Материал для изготовления крепежа – Материалы крепежных деталей
alexxlab | 22.11.2019 | 0 | Вопросы и ответы
Виды и характеристики крепежных изделий
При выполнении широкого ряда ремонтно-строительных работ, невозможно обойтись без применения различных крепежных элементов. На современном строительном рынке представлен широкий ассортимент данных изделий, которые необходимы для качественного решения различных технических и технологических задач. Их функциональное назначение может быть совершенно разным – начиная от фиксации доски при помощи простого гвоздя, и заканчивая монтажом анкера, который должен выдерживать повышенные эксплуатационные нагрузки.
В данном материале будут рассмотрены основные виды крепежных изделий, различные классификации, ГОСТы, маркировки и области их применения. Они представлены в широком многообразии форм, размеров и назначения – наиболее часто встречающимися на сегодняшний день являются:
- гайки;
- дюбели;
- анкеры;
- шурупы;
- саморезы;
- заклепки;
- шпильки;
- шайбы и другие.
В зависимости от резьбового шага, крепежные элементы бывают метрическими или неметрическими (приспособленными).
Кроме того, существует и другая классификация крепежных изделий – она основана на иных критериях. Согласно ей, данные элементы бывают:
- резьбовыми , повышенной прочности;
- крепежи массового использования;
- крепежи для безударной фиксации и одностороннего монтажа;
- элементы для герметичных конструкций;
- фиксаторы, необходимые для крепления полимерных композитных материалов.
Данная классификация, хоть и существенно упрощает процесс сортировки, но является условной, так как элементы одной группы могут относиться и к другой. Рассмотрим более подробно основные из них.
Гвозди
Пожалуй, сегодня нет мастера, который бы не использовал в процессе своей работы гвозди. Это наиболее древний и распространенный на сегодняшний день крепежный материал, который широко используется во многих отраслях хозяйственной деятельности человека. Материал их производства – как правило, сталь или стальные виды проволоки. Маркировка гвоздей состоит из двух цифр:
- диаметр стержня;
- его длина (в мм).
Шляпки данных элементов могут быть как гладкими, так и рифлеными, а винтовые и трефовые гвозди могут иметь на стержне винтообразные, продольные и поперечные бороздки, заусеницы или вмятины. Такие изделия оказывают существенное сопротивление процессам выдергивания.
В зависимости от технических характеристик материала, различается и сфера использования гвоздей. Например, изделия из закаленной стали могут спокойно быть забитыми в стены из кирпича или бетона. Однако, при работе с ними, следует обратить внимание на высокую хрупкость данного материала. Для того, чтобы их крепить к жестким поверхностям, необходимо использовать обойные, толевые и штукатурные разновидности гвоздей. Они производятся с более плоскими и широкими, чем обычно, шляпками, а также с более короткими стержнями. В условиях агрессивной среды могут быть использованы медные гвозди, которые практически не подвержены коррозионным процессам, а также оцинкованные гвозди или изделия из легированной стали.
Что касается технологических особенностей забивания гвоздей, то они также имеют свою специфику. Данные процессы требуют учета определенных нюансов, поэтому рекомендуем воспользоваться нашими профессиональными советами:
- для предотвращения возникновения вмятин во время вбивания гвоздей, необходимо применять зенкер;
- для обеспечения прочности фиксации, стержень крепежа должен минимум на 2/3 длины входить в нижнюю фиксируемую деталь;
- при забивании мелких гвоздей, лучше всего применять специальные вспомогательные аксессуары;
- чтобы увеличить прочность стыков, гвозди должны забиваться под углом, а не прямо. Это же касается случаев, если на него требуется что-то вешать;
- если гвоздь при забивании прошел сквозь стену, он должен быть аккуратно загнутым и отшлифован с помощью трехгранного напильника;
- для предотвращения повреждения поверхностей при выдергивании клещами, нужно под них просто поместить пластину, которая уменьшает показатели давления;
- если же в дальнейшем планируется демонтаж деталей, то лучше гвозди не использовать вообще, отдав предпочтение шурупам.
Очень часто в процессе работы могут быть использованы жидкие гвозди. Они изготавливаются из полимерных материалов и каучука и способны обеспечить должные показатели прочности крепежа не хуже традиционных гвоздей. Одна капля такого вещества способна выдержать до 50 кг нагрузки, однако главным их преимуществом является полное сохранение целостности декоративных поверхностей.
Сфера использования жидких гвоздей очень широкая. Они применяются для фиксации различных панелей, гипсокартона, ДСП, ДВП, фанеры, картона, керамики, камня, лепнины, стекла и много чего другого. Однако при выборе данных крепежных элементов необходимо повышенное внимание уделить показателям адгезии, так как разные виды материала имеют различную ее степень. Их наиболее целесообразно использовать при:
- температуре не ниже -90 С;
- высокой влажности помещений.
Например, некоторые виды нейтральных гвоздей являются безвредными, так как их основой является вода, однако они мало подходят для приклеивания металла. Жидкие гвозди на основе органических растворителей отличаются высокой скоростью схватывания и способны выдерживать воздействие температурного режима до -25 С. Единственный их минус – наличие вредных летучих компонентов, которые издают неприятные запахи на протяжении 5 суток.
Схватывание таких гвоздей происходит в течении 10-40 минут, в зависимости от типа и маркировки, однако полная полимеризация наступает только по истечению суток.
Саморезы
Особую нишу среди крепежных элементов также занимают саморезы. Их разновидностей на современном рынке не так уж и много – полноценная классификация возможна только по 3 основным критериям – материалу, в который они вкручиваются, размеру и функциональному назначению. По первому критерию различают такие виды саморезов:
- для металла;
- для древесины.
И те, и другие изделия могут иметь разную длину, ширину, диаметр, а также разные шаги резьбы. Обычно саморезы для металлических поверхностей имеют мелкий шаг резьбы, в отличие от «деревянных», которые обладают более крупным.
Изделия для металла могут быть нескольких видов – самонарезающиеся и те, которым необходимо предварительное сверление металла. У первого типа на кончике имеется специальное сверло, размер которого означает толщину металла, в который требуется его ввинтить. Примером таких саморезов являются тексы, которые используются для фиксации профилей ГКЛ. Что касается их второй подгруппы, то к ней можно отнести черные саморезы, которые необходимы для крепления ГКЛ к металлопрофилю.
