Формы под алюминий – – .
alexxlab | 11.12.2020 | 0 | Вопросы и ответы
Как и из чего сделать форму для заливки расплавленного алюминия, чтоб отлить нужную деталь?
Как вариант могу предложить изготовить форму для заливки из гипса или алебастра.
При условии, что Ваша деталь не сложной формы и не имеет замысловатых рельефов и внутренних полостей.
Подготавливаем емкость по размерам чуть больше Вашей детали, можно использовать любую готовую картонную коробочку или изготовить самому из любого картона или гофрокартона, можно половину пластиковой бутылки, посуды, главное потом извлечь полученную форму для заливки.
Обмазываем деталь техническим вазелином или другой густой смазкой.
Готовим две шпонки для центровки формы из двух половин, к примеру, отпиливаем от карандаша два кусочка по 2 см., обмазываем вазелином.
Выбираем для изготовления формы алебастр.
Алебастр разводим следующим образом: в емкость с холодной водой добавляем нужное количество алебастра, дожидаемся пока вода полностью впитается в порошок и затем размешиваем до получения однородной консистенции.
Раствор должен получиться как сметана средней густоты.
Вязкий раствор получается из пропорции на 1 часть алебастра 1 часть воды.
Разводите такое количество раствора, чтобы использовать его за один прием, поскольку смесь достаточно быстро отвердеет и ее надо будет выбросить, восстанавливать ее не имеет смысла, свойства алебастра не восстанавливаются.
Наливаем в емкость столько раствора, чтобы Ваша деталь погрузилась наполовину в него. Это будет половина Вашей формы.
Важно расположить деталь так, чтобы после застывания раствора ее можно было бы извлечь из данной половинки формы.
По диагонали формы отдельно от детали вертикально погружаем до половины две шпонки.
Когда раствор застынет, попробуем аккуратно извлечь деталь и возвращаем ее на место. Все получилось, продолжаем дальше.
Изготавливаем прокладку на застывшую форму из подручных материалом: полиэтиленовой пленки, кальки, тонкой бумаги, закрываем только форму, деталь не закрываем. Можно еще смазать вазелином.
Из пластилина по расстоянию от детали до края формы изготавливаем цилиндр с воронкой на краю и помещаем в форму, это будет заливной канал. С толщиной определитесь сами.
Разводим еще нужное количество раствора и заливаем деталь полностью и ждем полного застывания второй половинки формы.
Затем извлекаем полученную форму из емкости, аккуратно разъединяем на две половинки, вынимаем деталь и пластилин, подчищаем дефекты.
Форму соединяем, воронка к верху, все, можно заливать алюминий.
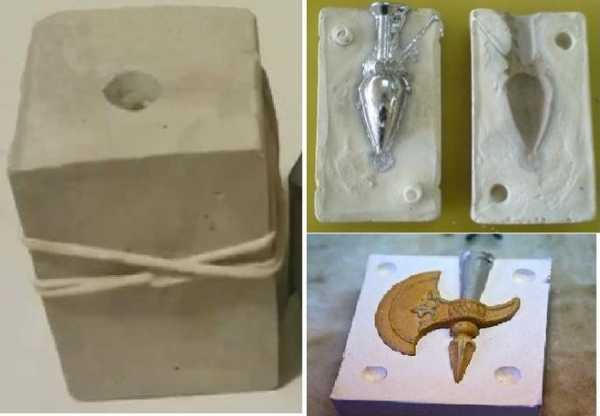
После заливки и извлечения из формы необходимо будет доработать вылилую деталь вручную с помощью шкурки, надфилей, резака и т. д. до размеров оригинала.
Успехов Вам! Да прибудет с Вами умение!
www.remotvet.ru
Алюминий. Формы всякие нужны, формы всякие важны. Часть 3.: shakherezada
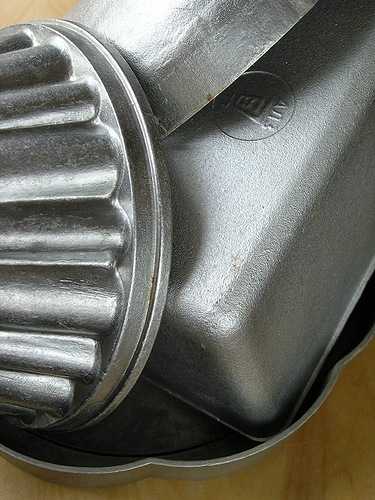
Краткое содержание предыдущих серий: Люмень – вездесущ и никуда от него не деться, ибо дёшево, надёжно и практично (с).
Так что перехожу к конкретике. 🙂
Тут меня в прошлый раз некоторые упрекали в цветовых искажениях.:) Так вот – тщательно выставленный цветовой баланс позволяет «на глазок» определить состав алюминиевого сплава нашей любимой кастрюльки. Чистый алюминий – серебристо белый металл и полированный блестит почти так же, как серебро. Добавки делают его темнее – от серого (Si,Fe,Mg) до темно-серого и почти черного (Сu, Zn).
Отливки из алюминиевого сплава обычно пористые, это хорошо видно даже невооруженным глазом. И невооруженным же глазом видна культура производства.
При этом качество литья – однородность, отсутствие раковин, наплывов и крупных пор выдвигается на первый план. Это – поверхность формы «черепашка», изготовленная на оборонном предприятии.
А это – обработка края формы-отливки. За долгие годы использования или хранения на ней появляются царапины, но на общую конструкцию и деформацию формы это никак не влияет.
Это – поверхность современной хлебной формы, предназначенной для промышленной выпечки хлеба. Заметна неравномерная пористость, которая приведет к скапливанию в углублениях нагара и ускорению коррозии.
Края у этой формы вообще никак не обрабатывались – видны следы отрезания одной отливки от другой. Ну правильно, чо. Промышленный дизайн, он такой промышленный.
Зато этой «парадной» форме для шарлоты на заводе старались придать даже некоторый глянец – полировкой или какой-то другой обработкой поверхность сглажена и блестит больше других форм. Но поры все равно видны.
Обработка края старой утятницы – приливы позволяют придать больше жесткости конструкции. Приливы на форме для «шарлотты» можно оценить на верхних фото.
Жесткость особенно важна была для тонких штампованных форм, поэтому чаще всего их края закатывали. Но если форма небольшая и тонкая, закатывание мало помогало – форма очень легко мялась прямо руками.
На эту форму, производства конца 80-х уже стали наносить антипригарное покрытие. Видны следы «напыления» тефлона первого поколения, которое поначалу царапалось на раз, даже при хранении.
Еще интересно изучать «товарные знаки заводов-изготовителей». Опознаны, правда, далеко не все. 🙂
Каменск-Уральский Литейный Завод.
Балезинский литейно-механический завод. На современных формах цену уже не отливают в алюминии. 🙂 только артикул формы Л7 и марку сплава АЛ3. Кстати, эта марка сплава в ГОСТах не обозначена.
