Как работает резак плазменный – Плазменный резак – преимущества и недостатки
alexxlab | 15.07.2017 | 0 | Вопросы и ответы
принцип работы и особенности технологии, устройство ручного резака
Плазменная резка – новая великолепная технология, позволяющая разрезать металлы солидной толщины и любой природы, даже самой капризной. В качестве режущего предмета выступает не нож, а плотная струя плазмы, которая позволяет формировать идеально точный рисунок реза в единицу заданного времени.
Этот способ работы с металлом содержит множество достоинств, которые мы разберем ниже. А сейчас начнем с физики – нужно разобраться с сутью процесса.
Физика плазмы
Технология плазменной резки металла отдает главную женскую роль нашей любимой электрической дуге. Он формируется между электродом и соплом. Иногда вместо электрода выступает металл, который нужно разрезать. Разберемся, что такое плазменная резка.
Начало процесса – включение источника электрического питания и подача тока высокой частоты в плазменный резак. Источник питания включается автоматически после нажатия тумблера розжига в аппарате.
Сначала формируется так называемая промежуточная дуга – она имеет временный характер и соединяет электрод с наконечником сопла резака. Нагревается эта дежурная дуга до уровня температуры около 8000°С.
Это важный момент общего процесса плазменной резки – нужно помнить, что настоящая дуга между электродом и металлом образуется не сразу, а через ее промежуточный вариант.
Следующий этап процесса – поступление воздуха из компрессора, который обычно прилагается к аппарату резки металла. Компрессор подает воздух в сжатом виде. Этот воздух поступает в камеру плазмотрона, в котором находится и уже раскалена временная электрическая дуга.
Дуга нагревает сжатый воздух, объем которого при нагреве увеличивается во много раз. Дополнительно к нагреву и увеличению объема воздух начинает ионизироваться и трансформироваться в настоящий проводник электрического тока. Он превращается в ту самую плазму
Малый диаметр сопла дает возможность разгонять поток этой раскаленной плазмы до огромных скоростей, с которыми струя вылетает из аппарата. Скорость потока может достигать трех метров в секунду.
Схема работы плазменной резки.
Температура воздуха – запредельная, вплоть до 30 000°С. При этих условиях электрическая проводимость воздуха – плазмы практически равна проводимости разрезаемого металла.
Настоящая конечная дуга появляется мгновенно, как только поток плазмы достигает и касается поверхности металла. Временная дуга, в свою очередь, автоматически выключается. Металл начинает плавится точно в месте среза.
Жидкие металлические капли сразу же сдуваются струей сжатого воздуха. Это и есть принцип плазменной резки. Как видите, все просто, логично и понятно.
Классификация видов плазменной резки
Виды плазменной резки будут зависеть от среды, в которой проводятся работы по металлу:
Простой
Главное отличие способа – ограниченность электрической дуги. Для резки используется электрический ток и воздух. Иногда вместо воздуха применяются газ в виде азота. Если металлически лист тонкий – всего несколько миллиметров, процесс можно сравнить с лазерным разрезанием.
При этом способе толщина металлов не должна превышать 10-ти мм. Способ отлично работает для низколегированных сплавов стали и других мягких металлов. Режущим элементом выступает кислород, из которого формируется сжатая струя, превращающаяся в итоге в плазму.
В разрезах получаются очень ровные кромки, не требующие дальнейшей доработки.
С применением защитного газа
При этом способе вместо воздуха используются защитные газы, которые превращаются в плазменный поток после преобразования в плазмотроне. Качество срезов в данном случае значительно повышается благодаря отличной защите процесса от воздействия окружающей среды.
Газ для плазменной резки не представляет из себя ничего необычного: это может быть водород или аргон – «газовая классика».
С водой вместо воздуха
Отличны способ со многими преимуществами, одно из которых – отсутствие необходимости в дорогостоящей и громоздкой системе охлаждения.
Существуют и другие критерии классификации плазменной резки. К примеру, виды резки бывают разделительными и поверхностными. Первый из них используется чаще.
Еще один параметр – способ резки. Один вид – резка дугой, в котором разрезаемый металл выступает в качестве элемента электрической цепи. Другой вид – резка струей, когда электрическая дуга соединяет электроды, а не металлическую заготовку.
Плазменные резаки представлены на рынке в самых разнообразных вариантах, так что их можно классифицировать по маркам, производителям и многим другим техническим и торговым параметрам.
Есть, например, ручная плазменная резка – самый демократичный способ и по цене, и по простоте исполнения. Есть машинные автоматические технологии, устройства для которых намного дороже и сложнее.
Преимущества резки плазмой
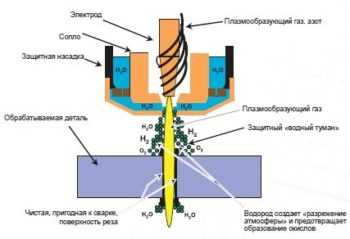
Принцип работы плазменной резки.
Самой близкой технологией является лазерная резка металлов, поэтому логично будет перечислить преимущества в сравнении с «соседкой»:
- Плазменной резке по плечу металлы любой природы, в том числе цветные, тугоплавкие и другие, сложные для обработки.
- Скорость процесса значительно выше, чем резка газовым резаком.
- Одна из значительных особенностей – возможность производить резы любой формы, включающие и геометрические узоры, и фигурную резку самой высокой сложности. Иными словами, резка с помощью плазмы – это реализация самых смелых творческих идей по металлу и другим трудно поддающимся материалам.
- Плазменному резаку нипочем любая толщина металла: скорость и качество никоим образом не теряются.
- Этому способу поддаются не только металлы, но и другие материалы: он вполне универсальный.
- Резка плазмой и быстрее, и эффективнее по качеству кромки, чем любые другие механические способы резки.
- В данном методе возможна работа не только перпендикулярно к поверхности металла, но под углом, что помогает освоить широкие листы металла.
- С экологической точки зрения это вполне благополучный вид работы с металлом с минимальным выбросом вредных веществ или загрязнений в воздух.
- Отличная экономия времени из-за отсутствия необходимости предварительно нагревать металл.
- Поскольку в методе не используются взрывоопасные газовые баллоны, он значительно безопаснее, чем другие способы.
Недостатки плазморезки
Ни один способ обработки металлов не обходится без недостатков, и плазменная резка здесь не исключение.
Недостатки плазменной резки следующие:
- Дороговизна всего модельного ряда аппаратов для плазменной резки, включая даже самые простые ручные варианты.
- Пределы толщины металла для резки плазмой: предельная толщина всего 100 миллиметров.
- Это шумный способ работы, потому что сжатый воздух или газ подаются с огромной скоростью.
- Оборудование непростое, дорогое и требующее грамотного и постоянного технического обслуживания.
Советы и нюансы
Еще одной отличительной положительно характеристикой метода является то, что во время процесса происходит нагрев лишь небольшого локального участка. Да и остывает этот участок намного быстрее, чем при лазерной или механической резке.
Охлаждение необходимо только для двух составных элементов – катода и сопла, как самых нагруженных. Это без проблем производится с помощью рабочей жидкости.
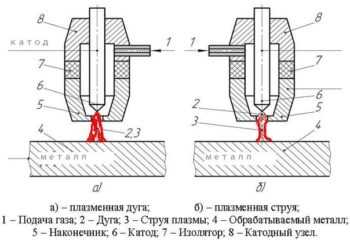
Плазменная дуга и струя.
Дуга начинает работать стабильно в результате рабочего соотношения катода и сопла с паром из сжатого раскаленного воздуха. На катоде локализуется отрицательный заряд, на наконечнике сопла – соответственно положительный. В результате этого образуется промежуточная дуга.
Лишняя влага впитывается специальным материалом, который находится в резервуаре камеры плазмотрона.
Правила безопасности при данном методе имеют строжайший характер, потому что все аппараты плазменной резки могут быть очень травматичными для мастера. Особенно это касается моделей с ручным управлением.
Все будет в порядке, если вы будете соблюдать рекомендации по защитной амуниции мастера: щиток, затемнённые очки, защитные ботинки и т.д. В этом случае вы сможете уберечься от главных факторов риска данного метода – капель расплавленного металла, высокого напряжения и раскаленного воздуха.
Еще один совет по безопасности – ни в коем случае не стучать резаком по металлу для удаления металлических брызг, как это делают некоторые мастера. Вы рискуете повредить аппарат, но главное – поймать кусочки расплавленного металла, например, лицом или другой незащищенной частью тела. Лучше поберечь себя.
Экономия расходных материалов занимает не последнее место в эффективной резке. Для этого зажигаем электрическую дугу не слишком часто, а точно и в срок, чтобы не обрывать ее без надобности.
Экономия ресурсов также распространяется на силу и мощность тока. Если рассчитать его правильно, вы получите не только экономию, но и отличный срез без заусениц, окалины и деформации металла.
Для этого следует работать по следующей схеме: сначала подать ток высокой мощности, сделать пару – тройку разрезов с его помощью. Если сила и мощность тока великоваты, на металле сразу же будет образовываться окалина из-за значительного перегрева.
После осмотра срезов будет ясно, оставить ток на этом уровне или изменить его. Иными словами, работаем экспериментально – малыми пробами.
Как работать плазморезкой?
Электрическая схема плазменного генератора.
Резка металлов с помощью плазменного потока – слишком серьезное дело, чтобы заниматься им без предварительного изучения и тщательной подготовки. Это поможет вам сделать резку эффективнее со всех точек зрения, и, что весьма немаловажно, минимизировать риски, связанные с производственными опасностями.
Прежде всего нужно знать принцип работы плазменной резки – видеть картинку физических явлений целиком.
Плазменную горелку следует держать очень близко к поверхности и краю металла, в отличие от лазерной резки. Когда тумблер с «пуском» включится, первой загорится временная электрическая дуга, и только затем – настоящая, которая будет главным режущим элементом. Горелку с режущей дугой нужно вести по материалу ровно и медленно.
Скорость резки следует строго контролировать. Это можно делать, наблюдая за искрами с обратной стороны листа разрезаемого металла. Если этих искр нет, то это значит, что разрезка металла произошла неполная.
Такое может произойти по нескольким причинам: из-за слишком большой скорости ведения горелки или прохождения аппарата, либо слишком недостаточной мощности подаваемого тока, либо несоблюдения прямого угла в 90° между горелкой и поверхностью металла.
Дело в том, что полная проплавка металла происходит лишь при наклоне плазморезки к поверхности металла под прямым углом и ни градусом больше или меньше.
После завершения работы резак нужно наклонить. Воздух будет выходить и после выключения аппарата – непродолжительное время.
Перед работой невредно изучить схему вашего аппарата: именно в ней можно прочитать самую достоверную информацию по допускаемой толщине металла, который можно прорезать или сделать в нем отверстие. Устройство плазменного резака может различаться, все зависит от функций его назначения.
Выбор аппарата для плазменной резки
Покупка любого технического оборудования – дело, для которого не нужно жалеть времени и усилий: слишком высок риск неудачного решения и потери денег. А деньги здесь немалые, вы не найдете плазменного резака дешевле 500 USD в принципе.
Сначала разбираемся с параметрами и техническими характеристиками прибора.
