Г 65 – 65
alexxlab | 18.09.2020 | 0 | Вопросы и ответы
Сталь марки 65г, её характеристики, ГОСТ и основные сферы применения
Что из себя представляет сталь марки 65 г? Она является многокомпонентной сталью, которую обычно используют как хороший конструкционный материал.
Как правило, пускается в ход в промышленности: в производство пружин рессоров, а также некоторых других изделий. Если же уходить от темы промышленного производства, то можно отметить изготовление спортивных метательных ножей и клинков для мечей.
Описание марки стали 65г
65 — содержание углерода в сплавах в сотых, а «г» — марганец (легирующий элемент).
Температура ковки стали: начала — 1250 °C, конца — 760−780°C.
65 г представляет собой износостойкий, вязкий, прочный, упругий материал, с хорошим сопротивлением разрыву и стойкостью к ударным нагрузкам.
Механические свойства стали — следующих категорий:
- 3;
- 3а;
- 3б;
- 3 г;
- 4;
- 4а;
- 4б.
Температура закалки — 830 °C, масляная. Температура отпуска — 470 °C.
Существует несколько видов поставки стали 65 г, одним из них является следующий:
ГОСТ 14959–79 — фасонный и сортовой прокат.
Технические характеристики и ГОСТ
Если это крайне необходимо, допускается замена стали 65 г, характеристики следующих марок достаточно похожи: 70, 70 г и некоторых других. А также материал имеет зарубежные аналоги, например: китайский аналог 65Mn, болгарский 65G, американские 1066, 1566, G15660 и некоторые другие.
Согласно ГОСТу 14959−79, в химическом составе этого металла содержатся следующие вхождения:
- углерод (C) — до 0,7% ;
- марганец (Mn) — до 1,2%;
- кремний (Si) — до 0,4%;
- и другие элементы, процентные доли которых составляют менее 0,035%.
В основу легировки данного вида стали ложится такой элемент, как марганец. Его доля в стали 65 г составляет от 0,9 процента до 1,2 процента.
Марганец необходим для того, чтобы: во-первых, устранять окислы железа, образующиеся при производстве литой стали, а во-вторых, — для увеличения твёрдости, повышения предела упругости и сопротивления разрыву. Также его наличие увеличивает плотность, что достаточно важно для пружинно-рессорной стали.
Также в составе стали 65 г есть кремний (от семнадцати сотых до четырёх десятых процента), который отвечает за повышение упругих свойств стали, и хром (до двадцати пяти десятых процента), в свою очередь, затрудняющий рост зерна при нагреве и повышающий механические свойства стали при таких нагрузках, как статические и ударные.
Из технологических характеристик стали можно отметить то, что она имеет низкую свариваемость, в связи с чем она не используется как элемент для свариваемых конструкций. КТС (контактно-точечная сварка) — без ограничений.
Способы применения стали:
Спиральные пружины, листовые и пружинные шайбы. Их твёрдость — Rc = 40−50. При приёме пружин обычно производится проверка их основных показателей — твёрдости и упругости. Проверка должна происходить максимально приближенной к обычным условиям работы пружин (растяжению, сжатию и изгибу).
Производство пружин
Отпуск
Основная сфера применения стали — использование при производстве пружинных изделий. Поступление металла производится обычно в виде прутьев, но возможны и другие варианты, такие, как листы и проволока, а также кованые заготовки.
На характеристики и качество готового продукта достаточно сильно влияет её термообработка.
При производстве изделий из сверхпрочной проволоки имеется необходимость подвергнуть элементы отпуску при температуре от 250 °C до 350 °C, эта процедура выполняется для снятия созданного при производстве внутреннего напряжения и, конечно, для повышения упругости витков изделия.
Вышеописанная процедура, как правило, осуществляется в селитровых ваннах, но может производится и в камерных электрических или нефтяных печах. В случае с электрическими печами время удержания составляет 10 минут, а в нефтяных — 40 минут.
Чтобы нагреть пружины для закалки, их помещают в заранее нагретые до определённой температуры соляные ванны или камерные печи. Во избежание деформации крупноразмерных изделий они подвергаются нагреву в приспособлении, специально для этого предназначенном.
