Газовая резка металла – Газовая резка металла: технология, оборудование для разделки
alexxlab | 23.07.2019 | 0 | Вопросы и ответы
Газовая резка металлов
Газовая резка – это процесс сгорания металла в струе кислорода и удаление образовавшихся окислов этой струёй.
Газовая резка бывает: резка окислением, резка плавлением и резка посредством того и другого.
Сущность резки окислением – состоит в нагреве места резки до температуры горения металла в кислороде (для стали 8000С), сгорании нагретого металла в струе кислорода и удалении продуктов сгорания струёй кислорода.
Основными видами резки окислением являются: кислородная, кислородно-флюсовая, кислородно-дуговая.
Сущность резки плавлением – состоит в нагреве места резки до расплавления металла и выдувание расплавленного металла из места реза дугой и газами.
Основные виды резки плавлением: плазменно-дуговая, газолазерная, газодуговая.
Не все металлы и сплавы поддаются резке окислением. Окислительная резка, требует выполнения следующих условий:
1.Температура воспламенения металла в кислороде должна быть меньше температуры плавления. Этому условию отвечают стали: 1540
2. Температура плавления окислов и шлаков должна быть меньше температуры плавления металла.
3. Металлы должны обладать небольшей теплопроводностью, чтобы не было сильного теплоотвода от места резки, иначе процесс прервётся. Медь и алюминий имеют высокую теплопроводность, поэтому они не поддаются кислородной резке.
4. Большая жидкотекучесть окислов, для лучшего их выдувания кислородом.
РЕЖИМЫ РЕЗКИ.
Основные показатели режима резки – это давление режущего кислорода и скорость резки, которые зависят от толщины разрезаемой стали, чистоты кислорода и конструкции резака.
При недостаточном давлении кислорода, струя не сможет выдуть шлаки из места реза и металл не будет прорезан на всю толщину. При большом давлении – расход кислорода увеличивается, а разрез получается недостаточно чистым. Выбор давления режущего кислорода зависит от толщины металла, размера режущего сопла и чистоты кислорода.
Если скорость резки мала, то будет происходить оплавление кромок. Если скорость велика, то будут образовываться непрорезанные участки из-за отставания кислородной струи, непрерывность резки нарушается. Приблизительную скорость резки можно определить по формуле:
(мм/мин), где S – толщина металла.
ОСНОВНЫЕ ВИДЫ РЕЗКИ.
Существуют следующие основные виды резки:
1. Разделительная – для раскроя листов, вырезки отверстий, фланцев и фасонных заготовок;
3. Резка кислородным копьём – для прожигания отверстий в металле.
Поверхностная резка отличается от разделительной тем, что струя режущего кислорода направляется под острым углом 15-40 градусов к поверхности металла и перемещается вдоль этой поверхности. Несмотря на внешнее различие поверхностной и разделительной резки сущность их одна и таже: нагрев до температуры воспламенения, сгорание металла в ограниченном объёме и удаление шлака.
РАЗРЕЗАЕМОСТЬ СТАЛЕЙ.
Разрезаемость – свойство стали разрезаться кислородом без образовывания закалённого участка вблизи места реза. По разрезаемости , в зависимости от химического состава стали делятся на 4 группы:
1.Хорошо разрезающиеся – разрезаются в любых условиях без ограничений по толщине: углеродистые с содержанием углерода до 0,3%, низколегированные с содержанием углеродасодержанием углерода новные виды резкиделить по формуалла, размера режущего сопла и чистоты кислорода. до 0,2%.
2. Удовлетворительно разрезающиеся – разрезаются с ограничениями, при резке большой толщины (до 100мм) с подогревом по линии реза до Т 1200С: углеродистые с содержанием углерода 0,3-0,4%, низколегированные с содержанием 0,2-0,3%.
3. Ограниченно разрезающиеся – требуется подогрев по линии реза до 200-3000С: углеродистые 0,4-0,5%С, низколегированные 0,3-0,4%С.
4. Плохо разрезающиеся – требуется подогрев до 300-4000С: углеродистые с содержанием углерода более 0,5%, низколегированные с содержанием углерода более 0,4 %.
Для резки легированных и высоколегированных сталей требуется специальная обработка, как до резки, так и после.
Сварка давлением
В процессе сварки давлением собранные детали сдавливают с определенным усилием. Всем видам данной сварки характерна пластическая деформация в зоне соединения. Пластическая деформация осуществляется за счёт приложения внешнего усилия, при этом материал в зоне соединения, как правило, нагревают с целью повышения пластичности. В процессе деформации происходит смятие поверхностей, разрушение окисных плёнок, в результате чего обеспечивается плотный контакт между заготовками.
Сварка давлением подразделяется на два класса:
1. Термомеханический (с разогревом кромок): индукционная, контактная, диффузионная, газопрессовая и др.
2. Механический (без разогрева кромок): холодная, взрывом,
ультрозвуковая, трением др.
Похожие статьи:
poznayka.org
Газовая резка металла – технология и оборудование
Газовая резка металла представляет собой трудоёмкий процесс, предполагающий нагревание определённых металлических деталей при помощи пламени газа. Происходит данный процесс под воздействием определённой температуры.Металл в ходе газовой резки воспламеняется, образуя окислы, которые потом просто сдуваются под воздействием струи кислорода.
При таком типе резки металлических заготовок, температура плавления всегда превосходит тот показатель, при котором данный металл может воспламеняться в кислороде. Иначе металл просто не будет подвержен сгоранию. А температура плавления окислов всегда меньше аналогичных показателей металла. Это не даёт возможности окислам покрывать всю поверхность обрабатываемого металла, что сделало бы процесс резки невозможным.
Область применения газовой резки металлов
Применение резки газом очень разнообразно: строительные, сельскохозяйственные, бытовые, ремонтные работы и т. п. Данный тип обработки металлов не требует наличия какого-то сложного профессионального оборудования или каких-либо источников энергии. К тому же, оборудование легко перемещается.
При помощи газовой резки свариваются трубы различных диаметров, материалы из алюминия, бронзы, свинца, чугуна. Могут заготавливаться также металлические изделия самой различной формы.