Кроме этого, классификация саморезов может быть осуществлена также и по функциональному назначению. Например, выделяют саморезы для кровли и общего назначения. Кровельные обладают широкой шляпкой с пресс-шайбой, которая необходима для герметизации отверстия с целью предотвращения протекания воды.
Анкеры: виды и особенности применения
Анкер представляет собой крепежный элемент, который предназначен для фиксации различных конструкций и материалов. Кроме того, данным названием характеризуют детали, частично забетонированные в любое изделие из бетона. В зависимости от конструкции, формы и назначения, различают такие виды анкеров:
- потолочные;
- забивные;
- клиновые;
- рамные;
- анкеры с полукольцами и кольцами;
- анкеры с гайками.
Их объединяет общая функция – крепежная. Например, забивные анкеры с внутренним типом резьбы и конусообразным клином необходимы для того, чтобы фиксировать различные изделия и материалы к кирпичному или бетонному основанию. Устанавливается он довольно просто: он фиксация осуществляется в заранее изготовленное отверстие. Его радиус и глубина подбираются, в зависимости от размеров самих анкеров.
Клиновидные изделия используются для оперативного крепления в бетонах планок, профилей, подвесных потолков. Такие виды анкеров очень часто используют для фиксации тяжелого оборудования в твердом основании. Для качественного монтажа клиновых анкеров, в бетонном основании просверливается отверстие, в которое с помощью молотка забивается изделие, впоследствии затягиваемое гайками. Что касается потолочных анкеров, то они могут изготавливаться из оцинкованной стали, и необходимы для фиксации профилей из металла, фасадов, перил, решеток и прочих изделий на бетонной или каменной основе без появления трещин. Рамные же анкеры необходимы для крепления рамы и дверных деревянных коробов к бетонным стенам.
Очень много пользователей пытается использовать данный вид крепежа не по назначению. Например, их крепят к стенам из кирпича, в результате чего портится крепежный элемент и нервы. Но главное – это очень большие отверстия, которые остаются в кирпиче после выемки анкера. Они используются, как правило, в бетонных материалах, в то время как в мягких такие болты имеют свойство просто прокручиваться. Классификация анкеров – это также очень трудная задача, так как изделия могут относиться к разным группам одновременно, однако обычно выделяют три их вида:
- крепежные;
- крюкообразные;
- петлевые.
Первый тип является универсальным, второй предназначен для подвешивания предметов, а третий – для того, чтобы что-то цеплять. Кроме того, данные крепежные элементы можно разделить и такие основные группы – с клином на конце и с клином в форме гайки. Анкера изготавливаются в фиксированных типоразмерах – самые маленькие имеют длину 50 мм и диаметр 6-8 мм, в самые большие – до 500 мм и диаметром до 22 мм.
Совет: вопрос, как установить анкер, может быть решен очень просто. Для этого достаточно просто корректно подобрать диаметр отверстия – сверлить необходимо буром точно такого же размера, как сам анкер – рассчитывать что болт 12 мм будет держаться в отверстии 15 мм не приходится. Также не желательно ничего наматывать на анкера, это не имеет никакого смысла – достаточно просто его вставить в отверстие и закрутить отверткой.
Дюбели
Данные крепежные элементы также являются чрезвычайно популярными на современном строительном рынке. Они необходимы для качественного крепления различных предметов и материалов к твердым конструкциям. Различают три вида дюбелей:
- металлические – наиболее древние. Могут быть использованы практически во всех поверхностях, однако при помощи простого молотка их забить проблематично, особенно в твердые материалы – поэтому чаще применяют пневматические, электрические или патронные пистолеты. Такие дюбели отличаются друг от друга только диаметром и длиной;
- монтажные – самые распространенные на сегодняшний день. Могут быть изготовлены в двух вариациях, которые отличаются друг от друга формой пластикового наконечника. В одних случаях они монтируются в специально подготовленный потай, а в другом – нет (пробка имеет грибкообразную форму). Монтируются такие дюбели при помощи перфоратора – делается отверстие, а потом в него вставляется пластиковая пробка, в которую вбивают или вкручивают стальной гвоздь. Его при необходимости можно потом очень легко выкрутить благодаря специальной резьбе. В зависимости от диаметра, дюбели бывают 6,8 – 14 мм, а длины – 30-300 мм;
- распорные (дюбель Биербаха) – производятся из стали и демонстрируют высокие эксплуатационные характеристики для применения в бетонных основаниях. Состоят из двух клиньев, которые соединяются между собой подвижным способом при помощи шайбы. Монтируются в предварительно просверленные отверстия, в котором они потом расклиниваются одним ударным усилием молотка.
Их используют обычно для крепежа в твердых стеновых конструкциях. Фиксация дюбеля основана на силе трения, которая возникает за счет распорки крепежного элемента при монтаже с появлением удерживающего усилия. Дюбель может выдерживать повышенные нагрузки статического характера – при его установке крепежи в процессе вытягивания разрушаются.
Само изделие изготавливается из полимерных материалов. Их физические и механические характеристики способны сильно трансформироваться, в зависимости от различных воздействий и условий. К ним относятся, в первую очередь – параметры наполнителя, соотношение составляющих полимерного материала, свойства связующего вещества. К недостаткам полимерных дюбелей можно отнести малую теплостойкость, склонность к деформированию под воздействием нагрузок, а также усиленное старение. Максимальные нагрузки способны выдерживать только шурупы, если их корректно подобрать под дюбель. Они должны иметь все параметры (длину и диаметр), полностью соответствующие параметрам дюбелей. Применение других крепежных элементов выдвигает повышенные требования к профилю резьбы, так как именно они определяют распорный эффект. Нежелательно использование саморезов и шурупов, которыми крепится гипсокартон.
Крепление гипсокартона: молли
Для качественной фиксации листов ГКЛ существует единственная группа крепежных элементов, которая носит название «молли», полученное от фирмы, разработавшей данный крепеж. Состоит он из двух частей – пустой складывающейся трубки со специальными прорезями, гайкой и винтом. По мере закручивания винта, трубка собирается и обжимается двух сторон ГКЛ. Существует два типа молли:
- металлический;
- пластиковый.
