Литейное производство хтс – Литье в формы ХТС (холодно твердеющие смеси)
alexxlab | 14.04.2016 | 0 | Вопросы и ответы
ПМК-Прогресс. Литейное производство.
ООО «ПМК-Прогресс» предлагает следующие виды литья:
— Литье по газифицированным моделям:
Литье по газифицированным моделям применяется для производства точных (минимальная механическая обработка) отливок из легированных сталей, высоколегированных жаропрочных (хладостойких) и износостойких углеродистых сплавов, высокомарганцовистых сталей, чугуна, высокопрочного чугуна, бронзы и латуни. Масса отливок от 0,2 до 500 кг. Точность отливок в зависимости от размеров 6-10 классов по ГОСТ 26645-85.
Габариты: размеры отливок до 2000×700×500мм. Масса: от 0,2 до 500 кг.
Материал:
сталь марок: 25Л, 35Л, 45Л, 30ХНЛ, 35ХМЛ, 20Х25Н19С2Л, 35Х18Н24С2Л, 35Х23Н7СЛ, 40Х9С2Л, 40Х24Н12СЛ, 40Х23Н10СЛ, 110Г13Л.
чугун марок: СЧ15, СЧ18, СЧ20, ВЧ40,ЧХ16М2,ЧХ28,ЧХ30 и т.д.
— Литье в ХТС (холодно твердеющие смеси):
Холодно-твердеющие смеси – это специальные смеси, которые после изготовления не требуют нагрева в сушильных печах. Благодаря связующим составляющим и отвердителям, они самозатвердевают на воздухе за 10-15 мин. Эта технология очень похожа на традиционную (литье металла в песчано-глинистые формы), только в виде связующего вещества для смесей песка применяют искусственные смолы. Для отверждения смол применяется продувка стержневых ящиков различными третичными аминами. Возможность получать отливки 7 класса точности по ГОСТ 26645-85. Холодно-твердеющие смеси крайне редко применяются в качестве общих формовочных материалов вследствие высокой стоимости связующих и затруднительной регенерации смесей. Применение ХТС для изготовления форм экономически оправдано в том случае, когда отношение массы формы к массе заливки металла не превышает 3:1. Поэтому эти смеси используются преимущественно для изготовления стержней, позволяющих формовать полости в отливке. Технология литья в ХТС позволяет обеспечить высокое качество поверхности литья, отсутствие газовых дефектов и засоров в отливке.
— Литье по выплавляемым моделям:
Это процесс, в котором для получения отливок применяются разовые точные неразъемные керамические оболочковые формы, получаемые по разовым моделям с использованием жидких формовочных смесей. Литье по выплавляемым моделям обеспечивает получение сложных по форме отливок массой от нескольких грамм до десятков килограмм, со стенками толщиной от 0,5 мм и более, с поверхностью, соответствующей 2—5-му классам точности (ГОСТ 26645-85), и с высокой точностью размеров по сравнению с другими способами литья. По выплавляемым моделям отливают лопатки турбин, режущий инструмент (фрезы, сверла), кронштейны, карабины, мелкие детали автомобилей, тракторов.
Габариты: максимальный диаметр, высота, длина, ширина – 300 мм; толщина стенок – от 3 мм.
Масса: от 0,02 до 30 кг (при художественном литье масса не ограничена)
— Литье в землю (литье в песчано-глинистые формы):
Литье в землю является сравнительно простым и экономичным технологическим процессом. Во многих отраслях машиностроения (автомобилестроение, станкостроение, вагоностроение и др.) при массовом производстве отливок чаще всего применяется этот метод. Его технологические возможности: в основном, в качестве материала отливок используется серый чугун, обладающий хорошей жидкотекучестью и малой усадкой (1%), малоуглеродистая сталь (< 0,35%С). Весьма ограничено производятся таким способом отливки из медных и алюминиевых сплавов. Качество металла отливок весьма низкое, что связано с возможностью попадания в металл неметаллических включений, газовой пористостью (из за бурного газообразования при заливки металла во влажную форму). Форма отливок может быть весьма сложной, но все же ограничена необходимостью извлечения модели из формы. Размеры отливки теоретически неограниченны. Таким способом получают самые крупные отливки (до сотни тонн). Это станины станков, корпуса турбин и т. д. Точность получаемых отливок обычно грубее 14 квалитета и определяется специальными нормами точности. Шероховатость поверхности отливок превышает 0,3мм, на поверхности часто наличествуют раковины и неметаллические включения. Поэтому сопрягаемые поверхности деталей, заготовки которых получают таким методом, всегда обрабатывают резанием.
— Центробежное литье:
Принцип центробежного литья заключается в том, что заполнение формы расплавом и формирование отливок происходят при вращение формы либо вокруг горизонтальной, вертикальной или наклонной оси, либо при её вращение по сложной траектории. Технология центробежного литья обеспечивает целый ряд преимуществ, зачастую недостижимых при других способах, к примеру: высокая износостойкость, высокая плотность металла, отсутствие раковин. В продукции центробежного литья отсутствуют неметаллические включения и шлак. Центробежным литьем получают литые заготовки, имеющие форму тел вращения: втулки, венцы червячных колес, барабаны для бумагоделательных машин, роторы электродвигателей. Наибольшее применение центробежное литье находит при изготовлении втулок из медных сплавов, преимущественно оловянных бронз. По сравнению с литьем в неподвижные формы центробежное литье имеет ряд преимуществ: повышаются заполняемость форм, плотность и механические свойства отливок. Однако для его организации необходимо специальное оборудование; недостатки, присущие этому способу литья: неточность размеров свободных поверхностей отливок, повышенная склонность к ликвации компонентов сплава, повышенные требования к прочности литейных форм.
— Литье в кокиль:
Кокильное литье – это литье металла, осуществляемое свободной заливкой кокилей. Кокиль – металлическая форма с естественным или принудительным охлаждением, заполняемая расплавленным металлом под действием гравитационных сил. После застывания и охлаждения, кокиль раскрывается и из него извлекается изделие. Затем кокиль можно повторно использовать для отливки такой же детали. Данный метод широко применяется при серийном и крупносерийном производстве. Точность отливок обычно соответствует классам 5 -9 для отливок из цветных металлов и классам 7-11 для отливок из черных металлов (ГОСТ 26645-85). Точность отливок, полученных в кокиле по массе примерно на один класс выше по сравнению с песчаными формами. Широкая гамма изделий для всех отраслей промышленности (детали двигателей, заготовки венцов зубчатых колес, корпусных деталей и т. д.).