Малоразмерные пружины
Малоразмерные пружины для закалки в печи помещают на специальном противне. Необходимо сократить время выдержки в печи до минимума для того, чтобы предотвратить окисление и обезуглероживание. Чтобы уменьшить время пребывания мелких пружин в печи, их кладут на заранее разогретый до определённой температуры противень.
Если в печи отсутствует защитная атмосфера, пружины подлежат упаковке в изолирующей среде, а также выполняется заброс небольшим количеством древесного угля.
Охлаждение пружин производится в масле. В воде охлаждать крайне не рекомендуется, так как могут возникнуть трещины на поверхности. Если охлаждение в воде необходимо, то время выдержки должно составлять 2−3 секунды, после чего нужно поместить готовый продукт в масло.
Отпуск малоразмерных пружин
Перед тем как отпустить пружины, их необходимо очистить от масла методом промывки содовым раствором или методом протирки в опилках. Если после очистки на поверхности пружин останется неудаленное масло, то при отпуске оно может вспыхнуть и изменять условия процедуры отпуска. Рекомендуемая температура отпуска — от 300 до 420 градусов по Цельсию. Крайние витки необходимо отжигать в свинцовой ванне.
Перед отпуском крупные пружины необходимо надеть на толстые трубы во избежание коррозии при нагреве.
Необходимо обращать внимание на поверхность материала, предназначенного для изготовления пружин. Всевозможные дефекты могут привести к трещинам, а обезуглероживание верхнего слоя приводит к снижению упругости изделия.
Зачастую при использовании антикоррозийных покрытий, иногда используемых для нанесения, пружины становятся хрупкими из-за перенасыщения стали водородом. Очень сильно это замечается на пружине из проволоки или из лент малых сечений. Такая хрупкость называется травильной и исправляется путём нагрева готового продукта в сушильном шкафу при температуре 150−180 градусов по Цельсию в течение 1,5−2 часов.
При большом времени травления происходит настолько сильное насыщение металла водородом, что температурная обработка не помогает устранить хрупкость и возникает необходимость отжига пружин. Чтобы избежать перенасыщения стали водородом, следует отказаться от травления перед процессом покрытия, а необходимо подвергнуть их очистке струёй песка и нагревать только после покрытия методом, описанным выше.
Пружины из отожжённого металла
Если пружины будут изготавливаться из отожжённого металла, то тогда, скорее всего, может быть необходимо не только закалить металл, так как основную роль будет играть его твёрдость. Например, при использовании в производстве толстой (более 6 мм) проволоки есть необходимость производить отпуск при температуре около 720 градусов по Цельсию. Делается это для того, чтобы придать готовому изделию прочности и только затем произвести закалку. Касаемо тех деталей, что навиваются в разогретом виде: в любом случае, здесь необходима нормализация, которая выполняется в самом начале обработки металла, перед остальными процессами.
tokar.guru
Сталь 65 Г термообработка – Термообработка
попытка вставить кучу таблиц.
Сталь 65Г
________________________________________
Общие сведения
Заменитель
стали: 70, У8А, 70Г, 60С2А, 9Хс, 50ХФА, 60С2, 55С2.
Вид поставки
Сортовой прокат, в том числе фасонный: ГОСТ 14959-79, ГОСТ 2590-71, ГОСТ 2591-71, ГОСТ 2879-69, ГОСТ 7419.0-78 – ГОСТ 7419.8-78. Калиброванный пруток ГОСТ 14959-79, ГОСТ 7417-75, ГОСТ 8559-75, ГОСТ 8560-78, ГОСТ 1051-73. Шлифованный пруток и серебрянка ГОСТ 14955-77, ГОСТ 7419.0-78 – ГОСТ 7419.8-78. Лист толстый ГОСТ 1577-81. Лента ГОСТ 1530-78, ГОСТ 2283-79, ГОСТ 21996-76, ГОСТ 21997-76, ГОСТ 10234-77, ГОСТ 19039-73. Полоса ГОСТ 103-76, ГОСТ 4405-75. Проволока ГОСТ 11850-72. Поковки и кованые заготовки ГОСТ 1133-71.