Первый тип является самым надежным – он устанавливается с помощью специальных щипцов, а для монтажа пластиковых необходимо заранее просверлить отверстия диаметром 8 мм, вставить в них крепежи, после чего закрутить саморезы. На гипсокартон с помощью таких элементов можно повесить только легкие предметы – если необходимо фиксировать тяжелые, тогда следует предусмотреть закладные профили.
Болты
Болты представляют собой крепежные изделия цилиндрической формы, которые обладают метрической цилиндрической наружной резьбой и головкой, которая рассчитана под гайку. Они дают возможность создавать соединения при помощи гаек или заранее сделанных отверстий с резьбой в фиксируемых деталях. По форме они бывают:
- ступенчатыми, в которых диаметр резьбы меньше, чем диаметр гладкой части;
- фундаментными, обладающими головкой особой формы, которая помогает крепить оборудование и агрегаты к основанию;
- с головкой в форме шестигранника под гаечный ключ – это наиболее распространенный вариант исполнения.
Вставляется болт в заранее подготовленное отверстие деталей, которые требуется скрепить, после чего на резьбу закручивается гайка и осуществляется стягивание элементов при помощи гаечного ключа. Фиксация соединения происходит за счет силы трения – но для переноса на болт части нагрузок, необходимо обеспечить максимальную точность производства стержня и отверстий для него. Для предотвращения деформации деталей, под головку болта и под гайки устанавливают шайбы. Болты всегда используются в комплексе с гайками.
Гайки: виды и принцип работы
Гайки – это также очень популярная разновидность крепежных изделий, которая отличается специально нарезанным внутри отверстия резьбовым соединением. Наиболее широкое распространение получили оцинкованные изделия, а их форма может быть совершенно разной – шестигранник, круглая с насечками, квадратная, с выступами для захвата пальцами. Главным функциональным назначением гайки является соединение деталей с применением болтов. Они бывают:
- шестигранными;
- квадратными;
- в форме «барашек»;
- фланцевыми с пазами для шплинта в форме колпачка;
- Т-образными, со специальными вставками из пластика.
Кроме того, гайки разделяются также по категории прочности в соответствии с типами болтов, с которыми они используются.
Заклепки
Вытяжные заклепки комбинированного типа состоят из алюминиевого тела и стержня, который изготавливается из оцинкованной стали. Такая конструктивная особенность является одной из самых распространенных и востребованных на сегодняшний день. Используются заклепки для того, чтобы соединять две или несколько поверхностей из тонких листов – с их помощью создается неразъемное соединение. Также на современном рынке встречаются вытяжные гайки-заклепки. Это крепежные элементы, широко используемые в электронике и машиностроении. Они необходимы для создания соединения с резьбой в металлических материалах или других тонких поверхностей, обладающих высокой прочностью.
Среди большого выбора данной крепежной продукции одними из самых прочных являются резьбовые стальные заклепки. От воздействия коррозии они защищаются при помощи оцинковки. По конструкции, такие изделия отличаются от простых вытяжных тем, что не только могут соединять между собой листы материалов, но также и обладают внутренней винтовой резьбой. Они монтируются в труднодоступных местах, куда невозможно добраться с заклепочником. На современном рынке представлен широкий выбор типоразмеров, поэтому выбрать их для решения нужной технической задачи не составляет труда.
Применение шурупов, винтов и других крепежных элементов
Для того, чтобы винты правильно выполняли возложенные на них функции, следует корректно подбирать их типоразмеры. Шурупы являются крепежными изделиями, которые необходимы для конструкций из дерева – их стержень сужается ближе к концу и выполняет функцию сверла. Данный вид крепежа нельзя использовать как гвозди, забивая в поверхность – они должны от начала и до конца быть полностью закрученными. Перед применением небольших шурупов, следует сделать предварительный прокол, а больших – отверстие меньшего диаметра.
Винты используются для фиксации конструкций из металла. Их головки позволяют качественно прижать соединяемую деталь, а форма подбирается таким образом, чтобы максимально облегчить процесс с использованием ключа или отвертки. В зависимости от этого, головки винтов могут иметь различную форму:
- шестигранную;
- полукруглую;
- потайную.
Они всегда вкручиваются в отверстия с резьбой, а в некоторых случаях могут иметь конструкцию, в которой на конце винта высверливается отверстие для шплинтов – проволочных стержней с полукруглым сечением. Оно необходимо для того, чтобы предотвратить самопроизвольное отвинчивание крепежного элемента.
В случае, если винт заржавел, то для его извлечения может применяться ударник или специальные обжимки. Часто помочь в данном процессе может нагревание гайки при помощи газовой горелки или паяльной лампы. Если же применение открытого огня по какой-либо запрещено, тогда может быть использован раскаленный прут из железа или паяльник.
Для качественного крепежа используются также и другие изделия:
- шайбы – круглые пластины, изготавливаемые из ленты холодной прокатки. Они применяются для того, чтобы увеличить прочность болтовых соединений посредством подкладывания под головку болта или под гайку;
- шпильки – цилиндрические стержни с нарезанной наружной резьбой во всей длине или на концах. Используется в тех случаях, если больше не один материал в соединении не имеет резьбы;
- шурупы – стрежневые крепежи с коническим острием, которые обладают свойством создавать новую резьбу в пластиковых или деревянных изделиях.
На рынке строительных материалов существует очень большой выбор крепежных элементов. Их необходимо подбирать в полном соответствии с технологическими особенностями применения и техническими целями, а также условиями эксплуатации.
indostroy.ru
Виды крепежа и их применение
При проведении строительных, ремонтных и других работ, в машиностроении…, почти в любом производстве невозможно, или крайне сложно обойтись без применения различного рода крепежных изделий. Металлический крепеж — это гарантия надежного соединения отдельных деталей между собой. Самыми распространенными и востребованными крепежными изделиями по праву считаются метизы — изделия из металла.
Классификация крепежных изделий
1. Анкерный крепеж — технически сложные стальные изделия, несущие высокие нагрузки (до 5 тонн).