Марки выплавляемых металлов: алюминиевые сплавы: АЛ2, АЛ4, АЛ9, АК12, АК9, АК7; магниевые сплавы МЛ5, МЛ6, МЛ12, МЛ10; медные сплавы; отливки из чугуна; отливки из стали: 20Л, 25Л, 35Л, 45Л, также некоторые легированные стали 110Г13Л, 5ХНВЛ.
Материалы применяемые при изготовлении отливок на литейном производстве:
Коррозионностойкая сталь, марки: 20Х13Л, 08Х14НДЛ, 09Х16Н4БЛ, 09Х17Н3СЛ, 10Х12НДЛ, 10Х18Н9Л, 15Х13Л, 03Х15Н4ДМЛ, 16Х18Н12С4ТЮЛ, 10Х18Н3Г3Д2Л, 07Х17Н16ТЛ;
Жаростойкая сталь, марки: 20Х5МЛ, 20Х8ВЛ, 15Х25ТЛ, 12Х25Н5ТМФЛ, 35Х23Н7СЛ, 40Х24Н12СЛ, 20Х20Н14С2Л, 55Х18Г14С2ТЛ, 20Х25Н19С2Л;
Жаропрочная сталь, марки: 40Х9С2Л, 20Х12ВНМФЛ, 12Х18Н9ТЛ, 10Х18Н11БЛ, 12Х18Н12М3ТЛ, 15Х23Н18Л;
Кислотоупорная сталь, марки: 18Х25Н19СЛ, 45Х17Г13Н3ЮЛ, 15Х14НЛ, 08Х12Н4ГСМЛ, 12Х21Н5Г2СЛ, 12Х21Н5Г2СТЛ, 12Х21Н52СМ2Л, 12Х19Н7Г2САЛ, 12Х21Н5Г2САЛ, 07Х18Н10Г2С2М2Л, 15Х18Н10Г2С2М2Л, 15Х18Н10Г2С2М2ТЛ;
Износоустойчивая сталь, марки
: 110Г13Л, 110Г13ФТЛ, 130Г14ХМФАЛ, 120Г10ФЛ, 110Г13Х2БРЛ, 85Х4М5Ф2В6Л (Р6М5Л), 90Х4М4Ф2В6Л;Чугун, марки: СЧ20-25, ВЧ40-70, ЧХ16, ЧХН2;
Алюминиевые сплавы, марки: АК5 — АК12, АК5М2;
Бронзовые сплавы, марки: Бр.ОЦС-5-5-5, Бр.О10Ф1 и др.
Контроль качества проводится по всем параметрам и осуществляется после каждой производственной операции. Предприятие имеет сертифицированную лабораторию проверки качества, дающую возможность с большой точностью проводить химический анализ продукции.
/p
pmkprogress.ru
Литье ХТС
Завод по производству литья стали и металла «Zavod-Litja.ru» ведет свои работы на протяжении долгого времени, соблюдая все правила и стандарты ГОСТ. Клиент останется довольным в получении своего заказа по всей России и СНГ. Отвечаем за качество готовой продукции перед самим клиентом и стандартами мирового уровня.
Литье ХТС
Наша работа заключается не только в литье из бронзы, но и стали, чугуна, выполнении оптовых поставок и единичной продукции. Работа также заключается в хороших взаимоотношениях с клиентами, индивидуальному, особому обращению к каждому из них, чтобы заключать договора на продолжительную совместную работу на взаимовыгодных условиях.
Наш завод работает в основном в узконаправленную сторону и предлагает все виды литья из черных и цветных металлов от 1кг. Это литье из различных материалов. Заготовки, отливки, модельная оснастка из чугуна и различных других сталей и сплавов.
Высокое качество изделий
Качественная и высоко технологичная обработка и полное изготовление деталей и других изделий, выполняется за счет лучших технических станков и машин мирового уровня. При таком оборудовании масштабность заказанных изделий не отражается на качестве выполненных работ.
Литье при помощи ХТС – немного похожа на литье в землю, то есть в глиняно-песчаную форму. Однако вместо глины и песка, из которых состоит эта форма, при ХТС расплавленный материал заливается в форму.
Сделана она с добавлением искусственной смолы, а также веществ, которые за 10 минут при нахождении на воздухе затвердевает. Такой метод литья ХТС позволяет быстро изготавливать формы и модельные оснастки, так как не требует высыхания в специальных сушильных печах. Также чтобы затвердитель сработал, идет продувка стержневых ящиков при использовании третичных аминов. При ХТС мы имеет возможность получения отливок высоко класса точности №7, все изделия соответствуют ГОСТ 26645-85.
Такой способ литья используют только в экономически выгодном случае, когда масса самой формы не должна превышать массу заливки. Соотношение должно выглядеть так — 3:1. ХТС применяется в большинстве случаев для отлива стержней, которыми делают полости и отверстия в отливках, также благодаря этому способу литья, можно избежать газовых дефектов и засорений в отливках.
При литье ХТС используют следующие материалы:
- 25Л, 30Л, 35Л, 45Л, 40ХЛ – это низколегированная конструкционная сталь.
- Л1, Л2, Л3, Л4, Л5, Л6 по ГОСТу 4832-95 – это литейный чугун.
- Алюминиевые сплавы для литья с ГОСТом 1583-93.
- Латунь для литья ГОСТ 1020-97.
- Бронза для литья с ГОСТом 613-79.
Что такое оснастка для литья
В способе литья ХТС используют линейную оснастку в опоку. Материалом для самой оснастки служит МДФ, композитный материал или пластик с помощью этого способа можно осуществить литье сплавов меди и других металлов.
А вот если требуется выполнить оптовый заказ, тогда линейная оснастка будет из алюминия или любых других металлов. Работая на машинах с ЧПУ, можно изготовить модельную оснастку учитывая все параметры, например, усадку при литье в форму, а также можно разработать и изготовить отливки, которым не нужна будет механическая обработка.
Изготавливая отливки подобным методом, мы получаем класс точности ЛТ3-ЛТ4 при погрешности 0,2-0,5 мм. Когда модельная оснастка пропитывается специальным составом, который делает ее очень прочной, такую оснастку можно использовать несколько тысяч раз, то есть съёмов.