Литейно-механический завод.
Большая и прочная штампованная форма начала 80-х. Завод не опознан.
Здесь отлита вообще одна буква «Л». Кстати, на этой форме хорошо виден белый налет гидроксида алюминия.
И еще один неопознанный товарный знак на старой утятнице.
Утятница и это фото демонстрируют, что такая пористая поверхность, даже на штампованном алюминии прекрасно впитывает все, эту форму окружающее. Что не улучшает внешний вид снаружи и не приносит пользу, будучи изнутри.
Исходя из свойств алюминия, периодически стоит устраивать чистку рядов с помощью простейших подручных средств – пищевой соды, горчичного порошка и лимонной кислоты.
Из соды и/или горчицы и горячей воды удобнее всего приготовить кашицу и нанести на поверхность мягкой тканью.
Обычные или недавние загрязнения удаляются на глазах.
Застарелые – через несколько часов и при помощи жестких, но не царапающих, щеток.
Сильное потемнение можно удалить кипячением с раствором уксуса или лимонной кислоты, затем поверхность тщательно протереть содовым раствором для нейтрализации и тщательно промыть обычной водой.
Белый налет также счищается жесткой щеткой, смешенной с крупной солью. Кстати, неравномерные участки темнее-светлее – также говорят о неоднородности отливки.
Вода, кстати, особенно наша московская «родниковая» содержит в себе хлор, фтор и прочую таблицу Менделеева, так что после мытья формы лучше всего насухо вытирать, иначе после высыхания естественным путем, на форме останутся пятна и разводы.
Ну и, этааа. «Куличики», что в результате получается во всех этих формах.
И еще лайфхаки.
Из опыта – чем сложнее форма, тем гуще должна быть консистенция теста.
В штампованных формах удобно варить разнообразные пудинги, плотно запечатав их сверху фольгой и установив на водяную баню.
Литые формы можно вынуть из духовки немного раньше. Середина пирога успеет дойти до готовности за время остывания.
Из рекомендаций ГОСТ о подготовке хлебопекарных форм. Если форма не покрыта антипригарным покрытием, ее необходимо полностью покрыть растительным маслом и нагреть в печи для образования полимерной пленки.
Даже в непокрытых антипригарным покрытием формах, мы сами каждый раз создаем это покрытие, смазывая формы маслом и посыпая мукой, покрывая бумагой для выпечки. Единственный минус – пропитывать кекс фруктовым соком придется, вынув его из формы полностью остывшим.
Надеюсь, вы поняли, что всю эту алюминиевую простыню я написала с одной целью – похвастаться моими формами для выпечки. 🙂
Еще немного занимательного металловедения:
О «нержавеющей посуде»: http://shakherezada.livejournal.com/252068.html
О чугуне: http://shakherezada.livejournal.com/101954.html
И когда-то давно был еще пост в сообществе pracooking, ссылка утрачена.
О меди и латуни: http://shakherezada.livejournal.com/143149.html
Отчасти и здесь: http://shakherezada.livejournal.com/89065.html
shakherezada.livejournal.com
Отливка алюминиевых деталей дома – это просто! Литье по пенопластовым моделям
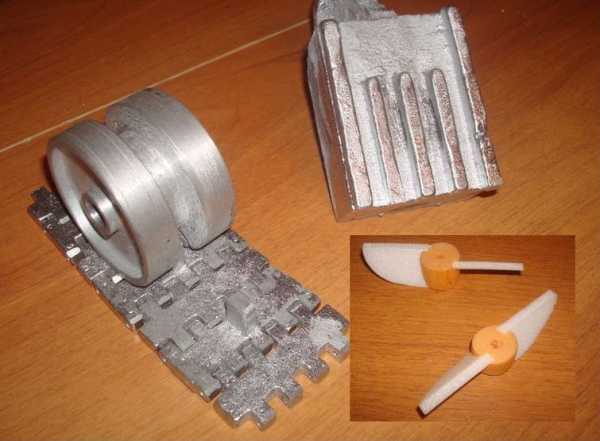
Описание моего способа литья небольших деталей из алюминия в домашних условиях.
В прошлой статье я достаточно подробно рассказал о том, как собрать миниатюрную муфельную печь из подручных материалов, чтобы отливать небольшие детали из алюминиевого сплава в домашних условиях, и лишь кратко о самом литье. В этой статье я постараюсь подробно описать то, каким образом отливаю я.Несмотря на то что я описываю способы, подходящие в принципе для отливки любых, даже самых сложных деталей, у самого меня потребности пока небольшие, а именно литье гусениц, катков и опорных рычагов для самодельного р/управляемого танка СУ-101. Постройки самого танка я касаться не буду, так же как и выкладывать какие то либо фото, отчет о постройки будет по окончании. Здесь же я постараюсь описать сам принцип.
Для работы мне требуется строительный гипс, разнообразные формы для смешивания и отливки, миксер (шуруповерт с насадкой), пенопласт (пенополистерол) и весь сопутствующий инструмент для работы с ним, место в очереди пользования духовкой (обмениваем абонементы у супруги на цветы, конфеты и прочие приятные взятки).
Изготовление модели. Я делаю из пенополистерола – плит теплоизоляции, продающихся в строительных магазинах, есть нескольких цветов и марок. Если нужен листовой определенного размера – режу нихромовой струной подключенной к трансформатору, детали круглой формы режу по лекалам. Наскоро изготовил несколько моделей чтобы наглядно продемонстрировать всю простоту. Отдельные детали модели скрепляю разведенным водой клеем для потолочной плитки (Титан), стараясь наносить минимальное количество. Все полости и швы следует также тщательно заклеивать, иначе при заливки гипсового раствора он затечет в них, а вот алюминий уже нет. К готовой модели необходимо сделать заливной канал, по которому будет затекать алюминий, его желательно делать побольше и подлиннее, чтобы алюминий тек в форму не только самотеком, но и на него немного давил алюминий в литнике. Вход в форму также стоит сделать побольше, чтобы не пришлось при заливке целиться в отверстие. После беглого изучения статей и форумов по металлургии и отливки, сделал вывод что объем литника спокойно может быть больше объема самого изделия. Когда пенопласт сгорает, газам нужно дать выход, поэтому следует предусмотреть газоотводные каналы. Я например втыкаю перед заливкой в модель алюминиевые присадочные прутки для аргонно-дуговой сварки, после затвердевания гипса их вытаскиваю.