Выбор нужно делать только под свои планы и нужды. Задача – найти не самый лучший резак, а самый подходящий для вас по принципу «здесь и сейчас».
Две большие группы плазморезов – это инверторные и трансформаторные. Названия говорят сами за себя.
Открытая и закрытая плазменная струя.
Если вам нужен компактный резак для работы с металлами небольшой толщины, вы можете остановить свой выбор на резаке инверторного типа. Они забирают немного энергии, легкие и с небольшими габаритами.
Вместе с тем работают они с перерывами и легко выходят из строя при перепадах сетевого напряжения. Цена на такие приборы вполне умеренная, из всех плазморезов это самые недорогие.
Другое дело – трансформаторные резаки. Здесь и с габаритами, и с весом «все в порядке»: серьезные аппараты по всем параметрам.
Энергии потребляют много, зато работать они могут практически без перерыва в течение целого дня. И толщина металла может быть побольше, чем при резке инверторной моделью. Стоимость таких устройств высокая – от 3000 до 20000 USD.
Выбор плазменного резака по мощности
Рассуждения начинаем со свойств и технических характеристик деталей, которые вы планируете обрабатывать и резать. Именно это этого рассчитывается мощность режущего прибора, потому что в нем будут различаться и сопло по своему диаметру, и тип используемого газа.
Применение плазменной резки – область чрезвычайно широкая, поэтому говорить нужно только о ваших конкретных нуждах.
К примеру, если толщина металлических заготовок около 30-ти мм, вам будет вполне достаточно резака с мощностью 90А. Он легко справится с вашим материалом.
А вот если ваш металл потолще, ищите подходящую модель в диапазоне мощности от 90 до 170А.
Выбор резака по времени и скорости разрезания материала
Скорость плазменной резки металла измеряют в сантиметрах за одну минуту. Эта скорость у разных аппаратов тоже разная и зависит от их общей мощности и природы разрезаемого металла.
Например, при всех прочих равных медленнее всего режется сталь, чуть быстрее – медь и ее сплавы. И еще быстрее – алюминий со своими алюминиевыми сплавами.
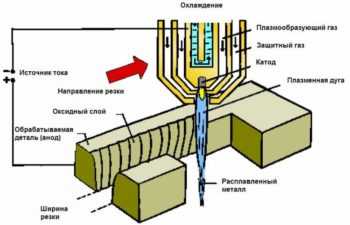
Устройство плазменного резака.
Если для вас важна скорость, не забывайте о таком показателе, как длительность работы без перегрева, то есть без перерыва. Если в технической спецификации к аппарату написано, что длительность работы 70%, это означает, что после семи минут резки аппарат должен быть выключенным в течение трех минут, чтобы остыть.
Среди трансформаторных резаков встречаются чемпионы с продолжительностью работы в 100%. Иными словами, они могут работать целый день без отключения. Стоят они, конечно, немало. Но если у вас впереди длинные разрезы, думайте о покупке «чемпионских» трансформаторных плазменных резаков.
Пара слов о горелке
Снова оцениваем природу металла или другого материала, который планируем разрезать. От этого будет зависеть мощность горелка плазмореза. Она должна быть достаточной для качественного реза.
При расчетах нужно учитывать факт, что вы можете встретиться со сложными условиями работы, которая, как назло, должны быть произведена в самые короткие сроки, то есть резка должна носить выраженных интенсивный характер.
Во многих источниках рекомендуется выбирать сопло из меди: оно прочное и отлично охлаждается воздухом, намного быстрее, чем сопла из других металлов.
Рукоятку горелку не упускаем из зоны внимания, это важная часть для комфортной, а значит качественной работы. На рукоятке можно зафиксировать дополнительные элементы, которые помогут держать сопло на одинаковом расстоянии от поверхности металла. Данный совет распространяется только на ручные модели аппаратов.
Если вы собираетесь резать тонкий металл, выбирайте модель с горелкой, которая предназначена для поступления воздуха.
Если же ваши планы связаны с массивными толстыми заготовками, покупайте резак с горелкой для приема защитного газа – азота, например.
tutsvarka.ru
Аппарат для плазменной резки металла, все о ручных плазморезах
Обычные сварочные аппараты не удобны при резке металлов и требуют особых навыков и практики у человека, использующего их для проведения работ по раскрою. Плазменные устройства более удобны и просты в эксплуатации.- Содержимое:
- Что такое плазморез, что им можно делать
- Принцип работы плазмореза, как устроен плазморез
- Какой и как выбрать плазморез для дома
- Как правильно резать плазморезом
- Ручная газовая и плазменная резка металла, что лучше
Первые модели плазменных резаков использовались исключительно в промышленных целях: машино- и судостроении, изготовлении металлоконструкций и т. д., то современный плазморез можно встретить и в обычном гараже используемую для личных нужд. Аппарат для плазменной резки металла позволяет точнее управлять технологическим процессом, а также значительно облегчает проведение работ.
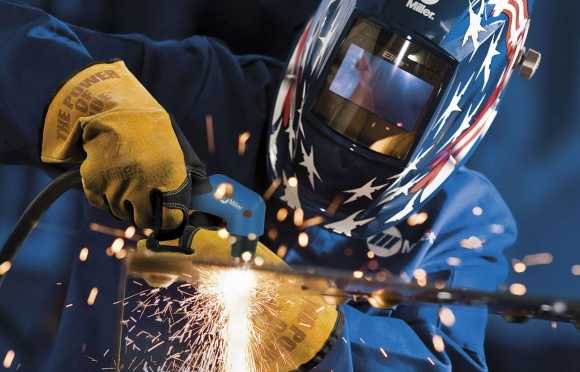
Что такое плазморез, что им можно делать
Переносная ручная плазменная резка металла в бытовых целях используется в основном во время капитального строительства. Плазморез позволяет заменить малоэффективную и опасную болгарку. С помощью плазмореза можно раскраивать необходимый листовой металлопрокат и трубы.
Еще одна сфера, где пригодится ручной аппарат плазменной резки металла – это художественная обработка материала. Точность, простота в эксплуатации и доступность использования плазменной установки практически в любых условиях, позволяет использовать оборудование в следующих целях:
- Промышленность – аппарат воздушно-плазменной резки металла в основном применяется в случаях, где существует необходимость в быстром разрезании любого токопроводящего материала. В промышленных целях используют не только аппарат для ручной плазменной резки металла, но и специальные плазменные станки позволяющие автоматизировать и сократить время выполнения работ.
- Бытовые цели – в этой сфере оборудование для ручной плазменной резки металла пока не получило широкого распространения. В основном это связано с тем, что ручные плазморезы сравнительно недавно поступили в свободную продажу. В основном применение плазмореза в бытовых целях связано с фигурной резкой металла. Некоторые строительные бригады используют оборудование во время кровельных, сантехнических и других работ.
В зависимости от основного назначения, аппарат для резки металла плазмой может отличаться техническими характеристиками и возможностями. Перед выбором плазменного оборудования следует определиться, как именно будет использоваться резак.
Принцип работы плазмореза, как устроен плазморез
Воздушно-плазменная резка основана на принципе подачи разогретого воздуха под давлением на обрабатываемую поверхность. Что такое плазма – это воздух, который разогревается до температуры 25 – 30 тыс. градусов с помощью электрической дуги.
Что происходит при этом? Принцип действия плазмореза основан на изменении свойств воздуха при его моментальном разогревании до максимально высоких температур. В этот момент воздух ионизируется и благодаря этому начинает пропускать электрический ток.
Двойное воздействие плазмы и электричества позволяет ускорить процесс резки металла. Чтобы это стало возможным в конструкцию резака входят следующие узлы:
- Плазмотрон – это резак, с помощью которого и выполняются все основные задачи. Устройство горелки плазмореза может быть прямого и косвенного воздействия:
- Плазморез прямого воздействия используется для обработки токопроводящих материалов, в таких случаях заготовка включается в электрическую цепь и отвечает за возникновение искры.
- Плазморез косвенного воздействия применяется в более дорогих и сложных устройствах и используется для обработки материалов, не проводящих электричество. Электрод в таких устройствах находится непосредственно в резаке.
- Плазморез прямого воздействия используется для обработки токопроводящих материалов, в таких случаях заготовка включается в электрическую цепь и отвечает за возникновение искры.
- Сопло – одна из самых функциональных деталей плазматрона. В зависимости от диаметра сопла, плазморезом можно делать либо простые операции, либо сложную фигурную резку. Скорость разрезания материала в основном зависит от длины сопла. Максимальным считается соотношение 1,5; 1,8 к диаметру сопла.
- Электрод – используется в дорогих моделях плазморезов косвенного воздействия. Преимущественно электроды изготавливаются из гафния.
- Компрессор – чтобы трансформировать воздух в плазму необходимо не только довести его до определенной температуры, но и создать поток определенной скорости. Именно по этой причине для плазмореза нужен компрессор. К качеству компрессора предъявляются высокие требования. Так, чтобы была возможность производства плазмы, воздух в горелку должен подаваться сухой и без примесей машинного масла. Важным является обеспечение равномерного потока воздушных масс без пульсации. Ручные плазменные резаки по металлу со встроенным компрессором являются оптимальным вариантом, так как в них производитель установил оборудование полностью соответствующее требованиям для проведения работ. В плазморезах со встроенным компрессором по умолчанию установлен влагоочиститель или осушитель. Плазморез с компрессором обеспечивает максимальную производительность и увеличивает срок эксплуатации резака.
Для мощных промышленных устройств понадобится отдельно приобрести не только компрессор, но и осушитель воздуха. При выборе плазмореза необходимо проследить, чтобы параметры каждого из этих узлов подходили остальным устройствам.
Какой и как выбрать плазморез для дома
При выборе плазмореза для дома необходимо учитывать не только технические параметры и производительность самой установки, но и комплектующие устройства. Обратить внимание необходимо на следующее:
- Тип питания – оборудование может подключаться как к обычной сети в 220В, так и трехфазной в 380В. От этой особенности во многом зависит производительность плазмореза и скорость резки. Для бытовых нужд лучше выбрать ручной плазморез с тем типом подключения, который есть в наличии. Производительности бытовой модели работающей от розетки будет достаточно для проведения всех необходимых работ по дому.
- Параметры мощности – наиболее популярными для бытового применения являются модели с производительностью 60-90 ампер. Бытовые плазморезы легко справляются с толстым металлом толщиной до 3 см. Если планируется ручная резка металла до 100 мм плазмой, тогда лучше выбрать модели, выдающие на выходе 90-170 ампер.
- Продолжительность работы – этот коэффициент можно посмотреть в технической документации установки. Обычно он обозначается сокращением ПВ. Если указано соотношение 80%, тогда плазморезом надо пользоваться в течение 8 минут, не больше. Для бытовых нужд будет достаточно оборудования с индексом ПВ 50-60%.
- Сопло для плазмореза – скорость резки напрямую связано с соплом. На скорость раскроя влияет соотношение диаметра к длине сопла. Скорость резки также указывается в технической документации. Выбор комплектующих зависит от используемой силы тока. Чем больше диаметр сопла, тем больше может быть напряжение на выходе.