С помощью газового оборудования можно осуществлять резку не только вручную, но и в автоматическом режиме. В автоматическом режиме разрешается использовать изделия диаметром не больше 120 см.
Какое оборудование применяется для резки газом?
Газовая резка металла (оборудование):
- шланги;
- газовая горелка;
- регулятор давления;
- смеситель;
- газовые баллоны.
С помощью такой установки производится не только обрезка металлических изделий, но и утилизация отходов и иные действия, которые не требуют особой точности.
Горелка газовой резки состоит из нескольких сопел. Внешние сопла предназначены для подачи защитного газа (смесь кислорода и ацетилена), а центральная – для подачи кислорода во время резки. Смесь кислорода с ацетиленом используется для предварительного нагревания изделия.
Аппаратура, которая нужна для осуществления резки газом, должна обязательно включать в себя вентили для баллонов и редукторы. Вентили обычно изготавливаются из стали или латуни, и в целях безопасности имеют отличия между собой. Редукторы, отвечающие за поддержание постоянного уровня давления газа, бывают двух типов: одно- и двухкамерные. Более надёжным признан редуктор с 2-мя камерами, так как его работа последовательна, и он не подвергается замерзанию.
Газовая резка металла (оборудование) должна также иметь два баллона (топливо и кислород), откуда газ подаётся по рукавам (шлангам), состоящим из нескольких слоёв резины и специального каркаса (хлопчатобумажной нити). Рабочая температура рукавов – до -35
Технологический процесс
Современная газовая резка металла (технология) несколько отличается от той, которая была ранее. В нынешних оборудованиях кислород подаётся к месту резки под очень высоким давлением (12 атмосфер). Под таким давлением можно повредить даже кожу на руках!
Образовывающийся флюс может выбрасываться пламенем в сторону или же полностью прожигаться через весь металл изделия. При правильной подаче кислорода «рваного» шва образовываться не должно. Если при этом использовать ещё и «трафареты», то рез может получиться практически без изъянов.
ВАЖНО: резка металлов газом не может быть применена к изделиям, которые плавятся ниже 600оС. Если использовать такой металл, то кислород будет просто удалять верхний слой материала, но не разрезать его.
При использовании таких металлов можно применять дополнительно мобильные нагреватели (баллончики со смесью сжатого газа с соплом на конце трубки).
В технологии кислородной резки используется направляющий резак из двух трубок с подачей кислорода и топлива. Расход кислорода зависит от температуры нагревания и толщины металла. При стандартном нагревании израсходуется примерно 10 м3 кислорода и до 0,7 м3 ацетилена (пропана).
Основные требования безопасности труда
Газовая резка металла (технология) должна быть подготовлена соответствующим образом:
- помещение, где планируется производить резку, должно быть хорошо проветриваемым и вентилируемым;
- должны присутствовать вытяжные зонты, которые в процессе резки будут удалять продукты сгорания;
- производить резку газом разрешается на расстоянии не менее 5 м от расположения газовых баллонов;
- газовые баллоны должны быть установлены на специальную тележку (носилки) во избежание взрывов при транспортировке;
- работать с газовой резкой необходимо в специальной маске и очках, огнеупорной одежде;
- во время перерыва процесса резки необходимо каждый раз гасить пламя горелки, а также во избежание утечек плотно закручивать вентили на баллонах.
Поделитесь со своими друзьями в соцсетях ссылкой на этот материал (нажмите на иконки):
swarka-rezka.ru
Газовая резка – технология обработки металла + Видео
Газовая резка, также нередко называемая автогенной либо кислородной, представляет собой процесс разрезания металлических заготовок посредством воздействия на них кислородного потока, подаваемого из специального агрегата.
1 Техника автогенной резки и ее ключевые положения
Данный вид обработки металла эксплуатируется весьма активно. На сегодняшний день он является популярным методом резки стальных и металлических изделий. Его суть состоит в том, что материал в зоне обработки доводится до температуры зажигания (горения) посредством смеси газа и кислорода, а затем на него наводят поток чистого кислорода.
Рекомендуем ознакомиться
Указанные действия приводят к сгоранию металла и удалению из зоны резки оксидов, которые образуются в ходе выполнения операции.
При горении поверхностного слоя заготовки отмечается выделение существенных объемов кислоты, в результате чего нагреваются нижние слои металла. Благодаря этому процесс горения охватывает деталь на всю глубину, формируется отверстие сквозного вида. Через него кислородная струя, выполняющая функцию режущего инструмента, пробивает заготовку полностью и выходит наружу. Передвигая с заданной скоростью приспособление для кислородной резки, получают точный разрез.
По сути, описываемый процесс включает в себя несколько основных этапов. Сначала металл подогревают, затем при помощи кислорода его сжигают, а на финальной стадии из полости реза происходит выдувание шлака, находящегося в расплавленном состоянии. В связи с тем, что при горении в кислороде железа выделяется сравнительно мало теплоты, тушения подогревательного пламени не производят. Это позволяет возмещать большие утраты тепла на участке обработки металла.
Если пламя потушить, металлическая заготовка очень быстро охлаждается, реакция горения затухает, и операция резки прекращается. Кислородная резка дает возможность вырезать сложные по форме изделия, а также без проблем осуществлять разрезание металлических деталей толщиной до 200 сантиметров. Отметим, что далеко не все сплавы и стали допускается подвергать автогенной резке. Она используется для металлов, которые соответствуют некоторым важным условиям. О них речь пойдет далее.
2 Условия для проведения кислородной резки
Газовая резка металла будет успешной только в том случае, если его температура плавления выше температуры воспламенения. Данному условию полностью отвечают сплавы с малым содержанием углерода. Плавятся они при температуре 1500 градусов, а воспламеняются при 1300 градусах. Средне- и высокоуглеродистые стали поддаются газовой обработке намного хуже, так как повышенное содержание углерода в них приводит к уменьшению температуры плавления и увеличению температуры воспламенения.