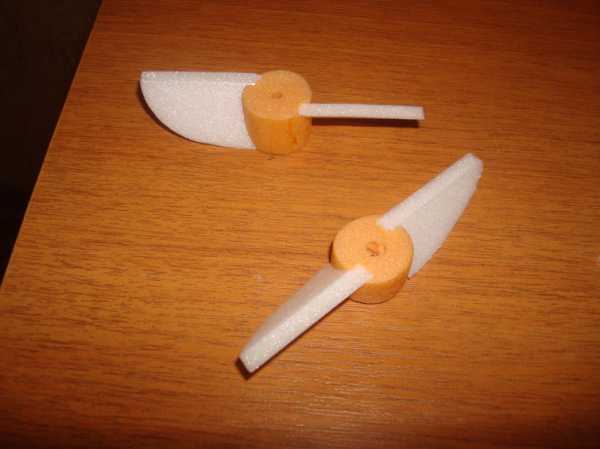
Заливка – дело очень быстрое. Все должно стоять наготове. У меня например гипс начинает схватываться меньше чем через 2 минуты после разведения смеси. Порядок такой – выбираю тару, куда буду заливать форму, исходя из размеров модели. В тару желательно положить полиэтиленовый мешок – это намного упростит извлечение формы после отвердевания. Наливаю в маленькое ведерко воды, объемом на четверть больше чем объем планируемой формы, в отдельной емкости уже насыпано гипса примерно столько же сколько и объем формы. Миксером (шуруповертом) начинаю мешать воду, понемногу но быстро добавляя приготовленный гипс. Консистенцию готовой смеси регулирую, добавляя гипс уже отдельной ложкой. Необходимая консистенция – жидкая сметана. Если гуще – схватиться еще быстрее, можно просто не успеть залить форму/повредить модель при заливке. Если жиже – форма будет рассыпчатой, излишки воды будут поверх формы, такую можно сразу выкидывать. Либо при сушке, либо при отливке она даст трещины и алюминий вытечет… Песок я как правило не добавляю, но он всегда есть под рукой. Иногда кладу, но немного, не более 4-5 части объема, в основном когда нужна большая форма, потому что из такой очень долго испаряется влага. Тару под форму достаточно просто изготовить из того же пенополистерола, используя клеевый пистолет. Даю гипсу схватиться и остыть, вытаскиваю и оставляю сушиться. Сушить в таре его бесполезно. Он конечно просохнет, эдак через пару лет))). Как правило неделю форма стоит в теплом сухом месте, лишь после этого ее можно сушить в духовке, понемногу увеличивая температуру.
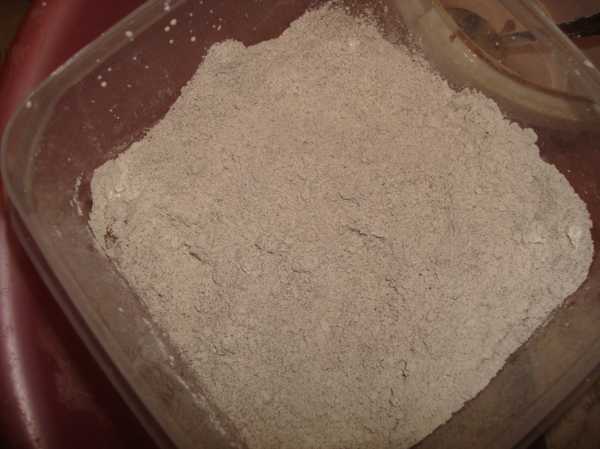
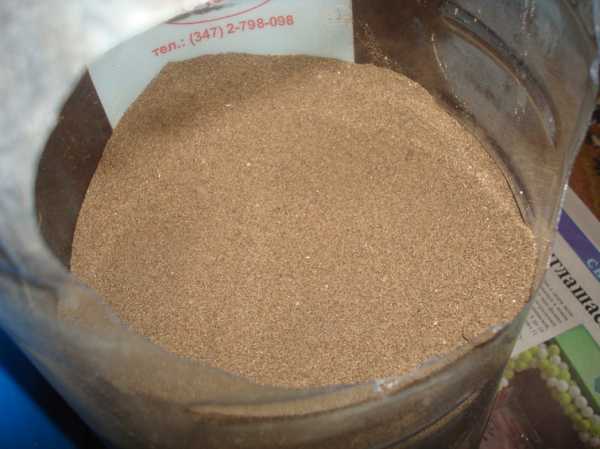

Отливка уже дело техники. Перед заливкой алюминия необходимо снять весь всплывший шлак и окислы, например нержавеющей ложкой. Форма в момент заливки должна стоять в каком нибудь металлическом подносе/тазике, на случай если расплавленный сплав протечет мимо. При заливке из формы идет огонь с дымом и копотью – вытяжка обязательна, причем нужно заливать форму до конца, несмотря на эти светопредставления, пока алюминий полностью не заполнит литник. После заливки оставляем форму до полного естественного остывания.
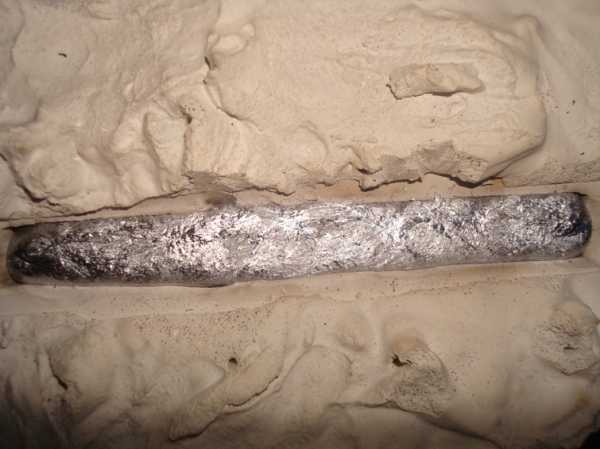
На фото ниже – часть заготовки для гусеницы и готовый ведомый каток для танка. Катки я отдаю для рихтовки после отливки знакомому токарю, он очень быстро и за симфолическую плату придает им идеально круглую форму. Также отлил заготовку для саркофага знакомому. Он хочет установить внутрь регулятор для своей TT eMTA.
П.С. сейчас начал делать формы полностью по технологии литья по газофицируемым моделям. Ее суть такова – пенопластовую модель на заливаю гипсом, его вообще почти не используют. Модель обмазывают газопроницаемой обмазкой на основе гипса/мела и засыпают в таре песком. При заливке алюминия, пенопласт выгорает и его газы выходят не через каналы как в гипсе, а прямо через стенки обмазки в песок (там создают разряжение насосом). Я решил чуть упростить, обмазываю, точнее окунаю дважды в гипс модель, потом засыпаю песком. Как будет свободное время, и просохнет обмазка – отолью первые экземпляры гребных винтов.
Спасибо за внимание!
www.parkflyer.ru
Изготовление пресс-форм для литья алюминия под давлением
Пресс-формы для литья алюминия
БЫСТРЫЙ ЗАКАЗ
Процесс производства пресс-форм – дорогостоящее и трудоемкое занятие, которое включает проектирование и само изготовление пресс-форм.
В процессе изготовления пресс-форм применяется инструментальная сталь в зависимости от того из какого материала изготавливается заготовка и от требований, предъявляемых к конструкции. Кроме того может использоваться немецкая сталь, дающая возможность производить формы для литья с высокой стойкостью и по низкой цене.
