Газовый резак универсальный – Газовые резаки и горелки
alexxlab | 10.03.2020 | 0 | Вопросы и ответы
Газовый резак: виды, назначение и особенности
Основным назначением аппаратов для газового раскроя металла является смешивание горючих веществ (жидкостей или газов) с кислородом для получения струи высокотемпературного пламени. В отличие от сварочной горелки, газовый резак снабжен трубкой и запорно-регулирующей арматурой для подачи кислорода режущей струи, а также имеет особое устройство головки.
Классификация аппаратов
Газовые резаки имеют достаточно много видов и классифицируются по таким признакам:
- тип резки: поверхностные и разделительные;
- назначение: ручные и механизированные;
- вид горючего: ацетиленовые, пропановые, метановые, керосиновые;
- конструкция: наличие или отсутствие инжектора;
- кислородная подача: низкого и высокого давления;
- тип мундштука: многосопловые и щелевые;
- мощность: малая (< 10 см разрезаемого металла), средняя (< 20 см) и высокая (> 20 см).
Сегодня разными производителями выпускается более десятка модификаций подобного оборудования, однако конструктивно они мало чем отличаются между собой. Для таких устройств характерно наличие ручки с вентилями для изменения подачи пламеобразующих газов, и наконечника с головкой, в которой происходит образование пламени.
На рисунке представлен пример газового резака фирмы KRASS
Внешне резак и сварочная горелка имеют много общего. Как отмечалось выше, основное отличие заключается в отсутствии у последней подачи кислорода режущей струи и другое устройство головки. Больше о горелках можно прочитать в статье: горелка газовоздушная для газопламенной обработки материалов.
Газовый резак инжекторного типа
Инжекторные устройства позволяют использовать горючий газ низкого, среднего и высокого давления. Проходя через инжектор, подогревающий кислород, реализует в смесительной камере эффект разрежения, вследствие чего осуществляется подсос газа. Далее смесь поступает в головку, а из нее подается в шлицевые каналы внутреннего мундштука.
Комплектация аппарата может состоять из 6 внутренних мундштуков (№№ 0-5), которые обеспечивают раскрой металла толщиной до 20 см при работе с ацетиленом, и 7 внутренних мундштуков (№№ 0-6) для толщин 0,3-30 см при работе с пропаном-бутаном. Данное оборудование также может комплектоваться разными модификациями наружных мундштуков (№1 для диапазона толщин 0,3-10 см; №2 для 10-30 см).
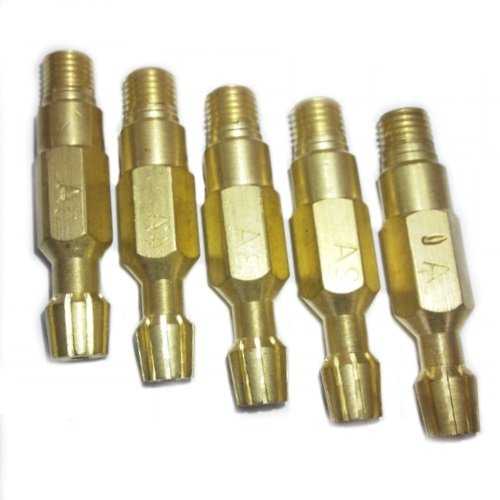
На рисунке представлены внутренние мундштуки
Для обработки углеродистых и низкоуглеродистых сталей толщиной до 10 см применяется инжекторный газовый резак Р3П-100 «Krass», который выпускается как для работы с ацетиленом, так и с пропаном-бутаном. Для более толстой стали (до 30 см) используется P3П-300 «Krass», работающий с ацетиленом, пропаном и метаном. Кстати, статьи о технических газах Вы можете прочитать в этом разделе.
Внутрисопловое смешение
В устройствах с внутрисопловым смешением смесь образуется в шлицевых каналах между наружной гильзой и внутренним мундштуком. Подача режущего кислорода осуществляется рычажным клапаном, а подогревающего и горючего газа – регуляторами, которые установлены на рукоятке.
