0,30 | – | 0,13 | ||||
Трапецеидальной, резцами | Р6М5 | Черновые ходы | 32,6 | 0,60 | 0,20 | – | 0,14 | 70 | |
Чистовые ходы | 47,8 | 0,50 | 0 | – | 0,18 | ||||
Метчиками | Р6М5 | – | 64,8 | – | 0,5 | 1,2 | 0,90 | 90 | |
Круглыми плашками | 9ХС У12А | – | 2,7 | – | 1,2 | 1,2 | 0,50 | 90 | |
Серый чугун, НВ 190 | Крепежной резцами | ВК6 | – | 83,0 | 0.45 | 0 | – | 0,33 | 70 |
Силумин | Метчиками | Р6М5 | – | 20,0 | – | 0.5 | 1,2 | 0,9 | 90 |
osntm.ru
Обрабатываемый материал | Коэффициент kГ для материала инструмента | Показатель степени nv при обработке | ||||||
резцами | осевым инструментом | фрезами | ||||||
из быстрореж. стали | из тв. сплава | из быстрореж. стали | из тв. сплава | из быстрореж. стали | из тв. сплава | из быстрореж. стали | из тв. сплава | |
Сталь: | ||||||||
углеродистая с sв< 550 МПа | 1 | 1 | -1 | 1 | -0,9 | 1 | -0,9 | 1 |
углеродистая с sв> 550 МПа | 1 | 1 | 1,75 | 0,9 | ||||
хромистая | 0,85 | 0,95 | 1,75 | 1,45 | ||||
жаропрочная и коррозионно-стойкая | 0,7 | 0,8 | 1,25 | 0,9 | 1 | |||
марганцовистая | 0,75 | 0,9 | 1,5 | |||||
быстрорежущая | 0,6 | 0,7 | 1,25 | |||||
Чугун: | ||||||||
серый | – | – | – | 1,25 | 1,3 | 1,3 | 0,95 | 1,25 |
ковкий | 0,85 | |||||||
Медные сплавы | KМv | Алюминиевые сплавы | KМv | |||||
Гетерогенные: НВ>140 НВ=100-140 | 0,7 1,0 | Закалённые: силумин и литейные сплавы с sв=200-300 МПа ; НВ>60 и дюралюминий НВ>100 | 0,8 | |||||
Гомогенные | 2,0 | силумин и литейные сплавы с sв =100-200 МПа; НВ Ј 60 и дюралюминий НВ Ј 100; | 1,0 | |||||
Сплавы с содержанием свинца < 10% | 4,0 | |||||||
Сплавы с содержанием свинца > 15% | 12,0 | sв=300-400 МПа | ||||||
Медь | 8,0 | дюралюминий с sв=200-300 МПа | 1,2 | |||||
Обрабатываемый материал | Значение коэффициента Kиv в зависимости от марки инструментального материала | |||||||
Сталь конструкционная | Т5К12 0,35 | Т5К10 0,65 | Т14К8 0,8 | Т15К6 1,0 | Т15К6В 1,15 | Т30К4 1,4 | ВК8 0,4 | |
Коррозионно-стойкие и жаропрочные стали | ВК8 1,0 | Т5К10 1,4 | Т15К6 1,9 | Р18 0,3 | – | – | – | |
Сталь закалённая | HRC 35-50 | HRC 51-62 | ||||||
Т15К6 1,0 | Т30К4 1,25 | ВК6 0,85 | ВК8 0,83 | ВК4 1,0 | ВК6 0,92 | ВК8 0,74 | ||
Серый и ковкий чугун | ВК8 0,83 | ВК6 1,0 | ВК4 1,1 | ВК3 1,15 | – | – | – | |
Сталь, чугун, медные и алюминиевые сплавы | Р6М5 1,0 | ВК4 2,5 | ВК6 2,7 | 9ХС 0,6 | ХВГ 0,6 | У12А 0,5 | – |
osntm.ru
Скорость резания
ТОКАРНОЕ ДЕЛО
На основании экспериментов выведена формула для расчета допускаемой скорости резания при различных условиях обработки:
С” • /<об, ц м/мин,
=
Fm. fxv. syv
Где Cv — коэффициент, зависящий от вида обработки и обрабатываемого материала; Т — заданная стойкость инструмента, мин; m — показатель относительной стойкости; tv — глубина резания, мм; s — величина подачи, мм/об; xv — дробный показатель степени
При глубине резания; yv — дробный показатель степени при подаче; — общий поправочный коэффициент, учитывающий конкретные условия работы.