- Дополнительные расходники к плазморезу. Стол-копир для ручной плазменной резки позволяет выполнять самые сложные детали, если процесс поставлен на конвейер. Часто даже в домашних условиях требуется воссоздать точную копию сделанной заготовки, для этого и проведения остальных работ, и предназначен стол-копир. Помимо стола понадобится определиться с другими комплектующими и приспособлениями, предназначенными для проведения работ с помощью плазмореза.
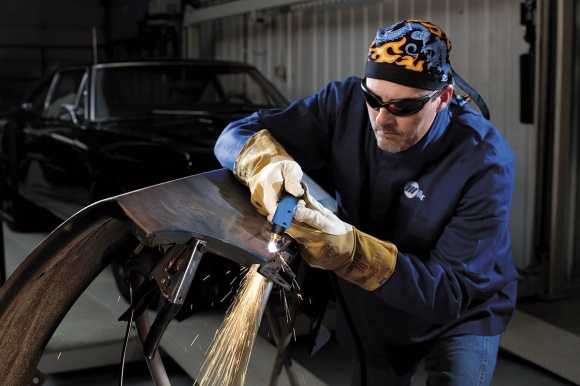
Многие критерии критичные для промышленного оборудования практически не влияют на производительность бытовой модели. Продолжительности работы плазмореза с индексом ПВ 50% будет достаточно для проведения работ в доме. Промышленное оборудование обычно имеет коэффициент равный 100%.
Как правильно резать плазморезом
Правильно работать плазморезом можно научиться практически с первого раза. Качественный рез достигается благодаря практике. Основные принципы работы с плазменным оборудованием следующие:
- На начальной стадии работ в аппарат подается сжатый воздух под давлением.
- Выполняется несколько надрезов при более высоком токе, после чего его силу уменьшают до необходимых параметров.
- Разрез делают в соответствии с выбранными параметрами. Неправильно подобранная сила тока или скорость резки свидетельствует окалинами, которые появляются в процессе резки.
- Держак для плазмореза располагают под углом около 40 градусов.
- После окончания резки, на горелку будет еще какое-то время подаваться воздух для охлаждения нагретого элемента.
При работе с плазматроном необходимо соблюдать требования относительно использования средств индивидуальной защиты. Потребуется одевать очки для плазменной резки и перчатки, даже если планируется использовать аппарат относительно короткое время.
Ручная газовая и плазменная резка металла, что лучше
Выбирая, что именно лучше следует учитывать цели, которые планируется достичь с использованием данной установки, желаемое качество выполнения работ и другие факторы.
Минусами газовой резки является зависимость от баллонов, что не всегда удобно, а для бытовых условий заправить их часто проблематично.
Плазменная резка имеет свои минусы, связанные в основном с тем, что качество реза напрямую зависит от профессионализма мастера. Также подаваемый воздух должен соответствовать определенным критериям, что требует использования дополнительного оборудования.
При плазменной резке может понадобиться использовать не только очки для работы, но и респираторную маску, и другие средства защиты. Проводить работы в помещении без хорошей вентиляции запрещается.
stroy-plys.ru
выбор аппарата для воздушно плазменной резки, станки и портативное оборудование
Договоримся-ка сразу. Если вас интересуют вопросы, касающиеся сварки в бытовых или кустарных условиях, то вам эту статью можно не читать. Плазменный резак – не детский сад и никоим образом не домашний инструмент. Если работы простые и разовые, можно поработать болгаркой.
Но уж если технические задачи стоят серьезные, а объемы работ огромные, то без резака для плазменной резки будет сложно. Это любимый инструмент в машиностроении всех профилей и многих других серьезных отраслях, где нужны «кройка и шитье» из металла.
Виды плазменных резаков
Все зависит от того, какие у вам планы, и где вы собираетесь работать. Дело в том, что плазморезы отличаются высокой вариативностью моделей. Они отличаются друг от друга не только эстетически, но и конструктивно: у них, к примеру, разные виды поджига электрической дуги и разные системы охлаждения.
Плазморезы могут быть переносными, могут представлять из себя целые портальные установки. Есть модели шарнирно-консольного типа, встречаются установки с приводом координатного вида. Особое место занимают аппараты с программным управлением.
Все резаки можно разделить следующим образом:
- Аппараты для работы в среде инертных и защитных газов: водорода, гелия и, конечно же, аргона.
- Резаки, функционирующие в среде окислительных газов – газов, которые насыщены кислородом.
- Резаки для работы с различными смесями.
- Для использования в стабилизаторах.
- Резаки с магнитной стабилизацией.
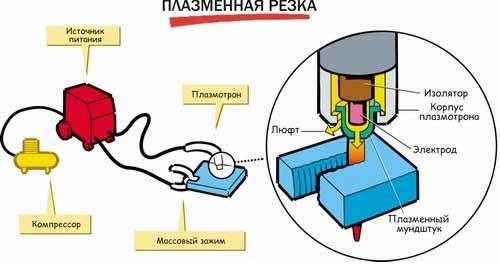
Принцип работы плазменной резки.
Классификация по виду потребляемой энергии:
- Бытовые резаки, которые подключаются к сети с напряжением 220 В.
- Профессиональные или промышленные, работающие только от сети с напряжением 380 В.
Следует учитывать, что даже бытовой плазменный резак с самыми скромными показателями мощности нужно проверить с подключением к общей сети: нагрузка сети будет очень серьезной. К тому же к резаку часто подключается компрессор для охлаждения. Его совсем немаленькую мощность также нужно учитывать при подключении.
Еще один критерий делит плазморезы ровно на две группы:
Резаки инверторного типа
отличный инструмент эконом-класса, который способен резать металл толщиной до 30-ти мм. Их используют чаще в быту и в малых мастерских. Энергопотребление у них весьма скоромное, они компактны: небольшого веса и изящных габаритов.
Большинство моделей являются переносными или ручными аппаратами. С их помощью можно работать в труднодоступных местах. Дополнительное преимущество – неплохой коэффициент полезного действия – выше на 30%.
Плазморезы трансформаторного типа
Они стоимостью подороже. Это больше походе на станок плазменной резки, как большой короб на колесиках. Режут металл с серьезной толщиной – вплоть до 80-ти мм. Они значительно тяжелее и больше по габаритам, чем инверторные.
Эти вес и размеры можно простить за большую надежность: обычно они не выходят из строя при скачках напряжения в сети, что чрезвычайно актуально для некоторых регионов. Продолжительность бесперебойного включения у этих аппаратов фантастическая – вплоть до 100%.
Это означает, что трансформаторный резак может работать весь день без перерыва. Кроме большого веса и крупных габаритов у этого вида аппаратов есть еще один недостаток: высокое потребление энергии. Как говориться, большому кораблю большое плавание.
Плазменные резаки можно разделить по виду контакта:
- Контактные, которые имеют контакт с металлом. Режут детали с толщиной не больше 18-ти мм.
- Бесконтактные, которым под силу резка металлов практически любой толщины.
Контактная плазменная резка
Это выглядит следующим образом: электрическая дуга соединяет плазмотрон и поверхность разрезаемой металлической детали, иными словами – дуга прямого действия. Вектор этой дуги всегда совмещается с потоком плазмы, выходящим из сопла под большим давлением с высокой скоростью.
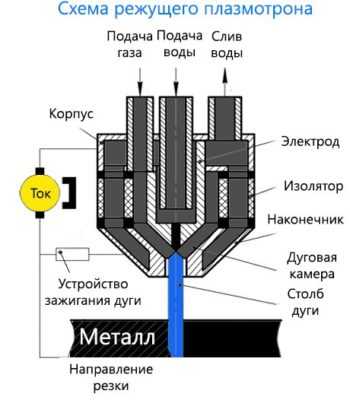
Схема режущего плазмотрона.
Раскаленный воздух представляет из себя плазму, он давит на дугу и сообщает ей режущие свойства. Если учесть высочайшую температуру на уровне 3000°С, происходит то самое механическое воздействие на металл, которое называется резкой.
Данный тип резки используется в работе с высокопроводными металлами. Преимущественно это детали с неправильными контурами, трубы, прутки, металлические полосы и уголки, различные отверстия в заготовках и т.д.
Бесконтактная плазменная резка
Здесь режущим инструментом является струя из плазмы, идущая из сопла с огромной скоростью. Что же касается дуги, то она формируется между наконечником плазмотрона и электродом.
Эта технология применяется в работе с материалами, которые плохо проводят ток. Это неметаллы, к примеру, камень.
Еще один принцип классификации резаков на аппараты ручной или машинной резки.
Ручные воздушно-плазменные резаки
Это самые демократичные модели и по цепне, и по сфере применения. Нельзя сказать, что они стали эдакими домашними котиками для резки новогодней фольги, но в автомастерских, к примеру, они стали широко использоваться для резки деталей самого разного калибра.
Производительность у них не бог весть какая прежде всего потому, что резак находится в руках у оператора, которому приходится держать его на весу и вести по линии разреза. Понятно, что об идеальной точности и ровности разреза говорить не приходится.
Чтобы исправить это, можно использовать специальный упор. Этот упор размещают на сопле, придавливают к поверхности заготовки и таким образом ведут резак по линии разреза.
Стоимость ручного плазменного резака зависит от их функциональных возможностей, включая применяемую силу тока и максимальную толщину металла, которую можно будет с их помощью разрезать.
На рынке появились чрезвычайно интересные универсальные модели, с помощью которых можно как резать, так и варить металлические детали. Стоят они недешево, но вполне приемлемо: около 500 USD. Заметить такие модели можно с помощью маркировки.
Аппараты плазменной резки машинного типа
Данные модели практически всегда снабжены программным обеспечением, благодаря которому участие оператора из процесса исключено. Понятно, что сразу же повышаются производительность и общая эффективность работы аппарата. Ну а главная фишка – идеальная точность резки.
Дополнительный бонус от машинного резака – отсутствие какой-либо необходимости обрабатывать края после резки, они и так идеальные.
Для начала работы вводится схема, по которой будет произведена любая форма или фигура резки.
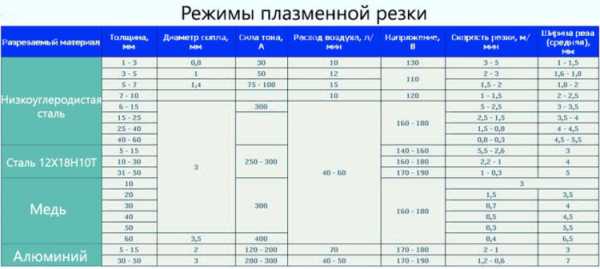
Режимы плазменной резки.
Стоимость машинных устройств на несколько порядков выше, чем у ручных аппаратов плазменной резки. Данные аппараты состоят из мощных трансформаторов и технического стола в виде ровной поверхности с направляющими.
Цена зависит от комплектующих, габаритов и функциональности программного обеспечения. Так или иначе стоимость любой машинной модели будет находиться в диапазоне 3000 – 20000 USD.
Водно-плазменные резаки
Помимо аппаратов воздушно-плазменной резки существуют и модели водно-плазменного типа. В этом случае вода играет роль охладителя, а плазму образует не воздух, а водяной пар.
Устройства воздушно-плазменной резки – отличная опция благодаря низкой цене и компактности, но у них есть существенный недостаток – ограничения в толщине разрезаемого металла, этот лимит составляет всего 80 мм.