Данное оборудование выпускается в 3-х исполнениях: для работы с ацетиленом, пропаном и природным газом. Поскольку газ смешивается не у рукоятки, как в инжекторных устройствах, а в головке, такие аппараты имеют повышенный уровень безопасности. Вместе с тем, подобный принцип действия требует более сложной конструкции, что приводит к увеличению стоимости приспособления. Также для стабильной работы требуется повышенное давление горючего газа – от 20 кПа.
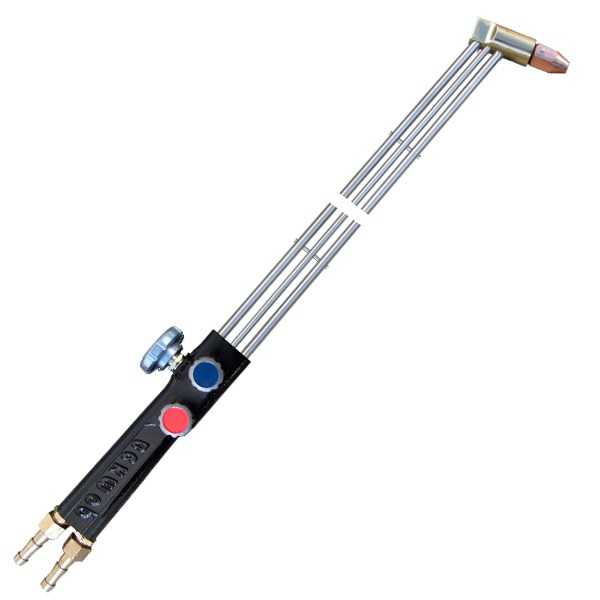
Устройства с внутрисопловым смешением
Керосино-кислородные резаки
Оборудование для резки металла, работающее на керосине, обладает конструктивными отличиями от газовых аппаратов, поскольку для получения пламени необходимо превращение жидкости в газообразное состояние. Данный процесс осуществляется в испарителе, подогрев керосина в котором реализуется с помощью специального подогревающего сопла.
Горючее подается из бачка по маслобензостойкому шлангу под давлением 30 кПа. Емкость снабжена предохранительным клапаном и ручным насосом, и с учетом конструкции позволяет залить до 8 л горючего. Устройство такого типа имеет востребованность при работе в полевых условиях.
Что нужно знать при работе с резаками
Прежде нужно знать принцип работы и классификацию этих устройств. Для этого можете посмотреть видео ниже:
- Каждый маховик вентиля имеет маркировку газа, подачу которого он регулирует.
- Стрелками на вентиле указывается направление при открытии и закрытии («О» — открытие, «З» — закрытие).
- На сменном мундштуке указывается индекс газа («А» — ацетилен, «П» — пропан, «М» — метан).
- Гайка кислородного штуцера имеет правую резьбу, а горючего газа – левую.
- Детали, соприкасающиеся с ацетиленом до камеры смешения, не изготавливаются из меди и медесодержащих сплавов (>65%).
Также советуем посмотреть видео о том, как выбрать данное устройство:
В компании «Промтехгаз» можно приобрести качественные резаки фирмы «Krass», которые осуществляют газовую резку металла (до 30 см), а также заправить баллон пропаном по оптимальной цене.
xn--80affkvlgiu5a.xn--p1ai
Газовый резак по металлу
Резка с помощью газа – операция не столь сложная, в сравнении с другими работами, поэтому для ее выполнения не нужны высокие квалификации. Для ее выполнения чаще других используется пропановый резак, поскольку газ имеет невысокую стоимость и весьма эффективен в работе. Этим оборудованием режут металлические листы, различной толщины, узлы и детали, вплоть до заготовок ювелирных украшений. Газовый резак по металлу широко используется, как на производстве, так и в быту. Оборудование действует за счет сгорания обрабатываемого материала, окислы выдуваются с помощью струи газа.
Устройство газового резака
Резак газовый представляет собой конструкцию из ствола и наконечника. Если наконечник имеет локальную конструкцию, то ствол состоит из следующих элементов:
- рукоять, обустроенная ниппелями, для соединения с газовым и кислородным рукавом;
- корпус с вентилями регуляции;
- смесительная камера;
- инжектор;
- трубы для подачи газовых сред.
Ствол крепится к корпусу с помощью накидной гайки.