В зависимости от вида обработки и обрабатываемого материала формулу скорости резания уточняют по справочникам. Например, для резцов, оснащенных пластинками из сплава Т15К6 (при s^0,75 мм/об), формула имеет вид
V = jO,2 ^15^0,35 ‘ Кобщ м/миН.
Коэффициент С„ принимается в зависимости от обрабатываемого материала и от угла ф резца по справочнику. Чем меньше угол ф, тем большая длина режущей кромки участвует в работе, тем лучше отвод тепла от головки резца в державку, выше стойкость и возможно
Увеличение скорости резания (рис. 297): Ко(,щ Км^’ Kqv” Kcmtit
Где K mv — коэффициент, учитывающий механические свойства обрабатываемого материала. Чем выше механические свойства металла (предел прочности для стали, твердость для чугуна), тем больше сопротивление резанию и больше выделяется тепла. Чтобы сохранить заданную стойкость, нужно уменьшить скорость резания. Следовательно, с увеличением предела прочности и твердости коэффициент Км уменьшается;
Kqv ————- Коэффициент, уЧИТЫВЭЮ-
Щий (только для быстрорежущих резцов) сечение державки резца. При большем сечении державки улучшается отвод тепла от головки резца в державку, стойкость резца увеличивается и соответственно можно увеличить скорость резания;
Кс<»к — коэффициент, зависящий от качества смазочно-ох – лаждагощей жидкости (учитывается только для быстрорежущих резцов). Чем лучше охлаждается резец, тем выше его стойкость и возможно увеличение скорости резания. Глубина резания t стоит в знаменателе, это означает, что с увеличением глубины и увеличением площади сечения стружки увеличивается сила, действующая на резец, и расходуемая мощность резания, соответственно растет теплота резания, вызывающая размягчение и износ резца. Чтобы сохранить заданную стойкость, уменьшают скорость резания. Дробный показатель xv указывает на двойственное влияние глубины резания: увеличение глубины резания хотя и вызывает повышение теплоты резания, но благодаря увеличению рабочей длины режущей кромки улучшает отвод тепла от резца (рис. 298).
Величина подачи s находится в знаменателе формулы; это означает, что с увеличением подачи также растет площадь сечения среза и соответственно
79R ВЛИЯНИЕ ГЛУБИНЫ РЕЗАНИЯ НА СКОРОСТЬ РЕЗАНИЯ (ОБРАБАТЫВАЕМЫЙ МАТЕРИАЛ — СТАЛЬ о = 75 кГ/мм РЕЗЕЦ ИЗ БЫСТРОРЕЖУЩЕЙ СТАЛИ, СТОЙКОСТЬ — 60 мин )
1 2 3 4 5 6 Увеличение глубины резания в п раз |
Падает стойкость резца. Дробный показатель степени yv при подаче объясняется тем, что возрастание силы резания отстает от возрастания подачи, соответственно отстает и возрастание расходуемой мощности, нагрев и износ резца (рис. 299).
Исследования показывают, что показатель степени при глубине резания всегда меньше, чем показатель степени при подаче, т. е. xv<yv. Отсюда следует закон резання: для повышения скорости резания при неизменной стойкости или для повышения стойкости при неизменной скорости резания следует увеличить глубину резания, соответственно уменьшив подачу.