Процесс производства включает несколько этапов и в зависимости от сложности занимается от 2 до 12 недель.
Этапы производства:
1) Анализ технического задания
Заказчик передает техническое задание на пресс-форму. Техническое задание должно содержать: необходимые условия для эксплуатации, материал, объем литья изделий и другие требования. Учитвая эти требования наши инженеры рассчитаеют оптимальные параметры формы.
2) Чертеж изделия
Заказчику необходимо предоставить чертеж изделия либо образец, который нужно отлить, Заказчик предоставляет чертеж изделия либо образец отливки, для которого нужно изготовить пресс-форму.
3) Создание 3D-модели и конструкторской документации
Во время этого этапа проектируется 3D-моделя изделия, наглядно показывающая внешний вид необходимого изделия, которое будет получено на выходе. Также наша компания разрабатывает для вас конструкторскую документацию.
4) Тестирование образца и пресс-формы
Заказчик получает образец изделий, полученного с помощью требуемой пресс-формы. Вы выдаете свои замечания и если это необходимо мы дорабатываем форму.
5) Изготовление нужного количества пресс-форм
Мы изготавливаем требуемое количество пресс-форм, которое указано в техническом задании.
Наши преимущества:
![]() |
Собственное производство В распоряжении собственное оборудование и штат из 5 инженеров |
|
Высокая скорость выполнения заказов Мы осуществляем полный технологический цикл включая создание мастер модели и отливок внутри своей компании. |
|
Разумные цены Мы не отдаем работу подрядчикам, а выполняем ее сами. За счет этого мы предлагаем конкурентные цены |
Достойное качество продукции Все наши инженеры прошли обучение и сертифицированы. Это гарантирует отсутствие брака в вашей продукции |
Для определения стоимости и сроков производства пресс-форм направьте ваш запрос через форму или на почту:
В запрос нужно включить следующую информацию:
1. Фотография объекта
2. Размеры объекта (длина, ширина, высота в мм)
3. Любую необходимую дополнительную инфомарцию
Наше оборудование:
Наше производство
Пресс-формы для литья алюминия
Алюминий – популярный материал для производства различных деталей. Он отличается своей дешевизной, легкостью и качеством. Для изготовления таких деталей используются пресс-формы. Они необходимы, чтобы получить максимально качественный результат работ, точно соответствующий требованиям. Полученные детали впоследствии будут использованы в машиностроении и других промышленных сферах, поэтому качество их должно быть высочайшим.
Сегодня технологии позволяют получить пресс-формы для литья алюминия под давлением высокой производительности. Даже из одной формы вы получите большое количество отливок за короткий промежуток времени, что позволит обеспечить большое количество поставок изделий.
Изготовление пресс-форм для литья алюминия подразумевает использование технологической оснастки, характеризующейся высоким качеством и скоростью производства. Оборудование, которое применяют в данном процессе – это специальные литьевые машины и вспомогательные устройства.
Самые качественные изделия предлагает приобрести наш магазин, мы реализуем только продукцию от ведущих производителей, а перед продажей самостоятельно проверяем все товары.
Магазин также реализует принтеры объемной печати, на нашей технике установлено программное обеспечение rhinoceros для трехмерного моделирования. Оно позволяет максимально быстро реализовать процессы объемной печати и характеризуется бесперебойностью в работе.
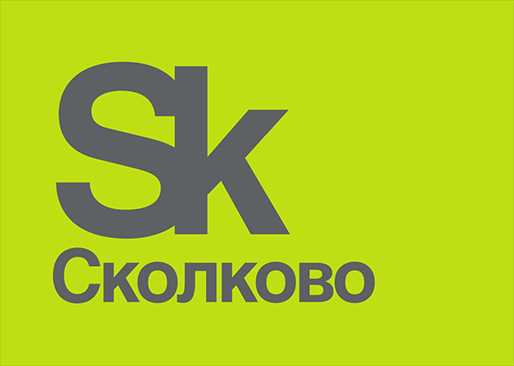
Владислав Зиновьев
“Мы долго искали подходящего поставщика. Не ожидал, что можно так оперативно купить 3д принтер и расходные материалы к нему в Санкт-Петербурге. Долго думали между DWS X FAB и Picaso Designer X PRO”
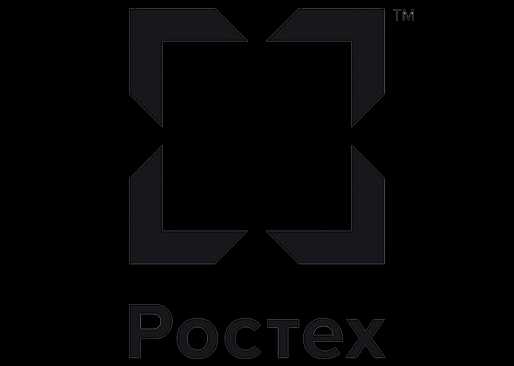
Вадим Евсеев
“Менеджеры не пытаются продать то, что вам не нужно. Вам подбирают модели по вашим задачам, материал подходящий. Мы это ценим, будем сотрудничать дальше.”
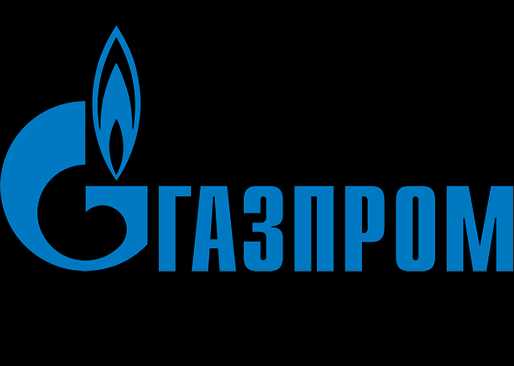
Вероника Захарова
“С магазином Top 3D Shop наша компания знакома уже давно. Сама техника отличная, работает не один год, расходники тоже самого высокого качества. Вежливость сотрудников и профессионализм, это так же присутствует в работниках этого магазина.”
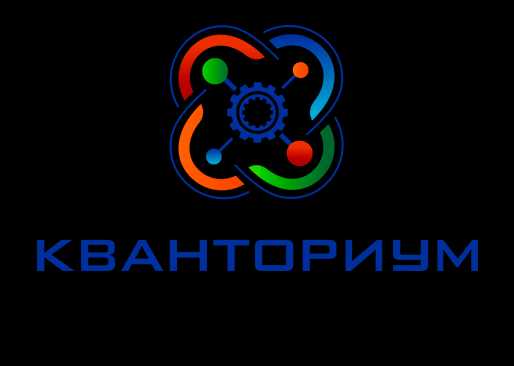
Пётр Нестеров
“Очень помог с доставкой при моём сложном графике менеджер Свириденко Илья. Доставили всё нам прямо в офис, прямо на мое рабочее место, вовремя и без малейших нервов. Однозначно буду работать с Вами в дальнейшем!”