Разновидности газовых резаков
Данное оборудование принято классифицировать по нескольким критериям.
По виду рабочего газа:
- ацетиленовый;
- пропановый;
- метановый и другие.
По технологии смешивания газов и кислорода:
- инжекторные;
- безинжекторные.
По назначению:
- универсальные;
- для работы под водой;
- для формирования отверстий;
- для разрезания толстых металлических листов и другие.
По видам резания:
- кислородно-флюсовый;
- разделительный;
- копьевый;
- поверхностный.
Преимущества газового оборудования для резки:
- резание в любом направлении металлических изделий и листов, толщиной до 30 см;
- компактный газовый резак прост в использовании;
- оборудование устойчиво;
- устройство имеет компактные размеры и небольшую массу, существуют мини модели;
- устройства прекрасно выдерживают удары обратного направления;
- невысокая стоимость готового оборудования позволяет иметь свой резак каждому домашнему мастеру;
- простая конструкция позволяет сделать резак своими руками;
- простая настройка интенсивности работы горелки.
Это оборудование имеет набор характеристик, которые обеспечивают продолжительную и надежную эксплуатацию, в том числе легкая заменимость всех элементов. Допустима установка аналоговых запасных частей. Газовый резак мини
Мини газовый резак по металлу представляет собой модель портативного автогена или зажигалки с дюзой резака. Работает устройство по тождественному принципу. После нажатия на клапан газ протекает через маленькое отверстие и попадает в дюзу уже с ускорением. Струя поджигается пьезоэлементом, образуется пламя, которое приобретает форму конуса. Портативный газовый резак нагревается незначительно, ее можно спокойно держать голой рукой. Газ довольно быстро заканчивается, поскольку емкость для него – небольшая. Зарядка портативного газового резака выполняется от цангового баллона.
Газовый резак своими руками
Переносной газовый резак имеет простую конструкцию, что позволяет мастерам делать их своими руками. Для работы вам понадобятся:
- обычная капельница, которую можно приобрести в любой аптеке;
- игра для накачивания спортивного мяча, оптимально – футбольного, будет использована в качестве наконечника;
- бутылка из пластика;
- баллон для газа можно демонтировать из зажигалки;
- проволока из меди;
- термопистолет;
- набор инструментов.
Процесс изготовления резака своими руками выполняется последовательно:
- на игле от мяча нужно сделать напильником надрез на расстоянии 1,5-2 см от конца;
- у иглы от капельницы, которая будет подавать воздух, нужно отрезать острый конец, а затем на расстоянии 2 см от края, загнуть под углом в 45 градусов и вставить в надрез, сделанный на игле для мяча;
- две иглы фиксируют между собой с помощью проволоки, паяльника и олова;
- капельницу надевают на концы иголок, при этом демонтировать колесики не нужно, впоследствии они станут регулировочными вентилями;
- затем нужно сделать сопло резака своими руками, здесь придется немного поусердствовать, поскольку диаметр капельницы меньше, чем у этого элемента;
- далее нужно сделать своими руками баллон для воздуха из 1,5-2-литровой пластиковой бутылки, для этого на ее дне нужно сделать отверстие для соска автошины, который закрепляется гайкой;
- герметичность можно обеспечить любым клейким составом, выдерживающим высокие температуры;
- в верхней части бутылки делается отверстие под капельницу, куда капельница и устанавливается – это система подачи сжатого воздуха;
- аналогично устанавливается емкость на иглу для накачки мяча – это система подачи газа;
- ограничители капельницы приоткрываются, поджигается выходящий газ, пламя нужно отрегулировать до голубого цвета, что обозначает температурный режим в 1,5 тысячи градусов;
- таким пламенем можно резать метал, толщиной в 1 мм.
Не стоит думать, что данная конструкция – одноразовая. При правильном уходе она прослужит вам годы.
Как настроить газовый резак
Данное оборудование собирается и настраивается легко, но если вы новичок, лучше проконсультироваться со специалистами, например, на форумах. Основное – это соблюдать технику безопасности. Обычный резак собирается следующим образом:
- Сначала устанавливаются редукторы. Синий – для кислородного баллона. Здесь нужно осмотреть вентиль на предмет масленых следов, наличие которых может привести к взрыву. Красный редуктор предназначен для баллона с газом. Обязательно проверьте состояние прокладок.