Задача. Определить скорость резания при наружном точении вала из стали 45 (ов= 75 кГ/ммs). Резец проходной из сплава Т15К6 сечением 16X25, «р=60°, работа без охлаждения, /=5 мм, подача s=0,6 мм/об, заданная стойкость резца Т=90 мин.
■ Кобщ мі мин.
Т>0,2 ^0,15. sO,35
С„=241 (по справочнику). Для Ов=75 кг/мм2 Kb, v= 0,77 (по справочнику) 90°’2=1,7, 5°-,5= 1,3, 0,6°-35=0,84.
241
299 ВЛИЯНИЕ ПОДАЧИ НА СКОРОСТЬ РЕЗАНИЯ (МАТЕРИАЛ И РЕЗЕЦ см. РИС. 298) |
Увеличение подачи в п раз |
Я h И О п С.« О о. А _ 0 S V а К X и А s 3 5 1 Я > |
По формулам скорости резания с учетом опыта новаторов производства разработаны таблицы, по которым можно
непосредственно определять скорость резания для заданных условий обработки. Такие таблицы приводятся в справочниках (см. приложение 4).
§ 94. Выбор рациональных режимов резания
Токарная обработка, как и всякая другая, должна вестись на таких режимах, при которых наиболее полно используются мощность станка и стойкость инструмента, обеспечивается высокое качество обработки и создаются безопасные условия работы. Рациональные режимы резания принимаются по справочным таблицам, данные которых определены по формулам теории резания и на основе обобщения опыта передовых предприятий. В приложении 4 приводятся таблицы для выбора режимов резания при работе резцами Р18 и Т5КЮ.
Пример определения рациональных режимов резания с помощью справочных таблиц. Исходные данные: обрабатываемая заготовка — валик £>=80 мм, материал — сталь 45, а„=85 кГ/мм2, резец прямой проходной, оснащенный пластинкой нз твердого сплава Т5К10, параметры <р=60°; cpi=30°; г= 1,0 мм, сечение 16X25, стойкость 60 мин, припуск на обработку 4 мм, заданная шероховатость поверхности V5. Станок 1К62 (Л =10 кет, ті=0,75). Последовательность определения: назначаем глубину резания. Учитывая, что требуемая чистота невысокая, снимаем припуск за один проход: t—4 мм-,
По справочнику (приложение 4, карта 3) назначаем подачу s=0,3 мм/об и уточняем ее по паспортным даииым станка; 5факт.=0,3 мм/об; по справочнику (приложение 4, карта 5) назначаем табличную скорость резания, определяем табличную силу резания і’таг»л-= 131 мімин; Ргтабл.^208 кГ;
По справочнику определяем поправочные коэффициенты на скорость резания и на силу резания: для стали 45 ов=85 кГ/мм2, Kmv =0,77, /СмРг = 1,14; для переднего угла у= 12° АуРг — = 1 (приложение 4).
Определяем скорость резания с учетом поправочных коэффициентов
T>= отаблК„ =131-0,77 = 101 м/мин; v
Определяем число оборотов в минуту
1000 V 1000-101 п =————– = — = 405 об! мин.
Я-80
Принимаем по паспорту станка Лфаит.= =400 об/мин;
Определяем силу резания с учетом поправочных коэффициентов
Pz = Pz табл. – KMpz KiPz =208- 1,14-1 = = 238 кГ;
Определяем фактическую скорость резания кРпф я 80-400
“ф==”Тооо” = =100 м, мин;
Определяем эффективную мощность, затрачиваемую на процесс резания
Pzv
Кет,
60-102
238-100
NЭ(1, =—————— = 3,95 кет;
9ф 60-102
Определяем потребную мощность двигателя станка:
Л’эф _ 3,95
————————— ———— 5,3 кет.
Ч 0,75
Мощность двигателя станка достаточна.