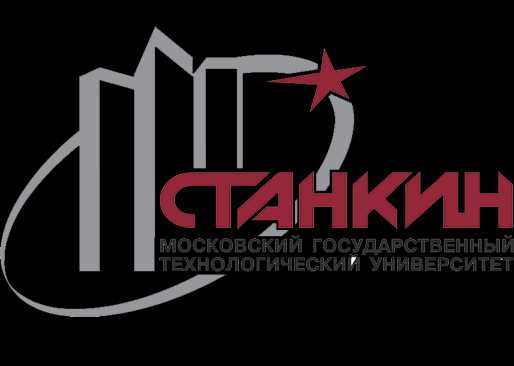
Леонид Беляков
“Ранее заказывал 3d принтер, проработал уже несколько месяцев, нареканий никаких, функционирует на отлично, помогает выполнять заказы вовремя. Сейчас, в очередной раз, заказал пластик, качество хорошее, подходит для модели моего принтера. Думаем над покупкой второго.”
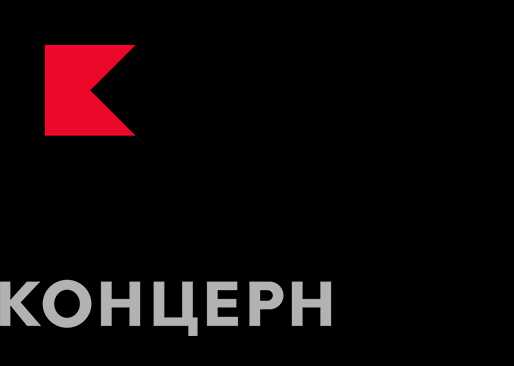
Филипп Ермаков
“Спасибо большое! Очень хорошее качество товара, вежливые и профессиональные сотрудники и конечно оперативность на высшем уровне! Мы довольны, будем продолжать сотрудничать.”
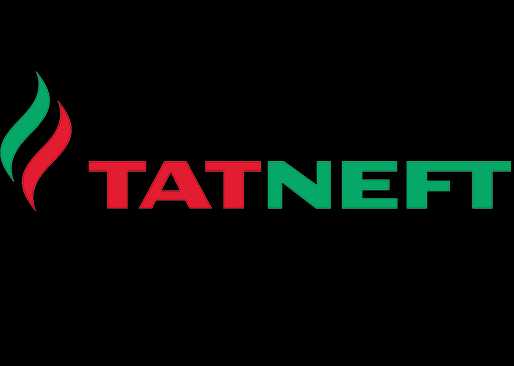
Ростислав Цветков
“Покупаю второй раз материал для 3D печати. Качеством доволен во всех направлениях. Уверен что и третий раз сюда обращусь! Полный комплект документов сразу, чтобы взять оборудование на баланс, всё круто. Молодцы.”
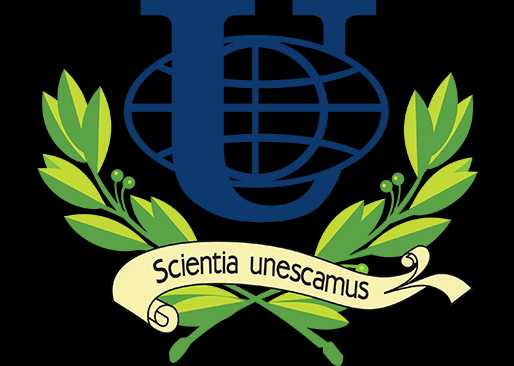
Владислав Юдин
“Обратная связь налажена и менеджеры имеют возможность консультировать по телефону сразу в режиме онлайн. Без них я вряд ли смог бы сделать достойный выбор. Подобрали оборудование по заявленным характеристикам очень быстро. Ближе к концу года будем брать еще.”
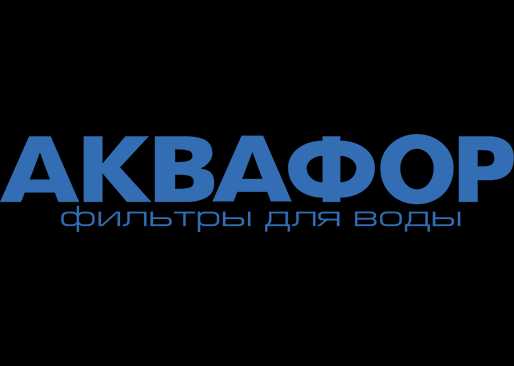
София Костюк
“Давно слышал от бизнес-коллег об этом интеграторе. Весьма удивило, что все цены, которые указаны на сайте, являются реальными и соответствуют действительности. Начали закупки, всё устраивает.”
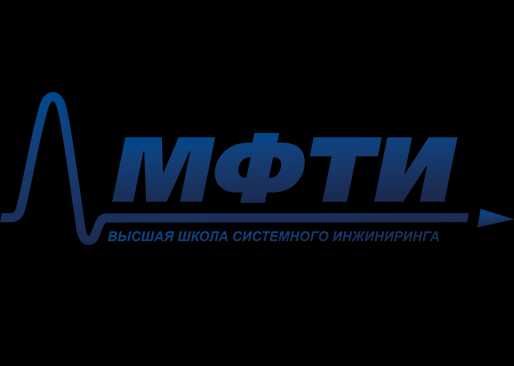
Яков Рожков
“Менеджер отреагировал мгновенно на заявку, отвечает на любые вопросы грамотно, посылку отправили на следующий день! Будем покупать еще и расширять парк техники.”
top3dshop.ru
Отливка алюминиевых деталей – это проще чем кажется! — Паркфлаер
Добрый день, моделисты. В этой статье я хотел бы подробно описать самый ПРОСТОЙ способ изготовления алюминиевых деталей любой сложности, а также наглядно его продемонстрировать.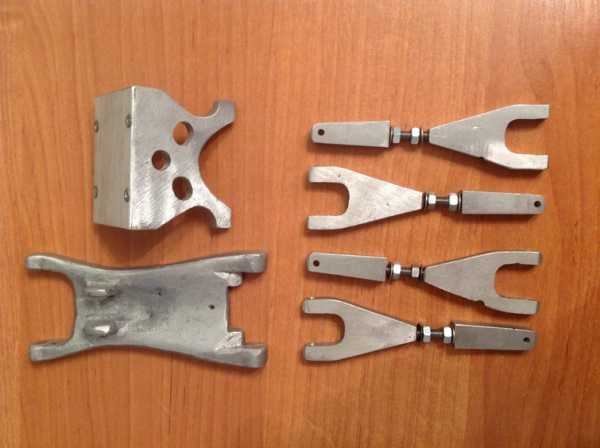
Теперь поговорим непосредственно о плавке.