- Проверьте штуцер на целостность и отсутствие дефектов, при необходимости его можно поправить напильником.
- Подобрать трубки согласно резьбе, также осмотреть на предмет дефектов. Они соединяются с редукторами посредством хомутов. Следует помнить, что кислородный шланг нельзя продувать газом, и – наоборот. Также запрещено менять их.
- На штуцер нужно установить клапан удара.
- Если резак инжекторный, нужно проверить инжекцию, это можно сделать пальцем, если он притягивается на штуцере – все в порядке.
- Далее соединяют трубку с газом. При работе с пропаном устанавливается давление 0,5. Соотношение кислорода рассчитывается, как 1/10.
- Приоткрывается кислород и пропан, смесь газов поджигается.
- Теперь нужно поднести пламя к металлу и добавить кислород, до момента, когда появляются коронки.
При завершении работы вентили нужно закрыть. Если в процессе резки пламя затухнет, нужно отключить приток пропана, а подачу кислорода увеличить на несколько секунд. Поскольку, если перекрыть кислород – создается взрывоопасная ситуация.
Поделись с друзьями
0
0
0
0
svarkalegko.com
Газовый резак — Википедия
Газовый резак (резак для ручной резки), также автоген — аппарат для резки металла с помощью нагревания до высоких температур. Сущность процесса заключается в сгорании металла в струе химически чистого кислорода, с последующим удалением этой струёй продуктов окисления из зоны реза (выдувом).
Ручные резаки для газовой резки классифицируются по следующим признакам:
- по роду горючего газа, на котором они работают: для ацетилена, газов-заменителей, жидких горючих;
- по принципу смешения горючего газа и кислорода на эжекторные и без эжекторные;
- по назначению — на универсальные и специальные;
- по виду резки для разделительной, поверхностной, кислородно-флюсовой, копьевой.
В настоящее время широкое применение получили универсальные резаки. К универсальным резакам предъявляются следующие основные требования: возможность резки стали толщиной от 3 до 300 мм в любом направлении, устойчивость против обратных ударов, малая масса и удобство в обращении. Как и сварочные горелки, резаки имеют эжекторное устройство, обеспечивающее нормальную работу горючего газа в диапазоне давлений 0,03—1,5 кгс/см². Эжекторный резак отличается от инжекторной горелки тем, что имеет отдельный канал для подачи режущего кислорода и специальную головку, которая включает в себя два сменных мундштука — внутренний и наружный.
Газокислородный инжекторный резак состоит из двух основных частей — ствола и наконечника. Ствол состоит из рукоятки с ниппелями для присоединения кислородного и газового рукавов, корпуса с регулировочными кислородным и газовым вентилями, инжектора, смесительной камеры, трубки, головки резака с внутренним мундштуком и наружным, трубки режущего кислорода с вентилем. Ствол присоединяется к корпусу накидной гайкой.
Кислород из баллона через редуктор и шланг с ниппелями поступает в резак, в корпусе разветвляется по двум каналам. Часть газа, проходя через вентиль, направляется в эжектор. Выходя из эжектора с большой скоростью, струя кислорода создаёт разрежение и подсасывает горючий газ, образующий с кислородом в смесительной камере горючую смесь, которая проходя через зазор между наружными и внутренними мундштуками, сгорает, образуя подогревающее пламя.
Другая часть кислорода через вентиль поступает в трубку режущего кислорода, выходя через центральный канал внутреннего мундштука, образует струю режущего кислорода. Основной деталью резака является мундштук и сопло, которые в процессе резки быстро изнашиваются. Для получения качественного реза необходимо иметь правильные размеры сопла, мундштука.Правильные соотношения давления подачи газа с соответствующей толщиной метала. Необходимо также не забывать про постоянный уход и чистку каналов сопла медными прутками.
Требования к металлу для возможности кислородной резки[править]
Для возможности кислородной резки к металлу предъявляются довольно жесткие требования:
- Температура плавления металла должна быть выше температуры его воспламенения в кислороде, так как металл не успевает сгорать (температура плавления железа составляет 1539 °C, а температура воспламенения — 1100—1200 °C). Например, высокоуглеродистые стали и чугуны резать обычным резаком невозможно, поскольку углерод заметно снижает температуру плавления.
