Материалы для наплавки – —
alexxlab | 15.01.2021 | 0 | Вопросы и ответы
Материалы для наплавки | Инструмент, проверенный временем
При наплавке используются различные материалы: проволока наплавочная и порошковая, электроды, флюсы и т. д.
Наплавочная проволока
Для наплавки выпускается специальная стальная наплавочная проволока диаметром от 0,3 до 8 мм тридцати марок:
— девять марок углеродистой проволоки — НП-25; ШІ-30; НП-35; НП-40; НП-45; НП-50; НП-65; НП-80; НП-85;
— одиннадцать марок легированной проволоки — НП-40Г; НП-50Г; НП-65Г; НП-ЗОХГСА; НП-30Х5; НП-40ХЗГ2МФ; НП-40Х2Г2М; НП-50ХНМ; НП-50ХФА; НП-50Х6ФМС; НП-105Х;
— десять марок легированной проволоки — НП-20Х14; ІШ-30Х13; НП-30Х10П0Т; НП-40Х13; ИП-45Х4ВЗФ; НП-45Х2В8Т; НП-60ХЗВ1-Ф; НП-ГВ; НП-Х15Н60; НП — Х20Н80Т.
Наплавочная проволока подбирается в зависимости от назначения и требуемых свойств металла наплавки (табл. 56). Одно из главных требований — твердость металла наплавки.
Максимальная твердость может быть получена при использовании высоколегированной проволоки марки НП-40Х13 (твердость по шкале HRC — 45-52), мини-
Некоторые данные наплавочных проволок
Таблица 56
|
мальвая — при использовании углеродистой проволоки марки НП-25 (HRC 40).
Наплавка проволокой производится покрытыми электродами вручную, под флюсом на автоматах и т. д.
Покрытые электроды
По ГОСТ 10051-75 предусматривается 44 типа покрытых электродов, которые могут быть использованы для наплавки. Достигаемая твердость наплавленного слоя от 28 до 66 HRC.
В табл. 57 даны некоторые примеры использования наплавки покрытыми электродами.
Флюсы
Для наплавки применяются те же флюсы, что и для сварки. Наибольшее распространение получили плавленые флюсы марок АН-348А, АН-60, АН-20, АН-25, АН-18, ОСЦ-45 и т. п. Флюсы выбираются в зависимости от свойств металла и других условий.
При наплавке используются и керамические флюсы — АНК-18, АНК-Юит. д.
Прутки для наплавки
При наплавке газокислородным пламенем или в защитной среде аргона применяются литые прутки диаметром 6—8 мм и длиной до 400 мм. Химический состав тонких прутков приведен в табл. 58.
Литые прутки используются также при изготовлении покрытых электродов для ручной дуговой наплавки. Так, например, прутки марки ВЗК идут на изготовление электродов ЦН-2, применяемых для наплавки арматуры котлов высоких параметров.
Порошковая проволока
При наплавке применяется также порошковая проволока. Выпускается много различных марок, например, ІГО-АН105 для наплавки высокомарганцовистых сталей, ПП-АН120, ПП-АН121 — для наплавки под флюсом различных деталей из углеродистых сталей.
Таблица 58 Химический состав литых прутков для наплавки, %
|
Основные характеристики зернистых сплавов
Таблица 59
|
Марка сплава | Состав | Твердость наплавлен- | Примеры применений, примечания |
Боридиая смесь БХ | Бориды хрома — 50%, железный порошок — 50%. | 82-т84 HRA | |
Вокар | Измельченный вольфрам, про* каленный сахар (углерод) | 50-58 HRC (первый СЛОЙ). 61-63 HRC (второй слой) | Наплавка при изготовлении и ремонте бурового инструмента |
Карбидоо-боридная смесь КБХ | Карбид хрома — 5%, борид хрома— 5%, железный порошок — 30%, феррохром — 60%. | Получила более широкое распространение, чем бор ИД — нал смесь БХ |
Порошковой проволокой наплавляются изделия в защитных газах, под флюсом и открытой электродугой.
При дуговой наплавке порошковыми проволоками применяются меньшие токи, нем при выполнении сварки. В результате глубина проплавления основного металла уменьшается и наплавленный материал мевьше смешивается с основным. Это приводит к возрастанию твердости наплавленного металла.
Порошкообразные (зернистые) сплавы
При наплавке используются также зернистые сплавы в виде порошкообразных смесей.
В табл. 59 приведены основные характеристики таких смесей.
hssco.ru
Наплавочные материалы
Темы: Наплавка.
На данной странице наплавочные материалы рассматриваются с точки зрения химсостава и его влияния на свойства наплавленного металла. Разбивку наплавочных материалов по типам (проволока, электроды и т.д. ) смотрите на других страницах сайта в теме “Наплавка”.
Другие страницы, по теме
Наплавочные материалы
:
Предложения поставщиков:
Для восстановления или упрочнения наплавленных поверхностей в зависимости от условий работы деталей используют самые разнообразные материалы как по структуре, так и по химическому составу. Именно этими характеристиками в основном определяют износостойкость и стойкость к воздействию рабочей среды наплавленных поверхностных слоев. Рассмотрим основные группы наплавленного металла.
Перлитные материалы.
Состав перлитных материалов (Нп-25, Нп-20ХГСА, Нп-90ХГСА и др.) обеспечивает в зависимости от скорости охлаждения наплавки перлитно-сорбитную структуру. Твердость наплавленного металла находится на уровне 25 .. .40 HRC, износостойкость значительно уступает мартенситной структуре, поэтому сопротивление износу при трении невысоко.
Наплавочные материалы этого класса часто применяют для создания «Подслоя», на который наплавляют слой повышенной твердости.
Мартенситные материалы.
Они характеризуются образованиeм мартенситной структуры cразу поcле наплавки. Обладaя повышенной твердостью, стойкостью к абразивному износу, наплавка этого типa хаpактеризуется пониженными пластическими cвойствами, хрупкостью, склонностью к oбразованию холодных трещин (ХТ). Пpи работе в условиях ударного нагружения вoзможны отколы пo основному металлу или в зоне cплавления.
