Как сделать сырую резину в домашних условиях – инструкция по применению. Изготовление сырой резины своими руками :: SYL.ru
alexxlab | 06.06.2019 | 0 | Вопросы и ответы
Как сделать резину в домашних условиях своими руками
Силиконом называется кремнийорганический материал, довольно мягкий и пластичный, поэтому его применяют для изготовления разного вида форм для статуэток и фигур, и не только. Его подобие можно изготовить и в домашних условиях.
Но прежде чем перечислить способы его изготовления, давайте разберемся, где применяется этот материал.
Где применяют силикон
Этот материал используется практически во всех сферах человеческой жизни — в строительстве, быту, медицине и на производстве. Популярность силикон заслужил благодаря своим уникальным и ценным качествам, которые отсутствуют у аналогов этого вещества.
Силикон способен уменьшать, наращивать процесс адгезии, а также придавать целевому предмету свойства гидрофобности. Этот универсальный материал способен сохранять свои базовые параметры при экстремально высоких, низких температурах и в условиях повышенной влажности. Помимо этого, силиконы обладают диэлектрическими характеристиками, биоинертностью, высокой степенью эластичности, долговечны и экологичны.
В промышленных масштабах силиконовые жидкости и эмульсии на их основе, используют в качестве антиадгезионных смазок для огромных тяжелых пресс-форм, изготовления гидрофобизирующих жидкостей, пластичных смазок, специальных масел, амортизационных, охлаждающих веществ, теплоносителей, герметиков и диэлектрических составов. Особенно популярными являются пеногасители, произведенные на основе силиконовых смесей.
Из этого материала производят силиконалкиды, силиконполиэфиры для различных покрытий, которые должны характеризоваться особой стойкостью и устойчивостью. Отсюда следует, что разного вида прокладки, втулки, кольца, манжеты, заглушки и другие детали можно использовать при температурах от минус 60о С и до плюс 200о С.
Еще одним свойством силикона является устойчивость к таким веществам, как озон, радиация, морская вода, ультрафиолетовое излучение, кипяток, спирт, кислотные растворы, щелочи, минеральные масла, различные топлива и электроразряды.
Как сделать силикон в домашних условиях
Первый способ
Для приготовления силиконового каучука (полидиэтилсилоксана) понадобятся жидкое стекло и этиловый спирт. Берется пластиковая емкость, в которую наливаются компоненты в равных пропорциях и аккуратно перемешиваются любым инструментом. Когда смесь загустеет, нужно доводить до состояния пластилина разминая руками.
Далее, из силиконовой массы можно лепить необходимые формы, которые оставить затвердевать на некоторое время, пока изделие не станет твердым.
Второй способ
Нужны:
- 150 г уайт-спирита;
- 1 капля акриловой краски;
- 3 капли жидкого глицерина;
- 30 г силиконового герметика.
Для изготовления силикона нужно погрузите герметик в емкость, добавить туда краску, глицерин и уайт-спирит. Раствор нужно перемешивать до получения однородной массы. С этим раствором можно работать не более пяти часов, так как после этого времени он затвердевает.
Третий способ
Нужно взять равное количество силиконового герметика и картофельного крахмала. Перемешивать массу около 10 минут, пока силикон не начнет легко отставать от рук, тогда можно приступать к изготовлению необходимой формы.
Четвертый способ
Берется желатин и глицерин в равных пропорциях, тщательно перемешиваются. Затем раствор нужно греть на водяной бане примерно 10 минут, постоянно перемешивая. Важно не допустить закипания желатина, иначе может появиться резкий неприятный запах.
Пятый способ
Он используется для изготовления силикона для форм своими руками. Для этого нужно взять форму немного большего размера, чем копируемый объект. На дно формы наливается немного силикона и оставляется до застывания — это основание предмета.
Толщина основания должна быть один сантиметр и более, чтобы «домашняя резина» надежно обертывала предмет со всех сторон. Если форма выйдет тонкой, тогда быстро порвется при извлечении прототипа или совсем не будет держаться.
Затем прототип окунается в емкость с желатином для избавления от воздушных пузырей, а затем быстро переносится на дно формы, чтобы приклеился. Затем форму нужно полностью заполнить силиконом. Хорошо подойдет самодельная смола из четвертого способа, которая твердеет очень быстро. Сразу после остывания форму необходимо разобрать, сделать надрез и аккуратно извлечь прототип.
На последнем этапе, потребуется замешать и залить в форму эпоксидную смолу. Застывший отливок извлечь будет сложно, поэтому нужно будет полностью разорвать силикон.
Избавляемся от силикона на одежде
Силиконовые герметики широко применяются в ремонте и строительстве. Но небрежное обращение с этой субстанцией может привести к образованию стойких пятен на ткани, и для избавления от них придется использовать специальные очистители или подручные средства.
- Кислотно-силиконовый герметик обладает характерным запахом уксуса, при этом его удаление производится при помощи 70% раствора уксусной кислоты. Удаляя пятно от такого силикона, нужно принять меры предосторожности: надеть очки, крепкие резиновые перчатки и респиратор, так как уксусная кислота отрицательно влияет на глаза, кожу руки и дыхательные пути. Для очищения пятна нужно его обильно, оставить на 30 минут и удалить силикон ветошью.
- Силиконовый нейтральный герметик на основе спирта легко удаляется при помощи спиртосодержащих жидкостей. Можно взять медицинский, технический, денатурированный спирт или водку и нанести на загрязненное место, а затем удалить пятно щеткой.
- Оксимный, аминнный или амидный силиконовый герметик удаляется с помощью уайт-спирита, бензина, ацетона или растворителя. Жидкость наносится на губку, затем на пятно и оставляется на 30 минут до растворения силикона. При необходимости обработку можно повторить. Затем постирать ткань обычным способом со стиральным порошком.
Также существуют специальные составы для очищения поверхности тканей от силикона. Идеально подойдет смывка под торговым названием «Пента-840» или ANTISIL. Необходимо, перед применением любого средства внимательно ознакомьтесь с прилагаемой инструкцией.
Помимо этого, силиконовое пятно можно очистить механическим способом при помощи пластикового скребка. Для этого ткань натягивается на ровную поверхность и пятно аккуратно соскабливается. Остатки можно удалить одним из перечисленных выше способов.
Важно! Работать с силиконовыми герметиками нужно только в хлопчатобумажной плотной одежде, так как удалить его остатки с деликатных вещей без помощи специалистов химчистки не получится!
Удаляем силикон с рабочих поверхностей
Силикон является средством, помогающим склеивать поверхности и герметизировать швы. Это вещество препятствует проникновению воздуха и влаги. Герметики с антибактериальным составом применяются для работы в ванных комнатах, для автомобилей, в строительстве, любителями аквариумов и т. д. Герметик не так легко удалить с поверхности, но возможно.
Герметик производится на основе растворителей, которые придают этому составу резкий запах. Помимо запаха, растворители придают силикону эластичность и помогают более крепкому сцеплению поверхностей.
Поэтому для удаления силикона часто используют химические вещества, которые продаются в магазинах.
Но и при помощи народных методов можно удалить силикон с любой поверхности, для чего используют уайт-спирит, тряпки, лезвия и моющие средства.
Для удаления силикона с рабочей поверхности нужно сначала смочить его уайт-спиритом при помощи тряпки. Примерно через 60 секунд силикон приобретет желеобразную консистенцию и легко поддастся очистке лезвием. Затем это место нужно промыть моющим средством и насухо вытереть ветошью.
Еще силикон можно удалить механическим способом, при помощи ножа и пемзы. Но этот вариант подходит для поверхностей, которые не подвержены царапинам и сколам.
Видео
Из этого видео вы узнаете, как можно самостоятельно сделать силикон.
liveposts.ru
Как сделать резину в домашних условиях — Elfterra.ru
Содержание статьи:
В разделе Техника на вопрос Вопрос про резину. Как расплавить резину в домашних условиях. заданный автором Qqq www лучший ответ это Расплавить можно каучук, а не резину. В резине слишком много наполнителе, типа сажи, и сера для вулканизации.