- Температура плавления металла должна быть выше температуры плавления его окислов, иначе оксидная пленка будет препятствовать доступу кислорода к металлу и горения (резки) не будет.
- Окислы, образующиеся при резке, должны быть достаточно жидко-текучими. При их избытке они налипают на кромки реза, и удалить их очень трудно (окислы кремния, хрома и др. обладают высокой вязкостью).
- Металл должен обладать низкой теплопроводностью, иначе тепла горелки не хватит для нагрева кромки перед началом резки.
- Удельная теплота сгорания металла должна обеспечивать большую часть энергии для разогрева слоев металла, прилегающих к резу.
В основном, этим требованиям удовлетворяют только низкоуглеродистые и низколегированные стали. Из цветных металлов кислородной резке поддается только титан.
Для некоторых материалов, не удовлетворяющих данным условиям, возможна кислородно-флюсовая резка. В кислородно-флюсовом резаке, кроме режущей кислородной струи, в рез подается струя железных опилок, сгорание которых увеличивает температуру в резе, добавляет системе мощности, а также разжижает тугоплавкие окислы.
Качество резки[править]
На качество резки влияет:
- Расход кислорода. Недостаток кислорода приводит к неполному окислению металла и малой интенсивности удаления окислов; а избыток — к охлаждению и выносу тепла из зоны резки.
- Чистота кислорода. Снижение чистоты влияет на качество кромок реза; Чем ниже чистота, тем больше налипает трудноотделимый шлак на нижней кромке реза.
- Мощность подогревающего пламени; В зависимости от состава смеси пламя бывает окислительным, нормальным и науглероживающим. Окислительное — для резки стали толщиной 3—8 мм. Нормальное — для толщин 10—100 мм. Науглероживающее — для больших толщин.
- Общая длина пламени должна быть больше толщины разрезаемого металла.
Скорость резки[править]
При малой скорости ведения резака — оплавляются кромки, при слишком большой скорости ведения — неполное разрезание металла из-за отставания кислородной струи.
газопламенная резка, правильная скорость и расстояния до металла.Для того чтобы расплавленный шлак свободно вытекал из зоны реза, под разогреваемым листом должно быть свободное пространство
L (мм),
L = S/2 + 100,
где S — толщина разрезаемого металла, мм; В зависимости от толщины разрезаемого металла устанавливают необходимые внутренний и наружный мундштуки.
- И. И. Соколов «Газовая сварка и резка металлов», Москва «Высшая школа» 1986.
www.wikiznanie.ru
Резак газовый Википедия
Работа резаком Р3 337У на ММК им. ИльичаГазовый резак (резак для ручной резки), также автоген — аппарат для резки металла с помощью нагревания до высоких температур. Сущность процесса заключается в сгорании металла в струе чистого кислорода, с последующим удалением этой струёй продуктов окисления из зоны реза (выдувом).
Ручные резаки для газовой резки классифицируются по следующим признакам:
- по роду горючего газа, на котором они работают: для ацетилена, газов-заменителей, жидких горючих;
- по принципу смешения горючего газа и кислорода на эжекторные и безэжекторные;
- по назначению — на универсальные и специальные;
- по виду резки для разделительной, поверхностной, кислородно-флюсовой, копьевой.
В настоящее время широкое применение получили универсальные резаки. К универсальным резакам предъявляются следующие основные требования: возможность резки стали толщиной от 3 до 300 мм в любом направлении, устойчивость против обратных ударов, малая масса и удобство в обращении. Как и сварочные горелки, резаки имеют эжекторное устройство, обеспечивающее нормальную работу горючего газа в диапазоне давлений 0,03—1,5 кгс/см². Эжекторный резак отличается от инжекторной горелки тем, что имеет отдельный канал для подачи режущего кислорода и специальную головку, которая включает в себя два сменных мундштука — внутренний и наружный.
Ссылки
Литература
- И. И. Соколов «Газовая сварка и резка металлов», Москва «Высшая школа» 1986.
wikiredia.ru
Газовый резак — Википедия
Газовый резак (резак для ручной резки), также автоген — аппарат для резки металла с помощью нагревания до высоких температур. Сущность процесса заключается в сгорании металла в струе химически чистого кислорода, с последующим удалением этой струёй продуктов окисления из зоны реза (выдувом).