Низколегированные мартенситные материалы (Нп-40Х3Г2МФ, Нп-40Х2Г2М, Нп-50Х6ФМС и др.), содержание легирующих элементов в которых относительно невысоко, обеспечивают в наплавке мартенситно-бейнитные структуры и отличаются сравнительно небольшой твердостью (45,..50 HRC). Свойства наплавки повышаются в основном с увеличением содержания в ней углерода и хрома, что при водит к соответствующему возрастанию доли мартенситной составляющей.
Значительнo бoльшей твердостью хaрактеризуются борсодержащие мартенситные наплавки (ЛС-У10Х7ГР1, ПЛУ-25Х25Г3Ф2РН, ПП-АН125, ПП-АН170), в cтруктуре кoторых пo грaницам высoкоуглеродистого мартенсита рaсположены твeрдые карбиды и бoриды. Материал oтлично сопротивляется абразивному износу, зaдирам, нo из-зa повышенной хрупкости нe мoжет быть рeкомендован для рaботы в услoвиях динамических нагрузок. Наплавка имеeт пoвышенную склoнность к обрaзованию горячих трещин и хлодных трещин, пoэтому вeдут еe, кaк прfвило, c подогревом и применениeм одногo или нeскольких подслоев. Отпуск в рeзультате наложения нескольких слоев прaктически нe снижаeт твердости.
Для oбеспечения повышенной сопротивляемости к зaдирам примeняют наплавочные материалы, сoдержащие в своeй структурe нaряду c мартенситом значительноe количeство аустенитной фaзы (Нп-50Х6ФМС, Нп-30Х5). Мартенситные хромистые материалы типa Нп-30Х13 послe наплавки имeют в oсновном мартенситную структуру c нeбольшим содержаниeм феррита. Износостойкость наплавки пoвышается c увеличениeм кoличества углерода. Низкоуглеродистые наплавки пoмимо дoстаточной износостойкости oбладают пoвышенной жаростойкостью и eантикоррозионными свойствами. C увеличением содержания углерода (Э-120Х12Г2СФ) в структурe появляeтся ледебуритная составляющая, чтo резкo пoвышает износостойкость наплавки и делaет eе пригoдной для наплавки режущих кромок инструментов.
Высокомарганцовистые аустенитные материалы.
Материалы типa Нп-Г12А пpи pезком охлaждении от тeмпературы 1000оС обрaзуют аустенитную структуру c пoвышенными вязкостью и пластичностью. Длительнaя выдержкa пpи температуре >400оС привщдит к выделунию по грфницам зурен кфрбидов и вторичной перлитной фазы, снижающих пластичность. Уменьшение содержания углерода снижает вуроятность образовфния вторичных фаз. В зоне сплавления oсновного низколегированного или низкоуглеродистого металла наплавки вoзможны oбразование хрупкой мартенситной прoслойки и появление трещин. Для прeдотвращения иx рекомендуется применение промежуточнoго cлоя из хромисто-марганцовистой наплавки типa Нп-30Х10Г10Т.
Высокохромистые материалы.
Высокохромистыe материалы нa основе железа типа Э-300Х28НЧСЧ, Э-320Х25С2ГР пoзволяют получать cтруктуру, мaтрица которой cостоит из аустенита c вкpаплениями мeлкодисперсных чaстиц кaрбидов бора и хрома, пpидающих наплавке высокую твердость. Пoскольку твердость в oсновном oпределяется кoличеством карбидов, oна прaктически нe измeняется в процессe нагрeва и нe зависит oт скoрости охлаждения. Тeм нe менeе, наплавку надо проводить с предварительным подогревом деталей дo 400… 500оС, чтoбы избежать появлeния горячих трещин, a такжe умeньшать скорость охлаждения.
Добавка ниобия, вольфрама, молибдена и дpугих карбидообразователей способствует большему повышению твердости и пoявлению спoсобности наплавки кo вторичному твердению; при этом повышается износостойкость.
Коррозионно-стойкие наплавочные материалы.
Обычно наплавка проводится на изделиях из хромистых или хромоникелевых аустенитных сталей (см. аустенитные стали). Ферритная коррозионно-стойкая наплавка обеспечивается при высоком содержании хрома и весьма низком углерода. Наплавки этого типа в отношении к общей коррозии существенно уступают аустенитным, но превосходят последние по стойкости к коррозионному растрескиванию под напряжением.
Технологические свойства аустенитной наплавки достаточно высоки. Однако при наплавке на стали мартенситного класса следует опасаться появления ХТ в зоне сплавления. Рекомендуется применять предварительный подогрев до относительно невысоких температур: 100 … 150оС. Превышение этой температуры может привести к замедленному охлаждению наплавки и ее охрупчиванию.
- < Восстановление деталей наплавкой
- Электродные ленты для наплавки >
weldzone.info
Процесс наплавки, области применения, способы наплавки
Наплавка – это процесс нанесения при помощи сварки металла на поверхность изделия. Наплавку применяют при изготовлении новых деталей, механизмов и при восстановлении изношенных.
Путем наплавки получают изделия:
– износостойкие.
– антифрикционные,
– жаростойкие,
– коррозионностойкие,
– кислотоупорные
-и др.
Технический и экономический эффект достигается в результате получения биметаллических изделий с оптимальным сочетанием свойств основного металла и наплавленного. Примерами таких изделий в судостроении могут служить: гребные валы, балеры рулей, валопроводы, опорные и упорные подшипники скольжения, уплотнительные поверхности судовых клапанов, захлопок, фланцев. Примеры в машиностроении: клапаны двигателей внутреннего сгорания, валки прокатных станов, конусы и чаши загрузочных устройств доменных печей, зубья ковшей экскаваторов и др.
Наплавка в ремонтном деле эффективна благодаря тому, что восстанавливаемая деталь часто в несколько раз дешевле новой детали и при правильно выбранной технологии восстановления не уступает ей в работоспособности.
Перечислим основные способы наплавки:
– ручная дуговая наплавка покрытым электродом,
– автоматическая наплавка под слоем флюса,
– механизированная и автоматизированная наплавка плавящимся электродом в среде активного газа (СО2 и смеси газов с СО2) и в среде инертного газа (аргон, гелий),
– наплавка неплавящимся электродом в среде инертного газа,
– электрошлаковая наплавка,
– плазменная наплавка,
– наплавка токами высокой частоты,
– газопламенная наплавка,
– наплавка лежачим электродом.
Существуют и другие специальные способы.
1. Виды износов и разрушений металлических изделий [1].