По закону сохранения энергии энергия, затраченная на процесс резания, не может исчезнуть: она превращается в другой вид —в тепловую энергию. В зоне резания возникает теплота резания. В процессе резания больше …
Особенностью современного технического прогресса является автоматизация на базе достижений электронной техники, гидравлики и пневматики. Главными направлениями автоматизации являются применение следящих (копировальных) устройств, автоматизация управления станками и контроля деталей. Автоматическое управление …
Рассмотренные ранее правила выбора установочных баз справедливы и при изготовлении деталей с участками сложной формы. Однако не всегда такие участки удобны для использования их в качестве баз, в других случаях, …
msd.com.ua
Формула – скорость – резание
Формула – скорость – резание
Cтраница 1
Формулы скорости резания, выведенные из зависимостей износа, приближают нас к пониманию сущности процесса. Как видно из вышеприведенных материалов, показатели степеней в формулах скорости резания больше при той величине, которая оказывает большее влияние на износ инструмента. Отсюда также можно сделать вывод, что показатели степеней при всех факторах, входящих в формулу скорости резания, являются выразителями интенсивности износа инструмента. [1]
Из формулы скорости резания следует, что в отличие or ранее рассмотренных факторов диаметр входит в числитель формулы; это значит, что с увеличением диаметра возрастает скорость, допускаемая фрезой. [2]
Графически формула скорости резания ( 7) в прямоугольной системе координат изображается лучевой диаграммой. [3]
По формуле скорости резания определить значение скорости резания v, если число п 320 об мин и диаметр фрезы D 120 мм. [4]
В качестве примера ниже приводится формула скорости резания для цилиндрических фрез из быстрорежущей стали при обработке сталей с подачей на зуб 0 1 мм и больше. [5]
Ниже приведены поправочные коэфициенты к формулам скорости резания ( 167) и ( 167а) в зависимости от материала инструмента. [6]
Применение охлаждения также учитывается в формуле скорости резания соответствующим поправочным коэффициентом. [7]
Значения постоянной Cv и показателей степени в формулах скорости резания, а также средние значения стойкости приведены в табл. 59; в табл. 60 указаны значения поправочного коэффициента KMV, учитывающего качество обрабатываемой стали, а в табл. 61 значения коэффициентов, учитывающих конструктивные и другие особенности инструментов. [8]
В табл. 38 приводятся значения коэффициентов в формулах скорости резания, усилия подачи и крутящих моментов при сверлении отвер стий сверлами из быстрорежущей стали. [9]
В табл. 38 приводятся значения коэффициентов в формулах скорости резания, усилия подачи и крутящих моментов при сверлении отверстий сверлами из быстрорежущей стали. [10]
В зависимости от вида обработки и обрабатываемого материала формулу скорости резания уточняют по справочникам. [11]
При анализе влияния различных факторов, входящих в формулу скорости резания, обычно больше внимания уделяется тепловому фактору. То или иное влияние отдельных факторов объясняется почти исключительно зависимостью от процесса образования и отвода тепла. [12]
Показатель относительной стойкости m 0 25, что следует из формулы скорости резания, допускаемой режущими свойствами сверла, оснащенного твердым сплавом. После подсчетов будем иметь Tz 82 мин. [13]
Для сверл, зенкеров и разверток, оснащенных твердыми сплавами, формулы скорости резания принимаются из справочников по режимам резания. [14]
Страницы: 1 2
www.ngpedia.ru
Расчет режимов резания при точении – вычисляем скорость и глубину + Видео
Выбор рациональных режимов резания при точении заготовок на токарных станках и других агрегатах является очень важной составляющей при создании эффективных техпроцессов ремонта либо изготовления деталей.
1 Режим резания – что это такое?
Под таким режимом понимают комплекс из нескольких элементов, которые определяют условия осуществления операции резания. Его расчет производят так, чтобы была обеспечена самая производительная и экономически целесообразная обработка поверхности детали по показателям шероховатости и точности.
Режимы резания включают в себя следующие моменты:
- скорость резки;
- время стойкости рабочего приспособления, используемого для выполнения операции;
- подача и глубина резания;
- мощность и сила процесса.