Ручные резаки для газовой резки классифицируются по следующим признакам:
- по роду горючего газа, на котором они работают: для ацетилена, газов-заменителей, жидких горючих;
- по принципу смешения горючего газа и кислорода на эжекторные и без эжекторные;
- по назначению — на универсальные и специальные;
- по виду резки для разделительной, поверхностной, кислородно-флюсовой, копьевой.
В настоящее время широкое применение получили универсальные резаки. К универсальным резакам предъявляются следующие основные требования: возможность резки стали толщиной от 3 до 300 мм в любом направлении, устойчивость против обратных ударов, малая масса и удобство в обращении. Как и сварочные горелки, резаки имеют эжекторное устройство, обеспечивающее нормальную работу горючего газа в диапазоне давлений 0,03—1,5 кгс/см². Эжекторный резак отличается от инжекторной горелки тем, что имеет отдельный канал для подачи режущего кислорода и специальную головку, которая включает в себя два сменных мундштука — внутренний и наружный.
Газокислородный инжекторный резак состоит из двух основных частей — ствола и наконечника. Ствол состоит из рукоятки с ниппелями для присоединения кислородного и газового рукавов, корпуса с регулировочными кислородным и газовым вентилями, инжектора, смесительной камеры, трубки, головки резака с внутренним мундштуком и наружным, трубки режущего кислорода с вентилем. Ствол присоединяется к корпусу накидной гайкой.
Кислород из баллона через редуктор и шланг с ниппелями поступает в резак, в корпусе разветвляется по двум каналам. Часть газа, проходя через вентиль, направляется в эжектор. Выходя из эжектора с большой скоростью, струя кислорода создаёт разрежение и подсасывает горючий газ, образующий с кислородом в смесительной камере горючую смесь, которая проходя через зазор между наружными и внутренними мундштуками, сгорает, образуя подогревающее пламя.
Другая часть кислорода через вентиль поступает в трубку режущего кислорода, выходя через центральный канал внутреннего мундштука, образует струю режущего кислорода. Основной деталью резака является мундштук и сопло, которые в процессе резки быстро изнашиваются. Для получения качественного реза необходимо иметь правильные размеры сопла, мундштука.Правильные соотношения давления подачи газа с соответствующей толщиной метала. Необходимо также не забывать про постоянный уход и чистку каналов сопла медными прутками.
Требования к металлу для возможности кислородной резки[править]
Для возможности кислородной резки к металлу предъявляются довольно жесткие требования:
- Температура плавления металла должна быть выше температуры его воспламенения в кислороде, так как металл не успевает сгорать (температура плавления железа составляет 1539 °C, а температура воспламенения — 1100—1200 °C). Например, высокоуглеродистые стали и чугуны резать обычным резаком невозможно, поскольку углерод заметно снижает температуру плавления.
- Температура плавления металла должна быть выше температуры плавления его окислов, иначе оксидная пленка будет препятствовать доступу кислорода к металлу и горения (резки) не будет.
- Окислы, образующиеся при резке, должны быть достаточно жидко-текучими. При их избытке они налипают на кромки реза, и удалить их очень трудно (окислы кремния, хрома и др. обладают высокой вязкостью).
- Металл должен обладать низкой теплопроводностью, иначе тепла горелки не хватит для нагрева кромки перед началом резки.
- Удельная теплота сгорания металла должна обеспечивать большую часть энергии для разогрева слоев металла, прилегающих к резу.
В основном, этим требованиям удовлетворяют только низкоуглеродистые и низколегированные стали. Из цветных металлов кислородной резке поддается только титан.
Для некоторых материалов, не удовлетворяющих данным условиям, возможна кислородно-флюсовая резка. В кислородно-флюсовом резаке, кроме режущей кислородной струи, в рез подается струя железных опилок, сгорание которых увеличивает температуру в резе, добавляет системе мощности, а также разжижает тугоплавкие окислы.
Качество резки[править]
На качество резки влияет:
- Расход кислорода. Недостаток кислорода приводит к неполному окислению металла и малой интенсивности удаления окислов; а избыток — к охлаждению и выносу тепла из зоны резки.