Также теплопроводность металлических композиций должна быть не очень высокой. Если подобное условие не выполняется, фиксируется активное отведение от зоны реза нагретого шлака и подогревающего пламени, что становится причиной неустойчивости операции. Она может прекратиться практически в любой момент резки. “Нужный” для проведения рассматриваемой в статье операции показатель теплопроводности отмечается исключительно у сталей, являющихся техническим сплавом железа, и непосредственно у железа. Автогенная резка прочих металлов в большинстве случаев невозможна.
Кроме того, должны выполняться и другие условия для резки:
- При сгорании в кислородной струе металла количество теплоты обязано быть таким, чтобы операция проходила непрерывно. Стоит помнить, что лишь 30 процентов теплоты образовывается от работы пламени резака, остальные же 70 процентов выделяются при сгорании металла.
- Температура расплавления металла должна быть выше температуры, при которой начинают плавиться металлические оксиды. В тех случаях, когда данное требование не соблюдается, операция резки нарушается из-за того, что кислородный поток не способен качественно выдуть тугоплавкие окислы. В связи с этим автогенная резка не рекомендуется для алюминия (его оксиды плавятся при температуре порядка 2050 градусов) и сталей с большим содержанием хрома (температура плавления их оксидов составляет около 2000 градусов). Впрочем, выход есть. Резать алюминий и высокохромистые сплавы допускается при помощи флюсов со специально подобранным составом.
- Жидкотекучесть шлаков, которые появляются в процессе резки, должна иметь высокие показатели, обеспечивающие простую выдувку шлаков из места выполнения операции.
3 Виды кислородной резки и их краткое описание
Резка с использованием газового оборудования бывает ручной и машинной, поверхностной и разделительной. При поверхностной разрезание металлической детали сопровождается формированием круглых по форме канавок, а при разделительной резке на поверхности появляются разрезы сквозного типа.
Разделительная ручная операция обычно назначается для обработки скрапа, профильных поковок и листов из углеродистой стали. Такая резка предполагает применение природного газа, смеси бутана и пропана, ацетилена в качестве горючей составляющей процесса. Как правило, используется ацетилен, так как он обеспечивает быстрый подогрев обрабатываемого изделия.
Ручная резка также применяется для вырезки отверстий и участков с теми или иными изъянами в трубопроводах, для обрезки под последующую газовую сварку концов трубных изделий. И листы, и трубы, и поковки режутся во всех пространственных положениях. При этом на качество процесса большое влияние оказывает квалификация специалиста, осуществляющего операцию, и наличие у него опыта работы резчиком.
Для повышения эффективности точности ручной прямолинейной резки рекомендуется производить процесс по направляющим и заранее нанесенным отметкам на изделии. Кроме того, нужно использовать и дополнительные приспособления (уголок, направляющие линейки, специальный циркуль для обработки отверстий и фланцев и так далее), которые дают возможность:
- четко выдерживать требуемую дистанцию между поверхностью заготовки и резаком;
- передвигать резак максимально равномерно;
- вовремя запускать кислородную струю.
Поверхностная резка (и машинная, и ручная) подразумевает удаление струей кислорода слоя металла определенной толщины. Ее отличие от распределительной состоит в том, что резак при поверхностной обработке передвигается быстро, причем под некоторым углом по отношению к металлической поверхности.
4 Особенности автогенной обработки металлов
Технология газовой резки предусматривает необходимость качественной очистки поверхности металлической детали от грязи, коррозии, окалины и лакокрасочных покрытий. При ручном разделении листов рекомендуется обдуть область реза на ширину не более 3–5 сантиметров (использовать пламя резака), после чего при помощи щетки из металла зачистить эту область.
При машинной резке, как правило, осуществляют очистку стальных листов на специальных агрегатах по дробеструйной либо химической методике. Дополнительно выполняют правку металлических заготовок на вальцах.
К ключевым характеристикам режима резки относят:
- давление кислорода;
- мощность пламени;
- скорость выполнения операции.
Качество и производительность операции зависит именно от этих показателей. Давление кислородной струи зависит от чистоты используемого газа, формы сопла на режущем инструменте и толщины изделия, подвергаемого разрезанию. При увеличении давления выше нормативных величин отмечается ухудшение качества поверхности и скорости процедуры, что, естественно, приводит к повышенному расходу кислорода.
Мощность пламени зависит от состояния сплава (поковка либо обычный прокат), его состава и толщины металла. Машинная резка выполняется на минимальном пламени, а вот для ручной его мощность необходимо повышать в 1,5–2 раза. Еще важный момент – при обработке изделий толщиной более 40 сантиметров следует использовать науглероживающее пламя (то, в котором имеется “лишний” ацетилен). В остальных случаях применяется стандартная мощность.
Скорости окисления металлической детали и процесса резки должны соответствовать друг другу. Чрезмерная скорость резки сопровождается искрами, она чревата тем, что металл может не прорезаться.
tutmet.ru
Газовая резка металлов » Привет Студент!
Газовая резка металлов
Кислородная резка
Кислородной или газовой резкой (ранее называвшейся автогенной резкой) называется процесс разрезания металла действием струи кислорода, в которой сгорает металл, предварительно подогретый до температуры воспламенения; горение металла идет на заранее намеченной плоскости.
Для осуществления этого процесса металл нагревают газовой горелкой в месте начала разреза до температуры воспламенения в кислороде и направляют на нагретую поверхность струю кислорода. Нагретый верхний слой металла воспламеняется; выделяющееся при сгорании этого слоя тепло нагревает следующий слой, который также сгорает; струя кислорода уносит образующиеся окислы, я процесс горения распространяется на лежащие ниже слои. Таким образом, постепенно под действием струи кислорода в определенном направлении металл выжигается, и кусок его может быть разрезан. В настоящее время при помощи газовой резки можно разрезать куски стали толщиной до 2000 мм и более. Применяя газовую резку, можно также вырезать детали, имеющие сложную форму.
Требования, которым должен удовлетворять металл, подвергаемый кислородной резке. Кислородной резке можно подвергать лишь те металлы, температура воспламенения которых ниже температуры их плавления; кроме того, для возможности газовой резки необходимо, чтобы температура плавления окислов металла была ниже температуры плавления самого металла.