Формы простые, состоят из двух половинок, также для того, чтобы сделать полости или отверстия, нужно изготовить специальные стержневые ящики.
Инженеры и конструкторы, которые работают на нашем заводе, занимаются проектировкой и разработкой оснасток. Благодаря их опыту мы исключаем возможные появления брака в процессе литья ХТС. Например, поры и раковины в отливках, или возможность смещения формы и других дефектов.
Только мы делаем продукцию высокого качества
Наше производство делает продукцию с минимальными припусками, так мы получаем отливки с малым весом. В нашем распоряжении имеются многоместные отливки, которые помогают работать еще быстрее при оптовых заказах, также снижается стоимость этих заказов. Чтобы осуществить доставку в сроки не только по Российской Федерации, но и по СНГ, мы делаем дополнительно определенные комплекты, если тираж заключается в целой серии отливок.
ХТС и его применение
Если поступает заказ, который требует выполнить большие отливки, тогда за неимением другой альтернативы, используют метод ХТС. Отливки, за счет добавления в состав ХТС 0,6% смолы и затвердителя, становятся качественнее по гладкости поверхностей, и точно соответствуют заданным формам и параметрам (уступы, отверстия, впадины).
Гладкость поверхности литье из меди на заказ в первую очередь зависит от формы, в которую льют металл или сплав. Мы делаем формы прочными в техническом и механическом смысле.
Мощнейшее производственное оборудование
В сталелитейных цехах нашего завода находятся индукционные печи ИСТ-0,5. Такие печи работают для плавления и перегрева посредством токов, которые работают на средней частоте.
Печь плавит сталь, чугун, металл цветной и драгоценный. Существуют и другие печи на нашем заводе – это печи сталеплавильные дуговые ДСП-0,3.
Работают они так
С помощью электрической дуги, которая подвергается температурному воздействию разрядом. Такие электрические печи и плавят сталь и металл. Печи, станки, методы литья и многое другое, одним словом оборудование, и дает нашему заводу производить высококачественный продукт.
Клиент, обратившийся к нам, может спокойно оставить свой заказ и быть уверенным в выполнении и соблюдении всех договоренностей. Продукт, который выпускает «Zavod-Litja.ru», подвергается всем лабораторным исследованиям, по завершению которых получает сертификат по стандартам и правилам ГОСТ.
Все работы по литью ХТС металла совершаются только профессионалами и людьми с высшим образованием. Каждая готовая продукция имеет все необходимые характеристики:
- химические,
- технологические,
- а также изготовлена из сырья высшего сорта и подобрана соответственно назначению.
Самый удобный и малобюджетный способ литья это способ ХТС. Именно такой способ позволяет отлить металл с наименьшими отклонениями на припуски и дефектами в отливке. Так как формы ХТС состоят из прочных материалов, за счет чего мы добиваемся гладкости поверхностей, которые не подвергаются дополнительной работе с механикой.
Подтверждает это 9 класс по ГОСТ 26645-85 размерной точности.
Чтобы убедится в наших словах, вы можете обратить внимание на снабжение цехов специальным оборудованием. В нашем заводе имеется самое лучшее и новое оборудование, которое ранее не применялось. Имя ему OMEGA и EGES. Новые технологии перевели наше производство на новый уровень.
В оборудование такого типа входят:
- индукционный комплекс для плавления, который может вести выработку жидкого метала 2 тонны в час,
- сюда же встроена система с замкнутым циклом для оборотного водоснабжения и охлаждения,
- специальная установка, которая автоматически готовит смесь для ХТС из песка, смолы и затвердителя, полностью компьютеризированная,
- система возобновления и добычи песка из ХТС, а также установка для охлаждения песка перед применением, вибродробилка, которая работает с уже отслужившей готовой смесью,
- система пневматического транспорта, которая поставляет песок в расходный бункер и на места формовок, также мы имеем рольганг – он доставляет опоку к местам заливок, формовок и выбивки,
- еще одна компрессорная установка и специальная система уборки пыли.
Благодаря использованию таких мощностей, «Zavod-Litja.ru» производит за сутки до двадцати тонн литья из меди на заказ в Москве. При таком наборе агрегатов мы используем метод ХТС, не боясь за окружающую среду, так как он абсолютно экологически безопасен. Не смотря на полную автоматику и компьютеризацию, ХТС довольно таки ресурсосберегающий метод.
Точность в добавлении затвердителя и смолы определяет компьютер, который исключает перерасход составляющих компонентов. Цех по литью работает с большей скоростью благодаря системе пневматического транспорта, который доставляет песок в нужное место по трубопроводу. Поэтому старый метод доставления песка по подземному тоннелю или в громоздких ленточных транспортерах не имеет смысла и полностью удален из цеха.
Пыль теперь убирается исключительно новой системой и не наносит вреда. Регенерация песка из смесей для ХТС позволяет добыть до 70%. Это значительно снижает затраты и защищает природу. Автоматически мы управляем всеми системами:
- охлаждение,
- пневмотранспорт,
- формовка и так далее.
Мы работаем с лучшим оборудованием и доставляем готовые заказы наших клиентов по адресам Российской Федерации и СНГ.
На нашем оборудовании, в цехах для литья, мы работаем с бронзовыми, алюминиевыми и чугунными отливками. Мы льем металл как в стандартные размеры кома 800х1000х300 мм, так и в жакеты, масштабом 2000х2000х450 мм для ручного формования.
zavod-litja.ru
Производство отливок методом ХТС на формовочной каруселе производства компании Omega (Великобритания)
Минимальный состав оборудования для производства литья в химически твердеющие смеси (ХТС) включает: смеситель непрерывного действия, вибростол и кантователь. Для серийного производства отливок или производства отливок широкой номенклатуры целесообразно иметь автоматическую формовочную линию. OMEGA FOUNDRY MACHINERY LTD (Великобритания) для этих целей производит автоматические формовочные линии двух типов: формовочная карусель и система «Fast-Loop». Пару дней назад на данном сайте был представлен интересный фильм отображающий работу линии «Fast-Loop». Сегодня будет представлен короткий фильм о функционировании формовочной карусели.