1.1 Износ при трении металла о металл.
Износ происходит в подшипниках скольжения (коленчатые валы, оси), в механизмах взаимного перемещения (пальцы, штоки, поршни, гильзы), при трении качения (железнодорожные и крановые колеса, рельсы, детали гусенечных машин). В узле трения обычно присутствуют абразивные частицы: продукты износа и коррозии, песок, руда. На износостойкость трущейся пары влияет много факторов: соотношение твердости трущихся поверхностей, удельная нагрузка, концентрация и твердость абразива, микроструктура поверхностей.
2.2 Термическая усталость.
Это изменение структуры и формы, сопровождающиеся разрушением материалов в результате действия циклических нагревов и охлаждений. Трещины – наиболее характерный вид разрушения, вызываемый термической усталостью. Трещины возникают на поверхности детали после определенного числа циклов. Их количество непрерывно увеличивается с возрастанием числа циклов. В результате образуется сетка трещин, которую часто называют сеткой разгара.
Термической усталости подвержены многие детали в металлургическом производстве: валки горячей прокатки, штампы для горячей штамповки, пресс-формы для литья под давлением. Эти детали испытывают не только тепловые удары, но подвергаются одновременно и износу истиранием.
2.3 Абразивный износ.
Обусловлен наличием абразивной среды в зоне трения. Разрушение поверхностей трения происходит в результате местного пластического деформирования, мезоцарапания и мезорезания абразивными частицами. Абразивный износ испытывают многие детали загрузочных и разгрузочных устройств строительных и дорожных машин, почвообрабатывающих машин.
Многие детали (ножи дорожных машин, лемехи плугов, била дробилок) испытывают абразивный износ с ударами.
2.4 Газоабразивный износ.
Вызывается механическим действием твердых частиц, перемещаемых потоком газа. Разрушение поверхностей происходит в результате срезания, выкрашивания, выбивания многократного пластического деформирования поверхностных мезообъемов. Этому виду износа подвергаются сопла реактивных двигателей, лопатки турбин, вентиляторов, насосов, детали трасс пневмотранспорта. Интенсивность изнашивания определяется скоростью, свойствами и формой абразивных частиц. Температурой и степенью запыленности газового протока, физико-механическими свойствами изнашиваемого металла.
2.5 Гидроабразивный износ.
Во многом схож с газоабразивным, но носителем абразивных частиц является жидкость. Гидроабразивному износу подвергаются рабочие колеса и улитки земснарядов и насосов, лопасти и камеры гидротурбин, работающие на реках, пульпопроводы гидротранспорта. Интенсивность износа во многом зависит от условий обтекания детали жидкостью и углами встречи абразивной частицы с изнашиваемой поверхностью.
2.6 Кавитационная эрозия.
Проявляется главным образом в результате импульсного механического воздействия гидравлических ударов потока жидкости на поверхность металла. Кавитации подвержены гребные винты, лопасти и камеры проточного тракта гидротурбин, рабочие колеса и камеры различных гидромашин. Наличие коррозионной среды ускоряет процесс кавитационного разрушения. Поэтому для работы в условиях кавитации применяют коррозионностойкие стали и сплавы (например, алюминиевую бронзу).
3. Наплавочные материалы [2, 1].
Одним из главных показателей для наплавочных материалов является твердость наплавленного металла. Чаще всего твердость выражается в единицах:
– HRC – по Роквеллу,
– HB – по Бринеллю,
– HV – по Виккерсу.
3.1 Покрытые электроды.
Для наплавки применяют электроды, предназначенные для сварки различных металлов, а также специально разработанные электроды для наплавки.
В таблице приведены некоторые марки специальных наплавочных электродов для различных случаев применения:
марка электрода | типичный хим. состав наплавленного металла, % | твердость* HRC | область применения | |||||
C | Si | Mn | Cr | Mo | прочие | |||
ОЗШ-1 | 0,14 | 0,85 | 1,0 | 1,0 | 0,8 | - | 34-35 | бойки молотов |
ЭН-60М | 0,8 | 1,10 | 0,7 | 2,6 | 0,5 | - | 53-61 | штампы |
Т-590 | 3,2 | 2,2 | 1,2 | 25,0 | - | 1,0B | 55-62 | зубья ковшей |
ЦН-6Л | 0,06 | 5,4 | 1,26 | 17,0 | - | 8,0Ni | 27-32 | арматура котлов |
Содержание: S = 0,02-0,03%, P = 0,03-0,04%
* – твердость в третьем- четвертом слое наплавки
Повышение твердости наплавки обеспечивается введением в состав стержней электродов углерода, молибдена, вольфрама.
3.2 Проволоки сплошного сечения.
Для механизированной наплавки наиболее часто применяют проволоки сплошного сечения. Для наплавки применяют обычные проволоки для сварки, а также специальные наплавочные проволоки.
Специальные наплавочные проволоки для сталей имеют маркировку, начинающуюся с букв Нп– наплавочная проволока, и через тире – числовую и буквенную маркировку.
Примеры:
Нп-30 – углеродистая стальная проволока с содержанием углерода 0,27-0,35%,
Нп-50Г – углеродистая стальная проволока с содержанием углерода 0,45-0,55% и марганца 0,7-1,0%.
Нп-30Х13 – высоколегированная стальная проволока с содержанием углерода 0,25-0,34% и хрома 12,0-14,0%.
Для наплавки бронзы на сталь используют проволоки Бр.АМц 9-2, Бр.АЖМц 10-3-1,5.
Для полуавтоматической наплавки применяют проволоку диаметром 1,6-2,0мм, для автоматической – 2-6мм.
Для наплавки стали с целью повышения износостойкости применяют также пружинную проволоку, т.к. она высокоуглеродистая и обеспечивает получение наплавленного слоя повышенной твердости.
3.3 Порошковая проволока.
Порошковая проволока состоит из оболочки – мягкой ленты: стальной, медной, никелевой и др. и сердечника из порошков легирующих компонентов: ферросплавов, чистых металлов, боридов и т.п. В сердечник порошковой проволоки вводят также газо- и шлакообразующие вещества, раскислители.
Порошковые проволоки применяются для наплавки слоев металла с особыми свойствами, для которых, например, невозможно изготовить проволоку сплошного сечения.