Для изготовления детали вам потребуются:
1) Мозг и руки
2) Ёмкость для плавки
3) Всякий ненужный металлолом (я настоятельно рекомендую использовать ДЮРАЛЬ, потому как чистый алюминий обладает очень плохими литейными свойствами)
4) Форма
5) Паяльная лампа
6) 10 (или больше) кирпичей
ШАГ №1
Емкость для плавки можно элементарно изготовить из куска стальной трубы, приварив к ней дно.
(температура плавления дюрали около 650 градусов по Цельсию, поэтому сталь вполне подойдет)
Также рекомендую для большего удобства сделать сверху на трубе подобие “носика”
ШАГ №2
Теперь приступим к самому сложному – к изготовлению ФОРМЫ для отливки.В зависимости от сложности отливаемой детали форма может состоять как из одной части, так и из нескольких (в моем случае форма собирается из двух половинок)
В первую очередь вам необходимо максимально упростить деталь (заклеить скотчем все отверстия), чтобы в процессе отливки ничто не создавало препятствий на пути у расплавленной дюрали
Форму для литья проще всего изготовить из гипса (алебастр не желателен!). Лучше всего использовать скульптурный гипс.
Перед заливкой гипса емкость необходимо намазать чем-нибудь жирным, чтобы гипс не прилипал (масло, отработка, литол…), то же самое нужно сделать с моделью деталиЗаливать гипс следует осторожно, слегка потряхивая форму, чтобы выходили пузыри (некоторые даже используют специальные вибростолы)
ПРИМЕЧАНИЕ: Гипс очень быстро твердеет, поэтому нужно не “проморгать” тот момент когда уже пора засовывать модель в гипс.
Я забыл сказать, очень важно вместе с моделью положить в гипс какой-нибудь стержень(-ни) (палку), он будет впоследствии каналом(-ами) для заливки дюрали.
После того, как первый слой застыл, подготавливаем его для дальнейшей заливки.
Сверлим большим сверлом 4 неглубоких отверстия (они нужны, чтобы готовые половины форм не “ездили” относительно друг друга в процессе отливки), мажем верхнюю часть формы маслом.
Заливаем второй слой прямо поверх первого.
После затвердевания вынимаем форму из емкости и аккуратно разъединяем полученные половинки.
Наждачкой или ножом зачищаем неровности, а также на одной из половин ножовкой по металлу делаем несколько неглубоких (2-3мм) пропилов.
ПРИМЕЧАНИЕ: Сделать данные пропилы необходимо, т.к. они будут отверстиями для выхода газов при отливке (алюминий будет пузыриться, если их не сделать)
Далее обе половины формы КРАЙНЕ ВАЖНО высушить (чем суше будет форма, тем более качественной будет деталь). Сушить можно где угодно (даже в печи).
Непосредственно перед отливкой форму нужно покрыть сажей, чтобы жидкий алюминий не прилипал.
ШАГ №3
Из заранее подготовленных кирпичей складываем подобие печки (сама по себе паяльная лампа не расплавит дюраль) и накрываем верхнее отверстие печки какой-нибудь железной пластиной.
Плавим.
В процессе плавления на поверхности жидкой дюрали будет скапливаться “шлак”, его необходимо убирать.
Заливаем жидкий металл в форму и ждем пока остынет.Полученную заготовку шлифуем, отрезаем от нее ненужные части, сверлим необходимые отверстия.
Ну вот собственно и вся технология. Пробуйте, интересуйтесь и помните, что нет ничего невозможного.
www.parkflyer.ru
Литьё изделий из алюминиевых сплавов / Производство / Стирол-ГАЗ
Литье под давлением
Для получения качественных прочных деталей из алюминиевого сплава используется метод алюминиевого литья под давлением. Процесс происходит в прочных стальных разъемных формах с помощью специальных поршневых машин. Высокое давление нагнетается гидравлическим прессом или особым поршнем, который действует под влиянием сжатого газа или масляного состава горячим или холодным способом. Высокая скорость прессования и качество готовых деталей обеспечивается давлением в 100-200 атмосфер, под воздействием которого отливки приобретают 3-5 класс точности и стабильно ровную поверхность, которая характеризуется по 5-8 классу.
Благодаря высокой точности отливки готовые детали не нуждаются в шлифовке и полировании, а их качество позволяет использовать эти детали на ответственных участках, где важное значение приобретает их точность. Таким способом отливаются детали сложных форм, с тонкими стенками, а также те из них, которые предназначены для сложных конструкций и комплектаций. Отличные технические свойства деталей из алюминиевых сплавов, отлитых методом горячего прессования, позволяют использовать их для отливки комбинированных усиленных деталей с армированием из другого, более прочного металла.
Алюминиевое литье под давлением — более экономически выгодный и более безопасный экологически способ. В течение короткого промежутка времени можно выполнить несколько отливок, используя лишь одну пресс-форму. В связи с тем, что при этом способе не возникает потребности в использовании алюминиевых формовочных смесей, такое производство является менее вредным и более предпочтительным, а точность конструкций снижает затраты на расход металла и в целом на производство.
Минимальная допустимая толщина стенок: 0,8-1,2 мм.
Масса отливок — 8 кг.
Литье алюминия в кокиль
Второй популярный способ отливки деталей из алюминиевых сплавов называется кокилем. Это специальная металлическая разъемная или неразъемная форма, которая применяется для формовки простых и сложных деталей из алюминиевых сплавов. Для простых деталей используют неразъемные формы, готовые отливки просто вытряхивают из них с помощью специальных приспособлений. Разъемные кокиля могут быть с разными плоскостями разъемов:
- вертикальная;
- горизонтальная;
- криволинейная.
Кокиль с вертикальной плоскостью разъема состоит из двух половинок, точность соединения которых обеспечивается использованием особых втулок и штырей. Перед использованием формы нагревают до 270-300°С и покрывают специальной огнеупорной краской, затем в него устанавливают специальные стержни, максимально точно и прочно скрепляют обе половинки формы.
Жидкий алюминий заливают в форму-кокиль и оставляют до полного остывания. Этот процесс не отличается быстротой, поэтому для изготовления большого количества деталей необходимо соответствующее количество кокилей. Точность отливки при этом способе формовки соответствует 5-9 классам, неровность поверхности — 4-6 классу. По сравнению с отливкой деталей под высоким давлением, в этом случае расход металла на припуски увеличивается на 0,5-2 мм. Такой способ отливки, как алюминиевое литье в кокиль, также довольно экономичен, а детали отличаются высокой точностью и прочностью. Форму-кокиль можно использовать многократно.
Минимально допустимая толщина стенок — 1,5 мм.
Масса отливок от 20 г до 100 кг.