Назначение
пружины, рессоры, упорные шайбы, тормозные ленты, фрикционные диски, шестерни, фланцы, корпусы подшипников, зажимные и подающие цанги и другие детали, к которым предъявляются требования повышенной износостойкости, и детали, работающие без ударных нагрузок.
________________________________________
Химический состав
Химический элемент %
Кремний (Si) 0.17-0.37
Медь (Cu), не более 0.20
Марганец (Mn) 0.90-1.20
Никель (Ni), не более 0.25
Фосфор (P), не более 0.035
Хром (Cr), не более 0.25
Сера (S), не более 0.035
________________________________________
Механические свойства
Механические свойства
Термообработка, состояние поставки Сечение, мм 0,2, МПа B, МПа 5, % , % HRCэ
Сталь категорий: 3,3А,3Б,3В,3Г,4,4А,4Б. Закалка 830 °С, масло, отпуск 470 °С. Образцы 785 980 8 30
Листы нормализованные и горячекатаные 80 730 12
Закалка 800-820 °С, масло. Отпуск 340-380 °С, воздух. 20 1220 1470 5 10 44-49
Закалка 790-820 °С, масло. Отпуск 550-580 °С, воздух. 60 690 880 8 30 30-35
Механические свойства при повышенных температурах
t испытания, °C 0,2, МПа B, МПа 5, % , %
Закалка 830 °С, масло. Отпуск 350 °С.
200 1370 1670 15 44
300 1220 1370 19 52
400 980 1000 20 70
Механические свойства в зависимости от температуры отпуска
t отпуска, °С 0,2, МПа B, МПа 5, % , % KCU, Дж/м2 HRCэ
Закалка 830 °С, масло.
200 1790 2200 4 30 5 61
400 1450 1670 8 48 29 46
600 850 880 15 51 76 30
Технологические свойства
Температура ковки
Начала 1250, конца 780-760. Охлаждение заготовок сечением до 100 мм производится на воздухе, сечения 101-300 мм – в мульде.
Свариваемость
не применяется для сварных конструкций. КТС – без ограничений.
Обрабатываемость резанием
В закаленном и отпущенном состоянии при НВ 240 и B = 820 МПа K тв.спл. = 0,85, K б.ст. = 0,80.
Склонность к отпускной способности
склонна при содержании Mn>=1\%
Флокеночувствительность
малочувствительна
________________________________________
Температура критических точек
Критическая точка °С
Ac1 721
Ac3 745
Ar3 720
Ar1 670
Mn 270
________________________________________
Ударная вязкость
Ударная вязкость, KCU, Дж/см2
Состояние поставки, термообработка +20 0 -20 -30 -70
Закалка 830 С. Отпуск 480 С. 110 69 27 23 12
________________________________________
Предел выносливости
-1, МПа -1, МПа B, МПа 0,2, МПа Термообработка, состояние стали
725 431 Закалка 810 С, масло. Отпуск 400 С.
480 284 Закалка 810 С, масло. Отпуск 500 С.
578 1470 1220 НВ 393-454 [84]
647 1420 1280 НВ 420
725 1690 1440 НВ 450
________________________________________
Прокаливаемость
Закалка 800 °С.