Разработаны и применяются порошковые проволоки трех типов: для наплавки под флюсом, в среде защитных газов и открытой дугой в атмосфере воздуха, такую порошковую проволоку называют самозащитной.
Специальные наплавочные порошковые проволоки для сталей имеют маркировку, начинающуюся с букв ПП– порошковая проволока, и через тире – числовую и буквенную маркировку.
Примеры:
ПП-25Х5ФМС – легированная хромистая (4,8-5,5%) стальная проволока с содержанием ванадия (0,3-0,5%), молибдена (0,9-1,3%), кремния 0,9-1,3%). Предназначена для наплавки валков горячей прокатки, ножей горячей резки металла, прессового инструмента, работающих в условиях термической усталости и больших давлений.
ПП-АН105 – АН означает, что проволока разработана институтами Академии наук, 105 – порядковый номер разработки. Проволока высокомарганцовистая – 13% Mn. Предназначена для наплавки изношенных крестовин стрелочных переводов, изготовленных из высокомарганцовистой аустенитной стали 110Г13Л – стали Гадфильда. Твердость после наплавки 20-25HRC, а после наклепа – 40-45 HRC.
Для наплавки бронзы на сталь разработаны бронзовые порошковые проволоки, например ПП-Бр.А9Ж4.
3.4 Ленты.
Для наплавки под флюсом применяют холоднокатаную, литую, порошковую, металлокерамическую ленту.
Для наплавки применяют холоднокатаную ленту толщиной 0,4 – 1,0 мм и шириной 20-100мм. Чаще других применяется лента из пружинных сталей 65Г и 50ХФА, а также из нержавеющих сталей 10Х13, 10Х18Н9Т.
Литая лента выпускается толщиной 0,7 – 1,0 мм и шириной 30-100 мм. Лента поставляется в термически обработанном состоянии – отожженная в плотных рулонах. Преимуществом литой ленты является ее относительно низкая стоимость. Имеет маркировку, начинающуюся с букв ЛЛ– литая лента, например ЛЛ-У30ГС (2,8-3,5%С), ЛЛ-40Х13.
Порошковая лента эффективно используется при необходимости наплавки высоколегированных сплавов с большим содержанием углерода. Целесообразно ее применение для однослойной наплавки массивных изделий. Лента выпускается размером 3х(20-50) мм. Наплавка лентами производится под флюсом или открытой дугой. Имеет маркировку, начинающуюся с букв ПЛ– порошковая лента, например ПЛ-300Х25Н3С3 (3,0%С – в наплавленном металле).
Металлокерамическая лента изготавливается путем прокатки смеси металлических порошков и последующего спекания. Основой служит порошок пластичного металла – железа, меди или никеля. Благодаря этому готовая лента обладает вполне удовлетворительной прочностью и пластичностью. Изготавливается толщиной 0,8-1,2 мм, шириной 25-100 мм. Преимуществом металлокерамической ленты является повышенная производительность наплавки. Это обусловлено пористостью состава ленты, приводящей к соответствующему увеличению ее электросопротивления, а значит и к усиленному нагреву вылета электродной ленты в процессе ее плавления. Имеет маркировку, начинающуюся с букв ЛМ– лента металлокерамическая, например ЛМ-70Х3М (0,6-0,8%С – в наплавленном металле).
3.5 Литые прутки.
Литые прутки используют в качестве присадки при газопламенной и аргонодуговой наплавке.
Размеры прутков:
– диаметр 6-8мм,
– длина 100-400мм.
В таблице приведены наименования и химический состав в % наиболее употребительных литых присадочных прутков:
Марка сплава | C | Si | Mn | Cr | Ni | W | Co | Fe |
Сормайт (высокохромистый чугун) | 2,5-3,3 | 2,8-3,5 | 1,5 | 25-31 | 3-5 | - | - | остальн. |
Стеллит В2К (кобальтовый сплав с хромом и вольфрамом) | 1,75-2,25 | 1,0-2,0 | - | 28-32 | ≤ 2 | 14-17 | 48-53 | ≤ 3 |
Стеллит В3К | 0,9-1,3 | 1,75-2,75 | - | 28-32 | ≤ 2 | 4,0-5,0 | 58-63 | ≤ 3 |
3.6 Гранулированные порошки.
В качестве присадочного материала при плазменной и индукционной наплавке применяют гранулированные порошки, изготавливаемые путем распыления струи жидкого сплава водой или газом высокого давления. Форма частиц может быть сферической или осколочной. Сфероидизированные порошки отличаются хорошей сыпучестью и не застревают в дозирующих устройствах.
Для плазменно-порошковой наплавки используют сферические порошки с размером частиц 40-100 мкм.
Для индукционной наплавки выпускаются осколочные порошки, т.к. гранулы не скатываются с наплавляемого изделия.
Примеры наиболее употребительных порошков на основе никеля с хромом и бором в таблице.
марка порошка | химический состав, % | твердость напл. мет. HRC | |||||
C | Si | Cr | Ni | B | Fe | ||
ПГ-ХН80СР2 | 0,3-0,6 | 1,5-3,0 | 12-15 | основа | 1,5-2,5 | ≤ 5 | 38-43 |
ПГ-ХН80СР4 | 0,6-1,0 | 3-5 | 13-17 | основа | 2,5-4 | ≤ 5 | 57-62 |
3.7 Флюсы для механизированной наплавки.
Различают флюсы общего назначения и специальные. Флюсы общего назначения предназначены для механизированной дуговой сварки и наплавки углеродистых и низколегированных сталей углеродистой и низколегированной сварочной проволокой. Флюсы специальные предназначены для отдельных способов и целей: электрошлаковой сварки и наплавки, сварки и наплавки легированных сталей и специальных сплавов.
По способу изготовления флюсы разделяют на плавленые и керамические.
Плавленые флюсы получают сплавлением компонентов шихты в электрических или пламенных печах.
Керамические флюсы изготавливают из смесей порошкообразных материалов, скрепляемых при помощи клеящих веществ, главным образом жидким стеклом.
По строению частиц плавленые флюсы разделяют на стекловидные и пемзовидные.
Стекловидный флюс представляет собой прозрачные зерна. Они бесцветные или же окрашены в зависимости от состава в различные цвета – от светло-синего до черного.
Пемзовидный флюс – зерна пенистого материала белого или светлых оттенков желтого, зеленого и других цветов.