Литье в песчано-глинистые формы
Этот способ получения отливок является наиболее древним. Они выполняются из специальных смесей в виде двух полуформ, которые составляются вместе и образуют единый объем для заливки расплава. В верхней полуформе делают заливочную воронку литник и каналы для выхода воздуха и газов. Верхняя часть канала, отводящего газы, которая не входит в объем литой детали, называется прибылью. После остывания металла литник и прибыль должны быть удалены. Детали больших габаритов и весом до десятков тонн льют в формы, которые выполняют прямо в полу формовочного цеха. Форму для деталей небольших размеров делают в опоках, представляющих собой ящики, собираемые из пластин, образующих стенки опоки. Формовка осуществляется по моделям и шаблонам. Модель часто выполняется из дерева и повторяет объемные очертания будущей детали. Шаблоном называют профильные доски, которой формуют в песчано-глинистой смеси необходимую поверхность. При большом количестве и простой форме выпускаемых изделий формовка осуществляется с помощью формовочных машин по модельному комплекту.
Процесс изготовления литой детали включает в себя изготовление модели или специальных шаблонов, приготовление формовочной смеси, выполнение полуформ с литниками и газовыми каналами, сборку полуформ, заливку форм расплавом. Некоторое время выдерживают изделие для кристаллизации, а затем производят выбивку форм, т.е. разрушение формы для извлечения готовой детали. Далее очищают поверхности от остатков формовочной смеси металлическими щетками или с помощью пескоструйной машины, обрубают остатки литниковой системы, прибыли и облой. Облоем называют металл, застывший в зазоре между полуформами.
Литейное производство очень трудоемкое и вредное, поэтому его всегда стремятся механизировать и уменьшить долю ручного труда. Литье в песчано-глинистую форму позволяет получить детали сложной формы и уникальной конфигурации. При большом объеме производства применяют более прогрессивные методы образования форм и литья.
Минимально допустимая толщина стенок — 3 мм.
Масса отливок 150 кг.
stirol-s.ru
Литье алюминия по форме из пенопласта
Вступление
Растущая популярность алюминия
Алюминий является вторым по популярности металлом в мире после железа, и его рынок растет в два раза по сравнению с темпом рынка стали, хотя это происходит с гораздо более низкой базой.
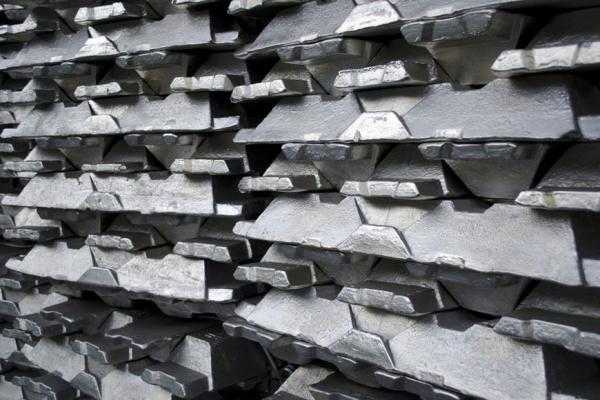
Алюминий также является самым распространенным металлом на земле, что составляет более 8% от массы ядра Земли, но его трудно дорабатывать по сравнению с железом. По этой причине использование алюминия отстает от других металлических изделий, в то время как для преодоления этих сложностей разрабатываются эффективные и экономичные методы. В середине 1880-х годов были изобретены два разных метода, которые последовательно используются для производства алюминия. В методе Байера используется химический процесс для извлечения алюминия из бокситов (обычная алюминиевая руда). В процессе Холла-Херульта используется электролиз для извлечения алюминия из оксида алюминия или оксида алюминия, полученного в результате процесса Байера.
Между алюминиевой и сталелитейной промышленностью существует много общего. Оба полагаются на извлечение металлов из минеральных руд, происходящих на земной поверхности. Процессы производства обоих энергоинтенсивны и включают заливку жидкого металла в отливки или с использованием машин непрерывного литья. Алюминий и сталь даже конкурируют на аналогичных рынках для автомобильной и аэрокосмической промышленности. Однако существуют существенные различия в обработке и свойствах этих металлов.
Производство и обработка
Большинство бокситов собирается из открытых шахтных операций в виде грязи, а не горной породы. Типичное содержание алюминия в бокситовой руде составляет от 45% до 60%.
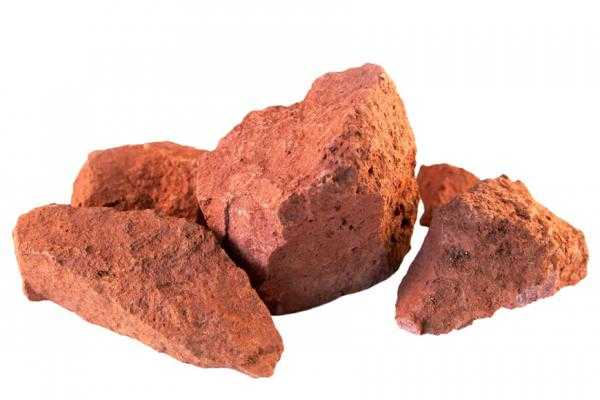
Процесс Байера
Бокситовая руда измельчается и смешивается с каустической содой для получения суспензии, содержащей мелкие частицы руды. Суспензию выдерживают при температуре от 140 до 280 ° С в зависимости от обрабатываемой конкретной руды. За это время алюминий растворяется в растворе каустической соды. Все примеси осаждаются из раствора в остаток, называемый красной грязью. Последним этапом процесса является добавление затравочных кристаллов в раствор каустической соды. Растворенный оксид алюминия присоединяется к этим затравочным кристаллам. Конечным продуктом из процесса Байера является оксид алюминия или оксид алюминия, который имеет вид белого порошка.
Процесс Холла-Херульта
Блок восстановления алюминиевого завода состоит из восстановительных горшков или ячеек, которые соединены последовательно. Каждый горшок изготовлен из стальной оболочки, облицованной углеродом. В каждый горшок выливают расплавленный криолит (фторид-минерал), содержащий оксид алюминия, и углеродные электроды вводят в раствор сверху. Ток проходит между углеродными электродами и углеродной подкладкой горшка. Когда ток проходит через раствор криолита, алюминий отделяется от кислорода, который присоединяется к углероду электродов, образующих газообразный диоксид углерода. Жидкий алюминий собирается на дне горшка.
Мощность для процесса исходит от постоянного тока через электроды. Напряжение поддерживается от 4 до 6 вольт, а генерируемый ток может достигать 4 KA. Мощность, подаваемая от электрического тока, удерживает раствор криолита примерно при 950 ° C.
Жидкий оксид алюминия всасывается из восстановительных горшков с регулярными интервалами в вакуумные ведра, переносится в печь, а затем наливается в слитки в пресс-формах или с помощью машины непрерывной разливки. Полученный через этот процесс алюминий составляет приблизительно 99,8%.
Как лить алюминий в пенопластовую форму
В этом видео мы покажем вам, как происходит литье алюминиевого пистолета, используя плавильную печь и форму из пенопласта, используя обычный песок и немного волшебства.