Расчет режима резания можно проводить на основании справочных и нормативных документов, коих российская школа обработки разнообразных металлов собрала немало. Суть такого метода заключается в выборе требуемых значений из специальных таблиц. Подобный расчет гарантирует подбор оптимальных показателей всех элементов, а значит, обеспечивает и максимально эффективное выполнение операции резания.
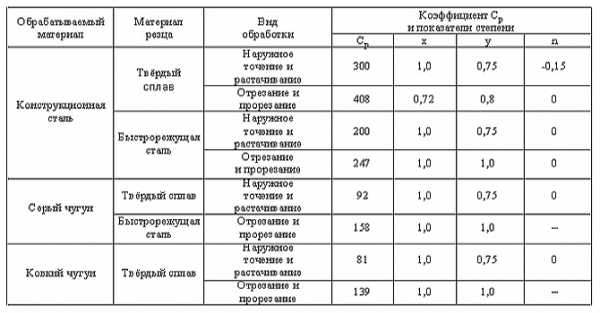
Фото таблицы для расчета режимов резания
Рекомендуем ознакомиться
Но он является очень громоздким. Специалисту необходимо проанализировать и сопоставить огромные массивы информации. При этом абсолютно все режимные характеристики напрямую связаны между собой. Как только один из них изменяет свое значение, остальные также становятся иными. Понятно, что в производственных условиях использовать табличную схему подбора режимов не всегда разумно.
В ряде случаев целесообразнее использовать расчетную (иногда ее называют аналитической) схему выбора режима. Ее смысл состоит в том, что специалист, применяя эмпирические формулы, производит расчет всех требуемых ему показателей. Абсолютно точное выполнение расчетов по аналитической методике обеспечивается тогда, когда известны такие паспортные характеристики токарного станка либо иного металлообрабатывающего агрегата:
- частота вращения шпинделя;
- мощность двигателя;
- величины подач.
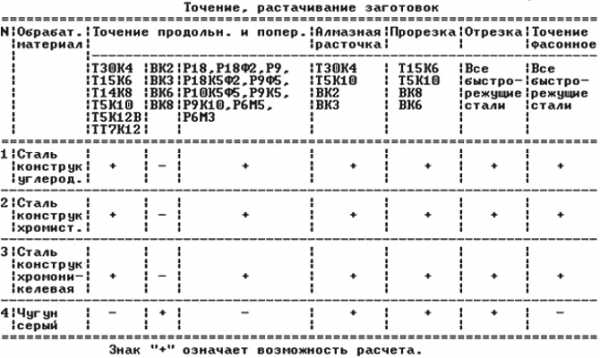
На фото – таблица характеристик токарных станков для точения заготовок
Если точных технических параметров оборудования нет, допускается осуществление приблизительного расчета. В этом случае в формулы подставляются справочные значения.
2 Тонкости определения элементов режима резания
Любой расчет начинается с того, что специалист подбирает глубину проведения операции резания. После этого устанавливается необходимая подача и только в последнюю очередь скорость процесса. Расчет выполняется именно в такой последовательности потому, что скорость оказывает наибольшее влияние на стойкость и показатель износа резца станочного оборудования, а глубина – наименьшее.
Все составляющие режима подбираются с учетом максимального использования потенциала станка и рабочего инструмента, применяемого для резания. По данной причине “идеальным” режим будет только в том случае, если специалист изучит геометрические размеры резца, материал, из которого он изготовлен, а также материал, использованный для выпуска обрабатываемой детали.