Расстояние от торца, мм / HRC э
1.5 3 4.5 6 9 12 15 18 27 39
58,5-66 56,5-65 53-64 49,5-62,5 41,5-56 38,5-51,5 35,5-50,5 34,5-49,5 35-47,5 31-45
Кол-во мартенсита, % Крит.диам. в воде, мм Крит.диам. в масле, мм Крит. твердость, HRCэ
50 30-57 10-31 52-54
90 До 38 До 16 59-61
________________________________________
Физические свойства
Температура испытания, °С 20 100 200 300 400 500 600 700 800 900
Модуль нормальной упругости, Е, ГПа 215 213 207 200 180 170 154 136 128
Модуль упругости при сдвиге кручением G, ГПа 84 83 80 77 70 65 58 51 48
Плотность, pn, кг/см3 7850 7830 7800 7730
Коэффициент теплопроводности Вт/(м •°С) 37 36 35 34 32 31 30 29 28
Температура испытания, °С 20- 100 20- 200 20- 300 20- 400 20- 500 20- 600 20- 700 20- 800 20- 900 20- 1000
Коэффициент линейного расширения (a, 10-6 1/°С) 11.8 12.6 13.2 13.6 14.1 14.6 14.5 11.8
Удельная теплоемкость (С, Дж/(кг • °С)) 490 510 525 560 575 590 625 705
Если надо то могу файлик этот скинуть на мыло…
www.chipmaker.ru
Закалка пружинно-рессорной стали 65гМастерская “Зброевы фальварак”
И холодное оружие согревает душу. Ара Багдасарян
Мастерская «Зброевы фальварак» на протяжении нескольких лет занимается изготовлением мечей и иного клинкового оружия для рыцарских фестивалей. Основной маркой стали, с которой работает наша мастерская, является сталь 65г.
Данная сталь в силу своих свойств, считается одной из лучших для изготовления длинноклинкового оружия предназначенного для рыцарских турниров.
Однако свойства стали, которые приобретаются в ходе изготовления меча, во многом есть результат правильной термической обработки. Так как же производится закалка стали 65г?
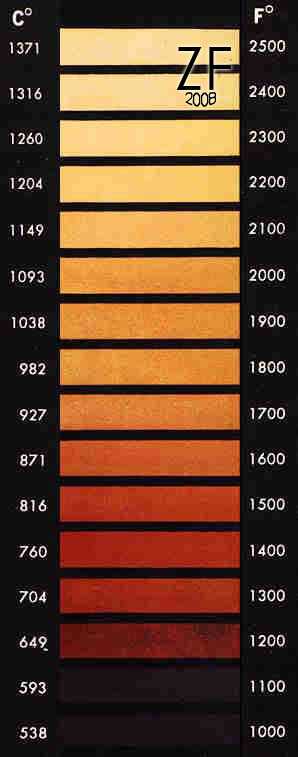
Нагрев стали, цвет в зависимости от температуры
Согласно справочнику, термообработка клинка должна происходить при следующих показателях:
закалка 830 (масло), отпуск 470 (воздух) HRC 38-45
закалка 810 (масло), отпуск 360 (воздух) HRC 44-49
закалка 830 (масло), отпуск 200 (воздух) HRC 44-49
В зависимости от толщины и площади детали, при отпуске от 200 до 400 градусов, может быть получена твердость в 55 единиц.
В случае с нашей мастерской, мы даем закалку на клинок в 52-55 единиц, соответственно закалка клинка происходит при температуре 830, а отпуск при 200 градусах. Конечно, это большая твердость для стали 65г, в этом процессе главное опытность термиста, потому что не правильно каленый клинок станет хрупким. Нужно чтобы клинок был достаточно мягким, т.е. при ударе о кромку лезвия не возникало сколов, кромка должна проминаться, а не откалываться.
Испытания нашей мастерской показали, что наши клинки соответствуют данным требованиям. Но еще раз, хочется повториться, что в деле термической обработки самое важное, это опыт термиста.
Сам процесс термической обработки стали происходит так:
Клинок перед закалкой нужно подогреть, а затем положить на коробчатый или П-образный противень и засыпать слоем отработанного древесно-угольного карбюризатора (так же может использоваться бура, у нее есть положительные свойства. Клинок после термообработки в среде буры требует меньшей шлифовки. Затем печка нагревается до температуры 830 градусов и выдерживается определенное время, в зависимости от толщины заготовки, в нашем случае клинка. Затем меч достается из печи и погружается в бак с маслом. Нужно помнить, что горячие детали с углем могут вспыхнуть и посему нужно быть осторожным при выполнении этого процесса. Также, нужно не забывать, что детали не должны успеть остыть после того как будут извлечены из печи. То есть бак с маслом должен находиться на весьма близком расстоянии от печи. Будет правильным, после закалки в масле обезжирить заготовку в горячем (90 град.) водном растворе ПАВ, например «Фери» или более дешевых аналогах. В крайнем случае, можно обезжирить клинок таким способом: дать маслу стечь, и просушить при температуре около 300 градусов, 2 часа, в результате масло высохнет, после чего можно делать отпуск на заданную твердость.