- Чистота кислорода. Снижение чистоты влияет на качество кромок реза; Чем ниже чистота, тем больше налипает трудноотделимый шлак на нижней кромке реза.
- Мощность подогревающего пламени; В зависимости от состава смеси пламя бывает окислительным, нормальным и науглероживающим. Окислительное — для резки стали толщиной 3—8 мм. Нормальное — для толщин 10—100 мм. Науглероживающее — для больших толщин.
- Общая длина пламени должна быть больше толщины разрезаемого металла.
Скорость резки[править]
При малой скорости ведения резака — оплавляются кромки, при слишком большой скорости ведения — неполное разрезание металла из-за отставания кислородной струи.
газопламенная резка, правильная скорость и расстояния до металла.Для того чтобы расплавленный шлак свободно вытекал из зоны реза, под разогреваемым листом должно быть свободное пространство
L (мм),
L = S/2 + 100,
где S — толщина разрезаемого металла, мм; В зависимости от толщины разрезаемого металла устанавливают необходимые внутренний и наружный мундштуки.
- И. И. Соколов «Газовая сварка и резка металлов», Москва «Высшая школа» 1986.
www.wikiznanie.ru
Газовый резак Википедия
Работа резаком Р3 337У на ММК им. ИльичаГазовый резак (резак для ручной резки), также автоген — аппарат для резки металла с помощью нагревания до высоких температур. Сущность процесса заключается в сгорании металла в струе чистого кислорода, с последующим удалением этой струёй продуктов окисления из зоны реза (выдувом).
Ручные резаки для газовой резки классифицируются по следующим признакам:
- по роду горючего газа, на котором они работают: для ацетилена, газов-заменителей, жидких горючих;
- по принципу смешения горючего газа и кислорода на эжекторные и безэжекторные;
- по назначению — на универсальные и специальные;
- по виду резки для разделительной, поверхностной, кислородно-флюсовой, копьевой.
В настоящее время широкое применение получили универсальные резаки. К универсальным резакам предъявляются следующие основные требования: возможность резки стали толщиной от 3 до 300 мм в любом направлении, устойчивость против обратных ударов, малая масса и удобство в обращении. Как и сварочные горелки, резаки имеют эжекторное устройство, обеспечивающее нормальную работу горючего газа в диапазоне давлений 0,03—1,5 кгс/см². Эжекторный резак отличается от инжекторной горелки тем, что имеет отдельный канал для подачи режущего кислорода и специальную головку, которая включает в себя два сменных мундштука — внутренний и наружный.
Ссылки[ | ]
Литература[ | ]
- И. И. Соколов «Газовая сварка и резка металлов», Москва «Высшая школа» 1986.
ru-wiki.ru
Газовый резак — Википедия
Газовый резак (резак для ручной резки), также автоген — аппарат для резки металла с помощью нагревания до высоких температур. Сущность процесса заключается в сгорании металла в струе химически чистого кислорода, с последующим удалением этой струёй продуктов окисления из зоны реза (выдувом).
Ручные резаки для газовой резки классифицируются по следующим признакам:
- по роду горючего газа, на котором они работают: для ацетилена, газов-заменителей, жидких горючих;
- по принципу смешения горючего газа и кислорода на эжекторные и без эжекторные;
- по назначению — на универсальные и специальные;
- по виду резки для разделительной, поверхностной, кислородно-флюсовой, копьевой.
В настоящее время широкое применение получили универсальные резаки. К универсальным резакам предъявляются следующие основные требования: возможность резки стали толщиной от 3 до 300 мм в любом направлении, устойчивость против обратных ударов, малая масса и удобство в обращении. Как и сварочные горелки, резаки имеют эжекторное устройство, обеспечивающее нормальную работу горючего газа в диапазоне давлений 0,03—1,5 кгс/см². Эжекторный резак отличается от инжекторной горелки тем, что имеет отдельный канал для подачи режущего кислорода и специальную головку, которая включает в себя два сменных мундштука — внутренний и наружный.