Так, например, температура плавления малоуглеродистой стали около 1500°, а температура воспламенения около 1350°; следовательно, такая сталь должна поддаваться газовой резке. Другой пример: температура плавления чугуна около 1200°, а температура воспламенения около 1350°; очевидно, что чугун не будет резаться газовым способом, а будет только выплавляться в месте нагрева.
Чем меньше теплопроводность металла, тем лучше при прочих равных условиях он режется газовым способом; чем больше теплоты выделяется металлом при сгорании его, тем лучше он поддается газовой резке. Так, например, железо выделяет при сгорании количество тепла, почти достаточное для нагрева соседних слоев металла и плавления окислов, а при резке, например, никеля требуется подвод большого количества тепла извне.
Подогрев металла при газовой резке происходит от резака, который, кроме струи кислорода, подает и подогревающее пламя.
Резаки. Резаками, или режущими горелками, называют горелки, применяемые при кислородной резке металла. На фиг. 354, а показано устройство головки резака с последовательно расположенными мундштуками, а на фиг. 354, б —-с концентрическими мундштуками.
При движении резака с последовательно расположенными мундштуками подогревательный мундштук идет впереди режущего. Резаки с концентрическими мундштуками могут перемещаться во всех направлениях, но дают более широкий разрез, чем первые.
На фиг. 355 показано устройство универсального резака, применяемого при резке металла толщиной от 5 до 300 мм; подрисуночные надписи вполне объясняют чертеж. Тележка служит для перемещения резака в процессе работы; она устраняет необходимость держать резак и позволяет сохранить одинаковое расстояние между мундштуком и поверхностью разрезаемого металла. Привернутое к тележке циркульное устройство применяют в случае резки по окружности.
Горючее. При газовой резке можно применять все названные выше горючие газы, а также пары бензина, бензола, керосина.
Кислород. Чем чище применяемый при газовой резке кислород, тем меньше его расходуется, тем быстрее идет процесс резки. В табл. 42 приведены данные, характеризующие влияние чистоты кислорода на расход его и скорость резки.
Влияние газовой резки на свойства металла в слоях, прилежащих к плоскости разреза. Газовая резка не оказывает существенного влияния на свойства металла вблизи плоскости разреза: отмечается лишь незначительное повышение предела прочности (на 3—8%) и незначительное уменьшение относительного удлинения (на 5—10%), глубина же зоны влияния газовой резки составляет всего 1—1,5 мм. При резке ножницами глубина зоны влияния достигает 3—4 мм; металл при этом оказывается наклепанным.
Газовая резка может сопровождаться и незначительным изменением химического состава металла у поверхности реза: отмечается небольшое выгорание кремния и в случае резки, например, ацетиленом увеличение содержания углерода, повышающее твердость у поверхности реза. Поэтому лучший результат дает резка с использованием в качестве горючего водорода. Таким образом, газовая резка не оказывает практически заметного влияния на свойства метaллa.
Процесс газовой резки
Приступая к резке, проверяют исправность резака; применительно к толщине подлежащего резке металла, в головку резака ввертывают соответствующих размеров мундштуки и устанавливают (редуктором) давление кислорода. После этого открывают ацетиленовый вентиль, приоткрывают кислородный вентиль подогревающего пламени, зажигают горючую смесь и регулируют пламя. Когда пламя будет отрегулировано, горелку устанавливают так, чтобы ось мундштука была перпендикулярна к поверхности подвергаемого резке металла, а расстояние от конца режущего сопла до этой поверхности составляло 3—6 мм. Поверхность металла нагревают до температуры воспламенения, пускают режущий кислород и начинают равномерно передвигать резак. Скорость передвижения резака определяют толщиной разрезаемого металла.
Качество резки зависит от равномерности перемещения резака и от правильного выбора скорости перемещения. При излишне медленном перемещении резака рез получается широкий, при слишком быстром перемещении металл недостаточно прогревается, и разрез получается несплошной.
Расход кислорода на 1 пог. м длины резки можно приближенно определить по эмпирической формуле
где Q — расход кислорода в л;
ð — толщина листа в мм;
а — ширина реза в мм.
В табл. 43 помещены данные, характеризующие процесс газовой резки стали в зависимости от толщины листа на 1 пог. м длины разреза. Данные, приведенные в табл. 4-3, являются средними и могут измениться в зависимости от конструкции резака.
Газовую резку применяют также для замены процесса ковки вырезкой деталей из толстых листов или болванок.
Подводная резка. Газовую резку применяют и при работах под водой. При подводной резке вода оттесняется от пламени либо продуктами горения, либо при помощи сжатого воздуха. Давление сжатого воздуха, а также горючего газа и кислорода, подаваемых в горелку, увеличивается с увеличением глубины, на которой ведется подводная резка. Подводную резку широко используют при водолазных работах ЭПРОН. В качестве горючего для подводной резки применяют главным образом водород (для больших глубин—до 40 м) и ацетилен (для меньших глубин — обычно до 15—20 м).
Машинная резка. При ручной резке качество реза не всегда однородно и удовлетворительно, так как трудно сохранить равномерность перемещения резака и постоянство расстояния его от поверхности разрезаемого металла. В виде примера дефектов ручной резки можно указать на оплавление краев поверхности разреза, глубокие борозды на ней.
Механизация процесса газовой резки улучшает качество реза и повышает производительность процесса.
Существуют полуавтоматические и автоматические машины для газовой резки. В полуавтоматах механизируется передвижение резака, а направление движению дается или вручную, или шаблонами. Полуавтоматы применяют при резке листов, вырезке из листов, для разделки шва под сварку.
В автоматах механизируется и направление движения резака.
Обработка поверхности металла методом газовой резки. Обработка поверхности металлического предмета резаком является разновидностью газовой резки металла. Этот вид обработки применяют вместо черновой обработки резном, и он может в ряде случаев заменить строгание, обточку (резка по касательной) и сверление.
При такой обработке газовая струя направляется не перпендикулярно поверхности металла, а под углом 25—30°. Самый процесс заключается в том, что поверхностный слой металла обрабатываемой детали выгорает в кислородной среде. Резаки, применяемые для этой цели, несколько отличаются от обычных резаков, в частности, имеют увеличенный размер отверстия в кислородном канале; этим достигается уменьшение скорости истечения кислородной струи.