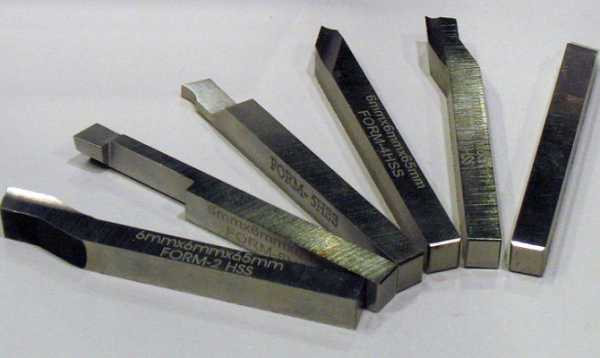
Фото рабочего инструмента для резания при точении
Сначала следует определить величину шероховатости заготовки. И на основании этого подобрать оптимальный способ обработки ее поверхности – данные берутся из таблицы, где указывается конкретный инструмент, рекомендованный для резания заготовки. На практике для выполнения отделочных операций (они считаются очень тонкими и ответственными) обычно берут резцы, произведенные из твердых инструментальных сталей. Они отлично подходят для обработки деталей на высокой (более 500 метров в минуту) скорости.
3 Схема выбора режима резания – основные требования
Глубина операции определяется в наибольшей степени показателем припуска на обработку заготовки. Этот самый припуск всегда стараются убрать за один-единственный проход режущего инструмента (если речь идет о черновой процедуре). Если же осуществляется чистовая обработка, срезание припуска добиваются за несколько проходов. При этом каждый последующий проход должен иметь меньшую глубину, нежели предшествующий ему.
Величина подачи (расстояние кромки резца, которое он проходит за оборот детали) подбирается в зависимости от категории необходимой чистоты обработки. Подача может быть нескольких видов:
- минутная;
- на оборот режущего инструмента;
- на один зуб резца.
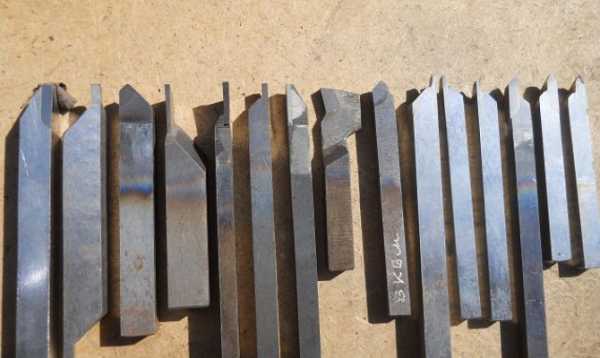
На фото – резцы для токарного станка
Максимальные величины подачи обычно назначают для чернового резания, минимальные – для чистового. Конкретный показатель определяется периодом стойкости резца, мощностью привода металлорежущего агрегата, прочностью и жесткостью обрабатываемой системы. В большинстве случаев расчет величины подачи вести нет необходимости, так как в паспорте каждого станка они четко указаны.
Под упомянутым выше периодом стойкости принято понимать время функционирования рабочего инструмента без остановок между последовательными переточками. Стандартный ряд такого периода включает величины от 15 до 120 минут с шагом в 15 минут. Скорость операции рассчитывается на базе всех указанных значений по специальным формулам, которые незначительно отличаются друг от друга в зависимости от варианта точения (фасонное, поперечное, продольное). Разрешается, как мы уже говорили, брать скорость и из таблиц.
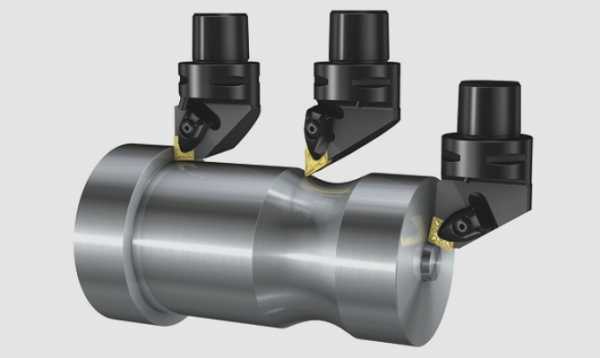
Фото продольного точения
Добавим, что полученный режим резания обязательно требуется проверить по прочности:
- резцедержателя;
- устройства подач станка;
- мощности агрегата.
tutmet.ru