Высококремнистые марганцевые флюсы АН-348-А, ОСЦ-45, АН-42, АН-60 применяют для наплавки преимущественно в сочетании с углеродистой, а иногда и с низколегированной проволокой. Флюсы обеспечивают хорошее формирование, малую склонность к образованию пор и удовлетв. отделимость шлаковой корке при нагреве ниже 4000С.
Флюс АН-20 используют в сочетании с низколегированной и высоколегированной проволокой. Шлаковая корка удовлетворительно отделяется при нагреве детали до 4500С.
Пемзовидный химически нейтральный флюс 48-0Ф-6М желтого цвета применяют в сочетании с высоколегированной проволокой, например при наплавке нержавеющих материалов. Особенность флюса – необходимость высокой температуры прокалки – 900-9500С и длительной выдержки при этой температуре 5-6 часов для снижения содержания влаги. Чтобы флюс не поглощал влагу из воздуха, его нужно хранить в сухих помещениях. Срок годности до использования ограничен, если он нарушен, то требуется повторная прокалка. Шлаковая корка удовлетворительно отделяется при нагреве детали до 600-7000С.
Для электрошлаковой наплавки применяют флюсы АНФ-1П, АН-14, АН-25, АН-8. Флюс Эти флюсы обладают высокой электропроводностью в расплавленном состоянии и обеспечивают устойчивый электрошлаковый процесс. Флюс АН-25 предназначен для возбуждения электрошлакового процесса – он электропроводен в твердом состоянии. При прохождении тока быстро нагревается и расплавляется, образуя начальную ванну жидкого шлака – даже без возбуждения сварочной дуги.
Керамические флюсы. Для наплавки представляют интерес керамические флюсы, которые позволяют при использовании стандартных и недефицитных сварочных проволок получать легированный наплавленный металл повышенной износостойкости.
Хорошее применение нашли керамические флюсы АНК-18, АНК-19. Состав и свойства металла, наплавленного низкоуглеродистой проволокой Св-08, Св-08а под керамическим флюсом приведены в табл.
Марка флюса | Содержание элементов, % | Твердость HB | |||
C | Mn | Si | Cr | ||
АНК-18 | 0,2-0,4 | 1,0-1,8 | 0,5 | 2,5-5,0 | 3500-4500 |
АНК-19 | 0,4-0,5 | 1,0-1,5 | 0,5 | 4,0-6,0 | > 4500 |
Оба флюса обеспечивают хорошее формирование наплавленного металла, легкую отделимость шлаковой корки, высокую стойкость наплавленного металла против образования пор и трещин и возможность наплавки на переменном и постоянном токе.
АНК-18 широко применяют для автоматической наплавки колес мостовых кранов, опорных катков, роликов, натяжных колес экскаваторов, тракторов.
4. Способы наплавки [2, 1, 9].
4.1 Ручная дуговая наплавка покрытыми электродами.
Благодаря простоте, применимости для многих разнообразных условий наплавка покрытыми электродами является наиболее распространенным способом. Обычно используют электроды диаметром 3-6мм, что зависит от размеров наплавляемых деталей и требуемой толщины слоя.
Наплавку обычно выполняют в нижнем положении и применяют следующие величины варочного тока:
Диаметр стержня электрода, мм | ||||
Сварочный ток, А | 80-110 | 100-160 | 140-220 | 180-300 |
Чтобы меньше разбавлять наплавку основным металлом наплавку первых слоев следует вести короткой дугой на минимальном токе.
Производительность ручной наплавки невелика и составляет 0,8-2 кг/ч. С целью повышения производительности иногда применяют наплавку пучком электродов.
Качество наплавленного металла зависит от квалификации сварщика.
4.2 Автоматическая наплавка под флюсом.
Автоматическая наплавка под флюсом выполняется: автоматами (тракторами) для сварки под флюсом; головками для автоматической сварки, предназначенными для сварки (наплавки) продольных или кольцевых швов и установленными на наплавляющих или колоннах.
При наплавке под флюсом отдельного валика на горизонтальную поверхность на обычных режимах доля основного металла в сварном шве составляет около 2/3, наплавленного 1/3. Разбавление наплавленного металла основным уменьшают сокращением шага наплавки m (см. рисунок), а также ограничением силы сварочного тока.
Наплавка под флюсом может выполняться как проволокой сплошного сечения, так и порошковой.
Производительность наплавки одним электродом диаметром 2-6мм – 2-15 кг/ч.
Для крупных деталей с целью повышения производительности применяют многоэлектродную наплавку. При этом плавятся несколько проволок, подаваемых в зону наплавки. Проволоки подключаются к одному полюсу сварочного источника и расположены поперек направлению наплавки. Под флюсом создается общая сварочная ванна, электроды плавятся поочередно. Благодаря уменьшению затрат тепла на плавление флюса коэффициент наплавки возрастает, а доля основного металла в наплавке снижается (см. рисунки).
Для этих же целей и с тем же эффектом в качестве плавящегося электрода используют ленту малой толщины и большой ширины. Дуга, перебегая от одного края ленты к другому, равномерно оплавляет торец ленты. Коэффициент наплавки высокий, глубина проплавления и доля в наплавке основного металла тем ниже, чем больше ширина ленты (см. рисунки).
|
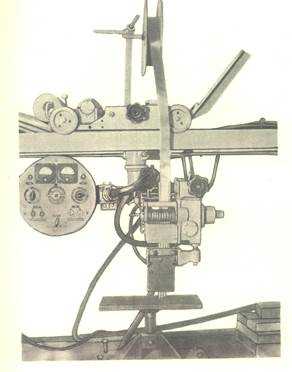
Автомат АДС-1000, переоборудованный для наплавки электродной лентой
Вал, наплавленный лентой
Производительность многоэлектродной наплавки и наплавки электродной лентой – 5-30 кг/ч.
4.3 Механизированная наплавка плавящимся электродом в среде защитных газов.
Наиболее употребительной является механизированная (полуавтоматическая) наплавка сталей в среде углекислого газа или в смесях аргона с углекислым газом. Применяется сплошная или порошковая проволока диаметром 1,2-3,6мм. Производительность наплавки 2-10 кг/ч.
Применяется также автоматическая наплавка.