Последовательность работы шестипозиционной формовочной карусели
На позиции смены оснастки происходит установка на формовочную карусель подмодельной плиты, с закреплённой на ней деревянной модельной оснасткой. Карусель делает поворот на 60° и толкатель перемещает плиту с модельной оснасткой на вибростол, где происходит заполнение формы смесью из смесителя, включается виброуплотнение, оператор счищает излишки смеси, заполненная форма возвращается на карусельную установку и карусель делает новый поворот на 60°.
Через четыре поворота заполненная форма попадает на позицию перемещения в автоматический кантователь. В течении этого времени в форме происходит процесс полимеризации и она набирает «манипуляторную прочность», позволяющую производить дальнейшие операции с формой. В кантователе происходит кантовка модельной оснастки, извлечение кома смеси из оснастки, передача кома на ленточный конвейер для дальнейшей работы с ним. Плита с модельной оснасткой возвращается на карусельную установку. На позиции смены оснастки она либо заменяется на другую оснастку, либо продолжает повторно использоваться.
Карусельная установка является компактным и экономичным решением для изготовления форм с размерами до 1600х1200х475 мм. Карусель можно использовать как отдельно стоящую установку, так и встраивать в полностью автоматизированную формовочную линию.
На шестипозиционной каруселе можно организовать изготовление трёх комплектов разных или одинаковых форм, используя шесть модельных оснасток. Если принять, для примера, период достижения «манипуляторной прочности» — 12 минут, то производительность формовочной карусели будет составлять 20 полуформ (или 10 форм) в час. Если же габариты изготавливаемых форм позволяют разместить их на подмодельную плиту попарно (форма низа и форма верха), то производительность карусельной установки вырастает в два раза.
Статьи по теме
Tags:
Литье в ХТСon-v.com.ua
Литье в формы ХТС – ООО ЗМИ-УРАЛ
Тем, кто эксплуатирует различные механизмы, приходится иногда сталкиваться с необходимостью наплавить металл в том или ином месте детали. Разбитое крепежное отверстие, истертая в процессе эксплуатации поверхность, выкрошенная кромка металлорежущего инструмента, изношенная втулка подшипника. Во всех этих случаях можно обойтись без замены детали, восстановив ее способом наплавки металла на изношенную часть. Наплавка на деталь металла позволяет не только восстановить первоначальные свойства изделия, но и придать ему совершенно новые ценные качества. В частности, наплавив на основание из низкоуглеродистой стали слой твердосплавного металла, можно получить износостойкий рабочий орган или режущий инструмент.
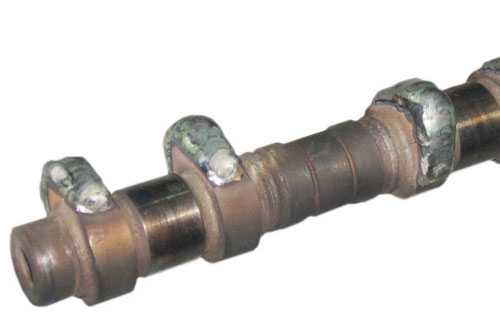
Наплавленные кулачки
Наплавкой называется процесс нанесения одного расплавленного металла (называемого присадочным) на поверхность другого (называемого основным). При этом основной металл также расплавляется на небольшую глубину для образования гомогенного соединения. Цель наплавки может быть различной: восстановление утраченной геометрии детали или придание ей новой формы, образование поверхностного слоя с заданными физико-механическими свойствами (такими как повышенная твердость, износостойкость, антифрикционность, коррозионная стойкость, жаростойкость и пр.), упрочнение наплавкой.
Наплавку можно производить на любые поверхности – плоские, конические, цилиндрические, сферические. В больших пределах может меняться и ее толщина – от нескольких долей миллиметра до сантиметра и более.
Основные принципы наплавки
В основных своих моментах технология наплавки сходна с технологией сварки. Перед ней стоят те же задачи, что и перед сваркой – защита наплавляемого металла от газов, содержащихся в воздухе, получение плотного, без пор, трещин и посторонних включений металла шва. При наплавке следует соблюдать основные принципы, заключающиеся в ряде требований:
- Необходимо стремиться к минимальному проплавлению основного металла. Это достигается путем наклона электрода в сторону, обратную ходу наплавки.
- Должно быть как можно меньшее перемешивание наплавленного металла с основным.
- Нужно стараться достичь минимальных остаточных напряжений и деформаций в детали. Это требование во многом обеспечивается соблюдением двух предшествующих.
- Необходимо снижать до приемлемых значений припуски на последующую обработку детали. Говоря другими словами, нужно наплавлять металла ровно столько, сколько необходимо, и не больше.
Применяются различные способы наплавки металла – электродуговая, газовая, электрошлаковая, индукционная, плазменная, импульсно-дуговая, вибродуговая, порошковая наплавки. Наибольшее распространение получила дуговая наплавка.
Материалы для наплавки существуют в различных формах. Это могут быть присадочные прутки, порошкообразные смеси, наплавочные покрытые электроды, порошковая и цельностержневая проволока. В электродуговой наплавке применяются в основном покрытые электроды, присадочные прутки и проволока.
Наплавка покрытыми электродами
Наплавка покрытыми наплавочными электродами относится к основным способам, применяемым как в промышленности, так и в быту, в силу ее простоты, удобства, отсутствия необходимости в специальном оборудовании. Выпускается большое количество марок электродов, создающих наплавочный слой с различными характеристиками, обеспечивающими требуемые качества изделий для работы в тех или иных условиях.
Наплавка требует определенных навыков в работе. Надо при минимальном токе и напряжении, чтобы не увеличивать долю основного металла в наплавленном, оплавить оба компонента. Состав металла будет определять тип электрода, а толщину и форму – диаметр электрода. Напряжение дуги определяет форму наплавленного валика, при его повышении увеличивается ширина и уменьшается высота валика, возрастает длина дуги и окисляемость легирующих примесей, особенно углерода. В связи с этим стремятся к минимальному напряжению, которое должно согласовываться с током дуги.
Наплавка деталей из стали осуществляется, как правило, постоянным током обратной полярности (на электроде “плюс”) в нижнем положении.
Прямая (слева) и обратная (справа) полярности подключения электрода
Детали из низкоуглеродистых и низколегированных сталей наплавляют обычно без предварительно нагрева. Но нередко требуется предварительный подогрев и последующая термообработка с целью снятия внутренних напряжений. Более детальные требования к наплавке сообщаются в документации на применяемые наплавочные электроды. Например, для электрода ОЗИ-3 приводятся следующие технологические особенности: “Наплавку производят в один-четыре слоя с предварительным подогревом до температуры 300-600°С. После наплавки рекомендуется медленное охлаждение. Возможна наплавка ванным способом на повышенных режимах. Прокалка перед наплавкой: 350°С, 1 ч.”