Производительность процесса достигает 150 кг снимаемого в час металла при вполне удовлетворительном для дальнейшей обработки качестве поверхности. Расход кислорода на 1 кг снимаемого металла около 450 л.
Скачать реферат: У вас нет доступа к скачиванию файлов с нашего сервера. КАК ТУТ СКАЧИВАТЬ
Пароль на архив: privetstudent.com
privetstudent.com
Газовая резка металла различного уровня сложности
Работа с металлическими деталями осуществляется с применением разнообразных способов обработки. Современное оборудование позволяет проводить операции быстро и с высокой точностью, сохраняя при этом все свойства поверхности из металла. Одной из таких технологий является газовая резка или, как ее еще называют, автогенная. Она получила широкое распространение благодаря относительной простоте, оперативности, доступной стоимости.
Что такое газовая резка металла
Это технология работы с металлическими элементами, которая предполагает использование кислорода и пропана, а также достаточно простого оборудования и инструментов. При помощи специального резака струя раскаленного газа направляется на поверхность металла, из-за чего он в этой точке теряет прочность и целостность. В результате можно получать разделенные детали, придавать пластинам необычный внешний вид и форму.
Имея определенные навыки, можно проводить операции даже в полевых условиях, так как эта технология не требует громоздких станков и специальных помещений. Давайте подробнее рассмотрим сам процесс обработки.
Технология газовой резки металла
Подготовка поверхности
Перед началом работ нужно позаботиться о том, чтобы обрабатываемый материал был очищен от грязи, лакокрасочных покрытий, коррозии, окалины. Если используется ручная резка, рекомендуется при помощи пламени резака обдуть область, где пройдет линия рассечения, а затем использовать металлическую щетку. При машинной обработке листы зачищаются и выравниваются на дробеструйном станке и вальцах, а также с использованием химических способов.
Подготовка инструментов
Состав оборудования, которое понадобится для газовой резки металла:
- Баллон с кислородом и пропаном;
- Шланги, рассчитанные на высокое давление;
- Резак;
- Мундштук.
Оборудование настраивается в зависимости от режима резки, при этом подгоняются под нужные параметры давление кислорода, мощность пламени и скорость выполнения операции.
Следует учитывать, что именно эти характеристики влияют на качество и производительность, поэтому их необходимо подирать тщательно, учитывая особенности обрабатываемого материала.
Давление газовой струи определяется по чистоте используемого кислорода, формы сопла на резаке и толщины металлического листа. Если этот параметр выходит за пределы нормативных, то отмечается ухудшение качества поверхности и снижение скорости работы, а также увеличение расхода газа.
Мощность пламени настраивается с учетом состояния материала (кованый металл или обычный прокат), его состава и толщины заготовки. Машинная резка из-за особенностей оборудования осуществляется при минимальном значении, для ручной необходимо увеличивать показатель в 1,5-2 раза.
Технологические этапы
- Поверхность металла разогревается при помощи специального агрегата до 1100 градусов по Цельсию. Для этого используется смесь газов – кислорода и пропана.
- На место будущего реза направляется кислородная струя под высоким давлением.
- Соприкосновение кислорода с горячей поверхностью металла вызывает воспламенение, материал в этом месте начинает сгорать, теряя свою прочность.
- Происходит рассечение листа, отделение детали от отходной части.
- В процессе сгорания на поверхности появляются продукты окисления, которые выдуваются из зоны обработки потоком газа. Получается, что металл окисляется только на участках непосредственного воздействия, и продукты реакции не попадают внутрь. Так сохраняется структура и свойства сырья, что позволяет создавать прочные и качественные изделия.
Вместо кислорода может применяться ацетилен, природный пиролизный или коксовый газ, а также пропано-бутановая смесь.
Сфера применения газовой резки металла
Кислородная обработка изделий из разных сплавов широко распространилась во многие сферы деятельности:
- Строительство;
- Сельское хозяйство;
- Ремонтные работы;
- Производство и пр.
При помощи оборудования для газовой резки осуществляют сварку труб и других элементов из алюминия, бронзы, свинца, чугуна.
Какие металлы подходят для газовой резки
Чтобы контуры получаемой детали были точными, ровными, нужно не только хорошо подготовить поверхность, но и изучить свойства обрабатываемого материала. По отношению к металлу действуют существенные ограничения.
Во-первых, он должен именно прогорать, а не плавиться, то есть температура горения должна быть ниже того значения, при которых твердая заготовка начнет терять форму и целостность. Расплавленный, но не сгоревший металл очень трудно удалять из полости реза.
Во-вторых, во время операции в инструменте образовываются оксиды, которые тоже не должны плавиться, чтобы было проще прочистить инструмент. Для этого нужно уточнить их температуру плавления и сравнить с аналогичным показателем обрабатываемого металла: у оксидов она должна быть ниже.
В-третьих, большое значение имеет тепловой коэффициент образования окислов – именно они дают наибольший нагрев поверхности. Благодаря процессу окисления резка идет непрерывно, а значит, торец детали будет ровным и аккуратным.
В-четвертых, металл должен плохо проводить тепло. В противном случае нагретая до нужной степени деталь быстро остывает, и требуется затратить больше времени и энергии на дополнительный нагрев и поддержание температуры.
Получается, что газовая резка металла подходит для следующих типов сплавов:
- Низкоуглеродистые и низколегированные марки стали;
- Титановые сплавы;
- Стали с содержанием углерода более 1% – с учетом, что в кислородный поток будут добавлены специальные порошкообразные флюсы. Эти частицы при сгорании выделяют дополнительно тепловую энергию и образуют оксиды, помогая тем самым выполнить резку более качественно.
Не подходят для газовой обработки:
- Медь, т.к. имеет низкую теплоту сгорания;
- Чугун, так как он отличается высокой температурой горения и низкой – плавления;
- Высоколегированные типы стали, алюминий – при газовой резке они образуют шлаки и тугоплавкие оксиды.