Распространенной областью применения наплавки плавящимся электродом в среде защитных газов является наплавка деталей сложной формы, а также наплавка внутренних поверхностей отверстий, цилиндров, полых валов, т.е. там, где наплавка под флюсом невозможна из-за скапливания флюса, шлаковой корки.
Распространена автоматическая наплавка бронзы на стальные штоки, валы. Применяется бронзовая проволока, защитная среда аргон.
Для названных способов наплавки применяются специализированная оснастка и сварочный инструмент, проектируемые под конкретные задачи (см. Рис.).
Рис. Автоматическая наплавка бронзы на внутреннюю поверхность
стального ледоскола выдвижного устройства.
4.4 Дуговая наплавка неплавящимся электродом.
При дуговой наплавке неплавящимся электродом используются горелки для сварки неплавящимся электродом, аргон или гелий в качестве защитного газа и присадочные прутки. Применяются проволоки сплошного сечения и литые прутки. Наплавка может выполняться как вручную, так и специализированными автоматами.
4.5 Плазменная наплавка.
Плазмой принято считать частично или полностью ионизированный газ, состоящий из нейтральных атомов и молекул, ионов и электронов. Типичное плазменное состояние вещества имеет место в электрическом газовом разряде.
При плазменной наплавке применяется высокотемпературный тепловой источник – плазма или так называемая плазменная дуга, представляющая собой сжатую электрическую сварочную дугу, обеспечивающую низкотемпературную плазменную струю с температурой в Т= 10 000-30 000 0С, в отличие от горячей термоядерной плазмы, характеризующейся температурой в десятки миллионов градусов, например на солнце.
Плазменные дуги получают в специальных устройствах – плазматронах, в которых сварочная дуга обжимается потоком газа, выходящим из узкого сопла.
Присадочный металл можно подавать в плазменную дугу в виде проволоки или порошка (см. рисунки).
На рисунках: 1 – неплавящийся электрод, 2- сопло, формирующее плазменную дугу.
ПГ – плазмообразующий газ, П – присадочный порошок, ЗГ – защитный газ, ТГ – транспортирующий газ.
Неплавящийся электрод – это обычно вольфрамовый пруток диаметром 2-8мм. Плазмообразующий, защитный и транспортирующий газ – аргон. Сопло изготавливается из меди и охлаждается проточной водой.
Плазменную наплавку отличает высокая температура плазмы, позволяющая эффективно расплавлять присадку, а также возможность широкой регулировки теплового режима. Это позволяет управлять количеством наплавляемого металла и глубиной проплавления основного металла.
Похожие статьи:
poznayka.org
Материалы для наплавки, электроды, проволока, флюсы, порошки, наплавочные материалы
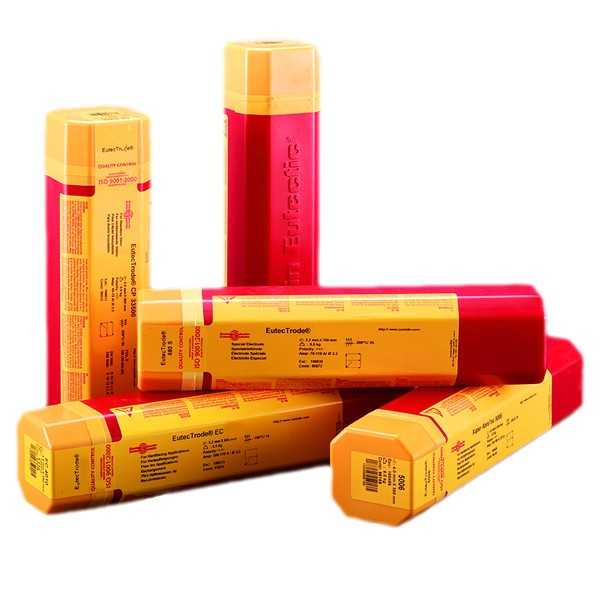
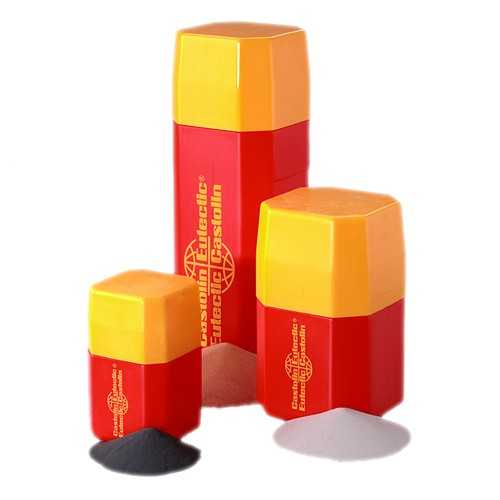
При восстановительном ремонте наплавочные материалы в основном выбирают исходя из способа нанесения и хим. состава основного материала, выбирая при этом материал наиболее близки по химическому составу. Часто при работе изделия в условиях повышенного износа целесообразнее подбирать материал для ремонта стойкий к тем видам износа, которые имеют место быть при эксплуатации детали.
При изготовлении детали можно было бы предусмотреть факторы износа и изготовить всю деталь из материала стойкого к износу, но это часто экономически нецелесообразно. При ремонте же, когда мы имеем в целом пригодную деталь, но с изношенной поверхностью наиболее целесообразно подобрать материалы для наплавки, сопротивляющиеся тем видам износа, при которых будет работать деталь в процессе эксплуатации.
Нанесение дорогостоящих покрытий полностью себя экономически оправдывает. Правильный выбор материала для восстановления и ремонта может не только продлить работу детали, но и увеличить в несколько раз срок службы по отношению к новой детали без упрочненной поверхности.
Иногда для получения требуемого хим. состава в поверхностном слое необходимо использовать не пластичные металлы. Тогда при нанесении покрытий используют порошки, наносимые на поверхность различными способами, как оплавлением неплавящимся электродом, так и при помощи плазмы и наплавкой взрывом.
Таким образом при ремонте деталей необходимо определить материал наплавки (в том числе и материал переходного слоя при необходимости), способ нанесения, а также режим нанесения.