Поверхность детали перед наплавкой очищается от масла, ржавчины и других загрязнений.
Применяются различные схемы расположения наплавочных швов. В случае плоских поверхностей различают два основных вида наплавки – использование узких валиков с перекрытием друг друга на 0,3-0,4 их ширины, и широких, полученных увеличенными поперечными движениями электрода относительно направления прохода.
Наплавка металла узкими валиками
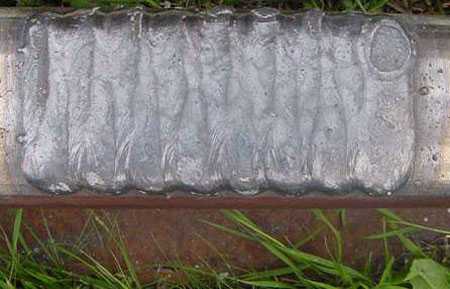
Наплавка металла широкими поперечными движениями электрода
Другой способ – укладка узких валиков на некотором расстоянии один от другого. При этом шлак удаляют после наложения нескольких валиков. После этого валики наплавляются и в промежутках.
Во избежание коробления деталей, наплавление рекомендуется проводить отдельными участками, “вразброс”, а укладку каждого последующего валика начинать с противоположной стороны по отношению к предыдущему.
Наплавка цилиндрической поверхности выполняется тремя способами – валиками вдоль образующей цилиндра, валиками по замкнутым окружностям и по винтовой линии. Последний вариант (по винтовой линии) является особенно удобным в случае механизированной наплавки, при которой детали в процессе наплавки придается равномерное вращение.
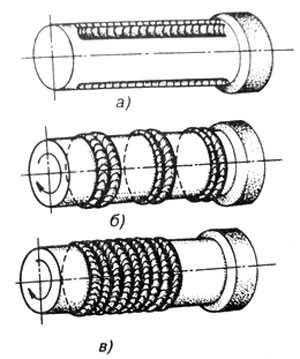
Наплавка металла на цилиндр
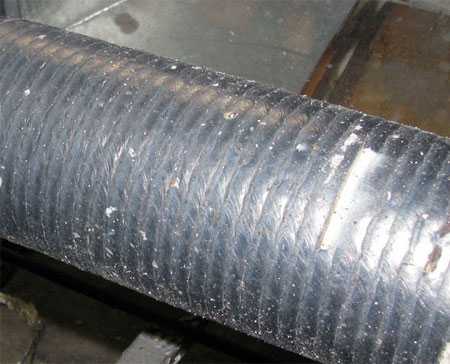
Цилиндр с наплавленным металлом
Для восстановления и повышения срока службы режущего, штампового и измерительного инструмента, а также деталей механизмов, работающих при интенсивном износе, применяется наплавка рабочих поверхностей твердыми сплавами, представляющими собой соединения таких металлов, как титан, вольфрам, тантал, марганец, хром и других с бором, углеродом, кобальтом, железом, никелем и пр.
При изготовлении новых инструментов и деталей с твердосплавной наплавкой, в качестве заготовок (оснований) применяются детали из углеродистых или легированных сталей. В случае ремонта деталей с большим износом, перед наплавкой твердыми сплавами делают предварительную наплавку электродами из малоуглеродистой стали.
Для получения более качественной наплавки, предупреждения образования трещин и снижения напряжений, во многих случаях целесообразен подогрев заготовок до температуры 300°C и выше.
Наплавка металлорежущего инструмента и штампов. Металлорежущие инструменты и штампы, работающие при холодной и горячей штамповке, наплавляют электродами ОЗИ-3, ОЗИ-5, ОЗИ-6, ЦС-1, ЦИ-1М и прочие марки. Металл, наплавленный этими электродами, обладает высокой сопротивляемостью к истиранию и смятию при больших удельных нагрузках и высоких температурах – до 650-850°C. Твердость наплавленного слоя без термообработки составляет от 52 HRC (ОЗИ-5) до 61 HRC (ОЗИ-3). Наплавляется 1-3 слоя общей толщиной 2-6 мм. Деталь перед наплавкой подогревают до температуры 300-700°С (в зависимости от марки электрода).
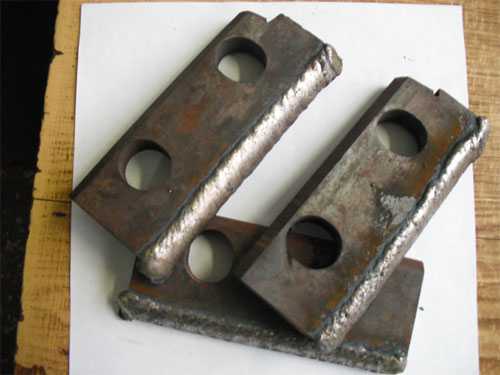
Наплавка ножей
Наплавка деталей, работающих на истирание без ударных нагрузок. Если требуется получить наплавленный металл особо высокой твердости, можно использовать электроды для наплавки Т-590 и Т-620. Они специально предназначены для покрытия деталей, работающих на интенсивное истирание. Их стержень изготовлен из малоуглеродистой стали, зато в покрытия входят феррохром, ферротитан, ферробор, карбид бора и графит. Благодаря этим материалам твердость наплавленного металла может достигать 62-64 единиц по HRC.
Из-за того, что наплавленный металл обладает хрупкостью и склонностью к образованию трещин, изделия, наплавленные электродами Т-590 и Т-620, не предназначены для эксплуатации в условиях значительных ударных нагрузок. Наплавка твердосплавного металла производится в один-два слоя. Если требуется наплавлять большую толщину, нижние слои наплавляются электродами из малоуглеродистой стали и лишь заключительные – твердосплавными.
Наплавка деталей, работающих на истирание с ударными нагрузками. Детали из марганцовистых сталей (110Г13Л и подобные ей), работающие в условиях интенсивного поверхностного износа и высоких ударных нагрузок (в частности, рабочие органы строительного и землеройного оборудования), наплавляют электродами ОМГ-Н, ЦНИИН-4, ОЗН-7М, ОЗН-400М, ОЗН-300М и прочие марки. При их использовании твердость наплавляемого металла во втором слое получается 45-65 HRC при высоких значениях вязкости.