А вот мощность водно-плазменных резаков намного выше, и поэтому позволяет работать с массивными деталями. Если говорить о пресловутой стоимости, то да, эти модели дороже.
Принцип работы у них совсем другой. Вместо воздуха под давлением используется водяной пар. При таком раскладе не нужен компрессор для воздуха, не нужны баллоны с газом – водяной пар отлично справляется со всеми задачами самостоятельно.
Дело в том, что по консистенции водяной пар значительно более вязкий, чем воздух. В результате этой «счастливой» вязкости водяного пара нужно намного меньше.
При прохождении через плазмотрон электрической дуги в него подается вода, которая мгновенно начинает испаряться. Пар ионизируется под действием загоревшейся электрической дуги и рабочей жидкости, которая поднимает катод полюса с минусом от катода полюса сопла с плюсом.
Одна из самых известных моделей водно-плазменного типа – аппарат «Горыныч» со стоимость примерно 800 USD.
Физика процесса плазменной резки
Чтобы аппарат плазменной резки работал, нужны всего лишь воздух и электрическая энергия. На режущую часть аппарата подается ток с высокой частотой. В результате в плазмотроне формируется дуга с очень высокой температурой: около 8000°С.
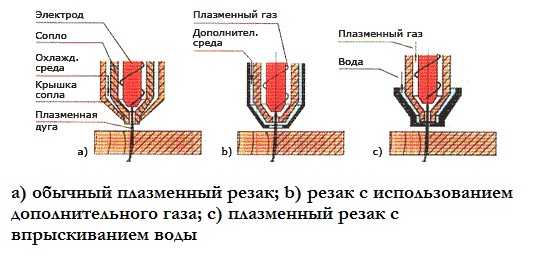
Разновидности плазменных резаков.
Туда же, в плазмотрон, поступает и проходит через раскаленную дугу воздух в сжатом состоянии, который впоследствии ионизируется. В результате этот воздух становится отличным проводником тока, он становится той самой плазмой.
Плазма под большим давлением выходит из сопла и разогревает металлическую деталь до начала плавления. Расплавленный металл частицами выдувается воздухом, выходящим из сопла под большим давлением. Это и есть та самая резка металла.
Скорость потока плазмы зависит от расхода воздуха: если его увеличить, скорость потока плазмы повысится. При силе переменного тока в 250 А скорость плазменного потока составляет примерно 800 м/сек.
Как устроен аппарат плазменной резки?
Главные элементы аппаратов плазменной резки металла – плазмотрон, источник электропитания и так называемый кабель-шланговый пакет для соединения с компрессором. В качестве источника питания могут быть использованы инвертор или трансформатор.
Плазмотрон
Это главная часть аппарата плазменной резки. В свою очередь, он состоит из сопла, электрода и изолятора. По своей форме это корпус с камерой цилиндрической формы и малым выходным каналом, в котором формируется дуга. Электрод находится с тыла камеры, его функция – возбуждение дуги.
Электроды
Это специальные расходники, сделанные именно для резки металла. Чаще их производят из циркония, тория или гафния. Самые распространенные – из гафния.
С бериллием и торием нужно быть поосторожнее – эти элементы обладают радиоактивным компонентом.
Все эти элементы отличаются тем, что на их поверхности формируются оксиды с тугоплавкими свойствами. Эти оксиды как раз и защищают электрод от разрушения.
Розжиг или возбуждение дуги напрямую между электродом и металлической заготовкой произвести сразу трудно. Поэтому первым делом разжигается промежуточная дуга между электродом и плазмотроном. Затем воздух под давлением проходит чрез дугу, ионизируясь и нагреваясь.
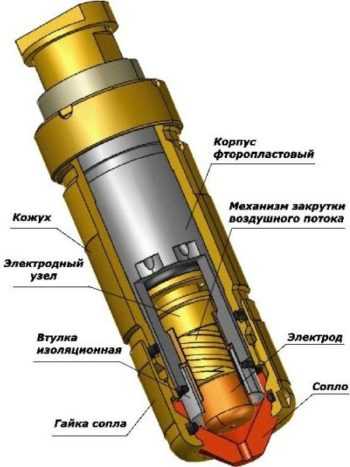
Схема устройства плазменного резака.
В итоге объем этого воздуха повышается в объеме во много раз, он превращается в поток плазмы. Плазма вырывается из суженого конца сопла с огромной скоростью и высочайшей температурой вплоть до 30000°С.
Такому потоку все по силам, в дополнение ко всему он обладает очень высокой теплопроводностью – практически такой же, как у металла заготовки, которую нужно резать.
Настоящая дуга – та самая, которая нужна, формируется при выходе плазмы из сопла плазмотрона. Теперь именно эта рабочая дуга является главным режущим фактором.
Сопло плазмотрона
Различается по диаметру, от которого будут зависеть функциональные возможности всего аппарата. Прежде всего эта зависимость касается объема ионизированного воздуха, выходящего из сопла: именно им обусловлены главные характеристики резака – скорости работы и охлаждения, ширина шага реза.
Чаще встречаются сопла с малым диаметром, не превышающим 3-х мм. Зато длина сопла больше – около 10-ти мм.
Защитные газы
Прежде всего эти газы образуют плазму, их даже называют плазмообразующими. Такие газы используются только в мощных промышленных аппаратах для резки толстых металлов. Чаще это гелий, аргон, азот и их различные смеси. Кстати, кислород сам по себе также является защитным и плазмообразующим газом. Он используется в резаках небольшой мощности для резки металлов не толще 50-ти мм.
В плазмотроне расходными материалами являются сопло и электроды. Их нужно менять в положенных сроки.
Преимущества метода плазменной резки
Плюсы этих устройств нужно хорошо знать, равно как и минусы, без которых не обходится ни одно техническое приспособление.
Прежде всего помним, что скромные бытовые задачи по резке металла вполне можно реализовать с помощью обычной болгарки и не заморачиваться с дорогим и непростым плазменным оборудованием.
Плазменный резак обладает следующими положительными свойствам:
- Высокая скорость рабочего процесса. Если сравнить ее с газовой горелкой, то скорость резки выше в шесть раз. Быстрее в природе только лазерная резка.
- Большая толщина металла, который он способен резать в отличие от болгарки.
- Плазменному резаку под силу любой тип металла. Для этого важно знать и верно выставлять необходимые режимы согласно спецификациям.
- Непродолжительные и несложные подготовительные работы. Не нужна зачистка поверхностей.
- Уникальная точность и ровность среза. Нет никаких наплывов, не нужны специальные упоры.
- Отсутствие каких-либо дефектов и деформаций металла благодаря невысокой температуре общего нагрева.
- Способность аппарата производить срезы любой формы, включая фигурные.
- Высокая безопасность процесса: нет баллонов с газом.
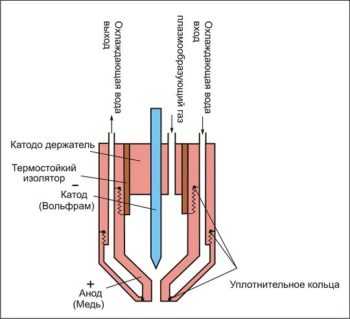
Чертеж устройства плазменного резака.
Недостатки плазменного резака:
- Высокая стоимость аппарата.
- Нет возможности резки одновременно несколькими резаками.
- Строгие требования к положению инструмента: плазма должна быть строго перпендикулярной поверхности заготовки. Сегодня выпускаются продвинутые аппараты, способные работать под углом от 20-ти до 50-ти градусов, но они еще дороже.
- Ограничение толщины разрезаемого металла – примерно до 10-ти с. В сравнении кислородная горелка режет металл толщиной в полметра.
При всех, казалось бы, значительных минусах плазморезы очень популярны. В небольших мастерских работают ручными моделями, которых предлагается на рынке огромное множество. Сегодня плазменная резка перестала быть недоступным элитарным методом работы.
Плазменный резак своими руками
Сразу заметим, что плазменной резки не обязательно быть профессиональным сварщиком, опыт в сварке здесь не нужен. Если вы задумали сделать такой аппарат своими руками, примите к сведению, что у вас появится возможность идеально резать кроме металла другие материалы: пластик, дерево, керамику и пр.
Плазменный резак – дорогое удовольствие даже в виде самых простых ручных моделей, поэтому сделать самодельный аппарат имеет смысл: овчинка выделки стоит.
Единственное, что нужно купить – это источник питания и сопло. Если вы все сделаете правильно, ваш аппарат не будет уступать заводским экземплярам по своим рабочим качествам.
Для образования плазмы нужен воздух, а для системы охлаждения нужна вода или тосол, которые заливаются в специальную емкость.
Стержень нужно брать вольфрамовый., с его помощью будет формироваться электрическая дуга. Все комплектующие всегда имеются в хозяйственных магазинах. Собрав все необходимое оборудование для плазменной резки металла, аппарат производится по схемам, которые представлены в сети в большом количестве.
Какой резак выбрать
Начнем с факта, известного любому сварщику, который распространяется и на плазменную резку: чем выше сила тока, тем выше скорость рабочего процесса. Есть и другие параметры, которые следует учитывать при выборе инструмента для своей работы.
Толщина и тип металла – один из главных критериев. В сети можно найти множество табличного материала с техническими характеристиками плазменных резаков в зависимости от них. К примеру, чтобы с успехом резать медный лист толщиной в 2 мм, вам понадобится устройство с допустимой силой тока в 12 А.
Важным правилом является обязательный «запас» силы тока: покупать резак помощнее, чем указывается в таблицах. Дело в том, что табличные параметры – это максимальные цифры, с этими значениями аппарат может работать лишь непродолжительное время.
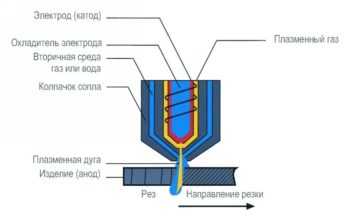
Схема работы плазменного резака.
Грамотнее всего выбор по трем критериям: скорости рабочего процесса, времени резки и мощности.
- Нужная рабочая мощность определяется с учетом толщины планируемого металла и его вида. К примеру, мощность в 90А позволит резать металл толщиной до 30-ти мм.
- Если металл толще, нужно выбирать резак с мощностью в диапазоне 80 – 180А.
- Диаметр сопла и выбор типа потока всегда зависит от типа разрезаемого металла.
- Важными параметрами выбора станка плазменного резака являются также номинальное первичное напряжение и сила тока.
- Нужно решить, какой тип аппарата вам нужен – универсальный или специального назначения.
- Проверка адекватности аппарата к электрической сети обязательна: можно ли его подключать к общей сети или нужна профессиональная с другим напряжением. Аппараты попроще работают только при 220 или 380В, фазы питания могут быть одно- и трехфазными.
- Скорость резки металла измеряется в см/мин.
- Еще один важный и показательный критерий – способность резака работать непрерывно в течение долгого времени, иными словами – продолжительность работы без перерыва. Если она указана как 50%, это значит, что аппарат после 5-ти минут непрерывной резки должен быть выключенным также 5 минут.