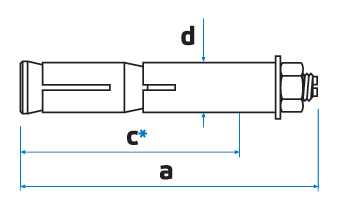
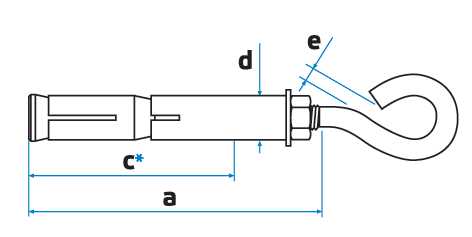
2. Шурупы и саморезы — наиболее часто востребованный и простой в исполнении вид крепежа. Имеет очень широкое распространение и применение.
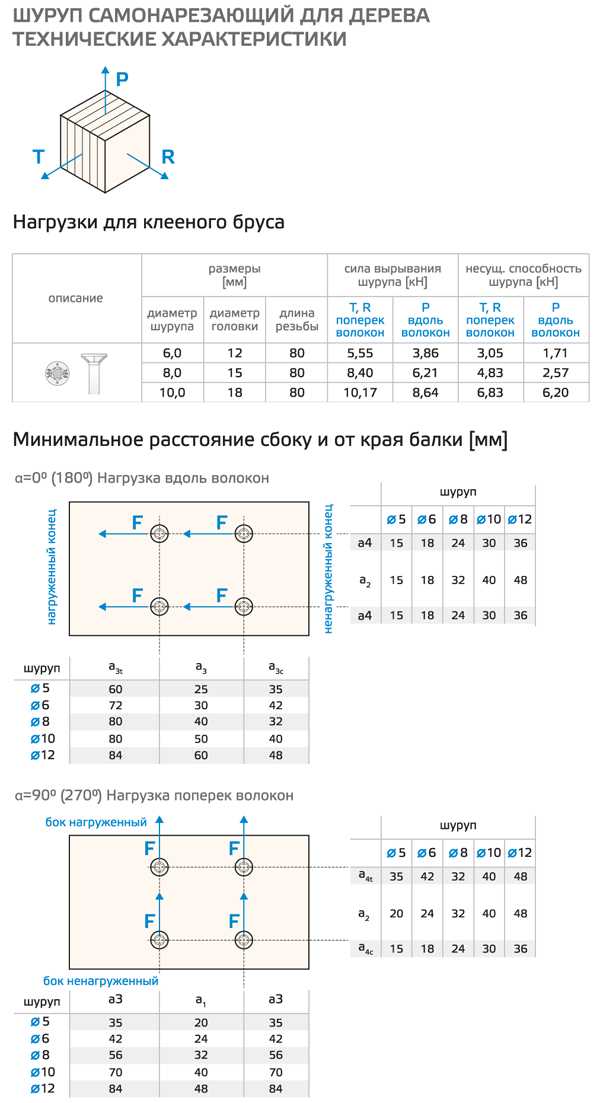
3. Метрические крепежные соединения — самый надежный и распространенный вид (гайки, болты, шайбы и т. д.)
4. Дюбеля — в основном изделия из пропилена или нейлона. Используются совместно с шурупами или саморезами.
5. Гвозди — изготавливаются из металла для крепления деталей на деревянных основаниях.
6. Перфорированные отверстиями ленты — производятся из листовой стали (уголки, перфолента…). Часто применяются при строительстве домов из дерева.
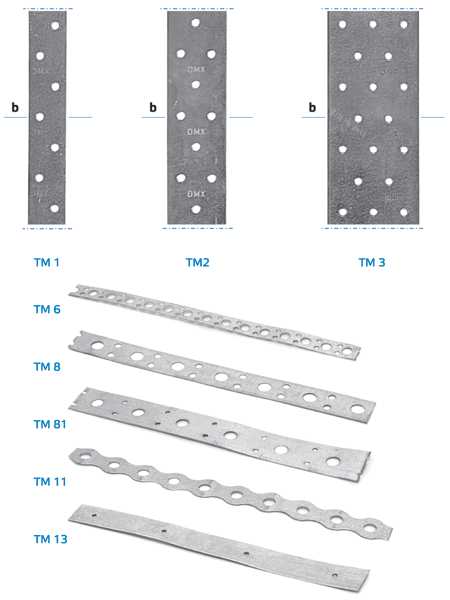
7. Такелажные крепежные изделия — служат для крепления и перемещения различных грузов (тросы, цепи, карабины…).
Анкерные крепежные изделия
Есть несколько видов анкеров:
- забивной анкер — металлическая втулка. С одной стороны резьба, другая сторона разрезана. Внутри имеется клин, который при забивании (в основном в бетон) надежно удерживает монтируемую конструкцию;
- клиновой — применяется также в бетонах и натуральных камнях. Забивается и дополнительно закручивается гаечным ключом;
- разжимной — специальный разжимной механизм раскрывается внутри основания;
- химический анкер — заранее подготовленное отверстие заполняется химическим составом и вводится крепежный стержень.
Электромонтажные крепежные изделия
Некоторые виды:
- дюбель-скоба для проводов круглых и плоских;
- стяжка кабельная;
- зажим провода универсальный;
- крепление плоского и круглого провода;
- хомуты;
- крепления для гофрированных труб, ПВХ и кабелей.
Саморезы и шурупы
Подразделяются по видам головки:
- шестигранная;
- полуцилиндрическая;
- потайная;
- полусферическая;
- с шлицем крестообразным.
По видам наконечников различаются:
- с острым концом;
- в виде сверла.
В зависимости от применения подразделяются:
- для соединения деревянных деталей;
- для соединения металлических деталей;
- кровельные.
Защита крепежных изделий гальваническим покрытием
Служит для увеличения срока службы. Антикоррозийное покрытие может быть:
- медным;
- оловянным;
- цинковым;
- никелевым;
- кадмиевым.
toolbuild.ru
Углеродистые стали, применяемые для изготовления крепежных изделий
Более 90% производства стального крепежа в мире осуществляется на основе углеродистой стали. Эта сталь обладает отличной работоспособностью, широким спектром манипулирования различными комбинациями прочностных свойств, а по сравнению с другими широко используемыми материалами, применяемыми для производства крепежа, менее дорогая.