Небольшие заготовки охлаждаются на воздухе, крупные — в замкнутом пространстве (ящике).
Если требования к твердости не предъявляются, то можно и вообще не калить. Сделайте отжиг-нормализацию. Получите мелкозернистую, ровную структуру. Что касается времени отпуска, то есть правило. Чем больше углерода в стали, тем меньше должна быть скорость нагрева (это правило касается и отжига и закалки).
В целом, этот процесс требует большого опыта, т.е. сделать все по инструкции в данном случаи не получится.
Поэтому ищите хорошего термиста или готовьтесь к серьезному испытанию и материальным затратам.
Чем резать листовую сталь 65г, и листовой дюраль Д16АТ?
zbroevy-falvarak.by
65Г
Марка стали 65Г
Общие сведения
Заменитель |
стали: 70, У8А, 70Г, 60С2А, 9Хс, 50ХФА, 60С2, 55С2. |
Вид поставки |
Сортовой прокат, в том числе фасонный: ГОСТ 14959-79, ГОСТ 2590-71, ГОСТ 2591-71, ГОСТ 2879-69, ГОСТ 7419.0-78 – ГОСТ 7419.8-78. Калиброванный пруток ГОСТ 14959-79, ГОСТ 7417-75, ГОСТ 8559-75, ГОСТ 8560-78, ГОСТ 1051-73. Шлифованный пруток и серебрянка ГОСТ 14955-77, ГОСТ 7419.0-78 – ГОСТ 7419.8-78. Лист толстый ГОСТ 1577-81. Лента ГОСТ 1530-78, ГОСТ 2283-79, ГОСТ 21996-76, ГОСТ 21997-76, ГОСТ 10234-77, ГОСТ 19039-73. Полоса ГОСТ 103-76, ГОСТ 4405-75. Проволока ГОСТ 11850-72. Поковки и кованые заготовки ГОСТ 1133-71. |
Назначение |
пружины, рессоры, упорные шайбы, тормозные ленты, фрикционные диски, шестерни, фланцы, корпусы подшипников, зажимные и подающие цанги и другие детали, к которым предъявляются требования повышенной износостойкости, и детали, работающие без ударных нагрузок. |
Химический состав
Химический элемент | % |
Кремний (Si) | 0.17-0.37 |
Медь (Cu), не более | 0.20 |
Марганец (Mn) | 0.90-1.20 |
Никель (Ni), не более | 0.25 |
Фосфор (P), не более | 0.035 |
Хром (Cr), не более | 0.25 |
Сера (S), не более | 0.035 |
Механические свойства
Механические свойства
Термообработка, состояние поставки | Сечение, мм | s 0,2 , МПа | s B , МПа | d 5 , % | y , % | HRC э |
Сталь категорий: 3,3А,3Б,3В,3Г,4,4А,4Б. Закалка 830 °С, масло, отпуск 470 °С. | Образцы | 785 | 980 | 8 | 30 | |
Листы нормализованные и горячекатаные | 80 | 730 | 12 | |||
Закалка 800-820 °С, масло. Отпуск 340-380 °С, воздух. | 20 | 1220 | 1470 | 5 | 10 | 44-49 |
Закалка 790-820 °С, масло. Отпуск 550-580 °С, воздух. | 60 | 690 | 880 | 8 | 30 | 30-35 |
Механические свойства при повышенных температурах
t испытания, °C | s 0,2 , МПа | s B , МПа | d 5 , % | y , % | ||||||||||
Закалка 830 °С, масло. Отпуск 350 °С. | ||||||||||||||
200 | 1370 | 1670 | 15 | 44 | ||||||||||
300 | 1220 | 1370 | 19 | 52 | ||||||||||
400 | 980 | 1000 | 20 | 70 |
Механические свойства в зависимости от температуры отпуска
t отпуска, °С | s 0,2 , МПа | s B , МПа | d 5 , % | y , % | KCU, Дж/м 2 | HRC э | ||||||||