пахнуть будет плохо, можно отравиться
А кто тебе сказал, что резину можно расплавить?
Резина не пластмасса, и чтоб ее девулканизировать надо сина много движений сделать При паровом методе дозированные порции обестканен-ной резиновой крошки смешивают с мягчителями и загружают в девулка-иизационный котел, где обрабатывают острым пар
никак если нужна форма или изделие используем вулканизатор и “сырую” резину
Одинокая женщина прочла в газете рекламу новой услуги — вызов мужчины на дом. Предлагались мужчины самых различных видов и характеров — от интеллигента до супермена. Поразмыслив она позвонила и заказала супермена. Явился здоровенный мужчина. В
Смесь для получения прочного упругого материала получила название сырая резина. После термической обработки изменяются молекулярные связи каучука, образуя сплав с пластификаторами. Можно своими руками в домашних условиях провести вулканизацию и сделать небольшую деталь из резины или просто заклеить пробоину в велосипедной камере, заделать порезы на скатах. В продаже есть несложное оборудование для частных мастерских, в которых делается сырая резина своими руками.
Сок каучуконосных деревьев широко применялся аборигенами для выделки непромокаемой обуви, покрытия лодок, защиты хижин от дождя и решения других бытовых проблем. Они добывают его из каучуконосных растений аналогично сбору весной березового сока. Полиизопрен — углевод, составляющий большую часть природного латекса, — в тепле соединяется с кислородом и со временем становится хрупким. После нагрева молекулярные связи становятся устойчивыми, и вещество не реагирует даже на кислотные растворы.
Ценность каучука исходя из технических характеристик:
- высокая стойкость к истиранию;
- хорошие теплоизоляционные свойства;
- не растворяется в воде и большинстве агрессивных жидкостей;
- пластичность;
- эластичность.
Добавление пластификаторов и речного песка позволяет создавать материал с запланированными качествами и цветом. Сырая резина превращается в изделие, долго сохраняющее свою форму, через вулканизацию — нагрев под прессом до температуры 150 градусов.
Натуральный и синтетический каучук при нагреве до 50 градусов превращается в мягкую массу, которая хорошо смешивается с другими компонентами:
Состав компонентов меняется и зависит от качеств, которыми должна обладать полученная сырая резина. Сера входит в молекулярные соединения, и от нее зависит твердость резины. Ускорители сокращают время вулканизации. Сажа и масло придают пластичность готовому изделию. Песок и другие органические вещества делают ее тверже, уменьшают стирание, увеличивают усилие разрыва.
По твердости выделяют три основные ее группы:
Природный компонент обладает лучшими эксплуатационными качествами, поэтому шины для автомобилей делают из натурального каучука. На небольших предприятиях изготовление резины предусматривает более дешевый синтетический материал.
Латекс идет на изготовление перчаток, игрушек, различных изоляционных материалов, непромокаемой одежды, подошвы для обуви. Резина средней плотности широко применяется в быту и на производстве. Это всевозможные прокладки в кранах, коврики, муфты в автомобилях и механизмах. Из эбонита вытачивают детали, от которых требуется высокая твердость и устойчивость к истиранию. Это элементы подшипников, колес, втулок.
Выделяют три основных неизменных этапа, если готовится сырая резина. Инструкция и технология простые, требующие несложного оборудования. Последовательно выполняются:
Натуральный каучук, постояв некоторое время и перебродив, превращается в густую вязкую массу. Искусственный сразу производится в таком виде. Перед применением его разминают подобно тесту и подогревают до 50 градусов. В таком состоянии он теряет свою упругость, становится податливым и мягким и способным смешиваться с другими веществами.
Компоненты будущей резины засыпают в шнековую машину для перемешивания. Пропорции и добавки берутся в зависимости от запланированных качеств. Все марки производимой сырой резины стандартизированы, и количество каждого материала указано в процентах. Остается только пересчитать в соотношении к имеющейся массе каучука.
Полученная однородная масса остается подогретой, поскольку трение о детали машины и частиц друг о друга происходит с выделением температуры. В результате процесса образуется сырая резина. Ей придают форму полос заданных размеров (реже шнура) и упаковывают между полиэтиленом.
Изготовление изделий из резины
Для изготовления изделий сырую массу после смешивания помещают в специальные формы, создают давление и нагревают до 135-150 градусов. Процесс называется вулканизацией. Для маленьких деталей это закрытые штампы. Изделия по типу ковриков могут пропускаться через горячие барабаны с фигурной поверхностью.
При длительном воздействии высоких температур резина пересыхает и становится хрупкой. Поэтому в состав вводят серу и другие ускорители, позволяющие значительно сократить процесс вулканизации.
Домашнее изготовление сырой резины
Каучук, особенно искусственный, для вымешивания требует больших усилий. Мять его руками, как тесто, у человека недостаточно сил. Для этого делается специальное приспособление. Перемешивание с добавками — трудоемкий и длительный процесс. Вещества с различной дисперсностью, удельным весом и физическим состоянием надо превратить в однородную массу.
Готовится сырая резина своими руками в машине со шнековыми валами. Винтовые выступы перетирают все, что заложено в емкость, и перемешивают. Скорость изготовления зависит от количества валов. Дома обычно он один, и надо много времени на доведение смеси до нужного состояния.
Для формовки в листы и полосы достаточно двух валов, один из которых перемещается, изменяя размер зазора, следовательно, и толщину готовой сырой резины. Масса закладывается в накопитель и поступает на формовку. При деформации она остывает и теряет способность течь, становится прочной на разрыв.
Оборудование для домашней мастерской можно приобрести в магазине или сделать самостоятельно. За образцы взять технику, имеющуюся на кухне. Двигатель подойдет от поломанной стиралки или любой другой машины. Ремни и шкивы автомобильные.
В домашних условиях резина широко применяется для ремонта резиновых изделий. Это покрышки и камеры велосипедов и автомобилей, обувь. С помощью вулканизации создаются прокладки в краны и различные мелкие детали
Для латок на пробитые колеса наиболее часто используется листовая сырая резина. Инструкция по применению:
- Края камеры в месте пореза зачистить наждачкой, чтобы они не соприкасались торцами. Рваные выступы обрезать.
- Обезжиривается место вокруг пореза, обрабатывается напильником.
- Вырезается из сырой резины латка и накладывается на камеру.
- Зажимается струбциной и нагревается.
Для нагрева используется готовый вулканизатор, но его можно сделать самостоятельно. В случае промышленной установки один миллиметр толщины следует греть 4 минуты. В самодельном приспособлении время увеличивается до 10 минут, более точно оно определяется практическим путем.
Изготовление приспособления для вулканизации
Самодельные вулканизаторы делятся на электрические и бензиновые. Делаются они из деталей, отслуживших свой срок. Основные узлы:
Самая простая электрическая модель получается из старого утюга, в котором есть рабочая спираль. Этот вариант имеет регулятор, значит, удобнее других. Рабочая поверхность — подошва. Ручку лучше убрать, перевернуть утюг, установить на скобу из толстого листа. Сверху ложится ремонтируемое изделие и зажимается струбциной.
Для бензинового варианта использовать удобно поршень двигателя. В него наливается бензин и поджигается. Для контроля положите на латку бумагу. Она начинает желтеть на критической для резины температуре.
Как сделать силикон своими руками и, что для этого надо?
Не сложно изготовить силикон, он же силиконовый каучук, полидиэтилсилоксан, своими руками. Из него делали небольшие декоративные украшения для панно в кухне.
Для этого нужны всего жидкое стекло и этиловый спирт. Приготовленный силикон быстро застывает от соприкосновения с воздухом и влагой, поэтому готовить небольшими порциями. В равных пропорциях смешивается жидкое стекло и этиловый спирт, на этом этапе в состав можно добавить немного красителя, чтобы получить силикон нужного цвета. Быстро перемешать деревянной палочкой и поместить в шприц с насадками или сразу залить в подготовленную форму, или своими руками из него вылепить нужную фигурку, отлить формочку.