Газокислородный инжекторный резак состоит из двух основных частей — ствола и наконечника. Ствол состоит из рукоятки с ниппелями для присоединения кислородного и газового рукавов, корпуса с регулировочными кислородным и газовым вентилями, инжектора, смесительной камеры, трубки, головки резака с внутренним мундштуком и наружным, трубки режущего кислорода с вентилем. Ствол присоединяется к корпусу накидной гайкой.
Кислород из баллона через редуктор и шланг с ниппелями поступает в резак, в корпусе разветвляется по двум каналам. Часть газа, проходя через вентиль, направляется в эжектор. Выходя из эжектора с большой скоростью, струя кислорода создаёт разрежение и подсасывает горючий газ, образующий с кислородом в смесительной камере горючую смесь, которая проходя через зазор между наружными и внутренними мундштуками, сгорает, образуя подогревающее пламя.
Другая часть кислорода через вентиль поступает в трубку режущего кислорода, выходя через центральный канал внутреннего мундштука, образует струю режущего кислорода. Основной деталью резака является мундштук и сопло, которые в процессе резки быстро изнашиваются. Для получения качественного реза необходимо иметь правильные размеры сопла, мундштука.Правильные соотношения давления подачи газа с соответствующей толщиной метала. Необходимо также не забывать про постоянный уход и чистку каналов сопла медными прутками.
Требования к металлу для возможности кислородной резки[править]
Для возможности кислородной резки к металлу предъявляются довольно жесткие требования:
- Температура плавления металла должна быть выше температуры его воспламенения в кислороде, так как металл не успевает сгорать (температура плавления железа составляет 1539 °C, а температура воспламенения — 1100—1200 °C). Например, высокоуглеродистые стали и чугуны резать обычным резаком невозможно, поскольку углерод заметно снижает температуру плавления.
- Температура плавления металла должна быть выше температуры плавления его окислов, иначе оксидная пленка будет препятствовать доступу кислорода к металлу и горения (резки) не будет.
- Окислы, образующиеся при резке, должны быть достаточно жидко-текучими. При их избытке они налипают на кромки реза, и удалить их очень трудно (окислы кремния, хрома и др. обладают высокой вязкостью).
- Металл должен обладать низкой теплопроводностью, иначе тепла горелки не хватит для нагрева кромки перед началом резки.
- Удельная теплота сгорания металла должна обеспечивать большую часть энергии для разогрева слоев металла, прилегающих к резу.
В основном, этим требованиям удовлетворяют только низкоуглеродистые и низколегированные стали. Из цветных металлов кислородной резке поддается только титан.
Для некоторых материалов, не удовлетворяющих данным условиям, возможна кислородно-флюсовая резка. В кислородно-флюсовом резаке, кроме режущей кислородной струи, в рез подается струя железных опилок, сгорание которых увеличивает температуру в резе, добавляет системе мощности, а также разжижает тугоплавкие окислы.
Качество резки[править]
На качество резки влияет:
- Расход кислорода. Недостаток кислорода приводит к неполному окислению металла и малой интенсивности удаления окислов; а избыток — к охлаждению и выносу тепла из зоны резки.
- Чистота кислорода. Снижение чистоты влияет на качество кромок реза; Чем ниже чистота, тем больше налипает трудноотделимый шлак на нижней кромке реза.
- Мощность подогревающего пламени; В зависимости от состава смеси пламя бывает окислительным, нормальным и науглероживающим. Окислительное — для резки стали толщиной 3—8 мм. Нормальное — для толщин 10—100 мм. Науглероживающее — для больших толщин.
- Общая длина пламени должна быть больше толщины разрезаемого металла.
Скорость резки[править]
При малой скорости ведения резака — оплавляются кромки, при слишком большой скорости ведения — неполное разрезание металла из-за отставания кислородной струи.
газопламенная резка, правильная скорость и расстояния до металла.Для того чтобы расплавленный шлак свободно вытекал из зоны реза, под разогреваемым листом должно быть свободное пространство
L (мм),
L = S/2 + 100,
где S — толщина разрезаемого металла, мм; В зависимости от толщины разрезаемого металла устанавливают необходимые внутренний и наружный мундштуки.
- И. И. Соколов «Газовая сварка и резка металлов», Москва «Высшая школа» 1986.
wp.wiki-wiki.ru