Чтобы качество сварки или производимой детали было высоким, убедитесь, что выбранный вами материал подходит для использования этой технологии.
Виды газовой резки металлов
По типу операции делят на:
- Разделительная резка. Металл пронзается кислородной струей насквозь, отделяя от основной пластины необходимую часть.
- Поверхностная. Заготовка остается цельной, но в ней прорезаются каналы, шлицы, иные элементы и заглубления.
- Газовая резка копьем. С помощью дополнительной насадки на резак в пластине формируется глухое или сквозное отверстие.
По используемому оборудованию газовую резку металла классифицируют так:
- Ручная. Операция выполняется мастером, при этом можно осуществлять ее в так называемых полевых условиях. Это удобно, если требуется провести ремонт трубопровода, статичного громоздкого оборудования. Работают ручным способом также с листами, трубами, поковками. Для повышения точности резки на материал наносят направляющие отметки, используют вспомогательные инструменты (уголок, циркуль и т.п.).
- Машинная. Используются особые станки с ЧПУ, которые позволяют достигать высочайшей точности. Такой способ резки хорош для листовых металлов, для производства деталей большого размера, для повышения качества и скорости выполнения операций.
Преимущества и недостатки газовой резки металла
Среди достоинств технологии выделяют:
- Несложное и относительно легкое оборудование, которое открывает широкие возможности. Это упрощает процесс работы, если речь идет о ручной резки. Благодаря такому методу можно совершать одинаковые операции по шаблону, качественно выполнять криволинейное рассечение. Газовая резка позволяет формировать глухие отверстия, производить металлические диски из листов большой толщины и пр.
- Экономичность. Техническое обслуживание процесса требует минимальных затрат. Это дает высокую эффективность газовой резки. Кроме того, перед операцией не нужна сложная механическая обработка металла.
- Главное достоинство – возможность работы с металлом, имеющим большую толщину (до 200 мм). Толщина самого среза будет маленькой – 2-2,5 мм. При помощи оборудования для автогенной резки можно провести вертикальную кромку среза, что улучшит процесс.
Технология имеет и свои недостатки:
- Она применима к очень ограниченному списку металлов. Чаще всего используется для низко- и среднеуглеродистых сталей, для обработки других материалов этот метод практически не применяется.
- После газовой резки поверхность деталей нуждается в дополнительной обработке.
- Если использовать автогенную обработку для листов менее 6 мм толщиной, возможно появление деформации, а итоговое качество произведенного элемента будет средним.
Таким образом, можно сделать вывод, что газовая резка металла – хороший и недорогой метод обработки материалов, помогающий справляться со сложными задачами и выполнять криволинейные срезы, а значит, полезный в производстве различных деталей и заготовок.
zmtgroup.org
краткое описание процесса и обзор оборудования
Газовая резка металла является одним из самых простых способов обработки низколегированных и низкоуглеродистых сталей. Суть этого процесса заключается в сгорании необходимого объема металла в кислородной струе с последующим удалением образующихся окислов из зоны резания.
Классификация газовой резки
В зависимости от характера реза газовая резка делится на несколько групп:
- разделительная;
- поверхностная резка металла газом;
- резка копьем.
В процессе разделительной резки выполняется сквозной рез, разделяющий металлическую заготовку на нужное количество частей. Поверхностная резка газом позволяет удалять поверхностные слои металла для образования канавок, шлицов и про чих конструктивных элементов.
Резка копьем – это прожиг металла с целью получения сквозных или глухих глубоких отверстий.
Краткое описание технологического процесса
В технологическом процессе газопламенной резки задействованы два газа:
- кислород;
- горючий газ (пропан-бутан, ацетилен, природный, пиролизный, коксовый газы и пр.).
В последнее время все чаще встречается кислородно-водородная резка. Но наиболее распространена технология резки с применением ацетилена или пропан-бутана.
Резак, постепенно продвигаясь по линии реза, разогревает металл. В зону резания подается кислородная струя, которая способствует быстрому сгоранию материала. В результате на заготовке (листе или трубе и т. д.) образуется узкий паз. Железо в процессе резания окисляется только в зоне взаимодействия с кислородом: он не проникает вглубь металла, следовательно, никаких побочных изменений в теле заготовки не происходит. Для обеспечения непрерывности процесса резки струя подогреваемого газа должна находиться перед кислородным потоком.
Режимы резания
Газовая сварка и резка металлов требует правильного подбора режимов, которые зависят от марки стали, условий проведения работы и толщины заготовки. Важную роль в качественном выполнении реза играет предварительный подогрев металла. При толщине заготовки менее 300 мм резание обеспечивается нормальным пламенем. Если же толщина металла превышает 400 мм, приходится увеличивать длину подогревающего пламени. Регулируется пламя за счет притока ацетилена (или другого подогревающего газа). Чем выше приток газа, тем длиннее пламя. Плохо поддается регулировке водородная резка: кислородно-водородное пламя не имеет четких очертаний, поэтому отследить размер пламени сложно.
Основными параметрами резки являются:
- Скорость резки: имеет прямое влияние на эффективность выполнения работы. Скорость перемещения инструмента (резака) выбирается в соответствии со скоростью горения металла. Опытные резчики контролируют данный параметр по характеру выброса искры и шлака( при правильном соответствии скоростей горения и перемещения искровой поток направлен вниз, на кромках заготовки не образуется подплавлений и натеков; недостаточная скорость выражается в опережении потоком искр движения резака, а кромки металла оплавляются, их поверхность покрывают натеки; слишком высокая скорость не позволяет выполнить сквозной рез, поток искр при этом отстает от резака)
- Давление кислорода: недостаточная величина этого параметра не позволяет струе выдуть окислы (шлаки) из зоны резки. В результате сквозного реза не получится. Избыточное давление режущего кислорода приведет к неэффективному его расходованию и нечистому разрезу.
Оборудование для газовой резки
Технология ручной резки не требует сложных аппаратов. Простейший комплект оборудования для газовой резки состоит из следующих компонентов:
- газовая горелка;
- регулятор давления;
- газовые баллоны;
- смеситель;
- шланги.