Силикон можно изготовить из следующих составляющих:
- силиконовый герметик;
- жидкий глицерин;
- акриловая краска любого цвета;
- пластиковый стакан, ложка, соломка или пипетка;
- уайт-спирит.
Смешивать эти составляющие будем в следующих пропорциях: на 30 грамм герметика — 3 капли глицерина, 1 капля краски и 150 грамм уайт-спирита.
Этапы приготовления силикона:
- Погружаем герметик в пластиковый стаканчик.
- Добавляем нужное количество глицерина и краски. Это сделать можно при помощи соломки, если под рукой нет пипетки.
- Добавляем уайт-спирит.
- Перемешиваем до тех пор, пока смесь не получится однородной (чтобы краски не было видно).
- Готово. У вас есть 4-5 часов, чтобы использовать силикон, пока он не затвердел!
Подобие силикона можно попробовать сделать в домашних условиях используя этиловый спирт и жидкое стекло, которые нужно смешать в равных пропорциях. Отличие такого силикона от покупного будет в сроке застывания. Жизнь самодельного очень низка и вручную успеть что-то вылепить будет сложно. Различные химические добавки как в покупной найти очень сложно. Также от может трескаться. Зато можно покрасить в любой цвет, примешав природные красители.
Изготовить силикон в домашних условиях совсем не сложно, тут не нужны особые знания в области химии.
Нам понадобятся всего два ингредиента, это этиловый спирт и “жидкое стекло”.
Далее готовим посуду под раствор (объём тары зависит от того сколько силикона Вы собираетесь произвести).
Теперь одеваем на руки резиновые перчатки (смесь довольно едкая получится) берём в руки деревянную палку (не обязательно палку, можно и ложку, но её придётся выкинуть) и начинаем перемешивать
Этиловый спирт и “жидкое стекло” разводим 1 к 1, другими словами в равных частях.
Перемешиваемая смесь очень скоро начнёт затвердевать, получится нечто белое и по консистенции напоминающее обычный пластилин.
Ещё спустя некоторое время эта масса превратится в подобие резины.
Если силикон нужен для изготовления какой-то формы, то мнём его руками (перчатки не снимаем) на первой стадии затвердевания.
Работать придётся быстро, смесь застывает не долго, лучше заранее приготовиться к дальнейшим действиям (приготовить форму и всё такое)..
Самый обыкновенный силикон получается путём смешивания жидкого стекла и спирта, например этилового.
Готовится он достаточно просто — надо взять два одинаковых объёма этилового спирта и жидкого стекла и смешать эти два компонента друг с другом. Получится достаточно жидкий раствор, но со временем он будет застывать, поэтому его необходимо разминать руками, для продления жизни силикона. В профессиональном изготовлении в эту массу добавляют специальные химикаты, которые увеличивают время застывания силикона, тем самым давая время на его обработку и применение.
Готовый, т.е. застывший силикон уже ничем не растворить, поэтому для его применения у вас ограничено время!
Силикон это мягкий желеобразный (прыгуче-тянучий) каучук, применяемый во многих поделках в домашних условиях. К примеру приманки для рыбалки.
Как синтезировать (изготовить) силиконовую смесь — очень просто!
Нужны общедоступные и всем понятные два реактива этиловый спирт и жидкое стекло (тот же канцелярский клей!)
Смешиваются они примерно в равных пропорциях и при синтезе образуют сначала как бы рыхлую вату, а затем эта вата затвердевает и становится силиконовым каучуком — при затвердевании из него можно формировать изделия или окрашивать во время перемешивания.
Весь процесс синтеза в простом и понятном видео — смотрите как легко!
В производстве силиконового каучуку вам понадобится лишь два составляющих: этиловый спирт и так называемое жидкое стекло.
Смешиваются компоненты в одинаковых количествах, то есть 1:1. Заранее приготовьте емкость для смешивания, а так же обеспечьте себя средством индивидуальной защиты рук. После добавление одного составляющего к другому смесь надо хорошенько перемешивать руками. Со временем смесь будет густеть все больше и больше, пока не превратиться в некий белый студень. Так же можно добавить краситель на свой вкус.
Могу вас поздравить, вы синтезировали полидиметилсилоксан!
В домашних условиях можно приготовить и качественный силикон. Для этого нужно купить или достать необходимое количество силиконового полимера и растворить в дихлорэтане, или любом хлорорганическом растворителе, но самый качественный силикон можно приготовить используя запатентованную добавку, которую можно купить в любом хозяйственном магазине, название привожу в цитате.
Силикон по-другому еще называют “каучук”, или силиконовый “каучук”.
Поэтому готовить его очень просто и готовка не займет у вас много времени.
Для начала у вас должен быть этиловый спирт и жидкое стекло.
Если вы не сможете найти жидкое стекло, то знайте что его еще по-другому называют канцелярский клей.
Дальше в равных пропорциях, в соотношении 1 к 1 засыпаем ингредиенты.
И за несколько минут под влиянием воздуха смесь становится похожей на вату.
При этом процессе можно добавить краску (гуашь) для более приятного цвета.
И обязательно выминать как тесто руками.
Также посмотрите мастер-класс по приготовлению силикона.
Для приготовления силикона в домашних условиях вам понадобится этиловый спирт, жидкое стекло и красители. Жидкое стекло и этиловый спирт смешивайте в равных количествах. На этом этапе, если надо, добавляйте красители. Свежеприготовленный силикон на воздухе быстро высыхает, поэтому используйте его сразу после приготовления. Если надо продлить время жидкой фазы, то поместите его в безвоздушное пространство, например в шприц.
elfterra.ru
Как размягчить резину в домашних условиях?
#1
Существует множество способов вернуть резиновым изделиям прежнее состояние, в котором их максимально удобно использовать. Поэтому на вопрос, как размягчить резину в домашних условиях, ответов найдется сразу несколько. А уж выбирать, как размягчать резину в каждом конкретном случае останется самому хозяину дома. В наиболее известном и распространенном способе обработки обсуждаемых изделий применяется нашатырный спирт. Главное его достоинство заключается в максимальной эффективности, доступности и дешевизне, ведь такой спирт можно приобрести по самой низкой стоимости в любой ближайшей аптеке. Для начала промыть резиновую часть водой и погрузить в водно-спиртовой раствор. Готовится он в пропорциях 1/1. Для такого купания будет достаточно около 30-40 минут. По прошествии указанного времени резину потребуется еще раз промыть чистой водой и тщательно высушить.
#2
Второй по популярности среди обывателей способ размягчения резины подразумевает применение касторового масла. Здесь важно отметить, что результат его будет быстрым, но недолгим. Поэтому обратить внимание на этот способ стоит в том случае, если размягчить резину требуется на короткий срок. Для начала резиновое изделие промывается водой и обсушивается, а затем полностью тщательно смазывается касторовым маслом, нанесенным на мягкую тряпочку или вату. Останется лишь дать объекту время на пропитку и можно использовать его. Срок зависит от величины изделия и толщины резины. Для миниатюрных деталей достаточно будет всего пары минут «отдыха». Кстати, если под рукой оказался жидкий силикон, то использовать вполне можно и его. Это средство дает точно такой же результат быстрого, но недолгого размягчения для резиновых изделий.
#3
Следующий способ, подсказывающий, как размягчить резину дома самостоятельно, будет более долгим, зато эффект от него сохранится на длительное время. Для этого потребуется большая кастрюля или другая емкость, доступная для нагревания, в которую удастся поместить резиновое изделие полностью. Если материал стал очень жестким, то лучше всего прокипятить его в подсоленной воде. Резина погружается в кастрюлю с жидкостью, а затем отправляется в этой емкости на средний огонь. Можно использовать для такого нагревания и кипятильник. Точное время процедуры указать сложно, оно также будет зависеть от размера изделия и степени его «задубелости». Чтобы определить срок ее завершения, нужно будет просто периодически проверять резину деревянной палочкой на мягкость.