Механические свойства крепежных изделий напрямую зависят от содержания углерода, который составляет обычно менее 1,0%. Наиболее распространенные стали для крепежа, как правило, подразделяются на три группы: низкоуглеродистая, среднеуглеродистая и легированная.
Углеродистые стали, нашедшие свое применение при изготовлении крепежных изделий, прежде всего, метрического крепежа – болтов, винтов, гаек, а также шайб, принято подразделять на три основные группы:
- низкоуглеродистые стали
- среднеуглеродистые стали
- легированные стали
Низкоуглеродистая сталь
Низкоуглеродистая сталь обычно содержит менее 0,25% углерода и не может быть усилена путем термообработки, усиление может быть достигнуто только путем холодной обработки. Низкоуглеродистая сталь является относительно мягкой и слабой, но имеет высокую пластичность и прочность, кроме того, эта сталь легко обрабатываема, свариваема и относительно недорога в производстве.
Низкоуглеродистые стали соответствуют ГОСТ 380-71. Их поставляют в виде качественного проката в нормализованном состоянии и применяют, как правило, для изготовления метизов общего назначения с пределом прочности на разрыв до 600 МПа.
Стандартизированная маркировка таких сталей имеет буквенно-цифровое написание: «Ст» и цифры от 0 до 6. Цифры — это условный номер марки. Большее число означает более высокое содержание углерода, следовательно, большую прочность и более низкую пластичность. Кроме того, для обозначения тех или иных свойств стали применяют следующие индексы (стоящие справа от цифрового обозначения):
- кп – кипящая;
- пс – полуспокойная;
- сп -спокойная сталь.
Между индексом и номером марки может стоять буква Г, это означает повышенное содержание марганца.
Среднеуглеродистая сталь (конструкционная)
Концентрация углерода в среднеуглеродистой стали составляет 0,25 – 0,85%. Эта сталь может подвергаться термообработке по аустениту, закалке и отпуску для улучшения механических свойств крепежных изделий.
Стали углеродистые качественные конструкционные соответствуют ГОСТ 1050-74. От сталей обыкновенного качества они отличаются меньшим содержанием серы, фосфора и других примесей, более узкими пределами содержания углерода в каждой марке и в большинстве случаев более высоким содержанием кремния (Si) и марганца (Мn). Эти стали нашли свое применение при изготовлении крепежных изделий (болтов, в первую очередь) с пределом прочности на разрыв свыше 600 Мпа.
Сталь маркируют двузначными числами, которые обозначают содержание углерода в сотых долях процента, и поставляют с гарантированными показателями химического состава и механических свойств. Буква Г в марках сталей указывает на повышенное содержание марганца (до 1%).
Сталь углеродистую качественную поставляют для производства метизной продукции в виде качественного сортопроката.
МЕХАНИЧЕСКИЕ СВОЙСТВА КАЧЕСТВЕННОЙ КОНСТРУКЦИОННОЙ СТАЛИ
Марка стали | Предел прочности на разрыв МПа | Относительное удлинение % | Твердость НВ |
08 | 330 | 33 | 131 |
10 | 340 | 31 | 143 |
15 | 380 | 27 | 149 |
20 | 420 | 25 | 163 |
25 | 460 | 23 | 170 |
30 | 500 | 21 | 179 |
35 | 540 | 20 | 207 |
40 | 580 | 19 | 217 |
45 | 610 | 16 | 229 |
50 | 640 | 14 | 241 |
55 | 660 | 13 | 255 |
60 | 690 | 12 | 255 |
65 | 710 | 10 | 255 |
70 | 730 | 9 | 269 |
75 | 1100 | 7 | 285 |
80 | 1100 | 6 | 285 |
85 | 1150 | 6 | 302 |
60Г | 710 | 11 | 269 |
70Г | 800 | 8 | 285 |
Легированная сталь
Углеродистая сталь может быть классифицирована как легированная сталь, когда содержание марганца превышает 1,65%, кремния или меди 0,60% или когда содержание хрома составляет менее 4%. Углеродистая сталь также может быть классифицирована как сплав, если указанный минимум содержания алюминия, титана, ванадия, никеля или любого другого элемента был добавлен для достижения конкретных результатов. Добавки хрома, никеля и молибдена улучшают способность изделий из этих сплавов к дальнейшей термической обработке и улучшают химические и механические свойства крепежных изделий.
Стали могут содержать один или несколько легирующих элементов, которые и придают им заданные свойства.
Основной структурной составляющей в конструкционной стали является феррит, занимающий в структуре не менее 90% по объему. Растворяясь в феррите, легирующие элементы упрочняют его. Твердость феррита (в состоянии после нормализации) наиболее сильно повышают кремний, марганец и никель — элементы с решеткой, отличающейся от решетки Fe. Молибден, вольфрам и хром влияют слабее. Большинство легирующих элементов, упрочняя феррит и мало влияя на пластичность, снижают ударную вязкость (за исключением никеля). При содержании до 1% марганец и хром повышают ударную вязкость. Что требуется, прежде всего, при использовании крепежных изделий в условиях больших перепадов температур, снижая тем самым возможное разрушение изделий. Свыше этого содержания ударная вязкость снижается, достигая уровня нелегированного феррита при 3% Сr и 1,5% Мn.
Повышению конструктивной прочности при легировании стали способствует увеличение прокаливаемости. Улучшение прокаливаемости стали достигается при ее легировании несколькими элементами, например Cr+Мо, Cr+Ni, Cr+Ni+Мо и другими сочетаниями различных элементов.
Высокая конструктивная прочность стали обеспечивается сбалансированным содержанием в ней легирующих элементов. Избыточное легирование после достижения необходимой прокаливаемости приводит к снижению вязкости и облегчает разрушение стали.
Хром оказывает благоприятное влияние на механические свойства конструкционной стали. Его вводят в сталь в количестве до 2%; он растворяется в феррите и цементите. Кроме того, хром – основной элемент, значительно уменьшающий проникновение водорода в кристаллическую решетку стали при определенных технологических процессах, уменьшая тем самым основную проблему высокопрочных крепежных изделий – водородное охрупчивание.