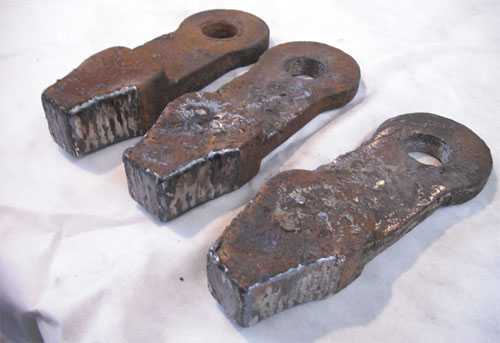
Наплавка деталей (молотков) мельницы
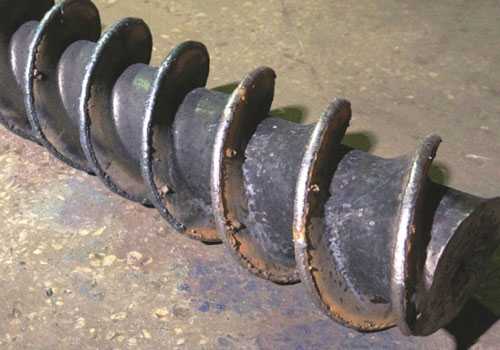
Наплавка шнека
Наплавка нержавеющих сталей. Для наплавки деталей из нержавеющих сталей применяются электроды ЦН-6Л, ЦН-12М-67 и прочие марки. Стержень этих электродов изготовлен из нержавеющей высоколегированной проволоки. Кроме высокой коррозионной стойкости, наплавленный металл имеет еще и устойчивость к задиранию, что позволяет использовать эти электроды для наплавки уплотнительных поверхностей в арматурных изделиях.
При использовании некоторых электродов для наплавки нержавеющих сталей, рекомендуется производить предварительный и сопутствующий подогрев детали до температуры 300-600°С и осуществлять после наплавки термообработку.
Наплавка меди и ее сплавов. Наплавка меди и ее сплавов (бронз) может осуществляться не только на медное или бронзовое основание, но также на сталь и чугун. В этом случае создаются биметаллические изделия, имеющие необходимые эксплуатационные качества (высокую стойкость против коррозии, низкий коэффициент трения и прочие ценные свойства, присущие меди и ее сплавам) и обладающие при этом гораздо более низкой стоимостью в сравнении с деталями, изготовленными полностью из меди или ее сплавов.
Алюминиевые бронзы, в частности, обладающие высокими антифрикционными свойствами, очень хорошо работают в узлах трения, поэтому их наплавляют на червячные колеса, сухари и другие детали, работающие в условиях трения.
Наплавка деталей из технически чистой меди может производиться электродами “Комсомолец-100” или присадочными прутками из меди или ее сплавов. При наплавке меди на медь применяют предварительный подогрев до температуры 300-500°С.
Наплавленный слой желательно подвергать проковке, при температуре меди выше 500°С.
Если требуется наплавка бронзой, можно использовать электроды ОЗБ-2М, содержащие помимо, составляющей основу, меди также олово, марганец, никель и железо. Изделия, наплавленные электродами ОЗБ-2М, имеют высокую поверхностную износостойкость.
Наплавка меди и ее сплавов производится постоянным током обратной полярности в нижнем положении.
Наплавка в среде защитных газов
Наряду с наплавкой покрытыми электродами, в домашних условиях можно осуществлять и наплавку в среде защитных газов – методом MIG/MAG (с автоматизированной подачей проволоки) или TIG (вольфрамовым электродом) с присадочными прутками. Для защиты можно применять различные газы: аргон, углекислый газ, гелий, азот – в зависимости от того, какой наплавляется металл.
При восстановлении наплавкой деталей из углеродистых сталей можно использовать более дешевый углекислый газ. Учитывая тот факт, что CO2 окисляет расплавленный металл, наплавочная проволока в этом случае должна иметь раскислители (марганец, кремний и пр.).
Наплавку меди и ее сплавов можно производить в азоте, который нейтрален по отношению к меди.
Высоколегированные стали, сплавы на магниевой и алюминиевой основе наплавляются в аргоне, гелии или их смеси.
Наплавку неплавящимся вольфрамовым электродом осуществляют в аргоне и гелии. Вообще, инертные газы, особенно, аргон, являются универсальными, подходящими для сварки и наплавки практически любого металла.
В качестве материалов для наплавки полуавтоматами углеродистых и низколегированных сталей применяются сварочные проволоки сплошного сечения (Св-08ГС, Св-08Г2С, Св-12ГС), и специальные наплавочные (Нп-40, Нп-50, Нп-30ХГСА). Для наплавки нержавейки применяют проволоку из нержавеющей стали. Может осуществляться наплавка и порошковой проволокой, позволяющей получить наплавленный слой с особыми свойствами.
При восстановлении деталей наплавкой методом MIG/MAG применяют как и в случае MMA постоянный ток обратной полярности, обеспечивающий меньшее проплавление основного металла. При использовании вольфрамового электрода (метод TIG) используют прямую полярность, исключающую оплавление вольфрамового электрода. Наплавку нужно стараться вести как можно более короткой дугой – во избежание разбрызгивания металла.
Источник: http://tool-land.ru/
zmi-ural.ru
Технология литья в песчаные формы
Определения литья в землю
Определим, какими терминами называют литейную технологию заливки металла в формы на основе песка
. Аналогичными считаются формулировки:
– Литье в песчаные формы, смеси;
– Литье в песчано-глинистые формы, смеси;
– Литье в землю.
Все эти термины обозначают одну и туже технологию литья. Применение далее любого из названий, будем считать аналогами.
Литейная продукция
Литье в песчаные формы – метод литья металлов и сплавов, при котором расплавленный металл заливается в форму сделанную из плотно утрамбованного песка. Для связи песчинок между собой, песок смешивают с глиной, водой и другими связующими материалами.
Более 70% всех металлических отливок производится с помощью процесса литья в песчаные формы.
Основные этапы
Есть шесть шагов в этом процессе:
Поместить модель в опоку с песком, чтобы создать форму.
-В необходимых местах присоединяются литниковая система и выпоры.