Главным элементом газовой горелки является головка с несколькими соплами. Одно из них — центральное – является главным, через него подается в зону реза кислород. Через вешние сопла подается кислородно-ацетиленовая смесь, служащая для предварительного подогрева металла.
Газовая сварка и резка в промышленных объемах требует более серьезного оборудования. Такая машина может производить прямолинейные резы с одновременной заправкой фаски под сварку, вырезать диски, отверстия, фланцы. Промышленному оборудованию под силу резать швеллеры и двутавры, вырезать детали по шаблону.
Так, например, машина серии CG2-150 мало похожа на привычный резак. Она представляет собой шарнирно-копировальный агрегат, работающий по стальному копиру. Машина используется в судостроении для раскроя листового металла.
Выпускаются и специальные модели, которые применяются для организации автоматизированной резки двутавровых балок. Такая машина перемещается без участия человека при помощи электродвигателя. Управляется данный агрегат при помощи джойстика, а резать он может как перпендикулярно, так и под углом 45 градусов к оси балки. К такому типу оборудования относится машина Minimantis II (Япония).
Особый интерес представляет модель, способная вырезать круги, фланцы и отверстия из листа толщиной до 100 мм. Из этой серии наиболее интересна машина – аналог модели Факел-К (фланцереза): небольшая, оборудованная магнитной опорой, способная вырезать отверстия диаметром до 200 мм.
Технология водородной резки требует оборудования, несколько отличающегося от машин кислородно-ацетиленовой резки. Одним из основных узлов установки в этом случае является электролизер, способный разделить воду на кислород и водород. Резка, выполненная с использованием данного оборудования, имеет очень низкую себестоимость. Кроме того, отпадает необходимость постоянно заботиться о приобретении баллонов с кислородом и ацетиленом.
Похожие статьиgoodsvarka.ru
Основы резки металла: инвертором, плазменной, газом
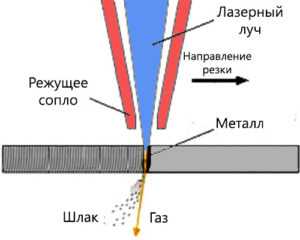
Резка металла при помощи сварки до определенного времени применялась активно, как основной способ обработки металлических конструкций в домашних условиях. Получаемый рез не отличался красотой, поэтому применение болгарки заметно потеснило сварку. К проверенному годами способу по-прежнему прибегают, его возможности расширились за счет использования нового оборудования.
При помощи сварки режут металл в следующих случаях:
- в полевых условиях, когда отсутствуют к источники электроэнергии,
- возникает необходимо разрезать очень толстый металл,
- при резке необходимо получить фигуру сложной формы,
- необходимо разрезать металл в труднодоступном месте.
Сварка относится к универсальным процессам, выполняя которые можно как соединить, так и разделить детали на части. Наиболее применимы в домашних условиях следующие варианты оборудования для резки металла:
- дугой (инвертором),
- газовым резаком,
- плазморезом.
В этой статье мы подробно поговорим об особенностях, технологии и основных принципах резки металла сварочным инвертором, газовой резке металла с помощью кислорода и пропана, и о плазменной резке металла. Изучив основные принципы работы с разными видами оборудования вы сможете осуществить резку металла своими руками.
Резка дугой
При обучении основам сварки новичок больше всего боится прожечь металл и полностью разрушить соединение. При резке металла цель сварщика именно прожечь, разрезать металл.
Для того чтобы разрезать металл сварочной дугой необходимо нагреть его до температуры плавления и удалить расплавленный металл из зоны сварки. Удаление выполняется под собственным весом расплавленного металла, за счет давления со стороны дуги или поток воздуха, подаваемый в зону сварки.
Для резки металла применяют такие электроды:
- покрытый металлический,
- угольный,
- трубчатый,
- вольфрамовый.
Этим способом режут сталь, в том числе и легированную, цветные металлы и сплавы.
К недостаткам относится низкое качество реза, неровные края, наличие окалины. Поэтому, если металл в дальнейшем идет для создания конструкций, кромки необходимо дополнительно обработать, например, зачистить.
Резку выполняют на том же оборудовании, что и сварку, во всех пространственных положениях. В качестве оборудования в домашних условиях ранее использовался трансформатор или выпрямитель, теперь чаще всего применяют инвертор.
Основы дуговой резки
Для того чтобы разрезать металл дугой устанавливают силу тока на 30-40% выше, чем при сварке. Зажигают мощную дугу на верхней кромке металла и углубляются вниз, при этом разрезают кромку.
Резка метала сварочным инвертором
Для резки выбирают электрод небольшого диаметра, а вот ток, наоборот, выставляют больше чем необходимо для сварки. Например, на диаметр электрода 2,5 мм, устанавливают 140А.
Зажигайте дугу и оставляйте электрод на одном месте. Стараетесь, чтобы дуга углублялась, как бы прожигала металл.
Если пластину разместить вертикально, расплавленный металл будет аккуратно стекать. При горизонтальной резке металла сварочным инвертором подтеки будут собираться внизу пластины.
Чтобы обеспечить лучший прогрев металла, при резке вбирают прямой полярности. В этом случае металл прогревается глубоко, но рез получается узким.
На видео показано, какие возможности открываются при применении резки дугой. Пластина в 10 — 20 мм толщиной разрезана буквально за несколько минут с легкостью и красиво.
Резка газовым резаком
До недавнего времени газорезка металла оставалось основным способом раздела металла, особенно если требовалось выполнить рез по сложному контуру, обработать кромку или получить отверстие. Преимущество в том, что для выполнения работ нет надобности в источнике электроэнергии.
Резка металла газовым резаком выполняется следующим образом: воспламеняют смесь кислорода с горючим газом, полученным факелом разогревают металл в зоне реза до температуры горения, не менее 12000С . Подают струю кислорода.
Металл воспламеняется и получается линия реза. Чаще всего для резки используется кислород в смеси с пропаном. Газовой резкой обрабатывают стали, как углеродистые, так и легированные, титановые сплавы.