Для начала возьмите кусок пенопласта и снимите защитную пленку. После этого нарисуйте или распечатать изображение изделия, которое хотите сделать. Используйте рисунок для того, чтобы разрезать пенопласт на части. На видео вырезан пенопластовый пистолет, который уже выглядит неплохо, но чтобы сделать его алюминиевым, нам нужен песок. Кроме того, нам нужна небольшая плавильня, которую, кстати, можно найти на нашем сайте, а конкретно в этой статье. В ней мы расплавим несколько кусков металла, полученных из банок из под газировки или пива.
Насыпем немного песка в 20 литровое ведро, заполнив его минимум на 5-8 см. Возьмите пенопластовую форму и прикрепите воронку для вливания расплавленного металла, а затем вставьте ее вертикально в песок. Если мы подсыпем еще немного песка вокруг пенопластовой формы, она будет надежно держаться. Делая это, не засыпьте воронку, это очень важно.
Когда песок все закроет, немного потрясите ведро, чтобы выровнять его и заполнить все полости. Хорошей идеей будет также смочить верхний слой песка водой из распылителя. Тогда вы сможете сформировать кратер вокруг воронки, чтобы подстраховать себя при вливании металла.
Когда мы вливаем жидкий алюминий в воронку, пенопласт мгновенно испаряется, жидкий алюминий моментально занимает его место. Это происходит очень быстро. Так что наливайте алюминий достаточно быстро, но не слишком, чтобы не переборщить с металлом. Подождите около десяти минут, металл должен остыть, чтобы его можно было зацепить щипцами. Затем вытащите его из списка. Пенопластовая форма превратилась в цельную алюминиевую словно по волшебству. Если хотите улучшить внешний вид изделия, то примените напильник и наждачную бумагу.
Таким образом можно просто можно сделать что угодно цельнометаллическим. Кстати это также работает с изоляционным покрытием. Если поместить меч из розового пенополистирола, то 10 минут спустя можно достать из плавильни меч из цельного алюминия.
Про то статья, как лить пластмассу.
Шаг за шагом — простое алюминиевое литье в домашних условиях
Алюминиевые заготовки для литья
Вы можете расплавить практически любые алюминиевые банки, даже если кусок, который уже был отлит (например, водяной насос, колесо или впускной коллектор), будет иметь сплав, который лучше подходит для литья.
Алюминий льется около 1500 градусов, поэтому у вас есть надлежащий предохранительный механизм и огнетушитель под рукой.
01] Вот материал, который мы использовали для изготовления нашей собственной тигельной печи для плавки металла: 12-дюймовый терракотовый горшок, оцинкованная металлическая ткань, пластиковый плантатор, 90-градусный сливной слив и 60-фунтовый мешок бетона.
02] Мы разрезаем техническую ткань, чтобы поместиться внутри нашего пластикового контейнера, а затем разрезаем отверстие в боковом отверстии для прохода сливного фитинга. Дренаж был подключен к плантатору и тканевой ткани, чтобы он соответствовал отверстию на дне нашей терракотовой плантации и позволял нам добавлять воздух в наш огонь.
03] Смешанный бетон заливали в пластиковую плантацию до тех пор, пока она не встретила слив. Мы упаковали часть мокрого бетона в ткань, прежде чем мы упали в терракоту и упаковали бетон вокруг него. Мы дали ему четыре дня.
04] Мы использовали четыре куска 1 × 6-дюймового лома, чтобы сделать литейную колбу. Полоски из дерева в середине закрепляют литейный песок, так как нам нужно перевернуть колбу во время процесса литья. Мы решили пойти с простой одночастной формой с открытым верхом, чтобы создать педаль сцепления / тормоза, используя пряжку из латунного ремня в качестве рисунка. Так как это было что-то, что уже было нанесено один раз, пряжка имела хорошие шансы потянуть чисто от песка.
05] Мы получили 5 галлонов литейного песка от Alcast, местного литейного завода, который отливает все от топливных форсунок до голов Ford Foss 429. Вы можете сделать свой собственный литейный песок, но мы хотели удалить как можно больше переменных. Песок прекрасный и содержит связующие и воду, которые делают его немного липким. Вы знаете, что песок — это правильная консистенция, когда он сохраняет свою форму после формирования вручную.
06] Для просеивания песка по шаблону использовался оконный экран размером $ 7. Просеивание держит мелкий песок рядом с рисунком для более детального, плавного литья. Вы можете видеть сгустки песка, которые не проникали сквозь сетку.
07] Мы просеяли несколько сантиметров песка на наш узор, прежде чем мы использовали два-четыре, чтобы уплотнить песок вокруг рисунка. Просеивание нужно только на песке рядом с узором, поэтому мы просто уплотняли ложки песка, пока колба не была заполнена.
08] Затем мы осторожно подняли колбу и перевернули ее, чтобы раскрыть наш узор, полностью упакованный в плотный песок. Хотя песок слегка липкий и привязывается к себе, деревянные ребра в колбе дают песку физическую покупку внутри колбы.
09] Несколько отводов на задней части ремня-пряжки гарантировали, что он был свободным, прежде чем мы вытащили его бесплатно. Центр плесени был чистым, поэтому мы просто продували рыхлый песок с края и отложили узор.
10]. Чтобы наша печь нагревала воздух, мы построили воздуховоды из алюминиевой фольги и подключили ее к феном с «прохладной» кнопкой, записанной вниз. Розовая клейкая лента необязательна. Мы положили немного металлолома на дно, чтобы наш домашний тигель блокировал наш воздухозаборник, наполнил печь древесным углем, добавил наш металлолом и затем осветил его.
11] Как только весь уголь зажжен, мы положили верхнюю крышку из шлакоблока, и менее чем за 10 минут у нас был расплавленный алюминий на дне тигля.
12] Мы добавили дополнительный алюминий, и вскоре он тоже был расплавлен, но на верхушке был какой-то шлак.
13] Мы сняли шлак сверху с помощью набора длинноручных щипцов и обнаружили блестящий, чистый алюминий под ним.
14] Тигель, который мы построили из квадратной трубки, имеет два булавки на стороне, которые позволили нам использовать раздвоенный инструмент, чтобы вытащить его, и крюк, чтобы наклонить его. Не так элегантно, как щипцы, но они работали, и алюминий легко выливался.
15] Пустой алюминий может быть установлен в песке в нашей второй колбе, служившей в качестве пресс-формы для слитка алюминия в следующий раз.
16] Было сложно оставить нашу новоиспеченную часть достаточно долго, чтобы охладиться, но мы дали ей почти 30 минут. У нашей первой педали сцепления / тормоза была проблема с пористостью на поверхности, но мы скоро вернемся к ней.
Электролитический процесс производства алюминия чрезвычайно энергоемкий, требуя 15 Мвт на тонну продукции. Поэтому большинство плавильных заводов расположены рядом с генератором энергии, таким как гидроэлектростанции.
izobreteniya.net