Закалка 830 °С, масло. | ||||||||||||||
200 | 1790 | 2200 | 4 | 30 | 5 | 61 | ||||||||
400 | 1450 | 1670 | 8 | 48 | 29 | 46 | ||||||||
600 | 850 | 880 | 15 | 51 | 76 | 30 |
Технологические свойства
Температура ковки |
Начала 1250, конца 780-760. Охлаждение заготовок сечением до 100 мм производится на воздухе, сечения 101-300 мм – в мульде. |
Свариваемость |
не применяется для сварных конструкций. КТС – без ограничений. |
Обрабатываемость резанием |
В закаленном и отпущенном состоянии при НВ 240 и s B = 820 МПа K u тв.спл. = 0,85, K u б.ст. = 0,80. |
Склонность к отпускной способности |
склонна при содержании Mn>=1% |
Флокеночувствительность |
малочувствительна |
Температура критических точек
Критическая точка | °С |
Ac1 | 721 |
Ac3 | 745 |
Ar3 | 720 |
Ar1 | 670 |
Mn | 270 |
Ударная вязкость
Ударная вязкость, KCU, Дж/см 2
Состояние поставки, термообработка | +20 | 0 | -20 | -30 | -70 |
Закалка 830 С. Отпуск 480 С. | 110 | 69 | 27 | 23 | 12 |
Предел выносливости
s -1 , МПа | t -1 , МПа | s B , МПа | s 0,2 , МПа | Термообработка, состояние стали |
725 | 431 | Закалка 810 С, масло. Отпуск 400 С. | ||
480 | 284 | Закалка 810 С, масло. Отпуск 500 С. | ||
578 | 1470 | 1220 | НВ 393-454 [84] | |
647 | 1420 | 1280 | НВ 420 | |
725 | 1690 | 1440 | НВ 450 |
Прокаливаемость
Закалка 800 °С.
Расстояние от торца, мм / HRC э | |||||||||||
1.5 | 3 | 4.5 | 6 | 9 | 12 | 15 | 18 | 27 | 39 | ||
58,5-66 | 56,5-65 | 53-64 | 49,5-62,5 | 41,5-56 | 38,5-51,5 | 35,5-50,5 | 34,5-49,5 | 35-47,5 | 31-45 |
Кол-во мартенсита, % | Крит.диам. в воде, мм | Крит.диам. в масле, мм | Крит. твердость, HRCэ |
50 | 30-57 | 10-31 | 52-54 |
90 | До 38 | До 16 | 59-61 |
Физические свойства
Температура испытания, °С | 20 | 100 | 200 | 300 | 400 | 500 | 600 | 700 | 800 | 900 |
Модуль нормальной упругости, Е, ГПа | 215 | 213 | 207 | 200 | 180 | 170 | 154 | 136 | 128 | |
Модуль упругости при сдвиге кручением G, ГПа | 84 | 83 | 80 | 77 | 70 | 65 | 58 | 51 | 48 | |
Плотность, pn, кг/см3 | 7850 | 7830 | 7800 | 7730 | ||||||
Коэффициент теплопроводности Вт/(м ·°С) | 37 | 36 | 35 | 34 | 32 | 31 | 30 | 29 | 28 | |
Температура испытания, °С | 20- 100 | 20- 200 | 20- 300 | 20- 400 | 20- 500 | 20- 600 | 20- 700 | 20- 800 | 20- 900 | 20- 1000 |
Коэффициент линейного расширения (a, 10-6 1/°С) | 11.8 | 12.6 | 13.2 | 13.6 | 14.1 | 14.6 | 14.5 | 11.8 | ||
Удельная теплоемкость (С, Дж/(кг · °С)) | 490 | 510 | 525 | 560 | 575 | 590 | 625 | 705 |
neva-stal.ru
что это такое и где используется
Сталь 65Г относится к группе пружинно-рессорных легированных сталей.
Данное изделие очень популярно, а также оно широко используется в сферах промышленности и народном использовании, из-за того, что материал имеет высокие показатели по механическим характеристикам и показателям прочности.