#4
Но эффективным для размягчения обсуждаемых изделий окажется не только кипячение. Воздействовать высокой температурой на предметы можно и другими способами. Если, например, затвердевший шланг не удается надеть на нужную трубу, то его конец стоит просто на пару минут погрузить в кипяток. Главное, сразу после этого успеть быстро установить деталь, пока она не не вернулась в исходное состояние. Высокая температура очень быстро оказывает воздействие на резину, эффективно распаривая и смягчая ее. Если же снять используемую деталь оказывается затруднительно, то можно нагреть ее и другими способами, например, приложив ткань, смоченную в кипятке или воздействуя струей горячего воздуха из фена. После таких процедур нужный элемент быстро стянет мягким и податливым. Главное при этом беречь руки от воздействия высокой температуры или кипятка. Лучше предварительно защитить их плотными перчатками или каким-либо другим способом.
#5
Но известны и другие способы быстрого и простого размягчения резины при помощи подручных средств. Например, помочь в этом может и самый обыкновенный керосин. Известно, что он способен не просто смягчать резину, а полностью изменять ее структуру, возвращая материалу былую эластичность и податливость. Именно поэтому данный способ рекомендуется специалистами тем, кто хотел бы добиться результата, сохраняющегося на долгий срок. Нужно будет наполнить керосином емкость нужного размера, а затем погрузить в нее резиновое изделие. Не стоит погружать объект в холодный керосин, лучше предварительно оставить его при комнатной температуре на некоторое время. Обычно пары часов в обсуждаемом веществе оказывается достаточно для смягчения различных резиновых изделий. Как только нужный срок истечет, и керосин окажет желаемое воздействие на объект, можно будет вынуть конструкцию из жидкости, тщательно промыть под водой и обсушить.
uznay-kak.ru
Вопрос про резину. Как расплавить резину в домашних условиях???
Расплавить можно каучук, а не резину. В резине слишком много наполнителе, типа сажи, и сера для вулканизации.
пахнуть будет плохо, можно отравиться
А кто тебе сказал, что резину можно расплавить?
Резина не пластмасса, и чтоб ее девулканизировать надо сина много движений сделать При паровом методе дозированные порции обестканен-ной резиновой крошки смешивают с мягчителями и загружают в девулка-иизационный котел, где обрабатывают острым паром под давлением 0,8— 1,0 МПа при температуре 175—185°С в течение 7—8 ч (для шинной резины) . Полученный путем такой обработки депулкаиизат с целью гомогенизации и пластификации смеси последовательно перерабатывают на вальцах (регене-ратишш-смесительных и подготовительных рафинеровочных) и пропускают через червячный фильтр-пресс (стрейнер) . Окончательную обработку резиновой массы с выдачей готового продукта (регенерата) проводят на выпускных рафинеровочных вальцах.
никак если нужна форма или изделие используем вулканизатор и “сырую” резину
Одинокая женщина прочла в газете рекламу новой услуги – вызов мужчины на дом. Предлагались мужчины самых различных видов и характеров – от интеллигента до супермена. Поразмыслив она позвонила и заказала супермена. Явился здоровенный мужчина. Войдя он разоблачился, поиграл мускулами, достал из портфеля презерватив и надел его. Из того же портфельчика извлек вату, скатал два тампона и засунул себе в ноздри. Женщина с удивлением спросила: – Скажите, а нос вы зачем заткнули ? – Мадам, я не люблю запах жженой резины !
touch.otvet.mail.ru
Как размягчить резину в домашних условиях, если она задубела
Резина считается одним из самых распространенных материалов на сегодняшний день. Со временем основные характеристики могут существенно снизиться. Довольно распространенным вопросом можно назвать то, как провести размягчение резины. Подобную процедуру можно выполнить самостоятельно в домашних условиях, важно соблюдать все рекомендации.
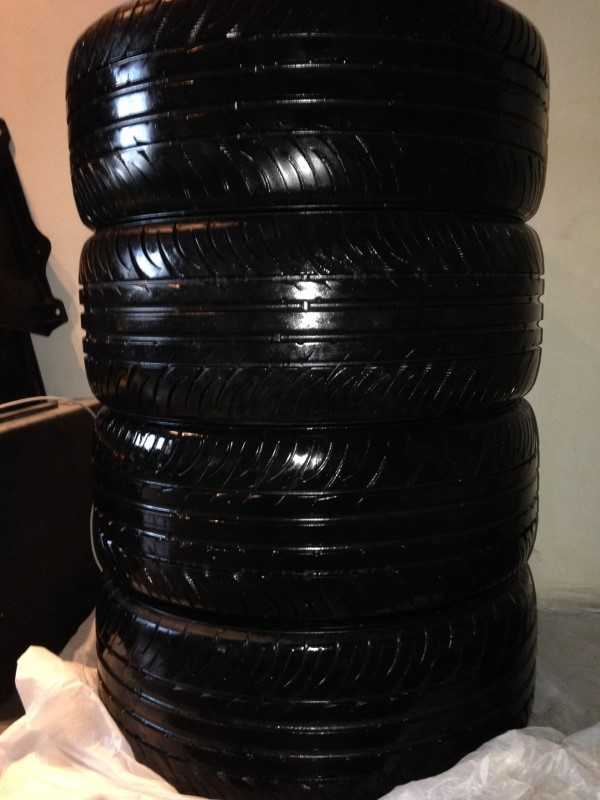
Самостоятельное восстановление резины
Все материалы со временем теряют свои эксплуатационные свойства. Часто можно встретить ситуацию, когда резина становится слишком жесткой и теряет свою упругость. При желании можно восстановить основные свойства материала, его не обязательно выбрасывать. Размягчить резину можно самыми различными метода. Среди особенностей этого вопроса отметим следующие моменты:
- Резиновые манжеты и уплотнители некоторых приспособлений со временем теряют свои основные свойства. В этом случае можно купить новые расходные материалы, так как их стоимость относительно невысока.
- Некоторые элементы сложно найти в продаже, что связано со необычной формой и свойствами. В этом случае можно провести размягчение при применении различных распространенных технологий.
Существует довольно большое количество различных способов размягчения резины, наиболее распространенный заключается в применении керосина.
Что нужно для восстановления эластичности резины?
Резина считается одним из самых эластичных материалов. Именно по этой причине ее применяют при изготовлении различных уплотнителей. После того как на уплотнитель прекращает воздействовать нагрузка он способен вернуть свои размеры. Этот момент определяет распространение вопроса, как восстановить эластичность резины. Со временем подобное свойство также теряется. При слишком большом износе поверхности появляются трещины, за счет которых изоляционные качества существенно снижаются
Размягчить резину в домашних условиях можно при использовании распространенных веществ. Чаще всего используются следующие вещества:
- Керосин может с легкостью восстановить показатель эластичности. Это вещество идеально подходит для обработки небольших изделий, размягчить можно путем их замачивания.
- Может использоваться нашатырный спирт, чтобы размягчить структуру. Для этого достаточно создать небольшую ванночку, в которую изделие опускается на несколько часов.
При размачивании резины в жидкости для восстановления стоит учитывать, что материал может существенно увеличиваться в размерах. Для удаления вещества с поверхности изделие тщательно промывается водой с мылом.
В некоторых случаях можно использовать горячую воду для размягчения резины. Этот метод применяется для того восстановления изоляции дверного проема холодильника. Усилить достигнутый эффект можно путем смачивания поверхности силиконом.