-Удалить из опоки модель и соединить полуформы.
-Заполнить полость формы расплавленным металлом.
-Выдержать застывающий металл в опоках согласно технологии.
-Выбить отливку и освободить от литников и выпоров.
Литейные модели
По чертежам и литейным технологиям, разработанных технологом или конструктором, опытный модельщик изготавливает модель детали из дерева, металла или пластмассы или пенополистирола.
Металл в процессе охлаждения даёт усадку, и кристаллизация может быть неоднородной из-за неравномерного охлаждения. Таким образом, модель должна быть чуть больше, чем готовая отливка, с применением, так называемого, коэффициента усадки металла. Различные усадочные коэффициенты используются для различных металлов. Модели в процессе формовки оставляют в песке полости-отпечатки в форме, в которые помещают стержень из песка. Такие стержни иногда усиливается проволочной арматурой, которые используются для создания полостей, которые не могут быть сформированы основной моделью, например, внутренние проходы клапанов или места охлаждения в блоках двигателей.
Литниковая система для входа металла в полости формы представляют собой направляющую и включает воронку, литники, которые поддерживают хороший напор жидкого металла, для более равномерного заполнения полости формы. Газ и пар, образующихся при литье выходят через проницаемые пески или через стояки, которые изготавливаются либо в самой модели, или в виде отдельных частей.
Опоки для формовочных материалов
Для формовки используют две или несколько опок. Опоки изготавливаются в виде ящиков, которые могут быть соединены друг с другом и скреплены между собой. Модель утапливается в нижней части опоки вплоть до её самого широкого поперечного сечения. Затем монтируется верхняя часть модели. К нижней части опоки зажимами прикрепляется верхняя и туда добавляется и утрамбовывается формовочная смесь таким образом чтобы она полностью закрывала модель. В необходимых местах устанавливаются литники и выпора. Затем опока половинится и из неё вынимается модель, деревянные литники и выпора.
Охлаждение металла
Для управления кристаллизацией структуры металла, в форму можно поставить металлические пластины, холодильники. Соответственно быстрое локальное охлаждения образует более детальную структуру металла в этих местах. В черной отливке эффект аналогичен закалке металла в кузнице. В других металлах, холодильники могут быть использованы для управления направленной кристаллизации отливки. При управлении способом охлаждения литья можно предотвратить внутренние пустоты или пористость внутри литья.
Производство
Для получения полостей в отливке, например, для охлаждающей жидкости в блоке двигателя и головок цилиндров используются стержни. Обычно стержни для литья ставятся в форму после удаления модели. После сушки опоку с формой устанавливают на литейный плац для заполнения расплавленным металлом, обычно сталь, бронза, латунь, алюминий, магний и цинк. После заполнения жидким металлом опоки не трогают до охлаждения отливки. После выбивки отливки, стержни удаляются из литья. Металл литников и прибылей любым способом должен быть отделен от отливки. Различные термические обработки могут быть использованы для снятия напряжений от первоначального охлаждения и добавить твёрдости в случае закалки в воде или масле. Поверхность литья может быть дополнительно упрочена дробеструйной обработкой, которая добавляет устойчивости к растрескиванию, растягивает и разглаживает шероховатую поверхность.
Разработка технологии
Чтобы было возможным удалить модель не нарушая целостности формовочной смеси все части модели должны быть предварительно рассчитаны технологом и иметь знаковые части для установки стержней. Небольшой уклон должен использоваться на поверхностях, перпендикулярных линии разъема, для того, чтобы была возможность удалить модель из формы. Это требование также распространяется на стержни, так как они должны быть удалены из полостей, которые они образуют. Выпора и стояки должны быть расположены так, чтобы обеспечить оптимальный поток металла в форму и газов из неё для того, чтобы избежать недолива литья.
Способы литья в землю
Различают два способа литья в песчаные формы, первый с использованием «сырого» песка, так называемые сырые формы, а второй метод – жидкостекольный.
Сырые формы
Мокрый песок, используются, чтобы сделать форму в опоке. Название произошло от того, что мокрым песком пользуются в процессе формования. “Сырой песок” – это смесь:
-кремнеземистый песок (SiO2), или хромистые пески (FeCr2O), или циркониевый песок (ZrSiO4), от 75 до 85%, и другие составляющие, включая графит, глину от 5 до 11%, воды от 2 до 4%, других неорганических элементов от 3 до 5%, антрацит до 1%.
Есть много формовочных смесей с глиной, но все они различны по пластичным свойствам смеси, качеству поверхности, а также возможностью применения в литье расплавленного металла в отношении пропускной способности для выхода газов. Графит, как правило, содержится в соотношении не более 5%, он частично сгорает при соприкосновении с расплавленным металлом с образованием и выделением органических газов. Сырые смеси как правило для литья цветных металлов не используются, так как сырые формы приводят к сильному окислению, особенно медного и бронзового литья. Сырые песчаные формы для литья алюминия не используют. Для алюминиевого литья используют более качественные формовочные смеси. Выбор песка для формовки зависит от температуры заливки металла. Температура заливки меди, стали и чугуна выше других металлов, поэтому, глина от воздействия высокой температуры далее не регенерируется. Для заливки чугуна и стали на основе железа как правило, работают с кварцевым песком – он относительно недорог по сравнению с другими песками. Так как глина выгорает, в новую порцию песчаной смеси добавляют новую порцию глины и некоторую часть старого песка. Кремний является нежелательным в песке, т.к. зерна кварцевого песка имеют тенденцию взрываться при воздействии высокой температуры во время заливки формы. Эти частицы находятся во взвешенном состоянии в воздухе, что может привести к силикозу у рабочих. В литейном цехе имеется активная вентиляция для сбора пыли. Мелкие древесные опилки (древесная мука) добавляется, чтобы создать место, при ее выгорании, для зерен песка, когда они расширяются без деформации формы.
Технология ЖСС (жидко-стекольная смесь)
Эта технология состоит в следующем:
в состав формовочной смеси входит прокаленный песок без глины, затем его в специальной емкости перемешивают с жидким стеклом и перемешанной массой заливают модель. Залитую форму накалывают для последующего подвода углекислоты. Опоку накрывают колпаком и подают газ СО2. После чего залитый формовочный состав ЖСС приобретает твердость.