Такая сталь поставляется покупателям, как сортовой или фасонный прокат.
Специализированные организации отгружают круги, полосы, квадраты и листы из стали 65Г.
Содержание:
1. Главные и характерные особенности
2. Особенности применения
Главные и характерные особенности
Главным легирующим компонентом в этом сплаве является марганец, содержание которого составляет от 0.9 до 1.2%. Также стоит отметить, что сталь 65Г содержит кремний в пределах 0.37% и хром в пределах 0.25%.
Именно это сочетание и обеспечивает основные эксплуатационные показатели.
Марганец здесь имеет две важнейшие функции. Первая – обеспечение и выведение окислов железа, которые способны появляться при процессе литейного производства. Вторая – ответственность за повышенные механические показатели.
Внедрение марганца в состав стали обеспечит повышение твёрдости и сопротивление на разрыв, в большой степени повысит пределы показателей упругости металла. Также стоит отметить, что благодаря марганцу повышается и плотность металла.
При использовании кремния, изделие приобретёт высокие свойства упругости. Кремний немного уменьшит ударную вязкость. Однако, повысит показатель сопротивляемости к ударам, статическим нагрузкам и жароустойчивости.
Исходя из вышесказанного, важно отметить, что лист сталь 65Г имеет прекрасную комбинацию механических показателей. Сталь обладает повышенной износостойкостью и стойкостью.
Высокая вязкость и показатель упругости позволит стали выдержать повышенные деформации без потерь важных эксплуатационных качеств.
Особенности применения
Сталь 65Г имеет очень широкую область использования.
Такая сталь применяется для создания деталей для машин, а также механизмов и деталей, которые работают под постоянными и высокими нагрузками.
Круги, полосы, листы и квадраты 65Г обычно используются для создания пружин и рессор, диск, лент для тормозов.
Часто из стали изготавливаются шестерёнки, корпуса подшипников и разнообразные детали. Кроме того, такая сталь применяется при производстве ножевых изделий.
otopleniedomov.com
Сталь 65Г – характеристики и химический состав
Сталь марки 65Г – поставки со склада. Отгрузка партиями любого объема в день оплаты.
Характеристики
Рессорно-пружинная сталь характеризуется повышенной износостойкостью, при этом относительно дешева. Именно эти характеристики позволили данному виду стали найти широкое применение в машиностроении.
Шайбы, пружины и рессоры, корпуса подшипников, тормозные ленты и диски, фланцы и шестерни, подающие и зажимные цанги, а также прочие элементы узлов и конструкций – все это изготавливается из стали. Как правило из нее изготовлены листовые рессоры заднего моста в грузовых автомашинах. Сталь 65Г не применяется в сварных конструкциях и для работы с ударной нагрузкой.
Как и любая пружинно-рессорная сталь, обладает хорошими режущими свойствами и поддается оксидированию (воронению, чернению). Полоса или лист 65Г успешно применяются для изготовления ножей. В основном из этой стали изготавливают метательные ножи, реже – разделочные. Методом ковки изготавливают казацкие шашки. Считается, что сталь 65Г один из самых дешевых материалов для изготовления ножей, так что ножи из этой стали будут делать еще долго.