Никель характеризуется прочностью, тугоплавкостью, способностью к пассивации. Его вводят в сталь в количестве от 1 до 5%. Никель заметно повышает предел текучести стали, но делает сталь чувствительной к перегреву. В связи с этим для измельчения зерна одновременно с никелем в сталь вводят карбидообразующие элементы.
Марганец вводят в сталь до 1,5%. Он распределяется между ферритом и цементитом, придавая тем самым, дополнительные свойства стали, прежде всего – упругость.
Кремний является некарбидообразующим элементом, и его количество в стали ограничивают до 2%. Он значительно повышает предел текучести стали и при содержании более 1% снижает вязкость и повышает порог хладноломкости.
Молибден и вольфрам являются карбидообразующими элементами, которые большей частью растворяются в цементите. Молибден в количестве 0,2— 0,4% и вольфрам в количестве 0,8—1,2% в комплексно легированных сталях способствуют измельчению зерна, увеличивают прокаливаемость и улучшают некоторые другие свойства стали.
Ванадий и титан — сильные карбидообразушие элементы, которые вводят в небольшом количестве (до 0,3% V и 0,1% Ti) в стали, содержащие хром, марганец, никель, для измельчения зерна. Повышенное содержание ванадия, титана, молибдена и вольфрама в конструкционных сталях недопустимо из-за образования специальных труднорастворимых при нагреве карбидов. Избыточные карбиды, располагаясь по границам зерен, способствуют хрупкому разрушению и снижают прокаливаемость стали.
Бор вводят для увеличения прокаливаемости в очень небольших количествах (0,002— 0,005%).
Марка легированной качественной стали состоит из сочетания букв и цифр, обозначающих ее химический состав. Легирующие элементы имеют следующие обозначения (ГОСТ 4547-71):
- хром (X)
- никель (Н)
- марганец (Г)
- кремний (С)
- молибден (М)
- вольфрам (В)
- титан (Т)
- алюминий (Ю)
- ванадий (Ф)
- медь (Д)
- бор(Р)
- кобальт (К)
- ниобий (Б)
- цирконий (Ц)
Цифра, стоящая после буквы, указывает на содержание легирующего элемента в процентах. Если цифра не указана, то легирующего элемента содержится до 1,5%.
В качественных конструкционных легированных сталях две первые цифры марки показывают содержание углерода в сотых долях процента. Высококачественные легированные стали имеют в конце марки букву А, а особо высококачественные — Ш (электрошлаковый переплав).
ves-krepej.ru
Технология производства крепежа
ОБОРУДОВАНИЕ ДЛЯ ПРОИЗВОДСТВА МЕТИЗОВ, КРЕПЕЖА И ДЕТАЛЕЙ ХОЛОДНЫМ СПОСОБОМ
ТЕХНОЛОГИЯ ПРОИЗВОДСТВА КРЕПЕЖА
(для справки)
В автомобильной и тракторной промышленности почти все крепежные детали изготовляют холодной высадкой. Холодная высадка применяется для формообразования головок болтов, винтов, заклепок при больших программах выпуска. Этим способом изготовляют и более сложные детали (например, шаровые и ступенчатые пальцы, ролики и шарики подшипников и др.). Холодной высадке подвергают калиброванные стальные прутки диаметром 0,6 до 38 мм, а также прутки из цветных сплавов (алюминиевых, медных и др.), круглых шестигранных и других форм сечения.
Холодную высадку, как правило, производят на холодно высадочных прессах-автоматах (обычно горизонтальных, одно ударных или многопозиционных). После подачи материала (калиброванной проволоки) через отрезную матрицу, нож отрезает заготовку и переносит ее на линию высадки. Пуансон заводит заготовку в матрицу, а после упора заготовки в выталкиватель осуществляет высадку головки. В момент возврата пуансона в исходное положение высаженная деталь выталкивателем удаляется из матрицы и цикл высадки повторяется. Если головка не может быть высажена за один удар пуансона, высадку производят на двух, трех и более ударных (многопозиционных) холодновысадочных автоматах (рис. 1). Производительность современных высадочных автоматов достигает 400 деталей в минуту.
Рисунок 1
Позиции: 0 — отрезка заготовки; 1 — предварительная высадка; 2 — окончательная высадка; 3 — редуцирование под резьбу и обрезка граней.
Процесс высадки метизов
Как правило болты DIN931, DIN 933 производят на 3х или 4х позиционных автоматах, технология производства гайки требует наличие на производственной площадке 5-ти позиционного автомата, сложные изделия (например, штуцера и аналогичные детали) изготавливают на 6 и 7 позиционных высадочных станках. Количество позиций (ковочных станций) прямо пропорционально уровню сложности деталей, чем сложнее деталь тем больше переделов должен совершить станок чтобы деформировать метал в готовую форму продукции (см. эскизы).
3-х позиционный автомат
4-х позиционный автомат
5-ти позиционный автомат
6-ти позиционный автомат
ПРОИЗВОДСТВО ШУРУПОВ
МИНИМАЛЬНЫЙ НАБОР ОБОРУДОВАНИЯ ДЛЯ ПРОИЗВОДСТВА ШУРУПОВ
Минимальный набор оборудования для производства шурупов включает в себя две модели оборудования:
- Оборудование для холодной высадки шурупов. Применяется для формирования болванки (основы) под шуруп. На этом этапе, на холодновысадочном автомате подобном гвоздильному, отрезают проволочную заготовку необходимой длины, формируют головку шурупа, его наконечник, шлиц и длину. Диаметр шурупа определяется диаметром используемой проволоки. После этого заготовки передаются на второй станок (резьбонакатной), который служит для накатки резьбы и формирования острого наконечника.