В обоих методах, песчаная смесь остается вокруг модельной оснастки, образуя полости формы для заливки металла. Формовка жидкостекольными смесями позволяет получить две полуформы, которые после затвердевания собирают. Модель удаляется, образуя полость формы. Эту полость заливают жидким металлом. После того, как металл остыл отливки очищают от формовочного состава. Форма из ЖСС полностью разрушается при извлечении отливки.
Точность литья напрямую связана с типом формовочной смеси и формовки. Сырые формы создают на поверхности отливки повышенную шероховатость. Поэтому литье в землю можно сразу отличить от литья по ЖСС и ХТС. Литье в формы из мелкого песка значительно чище и менее шероховато. Технология ЖСС позволяет изготавливать отливки с гладкой поверхности, особенно при использовании пластиковых моделей. В отдельных случаях, например при литье корпусных деталей, можно обойтись даже без механической обработки на больших поверхностях – это позволяет отливать крупногабаритные чугунные блоки цилиндров. Остатки пригоревшей к отливке формовочной смеси удаляются дробеструйной обработкой.
С 1950 года, частично автоматизированные литейные процессы литья были переработаны для полностью автоматизированных производственных линий.
Холодно твердеющая смесь (литье в ХТС)
Использование органических и неорганических связующих, которые укрепляют формы для литья химически связывают песок. Этот тип формовки получил свое название от того, что он не требует просушки, как другие виды песчаной формовки. Литье в ХТС является более точным, чем литье в землю. Размеры форм ХТС меньше, чем при литье в песчаные смеси, но дороже. Таким образом, ХТС используется реже, в тех случаях, когда требуется более качественное литье. Наше предприятие готово поставлять вам отливки по ХТС.
Формовка ХТС
Формы из холодно твердеющей смеси, требуют быстрой формовки, в отличие от песчано-глинистых смесей, т.к. они содержат быстро твердеющие жидкие смолы, ускорители затвердевания и катализаторы. Вместо трамбовки смеси (как при литье в землю), формовочную смесь ХТС заливают в опоку и дожидаются, когда смола затвердеет. Обычно затвердевание происходит при комнатной температуре в течение 20 минут. Литье в ХТС значительно улучшает качество необработанных поверхностей стальной отливки по сравнению с другими технологиями литья в песчаных формах. Обычно для изготовления модельной оснастки по ХТС используют дерево, металл или пластик МДФ. Чаще других формовка холодно твердеющими смесями применяется при литье меди, литье алюминия, углеродистой стали, жаропрочной и нержавеющей стали, а также легированного чугуна, так как значительно снижает вероятность образования литейного брака.
aitcom.ru
Точное литьё (ХТС)
“КАЧЕСТВО ДЛЯ СОЗИДАНИЯ”
ХОЛОДНОТВЕРДЕЮЩИЕ СМЕСИ, ХТС – смеси, отверждающиеся без нагрева при выдержке на воздухе или путем обработки внешними газообразными реагентами. К ХТС относятся смеси с цементным, гипсовым, фосфатным, жидкостекольным (CO2-процесс), этилсиликатными связующими. Наибольшее практическое применение получили ХТС с синтетическими смолами. ХТС состоит из огнеупорного наполнителя, связующего, отвердителя или катализатора, регуляторов скорости отверждения и добавок для улучшения технологических свойств ХТС (например, для улучшения выбиваемости).
Такие смеси имеют низкую сырую прочность; уплотняют их вибрацией или легким встряхиванием. Продолжительность отверждения смеси в форме от 10-30 с до десятков мин. Формы и стержни извлекаются до окончательного упрочнения по достижению ими манипуляторной прочности. Достоинство способа — самоупрочнение в оснастке, что обеспечивает получение форм и стержней высокого качества без расхода внешних энергоресурсов.
Наша компания производит литье на заказ по технологии ХТС (холоднотвердеющая смесь) – AlphaSet (альфасет) процесс.
Этот процесс позволяет получить хорошее качество поверхности отливки, её хорошие металлургические качества, а также высокую эффективность процеса изготовления форм и стержней, более экологичным воздействием при формовке, заливке и выбивке. По своим свойствам альфа-сет удовлетворяет всем требованиям, предъявляемым к современным литейным связующим.
В производстве литья используется серый чугун марок СЧ10, СЧ20, ЧХ16, ЧХ32 и др.
Для контроля качества чугуна используется эмиссионный спектрометр, который позволяет оперативно произвести анализ химического состава сталей и сплавов чугуна, по более чем 20-ти элементам (включая углерод, серу и фосфор). Также используется методика механических испытаний таким оборудованием как: разрывная машина, машины на твердость по Бринеллю и на твердость по Роквеллу.
Осуществляя литье по технологии ХТС на заказ, мы подходим индивидуально к потребностям каждого клиента. Ассортимент изготавливаемой продукции очень широк и включает в себя изделия разных модификаций и уровней сложности, вплоть до изделий нестандартного размера и изделий по чертежам заказчика, художественное литье.
Заказать
dpk40.ru
Литье в формы ХТС – ООО ЗМИ-УРАЛ
Литье в формы ХТС – технологичный способ изготовления отливки с повышенным качеством поверхности и точностью размеров, что позволяет назначать минимальные припуски на механическую обработку.
Технология литья в ХТС позволяет обеспечить высокое качество поверхности литья, отсутствие газовых дефектов и засоров в отливке. Размерная точность увеличена до 9 класса (ГОСТ 7293-85).
Особенно эффективно изготовление отливок для получения фасонных изделий сложной конфигурации, которые невозможно или экономически нецелесообразно изготавливать другими методами обработки металлов(давлением, сваркой, резанием),а также для получения изделий из малопластичных металлов и сплавов.
Конкурентные преимущества метода литья по в ХТС:
Точность:
- 9 класс точности по ГОСТ 266454-85
- Снижение расхода металла и объема механообработки
- Высокая точность стержней и форм
- Высокая чистота поверхности и отсутствие пригара
Поверхность:
- Отсутствие наплывов и отклонений от линейных размеров
- Чистовые поверхности без обработки
- Минимальные припуски на обрабатываемые поверхности
Смесь:
- Приготовление смеси и подача ее в опоки (стержневые ящики) совмещены в одном агрегате – смесителе.
Формовка:
- Уплотнение формовочной смеси с помощью вибростола, что обеспечивает равномерную плотность формы
- < Назад
- Вперёд >
zmi-ural.ru