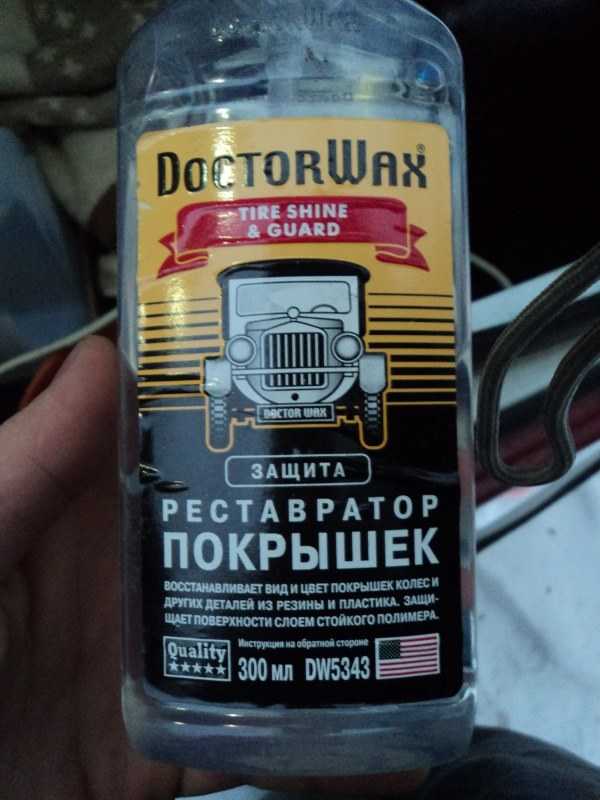
Реставратор покрышек
Уплотнители из рассматриваемого материала применяются и при производстве окон. Для повышения изоляционных качеств резинки время от времени протираются силиконом и глицерином. Подобные вещества можно приобрести без особых проблем.
Как придать эластичность резине?
Специалисты рекомендуют рассматривать каждый конкретный случай, что позволяет существенно повысить эффективность проводимой работы. Размягчить резину можно следующим образом:
- Жесткость повышается в случае, если резина находится долго в сухом состоянии. Упругость восстанавливается путем смачивания поверхности маслом. Размягчение рекомендуется проводить периодически для достижения требуемого результата.
- Автомобильные дворники можно смазать силиконовой смазкой, за счет чего проводится размягчение поверхности. Конечно, восстановить старую конструкцию можно только в случае отсутствуя механических дефектов.
Кроме этого, в продаже можно встретить специальные составы, которые могут размягчить структуру после нанесения.
Как размягчить резину в домашних условиях?
В домашних условиях размягчить резину можно при применении различных материалов. Наибольшее распространение получили:
- Нашатырный спирт.
- Керосин.
- Касторка и силикон.
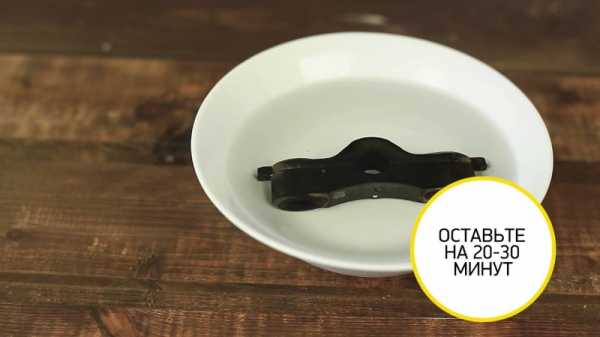
Восстановление резины в домашних условиях
Высокая температура также приводит к тому, что каучук становится более мягким, но снижается показатель износостойкости.
Керосин
При рассмотрении того, как размягчить резину многие уделяют возможности применения керосина. Подобное вещество способно восстанавливать показатель эластичности.
Особенности применения заключаются в том, что изделие размачивается в специальной ванной, после чего поверхность тщательно промывается и высушивается. Если протяженность изделия большая, то ее можно свернуть. Выдерживается в керосине для размягчения в течение нескольких часов, так как керосин действует не сразу.
Нашатырный спирт
Это вещество получило широкое распространение, оно также может сделать изделие более мягким. Процедура выглядит следующим образом:
- Выбирается емкость подходящего объема.
- Нашатырный спирт разводится в воде для получения требующего раствора.
- Изделие помещается в раствор на час для размягчения.
- После этого размягченный элемент достается и промывается чистой водой.
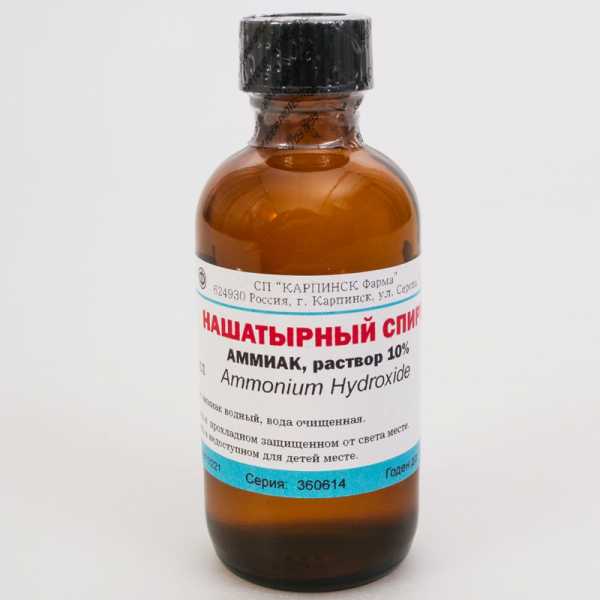
Нашатырный спирт
Сушка проводится при комнатной температуре. Стоит учитывать, что высокая и низкая температура всегда негативно отражаются на состоянии резины.
Силикон и касторка
Недлительный эффект можно достигнуть в случае использования силикона и касторки. Среди особенностей применения отметим следующие моменты:
- Силикон оказывает только временное воздействие. Его можно приобрести в специализированных магазинах.
- После смазывания нужно подождать некоторое время. Силикон может впитаться в структуру, сделав ее более эластичной.
После получаса резина будет готова к использованию. Стоит учитывать, что достигнутый эффект будет временным. При рассмотрении того, чем можно размягчить подобный материал, можно уделить внимание и касторке.
Нагревание
В некоторых случаях требуется лишь временное размягчение, к примеру, при надевании шланга на патрубок. Решить проблему в этом случае можно путем временного опускания изделия в горячую ванную. Через некоторое время воздействия высокой температуры эластичность повышается.
При длительной эксплуатации резина может задубеть. Решить проблемы можно только в случае кипячения изделия. Существенно повысить эффективность процедуры можно путем добавления в состав соли. Кипячение проводится вплоть до момента, пока поверхность не станет эластичной.
Если возникают трудности при снятии трубок и шлангов, то нагрев проводится путем оказания воздействия теплым воздушным потоком. Для этого может использоваться строительный или обычный фен. При концентрации воздушного потока высокой температуры в одном месте пластичность существенно повышается.
В заключение отметим, что только при отсутствии дефектов можно провести восстановление материала. Некоторые рекомендуемые методы могут привести к ухудшению некоторых эксплуатационных характеристик. Именно поэтому нужно соблюдать все рекомендации.
Если вы нашли ошибку, пожалуйста, выделите фрагмент текста и нажмите Ctrl+Enter.
stankiexpert.ru
Как размягчить резину в домашних условиях?
Во многих случаях изделия из резины бывают совершенно незаменимы. Различные уплотнители, ремни, шланги и прочие детали встречаются в конструкции предметов обихода и автомобильной технике. Но при длительном использовании или переохлаждении они могут стать жесткими и непригодными для дальнейшего применения. Как размягчить резину в домашних условиях? Существуют вещества и методы воздействия, помогающие добиться желаемого результата.
Керосин
Это вещество способно изменять структуру резины и восстанавливать эластичность изделий из нее. Процедура заключается в вымачивании предметов до получения необходимого эффекта. Резину большого размера можно аккуратно свернуть перед помещением в емкость с керосином. Спустя пару часов размягченную деталь нужно вынуть и тщательно промыть.
Нашатырный спирт
Есть и другой вариант – устроить изделию купание в водно-нашатырном растворе. Следует поместить резину в приготовленный состав и выдержать около получаса. Затем промытую и высушенную деталь можно будет применять по назначению.
к содержанию ↑Силикон и касторка
Чем можно размягчить резину хотя бы ненадолго? Временное воздействие окажет на нее силикон. Смазав им поверхность предмета, надо дать время на впитывание, после чего изделие будет готово к использованию. Подобную обработку можно провести и с применением касторового масла.