- Резьбонакатное оборудование для шурупов. Нарезание резьбы производится на специальных автоматах. В них болванки шурупов засыпаются в бункер. Из бункера с помощью вибрационного транспортера и анкерного механизма болванки поштучно поступают в зону нарезки резьбы. При этом они строго ориентированы по отношению к рабочим элементам. Рабочими элементами являются плоские плашки. Они перемещаются навстречу и параллельно друг другу и перпендикулярно оси шурупа, при этом плашки плотно прижимаются к стержню шурупа. Плашки изготавливаются по основным параметрам резьб шурупов. В России в соответствии с метрическими размерами. Зарубежные производители могут использовать плашки для нарезания дюймовых резьб на шурупах. Вариант кинематической схемы изготовления шурупов представлен на рис.2.
Рисунок 2.
По такой схеме изготавливаются шурупы до диаметра 10-12 мм. Свыше этих диаметров шурупы, как правило, изготавливаются методом горячей штамповки. Пример тому – путевой шуруп, диаметр которого – 24 мм, а длина – 170 мм. Дальнейшим развитием технологии изготовления шурупов является технология изготовления саморезов.
ПРОИЗВОДСТВО САМОРЕЗОВ
МИНИМАЛЬНЫЙ НАБОР ОБОРУДОВАНИЯ ДЛЯ ПРОИЗВОДСТВА САМОРЕЗОВ
Саморез вполне справедливо получил свое название, так как способен нарезать резьбу не только в мягких материалах типа дерева или пластика, но и в металле или бетоне. Способность самореза нарезать резьбу достигается тем, что его поверхность подвергается термической обработке (закалке). К тому же, для того что бы саморез оптимально вворачивался в скрепляемые конструкции, его окончание часто выполнено в виде сверла. Это сверло при вворачивании самореза просверливает отверстие именно того диаметра, которое требуется.
Для организации качественного, конкурентоспособного производства саморезов, как правило, требуется, пять моделей оборудования:
- Оборудование для холодной высадки саморезов. Для формирования головки и стержня самореза из заготовки.
- Оборудование для формирования пера (острия) саморезов. Для того что бы саморез оптимально вворачивался в скрепляемые конструкции.
- Резьбонакатное оборудование для саморезов. Для формирования резьбы на стержне самореза.
- Закалочная печь для саморезов. Для поверхностной закалки уже готовых саморезов для придания металлу дополнительной твердости и прочности. Закаливают саморезы до твердости не менее 55 ед. по HRC (по Роквэллу).
- Оборудование для цинкования (белым или желтым цинком), оксидирования или фосфатирования саморезов. Для защиты саморезов от коррозии.
- Упаковочное оборудование. Для упаковки готовой продукции в коробки или пластиковые пакеты.
Минимальный набор оборудования для изготовления саморезов включает в себя две модели оборудования:
- Оборудование для холодной высадки саморезов. Для формирования головки и стержня самореза из заготовки.
- Резьбонакатное оборудование для саморезов. Для формирования резьбы на стержне самореза.
Чтобы сделать точный расчет стоимости оборудования для организации производства саморезов пришлите нам пожалуйста подробные технические характеристики продукции которую Вы хотите производить и чертёж, а именно:
- Наименование изделия крепежа.
- Диаметр головки.
- Длина стержня.
- Производительность оборудования (шт./мин.).
- Чертёж продукции.
ПРОИЗВОДСТВО БОЛТОВ
МИНИМАЛЬНЫЙ НАБОР ОБОРУДОВАНИЯ ДЛЯ ПРОИЗВОДСТВА БОЛТОВ
Минимальный набор оборудования для производства болтов включает в себя две модели оборудования:
- Оборудование для холодной высадки болтов. Для формирования головки и стержня болта из заготовки.
- Резьбонакатное оборудование для саморезов. Для формирования резьбы на стержне болта.
Технологический процесс изготовления крепежа и крепежных изделий контролируется от исходного сырья до упаковки готовой продукции. Таким образом, в процесс производства крепежных изделий дополнительно рекомендуется включать оборудование для термообработки, цинкования, фосфатирования, автоматического тестирования качества крепежа, разбраковки и упаковочное, фасовочное оборудование для метизов, крепежа и деталей.
www.metiz.com.tw
Из каких материалов изготавливают крепежные изделия?
В зависимости от материала изготовления происходит разделение крепежных изделий на виды. Учитывая этот момент, можно смело отправляться за покупкой в магазин.
Алюминий
Алюминий – это удивительно прочный и гибкий материал, используемый для изготовления крепежных изделий. Он в несколько раз легче стали, не горит, не притягивается к магниту и устойчив к коррозии. При охлаждении алюминиевые изделия становятся крепче и не подвержены сгибанию.
Алюминиевый материал является отличным проводником тепла, у него рациональное соотношение веса и плотности. Если в состав крепежа добавляются другие сплавы (марганец, магний, медь), то это делает готовое изделий более прочным и сильным.
Латунь
Латунные крепежные изделия в Екатеринбурге и других городах широко используются в строительстве. Их отличительной чертой является высокая устойчивость к окислению. За счет этого латунные крепежи можно применять в любых, даже кислых средах, не переживая за возникновение коррозии. На сегодня эти изделия считаются самыми долговечными благодаря отсутствию ржавчины даже при работе в условиях повышенной влажности.
Титан
Титановые крепежи обладают уникальными свойствами:
- коррозийная устойчивость;
- жаропрочность;
- долговечность;
- высокая прочность.
За счет перечисленных свойств титановые изделия широко используются в машиностроении, где к крепежам предъявляются особо жесткие требования. Они не портятся под воздействием высоких температур и влажности. Часто можно встретить данные крепежи в спортивном инвентаре.
Сплав меди
Медные саморезы и другие виды крепежей устойчивы к окислению. Их можно использовать даже в едких кислотах, исключая вероятность возникновения ржавчины. Медь долговечна – она способна прослужить не менее 150 лет, сохраняя при этом свой свойства. Применение крепежным изделиям находят в машиностроении, строительстве и в различном оборудовании, где важна прочность и долговечность каждой детали. На сегодня это дорогой материал, который по свойствам уступает только титану.
Нержавеющий материал
Нержавеющие крепежи очень стойко выдерживают большую влажность и различные кислоты. Они не портятся и не гнутся при большой нагрузке и физическом давлении. Нержавеющий материал недорогой, за счет чего очень популярен.