Наша продукция
Химический состав
C | Si | Mn | Ni | S | P | Cr | Cu |
---|---|---|---|---|---|---|---|
0.62-0.7 | 0.17-0.37 | 0.9-1.2 | до 0.25 | до 0.035 | до 0.035 | до 0.25 | до 0.2 |
Физические свойства стали 65Г
T | E 10-5 | a106 | l | r | C | R 109 |
---|---|---|---|---|---|---|
Град | МПа | 1/Град | Вт/(м·град) | кг/м3 | Дж/(кг·град) | Ом·м |
20 | 2.15 | 37 | 7850 | |||
100 | 2.13 | 11.8 | 36 | 7830 | 490 | |
200 | 2.07 | 12.6 | 35 | 7800 | 510 | |
300 | 2.00 | 13.2 | 34 | 525 | ||
400 | 1.80 | 13.6 | 32 | 7730 | 560 | |
500 | 1.70 | 14.1 | 31 | 575 | ||
600 | 1.54 | 14.6 | 30 | 590 | ||
700 | 1.36 | 14.5 | 29 | 625 | ||
800 | 1.28 | 11.8 | 28 | 705 | |
www.str-invest.ru
65Г в Челябинске
- Главная
- Сталь конструкционная рессорно-пружинная
- 65Г
Марка: | 65Г |
Заменитель: | 70, У8А, 70Г, 60С2А, 9ХС, 50ХФА, 60С2, 55С2 |
Классификация: | Сталь конструкционная рессорно-пружинная |
Применение: | пружины, рессоры, упорные шайбы, тормозные ленты, фрикционные диски, шестерни, фланцы, корпусы подшипников, зажимные и подающие цанги и другие детали, к которым предъявляются требования повышенной износостойкости, и детали, работающие без ударных нагрузок. |
Химический состав в % материала 65Г
C | Si | Mn | Ni | S | P | Сr | Cu |
---|---|---|---|---|---|---|---|
0.62 – 0.7 | 0.17 – 0.37 | 0.9 – 1.2 | до 0.25 | до 0.035 | до 0.035 | до 0.25 | до 0.2 |
Температура критических точек материала 65Г
Ac1 = 721, Ac3(Acm) = 745, Ar3(Arcm) = 720, Ar1 = 670, Mn = 270
Механические свойства при Т=20oС материала 65Г
Сортамент | Размер | Напр. | σв | σт | δ5 | ψ | KCU | Термообр. |
---|---|---|---|---|---|---|---|---|
– | мм | – | МПа | МПа | % | % | кДж/м2 | – |
|
| 980 | 785 | 8 | 30 |
| Состояние поставки |
Физические свойства материала 65Г
T | E 10-5 | α106 | λ | ρ | С | R109 |
---|---|---|---|---|---|---|
Град | МПа | 1/Град | Вт(м·град) | кг/м3 | Дж(кг·град) | Ом·м |
20 | 2.15 |
| 37 | 7850 |
|
|
100 | 2.13 | 11.8 | 36 | 7830 | 490 |
|
200 | 2.07 | 12.6 | 35 | 7800 | 510 |
|
300 | 2 | 13.2 | 34 |
| 525 |
|
400 | 1.8 | 13.6 | 32 | 7730 | 560 |
|
500 | 1.7 | 14.1 | 31 |
| 575 |
|
600 | 1.54 | 14.6 | 30 |
| 590 |
|
700 | 1.36 | 14.5 | 29 |
| 625 |
|
800 | 1.28 | 11.8 | 28 |
| 705 |
|
T | E10-5 | α106 | λ | ρ | C | R109 |
Технологические свойства материала 65Г
Свариваемость: | не применяется для сварных конструкций |
Флокеночувствительность: | малочувствительна |
Склонность к отпускной хрупкости: | не склонна |
Обозначения:
Механические свойства:
σв – Предел кратковременной прочности, [МПа]
σT – Предел пропорциональности (предел текучести для остаточной деформации), [МПа]
δ5 – Относительное удлинение при разрыве, [ % ]
Ψ – Относительное сужение, [ % ]
KCU – Ударная вязкость, [ кДж / м2]
Физические свойства:
T – Температура, при которой получены данные свойства, [Град]
E – Модуль упругости первого рода, [МПа]
a – Коэффициент температурного (линейного) расширения (диапазон 20o – T ), [1/Град]
λ- Коэффициент теплопроводности (теплоемкость материала), [Вт/(м·град)]
ρ- Плотность материала, [кг/м3]
C – Удельная теплоемкость материала (диапазон 20o – T ), [Дж/(кг·град)]
R – Удельное электросопротивление, [Ом·м]
Свариваемость:
- без ограничений – сварка производится без подогрева и без последующей термообработки
- ограниченно свариваемая – сварка возможна при подогреве до 100-120 град. и последующей термообработке
- трудносвариваемая – для получения качественных сварных соединений требуются дополнительные операции: подогрев до 200-300 град. при сварке, термообработка после сварки – отжиг
www.uralpsk.ru