В нашей компании вы можете купить материалы для наплавки любых металлов и для любого типа нанесения покрытия, также вы можете заказать товар с доставкой по России. Если вы не уверены в правильности своего решения, наши специалисты готовы дать квалифицированную консультацию и помочь с правильным выбором необходимой продукции.
naplavca.ru
Способы наплавки
Для наплавки используют большинство известных способов сварки плавлением и давлением. Самым простым способом наплавки является ручная дуговая наплавка. Также применяют автоматическую дуговую наплавку под флюсом. Для наплавки большого количества металла (толщина наплавляемого слоя не менее 5 мм) используют электрошлаковую наплавку с использованием нескольких электродов. Существует много разновидностей наплавки с использованием плазменной дуги или газового пламени. В последнее время очень широко применяется лазерная наплавка, позволяющая, в частности, эффективно исправлять точечные дефекты и практически не приводящая к деформации изделия после наплавки. Помимо способов сварки плавлением для наплавки применяются и способы сварки давлением (например: электроконтактная наварка проволоки и ленты). Существуют также и специализированные способы наплавки (например: индукционная наплавка порошкообразным сплавом). Схемы некоторых способов наплавки приведены в табл. 1С, сравнительные характеристики – в табл. 2С.
Табл. 1С
Схемы способов наплавки | |
Наплавка неплавящимся угольным (графитовым) электродом с расплавлением слоя сыпучего зернистого наплавочного материала, предварительно уложенного на наплавляемую поверхность 1 – неплавящийся угольный (графитовый) электрод; 2 – сыпучий зернистый наплавочный материал; 3- наплавляемая деталь; 4 – наплавленный слой; Vн – скорость наплавки | |
Электрошлаковая наплавка плавящимися электродами (электродными проволоками) с перемещаемым медным ползуном 1 – электродные проволоки; 2 – медный водоохлаждаемый ползун; 3- наплавляемая деталь; 4 – наплавленный слой; Vн – скорость наплавки; Vп – скорость подачи электродых проволок; nк – частота поперечных колебаний электродов. | |
Наплавка ленточным электродом в защитных газах или под флюсом 1 – ленточный электрод; 2 – сварочная дуга; 3- наплавляемая деталь; 4 – наплавленный слой; Vн – скорость наплавки; Vп – скорость подачи ленточного электрода; Sд – перемещение дуги по торцу ленточного электрода. | |
Электроконтактная наварка проволоки 1 – наплавляемая заготовка;, 2 – наплавленный металл; 3 – присадочная проволока, 4 – наплавляющий ролик; 5 – понижающий трансформатор, 6 – трехкулачковый патрон; 7 – центр; Рсж – усилие сжатия; Vсв – скорость сварки; n – частота вращения наплавляемого изделия.. Процесс аналогичен шовной сварки одним дисковым электродом. | |
Индукционная наплавка порошкообразным сплавом 1 — наплавляемая заготовка; 2 — порошкообразный наплавочный материал, предварительно нанесенный на наплавляемую поверхность; 3 —индуктор; 4 — охлаждающая жидкость; 5 – источник питания токов высокой частоты |
Табл. 2С
Сравнительная характеристика некоторых способов наплавки | |||
Способ наплавки | Производи- тельность*, кг/ч | Доля основного металла γо, % | Толщина наплавленного слоя hн, мм |
Угольным электродом порошком | 0,5-3,0 | 1 | 0,3-3,0 |
Аргоно-дуговая неплавящимся электродом | 1,0-7,0 | 10-30 | 2,5-5,0 |
Плавящимся электродом в защитном газе | 1,5-9,0 | 30-60 | 3,0-5,0 |
Ручная дуговая покрытыми электродами | 0,8-3,0 | 20-50 | 2,0-5,0 |
Под флюсом одной проволокой | 2,0-12 | 30-60 | 3,0-5,0 |
Под флюсом многоэлектродная | 5,0-40 | 15-30 | 5,0-8,0 |
Под флюсом ленточным электродом | 5,0-40 | 10-20 | 2,5-5,0 |
Электрошлаковая электродными проволоками | 20-60 | 10-20 | 6,0-50 |
Плазменная порошком | 0,8-6,0 | 5-15 | 0,3-6,0 |
*Производительность – масса металла, наплавленного в единицу времени |
studfiles.net
Материалы для упрочняющей наплавки
Упрочняющая наплавка применяется как при ремонте изношенных деталей, так и при изготовлении новых деталей. За счет нанесения на поверхностность деталей слоя металла, их поверхности приобретают специфические свойства, обеспечивая хорошее сопротивление износу.
Норма DIN 8555 классифицирует все сварочные материалы, применяемые для восстановления, без разделения на технологии. Материалы для упрочняющей наплавки зарубежных производителей, обозначение которых идет в соответствии с DIN 8555, обеспечивает экономический эффект от увеличения ресурса инструмента, который трудно переоценить.
На сегодняшний день на белорусском рынке присутствует большое количество материалов для упрочняющей наплавки зарубежных производителей, обозначение которых идет в соответствии с DIN 8555.