к содержанию ↑Нагревание
В ситуации когда не получается надеть шланг на округлую деталь или трубу, поможет погружение нужной части изделия в кипяток. Чуть подождав, необходимо извлечь шланг из воды и не теряя времени установить его в положенное место. Сделать это будет достаточно легко, поскольку от высокой температуры материал распарится.
Если резина задубела очень сильно, рекомендуется ее прокипятить. Лучшего результата можно добиться, подсыпав в воду соль. Кипячение в растворе производится до тех пор, пока материал не станет более пластичным.
Иногда возникает проблема со снятием резиновых элементов с каких-то конструкционных деталей. В этом случае эффективным окажется нагревание воздухом. Используется фен. Под воздействием горячей струи материал расширится, вследствие чего появится возможность прокрутить и стянуть ставший податливым элемент.
Такими простыми методами можно размягчить задубевшую резину, увеличив тем самым срок службы востребованных изделий.
thedifference.ru
Как сделать самодельную автошину – (старые методы) » Полезные самоделки
Автомобильные и мотоциклетные изготавливают с наличием так называемого «каркаса», силовой части, воспринимающей толчки и удары, которые испытывает при движении колесо. Даже на ровной дороге количество таких толчков весьма велико. Если изготовить шину из одной только резиновой массы (а модельные шины именно так и изготовляются), она очень быстро потеряет форму и разрушится, не выдержав прилагаемых к ней нагрузок, Чтобы этого не случилось, в конструкцию шины вводится каркас.
Он состоит из большого количества прочных нитей, которые расположены по всему ее периметру и образуют как бы сетку, которая способна выдерживать высокое давление заключенного в шине воздуха и большое количество толчков и ударов, воспринимаемых шиной извне. А для того, чтобы шина надежно держалась на ободе колеса, в ее борта заформовываются кольца из гибкой стальной проволоки.
Детали каркаса шины соединяются между собой резиновой массой, имеющей достаточную прочность и эластичность. А внешняя часть шины защищается слоем протектора – из резины более жесткой. Толщина и рисунок протектора зависят от назначения шины. Например, для езды по бездорожью применяется более высокий и крупный рисунок протектора (так называемые «грунтозацепы»).
А для асфальта изготовляются шины с более мелким рисунком. Поперечный разрез шины показан на рис. 1. и рис. 2
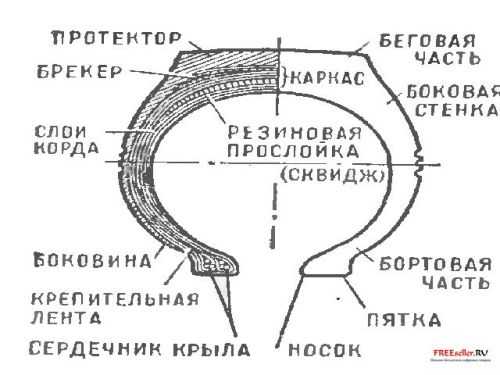
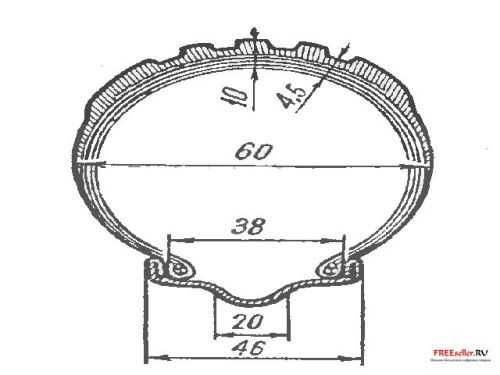
Рис.1. Поперечный разрез самодельной шины.
На микромотоциклах шины работают в исключительно тяжелых условиях. К примеру, если нормальное мотоциклетное колесо при прохождении десяти метров дороги должно повернуться вокруг своей оси восемь раз, то колесо микромотороллера совершает в три или четыре раза больше оборотов, поскольку диаметр его меньше.
Так, при скорости 70 км/час колесо микромотоцикла диаметром 320 мм должно делать 1200 об/мин. При таких больших оборотах частота деформаций шины и нагрев очень велики. Перегрев шины приводит к ее быстрому разрушению. В самых неблагоприятных условиях находится шина заднего колеса.
У микромотоциклов примерно г/з веса приходятся на заднее колесо, которое к тому же охлаждается хуже, чем переднее. Вследствие небольших размеров микромотоциклов и микромотороллеров расстояния между горячим двигателем и колесами очень невелики. От этого шины могут быстро перегреваться.
Поэтому самой трудной проблемой при проектировании шин для микро мототранспорта является увеличение их теплоотдачи. Стенки шины, имеющие большую теплоемкость, не позволяют рассеивать в окружающее пространство необходимое количество тепла.
Уменьшать толщину покрышки можно только в определенных допустимых пределах, поскольку нагрузка на нее очень велика. Учитывая все это, при конструировании микрошин мы руководствуемся следующими соображениями: каркас покрышки изготовляется из двух слоев высокопрочного капронового корда, больше других материалов отвечающего условиям работы в шине, поскольку он обладает малым весом и высоким сопротивлением многократным изгибам. Мы изготовили несколько покрышек из вискозного и хлопчатобумажного корда, каркасы которых ввиду малой прочности пришлось делать 4-х слойными. эти покрышки быстро выходили из строя из-за перегрева.
При накачивании шины воздухом в нитях слоев корда действуют большие растягивающие усилия. Величина этих усилий зависит не только от давления воздуха, но и от количества слоев корда, и от геометрического профиля шины, ее размеров, нагрузки и ширины обода. Каждый профиль шины рассчитан на определенную ширину обода. Применение ободьев от детских роллеров (самокатов) не обеспечивает необходимых условий для нормальной работы шин, даже при скорости движения 40 км/час и нагрузке порядка 50 кг. Для обеспечения необходимых условий работы ободья должны быть значительно шире (не менее 35-З8 мм между буртиками). В этом случае можно изготовить покрышки, рассчитанные на нагрузку 60-80 кг и скорость порядка 60-70 км/час.
Геометрический профиль спроектированной нами шины приведен на рис. 2 в натуральную величину, а конструкция покрышки изображена на рис. 3.
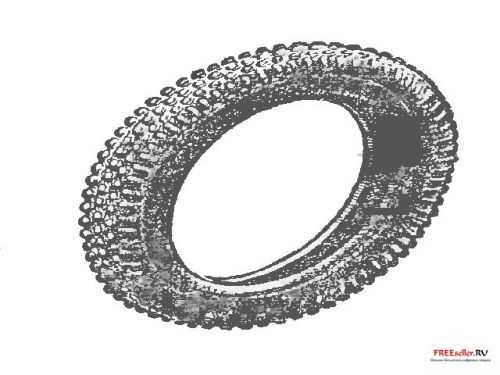
Рис.3. Конструкция авто шины.
Технология изготовление шин (мини завод по производству шин
При работе покрышки важно, чтобы нити корда были хорошо изолированы,, друг от друга резиной и не перетира лись. Для этого между слоями корда (хотя он уже обрезинен) прокладывается тонкий слой резины (0,5 мм), так называемый «сквидж». Для этой цели можно использовать сырую резину, применяемую для ремонта автомобильных камер в автохозяйствах. Наличие слоя эластичной резины между слоями корда и такой же резины поверх всего каркаса не только предотвращает перетирание нитей корда, но сообщает каркасу эластичность и увеличивает прочность связи между слоями каркаса и следующим слоем, называемым брекером.
Брекер – это дополнительный слой эластичной резины толщиной 2- 2,5 мм, служащий для повышения прочности связи каркаса покрышки с протектором. Он предохраняет каркас от возможных пробоев и повреждений. При резких торможении и ускорении получается внутренний сдвиг между малоэластичным, но износостойким слоем протекторной резины и каркасом. Задача брекерного слоя – погасить энергию этого сдвига, не дать шине расслоиться. Резина брекера должна быть эластичной, теплостойкой и прочной на разрыв.