Полезные советы по покупке и уходу
Особенности выбора и ухода за резаком:
- Если есть выбор, всегда останавливайтесь на тех моделях, у которых есть евроразъем.
В этих моделях не будет никаких проблем с подключением или удлинением кабель-шлангового пакета и других элементов между собой. - На расходных материалах не экономим.
Только качественные будут работать на идеальный рез и долговечность резака. Быстрее всего изнашиваются сопло и катод, следовательно, за стоянием этих элементов нужно следить с особой тщательностью. - Резак – это резак, поэтому правила безопасности в данном случае имеют железобетонный характер.
Нужно иметь защитный щиток, специальные очки. Имейте в виду, что плазменная резка – это брызги расплавленного металла. Поэтому вам не помешают и перчатки, и даже защитная обувь. - Работа на максимальной мощности предопределяет последующую остановку в работе.
Одна из важнейших технических характеристик станков плазменной резки металла – продолжительность их работы без перерыва. - Если в вашем доме старая проводка, обязательно проверьте, как «подружится» ваш новый резак с вашей старой сетью.
Скорее всего, дружбы не выйдет, это нужно принять во внимание.
tutsvarka.ru
Воздушно-плазменная резка своими руками | Строительный портал
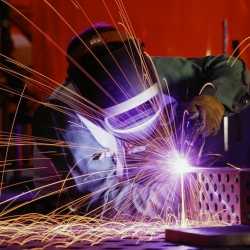
Все чаще в небольших частных мастерских и на маленьких предприятиях используют аппараты плазменной резки металла вместо болгарок и других аппаратов. Воздушно-плазменная резка позволяет выполнять качественные прямые и фигурные резы, выравнивать кромки листового металла, делать проемы и отверстия, в том числе и фигурные, в металлических заготовках и другие более сложные работы. Качество получившегося реза просто великолепно, он получается ровным, чистым, практически без окалины и заусениц, а также аккуратным. С помощью технологии воздушно-плазменной резки можно обрабатывать практически все металлы, а также нетокопроводящие материалы, такие как бетон, керамическая плитка, пластик и дерево. Все работы выполняются быстро, заготовка нагревается локально, только в области реза, поэтому металл заготовки не меняет своей геометрии вследствие перегрева. С аппаратом плазменной резки или как его еще называют – плазморезом сможет справиться даже новичок без опыта сварки. Но чтобы результат не разочаровал, все же не помешает изучить устройство плазмореза, понять его принцип действия, а также изучить технологию, как работать аппаратом воздушно-плазменной резки.
- Устройство аппарата воздушно-плазменной резки
- Принцип работы аппарата воздушно-плазменной резки
- Как выбрать аппарат воздушно-плазменной резки
- Воздушно-плазменная резка своими руками – технология работы
Устройство аппарата воздушно-плазменной резки
Знание устройства плазмореза позволит не только более осознанно производить работы, но и создать самодельный аналог, для чего необходимы не только более глубокие знания, но и желательно инженерский опыт.
Аппарат воздушно-плазменной резки состоит из нескольких элементов, среди которых:
- Источник питания;
- Плазмотрон;
- Кабель-шланговый пакет;
- Воздушный компрессор.
Источник питания для плазмореза служит для того, чтобы преобразовывать напряжение и подавать на резак/плазмотрон определенную силу тока, благодаря чему загорается электрическая дуга. В качестве источника питания могут выступать трансформатор или инвертор.
Плазмотрон – основной элемент аппарата воздушно-плазменной резки, именно в нем происходят процессы, благодаря которым появляется плазма. Плазмотрон состоит из сопла, электрода, корпуса, изолятора между соплом и электродом и каналов для воздуха. Такие элементы как электрод и сопло являются расходными материалами и требуют частой замены.
Электрод в плазмотроне является катодом и служит для возбуждения электрический дуги. Самым распространенным металлом, из которого делают электроды для плазмотронов, является гафний.
Сопло имеет конусообразную форму, обжимает плазму и формирует плазменную струю. Вырываясь из выходного канала сопла, плазменная струя дотрагивается до заготовки и разрезает ее. Размеры сопла влияют на характеристики плазмореза, его возможности и технологию работы с ним. Самый распространенный диаметр сопла – 3 – 5 мм. Чем больше диаметр сопла, тем больший объем воздуха в единицу времени оно можно пропустить через себя. От количества воздуха зависит ширина реза, а также скорость работы плазморезом и скорость охлаждения плазмотрона. Самая распространенная длина сопла 9 – 12 мм. Чем больше длина сопла, тем аккуратнее рез. Но слишком длинное сопло больше подвержено разрушению, поэтому оптимально длину увеличивают на размер, равный 1,3 – 1,5 диаметра сопла. Следует учитывать, что каждому значению силы тока соответствует оптимальный размер сопла, который обеспечивает стабильное горение дуги и максимальные параметры резки. Уменьшать диаметр сопла и делать менее 3 мм нецелесообразно, так как значительно снижается ресурс всего плазмотрона.
Компрессор подает сжатый воздух в плазмотрон для образования плазмы. В аппаратах воздушно-плазменной резки воздух выступает в качестве и плазмообразующего газа, и защитного. Существуют аппараты со встроенным компрессором, как правило, они маломощные, а также аппараты с внешним воздушным компрессором.
Кабель-шланговый пакет состоит из электрокабеля, соединяющего источник питания и плазмотрон, а также шланга для подачи воздуха от компрессора в плазмотрон. Что конкретно происходит внутри плазмотрона, рассмотрим ниже.
Принцип работы аппарата воздушно-плазменной резки
Установка воздушно плазменной резки работает по описанному ниже принципу. После нажатия кнопки розжига, которая находится на ручке плазмотрона, от источника питания на плазмотрон начинает подаваться ток высокой частоты. В результате загорается дежурная электрическая дуга. По причине того, что образование электрической дуги между электродом и заготовкой напрямую затруднительно, то в качестве анода выступает наконечник сопла. Температура дежурной дуги составляет 6000 – 8000 °С, а столб дуги заполняет весь канал сопла.
Спустя пару секунд после розжига дежурной дуги в камеру плазмотрона начинает подаваться сжатый воздух. Он проходит сквозь дежурную электрическую дугу, ионизируется, нагревается и увеличивается в объеме в 50 – 100 раз. Форма сопла плазмотрона заужена книзу, благодаря чему воздух обжимается, из него формируется поток, который вырывается из сопла со скоростью, близкой к звуковой – 2 – 3 м/с. Температура ионизированного разогретого воздуха, вырывающегося из выходного отверстия сопла, может достигать 20000 – 30000 °С. Электропроводность воздуха в этот момент примерно равна электропроводности обрабатываемого металла.
Плазмой как раз и называется разогретый ионизированный воздух, вырывающийся из сопла плазмотрона. Как только плазма достигает поверхности обрабатываемого металла, зажигается рабочая режущая дуга, в этот момент дежурная дуга гаснет. Режущая дуга разогревает заготовку в месте соприкосновения, локально, металл начинает плавиться, появляется рез. Расплавленный металл вытекает на поверхность заготовки и застывает в виде капель и мелких частичек, которые тут же сдуваются потоком плазмы. Данный способ воздушно-плазменной резки называют резкой плазменной дугой (дуга прямого действия), так как обрабатываемый металл входит в электрическую схему и является анодом режущей дуги.
В описанном выше случае для разрезания заготовки используется энергия одного из приэлектродных пятен дуги, а также плазмы столба и вытекающего из него факела. Для резки плазменной дугой используется дуга постоянного тока прямой полярности.
Плазменно-дуговая резка металла используется в таких случаях: если необходимо изготовить детали с фигурными контурами из листового металла, или изготовить детали с прямыми контурами, но так, чтобы не пришлось обрабатывать контуры дополнительно, для резки труб, полос и прутов, для вырезки отверстий и проемов в деталях и другого.
Но также есть еще один способ плазменной резки – резка плазменной струей. В таком случае режущая дуга загорается между электродом (катодом) и наконечником сопла (анодом), а обрабатываемая заготовка не включена в электрическую цепь. Часть плазмы выносится из плазмотрона в виде струи (дуга косвенного действия). Обычно такой способ резки используют для работы с неметаллическими нетокопроводящими материалами – бетоном, керамической плиткой, пластмассой.
Подача воздуха в плазмотрон прямого действия и косвенного действия производится по-разному. Для резки плазменной дугой требуется аксиальная подача воздуха (прямая). А для резки плазменной струей требуется тангенциальная подача воздуха.
Тангенциальная или вихревая (осевая) подача воздуха в плазмотрон необходима для того, чтобы катодное пятно располагалось строго по центру. Если тангенциальная подача воздуха нарушена, неизбежно смещение катодного пятна, а с ним и плазменной дуги. В результате плазменная дуга горит не стабильно, иногда загорается две дуги одновременно, а также весь плазмотрон выходит из строя. Воздушно-плазменная резка самодельная не способна обеспечить тангенциальную подачу воздуха. Так как для устранения турбулентностей внутри плазмотрона используют сопла специальной формы, а также вкладыши.
Сжатый воздух используется для воздушно-плазменной резки таких металлов:
- Меди и сплавов меди – толщиной не более 60 мм;
- Алюминия и сплавов алюминия – толщиной до 70 мм;
- Стали толщиной до 60 мм.
А вот для резки титана воздух использовать категорически нельзя. Более детально тонкости работы аппаратом ручной воздушно-плазменной резки рассмотрим ниже.
Как выбрать аппарат воздушно-плазменной резки
Чтобы сделать правильный выбор плазмореза для частных бытовых нужд или маленькой мастерской, необходимо точно знать для каких целей он будет использоваться. С какими заготовками придется работать, из какого материала, какой толщины, какова интенсивность загрузки аппарата и многое другое.
Для частной мастерской вполне может сгодиться инвертор, так как у таких аппаратов более стабильная дуга и больший на 30 % КПД. Трансформаторы подходят для работы с заготовками большей толщины и не боятся перепадов напряжения, но при этом они больше весят и менее экономичны.
Следующая градация – плазморезы прямого и косвенного действия. Если планируется резать только металлические заготовки, то необходим аппарат прямого действия.
Для частной мастерской или домашних нужд необходимо приобретать ручной плазморез с встроенным или внешним компрессором, рассчитанный на определенную силу тока.
Сила тока плазмореза и толщина металла
Сила тока и максимальная толщина заготовки – основные параметры для выбора аппарата воздушно-плазменной резки. Они взаимосвязаны между собой. Чем большую силу тока может подавать источник питания плазмореза, тем более толстую заготовку можно обрабатывать с помощью данного аппарата.
Выбирая аппарат для личных нужд, необходимо точно знать, какой толщины заготовки будут обрабатываться и из какого металла. В характеристиках плазморезов указывается и максимальная сила тока, и максимальная толщина металла. Но обратите внимание на то, что толщина металла указана из расчета на то, что обрабатываться будет черный металл, а не цветной и не нержавейка. А сила тока указана не номинальная, а максимальная, на данных параметрах аппарат может работать совсем непродолжительное время.
Для резки разных металлов требуется различная сила тока. Точные параметры можно увидеть в таблице ниже.
Таблица 1. Сила тока, необходимая для резки различных металлов.