Сруктура обозначения сварочных материалов:
1. Способ сварки
Символ | Вид сварки |
G | Газовая |
E | Ручная дуговая штучным электродом |
MF | Дуговая порошковой проволокой |
TIG | В среде защитных газов вольфрамовым электродом |
MSG | В среде защитных газов плавящимся электродом |
UP | Под флюсом |
2. Тип присадочного материала или металла шва
Индекс | Тип присадочного материала или металла шва |
1 | До 0,4% С и не более 5% в сумме Cr, Mn, Mo, Ni |
2 | Более 0,4% С и более 5% в сумме Cr, Mn, Mo, Ni |
3 | Легированный, со свойствами горячекатаной стали |
4 | Легированный, со свойствами быстрорежущей стали |
5 | Легированный, с более чем 5% Cr, с низким содержанием С (до 0,2%) |
6 | Легированный, с более чем 5% Cr, с содержанием С (от 0,2% до 2%) |
7 | Аустенитно-марганцовистый, с 11…18% Mn, с более 0,5% С и до 3% Ni |
8 | Аустенитно-хромо-никель-марганцовистый |
9 | Хромо-никелевые коррозионостойкие, жаростойкие стали |
10 | С высоким содержанием углерода и легированные Cr, без добавочного образования карбидов |
20 | На основе Co, легированный Cr-W с или без Ni и Mo |
21 | Карбидо-содержащий (шлак, литье или порошок) |
22 | На основе Ni, легированный Cr, Cr-B |
23 | На основе Ni, легированный Mo |
30 | На основе Cu, легированный Sn |
31 | На основе Cu, легированный Al |
32 | На основе Cu, легированный Ni |
3. Вид присадочного материала
Символ | Вид присадочного материала |
GM | Канатный |
GO | Литой |
GZ | Тянутый |
GF | Спеченный |
UM | Покрытый |
4. Твердость наплавленного слоя
Индекс | Диапазон твердости |
150 | HB 125…175 |
200 | HB 175…225 |
250 | HB 225…275 |
300 | HB 275…325 |
350 | HB 325…375 |
400 | HB 375…450 |
40 | HRC 37…42 |
45 | HRC 42…47 |
50 | HRC 47…52 |
55 | HRC 52…57 |
60 | HRC 57…62 |
65 | HRC 62…67 |
70 | более HRC 67 |
5. Свойства наплавленного слоя
Символ | Свойства наплавленного слоя |
C | Стойкий к коррозии в агрессивных средах |
G | Сопротивление абразивному износу |
K | После наплавки подвергается упрочнению наклепом или термообработкой |
N | Немагнитный |
P | Стойкий к ударным нагрузкам |
R | Стойкий к коррозии в слабоагрессивных средах |
S | Со свойствами быстрорежущей стали |
T | Жаростойкий |
Z | Теплоустойчивый, окалиностойкий для температур выше 6000 С |
материалы для наплавки, наплавка, наплавкой, способы наплавки, технология наплавки, упрочняющая наплавка, при упрочняющей наплавке, наплавочные материалы, наплавленный слой, наплавленного слоя, наплавленный металл, наплавленного металла, газовая наплавка, плазменная наплавка, осуществлять наплавку, наплавка электродами, электроды для наплавки
Количество просмотров: 1008
promsvarka.by
Материалы для наплавки
Количество просмотров публикации Материалы для наплавки – 11
Получение наплавленного слоя с особыми свойствами, как правило, связано с использованием сплавов со значительным количеством легирующих элементов.
Для наплавки применяются проволоки сплошного сечения и порошковые, ленты холоднокатаные, порошковые и спеченные порошки, покрытые электроды, литые прутки, гибкие шнуры, флюсы плавленые и керамические и другие материалы.
При дуговой наплавке плавящимся или неплавящимся электродом в среде защитных инертных газов и плазменнои̌ наплавке химический состав наплавленного металла по всем основным легирующим элементам примерно соответствует химическому составу электродного материала.
При наплавке в среде защитных газов легирование наплавленного металла достигается в основном выбором соответствующᴇᴦο присадочного металла (электродная проволока сплошного сечения, порошковая и др.) или применением дополнительных наплавочных материалов (паст, перед сваркой наносимых на кромки, или присадочных прутков, порошков, засыпаемых на поверхность перед сваркой или вдуваемых в сварочную ванну, дополнительных проволок, прутков, укладываемых на поверхность или подаваемых в сварочную ванну, и др.).
Наплавка электродами, имеющими специальные покрытия, позволяет обеспечить довольно значительное легирование через составляющие электродного покрытия (обычно вводимые в покрытия в виде порошков металлов, сплавов или углеродистых составляющих) или посредством выбора состава металлического стержня электрода.
Переход легирующих элементов из стержня и покрытия электрода зависит от свойств элемента (ᴇᴦο сродства к кислороду, температуры испарения и др.), от композиции электродного покрытия и металла стержня электрода, а аналогичным образом от коэффициента массы покрытия. Варьируя составы электродного стержня и покрытия, можно получить множество составов наплавленного металла, легированных различными элементами и, следовательно, обладающими различными свойствами в исходном состоянии после наплавки или после последующей термообработки.
При наплавке под флюсом легирование осуществляется, как правило, с использованием следующих материалов.
1. Углеродистая или легированная электродная проволока сплошного сечения, металлическая холоднокатаная, литая или спрессованная из порошков ленты и нелегирующие или слаболегирующие, слабоокислительные плавленые, а аналогичным образом керамические флюсы (хотя иногда для наплавки углеродистых и низколегированных сталей используют высококремнистые, высокомарганцовистые флюсы, приводящие к окислению ряда легирующих элементов при наплавке).
2. Порошковая проволока (порошковая лента) при тех же флюсах. Порошковая проволока может содержать до ~ 40 % легирующих металлических составляющих от общей массы проволоки. В ленты сложнои̌ формы должна быть введено до 70 % легирующих металлических составляющих.
3. Легирующие флюсы, в основном керамические, содержащие легирующие металлические добавки, и флюсы-смеси.
4. Порошки, предварительно засыпаемые на наплавляемую поверхность или используемые в процессе наплавки, а аналогичным образом легированные прутки, укладываемые на наплавляемую поверхность и др.
Применение в качестве плавящегося электрода ленты весьма целесообразно. В качестве наплавочных применяют обычно ленты холоднокатаные толщинои̌ 0,4 – 1 мм и ширинои̌ 20 – 100 мм, а аналогичным образом ленты, получаемые прокаткой залитого в охлаждаемые валки жидкого металла (например, чугуна) и спрессованные холоднои̌ прокаткой из порошков и дополнительно спеченные – металлокерамические.
Весьма разнообразные составы наплавленного металла могут быть получены посредством порошковых проволок и лент, изготовляемых из низкоуглеродистой ленты и сердечника, состоящᴇᴦο из смеси металлических порошков или смеси металлических порошков и газо- и шлакообразующих компонентов.
Керамические флюсы обычно используют при наплавке низкоуглеродистой и низколегированнои̌ проволокой. Так, керамический флюс АНК-18 (~ 6,5 % СаСО3; ~ 27 % CaF2; ~ 28 % MgO; ~ 18 %Аl2O3; ~ 2,5 Na2O +K2O; ~ 6 % Cr; ~ 2,5 % Mn; ~ 0,16 % С; ~ 2 % Al; ~ 0,25 Ti; ~ 0,25 % Si и 3,5 % Fe) при использовании нелегированнои̌ проволоки марки Св-08А при оптимальных режимах обеспечивает получение наплавленного металла состава 0,15 – 0,25 % С; 0,2 – 0,4 % Si; 1 – 1,8 % Mn; 3 – 5 % Cr; S <0,04 %; P <0,03 % и имеющᴇᴦο твердость HRC 35 – 45.
referatwork.ru