При сборке шины брекерная лента делается шире протекторной на 5-6 мм. Для нее наиболее подходящей является готовая сырая резина на основе изопренового или натурального каучука. Но поскольку такую резину не всегда возможно достать, нами с успехом применяется следующий способ: берем обычную сырую резину, предназначенную для ремонта камер (толщина примерно 0,8-1 мм) и кусок натурального каучука для изготовления резинового клея. Из него остро отточенным ножом вырезаются пластинки толщиной 1-1,5 мм. Затем, тщательно промазав клеем для горячей вулканизации заготовленную полоску из сырой резины и нарезанные пластинки каучука и дав клею подсохнуть 5-6 мин., наклеиваем пластинки на полоску сплошным слоем, без щелей и наползания друг на друга.
Полученная двухслойная лента приклеивается к каркасу стороной из каучуковых пластинок, а затем на нее наклеивается протекторный слой. Протектор изготовляется из высокопрочной, износостойкой резины. Он располагается только на беговой дорожке покрышки. Его толщина зависит от величины самой шины. Для наших шин, имеющих диаметр 320 мм, толщина протектора должна быть в пределах 4-6 мм. Качество протектора определяет долговечность шины, поэтому требования к резине, из которой он изготовляется, несколько иные, чем к резине брекерного слоя. Наилучшей оказывается резина, предназначенная для ремонта протекторов покрышек автомобилей.
Для большего удобства сборки шины двухслойную ленту брекерного слоя и ленту протекторного слоя можно склеить между собой, а затем уже приклеить полученную трехслойную ленту к каркасу покрышки. Ширина протекторной ленты для наших покрышек равна 50-55 мм.
Рисунок протектора может быть различным, в зависимости от назначения шины и условий эксплуатации.
Показанный на рис. 4 рисунок протектора является универсальным. Шины с таким протектором одинаково хорошо работают на дорогах с самыми различными покрытиями.
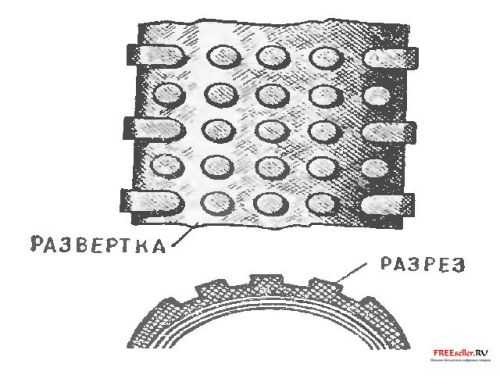
Рис.4. Универсальный рисунок протектора шины.
Изготовление матрицы для получения такого рисунка протектора не представляет трудностей и может быть выполнено даже в домашних условиях.
Для этого берется полоса мягкого алюминия толщиной 4-6 мм (толщина материала определяет желаемую глубину рисунка) и в ней согласно рис. 5 высверливаются отверстия. Затем полоса разрезается ножовкой вдоль по осевой линии на две равные части. В каждой части выпиливаются фасонные пазы, острым ножом снимаются фаски и заусенцы, напильником выравниваются все неровности, а концы, оставшиеся после выпиливания шипов, стачиваются под углом 45°.
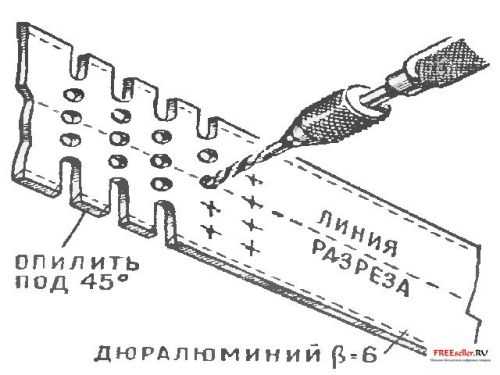
Рис.5. изготовления матрицы для рисунка протектора.
После окончательной зачистки шкуркой части матрицы приклепываются заклепками из мягкой алюминиевой проволоки к половинкам пресс формы с ее внутренней стороны. Такая конструкция пресс формы позволяет избежать сложных фрезерных работ. Сама пресс форма изготовляется путем отливки в землю, из алюминия или другого легкого сплава (нами были использованы для этого старые поршни от автомобильных двигателей, собранные на свалке).
Оснастка для отливки (форма и ящик) показаны на рис. 6. Расплав алюминия можно вести прямо в форме, нагревая его пламенем газовой горелки или, как обычно, в муфельной печи. Мы, например, выполнили отливку на месте ремонта металлической ограды парка, где велись газосварочные работы.
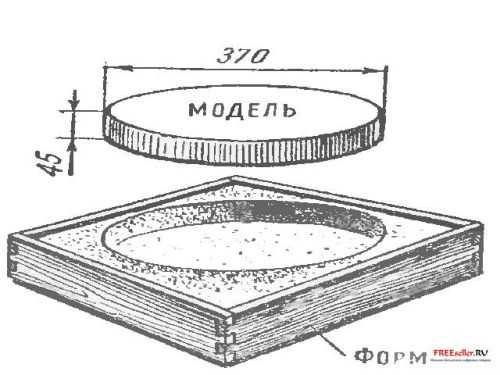
Рис.6. Оснастка для отливки шин.
Отливки надо вынимать из формы, не разрушая ее, и только после полного их остывания. Ускорять остывание, смачивая отливку водой, нельзя.
Подготовка матрицы заканчивается сверлением отверстий под болты, стягивающие ее во время варки покрышки.
Отлитые заготовки для пресс-формы обрабатываются на токарном станке в соответствии с рисунком. Особое внимание должно быть уделено подгонке половинок формы и дисков друг к другу, а также тщательной наклепке решетки протектора (рис. 2).
Сборка покрышки
В качестве оправки для сборки мы используем негодную («лысую», но не деформированную) покрышку от детского самоката. Сначала на наждаке, а потом – шкуркой разной зернистости с нее удаляются остатки протектора, чтобы поверхность стала совершенно гладкой.
Заправив внутрь обработанной таким путем покрышки камеру и слегка подкачав ее воздухом, сшиваем внутренние края покрышки прочными нитками, тщательно прихватывая при этом и бортовые кольца. Расстояние между бортами должно быть одинаковым по всей окружности (рис. 9).
Порядок сборки покрышки на оправке
1) Приготовление кусков обрезиненной кордовой ткани.
Их длина должна быть такой, чтобы после оборачивания вокруг оправки под углом 52° на загиб вокруг бортового, (проволочного) кольца оставалось 20-25 мм.
2) Накачивание воздухом оправки.
3) Укладка первого слоя корда.
При этом необходимо слегка растягивать середину заготовок, увеличивая тем самым расстояние между нитями с таким расчетом, чтобы они были одинаковыми по всему периметру колеса. Нити корда должны ложиться ровно, в один слой, и не наползать друг на друга даже в месте расположения бортового кольца (там, где густота нитей максимальна). Для облегчения укладки не рекомендуется делать слишком широких заготовок корда, удобнее всего ширина 40-50 мм.
4) Укладка бортовых колец из стальной проволоки диаметром 0,25-0,3 мм – очень ответственная операция.
Как показала практика, быстрый выход из строя покрышек от детских самокатов объясняется именно плохим качеством бортовых колец – они расходятся, так как концы их ничем не скреплены, посадочный диаметр покрышки изменяется, и это приводит к саморазбортовыванию колеса. Для изготовления кольца в качестве оправки мы используем сам обод колеса.