Например, если планируется резать стальную заготовку толщиной 2,5 мм, то необходима сила тока 10 А. А если заготовка выполнена из цветного металла, например, меди толщиной 2,5 мм, то сила тока должна быть 15 А. Чтобы рез получился высокого качества, необходимо учитывать некий запас мощности, поэтому лучше приобрести плазморез, рассчитанный на силу тока в 20 А.
На аппарат воздушно-плазменной резки цена напрямую зависит от его мощности – выдаваемой силы тока. Чем больше сила тока, тем дороже аппарат.
Режим работы – продолжительность включения (ПВ)
Режим работы аппарата определяется интенсивностью его загрузки. На всех аппаратах указан такой параметр, как продолжительность включения или ПВ. Что она означает? Например, если указана ПВ=35%, то это означает, что плазморезом можно работать 3,5 минуты, а затем ему необходимо дать остыть в течение 6,5 минут. Цикл продолжительности включения рассчитан на 10 минут. Есть аппараты с ПВ 40%, 45%, 50%, 60%, 80%, 100%. Для бытовых нужд, где аппарат не будет использоваться постоянно, достаточно аппаратов с ПВ от 35% до 50%. Для машинной резки с ЧПУ используются плазморезы с ПВ=100%, так как они обеспечивают непрерывную работу в течение всей смены.
Обратите внимание, что в процессе работы с ручной воздушно-плазменной резкой существует необходимость переместить плазмотрон или перейти на другой конец заготовки. Все эти интервалы учитываются в счет времени охлаждения. Также продолжительность включения зависит от загрузки аппарата. Например, с начала смены даже плазморез с ПВ=35% может без перерыва работать 15 – 20 минут, но чем чаще им будут пользоваться, тем короче будет время беспрерывной работы.
Воздушно-плазменная резка своими руками – технология работы
Плазморез выбрали, с принципом работы и устройством ознакомились, пора приступать к работе. Чтобы не наделать ошибок, для начала не помешает ознакомиться с технологией работы с аппаратом воздушно-плазменной резки. Как соблюсти все меры безопасности, как подготовить аппарат к работе и правильно подобрать силу тока, а затем, как разжечь дугу и соблюдать необходимую дистанцию между соплом и поверхностью заготовки.
Позаботьтесь о безопасности
Воздушно-плазменная резка сопряжена с рядом опасностей: электрический ток, высокая температура плазмы, раскаленный металл и ультрафиолетовое излучение.
Меры безопасности при работе с плазморезом:
- Работать необходимо в специальной экипировке: темные очки или щиток сварщика (4 – 5 класс затемнения стекла), плотные перчатки на руках, штаны из плотной ткани на ногах и закрытая обувь. При работе с резаком могут образовываться газы, которые представляют угрозу для нормальной работы легких, поэтому на лицо необходимо надевать маску или респиратор.
- Плазморез подключается в сеть через УЗО.
- Розетки, рабочая подставка или стол, окружающие предметы должны быть хорошо заземлены.
- Силовые кабели должны быть в идеальном состоянии, не допускается повреждение обмотки.
То, что сеть должна быть рассчитана на то напряжение, которое указано на аппарате (220 В или 380 В), это само собой разумеющееся. В остальном же соблюдение техники безопасности поможет избежать травм и профзаболеваний.
Подготовка аппарата воздушно-плазменной резки к работе
Как подключить все элементы аппарата воздушно-плазменной резки, подробно описано в инструкции к аппарату, поэтому сразу перейдем к дальнейшим нюансам:
- Аппарат необходимо установить так, чтобы к нему был доступ воздуха. Охлаждение корпуса плазмореза позволит дольше работать без перерыва и реже отключать аппарат для охлаждения. Место расположения должно быть таким, чтобы на аппарат не попадали капли расплавленного металла.
- Воздушный компрессор подключается к плазморезу через влаго- и маслоотделитель. Это очень важно, так как попавшие в камеру плазмотрона вода или капли масла могут привести к выходу из строя всего плазмотрона или даже его взрыву. Давление подаваемого в плазмотрон воздуха должно соответствовать параметрам аппарата. Если давление будет недостаточным, то плазменная дуга будет нестабильной, часто будет гаснуть. Если давление будет избыточным, то могут придти в негодность некоторые элементы плазмотрона.
- Если на заготовке, которую собираетесь обрабатывать, есть ржавчина, окалина или масляные пятна, их лучше отчистить и удалить. Хоть воздушно-плазменная резка и позволяет резать ржавые детали, все же лучше перестраховаться, так как при нагреве ржавчины выделяются ядовитые пары. Если планируется резать емкости, в которых хранились горючие материалы, то их необходимо тщательно отчистить.
Чтобы рез получился ровным, параллельным, без окалины и наплывов, необходимо правильно подобрать силу тока и скорость резки. В представленных ниже таблицах указаны оптимальные параметры резки различных металлов различной толщины.
Таблица 2. Сила и скорость резки с помощью аппарата воздушно-плазменной резки заготовок из различных металлов.
Первое время подбирать скорость ведения резака будет сложно, необходим опыт. Поэтому поначалу можно ориентироваться на такое правило: вести плазмотрон необходимо так, чтобы с обратной стороны заготовки были видны искры. Если искр не видно, значит, заготовка не разрезана насквозь. Обратите также внимание, что слишком медленное ведение резака негативно сказывается на качестве реза, на нем появляются окалина и наплывы, а также может нестабильно гореть дуга и даже гаснуть.
Теперь можно приступать к самому процессу резки.
Розжиг плазменной дуги
Перед тем как зажечь электрическую дугу, плазмотрон следует продуть воздухом, чтобы удалить случайный конденсат и инородные частицы. Для этого необходимо нажать, а затем отпустить кнопку поджига дуги. Так аппарат переходит в режим продувки. Спустя примерно 30 секунд можно нажимать кнопку поджига и удерживать ее. Как уже описывалось в принципе работы плазмореза, между электродом и наконечником сопла загорится дежурная (вспомогательная, пилотная) дуга. Как правило, она горит не долее 2 секунд. Поэтому за это время необходимо зажечь рабочую (режущую) дугу. Способ зависит от вида плазмотрона.
Если плазмотрон прямого действия, то необходимо сделать короткое замыкание: после образования дежурной дуги необходимо нажать кнопку розжига – прекращается подача воздуха и контакт замыкается. Затем воздушный клапан открывается автоматически, поток воздуха вырывается из клапана, ионизируется, увеличивается в размерах и выводит искру из сопла плазмотрона. В результате загорается рабочая дуга между электродом и металлом заготовки.
Важно! Контактный поджиг дуги не означает, что плазмотрон необходимо прикладывать или прислонять к заготовке.
Как только загорится режущая дуга, дежурная дуга гаснет. Если не получилось зажечь рабочую дугу с первого раза, необходимо отпустить кнопку розжига и нажать ее снова – начнется новый цикл. Причин, по которым может не зажигаться рабочая дуга, несколько: недостаточное давление воздуха, неправильная сборка плазмотрона или другие неполадки.
В процессе работы также бывают случаи, когда режущая дуга гаснет. Причина, скорее всего, в изношенности электрода или несоблюдении расстояния между плазмотроном и поверхностью заготовки.
Расстояние между горелкой плазмотрона и металлом
Ручная воздушно-плазменная резка сопряжена с той трудностью, что необходимо соблюдать расстояние между горелкой/соплом и поверхностью металла. При работе рукой это довольно сложно, так как даже дыхание сбивает руку, и рез получается неровным. Оптимальное расстояние между соплом и заготовкой 1,6 – 3 мм, для его соблюдения используются специальные дистанционные упоры, ведь сам плазмотрон нельзя прижимать к поверхности заготовки. Упоры надеваются сверху на сопло, затем плазмотрон опирается упором на заготовку и выполняется рез.
Обратите внимание, что держать плазмотрон необходимо строго перпендикулярно заготовке. Допустимый угол отклонения 10 – 50 °. Если заготовка слишком тонкая, то резак можно держать под небольшим углом, это позволит избежать сильных деформаций тонкого металла. Расплавленный металл при этом не должен попадать на сопло.
Работы с воздушно-плазменной резкой своими руками вполне можно осилить самостоятельно, только важно помнить о технике безопасности, а также о том, что сопло и электрод – расходные материалы, которые требуют своевременной замены.
strport.ru
принцип работы плазмореза и применение технологии резания на производстве
Резка металлов необходима во множестве технологических процессов. Почти всегда механическая обработка начинается с раскраивания и резки материала. Одним из наиболее удобных и экономичных способов является плазменная резка металла. Она позволяет получать заготовки любой формы, которые почти не требуют последующей обработки.
Содержание материала
Принцип работы
Для плазменной резки металла применяется воздействие струёй плазмы на заготовку. Плазма — это поток ионизированного газа, разогретого до температуры в тысячи градусов, который обладает электропроводностью и движется с большой скоростью. Формирование плазменной дуги из электрической производится аппаратом плазморез. Принцип работы плазмореза и этапы технологического процесса резки:
- Формируется дежурная электрическая дуга, которая зажигается между электродом плазмореза и его соплом или обрабатываемым металлом.
- После формирования дежурной дуги в камеру подаётся сжатый газ. Он расширяется в объёме и разогревается до температуры 20000 °C.
- Электрическая дуга ионизирует газ, он становится проводником электричества и превращается в струю плазмы. Эта струя разогревает металл в зоне обработки, расплавляет его и производит резку.
Для металлов и неметаллических материалов применяются разные принципы газоплазменной резки. Имеются два способа обработки материалов:
Также рекомендуем прочитать:
- Дуга горит между плазмотроном и изделием. Так работает резак прямого действия. Изделие при этом должно быть токопроводящим. Если требуется разрезать неметаллические изделия, применяется косвенный метод.
- Дуга зажигается в самом плазмотроне между электродом и соплом. Электрод является катодом, а на сопло подаётся положительный потенциал.
Во втором случае обработке могут подвергаться любые материалы: пластмассы, камень, бетон. Потенциал к детали не подводится и электропроводность не требуется.
Оборудование для резки плазмой
Для резки металла плазмой выпускаются аппараты промышленного и бытового назначения. Все агрегаты для резки плазмой имеют в своём составе:
- источник питания;
- плазмотрон;
- компрессор для нагнетания сжатого газа;
- кабели и шланги, служащие для соединения элементов оборудования.
Источник питания может представлять собой инвертор или трансформатор. Инверторные агрегаты лёгкие, экономичные, обладают высоким коэффициентом полезного действия. Их часто применяют в небольших производствах. Имеют ограничение по силе тока — 70 А, способны резать материал только небольшой толщины до 30 мм.
Трансформаторные устройства более мощные, имеют больший вес и размеры. Они более устойчивы к перепадам напряжений, способны к долгой непрерывной работе и часто используются в станках с ЧПУ. Оборудование с системой водяного охлаждения способно резать металл толщиной до 100 мм. Источники питания для резки с применением кислорода имеют силу тока в диапазоне 100—400 А. При использовании азота, как плазмообразующего газа, этот диапазон увеличивается до 600 А.
Плазмотрон — это основной узел всех установок. В его состав входит:
- внутренний электрод;
- рабочее сопло;
- изолирующий корпус с охлаждением;
- устройство подачи плазмообразующего вещества.