Выбирая крепежные изделия, важно обращать внимание на материал, из которого они изготовлены. Для скрепления обычных деталей будет неразумно покупать медные или титановые элементы. На производстве и для автомобиля лучше приобрести более дорогие крепежи, которые прослужат длительное время.
kapitalstrojservis.ru
Крепеж Выбор материала
Крепежные изделия бывают самых разных спецификаций, но, если вы планируете использовать болт, винт, заклепку или зажим, выбор материала, подходящего для предполагаемого применения является важной задачей. Например, выбирая крепеж http://prommetiz.com/p158232500-bolt-shgr-golovkoj.html из стали, а не из алюминия можно существенно повлиять на качество и продолжительность срока службы. Многочисленные факторы, такие как условия окружающей среды, наличие коррозионных элементов, требования к физическим нагрузкам, а также к общей структурной устойчивости, может так же влиять на материальную эффективность.
Большинство промышленных крепежных деталей изготавливаются из алюминия, латуни, некоторых синтетических неметаллов, а также различных марок стали и нержавеющей стали. Кроме того, металлы, такие как титан также являются ценным материалом для создания крепежных деталей, хотя они имеют очень специфические приложения в узком диапазоне полей применения. Как правило, скрепляющие материалы оцениваются по их механическим свойствам, давая потенциал для пост-обработки, эффективности затрат на изготовление, а также несколько других вторичных критериев.
Крепеж стальной
Крепеж закрывающий является наиболее широко используемым материалом в производстве крепежных деталей, составляя около 90 процентов всех крепежных деталей, изготовленных в год. Популярность этого крепежа из металла является результатом его высокой степени формуемости в сочетании с пределом прочности и долговечности. По сравнению с другими металлошихтами, сталь также относительно недорога в изготовлении. Она часто обрабатывается цинком или хромовым покрытием, но также может быть сформирована без каких-либо обработок поверхности.
Углеродистая сталь является наиболее распространенным типом стали, используемой в производстве крепежа. Сорта 2, 5 и 8, как правило, стандартный для винтов и болтов на основе из углеродистой стали, с легированной углеродистой стали, будучи более высокого класса, вариации этих металлов больше. Их механическая прочность составляет приблизительно от 50 KSI (кило-фунт на квадратный дюйм) до 300 KSI в готовом продукте.
Свойства материала для этих классов включают в себя:
• 2-й класс: Это низкая категория углерода, которая показывает наименее дорогой, но и не менее прочный виды стали. 2-го класс материал обладает высокой работоспособностью и формирует основную часть крепежа из марки.
• Оценка 5: 5-го класса стали изготавливаются из нелегированных средних групп углерода, такие как тип 1038, и, как правило, закаляются для повышения их прочности. Это наиболее распространенный класс, использующийся в автомобильной промышленности.
www.norma-stab.ru
Технология изготовления крепежа холодной высадкой
Крепежные изделия это одно из самых древних изобретений, ведь даже в далеком прошлом без них было трудно обойтись, и их так же использовали повсеместно. По мере прохождения времени менялась не только форма крепежа но технологии их производства, ручное изготовление постепенно сменялось машинным или полуавтоматическим, затем пришли токарные станки автоматы, участие человека в работе которых практически не требовалось, за исключением наладки и смены материала для изготовления.
Затем к станкам автоматам стали применять компьютерные технологии т.е. оснащать станки программно числовым управлением.
Изготовление крепежа с помощью высадки
В настоящее время самым распространенным видом изготовления крепежных изделий является холодная высадка, такую популярность она завоевала благодаря своей высокой скорости производства, а также снижению ресурсо и энергозатрат на изготовление одного изделия. Для холодной высадки используют как цветные так и черные металлы, минимальный диаметр заготовrи может быть от 0,6 мм. до 32 мм., сечение прутков может быть как круглое так и шестигранное.
Весь процесс производства проходит на специально оборудованных холодно высадочных прессовочных формах под давлением. Сначала подается материал как правило это может быть пруток, первым делом отрезается заготовка в матрице, определенной длины, затем она перемещается на линию высадки, затем заготовка помещается в другую матрицу посредством пуансона, после того как заготовка установлена и уперта в выталкиватель, происходит высадка головки. После того как пуансон вернется в исходное положение, изделие выходит из матрицы и все повторяется с начала. Бывают ситуации когда высадка не может быть произведена за один цикл, в таких случаях ее производят на нескольких холодно высадочных автоматах.
Производительность таких станков достигает 400 изделий в минуту, что очень хорошо.
Технология производства шурупов, холодной высадкой
Для изготовления шурупов холодной высадкой потребуется проволока определенного диаметра, которая поступает для нарезки под заготовки в холодно высадочный автомат, далее из отрезанной заготовки формируется головка шурупа, затем наконечник, все рассчитано с тем условием что изделие получится определенной длины. После этих операций заготовка попадает на резьбонакатной станок,
где происходит формирование резьбы и острого наконечника.
Нарезка резьбы производится на специальном оборудовании, сейчас вы кратко ознакомитесь с принципом его работы. Все будующие шурупы засыпаются в специальную емкость, далее посредством вибрационного механизма заготовки поштучно попадают на специальный конвеер который передает каждую заготовку для нарезки резьбы, транспортировка происходит по специальной канавке, в конце которой идут две проволоки расположенные параллельно друг другу, ножка заготовки проваливается между проволоками и зацепляется головкой, получается что она висит вертикально и готова к нарезке резьбы.
Резьбу нарезают две плашки, которые движутся параллельно друг другу в разные стороны. Деталь зажимается между ними и проходит цикл накатки, при котором плашки плотно прижимаются к оси шурупа и после прокатки оставляют на оси резьбу. Таким образом изготавливается практически все виды стандартных шурупов.
В нашей компании изготовление винтов, гаек и шурупов производится на станках автоматах, также мы изготавливаем винты можете посмотреть
здесь, также мы произведем изготовление другого крепежа в том числе и нестандартного и изделий из металла на станках автоматах, под заказ и по вашим чертежам, об этом по подробнее вы можете прочитать перейдя по ссылке на главную страницу http://pk-alef.ru. На этом все, в следующей статье мы рассмотрим технологию изготовления саморезов.
pk-alef.ru