Газовая резка металла на смеси пропана и кислорода
До начала работы металл подготавливают: очищают грязь, жир, окалину, ржавчину.
Оборудование для газовой резки
Для выполнения газовой резки требуется меньше навыков чем при сварке, потому что нет необходимости обеспечивать герметичность соединения. Из оборудования потребуется газовый резак, баллоны кислорода и пропана.
На каждом баллоне есть редуктор для регулирования давления. Газ от баллона к редуктору подается по шлангу высокого давления.
Перед тем как приступить к работе продувают шланги, чтобы очистить от грязи. Все шланги осматривают, места соединения с редуктором, все разъемные соединения проверяют на герметичность.
Проверяют исправность самого резака и продувают его кислородом. Для этого подсоединяют баллон с кислородом к месту крепления кислородного шланга. Баллон с горючим газом пока не подсоединяют. Устанавливают на редукторе 5 атм и открывают оба вентиля на резаке. Поднося палец ко второму штуцеру можно наблюдать, есть ли подсос. При его отсутствии, каналы резака необходимо продуть.
Порядок работы
Газовую резку выполняют, выдерживая пропорцию: 10 частей кислорода на 1 часть газа. Поэтому устанавливают на газовом редукторе 0,5 ати, а на редукторе кислорода 5 ати.
Для начала немного приоткрывают подачу пропана и поджигают газ. Соплом упираются в металл и понемногу начинают подачу кислорода. С помощью вращения вентилей можно отрегулировать величину пламени и получить необходимое пламя для работы. Чем толще металл предполагается разрезать, тем сильнее должно быть пламя, для чего необходима большая подача газа и кислорода.
Внимание: пламя регулируется при помощи давления кислорода регулирующего, а не режущего.
Горящее пламя подносится к металлу в том месте, где нужно выполнить рез, выдерживая расстояние между соплом и металлом в 5мм. Под действием пламени металл нагревается до требуемой температуры. Это происходит быстро, секунд за 10. Наблюдая за процессом замечают, что в этот момент металл как бы становится мокрым. Только металл воспламенится, тут же включают режущий кислород.
Для того чтобы избежать обратного удара пламени, который может сопровождаться хлопком, включают режущий кислород постепенно.
В этом случае кислород сам загорится как только дотронется к горячей поверхности металла. На видео показано, как с помощью газовой резки можно вырезать фигуры самой сложной формы.
На качество резки влияет скорость сварки. Контролируют скорость ориентируясь на искры в зоне резки. Если искры впереди, это означает что скорость недостаточна. При высокой скорости искры находятся позади резака, в этом случае трудно качественно разрезать заготовки.
Для того чтобы выполнить отверстие, место нагревается до требуемой температуры, подается режущий кислород. Металл воспламеняется. Резак подается в зону металла и пробивается отверстие.
Резка металла плазменным резаком или плазморезом
О возможностях плазмотрона хорошо рассказано в видео. Просмотрев ролик вы обязательно захотите иметь в хозяйстве такое чудесное оборудование, даже несмотря на его большую цену.
https://youtu.be/rg4PvBBr1CU
Резка металла происходит под действием энергии плазмы. Получается это следующим образом. Когда нажимают кнопку розжига, подается ток от источника и внутри плазмотрона образуется дежурная сварочная дуга. Через нее проходит сжатый воздух, ионизируется, и плазмой вырывается через сопло с высокой скоростью. Плазма имеет температуру свыше 10 тыс. градусов и скорость в два раза больше скорости звука. Этой энергии достаточно, чтобы металл расплавился и даже испарился.
Оператор подносит плазморез к месту, где необходимо выполнить разрез и металл начинает плавиться. Скорость ручного перемещения должна обеспечивать разрез металла. Параметрами резки есть сила тока и давление воздуха.
Подробности о том, как получается плазма и устроен резак хорошо показано в видео.
При неправильно подобранных параметрах на кромке может образоваться окалина. После окончания резки сразу не отключают подачу сжатого воздуха. Он подается некоторое время для охлаждения металла.
Технология работы с плазморезом
Перед началом работ зачищают кромки, удаляют с них загрязнения и ржавчину.
Работы по плазменной резке любого металла начинают с установки силы тока. Принцип прост: сила тока рассчитывается в зависимости от толщины металла. Величину силы тока, которая необходима для разрезания 1 мм толщины металла, умножают на толщину металла, который необходимо разрезать. Если необходимо разрезать 25 мм стали, то необходимо 25 умножить на 4А (ток, необходимый для реза 1 мм стали или чугуна). Итого на оборудовании выставляют 100А.
Скорость с которой необходимо выполнять резку непосредственно влияет на качество работы, но зависит от умения резчика. Специалисты советуют на начальной стадии выполнения работ ориентироваться на наличие искр с обратной стороны изделия. Если они отсутствуют, то металл прорезается не полностью.
Перед тем как разжечь дугу в течение полуминуты резак продувают газом, чтобы удалить грязь и возможный конденсат. Далее оператор нажимает кнопку розжига дежурной дуги, она горит 2 сек. Если режущая дуга не образовалась, процесс повторяют еще раз.
В зависимости от модели поджиг бывает контактный и бесконтактный:
- При контактном необходимо короткое замыкание. Как только плазма вышла из сопла между металлом и электродом образуется плазменная дуга и начинается процесс резки.
- При бесконтактном дуга зажигается между соплом и электродом. Когда сопло приближают к металлу, образуется рабочая дуга.
Во время резки необходимо поддерживать постоянную длину дуги. Если она не обеспечивается специальным упором, то этот параметр выдерживает резчик, он должен быть от 1,6 до 3 мм.
При работе необходимо сопло держать к металлу под углом 900С. Для того чтобы уменьшить деформации на тонком металле, горелку держат под небольшим углом. Во время резки обращают внимание, чтобы металл не засорял сопло горелки.
Подробно о работе плазматрона смотрите в видео.
С помощью рассмотренных способов резки можно порезать металл по самому сложному контуру. Эти работы по силам выполнить своими руками, после небольшой теоретической и практической подготовки. Главное — это наличие оборудования и соответствующих материалов.
Рекомендуем вам еще:
o-builder.ru