В зависимости от условий обработки применяют разные газы для плазменной резки. Для сталей и сплавов применяют кислород и воздух. Воздушно-плазменная резка используется для обработки низколегированных сталей. При обработке цветных металлов плазмообразующими газами могут быть аргон, азот, водород. Это обусловлено тем, что в среде кислорода цветные металлы начинают окисляться. Смесь аргона с водородом чаще используется для резки нержавеющей стали и алюминия.
Температура потока газа находится в пределах 5000—30000 °C. При нижних значениях температур обрабатываются цветные металлы, при верхних — тугоплавкие стали.
Скорость потока находится в пределах 500—1500 м/с. Настройка производится в зависимости от толщины, характеристик обрабатываемого материала и длительности работы.
Обработка в ручном режиме
Перед началом работы инвертор или трансформатор подключают к сети переменного тока. Обрабатываемую деталь подсоединяют к источнику питания. Следующий этап — сближение сопла и заготовки. Между ними должно оставаться 40 мм. После этого можно зажигать дежурную дугу. Когда дуга загорается, в сопло подаётся воздушный поток, который ионизируется и формирует струю плазмы.
При работах с плазморезом необходимо соблюдать правила техники безопасности. Нужно использовать специальный костюм и защитный лицевой щиток. Температуры при плазморезке достигают тысяч градусов, и для человека это может быть опасно. Поэтому надо стремиться автоматизировать процесс.
Достоинства и недостатки плазменной обработки
Работа агрегатов плазморезки часто внедряется в различные технологические процессы, связанные с раскроем и резкой металлических и неметаллических материалов. Это обусловлено наличием следующих преимуществ технологии раскроя с помощью плазменной дуги:
Универсальность. Возможность раскраивать любые материалы, в том числе камень, титан и сплавы из него. Без предварительного подогрева можно резать листы до 80 мм толщиной.
- Точность. Плазменный инструмент выполняет точный и ровный рез без термического деформирования краёв.
- Компактность. Многие агрегаты, особенно с использованием источника питания инверторного типа, имеют небольшие габариты и могут работать как в закрытых помещениях, так и на открытых площадках.
- Простота в эксплуатации. Плазморез удобен в работе и не требует высокой квалификации при использовании. Часто применяется в северных регионах в условиях повышенной влажности и низких температур.
Но у метода плазменного раскроя есть и недостатки. К ним относятся:
Усложнённость конструкции и высокая цена агрегатов.
- Повышенный уровень шума при использовании плазмореза.
- Выделение вредных веществ при использовании азота как плазмообразующего газа.
- Сложность рабочего оборудования не позволяет одновременное подключение двух резаков к одному аппарату.
Несмотря на эти недостатки, плазмотроны находят себе всё большее применение и на крупных предприятиях, и в маленьких домашних мастерских. Использование плазменной резки ускоряет обработку легированных сталей, а точность линии реза и способность вырезать криволинейные фигуры делают плазморезы незаменимыми во многих производственных процессах.
pochini.guru
Плазменная резка для начинающих.
Плазменная резка металлов для начинающих.
Уважаемые покупатели, в этой статье мы хотим вам рассказать что такое плазменная резка металлов, показать ее основные преимущества, рассказать об устройстве плазменных аппаратов и как их использовать, а теперь обо всем этом по порядку.
Иногда наши покупатели приобретая аппарат плазменной резки с удивлением узнают, что для его работы необходим компрессор. Компрессор необходим для того, чтобы выдувать металл который вы режете. Без компрессора резать плазмой невозможно. Компрессор подключается к аппарату, а к аппарату подключается плазматрон (плазменная горелка), так вот, когда возникает дежурная дуга между катодом и соплом, воздух эту дугу выдувает наружу, где дуга переходит в основную дугу при соприкосновении с металлом; далее происходит процесс плавления металла и выдувания его жидкой части из зоны расплава. При выборе компрессора стоит обратить особое внимание на его качество и на его параметры. Корректная работа аппарата плазменной резки возможно только в сочетании с хорошим компрессором. Мы рекомендуем использовать компрессоры способные выдавать 5-6 атмосфер.
Еще одна немаловажная деталь, на которую мы хотим обратить ваше внимание. В компрессоре должен стоять фильтр воздуха, он может быть встроен в компрессор изначально, а может подключаться отдельно. Воздух, который будет проходить через аппарат плазменной резки и выходить из плазматрона, должен быть чистым, в него не должны попадать никакие посторонние предметы и вещества. Недопустимо попадание паров и частиц масла, мельчайшей частицы металлической стружки, пыль и грязь. Особенно это важно, если вы планируете использовать плазму на пыльных производствах, в гаражах, цехах с бетонными полами и т.д. Чем чище воздух – тем лучше рез!
Если вы будете соблюдать эти условия, аппарат будет работать корректно и без сбоев.
Плазма или газорезка?
Мы не будем говорить о том, что газорезка хуже чем плазменная резка. У газорезки есть ряд преимуществ перед плазмой, например при резе металлолома в больших количествах вам не справиться с этой задачей если использовать плазменную резку. Плазменная резка экономически целесообразна при толщине металла до 50 мм, при большей толщине преимущество переходит к кислородной резке. Но качество и скорость раскроя всегда на стороне плазменной резки.
Для газорезки нужен газ, для плазмы нужно электричество. Выделим два основных преимущества плазмы: первое – вам не нужен газ (ацетилен) вы не связываетесь с взрывоопасными газами, второе – вы можете резать различные типы металлов (сталь, нержавейка, медь, алюминий и пр.)
Таким образом кому-то необходима газорезка, кому-то подойдет плазма, выбор за вами.
Как правильно выбрать аппарат плазменной резки?
Здесь все очень просто. Чем мощнее плазменный аппарат, тем толще металл он может резать. Если вы планируете резать разные толщины, вам лучше выбрать мощные аппарат, если вы будете резать тонкие металлы, вам нет необходимости покупать мощные аппарат, достаточно приобрести сорока амперный аппарат. Обратите внимание на такое понятие, как качество реза. Рез может быть «грязный» и «чистый». Грязный рез – это когда вам нужно просто отрезать кусок металла и для вас не имеет значение какой срез будет, аккуратный или нет. Чистый рез – это максимально ровно отрезанный металл. Как правило, производители указывают в параметрах грязный рез. Чтобы понять чистый рез, вам нужно отнять порядка 25% от указанной толщины. Так например если производитель указал 12 мм – значит чистый рез составит 8-9 мм. Не думайте, что производители вас обманывают, это всемирная практика указать в параметрах грязный рез, а не чистый. Этот параметр показывает максимальную возможность аппарата, а вы уже сами выбираете как вам резать металл, по “грязному” или по “чистому”.
Кроме того, перед покупкой желательно понять как часто вы будете включать аппарат плазменной резки. Обратите внимание на ПВ приобретаемого аппарата. Если ПВ аппарата 60% – значит в 10 минутном цикле вы можете резать 6 минут, а 4 минуты аппарат будет отдыхать, если ПВ 100% – значит можно не отрываться от работы, аппарат будет работать постоянно.
Расходные части.
Покупая аппарат плазменной резки, мы рекомендуем вам узнать у поставщика как обстоят дела с расходкой для плазменной горелки. Практически все производители вместе с аппаратом кладут расходные части, вы можете приступать к резке незамедлительно, но расходка горит, независимо от производителя. И когда встает вопрос о замене, выясняется, что там где аппарат покупался – “расходки” нет. Мы часто сталкиваемся с такими случаями, когда помогаем людям подобрать расходку, и стоит признать, что не всегда это получается. Расходка не всегда стыкуется. Так, например, расходка для аппаратов китайского происхождения не подходит к европейским товарам или американским. Кроме того, нет возможности поменять плазматрон (плазменную горелку) – разные разъемы. В нашем интернет-магазине продаются аппараты плазменной резки произведенные в Китае, все расходные части для горелок CUT всегда в наличии и как показывает практика, китайская расходка подходит практически на все аппараты сделанные в Китае.
Скорость с которой резать металл.
Этот вопрос нам часто задают покупатели. Определенного ответа на него нет, вы поймете, как быстро вам надо будет вести плазматрон по металлу только в процессе обучения, приноровиться очень просто. Все зависит от толщины металла и амперажности, которую вы выставите. Когда вы приступите к резу, вы сразу увидите – если вы ведете плазматрон очень быстро (в таком случае металл не будет прорезаться полностью) если очень медленно (в этом случае вы просто будете расходовать воздух и электроэнергию). Перед тем как резать нужные вам заготовки или отрезки, мы рекомендуем потренироваться на ненужных обрезках, чтобы выбрать оптимальный режим и скорость реза.
Еще один совет, когда вы включите аппарат – поставьте ток на максимум, а во время реза уменьшайте его, пока не поймете, что этого тока достаточно для реза вашей толщины металла. Начинайте с больших токов, затем идите на понижение.
И ещё, не старайтесь ставить максимальный ток, чтобы отрезать побыстрее, так как чем больше ток, тем быстрее выходит из строя расходка; не делайте слишком частые поджиги, поскольку именно в момент поджига происходит интенсивное «выветривание» тугоплавкой вставки на катоде и преждевременный выход его из строя, т.е. нажали на кнопку и режьте непрерывно. Если по условиям работы вам необходимо делать короткие резы, например резать сетку – приготовьтесь к частой замене расходки.
Как все работает.
Установки плазменной резки имеют напряжение холостого хода 250-300 В.
При нажатии на кнопку подаётся сжатый воздух и одновременно между катодом и соплом во внутренней камере плазмотрона прикладывается это напряжение холостого хода, но чтобы пробить этот промежуток и зажечь плазму, необходима поджигающая искра – эту функцию поджига выполняет осциллятор (напряжение поджига порядка 5-10 кВ). Как только дуга зажглась (и дуга в этот момент называется дежурной) воздух выдувает плазму наружу. Ток дежурной дуги как правило в мощных аппаратах ограничен внутри мощным сопротивлением для экономии расходки, для реза не предназначен; дежурная дуга горит 2-3 сек. Если в течение этого времени дуга не коснулась металла или металл по каким-то причинам не соединён с «+» установки (например, обрыв обратного кабеля), то дуга гаснет. Если же всё прошло нормально, то дежурная дуга переходит в основную дугу, блок осциллятора отключается. Далее происходит плавление металла дугой и одновременное выдувание расплавленного материала из расплава. Горение основной дуги происходит между тугоплавкой вставкой из гафния, впрессованной в торец катода и материалом изделия. Наибольшее разрушение этой вставки происходит именно в момент поджига, поэтому лучше стараться избегать слишком частых включений в целях экономии расходки.
Выбрать аппарат плазменной резки можно здесь.
Для наглядности, мы провели несколько тестов. Аппарат Сварог CUT 100 разрезал металл толщиной 10 мм. с увеличением до 35 мм. Ток резки был выставлен 90 Ампер.
Аппарат Сварог CUT 40 разрезал пластину толщиной 4 мм. Ток резки 20 Ампер.
svarkamall.ru
Плазменная резка металла – аппараты, технология, видео процесса
В последнее время использование плазменного потока для раскроя материалов набирает все большую популярность. Еще более расширяет сферу использования данной технологии появление на рынке ручных аппаратов, с помощью которых выполняется плазменная резка металла.