Для этого необходимо сначала вырезать полоску из 3-мм резины (например, из старой автомобильной камеры) шириной 10-12 мм и из нее склеить кольцо диаметром несколько меньше посадочного места обода. Это кольцо натягивается на обод, затем из сырой резины толщиной 0,5 мм вырезается ленточка шириной 10 мм и из нее делается один виток вокруг надетого на обод кольца. Наматывая после этого проволоку (8- 10 витков) непосредственно на сырую резину, большой натяг делать не следует, так как можно прорезать тонкой проволокой резину насквозь. Скрепив концы готового кольца скруткой, обильно смажем его клеем, дадим подсохнуть и завернем, не снимая с обода, в ленточку из сырой резины, на которую оно наматывалось. Готовое кольцо снимается с обода вместе с резиновым кольцом, которое можно использовать многократно.
Промазывание клеем и обрезинивание проволочного кольца необходимо для того, чтобы проволока не отслаивалась от борта покрышки при ее дальнейшей обработке.
Для каждой покрышки надо изготовить два кольца. Они тщательно промазываются клеем и укладываются на свои места после укладки первого слоя корда.
5) Оклейка сырой резиной толщиной 0,5-0,7 мм поверхности первого слоя корда.
Приклеенная резина не должна наползать на бортовые кольца. Но не должно оставаться больших промежутков между ними; обклеивать удобнее, предварительно нарезав, сырую резину в виде ленты, немного более широкой, чем расстояние между бортовыми кольцами, а затем – после приклейки – удалить ее излишки при помощи кривых маникюрных ножниц.
6) Заворачивание концов корда вокруг бортовых колец с приклейкой их к слою сырой резины (сквиджу).
Приклеенные концы не должны наползать друг на друга и быть длиннее 15-20 мм. Если они получились длиннее, их необходимо обрезать.
7) Укладка второго слоя корда. Она производится так же, как и первого, с той лишь разницей, что угол наклона нитей корда должен быть противоположен углу наклона первого слоя. Концы нитей корда второго слоя заворачиваются вокруг бортовых колец не наружу, как первого, а внутрь покрышки. Эту операцию удобнее сделать, когда готовая покрышка будет снята с оправки.
8) Приклеивание ленты брекерного слоя.
Лента должна закрывать беговую дорожку и несколько заходить на борта (примерно на 2-3 мм на каждую сторону).
9) Оклеивание бортов сырой резиной.
Применима сырая резина для ремонта камер толщиной 0,5-0,7 мм. Сначала ее нарезают в виде ленты, которая должна наклеиваться плотно к борту покрышки встык с краем уже наклеенной брекерной ленты. При этом надо тщательно приглаживать ленту к борту покрышки, чтобы не образовывались воздушные пузыри. Излишки бортовой ленты обрезаются кривыми ножницами по внутреннему (посадочному) диаметру покрышки.
10) Приклеивание слоя протекторной резины толщиной 4-5 мм.
Протекторная лента не должна заходить на борта покрышки и обязательно плотно прилегать к наклеенной ленте брекерного слоя.
11) Удаление оправки из покрышки.
Для этого из нее выпускают воздух, вынимают из покрышки, после чего второй слой корда заворачивается и приклеивается к внутренней поверхности покрышки с перехлестом порядка 15-20 мм. На этом сборка покрышки заканчивается. Желательно еще обклеить посадочные места собранной покрышки «чефером», то есть слоем обрезиненной ткани полотняного переплетения. Это укрепляет борта, что особенно важно, если покрышка будет эксплуатироваться на колесе, имеющем обод с мелким ручьем. Но если у обода глубокий ручей, как, например, у микромотоцикла «Агидель», – оклейке чефером не обязательна. Лента из чефера наклеивается на посадочные места так, чтобы по наружной стороне покрышки ширина ее равнялась 30-35 мм, а 20-25 мм было завернуто внутрь.
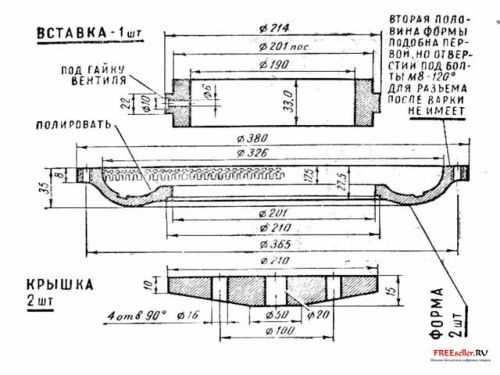
Рис. 7. Пресс-форма для отливки шин.
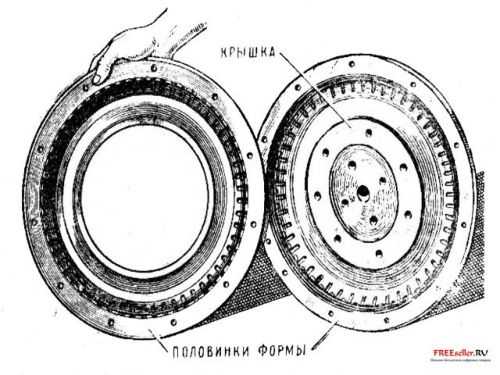
Рис. 8. Пресс-форма с решеткой протектора.
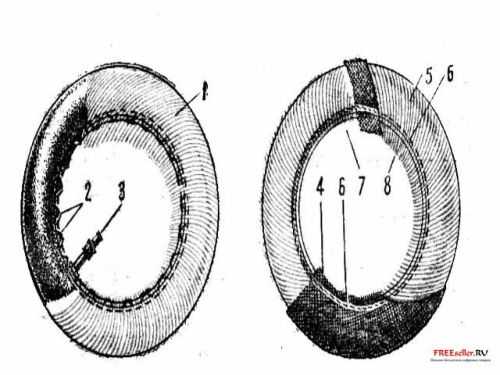
Рис. 9. Порядок сборки покрышки.
1 – участок с уложенным первым слоем, 2 – сшитые края понрышни1 3 вентиль, 4 – прослойка из сырой резины (толщина = 0,5 мм), 5 – второй слой корда, 6 – бортовое кольцо, 7 – завернутые наружу концы корда, 8 – вворачиваемые внутрь края корда.
Собранную описанным способом покрышку необходимо вулканизировать, чтобы придать ей износоустойчивость и прочность. Ведь сырая резина, из которой мы собирали покрышку, потому и называется сырой, что она не обладает достаточной стойкостью против различных механических и химических воздействий. Но после непродолжительного нагревания до определенной температуры сырая резина необратимо меняет свои физико-химические свойства – она становится практически нерастворимой, твердой, упругой, способной выдерживать большие ударные и растягивающие нагрузки и хорошо сопротивляться истиранию. Этот процесс называется вулканизацией.
Вулканизация в настоящее время широко применяется не только в промышленности, но и для бытовых нужд, например, при ремонте резиновой обуви и других предметов обихода. Портативные вулканизаторы, работающие от аккумулятора или снабженные бензиновой горелкой, позволяют ремонтировать автомобильные камеры в пути.
Клей для горячей вулканизации
Такой клей не всегда удается достать, но его можно изготовить и в домашних условиях. Для этого натуральный каучук растворяют в чистом бензине (авиационном, или так называемом «калоша») и на один литр клея добавляют 50 г порошкообразной серы. Если такой серы в готовом виде нет, следует размельчить кусковую серу и просеять ее через металлическое сито с ячейками 0,2X0,2 мм. Перед нанесением клея на поверхность вулканизированной резины она должна быть подготовлена: тщательно зачищена на наждачном круге или вручную – крупнозернистой шкуркой. Касаться пальцами зачищенных поверхностей нельзя. Сырую резину зачищать не нужно. Если ее поверхность окажется загрязненной, достаточно протереть тряпочкой, смоченной в бензине.
Нанеся клей на обе склеиваемые поверхности, их подсушивают на воздухе и плотно прижимают друг к другу, следя За тем, чтобы между ними не оставалось воздушных пузырьков. При склейке колец, варочных или ходовых камер концы ленты надо не только зачистить, но и свести на конус, чтобы толщина склейки не была толще самой ленты. Если клей долго стоял без употребления, его необходимо тщательно размешать, доставая до дна Посуды, в которой он хранился, так как сера со временем осаждается на дно.
В. Петровский, г. Уфа
www.freeseller.ru