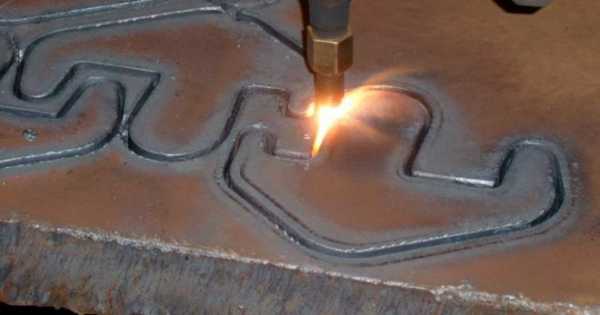
Плазменная резка металла значительной толщины
Суть плазменной резки
Плазменная резка предполагает локальный нагрев металла в зоне разделения и его дальнейшее плавление. Такой значительный нагрев обеспечивается за счет использования струи плазмы, формируют которую при помощи специального оборудования. Технология получения высокотемпературной плазменной струи выглядит следующим образом.
- Изначально формируется электрическая дуга, которая зажигается между электродом аппарата и его соплом либо между электродом и разрезаемым металлом. Температура такой дуги составляет 5000 градусов.
- После этого в сопло оборудования подается газ, который повышает температуру дуги уже до 20000 градусов.
- При взаимодействии с электрической дугой газ ионизируется, что и приводит к его преобразованию в струю плазмы, температура которой составляет уже 30000 градусов.
Полученная плазменная струя характеризуется ярким свечением, высокой электропроводностью и скоростью выхода из сопла оборудования (500–1500 м/с). Такая струя локально разогревает и расплавляет металл в зоне обработки, затем осуществляется его резка, что хорошо видно даже на видео такого процесса.
В специальных установках для получения плазменной струи могут использоваться различные газы. В их число входят:
- обычный воздух;
- технический кислород;
- азот;
- водород;
- аргон;
- пар, полученный при кипении воды.
Технология резки металла с использованием плазмы предполагает охлаждение сопла оборудования и удаление частичек расплавленного материала из зоны обработки. Обеспечивается выполнение этих требований за счет потока газа или жидкости, подаваемых в зону, где осуществляется резка. Характеристики плазменной струи, формируемой на специальном оборудовании, позволяют произвести с ее помощью резку деталей из металла, толщина которых доходит до 200 мм.
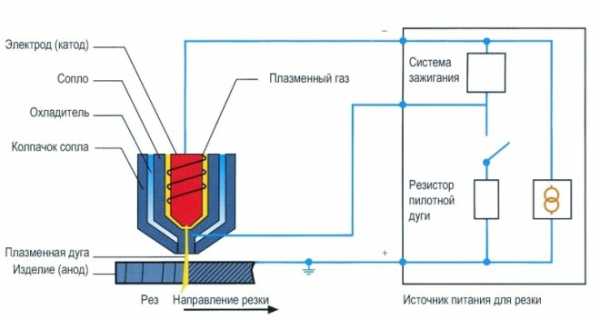
Устройство и принцип действия плазменной резки
Аппараты плазменной резки успешно используются на предприятиях различных отраслей промышленности. С их помощью успешно выполняется резка не только деталей из металла, но и изделий из пластика и натурального камня. Благодаря таким уникальным возможностям и своей универсальности, данное оборудование находит широкое применение на машиностроительных и судостроительных заводах, в рекламных и ремонтных предприятиях, в коммунальной сфере. Огромным преимуществом использования таких установок является еще и то, что они позволяют получать очень ровный, тонкий и точный рез, что является важным требованием во многих ситуациях.
Оборудование для плазменной резки
На современном рынке предлагаются аппараты, с помощью которых выполняется резка металла с использованием плазмы, двух основных типов:
- аппараты косвенного действия — резка выполняется бесконтактным способом;
- аппараты прямого действия — резка контактным способом.
Оборудование первого типа, в котором дуга зажигается между электродом и соплом резака, используется для обработки неметаллических изделий. Такие установки преимущественно применяются на различных предприятиях, вы не встретите их в мастерской домашнего умельца или в гараже ремонтника.
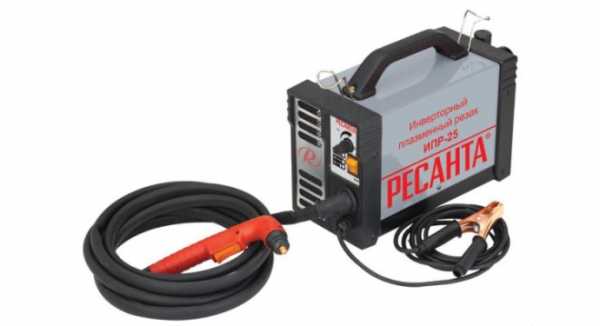
Аппарат для плазменной резки Ресанта ИПР-25
В аппаратах второго типа электрическая дуга зажигается между электродом и непосредственно деталью, которая, естественно, может быть только из металла. Благодаря тому, что рабочий газ в таких устройствах нагревается и ионизируется на всем промежутке (между электродом и деталью), струя плазмы в них отличается более высокой мощностью. Именно такое оборудование может использоваться для выполнения ручной плазменной резки.
Любой аппарат плазменной резки, работающий по контактному принципу, состоит из стандартного набора комплектующих:
- источника питания;
- плазмотрона;
- кабелей и шлангов, с помощью которых выполняется соединение плазмотрона с источником питания и источником подачи рабочего газа;
- газового баллона или компрессора для получения струи воздуха требуемой скорости и давления.
Главным элементом всех подобных устройств является плазмотрон, именно он отличает такое оборудование от обычного сварочного. Плазмотроны или плазменные резаки состоят из следующих элементов:
- рабочего сопла;
- электрода;
- изолирующего элемента, который отличается высокой термостойкостью.
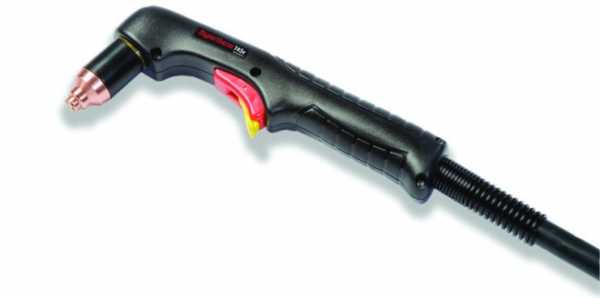
Резак для ручной плазменной резки
Основное назначение плазмотрона состоит в том, чтобы преобразовать энергию электрической дуги в тепловую энергию плазмы. Газ или воздушно-газовая смесь, выходящие из сопла плазмотрона через отверстие небольшого диаметра, проходят через цилиндрическую камеру, в которой зафиксирован электрод. Именно сопло плазменного резака обеспечивает требуемую скорость движения и форму потока рабочего газа, и, соответственно, самой плазмы. Все манипуляции с таким резаком выполняются вручную: оператором оборудования.
Учитывая тот факт, что держать плазменный резак оператору приходится на весу, бывает очень сложно обеспечить высокое качество раскроя металла. Нередко детали, для получения которых была использована ручная плазменная резка, имеют края с неровностями, следами наплыва и рывков. Для того чтобы избежать подобных недостатков, применяют различные приспособления: подставки и упоры, позволяющие обеспечить ровное движение плазмотрона по линии раскроя, а также постоянство зазора между соплом и поверхностью разрезаемой детали.
В качестве рабочего и охлаждающего газа при использовании ручного оборудования может использоваться воздух или азот. Такая воздушно-газовая струя, кроме того, применяется и для выдува расплавленного металла из зоны реза. При использовании воздуха он подается от компрессора, а азот поступает из газового баллона.
Необходимые источники питания
Несмотря на то что все источники питания для плазменных резаков работают от сети переменного тока, часть из них может преобразовывать его в постоянный, а другие — усиливать его. Но более высоким КПД обладают те аппараты, которые работают на постоянном токе. Установки, работающие на переменном токе, применяются для резки металлов с относительно невысокой температурой плавления, к примеру, алюминия и сплавов на его основе.
В тех случаях, когда не требуется слишком высокая мощность плазменной струи, в качестве источников питания могут использоваться обычные инверторы. Именно такие устройства, отличающиеся высоким КПД и обеспечивающие высокую стабильность горения электрической дуги, используются для оснащения небольших производств и домашних мастерских. Конечно, разрезать деталь из металла значительной толщины с помощью плазмотрона, питаемого от инвертора, не получится, но для решения многих задач он подходит оптимально. Большим преимуществом инверторов является и их компактные габариты, благодаря чему их можно легко переносить с собой и использовать для выполнения работ в труднодоступных местах.
Более высокой мощностью обладают источники питания трансформаторного типа, с использованием которых может осуществляться как ручная, так и механизированная резка металла с использованием струи плазмы. Такое оборудование отличается не только высокой мощностью, но и более высокой надежностью. Им не страшны скачки напряжения, от которых другие устройства могут выйти из строя.
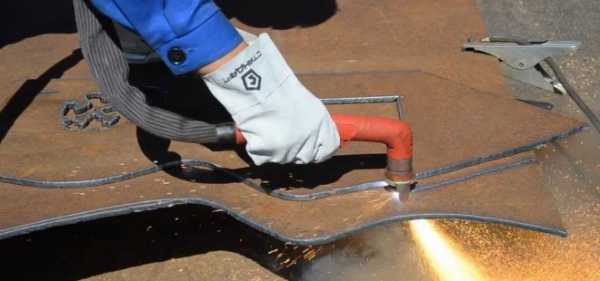
Резка по шаблону
У любого источника питания есть такая важная характеристика, как продолжительность включения (ПВ). У трансформаторных источников питания ПВ составляет 100%, это означает, что их можно использовать целый рабочий день, без перерыва на остывание и отдых. Но, конечно, есть у таких источников питания и недостатки, наиболее значимым из которых является их высокое энергопотребление.
Как выполняется ручная плазменная резка?
Первое, что необходимо сделать для того чтобы начать использование аппарата для плазменной резки металла, — это собрать воедино все его составные элементы. После этого инвертор или трансформатор подсоединяют к заготовке из металла и к сети переменного тока.
Далее технология резки предусматривает приближение сопла устройства к заготовке на расстояние порядка 40 мм и зажигание так называемой дежурной дуги, за счет которой будет осуществляться ионизация рабочего газа. После того как дуга загорелась, в сопло подается воздушно-газовый поток, который и должен сформировать плазменную струю.
Когда из рабочего газа сформируется плазменная струя, обладающая высокой электропроводностью, между электродом и деталью создается уже рабочая дуга, а дежурная автоматически отключается. Задача такой дуги состоит в том, чтобы поддерживать требуемый уровень ионизации плазменной струи. Случается, что рабочая дуга гаснет, в таком случае следует перекрыть подачу газа в сопло и повторить все описанные действия заново. Лучше всего, если нет опыта выполнения такого процесса, посмотреть обучающее видео, где подробно показана ручная резка металла.
Оценка статьи:
Загрузка…Поделиться с друзьями:
met-all.org